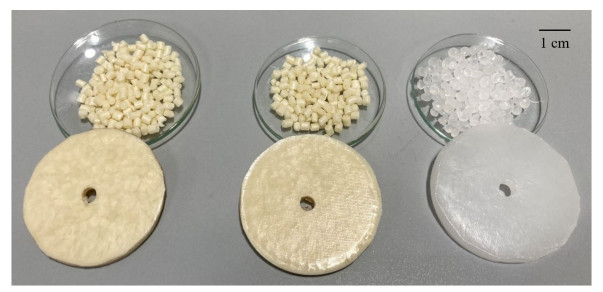
Recycling of plastic materials is a key sustainability topic. Hence, the scope of this study is to evaluate the potential of this purification step for achieving high-purity recyclates via mechanical recycling. In this study, the focus is set on the revalorization of poly(3-hydroxy butyrate) and poly(3-hydroxy butyrate-co-3-hydroxy valerate)—two biobased and biodegradable polymers that have properties similar to those of polyolefins and are therefore possible eco-friendly alternatives. Specifically, the washing process as an important part of polymer recycling processes is evaluated regarding different washing conditions on a laboratory scale. For this purpose, several virgin polymers were contaminated with volatile organic compounds that differed in functionality and molecular weight. Regarding contamination, concentration correlates with contamination time. Moreover, the contamination degree was found to be higher for polar contaminants since polar compounds show higher compatibility with the polymer. General beneficial effects of higher temperatures and longer washing times were observed. The choice of washing medium was relevant for different polarities of the contaminants. At higher process temperatures, material degradation occurred. Hence, recyclers have to pay attention to the difference in the interaction between impurities and the polymer and to the degradation of the polymer during recycling and the subsequent formation of degradation products. Since these biopolymers display comparable properties to polyolefins, great potential in packaging applications is apparent. Moreover, the method of analyzing the removal efficiency of volatile organic compounds via washing can be applied to all recyclable polymers.
Citation: Konstanze Kruta, Jörg Fischer, Peter Denifl, Christian Paulik. Effect of different washing conditions on the removal efficiency of selected compounds in biopolymers[J]. Clean Technologies and Recycling, 2023, 3(3): 134-147. doi: 10.3934/ctr.2023009
[1] | Yi Ji, Edwin E. Kpodzro, Chad T. Jafvert, Fu Zhao . Direct recycling technologies of cathode in spent lithium-ion batteries. Clean Technologies and Recycling, 2021, 1(2): 124-151. doi: 10.3934/ctr.2021007 |
[2] | Shuwen Zhang, Noah Kirumira . Techniques of recycling end-of-life wind turbine blades in the pavement industry: A literature review. Clean Technologies and Recycling, 2024, 4(1): 89-107. doi: 10.3934/ctr.2024005 |
[3] | Congying Wang, Fu Zhao, Carol Handwerker . Transforming and integrating informal sectors into formal e-waste management system: A case study in Guiyu, China. Clean Technologies and Recycling, 2022, 2(4): 225-246. doi: 10.3934/ctr.2022012 |
[4] | Dieuwertje L. Schrijvers, Philippe Loubet, Guido W. Sonnemann . The influence of market factors on the potential environmental benefits of the recycling of rare earth elements. Clean Technologies and Recycling, 2022, 2(1): 64-79. doi: 10.3934/ctr.2022004 |
[5] | Kyle Pender, Liu Yang . Glass fibre composites recycling using the fluidised bed: A study into the economic viability in the UK. Clean Technologies and Recycling, 2023, 3(3): 221-240. doi: 10.3934/ctr.2023014 |
[6] | Glenn Baxter . Towards sustainable airport waste management through the adoption of a "green" airport strategy: The case of Incheon International Airport. Clean Technologies and Recycling, 2022, 2(4): 247-278. doi: 10.3934/ctr.2022013 |
[7] | Grace Inman, Denis Prodius, Ikenna C. Nlebedim . Recent advances in acid-free dissolution and separation of rare earth elements from the magnet waste. Clean Technologies and Recycling, 2021, 1(2): 112-123. doi: 10.3934/ctr.2021006 |
[8] | Susana J. Castillo, Anna Hayes, Greg Colvin, Barrett G. Potter, Rongguang Liang, Krishna Muralidharan . Characterization of recycled Inconel 718 metal powder for assessing its reusability in the laser powder bed fusion process. Clean Technologies and Recycling, 2022, 2(1): 32-46. doi: 10.3934/ctr.2022002 |
[9] | Majid Alipanah, Sunday Oluwadamilola Usman, Apurba Kumar Saha, Hongyue Jin . Designing profitable supply chains for lithium-ion battery recycling in the United States. Clean Technologies and Recycling, 2024, 4(1): 22-42. doi: 10.3934/ctr.2024002 |
[10] | Wilson Uzochukwu Eze, Reginald Umunakwe, Henry Chinedu Obasi, Michael Ifeanyichukwu Ugbaja, Cosmas Chinedu Uche, Innocent Chimezie Madufor . Plastics waste management: A review of pyrolysis technology. Clean Technologies and Recycling, 2021, 1(1): 50-69. doi: 10.3934/ctr.2021003 |
Recycling of plastic materials is a key sustainability topic. Hence, the scope of this study is to evaluate the potential of this purification step for achieving high-purity recyclates via mechanical recycling. In this study, the focus is set on the revalorization of poly(3-hydroxy butyrate) and poly(3-hydroxy butyrate-co-3-hydroxy valerate)—two biobased and biodegradable polymers that have properties similar to those of polyolefins and are therefore possible eco-friendly alternatives. Specifically, the washing process as an important part of polymer recycling processes is evaluated regarding different washing conditions on a laboratory scale. For this purpose, several virgin polymers were contaminated with volatile organic compounds that differed in functionality and molecular weight. Regarding contamination, concentration correlates with contamination time. Moreover, the contamination degree was found to be higher for polar contaminants since polar compounds show higher compatibility with the polymer. General beneficial effects of higher temperatures and longer washing times were observed. The choice of washing medium was relevant for different polarities of the contaminants. At higher process temperatures, material degradation occurred. Hence, recyclers have to pay attention to the difference in the interaction between impurities and the polymer and to the degradation of the polymer during recycling and the subsequent formation of degradation products. Since these biopolymers display comparable properties to polyolefins, great potential in packaging applications is apparent. Moreover, the method of analyzing the removal efficiency of volatile organic compounds via washing can be applied to all recyclable polymers.
Abbreviations: GC-MS: gas chromatography–mass spectrometry; HAc: acetic acid, PHA: polyhydroxyalkanoate; PHB: poly (3-hydroxy butyrate); PHBV: poly(3-hydroxy butyrate-co-3-hydroxy valerate); LDPE: low-density polyethylene; SEC: size-exclusion chromatography; TD: thermal desorber; VOCs: volatile organic compounds
A large proportion of everyday products are made of various types of plastic. Since the service life of these disposable products which are often only used for a short period is limited, the recycling of plastic waste is one of the major challenges in modern society [1]. Besides landfilling and incineration, mechanical and chemical recycling are possible pathways to keep the raw material in the loop [2]. Although various aspects of recycling processes have been studied extensively in recent years, the washing step as an important part of the mechanical recycling process has received little attention [3].
Although washing as such is straightforward, the process can be relatively complex. In the course of this purification step, impurities are transferred from the plastic to the washing medium. As the operating costs of polymer recycling plants contribute significantly to the total costs of recyclates, an optimal balance between effective removal of impurities and cost efficiency is sought [4].
A well-established technique for reducing contamination is wet cleaning. The inherent advantages of washing with water are (i) high cleaning efficiency and (ii) the possibility of component separation according to density [5,6]. Disadvantages are high water consumption, the need for wastewater treatment and residual moisture that must be removed by costly drying procedures. Detergents and other additives can be added for improved removal of impurities but they may interact with the polymer matrix resulting in decomposition which for instance can have a negative effect on its mechanical properties [6]. Furthermore, these adjuvants may be harmful to the environment [7].
The recycling of biobased and biodegradable materials gained special attention. While the amount of biobased polymers globally produced was increasing steadily in the last few years [1], the circularity aspect is highly discussed [8]. Critics of recycling claim that recycling biodegradable polymers does not take advantage of their biodegradability. Besides, when these polymers enter the regular plastic streams they may cause severe complications in polymer recycling [8,9]. Nevertheless, excessive landfilling of biodegradable plastic products may lead to the emission of methane and the loss of valuable feedstock. Hence, different recycling routes for the revalorization of these materials are discussed. While mechanical recycling of conventional plastics is already established, the suitability of biopolymers has to be tested [8].
As an example for a bio-based, biodegradable plastic, the emphasis in this paper is on the purification of PHA. These aliphatic polyesters are obtained primarily by fermentation of lipids and sugars (e.g., of vegetable oils, glucose and sucrose) by various bacteria. Their synthesis includes polymerization of β-, γ- and δ-hydroxy alkanoic acids. High production efforts especially during fermentation and purification result in immense production costs. The most widely used PHAs are PHB and PHBV [10].
While PHB is very brittle and shows poor thermal stability when molten, it forms a decent barrier to water. Compared to PHB, PHBV with a copolymer content of 15% hydroxy valerate is more flexible and more easily processable. The biodegradation behavior of PHAs depends crucially on the degree of crystallinity and the chain configuration. For PHBVs, a degradation rate of about 80% after one year at 30 ℃ in marine environments has been reported [10].
The focus of this study is set on PHB and PHBV due to their comparable properties to polypropylene and polyethylene [11]. They are used commercially in the packaging of single-use items. Furthermore, due to their high biocompatibility, PHB and PHBV are currently being evaluated for use in the biomedical sector as bioresorbable sutures and wound dressings [10].
The materials used were PHB obtained from Tianan biopolymer (ENMAT Y1000P), PHBV from Tianan biopolymer (ENMAT Y3000P, 3-hydroxypentanoic acid content < 2%) and LDPE from Lyondell Basell (Lupolen 2426H). For evaluation of contaminations, sample plates made of PHB, PHBV and LDPE with a predefined circular geometry (50 mm diameter, 4 mm height) were produced using an automated hydraulic press (Vogt LaboPress P 200 T). The processing temperature was 180 ℃ [11]. After preheating for about one min, the samples were pressed for 7 min at 250 bar. The granulates and the processed sample plates are depicted in Figure 1.
To be able to measure washing efficiency, the sample plates were intentionally contaminated with various compounds.
The impacts of carbon chain length and functional groups on the efficiency of removing VOCs by washing were evaluated using a variety of analytes (Table 1). For contamination, a closed system was generated using desiccator equipment with equal weight concentrations of each contaminant. The desiccator solution was renewed every 14 days due to chemical reactions such as esterification of some compounds in the solution in the desiccator.
Compound | Supplier | Purity |
Acetic acid | Fisher scientific© | > 99% |
Pentanal | Aldrich | 97% |
1-Pentanol | Acros organics | 99% |
Pentanoic acid | Merck | 99% |
Octanoic acid | Merck | p.a. |
Decane | Carl roth | 99% |
1-Decanol | Merck | > 99% |
Decanoic acid | Alfa aesar | 99% |
After exposure of the samples to the contaminants for a defined time, all samples were dried at room temperature for 2 h and washed for 1 h. As shown in Figure 2, during washing a mechanical stirrer where the sample plated was fixed in combination with a magnetic stirrer in counter-current was used (both stirrers 100 rpm). The concentration of the contaminants was evaluated before and after washing. Figure 3 presents the experimental setup.
The analytes were quantified before and after the washing procedure with GC-MS by Perkin Elmer© in accordance with VDA 278 (TD TurboMatrix 650, Gas Chromatograph Clarus 690, Mass Spectrometer Clarus SQ 8T, Column Agilent J & W HP-ULTRA 2, 50 m × 0.32 mm i.d. × 0.52 μm, 0.2 mL/min He flow). About 0.1 g sample was measured. After thermal desorption (TD, 20 min 90 ℃), the contaminants were enriched in a trap. The following temperature program was used: 40 ℃ for 2 min, 40–92 ℃ (3 ℃/min), 92–160 ℃ (5 ℃/min), 160–280 ℃ (10 ℃/min), 280 ℃ for 10 min.
SEC was performed to evaluate the molecular weight distribution before and after washing. To dissolve PHB in chloroform, a 50 ℃ ultrasonic bath was used. An Agilent 1100 device with an Agilent PLGel 10 µm 50 × 7.5 precolumn, Agilent PLGel Mixed-B 10 µm 300 × 7.5 column and an Agilent PLGel Mixed-D 5 µm 300 × 7.5 column was employed. 100 µL was injected, a flow rate of 1 mL/min was adjusted and the analytes were detected via a refractive index detector.
Concerning the analysis of the reduction in sample weight after washing under various conditions, the washing was executed the same way as described above. The samples were dried after washing for four days at 50 ℃ and weighed with an analytical balance.
The removal rates of HAc from PHB, PHBV and LDPE after 10 and 60 min of washing are shown in Figures 4 and 5, respectively.
It can be seen that the washing processes at 25 ℃ in water and NaOH removed about the same amount of acetic acid from PHB and PHBV. Compared to LDPE, slightly more acetic acid was washed out from the biopolymers. Longer washing times led to a higher removal rate. At elevated temperatures (80 ℃), washing efficiency was high for both bio-based materials. This may have been due to the degradation of PHB and PHBV which is enhanced by increasing temperature and alkalinity [12]. Since PHB and PHBV exhibited almost identical behaviour, the number of experiments has been reduced by focussing on the washing profile of PHB.
The impact of washing temperature is illustrated in Figure 6 which plots the temperature profiles for acetic acid removal after 10 and 60 min.
A direct correlation between washing temperature and decontamination efficiency and the effect of washing time can be observed: The higher the temperature and the longer the washing time, the more efficient the decontamination.
The contamination behavior of contaminants depended on their properties. Figures 7 and 8 show the concentrations of various VOCs in a PHB matrix after a range of contact times.
Generally, a direct correlation between contact time and concentration was observed which is shown in Figure 8 with focus on the range between 0–0.3 µmol/g. Since PHB is a polyester and thus has polar functional groups, higher polarity of the contaminant led to higher concentration in the matrix. Molecular weight (carbon chain length) was indirectly correlated with the concentration. The highest concentration was measured for acetic acid, the analyte with the smallest molecular weight and the highest polarity. It is in the range of about 10 µmol/g which is about 10 times higher than all other contaminants. The divergence of correlation regarding the measurements on day 11 and day 12 may be based on inhomogeneous contamination due to esterification of the analytes.
Unlike in PHB, in LDPE the most apolar compound (decane) reached the highest concentration in the contamination experiments (Figure 9). This was due to the contrasting chemical properties of PE. The concentrations of all contaminants were about 10 to 35 times higher in LDPE than in PHB.
The results of decontamination by washing are shown in Figures 10 and 11. Some results were below the quantification limit of about 7 µg/g because the sample weight in the thermal desorption tube was too low. Unfortunately, the material was limited and repeated measurements were not planned.
It can be seen that the removal rate increased with increasing washing time. Furthermore, a higher washing temperature increased decontamination efficiency considerably. The addition of NaOH to the washing medium was beneficial in some cases. For carboxylic acids, deprotonation was favorable. For alcohols, the best washing efficiency was achieved in pure water. The beneficial effect of adding NaOH at 25 ℃ washing temperature increased with increasing chain length of the carboxylic acid.
Since degradation of PHB during washing has been reported in literature [12], SEC was performed to determine the molecular weight distributions before and after washing. For SEC, the samples had to be dissolved in a medium. According to the literature [11], the solubility of PHB in chloroform is good. For dissolving the polymer ultrasonication in an ultrasonic bath at a temperature of 50 ℃ was used. However, even under this condition complete dissolution of the polymer was not possible. This needs to be taken into consideration when analyzing the polymer weight distribution (Figure 12). Nevertheless, qualitative interpretation is possible.
In order to comprehend the high decontamination rates at elevated temperatures, SEC measurements give insight into the degradation of materials. Degradation of PHB is discussed in several publications [8,12,13]. Compared to unwashed PHB, the molecular weight distribution changed with each washing step. When pure water was used, high signals in the range of 103 g/mol were obtained and a decrease from the initial molecular weight was observed. Interestingly, no random cleavage occurred but a relatively defined fraction in the range of 103 g/mol appeared. The effect of temperature seemed to be insignificant. However, the high decontamination rates for higher temperatures may indicate chain cleavage resulting in water-soluble polymer chains with a very low molecular weight. Since the contaminants seem to be mainly on the surface, the degradation of the polymer benefits their removal.
With NaOH in the washing medium, a significantly smaller 103 g/mol fraction was observed compared to washing with water, a slight shift of the signal towards lower molecular weights occurred and the washing efficiency was very high. One possible explanation is the degradation of products with a very low molecular weight which are soluble in the washing medium. The reduction in molecular weight after 60 min of washing time was investigated, the results of which are shown in Table 2.
Washing conditions | Weight loss/g | Standard deviation/% |
25 ℃ Water | 0.013 | 0.00005 |
80 ℃ Water | 0.016 | 0.0016 |
25 ℃ NaOH | 0.017 | 0.00005 |
80 ℃ NaOH | 0.031 | 0.0034 |
The greatest reduction in molecular weight loss was observed after washing in NaOH at 80 ℃. This supports the theory that degradation occurred and that the resulting polymer chains had very low molecular weight and were thus soluble in the washing medium.
Effective cleaning of polymers clearly depends on both the polymer characteristics and the properties of the contaminants. The biopolymers PHB and PHBV which are polyesters with polar functional groups differed from LDPE in terms of the interaction of VOCs. Higher polarity and lower molecular weight of the contaminant led to a higher concentration in the sample matrix. The washing behavior of PHB and PHBV was very similar.
Decontamination efficiency increased with increasing washing temperature and washing time. Furthermore, a direct correlation between exposure time during sample preparation and resulting impurity concentration in the polymer was observed. Addition of NaOH to the washing medium increased decontamination but not for all contaminants.
Degradation of PHB after washing in water was observable in the form of a relatively defined fraction in the range of 103 g/mol due to chain scission. Washing with NaOH resulted in a significantly smaller 103 g/mol fraction and the greatest reduction in polymer sample weight. This may be explained by the degradation of products with a very low molecular weight that were soluble in the washing medium.
Hence, recyclers have to pay attention to the difference in interaction between impurities and the polymer and to the degradation of the polymer during recycling and the subsequent formation of degradation products. Since these biopolymers display comparable properties to polyolefins [11], great potential in packaging applications is apparent.
As a result, the suggested conditions for a high removal efficiency are washing in water at 80 ℃. The benefits are greater decontamination efficiency due to the elevated temperature and lower costs compared to washing with NaOH which includes production costs and wastewater treatment. However, the effect of physical properties such as surface area and volume of the tested specimen as well as the presence of other polymers and impurities in the waste mixture can have an impact on the washing efficiency [14] and should be evaluated more in future studies in detail.
In addition, the recyclability of the material must be assessed separately since thermal and chemical instability of the polymers under the tested and typically applied washing conditions in industry are major problems. For instance, one research field is acidic digestion before heat application [13].
The authors declare they have not used Artificial Intelligence (AI) tools in the creation of this article.
This work was accomplished within the collaborative project "BIOCYCLE-UA|Kreislaufwirtschaft am Beispiel ausgewählter Biopolymere" co-funded by the European Union within the IWB/EFRE/REACT-EU program "Investitionen in Wachstum & Beschäftigung. Österreich". This work was performed within the Competence Center CHASE GmbH. A special tribute is paid to Kompetenzzentrum Holz GmbH for providing the materials.
All authors declare no conflicts of interest in this paper.
All authors contributed to the study's conception and design. Material preparation, data collection and analysis were performed by Konstanze Kruta. The first draft of the manuscript was written by Konstanze Kruta and all authors commented on previous versions of the manuscript. All authors read and approved the final manuscript. All authors agree on the permission to participate and to publish. The datasets generated during and/or analyzed during the current study are available from the corresponding author upon reasonable request.
[1] | Plastics Europe, Plastics—the Facts 2022. Plastics Europe, 2022. Available from: https://plasticseurope.org/knowledge-hub/plastics-the-facts-2022/. |
[2] |
Eze WU, Umunakwe R, Obasi HC, et al. (2021) Plastics waste management: A review of pyrolysis technology. Clean Technol Recy 1: 50–69. https://doi.org/10.3934/ctr.2021003 doi: 10.3934/ctr.2021003
![]() |
[3] |
Soto JM, Blázquez G, Calero M, et al. (2018) A real case study of mechanical recycling as an alternative for managing of polyethylene plastic film presented in mixed municipal solid waste. J Clean Prod 203: 777–787. https://doi.org/10.1016/j.jclepro.2018.08.302 doi: 10.1016/j.jclepro.2018.08.302
![]() |
[4] |
Soto JM, Martín-Lara MA, Blázquez G, et al. (2020) Novel pre-treatment of dirty post-consumer polyethylene film for its mechanical recycling. Process Saf Environ 139: 315–324. https://doi.org/10.1016/j.psep.2020.04.044 doi: 10.1016/j.psep.2020.04.044
![]() |
[5] | Reclay StewardEdge, Analysis of flexible film plastics packaging diversion systems. Recsource Recycling Systems, and Moore Recycling Associates Inc., 2013. Available from: https://thecif.ca/projects/documents/714-Flexible_Film_Report.pdf. |
[6] |
Xia D, Zhang FS (2018) A novel dry cleaning system for contaminated waste plastic purification in gas-solid media. J Clean Prod 171: 1472–1480. https://doi.org/10.1016/j.jclepro.2017.10.028 doi: 10.1016/j.jclepro.2017.10.028
![]() |
[7] |
Liu W, Zhang B, Li Y, et al. (2014) An environmentally friendly approach for contaminants removal using supercritical CO2 for remanufacturing industry. Appl Surf Sci 292: 142–148. https://doi.org/10.1016/j.apsusc.2013.11.102 doi: 10.1016/j.apsusc.2013.11.102
![]() |
[8] |
Niaounakis M (2019) Recycling of biopolymers—The patent perspective. Eur Polym J 114: 464–475. https://doi.org/10.1016/j.eurpolymj.2019.02.027 doi: 10.1016/j.eurpolymj.2019.02.027
![]() |
[9] |
Cornell DD (2007) Biopolymers in the existing postconsumer plastics recycling stream. J Polym Environ 15: 295–299. https://doi.org/10.1007/s10924-007-0077-0 doi: 10.1007/s10924-007-0077-0
![]() |
[10] |
Fredi G, Dorigato A (2021) Recycling of bioplastic waste: A review. Adv Ind Eng Polym Res 4: 159–177. https://doi.org/10.1016/j.aiepr.2021.06.006 doi: 10.1016/j.aiepr.2021.06.006
![]() |
[11] |
McAdam B, Fournet MB, McDonald P, et al. (2020) Production of polyhydroxybutyrate (PHB) and factors impacting its chemical and mechanical characteristics. Polymers 12: 2908. https://doi.org/10.3390/polym12122908 doi: 10.3390/polym12122908
![]() |
[12] |
Yu J, Plackett D, Chen LXL (2005) Kinetics and mechanism of the monomeric products from abiotic hydrolysis of poly[(R)-3-hydroxybutyrate] under acidic and alkaline conditions. Polym Degrad Stabil 89: 289–299. https://doi.org/10.1016/j.polymdegradstab.2004.12.026 doi: 10.1016/j.polymdegradstab.2004.12.026
![]() |
[13] |
Pospisilova A, Melcova V, Figalla S, et al. (2021) Techniques for increasing the thermal stability of poly[(R)-3-hydroxybutyrate] recovered by digestion methods. Polym Degrad Stabil 193: 109727. https://doi.org/10.1016/j.polymdegradstab.2021.109727 doi: 10.1016/j.polymdegradstab.2021.109727
![]() |
[14] | Delva L, Van Kets K, Kuzmanovic M, et al., Mechanical recycling of polymers for dummies. Capture—Plastics To Resource, 2019. Available from: https://www.ugent.be/ea/match/cpmt/en/research/topics/circular-plastics/mechanicalrecyclingfordummiesv2.pdf. |
Compound | Supplier | Purity |
Acetic acid | Fisher scientific© | > 99% |
Pentanal | Aldrich | 97% |
1-Pentanol | Acros organics | 99% |
Pentanoic acid | Merck | 99% |
Octanoic acid | Merck | p.a. |
Decane | Carl roth | 99% |
1-Decanol | Merck | > 99% |
Decanoic acid | Alfa aesar | 99% |
Washing conditions | Weight loss/g | Standard deviation/% |
25 ℃ Water | 0.013 | 0.00005 |
80 ℃ Water | 0.016 | 0.0016 |
25 ℃ NaOH | 0.017 | 0.00005 |
80 ℃ NaOH | 0.031 | 0.0034 |
Compound | Supplier | Purity |
Acetic acid | Fisher scientific© | > 99% |
Pentanal | Aldrich | 97% |
1-Pentanol | Acros organics | 99% |
Pentanoic acid | Merck | 99% |
Octanoic acid | Merck | p.a. |
Decane | Carl roth | 99% |
1-Decanol | Merck | > 99% |
Decanoic acid | Alfa aesar | 99% |
Washing conditions | Weight loss/g | Standard deviation/% |
25 ℃ Water | 0.013 | 0.00005 |
80 ℃ Water | 0.016 | 0.0016 |
25 ℃ NaOH | 0.017 | 0.00005 |
80 ℃ NaOH | 0.031 | 0.0034 |