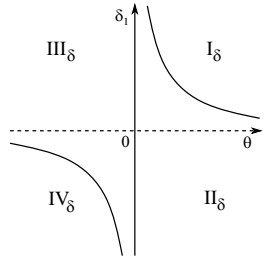
Low alloy nickel steel was chosen for this experiment because it is suitable for grinding balls application due to its high hardness and corrosion resistance. This study aimed to see the effect of different sub-zero treatments on the hardness, fractography and corrosion properties of low alloy nickel steel. The prepared specimens were heated to the austenitizing temperature of 980 ℃ in a furnace for one hour and water-quenched until they reached room temperature. Furthermore, the quenched specimens were chilled in liquid nitrogen for a variated time of 10, 60 or 360 min, followed by tempering treatment at 200 ℃ for one hour. According to the hardness test, the sub-zero treatment is effective in hardening materials, where the hardness value increases as the sub-zero treatment time increases, ranging from 204.93 to 417.98 HV. The fractography test indicated ductile fracture characterized by dimples at the fractured surface. Moreover, the corrosion test showed an enhancement of corrosion resistance with increased sub-zero treatment time.
Citation: Vinda Puspasari, Satrio Herbirowo, Alvin Muhammad Habieb, Dedi Pria Utama, Rahadian Roberto, Bintang Adjiantoro. Effect of sub-zero treatments on hardness and corrosion properties of low-alloy nickel steel[J]. AIMS Materials Science, 2023, 10(1): 55-69. doi: 10.3934/matersci.2023004
[1] | Mengting Sui, Yanfei Du . Bifurcations, stability switches and chaos in a diffusive predator-prey model with fear response delay. Electronic Research Archive, 2023, 31(9): 5124-5150. doi: 10.3934/era.2023262 |
[2] | Yang Jin, Wanxiang Li, Hongbing Zhang . Transition characteristics of the dynamic behavior of a vehicle wheel-rail vibro-impact system. Electronic Research Archive, 2023, 31(11): 7040-7060. doi: 10.3934/era.2023357 |
[3] | Qinghua Zhu, Meng Li, Fang Han . Hopf bifurcation control of the ML neuron model with Hc bifurcation type. Electronic Research Archive, 2022, 30(2): 615-632. doi: 10.3934/era.2022032 |
[4] | Yuan Xue, Jinli Xu, Yuting Ding . Dynamics analysis of a diffusional immunosuppressive infection model with Beddington-DeAngelis functional response. Electronic Research Archive, 2023, 31(10): 6071-6088. doi: 10.3934/era.2023309 |
[5] | Qixiang Wen, Shenquan Liu, Bo Lu . Firing patterns and bifurcation analysis of neurons under electromagnetic induction. Electronic Research Archive, 2021, 29(5): 3205-3226. doi: 10.3934/era.2021034 |
[6] | San-Xing Wu, Xin-You Meng . Hopf bifurcation analysis of a multiple delays stage-structure predator-prey model with refuge and cooperation. Electronic Research Archive, 2025, 33(2): 995-1036. doi: 10.3934/era.2025045 |
[7] | Fengrong Zhang, Ruining Chen . Spatiotemporal patterns of a delayed diffusive prey-predator model with prey-taxis. Electronic Research Archive, 2024, 32(7): 4723-4740. doi: 10.3934/era.2024215 |
[8] | Mengxin He, Zhong Li . Dynamic behaviors of a Leslie-Gower predator-prey model with Smith growth and constant-yield harvesting. Electronic Research Archive, 2024, 32(11): 6424-6442. doi: 10.3934/era.2024299 |
[9] | Wenxin Zhang, Lijun Pei . Bifurcation and chaos in N-type and S-type muscular blood vessel models. Electronic Research Archive, 2025, 33(3): 1285-1305. doi: 10.3934/era.2025057 |
[10] | Weiyu Li, Hongyan Wang . Dynamics of a three-molecule autocatalytic Schnakenberg model with cross-diffusion: Turing patterns of spatially homogeneous Hopf bifurcating periodic solutions. Electronic Research Archive, 2023, 31(7): 4139-4154. doi: 10.3934/era.2023211 |
Low alloy nickel steel was chosen for this experiment because it is suitable for grinding balls application due to its high hardness and corrosion resistance. This study aimed to see the effect of different sub-zero treatments on the hardness, fractography and corrosion properties of low alloy nickel steel. The prepared specimens were heated to the austenitizing temperature of 980 ℃ in a furnace for one hour and water-quenched until they reached room temperature. Furthermore, the quenched specimens were chilled in liquid nitrogen for a variated time of 10, 60 or 360 min, followed by tempering treatment at 200 ℃ for one hour. According to the hardness test, the sub-zero treatment is effective in hardening materials, where the hardness value increases as the sub-zero treatment time increases, ranging from 204.93 to 417.98 HV. The fractography test indicated ductile fracture characterized by dimples at the fractured surface. Moreover, the corrosion test showed an enhancement of corrosion resistance with increased sub-zero treatment time.
The theory of bifurcations is crucial in understanding qualitative properties of differential systems depending on one or more parameters. Bifurcations of codimension one and two are well-addressed in the literature [1,2,3] when they are non-degenerate, but many open problems emerge when they become degenerate [4] or the codimension is beyond 2.
The classical normal form of the double-Hopf bifurcation in differential systems of dimension 4 is based on six generic conditions (HH.0)–(HH.5) [1]. Some of the pioneering papers reporting results on non-degenerate double-Hopf bifurcation are references [5,6,7,8].
If one or more generic conditions fail to be satisfied, a degeneracy arises and, thus, the generic results are not valid anymore. In this work we study two degenerate double-Hopf bifurcations. The degeneracy we refer at is related to generic conditions which are necessary in obtaining normal forms.
Another added value of our results is that we discovered new bifurcation diagrams and new phase portraits and, thus, new properties of double-Hopf bifurcation which, to our knowledge, were not previously reported in the literature. The results emerged from the analysis of a new system which appeared due to degeneracy.
Our study is performed in a general framework and produces generic results which can be applied in particular systems exhibiting this bifurcation. The double-Hopf bifurcation (degenerate or not) can be often met in practical models based on differential systems and having a large number of equations (at least four) [4,9,10,11,12]. Interesting results on discrete time systems undergoing double-Hopf bifurcations are presented in [11]. Thus, understanding better this bifurcation and obtaining new generic properties of it is desirable and important for particular models describing real-world phenomena. This is the purpose of the present work.
The paper is organized as follows. In Section 2 the classical normal form obtained in [1] using six generic conditions (HH.0)–(HH.5) is presented and a new normal form up to order 3 in polar coordinates is obtained as two of the generic conditions, namely (HH.1) and (HH.3) fail. In Section 3, the dynamics and bifurcation of this normal form, around the origin, is analyzed as the condition (HH.3) is not satisfied, but (HH.1) is valid, while in Section 4 a similar study is done when the condition (HH.1) is not fulfilled, but (HH.3) is satisfied. In Section 5 some conclusions and the relationship between the dynamics of the 2D amplitude system and the dynamics of the 4D truncated normal form are given.
Consider a differential system of the form
$ \begin{equation} \dot{x} = f\left( x,\alpha \right) ,\ \ \ x\in \mathbb{R}^{4},\ \ \ \alpha = \left( \alpha _{1},\alpha _{2}\right) \in \mathbb{R}^{2}, \end{equation} $ | (2.1) |
with $ f $ smooth, $ \dot{x} = \frac{dx}{dt} $, and assume that $ x = 0 $ is an equilibrium point of the system for all $ \alpha $ with $ \left\vert \alpha \right\vert = \sqrt{\alpha _{1}^{2}+\alpha _{1}^{2}} $ small enough, that is, $ f\left(0, \alpha \right) \equiv 0; $ $ x = 0 $ stands for $ x = (0, 0, 0, 0) $ and $ \alpha = 0 $ for $ \alpha = (0, 0). $ The system (2.1) can be written as
$ \begin{equation} \dot{x} = A\left( \alpha \right) x+F\left( x,\alpha \right) \end{equation} $ | (2.2) |
where $ F\left(x, \alpha \right) = O\left(\left\vert x\right\vert ^{2}\right) $ is a smooth function denoting Taylor rest with terms of order at least $ 2. $
Assume the matrix $ A(\alpha) $ has two pairs of simple complex-conjugate eigenvalues $ \lambda _{1}, $ $ \overline{\lambda }_{1}, $ $ \lambda _{2}, $ $ \overline{\lambda }_{2}, $
$ \begin{equation*} \lambda _{1}\left( \alpha \right) = \mu _{1}\left( \alpha \right) +i\omega _{1}\left( \alpha \right) ,\ \ \ \lambda _{2}\left( \alpha \right) = \mu _{2}\left( \alpha \right) +i\omega _{2}\left( \alpha \right) \end{equation*} $ |
for all sufficiently small $ \left\vert \alpha \right\vert, $ where $ \mu _{1, 2}\left(\alpha \right) $ and $ \omega _{1, 2}\left(\alpha \right) $ are smooth functions of $ \alpha $ such that $ \mu _{1}\left(0\right) = \mu _{2}\left(0\right) = 0, $ respectively, $ \omega _{1}\left(0\right) = \omega _{10} > 0 $ and $ \omega _{2}\left(0\right) = \omega _{20} > 0. $ When these conditions are satisfied, the origin of system (2.1) is called a double-Hopf or Hopf-Hopf singularity, and, under supplementary conditions, a double-Hopf bifurcation occurs at $ \alpha = 0 $.
In complex coordinates, the system (2.2) can be further reduced to the form
$ \begin{equation} \left\{ \begin{array}{c} \dot{z}_{1} = \lambda _{1}\left( \alpha \right) z_{1}+g\left( z_{1},\overline{z }_{1},z_{2},\overline{z}_{2},\alpha \right) \\ \dot{z}_{2} = \lambda _{2}\left( \alpha \right) z_{2}+h\left( z_{1},\overline{z }_{1},z_{2},\overline{z}_{2},\alpha \right) \end{array} \right. \end{equation} $ | (2.3) |
where
$ \begin{equation*} g\left( z_{1},\overline{z}_{1},z_{2},\overline{z}_{2},\alpha \right) = \sum\limits_{j+k+l+m\geq 2}g_{jklm}\left( \alpha \right) z_{1}^{j}\overline{z} _{1}^{k}z_{2}^{l}\overline{z}_{2}^{m} \end{equation*} $ |
and
$ \begin{equation*} h\left( z_{1},\overline{z} _{1},z_{2},\overline{z}_{2},\alpha \right) = \sum\limits_{j+k+l+m\geq 2}h_{jklm}\left( \alpha \right) z_{1}^{j}\overline{z}_{1}^{k}z_{2}^{l} \overline{z}_{2}^{m}. \end{equation*} $ |
Other two equations are the conjugates of system $ \left(2.3\right) $ and are omitted in what follows.
A first normal form corresponding to system(2.3) is described in the following lemma, reported in [1].
Lemma 2.1. Assume that the following conditions take place [1]
$ \begin{equation*} \mathit{\mbox{(HH.0)}} \qquad k\omega _{10}\neq l\omega _{20},\ \ \ k,l > 0,\ \ \ k+l\leq 5. \end{equation*} $ |
Then, there exists a locally defined, smooth and smoothlyparameter-dependent, invertible transformation of the complex variables thatreduces system $ (2.3) $ for all sufficiently small $ \left\vert \alpha\right\vert $ into the following form:
$ \begin{equation} \left\{ \begin{array}{c} \dot{w}_{1} = \lambda _{1}w_{1}+w_{1}\left\vert w_{1}\right\vert ^{2}\left( a_{1}+ib_{1}\right) +w_{1}\left\vert w_{2}\right\vert ^{2}\left( a_{2}+ib_{2}\right) +w_{1}\left\vert w_{1}\right\vert ^{4}\left( a_{3}+ib_{3}\right) \\ +w_{1}\left\vert w_{1}\right\vert ^{2}\left\vert w_{2}\right\vert ^{2}\left( a_{4}+ib_{4}\right) +w_{1}\left\vert w_{2}\right\vert ^{4}\left( a_{5}+ib_{5}\right) +O\left( \left\Vert \left( w_{1},\overline{w}_{1},w_{2}, \overline{w}_{2}\right) \right\Vert ^{6}\right) \\ \dot{w}_{2} = \lambda _{2}w_{2}+w_{2}\left\vert w_{1}\right\vert ^{2}\left( c_{1}+id_{1}\right) +w_{2}\left\vert w_{2}\right\vert ^{2}\left( c_{2}+id_{2}\right) +w_{2}\left\vert w_{1}\right\vert ^{4}\left( c_{3}+id_{3}\right) \\ +w_{2}\left\vert w_{1}\right\vert ^{2}\left\vert w_{2}\right\vert ^{2}\left( c_{4}+id_{4}\right) +w_{2}\left\vert w_{2}\right\vert ^{4}\left( c_{5}+id_{5}\right) +O\left( \left\Vert \left( w_{1},\overline{w}_{1},w_{2}, \overline{w}_{2}\right) \right\Vert ^{6}\right) \end{array} \right. \end{equation} $ | (2.4) |
where $ w_{1, 2} $ are complex-valued functions, $ \left\Vert \left(w_{1}, \overline{w}_{1}, w_{2}, \overline{w}_{2}\right) \right\Vert ^{2} = \left\vert w_{1}\right\vert ^{2}+\left\vert w_{2}\right\vert ^{2} $.
In system (2.4) we used the following notations: $ a_{1}+ib_{1} = G_{2100}\left(\alpha \right), $ $ a_{2}+ib_{2} = G_{1011}\left(\alpha \right), $ $ a_{3}+ib_{3} = G_{3200}\left(\alpha \right), $ $ a_{4}+ib_{4} = G_{2111}\left(\alpha \right) $ and $ a_{5}+ib_{5} = G_{1022}\left(\alpha \right), $ respectively, $ c_{1}+id_{1} = H_{1110}\left(\alpha \right), $ $ c_{2}+id_{2} = H_{0021}\left(\alpha \right), $ $ c_{3}+id_{3} = H_{2210}\left(\alpha \right), $ $ c_{4}+id_{4} = H_{1121}\left(\alpha \right) $ and $ c_{5}+id_{5} = H_{0032}\left(\alpha \right), $ where $ a_{i} = a_{i}\left(\alpha \right), $ $ b_{i} = b_{i}\left(\alpha \right), $ $ c_{i} = c_{i}\left(\alpha \right) $ and $ d_{i} = d_{i}\left(\alpha \right), $ $ i = \overline{1, 5}, $ are real smooth functions of $ \alpha $ which depend on the coefficients $ g_{ijkl}\left(\alpha \right) $ and $ h_{ijkl}\left(\alpha \right). $ The coefficients of third order terms in system (2.4) are given explicitly in [1].
The system (2.4) has been transformed further in [1] to a normal form based on six generic conditions.
In polar coordinates $ w_{1} = r_{1}e^{i\varphi _{1}} $ and $ w_{2} = r_{2}e^{i \varphi _{2}}, $ the system (2.4) becomes
$ \begin{equation} \left\{ \begin{array}{l} \dot{r}_{1} & = & r_{1}\left( \mu _{1}+a_{1}r_{1}^{2}+a_{2}r_{2}^{2}+a_{3}r_{1}^{4}+a_{4}r_{1}^{2}r_{2}^{2}+a_{5}r_{2}^{4}\right) +\Phi _{1}\left( r_{1},r_{2},\varphi _{1},\varphi _{2},\alpha \right) \\ \dot{r}_{2} & = & r_{2}\left( \mu _{2}+c_{1}r_{1}^{2}+c_{2}r_{2}^{2}+c_{3}r_{1}^{4}+c_{4}r_{1}^{2}r_{2}^{2}+c_{5}r_{2}^{4}\right) +\Phi _{2}\left( r_{1},r_{2},\varphi _{1},\varphi _{2},\alpha \right) \\ \dot{\varphi}_{1} & = & \omega _{1}+\Psi _{1}\left( r_{1},r_{2},\varphi _{1},\varphi _{2},\alpha \right) \\ \dot{\varphi}_{2} & = & \omega _{2}+\Psi _{2}\left( r_{1},r_{2},\varphi _{1},\varphi _{2},\alpha \right) \end{array} \right. , \end{equation} $ | (2.5) |
where the real functions $ \Phi _{k}, $ $ \Psi _{k} $ are smooth functions of their arguments and are $ 2\pi $-periodic in $ \varphi _{j}, $ $ \Phi _{k} = O\left(\left(r_{1}^{2}+r_{2}^{2}\right) ^{3}\right) $, $ \Psi _{k}\left(0, 0, \varphi _{1}, \varphi _{2}\right) = 0 $.
The main dynamics of the system (2.5) is given by its first two equations
$ \begin{equation} \left\{ \begin{array}{l} \dot{r}_{1} = r_{1}\left( \mu _{1}+a_{1}r_{1}^{2}+a_{2}r_{2}^{2}+a_{3}r_{1}^{4}+a_{4}r_{1}^{2}r_{2}^{2}+a_{5}r_{2}^{4}\right) +O\left( \left( r_{1}^{2}+r_{2}^{2}\right) ^{3}\right) \\ \dot{r}_{2} = r_{2}\left( \mu _{2}+c_{1}r_{1}^{2}+c_{2}r_{2}^{2}+c_{3}r_{1}^{4}+c_{4}r_{1}^{2}r_{2}^{2}+c_{5}r_{2}^{4}\right) +O\left( \left( r_{1}^{2}+r_{2}^{2}\right) ^{3}\right) \end{array} \right., \end{equation} $ | (2.6) |
the other two describing only the rate of rotation of an orbit, and, because $ \omega _{1, 2}\left(0\right) \neq 0, $ they can be approximated by
$ \begin{equation*} \dot{\varphi}_{1} = \omega _{10},\ \ \dot{\varphi}_{2} = \omega _{20}. \end{equation*} $ |
Changing to $ \rho _{i} = r_{i}^{2}, $ $ i = 1, 2, $ and truncating the higher order terms, system (2.6) leads to the planar system
$ \begin{equation} \left\{ \begin{array}{l} \dot{\rho_{1}} & = & 2\rho _{1}\left( \mu _{1}+a_{1}\rho _{1}+a_{2}\rho _{2}+a_{3}\rho _{1}^{2}+a_{4}\rho _{1}\rho _{2}+a_{5}\rho _{2}^{2}\right) \\ \dot{\rho_{2}} & = & 2\rho _{2}\left( \mu _{2}+c_{1}\rho _{1}+c_{2}\rho _{2}+c_{3}\rho _{1}^{2}+c_{4}\rho _{1}\rho _{2}+c_{5}\rho _{2}^{2}\right) \end{array} \right. , \end{equation} $ | (2.7) |
referred as the amplitude equations; $ \dot{\rho}_{i} = \frac{d\rho _{i}}{dt}, $ $ i = 1, 2. $
In the hypotheses
$ \begin{align} \rm{(HH.0)}&\quad k\omega _{1}\left( 0\right) \neq l\omega _{2}\left( 0\right) ,\ \ \ k,l > 0,\ \ \ k+l\leq 5; \\ \rm{(HH.1)} &\quad p_{11}\left( 0\right) = Re\left( G_{2100}\left( 0\right) \right) \neq 0; \\ \rm{(HH.2)} &\quad p_{12}\left( 0\right) = Re\left( G_{1011}\left( 0\right) \right) \neq 0; \\ \rm{(HH.3)} &\quad p_{21}\left( 0\right) = Re\left( H_{1110}\left( 0\right) \right) \neq 0; \\ \rm{(HH.4)} &\quad p_{22}\left( 0\right) = Re\left( H_{0021}\left( 0\right) \right) \neq 0; \\ \rm{(HH.5)}&\quad \rm{the map }\alpha \longrightarrow \mu \left( \alpha \right) \rm{ is regular at }\alpha = 0, \end{align} $ | (2.8) |
in [1], the system (2.4) has been transformed further into the following normal form
$ \begin{equation} \left\{ \begin{array}{l} \dot{r}_{1} & = & r_{1}\left( \mu _{1}+p_{11}r_{1}^{2}+p_{12}r_{2}^{2}+s_{1}r_{2}^{4}\right) +\Phi _{1}\left( r_{1},r_{2},\varphi _{1},\varphi _{2},\alpha \right) \\ \dot{r}_{2} & = & r_{2}\left( \mu _{2}+p_{21}r_{1}^{2}+p_{22}r_{2}^{2}+s_{2}r_{1}^{4}\right) +\Phi _{2}\left( r_{1},r_{2},\varphi _{1},\varphi _{2},\alpha \right) \\ \dot{\varphi}_{1} & = & \omega _{1}+\Psi _{1}\left( r_{1},r_{2},\varphi _{1},\varphi _{2},\alpha \right) \\ \dot{\varphi}_{2} & = & \omega _{2}+\Psi _{2}\left( r_{1},r_{2},\varphi _{1},\varphi _{2},\alpha \right) \end{array} \right. , \end{equation} $ | (2.9) |
where the real functions $ \Phi _{k}, $ $ \Psi _{k} $ are smooth functions of their arguments and are $ 2\pi $-periodic in $ \varphi _{j}, $ $ \Phi _{k} = O\left(\left(r_{1}^{2}+r_{2}^{2}\right) ^{3}\right) $, $ \Psi _{k}\left(0, 0, \varphi _{1}, \varphi _{2}\right) = 0. $
Consequently, the truncated amplitude system obtained in [1] reads:
$ \begin{equation} \left\{ \begin{array}{l} \dot{\rho}_{1} & = & 2\rho _{1}\left( \mu _{1}+p_{11}\rho _{1}+p_{12}\rho _{2}+s_{1}\rho _{2}^{2}\right) \\ \dot{\rho}_{2} & = & 2\rho _{2}\left( \mu _{2}+p_{21}\rho _{1}+p_{22}\rho _{2}+s_{2}\rho _{1}^{2}\right) \end{array} \right. . \end{equation} $ | (2.10) |
This system is analyzed in two cases, the "simple case" as $ p_{11}(0)p_{22}(0) > 0 $ and the "difficult case" as $ p_{11}(0)p_{22}(0) < 0 $.
The study of the generic Hopf-Hopf bifurcation is also done in [2], starting with the amplitude system (2.6), truncated up to third order terms, in the nondegeneracy hypotheses
$ \begin{equation} a_{1}(0)\neq 0,a_{2}(0)\neq 0,c_{1}(0)\neq 0,c_{2}(0)\neq 0, \end{equation} $ | (2.11) |
and
$ \begin{equation} a_{1}(0)c_{2}(0)-a_{2}(0)c_{1}(0)\neq 0. \end{equation} $ | (2.12) |
In this paper we study the degenerate Hopf-Hopf bifurcation when conditions (HH.1) and (HH.3) are not satisfied. In order to do this, we derive a new normal form for the amplitude system.
Theorem 2.2. Assume that the following three generic conditions are satisfied:
$\textrm{(HH.2)}$ $ a_{2}\left(0\right) = Re\left[ G_{1011}\left(0\right) \right] \neq0, $
$\textrm{(HH.4)}$ $ c_{2}\left(0\right) = Re\left[ H_{0021}\left(0\right) \right] \neq0, $
$\textrm{(HH.5)}$ the map $ \alpha \mapsto \left(\mu _{1}\left(\alpha \right), \mu_{2}\left(\alpha \right) \right) $ is regular at $ \alpha = 0. $
Then, system $ (2.6) $ is locally topologically equivalent around theorigin $ O $, for all sufficiently small $ \left\vert \alpha \right\vert $, tothe following system
$ \begin{equation} \left\{ \begin{array}{l} \frac{d \rho_{1}}{d\tau} & = & 2\rho _{1}\left[ \mu _{1}+p_{11}\rho _{1}+p_{12}\rho _{2}+p_{13}\rho _{1}^{2}+p_{14}\rho _{1}\rho _{2}\right] + \sqrt{\rho _{1}}O\left( \left( \rho _{1}+\rho _{2}\right) ^{3}\right) \\ \frac{d \rho_{2}}{d\tau} & = & 2\rho _{2}\left[ \mu _{2}+p_{21}\rho _{1}+p_{22}\rho _{2}+p_{23}\rho _{1}^{2}+p_{25}\rho _{2}^{2}\right] +\sqrt{\rho _{2}} O\left( \left( \rho _{1}+\rho _{2}\right) ^{3}\right) \end{array} \right. , \end{equation} $ | (2.13) |
where
$ \begin{equation*} p_{11} = a_{1}+\mu _{1}n_{1},p_{12} = a_{2}+\mu _{1}n_{2},p_{13} = a_{3}+a_{1}n_{1},p_{14} = a_{4}+a_{1}n_{2}+a_{2}n_{1} \end{equation*} $ |
and
$ \begin{equation*} p_{21} = c_{1}+\mu _{2}n_{1},p_{22} = c_{2}+\mu _{2}n_{2},p_{23} = c_{3}+c_{1}n_{1},p_{25} = c_{5}+c_{2}n_{2}, \end{equation*} $ |
with $ n_{2}\left(\mu \right) = -\frac{a_{5}\left(\mu \right) }{a_{2}\left(\mu\right) } $ and $ n_{1}\left(\mu \right) = -\frac{c_{4}\left(\mu \right)+c_{1}\left(\mu \right) n_{2}\left(\mu \right) }{c_{2}\left(\mu \right) }, $ where $ p_{ij} = p_{ij}\left(\mu \right) $ for $ i = 1, 2 $ and $ j = \overline{1, 5}, $ are well-defined and smooth functions for all $ \left\vert \mu\right\vert $ small enough.
Proof. We rescale the time by
$ \begin{equation*} dt = \left( 1+n_{1}\rho _{1}+n_{2}\rho _{2}\right) d\tau \end{equation*} $ |
where $ n_{i} = n_{i}\left(\alpha \right), $ $ i = \overline{1, 2}, $ are smooth functions which will be determined later. Then, system (2.6) is orbitally equivalent to the system
$ \begin{equation*} \left\{ \begin{array}{l} \frac{d\rho _{1}}{d\tau } & = & 2\rho _{1}\left[ \mu _{1}+p_{11} \rho _{1}+p_{12}\rho _{2}+p_{13}\rho _{1}^{2}+p_{14}\rho _{1}\rho _{2}+p_{15} \rho _{2}^{2}\right] +\sqrt{\rho _{1}}O\left( \left\vert \rho \right\vert ^{3}\right) \\ \frac{d\rho _{2}}{d\tau } & = & 2\rho _{2}\left[ \mu _{2}+p_{21} \rho _{1}+p_{22}\rho _{2}+p_{23} \rho _{1}^{2}+p_{24}\rho _{1}\rho _{2}+p_{25}\rho _{2}^{2}\right] +\sqrt{\rho _{2}}O\left( \left\vert \rho \right\vert ^{3}\right) \end{array} \right. , \end{equation*} $ |
where $ p_{11} = a_{1}+\mu _{1}n_{1}, $ $ p_{12} = a_{2}+\mu _{1}n_{2}, $ $ p_{13} = a_{3}+a_{1}n_{1} $, $ p_{14} = a_{4}+a_{1}n_{2}+a_{2}n_{1}, $ and $ p_{15} = a_{5}+a_{2}n_{2} $, respectively $ p_{21} = c_{1}+\mu _{2}n_{1}, $ $ p_{22} = c_{2}+\mu _{2}n_{2}, $ $ p_{23} = c_{3}+c_{1}n_{1}, $ $ p_{24} = c_{4}+c_{1}n_{2}+c_{2}n_{1} $ and $ p_{25} = c_{5}+c_{2}n_{2}. $
Since $ a_{2}\left(0\right) \neq 0 $ and $ c_{2}\left(0\right) \neq 0, $ one can nullify the coefficients $ p_{15} $ and $ p_{24} $ by taking $ n_{2}\left(\alpha \right) = -\frac{a_{5}\left(\alpha \right) }{a_{2}\left(\alpha \right) } $ and $ n_{1}\left(\alpha \right) = -\frac{c_{4}\left(\alpha \right) +c_{1}\left(\alpha \right) n_{2}\left(\alpha \right) }{c_{2}\left(\alpha \right) }. $ Notice that $ n_{1}\left(\alpha \right) $ and $ n_{2}\left(\alpha \right) $ are well-defined for all $ \left\vert \alpha \right\vert $ small enough, and so are $ p_{ij}\left(\alpha \right). $
Assume the map $ \alpha \mapsto \left(\mu _{1}\left(\alpha \right), \mu _{2}\left(\alpha \right) \right) $ is regular at $ \alpha = 0, $ that is,
$ \begin{equation*} \left. \frac{\partial \mu _{1}}{\partial \alpha _{1}}\frac{\partial \mu _{2} }{\partial \alpha _{2}}-\frac{\partial \mu _{1}}{\partial \alpha _{2}}\frac{ \partial \mu _{2}}{\partial \alpha _{1}}\right\vert _{\alpha = 0}\neq 0. \end{equation*} $ |
From the Inverse Function Theorem this condition ensures that for any $ \mu _{1}, \mu _{2}\in \mathbb{R} $ with $ \left\vert \mu \right\vert = \sqrt{\mu _{1}^{2}+\mu _{2}^{2}} $ small enough, there exist $ \alpha _{1} = \alpha _{1}\left(\mu \right) $ and $ \alpha _{2} = \alpha _{2}\left(\mu \right) $ which are obtained locally from the system
$ \begin{equation*} \mu _{1,2} = \frac{\partial \mu _{1,2}}{\partial \alpha _{1}}\left( 0,0\right) \alpha _{1}+\frac{\partial \mu _{1,2}}{\partial \alpha _{2}}\left( 0,0\right) \alpha _{2}. \end{equation*} $ |
This implies that, one can consider further $ \mu = \left(\mu _{1}, \mu _{2}\right) $ as the parameter of the system. Thus, $ \omega _{1, 2} = \omega _{1, 2}\left(\mu \right), $ $ a_{i} = a_{i}\left(\mu \right), $ $ b_{i} = b_{i}\left(\mu \right), $ $ c_{i} = c_{i}\left(\mu \right), $ $ d_{i} = d_{i}\left(\mu \right), $ $ p_{ij} = p_{ij}\left(\mu \right), $ $ i = 1, 2, $ $ j = \overline{1, 5}. $ Since $ \mu _{1, 2}\left(0\right) = 0, $ the properties $ \omega _{1}\left(0\right) = \omega _{10} > 0 $ and $ \omega _{2}\left(0\right) = \omega _{20} > 0 $ are preserved. The theorem is proved.
Remark that the coefficients $ p_{ij} $ in system (2.13) are not the same as the ones in system (2.10), but the values $ p_{11}\left(0\right), $ $ p_{12}\left(0\right), $ $ p_{21}\left(0\right), $ $ p_{22}\left(0\right) $ are the same as in system (2.8).
The truncated 4D system of system (2.13) reads
$ \begin{equation} \left\{ \begin{array}{l} \frac{d\rho_{1}}{d\tau} = 2\rho _{1}\left[ \mu _{1}+p_{11}\rho _{1}+p_{12}\rho _{2}+p_{13}\rho _{1}^{2}+p_{14}\rho _{1}\rho _{2}\right] , \\ \frac{d\rho_{2}}{d\tau} = 2\rho _{2}\left[ \mu _{2}+p_{21}\rho _{1}+p_{22}\rho _{2}+p_{23}\rho _{1}^{2}+p_{25}\rho _{2}^{2}\right] , \\ \frac{d{\varphi}_{1}}{d\tau} = \omega _{10}, \\ \frac{d{\varphi}_{2}}{d\tau} = \omega _{20}, \end{array} \right. \end{equation} $ | (2.14) |
where $ p_{12}(0)p_{22}(0)\neq 0, $ because $ p_{12}(0) = a_{2}(0)\neq 0, \; \ $from (HH.2) and $ p_{22}(0) = c_{2}\left(0\right) \neq 0, $ from (HH.4).
We aim to tackle in this work the normal form system (2.13), truncated up to third order terms, when $ a_{2}\left(0\right) c_{2}\left(0\right) > 0. $
Assume $ p_{12}\left(0\right) = a_{2}\left(0\right) < 0 $ and $ p_{22}\left(0\right) = c_{2}\left(0\right) < 0. $ Make the changes
$ \begin{equation} \xi _{1} = -p_{12}\left( \mu \right) \rho _{1},\xi _{2} = -p_{22}\left( \mu \right) \rho _{2},t = 2\tau . \end{equation} $ | (2.15) |
The transformation $ \left(\rho _{1}, \rho _{2}\right) \longmapsto \left(\xi _{1}, \xi _{2}\right) $ is well defined for all $ \left\vert \mu \right\vert $ small enough, because $ p_{12}\left(0\right) \neq 0 $ and $ p_{22}\left(0\right) \neq 0 $ are satisfied from (HH.2) and (HH.4), and it is nonsingular as $ a_{2}\left(0\right) c_{2}\left(0\right) \neq 0. $ Since $ \frac{d\xi _{1}}{dt} = -p_{12}\left(\mu \right) \frac{d\rho _{1}}{ d\tau }\frac{d\tau }{dt} $ and $ \frac{d\xi _{2}}{dt} = -p_{22}\left(\mu \right) \frac{d\rho _{2}}{d\tau }\frac{d\tau }{dt}, $ the form system (2.13) in its lowest terms in $ \left(\xi _{1}, \xi _{2}\right) $, known as the truncated form, becomes $ \ $
$ \begin{equation} \left\{ \begin{array}{l} \dot{\xi}_{1} & = & \xi _{1}\left[ \mu _{1}-\theta \left( \mu \right) \xi _{1}-\gamma \left( \mu \right) \xi _{2}+M\left( \mu \right) \xi _{1}\xi _{2}+N\left( \mu \right) \xi _{1}^{2}\right] \\ \dot{\xi}_{2} & = & \xi _{2}\left[ \mu _{2}-\delta \left( \mu \right) \xi _{1}-\xi _{2}+S\left( \mu \right) \xi _{1}^{2}+P\left( \mu \right) \xi _{2}^{2}\right] \end{array} \right. , \end{equation} $ | (2.16) |
where $ \theta \left(\mu \right) = \frac{p_{11}}{p_{12}}\left(\mu \right), $ $ \gamma \left(\mu \right) = \frac{p_{12}}{p_{22}}\left(\mu \right), $ $ M\left(\mu \right) = \frac{p_{14}}{p_{12}p_{22}}\left(\mu \right), $ $ N\left(\mu \right) = \frac{p_{13}}{p_{12}^{2}}\left(\mu \right), $ $ \delta \left(\mu \right) = \frac{p_{21}}{p_{12}}\left(\mu \right), $ $ S\left(\mu \right) = \frac{p_{23}}{p_{12}^{2}}\left(\mu \right) $ and $ P\left(\mu \right) = \frac{p_{25}}{p_{22}^{2}}\left(\mu \right) $. However, in what follows, some of these expressions are needed only at $ \mu = 0.\ $
The dot over quantities stands now for the derivatives with respect to the new time. Denote also by $ f $ the smooth vector field associated with system (2.16).
Remark 1. Due to the transformation system (2.15), the stability of an equilibrium point in the 2D system (2.16) is preserved in the 4D system (2.14); see also [1].
Remark 2. 1) Notice that $ \theta (0) = \frac{a_{1}\left(0\right) }{ a_{2}\left(0\right) }, $ $ \gamma (0) = \frac{a_{2}\left(0\right) }{ c_{2}\left(0\right) } $ and $ \delta (0) = \frac{c_{1}\left(0\right) }{ a_{2}\left(0\right) } $ are well-defined from (HH.2), (HH.4). Moreover, $ \gamma (0) > 0 $ while $ \theta (0)\delta (0) $ can be $ 0. $
2) When $ p_{12}\left(0\right) > 0 $ and $ p_{22}\left(0\right) > 0, $ the change $ \xi _{1} = p_{12}\left(\mu \right) \rho _{1}, $ $ \xi _{2} = p_{22}\left(\mu \right) \rho _{2}, $ $ t = -2\tau $ lead to
$ \begin{equation} \left\{ \begin{array}{l} \dot{\xi}_{1} & = & \xi _{1}\left[ -\mu _{1}-\theta \left( \mu \right) \xi _{1}-\gamma \left( \mu \right) \xi _{2}-M\left( \mu \right) \xi _{1}\xi _{2}-N\left( \mu \right) \xi _{1}^{2}\right] \\ \dot{\xi}_{2} & = & \xi _{2}\left[- \mu _{2}-\delta \left( \mu \right) \xi _{1}-\xi _{2}-S\left( \mu \right) \xi _{1}^{2}-P\left( \mu \right) \xi _{2}^{2}\right] \end{array} \right. , \end{equation} $ | (2.17) |
that can be reduced to system (2.16).
As $ \rho _{i} = r_{i}^{2}\geq 0, $ $ i = 1, 2, $ taking into account system (2.15) and the fact that $ p_{12}\left(0\right) < 0, $ $ p_{22}\left(0\right) < 0, $ it follows that the system (2.16) must be studied only on the set (the first quadrant)
$ \begin{equation*} D = \left\{ \left( \xi _{1},\xi _{2}\right) \in \mathbb{R}^{2},\xi _{1}\geq 0,\xi _{2}\geq 0\right\} . \end{equation*} $ |
Thus, only the equilibria of system (2.16) situated in $ D $ will be analyzed.
Remark 3. The lines $ \xi _{1} = 0 $ and $ \xi _{2} = 0 $ are invariant curves for system (2.16), thus the set $ D $ is invariant with respect to the dynamical system associated to system (2.16).
In the following we analyze the truncated amplitude system (2.16) in two cases when the Hopf-Hopf bifurcation degenerates, namely (ⅰ) $ \delta \left(0\right) = 0, $ $ \theta (0)\neq 0; $ (ⅱ) $ \theta \left(0\right) = 0, $ $ \delta (0)\neq 0. $
Remind that system (2.16) which is analyzed in the next two sections was obtained in the hypotheses (HH.0), (HH.2), (HH.4), (HH.5), and, as $ p_{12}(0) < 0 $, $ p_{22}(0) < 0 $, we have $ \gamma(0) > 0 $.
In addition, our study is done for $ \mu $ in a neighborhood of the origin $ V_{\varepsilon } $ given by $ \left\vert \mu \right\vert < \varepsilon $, for $ \varepsilon > 0 $ sufficiently small.
As all the coefficients are smooth functions depending on the parameter $ \mu $, for $ \mu \in V_{\varepsilon } $ we can write
$ \theta (\mu ) = \theta(0)+ \frac{\partial \theta }{\partial \mu _{1}}\left( 0\right)\mu _{1} +\frac{\partial \theta }{\partial \mu _{2}}\left( 0\right)\mu _{2}+O(\left\vert \mu \right\vert ^{2}), $ |
and similar for the other coefficients. In all the expressions below only the significant lower order terms in $ \mu_1, \mu_2 $ will be considered, as necessary. Also, in order to save symbols, if, for instance we have $ N(0)\ne 0 $ we shall denote $ N = N(0), $ thus, close to $ \mu = 0 $, we have $ N(\mu) = N+O(|\mu |), $ and so on for the other coefficients.
Assume that $ \delta (0) = 0, $ $ \theta (0)\neq 0. $ This means that condition (HH.3) is not satisfied, but (HH.1) is valid.
Then $ \delta (\mu) = \delta _{1}\mu _{1}+\delta _{2}\mu _{2}+O(\left\vert \mu \right\vert ^{2}), $ with $ \delta _{1} = \frac{ \partial \delta }{\partial \mu _{1}}\left(0\right), $ $ \delta _{2} = \frac{ \partial \delta }{\partial \mu _{2}}\left(0\right). $ One of the equilibria of system (2.16) is $ E_{0} = \left(0, 0\right). $ Two more equilibria
$ \begin{equation*} E_{1} = \left( \frac{1}{\theta }\mu _{1}+O\left( \mu _{1}^{2}\right) ,0\right) \;{\rm{ and }}\;E_{2} = \left( 0,\mu _{2}+O\left( \mu _{2}^{2}\right) \right) \end{equation*} $ |
where $ \theta = \theta(0) $, bifurcate from $ E_{0} $ as soon as $ \mu _{1}\neq 0, $ respectively, $ \mu _{2}\neq 0 $, i.e. at the bifurcation lines
$ \begin{equation*} Y_{-} = \{(\mu _{1},\mu _{2}),\mu _{1} = 0,\mu _{2} < 0\},\quad Y_{+} = \{(\mu _{1},\mu _{2}),\mu _{1} = 0,\mu _{2} > 0\}, \end{equation*} $ |
and
$ \begin{equation*} X_{-} = \{(\mu _{1},\mu _{2}),\mu _{2} = 0,\mu _{1} < 0\},\quad X_{+} = \{(\mu _{1},\mu _{2}),\mu _{2} = 0,\mu _{1} > 0\}, \end{equation*} $ |
respectively. Their stability is described by Lemma 3.1.
Lemma 3.1. (1) The eigenvalues of $ E_{0} $ are $ \mu _{1} $ and $ \mu _{2}. $
(2) The eigenvalues of $ E_{1} $ are $ -\mu _{1}+O\left(\mu _{1}^{2}\right) $and $ \left(\mu _{2}+\frac{S-\delta _{1}\theta }{\theta ^{2}}\mu_{1}^{2}\right) \left(1+O\left(\mu _{1}\right) \right) $, thus, whenever $ E_{1} $ lies in $ D, $ $ E_{1} $ is either (i) a saddle as $ \mu _{1}\left(\mu_{2}+\frac{S-\delta _{1}\theta }{\theta ^{2}}\mu _{1}^{2}\right) > 0, $ (ii)an unstable node as $ \mu _{2}+\frac{S-\delta _{1}\theta }{\theta ^{2}}\mu_{1}^{2} > 0, \mu _{1} < 0, \ $(iii) a stable node as $ \mu _{2}+\frac{S-\delta_{1}\theta }{\theta ^{2}}\mu _{1}^{2} < 0, \mu _{1} > 0. $
(3) The eigenvalues of $ E_{2} $ are $ \mu _{1}-\gamma \mu _{2}+O(\mu _{2}^{2}) $and $ -\mu _{2}+O(\mu _{2}^{2}). $ Therefore, for $ \left\vert \mu \right\vert $sufficiently small, $ \ $ $ E_{2} $ is (i) a saddle as $ \mu _{1}-\gamma \mu_{2} > 0, $ (ii) a stable node as $ \mu _{1}-\gamma \mu _{2} < 0, $ whenever itexists in $ D. $
On the other hand, system (2.16) has the nontrivial equilibrium $ E_{3} = \left(\xi _{1}^{\ast }, \xi _{2}^{\ast }\right), $ with
$ \begin{equation*} \left\{ \begin{array}{c} \xi _{1}^{\ast } = \frac{1}{\theta }\mu _{1}\left( 1+O(\left\vert \mu \right\vert \right) -\frac{\gamma }{\theta }\mu _{2}\left( 1+O(\left\vert \mu \right\vert \right) \rm{ }\ \ \ \ \\ \xi _{2}^{\ast } = \mu _{2}\left( 1+O(\left\vert \mu \right\vert \right) + \frac{S-\delta _{1}\theta }{\theta ^{2}}\mu _{1}^{2}\left( 1+O\left( \left\vert \mu \right\vert \right) \right) \end{array} \right. . \end{equation*} $ |
The associated eigenvalues satisfy
$ \begin{eqnarray} \lambda _{1}\lambda _{2} & = &\xi _{1}^{\ast }\xi _{2}^{\ast }\left[ \theta +O\left( \left\vert \mu \right\vert \right) \right] , \\ \lambda _{1}+\lambda _{2} & = &-\mu _{1}+(\gamma -1)\mu _{2}+O\left( \left\vert \mu \right\vert ^{2}\right) . \end{eqnarray} $ | (3.1) |
When $ \theta > 0, $ $ E_{3} $ lies in $ D $ for parameters in the region
$ \begin{equation*} R_{1} = \left\{ \left( \mu _{1},\mu _{2}\right) \in V_{\varepsilon } ,\mu _{1}-\gamma \mu _{2} > 0,\mu _{2}+\frac{S-\delta _{1}\theta }{\theta ^{2}}\mu _{1}^{2} > 0\right\}. \end{equation*} $ |
It is easy to see that for $ \mu \in R_{1}, $ with $ \left\vert \mu \right\vert $ sufficiently small, we have $ \lambda _{1}\lambda _{2} > 0 $ and the curve $ \lambda _{1}+\lambda _{2} = 0 $ does not cross region $ R_{1}, $ thus $ \lambda _{1}+\lambda _{2} < 0, $ and $ E_{3} $ is stable.
When $ \theta < 0, $ $ E_{3} $ lies in $ D $ for parameters in region
$ \begin{equation*} R_{2} = \left\{ \left( \mu _{1},\mu _{2}\right) \in V_{\varepsilon } ,\mu _{1}-\gamma \mu _{2} < 0,\mu _{2}+\frac{S-\delta _{1}\theta }{\theta ^{2}}\mu _{1}^{2} > 0\right\} . \end{equation*} $ |
By system (3.1), it follows $ \lambda _{1}\lambda _{2} < 0, $ for sufficiently small $ \left\vert \mu \right\vert. $ Thus, $ E_{3} $ is a saddle. The following result is proved.
Lemma 3.2. If $ \theta < 0, $ then $ E_{3} $ is a saddle, while if $ \theta > 0, $ the equilibrium $ E_{3} $ is a hyperbolic attractor, for allsufficiently small $ \left\vert \mu \right\vert, $ for which $ E_{3} $ lies in $ D. $
Consequently there can be no Hopf bifurcation at $ E_{3}. $
As the term $ \delta _{2} $ does not influence the topological type of equilibria, we may restrict our attention only to the $ \left(\theta, \delta _{1}\right) - $ plane.
Regions $ R_{1} $ and $ R_{2} $ are delimitated by the curves
$ \begin{eqnarray} T_{1} & = &\left\{\left( \mu _{1},\mu _{2}\right) \in V_{\varepsilon }, \mu _{1} = \gamma \mu _{2}+O\left( \mu _{2}^{2}\right) ,\mu _{2} > 0\right\} , \end{eqnarray} $ | (3.2) |
$ \begin{eqnarray} \rm{ }T_{2} & = &\left\{ \left( \mu _{1},\mu _{2}\right) \in V_{\varepsilon },\mu _{2} = -\frac{S-\delta _{1}\theta }{\theta ^{2}}\mu _{1}^{2}+O\left( \mu _{1}^{3}\right) \right\} . \end{eqnarray} $ | (3.3) |
We notice that $ E_{3} $ collides with $ E_{2} $ on $ T_{1}, $ and it collides with $ E_{1} $ on $ T_{2}. $
Proposition 3.3. System $ (2.16) $ experiences the following transcritical bifurcations:
(i) at the point $ E_{0} $ as the parameter $ \mu _{1} $ varies through thebifurcation value $ \mu _{1} = 0, $ for a fixed $ \mu _{2}\neq 0 $ (when $ E_{0} = E_{1}); $
(ii) at the point $ E_{0} $ as the parameter $ \mu _{2} $ varies through thebifurcation value $ \mu _{2} = 0, $ for a fixed $ \mu _{1}\neq 0 $ (when $ E_{0} = E_{2}); $
(iii) at the point $ E_{1} $ as the parameter $ (\mu _{1}, \mu _{2}) $ crossesthe curve $ T_{2} $ (when $ E_{1} = E_{3}); $
(iv) at the point $ E_{2} $ as the parameter $ (\mu _{1}, \mu _{2}) $ crosses thecurve $ T_{1} $ (when $ E_{2} = E_{3}). $
Proof. We apply Sotomayor Theorem ([13,14], to prove these statements.
(ⅰ) The Jacobian matrix $ Df(E_{0}, \mu _{0}) $ at $ \mu _{0} = \left(0, \mu _{2}\right), $ $ \mu _{2}\neq 0, $ has a zero eigenvalue with the right eigenvector $ v = \left(1, 0\right) ^{T} $ and the left eigenvector $ w = \left(1, 0\right) ^{T}. $ It follows
$ \begin{equation*} w^{T}f_{\mu _{1}}\left( E_{0},\mu _{0}\right) = 0,\quad w^{T}Df_{\mu _{1}}(E_{0},\mu _{0}) = 1\neq 0,\quad w^{T}[D^{2}f(E_{0},\mu _{0})(v,v)] = -2\theta \neq 0, \end{equation*} $ |
thus the transcritical bifurcation conditions are satisfied.
(ⅱ) The Jacobian matrix $ Df(E_{0}, \mu _{0}) $ at $ \mu _{0} = \left(\mu _{1}, 0\right), $ $ \mu _{1}\neq 0, $ has a zero eigenvalue with the right eigenvector $ v = \left(0, 1\right) ^{T} $ and the left eigenvector $ w = \left(0, 1\right) ^{T}. $ It follows
$ \begin{equation*} w^{T}f_{\mu _{2}}\left( E_{0},\mu _{0}\right) = 0,\quad w^{T}Df_{\mu _{2}}(E_{0},\mu _{0}) = 1\neq 0,\quad w^{T}[D^{2}f(E_{0},\mu _{0})(v,v)] = -2\neq 0, \end{equation*} $ |
ensuring the existence of a transcritical bifurcation.
(ⅲ) Consider $ \mu _{0}\in T_{2}, $ $ \mu _{1}\neq 0, $ and $ \mu _{2} $ as a bifurcation parameter. We find that $ v = (-\gamma, \theta)^{T} $ and $ w = (0, 1)^{T} $ are right and left eigenvectors of the Jacobian matrix $ Df(E_{1}, \mu _{0}), $ respectively, corresponding to the zero eigenvalue, and
$ \begin{align*} &w^{T}f_{\mu _{2}}\left( E_{1},\mu _{0}\right) = 0,\quad w^{T}Df_{\mu _{2}}(E_{1},\mu _{0}) = \theta \neq 0,\\ & w^{T}[D^{2}f(E_{1},\mu _{0})(v,v)] = 2\theta (\delta \gamma -\theta )-4S\gamma \mu _{1}\neq 0, \end{align*} $ |
consequently, for sufficiently small $ \left\vert \mu \right\vert, \ $the conditions are satisfied.
(ⅳ) Finally, consider $ \mu _{0}\in T_{1}, $ $ \mu _{2}\neq 0, $ and $ \mu _{1} $ as a bifurcation parameter, thus $ \mu _{0} = (\gamma \mu _{2}, \mu _{2}) $. We find the eigenvectors $ v = (1, -\delta)^{T} $ and $ w = (1, 0)^{T}, $ and
$ \begin{align*} &w^{T}f_{\mu _{1}}\left( E_{2},\mu _{0}\right) = 0,\quad w^{T}Df_{\mu _{1}}(E_{2},\mu _{0}) = 2(\delta \gamma -\theta )+2M\mu _{2}\neq 0,\\ & w^{T}[D^{2}f(E_{1},\mu _{0})(v,v)] = 1\neq 0, \end{align*} $ |
for sufficiently small $ \left\vert \mu \right\vert. $
For a fixed $ \gamma > 0, $ and $ S > 0, $ the curves $ S-\delta _{1}\theta = 0, $ $ \theta = 0, $ determine four regions in the $ \left(\theta, \delta _{1}\right) - $ plane, illustrated in Figure 1, corresponding to the following cases:
Ⅰ$ _{\delta } $: $ \theta > 0, $ $ S-\delta _{1}\theta < 0; $
Ⅱ$ _{\delta } $: $ \theta > 0, \ $ $ S-\delta _{1}\theta > 0; $
Ⅲ$ _{\delta } $: $ \theta < 0, \ $ $ S-\delta _{1}\theta > 0; $
Ⅳ$ _{\delta } $: $ \theta < 0, \ $ $ S-\delta _{1}\theta < 0. $
For each region Ⅰ$ _{\delta } $-Ⅳ$ _{\delta }, $ in the parametric portraits in the $ \left(\mu _{1}, \mu _{2}\right) $- plane, the parameter strata are determined by the origin and the bifurcation curves $ X_{-}, $ $ X_{+}, $ $ Y_{-}, $ $ Y_{+}, $ $ T_{1}, $ and $ T_{2}. $ Consequently, the following result is obtained.
Theorem 3.4. For all $ \gamma > 0, S > 0, $ in the $ \left(\theta, \delta_{1}\right) - $ plane, the bifurcation curves consist of
$ \begin{equation*} O\cup T_{1}\cup T_{2}\cup X_{-}\cup X_{+}\cup Y_{-}\cup Y_{+}. \end{equation*} $ |
The four parameter portraits for $ (\theta, $ $ \delta _{1}) $ in regions Ⅰ$ _{\delta } $, Ⅱ$ _{\delta } $, Ⅲ$ _{\delta } $, Ⅳ$ _{\delta } $ are shown in Figure 2. The 14 generic phase portraits are given in Figure 3.
In Figure 3 we used the following markers to emphasize the topological type of the equilibria: a black disc for an attractor, a black square for a repeller and a diamond for a saddle point. All of these phase portraits are also found in the nondegenerate double-Hopf bifurcation case [1,2]. As $ S\leq 0, $ a similar study can be done.
Remark 4. As proved in Proposition 3.3, each of the curves $ X_{-}, $ $ X_{+}, $ $ Y_{-}, $ $ Y_{+}, $ $ T_{1}, $ $ T_{2} $ consists of values of transcritical bifurcation (for which two of the four equilibria collide and change topological type), separating two parameter strata, one where both equilibria involved in the transcritical bifurcation lie on $ D $ and one where only one of them lies on $ D. $ Although for parameters on a bifurcation curve the corresponding equilibrium is a saddle-node, the generic phase portrait is equivalent to the one of the stratum where only one of the two equilibria is in $ D. $
Assume $ \theta (0) = 0, $ $ \delta (0)\neq 0. $ In this case the condition (HH.1) is not satisfied, and (HH.3) is valid. Then $ \theta (\mu) = \theta _{1}\mu _{1}+\theta _{2}\mu _{2}+O(\left\vert \mu \right\vert ^{2}). $
In this case, two trivial equilibria of system (2.16) are $ E_{0} = \left(0, 0\right), $ with the eigenvalues $ \mu _{1} $ and $ \mu _{2}, $ and $ E_{2} = \left(0, \mu _{2}+O\left(\mu _{2}^{2}\right) \right) $ with eigenvalues $ \mu _{1}-\gamma \mu _{2}+O(\left\vert \mu\right\vert ^2) $ and $ -\mu _{2} +P\mu _{2}^{2}(1+O(\left\vert \mu\right\vert)) $. Remark that these equilibria keep the same form as in the case treated in the previous section, and their stability remains as described by Lemma 3.1.
As $ \xi _{2} = 0, $ the equation giving the equilibrium points reads:
$ \begin{equation} \mu _{1}-\theta (\mu) \xi _{1}+N (\mu)\xi _{1}^{2} = 0. \end{equation} $ | (4.1) |
Assume that $ N(0)\neq 0, $ thus $ N\left(\mu \right) \neq 0 $ for sufficiently small $ \left\vert \mu \right\vert. $ If $ \Delta (\mu) = \theta ^{2}(\mu)-4N(\mu)\mu _{1}\geq 0, $ Eq (4.1) has two real solutions
$ \begin{equation*} \xi _{11}\left( \mu \right) = \frac{\theta \left( \mu \right) -\sqrt{\Delta \left( \mu \right) }}{2N\left( \mu \right) },\quad \xi _{12}\left( \mu \right) = \frac{\theta \left( \mu \right) +\sqrt{\Delta \left( \mu \right) }}{ 2N\left( \mu \right) },\quad \xi _{11}\leq \xi _{12}. \end{equation*} $ |
Thus, as $ \mu _{1}N > 0, $ two equilibrium points, $ E_{11} = \left(\xi _{11}, 0\right) $ and $ E_{12} = \left(\xi _{12}, 0\right), $ are lying on the positive $ \xi _{1}- $axis, provided that $ \left(\mu _{1}, \mu _{2}\right) \in R_{3}, $ where $ R_{3} $ is a region in the parametric plane given by
$ \begin{equation} R_{3} = \left\{ \left( \mu _{1},\mu _{2}\right) \in V_{\varepsilon }\left\vert \Delta \left( \mu \right) > 0,\mu _{1}N > 0,\theta N > 0\right. \right\} . \end{equation} $ | (4.2) |
Obviously, as $ \Delta \left(\mu \right) = 0, $ we have $ E_{11} = E_{12} = \frac{ \theta }{2N}. $
As $ \mu _{1}N < 0, $ we have $ \xi _{11} < 0 < \xi _{12} $, thus, only the equilibrium $ E_{12} $ lies in D for parameters in region
$ \begin{equation} R_{4} = \left\{ \left( \mu _{1},\mu _{2}\right) \in V_{\varepsilon }\left\vert \Delta (\mu ) > 0,\mu _{1}N < 0\right. \right\} . \end{equation} $ | (4.3) |
As $ \mu _{1} = 0, $ we have $ E_{11} = E_{0} $ if $ \theta _{2}\mu _{2}N > 0, $ while $ E_{12} = E_{0} $ if $ \theta _{2}\mu _{2}N < 0. $ Using the Implicit Functions Theorem, we find that, for sufficiently small $ \left\vert \mu \right\vert, $ $ \Delta \left(\mu \right) = 0 $ for parameters on the curve, denoted also by $ \Delta, $ given as
$ \begin{equation*} \Delta = \left\{ \left( \mu _{1},\mu _{2}\right) \in V_{\varepsilon },\mu _{1} = \frac{\theta _{2}^{2}}{4N}\mu _{2}^{2}+O(\mu _{2}^{3}),\theta _{2}\mu _{2}N > 0\right\} . \end{equation*} $ |
The eigenvalues of $ E_{11} = \left(\xi _{11}, 0\right) $ satisfy $ \lambda _{1}^{E_{11}} = -\xi _{11}\sqrt{\Delta \left(\mu \right) }\leq 0, $ and
$ \begin{equation*} \lambda _{2}^{E_{11}} = \mu _{2}-\frac{S}{N}\mu _{1}+\xi _{11}\left( \frac{ \theta S}{N}-\delta \right) . \end{equation*} $ |
For $ E_{12} = \left(\xi _{12}, 0\right) $ we have $ \lambda _{1}^{E_{12}} = \xi _{12}\sqrt{\Delta \left(\mu \right) }\geq 0 $ and
$ \begin{equation*} \lambda _{2}^{E_{12}} = \mu _{2}-\frac{S}{N}\mu _{1}+\xi _{12}\left( \frac{\theta S}{N}-\delta \right) . \end{equation*} $ |
An important relation for studying the behavior of $ E_{11} $ and $ E_{12} $ is
$ \begin{equation} \lambda _{2}^{E_{11}}\lambda _{2}^{E_{12}} = \frac{1}{N}\delta ^{2}\mu _{1}(1+O(\left\vert \mu \right\vert ))+\frac{1}{N}(N-\theta _{2}\delta )\mu _{2}^{2}(1+O(\left\vert \mu \right\vert ). \end{equation} $ | (4.4) |
Note that as $ \lambda _{2}^{E_{11}}\lambda _{2}^{E_{12}} = 0, $ we get
$ \begin{equation*} \lambda _{2}^{E_{11}}+\lambda _{2}^{E_{12}} = \frac{1}{N}(2N-\theta _{2}\delta )\mu _{2}+O(\mu _{2}^{2}). \end{equation*} $ |
Lemma 4.1. As the parameter $ \mu $ crosses the curve $ \Delta, $ asaddle-node bifurcation takes place. In addition, if $ N > 0, $ for parameter sufficiently small, close to the curve $ \Delta, $ we have:
(i) $ E_{11} $ is an attractor and $ E_{12} $ is a saddle as $ \mu _{2}\left(2N-\delta \theta _{2}\right) < 0; $
(ii) $ E_{11} $ is a saddle and $ E_{12} $ is a repeller as $ \mu _{2}\left(2N-\delta \theta _{2}\right) > 0. $
Proof. Consider $ \mu _{0}\in \Delta. $ Then $ \xi _{11} = \xi _{12} = \frac{ \theta _{2}}{2N}\mu _{2}+O(\mu _{2}^{2}), $ and the eigenvalues of equilibrium $ E_{11} $ are $ \lambda _{1} = 0 $, $ \lambda _{2} = \frac{2N-\delta \theta _{2}}{2N}\mu _{2}+O(\mu _{2}^{2}). $ The Jacobian matrix $ Df(E_{11}, \mu _{0}), $ has for the zero eigenvalue the right eigenvector $ v = \left(1, 0\right) ^{T} $ and the left eigenvector $ w = \left(2N-\delta \theta _{2}, \gamma \theta _{2}\right) ^{T}. $ It follows
$ \begin{equation*} w^{T}f_{\mu _{1}}\left( E_{0},\mu _{0}\right) = \frac{\theta _{2}}{2N}\mu _{2}\neq 0,\quad w^{T}[D^{2}f(E_{0},\mu _{0})(v,v)] = \theta _{2}\mu _{2}+O(\mu _{2}^{2})\neq 0, \end{equation*} $ |
for sufficiently small $ \left\vert \mu \right\vert. $ Thus, according to Sotomayor Theorem, a saddle-node bifurcation takes place.
For parameters close to the bifurcation curve we have $ sign(\lambda _{1}^{E_{11}}) = -sign(N), $ $ sign(\lambda _{1}^{E_{12}}) = sign(N), $ and $ sign(\lambda _{2}^{E_{11}}) = sign(\lambda _{2}^{E_{12}}) = sign(\frac{2N-\delta \theta _{2}}{2N}\mu _{2}). $ Consequently, if $ N > 0, $ the equilibrium $ E_{11} $ is an attractor and $ E_{12} $ is a saddle as $ \mu _{2}\left(2N-\delta \theta _{2}\right) < 0, $ while as $ \mu _{2}\left(2N-\delta \theta _{2}\right) > 0, $ the equilibrium $ E_{11} $ is a saddle and $ E_{12} $ is a repeller.
Denote by
$ \begin{equation*} \Delta _{+} = \left\{ \left( \mu _{1},\mu _{2}\right) \in \Delta ,\mu _{2}\left( 2N-\delta \theta _{2}\right) > 0\right\} \end{equation*} $ |
and
$ \begin{equation*} \Delta _{-} = \left\{ \left( \mu _{1},\mu _{2}\right) \in \Delta ,\mu _{2}\left( 2N-\delta \theta _{2}\right) < 0\right\} . \end{equation*} $ |
As a consequence of Lemma 4.1, for a parameter $ \mu $ in $ \Delta _{+}, $ sufficiently small, the equilibrium $ E_{11}( = E_{12}) $ is a saddle-node, with one attractive direction and three repelling directions, while for a parameter $ \mu $ in $ \Delta _{-}, $ the equilibrium $ E_{11} $ is a saddle-node, with one repelling direction and three attractive ones.
Consider the curves
$ \begin{eqnarray*} Y_{-}^{\prime } & = &\left\{ \left( \mu _{1},\mu _{2}\right) \in V_\varepsilon,\mu _{1} = 0,\theta _{2}N\mu _{2} < 0\right\} , \\ Y_{+}^{\prime } & = &\left\{ \left( \mu _{1},\mu _{2}\right) \in V_\varepsilon ,\mu _{1} = 0,\theta _{2}N\mu _{2} > 0\right\} . \end{eqnarray*} $ |
Proposition 4.2. The following statements hold:
(i) for $ \mu \in Y_{+}^{\prime }, $ equilibria $ \ E_{0} $ and $ E_{11} $coincide; when parameters cross this curve, a transcritical bifurcationtakes place, and $ E_{0} $ and $ E_{11} $ interchange the topological type;
(ii) for $ \mu \in Y_{-}^{\prime }, $ equilibria $ \ E_{0} $ and $ E_{12}\ $coincide and are saddle-nodes. A transcritical bifurcation takes place whenparameters are crossing the curve $ Y_{-}^{\prime }, $ and $ E_{0} $ and $ E_{12} $interchange the topological type.
(iii) for $ \mu \in \left\{ \left(\mu _{1}, \mu _{2}\right), \mu _{2} = 0, \mu_{1}\neq 0\right\}, $ equilibria $ \ E_{0} $ and $ E_{2}\ $coincide and atranscritical bifurcation takes place when parameters are crossing thiscurve.
Proof. As in Proposition 3.3, we apply Sotomayor Theorem ([13]) to prove these statements.
(ⅰ) Consider $ \mu _{0}\in Y_{+}^{\prime }. $ As $ \mu _{1} = 0 $ and $ \theta _{2}\mu _{2}N > 0, $ it follows that $ E_{11} = E_{0} $. The Jacobian matrix $ Df(E_{0}, \mu _{0}) $ at $ \mu _{0} = \left(0, \mu _{2}\right), $ $ \mu _{2}\neq 0, $ has a zero eigenvalue with the right eigenvector $ v = \left(1, 0\right) ^{T} $ and the left eigenvector $ w = \left(1, 0\right) ^{T}. $ It follows
$ \begin{align*} &w^{T}f_{\mu _{1}}\left( E_{0},\mu _{0}\right) = 0,\quad w^{T}Df_{\mu _{1}}(E_{0},\mu _{0}) = 1\neq 0,\\ & w^{T}[D^{2}f(E_{0},\mu _{0})(v,v)] = -2\theta _{2}\mu _{2}\neq 0, \end{align*} $ |
for sufficiently small $ \left\vert \mu \right\vert, $ thus the transcritical bifurcation conditions are satisfied.
(ⅱ) Consider $ \mu _{0}\in Y_{-}^{\prime }. $ As $ \mu _{1} = 0 $ and $ \theta _{2}\mu _{2}N < 0, $ it follows that $ \xi _{12} = 0, $ thus $ E_{12} = E_{0} $. We obtain the same values for the quantities involved in the transcritical bifurcation conditions as in case (i).
(ⅲ) The Jacobian matrix $ Df(E_{0}, \mu _{0}) $ at $ \mu _{0} = \left(\mu _{1}, 0\right), $ $ \mu _{1}\neq 0, $ has a zero eigenvalue with the right eigenvector $ v = \left(0, 1\right) ^{T} $ and the left eigenvector $ w = \left(0, 1\right) ^{T}. $ It follows
$ \begin{equation*} w^{T}f_{\mu _{2}}\left( E_{0},\mu _{0}\right) = 0,\quad w^{T}Df_{\mu _{2}}(E_{0},\mu _{0}) = 1\neq 0,\quad w^{T}[D^{2}f(E_{0},\mu _{0})(v,v)] = -2\neq 0, \end{equation*} $ |
ensuring the existence of a transcritical bifurcation.
For $ E_{3} = \left(\xi _{1}^{\ast }, \xi _{2}^{\ast }\right), $ solution of system
$ \begin{equation*} \left\{ \begin{array}{c} \mu _{1}-(\theta _{1}\mu _{1}+\theta _{2}\mu _{2})\xi _{1}-\gamma (\mu) \xi _{2}+M(\mu)\xi _{1}\xi _{2}+N(\mu)\xi _{1}^{2} = 0, \\ \mu _{2}-\delta(\mu) \xi _{1}-\xi _{2}+S(\mu)\xi _{1}^{2}+P(\mu) \xi _{2}^{2} = 0, \end{array} \right. \end{equation*} $ |
we obtain
$ \begin{eqnarray*} \xi _{1}^{\ast } & = &-\frac{1}{\gamma \delta }(\mu _{1}-\gamma \mu _{2})+O(\left\vert \mu \right\vert ^{2}), \\ \xi _{2}^{\ast } & = &\frac{1}{\gamma }\mu _{1}(1+O(\left\vert \mu \right\vert ))+\frac{N-\theta _{2}\delta }{\delta ^{2}\gamma }\mu _{2}^{2}\left( 1+O\left( \left\vert \mu \right\vert \right) \right) . \end{eqnarray*} $ |
Thus, $ E_{3} $ is a nontrivial equilibrium for system (2.16) provided
$ \begin{equation*} \mu \in R_{5} = \left\{ \left( \mu _{1},\mu _{2}\right) \in V_\varepsilon ,\delta (\mu _{1}-\gamma \mu _{2}) < 0,\delta ^{2}\mu _{1}+\left( N-\theta _{2}\delta \right) \mu _{2}^{2} > 0\right\} . \end{equation*} $ |
Denote by
$ \begin{equation*} T_{3} = \left\{ \left( \mu _{1},\mu _{2}\right) \in V_\varepsilon ,\mu _{1} = \frac{\theta _{2}\delta -N}{\delta ^{2}}\mu _{2}^{2}+O(\mu _{2}^{3})\right\} \ \end{equation*} $ |
the parameter curve for which $ \xi _{2}^{\ast } = 0. $ Thus $ R_{5} $ is delimited by $ T_{1} $ and $ T_{3} $.
The eigenvalues of $ E_{3} $ satisfy
$ \begin{equation} \lambda _{1}\lambda _{2} = \xi _{1}^{\ast }\xi _{2}^{\ast }\left( -\gamma \delta +O\left( \left\vert \mu \right\vert \right) \right) \;{\rm{ and }}\; \lambda _{1}+\lambda _{2} = \frac{1}{\gamma \delta ^{2}}p\left( \mu \right) , \end{equation} $ | (4.5) |
where $ p(\mu) = -\delta ^{2}\mu _{1}\left(1+O\left(\left\vert \mu \right\vert \right) \right) +k_{1}\mu _{2}^{2}\left(1+O\left(\left\vert \mu \right\vert \right) \right) $ and $ k_{1} = \left(\theta _{2}\delta -N\right) +\gamma \left(2N-\theta _{2}\delta \right). $
Applying Implicit Functions Theorem to the implicit equation $ p\left(\mu _{1}, \mu _{2}\right) = 0, $ the following lemma is obtained.
Lemma 4.3. If $ (\theta _{2}\delta -N)+\gamma (2N-\theta _{2}\delta)\neq0, $ there exists a neighborhood $ U $ of $ 0 $ in the parameter plane such that $ p\left(\mu \right) = 0 $ in $ U $ iff $ \mu \in U\cap H, $ where
$ \begin{equation} H = \left\{ \left( \mu _{1},\mu _{2}\right) ,\mu _{1} = \frac{(\theta _{2}\delta -N)+\gamma (2N-\theta _{2}\delta )}{\delta ^{2}}\mu _{2}^{2}+O\left( \mu _{2}^{3}\right) \right\} \end{equation} $ | (4.6) |
for $ \left\vert \mu \right\vert $ sufficiently small.
As a consequence we obtain the following result concerning the topological type of the nontrivial equilibrium $ E_{3}. $
Lemma 4.4. Assume $ N > 0. $ For sufficiently small $ \left\vert \mu\right\vert, $ the following statements hold:
(1) If $ \delta > 0, $ then $ E_{3} $ is a saddle.
(2) If $ \delta < 0, $ $ \theta _{2}\delta -2N\geq 0, $ then $ E_{3} $ is ahyperbolic attractor.
(3) If $ \delta < 0, $ $ \theta _{2}\delta -2N < 0, $ then the equilibrium $ E_{3} $is a hyperbolic repeller as $ \delta ^{2}\mu _{1} < [\gamma (2N-\theta_{2}\delta)+(\theta _{2}\delta -N)]\mu _{2}^{2}, $ and a hyperbolicattractor for the other parameters in $ R_{5}\backslash H, $
A similar result can be obtained if $ N < 0. $ We explore next the local bifurcations at the equilibrium $ E_{3}. $
Proposition 4.5. The following statements hold:
(i) For $ \mu _{0}\in T_{1}, $ equilibria $ E_{2} $ and $ E_{3} $ coincide. Whenparameter $ \mu $ crosses $ T_{1} $ a transcritical bifurcation takes place at $ E_{3}.$
(ii) For $ \mu _{0}\in T_{3}, $ $ E_{3} $ coincides either with $ E_{11} $ if $ \frac{2N-\theta _{2}\delta }{2N\delta }\mu _{2} < 0, $ or with $ E_{12} $ if $ \frac{2N-\theta _{2}\delta }{2N\delta }\mu _{2} > 0. $
(iii) Assume $ 2N-\delta \theta _{2}\neq 0, $ and $ \frac{\partial \delta }{\partial \mu _{1}}\neq 0. $ Then, when parameter $ \mu $ crosses $ T_{3}, $ atranscritical bifurcation takes place at $ E_{3}. $
Proof. (ⅰ) Consider $ \mu _{0}\in T_{1}, $ $ \mu _{0} = (\gamma \mu _{2}+O(\mu _{2}^{2}), \mu _{2}), $ with $ \mu _{2} > 0. $ Applying Sotomayor theorem, we obtain the right eigenvector $ v = \left(1, -\delta \right) ^{T} $ and the left eigenvector $ w = \left(1, 0\right) ^{T}, \ $and
$ \begin{align*} &w^{T}f_{\mu _{1}}\left( E_{3},\mu _{0}\right) = 0,\quad w^{T}Df_{\mu _{1}}(E_{3},\mu _{0}) = 2\gamma \delta +O(\mu _{2})\neq 0,\\ & w^{T}[D^{2}f(E_{0},\mu _{0})(v,v)] = 1\neq 0, \end{align*} $ |
for $ \left\vert \mu _{0}\right\vert $ sufficiently small. Thus the transcritical bifurcation conditions are satisfied.
(ⅱ) Consider $ \mu _{0}\in T_{3}, $ sufficiently small. Then $ \mu _{0} = \left(\frac{\theta _{2}\delta -N}{\delta ^{2}}\mu _{2}^{2}+O(\mu _{2}^{3}), \mu _{2}\right), $ $ \mu _{2}\neq 0. $ We obtain $ \xi _{1}^{\ast } = \frac{1}{\delta }\mu _{2}+O(\mu _{2}^{2})\neq 0, $ $ \xi _{2}^{\ast } = 0, $ and
$ \begin{equation*} \xi _{1}^{\ast }-\frac{\theta _{1}\mu _{1}+\theta _{2}\mu _{2}}{2N} = \frac{ 2N-\theta _{2}\delta }{2N\delta }\mu _{2}+O(\mu _{2}^{2}), \end{equation*} $ |
consequently, $ E_{3} = E_{12} $ if $ \frac{2N-\theta _{2}\delta }{2N\delta }\mu _{2} > 0, $ and $ E_{3} = E_{11} $ if $ \frac{2N-\theta _{2}\delta }{2N\delta }\mu _{2} < 0. $
(ⅲ) Consider $ \mu _{0}\in T_{3}, $ sufficiently small. In order to prove the existence of a transcritical bifurcation, we choose $ \mu _{1} $ as the bifurcation parameter. Write $ \delta $ as
$ \begin{equation*} \delta (\mu ) = \delta (0)+\delta _{1}\mu _{1}+\delta _{2}\mu _{2}+O(\left\vert \mu \right\vert ^{2}). \end{equation*} $ |
The Jacobian matrix $ Df(E_{3}, \mu _{0}) $ has a zero eigenvalue with the right eigenvector
$ \begin{equation*} v = \left( \gamma \delta -M\mu _{2}+O(\mu _{2}^{2}),(2N-\theta _{2}\delta )\mu _{2}+O(\mu _{2}^{2})\right) ^{T} \end{equation*} $ |
and the left eigenvector $ w = \left(0, 1\right) ^{T}. $ It follows
$ \begin{equation*} w^{T}f_{\mu _{1}}\left( E_{3},\mu _{0}\right) = 0,\quad w^{T}Df_{\mu _{1}}(E_{3},\mu _{0}) = \frac{\delta _{1}}{\delta }(2N-\delta \theta _{2})\mu _{2}^{2}\left( 1+O\left( \mu _{2}\right) \right) \neq 0, \end{equation*} $ |
$ \begin{equation*} w^{T}[D^{2}f(E_{3},\mu _{0})(v,v)] = 2\gamma \delta ^{2}(2N-\delta \theta _{2})\mu _{2}\left( 1+O\left( \mu _{2}\right) \right) \neq 0, \end{equation*} $ |
for sufficiently small $ \left\vert \mu \right\vert, $ ensuring the existence of a transcritical bifurcation.
From Lemma 4.4 it follows that system (2.16) may exhibit a Hopf bifurcation at $ E_{3} $.
Remark 5. The above analysis shows that the term $ \theta _{1} $ does not influence the topological type of the equilibria, and only the coefficients $ \gamma, \delta, \theta _{2} $ and $ N $ are significant, for sufficiently small $ \left\vert \mu \right\vert. $
For a fixed $ \gamma > 0, $ and $ N > 0, $ the curves $ \delta = 0, $ $ \theta _{2} = 0, \theta _{2}\delta -N = 0, $ $ \theta _{2}\delta -2N = 0\ $determine eight regions in the $ \left(\theta _{2}, \delta \right) - $ plane (see Figure 4), corresponding to the following cases:
Ⅰ$ _{\theta } $: $ \theta _{2} > 0, \delta > 0, $ $ \theta _{2}\delta -2N > 0; $
Ⅱ$ _{\theta } $: $ \theta _{2} > 0, \delta > 0, \ \theta _{2}\delta -N > 0, $ $ \theta _{2}\delta -2N < 0; $
Ⅲ$ _{\theta } $: $ \theta _{2} > 0, \delta > 0, $ $ \theta _{2}\delta -N < 0; $
Ⅳ$ _{\theta } $: $ \theta _{2} < 0, \delta > 0, $ $ \theta _{2}\delta -N < 0; $
Ⅴ$ _{\theta } $: $ \theta _{2} < 0, \delta < 0, $ $ \theta _{2}\delta -2N > 0; $
Ⅵ$ _{\theta } $: $ \theta _{2} < 0, \delta < 0, $ $ \theta _{2}\delta -N > 0, \theta _{2}\delta -2N < 0; $
Ⅶ$ _{\theta } $: $ \theta _{2} < 0, \delta < 0, $ $ \theta _{2}\delta -N < 0; $
Ⅷ$ _{\theta } $: $ \theta _{2} > 0, \delta < 0, $ $ \theta _{2}\delta -N < 0. $
Theorem 4.6. For all $ \gamma > 0, N > 0, $ respectively, $ (\theta _{2}, \delta) $in regions I$ _{\theta } $, II$ _{\theta } $, III$ _{\theta } $, IV$ _{\theta } $, V$ _{\theta } $ in the $ \left(\theta _{2}, \delta \right) - $ plane, thebifurcation curves consist of
$ \begin{equation*} O\cup T_{1}\cup T_{3}\cup \Delta _{\pm }\cup X_{-}\cup X_{+}\cup Y_{-}^{\prime }\cup Y_{+}^{\prime }. \end{equation*} $ |
The generic parameter portraits are shown in Figures 5 and 7, and the corresponding generic phase portraits in Figures 6 and 8.
A Hopf bifurcation may occur when $ \left(\mu _{1}, \mu _{2}\right) $ crosses the curve $ H $ and $ \left(\theta _{2}, \delta \right) $ is situated in regions VI$ _{\theta } $, VII$ _{\theta } $, VIII$ _{\theta }. $ In the case when the first Lyapunov is non-zero, a limit cycle surrounding the equilibrium $ E_{3} $ appear. This cycle is stable if the Hopf bifurcation is supercritical (the first Lyapunov coefficient is negative) or is unstable if the Hopf bifurcation is subcritical (i.e., the first Lyapunov coefficient is positive). As the first Lyapunov coefficient is zero, the equilibrium $ E_{3} $ may be a nonlinear centre.
Remark that, as the parameters move away from $ H, $ towards the region containing the limit cycle generated by the Hopf bifurcation, the cycle may disappear, either by transforming into a homoclinic loop or by becoming too large, and no longer inside the visible neighborhood of the origin. In such cases there should exist a bifurcation curve $ L $ originating at $ \mu = 0, $ along which those situations may occur. The position of the curve $ L $ depends on the type of the Hopf bifurcation. These situations also appear in the "difficult case" in the nondegenerate double-Hopf bifurcation. The existence and location of the curve $ L $ can be proved following the lines in [1,2].
Theorem 4.7. For all $ \gamma > 0, N > 0, $ and $ (\theta _{2}, \delta) $ in regionsVI$ _{\theta } $, VII$ _{\theta } $, VIII$ _{\theta } $ in the $ \left(\theta_{2}, \delta \right) - $ plane, the bifurcation curves consist of
$ \begin{equation*} O\cup T_{1}\cup T_{3}\cup \Delta _{\pm }\cup X_{-}\cup X_{+}\cup Y_{-}^{\prime }\cup Y_{+}^{\prime }\cup H\cup L. \end{equation*} $ |
The generic parameter portraits are shown in Figure 7, in the hypothesis that the Lyapunov coefficient is negative. The corresponding generic phase portraits are given in Figure 8. Many of the phase portraits in Figures 6 and 8 cannot be found in the nondegenerate double-Hopf bifurcation.
The effect of adding higher-order terms to the truncated normal form system (2.16) and the correspondence between the properties of the 2D amplitude system (2.16) and the 4D system (2.1), have been described, for example, in [1,2,15,16,17,18]. However, the study of nonsymmetric general perturbations of the truncated normal forms is far from complete, as pointed out in [1].
Thus, we remark that the study of adding higher order terms to the truncated normal form is a complex open problem which is outside the aim of this article.
The classical normal form of the Hopf-Hopf bifurcation, in differential systems of dimension four and having minimum two independent parameters, is based on six generic conditions (2.8).
In this work we have studied two degenerate Hopf-Hopf bifurcations, namely:
1) the case when the generic condition (HH.3) in system (2.8) is not fulfilled, treated in Section 3;
2) the case when the generic condition (HH.1) in system (2.8) is not fulfilled, treated in Section 4.
In our study we have obtained new bifurcation diagrams and new phase portraits which were not previously reported in generic studies on double-Hopf bifurcation. Such an example is a saddle-node bifurcation in the amplitude system which corresponds to a fold bifurcation of cycles in the four dimensional system and which is present only in the degenerate case $ \theta = 0 $.
The results describing the dynamics, contribute to a better understanding of the behavior of a system presenting a Hopf-Hopf singularity.
Finally, we summarize in the Table 1 the correspondence of equilibria, cycles and bifurcations between the 2D amplitude system (2.16) and the 4D normal form system (2.14):
2D | 4D |
$ E_{0} $ | origin |
$ E_{3} $ | 2D torus |
cycle | 3D torus |
$ X_{+}, X_{-}, Y_{+}, Y_{-}, Y_{+}^{\prime }, Y_{-}^{\prime } $ | Hopf bifurcation |
$ T_{1}, T_{2}, T_{3} $ | Neimark-Sacker bifurcation of cycles |
$ \Delta _{+}, \Delta _{-} $ | fold bifurcation of cycles |
Hopf bifurcation $ H $ | branching of 3D torus from a 2D torus |
cycle blow up $ L $ | blow-up of a 3D torus |
This research was supported by Horizon2020-2017-RISE-777911 project.
The authors declare there is no conflicts of interest.
[1] |
Kartikasari R, Subardi A, Wijaya AE (2021) Development of Fe-5Al-1C alloys for grinding ball. Eastern-European J Enterp Technol 1: 29–35. https://doi.org/10.15587/1729-4061.2021.225421 doi: 10.15587/1729-4061.2021.225421
![]() |
[2] |
Foszcz D, Krawczykowski D, Gawenda T, et al. (2018) Analysis of process of grinding efficiency in ball and rod mills with various feed parameters. IOP Conf Ser-Mater Sci Eng 427: 012031. https://doi.org/10.1088/1757-899X/427/1/012031 doi: 10.1088/1757-899X/427/1/012031
![]() |
[3] |
Jankovic A, Wills T, Dikmen S (2016) A comparison of wear rates of ball mill grinding media. J Min Metall A Min 52: 1–10. https://doi.org/10.5937/JMMA1601001J doi: 10.5937/JMMA1601001J
![]() |
[4] |
Zurnadzhy VI, Efremenko VG, Wu KM, et al. (2020) Quenching and partitioning-based heat treatment for rolled grinding steel balls. Metall Mater Trans A 51: 3042–3053. https://doi.org/10.1007/s11661-020-05737-w doi: 10.1007/s11661-020-05737-w
![]() |
[5] |
Massola CP, Chaves AP, Albertin E (2016) A discussion on the measurement of grinding media wear. J Mater Res Technol 5: 282–288. https://doi.org/10.1016/j.jmrt.2015.12.003 doi: 10.1016/j.jmrt.2015.12.003
![]() |
[6] |
Stalinskii DV, Rudyuk AS, Solenyi VK, et al. (2017) Improving the quality of steel grinding balls. Steel Transl 47: 130–136. https://doi.org/10.3103/S0967091217020115 doi: 10.3103/S0967091217020115
![]() |
[7] |
Aissat S, Sadeddine A, Bradai MA, et al. (2017) Effect of heat treatment on the hardness and wear of grinding balls. Met Sci Heat Treat 59: 297–301. https://doi.org/10.1007/s11041-017-0146-5 doi: 10.1007/s11041-017-0146-5
![]() |
[8] |
Chyła P, Pater Z, Tomczak J, et al. (2016) Numerical analysis of a rolling process for producing steel balls using helical rolls. Arch Metall Mater 61: 485–492. https://doi.org/10.1515/amm-2016-0085 doi: 10.1515/amm-2016-0085
![]() |
[9] |
Hao Y, Li J, Li X, et al. (2020) Influences of cooling rates on solidification and segregation characteristics of Fe-Cr-Ni-Mo-N super austenitic stainless steel. J Mater Process Technol 275: 116236. https://doi.org/10.1016/j.jmatprotec.2019.116326 doi: 10.1016/j.jmatprotec.2019.116326
![]() |
[10] |
Zai L, You G, Tong X, et al. (2020) Microstructure and mechanical properties of inertia-friction-welded Fe-Cr-Ni-Mo high-strength steel. Steel Res Int 91: 1–12. https://doi.org/10.1002/srin.202000145 doi: 10.1002/srin.202000145
![]() |
[11] |
Sabih A, Radziszewski P, Mullany I (2017) Investigating grinding media differences in microstructure, hardness, abrasion and fracture toughness. Miner Eng 103: 43–53. https://doi.org/10.1016/j.mineng.2016.08.014 doi: 10.1016/j.mineng.2016.08.014
![]() |
[12] |
Efremenko VG, Popov ES, Kuz'Min SO, et al. (2014) Introduction of three-stage thermal hardening technology for large diameter grinding balls. Metallurgist 57: 849–854. https://doi.org/10.1007/s11015-014-9812-7 doi: 10.1007/s11015-014-9812-7
![]() |
[13] |
Çolak SS, Altun O, Benzer H, et al. (2018) Development of a preliminary media wear measurement test procedure for cement ball milling applications. Powder Technol 325: 678–686. https://doi.org/10.1016/j.powtec.2017.11.033 doi: 10.1016/j.powtec.2017.11.033
![]() |
[14] |
Daraio D, Villoria J, Ingram A, et al. (2020) Investigating grinding media dynamics inside a vertical stirred mill using the discrete element method: Effect of impeller arm length. Powder Technol 364: 1049–1061. https://doi.org/10.1016/j.powtec.2019.09.038 doi: 10.1016/j.powtec.2019.09.038
![]() |
[15] |
Jang JW, Iwasaki I, Moore JJ (1989) Effect of galvanic interaction between martensite and ferrite grinding media wear. Corrosion 45: 402–407. https://doi.org/10.5006/1.3582036 doi: 10.5006/1.3582036
![]() |
[16] |
Jurči P, Dománková M, Čaplovič Ľ, et al. (2015) Microstructure and hardness of sub-zero treated and no tempered P/M Vanadis 6 ledeburitic tool steel. Vacuum 111: 92–101. https://doi.org/10.1016/j.vacuum.2014.10.004 doi: 10.1016/j.vacuum.2014.10.004
![]() |
[17] |
Murthy BRN, Rangappa R (2021) Morphology and wear of high chromium and austempered ductile iron balls as grinding media in ball mills. J Phys-Conf Ser 2070: 012201. https://doi.org/10.1088/1742-6596/2070/1/012201 doi: 10.1088/1742-6596/2070/1/012201
![]() |
[18] |
Das D, Ray KK (2012) Structure-property correlation of sub-zero treated AISI D2 steel. Mater Sci Eng A-Struct 541: 45-60. https://doi.org/10.1016/j.msea.2012.01.130 doi: 10.1016/j.msea.2012.01.130
![]() |
[19] | Sobotova J, Ku-Gik M, Krum S, et al. (2016) Effect of sub-zero treatment on the wear resistance of P/M tool steels. J Appl Mech Eng 5: 1000243. |
[20] |
Jurči P, Bartkowska A, Hudáková M, et al. (2021) Effect of sub-zero treatments and tempering on corrosion behaviour of vanadis 6 tool steel. Materials 14: 3759. https://doi.org/10.3390/ma14133759 doi: 10.3390/ma14133759
![]() |
[21] |
Kosaraju S, Singh SK, Buddi T, et al. (2020) Evaluation and characterisation of ASS316L at sub-zero temperature. Adv Mater Process Technol 6: 445–455. https://doi.org/10.1080/2374068X.2020.1728650 doi: 10.1080/2374068X.2020.1728650
![]() |
[22] |
Shah N, Arora K, Dhokey NB, et al. (2019) Studies on wear behaviour and DBTT in sub-zero regimes of cryo-treated high nitrogen martensitic stainless steel (HNMS). Trans Indian Inst Met 72: 2121-2126. https://doi.org/10.1007/s12666-018-01555-2 doi: 10.1007/s12666-018-01555-2
![]() |
[23] |
Zhou Q, Luo D, Hua D, et al. (2022) Design and characterization of metallic glass/graphene multilayer with excellent nanowear properties. Friction 10: 1913–1926. https://doi.org/10.1007/s40544-021-0581-6 doi: 10.1007/s40544-021-0581-6
![]() |
[24] |
Yan XG, Li DY (2013) Effects of the sub-zero treatment condition on microstructure, mechanical behavior and wear resistance of W9Mo3Cr4V high speed steel. Wear 302: 854–862. https://doi.org/10.1016/j.wear.2012.12.037 doi: 10.1016/j.wear.2012.12.037
![]() |
[25] |
Li DH, He WC, Zhang X, et al. (2021) Effects of traditional heat treatment and a novel deep cryogenic treatment on microstructure and mechanical properties of low-carbon high-alloy martensitic bearing steel. J Iron Steel Res Int 28: 370–382. https://doi.org/10.1007/s42243-020-00527-5 doi: 10.1007/s42243-020-00527-5
![]() |
[26] |
Szala M, Winiarski G, Wójcik Ł, et al. (2020) Effect of annealing time and temperature parameters on the microstructure, hardness, and strain-hardening coefficients of 42CrMo4 Steel. Materials 13: 1–16. https://doi.org/10.3390/ma13092022 doi: 10.3390/ma13092022
![]() |
[27] |
Zhirafar S, Rezaeian A, Pugh M (2007) Effect of cryogenic treatment on the mechanical properties of 4340 steel. J Mater Process Technol 186: 298–303. https://doi.org/10.1016/j.jmatprotec.2006.12.046 doi: 10.1016/j.jmatprotec.2006.12.046
![]() |
[28] |
Shamsolhodaei A, Oliveira JP, Schell N, et al. (2020) Controlling intermetallic compounds formation during laser welding of NiTi to 316L stainless steel. Intermetallics 116: 106656. https://doi.org/10.1016/j.intermet.2019.106656 doi: 10.1016/j.intermet.2019.106656
![]() |
[29] |
Wang K, Gu K, Miao J, et al. (2019) Toughening optimization on a low carbon steel by a novel Quenching-Partitioning-Cryogenic-Tempering treatment. Mater Sci Eng A-Struct 743: 259–264. https://doi.org/10.1016/j.msea.2018.04.104 doi: 10.1016/j.msea.2018.04.104
![]() |
[30] |
Akincioğlu S, Gökkaya H, Uygur I (2015) A review of cryogenic treatment on cutting tools. Int J Adv Manuf Technol 78: 1609–1627. https://doi.org/10.1007/s00170-014-6755-x doi: 10.1007/s00170-014-6755-x
![]() |
[31] |
Gill SS, Singh J, Singh R, et al. (2012) Effect of cryogenic treatment on AISI M2 high speed steel: Metallurgical and mechanical characterization. J Mater Eng Perform 21: 1320–1326. https://doi.org/10.1007/s11665-011-0032-z doi: 10.1007/s11665-011-0032-z
![]() |
[32] |
Wang LY, Wu YX, Sun WW, et al. (2020) Strain hardening behaviour of as-quenched and tempered martensite. Acta Mater 199: 613–632. https://doi.org/10.1016/j.actamat.2020.08.067 doi: 10.1016/j.actamat.2020.08.067
![]() |
[33] | Patil PI, Tated RG (2012) Comparison of effects of cryogenic Treatment on different types of steels: A review. International Conference in Computional Intelligence (ICCIA) 9: 10–29. |
[34] |
Jovičević-Klug P, Jovičević-Klug M, Sever T, et al. (2021) Impact of steel type, composition and heat treatment parameters on effectiveness of deep cryogenic treatment. J Mater Res Technol 14: 1007-1020. https://doi.org/10.1016/j.jmrt.2021.07.022 doi: 10.1016/j.jmrt.2021.07.022
![]() |
[35] |
Alqarni ND, Wysocka J, El-Bagoury N, et al. (2018) Effect of cobalt addition on the corrosion behavior of near equiatomic NiTi shape memory alloy in normal saline solution: Electrochemical and XPS studies. RSC Adv 8: 19289–19300. https://doi.org/10.1039/C8RA02031K doi: 10.1039/C8RA02031K
![]() |
[36] |
Wang XH, Zhong SY, Song YH, et al. (2020) Effect of tantalum film on corrosion behaviour of AA6061 aluminium alloy in hydrochloric acid- and chloride-containing solutions. Trans Inst Met Finish 98: 243–249. https://doi.org/10.1080/00202967.2020.1802930 doi: 10.1080/00202967.2020.1802930
![]() |
[37] |
Zhou X, Liao C, Wang Y, et al. (2021) Constructing the Pourbaix diagram of Fe-Cl–-H2O ternary system under supercritical water conditions. Electrochim Acta 377: 138075. https://doi.org/10.1016/j.electacta.2021.138075 doi: 10.1016/j.electacta.2021.138075
![]() |
[38] |
Utomo EP, Herbirowo S, Puspasari V, et al. (2021) Characteristics and corrosion behavior of Ti-30Nb-5Sn alloys in histidine solution with various NaCl concentrations. Int J Corros Scale Inhib 10: 592–601. https://doi.org/10.17675/2305-6894-2021-10-2-7 doi: 10.17675/2305-6894-2021-10-2-7
![]() |
[39] |
Hu J, Zhu Y, Hang J, et al. (2021) The effect of organic core-shell corrosion inhibitors on corrosion performance of the reinforcement in simulated concrete pore solution. Constr Build Mater 267: 121011. https://doi.org/10.1016/j.conbuildmat.2020.121011 doi: 10.1016/j.conbuildmat.2020.121011
![]() |
[40] |
Li S, Xiao M, Ye G, et al. (2018) Effects of deep cryogenic treatment on microstructural evolution and alloy phases precipitation of a new low carbon martensitic stainless bearing steel during aging. Mater Sci Eng A-Struct 732: 167–177. https://doi.org/10.1016/j.msea.2018.07.012 doi: 10.1016/j.msea.2018.07.012
![]() |
[41] |
Samuel AP, Arul S (2018) Effect of cryogenic treatment on the mechanical properties of low carbon steel IS 2062. Mater Today Proc 5: 25065–25074. https://doi.org/10.1016/j.matpr.2018.10.307 doi: 10.1016/j.matpr.2018.10.307
![]() |
[42] |
Liao J, Li L, Peng J, et al. (2020) Effects of deep cryogenic treatment on the microstructure and friction performance of M35 high-speed steel. J Phys-Conf Ser 1676: 012098. https://doi.org/10.1088/1742-6596/1676/1/012098 doi: 10.1088/1742-6596/1676/1/012098
![]() |
[43] |
Sendya A, Marzuki H, Herbirowo S, et al. (2020) Study of Cr/Mo alloys lateritic steel with the soaking time cryogenic treatment on hardness, toughness, abrasive resistant, and microstructure. Met Indones 42: 21–27. https://doi.org/10.32423/jmi.2020.v42.20-27 doi: 10.32423/jmi.2020.v42.20-27
![]() |
[44] |
Jia Q, He W, Hua D, et al. (2022) Effects of structure relaxation and surface oxidation on nanoscopic wear behaviors of metallic glass. Acta Mater 232: 117934. https://doi.org/10.1016/j.actamat.2022.117934 doi: 10.1016/j.actamat.2022.117934
![]() |
1. | Juanjuan Huang, Qinsheng Bi, Mixed-mode bursting oscillations in the neighborhood of a triple Hopf bifurcation point induced by parametric low-frequency excitation, 2023, 166, 09600779, 113016, 10.1016/j.chaos.2022.113016 | |
2. | Raluca Efrem, Mihaela Sterpu, Local dynamics and bifurcation for a two-dimensional cubic Lotka-Volterra system (I), 2023, 50, 12236934, 247, 10.52846/ami.v50i1.1779 | |
3. | Sterpu Mihaela, Efrem Raluca , Local dynamics and bifurcation for a two-dimensional cubic Lotka-Volterra system (Part II), 2024, 51, 12236934, 561, 10.52846/ami.v51i2.2070 |
2D | 4D |
$ E_{0} $ | origin |
$ E_{3} $ | 2D torus |
cycle | 3D torus |
$ X_{+}, X_{-}, Y_{+}, Y_{-}, Y_{+}^{\prime }, Y_{-}^{\prime } $ | Hopf bifurcation |
$ T_{1}, T_{2}, T_{3} $ | Neimark-Sacker bifurcation of cycles |
$ \Delta _{+}, \Delta _{-} $ | fold bifurcation of cycles |
Hopf bifurcation $ H $ | branching of 3D torus from a 2D torus |
cycle blow up $ L $ | blow-up of a 3D torus |
2D | 4D |
$ E_{0} $ | origin |
$ E_{3} $ | 2D torus |
cycle | 3D torus |
$ X_{+}, X_{-}, Y_{+}, Y_{-}, Y_{+}^{\prime }, Y_{-}^{\prime } $ | Hopf bifurcation |
$ T_{1}, T_{2}, T_{3} $ | Neimark-Sacker bifurcation of cycles |
$ \Delta _{+}, \Delta _{-} $ | fold bifurcation of cycles |
Hopf bifurcation $ H $ | branching of 3D torus from a 2D torus |
cycle blow up $ L $ | blow-up of a 3D torus |