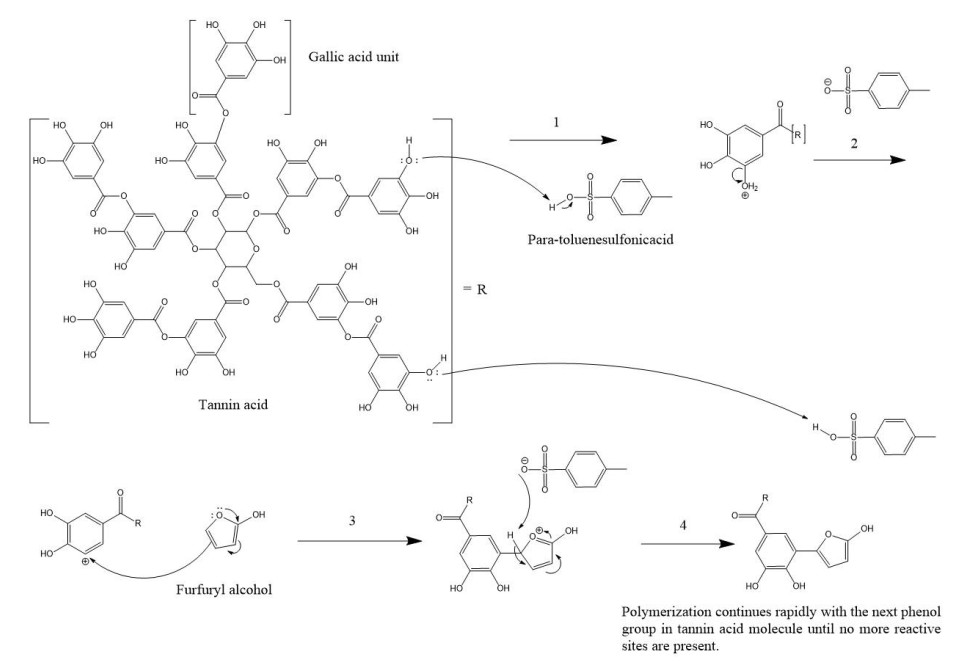
Citation: Toni Varila, Henrik Romar, Tero Luukkonen, Ulla Lassi. Physical activation and characterization of tannin-based foams enforced with boric acid and zinc chloride[J]. AIMS Materials Science, 2019, 6(2): 301-314. doi: 10.3934/matersci.2019.2.301
[1] | Ahmed Al-Ramthan, Ruaa Al Mezrakchi . Investigation of cementitious composites reinforced with metallic nanomaterials, boric acid, and lime for infrastructure enhancement. AIMS Materials Science, 2024, 11(3): 495-514. doi: 10.3934/matersci.2024025 |
[2] | Purinut Maingam, Ubolrat Wangrakdiskul, Natthakitta Piyarat . Potential of alternative waste materials: rice husk ash and waste glass cullet with boric acid addition for low-fired unglazed tiles. AIMS Materials Science, 2021, 8(2): 283-300. doi: 10.3934/matersci.2021019 |
[3] | Mahmoud A Rabah . Lead, zinc and copper fine powder with controlled size and shape. AIMS Materials Science, 2017, 4(6): 1358-1371. doi: 10.3934/matersci.2017.6.1358 |
[4] | Zulzamri Salleh, Md Mainul Islam, Jayantha Ananda Epaarachchi, Haibin Su . Mechanical properties of sandwich composite made of syntactic foam core and GFRP skins. AIMS Materials Science, 2016, 3(4): 1704-1727. doi: 10.3934/matersci.2016.4.1704 |
[5] | Mahmoud A. Rabah, Mohamed B. El Anadolly, Rabab A. El Shereif, Mohamed Sh. Atrees, Hayat M. El Agamy . Preparation of valuable products from cleaned carbon of fuel ash. AIMS Materials Science, 2017, 4(5): 1186-1201. doi: 10.3934/matersci.2017.5.1186 |
[6] | Alaa Ebrahiem, Sobhy S Ibrahim, Ahmed M El-Khaib, Ahmed S Doma . Ethylene-propylene-diene (EPDM) rubber/borax composite: kinetic thermal studies. AIMS Materials Science, 2023, 10(4): 556-574. doi: 10.3934/matersci.2023031 |
[7] | M. Kanta Rao, Ch. N. Satish Kumar . Influence of fly ash on hydration compounds of high-volume fly ash concrete. AIMS Materials Science, 2021, 8(2): 301-320. doi: 10.3934/matersci.2021020 |
[8] | Michael R. Koblischka, Anjela Koblischka-Veneva . Porous high-Tc superconductors and their applications. AIMS Materials Science, 2018, 5(6): 1199-1213. doi: 10.3934/matersci.2018.6.1199 |
[9] | V. Flores-Alés, F.J. Alejandre, F.J. Blasco-López, M. Torres-González, J.M. Alducin-Ochoa . Analysis of alterations presented in a white-concrete façade exposed to a marine environment——A case study in Cádiz (Spain). AIMS Materials Science, 2022, 9(2): 255-269. doi: 10.3934/matersci.2022015 |
[10] | S. Debbakh, K. Boumchedda . Development and characterization of cellular ceramic bricks using Algerian kaolin. AIMS Materials Science, 2020, 7(4): 431-440. doi: 10.3934/matersci.2020.4.431 |
Formulations and properties of tannin-based rigid foams have been widely studied. Physical properties of the tannin furanic foams like fire resistance, mechanical strength, adsorption of metals, conductivity and permeability have been reported by [1,2]. The foams have proved to be rather brittle with a low level of mechanical strength. A number of methods for preparing more rigid and stable tannin based- foams have also been published [3,4,5].
Tannin-based foams are generally produced using cross-linking agents such as formaldehyde, these agents are forming chemical bridges between the individual condensed or hydrolysable tannin molecules. Due to the toxicity of formaldehyde, more environmental friendly substances, like furfuryl alcohol or glutaraldehyde, are being used in the preparation. In the case of furfuryl alcohol, it acts as a heat-generating agent through both its auto-polymerisation and for its reaction with the tannin acid under acid conditions [3,6], as can be seen from Figure 1. The tanninic-furfuryl based structure is created by this polymerization reaction. Furthermore, the addition of furfuryl alcohol increases to some extent the mechanical strength of the tannin foams. The foaming process itself is carried out by adding a low boiling-point solvent such as pentane or diethyl ether as a blowing agent into the tanninic-furfuryl backbone. The highly exothermic polymeric reaction under acid condition generates the heat that is required to evaporate the blowing agent which raises the foam [1,7].
In the production process of activated carbons, the organic material is first carbonized at temperatures of 673–973 K, in this process most of the volatile components are released as pyrolysis gases in combination with the breakdown products from cellulose, hemicellulose and lignin, as pyrolytic oil [8]. The product from the carbonization stage is a solid with high carbon content, typically in the range of 60–70% calculated on a mass basis, depending on the starting material and the process parameters used.
In the second stage with physical activation, the carbons are activated to activated carbons using temperatures in the range of 973–1173 K in combination with activating agents, in the physical activation gases like water (steam) or carbon dioxide (CO2) are used as activators. Steam activation has an effect on the specific surface areas, pore volumes and pore size distributions and might increase the O-content. A number of factors are affecting the properties of activated carbons produced by physical activation, among them the biomass used, activation time and activation temperature used [9].
An alternative activating method to produce activated carbons is chemical activation. In chemical activation, chemical agents, e.g., zinc chloride (ZnCl2), KOH, NaOH, and H3PO4, can be used for activating carbon [10,11,12,13]. The procedure is rather simple, solutions containing the chemical activation agent is impregnated to the surface of biomass, dried in an oven and finally activated in the furnace at 673 to 873 K for 1 to 4 hours under an inert atmosphere (nitrogen atmosphere). After the activation, the chemical activation agent is refluxed away with diluted mineral acid, filtered, washed with water until pH is neutral and finally dried in an oven.
Chemical activation of the tannin furanic foams into activated carbons with ZnCl2 and H3PO4 has been successfully done by [14]. According to the authors, it is possible to obtain specific surface area as high as 1800 m2/g using ZnCl2 as the activating agent followed by thermal treatment of the Zn-impregnated foam. The carbons produced during this process were mostly micro-porous. However, it might be possible to modify the pore size distribution with other activation methods like physical activation using steam or CO2. Yet, information about physical activation of the tannin foams with steam or carbon dioxide has not been reported in the literature.
Only few reports about the effects of additives, like boric acid and hexamine, on the physical properties of the tannin foams have been previously reported [1]. Authors noticed that modification of foams by addition of boric acid affected the properties of the doped foams in a positive way, the doped foams had much higher fire resistance compared to the same type of foam without additives. This finding is important, because so far the most interesting purpose of these tannin foams is to replace flammable, non-environmental friendly, expensive polyurethane foams, used as insulating materials in the building industry. In addition, tannin foams can be used in several other applications as well. Floral foams, packaging materials, super capacitors, crash protection and ion adsorption are suitable application for these tannin foams [1,15,16,17].
From a biological point of view, tannins are defined as water soluble phenolic compounds that are able to bind or precipitate other molecules, such as proteins and metals, within aqueous solutions [18]. Tannins are naturally occurring compounds that exists in fruits, woods, seeds and in many vegetable oils. Tannins, also called polyphenols, can by divided in three groups: hydrolysable tannins, condensed tannins and phlorotannins (see Figure 2). Especially the hydrolysable tannins, which are used in this study play a major role in the polymerization reaction due to their high phenol content [19]. The structure of condensed tannins is well known. They consist of 15 carbon atoms arranged in three rings, as can been seen from Figure 2a [20]. Structurally, phlorotannins are the simplest of all the tannins. They consist of one or more phloroglucinol units (Figure 2b) that are attached to each other via C–C or C–O–C bonds and are mainly found in marine organisms [18,21]. Hydrolysable tannins structures are the most complex (Figure 2c). They consist of several molecules of polyphenolic acid such as gallic or ellagic acid, and are bounded through ester linkages to a central glucose molecule [22,23,24].
In this article, a new type of tannin foams is produced and the properties such as specific surface area, pore size distribution and mechanical strength are investigated before and after chemical and physical activation procedures. In addition, novel information about physical activation of tannin foams and its effect on aforementioned properties are studied and later on compared with foams activated chemically with ZnCl2 and H3BO3. The aim of this article is to prove that higher mechanical strength can be achieved, by first enforcing the tannin foams with ZnCl2 or H3BO3 and afterwards carbonizing them at high temperature, compared to the foams which are not carbonized and carbonized without additives.
The commercial tannin acid (95%), furfuryl alcohol (98%), surfactant (Tween 85) used in the experiments were ordered from Acros Organic. The catalyst, para-toluene sulfonic acid monohydrate (PTSA), and blowing agent (n-pentane) were ordered from Merck Company. Technical grade ZnCl2 was delivered from VWR chemicals and H3BO3 (99.4%) was order from J.T. Baker.
Tannin furanic foams (TFF) with para-toluenesulfanoic acid (PTSA) (P) were prepared according to the method described earlier by [25] and zinc chloride (Zn) and boric acid (B) based TFFs, (TFFZn) and (TFFB) respectively, were prepared by modifying the method described in the aforementioned article. Mixture of components is shown in Table 1, while samples were named according to the catalyst, and curing parameters used in the foaming and maturing processes. For example TFFB correspond to a foam, which was made using H3BO3 as catalyst and later on matured (M) at 378 K for 24 h.
Sample name | FA (98%) (g) | Tannin acid (95%) (g) | Catalyst | Blowing agents | Surfactant | |||||
H3BO3 (g) | PTSA (g) | ZnCl2 (g) | n-pentane (g) | Water (g) | Tween 85 (g) | |||||
TFFB | 14 | 30 | 5.2 | - | - | 4.5 | 9 | 2 | ||
TFFP | 14 | 30 | - | 5.2a | - | 4.5 | 9 | 2 | ||
TFFZn | 14 | 30 | - | - | 19.5a | 4.5 | 9 | 2 | ||
a Catalyst is dissolved in water to make 65% water solution. |
In short, the ingredients; water, furfuryl alcohol and surfactant Tween 85 were added in appropriate amounts and thoroughly mixed for 30 s in a one liter beaker. To this liquid mixture, tannin acid was added and mixed with a mechanical stirrer (2000 rpm) for 5–10 min. The blowing agent, n-pentane, was added to the homogenous solution followed by the addition of a catalyst, PTSA. The mixture was quickly mechanically stirred for 5–10 seconds. In the case of TFFZn, similar procedure was applied. Instead of PTSA, ZnCl2 (65% water solution) was added after the blowing agent and then quickly stirred mechanically for 5–10 seconds. In the case of TFFB, due to the poor solubility of boric acid in water, boric acid powder was added to the liquid mixture after the blowing agent and quickly stirred mechanically 5–10 seconds. Foaming, with PTSA and ZnCl2 occurred within a few seconds (5–10 seconds) but the foaming with H3BO3 occurred after a few minutes (5–10 min) when it was heated in an oven. All foams were then hardened in an oven using natural convection for 24 h at 378 K. After the maturing, rectangular shaped samples (2 cm × 0.9 cm × 1.4 cm) from each foam were taken and further analyzed for mechanical strength. These foams were considered as reference materials. In addition, from here on a letter M (matured) is added to the TFFP, TFFB and TFFZn samples to avoid confusion with carbonized foams.
The TFFPM foams were cut into rectangular pieces and placed in a stainless-steel fixed-bed reactor for physical (steam) activation and for carbonization without activation. Carbonization and activation parameters are shown in Table 2. Samples were named according to the temperature and the holding time used in the carbonization and activation processes. For example, the sample TFFPA1 corresponds to a matured foam, which was activated with steam at 1073 K for 1 hour (A) and sample TFFPC1 correspond to a matured foam, which was carbonized at 1073 K (C) for 1 hour without activation.
Method | Sample name | Ramp (K/min) | Activation agent | Temperature (K) | Holding time (h) |
Carbonization | TFFPC1 | 10 | None | 1073 | 1 |
TFFPC2 | 10 | None | 1073 | 2 | |
TFFPC4 | 10 | None | 1073 | 4 | |
Physical activation | TFFPA1 | 10 | Steam | 1073 | 1 |
TFFPA2 | 10 | Steam | 1073 | 2 | |
TFFPA4 | 10 | Steam | 1073 | 4 | |
Chemical activation | TFFZnA1 | 10 | ZnCl2 | 1073 | 1 |
TFFZnA2 | 10 | ZnCl2 | 1073 | 2 | |
TFFZnA4 | 10 | ZnCl2 | 1073 | 4 | |
TFFBA1 | 10 | H3BO3 | 1073 | 1 | |
TFFBA2 | 10 | H3BO3 | 1073 | 2 | |
TFFBA4 | 10 | H3BO3 | 1073 | 4 |
The reactor was placed in a tubular oven for the carbonization. During the heating process, the reactor was flushed with an inert gas (nitrogen) in order to avoid oxidation. The oven temperature was increased from room temperature to 1073 K using a 10 K/min heating ramp followed by different steam activation times at the target temperature. After the physical activation, samples TFFPA1, TFFPA2 and TFFPA4 were then further analyzed with various methods. TFFPA1, TFFPA2 and TFFPA4 were cut so that their final dimensions were the same (2 cm × 0.9 cm × 1.4 cm). These foams were analyzed for mechanical strength.
TFFZnM and TFFBM foams were chemically activated in a stainless-steel fixed-bed reactor. Chemical activation agents here were ZnCl2 and H3BO3, catalyst added during the foaming process. Like in physical activation, the reactor was placed in a tubular heating oven for the chemical activation. The oven temperature was increased from room level to temperatures shown in Table 2 using a 10 K/min heating ramp and different holding times. Samples were named in the same way as in physical activation.
Chemically activated TFFZnA1, TFFZnA2, TFFZnA4, TFFBA1, TFFBA2 and TFFBA4 samples were cut into their final dimension (2 cm × 0.9 cm × 1.4 cm) and further analyzed for mechanical strength. For the specific surface and pore size distribution, some samples were refluxed with 3 M HCl for 1 h, in order to remove any remaining ZnCl2 or H3BO3 in the foams. Samples, TFFZnA1, TFFZnA2, TFFZnA4, TFFBA1, TFFBA2 and TFFBA4 were then filtered and washed with distilled water until a neutral filtrate was obtained. Samples were finally dried in an oven over night at 378 K and used for further characterizations.
Prior to measurements, portions of each sample (about 200 mg) were pretreated for 3 h at low pressure (2 μm Hg) and elevated temperature (413 K) in order to clean their surfaces. Adsorption isotherms were obtained by immersing sample tubes in liquid nitrogen (76 K) in order to obtain isothermal conditions. Nitrogen was added to the samples in small steps and the resulting isotherms were obtained. Specific surface areas (SSA) were calculated from adsorption isotherms according to the BET (Brunauer–Emmett–Teller) method [26]. Pore size distributions were calculated from the experimentally measured adsorption data using the density functional theory (DFT) algorithm [27] by assuming slit-formed pores [28]. With the setup of the instrument used, a Micromeritics ASAP 2020 (Norcross USA), pores down to 1.5 nm in diameter can, according to the manufacturer, be measured precisely. The instruments calculate two sets of isotherms, which serve as kernel functions, for the characterization of porous materials from adsorption data. According to previous works the SSAs are measured with a precision of ±5% [29].
Compressive strengths of foams were determined using a Zwick/Roell Z010 testing machine (Kennesaw, Georgia) (with a load cell of 10 kN). The loading speed was 0.1 mm/s and the measurement ended when the force decreased by 50% from maximum or deformation reached 30%. Compressive strength was calculated with Eq 1.
(1) |
where F (N) is the maximum force at the linear region of the compression curve and A (mm2) is the surface area. The accuracy of the instrument was ±1%.
The stress–strain curve of cellular material has typically three distinguishable regions: linear part at low strain, a plateau region (collapse of the cell layers), and densification (all cell layers are compressed). The compressive strength can be defined as the value at the plateau whereas the slope of the linear part represents the elastic modulus (i.e., resistance against elastic or non-permanent deformation). The curve roughness ("noise") is a result of the redistribution of the compression after the fracture of layers of cells and subsequent loading of the next cell layers. Earlier work on tannin foams has shown that higher bulk density indicates higher compressive strength [6,30,31]. However, also the cell size affects: larger cells indicate lower compressive strength in the case of brittle foams [30]. Furthermore, amine-group-containing additives have also a positive effect on compressive strength as they can react and substitute hydroxyl groups of tannins. In addition, surfactants as additives improve compressive strengths of tannins foams [31].
Densities of each foam were characterized right after the maturation and after the activation of the tannin furanic foams. Measuring the total volume and mass of each sample, densities are obtained from Eq 2, which can be defined as,
(2) |
where m is the mass of the sample and V is the total volume obtained by measuring the dimensions, length, height and width of each rectangular shaped tannin furanic foam. The accuracy of this method was ±5%, depending on how accurately were each foam cut into their final dimension.
According to the results shown in Table 3, the unactivated foams themselves have low specific surface area and low or no porosity. There is a clear difference in pore volumes and specific surface areas when changing the activation times and physical or chemical activation agents. As expected the specific surface areas are highly dependent on the activation times used. In the case of TFFP samples, specific surface area raised from 0.83 to 845 m2/g when using 2 h steam activation. Longer activation times lowered the specific surface areas from 845 to 707 m2/g most likely due to a beginning expansion of micro-pores into meso-pores. Similar trend was observed in chemical activation. In case of ZnCl2 activated foam specific surface area increased from zero (value was too low to be measured) to 737 m2/g when using 2 h holding time at the target temperature. Like in physical activation, longer holding times reduced the specific surface areas. Boric acid activated foams behaved differently from steam activated and ZnCl2 activated foams. The lowest surface area, with boric acid activated foams, was obtained when using 2 h holding time. The result obtained, 0.56 m2/g, is interesting even though the sample was reproduced 2-times still same results was obtained. The reason for this is still unknown, but boric acid in not known as a chemical activation agent. Despite this, these foams followed the same route as ZnCl2 and steam activated foams. Specific surface area of boric acid activated foams raised from 0.023 to 404 m2/g using 1 hour holding time. Slightly lower specific surface areas were obtained with boric acid than with ZnCl2 and steam. One possible reason for this might be the physical properties of boric acid compared to ZnCl2. Pore volumes in all cases followed the same route as did the specific surface area. Highest pore volumes were obtained with steam and ZnCl2 activation, 0.350 g/cm3 and 0.306 g/cm3 respectively, using 2 h holding time. Boric acid activation produces pore volume, which was approximately half from the steam and ZnCl2 activated values. According to the literature, chemical activation is usually performed at lower temperatures, at 673–873 K. Chemical activation done at high temperatures with ZnCl2 will expands the existing micropores into mesopores, and this process leads to lower overall specific surface area and pore volume [32,33]. Many studies, found in the literature, support this finding. In our earlier study [13], we observed that it is possible to obtain specific surface areas as high as 1360 m2/g by chemically activation of peat with ZnCl2 at 873 K. Similarly, it obtained 1875 m2/g by chemically activating tannin foams with ZnCl2 at 773 K [14].
Calculation method | Unit | Physically activated foams | Chemically activated foams | |||||||||||
TFFPM | TFFPA1 | TFFPA2 | TFFPA4 | TFFZnM | TFFZnA1 | TFFZnA2 | TFFZnA4 | TFFBM | TFFBA1 | TFFBA2 | TFFBA4 | |||
BET | ||||||||||||||
SSA | m2g-1 | 0.83 | 685 | 845 | 707 | * | 689 | 737 | 548 | 0.023 | 404 | 0.56 | 344 | |
Pore volume | cm3g-1 | * | 0.287 | 0.350 | 0.299 | * | 0.287 | 0.306 | 0.230 | * | 0.169 | 0.00018 | 0.142 | |
Langmuir surface area | m2g-1 | 0.95 | 787 | 967 | 805 | * | 783 | 839 | 623 | * | 460 | * | 391 | |
t-plot | ||||||||||||||
Micropore volume | cm3g-1 | 0.00036 | 0.257 | 0.309 | 0.249 | * | 0.255 | 0.273 | 0.200 | * | 0.153 | * | 0.129 | |
Micropore area | m2g-1 | * | 638 | 765 | 618 | * | 633 | 679 | 498 | * | 380 | * | 322 | |
External surface area | m2g-1 | * | 46 | 79 | 89 | * | 56 | 58 | 50 | * | 25 | * | 22 | |
DFT | ||||||||||||||
Pore volume | cm3g-1 | 0.0002 | 0.237 | 0.292 | 0.247 | * | 0.238 | 0.254 | 0.190 | * | 0.140 | * | 0.119 | |
Micropores | cm3g-1 | 0.0002 | 0.237 | 0.291 | 0.240 | * | 0.237 | 0.254 | 0.187 | * | 0.139 | * | 0.118 | |
Mesopores | cm3g-1 | 0 | 0 | 0.001 | 0.007 | * | 0.001 | 0 | 0.002 | * | 0.001 | * | 0.001 | |
Macropores | cm3g-1 | 0 | 0 | 0 | 0 | * | 0 | 0 | 0.001 | * | 0 | * | 0 | |
Micropores | % | 100 | 100 | 99.7 | 97.2 | * | 99.6 | 100 | 98.4 | * | 99.3 | * | 99.2 | |
Mesopores | % | 0 | 0 | 0.3 | 2.8 | * | 0.4 | 0 | 1.1 | * | 0.7 | * | 0.8 | |
Macropores | % | 0 | 0 | 0 | 0 | * | 0 | 0 | 0.5 | * | 0 | * | 0 | |
* Values were too low to be measure |
According to the results, pore size distributions for all the samples were without any exceptions in microporous region. This can be seen even more clearly with the external surface areas (t-plot calculations). For all the samples, the external surface areas are in the range of 22–89 m2g−1. This indicates that a low occurrence of meso-pores is inside the activated foams. Comparing the micro-pore areas of all samples to total SSAs, it can be stated that 89–93% of the pores are micro-pores. As can be seen also from the DFT-calculations, there is only very little change in the pore size distribution when changing the holding times and activation procedure. For example, steam activation raises the amount of mesopores only 2.8% when increasing the holding time from 0 to 4 h. Therefore, more advanced procedures are needed in order to produce mesoporous tannin foams.
To conclude, different holding times and different activation methods have only minor or no effect on the pore size development of the tannin furanic foams. However, it is possible to produce relatively high surface areas using physical or chemical activation. Might be that even higher surface areas are obtained with chemical activation if lower activation temperatures are used. This might also effect the pore development more efficiently.
The compressive strengths of the present study tannin foams (0.040–0.547 MPa, Table 4) are in good agreement with earlier studies, which have reported compressive strengths in the range of 0.03–3.97 MPa [2]. The elastic moduli of the present study are, however, clearly smaller than reported for instance by [31]. Thus, resistance against non-permanent deformation is low, that is, the studied foams exhibit brittle behavior. When tannin furanic foams have been carbonized in earlier studies, the compressive strength has increased clearly compared to matured foams [34].
Sample | Elastic modulus [MPa] | Compressive strength [MPa] | Densities [g/cm3] | |
Matured foams | TFFPM | 0.0022 | 0.04 | 0.05 |
TFFZnM | 0.0134 | 0.10 | 0.15 | |
TFFBM | 0.0287 | 0.10 | 0.29 | |
Carbonized foams | TFFPC1 | 0.0095 | 0.18 | 0.05 |
TFFPC2 | 0.0063 | 0.14 | 0.05 | |
TFFPC4 | 0.0086 | 0.16 | 0.05 | |
ZnCl2 enforced foams | TFFZnA1 | 0.0229 | 0.21 | 0.10 |
TFFZnA2 | 0.0085 | 0.23 | 0.10 | |
TFFZnA4 | 0.0369 | 0.55 | 0.10 | |
Boric acid enforced foams | TFFBA1 | 0.0074 | 0.13 | 0.16 |
TFFBA2 | 0.0098 | 0.20 | 0.23 | |
TFFBA4 | 0.0071 | 0.26 | 0.13 |
It is well known, that mechanical strength is highly dependent on the relative densities of tannin furanic foams and many publications support this finding [34]. The results in this study are however in disagreement with earlier published studies [1,2]. As can be seen from Table 4, densities are lower for the activated than matured samples but mechanical strength is anyhow increasing. For example density for sample TFFZnM is 0.15 g/cm3 and for ZnCl2 activated foams densities are 0.10 g/cm3 regardless the holding time. While densities are decreasing the mechanical strength is anyhow increasing. Up to 5 times stronger materials were achieved when comparing mechanical strengths between TFFZnM and TFFZnA4 samples, 0.10 MPa and 0.55 MPa respectively. In all cases it seems that, the longer the holding time is the stronger is the behavior of the foams. This effect can be seen clearly from the foams prepared and activated with ZnCl2 and H3BO3. One possible reason for this can be that, during the activation, the tannin furanic foams are shrinking, approximately 20–30 v% from the original volume, and due to this, foams are more compact.
Furthermore there seems to be no correlation between the carbonized foams and densities of them. However, there is indications that indirect correlation between the mechanical strength of boric and ZnCl2 enforced foams and the densities of them. This can be seen in Figure 3.
In this study, the mechanical strength, density, specific surface area, pore volume and pore size distribution properties of matured, carbonized, and physically/chemically activated tannin foams are compared. According to the results, an evident correlation is found between the holding time used in the thermal process and the mechanical strength of tannin foams. There appears to be no difference in the pore size distributions between the physically and chemically activated tannin foams. In all cases, microporous material is formed. This study shows that these materials are promising candidates for a number of applications. The chemical agents used, ZnCl2 and H3BO3 appears to have an effect in the foaming process where they act as catalysts, the effect of these chemicals on the formation of porous structures is less obvious.
Toni Varila would like to thank the Green Bioraff Solutions Project (EU/Interreg/Botnia-Atlantica, 20201508) for funding this research.
All authors declare no conflicts of interest in this paper.
[1] |
Tondi G, Zhao W, Pizzi A, et al. (2009) Tannin-based rigid foams: A survey of chemical and physical properties. Bioresource Technol 100: 5162–5169. doi: 10.1016/j.biortech.2009.05.055
![]() |
[2] |
Tondi G, Pizzi A (2009) Tannin-based rigid foams: Characterization and modification. Ind Crop Prod 29: 356–363. doi: 10.1016/j.indcrop.2008.07.003
![]() |
[3] | Link M, Kolbitsch C, Tondi G, et al. (2011) Formaldehyde-free tannin based foams and their use as lightweight panels. BioResources 6: 4218–4228. |
[4] |
Szczurek A, Fierro V, Pizzi A, et al. (2014) A new method for preparing tannin-based foams. Ind Crop Prod 54: 40–53. doi: 10.1016/j.indcrop.2014.01.012
![]() |
[5] | Li X, Pizzi A, Lacoste C, et al. (2013) Physical properties of tannin/furanic resin foamed with different blowing agents. BioResources 8: 743–752. |
[6] |
Lacoste C, Basso MC, Pizzi A, et al. (2013) Bioresourced pine tannin/furanic foams with glyoxal and glutaraldehyde. Ind Crop Prod 45: 401–405. doi: 10.1016/j.indcrop.2012.12.032
![]() |
[7] |
Lacoste C, Basso MC, Pizzi A, et al. (2015) Natural albumin/tannin cellular foams. Ind Crop Prod 73: 41–48. doi: 10.1016/j.indcrop.2015.03.087
![]() |
[8] |
Antal MJ, Gronli M (2003) The art, science, and technology of charcoal production. Ind Eng Chem Res 42: 1619–1640. doi: 10.1021/ie0207919
![]() |
[9] | Tadda MA, Ahsan A, Shitu A, et al. (2016) A review on activated carbon: process, application and prospects. J Adv Civil Eng Pract Res 2: 7–13. |
[10] |
Yorgun S, Vural N, Demiral H (2009) Preparation of high-surface area activated carbons from Paulownia wood by ZnCl2 activation. Micropor Mesopor Mat 122: 189–194. doi: 10.1016/j.micromeso.2009.02.032
![]() |
[11] |
Lillo-Rodenas MA, Cazorla-Amoros D, Lineras-Solano A (2003) Understanding chemical reactions between carbons and NaOH and KOH: An insight into the chemical activation mechanism. Carbon 41: 267–275. doi: 10.1016/S0008-6223(02)00279-8
![]() |
[12] | Mohammad-Khah A, Ansari R (2009) Activated charcoal: preparation, characterization and applications: a review article. Int J Chem Tech Res 1: 859–864. |
[13] | Varila T, Bergna D, Lahti R, et al. (2017) Activated carbon production from peat using ZnCl2: Characterization and applications. BioResources 12: 8078–8092. |
[14] |
Tondi G, Pizzi A, Delmotte L, et al. (2010) Chemical activation of tannin–furanic carbon foams. Ind Crop Prod 31: 327–334. doi: 10.1016/j.indcrop.2009.11.013
![]() |
[15] |
Meikleham NE, Pizzi A (1994) Acid- and alkali-catalyzed tannin-based rigid foams. J Appl Polym Sci 53: 1547–1556. doi: 10.1002/app.1994.070531117
![]() |
[16] |
Tondi G, Oo CW, Pizzi A, et al. (2009) Metal adsorption of tannin based rigid foams. Ind Crop Prod 29: 336–340. doi: 10.1016/j.indcrop.2008.06.006
![]() |
[17] |
Das S, Heasman P, Ben T, et al. (2017) Porous organic materials: Strategic design and structure–function correlation. Chem Rev 117: 1515–1563. doi: 10.1021/acs.chemrev.6b00439
![]() |
[18] |
Salminen JP, Karonen M (2011) Chemical ecology of tannins and other phenolics: we need a change in approach. Funct Ecol 25: 325–338. doi: 10.1111/j.1365-2435.2010.01826.x
![]() |
[19] | Natural chemistry research group from university of Turku (2014–2019): Tannin definition and structures. Available from: http://naturalchemistry.utu.fi. |
[20] |
Pietta PG (2000) Flavonoids as Antioxidants. J Nat Prod 63: 1035–1042. doi: 10.1021/np9904509
![]() |
[21] |
Arnold TM, Targett NM (2002) Marine tannins: the importance of mechanistic framework for predicting ecological roles. J Chem Ecol 28: 1919–1934. doi: 10.1023/A:1020737609151
![]() |
[22] |
Kilkowski WJ, Gross GG (1999) Color reaction of hydrolyzable tannins with Bradford reagent, Coomassie brilliant blue. Phytochemistry 51: 363–366. doi: 10.1016/S0031-9422(98)00747-X
![]() |
[23] | Gross GG (1999) Biosynthesis, biodegradation, and cellular localization of hydrolyzable tannins, In: Lewis NG, Romeo JT, Towers GHN, Phytochemicals in Human Health Protection, Nutrition and Plant Defenses, New York: Plenum Press, 185–213. |
[24] |
Barbehenn RV, Jones CP, Hagerman AE, et al. (2006) Ellagitannins have greater oxidative activities than condensed tannins and galloyl glucoses at high pH: potential impact on caterpillars. J Chem Ecol 32: 2253–2267. doi: 10.1007/s10886-006-9143-7
![]() |
[25] | Basso MC, Lagel MC, Pizzi A, et al. (2015) First tools for tannin-furanic foams design. BioResources 10: 5233–5241. |
[26] |
Brunauer S, Emmett PH, Teller E (1938) Adsorption of gases in multimolecular layers. J Am Chem Soc 60: 309–319. doi: 10.1021/ja01269a023
![]() |
[27] |
Seaton NA, Walton JPRB, Quirke N (1989) A new analysis method for the determination of the pore size distribution of porous carbons from nitrogen adsorption measurements. Carbon 27: 853–861. doi: 10.1016/0008-6223(89)90035-3
![]() |
[28] |
Lastoskie C, Gubbins KE, Quirke N (1993) Pore size heterogeneity and the carbon slit pore: a density functional theory model. Langmuir 9: 2693–2702. doi: 10.1021/la00034a032
![]() |
[29] |
Hackley VA, Stefanial AB (2013) "Real-world" precision, bias, and between-laboratory variation for surface area measurement of a titanium dioxide nanomaterial in powder form. J Nanopart Res 15: 1742. doi: 10.1007/s11051-013-1742-y
![]() |
[30] |
Letellier M, Delgado-Sanchez C, Khelifa M, et al. (2017) Mechanical properties of model vitreous carbon foams. Carbon 116: 562–571. doi: 10.1016/j.carbon.2017.02.020
![]() |
[31] |
Santiago-Medina FJ, Delgado-Sánchez C, Basso MC, et al. (2018) Mechanically blown wall-projected tannin-based foams. Ind Crop Prod 113: 316–323. doi: 10.1016/j.indcrop.2018.01.049
![]() |
[32] |
Demiral H, Demiral I, Tümsek F, et al. (2008) Pore structure of activated carbon prepared from hazelnut bagasse by chemical activation. Surf Interface Anal 40: 616–619. doi: 10.1002/sia.2631
![]() |
[33] |
Bouchemal N, Belhachemi M, Merzougui Z, et al. (2009) The effect of temperature and impregnation ratio on the active carbon porosity. Desalin Water Treat 10: 115–120. doi: 10.5004/dwt.2009.828
![]() |
[34] |
Celzard A, Zhao W, Pizzi A, et al. (2010) Mechanical properties of tannin-based rigid foams undergoing compression. Mat Sci Eng A-Struct 527: 4438–4446. doi: 10.1016/j.msea.2010.03.091
![]() |
1. | Toni Varila, Eveliina Mäkelä, Riikka Kupila, Henrik Romar, Tao Hu, Reetta Karinen, Riikka L. Puurunen, Ulla Lassi, Conversion of furfural to 2-methylfuran over CuNi catalysts supported on biobased carbon foams, 2020, 09205861, 10.1016/j.cattod.2020.10.027 | |
2. | Antonio M. Borrero-López, Vincent Nicolas, Zelie Marie, Alain Celzard, Vanessa Fierro, A Review of Rigid Polymeric Cellular Foams and Their Greener Tannin-Based Alternatives, 2022, 14, 2073-4360, 3974, 10.3390/polym14193974 | |
3. | Jonas Eckardt, Thomas Sepperer, Emanuele Cesprini, Primož Šket, Gianluca Tondi, Comparing Condensed and Hydrolysable Tannins for Mechanical Foaming of Furanic Foams: Synthesis and Characterization, 2023, 28, 1420-3049, 2799, 10.3390/molecules28062799 | |
4. | Pasi Korkalo, Toni Varila, Hanna Brännström, Jarkko Hellström, Tuula Jyske, Ulla Lassi, Applicability of hybrid aspen (Populus tremula L. × P. tremuloides Michx.) bark extract as a precursor of rigid carbon foam and activated carbon, 2023, 174, 09619534, 106838, 10.1016/j.biombioe.2023.106838 | |
5. | Hakim Kurniawan, Kristina Dwiatmini, 2024, 3055, 0094-243X, 060005, 10.1063/5.0183913 |
Sample name | FA (98%) (g) | Tannin acid (95%) (g) | Catalyst | Blowing agents | Surfactant | |||||
H3BO3 (g) | PTSA (g) | ZnCl2 (g) | n-pentane (g) | Water (g) | Tween 85 (g) | |||||
TFFB | 14 | 30 | 5.2 | - | - | 4.5 | 9 | 2 | ||
TFFP | 14 | 30 | - | 5.2a | - | 4.5 | 9 | 2 | ||
TFFZn | 14 | 30 | - | - | 19.5a | 4.5 | 9 | 2 | ||
a Catalyst is dissolved in water to make 65% water solution. |
Method | Sample name | Ramp (K/min) | Activation agent | Temperature (K) | Holding time (h) |
Carbonization | TFFPC1 | 10 | None | 1073 | 1 |
TFFPC2 | 10 | None | 1073 | 2 | |
TFFPC4 | 10 | None | 1073 | 4 | |
Physical activation | TFFPA1 | 10 | Steam | 1073 | 1 |
TFFPA2 | 10 | Steam | 1073 | 2 | |
TFFPA4 | 10 | Steam | 1073 | 4 | |
Chemical activation | TFFZnA1 | 10 | ZnCl2 | 1073 | 1 |
TFFZnA2 | 10 | ZnCl2 | 1073 | 2 | |
TFFZnA4 | 10 | ZnCl2 | 1073 | 4 | |
TFFBA1 | 10 | H3BO3 | 1073 | 1 | |
TFFBA2 | 10 | H3BO3 | 1073 | 2 | |
TFFBA4 | 10 | H3BO3 | 1073 | 4 |
Calculation method | Unit | Physically activated foams | Chemically activated foams | |||||||||||
TFFPM | TFFPA1 | TFFPA2 | TFFPA4 | TFFZnM | TFFZnA1 | TFFZnA2 | TFFZnA4 | TFFBM | TFFBA1 | TFFBA2 | TFFBA4 | |||
BET | ||||||||||||||
SSA | m2g-1 | 0.83 | 685 | 845 | 707 | * | 689 | 737 | 548 | 0.023 | 404 | 0.56 | 344 | |
Pore volume | cm3g-1 | * | 0.287 | 0.350 | 0.299 | * | 0.287 | 0.306 | 0.230 | * | 0.169 | 0.00018 | 0.142 | |
Langmuir surface area | m2g-1 | 0.95 | 787 | 967 | 805 | * | 783 | 839 | 623 | * | 460 | * | 391 | |
t-plot | ||||||||||||||
Micropore volume | cm3g-1 | 0.00036 | 0.257 | 0.309 | 0.249 | * | 0.255 | 0.273 | 0.200 | * | 0.153 | * | 0.129 | |
Micropore area | m2g-1 | * | 638 | 765 | 618 | * | 633 | 679 | 498 | * | 380 | * | 322 | |
External surface area | m2g-1 | * | 46 | 79 | 89 | * | 56 | 58 | 50 | * | 25 | * | 22 | |
DFT | ||||||||||||||
Pore volume | cm3g-1 | 0.0002 | 0.237 | 0.292 | 0.247 | * | 0.238 | 0.254 | 0.190 | * | 0.140 | * | 0.119 | |
Micropores | cm3g-1 | 0.0002 | 0.237 | 0.291 | 0.240 | * | 0.237 | 0.254 | 0.187 | * | 0.139 | * | 0.118 | |
Mesopores | cm3g-1 | 0 | 0 | 0.001 | 0.007 | * | 0.001 | 0 | 0.002 | * | 0.001 | * | 0.001 | |
Macropores | cm3g-1 | 0 | 0 | 0 | 0 | * | 0 | 0 | 0.001 | * | 0 | * | 0 | |
Micropores | % | 100 | 100 | 99.7 | 97.2 | * | 99.6 | 100 | 98.4 | * | 99.3 | * | 99.2 | |
Mesopores | % | 0 | 0 | 0.3 | 2.8 | * | 0.4 | 0 | 1.1 | * | 0.7 | * | 0.8 | |
Macropores | % | 0 | 0 | 0 | 0 | * | 0 | 0 | 0.5 | * | 0 | * | 0 | |
* Values were too low to be measure |
Sample | Elastic modulus [MPa] | Compressive strength [MPa] | Densities [g/cm3] | |
Matured foams | TFFPM | 0.0022 | 0.04 | 0.05 |
TFFZnM | 0.0134 | 0.10 | 0.15 | |
TFFBM | 0.0287 | 0.10 | 0.29 | |
Carbonized foams | TFFPC1 | 0.0095 | 0.18 | 0.05 |
TFFPC2 | 0.0063 | 0.14 | 0.05 | |
TFFPC4 | 0.0086 | 0.16 | 0.05 | |
ZnCl2 enforced foams | TFFZnA1 | 0.0229 | 0.21 | 0.10 |
TFFZnA2 | 0.0085 | 0.23 | 0.10 | |
TFFZnA4 | 0.0369 | 0.55 | 0.10 | |
Boric acid enforced foams | TFFBA1 | 0.0074 | 0.13 | 0.16 |
TFFBA2 | 0.0098 | 0.20 | 0.23 | |
TFFBA4 | 0.0071 | 0.26 | 0.13 |
Sample name | FA (98%) (g) | Tannin acid (95%) (g) | Catalyst | Blowing agents | Surfactant | |||||
H3BO3 (g) | PTSA (g) | ZnCl2 (g) | n-pentane (g) | Water (g) | Tween 85 (g) | |||||
TFFB | 14 | 30 | 5.2 | - | - | 4.5 | 9 | 2 | ||
TFFP | 14 | 30 | - | 5.2a | - | 4.5 | 9 | 2 | ||
TFFZn | 14 | 30 | - | - | 19.5a | 4.5 | 9 | 2 | ||
a Catalyst is dissolved in water to make 65% water solution. |
Method | Sample name | Ramp (K/min) | Activation agent | Temperature (K) | Holding time (h) |
Carbonization | TFFPC1 | 10 | None | 1073 | 1 |
TFFPC2 | 10 | None | 1073 | 2 | |
TFFPC4 | 10 | None | 1073 | 4 | |
Physical activation | TFFPA1 | 10 | Steam | 1073 | 1 |
TFFPA2 | 10 | Steam | 1073 | 2 | |
TFFPA4 | 10 | Steam | 1073 | 4 | |
Chemical activation | TFFZnA1 | 10 | ZnCl2 | 1073 | 1 |
TFFZnA2 | 10 | ZnCl2 | 1073 | 2 | |
TFFZnA4 | 10 | ZnCl2 | 1073 | 4 | |
TFFBA1 | 10 | H3BO3 | 1073 | 1 | |
TFFBA2 | 10 | H3BO3 | 1073 | 2 | |
TFFBA4 | 10 | H3BO3 | 1073 | 4 |
Calculation method | Unit | Physically activated foams | Chemically activated foams | |||||||||||
TFFPM | TFFPA1 | TFFPA2 | TFFPA4 | TFFZnM | TFFZnA1 | TFFZnA2 | TFFZnA4 | TFFBM | TFFBA1 | TFFBA2 | TFFBA4 | |||
BET | ||||||||||||||
SSA | m2g-1 | 0.83 | 685 | 845 | 707 | * | 689 | 737 | 548 | 0.023 | 404 | 0.56 | 344 | |
Pore volume | cm3g-1 | * | 0.287 | 0.350 | 0.299 | * | 0.287 | 0.306 | 0.230 | * | 0.169 | 0.00018 | 0.142 | |
Langmuir surface area | m2g-1 | 0.95 | 787 | 967 | 805 | * | 783 | 839 | 623 | * | 460 | * | 391 | |
t-plot | ||||||||||||||
Micropore volume | cm3g-1 | 0.00036 | 0.257 | 0.309 | 0.249 | * | 0.255 | 0.273 | 0.200 | * | 0.153 | * | 0.129 | |
Micropore area | m2g-1 | * | 638 | 765 | 618 | * | 633 | 679 | 498 | * | 380 | * | 322 | |
External surface area | m2g-1 | * | 46 | 79 | 89 | * | 56 | 58 | 50 | * | 25 | * | 22 | |
DFT | ||||||||||||||
Pore volume | cm3g-1 | 0.0002 | 0.237 | 0.292 | 0.247 | * | 0.238 | 0.254 | 0.190 | * | 0.140 | * | 0.119 | |
Micropores | cm3g-1 | 0.0002 | 0.237 | 0.291 | 0.240 | * | 0.237 | 0.254 | 0.187 | * | 0.139 | * | 0.118 | |
Mesopores | cm3g-1 | 0 | 0 | 0.001 | 0.007 | * | 0.001 | 0 | 0.002 | * | 0.001 | * | 0.001 | |
Macropores | cm3g-1 | 0 | 0 | 0 | 0 | * | 0 | 0 | 0.001 | * | 0 | * | 0 | |
Micropores | % | 100 | 100 | 99.7 | 97.2 | * | 99.6 | 100 | 98.4 | * | 99.3 | * | 99.2 | |
Mesopores | % | 0 | 0 | 0.3 | 2.8 | * | 0.4 | 0 | 1.1 | * | 0.7 | * | 0.8 | |
Macropores | % | 0 | 0 | 0 | 0 | * | 0 | 0 | 0.5 | * | 0 | * | 0 | |
* Values were too low to be measure |
Sample | Elastic modulus [MPa] | Compressive strength [MPa] | Densities [g/cm3] | |
Matured foams | TFFPM | 0.0022 | 0.04 | 0.05 |
TFFZnM | 0.0134 | 0.10 | 0.15 | |
TFFBM | 0.0287 | 0.10 | 0.29 | |
Carbonized foams | TFFPC1 | 0.0095 | 0.18 | 0.05 |
TFFPC2 | 0.0063 | 0.14 | 0.05 | |
TFFPC4 | 0.0086 | 0.16 | 0.05 | |
ZnCl2 enforced foams | TFFZnA1 | 0.0229 | 0.21 | 0.10 |
TFFZnA2 | 0.0085 | 0.23 | 0.10 | |
TFFZnA4 | 0.0369 | 0.55 | 0.10 | |
Boric acid enforced foams | TFFBA1 | 0.0074 | 0.13 | 0.16 |
TFFBA2 | 0.0098 | 0.20 | 0.23 | |
TFFBA4 | 0.0071 | 0.26 | 0.13 |