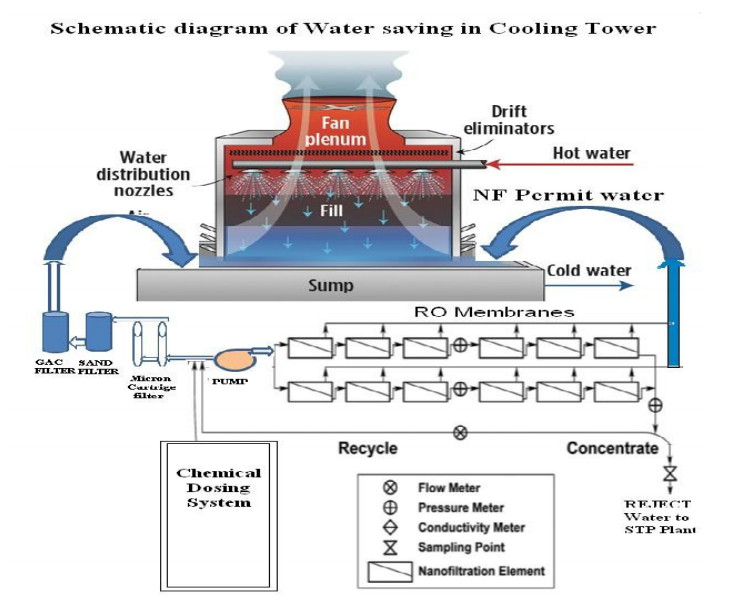
A study was carried to investigate by placing a side stream filter in a cooling tower to observe the water conservation in the system. For any coal based power plant cycles of concentration plays important role for water conservation. The cycles of concentration in cooling tower was increased by installation of membrane system. The drain of the side stream filter was disposed to effluent treatment plant (ETP), while the filtered water will be recycled to the cooling tower inlet. The water parameter was measured by using various flow rates, pressure, and other factors. Significant water savings were demonstrated in the pilot. Maximum make-up water and outflow were both reduced by 14% and 48%, respectively. To save the most water, permeate recovery must be as high as possible. Water savings were minimal due to silica scaling on the membranes. Selected membranes are capable of lower total dissolved system (TDS) rejection than the 88% of total required membranes in the primary study, which might help to save water. The increased energy consumed by membrane treatment was compensated for by lower water outlays. To prevent scaling antiscalent chemical with chemical dosing system was installed along with membrane system.
Citation: Chetan Dhokai, Ritesh Ramesh Palkar, Vicky Jain. Water saving in thermal power plant by use of membrane filter in cooling tower treatment[J]. AIMS Environmental Science, 2022, 9(3): 282-292. doi: 10.3934/environsci.2022020
[1] | Jianfeng Wen, Yanjin Liu, Yunjie Tu and Mark W. LeChevallier . Energy and chemical efficient nitrogen removal at a full-scale MBR water reuse facility. AIMS Environmental Science, 2015, 2(1): 42-55. doi: 10.3934/environsci.2015.1.42 |
[2] | Laura Romero, Modesto Pérez-Sánchez, P. Amparo López-Jiménez . Improvement of sustainability indicators when traditional water management changes: a case study in Alicante (Spain). AIMS Environmental Science, 2017, 4(3): 502-522. doi: 10.3934/environsci.2017.3.502 |
[3] | Nasrul Arahman, Cut Meurah Rosnelly, Sri Mulyati, Wafiq Alni Dzulhijjah, Nur Halimah, Rinal Dia'ul Haikal, Syahril Siddiq, Sharfina Maulidayanti, Muhammad Aziz, Mathias Ulbricht . Investigation of microplastics in community well water in Banda Aceh, Indonesia: a separation technique using polyethersulfone-poloxamer membrane. AIMS Environmental Science, 2025, 12(1): 53-71. doi: 10.3934/environsci.2025003 |
[4] | Melanie Voigt, Alexander Wirtz, Kerstin Hoffmann-Jacobsen, Martin Jaeger . Prior art for the development of a fourth purification stage in wastewater treatment plant for the elimination of anthropogenic micropollutants-a short-review. AIMS Environmental Science, 2020, 7(1): 69-98. doi: 10.3934/environsci.2020005 |
[5] | Dong Chen, Marcus Thatcher, Xiaoming Wang, Guy Barnett, Anthony Kachenko, Robert Prince . Summer cooling potential of urban vegetation—a modeling study for Melbourne, Australia. AIMS Environmental Science, 2015, 2(3): 648-667. doi: 10.3934/environsci.2015.3.648 |
[6] | Joyce Cristale, Silvia Lacorte . PBDEs versus NBFR in wastewater treatment plants: occurrence and partitioning in water and sludge. AIMS Environmental Science, 2015, 2(3): 533-546. doi: 10.3934/environsci.2015.3.533 |
[7] | Yenni, Mohd Hafiz Ibrahim, Rosimah Nulit, Siti Zaharah Sakimin . The interactive effects of fertilizer and water stress on plant growth, leaf gas exchange and nutrient uptake on strawberry (Fragaria x ananassa, Duch). AIMS Environmental Science, 2021, 8(6): 597-618. doi: 10.3934/environsci.2021038 |
[8] | Lin Ma, Jun Zhang, Lixing Chen, Shuling Xiao, Yingzi Zhang . A field research on the impact of underlying surface configuration on street thermal environment in Lhasa. AIMS Environmental Science, 2019, 6(6): 483-503. doi: 10.3934/environsci.2019.6.483 |
[9] | Volodymyr Ivanov, Viktor Stabnikov, Chen Hong Guo, Olena Stabnikova, Zubair Ahmed, In S. Kim, and Eng-Ban Shuy . Wastewater engineering applications of BioIronTech process based on the biogeochemical cycle of iron bioreduction and (bio)oxidation. AIMS Environmental Science, 2014, 1(2): 53-66. doi: 10.3934/environsci.2014.2.53 |
[10] | Mohammed Basahi . Humic acid improved germination rate, seedling growth and antioxidant system of pea (Pisum sativum L. var. Alicia) grown in water polluted with CdCl2. AIMS Environmental Science, 2021, 8(4): 358-370. doi: 10.3934/environsci.2021023 |
A study was carried to investigate by placing a side stream filter in a cooling tower to observe the water conservation in the system. For any coal based power plant cycles of concentration plays important role for water conservation. The cycles of concentration in cooling tower was increased by installation of membrane system. The drain of the side stream filter was disposed to effluent treatment plant (ETP), while the filtered water will be recycled to the cooling tower inlet. The water parameter was measured by using various flow rates, pressure, and other factors. Significant water savings were demonstrated in the pilot. Maximum make-up water and outflow were both reduced by 14% and 48%, respectively. To save the most water, permeate recovery must be as high as possible. Water savings were minimal due to silica scaling on the membranes. Selected membranes are capable of lower total dissolved system (TDS) rejection than the 88% of total required membranes in the primary study, which might help to save water. The increased energy consumed by membrane treatment was compensated for by lower water outlays. To prevent scaling antiscalent chemical with chemical dosing system was installed along with membrane system.
Freshwater availability is under threat in several parts of the globe. More than 50% water in US and European nation are used in Power generation [1]. It is exacerbated by urban growth and industrialization, as well as global warming and drought. The large amount of water is required for coal-based thermal power plants. The maximum amount of water is used in a cooling tower. The stock of fresh water decrease day by day for cooling tower in thermal power plant [2]. Thermoelectric power plant consumes the water around 3 billion [3]. As freshwater supplies get scarcer, freshwater use will become more competitive and more costly. Water disposal charges may also apply. It is essential for the power-producing industry to find techniques to reduce emissions. And to conserve water.
By decreasing water use and increasing the efficiency of the cooling tower may allow power plants to expand their operations. As a result, freshwater makes up requirements and blowdown water discarding is minimized. A thermal power plant can be benefitted by optimizing water consumption in cooling towers. Recirculation of wet cooling tower is operated at its maximum efficiency of around 40% in the thermal power plant. During continuously water circulation is in condenser tubes, the TDS also increases with increase different parameters like conductivity, chlorides, silica, hardness, etc. [4].
As the TDS reaches to set value the blowdown is carried out from the system and then freshwater is added to the system to maintain the water level of sump. The system is depicted in Figure 1. There are two parts of the water system: makeup water and blowdown to avoid the formation of scale, higher salt concentrations use of a side-stream filter can aid in the reduction of scale growth and water consumption. As a side stream filtration higher TDS blowdown water treatment-hardness as calcium and magnesium controlled by brine concentrators and lime treatment. In the lime using lime in the process magnesium will be precipitated in the form of magnesium hydroxide and calcium will precipitate as calcium hydroxide as a make-up, pH-adjusted, clean, filtered water is added. This method does not remove sodium, potassium, sulfate, or chloride. Drift losses and sludge discharge are examples of softening. Brine concentrators control blowdown at the San Juan Generating Station[5]. The brine concentrator, according to studies, recovers roughly 98% of the water in the brine, the incoming tide. Membrane based system consume less amount of energy than compared to thermal desalination [6]. Desalination membrane technologies are extensively used and discuss in depth. The use of chemical treatment in cooling tower can be greatly reduced by used of nano filtration[7]. In desalination membrane technology, there are multiple types of membrane filters available in the market. Based on the particle size membrane filter will be selected. Like micron filter-5µ, ultrafilter-0.01µ, Nano filter-0.001µ, and RO filter-0.0001µ pore size membrane. The TDS removal capacity and energy requirements of these pressure-driven membranes are listed in decreasing order of removal capacity to maximum removal capacity, with RO needing the most energy [8]. The equation can be simplified by removing monovalent ions. The bulk of the time, NF rejects multivalent ions. Thin-film composite (TFC) membranes may be used to make both RO and NF membranes. An absorbent substrate, for example, layered with a slim polymer layer Polyamide is a polymer that may be used to make a variety of products
They are non-porous due to the lack of a well-defined pore structure, allowing them to reject organisms with low molar masses. When selecting the best membrane for a certain application, the properties of each membrane must be thoroughly examined. Recovery rates for brackish water are 50% to 90% and sea water are generally 35% to 60% [9]. A side stream is installed with the cooling-tower water. Some amount of water is filtered through a membrane system, which removes hardness that dissolves in the water. The filtered water is recycled with tower makeup water. The wastewater with higher concentrations has been released and disposed of. The volume of blow-down water can be reduced by the application of a side stream filter system. The concentration must not rise suddenly or keep well below the specified limit [10]. The system is depicted schematically in Figure 1 projecting computations indicated that the optimal choice was ultra pure water (N90 percent chemical purity). The main motive of this study is to explore the result of pilot research to determine to conserve water by placing side stream filters [11]. The information gathered throughout the study will be analyzed to assess membrane performance and possible water savings [12]. The cost-benefit analysis is also included. This report outlines pilot research that was carried out to see if the process of cooling-tower treatment by membrane leads to water saving [13]. The study was conducted over three months from January 2020 to March 2020. The pilot data is analyzed to evaluate memory performance, measured water savings, and prospective water savings. The water source is river water. River water is used in the cooling tower for makeup. Water from the forebay enters the cooling tower and circulates through condenser tubes and returns back to the forebay. The water quality of circulating water is analyzed and conductivity is kept below 1300 us/cm to avoid scale and corrosion in condenser tubes. Cooling tower cooling capacity is 298 tons with a flow of 3.3 m3/min. Normal cooling water treatment is for prevent scale formation and corrosion. Organic phosphate (HEDP) is utilized to control calcium precipitate and a terpolymer was used for dispersion of calcium and silica precipitate and to prevent settling and clumping [14]. The Cooling tower water treatment chemicals are supplied by vasu chemicals with product names HD-60, PB-50, Scacil-4254, and special-4254. Figure 1 shows a schematic diagram of the experimental study. Small size water pump drew water from the forebay and kept it in the circulation path of the scheme. Which as soon as the water was passed by dual media filters, one meant to remove small size particles and the other an activated carbon filter designed to remove certain organic pollutants and free residual chlorine. To remove particles, water was cycled from the media filters via a 20-inch dia, 50 m filter, and 1 m micron cartridge filter. The antiscalant dosing is done between the membrane system and cartridge filter by chemical dosing pump [15]. According to the seller product sheet, it suppresses feed water hardness scale and colloids in the membrane, such as SiO2, CaSO4, Ca3(PO4)2, and CaCO3. As the water reached the elements, a high-pressure pump (5 HP) pressurized it. The membrane system was made up of each six-element array with two parallel line vessels that were identical. Each array included six 2.5 inches. Components in sequence, each housed in a single SS pressure vessel. KOCH TFC® softening membranes were utilized as the elements. These elements were chosen because they have capable of 90 % chloride and 98.5 % calcium and magnesium hardness rejection and are low-pressure elements. As stated in the introduction, the goal was to find a membrane that would consume the least amount of energy while yet rejecting maximum TDS. The permeate water flow was recycled to the forebay sump, while they reject water flow was released into the effluent water treatment plant. The main parameters like pressure and temperature analog meters were used online. Conductivity & flow rates were continuously measured using digital meters installed. The pressure gauge was installed at feed water, at reject line and between the two arrays of membranes Flow rates were monitored from the forbay sump (XT), recycling flow (XR), combined feed water (XT +XR), permeate water (XP), and reject water flow (XC).
From 05 July 2020 to 28 November 2020, the pilot trial taken in operation. By 12 August 2020, the system was thought to be stable. Throughout the pilot trial operation, samples has been analyzed on a regular basis. At the start of operations, sampling was done three times a day, but it was reduced to once or twice a week after the system had stabilized.
Several times during the pilot, the membranes were cleansed. To begin, a base washing with caustic solution and Alconox was conducted to achieve pH from 10.5 to 11.0. After getting a pH, circulate solution in the system up to 30 minutes. The base wash was followed by an HCl acid solution wash with a pH of around 2. During the base wash acid solution pH was measured on a regular basis to monitor the acid's neutralization [16]. The solution pH increased up to 5 and 6 during circulation, more hydrochloric acid has been added to bring it back down to 2. When circulated acid solution could not much more be neutralized, then it has been judged that cleaning is completed by this procedure by it max.capacity of efficacy and it was discontinued [17]. To evaluate potential scalants, they were inspected visually as well as through SEM-X-ray Spectroscopy principle. The two types of instrument were used are energy dispersive X-ray spectroscopy and scanning electron microscopy.
Cations: .The cations which are determined by inductively coupled plasma mass spectrometer are calcium, sodium, potassium, magnesium.
Anions: Most anions (e.g. sulfate, chloride, fluoride, orthophosphate, bromide, and nitrate) was analyzed by column ion chromatograph-Make: dionex, model no. ICS 2100 with RFIC Ionpac AS18.
pH: Water sample pH was checked by WTW-720 pH meter.
Conductivity: Water sample conductivity checked by WTW-3210 conductivity meter.
Turbidity: Water sample turbidity checked by HF scientific-Micro 100 turbidity meter.
SiO2: Silica was checked by Hach DR2400 spectrophotometer method- silicomolybdate technique (Hach Method 8185). Polymerized silica cannot be detected using this technique. At room temperature, samples were kept and measurements were taken.
Feed spacer Images and membrane surface were obtained by scanning electron microscope (SEM)-Zeiss Supra 55VP using. The relative amounts of inorganic components in the deposits were determined using energy dispersive spectroscopy (EDS).
The water passing by membrane (R) is calculated by following equation:
R1=XC/XT | (1) |
Where x denotes flow rates, C denotes concentrate and T denote cooling tower flow stream. In order to determine total recovery, stream from the CT was employed as an alternative of the combined feed water flow of membrane components.
Calculated water savings by XM and CT data comparison, which was collected during the pilot's operating month (August 2020) to same month of prior year (August 2018). As a control, performance comparison between July 2020 (just before to the pilot trial run) and July 2018 & 2019, avg. & max. Temperatures also compared for these months, since the greater the temperature, chance of rain is higher.
The bulk w were calculated using the specific conductivity obtained using a conductivity probe (rather than in-line meters) (as opposed to w for specific solutes). Theoretical water savings were calculated using flow and mass-balance equations (Table 1). For XM and XC values, CT and pilot trial run flow-rate data were employed. Conductivity was set to 1400 S/cm, the cooling tower water set-point. Cc was calculated using measurements taken from manual grab samples during pilot trial run. For CM, a const. 400 S/cm value was utilized, which was average (round of Figure 2) measurement at regular intervals of 375 S/cm taken from the cooling tower make up.
System description | Flow calculation | Mass calculation |
Normal cooling tower (without using membrane filter) | Xm = Xe + XBD | XmCm = XBDCT |
Cooling tower using side stream and membrane and blowdown | Xm = Xe + XBD + XC | XmCm = XBDCT + XCCC |
Cooling tower using side stream and membrane and zero blowdown | Xm = Xe + XC | XmCm = XCCC |
The economical feasibility of cooling tower water treatment by using membranes has been investigated [18]. This was accomplished by calculating clean water savings and water disposal expenses to cover electricity expenses of operating this membrane operating system. Its assumed that water removal cost was same as fresh water cost [19]. The energy use was computed assuming that the pump in our system was using 50% of its capacity (1.87 kWh). The energy cost per permeate water volume generated as a function of membrane efficiency was estimated by taken the average QP as R derived from the pilot trial run data. Electricity costs was taken as Rs4.10, Rs 4.20, Rs 4.30, and Rs 4.40 per kWh.
As reductions in permeate water flow rates, there was obvious due to membrane scaling or fouling (Figure 3). Permeate water rate increase again after cleaning of membrane, but then rapidly dropped. With each consecutive cleaning, membrane performance increased less and less. Reduced permeate flux resulted in lower cooling tower flow rates. The permeate water recovery (R) varied from up to 64% from 0, with an 23% on average.
The pressure remain almost constant unless the capacity of pump was changed as shown in Table 3. The sump pressure was continuously monitored to determine whether there is any pressure increase because of biofouling or scaling in system. Pressure between sump and feed was higher compare to sump and discharge line. Over the course of the plot, the CT flow rate varied from 3.8 to 18.5 m3/d (0.7–3.4 gpm) (Table 2 and Figure 3). The flow rates of permeate water and concentrate reject water are both favorably linked with the CT flow rate. Maintaining a reasonably steady feed water rate in the pass through the membrane filter water system is adversely associated with recycle flow rate.
Outline of Water data m3/d | Recycle water | Permeate water | Cooling tower water | Feed water | Concentrate water |
Average flow | 19.3 | 2.2 | 8.4 | 27.6 | 6.3 |
Standard deviation | 6.8 | 1.7 | 2.8 | 8.1 | 1.5 |
Minimum | 8.8 | 0.1 | 3.8 | 12.6 | 2.8 |
Maximum | 36.1 | 9.4 | 18.7 | 44.3 | 9.8 |
Feed (Bar) | Concentrate (Bar) | First Sump (Bar) | Second Sump (Bar) | |
Mean pressure | 8.4 | 6.5 | 7.2 | 7.6 |
Standard deviation | 1.6 | 2.1 | 2 | 1.9 |
Minimum | 6.2 | 3.2 | 4.7 | 5 |
Maximum | 11.7 | 11.1 | 10.9 | 10.8 |
The membranes filter average solute rejection varied from 89% (Na & Cl) to 99% SO4 (Table 4). Membranes for NF and RO reject order depending on charge and size. It was found that membrane was more efficient in removal of divalent ions compared to monovalent ions [20]. Given that potassium has one of the greatest atomic radius any other ion with single covalent bond, it is not unexpected that the rejection was near about 96%. The silica was removed 90% of cases. By using the conductivity data, w ranges from 76% to 99.9 %, with avg. of 91%.
Constituent | Feed | Make-up | Post-GAC | Cooling tower | Permeate | Concentrate | w (%) |
Silica | 134 | 24 | 113 | 112 | 37 | 152 | 89 |
Sulfate | 154 | 34 | 118 | 118 | 5.2 | 174 | 98 |
Chloride | 102 | 20 | 87 | 87 | 20.8 | 116 | 90 |
Potassium | 20 | 3.7 | 18 | 17 | 5.4 | 28 | 96 |
Calcium | 144 | 34 | 113 | 110 | 9.9 | 170 | 96 |
Magnesium | 26 | 5.7 | 22 | 21 | 1.8 | 34 | 96 |
Sodium | 134 | 24 | 103 | 100 | 31 | 141 | 88 |
Fluoride | 2.3 | 0.52 | 2 | 1.7 | 0.6 | 2.7 | 93 |
Bicarbonate | 502 | 112 | 36 | 396 | 70 | 544 | 93 |
The CT blow down may decreased up to 49%, with avg. computed reduction of 17% during course of the trial run (Figure 4). Feed water saving have been determined as high as 16%, with avg. 6% savings. Similarly, concentration of cycle may be raised from 3 to 4.9, with avg. 3.4 during course of the pilot trial run (Figure 5). R is positively linked with decreases in reject blowdown and water make up, as well as concentration of cycle increases. Water savings and CoC rise considerably after membrane cleaning, but soon declined with a reduction in R.
The avg. make-up water flow rate in September 2020 after the trial starting was 28% lower than in September 2020 before the trial (53.3 cubic meter per day against 6932 cubic meter per day. August 2020 XM was similarly lower than August 2018 & July 2019, although only by 8% and 6%, respectively. Because avg. Temp. in September 2018 & September 2020 were about 3 degrees Celsius for twenty five days in pre- and post-trial run water uses levels are compare. After August 4, daily temperature difference is more than 3 degrees Celsius were all warmer in 2020 than in 2018. Net precipitation in September 2018 & September 2020 was 1.04 inch & 1.04 inch respectively.
The conductivity of the CT water stayed very near to the limit point of 1400 S/cm in August 2018. In contrast, conductivity was below the limit point for much of August 2010, following the start of the pilot trial run. The conductivity varied between the specified value and less than 1000 S/cm. However, no obvious relationship exists between CT conductivity and other variable parameters such as membrane filter system cleanings and precipitation [21].
The study of EDS shows that the main component was found to be silica of 96% of total surface calcium made up 3% of the components, with the rest made up of phosphorus, magnesium, and aluminum. There was no evidence of iron. SEM images revealed obvious deposits on the spacer surface as well as some mineral on the downstream membranes. Based on the EDS data, it is presumed that the deposits are silica. There was no evidence of macroscopic mineralization or clear crystals visible by SEM, as shown in figure 5.
Evidence that cooling tower side-stream treatment reduces water use includes. Generally anti-scalant are less efficient on silica than calcium [22].
The acid wash should have removed any calcium deposits [23]. However, because silica is more soluble e contrast in findings between these two pilots demonstrates the anti-scalent effectiveness on calcium salts. More power consumption is in membrane based system if there is more salinity in make up water. Our research reflects in case of permeate recovery can be obtain at a high level around 0.3, the savings in make up of fresh water and water removal expenses should be sufficient to balance for the power at Rs5.10/kWh. If R is more than or equal to 0.44 at Rs4.20/kWh, water conservation will cover the cost of electricity. Our study is limited to pilot trial run data. A permeate rate may rise by using higher efficiency pump which consumes less energy. The membrane performance can modify if the process is line up for use in thermal power plant. Furthermore, the correlation between reject and permeate water changes depending on the system [24]. While economical study looks to be promising, further research is required before constructing a system. Seasonal fluctuations in evaporation rates, for example, should be considered when estimating appropriate side-stream flow rates. Water, water disposal, energy, and capital expenses must all be included in the research. In general, membrane systems recover less water while using less power consumption. Depending upon the location the cost of water vs. energy changes that that will decide whether approach is feasible or not.
Our simulations also suggest that if membranes with chemical rejection rates of 70%–90% and better water recovery might be built, considerable water conservation might be obtained. Lots of commercial available membranes large rejection rates that are either too high or far too low for cooling system water treatment (b 40). Advanced systems that employ various membrane varieties and/or arranging may potentially provide scale prevention due to the operational efficiency required to maximize water consumption.
Estimated reductions in blow down and cooling tower inlet water usage based mass and water flow. Estimated cycles of concentration was increased, by keeping the almost same temperature and other parameters the make up water was reduced to much extent compared to previous year of same duration. And the conductivity of cooling water analysis was observed less than the set points scaling must be properly managed for an optimal system since the quantity of water saved which is directly related to permeate water recovery [25]. According to the EDS results, silica is a major scalant. Given the usage of antiscalants, CT (cooling tower) feed, and concentrate waters are all super-saturated in amorphous silica and calcite. The future scope for water conservation can be achieved higher by using membrane advanced design membrane which are higher than commercial membrane. The waste water obtained in effluent treatment plant can further used in coal handling plant for dust suppression system hence zero liquid discharge is possible by above study.
The authors would like to thanks Dr. Pratik Mehta for providing guidance throughout the project. No financial help is taken from any organization for this research work.
The all mention authors above has no conflict of interest of the above research work.
[1] | EEA, OPOCE (2009) Water resources across Europe-confronting water scarcity and drought (EEA Report No. 2). European Environment Agency (EEA), Office for Official Publications of the European Communities (OPOCE), Copenhagen, Denmark. |
[2] |
MurrantD, QuinnA, ChapmanL, et al. (2017) Water use of the UK thermal electricity generation fleet by 2050: Part 2 quantifying the problem. Energy Policy 108: 859-874. https://doi.org/10.1016/j.enpol.2017.03.047 doi: 10.1016/j.enpol.2017.03.047
![]() |
[3] |
Feeley TJ, Skone TJ, Stlegel GJ, et al. (2008) Water: a critical resource in the thermoelectric power industry. Energy 33: 1-11. https://doi.org/10.1016/j.energy.2007.08.007 doi: 10.1016/j.energy.2007.08.007
![]() |
[4] | Matson J, Harris, T (1979) Zero Discharge of Cooling Water by Side stream Softening. Water Pollution Control Federation 51: 2602-2614. |
[5] | CutlerDS, DeanJD, DawJA, et al. (2019) Alternative Water Treatment Technologies for Cooling Tower Applications (No. NREL/TP-7A40-71845). National Renewable Energy Lab. (NREL), Golden, CO (United States). |
[6] | Jones R(1991) Waste water purification system. Wastewater Resources Inc, USA. |
[7] | NRC (2008) Desalination A National Perspective. The National Academies Press, Washington D. C, United States. |
[8] |
Kumar P, Gupta P, Kumar S (2022) Comparing energy nexus efficiency of Energy Recovery Inc (ERI) over turbo pumps for cost saving of 12.6 MLD SWRO based desalination plant. Energy Nexus 5: 100015. https://doi.org/10.1016/j.nexus.2021.100015 doi: 10.1016/j.nexus.2021.100015
![]() |
[9] | Walton B (2010) The Price of Water: A Comparison of Water Rates. Usage in 30 U.S. Cities in, Circle of Blue. |
[10] |
Shahzad MW, Burhan M, Ang L, et al. (2017) Energy-water-environment nexus underpinning future desalination sustainability. Desalination 413: 52-64. http: https://doi.org/10.1016/j.desal.2017.03.009 doi: 10.1016/j.desal.2017.03.009
![]() |
[11] |
Jensen Q, Macedonio CA, Drioli F (2015) Membrane technology for water production inagriculture: Desalination and wastewater reuse. Desalination 364: 17-32. https://doi.org/10.1016/j.desal.2015.03.001 doi: 10.1016/j.desal.2015.03.001
![]() |
[12] |
Hightower M, Pierce SA (2008) The energy challenge. Nature 452: 285-286. https://doi.org/10.1038/452285a doi: 10.1038/452285a
![]() |
[13] |
Sardari K, Fyfe P, Lincicome D, et al. (2018) Combined electrocoagulation andmembrane distillation for treating high salinity produced waters. J Membr Sci 564: 82-96. https://doi.org/10.1016/j.desal.2020.114886 doi: 10.1016/j.desal.2020.114886
![]() |
[14] |
Tzotzi C, Pahiadaki T, Yiantsios SG, et al. (2007) A study of CaCO3scale formation and inhibition in RO and NF membrane processes. J Membr Sci 296: 171-184. https://doi.org/10.1016/j.memsci.2007.03.031 doi: 10.1016/j.memsci.2007.03.031
![]() |
[15] |
Semiat R, Sutzkover I, Hasson D (2003) Characterization of the effectiveness of silicaanti-scalants. Desalination 159: 11-19. https://doi.org/10.1016/S0011-9164(03)90041-5 doi: 10.1016/S0011-9164(03)90041-5
![]() |
[16] |
Drak A, Glucina K, Busch M, et al. (2000) Laboratory technique for predicting the scaling propensity of RO feed waters. Desalination 132: 233-242. https://doi.org/10.21608/bfemu.2020.126197 doi: 10.21608/bfemu.2020.126197
![]() |
[17] |
Ravanchi MT, Kaghazchi T, KargariA (2009) Application of membrane separation processes in petrochemical industry: A review. Desalination 235: 199-244. https://doi.org/10.1016/j.desal.2007.10.042 doi: 10.1016/j.desal.2007.10.042
![]() |
[18] |
Jhaveri JH, Murthy ZVP (2016) A comprehensive review on anti-fouling nanocomposite membranes for pressure driven membrane separation processes. Desalination 379: 137-154. https://doi.org/10.1016/j.desal.2015.11.009 doi: 10.1016/j.desal.2015.11.009
![]() |
[19] |
Greenlee LF, Lawler DF, Freeman BD, et al. (2009) Reverse osmosis desalination: Water sources, technology, and today's challenges. Water Res 43: 2317-2348. http://dx.doi.org/10.1016/j.watres.2009.03.010 doi: 10.1016/j.watres.2009.03.010
![]() |
[20] |
Huang H, Schwab K, Jacangelo JG (2009) Pretreatment for Low Pressure Membranes in Water Treatment: A Review. Environ Sci Technol 43: 3011-3019. https://doi.org/10.1021/es802473r doi: 10.1021/es802473r
![]() |
[21] |
Liron S, Asher B, Chaim S (2017) Use of an integrated biophysical process for the treatment of halo- and nitro- organic wastes. AIMS Environmental Science 4: 523-539. https://doi.org/10.3934/environsci.2017.4.523 doi: 10.3934/environsci.2017.4.523
![]() |
[22] |
Kateřina S, Denisa P, Hana S, et al. (2016) Selective adhesion of wastewater bacteria to Pleurotus ostreatus mycelium in a trickle-bed bioreactor. AIMS Environmental Science 3: 395-407. https://doi.org/10.3934/environsci.2016.3.395 doi: 10.3934/environsci.2016.3.395
![]() |
[23] | Kretzschmar AL, Manefield M (2015) The role of lipids in activated sludge floc. formation. AIMS Environmental Science 2: 122-133. https://doi.org/10.3934.2015.2.122 |
[24] |
Wen JF, Liu YJ, Tu YJ, et al. (2015) Energy and chemical efficient nitrogen removal at a full-scale MBR water reuse facility. AIMS Environmental Science 2: 42-55. https://doi.org/10.3934/environsci.2015.1.42 doi: 10.3934/environsci.2015.1.42
![]() |
[25] |
Naderi E, Azizivahed A, Asrari A (2022) A step toward cleaner energy production: A water saving-based optimization approach for economic dispatch in modern power systems. Electric Power Systems Research 4: 107689. https://doi.org/10.1016/j.epsr.2021.107689 doi: 10.1016/j.epsr.2021.107689
![]() |
1. | Olha Biedunkova, Pavlo Kuznietsov, Vasyl Korbutiak, Evaluation of return cooling water reuse in the wet cooled power plant to minimise the impact of water intake and drainage, 2024, 7, 29498392, 100151, 10.1016/j.scenv.2024.100151 | |
2. | Jawwad Ahmed, Amir Younas, Yousuf Jamal, Muhammad Shujaatullah, A pilot study on recycling cooling tower blowdown water through ultrafiltration and reverse osmosis, 2023, 307, 19443986, 8, 10.5004/dwt.2023.29855 | |
3. | Junjie Li, Yulong Yan, Yirong Wang, Yifu Zhang, Lianwei Shao, Menggang Li, Spatial-successive transfer of virtual scarcity water along China's coal-based electric chain, 2024, 288, 03605442, 129678, 10.1016/j.energy.2023.129678 | |
4. | Syed Taufiq Ahmad, Ashfaq Ahmad, Rizwan Ahmad, Ahmed Fuwad, Azeem Mushtaq, Muhammad Kashif Shahid, Recovery and Treatment of Cooling Tower Blowdown Water: Challenges, Recent Advancement, and Future perspectives, 2025, 22133437, 115399, 10.1016/j.jece.2025.115399 | |
5. | Pavlo Kuznietsov, Olha Biedunkova, The role of carbonate equilibrium in scale formation of calcium carbonate in a power plant open recirculating system, 2025, 6, 2632-6736, 10.1017/dce.2025.9 |
System description | Flow calculation | Mass calculation |
Normal cooling tower (without using membrane filter) | Xm = Xe + XBD | XmCm = XBDCT |
Cooling tower using side stream and membrane and blowdown | Xm = Xe + XBD + XC | XmCm = XBDCT + XCCC |
Cooling tower using side stream and membrane and zero blowdown | Xm = Xe + XC | XmCm = XCCC |
Outline of Water data m3/d | Recycle water | Permeate water | Cooling tower water | Feed water | Concentrate water |
Average flow | 19.3 | 2.2 | 8.4 | 27.6 | 6.3 |
Standard deviation | 6.8 | 1.7 | 2.8 | 8.1 | 1.5 |
Minimum | 8.8 | 0.1 | 3.8 | 12.6 | 2.8 |
Maximum | 36.1 | 9.4 | 18.7 | 44.3 | 9.8 |
Feed (Bar) | Concentrate (Bar) | First Sump (Bar) | Second Sump (Bar) | |
Mean pressure | 8.4 | 6.5 | 7.2 | 7.6 |
Standard deviation | 1.6 | 2.1 | 2 | 1.9 |
Minimum | 6.2 | 3.2 | 4.7 | 5 |
Maximum | 11.7 | 11.1 | 10.9 | 10.8 |
Constituent | Feed | Make-up | Post-GAC | Cooling tower | Permeate | Concentrate | w (%) |
Silica | 134 | 24 | 113 | 112 | 37 | 152 | 89 |
Sulfate | 154 | 34 | 118 | 118 | 5.2 | 174 | 98 |
Chloride | 102 | 20 | 87 | 87 | 20.8 | 116 | 90 |
Potassium | 20 | 3.7 | 18 | 17 | 5.4 | 28 | 96 |
Calcium | 144 | 34 | 113 | 110 | 9.9 | 170 | 96 |
Magnesium | 26 | 5.7 | 22 | 21 | 1.8 | 34 | 96 |
Sodium | 134 | 24 | 103 | 100 | 31 | 141 | 88 |
Fluoride | 2.3 | 0.52 | 2 | 1.7 | 0.6 | 2.7 | 93 |
Bicarbonate | 502 | 112 | 36 | 396 | 70 | 544 | 93 |
System description | Flow calculation | Mass calculation |
Normal cooling tower (without using membrane filter) | Xm = Xe + XBD | XmCm = XBDCT |
Cooling tower using side stream and membrane and blowdown | Xm = Xe + XBD + XC | XmCm = XBDCT + XCCC |
Cooling tower using side stream and membrane and zero blowdown | Xm = Xe + XC | XmCm = XCCC |
Outline of Water data m3/d | Recycle water | Permeate water | Cooling tower water | Feed water | Concentrate water |
Average flow | 19.3 | 2.2 | 8.4 | 27.6 | 6.3 |
Standard deviation | 6.8 | 1.7 | 2.8 | 8.1 | 1.5 |
Minimum | 8.8 | 0.1 | 3.8 | 12.6 | 2.8 |
Maximum | 36.1 | 9.4 | 18.7 | 44.3 | 9.8 |
Feed (Bar) | Concentrate (Bar) | First Sump (Bar) | Second Sump (Bar) | |
Mean pressure | 8.4 | 6.5 | 7.2 | 7.6 |
Standard deviation | 1.6 | 2.1 | 2 | 1.9 |
Minimum | 6.2 | 3.2 | 4.7 | 5 |
Maximum | 11.7 | 11.1 | 10.9 | 10.8 |
Constituent | Feed | Make-up | Post-GAC | Cooling tower | Permeate | Concentrate | w (%) |
Silica | 134 | 24 | 113 | 112 | 37 | 152 | 89 |
Sulfate | 154 | 34 | 118 | 118 | 5.2 | 174 | 98 |
Chloride | 102 | 20 | 87 | 87 | 20.8 | 116 | 90 |
Potassium | 20 | 3.7 | 18 | 17 | 5.4 | 28 | 96 |
Calcium | 144 | 34 | 113 | 110 | 9.9 | 170 | 96 |
Magnesium | 26 | 5.7 | 22 | 21 | 1.8 | 34 | 96 |
Sodium | 134 | 24 | 103 | 100 | 31 | 141 | 88 |
Fluoride | 2.3 | 0.52 | 2 | 1.7 | 0.6 | 2.7 | 93 |
Bicarbonate | 502 | 112 | 36 | 396 | 70 | 544 | 93 |