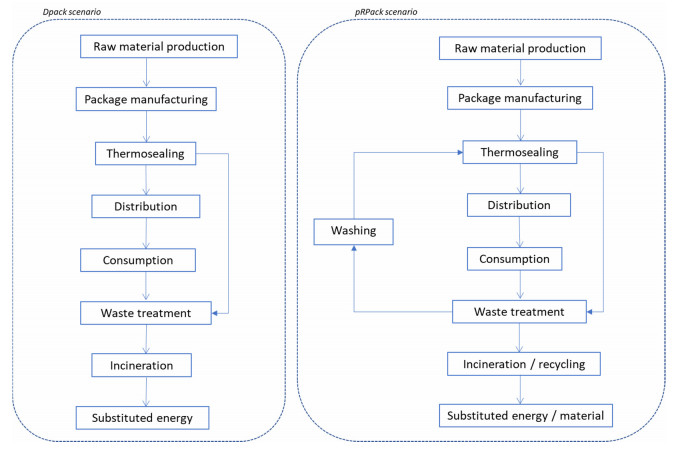
To limit the huge damage caused by plastic pollution, major changes need to be made in the food and beverage packaging sector. In this context, a new packaging system for dry-cured ham slices, containing natural antioxidants, was developed; it consists of a reusable polymer tray sealed with disposable polymer film. The life cycle of the packaging was assessed to compare its environmental impacts with a reference disposable packaging system already in use. The life cycle assessment was performed in accordance with the ISO 14040-14044 series; the system was model using the Gabi software and the ILCD PEF method was used to evaluate the impacts. The functional unit chosen was to pack 1000 batches of 4 slices of dry-cured ham in France. Three packaging scenarios were compared: a reference disposable packaging system, incinerated at end of life; the partially reusable packaging, recycled at end of life and the same partially reusable packaging, incinerated at end of life. The study of the relative impacts of each scenario revealed that for the reference packaging, the production of the tray was the highest-impact stage. With the reusable packaging, the highest-impact stages were the thermosealing process and the production of the trays and films. A significant reduction in all impacts was observed with the use of the reusable packaging. Sensitivity analysis was carried out to study the influence of the breakage rate of the tray during reuse and the number of reuse cycles of the tray. Except for freshwater resource depletion, the reusable packaging had lower environmental impacts even with a high tray breakage rate or a low number of reuses. This paper demonstrates the interest of this reusable and recyclable food contact packaging to lower the environmental footprint of packaging; the reuse and recycling stages now need to be tested in real situations for the packaging prototype to confirm the feasibility of the reuse process.
Citation: Joana Beigbeder, Ahmed Allal, Nathalie Robert. Ex-ante life cycle assessment of a partially reusable packaging system for dry-cured ham slices[J]. Clean Technologies and Recycling, 2022, 2(3): 119-135. doi: 10.3934/ctr.2022007
[1] | Dieuwertje L. Schrijvers, Philippe Loubet, Guido W. Sonnemann . The influence of market factors on the potential environmental benefits of the recycling of rare earth elements. Clean Technologies and Recycling, 2022, 2(1): 64-79. doi: 10.3934/ctr.2022004 |
[2] | Nighat Afroz Chowdhury, Apurba Kumar Saha, Gwendolyn Bailey, Andrea Di Maria, Dieuwertje Schrijvers, Hongyue Jin . Life cycle assessment of clean technologies and recycling. Clean Technologies and Recycling, 2023, 3(1): 1-3. doi: 10.3934/ctr.2023001 |
[3] | Susana J. Castillo, Anna Hayes, Greg Colvin, Barrett G. Potter, Rongguang Liang, Krishna Muralidharan . Characterization of recycled Inconel 718 metal powder for assessing its reusability in the laser powder bed fusion process. Clean Technologies and Recycling, 2022, 2(1): 32-46. doi: 10.3934/ctr.2022002 |
[4] | Carly A. Fletcher . Is the consumer experience creating barriers for the effective uptake and disposal of bioplastics?. Clean Technologies and Recycling, 2022, 2(4): 308-320. doi: 10.3934/ctr.2022016 |
[5] | Shadia Moazzem, Delwyn Jones, Mathilde Vlieg, Direshni Naiker . Inaccurate polyester textile environmental product declarations. Clean Technologies and Recycling, 2022, 2(1): 47-63. doi: 10.3934/ctr.2022003 |
[6] | Wilson U. Eze, Toyese Oyegoke, Jonathan D. Gaiya, Reginald Umunakwe, David I. Onyemachi . Review of personal protective equipment and their associated wastes, life-cycle and effective management during the Covid-19 pandemic in developing nations. Clean Technologies and Recycling, 2022, 2(1): 1-31. doi: 10.3934/ctr.2022001 |
[7] | Andrea Di Maria, Annie Levasseur, Karel Van Acker . Assessing the long term effects on climate change of metallurgical slags valorization as construction material: a comparison between static and dynamic global warming impacts. Clean Technologies and Recycling, 2021, 1(1): 88-111. doi: 10.3934/ctr.2021005 |
[8] | Majid Alipanah, Apurba Kumar Saha, Ehsan Vahidi, Hongyue Jin . Value recovery from spent lithium-ion batteries: A review on technologies, environmental impacts, economics, and supply chain. Clean Technologies and Recycling, 2021, 1(2): 152-184. doi: 10.3934/ctr.2021008 |
[9] | Wilson Uzochukwu Eze, Reginald Umunakwe, Henry Chinedu Obasi, Michael Ifeanyichukwu Ugbaja, Cosmas Chinedu Uche, Innocent Chimezie Madufor . Plastics waste management: A review of pyrolysis technology. Clean Technologies and Recycling, 2021, 1(1): 50-69. doi: 10.3934/ctr.2021003 |
[10] | Javier Guillén-Mallette, Irma Flores-Cerón, Soledad Cecilia Pech-Cohuo, Edgar José López-Naranjo, Carlos Vidal Cupul-Manzano, Alex Valadez-González, Ricardo Herbé Cruz-Estrada . Effect of moisture absorption-desorption cycles, UV irradiation and coupling agent on the mechanical performance of pinewood waste/polyethylene composites. Clean Technologies and Recycling, 2023, 3(3): 193-220. doi: 10.3934/ctr.2023013 |
To limit the huge damage caused by plastic pollution, major changes need to be made in the food and beverage packaging sector. In this context, a new packaging system for dry-cured ham slices, containing natural antioxidants, was developed; it consists of a reusable polymer tray sealed with disposable polymer film. The life cycle of the packaging was assessed to compare its environmental impacts with a reference disposable packaging system already in use. The life cycle assessment was performed in accordance with the ISO 14040-14044 series; the system was model using the Gabi software and the ILCD PEF method was used to evaluate the impacts. The functional unit chosen was to pack 1000 batches of 4 slices of dry-cured ham in France. Three packaging scenarios were compared: a reference disposable packaging system, incinerated at end of life; the partially reusable packaging, recycled at end of life and the same partially reusable packaging, incinerated at end of life. The study of the relative impacts of each scenario revealed that for the reference packaging, the production of the tray was the highest-impact stage. With the reusable packaging, the highest-impact stages were the thermosealing process and the production of the trays and films. A significant reduction in all impacts was observed with the use of the reusable packaging. Sensitivity analysis was carried out to study the influence of the breakage rate of the tray during reuse and the number of reuse cycles of the tray. Except for freshwater resource depletion, the reusable packaging had lower environmental impacts even with a high tray breakage rate or a low number of reuses. This paper demonstrates the interest of this reusable and recyclable food contact packaging to lower the environmental footprint of packaging; the reuse and recycling stages now need to be tested in real situations for the packaging prototype to confirm the feasibility of the reuse process.
Plastics are the cause of huge quantities of waste pollution all around the world [1,2]. Plastics from food and drink packaging are predominant in litter [3,4]. Recently, the planetary boundary for novel entities was proven to be exceeded [5], the authors pointed out that plastic pollution is a critical concern. Indeed, the plastic crisis causes various negative environmental effects such as contamination by hazardous substances [6,7], lethal effects on fauna [8,9], ecosystem water pollution [10] or microplastic and nanoplastic contamination [11,12].
To face this environmental burden, the use of plastic must be rethought, especially in the field of food and beverage packaging. Usually, when the life cycle of a food product is examined, packaging is at the origin of the main environmental impacts, as for wine [13,14], tomato puree [15] and beverages [16] for instance. Several strategies are emerging to improve food and beverage packaging: buying in bulk [17], the use of biodegradable materials [18], reusable and returnable containers [19,20]. Buying bulk products with reusable packaging and returnable containers tends to be the most environmentally friendly option, preventing waste generation in a circular economy approach, in accordance with the European Union waste hierarchy [21]. Moreover, since 2018, the European Union has required a considerable reduction in packaging waste in Europe; it fixed a target of 70% of packaging waste to be recycled in 2030 (55% for plastic packaging) [22]. It is worth noting that consumer behaviour is a key factor in plastic packaging waste reduction [23] and that convenience is essential to reach a wide range of consumers. Using recycled plastic as food contact material is a sensitive issue as the migration of hazardous substances into food must not be increased with the use of recycled materials [24]. Ecodesign is a key point for achieving European Union targets. Thus, in 2018, the European Commission created the Circular Plastics Alliance which federates public and private stakeholders to enhance the recycling of plastic by working on product designs, sorting and the quality of recycled plastics [25].
Life cycle analysis (LCA) is a standardized methodology (ISO 14040:2006/ISO 14044:2006 [26,27]) developed to assess the environmental impacts of a product or system. Improvements in packaging systems have already been studied by LCA, especially in the fields of food and beverage packaging. In most studies, the use of reusable food or beverage packaging leads to better environmental profiles [28,29,30,31]. However, in some cases, washing packages before reuse inverses the trend, and leads to higher impacts for the reusable option. For instance, Tamburini et al. [32] compared the environmental impacts of one-way polyethylene terephthalate (PET) bottles, one-way polylactic acid bottles and aluminium refillable bottles by LCA; the results showed that the daily washing stage of the aluminium reusable bottle increased its environmental footprint compared to PET bottles. A complete review of LCA and beverage packaging has shown that the definition of the functional unit is a critical point for tackling packaging within a circular economy [33]. The number of reuses also appeared as a key aspect [34], some studies evaluated the critical number of reuses needed to outweigh the impact of a disposable packaging (break-even point), this number varied between 18 and 208 times, depending on the nature of the packaging studied [35,36,37]. No LCA about the reuse of food packaging trays was found in the literature.
In this context, this paper presents an ex-ante life cycle analysis of the use of a partially reusable packaging system for dry-cured ham slices, made up of a tray and a transparent film. The packaging was developed during an Interreg project gathering together academic researchers and dry-curing industry professionals, represented by the company Pyragena. The goals of the project were to develop a healthier but also more environmentally friendly packaging design containing natural antioxidants, to test the food packaging's properties and durability and to evaluate its environmental footprint through LCA. The packaging is called "partially reusable" as only the tray is reusable. The 'ex-ante LCA' term refers to the LCA of the scaling up of an emerging product with the most likely scenario, as defined by Buyle et al. [38]. The goal is to evaluate the environmental benefits of the reusable packaging before its implementation. The new formulation of the reusable packaging was developed with natural oxidants, used as stabilizers for the polymers, preventing oxidation and ensuring the shelf life of the dry-cured ham [39], the formulation of the material was patented. Tests were performed at lab-scale to validate the food packaging's properties and the reuse of the packages [40]. The antioxidants selected were vitamin E and tannins, at concentrations lower than 0.1 wt%. As the collection, washing and recycling management of the reusable trays have not been developed yet; those stages were modelled by means of literature data. Results were compared to a standard disposable packaging already used in the dry-cured ham market.
Life cycle assessment was performed following the ISO 14040-14044 framework, which consists of four main steps: goal and definition, inventory analysis, impact assessment and interpretation. The studied products were modelled on the Gabi ts software from SpheraTM (version 9.5.2.49) and using the ecoinvent 3.5 database. Environmental impacts were evaluated using the product environmental footprint method (PEF v1.9), which is appropriate to the European context, provides a wide range of mid-point impacts and is recommended by International Life Cycle Data (ILCD), a European Union initiative to provide guidance for LCA. 14 environmental impacts provided by the PEF method were selected to compare the systems. System expansion was used to evaluate the impacts avoided due to electricity or recycled plastic production in end-of-life treatments.
The goal of the study is to assess the environmental impacts of partially reusable food packages and to compare them to reference disposable packages already in use. The food packaging is studied dedicated to dry-cured ham slices and produced in the south-west of France by the company Pyragena. The functional unit chosen is "to pack 1000 batches of 4 dry-cured ham slices (100 g) in France". All the studied packages conserve the dry-cured ham for 3 months and also enable the consumer to see the food product. They consist of a transparent upper film and a black tray, both made of polymers. After depositing the dry-cured ham on the tray, the film is sealed on the tray by thermosealing.
The studied systems are presented in Figure 1. A first scenario (DPack) is dedicated to a disposable package already used by the dry-cured ham industry. The transparent upper film of the DPack is made of a layer of multiextruded polyethylene (PE), polyamide, ethylene-vinyl alcohol copolymer polyamide and polyethylene film, with a thickness of 40 µm. The bilayer tray is made of PET and PE.
In the alternative scenario, partially reusable packages (pRPack) are used, with reusable trays and disposable films. Package dimensions and masses are identical to those of the first scenario, only the materials used change. The tray of the pRPack is made of polypropylene (PP) with natural antioxidants (vitamin E, tannins), while the upper film is made of PE with the same natural antioxidants. Physicochemical analysis proved that the materials used in the pRPack trays can withstand 100 washing cycles without deterioration. Concerning the additional reusable packaging needed to serve the reusable system, a simplified case is studied: the stocking of packaging for normal functioning of the reusable system is not considered.
For both packages, the masses of the tray and upper film layer are 15 g and 1 g respectively, the dimensions are 14 cm by 24 cm.
The reference flows for the functional unit are presented in the last column of Table 1. For the first DPack scenario, 1000 packages will be used while for the pRPack scenario, 10 packages will be reused 100 times, discontinuously. Packages broken during thermosealing are considered for both scenarios (6.7%); for the pRPack scenario, the trays lost and broken during reuse are included (5%). Masses are determined by multiplying the mass of one package by the number of packages needed, plus the mass lost during thermosealing, plus the mass of lost and broken trays for the pRPack scenario.
Scenario | Packaging | Material | Mass | Reference flow |
DPack | Tray | 90% PET, 10% PE | 15 g | 16.00 kg |
Film | Multilayer polymers film | 1 g | 1.07 kg | |
pRPack | Tray | PP + Natural antioxidants | 15 g | 1.89 kg |
Film | PE + Natural antioxidants | 1 g | 1.07 kg |
To distinguish the influence of the end-of-life stage, fictional scenarios were considered, with 100% incineration or recycling for the trays. All plastic waste generated during the DPack scenario is incinerated with energy recovery. Two end-of-life options are considered for the pRPack scenario. First, all broken or used trays are assumed to be recycled (sub-scenario pRPack-r) and the upper-layer films are incinerated with energy recovery. In a second sub-scenario, pRPack-i, all broken and lost trays but also packaging waste produced during the life cycle are incinerated with energy recovery.
The whole life cycle is considered, from cradle to grave, i.e., from the production of the raw materials to the end of life of the packaging (Figure 1). After production of the raw materials, films and trays are produced at the packaging production sites and then sent to the dry-cured ham factory. The thermosealing step closes the packaging by sealing the upper film on the tray, once the dry-cured ham slices have been placed. Waste packaging produced during thermosealing is collected and incinerated or recycled. Then, the dry-cured ham packaging is sent to the distribution site by lorry, transported to the consumer's home by car, collected as waste from the consumer's house, sent to the waste treatment site and then sent to the final treatment site (incineration plant or recycling site or dry-cured ham factory for reuse).
Confidential data about materials used and thermosealing process were provided by researchers and industrials partners of the Interreg Project Foodyplast (University of Pau, Pyragena). For the processes of extrusion and incineration, data from the Gabi database were used, whereas all the other data for the processes were from ecoinvent (raw materials production, transport, electricity…).
For the DPack, the multilayer polymer film was assimilated to a bilayer film with PET and PE, containing 90 wt% of PET and 10% of PE. Packaging additives, such as natural antioxidants, were not considered, as their concentrations are negligible (0.1 wt%). 6.7% of packed trays are lost during the setting up of the thermosealing machine (data from Pyragena, producer of dry-cured ham). The use of the machine and the building were taken into consideration for the thermosealing stage. The share of machine and building used were determined from the dimensions of the machine, time of use for the functional unit, building and machine lifetimes. At each reuse cycle of the pRPack tray, we assumed that 5% of the trays would be broken or lost (hypothetical data) and therefore not collected. This low ratio of broken and lost trays represents an idealist case, where the collect is perfectly managed to limit the losses. Trays were assumed to be washed before reuse in a washer with hot water and sodium hydroxide, by means of a process already used for PET bottles and plastic scraps [41,42]: 1.4 × 10−3 kg of sodium hydroxide and 1.43 kg of water were used per kg of trays washed. The use phase was assumed to be negligible. At end of life, waste is collected by lorry. For incineration, only electricity recovery is considered, the amount of electricity produced was calculated with the lower heating values of the polymers and with an electricity generation efficiency of 13% [43]. When trays are recycled after reuse, they follow a standard treatment with stages of shredding (electrical consumption of 158 MJ/t), washing (same data as tray washing) and extrusion. The default PEF approach was used to calculate the credits du to PP recycling (A = 0.5, Qs/Qp = 0.9) [44]. The A factor defines the allocation between the recycling stage and the end of life, while the Qs/Qp factor represents the quality of the recycled plastic. Thus, in that case, 45% of the credits from recycling PP were attributed to the system.
The transport distances are presented in Table 2. All the intermediate transport for raw material and package production was provided by Pyragena, a partner in the Foodyplast project, representing professionals in the dry-cured ham industry. Other distances were estimated based on the literature, with the hypothesis of regional use of the packages. The reusable trays were assumed to be collected like standard packaging, then separated at the waste treatment site and sent to the dry-cured ham production site (250 km away), where they are washed before reusing. Trays lost during the process separation are sent for incineration or recycling.
DPack | pRPack | |
Distance from polymer production to package manufacturing site | 280 km | 570 km |
Distance from package manufacturing site to dry-cured ham factory | 752 km | 220 km |
Delivery | 250 km | 250 km |
Consumer journey | 5 km | 5 km |
Waste collection | 50 km | 50 km |
Distance to the final waste disposal site | 100 km | 100 km |
Distance for return of reusable trays | - | 250 km |
Figure 2 presents the relative contributions of the main stages of the DPack scenario. For all the impacts studied, production of the trays is the highest-impact step with ratios between 47% and 88%. Most of these impacts come from the PET and PE production stages. With around 16 kg of polymers needed, itis the largest material flow in the system. For climate change impact, incineration is the second highest impact stage; this is mainly due to the emission of CO2 during incineration. For 8 of the other impacts (ozone depletion, human toxicity with and without cancer, freshwater eutrophication, freshwater ecotoxicity, resource depletion of water and materials, primary energy demand), it is the thermosealing stage which is the second highest impact stage. The electricity consumption needed for this stage is the main contributor to the impacts, impacts from the use of the machine and the building during thermosealing are negligible. For the other impacts, film production, thermosealing, packaging transport and incineration are approximately at the same level. Other transport stages are very low with impacts around 1% (waste collection, consumer journey, delivery). The electricity produced during incineration leads to notable credits for ozone depletion, resource depletion water and primary energy demand (between 11% and 23%). For the remaining impact categories, avoided impacts are lower than 7%.
The relative share of the different stages of the pRPAck-r and pRPack-i scenarios are presented in Figures 3 and 4 respectively. For most of the studied impacts, the stage thermosealing has the highest impact. Tray and film production both also have notable impacts, with ratios proportional to the mass of the material flows, slightly higher for the tray. For 5 of the studied impacts (climate change, photochemical ozone formation, acidification, terrestrial eutrophication, marine eutrophication), the total contribution of tray and film production is between 50% and 65%. As for the DPack scenario, incineration contributes around 20% for the climate change impact, due to emissions in the air; for all the other impacts, this stage is negligible. Avoided impacts are lower than 10% for all impacts; they are due to the incineration of the films and the recycling of the tray after reuse. Using a lower substitution factor for the recycled PP would lead to a reduction in the avoided impacts, and therefore an increase in the total scores of the pRPack-r option. The reuse and recycling stages make low contributions (<10%). For the transport stages, delivery makes a minor contribution, around 3–5%, while waste collection and consumer driving are negligible.
When incineration of the tray is chosen after reuse (Figure 4), thermosealing is still the highest-impact stage for 7 of the studied impacts (ozone depletion, human toxicity with and without cancer, freshwater ecotoxicity, water and materials depletion, primary energy demand). The total contributions of the trays and films production are predominant for 5 of the impacts (climate change, particulate matter, photochemical ozone formation, acidification, marine eutrophication). Incineration at end of life leads to avoided impacts for all the impacts considered. The reuse stage has notable impacts for the human toxicity, non-cancer impact and the marine eutrophication impact, due to the washing of the tray. For the other transport stages, delivery makes a minor contribution, around 3–5%, while waste collection and consumer journeys are negligible.
As expected, the production of the trays is at the origin of the main impacts for the standard packaging. Changing the raw materials used or the usage of the tray is thus a good option to lower the environmental impacts of the packaging. Indeed, when using a reusable tray, the relative share of the various stages is completely modified. The main contributors become the thermosealing stage and the production of all the packaging (trays + films).
The total scores of each impact for the three scenarios are compared in Figure 5, relative to the standard packaging DPack. Net values are presented in Table 3. For all the impacts, significant reductions can be observed; the scores of the pRPack scenarios are between 14% and 52% of the DPack option. As seen above, the tray production stage is the main contributor of the DPack scenario (Figure 2); reusable trays greatly reduce the quantities of raw materials required (Table 1) and lead to significantly lower impacts. The materials used also have a notable influence. Figure 6 compares the environmental impacts of only the production stage of one tray (raw materials production, transport, injection), relative to DPack tray production. Shifting from PET/PE to PP reduces some of the studied impacts; pRPack tray production has 7 impact scores lower than 50% compared to the DPack tray production scores. The impacts of collecting and washing the used trays do not cancel out the benefits of reuse. Comparing the two end-of-life options of the reused trays, for most of the impacts the results are quite similar. A difference above 5% can be observed for the impacts on climate change, ozone depletion, marine eutrophication and water resource depletion. For the climate change and the marine eutrophication impacts, incineration leads to higher impacts. For the two other impacts (ozone depletion, water resource depletion), the inverse phenomenon is observed, the recycling option has a higher impact than the incineration one, due to less impacts being avoided. The relative impacts when the trays are incinerated or recycled after being reused are quite similar. The changes are mainly observed for avoided impacts (Figures 3 and 4).
DPack | pRPack-i | pRPack-r | |
Climate change, excl biogenic carbon, kg CO2 eq. | 9.40E+01 | 2.13E+01 | 1.36E+01 |
Ozone depletion, kg CFC-11 eq. | 3.82E−06 | 1.52E−06 | 1.94E−06 |
Human toxicity, non-cancer effects, CTUh | 1.31E−05 | 2.66E−06 | 2.47E−06 |
Human toxicity, cancer effects, CTUh | 3.32E−06 | 7.24E−07 | 7.70E−07 |
Particulate matter/respiratory inorganics, kg PM2.5 eq. | 3.02E−02 | 4.15E−03 | 4.69E−03 |
Photochemical ozone formation, human health, kg NMVOC eq. | 1.75E−01 | 3.87E−02 | 3.79E−02 |
Acidification, Mole of H+ eq. | 2.54E−01 | 4.82E−02 | 5.15E−02 |
Terrestrial eutrophication, Mole of N eq. | 5.07E−01 | 1.08E−01 | 1.13E−01 |
Freshwater eutrophication, kg P eq. | 1.38E−02 | 2.16E−03 | 2.80E−03 |
Freshwater ecotoxicity, kg Sb eq. | 4.60E−02 | 1.39E−02 | 1.00E−02 |
Resource depletion, mineral, fossils and renewables, kg Sb eq. | 3.99E+02 | 7.30E+01 | 8.75E+01 |
Resource depletion, water, m³ eq. | 2.45E−03 | 4.75E−04 | 5.29E−04 |
Primary energy demand, MJ | 5.57E−01 | 2.17E−01 | 2.89E−01 |
Sensitivity analysis was performed on two parameters: the number of tray reuse cycles and the rate of broken trays at each reuse cycle, with a recycling treatment of the tray at the end of life. The results are presented in Figures 7 and 8, in percentages, compared to the DPack scenario.
Concerning the influence of the number of reuse cycles (Figure 7), when the trays are reused 50 times instead of 100 times, a low variation is observed for all the impacts, between 2% and 8%. When trays are only reused 10 times, a higher increase is observed compared to reusing them 100 times. However, except for water resource depletion, all the scores stay below the reference disposable pack DPack.
For the influence of the broken tray rate, the trend is similar (Figure 8). When 10% of the trays are broken during reuse, scores are similar to the 5% scenario. Whereas, when 50% are broken, a higher increase occurs, with scores still lower than the DPack option, except for water resource depletion.
When more trays are broken or when trays are less reused, the masses of polymers needed for the p-RPack option increase. The production of polymers and extrusion stages are responsible for the notable increase in some impacts with 10 cycles of reuse or 50% of broken trays.
The environmental impacts of two packaging systems for dry-cured ham slices were assessed by LCA. A disposable package made of a multilayer polymeric film sealed on a PET/PE tray was compared with a prototype of a partially reusable and recyclable package, made of a reusable tray in PP sealed by a PE film. The results show that the highest-impact stage for the disposable packaging was the production of the tray. This confirmed that improvement of tray design is a good option for improving the environmental footprint of the packaging. For the partially reusable packaging, impacts mainly came from four stages: thermosealing, production of the tray and the films, reuse of the tray. The comparison of the total scores for the three scenarios revealed that the use of partially reusable packaging led to a significant reduction in all the impacts studied, despite the reuse stages (collection, washing). The different end-of-life treatment slightly influenced the total scores of the partially reusable packaging. Sensitivity analysis was performed on two parameters: the rate of broken trays during reuse and the number of reuse cycles. Even with a high broken-tray rate, which would be more representative of a realistic case, and a low number of reuse cycles, the partially reusable tray had lower environmental impacts than the disposable one, except for the water resource depletion impact. This study proves that reusing the tray of packaging for dry-cured ham slices leads to significant environmental benefits. However, before implementation, more tests are needed, especially to optimize the sorting stage and the feasibility of the collect. Specific collection by dry-cured ham distributors could simplify the logistic chain and the sorting. Social benefits could also be assessed through social life-cycle assessment to evaluate the job creation potential due to reusable packaging systems.
The authors thank the ERDF Interreg Poctefa for financial support (EFA099/15 acronym FOODYPLAST).
The authors declare that there is no conflict of interest.
[1] | Horton AA (2022) Plastic pollution: When do we know enough? J Hazard Mater 422: 126885. |
[2] |
Iroegbu AOC, Ray SS, Mbarane V, et al. (2021) Plastic Pollution: A Perspective on Matters Arising: Challenges and Opportunities. ACS Omega 6: 19343-19355. https://doi.org/10.1016/j.jhazmat.2021.126885 doi: 10.1016/j.jhazmat.2021.126885
![]() |
[3] | Ellen MacArthur Foundation, The New Plastics Economy—Rethinking the future of plastics, 2016. Available form: https://ellenmacarthurfoundation.org/the-new-plastics-economy-rethinking-the-future-of-plastics-and-catalysing. https://doi.org/10.1021/acsomega.1c02760. |
[4] |
Phelan AA, Meissner K, Humphrey J, et al. (2022) Plastic pollution and packaging: Corporate commitments and actions from the food and beverage sector. J Clean Prod 331: 129827. https://doi.org/10.1016/j.jclepro.2021.129827 doi: 10.1016/j.jclepro.2021.129827
![]() |
[5] |
Persson L, Carney Almroth BM, Collins CD, et al. (2022) Outside the safe operating space of the planetary boundary for novel entities. Environ Sci Technol 56: 1510-1521. https://doi.org/10.1021/acs.est.1c04158 doi: 10.1021/acs.est.1c04158
![]() |
[6] | Karlsson T, Brosché S, Alidoust M, et al. (2021) Plastic pellets found on beaches all over the world contain toxic chemicals. Available form: https://ipen.org/documents/plastic-pellets-found-beaches-all-over-world-contain-toxic-chemicals. |
[7] |
Wiesinger H, Wang Z, Hellweg S (2021) Deep dive into plastic monomers, additives, and processing aids. Environ Sci Technol 55: 9339-9351. https://doi.org/10.1021/acs.est.1c00976 doi: 10.1021/acs.est.1c00976
![]() |
[8] |
Senko JF, Nelms SE, Reavis JL, et al. (2020) Understanding individual and population-level effects of plastic pollution on marine megafauna. Endanger Species Res 43: 234-252. https://doi.org/10.3354/esr01064 doi: 10.3354/esr01064
![]() |
[9] |
Gall SC, Thompson RC (2015) The impact of debris on marine life. Mar Pollut Bull 92: 170-179. https://doi.org/10.1016/j.marpolbul.2014.12.041 doi: 10.1016/j.marpolbul.2014.12.041
![]() |
[10] |
Kasavan S, Yusoff S, Rahmat Fakri MF, et al. (2021) Plastic pollution in water ecosystems: A bibliometric analysis from 2000 to 2020. J Clean Prod 313: 127946. https://doi.org/10.1016/j.jclepro.2021.127946 doi: 10.1016/j.jclepro.2021.127946
![]() |
[11] |
Kurniawan SB, Said NSM, Imron MF, et al. (2021) Microplastic pollution in the environment: Insights into emerging sources and potential threats. Environ Technol Innov 23: 101790. https://doi.org/10.1016/j.eti.2021.101790 doi: 10.1016/j.eti.2021.101790
![]() |
[12] |
Jaiswal KK, Dutta S, Banerjee I, et al. (2022) Impact of aquatic microplastics and nanoplastics pollution on ecological systems and sustainable remediation strategies of biodegradation and photodegradation. Sci Total Environ 806: 151358. https://doi.org/10.1016/j.scitotenv.2021.151358 doi: 10.1016/j.scitotenv.2021.151358
![]() |
[13] |
Fusi A, Guidetti R, Benedetto G (2014) Delving into the environmental aspect of a Sardinian white wine: From partial to total life cycle assessment. Sci Total Environ 472: 989-1000. https://doi.org/10.1016/j.scitotenv.2013.11.148 doi: 10.1016/j.scitotenv.2013.11.148
![]() |
[14] |
Gazulla C, Raugei M, Fullana-i-Palmer P (2010) Taking a life cycle look at crianza wine production in Spain: Where are the bottlenecks? Int J Life Cycle Assess 15: 330-337. https://doi.org/10.1007/s11367-010-0173-6 doi: 10.1007/s11367-010-0173-6
![]() |
[15] |
Manfredi M, Vignali G (2014) Life cycle assessment of a packaged tomato puree: A comparison of environmental impacts produced by different life cycle phases. J Clean Prod 73: 275-284. https://doi.org/10.1016/j.jclepro.2013.10.010 doi: 10.1016/j.jclepro.2013.10.010
![]() |
[16] |
Pasqualino J, Meneses M, Castells F (2011) The carbon footprint and energy consumption of beverage packaging selection and disposal. J Food Eng 103: 357-365. https://doi.org/10.1016/j.jfoodeng.2010.11.005 doi: 10.1016/j.jfoodeng.2010.11.005
![]() |
[17] |
Louis D, Lombart C, Durif F (2021) Packaging-free products: A lever of proximity and loyalty between consumers and grocery stores. J Retail Consum Serv 60: 102499. https://doi.org/10.1016/j.jretconser.2021.102499 doi: 10.1016/j.jretconser.2021.102499
![]() |
[18] |
Flury M, Narayan R (2021) Biodegradable plastic as an integral part of the solution to plastic waste pollution of the environment. Curr Opin Green Sustain Chem 30: 100490. https://doi.org/10.1016/j.cogsc.2021.100490 doi: 10.1016/j.cogsc.2021.100490
![]() |
[19] |
Silva DAL, Renó GWS, Sevegnani G, et al. (2013) Comparison of disposable and returnable packaging: A case study of reverse logistics in Brazil. J Clean Prod 47: 377-387. https://doi.org/10.1016/j.jclepro.2012.07.057 doi: 10.1016/j.jclepro.2012.07.057
![]() |
[20] |
Coelho PM, Corona B, ten Klooster R, et al. (2020) Sustainability of reusable packaging-Current situation and trends. Resour Conserv Recycl X 6: 100037. https://doi.org/10.1016/j.rcrx.2020.100037 doi: 10.1016/j.rcrx.2020.100037
![]() |
[21] | European Union, Directive 2006/12/EC of the European parliament and of the council of 5 April 2006 on waste. OJEU, 2006. Available form: https://eur-lex.europa.eu/legal-content/EN/TXT/PDF/?uri=CELEX:32006L0012&from=RO. |
[22] | The European Parliament and the Council of the European Union, Directive (EU) 2018/852 of the European Parliament and of the Council of 30 May 2018 amending Directive 94/62/EC on packaging and packaging waste, 2018. Available form: http://data.europa.eu/eli/dir/2018/852/oj. |
[23] |
Fogt Jacobsen L, Pedersen S, Thøgersen J (2022) Drivers of and barriers to consumers' plastic packaging waste avoidance and recycling—A systematic literature review. Waste Manage 141: 63-78. https://doi.org/10.1016/j.wasman.2022.01.021 doi: 10.1016/j.wasman.2022.01.021
![]() |
[24] |
Hesser F (2015) Environmental advantage by choice: Ex-ante LCA for a new Kraft pulp fibre reinforced polypropylene composite in comparison to reference materials. Compos Part B-Eng 79: 197-203. https://doi.org/10.1016/j.compositesb.2015.04.038 doi: 10.1016/j.compositesb.2015.04.038
![]() |
[25] | European Commission, Circular Plastics Alliance, 2022. Available from: https://ec.europa.eu/growth/industry/strategy/industrial-alliances/circular-plastics-alliance_en. |
[26] | ISO 14040: 2006(en): Environmental management—life cycle assessment—Principles and framework. The International Organization for Standardization, 2006. Available from: https://www.iso.org/obp/ui#iso:std:iso:14040:ed-2:v1:en. |
[27] | ISO 14044: 2006: Environmental management—Life cycle assessment—Requirements and guidelines. The International Organization for Standardization, 2006. Available from: https://www.iso.org/obp/ui/#iso:std:iso:14044:ed-1:v1:en. |
[28] | Camps-Posino L, Batlle-Bayer L, Bala A, et al. (2021) Potential climate benefits of reusable packaging in food delivery services. A Chinese case study. Sci Total Environ 794: 148570. https://doi.org/10.1016/j.scitotenv.2021.148570 |
[29] |
Postacchini L, Mazzuto G, Paciarotti C, et al. (2018) Reuse of honey jars for healthier bees: Developing a sustainable honey jars supply chain through the use of LCA. J Clean Prod 177: 573-588. https://doi.org/10.1016/j.jclepro.2017.12.240 doi: 10.1016/j.jclepro.2017.12.240
![]() |
[30] |
Accorsi R, Cascini A, Cholette S, et al. (2014) Economic and environmental assessment of reusable plastic containers: A food catering supply chain case study. Int J Prod Econ 152: 88-101. https://doi.org/10.1016/j.ijpe.2013.12.014 doi: 10.1016/j.ijpe.2013.12.014
![]() |
[31] |
Arunan I, Crawford RH (2021) Greenhouse gas emissions associated with food packaging for online food delivery services in Australia. Resour Conserv Recy 168: 105299. https://doi.org/10.1016/j.resconrec.2020.105299 doi: 10.1016/j.resconrec.2020.105299
![]() |
[32] |
Tamburini E, Costa S, Summa D, et al. (2021) Plastic (PET) vs bioplastic (PLA) or refillable aluminium bottles—What is the most sustainable choice for drinking water? A life-cycle (LCA) analysis. Environ Res 196: 110974. https://doi.org/10.1016/j.envres.2021.110974 doi: 10.1016/j.envres.2021.110974
![]() |
[33] |
Sazdovski I, Bala A, Fullana-i-Palmer P (2021) Linking LCA literature with circular economy value creation: A review on beverage packaging. Sci Total Environ 771: 145322. https://doi.org/10.1016/j.scitotenv.2021.145322 doi: 10.1016/j.scitotenv.2021.145322
![]() |
[34] | Ligthart TN, Ansems AMM (2007) Single use cups or reusable (coffee) drinking systems: an environmental comparison. Available form: http://www.bekerrecycling.nl/nl/file/20110104172024/3/tno-eng.pdf. |
[35] |
Changwichan K, Gheewala SH (2020) Choice of materials for takeaway beverage cups towards a circular economy. Sustain Prod Consum 22: 34-44. https://doi.org/10.1016/j.spc.2020.02.004 doi: 10.1016/j.spc.2020.02.004
![]() |
[36] |
Gallego-Schmid A, Mendoza JMF, Azapagic A (2019) Environmental impacts of takeaway food containers. J Clean Prod 211: 417-427. https://doi.org/10.1016/j.jclepro.2018.11.220 doi: 10.1016/j.jclepro.2018.11.220
![]() |
[37] |
Cottafava D, Costamagna M, Baricco M, et al. (2021) Assessment of the environmental break-even point for deposit return systems through an LCA analysis of single-use and reusable cups. Sustain Prod Consum 27: 228-241. https://doi.org/10.1016/j.spc.2020.11.002 doi: 10.1016/j.spc.2020.11.002
![]() |
[38] |
Buyle M, Audenaert A, Billen P, et al. (2019) The future of ex-ante LCA? Lessons learned and practical recommendations. Sustain 11: 5456. https://doi.org/10.3390/su11195456 doi: 10.3390/su11195456
![]() |
[39] | Issart A (2019) Potential of natural antioxidants for the stabilization of polymers for food packaging and the development of methods for evaluating their migration[PhD's thesis]. Université de Pau et des Pays de l'Adour, France. |
[40] | Allal AM, Issart A (2021) Patent material for food packaging and method for the preparation thereof. European Patent Office, WO/2020/260829. Available form: https://patentscope.wipo.int/search/en/detail.jsf?docId=WO2020260829. |
[41] | Shonfield P (2008) LCA of management options for mixed waste plastics. Available form: https://silo.tips/download/final-report-lca-of-management-options-for-mixed-waste-plastics. |
[42] |
Krehula LK, Siročić AP, Dukić M, et al. (2012) Cleaning efficiency of poly (ethylene terephthalate) washing procedure in recycling process. J Elastom Plast 45: 429-444. https://doi.org/10.1177/0095244312457798 doi: 10.1177/0095244312457798
![]() |
[43] | Doka G (2003) Life cycle inventories of waste treatment services. Available form: https://www.doka.ch/13_I_WasteTreatmentGeneral.pdf. |
[44] | European Commission, Product environmental footprint category rules guidance—version 6.3, 2018. Available form: https://ec.europa.eu/environment/eussd/smgp/pdf/PEFCR_guidance_v6.3.pdf. |
1. | Nighat Afroz Chowdhury, Apurba Kumar Saha, Gwendolyn Bailey, Andrea Di Maria, Dieuwertje Schrijvers, Hongyue Jin, Life cycle assessment of clean technologies and recycling, 2023, 3, 2770-4580, 1, 10.3934/ctr.2023001 | |
2. | Minh-Hieu Le, Wen-Min Lu, Jui-Chen Chang, Recycling E-Waste and the Sustainable Economy: A Bibliometric Exploration, 2023, 15, 2071-1050, 16108, 10.3390/su152216108 |
Scenario | Packaging | Material | Mass | Reference flow |
DPack | Tray | 90% PET, 10% PE | 15 g | 16.00 kg |
Film | Multilayer polymers film | 1 g | 1.07 kg | |
pRPack | Tray | PP + Natural antioxidants | 15 g | 1.89 kg |
Film | PE + Natural antioxidants | 1 g | 1.07 kg |
DPack | pRPack | |
Distance from polymer production to package manufacturing site | 280 km | 570 km |
Distance from package manufacturing site to dry-cured ham factory | 752 km | 220 km |
Delivery | 250 km | 250 km |
Consumer journey | 5 km | 5 km |
Waste collection | 50 km | 50 km |
Distance to the final waste disposal site | 100 km | 100 km |
Distance for return of reusable trays | - | 250 km |
DPack | pRPack-i | pRPack-r | |
Climate change, excl biogenic carbon, kg CO2 eq. | 9.40E+01 | 2.13E+01 | 1.36E+01 |
Ozone depletion, kg CFC-11 eq. | 3.82E−06 | 1.52E−06 | 1.94E−06 |
Human toxicity, non-cancer effects, CTUh | 1.31E−05 | 2.66E−06 | 2.47E−06 |
Human toxicity, cancer effects, CTUh | 3.32E−06 | 7.24E−07 | 7.70E−07 |
Particulate matter/respiratory inorganics, kg PM2.5 eq. | 3.02E−02 | 4.15E−03 | 4.69E−03 |
Photochemical ozone formation, human health, kg NMVOC eq. | 1.75E−01 | 3.87E−02 | 3.79E−02 |
Acidification, Mole of H+ eq. | 2.54E−01 | 4.82E−02 | 5.15E−02 |
Terrestrial eutrophication, Mole of N eq. | 5.07E−01 | 1.08E−01 | 1.13E−01 |
Freshwater eutrophication, kg P eq. | 1.38E−02 | 2.16E−03 | 2.80E−03 |
Freshwater ecotoxicity, kg Sb eq. | 4.60E−02 | 1.39E−02 | 1.00E−02 |
Resource depletion, mineral, fossils and renewables, kg Sb eq. | 3.99E+02 | 7.30E+01 | 8.75E+01 |
Resource depletion, water, m³ eq. | 2.45E−03 | 4.75E−04 | 5.29E−04 |
Primary energy demand, MJ | 5.57E−01 | 2.17E−01 | 2.89E−01 |
Scenario | Packaging | Material | Mass | Reference flow |
DPack | Tray | 90% PET, 10% PE | 15 g | 16.00 kg |
Film | Multilayer polymers film | 1 g | 1.07 kg | |
pRPack | Tray | PP + Natural antioxidants | 15 g | 1.89 kg |
Film | PE + Natural antioxidants | 1 g | 1.07 kg |
DPack | pRPack | |
Distance from polymer production to package manufacturing site | 280 km | 570 km |
Distance from package manufacturing site to dry-cured ham factory | 752 km | 220 km |
Delivery | 250 km | 250 km |
Consumer journey | 5 km | 5 km |
Waste collection | 50 km | 50 km |
Distance to the final waste disposal site | 100 km | 100 km |
Distance for return of reusable trays | - | 250 km |
DPack | pRPack-i | pRPack-r | |
Climate change, excl biogenic carbon, kg CO2 eq. | 9.40E+01 | 2.13E+01 | 1.36E+01 |
Ozone depletion, kg CFC-11 eq. | 3.82E−06 | 1.52E−06 | 1.94E−06 |
Human toxicity, non-cancer effects, CTUh | 1.31E−05 | 2.66E−06 | 2.47E−06 |
Human toxicity, cancer effects, CTUh | 3.32E−06 | 7.24E−07 | 7.70E−07 |
Particulate matter/respiratory inorganics, kg PM2.5 eq. | 3.02E−02 | 4.15E−03 | 4.69E−03 |
Photochemical ozone formation, human health, kg NMVOC eq. | 1.75E−01 | 3.87E−02 | 3.79E−02 |
Acidification, Mole of H+ eq. | 2.54E−01 | 4.82E−02 | 5.15E−02 |
Terrestrial eutrophication, Mole of N eq. | 5.07E−01 | 1.08E−01 | 1.13E−01 |
Freshwater eutrophication, kg P eq. | 1.38E−02 | 2.16E−03 | 2.80E−03 |
Freshwater ecotoxicity, kg Sb eq. | 4.60E−02 | 1.39E−02 | 1.00E−02 |
Resource depletion, mineral, fossils and renewables, kg Sb eq. | 3.99E+02 | 7.30E+01 | 8.75E+01 |
Resource depletion, water, m³ eq. | 2.45E−03 | 4.75E−04 | 5.29E−04 |
Primary energy demand, MJ | 5.57E−01 | 2.17E−01 | 2.89E−01 |