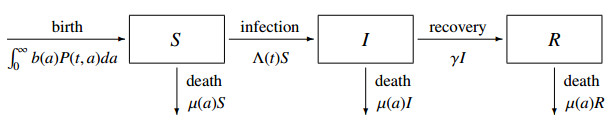
Nanomaterials integration within construction materials could promote the generation of more sophisticated structural materials, as it imbues reinforcement at the nanoscale. This research adopted experimental approaches to assess the influence of metallic nanomaterials on the performance of cementitious composites with various ratios of boric acid (1%, 3%, and 5% by sand's weight) and lime (0.5%, 1.5%, and 2.5% by sand's weight), respectively, for use in construction infrastructure facilities. This research provides valuable insight into the potential of using boric acid and lime as well as metallic nanomaterials to strengthen cement-based composites. Initial curing stages revealed a notable decrease in compressive strength attributed to the inhibitory effects of boric acid and lime on cement hydration. However, the introduction of TiO2 nanoparticles demonstrated significant enhancements in compressive strength and durability. Statistical analysis emphasized the significance of nanomaterials in augmenting compressive strength, with implications for long-term performance. This study has shown that the addition of nano-titanium dioxide TiO2 can significantly enhance the compressive strength of Portland cement mortars, particularly when used in conjunction with appropriate ratios of boric acid and lime. The results of the 7 days test indicated that the inclusion of boric acid and lime in the cement mortars significantly decreased the compressive strength. However, the addition of nano-TiO2 to cement mortars containing 1% boric acid and 0.5% lime resulted in a 31-fold increase in compressive strength compared to cementitious composites without nano-TiO2. In contrast, the compressive strength significantly increased by 1.2 times, 85.3 times, and 65.1 times, respectively, after 56 days for the addition of boric acid (1%, 3%, and 5%) with lime (0.5%, 1.5%, and 2.5%), respectively, in the presence of nano-TiO2, compared to the 7 days strength. The results also illustrated that, in general, the incorporation of various types of nano-TiO2 into cementitious composites containing boric acid and lime increases their compressive strength as the ratios of boric acid and lime increase, as long as sufficient curing time is allowed.
Citation: Ahmed Al-Ramthan, Ruaa Al Mezrakchi. Investigation of cementitious composites reinforced with metallic nanomaterials, boric acid, and lime for infrastructure enhancement[J]. AIMS Materials Science, 2024, 11(3): 495-514. doi: 10.3934/matersci.2024025
[1] | Kento Okuwa, Hisashi Inaba, Toshikazu Kuniya . Mathematical analysis for an age-structured SIRS epidemic model. Mathematical Biosciences and Engineering, 2019, 16(5): 6071-6102. doi: 10.3934/mbe.2019304 |
[2] | Kento Okuwa, Hisashi Inaba, Toshikazu Kuniya . An age-structured epidemic model with boosting and waning of immune status. Mathematical Biosciences and Engineering, 2021, 18(5): 5707-5736. doi: 10.3934/mbe.2021289 |
[3] | Mostafa Adimy, Abdennasser Chekroun, Claudia Pio Ferreira . Global dynamics of a differential-difference system: a case of Kermack-McKendrick SIR model with age-structured protection phase. Mathematical Biosciences and Engineering, 2020, 17(2): 1329-1354. doi: 10.3934/mbe.2020067 |
[4] | Hui Cao, Dongxue Yan, Ao Li . Dynamic analysis of the recurrent epidemic model. Mathematical Biosciences and Engineering, 2019, 16(5): 5972-5990. doi: 10.3934/mbe.2019299 |
[5] | Zhiping Liu, Zhen Jin, Junyuan Yang, Juan Zhang . The backward bifurcation of an age-structured cholera transmission model with saturation incidence. Mathematical Biosciences and Engineering, 2022, 19(12): 12427-12447. doi: 10.3934/mbe.2022580 |
[6] | Xiaohong Tian, Rui Xu, Ning Bai, Jiazhe Lin . Bifurcation analysis of an age-structured SIRI epidemic model. Mathematical Biosciences and Engineering, 2020, 17(6): 7130-7150. doi: 10.3934/mbe.2020366 |
[7] | Fang Zhang, Wenzhe Cui, Yanfei Dai, Yulin Zhao . Bifurcations of an SIRS epidemic model with a general saturated incidence rate. Mathematical Biosciences and Engineering, 2022, 19(11): 10710-10730. doi: 10.3934/mbe.2022501 |
[8] | Abdennasser Chekroun, Mohammed Nor Frioui, Toshikazu Kuniya, Tarik Mohammed Touaoula . Global stability of an age-structured epidemic model with general Lyapunov functional. Mathematical Biosciences and Engineering, 2019, 16(3): 1525-1553. doi: 10.3934/mbe.2019073 |
[9] | Maria Guadalupe Vazquez-Peña, Cruz Vargas-De-León, Jorge Velázquez-Castro . Global stability for a mosquito-borne disease model with continuous-time age structure in the susceptible and relapsed host classes. Mathematical Biosciences and Engineering, 2024, 21(11): 7582-7600. doi: 10.3934/mbe.2024333 |
[10] | Yicang Zhou, Zhien Ma . Global stability of a class of discrete age-structured SIS models with immigration. Mathematical Biosciences and Engineering, 2009, 6(2): 409-425. doi: 10.3934/mbe.2009.6.409 |
Nanomaterials integration within construction materials could promote the generation of more sophisticated structural materials, as it imbues reinforcement at the nanoscale. This research adopted experimental approaches to assess the influence of metallic nanomaterials on the performance of cementitious composites with various ratios of boric acid (1%, 3%, and 5% by sand's weight) and lime (0.5%, 1.5%, and 2.5% by sand's weight), respectively, for use in construction infrastructure facilities. This research provides valuable insight into the potential of using boric acid and lime as well as metallic nanomaterials to strengthen cement-based composites. Initial curing stages revealed a notable decrease in compressive strength attributed to the inhibitory effects of boric acid and lime on cement hydration. However, the introduction of TiO2 nanoparticles demonstrated significant enhancements in compressive strength and durability. Statistical analysis emphasized the significance of nanomaterials in augmenting compressive strength, with implications for long-term performance. This study has shown that the addition of nano-titanium dioxide TiO2 can significantly enhance the compressive strength of Portland cement mortars, particularly when used in conjunction with appropriate ratios of boric acid and lime. The results of the 7 days test indicated that the inclusion of boric acid and lime in the cement mortars significantly decreased the compressive strength. However, the addition of nano-TiO2 to cement mortars containing 1% boric acid and 0.5% lime resulted in a 31-fold increase in compressive strength compared to cementitious composites without nano-TiO2. In contrast, the compressive strength significantly increased by 1.2 times, 85.3 times, and 65.1 times, respectively, after 56 days for the addition of boric acid (1%, 3%, and 5%) with lime (0.5%, 1.5%, and 2.5%), respectively, in the presence of nano-TiO2, compared to the 7 days strength. The results also illustrated that, in general, the incorporation of various types of nano-TiO2 into cementitious composites containing boric acid and lime increases their compressive strength as the ratios of boric acid and lime increase, as long as sufficient curing time is allowed.
In the field of mathematical epidemiology, the SIR epidemic model is known as one of the most basic epidemic models, in which the host population is divided into three classes called susceptible, infective and removed [1]. In the study of epidemic models, the basic reproduction number R0 is one of the key concepts, and it is defined by the expected value of secondary cases produced by a typical infective individual in a totally susceptible population [2]. Mathematically, R0 is defined by the spectral radius of the next generation operator, and the method of numerical computation of R0 has been studied for structured epidemic models [3]. In a simple SIR epidemic model given by a system of ordinary differential equations, R0 completely determines the model dynamics in the sense of global stability of each equilibrium: If R0≤1, then the disease-free equilibrium is globally asymptotically stable, whereas if R0>1, then the endemic equilibrium is globally asymptotically stable [4, Section 5.5.2]. On the other hand, in some more complicated epidemic models, a stable endemic equilibrium can exist even if R0<1 due to a backward bifurcation [5]. Also, an endemic equilibrium can be destabilized, and a stable periodic solution can arise for R0>1 due to a Hopf bifurcation [6]. Periodic solutions in epidemic models have attracted much attention because they can describe non-seasonal oscillations of epidemics. Some of the known causes of the periodicity in epidemic models are periodic coefficients, time delay, nonlinear incidence and age structure [7,8,9,10]. In this study, we consider the periodicity in an age-structured SIR epidemic model. Age-structured epidemic models have been widely applied for epidemiological considerations in the era of COVID-19 [11].
In the field of mathematical epidemiology, the time elapsed since the infection is called the infection age, whereas the time elapsed since the birth is called the chronological age. For an infection age-structured SIR epidemic model, a complete threshold property of R0 in the sense of the global stability of each equilibrium was shown by constructing a suitable Lyapunov function [12]. In contrast, for a chronological age-structured SIR epidemic model, the complete threshold property of R0 does not hold in general. More precisely, although the global stability of the disease-free equilibrium for R0<1 was proved in [13], some additional conditions were needed to guarantee the local or global asymptotic stability of the endemic equilibrium for R0>1 [13,14], and the possibility of the instability of the endemic equilibrium for R0>1 was studied in [15,16,17,18].
In [15], Thieme showed that the unique endemic equilibrium can be unstable for R0>1 in a chronological age-structured SIR epidemic model with age-dependent infectivity. However, the existence of periodic solutions and the occurrence of Hopf bifurcation have not yet been proved for this model. The purpose of this study is to tackle this problem when the transmission rate has a specific form. More precisely, we assume that the transmission rate is a shifted exponential function (see (A5) in the next section) and perform a Hopf bifurcation analysis regarding the infimum of the support of the function as a bifurcation parameter. Epidemiologically, such a shifted exponential function represents the case where infected people do not have infectivity until a certain critical age, and the infectivity decreases in an exponential sense after the critical age. This function enables us to consider a special case studied in [15], where the product of the transmission rate and the stable age distribution is highly concentrated in a particular age class. In this paper, we obtain concrete sufficient conditions for a Hopf bifurcation.
This paper is organized as follows: In Section 2, we introduce the model in this study. In Section 3, we give some preliminaries for the analysis, including the existence and uniqueness of the endemic equilibrium for R0>1. In Section 4, we perform a Hopf bifurcation analysis for a special case where the force of infection in the steady state is equal to the removal rate. We show that there always exists a critical value such that a Hopf bifurcation occurs when the bifurcation parameter reaches it. In Section 5, we perform a more general analysis for the case where the force of infection in the steady state is not equal to the removal rate. We obtain a similar Hopf bifurcation result as in Section 4 when the distance between the force of infection and the removal rate is sufficiently small. Moreover, we numerically confirm a special case where the stability switch of the endemic equilibrium occurs more than once. Finally, Section 6 is devoted to a discussion.
Let S(t,a), I(t,a) and R(t,a) be the susceptible, infective and removed populations of age a at time t, respectively. In this paper, we consider the following SIR epidemic model with chronological age structure:
{(∂∂t+∂∂a)S(t,a)=−Λ(t)S(t,a)−μ(a)S(t,a),t>0, a>0,(∂∂t+∂∂a)I(t,a)=Λ(t)S(t,a)−[μ(a)+γ]I(t,a),t>0, a>0,(∂∂t+∂∂a)R(t,a)=γI(t,a)−μ(a)R(t,a),t>0, a>0,S(t,0)=∫∞0b(a)P(t,a)da,I(t,0)=0,R(t,0)=0,t>0, | (2.1) |
where μ(a) is the mortality rate, γ is the removal rate, b(a) is the birth rate, P(t,a):=S(t,a)+I(t,a)+R(t,a) is the population age density, and
Λ(t):=1∫∞0P(t,a)da∫∞0β(a)I(t,a)da |
is the force of infection with the transmission rate β(a). We assume γ>0, and the following
(A1) μ∈L1+,loc(0,∞), and ∫∞0μ(a)da=∞.
(A2) ∫∞0b(a)ℓ(a)da=1, where ℓ(a):=e−∫a0μ(σ)dσ is the survival probability.
(A3) The population has attained the stable age distribution, that is, P(t,a)=P∗(a):=Nℓ(a)/L for all t>0 and a>0, where N>0 is the stationary population size, and L:=∫∞0ℓ(a)da is the life expectancy.
Let
˜S(t,a):=S(t,a)P∗(a),˜I(t,a):=I(t,a)P∗(a). |
For notational simplicity, dropping the tildes on ˜S and ˜I, we obtain the following normalized SI system:
{(∂∂t+∂∂a)S(t,a)=−Λ(t)S(t,a),t>0, a>0,(∂∂t+∂∂a)I(t,a)=Λ(t)S(t,a)−γI(t,a),t>0, a>0,S(t,0)=1,I(t,0)=0,t>0, | (2.2) |
where
Λ(t)=1N∫∞0β(a)P∗(a)I(t,a)da. |
Note that these S and I are the normalized age-densities satisfying 0≤S,I≤1, and we can omit the equation of R as it does not affect the dynamics of system (2.2).
In [15], Thieme investigated the stability of the endemic equilibrium of system (2.2) when it uniquely exists. He analytically showed that it can be destabilized if β(a)P∗(a) is highly concentrated in a particular age class. However, the problem of the existence of periodic solutions when the endemic equilibrium is unstable was unsettled. In this paper, we deal with this problem by applying the method of local Hopf bifurcation theory. In [15], it was assumed that there exist constants c1,c2>0 such that β(a)ℓ(a)≤c1e−c2a for all a>0. In this paper, we make the following additional assumptions:
(A4) μ(a)=μ>0 for all a>0.
(A5) There exist β0>0 and τ,k≥0 such that
β(a)={0,a<τ,β0e−ka,a≥τ. |
In other words, the transmission rate β(a) is a shifted exponential function. One can then see that β(a)ℓ(a)≤c1e−c2a for all a>0 holds for c1=β0 and c2=μ+k. If both β0 and k are large, we can say that β(a)P∗(a) is highly concentrated in a particular age τ as in the case studied in [15]. Here, we remark that we can consider a different situation where β(a)P∗(a) is exponentially distributed for a≥τ. Regarding τ as a bifurcation parameter, we investigate the existence of a critical value τc>0 such that a Hopf bifurcation occurs, and a periodic solution bifurcates from the endemic equilibrium when τ=τc.
Let X:=L1(0,a†) and X+:=L1+(0,a†). It is easy to see that system (2.2) always has the disease-free equilibrium E0=(1,0)∈X+×X+. Let E∗=(S∗,I∗) denote an endemic equilibrium of system (2.2). It then holds
{dS∗(a)da=−Λ∗S∗(a),a>0,dI∗(a)da=Λ∗S∗(a)−γI∗(a),a>0,S∗(0)=1,I∗(0)=0, | (3.1) |
where the endemic force of infection obeys
Λ∗=1N∫∞0β(a)P∗(a)I∗(a)da. | (3.2) |
Solving (3.1), we obtain
S∗(a)=e−Λ∗a,I∗(a)=∫a0e−γ(a−σ)Λ∗S∗(σ)dσ=Λ∗e−γa∫a0e(γ−Λ∗)σdσ. | (3.3) |
Substituting the equation of I∗ into the right-hand side of (3.2) and dividing both sides by Λ∗, we obtain
1=1N∫∞0β(a)P∗(a)e−γa∫a0e(γ−Λ∗)σdσda. | (3.4) |
Since the right-hand side of (3.4) is monotone decreasing for Λ∗, we see that a unique Λ∗>0 satisfying (3.4) exists if and only if R0>1, where
R0=1N∫∞0β(a)P∗(a)e−γa∫a0eγσdσda=1γN∫∞0β(a)P∗(a)(1−e−γa)da |
is the basic reproduction number [2] for system (2.2). More precisely, we obtain the following proposition.
Proposition 3.1. If R0>1, then system (2.2) has a unique endemic equilibrium E∗=(S∗,I∗)∈X+×(X+∖{0}).
Proof. As explained above, if R0>1, then there exists a unique Λ∗>0 such that (3.4) is satisfied. We then obtain S∗(a) and I∗(a) from (3.3). This completes the proof.
In what follows, we assume R0>1 and investigate the local stability of the endemic equilibrium E∗. Let
U(t,a):=S(t,a)−S∗(a),V(t,a):=I(t,a)−I∗(a), |
be the perturbation from E∗. We then have the following linearized system.
{(∂∂t+∂∂a)U(t,a)=−Λ∗U(t,a)−S∗(a)N∫∞0β(a)P∗(a)V(t,a)da,t>0, a>0,(∂∂t+∂∂a)V(t,a)=Λ∗U(t,a)+S∗(a)N∫∞0β(a)P∗(a)V(t,a)da−γV(t,a),t>0, a>0,U(t,0)=0,V(t,0)=0,t>0. | (3.5) |
Substituting U(t,a)=eλtu(a) and V(t,a)=eλtv(a)(λ∈C) into (3.5) and dividing each equation by eλt, we have
{(λ+dda)u(a)=−Λ∗u(a)−wS∗(a),a>0,(λ+dda)v(a)=Λ∗u(a)+wS∗(a)−γv(a),a>0,u(0)=0,v(0)=0,w=1N∫∞0β(a)P∗(a)v(a)da. | (3.6) |
We first show that λ=0 is not an eigenvalue.
Lemma 3.1. If λ=0, then there exists no (u,v)≠(0,0) satisfying (3.6).
Proof. For λ=0, recalling that S∗(a)=e−Λ∗a, we obtain
u(a)=∫a0e−Λ∗(a−σ)[−wS∗(σ)]dσ=−we−Λ∗aa,v(a)=∫a0e−γ(a−σ)[Λ∗u(σ)+wS∗(σ)]dσ=we−γa∫a0e(γ−Λ∗)σ(1−Λ∗σ)dσ. |
Substituting the equation of v(a) into w=N−1∫∞0β(a)P∗(a)v(a)da and dividing both sides by w, we have
1=1N∫∞0β(a)P∗(a)e−γa∫a0e(γ−Λ∗)σ(1−Λ∗σ)dσda. |
However, by (3.4), we have
1N∫∞0β(a)P∗(a)e−γa∫a0e(γ−Λ∗)σ(−Λ∗σ)dσda=0, |
which is a contradiction. This completes the proof.
By Lemma 3.1, we can focus on λ≠0. Recalling that S∗(a)=e−Λ∗a, we obtain
u(a)=−w∫a0e−(λ+Λ∗)(a−σ)S∗(σ)dσ=−we−Λ∗a1−e−λaλ,v(a)=∫a0e−(λ+γ)(a−σ)[Λ∗u(σ)+wS∗(σ)]dσ=we−(λ+γ)a∫a0e(λ+γ−Λ∗)σ(1−Λ∗1−e−λσλ)dσ=we−(λ+γ)aλ∫a0[(λ−Λ∗)e(λ+γ−Λ∗)σ+Λ∗e(γ−Λ∗)σ]dσ. |
Substituting the equation of v(a) into w=∫∞0β(a)P∗(a)v(a)da and dividing both sides by w, we have
1=1N∫∞0β(a)P∗(a)e−(λ+γ)aλ∫a0[(λ−Λ∗)e(λ+γ−Λ∗)σ+Λ∗e(γ−Λ∗)σ]dσda. |
Under assumptions (A4) and (A5), this equation can be rewritten as
1=β1λ∫∞τe−(λ+p)a∫a0[(λ−Λ∗)e(λ+γ−Λ∗)σ+Λ∗e(γ−Λ∗)σ]dσda, | (3.7) |
where β1:=β0/L and p:=k+μ+γ. Eq (3.7) is the starting point of our Hopf bifurcation analysis.
We now consider a special case where Λ∗=γ. In this case, Eq (3.7) can be rewritten as
1=β1λ∫∞τe−(λ+p)a∫a0[(λ−γ)eλσ+γ]dσda. | (4.1) |
Since we are interested in a Hopf bifurcation at which Reλ=0, we restrict our attention to λ such that Reλ>−p. We can then rewrite (4.1) as
1=β1λ∫∞τe−(λ+p)a[λ−γλ(eλa−1)+γa]da=β1λ2[(λ−γ)(e−pτp−e−(λ+p)τλ+p)+γλe−(λ+p)τλ+p(τ+1λ+p)]. | (4.2) |
On the other hand, from Eq (3.4), we have
1=β1∫∞τae−pada=β1(τp+1p2)e−pτ, |
and thus,
β1=p2epτpτ+1. | (4.3) |
Substituting (4.3) into (4.2), we obtain
1=p2(pτ+1)λ2[(λ−γ)(1p−e−λτλ+p)+γλe−λτλ+p(τ+1λ+p)]=1(pτ+1)λ2(λ+p)2{p(λ−γ)(λ+p)2+p2[−(λ−γ)(λ+p)+γτλ(λ+p)+γλ]e−λτ}, |
which is equivalent to
(pτ+1)λ2(λ+p)2=p(λ−γ)(λ+p)2+p2[−(λ−γ)(λ+p)+γτλ(λ+p)+γλ]e−λτ. |
Hence, we obtain the following characteristic equation:
a4λ4+a3λ3+a2λ2+a1λ+a0+(b2λ2+b1λ+b0)e−λτ=0, | (4.4) |
where
a4=pτ+1,a3=2p2τ+p,a2=p3τ−p2+γp,a1=−p3+2γp2,a0=γp3,b2=−γp2τ+p2,b1=−γp3τ+p3−2γp2,b0=−γp3. |
Note that although λ=0 satisfies (4.4), we can disregard it by virtue of Lemma 3.1. We now prove the following lemma.
Lemma 4.1. If τ=0, then all nonzero roots λ of the characteristic Eq (4.4) have negative real parts.
Proof. If τ=0, Eq (4.4) can be rewritten as λ4+pλ3+γpλ2=0. As λ≠0, dividing both sides by λ2, we have λ2+pλ+γp=0. We then easily see that all λ have negative real parts because p and γp are strictly positive. This completes the proof.
Lemmas 3.1 and 4.1 imply that the endemic equilibrium E∗, which uniquely exists under R0>1, is locally asymptotically stable if τ=0. By the continuity, E∗ is locally asymptotically stable for small τ>0. In what follows, we investigate the existence of a τc>0 such that E∗ is locally asymptotically stable for τ∈[0,τc) and destabilized at τ=τc.
We now seek a pair of simple pure imaginary roots λ=±iω (ω>0) of the characteristic Eq (4.4). Since all coefficients in (4.4) are real, if λ=iω satisfies (4.4), then λ=−iω also satisfies (4.4). Therefore, we focus on λ=iω. Substituting λ=iω into (4.4), we have
a4ω4−ia3ω3−a2ω2+ia1ω+a0+(−b2ω2+ib1ω+b0)e−iωτ=0. |
As e−iωτ=cosωτ−isinωτ, we obtain the following two equations for real and imaginary parts, respectively:
{a4ω4−a2ω2+a0=(b2ω2−b0)cosωτ−b1ωsinωτ,a3ω3−a1ω=b1ωcosωτ+(b2ω2−b0)sinωτ. | (4.5) |
Taking squares of both sides in the two equations of (4.5) and adding them, we obtain
(a4ω4−a2ω2+a0)2+(a3ω3−a1ω)2=(b2ω2−b0)2+b21ω2. |
Rearranging this equation, we obtain
ω2[c3(ω2)3+c2(ω2)2+c1ω2+c0]=0 | (4.6) |
(note that a20−b20=0), where
c3=a24,c2=−2a2a4+a23,c1=2a0a4+a22−2a1a3−b22,c0=−2a0a2+a21+2b0b2−b21. |
As we can rule out ω=0 by Lemma 3.1, dividing both sides of (4.6) by ω2, we obtain
c3(ω2)3+c2(ω2)2+c1ω2+c0=0. | (4.7) |
On the existence of a positive ω>0 satisfying (4.7), we prove the following lemma:
Lemma 4.2. The Eq (4.7) has a unique nonzero positive root ω>0.
Proof. Let h(x)=c3x3+c2x2+c1x+c0. It suffices to show that h(x)=0 has a unique positive root x∗>0, for which ω=√x∗>0 is the desired root of (4.7). It is obvious that c3=(pτ+1)2>0. Moreover, we have, using p=k+μ+γ>γ,
c2=−2(p3τ−p2+γp)(pτ+1)+(2p2τ+p)2=2p4τ2+4p3τ+3p2−2γp(pτ+1)>2p4τ2+4p3τ+3p2−2p2(pτ+1)=2p4τ2+2p3τ+p2>0, |
and, using b0=−a0 and b1=−γp3τ−a1,
c0=−2a0(a2+b2)+a21−(γp3τ+a1)2=−2γp3(p3τ+γp−γp2τ)−γ2p6τ2−2γp3τa1=−2γp3(p3τ+γp−γp2τ)−γ2p6τ2−2γp3τ(−p3+2γp2)=−2γ2p4−2γ2p5τ−γ2p6τ2<0. |
c0<0 and c2,c3>0 imply that h(x)=0 has a unique positive root x∗>0. This completes the proof.
The following corollary will be used in the proof of the transversality:
Corollary 4.1. Let h(x) and x∗ be as defined in the proof of Lemma 4.2. Then, h′(x∗)>0.
Proof. The assertion immediately follows from c0<0 and c2,c3>0.
Note that since a2,a3,a4,b1 and b2 in (4.4) depend on τ, the root ω also depends on τ: ω=ω(τ). Since (4.7) is a necessary condition for λ=iω to be a root of (4.4), we have to find a τc>0 such that ω(τc) satisfies not only (4.7) but also (4.5). By (4.5), we have
{cosωτ=(a4ω4−a2ω2+a0)(b2ω2−b0)+(a3ω3−a1ω)b1ω(b2ω2−b0)2+b21ω2=:φ,sinωτ=−(a4ω4−a2ω2+a0)b1ω+(a3ω3−a1ω)(b2ω2−b0)(b2ω2−b0)2+b21ω2=:ψ. | (4.8) |
We define θ∈(0,2π] by
θ:={arccosφ,ψ>0,2π−arccosφ,ψ≤0. |
It then follows from (4.8) that ωτ=θ, and thus,
τ=θω. |
Note that φ, ψ and θ also depend on τ. Let f(τ):=θ(τ)/ω(τ). Then, the desired τc is a positive fixed point of f: τc=f(τc). Before proving the existence of such τc, we give the following lemma:
Lemma 4.3. For coefficients c0,c1,c2 and c3, it holds that
limτ→∞1(pτ)2(c0c1c2c3)=(−γ2p4p2(p2−γ2)2p21). |
Proof. The convergence of ci/(pτ)2 (i=0,2,3) can be easily checked by using the expressions of c0,c2 and c3 given in the proof of Lemma 4.2. For c1, we have
c1=2γp3(pτ+1)+(p3τ−p2+γp)2−2(−p3+2γp2)(2p2τ+p)−(−γp2τ+p2)2=2γp4τ+2γp3+p6τ2+p4+γ2p2−2p5τ+2γp4τ−2γp3+4p5τ+2p4−8γp4τ−4γp3−γ2p4τ2+2γp4τ−p4=−2γp4τ−4γp3+p6τ2+γ2p2+2p5τ+2p4−γ2p4τ2=(p2−γ2)p4τ2+2(p−γ)p4τ−4γp3+γ2p2+2p4=p2[(p2−γ2)p2τ2+2(p−γ)p2τ−4γp+γ2+2p2], |
and hence, limτ→∞c1/(pτ)2=p2(p2−γ2). This completes the proof.
We now prove the following proposition:
Proposition 4.1. There exists a τc>0 such that λ=±iω(τc) is a pair of simple pure imaginary roots of the characteristic Eq (4.4).
Proof. By Lemma 4.2 and its proof, one can see that ω(τ) is continuous and finite for all τ≥0. Thus, θ(τ) and f(τ) are also continuous and finite for all τ≥0. Moreover, it follows that f(0)=θ(0)/ω(0)>0. Hence, by the continuity, if limτ→∞f(τ)<∞, then we can conclude that there exists a τc>0 such that τc=f(τc).
Let {τn}∞n=1 be an increasing sequence in (0,∞), and let ωn:=ω(τn). By dividing both sides of (4.7) by (pτn)2, we have
c3(pτn)2(ω2n)3+c2(pτn)2(ω2n)2+c1(pτn)2ω2n+c0(pτn)2=0. |
By Lemma 4.3, we see that {ωn}∞n=1 converges to ω∞, which is the unique positive root of the following equation:
(ω2∞)3+2p2(ω2∞)2+p2(p2−γ2)ω2∞−γ2p4=0. |
Thus, we have limτ→∞f(τ)≤2π/ω∞<∞. This completes the proof.
Proposition 4.1 guarantees the existence of a pair of pure imaginary roots at τ=τc>0.
We next investigate the transversality condition at τ=τc, that is,
dReλdτ|λ=iωc>0, | (4.9) |
where ωc:=ω(τc). Following a general result given by [19], we define g(τ):=τ−f(τ). Now, we have the following proposition.
Proposition 4.2. If g′(τc)>0, then (4.9) holds.
Proof. Let y(ω) be the left-hand side of (4.6):
y(ω):=ω2[c3(ω2)3+c2(ω2)2+c1ω2+c0]=ω2h(ω2). |
Following a calculation in [19, Proof of Theorem 2.2] for a general characteristic equation, we can obtain a similar result as in [19, Theorem 2.2]:
sign{dReλdτ|λ=iωc}=sign{∂y(ωc)∂ω} sign{g′(τc)}. |
Note that from Lemma 4.2 and Corollary 4.1, it follows that h(ω2c)=0 and h′(ω2c)>0. We then have that
∂y(ωc)∂ω=2ωch(ω2c)+ω2ch′(ω2c)2ωc=2ω3ch′(ω2c)>0. |
Hence, we have
sign{dReλdτ|λ=iωc}=sign{g′(τc)}. |
This completes the proof.
As shown in the proof of Proposition 4.1, we have f(0)>0 and limτ→∞f(τ)<∞. This implies that there exists at least one τc>0 such that g(τc)=τc−f(τc)=0 and g′(τc)>0. That is, a Hopf bifurcation is always possible in model (2.2) with R0>1 and Λ∗=γ. More precisely, we obtain the following main result:
Proposition 4.3. Suppose that β1 depends on τ as for (4.3). Then, R0>1 and Λ∗=γ hold for all τ≥0, and there exists a τc>0 such that a pair of simple pure imaginary roots ±iω(τc) ( = ±iωc) satisfies the characteristic Eq (4.4) and crosses the imaginary axis from left to right as τ increases over τc.
Under the condition in Proposition 4.3, there always exists a critical value τc>0 such that a Hopf bifurcation occurs, and a periodic solution arises when the infimum τ of the support of function β(a) reaches τ=τc. In the next subsection, we numerically confirm this result.
For simplicity, we fix μ=γ=k=1. Note that these parameters are technically chosen in order to confirm the validity of Proposition 4.3, and thus, there is no biological reason for this choice. In this case, p=3, and we can numerically calculate functions ω(τ), θ(τ), f(τ) and g(τ), and τc≈3.84 as shown in Figure 2. Note that L=1/μ=1, and the force of infection is
Λ(t)=1N∫∞0β(a)P∗(a)I(t,a)da=β0L∫∞τe−(k+μ)aI(t,a)da=β0∫∞τe−(k+μ)aI(t,a)da. |
It then follows from (4.3) that β0=β1=p2epτ/(pτ+1). For the normalized system (2.2), we choose the initial condition as S(0,a)=0.99 and I(0,a)=0.01 for all a>0.
For τ=3.7<τc, we see in Figure 3 that the numerical solutions of I(t,a) and Λ(t) converge to the positive steady states I∗(a) and Λ∗, respectively. In particular, we can confirm that Λ∗=γ=1 in Figure 3 (b).
For τ=4>τc, we see in Figure 4 that the numerical solutions of I(t,a) and Λ(t) do not converge to the positive steady states but to positive periodic solutions.
Thus, we can conclude that a Hopf bifurcation occurs at τ=τc. In this case, the outbreaks occur periodically if the length τ of the period with no infectivity is sufficiently large.
We next consider the case where Λ∗≠γ. Let q:=γ−Λ∗≠0. Note that p−q=k+μ+Λ∗>0. As in the previous section, since we are interested in a Hopf bifurcation at which Reλ=0, we restrict our attention to λ such that Reλ>max(−p,−(p−q)) and λ≠−q. Equation (3.7) can then be rewritten as
1=β1λ∫∞τe−(λ+p)a∫a0[(λ−Λ∗)e(λ+q)σ+Λ∗eqσ]dσda=β1λ∫∞τ[λ−Λ∗λ+q(e−(p−q)a−e−(λ+p)a)+Λ∗q(e−(λ+p−q)a−e−(λ+p)a)]da=β1λ[λ−Λ∗λ+q(e−(p−q)τp−q−e−(λ+p)τλ+p)+Λ∗q(e−(λ+p−q)τλ+p−q−e−(λ+p)τλ+p)]. | (5.1) |
On the other hand, Eq (3.4) can be rewritten as
1=β1∫∞τe−pa∫a0eqσdσda=β1q∫∞τ(e−(p−q)a−e−pa)da=β1q(e−(p−q)τp−q−e−pτp). |
Thus, we have
β1=pq(p−q)epτpeqτ−(p−q). | (5.2) |
Let Q=Q(q,τ):=(eqτ−1)/q. Note that Q(q,τ)>0 for all q∈R∖{0} and τ>0, and
limq→0Q(q,τ)=τ for each fixed τ>0,limτ→0Q(q,τ)=0 for each fixed q≠0. |
(5.2) can then be rewritten as
β1=p(p−q)epτpQ+1. | (5.3) |
Substituting this β1 into (5.1) and rearranging it, we obtain
(pQ+1)λ=p(p−q)[λ−Λ∗λ+q(eqτp−q−e−λτλ+p)+Λ∗q(e−(λ−q)τλ+p−q−e−λτλ+p)]=peqτλ−Λ∗λ+q+p(p−q)[−λ−Λ∗(λ+p)(λ+q)+Λ∗qeqτ(λ+p)−(λ+p−q)(λ+p)(λ+p−q)]e−λτ. |
We then have
(pQ+1)λ−peqτλ−Λ∗λ+q+p(p−q)[λ−Λ∗(λ+p)(λ+q)−Λ∗qeqτ(λ+p)−(λ+p−q)(λ+p)(λ+p−q)]e−λτ=0. |
Multiplying by (λ+p)(λ+q)(λ+p−q) on both sides, we obtain
(pQ+1)λ(λ+p)(λ+q)(λ+p−q)−peqτ(λ−Λ∗)(λ+p)(λ+p−q)+p(p−q){(λ−Λ∗)(λ+p−q)+Λ∗q[(1−eqτ)λ+p−q−peqτ](λ+q)}e−λτ=0. |
Note that eqτ=qQ+1. We then have
(pQ+1)λ(λ+p)(λ+q)(λ+p−q)−p(qQ+1)(λ−Λ∗)(λ+p)(λ+p−q)+p(p−q){(λ−Λ∗)(λ+p−q)−Λ∗(Qλ+pQ+1)(λ+q)}e−λτ=0. |
It can be rewritten as
A4λ4+A3λ3+A2λ2+A1λ+A0+(B2λ2+B1λ+B0)e−λτ=0, | (5.4) |
where
A4=pQ+1,A3=(2p−q)pQ+p,A2=[p(p−q)+Λ∗q]pQ+Λ∗p−(p−q)2,A1=−p(p−q)2+Λ∗(2p−q)p(qQ+1),A0=Λ∗p2(p−q)(qQ+1),B2=p(p−q)(1−Λ∗Q),B1=p(p−q)2−Λ∗p(p−q)(2+pQ+qQ),B0=−Λ∗p2(p−q)(qQ+1). |
We can check that (5.4) is equivalent to (4.4) if q→0. In fact, we have the following lemma:
Lemma 5.1. For each fixed τ>0, it holds that
limq→0(A4,A3,A2,A1,A0,B2,B1,B0)=(a4,a3,a2,a1,a0,b2,b1,b0). | (5.5) |
Proof. For each fixed τ>0, recalling that limq→0(Q,Λ∗)=(τ,γ), we obtain
limq→0A4=pτ+1=a4,limq→0A3=2p2τ+p=a3,limq→0A2=p3τ+γp−p2=a2,limq→0A1=−p3+2γp2=a1,limq→0A0=γp3=a0,limq→0B2=p2(1−γτ)=b2,limq→0B1=p3−γp2(2+pτ)=b1,limq→0B0=−γp3=b0. |
This completes the proof.
By Proposition 4.3 and Lemma 5.1, regarding τ as a bifurcation parameter, we see that a Hopf bifurcation can occur as in Section 4 if |q| is sufficiently small. More precisely, we obtain the following corollary:
Corollary 5.1. Suppose that q≠0, |q| is sufficiently small, and β1 depends on τ as for (5.3). Then, R0>1 and Λ∗=γ−q>0 hold for all τ≥0, and there exists a τc>0 such that a pair of simple pure imaginary roots ±iΩ(τc)(=±iΩc) satisfies the characteristic Eq (5.4) and crosses the imaginary axis from left to right as τ increases over τc.
We next proceed to a more general case where |q| is not small. We can prove the following lemma, which corresponds to Lemma 4.1.
Lemma 5.2. If τ=0, then all roots λ except 0 and −q of the characteristic Eq (5.4) have negative real parts.
Proof. If τ=0, then Q=0, and the characteristic Eq (5.4) can be rewritten as
λ4+pλ3+[q(p−q)+Λ∗p]λ2+Λ∗pqλ=0. |
This equation is equivalent to
λ(λ+q)[λ2+rλ+Λ∗p]=0. |
If λ≠0,−q, then we have
λ2+(p−q)λ+Λ∗p=0. |
We then see that all roots λ have negative real parts because p−q>0 and Λ∗p>0. This completes the proof.
Using Lemma 5.2, we prove the following proposition on the local asymptotic stability of E∗ for τ=0:
Proposition 5.1. If R0>1, q≠0 and τ=0, then the endemic equilibrium E∗ of system (2.2) is locally asymptotically stable.
Proof. By Lemma 5.2, it suffices to show that λ=0 and −q do not affect the stability of E∗. In fact, by Lemma 3.1, λ=0 cannot be a characteristic eigenvalue. If q>0, then λ=−q does not affect the stability of the endemic equilibrium E∗. If q<0, substituting λ=−q into the first equation in (5.1), we obtain, for τ=0,
1=β1−q∫∞0e−(p−q)a[−(q+Λ∗)a+Λ∗q(eqa−1)]da=β1γq∫∞0ae−(p−q)ada+β1Λ∗q2∫∞0[e−(p−q)a−e−(p−2q)a]da=β1γq1(p−q)2+β1Λ∗q2(1p−q−1p−2q)=β1q(p−q)(γp−q−Λ∗p−2q)=β1(p−q−γ)(p−q)2(p−2q). |
Since β1=p(p−q) for τ=0, we have
1=p(p−q−γ)(p−q)(p−2q)<(p−2q)(p−q)(p−q)(p−2q)=1, |
which is a contradiction (note that p<p−2q as q<0). Hence, λ≠−q. This completes the proof.
As in Section 4.1, substituting λ=iΩ (Ω>0) into (5.4), we obtain
A4Ω4−iA3Ω3−A2Ω2+iA1Ω+A0+(−B2Ω2+iB1Ω+B0)e−iΩτ=0. |
Dividing this equation into real and imaginary parts, we have
{A4Ω4−A2Ω2+A0=(B2Ω2−B0)cosΩτ−B1ΩsinΩτ,A3Ω3−A1Ω=B1ΩcosΩτ+(B2Ω2−B0)sinΩτ. | (5.6) |
Taking squares of both sides in the two equations and adding them, we obtain
(A4Ω4−A2Ω2+A0)2+(A3Ω3−A1Ω)2=(B2Ω2−B0)2+B21Ω2. |
Rearranging this equation, we have
Ω2[C3(Ω2)3+C2(Ω2)2+C1Ω2+C0]=0 | (5.7) |
(note that A20−B20=0), where
C3=A24, C2=−2A2A4+A23, C1=2A0A4+A22−2A1A3−B22, C0=−2A0A2+A21+2B0B2−B21. |
By Lemma 3.1, we can rule out Ω=0. Hence, we obtain
C3(Ω2)3+C2(Ω2)2+C1Ω2+C0=0. | (5.8) |
As in Section 4.1, we define H(x):=C3x3+C2x2+C1x+C0. If H(x)=0 has a positive root x∗>0, then Ω=√x∗ satisfies (5.7). To find such x∗, we investigate the signs of coefficients in (5.8). We prove the following lemma:
Lemma 5.3. C2>0 and C3>0 for all τ≥0.
Proof. It is obvious that C3=(pQ+1)2≥1>0 for all τ≥0. On C2, we have
C2=−2A2A4+A23=−2{[p(p−q)+Λ∗q]pQ+Λ∗p−(p−q)2}(pQ+1)+[(2p−q)pQ+p]2=−2{p2(p−q)Q−(p−q)2}(pQ+1)−2Λ∗p(qQ+1)(pQ+1)+[(2p−q)pQ+p]2. | (5.9) |
Recalling that p−q=k+μ+Λ∗>Λ∗ and qQ+1=eqτ>0, we obtain
C2>−2{p2(p−q)Q−(p−q)2}(pQ+1)−2(p−q)p(qQ+1)(pQ+1)+[(2p−q)pQ+p]2={−2[p(p−q)+(p−q)q]+(2p−q)2}(pQ)2+{−2[p(p−q)+(p−q)(p+q)−(p−q)2]+2p(2p−q)}pQ−2[p(p−q)−(p−q)2]+p2=[2(p−q)2+q2](pQ)2+2[(p−q)2+q2]pQ+(p−q)2+q2≥(p−q)2+q2>0, | (5.10) |
for all τ≥0. This completes the proof.
By Lemma 5.3, if C0<0 for all τ≥0, then a similar argument as in the proof of Lemma 4.2 gives the existence of the unique Ω>0 satisfying (5.8). However, unlike the case of Λ∗=γ in Section 4, C0<0 for all τ≥0 does not hold in general. To clarify this point, we investigate a special case where the following additional condition is satisfied:
(A6) γ≫k+μ.
For example, if the reduction rate k of infectivity is small, then (A6) is not so unrealistic because, in many human infectious diseases, the infection period is much shorter than the average life span (that is, γ≫μ). Under assumption (A6), p≈γ, and coefficients in (5.4) can be rewritten as
A4=γQ+1,A3=(2γ−q)γQ+γ,A2=[γ(γ−q)+Λ∗q]γQ+Λ∗γ−(γ−q)2=(γ−q)[(γ+q)γQ+γ−(γ−q)]=(γ−q)[(γ+q)γQ+q],A1=−γ(γ−q)2+Λ∗(2γ−q)γ(qQ+1)=(γ−q)[−γ(γ−q)+(2γ−q)γ(qQ+1)]=γ(γ−q)2qQ+(γ−q)γ2(qQ+1),A0=(γ−q)2γ2(qQ+1),B2=γ(γ−q)(1−Λ∗Q)=(γ−q)[γ−(γ−q)γQ],B1=γ(γ−q)2−Λ∗γ(γ−q)[2+(γ+q)Q]=γ(γ−q)2[−1+(γ+q)Q],B0=−A0 |
(note that Λ∗=γ−q>0). We next prove the following lemma on the sign of C0:
Lemma 5.4. Suppose that (A6) holds. Then, the following properties hold:
(ⅰ) If |q|<γ/√2, then C0<0 for all τ≥0. In particular, C0 is monotone decreasing for τ≥0.
(ⅱ) If q>(√3−1)γ or q<−(√3+1)γ, then C0>0 for all τ≥0. In particular, C0 is monotone increasing for τ≥0.
Proof. Under assumption (A6), C0 can be calculated as
C0=−2A0(A2+B2)+A21−B21=−2(γ−q)3γ2(qQ+1)(2qγQ+q+γ)+γ2(γ−q)2{[(γ−q)qQ+γ(qQ+1)]2−(γ−q)2[(γ+q)Q−1]2}=γ2(γ−q)2{2(q−γ)[2q2γQ2+(q2+3qγ)Q+(q+γ)]+(6γ2q2−4γq3−γ4)Q2+(−2γ3+6γ2q−2q3)Q+2qγ−q2}=γ2(γ−q)2[(2q2−γ2)(γQ)2+2(2q2−γ2)γQ+(q+γ)2−3γ2]. | (5.11) |
If |q|<γ/√2, then 2q2−γ2<0, and thus,
C0<γ2(γ−q)2[(q+γ)2−3γ2]=γ2(γ−q)2[q−(√3−1)γ][q+(√3+1)γ]<0, |
for all τ≥0 (note that √3+1>√3−1>1/√2). The second assertion follows from (5.11) and the fact that ∂Q/∂τ=eqτ>0. This proves (ⅰ).
If q>(√3−1)γ or q<−(√3+1)γ, then 2q2−γ2>0 (note that √3−1>1/√2), and thus,
C0>γ2(γ−q)2[(q+γ)2−3γ2]=γ2(γ−q)2[q−(√3−1)γ][q+(√3+1)γ]>0, |
for all τ≥0. The second assertion follows in a similar way as in (ⅰ). This proves (ⅱ).
Figure 5 shows an example of each case in Lemma 5.4. (k,μ,γ)=(0.01,0.01,1) is fixed so that γ≫k+μ. In Figure 5(a), q=0.95γ/√2, and hence, |q|<γ/√2 holds. In this case, as stated in Lemma 5.4 (ⅰ), we can check that C0=H(0) is negative and monotone decreasing for each τ≥0. By Lemma 5.3, as in Lemma 4.2, there always exists a unique x∗>0 such that H(x∗)=0, and hence, Ω=√x∗ satisfies (5.8). In addition, one can see that H′(x∗)>0.
On the other hand, in Figure 5(b), q=1.1(√3−1)γ>(√3−1)γ. As stated in Lemma 5.4 (ⅱ), we can check that C0=H(0) is positive and monotone increasing for each τ≥0. As shown in this figure, there can exist two positive numbers x∗+>0 and x∗−>0 (x∗+>x∗−) such that H(x∗±)=0. In this case, (5.8) has two positive solutions Ω=√x∗±. In addition, one can see that H′(x∗+)>0 and H′(x∗−)<0.
Note that, as in Section 4, (5.8) is a necessary condition for λ=±iΩ to be a pair of simple pure imaginary roots of the characteristic Eq (5.4). From (5.6), we have
{cosΩτ=(A4Ω4−A2Ω2+A0)(B2Ω2−B0)+(A3Ω3−A1Ω)B1Ω(B2Ω2−B0)2+B21Ω2=:Φ,sinΩτ=−(A4Ω4−A2Ω2+A0)B1Ω+(A3Ω3−A1Ω)(B2Ω2−B0)(B2Ω2−B0)2+B21Ω2=:Ψ, | (5.12) |
and define Θ∈(0,2π] by
Θ:={arccosΦ,Ψ>0,2π−arccosΦ,Ψ≤0. |
It then follows from (5.12) that Ωτ=Θ. For each τ≥0, let F(τ):=Θ(τ)/Ω(τ). Our aim is then to show the existence of a positive fixed point F(τc)=τc>0, which implies that λ=±iΩ(τc) is a pair of simple pure imaginary roots of the characteristic Eq (5.4). To this end, we now show the following lemma:
Lemma 5.5. Suppose that (A6) holds. For coefficients C0,C1,C2 and C3, it holds that
limτ→∞1(γQ)2(C0C1C2C3)=(γ2(γ−q)2(2q2−γ2)−2(γ−q)[(γ−q)γq+q3]2(γ−q)2+q21). |
Proof. Note that limτ→∞Q=∞. It then follows that
limτ→∞C3(γQ)2=limτ→∞(γQ+1)2(γQ)2=1. |
From (5.11), it follows that
limτ→∞C0(γQ)2=limτ→∞γ2(γ−q)2[(2q2−γ2)+2(2q2−γ2)γQ+(q+γ)2−3γ2(γQ)2]=γ2(γ−q)2(2q2−γ2). |
Moreover, replacing p and Λ∗ in (5.9) by γ and γ−q, respectively, we can perform a similar calculation as in (5.10) and obtain
limτ→∞C2(γQ)2=limτ→∞[2(γ−q)2+q2+2(γ−q)2+2q2γQ+(γ−q)2+q2(γQ)2]=2(γ−q)2+q2. |
For C1, we have
C1=2A0A4+A22−2A1A3−B22=2(γ−q)2γ2(qQ+1)(γQ+1)+(γ−q)2[(γ+q)γQ+q]2−2γ(γ−q)[(γ−q)qQ+γ(qQ+1)][(2γ−q)γQ+γ]−(γ−q)2[γ−(γ−q)γQ]2=2(γ−q)γ2(qQ+1)[(γ−q)(γQ+1)−(2γ−q)γQ−γ]+(γ−q)2[4γq(γQ)2+2(γ2+q2)γQ+q2−γ2]−2(γ−q)2qγQ[(2γ−q)γQ+γ]=−2(γ−q)γ2(qQ+1)(γ2Q+q)+(γ−q)2[4γq(γQ)2+2(γ2+q2)γQ+q2−γ2]−2(γ−q)2qγQ[(2γ−q)γQ+γ]=2(γ−q)[−γ2q+2(γ−q)γq−(γ−q)q(2γ−q)](γQ)2+2(γ−q)[−(q2+γ2)γ+(γ−q)(γ2+q2)−(γ−q)qγ]γQ+(γ−q)[−2γ2q+(γ−q)(q2−γ2)]=−2(γ−q)[(γ−q)γq+q3](γQ)2−2(γ−q)[(γ−q)γq+(γ2+q2)q]γQ−(γ−q)[(γ−q)γq+γ3+q3]. |
We then have limτ→∞C1/(γQ)2=−2(γ−q)[(γ−q)γq+q3]. This completes the proof.
Using Lemmas 5.3–5.5, we prove the following proposition on the existence of a pair of simple pure imaginary roots for |q|<γ/√2:
Proposition 5.2. Suppose that (A6) holds, and |q|<γ/√2. Then, there exists a τc>0 such that λ=±iΩ(τc) is a pair of simple pure imaginary roots of the characteristic Eq (5.4).
Proof. By Lemmas 5.3 and 5.4, for each τ≥0, the positive Ω(τ)>0 uniquely exists. Hence, we have F(0)=Θ(0)/Ω(0)>0. As in the proof of Proposition 4.1, by the continuity, it suffices to show that limτ→∞F(τ)<∞.
Let {τn}∞n=1 be an increasing sequence in (0,∞), and let Ωn:=Ω(τn) and Qn:=Q(⋅,τn). By dividing both sides of (5.8) by (γQn)2, we have
C3(γQn)2(Ω2n)3+C2(γQn)2(Ω2n)2+C1(γQn)2Ω2n+C0(γQn)2=0. |
By Lemma 5.5, we see that {Ωn}∞n=1 converges to Ω∞, which is the unique positive root of the following equation:
(Ω2∞)3+[2(γ−q)2+q2](Ω2∞)2−2(γ−q)[(γ−q)γq+q3]Ω2∞+γ2(γ−q)2(2q2−γ2)=0. |
Thus, we have limτ→∞F(τ)≤2π/Ω∞<∞. This completes the proof.
For q>(√3−1)γ or q<−(√3+1)γ, by Lemma 5.4 (ⅱ), C0>0 for all τ≥0, and hence, H(x)=0 may have multiple positive roots x∗±>0 such that H′(x∗+)>0 and H′(x∗−)<0 (see Figure 5(b)). In this case, it seems difficult to show analytically the existence of a pair of simple pure imaginary roots. Instead, we will investigate it numerically in Section 5.3.
As in Section 4.2, we investigate the transversality condition of a Hopf bifurcation. Let G(τ):=τ−F(τ).
Lemma 5.6. Suppose that there exists a τc>0 such that G(τc)=0. Then, the characteristic Eq (5.4) has a pair of simple pure imaginary roots λ=±iΩ(τc)=±iΩc, and
sign{dReλdτ|λ=iΩc}=sign{H′(Ω2c)}sign{G′(τc)}. | (5.13) |
Proof. As in the proof of Proposition 4.2, we have
sign{dReλdτ|λ=iΩc}=sign{∂Y(Ωc)∂ω} sign{G′(τc)}, | (5.14) |
where Y(Ω) is defined by the left-hand side of (5.7):
Y(Ω):=Ω2[C3(Ω2)3+C2(Ω2)2+C1Ω2+C0]=Ω2H(Ω2). |
Now, we have
∂Y(Ωc)∂ω=2Ω2cH(Ω2c)+Ω2cH′(Ω2c)2Ωc=2Ω3cH′(Ω2c) |
(note that H(Ω2c)=0). As Ω3c>0, we then have
sign{∂Y(Ωc)∂ω}=sign{H′(Ω2c)}, |
and hence, (5.13) follows from (5.14). This completes the proof.
In the case of Lemma 5.4 (ⅰ), H(x)=0 has only one positive root x∗>0 such that H′(x∗)>0 (see Figure 5(a)). Therefore, by Lemma 5.6, we see that if λ=±iΩc=±i√x∗ is a pair of simple pure imaginary roots of (5.4), then it crosses the imaginary axis from left to right. This together with Lemma 5.4 (ⅰ) and Proposition 5.2 gives the following main theorem:
Theorem 5.1. Suppose that (A6) holds, q≠0, and |q|<γ/√2. If β1 depends on τ as for (5.3), then R0>1 and Λ∗=γ−q>0 hold for all τ≥0, and there exists a τc>0 such that a pair of simple pure imaginary roots ±iΩ(τc)(=±iΩc) satisfies the characteristic Eq (5.4) and crosses the imaginary axis from left to right as τ increases over τc.
Under the condition in Theorem 5.1, there always exists a critical value τc>0 such that a Hopf bifurcation occurs, and a periodic solution arises at τ=τc. Note that, under assumption (A6), "sufficiently small |q|" in Corollary 5.1 is improved to the inequality |q|<γ/√2 in Theorem 5.1. For the case of Lemma 5.4 (ⅱ), we have the following remark:
Remark 5.1. In the case of Lemma 5.4 (ii), H(x)=0 may have two positive roots x∗+>x∗−>0 such that H′(x∗+)>0>H′(x∗−) (see Figure 5(b)). Therefore, by Lemma 5.6, we see that if λ=±iΩc=±i√x∗+ (resp. ±i√x∗−) is a pair of simple pure imaginary roots of (5.4), then it crosses the imaginary axis from left to right (resp. from right to left). In other words, λ=±i√x∗+ (resp. ±i√x∗−) can lead to the destabilization (resp. stabilization) of the endemic equilibrium E∗.
In other words, in the case of Lemma 5.4 (ⅱ), the stability switch of the endemic equilibrium E∗ can occur more than once. We numerically confirm this point in the next subsection.
Fix the following parameters:
k=μ=0.05,γ=10,p=10.1(=k+μ+γ). |
Note that they are chosen for a technical reason to confirm the validity of Theorem 5.1 and Remark 5.1, and there is no biological justification. We can regard γ≫k+μ, and thus, assumption (A6) holds. For each q∈(−∞,0)∪(0,γ) and τ≥0, set β1 as (5.3). Then, R0>1, and Λ∗=γ−q>0 holds. To investigate the stability of the endemic equilibrium E∗, set the initial condition as
S(0,a)=S∗(a)=e−Λ∗a,I(0,a)=0.9I∗(a)=0.9Λ∗q(e−Λ∗a−e−γa),a≥0. |
First, set q=0.95γ/√2≈6.7175. In this case, by Theorem 5.1, there exists a τc>0 such that a Hopf bifurcation occurs. In fact, we can calculate τc≈0.446 (see Figure 6(a)).
Figure 7(a) and (b) show that, for τ=0.4<τc, I(t,a) and Λ(t) converge to the steady states I∗(a) and Λ∗=γ−q≈3.2825, respectively.
On the other hand, Figure 7(c) and (d) show that, for τ=0.5>τc, I(t,a) and Λ(t) converge to positive periodic solutions. This indicates that a Hopf bifurcation occurs at τ=τc.
Next, set q=1.36(√3−1)γ≈9.9559. In this case, by Lemma 5.4 (ⅱ), C0>0 for all τ≥0, and hence, H(x)=0 may have two positive roots x∗+>x∗−>0 such that H′(x∗+)>0>H′(x∗−). As stated in Remark 5.1, λ=±i√x∗+ (resp. ±i√x∗−) can lead to the destabilization (resp. stabilization) of the endemic equilibrium E∗. To clarify this point, let F+(τ) and G+(τ) (resp. F−(τ) and G−(τ)) be F(τ) and G(τ) corresponding to Ω(τ)=√x∗+(τ) (resp. √x∗−(τ)), respectively. If there exists a τ+>0 (resp. τ−>0) such that G+(τ+)=0 (resp. G−(τ−)=0), then the destabilization (resp. stabilization) of the endemic equilibrium E∗ can occur at τ=τ+ (resp. τ−). In fact, we can compute F±(τ) and G±(τ) as shown in Figure 6(b) and obtain τ+≈2.55 and τ−≈8.7. That is, we can predict that the endemic equilibrium E∗ is stable for τ∈[0,τ+), is unstable for τ∈(τ+,τ−) and becomes stable again when τ increases over τ−. Indeed, in Figure 8(a), the force of infection Λ(t) converges to the positive steady state Λ∗=γ−q≈0.0441 for τ=2<τ+, whereas in Figure 8(b), τ=3>τ+, and Λ(t) converges to a periodic solution.
In Figure 8(c), for τ=8.2<τ−, Λ(t) converges to a periodic solution, whereas in Figure 8(d), for τ=9.2>τ−, Λ(t) converges to the positive steady state. That is, the stability switch of the endemic equilibrium E∗ occurs twice at τ=τ+ and τ−.
In this paper, we have studied the local stability of the endemic equilibrium in a chronological age-structured SIR epidemic model with age-dependent infectivity. We assumed that the transmission rate is a shifted exponential function and investigated the possibility of a Hopf bifurcation regarding the infimum of the support of the transmission rate as a bifurcation parameter. We have shown that, if the distance between the force of infection at the endemic equilibrium and the removal rate is zero or sufficiently small (|q|≪1), then there always exists a critical value of the bifurcation parameter at which a Hopf bifurcation occurs. Furthermore, in a special case where the removal rate is sufficiently larger than the sum of the mortality rate and the reduction rate of infectivity, we have obtained a specific inequality (|q|<γ/√2) for which a similar critical value for a Hopf bifurcation always exists. We have performed numerical simulations and observed bifurcations of a stable periodic solution from the endemic equilibrium. On the other hand, for the case where q>(√3−1)γ, we have numerically confirmed that the stability switch of the endemic equilibrium can occur multiple times.
Our results have given a partial answer to a question of the possibility of a Hopf bifurcation in a chronological age-structured SIR epidemic model with age-dependent infectivity, which was raised in [15]. As our results are restricted to a special case where the transmission rate is a shifted exponential function, the study of other cases would be interesting future work. In particular, although we disregarded the age-dependent susceptibility for the sake of simplicity in the analysis, it would make the model more realistic because the assumption of the shifted exponential function could be suitable for some sexually transmitted diseases for which people under a certain age do not have the infectivity and susceptibility. It is an open problem whether a Hopf bifurcation still occurs if we introduce the age-dependent susceptibility to our model. Although it might be easily checked by numerical simulations, the analytical proof may be a more challenging task because it may be difficult to obtain a concrete characteristic equation like (4.4) when the force of infection depends on the age of the susceptible population.
Although our work in this paper was motivated by the mathematical analysis, periodic solutions in autonomous systems like our model could help in understanding the mechanism of the non-seasonal recurrent outbreaks which have been observed in many diseases such as measles. The application of our results to epidemiological considerations would also be important future work.
We deeply appreciate the editor and the anonymous referees for their valuable and constructive comments that helped us to improve the manuscript. T. Kuniya was supported by the Japan Society for the Promotion of Science (JSPS) [grant numbers 19K14594, 23K03214]. H. Inaba was supported by the Japan Society for the Promotion of Science (JSPS) [grant number 22K03433].
The authors declare there is no conflict of interest.
[1] | Pacheco-Torgal F, Diamanti MV, Nazari A, et al. (2019) Nanotechnology in Eco-Efficient Construction: Materials, Processes and Applications, 2 Eds., Amsterdam: Woodhead Publishing. https://doi.org/10.1016/B978-0-08-102641-0.01001-X |
[2] | Bartos P, Hughes J, Trtik P, et al. (2004) Nanotechnology in Construction, London: Royal Society of Chemistry. https://doi.org/10.1039/9781847551528 |
[3] |
Al-Mezrakchi R, Al-Ramthan A, Alam S (2020) Designing and modeling new generation of advanced hybrid composite sandwich structure armors for ballistic threats in defense applications. AIMS Mater Sci 7: 608–631. https://doi.org/10.3934/matersci.2020.5.608 doi: 10.3934/matersci.2020.5.608
![]() |
[4] |
Al-Mezrakchi R (2018) An investigation into scalability production of ultra-fine nanofiber using electrospinning systems. Fibers Polym 19: 105–115. https://doi.org/10.1007/s12221-018-7506-z doi: 10.1007/s12221-018-7506-z
![]() |
[5] |
Lee B, Woo BH, Ryou JS (2021) Basic mechanical and neutron shielding performance of mortar mixed with boron compounds with various alkalinity. Sustainability 13: 6252. https://doi.org/10.3390/su13116252 doi: 10.3390/su13116252
![]() |
[6] |
Qadir W, Ghafor K, Mohammed A (2019) Evaluation the effect of lime on the plastic and hardened properties of cement mortar and quantified using Vipulanandan model. Open Eng 9: 468–480. https://doi.org/10.1515/eng-2019-0055 doi: 10.1515/eng-2019-0055
![]() |
[7] |
Golewski GL (2023) Mechanical properties and brittleness of concrete made by combined fly ash, silica fume and nanosilica with ordinary Portland cement. AIMS Mater Sci 10: 390–404. https://doi.org/10.3934/matersci.2023021 doi: 10.3934/matersci.2023021
![]() |
[8] | Al-Ramthan A (2019) Behavior of walls and piles in cohesive soils under cyclic loads. Texas A & M University. Available from: https://hdl.handle.net/1969.1/185013. |
[9] |
Akkaya Y, Shah S, Ghandehari M (2003) Influence of fiber dispersion on the performance of microfiber reinforced cement composites. ACI 216: 1–18. https://doi.org/10.14359/12888 doi: 10.14359/12888
![]() |
[10] |
Yang H, Cui H, Tang W, et al. (2017) A critical review on research progress of graphene/cement based composites. Compos Part A Appl Sci Manuf 102: 273–296. https://doi.org/10.1016/j.compositesa.2017.07.019 doi: 10.1016/j.compositesa.2017.07.019
![]() |
[11] | Jóźwiak-Niedźwiedzka D, Lessing PA (2019) High-density and radiation shielding concrete, In: Mindess S, Developments in the Formulation and Reinforcement of Concrete, 2Eds., Amsterdam: Elsevier, 193–228. https://doi.org/10.1016/B978-0-08-102616-8.00009-5 |
[12] | Vera-Agullo J, Chozas-Ligero V, Portillo-Rico D, et al. (2009) Mortar and concrete reinforced with nanomaterials. Nanotechnology in Construction 3, Springer, Berlin, Heidelberg, 383–388. https://doi.org/10.1007/978-3-642-00980-8_52 |
[13] |
Zhao Z, Qi T, Zhou W, et al. (2020) A review on the properties, reinforcing effects, and commercialization of nanomaterials for cement-based materials. Nanotechnol Rev 9: 303–322. https://doi.org/10.1515/ntrev-2020-0023 doi: 10.1515/ntrev-2020-0023
![]() |
[14] |
Konsta-Gdoutos MS, Metaxa ZS, Shah SP (2010) Highly dispersed carbon nanotube reinforced cement based materials. Cement Concrete Res 40: 1052–1059. https://doi.org/10.1016/j.cemconres.2010.02.015 doi: 10.1016/j.cemconres.2010.02.015
![]() |
[15] |
Chu SH, Yang EH, Unluer C (2023) Development of nanofiber reinforced reactive magnesia-based composites for 3D printing. Constr Build Mater 366: 130270. https://doi.org/https://doi.org/10.1016/j.conbuildmat.2022.130270 doi: 10.1016/j.conbuildmat.2022.130270
![]() |
[16] |
Chu SH, Li LG, Kwan AKH (2021) Development of extrudable high strength fiber reinforced concrete incorporating nano calcium carbonate. Addit Manuf 37: 101617. https://doi.org/https://doi.org/10.1016/j.addma.2020.101617 doi: 10.1016/j.addma.2020.101617
![]() |
[17] |
Konsta-Gdoutos MS, Batis G, Danoglidis PA, et al. (2017) Effect of CNT and CNF loading and count on the corrosion resistance, conductivity and mechanical properties of nanomodified OPC mortars. Constr Build Mater 147: 48–57. https://doi.org/10.1016/j.conbuildmat.2017.04.112 doi: 10.1016/j.conbuildmat.2017.04.112
![]() |
[18] |
Cuenca E, Rigamonti S, Gastaldo Brac E, et al. (2021) Crystalline admixture as healing promoter in concrete exposed to chloride-rich environments: Experimental study. J Mater Civil Eng 33: 04020491. https://doi.org/10.1061/(ASCE)MT.1943-5533.0003604 doi: 10.1061/(ASCE)MT.1943-5533.0003604
![]() |
[19] |
Cuenca E, Mezzena A, Ferrara L (2021) Synergy between crystalline admixtures and nano-constituents in enhancing autogenous healing capacity of cementitious composites under cracking and healing cycles in aggressive waters. Constr Build Mater 266: 121447. https://doi.org/10.1016/j.conbuildmat.2020.121447 doi: 10.1016/j.conbuildmat.2020.121447
![]() |
[20] |
Alatawna A, Birenboim M, Nadiv R, et al. (2020) The effect of compatibility and dimensionality of carbon nanofillers on cement composites. Constr Build Mater 232: 117141. https://doi.org/10.1016/j.conbuildmat.2019.117141 doi: 10.1016/j.conbuildmat.2019.117141
![]() |
[21] |
Qureshi TS, Panesar DK (2019) Impact of graphene oxide and highly reduced graphene oxide on cement based composites. Constr Build Mater 206: 71–83. https://doi.org/10.1016/j.conbuildmat.2019.01.176 doi: 10.1016/j.conbuildmat.2019.01.176
![]() |
[22] |
Lu L, Zhao P, Lu Z (2018) A short discussion on how to effectively use graphene oxide to reinforce cementitious composites. Constr Build Mater 189: 33–41. https://doi.org/10.1016/j.conbuildmat.2018.08.170 doi: 10.1016/j.conbuildmat.2018.08.170
![]() |
[23] |
Lu Z, Li X, Hanif A, et al. (2017) Early-age interaction mechanism between the graphene oxide and cement hydrates. Constr Build Mater 152: 232–239. https://doi.org/10.1016/j.conbuildmat.2017.06.176 doi: 10.1016/j.conbuildmat.2017.06.176
![]() |
[24] |
Sanchez F, Sobolev K (2010) Nanotechnology in concrete—A review. Constr Build Mater 24: 2060–2071. https://doi.org/10.1016/j.conbuildmat.2010.03.014 doi: 10.1016/j.conbuildmat.2010.03.014
![]() |
[25] |
Rehman F, Zhao C, Jiang H, et al. (2016) Biomedical applications of nano-titania in theranostics and photodynamic therapy. Biomater Sci 4: 40–54. https://doi.org/10.1039/C5BM00332F doi: 10.1039/C5BM00332F
![]() |
[26] |
Hassan MM, Dylla H, Mohammad LN, et al. (2010) Evaluation of the durability of titanium dioxide photocatalyst coating for concrete pavement. Constr Build Mater 24: 1456–1461. https://doi.org/10.1016/j.conbuildmat.2010.01.009 doi: 10.1016/j.conbuildmat.2010.01.009
![]() |
[27] |
Loh K, Gaylarde CC, Shirakawa MA (2018) Photocatalytic activity of ZnO and TiO2 'nanoparticles' for use in cement mixes. Constr Build Mater 167: 853–859. https://doi.org/10.1016/j.conbuildmat.2018.02.103 doi: 10.1016/j.conbuildmat.2018.02.103
![]() |
[28] |
Carp O, Huisman CL, Reller A (2004) Photoinduced reactivity of titanium dioxide. Prog Solid State Ch 32: 33–177. https://doi.org/10.1016/j.progsolidstchem.2004.08.001 doi: 10.1016/j.progsolidstchem.2004.08.001
![]() |
[29] |
Cassar L (2004) Photocatalysis of cementitious materials: clean buildings and clean air. MRS Bull 29: 328–331. https://doi.org/10.1557/mrs2004.99 doi: 10.1557/mrs2004.99
![]() |
[30] |
Folli A, Pade C, Hansen TB, et al. (2012) TiO2 photocatalysis in cementitious systems: Insights into self-cleaning and depollution chemistry. Cement Concrete Res 42: 539–548. https://doi.org/10.1016/j.cemconres.2011.12.001 doi: 10.1016/j.cemconres.2011.12.001
![]() |
[31] |
Gopalan AI, Lee JC, Saianand G, et al. (2020) Recent progress in the abatement of hazardous pollutants using photocatalytic TiO2-based building materials. Nanomaterials 10: 1854. https://doi.org/10.3390/nano10091854 doi: 10.3390/nano10091854
![]() |
[32] |
Chen J, Poon CS (2009) Photocatalytic construction and building materials: From fundamentals to applications. Build Environ 44: 1899–1906. https://doi.org/10.1016/j.buildenv.2009.01.002 doi: 10.1016/j.buildenv.2009.01.002
![]() |
[33] |
Chen F, Yang X, Mak HKC, et al. (2010) Photocatalytic oxidation for antimicrobial control in built environment: A brief literature overview. Build Environ 45: 1747–1754. https://doi.org/https://doi.org/10.1016/j.buildenv.2010.01.024 doi: 10.1016/j.buildenv.2010.01.024
![]() |
[34] |
Macphee DE, Folli A (2016) Photocatalytic concretes—The interface between photocatalysis and cement chemistry. Cement Concrete Res 85: 48–54. https://doi.org/https://doi.org/10.1016/j.cemconres.2016.03.007 doi: 10.1016/j.cemconres.2016.03.007
![]() |
[35] |
Hamidi F, Aslani F (2019) TiO2-based photocatalytic cementitious composites: Materials, properties, influential parameters, and assessment techniques. Nanomaterials 9: 1444. https://doi.org/10.3390/nano9101444 doi: 10.3390/nano9101444
![]() |
[36] | Essawy AA, Abd El.Aleem S (2014) Physico-mechanical properties, potent adsorptive and photocatalytic efficacies of sulfate resisting cement blends containing micro silica and nano-TiO2. Constr Build Mater 52: 1–8. https://doi.org/10.1016/j.conbuildmat.2013.11.026 |
[37] |
Chen J, Kou SC, Poon CS (2012) Hydration and properties of nano-TiO2 blended cement composites. Cement Concrete Comp 34: 642–649. https://doi.org/10.1016/j.cemconcomp.2012.02.009 doi: 10.1016/j.cemconcomp.2012.02.009
![]() |
[38] |
Zhang R, Cheng X, Hou P, et al. (2015) Influences of nano-TiO2 on the properties of cement-based materials: Hydration and drying shrinkage. Constr Build Mater 81: 35–41. https://doi.org/10.1016/j.conbuildmat.2015.02.003 doi: 10.1016/j.conbuildmat.2015.02.003
![]() |
[39] | ASTM International (2021) Standard specification for standard sand. ASTM C778, West Conshohocken, PA. https://doi.org/10.1520/C0778-21 |
[40] |
Yousefi A, Allahverdi A, Hejazi P (2013) Effective dispersion of nano-TiO2 powder for enhancement of photocatalytic properties in cement mixes. Constr Build Mater 41: 224–230. https://doi.org/10.1016/j.conbuildmat.2012.11.057 doi: 10.1016/j.conbuildmat.2012.11.057
![]() |
[41] | ASTM International (2021) Standard test method for compressive strength of hydraulic cement mortars (using 2-in. or 50 mm cube specimens). ASTM C109/C109M, West Conshohocken, PA. https://doi.org/10.1520/C0109_C0109M-21 |
[42] |
Rajadesingu S, Arunachalam KD (2020) Hydration effect of boric acid on the strength of high-performance concrete (HPC). IOP Conf Ser Mater Sci Eng 912: 062073. https://doi.org/10.1088/1757-899X/912/6/062073 doi: 10.1088/1757-899X/912/6/062073
![]() |
[43] | Davraz M (2015) The effect of boron compound to cement hydration and controllability of this effect. Acta Phys Pol A 128. https://doi.org/10.12693/APhysPolA.128.B-26 |
[44] |
Volkman D, Bussolini P (1992) Comparison of fine particle colemanite and boron frit in concrete for time-strength relationship. J Test Eval 20: 92–96. https://doi.org/10.1520/JTE11903J doi: 10.1520/JTE11903J
![]() |
[45] |
Olgun A, Kavas T, Erdogan Y, et al. (2007) Physico-chemical characteristics of chemically activated cement containing boron. Build Environ 42: 2384–2395. https://doi.org/10.1016/j.buildenv.2006.06.003 doi: 10.1016/j.buildenv.2006.06.003
![]() |
[46] |
Targan Ş, Olgun A, Erdogan Y, et al. (2002) Effects of supplementary cementing materials on the properties of cement and concrete. Cement Concrete Res 32: 1551–1558. https://doi.org/10.1016/S0008-8846(02)00831-1 doi: 10.1016/S0008-8846(02)00831-1
![]() |
[47] | Jayapalan A, Lee B, Kurtis K (2009) Effect of nano-sized titanium dioxide on early age hydration of Portland cement. Nanotechnology in Construction 3, Springer, Berlin, Heidelberg, 267–273. https://doi.org/10.1007/978-3-642-00980-8_35 |
[48] | Parveen S (2016) Microstructure and mechanical properties of nanomaterial reinforced cementitious composites. Universidade do Minho (Portugal). Available from: https://hdl.handle.net/1822/45268. |
1. | Jordi Ripoll, Jordi Font, Numerical approach to an age-structured Lotka-Volterra model, 2023, 20, 1551-0018, 15603, 10.3934/mbe.2023696 | |
2. | Desmond Z. Lai, Julia R. Gog, Waning immunity can drive repeated waves of infections, 2024, 21, 1551-0018, 1979, 10.3934/mbe.2024088 | |
3. | Dongxue Yan, Yongxian Jin, Hui Cao, Yu Cao, Stability and Hopf Bifurcation for a delayed hand–foot–mouth disease model with continuous age-structure in the exposed class, 2025, 84, 14681218, 104310, 10.1016/j.nonrwa.2024.104310 |