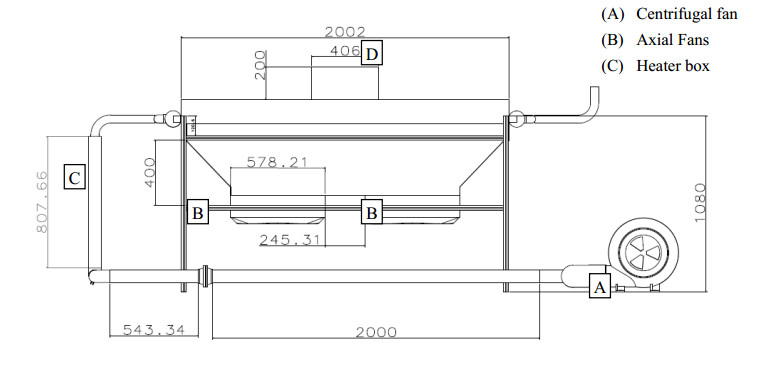
Citation: Araz Alizadeh, MohammadBehshad Shafii, Alireza hajiseyed Mirzahosseini, Abtin Ataei. Experimental and simulation investigation of pulsed heat pipes in gas compressors[J]. AIMS Energy, 2020, 8(3): 438-454. doi: 10.3934/energy.2020.3.438
[1] | Khaled M. Bataineh, Assem N. AL-Karasneh . Direct solar steam generation inside evacuated tube absorber. AIMS Energy, 2016, 4(6): 921-935. doi: 10.3934/energy.2016.6.921 |
[2] | Caliot Cyril, Flamant Gilles . Pressurized Carbon Dioxide as Heat Transfer Fluid: In uence of Radiation on Turbulent Flow Characteristics in Pipe. AIMS Energy, 2014, 1(2): 172-182. doi: 10.3934/energy.2014.2.172 |
[3] | Xiaolong Wang, Lingning Zhang, Yuan Chang, Yang Song, Liang Wang . Numerical simulation study on heat performance and pressure loss of solar air heater with sinusoidal baffles. AIMS Energy, 2024, 12(3): 617-638. doi: 10.3934/energy.2024029 |
[4] | Tan Nguyen Tien, Quang Khong Vu, Vinh Nguyen Duy . Novel designs of thermoelectric generator for automotive waste heat recovery: A review. AIMS Energy, 2022, 10(4): 922-942. doi: 10.3934/energy.2022042 |
[5] | Junaid Akhlas, Silvia Baesso, Alberto Bertucco, Fabio Ruggeri . Coal gasification by indirect heating in a single moving bed reactor: Process development & simulation. AIMS Energy, 2015, 3(4): 635-665. doi: 10.3934/energy.2015.4.635 |
[6] | Degaga Abdi, Addisu Bekele, Chandraprabu Venkatachalam, Mohanram Parthiban . Energy performance analysis of pasta and macaroni factory-a case study. AIMS Energy, 2021, 9(2): 238-256. doi: 10.3934/energy.2021013 |
[7] | Fazri Amir, Hafiz Muhammad, Nasruddin A. Abdullah, Samsul Rizal, Razali Thaib, Hamdani Umar . Performance analysis of heat recovery in Heat Pipe Heat Exchanger on room air conditioning systems. AIMS Energy, 2023, 11(4): 612-627. doi: 10.3934/energy.2023031 |
[8] | Kaovinath Appalasamy, R Mamat, Sudhakar Kumarasamy . Smart thermal management of photovoltaic systems: Innovative strategies. AIMS Energy, 2025, 13(2): 309-353. doi: 10.3934/energy.2025013 |
[9] | O. Corigliano, G. De Lorenzo, P. Fragiacomo . Techno-energy-economic sensitivity analysis of hybrid system Solid Oxide Fuel Cell/Gas Turbine. AIMS Energy, 2021, 9(5): 934-990. doi: 10.3934/energy.2021044 |
[10] | Tingting Wu, Kakali Mukhopadhyay, Paul J. Thomassin . A life cycle inventory analysis of wood pellets for greenhouse heating: a case study at Macdonald campus of McGill University1. AIMS Energy, 2016, 4(5): 697-722. doi: 10.3934/energy.2016.5.697 |
In recent years, the use of natural gas for power generation, as well as industrial sector consumption has dramatically increased [1,2,3]. Gas pressure boosting stations are used along the transmission lines to supply the required pressure to move from a site to another [4,5,6,7]. On the other hand, due to the pressure constraints of transmission lines, several pressure boosting stations are required for gas transmission across the whole transmission lines [8,9,10]. The locations and pressures required for pressure boosting stations are determined by permissible pressures, available power, and geographical and environmental factors. This is due to the fact that the pressure drop is highly dependent on elevation conditions, which reduces the pressure drop through the gas movement path [11,12,13,14]. Each pressure boosting station consists of several scrubbers to filter the inlet gas, a gas compressor to increase the pressure, and also an air cooler. Indeed, increasing the gas pressure by the compressor causes a rise in gas temperature. The high temperature of the gas necessitates the use of air coolers in the design of pressure boosting stations. Air coolers are among the exchangers that reduce the gas temperature through blowing the air, mostly done by fans, to the tubes carrying high-pressure gas. The cost of generating pressure at a boosting station can be up to 50% of the total gas transportation expenditures [15,16,17,18]. The use of air coolers in gas pressure boosting stations has some disadvantages, such as relatively high-pressure drop and significant power consumption due to the use of electro fans [19,20,21].
Heating pipe is a means of heat transfer, which is now widely used in commercial applications. It is more commonly used as a waste heat recycling device due to bringing high efficiency and low volume without any pollution. Heating pipes usually operate at temperatures ranging from 40 ℃ to 350 ℃. This range can be extended by careful selection of parts of the system. Additionally, the length of individual pipes may vary from a few inches to 5 feet long. Vasiliev and Luikov (2005) investigated a variety of modern heating pipe types. They ultimately concluded that the selection and design of heating pipes required careful consideration of the exact conditions and limitations of the system. It was also stated that heating pipes have different advantages, including high conductivity, isothermal conductivity, low maintenance [22].
Delpach et al. (2019) first addressed the need for energy optimization and its importance in the ceramic furnace sector, which has a substantial consumption share (more than 50% of the total). Also, in the cooling section and to improve the heating recovery, the radiant heating pipe was investigated. Experimental results revealed that the heating pipe could recover the radiant heat and also the natural displacement (About 4 kW) [23]. Ma et al. (2016) discussed the steel industry in China and selected a sample in the melting sector for further investigation. Thermal performance evaluation of heating pipe exchangers has been achieved and analyzed based on heat transfer rate, heat transfer coefficient, energy efficiency and NTU [24]. The results revealed that energy and thermal efficiency has improved and exergy efficiency increased from 34% to 41%. Additionally, by using this system, the heat transfer rate, heat transfer coefficient, and system efficacy rose by 6, 10 and 7%, respectively. In a similar study, Mosleh et al. (2019) investigated the use of pulse heating pipes in the exchanger structure through laboratory works. The results proved that utilizing pulse heating pipes can improve the heat transfer coefficient up to 310%. In their research, R134a operating fluid was used to evaluate the thermal performance of the exchanger. Overall, the authors' studies express that the use of heating pipes, in various sectors of industry and also in building works, significantly contributes to improving efficiency, heat transfer and other relevant indicators [25].
Previous researches have primarily focused on only the application of heat pipes in thermal efficiency and overall heat transfer in different sector such as building and industrial. As mentioned before, air cooler in gas pressure boosting station is an important facility as an energy performance aspect in natural gas increasing pressure process. The other hand, increasing natural gas pressure is the main target in each gas pressure boosting station, and reduce presser drop in air coolers cause to improve energy performance index. Besides, heat transfer can be improved by using heat pipes in the finned tube and cause to decrease the length of the tubes in air cooler with same heat transfer performance. Hence pressure drop can be reduced. Therefore, the loss of pressure and the required power will be reduced, and the efficiency and energy performance index will be improved. To our knowledge, no prior work has been done to assess experimentally in real air cooler size with all limitation at natural gas pressure boosting station.
Recently, different experiences have been studied to use of pulsed heat pipe in different industry. Innovate of this paper is a laboratory system designed by creating similar boundary conditions in natural gas compression station. In natural gas compressor stations industry by use of air coolers, reduce natural gas temperatures, so in this study, similar conditions have been established in the laboratory system as well as laboratory testing at different velocity of inlet fluid, cooling fan system and tubes that no article has been published so far.
In this paper, a laboratory system was first designed and developed to investigate the pressure drop in a tube and then the information and data relevant to a gas pressure boosting station in Iran were gathered and utilized to evaluate two different situations (tubes equipped with finished pipes and also tubes equipped with heating pipes). A case study of a typical gas pressure boosting station shows that under designing conditions, the gas must have a pressure increase of about 1.72 MPa throughout the station, while the triggered pressure drop in the air coolers of the subject station is only 0.2 MPa. In other words, about 11% of the total pressure increased by the gas compressor is lost in the cooling section, which results in lower gas pressure at the next station. Also at the station under study, more than 75% of electrical energy consumption is due to the use of air cooler electro fans at the gas pressure boosting station. Given the importance of increasing the pressure of natural gas at pressure boosting stations, the reduction of energy performance at each station is an objective and indicator of energy performance. In this paper, based on the laboratory and test results, in the designed exchanger, having one tube equipped with pulse heating pipe and another equipped with real-size fins, the effect of pressure drop on energy performance index at different fan speeds was thoroughly discussed and analyzed.
Due to the technical considerations and requirements demanded in this paper, a test system was designed. In the designed device, a fin-equipped tube and also a tube with pulse heating pipes implemented on are used. The purpose of designing such a system is to compare the pressure drop triggered in the fin-equipped tube with the heating-equipped one utilizing R134a operating fluid. For this reason, various equipment was employed to provide real thermodynamic conditions for the internal and external flows of the test tubes. For this purpose, it is necessary to have a system capable of providing process conditions in addition to performing gas cooling to the desired level. Therefore, a system was designed and developed which was capable to initially raise the fluid process temperature to the desired extent and then perform the cooling operation to reach the subject temperature to investigate the pressure drop in various conditions. The axial fan is also used to create external flow. Figure 1 shows the laboratory image of the testing system.
The designed system includes a centrifuge fan equipped with an inverter system to determine the speed of the blown air to create flow inside the pipes. The airflow generated by the centrifuge fan, with 3 kW power and rated 2860 rpm rotation speed, first passes through a box of electric heaters containing twelve 500-watt heating elements and reaches the desired temperature. It should be noted that the heater capacity is variable and can be reached at different temperatures during testing. Each pair of heaters is connected to a switch and can be switched on and off to meet different temperatures of tubes inlet. The hot airflow is then passed through the connections into the inlet header and divided into the internal flow of the pipes. A flow regulating valve is placed on each tube to control the amount of air in each tube and to establish the same conditions through the tubes. Thermocouple K-type thermometer is placed at the beginning and end of the pipes. Ultimately, the airflow passes through the Anemometer flowmeters, Model 6252A, and is discharged into the ambient.
To fill the gas operating fluid, the weight of the test apparatus and the devices attached there are first measured. A weighing scale with 0.05 g accuracy was used to measure weight. To fill the device with R134a gas, both valves are closed first. Then the R134a gas capsule attached to one of the valves with a gas hose. The capsule was placed in a way that it was positioned higher than the upper valve. The capsule is also reversed to place the outlet at the bottom of the device. This is because the R134a liquid is inserted into the outlet of the capsule to fill the heating pipe with this liquid while filling. After the steps as mentioned above, first, we open the capsule valve. Then we open the upper valve of the apparatus and then open the lower one. The gas pressure causes the liquid R134a to fill the oscillating heat pipe and also to expel the air inside the tube. When the liquid R134a is excreted vigorously from the second valve, the second valve closes, and then the first one is shut. The gas hose is slightly loosened to remove the R134a in the hose slowly. The hose is then removed from the device. This method fills the heating pipe with a filling proportion above 90% of the operating fluid. Then, regarding the internal volume of the heating pipes and the operational fluid density at ambient temperature, by the continuous discharge of the R134a gas out of the pipes and simultaneous weighing of the whole apparatus with scales, the desired filling ratio is measured. Thermodynamics properties in experiment situation are statistically shown in Table 1.
Parameters | Unit | R134 |
Viscosity liquid | cp | 0.20 |
Boiling Point @ 1 atm | C | -26.1 |
Liquid density @ 25 C | kg/m3 | 1206 |
Vapor density @ Boiling point | kg/m3 | 5.25 |
Specific heat liquid @ 25 C | kJ/kgK | 1.44 |
After completing and running of the laboratory system, the pressure drop was measured in two various situations. One using a tube equipped by pulse heating pipes (L1) and the other utilizing fin heating pipes (L2), provided that the temperature of the outlet gas is 50 ℃ and the pressure drop measurement is carried out through two Gauge-like barometers at the end of both tubes. Previous studies showed that the overall heat transfer coefficient in a tube using a pulse heating pipe is far better than that of using fins [25]. Therefore, the surface of the exchanger utilized to supply the same temperature in the tube with a pulse heating pipe is expected to be lower, in fact, the tube length is longer, and the surface should be more extensive. For this purpose, through the carried out experiments up to 30 minutes, the axial fans are switched off, and after 30 minutes the fans are switched on (the inverter frequency is set to 10 Hz). It is observed that the performance of both the heating pipe and fin-equipped tubes has improved. Ultimately, after 30 minutes, the condition is balanced. The purpose of this section is to experimentally select the specified length in the exchanger to obtain the same output temperature in both tubes. The results of this test are brought in Figure 2.
Test results show that the temperature within a meter of a tube equipped with heating pulse pipe is 50 ℃, which at the same temperature conditions is 1.5 m long for the tube equipped with fins. The schematics of the experimental system are being shown in Figures 3-5.
The NTU method, using to calculate the heat transfer rate in heat exchangers. This method is used when the temperature not defined in all streams. NTU is a dimensionless parameter ratio that calculated Eqs 1 and 2.
NTU=UtAtCmin | (1) |
Cmin=(˙mcp)min | (2) |
According to Eq 1, total heat transfer area in both tubes in our investigation can be calculated and determine for setup system.
As previously mentioned, the study performed in the laboratory system is following the thermodynamic and operating conditions of one of the pressure boosting stations in Iran. The operating considerations of the station, as well as the design conditions of the air-cooling exchanger which have been the basis of boundary conditions selection in this study, are listed through Tables 2 and 3.
Parameter | Input | Output |
Natural gas temperature (℃) | 86.2 | 50 |
Inserted gas temperature by the fan (℃) | 50 | 55 |
Natural gas flow rate (kg/hr) | 631336 | 631336 |
Inserted gas flow rate (kg/hr) | 4574556 | 4574556 |
Natural gas pressure (kPa) | 6823 | 6623 |
*Gas density in the standard condition is assumed 53.23 kg/m3 in the input. |
Parameter | Unit | Value |
Heat transfer rate | kW | 14300 |
Heat transfer area | m2 | 52011 |
Electro fans number | - | 24 |
Fan power consumption | kW | 37 |
After conducting laboratory tests regarding different inlet gas flow rates to the tube, the results show that the outlet pressure of the tube equipped with a pulse heating pipe is much higher due to the shorter gas passage through the tube. The test results in 4 different gas flow rates, from the highest flow (v1) to the lowest one (v4) inside the tube is shown in Figure 6.
The results pertinent to the measurements in test system prove that in all four modes of inlet fluid velocity to the tube, the L1 tube equipped with a pulse heating pipe endures a higher gas pressure, which was also true in the real conditions of the gas pressure boosting station. Figure 7 shows the improvement in pressure drop (%).
Regarding the laboratory scale, it is not possible to provide the inlet pressure to the exchanger at the gas pressure boost station, which is the output of the gas compressor. For this purpose and considering the linear relationship between velocity and pressure, the percentage of improvement impact in two tubes is used for simulation.
The primary purpose of this study is to reduce the pressure drop triggered in the heat exchanger and to increase the energy performance of the gas pressure boosting station. Since the energy performance index at a pressure boosting station is defined as the ratio of total energy consumed to the overall increase in pressure, the reduction of the energy performance index per a constant pressure rate rise at the gas pressure boosting station requires the decline of the electrical energy or gas consumption. As perceived in this study, the heating pipe is widely utilized as it reduces the surface area of the exchanger and consequently uses a shorter tube to cool the gas to the desired extent, causing the gas to travel through a shorter path in the exchanger. On the other hand, lowering the pressure drop in the case study station will result in entering natural gas to the next station with higher pressure, thus reducing fuel consumption in the turbine. To evaluate the gas-saving capability, the pressure boosting station studied at the next station was simulated in Aspen Hysys software. Then, the inlet pressure to the station was calculated in two different scenarios which are shown schematically in Figure 8.
In the above simulation, the station inlet gas flow (No. 1) with 4903 kPa pressure and 25 ℃ temperature is initially divided into three parts. These three flows include by-pass flow (No. 2), gas flow to boost gas pressure (No. 3), and gas flow to fuel turbine compressors. The exhausted gas from the turbo-compressors flows to the air coolers to lower the temperature, and at the air-cooling exchangers, the gas temperature is reduced to 50 ℃.
After the simulation process in ASPEN-HYSYS, some parameters such as natural gas suction pressure and fuel gas selected to validate the simulation. So, average daily operation data and simulation results in 30 days compared and uncertainty calculation in Figures 9 and 10 show 0.02% and 0.09% error in pressure and temperature suction, respectively. Deviation means that simulation results are acceptable.
The simulation results demonstrate that assuming constant pressure at the gas compressor outlet, the difference in air cooler pressure drop at the previous station will result in lower gas turbine consumption, which this pressure increase at V1 condition (maximum gas flow rate) is about 100 kPa. Figure 11 shows the effect of increasing the inlet pressure to the pressure boosting station at different intervals on a gas turbine.
It should be noted that the results of Figure 11 are calculated for one gas turbine unit. To this end, to calculate the total reduction in turbine fuel consumption considering the layout of the sampling station and the use of 2 turbo-compressors continuously throughout the year, fuel consumption is estimated to be annual as 1.115 MMM3.
The energy performance index, in each natural gas boosting station, includes thermal, electrical and total energy performance that calculated with Eqs 3 to 5.
Total Energy Performance Index= Tetal Energy consumption (kJ) Increased pressure (ΔP) | (3) |
Thermal Energy Perfarmance Index =Fuel Consumption (k)Increased pressure (ΔP) | (4) |
Electrical Energy Performance Index=Electrical Energy Consumptton (kJ)Lncreased pressure (ΔP) | (5) |
The total energy consumption at the gas pressure boosting station divided by the increased pressure indicates the station's energy performance. Also, thermal energy includes fuel gas consumption in the gas turbine, and Electrical energy performance is all electrical consumption related to increased pressure that significant energy users are electro motors in air coolers.
Accordingly, the use of tubes equipped with heating pipes will improve the energy performance index, as illustrated in Figures 12-14.
In the calculations, the thermal value of the gas is considered 45000 kJ/m3 and also the results of the operating conditions survey pertinent to the subject station indicate that amongst the 24 air cooler fans, on average half of them are permanently used during the year. Also, a significant portion of the power consumption at each power-boosting station depends on the air more cooling electro fans and therefore has a dramatic impact on the electrical energy performance index of the station.
Figure 15 shows the results of pressure drop reduction under different conditions of this study.
The calculated pressure drop in the tubes equipped with the heating pipes of the current study shows that in the hot section, 53 kPa is dropped (for natural gas), while in operating conditions for cooling parts, the pressure drop reported in the technical sheet by the air cooling manufacturer has been 200 kPa. In other words, the pressure drop in the heating pipe exchanger design conditions will be approximately four times lower than the current circumstances. In a similar study by Sun et al. (2018), in particular, by combining a series of heating pipes with the use of gravitational force in thermoelectric coolers (TEC), they empirical investigated the valid parameters. The results of this study showed that using the combination mentioned above can improve the cooling capacity by 68% [26]. Another survey by Borlaco et al. in 2018 on the use of a heating pipe system in a building installation proves that the thermal energy performance index has improved by about 30% [27]. Also, researches by Honghai et al. (2007) on the utilization of a type of heating pipe in the building sector have resulted in a 30-50% improvement in air conditioning operation [28].
The goal of this investigation was the experimental implementation of the heat pipe in the finned tube instead of simple finned tube and assets pressure drop and infused in energy performance index in natural gas pressure boosting station. For this purpose, the real case study selected and boundary condition, air cooler size and operation data was recorded. Next, the experimental setup was designed, fabricated and tested in different condition. Also for creating real boundary condition, the gas pressure boosting stations simulated in HYAYS. Comparing results with real the in suction pressure and temperature, show 0.02% and 0.09% error respectively.
One advantage of using tubes equipped with pulse heat pipe is triggering a very low-pressure drop in natural gas. The purpose of a gas pressure boosting station design is to increase the pressure; nevertheless in the current process of a station, as soon as the pressure is enhanced through the turbo-compressor cycle, a percentage of the total pressure increase provided in the cooling section is lost. The results of the analyzing and evaluating the cooling section of the case study gas pressure boosting stations reveal that this section of the station has the potential to improve the energy performance as well as reduce energy consumption and improve its performance. First, outlet temperature in tubes (finned tube, and fin with PHP tube) adjusted at 50 ℃. Experimental results show that the outlet temperature in 1.5 meters of the finned tube and 1-meter fin with PHP tube length is equal. Afterwards, in four-velocity, outlet pressure was calculated and result from show 44.59, 40.40, 36.78 and 23.34% in V1 to V4 improvement in pressure drop. Reducing the pressure drop in air cooler lead to increase suction pressure in the next gas pressure boosting station. Results of simulation show with using PHP tube in an air cooler, energy saving in fuel gas consumption in the next station will be 1, 114, 116 Sm3 annually. Also implemented these type of tube cause to reduce 3, 889, 440 kWh electrical consumption in air coolers. Energy performance calculations for the case study station have revealed the improvement in overall energy performance, thermal performance and electrical energy performance indices up to 3, 2.3 and 79%, respectively. Besides, the development of this design at all pressure boosting stations will also create a very high potential for energy savings.
The authors declare that they have no conflict of interest.
[1] |
Man Y, Han Y, Hu Y, et al. (2018) Synthetic natural gas as an alternative to coal for power generation in China: Life cycle analysis of haze pollution, greenhouse gas emission, and resource consumption. J Cleaner Prod 172: 2503-2512. doi: 10.1016/j.jclepro.2017.11.160
![]() |
[2] |
Mohd NS, Francisco MJ, Olav B, et al. (2018) Techno-economic assessment of chemical looping reforming of natural gas for hydrogen production and power generation with integrated CO2 capture. Int J Greenhouse Gas Control 78: 7-20. doi: 10.1016/j.ijggc.2018.07.022
![]() |
[3] | Valizadeh K, Farahbakhsh S, Bateni A, et al. (2019) A parametric study to simulate the non‐Newtonian turbulent flow in spiral tubes. J Energy Sci Eng 8: 134-149. |
[4] |
Borelli D, Devia F, Cascio EL, et al. (2018) Energy recovery from natural gas pressure reduction stations: Integration with low temperature heat sources. J Energy Convers Manage 159: 274-283. doi: 10.1016/j.enconman.2017.12.084
![]() |
[5] | Vaughn T, Bell C,Yacovitch T, et al. (2017) Comparing facility-level methane emission rate estimates at natural gas gathering and boosting stations. J Elem Sci Anth 5: (NREL/JA-6A20-70688). |
[6] |
Bac S, Keskin S, Avci AK (2018) Modeling and simulation of water-gas shift in a heat exchange integrated microchannel converter. Int J Hydrogen Energy 43: 1094-1104. doi: 10.1016/j.ijhydene.2017.09.141
![]() |
[7] | Wang L, Davarpanah A (2020) An experimental investigation to consider thermal methods efficiency on oil recovery enhancement. J Heat Transfer. |
[8] | Agwu O, Markson I, Umana M (2016) Minimizing energy consumption in compressor stations along two gas pipelines in Nigeria. J Mech Eng Autom 3: 29-34. |
[9] |
Demissie A, Zhu W, Belachew C (2017) A multi-objective optimization model for gas pipeline operations. J Comput Chem Eng 100: 94-103. doi: 10.1016/j.compchemeng.2017.02.017
![]() |
[10] | Davarpanah A, Mirshekari B (2019a) Experimental investigation and mathematical modeling of gas diffusivity by carbon dioxide and methane kinetic adsorption. J Ind Eng Chem Res 58: 12392-12400. |
[11] | Zarei M, Davarpanah A, Mokhtarian N, et al. (2020) Integrated feasibility experimental investigation of hydrodynamic, geometrical and, operational characterization of methanol conversion to formaldehyde. J Energy Sources, Part A: Recovery, Util, Environ Eff 42: 89-103. |
[12] | Cordova JL, Heshmat H (2018) High effectiveness low pressure drop heat exchanger. Google Patents. |
[13] |
Wan Mohamed WAN, Talib S, Zakaria I, et al. (2018) Effect of dynamic load on the temperature profiles and cooling response time of a proton exchange membrane fuel cell. J Energy Inst 91: 349-357. doi: 10.1016/j.joei.2017.02.006
![]() |
[14] | Davarpanah A, Mirshekari B (2019b) Experimental study of CO2 solubility on the oil recovery enhancement of heavy oil reservoirs. J Therm Anal Calorim. |
[15] |
Rosli RE, Sulong AB, Daud WRW, et al. (2017) A review of high-temperature proton exchange membrane fuel cell (HT-PEMFC) system. Int J Hydrogen Energy 42: 9293-9314. doi: 10.1016/j.ijhydene.2016.06.211
![]() |
[16] |
Zhao J, Qifei J, Luo L, et al. (2018) Dynamic behavior study on voltage and temperature of proton exchange membrane fuel cells. J Appl Therm Eng 145: 343-351. doi: 10.1016/j.applthermaleng.2018.09.030
![]() |
[17] |
Tao H, Wang C, Zhu C, et al. (2018) Optimization of waste heat recovery power generation system for cement plant by combining pinch and exergy analysis methods. J Appl Therm Eng 140: 334-340. doi: 10.1016/j.applthermaleng.2018.05.039
![]() |
[18] |
Davarpanah A, Mazarei M, Mirshekari B (2019) A simulation study to enhance the gas production rate by nitrogen replacement in the underground gas storage performance. J Energy Rep 5: 431-435. doi: 10.1016/j.egyr.2019.04.004
![]() |
[19] | Davarpanah A, Zarei M, Valizadeh K, et al. (2019) CFD design and simulation of ethylene dichloride (EDC) thermal cracking reactor. J Energy Sources, Part A: Recovery, Util, Environ Eff 41: 1573-1587. |
[20] |
Kwon HM, Kim TS, Sohn JL (2018) Performance improvement of gas turbine combined cycle power plant by dual cooling of the inlet air and turbine coolant using an absorption chiller. J Energy 163: 1050-1061. doi: 10.1016/j.energy.2018.08.191
![]() |
[21] |
Rahman AA, Mokheimer EMA (2018) Comparative analysis of different inlet air cooling technologies including solar energy to boost gas turbine combined cycles in hot regions. J Energy Resour Technol 140: 112006. doi: 10.1115/1.4040195
![]() |
[22] |
Vasiliev LL (2005) Heat pipes in modern heat exchangers. J Appl Therm Eng 25: 1-19. doi: 10.1016/j.applthermaleng.2003.12.004
![]() |
[23] |
Delpech B, Axcell B, Jouhara H (2019) Experimental investigation of a radiative heat pipe for waste heat recovery in a ceramics kiln. J Energy 170: 636-651. doi: 10.1016/j.energy.2018.12.133
![]() |
[24] |
Ma H, Yin L, Shen X, et al. (2016) Experimental study on heat pipe assisted heat exchanger used for industrial waste heat recovery. J Appl Energy 169: 177-186. doi: 10.1016/j.apenergy.2016.02.012
![]() |
[25] |
Jafari-Mosleh H, Bijarchi MA, Shafii MB (2019) Experimental and numerical investigation of using pulsating heat pipes instead of fins in air-cooled heat exchangers. J Energy Convers Manage 181: 653-662. doi: 10.1016/j.enconman.2018.11.081
![]() |
[26] |
Sun X, Ling L, Liao S, et al. (2018) A thermoelectric cooler coupled with a gravity-assisted heat pipe: An analysis from heat pipe perspective. J Energy Convers Manage 155: 230-242. doi: 10.1016/j.enconman.2017.10.068
![]() |
[27] |
Burlacu A, Sosoi G, Vizitiu RS, et al. (2018) Energy efficient heat pipe heat exchanger for waste heat recovery in buildings. J Procedia Manuf 22: 714-721. doi: 10.1016/j.promfg.2018.03.103
![]() |
[28] |
Hagens H, Ganzevles FLA, Geld CWM, et al. (2007) Air heat exchangers with long heat pipes: experiments and predictions. J Appl Therm Eng 27: 2426-2434. doi: 10.1016/j.applthermaleng.2007.03.004
![]() |
1. | Fazri Amir, Hafiz Muhammad, Nasruddin A. Abdullah, Samsul Rizal, Razali Thaib, Hamdani Umar, Performance analysis of heat recovery in Heat Pipe Heat Exchanger on room air conditioning systems, 2023, 11, 2333-8334, 612, 10.3934/energy.2023031 |
Parameters | Unit | R134 |
Viscosity liquid | cp | 0.20 |
Boiling Point @ 1 atm | C | -26.1 |
Liquid density @ 25 C | kg/m3 | 1206 |
Vapor density @ Boiling point | kg/m3 | 5.25 |
Specific heat liquid @ 25 C | kJ/kgK | 1.44 |
Parameter | Input | Output |
Natural gas temperature (℃) | 86.2 | 50 |
Inserted gas temperature by the fan (℃) | 50 | 55 |
Natural gas flow rate (kg/hr) | 631336 | 631336 |
Inserted gas flow rate (kg/hr) | 4574556 | 4574556 |
Natural gas pressure (kPa) | 6823 | 6623 |
*Gas density in the standard condition is assumed 53.23 kg/m3 in the input. |
Parameter | Unit | Value |
Heat transfer rate | kW | 14300 |
Heat transfer area | m2 | 52011 |
Electro fans number | - | 24 |
Fan power consumption | kW | 37 |
Parameters | Unit | R134 |
Viscosity liquid | cp | 0.20 |
Boiling Point @ 1 atm | C | -26.1 |
Liquid density @ 25 C | kg/m3 | 1206 |
Vapor density @ Boiling point | kg/m3 | 5.25 |
Specific heat liquid @ 25 C | kJ/kgK | 1.44 |
Parameter | Input | Output |
Natural gas temperature (℃) | 86.2 | 50 |
Inserted gas temperature by the fan (℃) | 50 | 55 |
Natural gas flow rate (kg/hr) | 631336 | 631336 |
Inserted gas flow rate (kg/hr) | 4574556 | 4574556 |
Natural gas pressure (kPa) | 6823 | 6623 |
*Gas density in the standard condition is assumed 53.23 kg/m3 in the input. |
Parameter | Unit | Value |
Heat transfer rate | kW | 14300 |
Heat transfer area | m2 | 52011 |
Electro fans number | - | 24 |
Fan power consumption | kW | 37 |