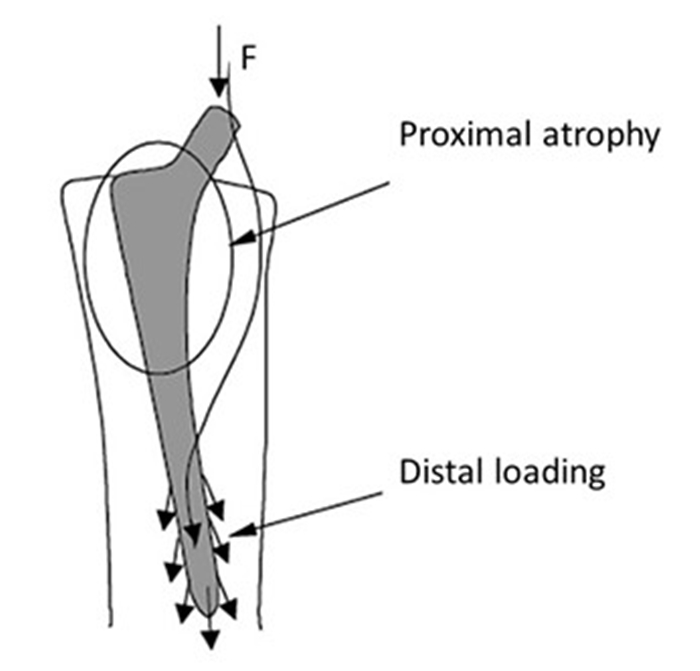
Arthroplasty is generally used to treat advanced osteoarthritis or other degenerative joint diseases. However, it can also be considered in younger patients with severe joint damage that seriously limits their function and quality of life. Young patients are at risk of aseptic mobilization and bone resorption due to the uneven distribution of stress on the contact surface between the prosthesis and the femur that generates the stress-shielding phenomenon. To overcome this occurrence, it is necessary to use biocompatible materials with a stiffness that is similar to bone. Composite hip prostheses, consisting of continuous fiber-reinforced polymers, play a progressively key role in the development of prosthetic devices. Composite materials can be designed more carefully than monolithic stems (single-phase materials such as metals), allowing for the development of more effective tissue substitutes. Our purpose of this review was to analyze the state of the art in the use of carbon femoral prostheses. In particular, the major mechanical properties of reinforcement (fiber) and matrix were outlined with their applications in the prosthetic field.
Citation: Mario Ceddia, Bartolomeo Trentadue. A review of carbon fiber-reinforced polymer composite used to solve stress shielding in total hip replacement[J]. AIMS Materials Science, 2024, 11(3): 449-462. doi: 10.3934/matersci.2024023
[1] | Kator Jeff Jomboh, Adele Dzikwi Garkida, Emmanuel Majiyebo Alemaka, Mohammed Kabir Yakubu, Vershima Cephas Alkali, Wilson Uzochukwu Eze, Nuhu Lawal . Properties and applications of natural, synthetic and hybrid fiber reinforced polymer composite: A review. AIMS Materials Science, 2024, 11(4): 774-801. doi: 10.3934/matersci.2024038 |
[2] | Araya Abera Betelie, Yonas Tsegaye Megera, Daniel Telahun Redda, Antony Sinclair . Experimental investigation of fracture toughness for treated sisal epoxy composite. AIMS Materials Science, 2018, 5(1): 93-104. doi: 10.3934/matersci.2018.1.93 |
[3] | Yong X. Gan . A review of electrohydrodynamic casting energy conversion polymer composites. AIMS Materials Science, 2018, 5(2): 206-225. doi: 10.3934/matersci.2018.2.206 |
[4] | Harikrishnan Pulikkalparambil, Jyotishkumar Parameswaranpillai, Jinu Jacob George, Krittirash Yorseng, Suchart Siengchin . Physical and thermo-mechanical properties of bionano reinforced poly(butylene adipate-co-terephthalate), hemp/CNF/Ag-NPs composites. AIMS Materials Science, 2017, 4(3): 814-831. doi: 10.3934/matersci.2017.3.814 |
[5] | Yohannes Regassa, Hirpa G. Lemu, Belete Sirhabizu . Investigation of spider web oriented composite fabrics burst strength. AIMS Materials Science, 2021, 8(4): 622-639. doi: 10.3934/matersci.2021038 |
[6] | Suman Chhetri, Pranab Samanta, Naresh Chandra Murmu, Suneel Kumar Srivastava, Tapas Kuila . Electromagnetic interference shielding and thermal properties of non-covalently functionalized reduced graphene oxide/epoxy composites. AIMS Materials Science, 2017, 4(1): 61-74. doi: 10.3934/matersci.2017.1.61 |
[7] | Gregory N. Haidemenopoulos, Kostantinos N. Malizos, Anna D. Zervaki, and Kostantinos Bargiotas . Human bone ingrowth into a porous tantalum acetabular cup. AIMS Materials Science, 2017, 4(6): 1220-1230. doi: 10.3934/matersci.2017.6.1220 |
[8] | Raffaele Conte, Anna Di Salle, Francesco Riccitiello, Orsolina Petillo, Gianfranco Peluso, Anna Calarco . Biodegradable polymers in dental tissue engineering and regeneration. AIMS Materials Science, 2018, 5(6): 1073-1101. doi: 10.3934/matersci.2018.6.1073 |
[9] | Mohammed Y. Abdellah, Hamzah Alharthi, Mohamed K. Hassan, Ahmed F. Mohamed . Effect of specimen size on natural vibration of open hole copper/glass-reinforced epoxy laminate composites. AIMS Materials Science, 2020, 7(4): 499-517. doi: 10.3934/matersci.2020.4.499 |
[10] | Mnvrl Kumar, R. Ramakrishnan, Alnura Omarbekova, Santhosh Kumar. R . Experimental characterization of mechanical properties and microstructure study of polycarbonate (PC) reinforced acrylonitrile-butadiene-styrene (ABS) composite with varying PC loadings. AIMS Materials Science, 2021, 8(1): 18-28. doi: 10.3934/matersci.2021002 |
Arthroplasty is generally used to treat advanced osteoarthritis or other degenerative joint diseases. However, it can also be considered in younger patients with severe joint damage that seriously limits their function and quality of life. Young patients are at risk of aseptic mobilization and bone resorption due to the uneven distribution of stress on the contact surface between the prosthesis and the femur that generates the stress-shielding phenomenon. To overcome this occurrence, it is necessary to use biocompatible materials with a stiffness that is similar to bone. Composite hip prostheses, consisting of continuous fiber-reinforced polymers, play a progressively key role in the development of prosthetic devices. Composite materials can be designed more carefully than monolithic stems (single-phase materials such as metals), allowing for the development of more effective tissue substitutes. Our purpose of this review was to analyze the state of the art in the use of carbon femoral prostheses. In particular, the major mechanical properties of reinforcement (fiber) and matrix were outlined with their applications in the prosthetic field.
Total hip replacement is a surgical procedure that replaces a damaged hip joint with a prosthetic implant called hip prosthesis. The presence of an artificial joint, such as that used in total hip replacements, can alter the normal process of bone remodeling through a phenomenon known as the 'stress-shielding effect'. This phenomenon occurs due to differences in mechanical properties between the prosthesis material and the surrounding bone, leading to a non-physiological distribution of load on the bone tissue. When a prosthesis is inserted into bone, differences in stiffness between the prosthesis material (usually metal) and the natural bone can cause a reduction in the load transferred to the surrounding bone [1]. Under normal conditions, the bone responds to the applied load through a remodeling process, in which the bone tissue adapts to the force exerted on it. However, with the presence of a prosthesis that absorbs part of the load, the bone near the prosthesis may be subjected to less mechanical stress than non-prosthetic areas. This reduced stress may lead to a decrease in osteoblastic activity (cells responsible for bone formation) and an increase in osteoclastic activity (cells responsible for bone resorption), causing an imbalance in the bone remodelling process. As a result, a loss of bone density may occur. It is important to achieve proximal fixation to increase loading of the area near the epiphysis and thereby reduce the potential for bone atrophy. If sufficient fit cannot be achieved, stress shielding will occur. Loads acting on the stem are transferred directly to the remote area. For cementless prostheses, the degree of adhesion that can be achieved at the interface between stem and bone tissue is a key parameter for the success of the prosthesis. Looking at Figure 1, insertion of the prosthesis results in reduced stresses on the proximal zone leading to proximal atrophy, while the distal zone is subjected to an increased stress [2,3,4,5].
Stress shielding is characterized by its intensity levels (1st, 2nd, and 3rd), which signify the extent of change in load transmission between the implant and the adjacent bone. In the 1st level, there is a minor physiological transfer of load from the implant to the bone. This can be effectively controlled and supervised. The 2nd level indicates a further reduction of the transmitted load. In the 3rd level, there is a significant reduction of mechanical stimulation on the surrounding bone. This grade is associated with higher risks of complications such as osteolysis (reduction in bone density) and implant failure. There are currently several solutions to the stress shielding phenomenon, including redesigning the prosthesis. In fact, prostheses with short stems have been developed to better transfer load to the femoral metaphysis, thus reducing this adverse effect [6]. The choice of fixation method affects the stress distribution in the surrounding bone [7]. Developing stiffness functionally graded materials and prostheses made of specific alloys, stress shielding effects can be reduced and osseointegration can be improved [8,9]. Femoral components are typically made from Co-Cr-Mo or Co-Ni-Cr-Mo alloys or titanium alloys. The femoral head (the articulating portion of the femoral component) is made of a very smooth cobalt-chromium alloy or ceramic (such as aluminum oxide). An acetabular shell is when the stem and ball are made of two different materials. For example, a hip replacement with a titanium femoral stem has a cobalt-chromium femoral head. Additionally, for general acetabular replacement, the UHMWPE cup can be embedded directly into the pelvis or be part of a modular arrangement in which the cup is placed in a metal tray. Table 1 shows the material combinations of hip components between the femoral head and acetabular cup (plastic lining) [6,7,8,9,10,11,12].
Femoral head | Acetabulum shell | Results |
Co-Cr-Mo | Co-Cr-Mo | Early high loosening rate and limited use |
Co-Cr-Mo | UHMWPE | Widely employed; Low wear |
Aluminia/zirconia | UHMWPE | Very low wear rate |
Aluminia | Aluminia | Minimum wear rate |
Ti6Al4V | UHMWPE | Reports of high UHMWPE wear due to titanium surface breakage |
In a study conducted by Solarino et al. [12], it was found that utilizing the CoC coupling joint in total hip arthroplasties for young patients yields positive long-term outcomes, including minimal wear and no negative effects from the ceramic material. Over the years, various materials have been used to produce these implants, including carbon fiber. This material is known for its high strength-to-weight ratio, low thermal expansion and biocompatibility. The incorporation of carbon fiber into prosthetic structures has generated significant interest because of its potential to closely mimic the mechanical properties of human bone. The primary consideration with these implants is the elastic modulus, which should ideally match that of the proximal femur to prevent stress shielding and promote normal load transfer. Composites, such as those used in carbon fiber hip stems, play a key role in achieving this mechanical compatibility. The finite element (FE) model used to evaluate the mechanical performance of the carbon fiber-based hip stem showed lower stiffness than standard metal hip replacements. Showing a more bone-like response to stresses and physiological loads [13,14]. Additionally, the orientation of the fibers within the composite is a critical factor. When the fibers are aligned in the same direction, the elastic modulus can be adjusted so that they are similar to fibers themselves, which becomes more pronounced with a reduction in the matrix component. Using the unique properties of carbon fiber composites in hip prosthetic design, engineers and surgeons aim to improve patient outcomes through implants that offer better compatibility with the body's natural biomechanics. Our aim is to investigate the properties, technical data and application of carbon fiber composites in total hip arthroplasty. In particular, a comprehensive search on PubMed was conducted using "carbon fiber-reinforced in total hip replacement" as a keyword to search for and identify the most relevant articles. The search was conducted by considering the period between 2008-2024 because very few applications of carbon fiber in total hip arthroplasty were conducted prior to 2008. The search was also extended by examining Google Schoolar for the period between 2014-2024. In this way, only the most recent articles from the last 10 years were uniquely considered. As the available literature evaluating the performance of carbon fiber reinforced-polyetheretherketone (CFR-PEEK) as an implant material for arthroplasty devices is limited, in fact, in this review about 34 articles were considered in total. However, the studies available strongly support that carbon fiber composite is a promising and suitable material for orthopedic implants due to its biocompatibility, material characteristics, and mechanical durability. Further studies should continue to investigate the potential benefits of CFR-PEEK.
In many high-tech applications, such as aerospace, marine, or bioengineering, materials with specific and unusual properties are required [15]. Generally, among monolithic materials, the most resistant are the densest and, therefore, the heaviest. The combination of different properties such as lightness and resistance in a single material and extending the validity intervals has been achieved with composite materials. In principle, a composite material is a multiphase material having two or more constituent phases in which the overall mechanical properties are the combination of those the mechanical properties of the individual phases. Figure 2 shows the stress-strain graph of the composite material, which results from the combination of fiber and polymer behaviors [16,17]. Generally, composite materials consist of only two phases; a matrix which is a continuous phase and a dispersed phase.
From a technological point of view, the most important composite materials are those in which the dispersed phase is in the form of fibers. In general, fiber-reinforced composites are divided according to the length of the fibers, although the mechanical properties depend not only on the mechanical properties of the fibers, but also on the level of stress that the matrix can transmit to them [18,19,20]. When a load is applied, stresses are created at the fiber-matrix interface. Therefore, to ensure reinforcement and effective mechanical strength, the fiber length must be greater than a certain dimension, called critical length (lc), Figure 3.
This length depends on the diameter of the fiber (d), the breaking stress of the interface with the matrix , and the shear yield strength of the matrix , Eq 1.
(1) |
As the length of the fiber increases, the reinforcement effect becomes more efficient. Therefore, according to the critical length, it is possible to classify the fibers into short fibers if l < lc or long fibers if l > lc [20,21]. From a mechanical strength perspective, long fibers have a tensile strength σ₁ of around 2000 MPa compared to σ₂ of about 170 MPa for short fibers as observed in Figure 4, which shows a comparison between the two types, with long ones on the left and short fibers on the right [20,21].
Carbon fibers can be classified according to their carbon source. The most common types are polyacrylonitrile-based carbon fibers (PAN) and tar-based carbon fibers. Other types include vaporization-grown fibers and carbon nanotubes. In addition, carbon fibers can be classified based on their mechanical properties, such as tensile strength, Young's modulus and strain at break. From the point of view of mechanical strength, carbon fiber has a higher tensile strength than comparable metal materials, with an ultimate strength of 3450 MPa [22,23,24]. The lightness of carbon fiber contributes to the increase in the strength-to-weight ratio. In fact, they have a density of 1.6-2.2 g/cm3 [22,23,24] close to that of bone which is about 2.0 g/cm3 [24]. Carbon fibers, due to their small diameter, can be molded to fit complex curved surfaces with multiple variations [25]. Individually, carbon fiber has a graphitic structure with strong crystalline covalent bonds along the direction of the longitudinal axis of the fiber itself and weak cross-links. This feature mainly imparts anisotropic behavior [26]. Therefore, to increase the mechanical properties of the fiber, the graphite crystal can be oriented along the main direction where the greatest stress occurs through heat treatment and stretching processes [27,28,29,30]. The arrangement and orientation of the carbon fibers and the ratio of carbon fiber (CF) to polymer matrix further increase the strength of carbon fiber devices. Table 2 shows the major mechanical properties of carbon fiber compared to steel wire [31].
Material | Density (g/cm3) | Tensile strenght (GPa) | Specific strenght (GPa) | Modulus of elasticity (GPa) | Specific modulus (GPa) |
Carbon fiber | 1.6-2.2 | 1.5-5.65 | 0.70-3.12 | 228-790 | 106-407 |
Stell wire | 7.9 | 2.39 | 0.30 | 210 | 26.6 |
The inert nature of carbon fiber makes it resistant to moisture and chemicals at room temperature. Although at temperatures between 300 and 400 ℃, the presence of impurities increases the oxidation of the fiber [31].
The biocompatibility properties of carbon fiber include the ability to stimulate the growth of bone tissue, to osseointegrate with living bone, and to remove excess electrons through electrochemical gradients [31,32,33,34]. In addition, carbon fibers have electrical properties that can influence cell movement and polymerization of actin filaments, thus contributing to biocompatibility. Some biocompatibility features were investigated by Rajzer et al. [35], in which on in vitro and in vivo analysis of porous carbon and hydroxyapatite (HAP) modified carbon fibers, was conducted through culturing human bone cells in contact with both types of carbon fibers. This work emphasized the growth-stimulating effect of connective tissue and showed that in the case of hydroxyapatite-modified fibers, the inflammatory reaction time was shorter than in the case of traditional fibers. Another study conducted by Petersen et al. [36] highlighted how carbon fibers can stimulate the growth of bone cells through the chemotactic influence of free radicals, improving the osseointegration process compared to titanium alloys.
In the case of fiber-reinforced composite materials, the matrix performs various functions. It primarily serves to link fibers together and is a means of transferring externally applied stress and distributing it across the fibers. The second function is to protect each fiber at surface damage or chemical reactions with the environment [37,38,39]. Finally, the matrix separates the fibers, making it difficult for brittle cracks to propagate between the fibers, which can lead to composite failure. Consequently, it is important that the interfacial adhesive bond is very high to avoid the fiber pull-out phenomenon. It is, therefore, no coincidence that the failure stress of a composite material depends largely on the characteristics of the fiber-matrix connection. Typically, polymer resins are used, which can be classified into epoxy resins used in aerospace industries as they have better mechanical properties and greater resistance to moisture. For applications at high temperatures, polyimide resins are used as they have a limit of use of about 230 ℃. Finally, there are high-temperature-resistant thermoplastic resins such as polyetheretherketone (PEEK), which are used in aerospace and medicine [40,41]. In particular, PEEK, as said in some in vitro and in vivo studies [41,42,43,44], has shown excellent biocompatibility properties, minimizing the cellular reaction. The mechanical properties of thermoplastics depend on the type of polymer used. For example, polycarbonate (PC) has high impact strength and good fatigue strength, while polypropylene (PP) has good tensile and flexural strength. High-density polyethylene (HDPE) has good impact and fatigue strength, but low tensile strength. Polystyrene (PS) has good compressive and flexural strength, but minimal impact strength. When it comes to thermosetting resins, epoxy resin is known for its high tensile strength, compressive strength, and flexural strength as well as its high impact strength. Phenolic resins are prized for their high temperature and flame resistance, but they have lower mechanical strength than epoxy. Polyester resins are mainly used for low-cost, low-strength applications. In general, thermoset polymers have higher mechanical strength than thermoplastics, but are less ductile and less resistant to impact Table 3 [45].
Material | Density (mg/m3) | Young's modulus (GPa) | Breaking stress (MPa) |
PE | 0.952-0.965 | 0.17-0.28 | 8.3-31.0 |
PS | 1.04-1.05 | 2.8-4.1 | 48.3-72.4 |
PC | 1.20 | 2.38 | 65.8-72.4 |
PP | 0.90-0.91 | 1.14-1.55 | 31.0-41.4 |
PEEK | 1.3 | 3.6 | 90-100 |
For THR, stainless steel, Co-Cr, and Ti alloys for the femoral stem and neck, and Co-Cr alloys or ceramics such as aluminum and zirconium for the head or ball are commonly used. We showed that CF/PEEK composites can provide a more uniform load transfer from the implant to the bone, thereby reducing the stress shielding effect. The mechanical properties of these materials vary depending on the orientation of the carbon fibers and their total share in the composite (with strength from 70 to 1900 MPa and stiffness from 10 to 100 GPa). Moreover, CF/PEEK composites have demonstrated excellent biocompatibility, environmental stability, and chemical resistance [46,47]. Nakahara et al. [48] studied the radiographic and histological results of uncemented and cemented CF/PEEK hip prosthesis implantation in a sheep bone. After 52 weeks, five uncemented and four cemented cases showed resistance to first-degree stresses, and two cemented cases showed resistance to second-degree stresses, but no third-degree stress shielding phenomenon was observed in any of the cases. In an in vivo study conducted by Hacking et al. [49], the tissue response around a hydroxyapatite-coated composite femoral implant was evaluated. Three materials were examined: Hydroxyapatite coating, carbon fiber composite, and a crystalline hydroxyapatite particle composite layer. All materials showed a certain degree of bone apposition. Furthermore, no obvious adverse tissue reactions or signs of bone resorption were observed. In an in vitro study conducted by Scotchford et al. [50], the attachment proliferation of human osteoblast-like cells and activation of macrophages in response to this composite material was studied. The authors demonstrated that the carbon fiber-based composite material showed excellent biocompatibility in vitro by exhibiting Ti6Al4V-like attachment and proliferation of osteoblasts.
It is important to highlight that these materials can be produced with different carbon fiber arrangements within the PEEK matrix, offering the ability to adjust the elastic modulus along the stem to reduce the stress shield effect.
In a finite element analysis (FEA) study conducted by Ayham Darwich et al. [51], the effect of stress shielding on hip implant stems coated with composite (carbon/PEEK) and polymer (PEEK) coating materials was evaluated. The results of the study showed that the use of coating materials such as PEEK and carbon/PEEK composite on a titanium alloy hip implant stem can reduce the stress shielding effect by helping to distribute the applied load and transfer it to the bone. In particular, it was found that the configuration material coating (carbon/PEEK composite) appeared to perform best in the femur, effectively reducing stress shielding and extending system life of femoral stem. In another FEA study by Caouette et al. [52] showed the performance of a biomimetic hip arthroplasty stem made of a carbon fiber composite coated with hydroxyapatite. Various static loading conditions were considered, stresses were screened and micromovements of the bone-implant interface were assessed. The composite rod allowed for reduced stress shielding compared to the traditional titanium rod, with slightly greater micromovements than titanium, but still below the critical threshold (40 mm) on most of the hydroxyapatite (HA) coated surface. A study conducted by Sridhar et al. [53] showed that the tensile and flexural modulus of CF/PEEK composites were very similar to those of human cortical bone. This similarity suggests that these composites could potentially reduce the effect of stress shielding. Ceddia et al. [54], using the finite element method (FEM), investigated the application of a topological optimization process for femoral stem design, which includes a modification of geometry as a function of Von Mises stress distribution and a variation of material, opting for a composite material, Figure 5.
Topological optimization solved the problem of stress shielding, with the reduction of the Von Mises stress from 987 to 810 MPa in the titanium alloy femoral stem and to 509 MPa in the composite femoral stem. The results of the study suggested that the use of carbon-based composite materials may be an effective solution to reduce stress shielding and improve bone integration in femoral prostheses.
In another study conducted by Tavakkoli et al. [55], a mechanical-biochemical model was used to compare the behavior of a biomimetic polymer composite hip stem with that of a metal rod. The results showed that the biomimetic polymer composite rod significantly reduced the stress-shielding effect compared to the metal rod. In fact, there was a bone loss of 9% with the use of a composite stem, compared to 27% (CoCrMo) and 21% (Ti6Al4V). In particular, the biomimetic polymer composite rod showed a greater load distribution to the surrounding bone than the metal rod.
In a prospective clinical trial conducted by Adam et al. [56] to evaluate the efficacy of carbon fiber femoral prostheses, a high percentage of early loosening was observed. The authors emphasized the importance of effective bone growth on the surface to ensure the success of carbon fiber hip replacement. While in a randomly controlled trial [57], with a median follow-up of ten years on the use of carbon-metal fiber-composite femoral stems in hip replacements an increase in proximal bone density and a decrease in distal bone density were shown, saying an improvement in proximal load transfer. Campbell et al. [58] conducted a series of studies to evaluate the mechanical properties and long-term durability of carbon fiber femoral stems. Static test results showed that the composite stems have properties comparable to human femur cortical bone in terms of elastic modulus flexural strength and compressive strength. Specifically, the modulus of stiffness evaluated in the carbon fiber prosthesis was about 12.2 GPa compared with 7.0 GPa for the cortical bone. While the ultimate strength was 155 MPa for the stem and 175 MPa for the cortical bone. These similar values of mechanical behavior suggest reduced stress shielding and better load distribution on the bone. The weak interfacial adhesion caused by the poor wettability of CF and inert PEEK hinders the great application potential of CF/PEEK composites. In an experimental study by Lyu et al. [59], the interface between CF and PEEK was modified through a coating that increased their surface roughness. In this way, the rougher surfaces showed increased surface energy by improving physical adhesion. In addition, the prediction of damage in a carbon fiber composite prosthesis is a complex challenge as it requires accurate analysis. As composite femoral prostheses are thick structures that can contain more than 100 layers of composite materials, they make design and stress analysis at the single layer level very complex and computationally intensive [60].
Carbon fiber is a material with a unique combination of tensile strength, lightness, and flexibility making it ideal for a variety of applications. Compared with similar metal materials, it has excellent tensile strength and is lightweight, with an excellent strength-to-weight ratio. Carbon fiber stimulates bone cell growth and may be a promising option to improve proximal hip load transfer and reduce stress shielding during primary hip replacement surgery. The use of carbon fiber and metal composite femoral stems has shown long-term results of increased proximal bone density and decreased distal bone density, showing improved proximal load transfer. More research is needed to confirm the use of these materials in prosthetic rehabilitation and extend their use to increasingly broad areas of prosthetics.
The authors declare that they have not used Artificial Intelligence (AI) tools in the creation of this article.
The authors declare no conflict of interest.
[1] |
Savio D, Bagno A (2022) When the total hip replacement fails: A review on the stress-shielding effect. Processes 10: 612. https://doi.org/10.3390/pr10030612 doi: 10.3390/pr10030612
![]() |
[2] |
Brodt S, Matziolis G, Buckwitz B, et al. (2020) Long-term follow-up of bone remodelling after cementless hip arthroplasty using different stems. Sci Rep 10: 10143. https://doi.org/10.1038/s41598-020-67189-x doi: 10.1038/s41598-020-67189-x
![]() |
[3] |
Koh Y, Park K, Lee J, et al. (2019) Total knee arthroplasty application of polyetheretherketone and carbon-fiber-reinforced polyetheretherketone: A review. Mater Sci Eng C 100: 70–81. https://doi.org/10.1016/j.msec.2019.02.082 doi: 10.1016/j.msec.2019.02.082
![]() |
[4] |
Kheir M, Drayer N, Chen A (2020) A update on cementless femoral fixation in total hip arthroplasty. J Bone Joint Surg Am 102: 1646–1661. https://doi.org/10.2106/JBJS.19.01397 doi: 10.2106/JBJS.19.01397
![]() |
[5] |
Solórzano W, Ojeda C, Lantada A (2020) Biomechanical study of proximal femur for designing stems for total hip replacement. Appl Sci 10: 4208. https://doi.org/10.3390/app10124208 doi: 10.3390/app10124208
![]() |
[6] |
Naghavi S, Lin C, Sun C, et al. (2022) Stress shielding and bone resorption of press-fit polyether-ether-ketone (PEEK) hip prosthesis: A sawbone model study. Polymers 14: 4600. https://doi.org/10.3390/polym14214600 doi: 10.3390/polym14214600
![]() |
[7] |
Ait Moussa A, Fischer J, Yadav R, et al. (2017) Minimizing stress shielding and cement damage in cemented femoral component of a hip prosthesis through computational design optimization. Adv Orthop 2017: 8437956. https://doi.org/10.1155/2017/8437956 doi: 10.1155/2017/8437956
![]() |
[8] |
Niinomi M (2008) Mechanical biocompatibilities of titanium alloys for biomedical applications. J Mech Behav Biomed Mater 1: 30–42. https://doi.org/10.1016/j.jmbbm.2007.07.001 doi: 10.1016/j.jmbbm.2007.07.001
![]() |
[9] |
Savin L, Pinteala T, Mihai D, et al. (2023) Updates on biomaterials used in total hip arthroplasty (THA). Polymers 15: 3278. https://doi.org/10.3390/polym15153278 doi: 10.3390/polym15153278
![]() |
[10] | Bhaskar B, Arun S (2016) Biomaterials in total hip joint replacements: The evolution of basic concepts, trends, and current limitations—A review, In: Kothiyal GP, Srinivasan A, Trends in Biomaterials, New York: Jenny Stanford Publishing. https://doi.org/10.1201/b19906 |
[11] |
Pezzotti G, Kengo Y (2014) Artificial hip joints: The biomaterials challenge. J Mech Behav Biomed Mater 31: 3–20. https://doi.org/10.1016/j.jmbbm.2013.06.001 doi: 10.1016/j.jmbbm.2013.06.001
![]() |
[12] |
Solarino G, Zagra L, Piazzolla A, et al. (2019) Results of 200 consecutive ceramic-on-ceramic cementless hip arthroplasties in patients up to 50 years of age: A 5–24 years of follow-up study. J Arthroplasty 34: S232–S237. https://doi.org/10.1016/j.arth.2019.01.057 doi: 10.1016/j.arth.2019.01.057
![]() |
[13] |
Zhu W, Fu H, Li F, et al. (2022) Optimization of CFRP drilling process: A review. Int J Adv Manuf Technol 123: 1403–1432. https://doi.org/10.1007/s00170-022-10112-7 doi: 10.1007/s00170-022-10112-7
![]() |
[14] |
Theivendran K, Arshad F, Hanif U, et al. (2021) Carbon fibre reinforced PEEK versus traditional metallic implants for orthopaedic trauma surgery: A systematic review. J Clin Orthop Trauma 23: 101674. https://doi.org/10.1016/j.jcot.2021.101674 doi: 10.1016/j.jcot.2021.101674
![]() |
[15] | Kumar N, Gangwar A, Devi K (2018) Carbon fibers in biomedical applications, In: Khanna R, Cayumil R, Recent Developments in the Field of Carbon Fibers, London: IntechOpen Limited, 6: 83–102. http://dx.doi.org/10.5772/intechopen.75826 |
[16] |
Sun G, Tong S, Chen D, et al. (2018) Mechanical properties of hybrid composites reinforced by carbon and basalt fibers. Int J Mech Sci 148: 636–651. http://dx.doi.org/10.1016/j.ijmecsci.2018.08.007 doi: 10.1016/j.ijmecsci.2018.08.007
![]() |
[17] |
Naranjo-Lozada J, Ahuett-Garza H, Orta-Castañ ón P, et al. (2019) Tensile properties and failure behavior of chopped and continuous carbon fiber composites produced by additive manufacturing. Addit Manuf 26: 227–241. http://dx.doi.org/10.1016/j.addma.2018.12.020 doi: 10.1016/j.addma.2018.12.020
![]() |
[18] |
Elanchezhian C, Ramnath B, Ramakrishnan G, et al. (2018) Review on mechanical properties of natural fiber composites. Mater Today Proc 5: 1785–1790. http://dx.doi.org/10.1016/j.matpr.2017.11.276 doi: 10.1016/j.matpr.2017.11.276
![]() |
[19] |
Jebaraj J, Ramadoss R, Gunasekaran K, et al. (2021) Studies on mechanical properties and characterization of carbon fiber reinforced hybrid composite for aerospace application. Mater Today Proc 47: 4438–4443. http://dx.doi.org/10.1016/j.matpr.2021.05.304 doi: 10.1016/j.matpr.2021.05.304
![]() |
[20] | Callister W, Rethwisch D (2020) Callister's Materials Science and Engineering, Hoboken: John Wiley & Sons. |
[21] |
Li H, Shi J, Zhao J, et al. (2021) Tensile behavior analysis of CFRP (carbon‐fiber‐reinforced‐polymer)–titanium joint under preload. Polym Compos 44: 2205–2221. https://doi.org/10.1002/pc.27237 doi: 10.1002/pc.27237
![]() |
[22] |
Pathak A, Garg H, Subhedar K, et al. (2021) Significance of carbon fiber orientation on thermomechanical properties of carbon fiber reinforced epoxy composite. Fibers Polym 22: 1923–1933. https://doi.org/10.1007/s12221-021-0703-9 doi: 10.1007/s12221-021-0703-9
![]() |
[23] |
Jiang D, Smith D (2017) Anisotropic mechanical properties of oriented carbon fiber filled polymer composites produced with fused filament fabrication. Addit Manuf 18: 84–94. http://dx.doi.org/10.1016/j.addma.2017.08.006 doi: 10.1016/j.addma.2017.08.006
![]() |
[24] |
Park J, Hwang T, Kim H, et al. (2006) Experimental and numerical study of the electrical anisotropy in unidirectional carbon-fiber-reinforced polymer composites. Smart Mater Struct 16: 57. http://dx.doi.org/10.1088/0964-1726/16/1/006 doi: 10.1088/0964-1726/16/1/006
![]() |
[25] |
Hak D, Mauffrey C, Seligson D, et al. (2014) Use of carbon-fiber-reinforced composite implants in orthopedic surgery. Orthopedics 37: 825–830. https://doi.org/10.3928/01477447-20141124-05 doi: 10.3928/01477447-20141124-05
![]() |
[26] |
Asgari S, Hamouda A, Mansor S, et al. (2005) Natural fiber reinforced composites for femoral component of total hip arthroplasty. J Mech Med Biol 5: 443–454. http://dx.doi.org/10.1142/S0219519405001576 doi: 10.1142/S0219519405001576
![]() |
[27] |
Shao Y, Matsushita M, Yang Y, et al. (2020) Effect of the carding process and reinforcement method of carbon fiber/polypropylene fiber nonwoven fabrics on the anisotropic mechanical properties of hot-pressed composites. Fibers Polym 21: 1115–1125. http://dx.doi.org/10.1007/s12221-020-9622-4 doi: 10.1007/s12221-020-9622-4
![]() |
[28] |
Gupta A, Gurunathan P, Ramesha K, et al. (2019) Effect of heat treatment temperature on energy storage performance of PAN co‐MMA-based carbon nanofibers as freestanding lithium-ion batteries anode. Energy Storage 1: 89. http://dx.doi.org/10.1002/est2.89 doi: 10.1002/est2.89
![]() |
[29] |
Zeng S, Li X, Li M, et al. (2019) Flexible PVDF/CNTs/Ni@CNTs composite films possessing excellent electromagnetic interference shielding and mechanical properties under heat treatment. Carbon 155: 34–43. https://doi.org/10.1016/j.carbon.2019.08.024 doi: 10.1016/j.carbon.2019.08.024
![]() |
[30] |
Geng P, Zhao J, Wu W, et al. (2018) Effect of thermal processing and heat treatment condition on 3D printing PPS properties. Polymers 10: 875. https://doi.org/10.3390/polym10080875 doi: 10.3390/polym10080875
![]() |
[31] |
Chua C, Liu H, Di Trani N, et al. (2021) Carbon fiber reinforced polymers for implantable medical devices. Biomaterials 271: 120719. https://doi.org/10.1016/j.biomaterials.2021.120719 doi: 10.1016/j.biomaterials.2021.120719
![]() |
[32] |
Jeon I, Lee M, Choi H, et al. (2021) Mechanical properties and bioactivity of polyetheretherketone/hydroxyapatite/carbon fiber composite prepared by the mechanofusion process. Polymers 13: 1978. https://doi.org/10.3390/polym13121978 doi: 10.3390/polym13121978
![]() |
[33] |
Hendler-Neumark S, Wulf V, Bisker G (2021) In vivo imaging of fluorescent single-walled carbon nanotubes within C. elegans nematodes in the near-infrared window. Mater Today Bio 12: 100175. https://doi.org/10.1016/j.mtbio.2021.100175 doi: 10.1016/j.mtbio.2021.100175
![]() |
[34] |
Chen M, Ren M, Shi Y, et al. (2023) State-of-the-art polyetheretherketone three-dimensional printing and multifunctional modification for dental implants. Front Bioeng Biotech 11: 1271629. https://doi.org/10.3389/fbioe.2023.1271629 doi: 10.3389/fbioe.2023.1271629
![]() |
[35] |
Rajzer I, Menaszek E, Bacakova L, et al. (2010) In vitro and in vivo studies on biocompatibility of carbon fibres. Mater Sci: Mater Med 21: 2611–2622. https://doi.org/10.1007/s10856-010-4108-3 doi: 10.1007/s10856-010-4108-3
![]() |
[36] |
Petersen R (2016) Carbon fiber biocompatibility for implants. Fibers 4: 1. https://doi.org/10.3390/fib4010001 doi: 10.3390/fib4010001
![]() |
[37] |
Zheng H, Zhang W, Li B, et al. (2022) Recent advances of interphases in carbon fiber-reinforced polymer composites: A review. Compos Part B-Eng 233: 109639. https://doi.org/10.1016/j.compositesb.2022.109639 doi: 10.1016/j.compositesb.2022.109639
![]() |
[38] |
Istgaldi H, Nayebi B, Ahmadi Z, et al. (2020) Characterization of ZrB2–TiC composites reinforced with short carbon fibers. Ceram Int 46: 23155–23164. http://dx.doi.org/10.1016/j.ceramint.2020.06.095 doi: 10.1016/j.ceramint.2020.06.095
![]() |
[39] |
Li H, Liebscher M, Zhao D, et al. (2023) A review of carbon fiber surface modification methods for tailor-made bond behavior with cementitious matrices. Prog Mater Sci 132: 101040. http://dx.doi.org/10.1016/j.pmatsci.2022.101040 doi: 10.1016/j.pmatsci.2022.101040
![]() |
[40] |
Tang S, Hu C (2017) Design, preparation and properties of carbon fiber reinforced ultra-high temperature ceramic composites for aerospace applications: A review. J Mater Sci Technol 33: 117–130. https://doi.org/10.1016/j.jmst.2016.08.004 doi: 10.1016/j.jmst.2016.08.004
![]() |
[41] |
Shivam V, Nitin S, Saurabh K, et al. (2021) Developments of PEEK (polyetheretherketone) as a biomedical material: A focused review. Eur Polym J 147: 110295. http://dx.doi.org/10.1016/j.eurpolymj.2021.110295 doi: 10.1016/j.eurpolymj.2021.110295
![]() |
[42] |
Akay C, Ersöz M (2020) PEEK in dentistry, properties and application areas. Int Dent Res 10: 60–65. http://dx.doi.org/10.5577/intdentres.2020.vol10.no2.6 doi: 10.5577/intdentres.2020.vol10.no2.6
![]() |
[43] |
Sofia A, Lisa P (2020) Nanomechanical analysis of medical grade PEEK and carbon fiber-reinforced PEEK composites. J Mech Behav Biomed Mater 111: 104008. https://doi.org/10.1016/j.jmbbm.2020.104008 doi: 10.1016/j.jmbbm.2020.104008
![]() |
[44] |
Ma H, Suonan A, Zhou J, et al. (2021) PEEK (Polyether-ether-ketone) and its composite materials in orthopedic implantation. Arab J Chem 14: 102977. http://dx.doi.org/10.1016/j.arabjc.2020.102977 doi: 10.1016/j.arabjc.2020.102977
![]() |
[45] |
Adil S, Lazoglu I (2023) A review on additive manufacturing of carbon fiber‐reinforced polymers: Current methods, materials, mechanical properties, applications and challenges. J Appl Polym Sci 140: 53476. https://doi.org/10.1002/app.53476 doi: 10.1002/app.53476
![]() |
[46] |
Stratton-Powell A, Pasko K, Brockett C, et al. (2016) The biologic response to polyetheretherketone (PEEK) wear particles in total joint replacement: A systematic review. Clin Orthop Relat R 474: 2394–2404. https://doi.org/10.1007/s11999-016-4976-z doi: 10.1007/s11999-016-4976-z
![]() |
[47] |
Chua C, Liu H, Di Trani N, et al. (2021) Carbon fiber reinforced polymers for implantable medical devices. Biomaterials 271: 120719. https://doi.org/10.1016/j.biomaterials.2021.120719 doi: 10.1016/j.biomaterials.2021.120719
![]() |
[48] |
Nakahara I, Takao M, Bandoh S, et al. (2013) In vivo implant fixation of carbon fiber-reinforced PEEK hip prostheses in an ovine model. J Orthop Res 31: 485–492. https://doi.org/10.1002/jor.22251 doi: 10.1002/jor.22251
![]() |
[49] |
Hacking S, Pauyo T, Lim L, et al. (2010) Tissue response to the components of a hydroxyapatite-coated composite femoral implant. J Biomed Mater Res 94: 953–960. https://doi.org/10.1002/jbm.a.32758 doi: 10.1002/jbm.a.32758
![]() |
[50] |
Scotchford C, Garle M, Batchelor J, et al. (2003) Use of a novel carbon fibre composite material for the femoral stem component of a THR system: In vitro biological assessment. Biomaterials 24: 4871–4879. https://doi.org/10.1016/s0142-9612(03)00403-4 doi: 10.1016/s0142-9612(03)00403-4
![]() |
[51] |
Darwich A, Nazha H, Abbas W (2019) Numerical study of stress shielding evaluation of hip implant stems coated with composite (carbon/PEEK) and polymeric (PEEK) coating materials. Biomed Res-India 30: 169–174. https://doi.org/10.35841/biomedicalresearch.30-18-1048 doi: 10.35841/biomedicalresearch.30-18-1048
![]() |
[52] |
Caouette C, Yahia L, Bureau M (2011) Reduced stress shielding with limited micromotions using a carbon fibre composite biomimetic hip stem: A finite element model. Proc Inst Mech Eng H 225: 907–919. https://doi.org/10.1177/0954411911412465 doi: 10.1177/0954411911412465
![]() |
[53] |
Sridhar I, Adie P, Ghista D (2010) Optimal design of customised hip prosthesis using fiber reinforced polymer composites. Mater Design 31: 2767–2775. https://doi.org/10.1016/j.matdes.2010.01.016 doi: 10.1016/j.matdes.2010.01.016
![]() |
[54] |
Ceddia M, Trentadue B, De Giosa G, et al. (2023) Topology optimization of a femoral stem in titanium and carbon to reduce stress shielding with the FEM method. J Compos Sci 7: 298. https://doi.org/10.3390/jcs7070298 doi: 10.3390/jcs7070298
![]() |
[55] |
Tavakkoli Avval P, Samiezadeh S, Klika V, et al. (2015) Investigating stress shielding spanned by biomimetic polymer-composite vs. metallic hip stem: A computational study using mechano-biochemical model. J Mech Behav Biomed Mater 41: 56–67. https://doi.org/10.1016/j.jmbbm.2014.09.019 doi: 10.1016/j.jmbbm.2014.09.019
![]() |
[56] |
Adam F, Hammer D, Pfautsch S, et al. (2002) Early failure of a press-fit carbon fiber hip prosthesis with a smooth surface. J Arthroplasty 17: 217–223. https://doi.org/10.1054/arth.2002.30285 doi: 10.1054/arth.2002.30285
![]() |
[57] |
Bennett D, Hill J, Dennison J, et al. (2014) Metal-carbon fiber composite femoral stems in hip replacements: a randomized controlled parallel-group study with mean ten-year follow-up. J Bone Joint Surg Am 96: 2062–2069. https://doi.org/10.2106/JBJS.M.01542 doi: 10.2106/JBJS.M.01542
![]() |
[58] |
Campbell M, Bureau MN, Yahia L (2008) Performance of CF/PA12 composite femoral stems. J Mater Sci 19: 683–693. https://doi.org/10.1007/s10856-007-3073-y doi: 10.1007/s10856-007-3073-y
![]() |
[59] |
Lyu H, Jiang N, Li Y, et al. (2021) Enhancing CF/PEEK interfacial adhesion by modified PEEK grafted with carbon nanotubes. Compos Sci Technol 210: 108831. http://dx.doi.org/10.1016/j.compscitech.2021.108831 doi: 10.1016/j.compscitech.2021.108831
![]() |
[60] |
Li C, Granger C, Del Schutte H, et al. (2002) Progressive failure analysis of laminated composite femoral prostheses for total hip arthroplasty. Biomaterials 23: 4249–4262. https://doi.org/10.1016/s0142-9612(02)00188-6 doi: 10.1016/s0142-9612(02)00188-6
![]() |
1. | Mario Ceddia, Giuseppe Solarino, Pasquale Dramisino, Giuseppe De Giosa, Stefano Rizzo, Bartolomeo Trentadue, Comparison of Stress between Three Different Functionally Graded Hip Stem Implants Made of Different Titanium Alloys and Composite Materials, 2024, 8, 2504-477X, 449, 10.3390/jcs8110449 | |
2. | Mario Ceddia, Giuseppe Solarino, Maria Tucci, Luciano Lamberti, Bartolomeo Trentadue, Stress Analysis of Tibial Bone Using Three Different Materials for Bone Fixation Plates, 2024, 8, 2504-477X, 334, 10.3390/jcs8090334 |
Femoral head | Acetabulum shell | Results |
Co-Cr-Mo | Co-Cr-Mo | Early high loosening rate and limited use |
Co-Cr-Mo | UHMWPE | Widely employed; Low wear |
Aluminia/zirconia | UHMWPE | Very low wear rate |
Aluminia | Aluminia | Minimum wear rate |
Ti6Al4V | UHMWPE | Reports of high UHMWPE wear due to titanium surface breakage |
Material | Density (g/cm3) | Tensile strenght (GPa) | Specific strenght (GPa) | Modulus of elasticity (GPa) | Specific modulus (GPa) |
Carbon fiber | 1.6-2.2 | 1.5-5.65 | 0.70-3.12 | 228-790 | 106-407 |
Stell wire | 7.9 | 2.39 | 0.30 | 210 | 26.6 |
Material | Density (mg/m3) | Young's modulus (GPa) | Breaking stress (MPa) |
PE | 0.952-0.965 | 0.17-0.28 | 8.3-31.0 |
PS | 1.04-1.05 | 2.8-4.1 | 48.3-72.4 |
PC | 1.20 | 2.38 | 65.8-72.4 |
PP | 0.90-0.91 | 1.14-1.55 | 31.0-41.4 |
PEEK | 1.3 | 3.6 | 90-100 |
Femoral head | Acetabulum shell | Results |
Co-Cr-Mo | Co-Cr-Mo | Early high loosening rate and limited use |
Co-Cr-Mo | UHMWPE | Widely employed; Low wear |
Aluminia/zirconia | UHMWPE | Very low wear rate |
Aluminia | Aluminia | Minimum wear rate |
Ti6Al4V | UHMWPE | Reports of high UHMWPE wear due to titanium surface breakage |
Material | Density (g/cm3) | Tensile strenght (GPa) | Specific strenght (GPa) | Modulus of elasticity (GPa) | Specific modulus (GPa) |
Carbon fiber | 1.6-2.2 | 1.5-5.65 | 0.70-3.12 | 228-790 | 106-407 |
Stell wire | 7.9 | 2.39 | 0.30 | 210 | 26.6 |
Material | Density (mg/m3) | Young's modulus (GPa) | Breaking stress (MPa) |
PE | 0.952-0.965 | 0.17-0.28 | 8.3-31.0 |
PS | 1.04-1.05 | 2.8-4.1 | 48.3-72.4 |
PC | 1.20 | 2.38 | 65.8-72.4 |
PP | 0.90-0.91 | 1.14-1.55 | 31.0-41.4 |
PEEK | 1.3 | 3.6 | 90-100 |