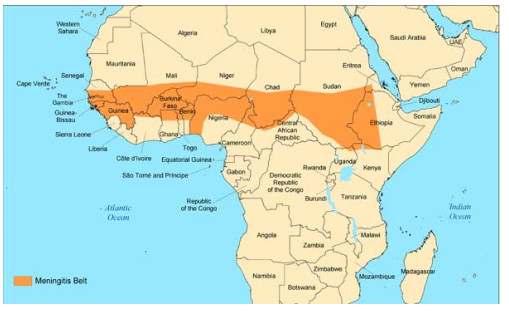
In order to grasp the degradation of rolling bearings and prevent the failure of mechanical equipment, a remaining useful life (RUL) prediction method of rolling bearings based on degradation detection and deep bidirectional long short-term memory networks (BiLSTM) was proposed, considering the incomplete degradation feature extraction and low prediction accuracy of existing methods. By extracting the characteristics of time domain, frequency domain, and time-frequency domain of the full-life bearing vibration signal, the monotonicity, trend, and robustness measurement indexes of each feature were calculated. The best feature set that can fully reflect the degradation information was constructed by ranking the weighted comprehensive indexes of the features. A degradation detection strategy was used to determine the degradation starting time for setting piecewise linear network label. The RUL prediction model based on deep BiLSTM was established and optimized through Dropout technology and piecewise learning rate. The model was verified by the full-life data set of rolling bearings. The results showed that compared with the support vector machine (SVM), the traditional recurrent neural network (RNN), the single-layer BiLSTM, and long short-term memory networks (LSTM) model without Dropout, the proposed method fitted the degradation trend best, and the root mean square error (RMSE) was the smallest and only 0.0281, which improved the accuracy of RUL prediction of rolling bearings, helped prevent bearing failure, and ensured the safe and reliable operation of rotating machinery.
Citation: Shuang Cai, Jiwang Zhang, Cong Li, Zequn He, Zhimin Wang. A RUL prediction method of rolling bearings based on degradation detection and deep BiLSTM[J]. Electronic Research Archive, 2024, 32(5): 3145-3161. doi: 10.3934/era.2024144
[1] | Yangrong Li, Shuang Yang, Qiangheng Zhang . Odd random attractors for stochastic non-autonomous Kuramoto-Sivashinsky equations without dissipation. Electronic Research Archive, 2020, 28(4): 1529-1544. doi: 10.3934/era.2020080 |
[2] | Lianbing She, Nan Liu, Xin Li, Renhai Wang . Three types of weak pullback attractors for lattice pseudo-parabolic equations driven by locally Lipschitz noise. Electronic Research Archive, 2021, 29(5): 3097-3119. doi: 10.3934/era.2021028 |
[3] | Shu Wang, Mengmeng Si, Rong Yang . Dynamics of stochastic 3D Brinkman-Forchheimer equations on unbounded domains. Electronic Research Archive, 2023, 31(2): 904-927. doi: 10.3934/era.2023045 |
[4] | Dingshi Li, Xuemin Wang . Regular random attractors for non-autonomous stochastic reaction-diffusion equations on thin domains. Electronic Research Archive, 2021, 29(2): 1969-1990. doi: 10.3934/era.2020100 |
[5] | Meiyu Sui, Yejuan Wang, Peter E. Kloeden . Pullback attractors for stochastic recurrent neural networks with discrete and distributed delays. Electronic Research Archive, 2021, 29(2): 2187-2221. doi: 10.3934/era.2020112 |
[6] | Wenlong Sun . The boundedness and upper semicontinuity of the pullback attractors for a 2D micropolar fluid flows with delay. Electronic Research Archive, 2020, 28(3): 1343-1356. doi: 10.3934/era.2020071 |
[7] | Xin-Guang Yang, Lu Li, Xingjie Yan, Ling Ding . The structure and stability of pullback attractors for 3D Brinkman-Forchheimer equation with delay. Electronic Research Archive, 2020, 28(4): 1395-1418. doi: 10.3934/era.2020074 |
[8] |
Guifen Liu, Wenqiang Zhao .
Regularity of Wong-Zakai approximation for non-autonomous stochastic quasi-linear parabolic equation on |
[9] | Xiaojie Yang, Hui Liu, Haiyun Deng, Chengfeng Sun . Pullback D-attractors of the three-dimensional non-autonomous micropolar equations with damping. Electronic Research Archive, 2022, 30(1): 314-334. doi: 10.3934/era.2022017 |
[10] | Guowei Liu, Hao Xu, Caidi Zhao . Upper semi-continuity of pullback attractors for bipolar fluids with delay. Electronic Research Archive, 2023, 31(10): 5996-6011. doi: 10.3934/era.2023305 |
In order to grasp the degradation of rolling bearings and prevent the failure of mechanical equipment, a remaining useful life (RUL) prediction method of rolling bearings based on degradation detection and deep bidirectional long short-term memory networks (BiLSTM) was proposed, considering the incomplete degradation feature extraction and low prediction accuracy of existing methods. By extracting the characteristics of time domain, frequency domain, and time-frequency domain of the full-life bearing vibration signal, the monotonicity, trend, and robustness measurement indexes of each feature were calculated. The best feature set that can fully reflect the degradation information was constructed by ranking the weighted comprehensive indexes of the features. A degradation detection strategy was used to determine the degradation starting time for setting piecewise linear network label. The RUL prediction model based on deep BiLSTM was established and optimized through Dropout technology and piecewise learning rate. The model was verified by the full-life data set of rolling bearings. The results showed that compared with the support vector machine (SVM), the traditional recurrent neural network (RNN), the single-layer BiLSTM, and long short-term memory networks (LSTM) model without Dropout, the proposed method fitted the degradation trend best, and the root mean square error (RMSE) was the smallest and only 0.0281, which improved the accuracy of RUL prediction of rolling bearings, helped prevent bearing failure, and ensured the safe and reliable operation of rotating machinery.
Meningitis is a disease of the central nervous system that leads to soreness of the lining around the brain and spinal cord. It is an acute inflammation of the defensive membranes covering the brain and spinal cord, collectively known as the meninges. This occurs when fluid surrounding the meninges is infected. Meningitis may be fatal because of the severe nature of inflammation of the brain and spinal cord, so the illness is treated as a medical emergency [1]. If not treated immediately, it can lead to permanent disability, coma, brain swelling, or even death. It is mainly detected by a lumbar puncture where a needle is used to extract a sample of cerebrospinal fluid from the spinal canal. It can also be diagnosed by brain imaging such as computerized tomography scan or magnetic resonance imaging, swab of fluid from the nose or throat, and blood and urine testing [2].
Meningitis infections can be caused by different pathogens, but most of these infections are attributed to virus, which is the least serious type with the next common cause being bacteria, fungi and parasites [3]. Bacterial meningitis is the most severe and epidemic-prone disease, affecting a significant part of the world's population. The bacteria are present worldwide, although in Africa, the disease is endemic to the meningitis belt. The meningitis belt spans from the Atlantic Ocean to the Red Sea, semi-arid area of sub-Saharan Africa. There is also a high tendency for outbreaks to spread across countries due to the insecure state of African borders. Other sub-Saharan African countries have also recorded large outbreaks [4].
Case fatality rates, which are often between 1 and 2 days after the onset of symptoms, may be as high as 50–80% when not treated and approximately 8–15% when treated [5]. The northern part of Ghana, namely, the Northern, North East, Savannah, Upper East and Upper West regions, lies completely in the meningitis belt and has experienced recurrent outbreaks, often during dry weather seasons characterized by low humidity, high temperatures and abundance of dust. The Brong Ahafo, Bono East and upper parts of the Volta region have also recorded sporadic cases [6].
Figure 1 shows the geographic distribution of meningitis in West African affected countries.
Bacterial meningitis was initially transmitted from an animal to a human being but has since become a person-to-person transmission through infected air droplets, saliva, respiratory secretions and direct contact with contaminated surfaces. The infection spreads easily when an infected person comes into close proximity or has long-term contact with others. Staying in overcrowded housing, attending sports or cultural events, sharing utensils, coughing, sneezing and kissing can all contribute to disease outbreaks [8].
Bacterial meningitis is caused by some strains of bacteria such as Streptococcus pneumoniae (pneumococcus), Neisseria meningitidis (meningococcus), Haemophilus influenzae (Haemophilus) and Listeria monocytogenes (Listeria). Neisseria meningitidis, Streptococcus pneumoniae and Haemophilus influenzae type B were the most common bacteria, accounting for over 80% of all bacterial meningitis cases. Meningitis caused by Haemophilus influenzae type B is much less common, now that the Haemophilus influenzae type B vaccine is administered to all children as part of routine immunization [1].
Most patients recover well after prompt treatment; however, several patients experience severe health complications even after prompt treatment. These complications include hearing impairments, neurological disabilities and loss of limb function [9]. The estimated risk of at least one complication after recovery is nearly 4 out of every 10 patients, with a median risk of approximately 20% in such patients [10].
The awareness of bacterial meningitis as a vaccine-preventable disease is commendable, but a number of people may not know that these vaccines are strain specific. Several previous researchers have used mathematical models to analyze the transmission and control dynamics of bacterial meningitis [11,12,13,14]. For models that consider vaccination, there is a common assumption that the vaccine does not confer immunity to all recipients, and is used as a means of treatment for infected people. However, this assumption must be lifted, as it is nowhere close to the real-life situation where the available vaccines confer varying degrees of duration of immunity against the specified strain. Furthermore, these specific vaccines are used for prevention (routine immunization) and in response to outbreaks (prompt reactive vaccination) but not for treatment [15].
The dynamics of cerebrospinal meningitis in the Jirapa district of the Upper West region of Ghana was presented via mathematical modeling by [13]. The existence of a solution to the model and its stability were examined. It was discovered that early treatment, adherance to cerebrospinal meningitis protocols, and the combined efforts of medical personnel and traditional healers could help control the disease.
In [16,17], an age-structured mathematical model of meningitis A (MenA) transmission, colonization and disease in the African meningitis belt was formulated and used to investigate the effects of various vaccination strategies. The validity of the model was assessed by comparing the simulated incidence of invasive MenA and the prevalence of MenA carriage with the observed incidence and carriage data. The model was able to reproduce the observed dynamics of MenA epidemics in the African meningitis belt, including seasonal increases in incidence, with large epidemics occurring every 8–12 years. It was established that the most effective modeled vaccination strategy is to conduct mass vaccination campaigns every 5 years for children aged 1–5 years.
Research [18] also used mathematical models to identify the crucial factors determining the dynamics of meningitis. Their simulated results suggest that temporal population immunity plays a key role and should be considered during disease monitoring and assessment of the efficiency of the vaccines deployed. A deterministic model for meningococcal meningitis transmission dynamics with variable total population size was presented in [19]. It was shown analytically and numerically that the disease can be eradicated using effective control measures. Their simulation suggested control measures that can reduce the disease transmission rate and immunity waning rate, as well as boost the vaccination and treatment rates.
A discrete mathematical model for the spread of meningococcal meningitis using cellular automata on graphs was presented in [20]. The discrete nature of the mathematical objects used in the algorithm renders model implementation simple and efficient. It was concluded that both the individual and global behaviours of the disease could be determined.
Research[21] presented a nonlinear deterministic model on the dynamics of bacterial meningitis by incorporating time-dependent controls. Their results showed that carriers had a more significant effect on disease transmission than did the infectious class. This can be attributed to the fact that symptomatic patients are often admitted during the acute phase of the infection. This model was formulated as an optimal control problem to determine the optimal strategies for disease control. It was ascertained that vaccination played a key role in curtailing the spread of the disease. Hence, stakeholders are admonished for pushing for existing or new vaccines and antibiotics to be disbursed in the most affected areas.
To study the dynamics of the 2017 meningitis outbreak in Nigeria, [22] presented a deterministic model for meningitis caused by Neisseria meningitidis. This model was used to investigate the optimal strategy for curtailing the disease spread. The results indicated that combining the two control variables is the most cost-effective strategy because it averts more infections at low costs.
Because the after-effects of meningitis are not always pleasant, [23] presented a susceptible-vaccinated-carrier-infected-recovered-susceptible model to study the dynamics of meningitis. They distinguished between those who recovered with disabilities and those who did not. Their model suggests that a high vaccine uptake rate could control the disease. As an extension of the model for incorporating the treated population, an susceptible-vaccinated-carrier-infected-recovered deterministic compartmental model of the transmission dynamics of bacterial meningitis was presented in [24]. The numerical simulation results demonstrated the effects of the model parameters on each compartment, and established that efficient and effective vaccination and treatment are crucial for disease control.
Even with the availability of drugs and vaccines in the management of meningitis outbreaks, case fatality rate in Ghana remain high ranging between 36–50% [25]. In this study, a novel two-strain deterministic model based on the susceptible-vaccinated-carrier-infected-recovered is developed with new model parameters to obtain a more realistic model.
To formulate the model, a wide range of parameters was used to incorporate the coexistence of two bacterial meningitis strains: Streptococcus pneumoniae and Neisseria meningitidis. It is evident that the available vaccines are strain-specific [26], making the risk of contracting an infection from a strain one has not been vaccinated against great concern. In the proposed model, the total population at time t, denoted by N(t), is divided into nine mutually exclusive epidemiological classes: the susceptible class S(t) that can contract strains 1 and 2, vaccinated classes V1(t),V2(t), carrier classes C1(t),C2(t), infected classes I1(t),I2(t), and two recovered classes R1(t) and R2(t). Thus, N(t) is given by
N(t)=S(t)+V1(t)+V2(t)+C1(t)+C2(t)+I1(t)+I2(t)+R1(t)+R2(t). | (2.1) |
The susceptible class is a population that has not yet been infected and has not received any vaccine against the disease. This is generated by the birth or recruitment rate α and the loss of immunity acquired through previous vaccinations at waning rates ω1,ω2. The susceptible population is reduced by infection through effective contact with infected individuals at rates λ1 and λ2, which are defined as
λ1=β[ηC1(t)+I1(t)]N(t), | (2.2) |
λ2=β[ηC2(t)+I2(t)]N(t), | (2.3) |
where β is the effective transmission probability per contact and 0<η≤1 is a modification parameter indicating the infectiousness of individuals in the carrier class. The population is also reduced by the natural death rate μ and the vaccination rates θ1,θ2. Hence, the rate of change of the susceptible population is represented by the ordinary differential equation (ODE):
dSdt=α+ω1V1+ω2V2−(λ1+λ2+θ1+θ2+μ)S. | (2.4) |
The vaccinated class was divided into two based on the vaccines available against the two strains considered. The vaccinated population with immunity to strain 1 received pneumococcal conjugate vaccines as a form of protection against disease. This population is increased by the vaccination of susceptible individuals at rate θ1. On average, pneumococcal conjugate vaccines take 2 weeks to fully kick in and should protect up to 5 years. As this vaccine does not confer immunity to all strains of bacteria causing meningitis, vaccinated individuals of strain 1 may be infected by another strain, but at a lower rate than unvaccinated individuals. This population is decreased by exposure to the disease or by vaccine waning and natural death. Therefore, the rate of change in the vaccinated population with immunity to strain 1 is represented as
dV1dt=θ1S−(1−ϵ1)λ1V1−(λ2+ω1+μ)V1, | (2.5) |
where 0≤ϵ1≤1 is the level of efficacy of the pneumococcal conjugate vaccine.
The vaccinated population with immunity to strain 2 is the population of individuals who received meningococcal conjugate vaccines as a form of protection from the disease. This population is increased by vaccination of susceptible individuals to this specific strain at a rate of θ2. Individuals often develop immunity within 2 weeks of receiving meningococcal conjugate vaccines and should protect them for 3–5 years. Because this vaccine does not confer immunity to all strains of bacteria causing meningitis, vaccinated individuals of strain 2 may be infected with strain 1 at an effective contact rate λ1, but at a lower rate than unvaccinated individuals. This population is decreased by exposure to infection (1−ϵ1)λ1 or by vaccine waning ω2 and natural death μ. Thus, the rate of change of the vaccinated population with immunity to strain 2 is given as
dV2dt=θ2S−(1−ϵ2)λ2V2−(λ1+ω2+μ)V2, | (2.6) |
where 0≤ϵ2≤1 is the level of efficacy of the meningococcal conjugate vaccine.
The carrier population of strain 1 is made up of a population infected with Streptococcus pneumoniae but does not show any signs or symptoms even though they are infectious. This is generated by the effective contact rate λ1 and decreased as a result of the population becoming symptomatic at rate σ1. This population is decreased by the recovery rate γC1 and natural death rate μ. Consequently, the rate of change in the carrier population of strain 1 is expressed as
dC1dt=λ1(1−τ1)S+(1−ϵ1)λ1V1−(σ1+γC1+μ)C1, | (2.7) |
where τ1 is the proportion moving to the infected class of strain 1 without first passing through here.
The carrier population of strain 2 is composed of a population infected with Neisseria meningitidis, but do not show any signs or symptoms even though they are infectious. This is generated by the effective contact rate λ2, and decreased as a result of the progression of individuals to the infected population of strain 2 at rate σ2. This population is also decreased by the recovery rate γC2 and natural death rate μ. Therefore, the rate of change in the carrier population of strain 2 can be described by the following differential equation
dC2dt=λ2(1−τ2)S+(1−ϵ2)λ2V2−(σ2+γC2+μ)C2, | (2.8) |
where τ2 is the proportion that moves to the infected class of strain 2 without first passing through the carrier population.
The infected population of strain 1 is a population with a fully blown infection of Streptococcus pneumoniae and shows signs and symptoms. This population is said to have survived an average incubation period of 1–3 days. This is also generated by the effective contact rate λ1 and carrier progression at rate σ1. The population is decreased by the recovery rate γI1, disease-induced death rate δ, and natural death rate μ. Hence, the ODE governing the dynamics of the infected population of strain 1 is given by
dI1dt=σ1C1+λ1τ1S+λ1V2−(γI1+δ+μ)I1. | (2.9) |
The infected population of strain 2 is a population with a fully blown infection from Neisseria meningitidis that exhibits signs and symptoms of infection. This population is said to have survived an average incubation period of 4 days. This is also generated by the force of infection λ2 and the progression of the carrier at the rate σ2. The population is decreased by the recovery rate γI2, disease-induced death rate δ, and natural death rate μ. It follows that the rate of change of the infected population of strain 2 is described by the ODE, given as
dI2dt=σ2C2+λ2τ2S+λ2V1−(γI2+δ+μ)I2. | (2.10) |
The first recovered class, R1(t), is the population of individuals who have fully recovered from infection by either strain. This population increases because of the recovery of carriers at rates γC1,γC2 and infections at rates γI1,γI2. They are decreased by the complication rate after a period ∧ and the natural death rate μ. Thus, the rate of change of the fully recovered population is expressed as
dR1dt=γC1C1+γC2C2+γI1ρ1I1+γI2ρ2I2−(∧+μ)R1. | (2.11) |
The second recovered class, R2(t), is the number of individuals who recovered from infection by either strain with complications owing to the sequelae of the delibitating effects among survivors, even after recovery. This population is also increased by the recovery rates of the infected populations γI1,γI2, and the complication rate ∧ and decrease because of the natural death rate μ. Hence, the rate of change of the recovered with complication population is described by the ODE, given by
dR2dt=γI1(1−ρ1)I1+γI2(1−ρ2)I2+∧R1−μR2. | (2.12) |
We note that all parameters are assumed to be nonnegative in an epidemiological sense.
The model parameters and model state variables are shown in Tables 1 and 2.
Parameters | Description |
α | Birth or recruitment rate into susceptible population |
β | Transmission probability |
δ | Disease-induced death rate |
μ | Natural death rate |
σ1 | Rate of progression from carrier of strain 1 to infected population of strain 1 |
σ2 | Rate of progression from carrier of strain 2 to infected population of strain 2 |
γC1 | Recovery rate of carriers of strain 1 |
γC2 | Recovery rate of carriers of strain 2 |
γI1 | Recovery rate of infected with strain 1 |
γI2 | Recovery rate of infected with strain 2 |
θ1 | Strain 1 vaccine uptake rate |
θ2 | Strain 2 vaccine uptake rate |
ϵ1 | Strain 1 vaccine efficacy |
ϵ2 | Strain 2 Vaccine efficacy |
ω1 | Vaccine waning of strain 1 |
ω2 | Vaccine waning of strain 2 |
τ1 | Proportion moving to I1 without first passing through C1 |
τ2 | Proportion moving to I2 without first passing through C2 |
∧ | Complication rate after a period of time |
ρ1 | Proportion moving to R1(t) from strain 1 without first passing through R2(t) |
ρ2 | Proportion moving to R1(t) from strain 2 without first passing through R2(t) |
Variables | Description |
S(t) | Susceptible population who can contract both strains 1 and 2 |
V1(t) | Vaccinated population with immunity to strain 1 |
V2(t) | Vaccinated population with immunity to strain 2 |
C1(t) | Carrier population of strain 1 |
C2(t) | Carrier population of strain 2 |
I1(t) | Infected population of strain 1 |
I2(t) | Infected population of strain 2 |
R1(t) | Fully recovered population from both strains 1 and 2 |
R2(t) | Recovered with complications from both strains 1 and 2 |
(1) Only two strains of bacterial meningitis were considered in this study.
(2) Every individual in the studied population is susceptible to one of the two strains at a given time.
(3) Individuals cannot be infected by more than one bacteria strain at the same time.
(4) The vaccines are only administered to the susceptible population.
(5) A vaccinated individual who loses immunity will return to the susceptible class with no vaccine protection.
(6) There is permanent immunity after full recovery.
Following the descriptions given in Eqs (2.4)–(2.12) and the flow diagram of the two-strain bacterial meningitis model presented in Figure 2, the model governing the system of nine mutually exclusive ODEs for bacterial meningitis population dynamics is expressed as
dSdt=α+ω1V1+ω2V2−(λ1+λ2+θ1+θ2+μ)S,dV1dt=θ1S−(1−ϵ1)λ1V1−(λ2+ω1+μ)V1,dV2dt=θ2S−(1−ϵ2)λ2V2−(λ1+ω2+μ)V2,dC1dt=λ1(1−τ1)S+(1−ϵ1)λ1V1−(σ1+γC1+μ)C1,dC2dt=λ2(1−τ2)S+(1−ϵ2)λ2V2−(σ2+γC2+μ)C2,dI1dt=σ1C1+λ1τ1S+λ1V2−(γI1+δ+μ)I1,dI2dt=σ2C2+λ2τ2S+λ2V1−(γI2+δ+μ)I2,dR1dt=γC1C1+γC2C2+γI1ρ1I1+γI2ρ2I2−(∧+μ)R1,dR2dt=γI1(1−ρ1)I1+γI2(1−ρ2)I2+∧R1−μR2, | (2.13) |
subject to the initial conditions:
S(0)=S0,V1(0)=V01, V2(0)=V02,C1(0)=C01,C2(0)=C02,I1(0)=I01,I2(0)=I02,R1(0)=R01,R2(0)=R02. | (2.14) |
Definition 3.1. A region within which the solutions to the model are uniformly bounded is defined as Ω∈ℜ9+.
From the total population in Eq (2.1), we have
dN(t)dt=dS(t)dt+dV1(t)dt+dV2(t)dt+dC1(t)dt+dC2(t)dt+dI1(t)dt+dI2(t)dtx+dR1(t)dt+dR2(t)dt. | (3.1) |
Substituting (2.13) into (3.1) and simplifying yields
dN(t)dt=α−μN−δI1−δI2, | (3.2) |
dN(t)dt≤α−μN(t). | (3.3) |
Integrating both sides of Eq (3.3), we have
−1μln(α−μN)≤t+c, | (3.4) |
where c is the constant of integration. Thus,
ln(α−μN)≥−(μt+c), | (3.5) |
(α−μN)≥ke−μt, | (3.6) |
where k is ec.
Let N(0)=N0, this implies
(α−μN0)≥k. | (3.7) |
From (3.6) and (3.7), we get
(α−μN)≥(α−μN0)e−μt, | (3.8) |
N(t)≤αμ−(α−μN0)μe−μt, | (3.9) |
So,
N(t)→αμ as t→∞, | (3.10) |
implies N(t)∈[0,αμ]. Therefore, the feasible set of solutions of the model equations enter and remain in the invariant region
Ω={(S,V1,V2,C1,C2,I1,I2,R1,R2)∈ℜ9+:N(t)≤αμ}. | (3.11) |
Therefore, N(t) is bounded; thus, the model is mathematically and epidemiologically well-posed because region Ω is positively invariant and attractive. Hence, it is sufficient to study the dynamics of model (2.13) in Ω.
Theorem 3.1. The positivity theorem: Let
Ω={(S,V1,V2,C1,C2,I1,I2,R1,R2)∈ℜ9+:S0>0,V01>0,V02>0,C01>0,C02>0,I01>0,I02>0,R01>0,R02>0}, |
then, the solutions (S,V1,V2,C1,C2,I1,I2,R1,R2) are positive for t≥0.
Proof. Considering the first equation of the model
dSdt=α+ω1V1+ω2V2−(λ1+λ2+θ1+θ2+μ)S,dSdt≥−(λ1+λ2+θ1+θ2+μ)S,∫dSS≥−∫(λ1+λ2+θ1+θ2+μ)dt,lnS(t)≥−f(t)+c, |
where
f(t)=∫(λ1+λ2+θ1+θ2+μ)dt |
and c is the constant of integration. Hence,
S(t)≥e(−f(t)+c)=A1e−f(t), | (3.12) |
where A1=ec. From Theorem 3.1, at t=0, S0>0 which implies A1=ec≥0 since S(0)≥A1. Consequently,
S(t)≥S0e−f(t)≥0, ∀t≥0. |
Similarly, it can be shown that
V1(t)≥V01e−g(t)≥0,∀t≥0,V2(t)≥V02e−h(t)≥0,∀t≥0,C1(t)≥C01e−k1t≥0,∀t≥0,C2(t)≥C02e−k2t≥0,∀t≥0,I1(t)≥I01e−k3t≥0,∀t≥0,I2(t)≥I02e−k4t≥0,∀t≥0,R1(t)≥R01e−k5t≥0,∀t≥0,R2(t)≥R02e−μt≥0,∀t≥0, | (3.13) |
where
g(t)=∫[(1−ϵ1)λ1+λ2+ω1+μ]dt, |
h(t)=∫[(1−ϵ2)λ2+λ1+ω2+μ]dt, |
k1=(σ1+γC1+μ), k2=(σ2++γC2+μ), |
k3=(γI1+δ+μ), k4=(γI2+δ+μ), k5=(∧+μ). |
This completes the proof of the theorem.
For the developed model, four equilibrium points are identified when each compartment is in steady state. These are the disease-free equilibrium (DFE), endemic equilibrium and the boundary equilibrium points.
The DFE of the model is defined as (S∗(t),V∗1(t),V∗2(t),0,0,0,0,0,0) satisfying
dS(t)dt=dV1(t)dt=dV2(t)dt=dC1(t)dt=dC2(t)dt=dI1(t)dt=dI2(t)dt=dR1(t)dt=dR2(t)dt=0. |
Equating the system of equations in (2.13) to 0 and substituting
C1=C2=I1=I2=R1=R2=0, |
the DFE is obtained as
E0=((ω1+μ)(ω2+μ)αχμ,(ω2+μ)θ1αχμ,(ω1+μ)θ2αχμ,0,0,0,0,0,0), | (3.14) |
where
χ=(μ2+μω1+μω2+μθ1+μθ2+ω1ω2+ω1θ2+ω2θ1). | (3.15) |
The edemic equilibrium point of the model is defined as
(S∗(t),V∗1(t),V∗2(t),C∗1(t),C∗2(t),I∗1(t),I∗2(t),R∗1(t),R∗2(t)) |
satisfying
dS(t)dt=dV1(t)dt=dV2(t)dt=dC1(t)dt=dC2(t)dt=dI1(t)dt=dI2(t)dt=dR1(t)dt=dR2(t)dt=0. |
Two boundary equilibrium points denoted by E1 and E2 are defined by
E1=(S∗(t),V∗1(t),V∗2(t),C∗1(t),0,I∗1(t),0,R∗1(t),R∗2(t)), | (3.16) |
where only strain 1 survives, and
E2=(S∗(t),V∗1(t),V∗2(t),0,C∗2(t),0,I∗2(t),R∗1(t),R∗2(t)), | (3.17) |
where only strain 2 survives.
Solving the system of equations for E1 results in
S∗=(λ1+b7)[(1−ϵ1)λ1+b4]α(1−ϵ1)λ13+G2λ12+G1λ1+μχ,V∗1=θ1S∗(1−ϵ1)λ1+b4,V∗2=θ2S∗λ1+b7,C∗1=λ1S∗[θ1(1−ϵ1)+(1−τ1)((1−ϵ1)λ1+b4)]a2((1−ϵ1)λ1+b4),I∗1=λ1τ1S∗+σ1C∗1+λ1V∗2a1,R∗1=γI1ρ1I∗1+γc1C∗1∧+μ,R∗2=γI1[(1−ρ1)μ+∧]I∗1+γC1∧C∗1μ(∧+μ), | (3.18) |
where
a1=γI1+δ+μ, a2=σ1+γC1+μ, b4=ω1+μ, b7=ω2+μ, |
G1=[χ−ω1(b7+θ2)](1−ϵ1)+μb4−ω2θ1+χ, |
G2=(1−ϵ1)(b7+θ1+θ2+μ)+b4. |
Substituting the state solutions in Eq (3.18) into the force of infection in Eq (2.2) yields the following cubic polynomial after some computation
K1λ∗31+K2λ∗21+K3λ∗1+K4=0, | (3.19) |
where
K1=(1−ϵ1)[(1−τ1)((μ+γI1)σ1+(μ+γc1)a1)+a2(μ+γI1)τ1],K2=(1−τ1)[(1−ϵ1)b7+b4][σ1(μ+γI1)+a1(μ+γc1)]+a1θ1(1−ϵ1)(μ+γc1)+(1−ϵ1)(μ+γI1)[a2(τ1b7+θ2)+σ1θ1]−βμ(1−ϵ1)(1−τ1)(ηa1+σ1)+a2b4τ1(μ+γI1)−μa2(1−ϵ1)(βτ1−a1),K3=b7σ1(μ+γI1)[(1−τ1)b4+(1−ϵ1)θ1]+a1b7[(1−τ1)b4+(1−ϵ1)θ1](μ+γc1)+a2(b7τ1+θ2)[b4(μ+γI1)−μβ(1−ϵ1)]+μa1a2(1−ϵ1)(θ2+b7)+μa1a2(θ1+b4)−βμa2b4τ1−μβ(ηa1+σ1)((1−τ1)(1−ϵ1)b7+(1−τ1)b4+(1−ϵ1)θ1),K4=−βμ(−b4b7(−1+τ1)(ηa1+σ1)+b7θ1(1−ϵ1)(ηa1+σ1)+b4(b7τ1+θ2)a2)+μa1a2χ,=−βμ(b7(ηa1+σ1)((1−τ1)b4+(1−ϵ1)θ1)+b4(b7τ1+θ2)a2)+μa1a2χ,=(1−β(b7(ηa1+σ1)((1−τ1)b4+(1−ϵ1)θ1)+b4(b7τ1+θ2)a2)a1a2χ)⋅μa1a2χ=μa1a2χ(1−R01), |
and R01 is the basic reproduction number related to strain 1 as later defined in Eq (3.29).
Solving the system of equations for E2 results in
S∗=(λ2+b4)[(1−ϵ2)λ2+b7]α(1−ϵ2)λ23+G4λ22+G3λ2+μχ,V∗1=θ1S∗λ2+b4,V∗2=θ2S∗(1−ϵ2)λ2+b7,C∗2=λ2S∗[θ2(1−ϵ2)+(1−τ2)((1−ϵ2)λ2+b7)]a4((1−ϵ2)λ2+b7),I∗2=λ2τ2S∗+σ2C∗2+λ2V∗1a3,R∗1=γI2ρ2I∗2+γc2C∗2∧+μ,R∗2=γI2[(1−ρ2)μ+∧]I∗2+γC2∧C∗2μ(∧+μ), | (3.20) |
where
a3=γI2+δ+μ, a4=σ2+γC2+μ, |
G3=[χ−ω2(b4+θ1)](1−ϵ2)+μb7−ω1θ2+χ, |
G4=(1−ϵ2)(b4+θ1+θ2+μ)+b7. |
Substituting the state solutions in Eq (3.20) into the force of infection in Eq (2.3) also yields the following cubic polynomial after some computations
K5λ∗32+K6λ∗22+K7λ∗2+K8=0, | (3.21) |
where
K5=(1−ϵ2)[(1−τ2)((μ+γI2)σ2+(μ+γc2)a3)+a4(μ+γI2)τ2],K6=(1−τ2)[(1−ϵ2)b4+b7][σ2(μ+γI2)+a3(μ+γc2)]+a3θ2(1−ϵ2)(μ+γc2)+(1−ϵ2)(μ+γI2)[a4(τ2b4+θ1)+σ2θ2]−βμ(1−ϵ2)(1−τ2)(ηa3+σ1)−μa4(1−ϵ2)(βτ2−a3)+a4b7τ2(μ+γI2),K7=b4σ2(μ+γI2)[(1−τ2)b7+(1−ϵ2)θ2]+a3b4[(1−τ2)b7+(1−ϵ2)θ2](μ+γc2)+a4(b4τ2+θ1)[b7(μ+γI2)−μβ(1−ϵ2)]+μa3a4(1−ϵ2)(θ1+b4)+μa3a4(θ2+b7)−βμa4b7τ2−μβ(ηa3+σ2)((1−τ2)(1−ϵ2)b4+(1−τ2)b7+(1−ϵ2)θ2),K8=−βμ(−b4b7(−1+τ2)(ηa3+σ2)+b7θ2(1−ϵ2)(ηa3+σ2)+b7(b4τ2+θ1)a4)+μa3a4χ,=−βμ(b4(ηa3+σ2)((1−τ2)b7+(1−ϵ2)θ2)+b7(b4τ2+θ1)a4)+μa3a4χ=μa3a4χ(1−R02), |
and R02 is the basic reproduction number relating to strain 2 as later defined in Eq (3.30).
The basic reproduction number is defined as the average number of secondary infections caused by a single infectious individual in a completely susceptible population. It helps forecast the transmission potential of a disease. According to the principle of the next generation matrix, the basic reproduction number is the spectral radius of the next generation matrix FV−1 in model (2.13). Following [27,28], the basic reproduction number associated with model (2.13) is derived as follows
(dC1dtdI1dtdC2dtdI2dt)=fi−vi, |
with
fi=(λ1(1−τ1)S+(1−ϵ1)λ1V1λ1τ1S+λ1V2λ2(1−τ2)S+(1−ϵ2)λ2V2λ2τ2S+λ2V1) | (3.22) |
and
vi=((σ1+γC1+μ)C1(γI1+δ+μ)I1−σ1C1(σ2+γC2+μ)C2(γI2+δ+μ)I2−σ2C2), | (3.23) |
where, fi is the rate of appearance of new infection(s) in compartment i, vi represents the rate of transfer of individuals into compartment i, with i∈[1,2].
The Jacobian of fi at E0 is given as
F=(ηβb7[θ1(1−ϵ1)+(1−τ1)b4]χβb7[θ1(1−ϵ1)+(1−τ1)b4]χ00ηβb4(b7τ1+θ2)χβb4(b7τ1+θ2)χ0000ηβb4[θ2(1−ϵ2)+(1−τ2)b7]χβb4[θ2(1−ϵ2)+(1−τ2)b7]χ00ηβb7(b4τ2+θ1)χβb7(b4τ2+θ1)χ) | (3.24) |
and that of vi at E0 is given as
V=(σ1+γC1+μ000−σ1γI1+δ+μ0000σ2+γC2+μ000−σ2γI2+δ+μ) | (3.25) |
with
V−1=(1σ1+γC1+μ000σ1(σ1+γC1+μ)(γI1+δ+μ)1γI1+δ+μ00001σ2+γC2+μ000σ2(σ2+γC2+μ)(γI2+δ+μ)1γI2+δ+μ). | (3.26) |
Thus, the next generation matrix is calculated as
G=FV−1=(ηβb7b1(ηa1+σ1)χa1a2βb7b1χa100ηβb4(b7τ1+θ2)(ηa1+σ1)χa1a2βb4(b7τ1+θ2)χa10000βb4b2(ηa3+σ2)χa3a4βb4b2χa300βb7(b4τ2+θ1)(ηa3+σ2)χa3a4βb7(b4τ2+θ1)χa3), | (3.27) |
where,
b1=θ1(1−ϵ1)+(1−τ1)b4, b2=θ2(1−ϵ2)+(1−τ2)b7. |
The eigenvalues of the matrix G in Eq (3.27) are
λT=(00β[b7(ηa1+σ1)(b4(1−τ1)+θ1(1−ϵ1))+a2b4(b7τ1+θ2)]a1a2χβ[b4(ηa3+σ2)(b7(1−τ2)+θ2(1−ϵ2))+a4b7(b4τ2+θ1)]a3a4χ). | (3.28) |
Consequently, the basic reproduction number, which is the spectral radius of G is given as R0=max{R01,R02}, with
R01=β[b7(ηa1+σ1)(b4(1−τ1)+θ1(1−ϵ1))+a2b4(b7τ1+θ2)]a1a2χ, | (3.29) |
R02=β[b4(ηa3+σ2)(b7(1−τ2)+θ2(1−ϵ2))+a4b7(b4τ2+θ1)]a3a4χ, | (3.30) |
representing the basic reproduction numbers related to strain 1 and 2, respectively.
The expression R01 in Eq (3.29) provides the expected number of newly infected individuals that would arise as a result of introducing a single case of strain 1 into a completely susceptible population [29]. Similarly, R02, given by Eq (3.30), yields the expected number of newly infected individuals that would arise if a single case of strain 2 is introduced into a completely susceptible population.
Theorem 3.2. The DFE is locally asymptotically stable if R0<1 and unstable if R0>1.
Using Theorem 3.2, the result in Lemma 3.1 follows immediately based on the expressions of R01,R02.
Lemma 3.1. The DFE of the two-strain bacterial meningitis model in (2.13) is locally asymptotically stable if both R01,R02<1 and unstable if R01,R02>1.
Definition 3.2. The DFE of model (2.13) is said to be locally stable if each eigenvalue of the associated Jacobian matrix is negative.
Following Definition 3.2, the Jacobian matrix, J evaluated at E0 is given as
J=(−b3ω1ω2−βηb4b7χ−βηb4b7χ−βb4b7χ−βb4b7χ00θ1−b40−βηθ1(1−ϵ1)b7χ−βηb7θ1χ−βθ1(1−ϵ1)b7χ−βb7θ1χ00θ20−b7−βηb4θ2χ−βηθ2(1−ϵ2)b4χ−βb4θ2χ−βθ2(1−ϵ2)b4χ00000βηb1b7χ−a20βb1b7χ0000000βηb2b4χ−a40βb2b4χ00000βηb4b6χ+σ10βb4b6χ−a10000000βηb7b5χ+σ20βb7b5χ−a300000γC1γC2γI1ρ1γI2ρ2−(∧+μ)000000γI1(1−ρ1)γI2(1−ρ2)∧−μ) | (3.31) |
where
b3=θ1+θ2+μ, b5=b4τ2+θ1, b6=b7τ1+θ2. |
The eigenvalues of the Jacobian matrix, J are
λ1,2=−(a1+a2)χ−βηb1b7−βb4b6±√W12χ,λ3,4=−(a3+a4)χ−βηb2b4−βb5b7±√W22χ,λ5=−μ, λ6=−(∧+μ), |
where
W1=β2(ηb1b7+b4b6)2+2χβηb1b7(a1−a2)−2χβb4b6(a1−a2)+4χβb1b7σ1+χ2(a1−a2)2 |
and
W2=β2(ηb2b4+b5b7)2+2χβηb2b4(a3−a4)−2χβb5b7(a3−a4)+4χβb2b4σ2+χ2(a3−a4)2. |
The remaining three eigenvalues of J are obtained as the roots of the following polynomial
c1λ3+c2λ2+c3λ+c4 | (3.32) |
where
c1=1,c2=b3+b4+b7,c3=b4b7+b3(b4+b7)−ω1θ1−ω2θ2=χ+μ(b3+b4+ω2),c4=b3b4b7−b4ω2θ2−b7ω1θ1=χμ.
Applying the Routh-Hurwitz criteria to cubic polynomial in Eq (3.32).
Because all the parameters of model (2.13) are positive, it is clear that the condition of stability is established with c1>0, c2>0, c3>0 and c4>0.
The global asymptotic stability of the model in (2.13) is investigated by following [29,30]. The model is denoted by
{dXdt=F(X,Y),dYdt=G(X,Y), | (3.33) |
where X=(S,V1,V2,R1,R2) denotes the right-hand side of the uninfected population with C1=C2=I1=I2=0 and Y=(C1,C2,I1,I2) denotes the right-hand side of the infected population.
Theorem 3.3. The DFE is said to be globally asymptotically stable in Ω if R01,R02<1 and the following two conditions hold:
C1: For dXdt=F(X,0), E0 is globally asymptotically stable.
C2: G(X,Y)=J[G(X∗,0)]Y−ˆG(X,Y), ˆG(X,Y)≥0, ∀(X,Y)∈Ω,
where
(X∗,0)=E0=(αb4b7μχ,αθ1b7μχ,αθ2b4μχ,0,0,0,0,0,0), |
J[G(X∗,0)] is the Jacobian of G(X,Y) obtained with respect to (C1,C2,I1,I2) and evaluated at (X∗,0).
Proof. C1: From the model, it follows that
F(X,0)=(α+ω1V1+ω2V2−(θ1+θ2+μ)Sθ1S−b4V1θ2S−b7V2−(∧+μ)R1∧R1−μR2). | (3.34) |
From Eq (3.34), it is clear that
E0=(S,V1,V2,C1,C2,I1,I2,R1,R2)=(αb4b7μχ,αθ1b7μχ,αθ2b4μχ,0,0,0,0,0,0). |
This can be verified using the method of integrating factors. From Eq (3.34), we have
dV1dt+b4V1=θ1S. | (3.35) |
The integrating factor is given as
e∫b4dt=eb4t. |
Multiplying Eq (3.35) through by the integrating factor yields
eb4t(dV1dt+b4V1)=(θ1S)eb4t,∫ddt(V1eb4t)dt=θ1∫Seb4tdt. |
Let
I=∫Seb4tdt. |
Integrating by parts, we have
u=S⟹du=S′dt |
and
dv=eb4t⟹v=eb4tb4. |
So,
I=Seb4tb4−1b4∫S′eb4tdt |
implying that
V1eb4t=θ1[Seb4tb4−1b4∫S′eb4tdt]. |
Therefore,
V1=θ1Sb4−θ1b4eb4t∫S′eb4tdt. | (3.36) |
From Eq (3.36), V1→θ1Sb4 as t→∞.
Similarly, we can deduce from Eq (3.34) that, V2→θ2Sb7 as t→∞. Furthermore, from Eq (3.34), we have
dSdt=α+ω1V1+ω2V2−(θ1+θ2+μ)S. | (3.37) |
Since V1→θ1Sb4 and V2→θ2Sb7, Eq (3.37) is rewritten as
dSdt=α+ω1θ1Sb4+ω2θ2Sb7−(θ1+θ2+μ)S, | (3.38) |
dSdt+μχb4b7S=α. | (3.39) |
The integrating factor of Eq (3.39) is given as
e∫μχb4b7dt=eμχb4b7t. |
Multiplying Eq (3.39) through by the integrating factor gives
eμχb4b7t(dSdt+μχb4b7S)=αeμχb4b7t,∫ddt(Seμχb4b7t)dt=∫αeμχb4b7tdt,Seμχb4b7t=αb4b7μχeμχb4b7t+c, |
where c is the constant of integration. Therefore,
S=αb4b7μχ+Ce−μχb4b7t. | (3.40) |
From Eq (3.40), S→αb4b7μχ as t→∞; and this implies the global convergence of Eq (3.34) in Ω.
C2: G(X,Y) is given as
G(X,Y)=[λ1(1−τ1)S+(1−ϵ1)λ1V1−a2C1λ2(1−τ2)S+(1−ϵ2)λ2V2−a4C2σ1C1+λ1τ1S+λ1V2−a1I1σ2C2+λ2τ2S+λ2V1−a3I2], | (3.41) |
where λ1 and λ2 are the forces of infection defined in Eqs (2.2) and (2.3).
By the condition in C2 with Eqs (3.41) and (3.43), ˆG(X,Y) is given by
(β(ηC1+I1)[(1−ϵ1)V∗1+(1−τ1)S∗]N∗(1−(1−ϵ1)V1+(1−τ1)SNN∗(1−ϵ1)V∗1+(1−τ1)S∗)β(ηC2+I2)[(1−ϵ2)V∗2+(1−τ2)S∗]N∗(1−(1−ϵ2)V2+(1−τ2)SNN∗(1−ϵ2)V∗2+(1−τ2)S∗)β(ηC1+I1)(τ1S∗+V∗2)N∗(1−(τ1S+V2)NN∗(τ1S∗+V∗2))β(ηC2+I2)(τ2S∗+V∗1)N∗(1−(τ2S+V1)NN∗(τ2S∗+V∗1))). | (3.42) |
The Jacobian matrix of G(X,Y), J[G(X∗,0)] is given as
(βη[(1−ϵ1)V∗1+(1−τ1)S∗]−a2N∗N∗0β[(1−ϵ1)V∗1+(1−τ1)S∗]N∗00βη[(1−ϵ2)V∗2+(1−τ2)S∗]−a4N∗N∗0β[(1−ϵ2)V∗2+(1−τ2)S∗]N∗βη(τ1S∗+V∗2)+σ1N∗N∗0β(τ1S∗+V∗2)−a1N∗N∗00βη(τ2S∗+V∗1)+σ2N∗N∗0β(τ2S∗+V∗1)−a3N∗N∗). | (3.43) |
Since
S∗=αb4b7μχ, V∗1=αθ1b7μχ, V∗2=αθ2b4μχ and N∗=αμ, |
we have that S≤S∗, V1≤V∗1and V2≤V∗2. Thus, it follows that S≤N, V1≤Nand V2≤N in Ω. Therefore, if the total population is at the equilibrium level, we have
(1−(1−ϵ1)V1+(1−τ1)SNN∗(1−ϵ1)V∗1+(1−τ1)S∗)>0, |
(1−(1−ϵ2)V2+(1−τ2)SNN∗(1−ϵ2)V∗2+(1−τ2)S∗)>0, |
(1−(τ1S+V2)NN∗(τ1S∗+V∗2))>0 |
and
(1−(τ2S+V1)NN∗(τ2S∗+V∗1))>0; |
thus, ˆG(X,Y)≥0. Hence, it follows from Theorem 3.3 that the DFE, E0=(X∗,0) is globally asymptotically stable.
The base year used in the simulations is 2017. As the disease is endemic to the northern part of Ghana, the total population of the northern part as of 2017, was 4953293 [31]; thus, the initial total population, N(0)=4953293. Since the outbreak that year was due to the Neisseria meningitidis strain, the initially infected individuals of strain 2 were considered, I2(0)=69, which is the same number reported in data. We assumed I1(0)=153. According to a literature review, Streptococcus pneumoniae is found in the nose and throat of 20–40% of people, whereas Neisseria meningitidis is found in 1–10% of these people without causing any symptoms of illness. Thus, taking 140% and 110% of I1(0) and I2(0), respectively gives C1(0)=214 and C2(0)=76. We assumed
V1(0)=V2(0)=R1(0)=R2(0)=0, |
so the initial susceptible is
S(0)=N(0)−V1(0)−V2(0)−C1(0)−C2(0) |
−I1(0)−I2(0)−R1(0)−R2(0) |
=4952781. |
(1) Natural death rate (μ): The average lifespan in Ghana is 64.17 years. Therefore,
μ=164.17×365=4.269×10−5 |
per day.
(2) Birth or recruitment rate (α): The limiting total human population in the absence of the disease is assumed to be αμ=4953293, so α=211 per day.
(3) Disease-induced death rate (δ): The mortality rate due to bacterial meningitis disease in Ghana is 36–50%. By taking the average of 43%, we obtain that δ=0.43.
(4) Progression rates (σ1,σ2): The average incubation period for Streptococcus pneumonaie is 1–3 days while Neisseria meningitidis is 4 days. Thus,
σ1=12=0.5andσ2=14=0.25 |
(5) Vaccine waning rates (ω1,ω2): It takes 5 years for the pneumococcal conjugate vaccines to wane while that of the meningococcal conjugate vaccines is 3–5 years. Therefore,
ω1=15×365=5.47×10−4 |
per day and
ω2=14×365=6.8×10−4 |
per day. (6) Recovery rates (γC1,γI1): The period of infection of the disease is 1-2 weeks with hospitalization and right treatment, so taking the average, we have 8 days. Thus,
γI1=18=0.125. |
For individuals exposed to the disease, prophylaxis is administered and it has been shown to be effective for 1-2 weeks of follow-up [32]. Thus,
γC1=17=0.143. |
(7) Complication rate (∧): Even with appropriate treatment, 10–20% of survivors have serious complications or long-term sequelae. Therefore,
∧=15100=0.15. |
The summary of the estimated model parameter values and the relative sources is given in Table 3.
Parameter | Value | Source |
α | 211 | Estimated |
μ | 0.000043 | Estimated |
ω1 | 0.000547 | Estimated |
ω2 | 0.00068 | Estimated |
β | 0.88 | [21] |
γC1 | 0.143 | Estimated |
γC2 | 0.3 | [13] |
γI1 | 0.125 | Estimated |
γI2 | 0.1 | [13] |
η | 0.75 | Assumed |
δ | 0.43 | Estimated |
ϵ1 | 0.85 | [1] |
ϵ2 | 0.90 | [1] |
σ1 | 0.5 | Estimated |
σ2 | 0.25 | Estimated |
τ1 | 0.3 | [23] |
τ2 | 0.5 | Assumed |
θ1 | 0.2 | Assumed |
θ2 | 0.5 | [13] |
ρ1 | 0.85 | [23] |
ρ2 | 0.9 | Assumed |
∧ | 0.15 | Estimated |
Using the model parameter values given in Table 3, the estimated value of R01 is approximately 1.3409, while that of R02 is 0.4853. Therefore,
R0=max{R01,R02}=max{1.3409,0.4853}=1.3409. |
From a biological perspective, this threshold value indicates that bacterial meningitis has high potential to invade a population if no control efforts are implemented to curtail the transmission and spread of the disease. Therefore, it is important to determine the proportion of the population that needs to be immunized to prevent large outbreaks of bacterial meningitis in Ghana. When a large-scale population is immunized against a contagious infectious disease (either by vaccination or recovery from the infection), indirect protection is provided to the remaining population, which is not immune to the disease. This type of protection is referred to as herd immunity [33,34]. Herd immunity plays a major role in epidemic control by providing a better understanding of the effectiveness of vaccination without reaching 100% population coverage.
Therefore, the critical level of population immunity, denoted by ˆp, is calculated with respect to the estimated R0 value for Ghana's bacterial meningitis outbreaks as
ˆp=1−1R0=0.25. | (3.44) |
This finding implies that bacterial meningitis will not spread if at least 25% of the population is immune to the disease. Hence, successful vaccination of approximately 25% of the entire population of both strains may lead to eradication of the disease in Ghana.
In the mathematical modeling of infectious diseases, it is pertinent to determine the major model parameters that affect disease transmission. Sensitivity analysis aids in identifying parameters that have a high impact on the basic reproduction number, thereby providing insight into the parameters to be considered for control strategies. Following [29], the standardized forward sensitivity index was employed to carry out a sensitivity analysis of model (2.13). The standardized forward sensitivity index of R0 with respect to parameter ψ is the proportion of the relative change in ψ. Therefore, Table 4 provides all the model parameters that are partially differentiable with respect to R01 and R02, their values, and the sensitivity indices with respect to each strain.
Parameter | Value | SI for strain 1 | SI for strain 2 |
μ | 0.000043 | +1.93×10−3 | −6.28×10−3 |
ω1 | 0.000547 | +0.1362 | −0.4413 |
ω2 | 0.00068 | −0.1376 | +0.4507 |
β | 0.88 | +1 | +1 |
γC1 | 0.143 | −1.14×10−2 | ⋯ |
γC2 | 0.3 | ⋯ | −0.1775 |
γI1 | 0.125 | −0.2200 | ⋯ |
γI2 | 0.1 | ⋯ | −0.1510 |
η | 0.75 | +0.0232 | +0.1998 |
δ | 0.43 | −0.7567 | −0.6492 |
ϵ1 | 0.85 | −0.2816 | ⋯ |
ϵ2 | 0.90 | ⋯ | −2.9077 |
σ1 | 0.5 | −1.18×10−2 | ⋯ |
σ2 | 0.25 | ⋯ | −2.23×10−2 |
τ1 | 0.3 | −1.75×10−4 | ⋯ |
τ2 | 0.5 | ⋯ | −3.52×10−4 |
θ1 | 0.1 | −0.1469 | +0.4760 |
θ2 | 0.5 | +0.1463 | −0.4791 |
The sensitivity indices for strain 1 show that when the parameters μ, ω1, β, η and θ2 are increased, keeping all other parameters constant, the value of R01 is increased, thereby increasing the endemicity of the disease, as they have positive indices. In contrast, the parameters ω2, γC1, γI1, δ, ϵ1, σ1, τ1 and θ1 decrease the value of R01 when increased, with all other parameters held constant, resulting in a decrease in the endemicity of the disease as they have negative indices. Similarly, for strain 2, when parameters ω2, β, η and θ1 are increased, keeping all other parameters constant, the value of R02 is increased, resulting in an increase in the endemicity of the disease, as they have positive indices. The parameters μ, ω1, γC2, γI2, δ, ϵ2, σ2, τ2 and θ2, on the other hand, decrease the value of R02 when increased, with all other parameters held constant, thereby decreasing the endemicity of the disease as they have negative indices. For instance, increasing the vaccine waning rate of strain 1, ω1, by 10% will lead to a 1.362% increase in R01, whereas increasing the recovery rate of the carriers of strain 2, γC2, by 10% will result in a reduction of 1.775% on R02.
The numerical solution of model (2.13) is obtained using the MATLAB ODE 45 algorithm for solving non-stiff system of ordinary differential equations with initial conditions and parameter values, as shown in Table 3. The graphs of each model compartment against time are presented, with time ranging from 0 to 30 days.
Figure 3 indicates that the susceptible population starts to decrease after 11 days due to the forces of infection for strains 1 and 2. It can be observed from this compartment that an increase in the vaccine uptake rates for both strains, θ1,θ2, leads to a rapid decrease in the population. Hence, the awareness of the affected population to be vaccinated decreases susceptibility. Figure 4 shows the vaccinated population of strains 1 and 2 at vaccine uptake rates of θ1,θ2=0. This presents a steady-state solution for both compartments. In Figure 5, the population increased at a faster rate within 15 days owing to inflow from the susceptible compartment. Thereafter, an equilibrium point was reached, and the population began to decrease due to the progression of the carriers to the infected population, as the average incubation period of strain 1 infection is 2 days. This decrease can also be due to the recovery of carriers from the infection, because an increase in the recovery rate of carriers of strain 1, γC1, leads to a decrease in the population.
Figure 6 also shows an increase in population as a result of susceptible becoming a carrier. The population achieves stationarity momentarily and begins to decrease as the carriers progress to the infected population, since the average incubation period of strain 2 infection is 4 days. The population also decreased owing to the recovery of the carriers. It can be seen that an increase in the recovery rate of carriers of strain 2, γC2, drastically reduces the population.
Figure 7 shows an increase in the infected population of strain 1 as a result of the movement of its susceptible and carrier population. However, population size decreased after this period. This decrease can be ascribed to the availability of treatment for infected compartments since they are symptomatic and can be easily diagnosed. It also decreases due to recovery from infection and disease-induced death. It can be observed that an increase in the recovery rate of infected population of strain 1, γI1 decreases the population. The infected population of strain 2 in Figure 8 increased because of inflow from the susceptible and carrier populations. The population achieves stationarity momentarily and begins to decrease owing to recovery from infection and disease-induced death. This decrease can also be attributed to the population receiving urgent treatment since the disease is considered a medical emergency. In addition, an increase in the recovery rate of infected with strain 2, γI2, rapidly decreases the population.
In Figure 9, the fully recovered population maintained a stable state for the first 10 days, then began to increase afterwards. This is because at the onset of the disease, there were no recovered individuals, so as they became infected and recovered, the population increased. Thereafter, we observed a small decrease in the population, which can be attributed to those who recovered from the acute phase of the disease and only found that they experienced some difficulties/complications. The recovered population with complications in Figure 10 also showed a stable state for the first 12 days and a sharp increase over time. It can be observed that an increase in the recovery rates of strains 1 and 2, γI1,γI2, leads to a decrease in the population.
Varying θ1 to the vaccinated population with immunity to strain 1 resulted in a sharp increase in the population within the first 3 days, as shown in Figure 11a. This result is in agreement with those of [22,23]. Moreover, a stable state was achieved in the following days as the population became immune to the specific strain. However, by varying θ1, the carrier population of strain 1 decreases, indicating that increasing the number of vaccinated individuals reduced the number of carriers. Varying θ1 on the infected population of strain 1 shows a rapid decrease in the population, which reveals that the more people receive the vaccine, the lower is the infection. The variation in θ1 in the recovered population with complications also showed a dramatic decrease in the population. This can be attributed to the immune response of the human body to recognize and fight bacteria after vaccination. The variation in θ2 in the vaccinated population with immunity to strain 2 displays a surge in the population within the first 3 days and achieves stability as the population becomes immune to the specified strain, as shown in Figure 12a. Varying θ2 on the carrier population of strain 2 decreases the population as the vaccine uptake rate increased. As θ2 varies with the infected population of strain 2, a sharp decrease is observed, indicating the impact of vaccination on curtailing infection. Varying θ2 on the recovered population with complications shows a rapid decrease in the population, which means that the more we get vaccinated, the fewer are the complications after an acute infection.
This study proposes a novel deterministic model of a coupled system of nine ordinary differential equations for the transmission dynamics of two-strain bacterial meningitis. The introduction of vaccination populations against strains 1 and 2 accounts for most of the total population, thereby curbing the spread of infections. Positivity analysis of the two-strain model showed that it is epidemiologically feasible and represents what can be obtainable in real life. The mathematical analysis of the model shows that the model has a DFE that is locally and globally asymptotically stable if R01,R02<1, and unstable if R01,R02>1. The basic reproduction number indicates that with herd immunity of 25%, the disease can be eradicated over a certain period of time, as represented in the numerical simulation results. The robustness of the model predictions to the parameter values was examined via a sensitivity analysis, which established that the transmission probability, β is an effective contributor to R0, which is essential for the spread and control of the disease.
The authors declare they have not used Artificial Intelligence (AI) tools in the creation of this article.
The authors declare that they have no conflicts of interest in this paper.
[1] |
Z. Y. Fan, W. R. Li, K. C. Chang, A bidirectional long short-term memory autoencoder transformer for remaining useful life estimation, Mathematics, 11 (2023), 4972. https://doi.org/10.3390/math11244972 doi: 10.3390/math11244972
![]() |
[2] |
Y. G. Lei, N. P. Li, L. Guo, N. B. Li, T. Yan, J. Lin, Machinery health prognostics: A systematic review from data acquisition to RUL prediction, Mech. Syst. Signal Process., 104 (2018), 799–834. https://doi.org/10.1016/j.ymssp.2017.11.01 doi: 10.1016/j.ymssp.2017.11.01
![]() |
[3] |
F. Q. Zhao, Z. G. Tian, Y. Zeng, Uncertainty quantification in gear remaining useful life prediction through an integrated prognostics method, IEEE Trans. Reliab., 62 (2013), 146–159. https://doi.org/10.1109/TR.2013.2241216 doi: 10.1109/TR.2013.2241216
![]() |
[4] | S. C. Deng, Z. Q. Chen, Z. Chen, Auxiliary particle filter-based remaining useful life prediction of rolling bearing, in 2017 International Conference on Sensing, Diagnostics, Prognostics, and Control (SDPC), (2017), 15–19. |
[5] |
Y. X. Li, X. Z. Huang, T. H. Gao, C. Y. Zhao, S. J. Li, A wiener-based remaining useful life prediction method with multiple degradation patterns, Adv. Eng. Inf., 57 (2023), 102066. https://doi.org/10.1016/j.aei.2023.102066 doi: 10.1016/j.aei.2023.102066
![]() |
[6] |
N. P. Li, Y. G. Lei, J. Lin, S. X. Ding, An improved exponential model for predicting remaining useful life of rolling element bearings, IEEE Trans. Ind. Electron., 62 (2015), 7762–7773. https://doi.org/10.1109/TIE.2015.2455055 doi: 10.1109/TIE.2015.2455055
![]() |
[7] |
A. Rai, S. H. Upadhyay, The use of MD-CUMSUM and NARX neural network for anticipating the remaining useful life of bearings, Measurement, 111 (2017), 397–410. https://doi.org/10.1016/j.measurement.2017.07.030 doi: 10.1016/j.measurement.2017.07.030
![]() |
[8] |
Z. Liu, M. J. Zuo, Y. Qin, Remaining useful life prediction of rolling element bearings based on health state assessment, Proc. Inst. Mech. Eng., Part C: J. Mech., 230 (2016), 314–330. https://doi.org/10.1177/0954406215590167 doi: 10.1177/0954406215590167
![]() |
[9] |
F. Deng, Y. Bi, Y. Liu, S. Yang, Deep-learning-based remaining useful life prediction based on a multi-scale dilated convolution network, Mathematics, 9 (2021), 3035. https://doi.org/10.3390/math9233035 doi: 10.3390/math9233035
![]() |
[10] |
B. Rezaeianjouybari, Y. Shang, Deep learning for prognostics and health management: State of the art, challenges, and opportunities, Measurement, 163 (2020), 107929. https://doi.org/10.1016/j.measurement.2020.107929 doi: 10.1016/j.measurement.2020.107929
![]() |
[11] |
B. Zhang, S. H. Zhang, W. H. Li, Bearing performance degradation assessment using long short-term memory recurrent network, Comput. Ind., 106 (2019), 14–29. https://doi.org/10.1016/j.compind.2018.12.016 doi: 10.1016/j.compind.2018.12.016
![]() |
[12] |
Z. H. Chang, W. Yuan, K. Huang, Remaining useful life prediction for rolling bearings using multi-layer grid search and LSTM, Comput. Electr. Eng., 101 (2022), 108083. https://doi.org/10.1016/j.compeleceng.2022.108083 doi: 10.1016/j.compeleceng.2022.108083
![]() |
[13] |
J. Y. Guo, J. Wang, Z. Y. Wang, Y. Gong, J. L. Qi, G. Y. Wang, et al., A CNN‐BiLSTM‐Bootstrap integrated method for remaining useful life prediction of rolling bearings, Qual. Reliab. Eng. Int., 39 (2023), 1796–1813. https://doi.org/10.1002/qre.3314 doi: 10.1002/qre.3314
![]() |
[14] |
B. Zhang, L. J. Zhang, J. W. Xu, Degradation feature selection for remaining useful life prediction of rolling element bearings, Qual. Reliab. Eng. Int., 32 (2016), 547–554. https://doi.org/10.1002/qre.1771 doi: 10.1002/qre.1771
![]() |
[15] |
Y. G. Lei, N. P. Li, S. Gontarz, J. Lin, S. Radkowski, J. Dybala, A model-based method for remaining useful life prediction of machinery, IEEE Trans. Reliab., 65 (2016), 1314–1326. https://doi.org/10.1109/TR.2016.2570568 doi: 10.1109/TR.2016.2570568
![]() |
[16] |
B. Wang, Y. G. Lei, N. P. Li, N. B. Li, A hybrid prognostics approach for estimating remaining useful life of rolling element bearings, IEEE Trans. Reliab., 69 (2020), 401–412. https://doi.org/10.1109/TR.2018.2882682 doi: 10.1109/TR.2018.2882682
![]() |
1. | Umar Shafique, Mohamed Mahyoub Al-Shamiri, Ali Raza, Emad Fadhal, Muhammad Rafiq, Nauman Ahmed, Numerical Analysis of Bacterial Meningitis Stochastic Delayed Epidemic Model through Computational Methods, 2024, 141, 1526-1506, 311, 10.32604/cmes.2024.052383 | |
2. | Anita T. Kurniawati, Chidozie W. Chukwu, Faishal F. Herdicho, Optimal control of dengue fever model with a logistically growing human population, 2025, 5, 2767-8946, 48, 10.3934/mmc.2025004 |
Parameters | Description |
α | Birth or recruitment rate into susceptible population |
β | Transmission probability |
δ | Disease-induced death rate |
μ | Natural death rate |
σ1 | Rate of progression from carrier of strain 1 to infected population of strain 1 |
σ2 | Rate of progression from carrier of strain 2 to infected population of strain 2 |
γC1 | Recovery rate of carriers of strain 1 |
γC2 | Recovery rate of carriers of strain 2 |
γI1 | Recovery rate of infected with strain 1 |
γI2 | Recovery rate of infected with strain 2 |
θ1 | Strain 1 vaccine uptake rate |
θ2 | Strain 2 vaccine uptake rate |
ϵ1 | Strain 1 vaccine efficacy |
ϵ2 | Strain 2 Vaccine efficacy |
ω1 | Vaccine waning of strain 1 |
ω2 | Vaccine waning of strain 2 |
τ1 | Proportion moving to I1 without first passing through C1 |
τ2 | Proportion moving to I2 without first passing through C2 |
∧ | Complication rate after a period of time |
ρ1 | Proportion moving to R1(t) from strain 1 without first passing through R2(t) |
ρ2 | Proportion moving to R1(t) from strain 2 without first passing through R2(t) |
Variables | Description |
S(t) | Susceptible population who can contract both strains 1 and 2 |
V1(t) | Vaccinated population with immunity to strain 1 |
V2(t) | Vaccinated population with immunity to strain 2 |
C1(t) | Carrier population of strain 1 |
C2(t) | Carrier population of strain 2 |
I1(t) | Infected population of strain 1 |
I2(t) | Infected population of strain 2 |
R1(t) | Fully recovered population from both strains 1 and 2 |
R2(t) | Recovered with complications from both strains 1 and 2 |
Parameter | Value | Source |
α | 211 | Estimated |
μ | 0.000043 | Estimated |
ω1 | 0.000547 | Estimated |
ω2 | 0.00068 | Estimated |
β | 0.88 | [21] |
γC1 | 0.143 | Estimated |
γC2 | 0.3 | [13] |
γI1 | 0.125 | Estimated |
γI2 | 0.1 | [13] |
η | 0.75 | Assumed |
δ | 0.43 | Estimated |
ϵ1 | 0.85 | [1] |
ϵ2 | 0.90 | [1] |
σ1 | 0.5 | Estimated |
σ2 | 0.25 | Estimated |
τ1 | 0.3 | [23] |
τ2 | 0.5 | Assumed |
θ1 | 0.2 | Assumed |
θ2 | 0.5 | [13] |
ρ1 | 0.85 | [23] |
ρ2 | 0.9 | Assumed |
∧ | 0.15 | Estimated |
Parameter | Value | SI for strain 1 | SI for strain 2 |
μ | 0.000043 | +1.93×10−3 | −6.28×10−3 |
ω1 | 0.000547 | +0.1362 | −0.4413 |
ω2 | 0.00068 | −0.1376 | +0.4507 |
β | 0.88 | +1 | +1 |
γC1 | 0.143 | −1.14×10−2 | ⋯ |
γC2 | 0.3 | ⋯ | −0.1775 |
γI1 | 0.125 | −0.2200 | ⋯ |
γI2 | 0.1 | ⋯ | −0.1510 |
η | 0.75 | +0.0232 | +0.1998 |
δ | 0.43 | −0.7567 | −0.6492 |
ϵ1 | 0.85 | −0.2816 | ⋯ |
ϵ2 | 0.90 | ⋯ | −2.9077 |
σ1 | 0.5 | −1.18×10−2 | ⋯ |
σ2 | 0.25 | ⋯ | −2.23×10−2 |
τ1 | 0.3 | −1.75×10−4 | ⋯ |
τ2 | 0.5 | ⋯ | −3.52×10−4 |
θ1 | 0.1 | −0.1469 | +0.4760 |
θ2 | 0.5 | +0.1463 | −0.4791 |
Parameters | Description |
α | Birth or recruitment rate into susceptible population |
β | Transmission probability |
δ | Disease-induced death rate |
μ | Natural death rate |
σ1 | Rate of progression from carrier of strain 1 to infected population of strain 1 |
σ2 | Rate of progression from carrier of strain 2 to infected population of strain 2 |
γC1 | Recovery rate of carriers of strain 1 |
γC2 | Recovery rate of carriers of strain 2 |
γI1 | Recovery rate of infected with strain 1 |
γI2 | Recovery rate of infected with strain 2 |
θ1 | Strain 1 vaccine uptake rate |
θ2 | Strain 2 vaccine uptake rate |
ϵ1 | Strain 1 vaccine efficacy |
ϵ2 | Strain 2 Vaccine efficacy |
ω1 | Vaccine waning of strain 1 |
ω2 | Vaccine waning of strain 2 |
τ1 | Proportion moving to I1 without first passing through C1 |
τ2 | Proportion moving to I2 without first passing through C2 |
∧ | Complication rate after a period of time |
ρ1 | Proportion moving to R1(t) from strain 1 without first passing through R2(t) |
ρ2 | Proportion moving to R1(t) from strain 2 without first passing through R2(t) |
Variables | Description |
S(t) | Susceptible population who can contract both strains 1 and 2 |
V1(t) | Vaccinated population with immunity to strain 1 |
V2(t) | Vaccinated population with immunity to strain 2 |
C1(t) | Carrier population of strain 1 |
C2(t) | Carrier population of strain 2 |
I1(t) | Infected population of strain 1 |
I2(t) | Infected population of strain 2 |
R1(t) | Fully recovered population from both strains 1 and 2 |
R2(t) | Recovered with complications from both strains 1 and 2 |
Parameter | Value | Source |
α | 211 | Estimated |
μ | 0.000043 | Estimated |
ω1 | 0.000547 | Estimated |
ω2 | 0.00068 | Estimated |
β | 0.88 | [21] |
γC1 | 0.143 | Estimated |
γC2 | 0.3 | [13] |
γI1 | 0.125 | Estimated |
γI2 | 0.1 | [13] |
η | 0.75 | Assumed |
δ | 0.43 | Estimated |
ϵ1 | 0.85 | [1] |
ϵ2 | 0.90 | [1] |
σ1 | 0.5 | Estimated |
σ2 | 0.25 | Estimated |
τ1 | 0.3 | [23] |
τ2 | 0.5 | Assumed |
θ1 | 0.2 | Assumed |
θ2 | 0.5 | [13] |
ρ1 | 0.85 | [23] |
ρ2 | 0.9 | Assumed |
∧ | 0.15 | Estimated |
Parameter | Value | SI for strain 1 | SI for strain 2 |
μ | 0.000043 | +1.93×10−3 | −6.28×10−3 |
ω1 | 0.000547 | +0.1362 | −0.4413 |
ω2 | 0.00068 | −0.1376 | +0.4507 |
β | 0.88 | +1 | +1 |
γC1 | 0.143 | −1.14×10−2 | ⋯ |
γC2 | 0.3 | ⋯ | −0.1775 |
γI1 | 0.125 | −0.2200 | ⋯ |
γI2 | 0.1 | ⋯ | −0.1510 |
η | 0.75 | +0.0232 | +0.1998 |
δ | 0.43 | −0.7567 | −0.6492 |
ϵ1 | 0.85 | −0.2816 | ⋯ |
ϵ2 | 0.90 | ⋯ | −2.9077 |
σ1 | 0.5 | −1.18×10−2 | ⋯ |
σ2 | 0.25 | ⋯ | −2.23×10−2 |
τ1 | 0.3 | −1.75×10−4 | ⋯ |
τ2 | 0.5 | ⋯ | −3.52×10−4 |
θ1 | 0.1 | −0.1469 | +0.4760 |
θ2 | 0.5 | +0.1463 | −0.4791 |