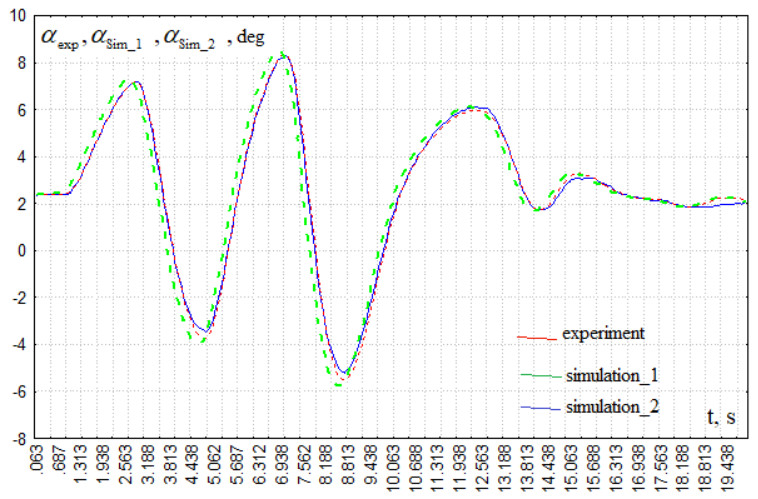
The mathematical analysis of the problem of irregularity of estimates inherent in the problem of parametric identification of aircraft mathematical models according to flight experiments data is carried out. It is shown that to ensure the reliability of identification results, usually it is not enough to use only observations of the input and output signals of the object, but it is necessary to attract additional information taken from the basic scientific and engineering disciplines related to the subject under study, and apply other special techniques. For the task of estimating the parameters of aircraft models using flight experiment data, the basic rules for performing identification are formulated.
Citation: O.N. Korsun, Om Moung Htang. The practical rules for aircraft parameters identification based on flight test data[J]. Metascience in Aerospace, 2024, 1(1): 53-65. doi: 10.3934/mina.2024003
[1] | James H. Page, Lorenzo Dorbolò, Marco Pretto, Alessandro Zanon, Pietro Giannattasio, Michele De Gennaro . Sensitivity analysis of mixed analysis-synthesis flight profile reconstruction. Metascience in Aerospace, 2024, 1(4): 401-415. doi: 10.3934/mina.2024019 |
[2] | Jubilee Prasad Rao, Sai Naveen Chimata . Machine learning-based surrogates for eVTOL performance prediction and design optimization. Metascience in Aerospace, 2024, 1(3): 246-267. doi: 10.3934/mina.2024011 |
[3] | Simon Kim, Donghyun Lee, Byunggil Kwak, Myeonghyo Kim . For electrified aircraft propulsion, SiC MOSFET inverter design with power redundancy in both escape event and failure. Metascience in Aerospace, 2025, 2(1): 1-14. doi: 10.3934/mina.2025001 |
[4] | Wenchao Cai, Yadong Zhou . Preventing aircraft from wildlife strikes using trajectory planning based on the enhanced artificial potential field approach. Metascience in Aerospace, 2024, 1(2): 219-245. doi: 10.3934/mina.2024010 |
[5] | Grégoire Dannet, Olivier Boucher, Nicolas Bellouin . Features and evolution of civil aviation CO$ _2 $ emissions based on ADS-B data for the period between 2019–2024. Metascience in Aerospace, 2024, 1(4): 346-370. doi: 10.3934/mina.2024016 |
[6] | Igor V. Bezmenov . Trend detection in time series of measurement data in solving problems in space geodynamics and other research areas. Metascience in Aerospace, 2024, 1(3): 268-291. doi: 10.3934/mina.2024012 |
[7] | Igor V. Bezmenov . Fast algorithm for cleaning highly noisy measurement data from outliers, based on the search for the optimal solution with the minimum number of rejected measurement data. Metascience in Aerospace, 2024, 1(1): 110-129. doi: 10.3934/mina.2024005 |
[8] | Jiaqing Kou, Tianbai Xiao . Artificial intelligence and machine learning in aerodynamics. Metascience in Aerospace, 2024, 1(2): 190-218. doi: 10.3934/mina.2024009 |
[9] | Shorob Alam Bhuiyan, Ikram Hossain, Redwan Hossain, Md. Sakib Ibn Mobarak Abir, Dewan Hasan Ahmed . Effect of a bioinspired upstream extended surface profile on flow characteristics and a drag coefficient of a circular cylinder. Metascience in Aerospace, 2024, 1(2): 130-158. doi: 10.3934/mina.2024006 |
[10] | Sarker Ashraful Islam, Farhana Kabir Esheta, Md Mahir Shahriar, Dewan Hasan Ahmed . Numerical study of aerodynamic drag reduction of a circular cylinder with an inbuilt nozzle. Metascience in Aerospace, 2024, 1(4): 379-400. doi: 10.3934/mina.2024018 |
The mathematical analysis of the problem of irregularity of estimates inherent in the problem of parametric identification of aircraft mathematical models according to flight experiments data is carried out. It is shown that to ensure the reliability of identification results, usually it is not enough to use only observations of the input and output signals of the object, but it is necessary to attract additional information taken from the basic scientific and engineering disciplines related to the subject under study, and apply other special techniques. For the task of estimating the parameters of aircraft models using flight experiment data, the basic rules for performing identification are formulated.
The identification problem, as it is widely known [1,2,3,4], consists of finding an object model based on measurements of the object's input and output signals. The identification theory [1,2,4] provides us with mathematical identifiability requirements, which enable us to obtain the solution. However, the application of identification methods to experimental data reveals another problem, of a fundamental nature. The manifestation of this problem consists of the following. Most of the existing identification algorithms give good results when tested on the data obtained by mathematical simulation. This simulation data normally includes the object deterministic signals, such as the parameters of the aircraft motion, and the stochastic processes, such as measurement errors and object noise. Here, the expression "good results" means that the identification estimates are unbiased, and their variances follow the laws of mathematical statistics. However, when we start to apply the same identification algorithms to processing, for example, the flight test data, this satisfactory picture usually suffers considerable deterioration. Here, we often encounter the irregularity of identification estimates, where estimates corresponding to different sections of the flight may differ significantly from each other even when the data were obtained in the same flight modes, which implies the unity of the object model. At the same time, the degree of correspondence of the output signals of the model and the object often turns out to be quite good and approximately the same for all the compared sections.
The general reason can be easily determined by finding out the fact how the testing based on the data generated using the model differs from processing measurements recorded in a real flight.
In the case of testing, the assumptions on object models, observations, as well as statistical characteristics of object noise and observations that are used in identification correspond to the assumptions accepted in data generation. In the case of a real object, this correspondence is often disrupted, since our knowledge of the real object is often imperfect. From the point of view of identification, this means that there are unknown interferences in the experimental data that are not taken into account by the identification algorithm. It should be noted that structural or parametric differences in the models of the object and the measurement system generate, as a rule, deterministic interference, the influence of which cannot be taken into account in the framework of a stochastic formulation when independent noises are usually assumed. As a result, we obtain biased identification estimates. These biases depend on the degree of mismatch between the model and the object, as well as on the performed maneuver and the type of input signal.
Let us formulate the problem described above mathematically. We will obtain an expression for the biases of parameter estimates caused by interference.
Let us first consider the traditional problem formulation of the parametric identification, in which assumptions about object models, measurement systems and measurement noise correspond to true ones with high accuracy. It is known [1,4] that in this case, the parameter estimates should be biased.
Let the object and observation models be given in the form
y'(t)=f(y(t),a,u(t)), | (1) |
z(ti)=h(y(ti),a,u(ti))+η(ti), | (2) |
where y(t),u(t) are vectors of output and input signals,
z(ti) is an observation vector,
f(⋅),h(⋅) are known vector functions of vector arguments,
η(ti) is observation noise, which is a vector normal random sequence of the white noise type with zero mean and a known variance matrix R(ti),
a is a vector of unknown parameters to be identified.
It is also assumed that the observation noise is not correlated with the signals of the system and the input signal u(t), which is a known function of time.
In order to find parameter estimates, the following functional is to be minimized:
J(a)=∑Ni−1(z(ti)−ˆz(ti,a))TR−1(ti)(z(ti)−ˆz(ti,a)), | (3) |
where N is the number of observations,
ˆz(ti,a) is the vector of estimates of forecast, obtained by numerical solution of Equations (1), (2) under given initial conditions and η(ti)=0.
Suppose that in the neighborhood of some point ak, the functional J(a) may be approximated by expansion into a Taylor series to terms of the second order. Then, by means of differentiating with respect to a and equating the resulting derivative to zero, a value a that delivers a minimum to the functional in the neighborhood of ak can be obtained:
a=ak−(d2J(ak)da2k)−1dJ(ak)dak. | (4) |
Differentiating (3) twice, taking into account (1), (2) and substituting the corresponding derivatives in (4) will result in the following:
a=ak−(∑Ni=1dˆzT(ti,ak)dakR−1(ti)dˆzT(ti,ak)dak)−1×N∑i=1dˆzT(ti,ak)dakR−1(ti)(z(ti)−ˆz(ti,ak)). | (5) |
In Equation (5), an approximate expression for the second derivative is used. Arguments in favor of the admissibility of this technique are considered in [1].
Let us introduce a notation for the sensitivity functions of the forecast by parameters:
ϕ(ti)=dˆzT(ti,ak)dak. | (6) |
Let us now consider the neighborhood of the true values of the parameters ak=aucm. Note that Equation (2) can be written as
z(ti)=zucm(ti)+η(ti), | (7) |
where zucm(ti)=h(yucm(ti),aucm,u).
From Equation (5), the following Equation is obtained:
a=aucm−(∑Ni=1ϕ(ti)R−1(ti)ϕT(ti))−1× |
×∑Ni=1ϕ(ti)R−1(ti)(zucm(ti)−ˆz(ti,aucm))+ϕ(ti)R−1(ti)η(ti) | (8) |
In the right part of (8), zucm(ti)−ˆz(ti,aucm)≈0,i=¯1,N, since with the true values of the parameters, the estimates of forecast should coincide with the true values of the observations with high accuracy.
The second term ∑Ni=1ϕ(ti)R−1(ti)η(ti) up to multiplier R−1(ti)╱N is equal to the estimate of the mutual correlation function of the signals φ(ti) and η(ti) at zero shift. As N increases, it tends to zero, since by definition, the observation noise η(ti) is not correlated with the useful signals of the system.
Thus, the second term in (8) is approximately equal to zero, and the minimum of the functional in the neighborhood of the point aucm is reached at a≈aucm. So, the estimates are unbiased.
Now let us assume that the observations contain the interference υ(ti), caused by the mismatch between the model and the object. In this case,
z(ti)=zucm(ti)+η(ti)+υ(ti). | (9) |
Substituting (9) into (5) and taking into account (8) results in the following.
a=aucm−(N∑i=1ϕ(ti)R−1(ti)ϕT(ti))−1× |
×N∑i=1ϕ(ti)R−1(ti)(zucm(ti)−ˆz(ti,aucm))+ϕ(ti)R−1(ti)η(ti)+ϕ(ti)R−1(ti)υ(ti)≈ |
≈aucm−(∑Ni=1ϕ(ti)R−1(ti)ϕT(ti))−1∑Ni=1ϕ(ti)R−1(ti)υ(ti). | (10) |
Equation (10) shows that in the presence of interference interconnected with the signals of the system, the minimum of the functional (3) is reached at a point, shifted relative to aucm by a magnitude proportional to the product of the interference and the sensitivity functions (6).
For the interference caused by the mismatch between the model and the object, this product is generally not equal to zero, whereas the interference and the sensitivity functions are interrelated and determined by the type of input signal.
It can be seen from formula (10) that the bias of the parameter vector is a decomposition of the N-dimensional interference vector along the basis formed by sensitivity functions, which are also considered as N-dimensional vectors. If the interference belongs to the subspace formed by the sensitivity functions, then the parameter biases completely compensate for the interference. This means that when the biased estimates (10) are substituted into the model (1)–(2), a high degree of correspondence (up to noise η(ti),i=¯1,N) of the output signals of the model and the object will be observed. Therefore, the detection of interference υ(ti) and, accordingly, the fact of the bias of the parameter estimates turns out to be impossible in this case.
Therefore, parametric identification provides reliable results only if the object models, measurement systems object noise and measurements used for identification correspond to the true ones with high accuracy, and all unknown quantities are evaluated during identification.
If the tested object has factors that are unknown to the researcher and which cannot be taken into account in the used model or in the vector of the estimated parameters, then the identification estimates have biases, whose magnitude cannot be estimated by the degree of coincidence of the output signals of the model and the object.
This problem also occurs in structural identification, with the difference that it becomes more complicated due to the multiplicity of possible structures.
In this section, the general formulation of the identification problem will be discussed in more detail.
In the well-known monograph by P. Eickhoff [2], the following formulation of the identification problem is given, belonging to one of the founders of the identification theory, Zadeh [3]: "Identification is the determination by the input and output of such a system from a certain class of systems to which the system under test is equivalent." Another mathematical meaning is given to this definition in [2]: "It is necessary to define a class of systems L={S}, a class of input signals U and the concept of equivalence that is understood in the sense of an error criterion or a loss function, which is a functional from the output of the object y and the output of the model yM, that is E=E(y,yM)."
The purposes of identification are to find a model from a given class and the way to solve it and to analyze input and output signals.
This formulation of the problem does not go beyond purely mathematical categories (class of systems, class of signals and the concept of equivalence).
In the theory of identification, methods are developed to ensure the successful solution of the task. This is also confirmed by the testing of identification algorithms mentioned in the introduction based on data, generated using mathematical models.
In this approach, the problem of correspondence of the considered mathematical models to the world of real objects must be solved at the stage of formation of the initial class of systems, that is, beyond the scope of the identification process.
In the case of parametric identification, this approach means that before the start of parametric identification, a model has been formed that fully corresponds to the object, except a set of unknown parameters to be estimated.
The main problem of applying identification to real objects, in our opinion, is that in many subject areas, the a priori models available at the time of the beginning of natural tests of the object do not meet the assumption mentioned above. Therefore, it is highly probable that input and output signals of the object and also measurement and object noises contain components that are not taken into account in the model. Their negative impact on the estimates of the identification is described in the previous section.
The constructive way to move forward under such circumstances, we believe, is the joint use of identification and scientific and engineering disciplines responsible for this subject area.
It should be borne in mind that in this case we go beyond the framework of classic identification theory [2,3], which examines input and output signals on a predetermined set of mathematical models, and consider a broader problem referring to research of physical objects. To solve it, it is advisable to develop a system of methodological recommendations, in which the identification itself is only one of the stages.
The following parts of this article are devoted to the development of general rules that should guide the practical implementation of identification. We will consider the field of parameters identification of aircraft models using flight test data. The general nature of the rules suggests that they may be of interest in identifying objects of other types.
The above study allows us to formulate general rules for the implementation of the aircraft parameters identification using flight test data.
The rules are based on recognition of the fact that the experimental data may contain components that are not taken into account in the models used for identification, which produces biased identification estimates. Therefore, the main goal is to ensure the reliability of the obtained results.
From what was said earlier, it follows that the identification of models of real objects is not a purely mathematical task; therefore, close analogues should be sought in the area of complex human-machine systems or high-tech production. For example, it is well known [5] that one of the basic principles of quality management of high-tech products is quality monitoring at all stages of the production process, that is, input monitoring of raw materials and components, monitoring of all technological operations and final output monitoring. This approach is fully applicable to ensuring the reliability of identification. It is necessary to check the compatibility of experimental data, the correctness of the functioning of identification algorithms, the convergence of the model and experiment in the terms of output signals, the consistency of the identification results with each other, their compliance with the laws of aerodynamics and the degree of consistency with a priori data. Therefore, the first rule is the need for reliability control at all stages of implementation of identification.
From the formula for the bias of parameter estimates obtained in section 2, it follows that an unaccounted-for interference then creates biases of parameter estimates when it fully or partially belongs to the subspace determined by the sensitivity functions of the identified parameters. Those components of interference that do not belong to this subspace, first, do not affect parameter estimates and, second, are easily detected when comparing the output signals of the model and the object. It is obvious that the smaller the subspace of sensitivity functions is, the smaller the number of estimated parameters.
Hence, the second rule follows: It is necessary to strive for the decomposition of the general identification problem into particular subtasks with a small number of parameters that are solved autonomously. Thus, in the problem of aircraft parameters identification, it is advisable to separate the verification of the measurements and registration system (data control) and the identification of the aircraft motion model (estimation of aerodynamic coefficients). In the process of identification, the various motion channels (pitch and lateral motion) should also be evaluated separately.
In applied sciences and engineering practice, there is a well known approach where, instead of general problems, the solution of which is difficult or impossible, partial problems are successfully solved, based on knowledge from a specific subject area. Thus, the third rule involves the widespread use of known data about the object of identification contained in related scientific and engineering disciplines.
In accordance with the fourth rule, identification should be considered as a human-machine process in which the key role belongs to the researcher, since it is he who ensures the correctness of the identification and the correct interpretation of the obtained results. In particular, it is necessary to provide for such a form of identification results that is convenient for a human researcher to perceive.
The final rule is compactness. All work carried out in accordance with the previous rules should be carried out to the minimum required extent, as the identification of real technical objects is always carried out under strict constraints and in terms of time and the amount of labor of involved specialists.
Thus, the following are general rules for practical aircraft parameters identification:
1. reliability control at all stages of identification,
2. decomposition of the general problem with subsequent complex verification,
3. wide use of well-known scientific and engineering results obtained in this subject area,
4. recognition of the key role of the researcher making the final decision and the use in the identification process of the ability of a human researcher to analyze information presented in an informal (for example, graphical) form,
5. compactness of all performed works.
In order to clarify the meaning of the general rules formulated above, a few specific cases are considered in this section.
Case 1. One of the tasks solved in the identification of aerodynamic coefficients of aircraft according to flight experiments data is the choice of equations of motion of the object. In the discipline of flight dynamics, a wide range of models has been created, differing in degrees of simplification: the division of spatial motion into longitudinal and lateral, short- and long-period, linearization relative to a steady trajectory, the use of relations of the form sinα≈α,cosα≈1 for small values of angular quantities, etc. These models were developed in order to reduce the amount of calculations, apply methods for studying linear systems, obtain analytical solutions and other reasons. For identification algorithms of nonlinear dynamic systems implemented numerically on modern computers, these considerations lose relevance. On the contrary, replacing exact ratios with approximations generates additional non-random interference associated with useful signals and, as shown above, is capable of creating biases in parameter estimates. Therefore, it is advisable to use for identification complete and very accurate equations of spatial motion of the aircraft, obtained from the basic laws of mechanics with minimal simplifications [6]. We consider one of these models below in Case 2. As for Case 1, it illustrates the rule of wide use of well-known results obtained in this subject area.
Case 2. When identifying the aerodynamic coefficients of the aircraft, a model of the measurement system is used. Undetected errors of this model can lead to biases in the estimates of the identified parameters. Due to the rules of decomposition and reliability control at all stages, the model of the measurement system should be checked separately. To increase reliability, in addition to regular checks of the on-board measurement system according to the operating manual, the following comprehensive check is recommended, using the relations between the main flight parameters determined by the equations of motion.
The following equations are derived from the general model of the spatial motion of the aircraft [6]:
dαdt=ωz−1cosβ[(axV−ωysinβ)sinα+(ayV+ωxsinβ)cosα], |
dβdt=azVcosβ−(axVsinβ−ωy)cosα+(ayVsinβ+ωx)sinα, |
dVdt=axcosαcosβ−aysinαcosβ+azsinβ, | (11) |
dυdt=ωysinγ+ωzcosγ, |
dγdt=ωx−tgυ(ωycosγ−ωzsinγ), |
where α, β are the angles of attack and sideslip (rad);
ωx,ωy,ωz are angular velocities relative to body-fixed axes (rad/s);
υ,γ are angles of pitch and roll (rad);
V is true airspeed (m/s);
ax,ay,az are accelerations along body-fixed axes determined by the formulae
ax=g(nx−sinυ), |
ay=g(ny−cosυcosγ), | (12) |
az=g(nz+cosυsinγ), |
where nx,ny,nz are overloads along body-fixed axes.
The main feature of these equations is that they do not depend on the aerodynamic coefficients of the aircraft, since the accelerations included in the right parts can be calculated through the values of overloads measured in flight.
Equations (11), (12) take the following vector form:
y'(t)=f(y(t),a,u(t)), |
where y(t),u(t) are vectors of output and input signals,
a is a vector of parameters to be identified.
In this case, the vector y(t) consists of the signals α(t),β(t),V(t),υ(t),γ(t). The vector of input signals includes the values of angular velocities measured in flight ωx,ωy,ωz and overloads nx,ny,nz.
The initial conditions y(t0) are set based on the results of parameter measurements α(t),β(t),V(t),υ(t),γ(t) at the beginning of the processing section.
Direct numerical integration of the system of differential Equations (11) taking into account (12) generally does not give positive results, as the constant components of the measurement errors of the input signals ωx,ωy,ωz and nx,ny,nz create errors of the linear trend type at the output of the integrals, which does not allow comparing the output signals of the model and the object. To eliminate this effect, a vector of unknown parameters aT consisting of constant components of measurement errors of signals ωx,ωy,ωz and nx,ny,nz is introduced:
aT=[CωxCωyCωzCnxCnyCnz]. |
To find parameter estimates, some kind of parametric identification algorithm is applied [4]. After obtaining estimates of constant errors, numerical integration of Equations (11), (12) is performed. With a properly functioning measurement system, the output signals of the model should match well with the corresponding measurements made in flight. The mismatches are random and, for example, for angles of attack and pitch usually do not exceed 0.4 degrees. On the contrary, the presence of significant mismatches indicates unaccounted-for measurement errors. In some cases, the source of the error can be determined by visual analysis. For example, time-shift errors are easily detected on graphs, and they often occur in modern measuring systems due to inaccurate synchronization of information flows from various onboard systems. The use of this approach is discussed in more detail in [7,8] and further in case 3.
Case 3. In this case, the comparison of the flight data with simulation data is conducted. In Figure 1, the angle of attack for multistep aircraft control stick deviations channel is shown.
A comparison of the flight and simulated angles of attack αexp,αsim_1 shows the presence of a dynamic error of the time shift type. Additional analysis showed that a low-frequency filter was installed on board in the angle of attack channel, smoothing out measurement noise and creating delays of up to 0.25 s. After taking into account the specified filter, a high degree of compliance (signals αexp,αsim_2) was obtained in the model.
Case 4. The dynamic error revealed in the Case 3 can lead to various errors in the analysis of flight data. For example, in flight tests the relation cy(α) is calculated from experimental data. The values of the lift coefficient are determined by the formula
cye(ti)=(ny(ti)cosα(ti)+nx(ti)sinα(ti))mg−Psin(α(ti))qS, | (13) |
where P is the engine thrust and which is true under the condition β≈0.
Figure 2 shows the dependence of Cy(α) obtained by using the angle of attack measured in flight αexp with delay of up to 0.25 s, as it was shown in case 3. The view of the graph leads to the idea of the presence of aerodynamic hysteresis, but according to aerodynamics, such a type of hysteresis may not happen in small angles of attack. Here, we again employ the rule of the wide use of well-known results obtained in this subject area. Indeed, the actual reason—the dynamic error of the smoothing filter—was revealed above in case 3. In Figure 3, the same data are shown after correcting the angle of attack measurements by a time shift of 0.25 seconds ahead of time (αexp_corr). As one can see, the nature of the dependence is approaching a straight line, which coincides with a priori aerodynamic characteristics of this aircraft. The remaining fluctuations characterize the level of non-excluded experimental errors.
Case 5. In the case of a properly functioning on-board measurement and registration system, the degree of compliance of the signals measured in flight and calculated in the model is very high even in intensive maneuvering modes.
Figure 4 shows the convergence of signals of pitch and roll angles during the "barrel roll" maneuver.
As a result of a generalized analysis of more than 20 different flight intervals for proper measurements, the following values of standard deviation of mismatches were obtained: along the channels of the angles of attack and sideslip 0.1... 0.4 degrees, pitch angle 0.2... 0.4 degrees, roll angle 0.3... 1.3 degrees, true airspeed 0.5... 0.8 m/s. Significant discrepancies usually indicate a violation of the correct operation of the measurement system. Therefore, in Figure 5, deviations of the pitch angle values in flight from the corresponding signal of the model characterize the errors of the aircraft artificial horizon (attitude indicator) due to vigorous maneuvering in the roll channel.
The formulated general principles allow the practical implementation of identification methods to processing the flight test data. The cases of application to flight data processing are shown. The detailed presentation of this technique is given in [8,9]. The technique was successfully applied to refine the bank of aerodynamic data of several aircraft in the main operational range of flight modes and at the overcritical angles of attack [9].
This work was carried out with the support of the Russian Foundation for Basic Research, project 20-08-00449.
The authors declare they have not used artificial intelligence (AI) tools in the creation of this article.
The authors declare that they have no conflict of interest.
[1] | Ljung L (1987) System Identification: Theory for User. - Prentice-Hall, Englewood Cliffs, New Jersey. |
[2] | Eykhoff P (1974) System Identification: Parameters and State Estimation. – John Wiley and Sons Ltd. |
[3] | Zadeh LA (1962) From Circuit Theory to System Theory. Proc. IRE, 50: 856–865. |
[4] | Klein V, Morelli E (2006) Aircraft System Identification. Theory and Practice (AIAA, Reston). |
[5] | ISO GR (2015) Quality management systems – Requirements. IDT. 9001. |
[6] | Nauka Moscow (1998) Aerodynamics, Stability, and Controllability of Hypersonic Aircraft, Ed. by G. S. Byushgens. |
[7] | Jategaonkar RV (2006) Flight vehicle system identification: A tie domain methodology, American Institute of Aeronautics and Astronautics. Reston, VA: AIAA, Inc. |
[8] | Korsun ON, Nikolaev SV, Om MH, et al. (2021) Detection of dynamic errors in aircraft flight data, IOP Conference Series: Materials Science and Engineering, IOP Publishing, 1027: 012011. https://doi.org/10.1088/1757-899X/1027/1/012011 |
[9] |
Korsun ON, Stulovskii AV, Ovcharenko VN, et al. (2018) Identification of aerodynamic coefficients of longitudinal movement and error estimates for onboard measurements of supercritical angles of attack. J Comput Sys Sci Int 57: 374–389. https://doi.org/10.1134/S1064230718030048 doi: 10.1134/S1064230718030048
![]() |
1. | O. N. Korsun, B. K. Poplavsky, A. V. Stulovskii, Moung Htang Om, Identification of Engine Thrust and Aerodynamic Drag Force According to Flight Test Data with Smoothing of Random Measurement Errors, 2024, 63, 1064-2307, 432, 10.1134/S1064230724700321 | |
2. | O. N. Korsun, B. K. Poplavsky, A. V. Stulovskii, Moung Htang Om, Identification of Engine Thrust and Aerodynamic Drag Force According to Flight Test Data with Smoothing of Random Measurement Errors, 2024, 0002-3388, 69, 10.31857/S0002338824030066 | |
3. | O. N. Korsun, M. H. Om, Evaluation of the Reliability of Empirical Mathematical Models of Dynamic Systems Using Input Signal Shift Method, 2025, 26, 2619-1253, 111, 10.17587/mau.26.111-118 | |
4. | O. N. Korsun, Moung Htang Om, A. V. Stulovskii, The use of optimal control in the problem of thrust and drag force coefficient identification, 2025, 2523-3947, 10.1007/s42401-025-00356-y |