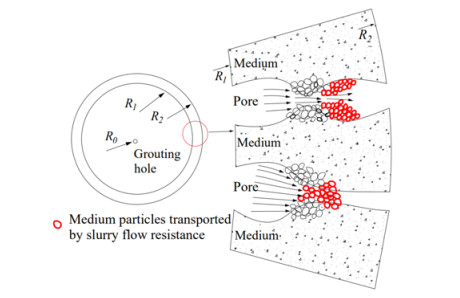
This investigative study explored the field of electrical discharge machining (EDM), with a particular focus on the machining of Ti6Al4V, a titanium alloy that finds widespread application in aerospace, airframes, engine components, and non-aerospace applications such as power generation and marine and offshore environments. Ti6Al4V presents difficulties for conventional metal cutting techniques because of high cutting forces, poor surface integrity, and tool wear. This has led to the adoption of unconventional techniques like EDM. However, problems like high electrode wear rates, low material removal rates, long machining times, and less-than-ideal surface finishes still exist, especially in large-scale applications. By addressing the particular difficulties associated with large-scale electrical discharge machining and by putting forth a multi-objective optimization strategy, this research makes a substantial contribution to the field. With an emphasis on the optimization of input parameters like pulse on time (Ton), pulse off time (Toff), voltage (HV), and current (LV), which are critical in large-scale industrial applications, the study attempts to evaluate the optimal parameter states that simultaneously accomplish multiple goals during the machining process. This work is the first to simultaneously optimize all relevant output responses, such as material removal rate (MRR), electrode wear rate (EWR), machining time (Tm), surface roughness (Ra), and base radius. Previous studies have concentrated on one or two output responses. To optimize MRR, EWR, Tm, Ra, and base radius, the experiments were carefully planned using design of experiment (DOE) and response Surface methodology (RSM). Regression analysis and ANOVA are two statistical techniques that were used with Minitab 15 to help interpret experimental data and build a solid regression model specifically for Ti6Al4V. Throughout the experiment, a variety of input factor settings were employed, and the responses to those were noted. The following parameters were used to obtain the experimental data: current (LV) at 30 and 50 A, voltage (HV) at 0.3 and 0.7 V, pulse on time (Ton) at 4 and 6.5 µs, and pulse off time (Toff) at 5.5 and 6.5 µs. Ton and current are the most significant variables that influence most of the output responses. By addressing the simultaneous optimization of multiple output responses, this investigative study not only sets a new standard in the field but also identifies current bottlenecks and offers solutions.
Citation: Muhammad Mansoor Uz Zaman Siddiqui, Syed Amir Iqbal, Ali Zulqarnain, Adeel Tabassum. An investigative study on the parameters optimization of the electric discharge machining of Ti6Al4V[J]. Clean Technologies and Recycling, 2024, 4(1): 43-60. doi: 10.3934/ctr.2024003
[1] | Jiwei Jia, Young-Ju Lee, Yue Feng, Zichan Wang, Zhongshu Zhao . Hybridized weak Galerkin finite element methods for Brinkman equations. Electronic Research Archive, 2021, 29(3): 2489-2516. doi: 10.3934/era.2020126 |
[2] | Linlin Tan, Bianru Cheng . Global well-posedness of 2D incompressible Navier–Stokes–Darcy flow in a type of generalized time-dependent porosity media. Electronic Research Archive, 2024, 32(10): 5649-5681. doi: 10.3934/era.2024262 |
[3] | Nisachon Kumankat, Kanognudge Wuttanachamsri . Well-posedness of generalized Stokes-Brinkman equations modeling moving solid phases. Electronic Research Archive, 2023, 31(3): 1641-1661. doi: 10.3934/era.2023085 |
[4] | Xiang Zhang, Tingting Zheng, Yantao Luo, Pengfei Liu . Analysis of a reaction-diffusion AIDS model with media coverage and population heterogeneity. Electronic Research Archive, 2025, 33(1): 513-536. doi: 10.3934/era.2025024 |
[5] | Jichun Li . Recent progress on mathematical analysis and numerical simulations for Maxwell's equations in perfectly matched layers and complex media: a review. Electronic Research Archive, 2024, 32(3): 1901-1922. doi: 10.3934/era.2024087 |
[6] | Ning Li, Yuequn Gao . Modified fractional order social media addiction modeling and sliding mode control considering a professionally operating population. Electronic Research Archive, 2024, 32(6): 4043-4073. doi: 10.3934/era.2024182 |
[7] | Xin-Guang Yang, Lu Li, Xingjie Yan, Ling Ding . The structure and stability of pullback attractors for 3D Brinkman-Forchheimer equation with delay. Electronic Research Archive, 2020, 28(4): 1395-1418. doi: 10.3934/era.2020074 |
[8] | N. Bazarra, J. R. Fernández, R. Quintanilla . A dual-phase-lag porous-thermoelastic problem with microtemperatures. Electronic Research Archive, 2022, 30(4): 1236-1262. doi: 10.3934/era.2022065 |
[9] | Wenya Qi, Padmanabhan Seshaiyer, Junping Wang . A four-field mixed finite element method for Biot's consolidation problems. Electronic Research Archive, 2021, 29(3): 2517-2532. doi: 10.3934/era.2020127 |
[10] | Quan Dai, Biao Zhao, Shuguang Wang, Dongliang Huang, Changrui Jin . Numerical simulation scheme of jointed rock masses using UAV photogrammetry and a disk-based discontinuous deformation analysis model. Electronic Research Archive, 2023, 31(6): 3381-3399. doi: 10.3934/era.2023171 |
This investigative study explored the field of electrical discharge machining (EDM), with a particular focus on the machining of Ti6Al4V, a titanium alloy that finds widespread application in aerospace, airframes, engine components, and non-aerospace applications such as power generation and marine and offshore environments. Ti6Al4V presents difficulties for conventional metal cutting techniques because of high cutting forces, poor surface integrity, and tool wear. This has led to the adoption of unconventional techniques like EDM. However, problems like high electrode wear rates, low material removal rates, long machining times, and less-than-ideal surface finishes still exist, especially in large-scale applications. By addressing the particular difficulties associated with large-scale electrical discharge machining and by putting forth a multi-objective optimization strategy, this research makes a substantial contribution to the field. With an emphasis on the optimization of input parameters like pulse on time (Ton), pulse off time (Toff), voltage (HV), and current (LV), which are critical in large-scale industrial applications, the study attempts to evaluate the optimal parameter states that simultaneously accomplish multiple goals during the machining process. This work is the first to simultaneously optimize all relevant output responses, such as material removal rate (MRR), electrode wear rate (EWR), machining time (Tm), surface roughness (Ra), and base radius. Previous studies have concentrated on one or two output responses. To optimize MRR, EWR, Tm, Ra, and base radius, the experiments were carefully planned using design of experiment (DOE) and response Surface methodology (RSM). Regression analysis and ANOVA are two statistical techniques that were used with Minitab 15 to help interpret experimental data and build a solid regression model specifically for Ti6Al4V. Throughout the experiment, a variety of input factor settings were employed, and the responses to those were noted. The following parameters were used to obtain the experimental data: current (LV) at 30 and 50 A, voltage (HV) at 0.3 and 0.7 V, pulse on time (Ton) at 4 and 6.5 µs, and pulse off time (Toff) at 5.5 and 6.5 µs. Ton and current are the most significant variables that influence most of the output responses. By addressing the simultaneous optimization of multiple output responses, this investigative study not only sets a new standard in the field but also identifies current bottlenecks and offers solutions.
Since the 20th century, there have been tremendous changes in the infrastructure construction in China, and underground excavation projects such as tunnels and subways have been continuously developed [1]. However, geological hazards such as large deformation of tunnel surrounding rock, water inrush, groundwater and weak strata also pose a threat to underground engineering. Reinforcement is the most effective way to solve such disasters, such as anchor reinforcement [2,3,4], grouting reinforcement. Currently, grouting is widely used in engineering projects such as plugging and reinforcement during subway and tunnel construction [5,6].
Infiltration grouting has become the most widely used and extensively researched grouting method in engineering practice due to its relatively easy control during the grouting process and its non-destructive effect on surrounding strata [7]. Domestic and foreign scholars [8,9,10,11,12] have conducted a large number of laboratory tests on infiltration grouting, studying the relationship between the diffusion range of grout mixture and grouting parameters such as grouting time, grouting pressure, and water-cement ratio of the grout mixture. Compared to the widespread application of infiltration grouting in engineering, the theoretical development of infiltration grouting has been lagging behind due to the many influencing factors involved. Earlier, scholars established the Mag theory and the Lefranc-Greenwood theory based on Darcy's law for Newtonian fluids [13,14]. Later, many scholars further studied the diffusion path of cement-based grout columns [15,16], the time-dependent viscosity of the grout mixture [17,18,19], the filtration effect of the grout mixture [20,21,22], and the gravity of the grout mixture [23,24] on the diffusion range of infiltration grouting.
The above studies assume that the pores in rock and soil porous media are uniformly distributed. However, the distribution of pores in rock and soil porous media is complex, and assuming that the pores are uniformly distributed often results in an overestimation of the diffusion range of the grout mixture in infiltration grouting practice.
Pore distribution in porous media is characterized by curvature and uncertainty and can generally be classified into capillary, throat, and pipe-ball models [25,26]. When fluid flows through curved and unevenly distributed pores and throats in porous media, it inevitably acts on the particles around the porous media, causing changes in pore shape and size. The distribution and size of pores in porous media determine the permeability of porous media. Therefore, the permeability of rock and soil porous media will inevitably change when fluid flows through it. Permeability of porous media is an important factor in analyzing and studying porous media. For example, Sun [27] studied the effect of pore pressure on the permeability of mudstone sandstone, and Qu et al. [28] used machine learning to study the effect of pore stress concentration on the permeability of porous media and verified a stress-dependent permeability model influenced by stress concentration with experimental data. In the field of oil and gas engineering, the stress sensitivity of permeability is often considered [29,30,31].
Bear [32] proposes that when fluid flows through porous media, it will produce flow resistance along the velocity direction of the solid boundary. However, the influence of fluid flow resistance on the permeability of porous media in infiltration grouting has not been considered in the study of the factors affecting the diffusion range of grout mixture. As shown in Figure 1, after the grout mixture is injected into the porous media, the flow resistance it produces will act on the curved and unevenly distributed pores, causing the particles around the pores to migrate in the direction of the grout mixture velocity, resulting in a narrowing of the pores, and even blocking them, thereby changing the permeability of the porous media.
Therefore, this paper aims to investigate the impact of flow resistance of the grout mixture on the permeability of porous media during the infiltration grouting process. A model for the variation of permeability in porous media is obtained by applying the diffusion law of infiltration grouting column-hemispherical diffusion. An infiltration grouting diffusion model is then developed by combining the rheological equation and the equilibrium equation of the Newtonian fluid, which takes into account the variation of permeability in rock and soil porous media. Also the effectiveness of the proposed model is evaluated by comparing the numerical simulation results with the laboratory test data.
1) Neglecting the effects of filtration, gravity, and flow pattern changes during the grouting process 2) considering the grout mixture as an incompressible, isotropic fluid during the grouting process; 3) ignoring the effects of turbulence near the injection hole and assuming laminar flow throughout the grouting process and 4) assuming that the grout mixture diffuses according to the column-hemispherical infiltration diffusion and Darcy's law applies.
Iberall [33] derived an expression for the permeability of porous media using a flow resistance model,
K=316⋅ϕ1−ϕ⋅δ2⋅2−lnRe4−lnRe | (1) |
Re=ρvδμ | (2) |
where Re represents the Reynolds number, ρ represents the density of the grout mixture, v represents the average velocity of the grout mixture, δ represents the initial pore diameter of the porous media, μ represents the viscosity of the grout mixture, andφ represents the porosity of the porous media.
When the diffusion radius of the grout mixture is l, the grouting volume Q can be expressed as:
Q=vAt | (3) |
where v represents the average velocity of the grout mixture during diffusion, t represents the grouting time, and A represents the spherical surface area over which the grout mixture diffuses during time t.
The surface area A of the column-hemispheric diffusion zone can be expressed as [37]:
A=2πl2+2πlh | (4) |
where l is the slurry diffusion radius in the hemisphere in time t, h is the slurry diffusion height in the cylindrical area.
Combining Eq (1) to Eq (4)
Re=ρδμ⋅Q2πl(l+h)t | (5) |
The total grouting volume Q as:
Q=(23πl3+πl2h)⋅ϕ | (6) |
Bear derived an expression for the permeability of porous media using a flow resistance model that depends on the geometry of the pore system, as shown in Eq (7):
C = K0δ2=πϕ26λ(1−ϕ) | (7) |
where C is a coefficient that depends on the geometry of the pore system, K0 is the initial value of permeability, λ is the influence coefficient of soil particles in porous media, and for spherical soil particles, λ = 3π [32].
By substituting the initial permeability of the porous media into Eq (7), the value of the pore diameter d can be obtained, Harleman et al. [34] verified the correctness of this formula through experiments.
Combining Eqs (1) and (5) to Eq (7), the permeability variation model in porous media can be expressed as:
K=316⋅6K0λπϕ⋅(1−24−lnρδϕα2μt) | (8) |
where α = ((2/3l + h)l)/(l + h), δ = sqrt((6K0λ(1 - φ))/πφ2), t is the grouting time, l is the slurry diffusion radius in the hemisphere, h is the slurry diffusion height in the cylindrical region, K0 is the initial permeability of porous media, ρ is the slurry density, δ is the initial pore diameter of porous media, μ is the slurry viscosity, Φ is the porosity of porous media, λ is the influence coefficient of porous media soil particles, and for spherical soil particles, λ = 3π.
The flow diagram of Newtonian fluid in the tube is shown in Figure 2 [35].
The force analysis of the fluid unit is carried out without considering the gravity of the slurry.
pπr2−(p + Δp)πr2−2πrτdl = 0 | (9) |
where r0 is the radius of the tube, r is the radius of the fluid unit, where r < r0. p and p+Δp are the pressure at both ends of the unit body, Δp is the slurry unit body pressure increment, dl is for the length of the unit body, and τ is the surface shear stress of the unit body.
The rheological equation of Newton fluid is
τ=μγ | (10) |
where μ is the viscosity coefficient, γ is the shear rate.
Substituting Eq (10) to Eq (9)
γ=−dvdr=τμ=−r2μdpdl | (11) |
Substitute boundary conditions
r=r0,v=0 | (12) |
Combining Eqs (11) and (12), the grout flow rate in the pipe is
vx(r)=−14μdpdl(r02−r2) | (13) |
The unit grouting volume is
q=∫r002πrvx(r)dr | (14) |
Combining Eq (13) to Eq (14),
q=−π408μdpdl | (15) |
Therefore, the average flow velocity of the slurry in the tube is
¯v=qπr02=−r028μdpdl | (16) |
Introducing permeability, defined as [36]
K=ϕr028 | (17) |
The seepage velocity of grout in the injected medium is
vp=¯vϕ=Kμ⋅(−dpdl) | (18) |
Therefore, the amount of grouting in time t is
Q=vp⋅A⋅t | (19) |
Substituting Eq (5) into Eq (19),
Q=vp⋅2πl(l+h)⋅t | (20) |
The relationship between hemispherical diffusion radius and cylindrical diffusion height is [14].
h=2l3(2a+1) | (21) |
where a is the number of grouting holes for the side wall of the grouting pipe.
Combining Eqs (18)-(21) the pressure gradient expression in the grouting process is obtained as
dpdl=−3Q2πl2(4a+5)⋅t⋅μK | (22) |
Substitute boundary conditions
l=l0,p=p0 | (23) |
where l0 is the Grouting tube radius, p0 is the grouting initial pressure.
Get
p=p0+3Qμ2πK(4a+5)⋅t⋅(l−1−l0−1) | (24) |
For column-hemispheric diffusion grout, the total grouting amount can be expressed as
Q=(23πl3+πl2h)⋅ϕ | (25) |
Combining Eq (7), the governing equation of the diffusion radius of Newtonian fluid seepage grouting considering the permeability change of porous media is obtained:
p=p0+32μ(a+1)3⋅K0λβϕ⋅(1−24−lnρδϕα2μt)(4a+5)⋅t⋅(l2−l0−1l3) | (26) |
where α = ((2/3l + h)l)/(l + h), δ = sqrt((6K0λ(1 - φ))/πφ2), t is the grouting time, l is the hemispherical region slurry diffusion radius during the time t, h is the cylindrical region slurry diffusion height, which satisfies the condition h = (2l/3(a2 + l), φ is the porosity of porous media, μ is the slurry viscosity, δ is the porous media pore diameter, ρ is the slurry density, l0 is the grouting hole radius, p0 is the grouting pressure, a is the grouting pipe side wall grouting number, λ = 3π, K0 is the initial permeability.
When the permeability change of porous media is not considered, Equation (26) can be transformed into Eq (27), which is equivalent to the control equation of Newtonian fluid seepage grouting column-hemispherical diffusion radius derived by Yang et al. [37].
p=p0+2μϕ(a+1)Kt(4a+5)⋅(l2−l0−1l3) | (27) |
where the symbolic meaning is the same as in Eq (26).
In order to study the relationship between the change of permeability of porous media and grouting pressure, this paper needs to calculate the mathematical equation between permeability of porous media and grouting pressure.
From Eq (8), the factors affecting the change of permeability are parameters such as grouting time t and diffusion distance l. Meanwhile, from Eq (15), it is known that the diffusion distance l has a function relationship with the grouting pressure p. Therefore, substituting Eq (25) into Eq (22)
dpdl=−64l(a+1)μ(4a+5)tδ2 | (28) |
Substituting Eq (22) boundary conditions into Eq (28)
l=√(p0−p)(4a+5)tδ232(a+1)μ | (29) |
where the meaning of the symbols is consistent with Eq (26).
Based on the mathematical expressions of permeability versus grouting time and grouting pressure, the relationship between permeability of porous media and grouting pressure and grouting time is investigated in this paper. Based on the relevant laboratory test study [13,14,15,17,23,37,38,40] the slurry parameters and medium parameters are selected, as shown in Table 1. When studying the influence of grouting time on permeability, the time range is 0-300 s, and three groups of control examples of grouting pressure 80, 100 and 120 KPa are set. When studying the influence of grouting pressure on permeability, the pressure range is selected as 0-600 KPa, and three groups of control examples of grouting time of 300, 600 and 900 s are set.
W/C | μ0/(Pa·s) | ρ/(g/cm3) | K0/(cm/s) | φ | r0/cm | τ0/Pa |
2.0 | 0.0067 | 1.30 | 0.0334 | 0.4 | 0.5 | 0.0971 |
Based on Eq (8), the relationship between the permeability of geotechnical porous media affected by slurry flow resistance and grouting time and grouting pressure is obtained, as shown in Figure 2.
It can be seen from Figure 3(a) that with the increase of grouting time, the permeability of geotechnical porous media decreases first and then increases. This is because the slurry flow rate is large at the moment of grouting, which has a great influence on the pore medium particles near the grouting hole, which is bound to cause a large number of medium particles to migrate, so that the permeability of porous media decreases greatly. With the increase of grouting time, the slurry pressure and flow rate gradually dissipate, and the influence on the surrounding medium particles decreases, so that the permeability of porous media gradually rises. It can be seen from Figure 3(b) that with the increase of grouting pressure, the permeability of geotechnical porous media decreases gradually. This is because the greater the grouting pressure, the greater the slurry diffusion range and the top pressure of the slurry at a certain grouting time, the greater the influence on the pore medium particles, and the more significant the influence on the permeability of the porous medium of the rock and soil, resulting in the gradual decrease of the permeability of the porous medium.
In order to verify the validity of the theory in this paper, the indoor test results in Reference 37 are compared with the theoretical results in this paper. In the test of Reference [37], three groups of ordinary Portland cement slurry with water cement ratio of 2.0, 5.0 and 10.0 were used to carry out three groups of different grouting pressure tests. The grouting test device is shown in Figure 4, which is composed of a pressure supply device, a slurry storage container and a model test box. The water of the cement slurry and the temperature of the test environment were both 20 ℃. According to Reference [38], it can be seen that the cement slurry of these three water cement ratios conforms to the properties of Newtonian fluid. The properties of the injected medium and grouting parameters are shown in Tables 2 and 3, and the rheological equation of cement slurry is shown in Table 4.
Group | Injection medium particle size distribution/mm | Porosity | Permeability coefficient/(cm/s) |
G1 | 1-3 | 0.3993 | 0.65 |
G2 | 3-5 | 0.4505 | 2.11 |
G3 | 5-10 | 0.5074 | 8.94 |
Based on Eqs (26) and (27), the diffusion radius of Newtonian fluid hemisphere considering the change of permeability of porous media and not considering the change of permeability of porous media is obtained. And the diffusion height of cylinder can also be obtained according to the diffusion radius of sphere part by Eq (20). And the theoretical diffusion radius and diffusion height, compared with the established literature indoor test values were analyzed, the results are shown in Figure 5.
Group | Water cement ratio | Grouting pressure/m | Grouting hole radius/cm | Grouting time/s |
G1 | 2.0 | 4.08 | 0.75 | 8 |
G2 | 5.0 | 6.12 | 0.75 | 6 |
G3 | 10.0 | 8.16 | 0.75 | 4 |
Water cement ratio | Rheological equation |
2.0 | τ = 0.0372 + 0.0047γ |
5.0 | τ = 0.0880 + 0.0027γ |
10.0 | τ = 0.0454 + 0.0019γ |
It can be seen from Figure 5 that the theoretical value considering the change of permeability is about 1.14 times of the experimental value, while the theoretical value without considering the change of permeability is about 1.60 times of the experimental value, indicating that the slurry diffusion length considering the change of permeability of geotechnical porous media is closer to the actual diffusion radius of Newtonian fluid infiltration grouting, thus verifying the validity of the theory in this paper. With the increase of water-cement ratio, the theoretical value considering the change of permeability is closer to the experimental value. This is because with the increase of water-cement ratio, the larger the slurry diffusion radius is, the greater the influence of slurry on the permeability of porous media is. It is more necessary to consider the change of permeability of porous media, so the theoretical results considering the change of permeability are closer to the experimental values.
In order to further verify the adaptability and reliability of the theory in this paper, based on the numerical simulation software COMSOL, the numerical simulation of Newtonian fluid seepage grouting column-hemisphere seepage diffusion with different grouting pressure heads is carried out, and the theoretical results are compared with the simulation results and test results to verify the effectiveness of the theory in this paper.
1) Model construction
The size of the model is 1000 mm × 1000 mm × 2000 mm, the grouting hole is located in the center, the radius of the orifice and the side grouting hole is 7.5 mm, the side grouting hole is set to 4, and the vertical interval is 20 mm (Figure 6). The pressure inlet boundary is selected, and the model boundary is a non-pressure boundary. The numerical simulation is based on the COMSOL two-phase Darcy's law module, the permeability change model function (Eq 8) derived in this paper is introduced through the built-in custom function of the software, so as to realize the simulation of diffusion of the infiltration column-hemisphere of porous media considering the permeability change. The grouting parameters and the parameters of the injected medium are set according to Tables 2-4.
2) Numerical results
In the numerical calculation, the surface Darcy velocity is used to represent the slurry diffusion range, that is, when the slurry diffusion velocity is 0, the slurry is no longer diffused [39]. Figure 7 shows the G3 group of Newtonian fluid cement slurry column-hemispherical diffusion model diagram. Figure 5 shows that the lower part of the slurry model diagram conforms to the hemispherical diffusion, and the upper part of the model diagram is not the standard cylindrical diffusion, but the diffusion form of the cylinder and the top semi-ellipsoid, which is different from the standard cylindrical diffusion. The simulation results are consistent with the indoor test results obtained by Yang et al. [40].
In order to verify the validity of the theoretical results, the numerical simulation values of the diffusion radius of the three groups of G1, G2 and G3 with different grouting pressure heads and the theoretical calculation values of the diffusion radius considering the permeability change of the porous medium are selected to compare with the experimental actual values. In order to make the comparison effect obvious, the middle section of the three-dimensional simulation diagram is selected. Since the upper cylindrical diffusion result is not a standard cylindrical shape, in order to better compare and verify the theoretical cylindrical diffusion results, this paper refers to Eq (30), that is, the equal product method adopted by Yang et al. [40] to calculate the equivalent height of cylindrical diffusion. The results are shown in Figure 8 and Table 5.
hd=√Vπl | (30) |
where hd is the cylindrical diffusion equivalent height; V the diffusion volume of Newtonian fluid stone can be obtained by calculation. l is a hemispherical diffusion radius, which can be measured.
Group | Hemisphere part diffusion radius/cm | Cylindrical part diffusion height (cm) | ||||
Simulated value | theoretical value | experimental value | Simulated value | theoretical value | experimental value | |
G1 | 16.32 | 14.39 | 11.8 | 50.12 | 47.98 | 39.33 |
G2 | 20.01 | 18.27 | 15.2 | 62.21 | 60.91 | 50.67 |
G3 | 21.58 | 20.98 | 18.4 | 70.37 | 69.93 | 61.33 |
It can be seen from Figure 6 and Table 5 that the theoretical calculation results are compared with the numerical simulation results. The radius difference of the hemisphere part is 2-10 %, and the height difference of the cylinder part is 1.5-4 %. It shows that the numerical simulation results of Newtonian fluid column-hemisphere diffusion inserted into the permeability change of porous media are basically consistent with the theoretical calculation results, which further verifies the validity of the theory in this paper. Both results are greater than the indoor test results, because this paper does not consider the filtration effect of slurry, diffusion path and other reasons.
Through the above analysis, it can be seen that there is still a difference between the theoretical analytical value and the numerical simulation value of the Newtonian fluid seepage grouting column-hemisphere diffusion radius considering the permeability change and the indoor test value. This is because this paper does not take into account the time-varying viscosity of the slurry, slurry diffusion path, slurry filtration effect and other effects on the slurry diffusion range.
Ruan et al. [38] obtained the relationship curve between slurry viscosity and time through laboratory test analysis. It can be seen that the slurry viscosity gradually increases with the increase of time, so the viscosity of the slurry in the diffusion process gradually increases. In this paper, the slurry viscosity value is certain, which leads to the theoretical value of the slurry diffusion radius in this paper is larger than the actual value of the slurry diffusion. Maghous et al. [41] and Fang et al. [20] theoretically analyzed that the cement slurry will produce cement particles to block the pores during the diffusion process of the porous medium, resulting in a decrease in the permeability of the porous medium. Because this article does not take into account the filtration effect of the cement slurry, the theoretical results are greater than the actual diffusion results. Bear et al. [32] and Lu et al. [15] proposed that the path of the slurry in the diffusion process is a curve rather than a straight line, and proved this view through theoretical analysis and laboratory tests. However, this paper does not consider the tortuosity in the slurry diffusion process, resulting in a deviation between the theoretical value and the actual value. Therefore, the influence of the above factors on the diffusion range of slurry infiltration grouting can be considered in the follow-up study.
In order to obtain the relationship between the diffusion range of Newtonian fluid seepage grouting column-hemisphere and grouting parameters considering the permeability change of porous media, the sensitivity analysis of slurry diffusion radius to grouting pressure and grouting time is carried out in this paper.
Based on the relevant literature research [15,16,17,23,37,38,39,40], the grouting pressure head range is 0-8 m, and the grouting time range is 0-10 min. The porosity is set to 0.4, the radius of grouting hole and side grouting hole is set to 15 mm, the side grouting hole is set to 4, the water cement ratio of slurry is 5.0, the viscosity of slurry is 0.0027 Pa·s, and the permeability coefficient is 0.6 cm/s.
At the same time, based on COMSOL numerical simulation software, numerical simulation tests with grouting pressure head of 0-8 m and grouting time of 0-10 min were carried out respectively. The numerical simulation results were compared with the theoretical calculation results to obtain the relationship between the diffusion radius of Newtonian fluid seepage grouting column-hemisphere and grouting time and grouting pressure. The parameter setting is the same as the above theoretical calculation parameters.
From Section 2.1, it can be seen that the change trend of diffusion radius and diffusion height of Newtonian fluid seepage grouting column-hemisphere is completely consistent, so this section only studies the sensitivity analysis of hemisphere diffusion radius. Based on the Eq (26), the relationship between the diffusion radius of Newtonian fluid cement slurry and the grouting pressure head and grouting time considering the permeability change of porous media is obtained, and the results are compared with the numerical simulation results. The comparison results are shown in Figures 9 and 10.
Figure 9 shows that with the increase of grouting pressure head, the slurry diffusion range gradually increases. At low grouting pressure, the slurry diffusion radius increases rapidly, from 0 to 1 m is the most obvious; with the further increase of grouting pressure, the rate gradually decreases. This is because the greater the grouting pressure, the greater the diffusion radius of the slurry, the greater the influence range on the permeability of the porous medium, resulting in a decrease in the rate of increase in the diffusion radius.
It can be seen from Figure 10 that with the increase of grouting time, the slurry diffusion radius increases rapidly at first and then increases slowly. This is because the slurry increases rapidly at the initial stage of grouting, but with the increase of grouting time, the slurry pressure gradually dissipates, so the diffusion rate gradually decreases.
In this paper, the influence of slurry flow resistance on the permeability of geotechnical porous media is introduced. Combined with the Newtonian fluid seepage grouting column-hemispherical diffusion law, the permeability change model of geotechnical porous media is obtained. Combined with the rheological equation and equilibrium equation of Newtonian fluid, a seepage grouting diffusion model considering the influence of slurry flow resistance on the permeability of porous media is established. The theoretical results are compared with the existing literature results and numerical simulation results to verify the effectiveness of the theoretical mechanism. At the same time, the parameter analysis of the diffusion radius of Newtonian fluid seepage grouting considering the permeability change of porous media is carried out. The following conclusions are obtained:
1) The influence of cement slurry flow resistance on the permeability of porous media in rock and soil during grouting is introduced. The analytical expression of the permeability of porous media with grouting construction parameters, slurry diffusion radius and pore characteristics of porous media is established.
2) The comparison between the theoretical results of this paper and the experimental results of the existing literature shows that the theoretical results considering the change of permeability are about 1.14 times of the experimental results, and the theoretical results without considering the change of permeability are about 1.6 times of the experimental results. At the same time, based on COMSOL numerical simulation software, the permeability change function of porous media is introduced, and the numerical simulation results are basically consistent with the theoretical results, which verifies the effectiveness of the theoretical mechanism in this paper.
3) The parametric analysis can be obtained that with the increase of grouting pressure and grouting time, the diffusion radius of Newtonian fluid infiltration grouting considering the change of permeability of the porous medium increases rapidly at first, and then the rate of increase becomes smaller gradually.
The authors declare they have not used Artificial Intelligence (AI) tools in the creation of this article.
This work was supported by the Scientific and Technological Research and Development Project of China Railway Guangzhou Bureau Co. Ltd. (No.2020K033-G), the Scientific and Technological Progress and Innovation Project of Hunan Provincial Department of Transportation (Nos. 202017; 202115), and the Fundamental Research Funds for the Central Universities of Central South University (No. 2023ZZTS0341). All financial supports are greatly appreciated.
The authors declare there is no conflict of interest.
[1] |
Okokpujie IP, Bolu CA, Ohunakin OS, et al. (2019) A review of recent application of machining techniques, based on the phenomena of CNC machining operations. Procedia Manuf 35: 1054–1060. https://doi.org/10.1016/j.promfg.2019.06.056 doi: 10.1016/j.promfg.2019.06.056
![]() |
[2] |
Natsu W, He J, Iwanaga Y (2020) Experimental study on electrochemical machining with electrolyte confined by absorption material. Procedia CIRP 87: 263–267. https://doi.org/10.1016/j.procir.2020.02.106 doi: 10.1016/j.procir.2020.02.106
![]() |
[3] |
Farooq MU, Anwar S, Bhatti HA, et al. (2023) Electric discharge machining of Ti6Al4V ELI in biomedical industry: Parametric analysis of surface functionalization and tribological characterization. Materials 16: 4458. https://doi.org/10.3390/ma16124458 doi: 10.3390/ma16124458
![]() |
[4] |
Happonen A, Stepanov A, Piili H, et al. (2015) Innovation study for laser cutting of complex geometries with paper materials. Phys Procedia 78: 128–137. https://doi.org/10.1016/j.phpro.2015.11.025 doi: 10.1016/j.phpro.2015.11.025
![]() |
[5] |
Gilmore R (1991) Ultrasonic machining: A case study. J Mater Process Tech 28: 139–148. https://doi.org/10.1016/0924-0136(91)90213-X doi: 10.1016/0924-0136(91)90213-X
![]() |
[6] |
Samsudeensadham S, Mohan A, Krishnaraj V (2021) A research on machining parameters during dry machining of Ti-6Al-4V alloy. Mater Today: Proc 46: 9354–9360. https://doi.org/10.1016/j.matpr.2020.02.821 doi: 10.1016/j.matpr.2020.02.821
![]() |
[7] |
Prasad AVSR, Ramji K, Datta GL (2014) An experimental study of wire EDM on Ti-6Al-4V alloy. Procedia Mater Sci 5: 2567–2576. https://doi.org/10.1016/j.mspro.2014.07.517 doi: 10.1016/j.mspro.2014.07.517
![]() |
[8] |
Rathod R, Kamble D, Ambhore N (2022) Performance evaluation of electric discharge machining of titanium alloy—A review. J Eng Appl Sci 69: 64. https://doi.org/10.1186/s44147-022-00118-z doi: 10.1186/s44147-022-00118-z
![]() |
[9] |
Nagadeepan A, Jayaprakash G, Senthilkumar V (2023) Advanced optimization of surface characteristics and material removal rate for biocompatible Ti6Al4V using WEDM process with BBD and NSGA Ⅱ. Materials 16: 4915. https://doi.org/10.3390/ma16144915 doi: 10.3390/ma16144915
![]() |
[10] |
Dewangan S, Kumar SD, Jha SK, et al. (2020) Optimization of micro-EDM drilling parameters of Ti-6Al-4V alloy. Mater Today: Proc 33: 5481–5485. https://doi.org/10.1016/j.matpr.2020.03.307 doi: 10.1016/j.matpr.2020.03.307
![]() |
[11] |
Garba E, Abdul-Rani AM, Yunus NA, et al. (2023) A review of electrode manufacturing methods for electrical discharge machining: Current status and future perspectives for surface alloying. Machines 11: 906. https://doi.org/10.3390/machines11090906 doi: 10.3390/machines11090906
![]() |
[12] |
Banu A, Ali MY (2016) Electrical discharge machining (EDM): A review. Int J Eng Mater Manuf 1: 3–10. https://doi.org/10.26776/ijemm.01.01.2016.02 doi: 10.26776/ijemm.01.01.2016.02
![]() |
[13] |
Galati M, Antonioni P, Calignano F, et al. (2023) Experimental investigation on the cutting of additively manufactured Ti6Al4V with wire-EDM and the analytical modelling of cutting speed and surface roughness. J Manuf Mater Process 7: 69. https://doi.org/10.3390/jmmp7020069 doi: 10.3390/jmmp7020069
![]() |
[14] |
Kamenskikh AA, Muratov KR, Shlykov ES, et al. (2023) Recent trends and developments in the electrical discharge machining industry: A review. J Manuf Mater Process 7: 204. https://doi.org/10.3390/jmmp7060204 doi: 10.3390/jmmp7060204
![]() |
[15] |
Ram JS, Jeavudeen S, Mouda PA, et al. (2023) The role of various dielectrics used in EDM process and their environmental, health, and safety issues. Mater Today: Proc. https://doi.org/10.1016/j.matpr.2023.05.137 doi: 10.1016/j.matpr.2023.05.137
![]() |
[16] |
Nadda R, Nirala CK, Singh PK, et al. (2024) An overview of techniques for monitoring and compensating tool wear in micro-electrical discharge machining. Heliyon 10: e26784. https://doi.org/10.1016/j.heliyon.2024.e26784 doi: 10.1016/j.heliyon.2024.e26784
![]() |
[17] |
Nguyen VQ, Duong TH, Kim HC (2015) Precision micro EDM based on real-time monitoring and electrode wear compensation. Int J Adv Manuf Tech 79: 1829–1838. https://doi.org/10.1007/s00170-015-6964-y doi: 10.1007/s00170-015-6964-y
![]() |
[18] |
Di Campli R, Maradia U, Boccadoro M, et al. (2020) Real-time wire EDM tool simulation enabled by discharge location tracker. Procedia CIRP 95: 308–312. https://doi.org/10.1016/j.procir.2020.01.176 doi: 10.1016/j.procir.2020.01.176
![]() |
[19] |
Mhatre MS, Sapkal SU, Pawade RS (2014) Electro discharge machining characteristics of Ti-6Al-4V alloy: A grey relational optimization. Procedia Mater Sci 5: 2014–2022. https://doi.org/10.1016/j.mspro.2014.07.534 doi: 10.1016/j.mspro.2014.07.534
![]() |
[20] |
Gu L, Li L, Zhao W, et al. (2012) Electrical discharge machining of Ti6Al4V with a bundled electrode. Int J Mach Tool Manu 53: 100–106. https://doi.org/10.1016/j.ijmachtools.2011.10.002 doi: 10.1016/j.ijmachtools.2011.10.002
![]() |
[21] |
Świercz R, Oniszczuk-Świercz D, Chmielewski T (2019) Multi-response optimization of electrical discharge machining using the desirability function. Micromachines 10: 72. https://doi.org/10.3390/mi10010072 doi: 10.3390/mi10010072
![]() |
[22] |
Maniyar KG, Ingole DS (2018) Multi response optimization of EDM process parameters for aluminium hybrid composites by GRA. Mater Today: Proc 5: 19836–19843. https://doi.org/10.1016/j.matpr.2018.06.347 doi: 10.1016/j.matpr.2018.06.347
![]() |
[23] |
Agarwal N, Irshad M, Singh M R, et al. (2022) Optimization of material removal rate of Ti-6Al-4V using Rao-1 algorithm. Mater Today: Proc 62: 6722–6726. https://doi.org/10.1016/j.matpr.2022.04.760 doi: 10.1016/j.matpr.2022.04.760
![]() |
[24] |
Klocke F, Schwade M, Klink A, et al. (2013) Analysis of material removal rate and electrode wear in sinking EDM roughing strategies using different graphite grades. Procedia CIRP 6: 163–167. https://doi.org/10.1016/j.procir.2013.03.079 doi: 10.1016/j.procir.2013.03.079
![]() |
[25] |
Kumar R, Roy S, Gunjan P, et al. (2018) Analysis of MRR and surface roughness in machining Ti-6Al-4V ELI titanium alloy using EDM process. Procedia Manuf 20: 358–364. https://doi.org/10.1016/j.promfg.2018.02.052 doi: 10.1016/j.promfg.2018.02.052
![]() |
[26] |
Shao F, Liu Z, Wan Y, et al. (2010) Finite element simulation of machining of Ti-6Al-4V alloy with thermodynamical constitutive equation. Int J Adv Manuf Tech 49: 431–439. https://doi.org/10.1007/s00170-009-2423-y doi: 10.1007/s00170-009-2423-y
![]() |
[27] | Caballero B, Finglas P, Toldrá F (2016) Encyclopedia of Food and Health, New York: Academic Press, 321–326. |
[28] |
Iqbal A, Khan AA (2010) Modeling and analysis of MRR, EWR and surface roughness in EDM milling through response surface methodology. Am J Eng Appl Sci 3: 611–619. https://doi.org/10.3923/jeasci.2010.154.162 doi: 10.3923/jeasci.2010.154.162
![]() |
[29] |
Liu Y, Fearn T, Strlič M (2021) Factorial experimentation on photodegradation of historical paper by polychromatic visible radiation. Herit Sci 9: 130. https://doi.org/10.1186/s40494-021-00602-4 doi: 10.1186/s40494-021-00602-4
![]() |
[30] |
Sultan T, Kumar A, Gupta RD (2014) Material removal rate, electrode wear rate, and surface roughness evaluation in die sinking EDM with hollow tool through response surface methodology. Int J Manuf Eng 2014: 259129. https://doi.org/10.1155/2014/259129 doi: 10.1155/2014/259129
![]() |
[31] |
Seshaiah S, Sampathkumar D, Mariappan M, et al. (2022) Optimization on material removal rate and surface roughness of stainless steel 304 wire cut EDM by response surface methodology. Adv Mater Sci Eng 2022: 6022550. https://doi.org/10.1155/2022/6022550 doi: 10.1155/2022/6022550
![]() |
[32] |
Jin HT, Wang F, Zhang W, et al. (2023) Linear regression analysis of sleep quality in people with insomnia in Wuhan city during the COVID-19 pandemic. Int J Clin Pract 2023: 6746045. https://doi.org/10.1155/2023/6746045 doi: 10.1155/2023/6746045
![]() |
[33] | Sarstedt M, Mooi E (2014) A Concise Guide to Market Research, 2 Eds., Berlin: Springer, 193–233. |
[34] |
Harane PP, Wojciechowski S, Unune DR (2022) Investigating the effect of different tool electrodes in electric discharge drilling of Waspaloy on process responses. J Mater Res Technol 20: 2542–2557. https://doi.org/10.1016/j.jmrt.2022.08.015 doi: 10.1016/j.jmrt.2022.08.015
![]() |
[35] |
Devarajaiah D, Muthumari C (2018) Evaluation of power consumption and MRR in WEDM of Ti-6Al-4V alloy and its simultaneous optimization for sustainable production. J Braz Soc Mech Sci 40: 400. https://doi.org/10.1007/s40430-018-1318-y doi: 10.1007/s40430-018-1318-y
![]() |
[36] |
Tang L, Du YT (2014) Experimental study on green electrical discharge machining in tap water of Ti-6Al-4V and parameters optimization. Int J Adv Manuf Tech 70: 469–475. https://doi.org/10.1007/s00170-013-5274-5 doi: 10.1007/s00170-013-5274-5
![]() |
![]() |
![]() |
W/C | μ0/(Pa·s) | ρ/(g/cm3) | K0/(cm/s) | φ | r0/cm | τ0/Pa |
2.0 | 0.0067 | 1.30 | 0.0334 | 0.4 | 0.5 | 0.0971 |
Group | Injection medium particle size distribution/mm | Porosity | Permeability coefficient/(cm/s) |
G1 | 1-3 | 0.3993 | 0.65 |
G2 | 3-5 | 0.4505 | 2.11 |
G3 | 5-10 | 0.5074 | 8.94 |
Group | Water cement ratio | Grouting pressure/m | Grouting hole radius/cm | Grouting time/s |
G1 | 2.0 | 4.08 | 0.75 | 8 |
G2 | 5.0 | 6.12 | 0.75 | 6 |
G3 | 10.0 | 8.16 | 0.75 | 4 |
Water cement ratio | Rheological equation |
2.0 | τ = 0.0372 + 0.0047γ |
5.0 | τ = 0.0880 + 0.0027γ |
10.0 | τ = 0.0454 + 0.0019γ |
Group | Hemisphere part diffusion radius/cm | Cylindrical part diffusion height (cm) | ||||
Simulated value | theoretical value | experimental value | Simulated value | theoretical value | experimental value | |
G1 | 16.32 | 14.39 | 11.8 | 50.12 | 47.98 | 39.33 |
G2 | 20.01 | 18.27 | 15.2 | 62.21 | 60.91 | 50.67 |
G3 | 21.58 | 20.98 | 18.4 | 70.37 | 69.93 | 61.33 |
W/C | μ0/(Pa·s) | ρ/(g/cm3) | K0/(cm/s) | φ | r0/cm | τ0/Pa |
2.0 | 0.0067 | 1.30 | 0.0334 | 0.4 | 0.5 | 0.0971 |
Group | Injection medium particle size distribution/mm | Porosity | Permeability coefficient/(cm/s) |
G1 | 1-3 | 0.3993 | 0.65 |
G2 | 3-5 | 0.4505 | 2.11 |
G3 | 5-10 | 0.5074 | 8.94 |
Group | Water cement ratio | Grouting pressure/m | Grouting hole radius/cm | Grouting time/s |
G1 | 2.0 | 4.08 | 0.75 | 8 |
G2 | 5.0 | 6.12 | 0.75 | 6 |
G3 | 10.0 | 8.16 | 0.75 | 4 |
Water cement ratio | Rheological equation |
2.0 | τ = 0.0372 + 0.0047γ |
5.0 | τ = 0.0880 + 0.0027γ |
10.0 | τ = 0.0454 + 0.0019γ |
Group | Hemisphere part diffusion radius/cm | Cylindrical part diffusion height (cm) | ||||
Simulated value | theoretical value | experimental value | Simulated value | theoretical value | experimental value | |
G1 | 16.32 | 14.39 | 11.8 | 50.12 | 47.98 | 39.33 |
G2 | 20.01 | 18.27 | 15.2 | 62.21 | 60.91 | 50.67 |
G3 | 21.58 | 20.98 | 18.4 | 70.37 | 69.93 | 61.33 |