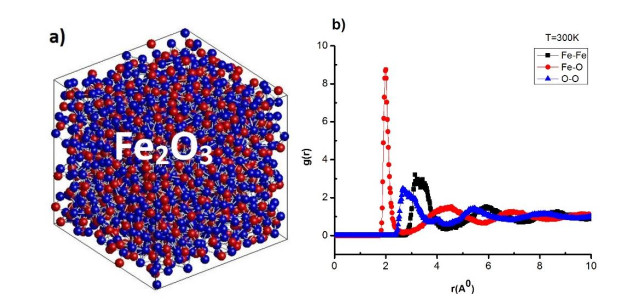
This paper uses Molecular Dynamics (MD) method to study the influence of high temperature (T) and high pressure (P) on the structure and phase transition of Fe2O3 materials. The results show that, when increasing the temperature from T = 300 K to T = 7000 K, P = 0.0 GPa, the size (1) of the Fe2O3 materials increases, the energy (E) increases, the length link (r) decreased, the number of structural units FeO4, FeO5 increased, and FeO6 decreased. Similarly, as the pressure (P) is increased, from P = 0 GPa to P = 360 GPa at temperatures T, l decreases, E increases, r decreases, FeO4 decreases and disappears, FeO5 decreases, and FeO6 increases at high P with P ≥ 150 GPa, FeO5 disappeared at P ≥ 250 GPa and only FeO6 appeared at T = 2300, 7000 K. In addition, when increasing T, P, the bond angle of Fe–O–Fe, O–Fe–O decreases, E increases, r decreases, l increases when T increases and l decreases when P increases, leading to the number of structural units FeO4, FeO5 increasing and FeO6 decreasing when T increases and vice versa when P increases. In addition, the phase transition temperature (Tm), Tm = 2300 K was determined. All the obtained results will be the basis for future experimental studies of amorphous Fe2O3 materials.
Citation: Dung Nguyen Trong, Van Cao Long, Phu Nguyen Dang, Ştefan Ţălu. A molecular dynamics study concerning the effect of high-temperature and high-pressure on the structure and phase transition of Fe2O3 material[J]. AIMS Materials Science, 2022, 9(3): 406-429. doi: 10.3934/matersci.2022024
[1] | Rahmad Doni Widodo, Rusiyanto, Wahyudi, Melisa Kartika Sari, Deni Fajar Fitriyana, Januar Parlaungan Siregar, Tezara Cionita, Natalino Fonseca Da Silva Guterres, Mateus De Sousa Da Silva, Jamiluddin Jaafar . Effect of compression molding temperature on the characterization of asbestos-free composite friction materials for railway applications. AIMS Materials Science, 2023, 10(6): 1105-1120. doi: 10.3934/matersci.2023059 |
[2] | Bauyrzhan Rakhadilov, Lyaila Bayatanova, Sherzod Kurbanbekov, Ravil Sulyubayev, Nurdaulet Shektibayev, Nurbol Berdimuratov . Investigation on the effect of technological parameters of electrolyte-plasma cementation method on phase structure and mechanical properties of structural steel 20X. AIMS Materials Science, 2023, 10(5): 934-947. doi: 10.3934/matersci.2023050 |
[3] | Ayu Azera Izad, Rosimah Nulit, Che Azurahanim Che Abdullah, A'fifah Abdul Razak, Teh Huey Fang, Mohd Hafiz Ibrahim . Growth, leaf gas exchange and biochemical changes of oil palm (Elaeis guineensis Jacq.) seedlings as affected by iron oxide nanoparticles. AIMS Materials Science, 2019, 6(6): 960-984. doi: 10.3934/matersci.2019.6.960 |
[4] | Leydi J. Cardenas F., Josep Ma. Chimenos, Luis C. Moreno A., Elaine C. Paris, Miryam R. Joya . Enhancing Co3O4 nanoparticles: Investigating the impact of nickel doping and high-temperature annealing on NiCo2O4/CoO heterostructures. AIMS Materials Science, 2023, 10(6): 1090-1104. doi: 10.3934/matersci.2023058 |
[5] | Larysa Khomenkova, Mykola Baran, Jedrzej Jedrzejewski, Caroline Bonafos, Vincent Paillard, Yevgen Venger, Isaac Balberg, Nadiia Korsunska . Silicon nanocrystals embedded in oxide films grown by magnetron sputtering. AIMS Materials Science, 2016, 3(2): 538-561. doi: 10.3934/matersci.2016.2.538 |
[6] | Khang Duy Vu Nguyen, Khoa Dang Nguyen Vo . Magnetite nanoparticles-TiO2 nanoparticles-graphene oxide nanocomposite: Synthesis, characterization and photocatalytic degradation for Rhodamine-B dye. AIMS Materials Science, 2020, 7(3): 288-301. doi: 10.3934/matersci.2020.3.288 |
[7] | Laís Weber Aguiar, Cleiser Thiago Pereira da Silva, Hugo Henrique Carline de Lima, Murilo Pereira Moises, Andrelson Wellington Rinaldi . Evaluation of the synthetic methods for preparing metal organic frameworks with transition metals. AIMS Materials Science, 2018, 5(3): 467-478. doi: 10.3934/matersci.2018.3.467 |
[8] | Endi Suhendi, Andini Eka Putri, Muhamad Taufik Ulhakim, Andhy Setiawan, Syarif Dani Gustaman . Investigation of ZnO doping on LaFeO3/Fe2O3 prepared from yarosite mineral extraction for ethanol gas sensor applications. AIMS Materials Science, 2022, 9(1): 105-118. doi: 10.3934/matersci.2022007 |
[9] | Yana Fajar Prakasa, Sumari Sumari, Aman Santoso, Muhammad Roy Asrori, Ririn Cahyanti . The performance of radar absorption of MnxFe3–xO4/rGO nanocomposites prepared from iron sand beach and coconut shell waste. AIMS Materials Science, 2023, 10(2): 227-248. doi: 10.3934/matersci.2023013 |
[10] | Tetsuji Saito, Daisuke Nishio-Hamane . Magnetic properties of Sm5Fe17 melt-spun ribbons and their borides. AIMS Materials Science, 2015, 2(4): 392-400. doi: 10.3934/matersci.2015.4.392 |
This paper uses Molecular Dynamics (MD) method to study the influence of high temperature (T) and high pressure (P) on the structure and phase transition of Fe2O3 materials. The results show that, when increasing the temperature from T = 300 K to T = 7000 K, P = 0.0 GPa, the size (1) of the Fe2O3 materials increases, the energy (E) increases, the length link (r) decreased, the number of structural units FeO4, FeO5 increased, and FeO6 decreased. Similarly, as the pressure (P) is increased, from P = 0 GPa to P = 360 GPa at temperatures T, l decreases, E increases, r decreases, FeO4 decreases and disappears, FeO5 decreases, and FeO6 increases at high P with P ≥ 150 GPa, FeO5 disappeared at P ≥ 250 GPa and only FeO6 appeared at T = 2300, 7000 K. In addition, when increasing T, P, the bond angle of Fe–O–Fe, O–Fe–O decreases, E increases, r decreases, l increases when T increases and l decreases when P increases, leading to the number of structural units FeO4, FeO5 increasing and FeO6 decreasing when T increases and vice versa when P increases. In addition, the phase transition temperature (Tm), Tm = 2300 K was determined. All the obtained results will be the basis for future experimental studies of amorphous Fe2O3 materials.
Fe2O3 material is the most common oxide material, very environmentally friendly and used in many fields of science and technology: Welding [1], magnetism [2], supercapacitor electrode [3], biomedicine [4], environment [5], ceramic materials [6,7,8,9,10], environmental contaminant removal [11], photocatalysis [12], chemical sensors [13], electrochemistry [14], magnetic resonance imaging, data storage [15,16,17,18,19], energy [20]. Energy with bandgap (Eg) of Fe2O3 materials with absorption range of 1.9-2.2 eV [21] that corresponds to half of the visible light region of wavelength (λ), λ > 600 µm, absorbing 40% of the sun's spectrum and this is a stable material in solutions with concentrations (pH), pH > 3.0 [22]. Fe2O3 exists in 5 allotropic states: α-Fe2O3 (hematite), β-Fe2O3 [23,24], γ-Fe2O3 (maghemite), ε-Fe2O3, [9,10,25] and ζ-Fe2O3 [25]. In literature, the polymorphic existence of amorphous Fe2O3 was investigated at temperature (T), T = 923 K [26,27,28]. Among them, ε-Fe2O3 was first identified in 1998 [29] and is considered a remarkable phase, with room temperature magnetic resonance T = 300 K [7,10,30] and is applied in the technology of making Jian ceramics of ancient China by heating clay containing Fe, T = ∼1573 K [31]. While, at T = 923 K, Fe2O3 can be converted to Fe3O4 with the energy (E) that decreases very quickly [32,33,34]. On the other hand, the polymorphic phase transition from γ-Fe2O3 → ε-Fe2O3 → α-Fe2O3 has been studied in many previous works. The obtained results show that the material has a thermodynamically unstable structure [10,35]. Wheeler et al. [36] have successfully fabricated single-crystal Fe2O3 nanowires with high density, which have reduced the charge loss by electron-hole recombination. Also, it is known that the magnetic Curie temperature (Tc) of the ferrimagnet material is respectively Tc = 500/585 K [37,38,39]. To study and fabricate Fe2O3 materials based on the experimental methods [40,41], there are the following methods: X-ray diffraction (XRD), Extended X-ray Absorption Fine Structure (EXAFS) method [42], transmission electron microscopy, and High-Resolution Transmission Electron Microscopy (HRTEM) [43]. Schaetz et al. [44] have successfully determined the influence of nano-size, shape and surface elevation effect of nanomaterials on the structure of hematite (α-Fe2O3), and maghemite (γ-Fe2O3). In practical applications, Fe2O3 is also used in the separation of water by electrolysis of α-Fe2O3. Hematite electrodes can generate photons by illumination with a wavelength (λ), λ = 350 μm, without the need for a power source [45,46]. Fe2O3 thin films have been used in photovoltaic cells [47] with hematite nanorods (α-Fe2O3) with thicknesses from 5 nm to 7 nm with lengths from 3 nm to 4 nm [48]. In practical applications [49,50], when it is welded Fe2O3-doped Austenitic steel, better results are obtained than previous conventional methods, due to the self-reversing energy of Marangoni flow at the lower melting temperature of nanowire flux. Similarly, the practical applications of supercapacitor electrodes have also been solved by optimizing the structure of Fe2O3 nanotubes based on polyaniline (PANI) combination [3]. Besides, under the influence of Fe2O3, the positions of defects and oxygen-containing functional groups are improved significantly with band gap (Eg), Eg < 2.8 eV. Because of that, composites Fe2O3 are considered as materials that have visible light with photocatalysts and exhibit photocatalytic activity towards the degradation of cationic dye Rhodamine B (RhB) [12]. O. Iglesias and A. Labarta [51] applied the theoretical method (the Monte Carlo (MC) simulation method combined with periodic boundary conditions) to study the influence of the surface layer on the magnetic properties of nanomaterials at the temperature T = 350 K. VV Hoang and Khanh BTHL used the Molecular Dynamics (MD) method for the determination of the static and thermodynamic properties of liquid and amorphous Fe2O3 nanoparticles and concluded that with amorphous Fe2O3 nano, at T = 3500 K, the Fe-Fe, Fe-O, and O-O corresponding to links lengths are rFe-Fe = 3.1 Å, rFe-O = 1.9 Å, rO-O = 2.7 Å [52]. In other studies, researchers found with the experimental method that Fe2O3 has rFe-Fe = 3.35 Å, rFe-O = 1.91/1.95 Å, rO-O = 2.91 Å [33,53] and rFe-O = 2.08 Å [54]. Among these research methods, the MD simulation method is considered to have many advantages. With a simple method, just by the determination of the interaction between atoms by Newton's second law, together with the averaging statistics method, and applying the computational methods, it serves as a complement to conventional experiments. Based on these obtained results it can be concluded that the nanomaterials have a link length (r) always smaller than that of the bulk material. With the nanomaterials, no pick separation at the first pick of the Radial Distribution Function (RDF) can be observed. With amorphous material, the pick separation occurs at the first vertex of RDF and has 02 Picks, the first Pick has a link length of r11 = 3.11 Å and the second Pick has a link length of r12 = 3.40 Å [55] with link length rFe-Fe = 3.11 Å related to octahedral link pair. Furthermore, the positions of Fe atoms are link to their edges and gradually increase to rFe-Fe = 3.40 Å. Besides, the Coordination Number (CN) of nanomaterials increases when is increased the nano-size. The average coordination number (CN), CNFe-O the range of 4.71-5.28, shows that α-Fe2O3, β-Fe2O3 tend to form an octahedral FeO6 structure in the liquid state with T = 3500 K [54,56,57,58]. Similarly, the bond angle Fe-O-Fe of liquid Fe2O3 nanomaterials at T = 3500 K ranges from 83° to 99°. It is known that for the ideal FeO6 configuration, the O-Fe-O angle is 90°, and for the ideal FeO4 it is 109.5°. However, β-Fe2O3 and ε-Fe2O3 polymorphic structures with only superparamagnetic Fe2O3 nanomaterials [59] have octahedral structural units number of FeO6, FeO4 tetrahedra in ε-Fe2O3 [60,61,62]. The glass temperature (Tg) is an important parameter used for studies about amorphous materials. The glass temperature of Fe2O3 nanomaterials usually is calculated through the intersection of high linear temperature and low temperature extrapolated to the total energy. The values Tg = 2182.18 K, 1897.26 K, 1784.19 K, and 1610.33 K of nanomaterials correspond for the nano-size (D) (2, 3, 4, and 5 nm). Besides, there are also results showing that Tg increases with the increases of D [63,64]. For Fe2O3 materials, Tg = 1400 K has a much smaller value than nanomaterials. Based on the existing data it can be concluded that the results obtained are contradictory, and there are not yet results covering all types of materials such as nanomaterials, thin films, and bulk materials [63,64,65,66]. Besides, in some studies is also determined the phase transition temperature (Tm) [67]. It has been demonstrated that the obtained results depend on the specified research method and applied boundary conditions [66]. Well-documented studies highlighted that there are various factors such as the atomic number (N), temperature (T), pressure (P), surface elevation (h) of the earth's, phase transition process, and heterogeneous kinetic, that can influence the oxide materials CaSiO3 [68], MgSiO3 [69,70]. In these reports, the researchers found a shift in the number of SiOx, MgOy, CaOz structural units with x, y, z = 4/12. However, so far, there have been no specific studies about the structural characteristics of Fe2O3 materials at the high temperature (T) the range is 300-7000 K, and high pressure (P) from P = 0 GPa to P = 360 GPa. To elucidate, the phase transition process can be studied based on the change of the number of structural units FeO4, FeO5, FeO6 in the Fe2O3 material. In our study are given the results of molecular dynamics simulations to determine the structure, phase transition process of Fe2O3 material.
Initially, a Fe2O3 material with 2000 atoms (800 Fe atoms, 1200 O atoms) was randomly seeded into a model, a cube a nano-size (l), determined by the Eq 1:
l=(Nρ)13=((2mFenFe+3mOnO)ρ)13 | (1) |
where: ρ = 5.19 g/cm3, and ρ is the specific gravity of Fe2O3.
We use this model by the MD simulation method [51,52,71,72,73,74,75,76,77] with the force field of the Born-Mayer (BM) pair interaction potential calculated with the Eq 2 [52,58]:
Uij(r)=qiqjr+Bijexp(−rRij) | (2) |
where: qi, qj are the charges of ions Fe, O; r is the distance from the ith atom to the jth atom, and Bij, Rij are the parameters chosen as: BFe-Fe = 0.0 eV, BFe-O = 2453 eV, BO-O = 1500 eV, Rij = 29 pm, qFe = +3e, qO = −2e [52,58].
To obtain accurate results, we applied periodic boundary conditions to eliminate surface effects.
With the content of the MD method, it is only necessary to determine the interaction between atoms according to the content of Newton's II law. With the interaction of the force field, the atoms will move with the displacement (r) and velocity (v). Within the scope of the content of the article, the interactive force field includes the interaction force field between atoms that obeys Newton's II law and the electronic interaction force field between atoms. To determine the quantities, we use Verlet's algorithm to integrate the equations of motion and are combined them with the average statistical method to determine the energy (E) of each atom, according to the following Eq 3:
E=U+K;U=∑i>jUij(rij),K=N∑i=1miv2i2 | (3) |
The rate of increase in temperature (T) and pressure (P) can be calculated with the Eqs 4, 5:
T(t)=13NkBN∑i=1mi(vi(t))2 | (4) |
P(t)=NVkBT(t)+13V∑i<jrij(t)Fij(t) | (5) |
where: U, K, N, V are the potential energy, kinetic energy, atomic number, material volume, and kB = 1.381 × 10−23 J/K is the Boltzmann constant.
The heating process of the model is carried out according to the Eq 6 [52,58]:
T=T0−γt | (6) |
where: γ is the cooling coefficient, γ = 4.357 × 1013 Ks−1.
Initially, it was considered the Fe2O3 material model at a temperature (T), T = 7000 K, and it was run 4 × 104 steps of NVT, with NVP recovery statistics (N is the atomic number, V is volume, T is temperature, and pressure P is constant). The simulation was made for each time step of 0.5 fs so that the model discards the initial configuration and stabilizes at the desired temperature (T), and pressure (P). Then, it was decreased T from T = 7000 K to T = 300 K with a heating rate of dT = 5 K/fs to convert the material model to an amorphous state. This process was followed by an increasing of the temperature T from T = 300 K to T = 900, 1300, 1900, 2300, 2900, 3400, 4500, 5700, 7000 K at P = 0 GPa. Similarly, at T = 300, 2300, 4500, 7000 K, it was increased the pressure P from P = 0 GPa to P = 50, 150, 250, 360 GPa with a turbocharge rate dP = 0.001 GPa/fs with 4 × 104 regression steps that fits all models. After it was obtained the equilibrium in these models, was applied for all models simultaneously running with 107 NVE steps (N is the number of atoms, V is the volume, and E is the energy-being constant). The structural results of the models were determined by an average process after 100 simulation steps. During the computation, for all models, the same conditions (N, V, T, P, and E constant) were applied. To study the structure, phase transition process, and heterogeneous kinetics, data analysis, and visualization methods were used. With the obtained results, the structural features were investigated through the radial distribution function (RDF) with the Eq 7 [68,69,70]:
g(r)=VN2⟨∑ini(r)4πr2Δr⟩ | (7) |
where: r, ni(r), V, N, g(r) are the distance between atoms, the density of atoms, volume, number of atoms, and probability of finding an atom between r to r + Δr.
In addition, there are other quantities such as nano-size (1), angular distribution, and average coordination number (CN) that are calculated using the following Eq 8 [68,69,70]:
CN=4πρr1∫0g(r)r2dr | (8) |
where: r1 is the first peak position of the RDF, and the phase transition temperature (Tm) is determined through the relationship between E and T.
For the bond angle, the relationship between the Fe-O-Fe and O-Fe-O bond angle is used for the link lengths (applied for the links O-O, Fe-O, Fe-Fe), which are determined by the Eq 9:
cosα=2r2Fe−O−r2Fe−Fe2r2Fe−O | (9) |
where: α = Fe-O-Fe or O-Fe-O for the model defined at T and P. During heating and pressure, the model annealing is determined by the Nosé-Hoover formula [78,79]. To confirm the accuracy of the results, it was compared our results with those obtained previously under the same T and P conditions. All these results were written in the C programming language and were computed on the computer central system of the Institute of Physics, the Department of Physics and Astronomy of Zielona Gora University, Poland.
To study the structure, and phase transition process of Fe2O3 materials with atomic number (N), N = 2000 atoms at temperature (T), T = 300, 900, 1300, 1900, 2300, 3400, 4500, 5700, 7000 K at pressure (P), P = 0 GPa has applied the simulation method of molecular dynamics (MD) with pair interaction potential Born-Mayer (BM) and conditions periodic boundary, according to Eq 2. The results of the shape, nano-size (l), energy (E) of the system, and radial distribution function (RDF) of links Fe-Fe, Fe-O, O-O pairs are different according to Eq 7 (Figure 1, and Table 1).
T(K) | rij(Å) | gij(r) | 1 (nm) | E (eV) | ||||
Fe-Fe | Fe-O | O-O | Fe-Fe | Fe-O | O-O | |||
300 | 3.14 | 2.00 | 2.66 | 3.20 | 8.75 | 2.49 | 2.92 | −29.56 |
900 | 3.24 | 1.98 | 2.72 | 2.88 | 7.23 | 2.28 | 2.926 | −29.40 |
1300 | 3.32 | 1.98 | 2.78 | 2.83 | 6.53 | 2.30 | 2.932 | −29.29 |
1900 | 3.32 | 1.98 | 2.82 | 2.73 | 5.87 | 2.23 | 2.946 | −29.13 |
2300 | 3.32 | 1.96 | 2.84 | 2.72 | 5.44 | 2.20 | 2.936 | −29.01 |
3400 | 3.36 | 1.96 | 2.86 | 2.57 | 4.73 | 2.05 | 2.98 | −28.67 |
4500 | 3.40 | 1.92 | 2.94 | 2.40 | 4.56 | 1.88 | 3.05 | −28.24 |
5700 | 3.42 | 1.94 | 2.92 | 2.22 | 4.26 | 1.79 | 3.10 | −27.86 |
7000 | 3.46 | 1.88 | 2.96 | 2.09 | 4.18 | 1.71 | 3.19 | −27.41 |
previous results | 3.35 [33,34,53]; 3.11 [33,55,58]; 3.1 [52] |
1.91/1.95 [33,34,53]; 2.08 [54]; 1.925/1.945 [33,53]; 1.9 [33,42,52,55,58] |
2.91 [34,33,53]; 2.7 [33,42,52,55,58] |
The results show that the Fe2O3 material at T = 300 K, P = 0 GPa has a cubic shape, nano-size (1), 1 = 2.92 nm, the energy (E), E = −29.56 eV and it is generated by two atoms Fe and O (Fe in red, O in blue) (Figure 1a). In addition, the Fe2O3 material is made by links Fe-Fe, Fe-O, O-O with the corresponding links lengths rFe-Fe = 3.14 Å, rFe-O = 2.00 Å, rO-O = 2.66 Å (Figure 1b). In this case, the obtained results are completely consistent with experimental results with rFe-Fe = 3.35 Å, rFe-O = 1.93 Å, rO-O = 2.91 Å [34] and rFe-Fe = 3.35 Å, rFe-O = 1.91/1.95 Å, rO-O = 2.91 Å [33,53] and rFe-O = 2.08 Å [54]; whereas the simulation results with rFe-Fe = 3.11 Å, rFe-O = 1.90 Å, rO-O = 2.70 Å [33,55,58] and rFe-Fe = 3.1 Å, rFe-O = 1.9 Å, rO-O = 2.7 Å [52]. It can be noted that the link length of bulk materials is always larger than the link length of nanomaterials with nanomaterials is rFe-Fe = 3.10 Å, rFe-O = 1.9 Å, rO-O = 2.7 Å [33,42,52]. The Fe-Fe link length appears a Pick separation at the first vertex of the RDF into two small peaks, r11 = 3.14 Å, r12 = 3.4 Å, which shows that the Fe2O3 material, at T = 300 K, exists in the amorphous state, and confirms this result as consistent with previous simulation results [33,34,55]. Besides, the Fe-Fe link length of r11 = 3.11 Å is related to the number of FeO4 structural units, whereas r12 = 3.40 Å is related to the number of FeO6 structural units and has a common peak [55]. When it is increased the temperature from T = 300 K to T = 900, 1300, 1900, 2300, 3400, 4500, 5700, 7000 K, l increases from 1 = 2.92 nm to 1 = 2.926, 2.932, 2.946, 2.936, 2.98, 3.05, 3.10, 3.19 nm altitude and the energy (E) increases from E = −29.56 eV to E = −29.40, −29.29, −29.13, −29.01, −28.67, −28.24, −27.86, −27.41 eV. It can be seen that the influence of temperature on the link lengths r of Fe-Fe, Fe-O, O-O of Fe2O3 bulk is very large as rFe-Fe and increases from rFe-Fe = 3.14 Å to rFe-Fe = 3.24, 3.32, 3.32, 3.32, 3.36, 3.40, 3.42, 3.46 Å; rFe-O decreases from rFe-O = 2.00 Å to rFe-O = 1.98, 1.98, 1.98, 1.96, 1.96, 1.92, 1.94, 1.88 Å; rO-O increases from rO-O = 2.66 Å to rO-O = 2.72, 2.78, 2.82, 2.84, 2.86, 2.94, 2.92, 2.96 Å corresponding to the height of the first peak. Also, the radial distribution function g(r) decreases as gFe-Fe increases from gFe-Fe = 3.20 to gFe-Fe = 2.88, 2.83, 2.73, 2.72, 2.57, 2.40, 2.22, 2.09; gFe-O decreases from gFe-O = 8.75 to gFe-O = 7.23, 6.53, 5.87, 5.44, 4.73, 4.56, 4.26, 4.18; gO-O increases from gO-O = 2.49 to gO-O = 2.28, 2.30, 2.23, 2.20, 2.09, 1.88, 1.79, 1.71 (Table 1). On the other hand, during the study, it was found that in the temperature range from T = 300 K to T = 900, 1900, 2300 K and T = 2300 K to T = 3400, 4500, 5700, 7000 K, the g(r) of Fe-O decreases to the smallest value, showing that the Fe2O3 material was a phase transition from the amorphous state to the liquid state. The phase transition of Fe2O3 materials is a type 1 phase transition. During the heating process of Fe2O3 materials, Eq 6 is always applied and the accuracy is evaluated according to the Nosé-Hoover formula [78,79]. To confirm the influence of temperature on structural change, and heterogeneous kinetics, it was determined the average coordination number (CN) according to the Eq 8, and the energy (E) at high temperature (T) (Table 2).
T(K) | CN | |||
Fe-Fe | Fe-O | O-Fe | O-O | |
300 | 11.20 | 5.44 | 3.63 | 15.95 |
900 | 11.42 | 5.35 | 3.57 | 15.90 |
1300 | 11.40 | 5.33 | 3.55 | 15.82 |
1900 | 11.32 | 5.29 | 3.53 | 15.64 |
2300 | 11.67 | 5.60 | 3.73 | 15.93 |
3400 | 11.06 | 5.11 | 3.41 | 15.28 |
4500 | 11.35 | 5.34 | 3.56 | 14.37 |
5700 | 9.63 | 4.64 | 3.09 | 13.78 |
7000 | 8.63 | 4.12 | 2.75 | 3.55 |
The results show that, as the temperature increases, the average coordination number (CN) of the link Fe-Fe changes from CNFe-Fe = 11.20 to CNFe-Fe = 11.42, 11.40, 11.32, 11.67, 11.06, 11.35, 9.67, 8.63; Fe-O changes from CNFe-O = 5.44 to CNFe-O = 5.35, 5.33, 5.29, 5.60, 5.11, 5.34, 4.64, 4.12; O-Fe changes from CNO-Fe = 3.63 to CNO-Fe = 3.57, 3.55, 3.53, 3.73, 3.41, 3.56, 3.09, 2.75; O-O changes from CNO-O = 15.95 to CNO-O = 15.90, 15.82, 15.64, 15.93, 15.28, 14.37, 13.78, 3.55 (Table 2), and the energy (E) increases (Table 1).
In this case, the average coordination number of Fe-O decreases from CN = 5.44 to CN = 5.26; this is the FeO5 structure of Fe2O3 material. When it is increased the temperature from T = 300 K to T = 900, 1900, 2300, 3400, 4500, 5700, 7000 K, the average coordination number (CN), and the bonding density of Fe-O, O-Fe tends to decrease, indicating that the oxide material tends to shift to the liquid state. Based on these results, we can realize that the increase of the temperature leads to an increase in the size (1) and E of the material, which proves that there is a major influence of temperature. With extremes, the distribution number of coordination has the value CN > 5.26 with Fe-O and CN > 3.51 with O-Fe, of which the majority is CN = 5.0 with Fe-O, and at CN = 4.0 with O-Fe. On the other hand, at T = 300 K, the amorphous Fe2O3 material has a distorted FeO6 structure with the average coordination number of the Fe-O pair with CNFe-O value ≈ 6 and it was considered that these FeO6 structural units are as structural defects [58]. In addition, to analyze the structure of the Fe2O3 material oxide material, it was applied the visualization method to study the number of structural units of the material (Figure 2).
The Fe2O3 material at T = 300 K, P = 0 GPa exists with 03 structural units: FeO4 corresponds to one Fe atom link to four O atoms (Figure 2a), similar with FeO5 (Figure 2b), FeO6 (Figure 2c), and the structure shape of Fe2O3 material with the number of the structural unit of FeO4 is black, FeO5 is red, FeO6 is blue at T = 300 K, P = 0 GPa (Figure 2d). The number of structural units in the Fe2O3 material at different temperatures (T) is shown in Table 3.
Temperature (K) | FeO4 | FeO5 | FeO6 |
300 | 419 | 1627 | 1080 |
900 | 453 | 1647 | 1018 |
1300 | 540 | 1621 | 1018 |
1900 | 676 | 1640 | 850 |
2300 | 789 | 1552 | 833 |
3400 | 1175 | 1501 | 462 |
4500 | 1551 | 1225 | 209 |
5700 | 1634 | 1949 | 201 |
7000 | 1634 | 1049 | 201 |
The obtained results show that, when the temperature is increased, the number of structural units FeO4 increases from 419 to 453, 540, 676, 789, 1175, 1551, 1634, 1634; FeO5 changes about from 1627 to 1647, 1621, 1640, 1552, 1501, 1225, 1949, 1049; FeO6 decrease from 1080 to 1018, 1018, 850, 833, 462, 209, 201, 201 (Table 3), showing that the Fe2O3 material tends to shift to the liquid state, which demonstrates the influence of temperature on link lengths and the number of structural units that are very big. In addition, the angular distributions of Fe-O-Fe and O-Fe-O are shown in Table 4.
Temperature (K) | Angular distribution | |
Fe-O-Fe | O-Fe-O | |
300 | 105 | 95 |
900 | 105 | 95 |
1300 | 100 | 95 |
1900 | 100 | 95 |
2300 | 100 | 95 |
3400 | 100 | 95 |
4500 | 95 | 95 |
5700 | 95 | 95 |
7000 | 95 | 95 |
The obtained results show that, when increasing the temperature, the angle distribution Fe-O-Fe, O-Fe-O between Fe and O atoms has a negligible change around the value of 105° with Fe-O-Fe and with O-Fe-O is 95°. When it is increased the temperature from T = 300 K to T = 900, 1900, 2300, 3400, 4500, 5700, 7000 K, Fe-O-Fe decreases from 105° to 95° and O-Fe-O has a constant value is 95° (Table 4). The obtained results are completely consistent with the simulation results [55,58].
For O-Fe-O bond angle nanomaterials, O-Fe-O has major peaks between 99° and 83°. While the ideal uniform octahedral model has a value of 90°, this is considered the ideal tetrahedral value. The value of 109.5°, confirms the reason that there is a moving to the liquid state, and there are structural units of FeO5.
The results show that the bond angle O-Fe-O reduced from 105° to 90° when the material changes to the liquid state. These results raise the question of whether the bond angle depends on the length of the links. Through the computational process, was applied the Eq 9, and it was highlighted when rFe-Fe, rO-O increases, rFe-O decreases. Besides, there is a relationship between the temperature (T) and the energy (E), (Figure 3).
The results show that, when it is increased the temperature (T), form 300-2300 K to 2300-7000 K, the energy (E) of Fe2O3 material increases from E = −29.56 eV to E = −29.00 eV and from E = −29.00 eV to E = −27.41 eV. When T increases, T = 300-2300 K then E increases slowly, and between T = 2300 K to T = 7000 K this leads to an E rapid increase. These results show that from T = 300 K to T = 2300 K the Fe2O3 material exists in an amorphous state, and E increases slowly. When there is the Fe2O3 material at state liquid, E increases rapidly, due to the intersection between the fast-rising energy region and the slowly increasing energy region of 2300 K and calling this is as a point of the phase transition or phase transition temperature (Tm), Tm = 2300 K, corresponding to E = −29.00 eV (Figure 3). This leads to an abrupt change in the density of atoms. When it is increased T, this leads to an increase in nano-size (1), E increases, and the results are like those in simulations of CaSiO3 [68], MgSiO3 [69,70] materials.
The phase transition temperature is one of the most important parameters of amorphous materials, and only the glass temperature (Tg) of Fe2O3 nanomaterials was found in the scientific literature [52]. The obtained results show that Tg depends greatly on the nanoparticle nano-size. When it is increased the nano-size (D) of nanomaterials is D = 2-5 nm, the Tg decreases Tg = 2182-1610 K. These results appear to be incomplete in contradiction to previously published bulk materials. In addition, the characteristics of the phase transition from the liquid state to the crystalline state are still unclear with the statements for previously published papers [65,66]. With the phase transition temperature Tm, there is a lack of consensus on studying the nature of the phase transition [63,64,67]. The obtained results show that there is a great influence of temperature on the structure, phase transition process of Fe2O3 material.
Similarly, it was studied the effect of pressure (P), P = 0, 50, 150, 250, 360 GPa at temperature (T), T = 300, 2300, 4500, 7000 K, to elucidate the structure, phase transition process of Fe2O3 material.
The Fe2O3 material at T = 300 K, leads to an P increasing from P = 0 GPa to P = 50, 150, 250, 360 GPa with structural characteristic results (Figure 4).
The results show for the material Fe2O3 material at T = 300 K, P = 0 GPa, that it has a structure shape (Figure 4a) and the Fe-Fe, Fe-O, O-O bonding length of Fe-Fe is rFe-Fe = 3.14 Å, rFe-O = 2.0 Å, rO-O = 2.66 Å.
Also, the first peak height of the radial distribution function (RDF) of the links is gFe-Fe = 3.20, gFe-O = 8.75, gO-O = 2.49. When it is increased P from P = 0 GPa to P = 50, 150, 250, 360 GPa, then rFe-Fe decreases from rFe-Fe = 3.14 Å to rFe-Fe = 3.10, 2.86, 2.74, 2.66 Å, and gFe-Fe increases, and decreases from gFe-Fe = 3.20 to gFe-Fe = 3.30, 3.20, 2.83, 2.76; rFe-O decreases from rFe-O = 2.0 Å to rFe-O = 1.92, 1.86, 1.84, 1.84 Å, and gFe-O decreases from gFe-O = 8.75 to gFe-O = 7.28, 6.86, 6.49, 5.99; rO-O decreases from rO-O = 2.66 Å to rO-O = 2.66, 2.50, 2.38, 2.24 Å, and gO-O changes from gO-O = 2.49 to gO-O = 2.72, 2.66, 2, 76, 2.72 (Figure 4b, c); size (1), decreases from 1 = 2.92 nm to 1 = 2.72, 2.55, 2.44, 2.36 nm (Figure 4d), the energy (E) increases from E = -29.56 eV to E = -29.22, -28.34, -27.33, -26.27 eV (Figure 4e) corresponding to the mean coordinate number (CN), CNFe-Fe increases from CNFe-Fe = 11.20 to CNFe-Fe = 13.91, 16.42, 18.69, 20.70; CNFe-O increases from CNFe-Fe = 5.44 to CNFe-Fe = 6.28, 7.25, 8.12, 8.73; CNO-Fe increases from CNFe-Fe = 3.63 to CNFe-Fe = 4.19, 4.83, 5.41, 5.82; CNO-O increases from CNFe-Fe = 15.95 to CNFe-Fe = 18.64, 23.02, 26.80, 30.07 (Figure 4g). In addition, the bonding angle of Fe-O-Fe, O-Fe-O and the number of structural units FeO4, FeO5, FeO6 are determined by Figure 5.
The results show at P = 0 GPa that the angle of Fe-O-Fe is 105°, and of O-Fe-O is 95° corresponding to the number of structural units FeO4, FeO5, FeO6 is 419, 1627, 1080. When it is increased P from P = 0 GPa to P = 50, 150, 250, 360 GPa, then Fe-O-Fe decreases from 105° to 0°, O-Fe-O is 95° (Figure 5a) and FeO4, FeO5 decreases from 419 to 48, 15, 0, 0; FeO5 decreases from 1627 to 1217, 336, 63, 12; FeO6 increases from 1080 to 1638, 1936, 1989, 1998 (Figure 5b). The obtained results are completely consistent with the results from the literature [80]. Besides, it also shows that r, g(r) decreases when Fe2O3 material is at high pressure and low temperature.
Similarly, with Fe2O3 material at T = 2300 K, when P increases from P = 0 GPa to P = 50, 150, 250, 360 GPa, there are structural characteristic results (Figure 6).
The results show, when Fe2O3 material at T = 2300 K, P = 0 GPa, there is a structure shape (Figure 6a), with the length of Fe-Fe, Fe-O, O-O links is 3.32 Å, rFe-O = 1.96 Å, respectively rO-O = 2.84 Å, the first peak radial distribution function (RDF) of the links is gFe-Fe = 2.72, gFe-O = 5.44, gO-O = 2.22 (Figure 6a). When it is increased P from P = 0.0 GPa to P = 50, 150, 250, 360 GPa, rFe-Fe decreases from rFe-Fe = 3.32 Å to rFe-Fe = 3.14, 2.96, 2.80, 2.77 Å, and gFe-Fe increased, decreases from gFe-Fe = 2.72 to gFe-Fe = 2.94, 2.72, 2.70, 2.51; rFe-O decreases from rFe-O = 1.96 Å to rFe-O = 1.92, 1.86, 1.84, 1.82, and gFe-O increased, decreases from gFe-O = 5.44 to gFe-O = 6.29, 5.52, 5.42, 5.18; rO-O decreases from rO-O = 2.84 Å to rO-O = 2.64, 2.48, 2.32, 2.22 Å, and gO-O increased, decreases from gO-O = 2.20 to gO-O = 2.44, 2.53, 2.53, 2.48 (Figure 6b, c); nano-size (1), decreases from 1 = 2.94 nm to 1 = 2.72, 2.55, 2.44, 2.36 nm (Figure 6d) and energy (E) increases from E = −29.01 eV to E = −28.78, −27.92, −26.97, −26.00 eV (Figure 6e) corresponding to the mean coordinate number (CN), CNFe-Fe increases from CNFe-Fe = 11.67 to CNFe-Fe = 14.07, 16.61, 18.87, 20.60; CNFe-O increases from CNFe-O = 5.60 to CNFe-O = 6.42, 7.44, 8.32, 8.88; CNO-Fe increases from CNO-Fe = 3.73 to CNO-Fe = 4.28, 4.96, 5.55, 5.92; CNO-O increases from CNO-O = 15.93 to CNO-O = 18.99, 23.32, 26.99, 30.42; (Figure 6g). The same results are also obtained, with T = 2300 K (Figure 7).
The obtained results show at P = 0 GPa the bonding angle of Fe-O-Fe is 100°, O-Fe-O is 95° corresponding to the number of structural units (FeO4, FeO5, FeO6 is 789, 1552, 833). When it is increased P from P = 0 GPa to P = 50, 150, 250, 360 GPa, then Fe-O-Fe decreases from 100° to 0°, O-Fe-O increases from 95° to 110° (Figure 7a), and FeO4 decreases from 789 to 170, 15, 0, 0; FeO5 decreases 1552 to 1153, 353, 74, 0, and FeO6 increases from 833 to 1661, 1933, 1987, 2000 (Figure 7b). In it, all r, g(r), 1 decrease and E, CN increase but a smaller decrease at T = 300 K; it shows that in the phase transition temperature Tm = 2300 K, Fe2O3 material structure changes to the liquid state, so Fe2O3 material structure changes is more stable, when increasing P, it leads to changes in smaller structural features.
Similarly, when Fe2O3 material at T = 4500 K, P is increased from P = 0 GPa to P = 50, 150, 250, 360 GPa there are the structural characteristic results (Figure 8).
The results show when Fe2O3 material at T = 4500 K, P = 0 GPa has a structure shape (Figure 8a), and the length of Fe-Fe, Fe-O, O-O links respectively, rFe-Fe is 3.40 Å, rFe-O is 1.92 Å, rO-O is 2.94 Å, the first peak radial distribution function (RDF) of the links is gFe-Fe = 2.40, gFe-O = 4.56, gO-O = 1.88. When it is increased P from P = 0 GPa to P = 50, 150, 250, 360 GPa, then rFe-Fe decreases from rFe-Fe = 3.40 Å to rFe-Fe = 3.10, 2.92, 2.78, 2.74 Å, and gFe-Fe increased, decreases from gFe-Fe = 2.40 down to gFe-Fe = 2.57, 2.52, 2.51, 2.41; rFe-O decreases from rFe-O = 1.92 Å to rFe-O = 1.90, 1.88, 1.84, 1.84, and gFe-O decreases, increased from gFe-O = 4.56 to gFe-O = 4.52, 4.41, 4.55, 4.57; rO-O decreases from rO-O = 2.94 Å to rO-O = 2.80, 2.46, 2.34, 2.22 Å, and gO-O increases from gO-O = 1.88 to gO-O = 2.12, 2.18, 2.26, 2.39 (Figure 8b, c); that corresponds to nano-size (1), that decreases from 1 = 3.05 nm to 1 = 2.72, 2.55, 2.44, 2.36 nm (Figure 8d), and energy (E) increases from E = −28.24 eV to E = −28.17, −27.47, −26.49, −25.45 eV (Figure 8e) corresponding to the mean coordinate number (CN); CNFe-Fe increases from CNFe-Fe = 11.35 to CNFe-Fe = 14.40, 16.87, 18.99, 20.70; CNFe-O increases from CNFe-O = 5.34 to CNFe-O = 6.56, 7.69, 8.40, 8.91; CNO-Fe increases from CNO-Fe = 3.56 to CNO-Fe = 4.37, 5.12, 5.60, 5.94; CNO-O increases from CNO-O = 14.37 to CNO-O = 19.21, 23.56, 27.35, 30.51 (Figure 8g). The same results are obtained with T = 4500 K (Figure 9).
The obtained results show when P = 0 GPa the bonding angle of Fe-O-Fe is 100°, O-Fe-O is 95° corresponding to the number of structural units FeO4, FeO5, FeO6 is 1551, 1225, 209. When it is increased P from P = 0 GPa to P = 50, 150, 250, 360 GPa, then Fe-O-Fe decreases from 100° to 0°, O-Fe-O increases from 95° to 100° (Figure 9a) and FeO4 decreases from 1551 to 222, 5, 0, 0; FeO5 decreases from 1225 to 1271, 285, 46, 6, and FeO6 increases from 209 to 1583, 1948, 1992, 1999 (Figure 9b).
It can be observed that r, g(r), 1 decrease and E, CN increases, but a smaller decrease at T = 300, 2300 K show that in the high-temperature region, the Fe2O3 structure in the liquid state has a smaller structural change.
Similarly, when Fe2O3 material at T = 7000 K, P increased from P = 0 GPa to P = 50, 150, 250, 360 GPa, there are structural characteristic results (Figure 10).
The results show when Fe2O3 material at T = 7000 K, P = 0 GPa there is a structure shape (Figure 10a) and the length of Fe-Fe, Fe-O, O-O links respectively, rFe-Fe is 3.46 Å, rFe-O is 1.88 Å, rO-O is 2.96 Å, the first peak radial distribution function (RDF) of the links is gFe-Fe = 2.09, gFe-O = 4.18, gO-O = 1.71. When it is increased P from P = 0 GPa to P = 50, 150, 250, 360 GPa, rFe-Fe decreases from rFe-Fe = 3.46 Å to rFe-Fe = 3.10, 2.94, 2.78, 2.68 Å, and gFe-Fe increases, decreases from gFe-Fe = 2.09 to gFe-Fe = 2.37, 2.37, 2.36, 2.29; rFe-O decreases from rFe-O = 1.88 Å to rFe-O = 1.90, 1.88, 1.84, 1.82 Å, and gFe-O decreases from gFe-O = 4.18 to gFe-O = 3.62, 3.73, 3.93, 3.96; rO-O decreases from rO-O = 2.96 Å to rO-O = 2.62, 2.42, 2.28, 2.24 Å, and gO-O increases from gO-O = 1.71 to gO-O = 1.97, 2.05, 2.04, 2.15 (Figure 10b, c). Also, nano-size (1), decreases from 1 = 3.19 nm to 1 = 2.72, 2.55, 2.44, 2.36 nm (Figure 10d), energy (E) increases from E = −27.41 eV to E = −27.51, −26.81, −25.87, −24.83 eV (Figure 10e), corresponding to the average number of coordinates (CN); CNFe-Fe increases from CNFe-Fe = 8.63 to CNFe-Fe = 14.58, 17.01, 19.11, 20.83; CNFe-O increases from CNFe-O = 3.55 to CNFe-O = 6.69, 7.79, 8.49, 8.96; CNO-Fe increases from CNO-Fe = 2.75 to CNO-Fe = 4.46, 5.19, 5.66, 5.98; CNO-O increases from CNO-O = 4.12 to CNO-O = 19.36, 23.79, 27.79, 30.52 (Figure 10g). The results are similar with T = 7000 K (Figure 11).
The obtained results show, at P = 0 GPa the bonding angle of Fe-O-Fe is 95°, O-Fe-O is 95° corresponding to the number of structural units FeO4, FeO5, FeO6 is 1634, 1049, 201. When increasing P from P = 0 GPa to P = 50, 150, 250, 360 GPa then Fe-O-Fe decreases from 95° to 0°, O-Fe-O increases from 95° to 100° (Figure 11a) and FeO4 decreases from 1634 to 368, 20, 0, 0; FeO5 changes from 1049 to 1259, 397, 47, 0 and FeO6 increases from 201 to 1520, 1925, 1992, 2000 (Figure 11b).
In it, all r, g(r), 1 decreases and E, CN increase but with a smaller decrease at T = 2300, 4500 K. All obtained results, when an increase of T = 300-7000 K at P = 0.0 GPa and an increasing of P from P = 0 GPa to P = 50, 150, 250, 360 GPa at T = (300, 2300, 4500, 7000 K) then r, g(r) and 1, E all decrease with T > 4500 K, the decrease led to less, the smallest at T = 7000 K, this result corresponding to CN also increases fewer. In addition, the disappearance in the number of structural units appears with T = 2300 K; with T = 4500 K, FeO4 disappears at all material with P ≥ 250 GPa and Fe-O-Fe disappears with P ≥ 150 GPa. The obtained results are used as the basis for future experimental results such as determining the link length, and the bonding angle between atoms.
The molecular dynamics simulation method has successfully studied the influence of high temperature and high pressure on the structure and phase transition of Fe2O3 materials. The results show that with increasing temperature, the nano-size (1), energy increase, length link decreases, the number of structural units FeO4, FeO5 increases, and FeO6 decreases. In contrast, as pressure increases, then l decreases, E increases, FeO4, FeO5 decreases, and FeO6 increases. In addition, when P ≥ 150 GPa, FeO4 disappears, FeO5 disappears at P ≥ 250 GPa), then only FeO6 exists at T = 2300, 7000 K. It shows that when T increases, FeO4 increases, FeO5 increases, FeO6 decrease when increasing P gives the opposite result. The cause of this phase transition (the phase transition between the amorphous state to the liquid state and from the liquid to the amorphous state) is caused by the nano-size effect. The phase transition follows a type 1 phase transition. With the phase transition, the phase transition temperature (Tm) has been successfully determined, Tm = 2300 K, which is the phase transition temperature from the amorphous state to the state. liquid. The obtained results form the basis for future experimental studies.
The authors declare no conflict of interest.
[1] |
Zhang L, Hu A (2021) Fe2O3 Nanowire flux enabling tungsten inert gas welding of high-manganese steel thick plates with improved mechanical properties. Appl Sci 11: 5052. https://doi.org/10.3390/app11115052. doi: 10.3390/app11115052
![]() |
[2] |
Serga V, Burve R, Maiorov M, et al. (2020) Impact of gadolinium on the structure and magnetic properties of nanocrystalline powders of iron oxides produced by the extraction-pyrolytic method. Materials 13: 4147. https://doi.org/10.3390/ma13184147 doi: 10.3390/ma13184147
![]() |
[3] |
Azimov F, Kim J, Choi SM, et al. (2021) Synergistic effects of Fe2O3 Nanotube/Polyaniline composites for an electrochemical supercapacitor with enhanced capacitance. Nanomaterials 11: 1557. https://doi.org/10.3390/nano11061557 doi: 10.3390/nano11061557
![]() |
[4] |
Essandoh M, Garcia RA (2018) Efficient removal of dyes from aqueous solutions using a novel hemoglobin/iron oxide composite. Chemosphere 206: 502-512. https://doi.org/10.1016/j.chemosphere.2018.04.182 doi: 10.1016/j.chemosphere.2018.04.182
![]() |
[5] |
Milagres JL, Bellato CR, Ferreira SO, et al. (2020) Preparation and evaluation of hydrocalumite-iron oxide magnetic intercalated with dodecyl sulfate for removal of agrichemicals. J Environ Manage 255: 109845. https://doi.org/10.1016/j.jenvman.2019.109845 doi: 10.1016/j.jenvman.2019.109845
![]() |
[6] |
Ge YL, Zhang YF, Yang Y, et al. (2019) Enhanced adsorption and catalytic degradation of organic dyes by nanometer iron oxide anchored to single-wall carbon nanotubes. Appl Surf Sci 488: 813-826. https://doi.org/10.1016/j.apsusc.2019.05.221 doi: 10.1016/j.apsusc.2019.05.221
![]() |
[7] |
Jin J, Ohkoshi S, Hashimoto K (2004) Giant coercive field of nanometer-sized iron oxide. Adv Mater 16: 48-51. https://doi.org/10.1002/adma.200305297 doi: 10.1002/adma.200305297
![]() |
[8] |
Jolivet JP, Tronc E, Chaneac C (2006) Iron oxides: From molecular clusters to solid. A nice example of chemical versatility. C R Geosci 338: 488-497. https://doi.org/10.1016/j.crte.2006.04.014 doi: 10.1016/j.crte.2006.04.014
![]() |
[9] |
Li Y, Zhao L, Wang Y, et al. (2018) Effects of Fe2O3 on the properties of ceramics from steel slag. Int J Miner Metall Mater 25: 413-419. https://doi.org/10.1007/s12613-018-1586-7 doi: 10.1007/s12613-018-1586-7
![]() |
[10] |
Tao S, Liu S, Yuan Y, et al. (2022) A microstructural and compositional study of ε-Fe2O3 crystals in the Hare's Fur Jian Ware. Crystals 12: 367. https://doi.org/10.3390/cryst12030367 doi: 10.3390/cryst12030367
![]() |
[11] |
Malviya KD, Dotan H, Shlenkevich D, et al. (2016) Systematic comparison of different dopants in thin film hematite (α-Fe2O3) photoanodes for solar water splitting. J Mater Chem A 4: 3091-3099. https://doi.org/10.1039/C5TA07095C doi: 10.1039/C5TA07095C
![]() |
[12] |
Xu J, Wen Q, Zhang X, et al. (2021) One-Step construction of multi-walled CNTs loaded with α-Fe2O3 nanoparticles for efficient, photocatalytic properties. Materials 14: 2820. https://doi.org/10.3390/ma14112820 doi: 10.3390/ma14112820
![]() |
[13] |
Sivula K, Formal FL, Gratzel M (2011) Solar water splitting: progress using hematite (α-Fe2O3) photoelectrodes. Chem Sus Chem 4: 432-449. https://doi.org/10.1002/cssc.201000416 doi: 10.1002/cssc.201000416
![]() |
[14] |
Yu S, Hong VMN, Wang F, et al. (2018) Synthesis and application of iron-based nanomaterials as anodes of lithiumion batteries and supercapacitors. J Mater Chem A 6: 9332-9367. https://doi.org/10.1039/C8TA01683F doi: 10.1039/C8TA01683F
![]() |
[15] |
Machala L, Zboril R, Gendanken A (2007) Amorphous iron (Ⅲ) oxide A review. J Phys Chem B 111: 4003-4018. https://doi.org/10.1021/jp064992s doi: 10.1021/jp064992s
![]() |
[16] |
Kment S, Riboni F, Pausova S, et al. (2017) Photoanodes based on TiO2 and α-Fe2O3 for solar water splitting-superior role of 1D nanoarchitectures and of combined heterostructures. Chem Soc Rev 46: 3716-3769. https://doi.org/10.1039/C6CS00015K doi: 10.1039/C6CS00015K
![]() |
[17] |
Gong XB, You SJ, Wang XH, et al. (2014) A novel stainless steel mesh/cobalt oxide hybrid electrode for efficient catalysis of oxygen reduction in a microbial fuel cell. Biosens Bioelectron 55: 237-241. https://doi.org/10.1016/j.bios.2013.12.015 doi: 10.1016/j.bios.2013.12.015
![]() |
[18] |
Zhu Y, Zhang B, Wang DW, et al. (2015) Order of activity of nitrogen, iron oxide, and FeNx complexes towards oxygen reduction in alkaline medium. ChemSusChem 8: 4016-4021. https://doi.org/10.1002/cssc.201501141 doi: 10.1002/cssc.201501141
![]() |
[19] |
Teja AS, Koh PY (2009) Synthesis, properties, and applications of magnetic iron oxide nanoparticles. Cheminform 55: 22-45. https://doi.org/10.1002/cssc.201501141 doi: 10.1002/cssc.201501141
![]() |
[20] |
Shen S, Lindley SA, Chen X, et al. (2016) Hematite heterostructures for photoelectrochemical water splitting: rational materials design and charge carrier dynamics. Energy Environ Sci 9: 2744-2775. https://doi.org/10.1039/C6EE01845A doi: 10.1039/C6EE01845A
![]() |
[21] |
Zhang N, Guo Y, Wang X, et al. (2017) A beta-Fe2O3 nanoparticle-assembled film for photoelectrochemical water splitting. Dalton Trans 46: 10673-10677. https://doi.org/10.1039/C7DT00900C doi: 10.1039/C7DT00900C
![]() |
[22] |
Schrebler R, Ballesteros LA, Gomez H, et al. (2014) Electrochemically grown self-organized hematite nanotube arrays for photoelectrochemical water splitting. J Electrochem Soc 161: 903-908. https://doi.org/10.1149/2.0481414jes doi: 10.1149/2.0481414jes
![]() |
[23] |
Danno T, Nakatsuka D, Kusano Y, et al. (2013) Crystal structure of β-Fe2O3 and topotactic phase transformation to α-Fe2O3. Cryst Growth Des 13: 770-774. https://doi.org/10.1021/cg301493a doi: 10.1021/cg301493a
![]() |
[24] |
Zhang N, Wang X, Feng J, et al. (2020) Paving the road toward the use of β-Fe2O3 in solar water splitting: Raman identification, phase transformation and strategies for phase stabilization. Natl Sci Rev 7: 1059-1067. https://doi.org/10.1093/nsr/nwaa039 doi: 10.1093/nsr/nwaa039
![]() |
[25] |
Tucek J, Machala L, Ono S, et al. (2015) Zeta-Fe2O3-A new stable polymorph in iron (Ⅲ) oxide family. Sci Rep 5: 15091. https://doi.org/10.1038/srep15091 doi: 10.1038/srep15091
![]() |
[26] | Chirita M, Grozescu I (2009) Fe2O3-Nanoparticles, physical properties and their photochemical and photo electrochemical applications. Chem Bull 54: 1-8. |
[27] |
Ding Y, Morber JR, Snyder RL, et al. (2007) Nanowire structural evolution from Fe3O4 to ε-Fe2O3. Adv Funct Matter 17: 1172-1178. https://doi.org/10.1002/adfm.200601024 doi: 10.1002/adfm.200601024
![]() |
[28] |
Yu Q, Meng X, Wang T, et al. (2015) Hematite films decorated with nanostructured ferric oxyhydroxide as photoanodes for efficient and stable photoelectrochemical water splitting. Adv Funct Mater 25: 2686-2692. https://doi.org/10.1002/adfm.201500383 doi: 10.1002/adfm.201500383
![]() |
[29] |
Tronc E, Chaneac C, Jolivet JP (1998) Structural and magnetic characterization of ɛ-Fe2O3. J Solid State Chem 139: 93-104. https://doi.org/10.1006/jssc.1998.7817 doi: 10.1006/jssc.1998.7817
![]() |
[30] |
Yoshikiyo M, Yamada K, Namai A, et al. (2012) Study of the electronic structure and magnetic properties of ε-Fe2O3 by first-principles calculation and molecular orbital calculations. J Phys Chem C 116: 8688-8691. https://doi.org/10.1021/jp300769z doi: 10.1021/jp300769z
![]() |
[31] |
Wang L, Wang Y, Zhang M, et al. (2019) Three-dimensional microstructure of ε‑Fe2O3 crystals in ancient chinese sauce glaze porcelain revealed by focused ion beam scanning electron microscopy. Anal Chem 91: 13054-13061. https://doi.org/10.1021/acs.analchem.9b03244 doi: 10.1021/acs.analchem.9b03244
![]() |
[32] |
Yusuf SM, Mukadama MD, Teresa JMD, et al. (2010) Structural and magnetic properties of amorphous iron oxide. Physica B 405: 1202-1206. https://doi.org/10.1016/j.physb.2009.11.040 doi: 10.1016/j.physb.2009.11.040
![]() |
[33] | Signorini L, Pasquini L, Savini L, et al. (2003) Size-dependent oxidation in iron/iron oxide core-shell nanoparticles. Phys Rev B 195423. https://doi.org/10.1103/PhysRevB.68.195423 |
[34] |
Townsend TK, Sabio EM, Browning ND, et al. (2011) Photocatalytic water oxidation with suspended alpha-Fe2O3 particles-effects of nano scaling. Energy Environ Sci 4: 4270-4275. https://doi.org/10.1039/C1EE02110A doi: 10.1039/C1EE02110A
![]() |
[35] |
Yen FS, Chen WC, Yang JM, et al. (2002) Crystallite size variations of nano sized Fe2O3 powders during γ-to α-phase transformation. Nano Lett 2: 245-252. https://doi.org/10.1021/nl010089m doi: 10.1021/nl010089m
![]() |
[36] |
Wheeler DA, Wang G, Ling Y, et al. (2012) Nanostructured hematite: synthesis, characterization, charge carrier dynamics, and photoelectrochemical properties. Energy Environ Sci 5: 6682-6702. https://doi.org/10.1039/C2EE00001F doi: 10.1039/C2EE00001F
![]() |
[37] |
Machala L, Tucek J, Zboril R (2011) Polymorphous transformations of nanometric iron (Ⅲ) oxide: A review. Chem Mater 23: 3255-3272. https://doi.org/10.1021/cm200397g doi: 10.1021/cm200397g
![]() |
[38] |
Tucek J, Zboril R, Namai A, et al. (2010) ɛ-Fe2O3: An advanced nanomaterial exhibiting giant coercive field, millimeter-wave ferromag-netic resonance, and magnetoelectric coupling. Chem Mater 22: 6483-6505. https://doi.org/10.1021/cm101967h doi: 10.1021/cm101967h
![]() |
[39] |
Yamada K, Tokoro H, Yoshikiyo M, et al. (2012) The phase transition of ɛ-InxFe2−xO3 nanomagnets with a large thermal hysteresis loop. J Appl Phys 111: 07B506. https://doi.org/10.1063/1.3672075 doi: 10.1063/1.3672075
![]() |
[40] |
Lindgren T, Wang H, Beermann N, et al. (2002) Aqueous photoelectrochemistry of hematite nanorod array. Sol Energy Mater Sol Cells 71: 231-243. https://doi.org/10.1016/S0927-0248(01)00062-9 doi: 10.1016/S0927-0248(01)00062-9
![]() |
[41] |
Li Y, Wang Z, Liu R (2021) Superparamagnetic-Fe2O3/Fe3O4 heterogeneous nanoparticles with enhanced biocompatibility. Nanomaterials 11: 834. https://doi.org/10.3390/nano11040834 doi: 10.3390/nano11040834
![]() |
[42] |
Husain H, Hariyanto B, Sulthonul M, et al. (2018) Local structure examination of mineral-derived Fe2O3 powder by Fe K-edge EXAFS and XANES. IOP Conference Series: Materials Science and Engineering 367: 012027. https:// doi:10.1088/1757-899X/367/1/012027. doi: 10.1088/1757-899X/367/1/012027
![]() |
[43] |
Demangeat E, Pédrot M, Dia A, et al. (2018) Colloidal and chemical stabilities of iron oxide nanoparticles in aqueous solutions: the interplay of structural, chemical and environmental drivers. Environ Sci Nano 5: 992-1001. https://doi.org/10.1039/C7EN01159H doi: 10.1039/C7EN01159H
![]() |
[44] |
Schaetz A, Reiser O, Stark W (2010) Nanoparticles as semi-heterogeneous catalyst supports. Chem Eur J 16: 8950-8967. https://doi.org/10.1002/chem.200903462 doi: 10.1002/chem.200903462
![]() |
[45] |
Vayssieres L, Beermann N, Lindquist SE, et al. (2001) Controlled aqueous chemical growth of oriented three-dimensional crystalline nanorod arrays: application to iron (Ⅲ) oxides. Chem Mater 13: 233-235. https://doi.org/10.1021/cm001202x doi: 10.1021/cm001202x
![]() |
[46] |
Beermann N, Vayssieres L, Lindquist SE, et al. (2000) Photoelectrochemical studies of oriented nanorod thin films of hematite. J Electrochem Soc 147: 2456-2461. https://doi.org/10.1149/1.1393553 doi: 10.1149/1.1393553
![]() |
[47] |
Vayssieres L, Sathe C, Butorin SM, et al. (2005) One-dimensional quantum-confinement effect in α-Fe2O3 ultrafine nanorod arrays. Adv Mater 17: 2320-2323. https://doi.org/10.1002/adma.200500992 doi: 10.1002/adma.200500992
![]() |
[48] |
Erlebach A, Kurland HD, Grabow J, et al. (2015) Structure evolution of nanoparticulate Fe2O3. Nanoscale 7: 2960-2969. https://doi.org/10.1039/C4NR06989G doi: 10.1039/C4NR06989G
![]() |
[49] |
Touileb K, Hedhibi A, Djoudjou R, et al. (2019) Mixing design for ATIG morphology and microstructure study of 316L stainless steel. Eng Technol Appl Sci Res 9: 3990-3997. https://doi.org/10.48084/etasr.2665 doi: 10.48084/etasr.2665
![]() |
[50] |
Chandrasekar G, Kailasanathan C, Vasundara M (2018) Investigation on un-peened and laser shock peened dissimilar weldments of Inconel 600 and AISI 316L fabricated using activated-TIG welding technique. J Manuf Process 35: 466-478. https://doi.org/10.1016/j.jmapro.2018.09.004 doi: 10.1016/j.jmapro.2018.09.004
![]() |
[51] |
Iglesias O, Labarta A (2001) Finite-size and surface effects in maghemite nanoparticles: Monte Carlo simulations. Phys Rev B 63: 184416. https://doi.org/10.1103/PhysRevB.63.184416 doi: 10.1103/PhysRevB.63.184416
![]() |
[52] |
Hoang VV, Khanh BTHL (2009) Static and thermodynamic properties of liquid and amorphous Fe2O3 nanoparticles. J Phys Condens Matter 21: 075103. https://doi.org/10.1088/0953-8984/21/7/075103 doi: 10.1088/0953-8984/21/7/075103
![]() |
[53] |
Zhonghua W, Lin G, Qianshu L, et al. (1999) Surface atomic structures of Fe2O3 nanoparticles coated with cetyltrimethyl ammonium bromide and sodium dodecyl benzene sulphonate: an extended x-ray absorption fine-structure study. J Phys Condens Matter 11: 4961-4970. https://doi.org/10.1088/0953-8984/11/26/301 doi: 10.1088/0953-8984/11/26/301
![]() |
[54] |
Chen LX, Liu T, Thurnauer MC, et al. (2002) Fe2O3 nanoparticle structures investigated by x-ray absorption near-edge structure, surface modifications, and model calculations. J Phys Chem B 106: 8539-8546. https://doi.org/10.1021/jp025544x doi: 10.1021/jp025544x
![]() |
[55] |
Khanh BTHL, Hoang VV, Zung H (2008) Structural properties of amorphous Fe2O3 nanoparticles. Eur Phys J D 49: 325-332. https://doi.org/10.1140/epjd/e2008-00168-1 doi: 10.1140/epjd/e2008-00168-1
![]() |
[56] |
Kelm K, Mader W (2005) Synthesis and structural analysis of ε-Fe2O3. Z Anorg Allg Chem 631: 2383-2389. https://doi.org/10.1002/zaac.200500283 doi: 10.1002/zaac.200500283
![]() |
[57] |
Lee S, Xu H (2016) Size-dependent phase map and phase transformation kinetics for nanometric iron (Ⅲ) oxides (γ → ε →α pathway). J Phys Chem 120: 13316-13322. https://doi.org/10.1021/acs.jpcc.6b05287 doi: 10.1021/acs.jpcc.6b05287
![]() |
[58] |
Belashchenko DK (1997) Computer simulation of the structure and properties of non-crystalline oxides. Russ Chem Rev 66: 733-762. https://doi.org/10.1070/RC1997v066n09ABEH000236 doi: 10.1070/RC1997v066n09ABEH000236
![]() |
[59] | Mahmoudi M, Stroeve P, Milani AS, et al. (2011) Superparamagnetic Iron Oxide Nanoparticles: Synthesis, Surface Engineering, Cytotoxicity and Biomedical Applications, New York: Nova Science Publishers. |
[60] |
Muñoz JLG, Romaguera A, Fauth F, et al. (2017) Unveiling a new high-temp erature ordered magnetic phase in ε-Fe2O3. Chem Mater 29: 9705-9713. https://doi.org/10.1021/acs.chemmater.7b03417 doi: 10.1021/acs.chemmater.7b03417
![]() |
[61] |
Dejoie C, Sciau P, Li W, et al. (2014) Learning from the past: rare ε-Fe2O3 in the ancient black-glazed Jian (Tenmoku) wares. Sci Rep 4: 4941. https://doi.org/10.1038/srep04941 doi: 10.1038/srep04941
![]() |
[62] |
Xu H, Lee S, Xu H (2017) Luogufe ngite: a new nano-mineral of Fe2O3 polymorph with giant coercive field. Am Mineral 102: 711-719. https://doi.org/10.2138/am-2017-5849 doi: 10.2138/am-2017-5849
![]() |
[63] |
Wang X, Zhou W (2002) Glass transition of microtome-sliced thin films. Macromolecules 35: 6747-6750. https://doi.org/10.1021/ma020291r doi: 10.1021/ma020291r
![]() |
[64] |
Schuller J, Melnichenko YB, Richert R, et al. (1994) Dielectric studies of the glass transition in porous media. Phys Rev Lett 73: 2224-2228. https://doi.org/10.1103/PhysRevLett.73.2224 doi: 10.1103/PhysRevLett.73.2224
![]() |
[65] |
Zhang Z, Zhao M, Jiang Q (2001) Glass transition thermodynamics of organic nanoparticles. Physica B 293: 232-236. https://doi.org/10.1016/S0921-4526(00)00564-0 doi: 10.1016/S0921-4526(00)00564-0
![]() |
[66] |
Alcoutlabi M, McKenna GB (2005) Effects of confinement on material behavior at the nanometre size scale. J Phys Condens Matter 17: 461-524. https://doi.org/10.1088/0953-8984/17/15/R01 doi: 10.1088/0953-8984/17/15/R01
![]() |
[67] |
Jackson CL, McKenna GB (1996) Vitrification and crystallization of organic liquids confined to nanoscale pores. Chem Mater 8: 2128-2137. https://doi.org/10.1021/cm9601188 doi: 10.1021/cm9601188
![]() |
[68] |
Dung NT (2020) Factors affecting the earth's surface on heterogeneous dynamics of CaSiO3 material. Mater Sci Eng B 260: 114648. https://doi.org/10.1016/j.mseb.2020.114648 doi: 10.1016/j.mseb.2020.114648
![]() |
[69] |
Tuan TQ, Dung NT (2019) Molecular dynamics studies the effects of the earth's surface depth on the heterogeneous kinetics of MgSiO3. Results Phys 15: 102671. https://doi.org/10.1016/j.rinp.2019.102671 doi: 10.1016/j.rinp.2019.102671
![]() |
[70] |
Dung NT, Cuong NC, Van DQ (2019) Molecular dynamics studies the effect of structure MgSiO3 bulk on formation process geology of the Earth. Int J Comput Mater Sci Eng 8: 1950011. https://doi.org/10.1142/S2047684119500118 doi: 10.1142/S2047684119500118
![]() |
[71] |
Zarringhalam M, Ahmadi-Danesh-Ashtiani H, Toghraie D, et al. (2019) The effects of suspending copper nanoparticles into argon base fluid inside a microchannel under boiling flow condition by using of molecular dynamic simulation. J Mol Liq 293: 111474. https://doi.org/10.1016/j.molliq.2019.111474 doi: 10.1016/j.molliq.2019.111474
![]() |
[72] |
Javadzadegan A, Joshaghani M, Moshfegh A, et al. (2020) Accurate meso-scale simulation of mixed convective heat transfer in a porous media for a vented square with hot elliptic obstacle: an LBM approach. Physica A 537: 122439. https://doi.org/10.1016/j.physa.2019.122439 doi: 10.1016/j.physa.2019.122439
![]() |
[73] |
Hadipeykani M, Aghadavoudi F, Toghraie D (2020) A molecular dynamics simulation of the glass transition temperature and volumetric thermal expansion coefficient of thermoset polymer based epoxy nanocomposite reinforced by CNT: a statistical study. Physica A 546: 123995. https://doi.org/10.1016/j.physa.2019.123995 doi: 10.1016/j.physa.2019.123995
![]() |
[74] |
Dung NT, Van CL, Tălu S (2022) Molecular dynamics simulation of bulk Cu material under various factors. Appl Sci 12: 4437. https://doi.org/10.3390/app12094437. doi: 10.3390/app12094437
![]() |
[75] |
Koparde VN, Cummings PT (2005) Molecular dynamics simulation of titanium dioxide nanoparticle sintering. J Phys Chem B 109: 24280-24287. https://doi.org/10.1021/jp054667p doi: 10.1021/jp054667p
![]() |
[76] |
Song P, Wen D (2010) Molecular dynamics simulation of the sintering of metallic nanoparticles, J Nanopart Res 12: 823-829. https://doi.org/10.1007/s11051-009-9718-7 doi: 10.1007/s11051-009-9718-7
![]() |
[77] |
Harris RA (2019) Chemotherapy drug temozolomide adsorbed onto iron-oxide (Fe3O4) nanoparticles as nanocarrier: A simulation study. J Mol Liq 288: 111084. https://doi.org/10.1016/j.molliq.2019.111084 doi: 10.1016/j.molliq.2019.111084
![]() |
[78] |
McWilliams RS, Dylan KS, Jon HE, et al. (2012) Phase transformations and metallization of magnesium oxide at high pressure and temperature. Science 338: 1330-1333. https://doi.org/10.1126/science.1229450 doi: 10.1126/science.1229450
![]() |
[79] |
Spaulding DK, McWilliams RS, Jeanloz R, et al. (2017) Evidence for a phase transition in silicate melt at extreme pressure and temperature conditions. Phys Rev Lett 108: 065701. https://doi.org/10.1103/PhysRevLett.108.065701 doi: 10.1103/PhysRevLett.108.065701
![]() |
[80] |
Sans JA, Monteseguro V, Garbarino G, et al. (2018) Stability and nature of the volume collapse of ε-Fe2O3 under extreme conditions. Nature communications 9: 4554. https://doi.org/10.1038/s41467-018-06966-9 doi: 10.1038/s41467-018-06966-9
![]() |
1. | Dung Nguyen Trong, Van Cao Long, Ştefan Ţălu, Umut Saraç, Phu Nguyen Dang, Kien Pham Huu, A New Study on the Structure, and Phase Transition Temperature of Bulk Silicate Materials by Simulation Method of Molecular Dynamics, 2022, 6, 2504-477X, 234, 10.3390/jcs6080234 | |
2. | Dung Nguyen Trong, Van Cao Long, Ştefan Ţălu, Effects of Number of Atoms and Doping Concentration on the Structure, Phase Transition, and Crystallization Process of Fe1-x-yNixCoy Alloy: A Molecular Dynamic Study, 2022, 12, 2076-3417, 8473, 10.3390/app12178473 | |
3. | Nguyen Quang Hoc, Dung Nguyen Trong, Nguyen Chinh Cuong, Bui Duc Tinh, Nguyen Duc Hien, Van Cao Long, Umut Saraç, Ştefan Ţălu, Determination of Young Modulus and Stress-Strain Curve for Metal Fe and Interstitial Alloy FeC, 2022, 6, 2504-477X, 250, 10.3390/jcs6090250 | |
4. | Dung Nguyen Trong, Van Cao Long, Ştefan Ţălu, New insights on the factors affecting the heterogeneous kinetics of bulk Fe2O3 on the Earth: A molecular dynamic simulation, 2022, 12, 2158-3226, 065016, 10.1063/5.0094033 |
T(K) | rij(Å) | gij(r) | 1 (nm) | E (eV) | ||||
Fe-Fe | Fe-O | O-O | Fe-Fe | Fe-O | O-O | |||
300 | 3.14 | 2.00 | 2.66 | 3.20 | 8.75 | 2.49 | 2.92 | −29.56 |
900 | 3.24 | 1.98 | 2.72 | 2.88 | 7.23 | 2.28 | 2.926 | −29.40 |
1300 | 3.32 | 1.98 | 2.78 | 2.83 | 6.53 | 2.30 | 2.932 | −29.29 |
1900 | 3.32 | 1.98 | 2.82 | 2.73 | 5.87 | 2.23 | 2.946 | −29.13 |
2300 | 3.32 | 1.96 | 2.84 | 2.72 | 5.44 | 2.20 | 2.936 | −29.01 |
3400 | 3.36 | 1.96 | 2.86 | 2.57 | 4.73 | 2.05 | 2.98 | −28.67 |
4500 | 3.40 | 1.92 | 2.94 | 2.40 | 4.56 | 1.88 | 3.05 | −28.24 |
5700 | 3.42 | 1.94 | 2.92 | 2.22 | 4.26 | 1.79 | 3.10 | −27.86 |
7000 | 3.46 | 1.88 | 2.96 | 2.09 | 4.18 | 1.71 | 3.19 | −27.41 |
previous results | 3.35 [33,34,53]; 3.11 [33,55,58]; 3.1 [52] |
1.91/1.95 [33,34,53]; 2.08 [54]; 1.925/1.945 [33,53]; 1.9 [33,42,52,55,58] |
2.91 [34,33,53]; 2.7 [33,42,52,55,58] |
T(K) | CN | |||
Fe-Fe | Fe-O | O-Fe | O-O | |
300 | 11.20 | 5.44 | 3.63 | 15.95 |
900 | 11.42 | 5.35 | 3.57 | 15.90 |
1300 | 11.40 | 5.33 | 3.55 | 15.82 |
1900 | 11.32 | 5.29 | 3.53 | 15.64 |
2300 | 11.67 | 5.60 | 3.73 | 15.93 |
3400 | 11.06 | 5.11 | 3.41 | 15.28 |
4500 | 11.35 | 5.34 | 3.56 | 14.37 |
5700 | 9.63 | 4.64 | 3.09 | 13.78 |
7000 | 8.63 | 4.12 | 2.75 | 3.55 |
Temperature (K) | FeO4 | FeO5 | FeO6 |
300 | 419 | 1627 | 1080 |
900 | 453 | 1647 | 1018 |
1300 | 540 | 1621 | 1018 |
1900 | 676 | 1640 | 850 |
2300 | 789 | 1552 | 833 |
3400 | 1175 | 1501 | 462 |
4500 | 1551 | 1225 | 209 |
5700 | 1634 | 1949 | 201 |
7000 | 1634 | 1049 | 201 |
Temperature (K) | Angular distribution | |
Fe-O-Fe | O-Fe-O | |
300 | 105 | 95 |
900 | 105 | 95 |
1300 | 100 | 95 |
1900 | 100 | 95 |
2300 | 100 | 95 |
3400 | 100 | 95 |
4500 | 95 | 95 |
5700 | 95 | 95 |
7000 | 95 | 95 |
T(K) | rij(Å) | gij(r) | 1 (nm) | E (eV) | ||||
Fe-Fe | Fe-O | O-O | Fe-Fe | Fe-O | O-O | |||
300 | 3.14 | 2.00 | 2.66 | 3.20 | 8.75 | 2.49 | 2.92 | −29.56 |
900 | 3.24 | 1.98 | 2.72 | 2.88 | 7.23 | 2.28 | 2.926 | −29.40 |
1300 | 3.32 | 1.98 | 2.78 | 2.83 | 6.53 | 2.30 | 2.932 | −29.29 |
1900 | 3.32 | 1.98 | 2.82 | 2.73 | 5.87 | 2.23 | 2.946 | −29.13 |
2300 | 3.32 | 1.96 | 2.84 | 2.72 | 5.44 | 2.20 | 2.936 | −29.01 |
3400 | 3.36 | 1.96 | 2.86 | 2.57 | 4.73 | 2.05 | 2.98 | −28.67 |
4500 | 3.40 | 1.92 | 2.94 | 2.40 | 4.56 | 1.88 | 3.05 | −28.24 |
5700 | 3.42 | 1.94 | 2.92 | 2.22 | 4.26 | 1.79 | 3.10 | −27.86 |
7000 | 3.46 | 1.88 | 2.96 | 2.09 | 4.18 | 1.71 | 3.19 | −27.41 |
previous results | 3.35 [33,34,53]; 3.11 [33,55,58]; 3.1 [52] |
1.91/1.95 [33,34,53]; 2.08 [54]; 1.925/1.945 [33,53]; 1.9 [33,42,52,55,58] |
2.91 [34,33,53]; 2.7 [33,42,52,55,58] |
T(K) | CN | |||
Fe-Fe | Fe-O | O-Fe | O-O | |
300 | 11.20 | 5.44 | 3.63 | 15.95 |
900 | 11.42 | 5.35 | 3.57 | 15.90 |
1300 | 11.40 | 5.33 | 3.55 | 15.82 |
1900 | 11.32 | 5.29 | 3.53 | 15.64 |
2300 | 11.67 | 5.60 | 3.73 | 15.93 |
3400 | 11.06 | 5.11 | 3.41 | 15.28 |
4500 | 11.35 | 5.34 | 3.56 | 14.37 |
5700 | 9.63 | 4.64 | 3.09 | 13.78 |
7000 | 8.63 | 4.12 | 2.75 | 3.55 |
Temperature (K) | FeO4 | FeO5 | FeO6 |
300 | 419 | 1627 | 1080 |
900 | 453 | 1647 | 1018 |
1300 | 540 | 1621 | 1018 |
1900 | 676 | 1640 | 850 |
2300 | 789 | 1552 | 833 |
3400 | 1175 | 1501 | 462 |
4500 | 1551 | 1225 | 209 |
5700 | 1634 | 1949 | 201 |
7000 | 1634 | 1049 | 201 |
Temperature (K) | Angular distribution | |
Fe-O-Fe | O-Fe-O | |
300 | 105 | 95 |
900 | 105 | 95 |
1300 | 100 | 95 |
1900 | 100 | 95 |
2300 | 100 | 95 |
3400 | 100 | 95 |
4500 | 95 | 95 |
5700 | 95 | 95 |
7000 | 95 | 95 |