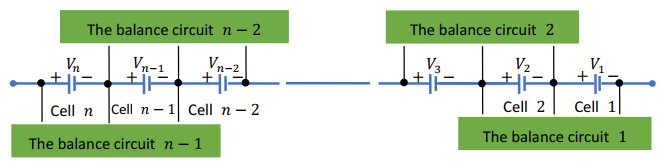
This paper proposes a design of energy balance circuit for two adjacent Lithium-ion battery cells in the cell string based on the modifying of the bidirectional CuK converter principle. This design only uses one MOSFET to transfer energy between two cells in a direction controlled by the first relay, second relay controls the cutting energy balance circuit off the cells when they have the same energy level. The control command sent by the management battery system (BMS) to the energy balance circuit via an RS485 communication protocol controls the direction of transferring energy, the amplitude of the balance current, the frequency and duty of PWM, the PWM signal applied to MOSFET is programmed by a microprocessor PIC18F2685. This design overcomes some disadvantages caused by applying the principle of bidirectional CuK converter to design the energy balancing circuit, these are the need for a multiple level DC source to open MOSFETs and issue of the energy loss on the elements of energy balance circuit. This design is also easy to expand for the battery string with a large number of cells. The energy balance control strategy can be implemented directly by each the energy balance circuit or remotely by BMS using RS485 communication. The experimental results of online optimal energy balance control based on state of charge (SoC) feedback for 07 SAMSUNG 22P battery cells connected in series are presented to prove the efficiency of the energy balance circuit design for two adjacent cells proposed in this paper.
Citation: Chi Van Nguyen, Thuy Nguyen Vinh. Design of energy balancing circuit for battery cells connected in series based on modifying the bidirectional CuK converter[J]. AIMS Energy, 2022, 10(2): 219-235. doi: 10.3934/energy.2022012
[1] | A.M.S.M.H.S.Attanayaka, J.P.Karunadasa, K.T.M.U.Hemapala . Estimation of state of charge for lithium-ion batteries - A Review. AIMS Energy, 2019, 7(2): 186-210. doi: 10.3934/energy.2019.2.186 |
[2] | Nan Liu, Thomas G. Habetler . Design of a parallel-LC-compensated on-board charger for universal inductive charging in electric vehicles. AIMS Energy, 2016, 4(5): 658-674. doi: 10.3934/energy.2016.5.658 |
[3] | Saad Jarid, Manohar Das . An Electro-Thermal Model based fast optimal charging strategy for Li-ion batteries. AIMS Energy, 2021, 9(5): 915-933. doi: 10.3934/energy.2021043 |
[4] | Junguang Sun, Xiaodong Zhang, Wenrui Cao, Lili Bo, Changhai Liu, Bin Wang . State of health estimation of lithium-ion batteries based on data-driven methods with a selected charging voltage interval. AIMS Energy, 2025, 13(2): 290-308. doi: 10.3934/energy.2025012 |
[5] | Steven B. Sherman, Zachary P. Cano, Michael Fowler, Zhongwei Chen . Range-extending Zinc-air battery for electric vehicle. AIMS Energy, 2018, 6(1): 121-145. doi: 10.3934/energy.2018.1.121 |
[6] | Xiaoyu Zheng, Dewang Chen, Yusheng Wang, Liping Zhuang . Remaining useful life indirect prediction of lithium-ion batteries using CNN-BiGRU fusion model and TPE optimization. AIMS Energy, 2023, 11(5): 896-917. doi: 10.3934/energy.2023043 |
[7] | Imam Abadi, Chairul Imron, Mohammad Musa Bachrowi, Dwi Nur Fitriyanah . Design and implementation of battery charging system on solar tracker based stand alone PV using fuzzy modified particle swarm optimization. AIMS Energy, 2020, 8(1): 142-155. doi: 10.3934/energy.2020.1.142 |
[8] | Rasool M. Imran, Kadhim Hamzah Chalok . Innovative mode selective control and parameterization for charging Li-ion batteries in a PV system. AIMS Energy, 2024, 12(4): 822-839. doi: 10.3934/energy.2024039 |
[9] | Mohammed A. Al-Yasiri . Enhancing the vanadium redox flow battery efficiency by adjusting the electrode configuration. AIMS Energy, 2020, 8(5): 771-782. doi: 10.3934/energy.2020.5.771 |
[10] | Mansoor Soomro, Zeeshan Ali Shaikh, Mazhar Baloch, Abdul Manan Shaikh, Sohaib Tahir Chauhdary . Development of wind and solar systems for power charging: An application of an electric vehicle to grid systems. AIMS Energy, 2024, 12(3): 664-685. doi: 10.3934/energy.2024031 |
This paper proposes a design of energy balance circuit for two adjacent Lithium-ion battery cells in the cell string based on the modifying of the bidirectional CuK converter principle. This design only uses one MOSFET to transfer energy between two cells in a direction controlled by the first relay, second relay controls the cutting energy balance circuit off the cells when they have the same energy level. The control command sent by the management battery system (BMS) to the energy balance circuit via an RS485 communication protocol controls the direction of transferring energy, the amplitude of the balance current, the frequency and duty of PWM, the PWM signal applied to MOSFET is programmed by a microprocessor PIC18F2685. This design overcomes some disadvantages caused by applying the principle of bidirectional CuK converter to design the energy balancing circuit, these are the need for a multiple level DC source to open MOSFETs and issue of the energy loss on the elements of energy balance circuit. This design is also easy to expand for the battery string with a large number of cells. The energy balance control strategy can be implemented directly by each the energy balance circuit or remotely by BMS using RS485 communication. The experimental results of online optimal energy balance control based on state of charge (SoC) feedback for 07 SAMSUNG 22P battery cells connected in series are presented to prove the efficiency of the energy balance circuit design for two adjacent cells proposed in this paper.
Recently, there is a growing rapidly in electric vehicles with low contamination and low noise in comparison with traditional gasoline-powered vehicles. To power for electric vehicles (EV), the battery pack with a lot of cells connected in series and parallel to achieve high voltage and capacity is the main part of electric vehicles. Lithium-on battery cells are used widely for EV because of their advantages such as self-discharge rate, high density, no memory effect, and lower weight. To keep the battery pack operating safely, optimally, and protect it from overcharging/discharging, catching fire or exploding, etc., the battery management system (BMS) is equipped with the battery pack [1]. One of the main functions of BMS is energy balancing control of cells, there are two strategies for energy balancing control that is energy balancing control based on voltage and state-of-charge (SoC) feedback [2]. The energy level of cells in the string may be different in the practical operation because the cells normally are different in terms of manufacturing tolerances, different self-discharge rates, uneven operating temperature across the battery cells, and nonuniform aging process [1,4].
To ensure all cells in string operate safely and to avoid events such as over discharging, overcharging, and explosion during operation, the remaining energy of cells must be equal all the time. If a cell has lower energy than other cells, it can be over discharged, while the other cells still have energy. Consequently, that cell is damaged and may not even be able to provide electrical energy to the load. Meanwhile, if a cell has higher energy than other cells, it can be overcharged. A cell overcharged or over discharged can be exploded, caused fire, so this can damage to the devices [5]. Hence, the battery pack is usually equipped with energy balance circuits to keep the energy level of cells at the same level to avoid the states mentioned above. In practical operations, it is very important to maintain balanced energy levels in order to enhance the battery life; the remaining energy of the cell is usually presented by the SoC, the minimum SoC difference between all cells in the string must not exceed 2%.
There have been many literatures about the energy balancing control method; the two main types include active cell balancing method and passive cell balancing method. Passive balancing methods are gradually not used in energy storage system applications and electrical vehicles because they dissipate electrical energy in the power resistors and cause electrical energy wastage [6]. Active cell balancing methods use capacitors and inductors, together with switching circuits, to transfer the electrical energy from cells with higher energy levels to those with lower energy levels. So the electrical energy stored in the cells is not wasted, although the structure of the energy balancing circuit and balancing control strategy are complex, especially for a large electrical storage system with many serially connected cells. In addition, the cost of the processor for this energy balancing circuit is high.
Active cell energy balancing methods include cell bypass, cell-to-cell, cell-to-pack, pack-to-cell, and cell-to-pack-to-cell methods as presented in the materials [7,8,9]. In reference [10], all active balancing methods were compared. By analyzing the parameters, the authors showed that cell-to-cell methods are more efficient and can be used in high power applications. To realize the cell-to-cell methods, power converters have been applied to equalize the energy level of cells in the battery pack. In references [1] and [11], the authors commented that the Cuk converter is very efficient to transfer energy between two adjacent cells. The Cuk converter is a DC-DC nonisolated converter [9,12,13], it requires two inductors, one internal capacitor, and two MOSFETs to transfer or receiver the energy for every pair of adjacent cells in the string. The advantage of this converter is the control of the demanded current and the current delivered to each cell by changing the duty of the PWM signals applied to MOSFETs, which allows a smooth regulated current in both cells involved in the transfer. However, it is expensive and complex to design and implement in the practice.
There are two disadvantage problems when applying the principle of the bidirectional Cuk converter to create a energy balance circuit for the cell string: The first is that the original CuK circuit uses two MOSFETs to control the energy transfer in two directions. For the energy balancing control of n cells in the string, an n−1 energy balance circuit is required based on the conventional CuK circuit [9]. To open 2(n−1) MOSFETs in the n–1 energy balance circuit, there is the need for DC power with differential voltage levels, so it causes an inconvenience during circuit fabrication. The second is that when the energy levels of all cells are balanced, the n–1 energy balance circuit would still be connected to the cells; this will cause leakage current through the capacitors between the two cells, leading to energy loss [14]. In this study, to overcome the two above disadvantages, the energy balancing circuit is formed by using only one MOSFET and a relay to control the energy transfer between two adjacent cells; another relay is used to cut off the energy balancing circuit from the two cells when the two cells have the same energy level. When the energy levels of cells are balanced, relay 1 is opened, and the energy balance circuit is separated from the two cells; hence, the loss of electrical energy is zero. The balance control can be implemented directly by each the energy balance circuit for any two adjacent cells or remotely for all cells in the string by BMS using communication driven by a microprocessor using the RS485 communication protocol [15].
The remainder of this paper is organized as follows. In Section 2, the energy balancing circuit based on the original CuK converter and its disadvantages is presented. Section 3 presents the proposed energy balancing circuit for two adjacent cells based on the modifying of the bidirectional CuK converter. Section 4 describes the experimental results of the energy balancing control remotely based on SoC feedback. Finally, the conclusions are drawn in Section 5.
Suppose that there are n cells connected in series, n−1 energy balance circuit based on the bidirectional Cuk converter as shown in Figure 1. In general, each energy balance circuit equalizes the energy level of two adjacent cells. Figure 2 explains the energy balance circuit for cell 1 and cell 2, the energy of cell 1 is transferred to cell 2 by applying the PWM signal with desired amplitude and frequency to the left MOSFET Q1. In the switching duty cycle, the conductor L1 stores energy from cell 1, the energy stored in the capacitor C in the previous period is charged to cell 2. In the remaining time of switching period, the stored energy of L1 is transferred to C. Therefore, the energy of cell 1 is transferred to cell 2 by accumulating and transmitting the energy of inductor L1 and capacitor C. The same process is explained for transferring energy from cell 2 to cell 1, the PWM signal is applied to the right MOSFET Q2. In the switching duty cycle, the energy of cell 2 is stored in the L2, the capacitor transfers its energy to cell 1, in the remaining time of switching period, the stored energy of L2 is transferred to C [9,19]. The frequency of the PWM signal is 10kHz and higher, so the currents of L1, L2 are always operated in the transient period.
Let's consider 02 MOSFETs of the cell balance circuit (see Figure 2). Two MOSFETs have no same voltage level on their pins D and S because the pin D of MOSFET 1 and pin S of MOSFET 2 are connected. To turn on MOSFET 1, the voltage of the PWM signal in the switching duty cycle is large than V2+3.6V with 3.6V is voltage Vds of MOSFET. Similarly, to turn on MOSFET 2, the voltage of PWM signal applied to pin G is higher than V1+3.6V. Thus, to realize n−1 balance circuits for n cells connected in series, there is the need for power supply with 2(n−1) voltage levels, so the system is quite inconvenient to implement. On the other hand, when the energy levels of two adjacent cells are balanced, two MOSFETs are turned off, there is no PWM pulse on the MOSFETs, but because the electronic components are not ideal, so there are leakage currents through inductors and capacitors, this causes the dissipating unnecessarily the electrical energy of the cells.
Two things presented above are two disadvantages of applying the principle of bidirectional Cuk converter to design the cell balance circuits for cell string with ncells connected in series. In part 3, the cell balancing circuit for two adjacent cells based on the modifying of the bidirectional Cuk converter is proposed to overcome the two above disadvantages.
The cell balancing circuit i for two adjacent cells i and i+1 based on the modifying of the bidirectional CuK converter is proposed as shown in Figure 3 below, in which there is main part as 02 conductors L1, L2, capacitor C, 01 MOSFET, 02 relays, the microprocessor PIC 18F2685, 02 diodes.
Suppose that the energy level of two cells is equalized based on the SoC feedback, SoCi denote SoC of cell i, the operation principle of the cell balancing circuit is presented as follow:
When SoCs of two cells i and i+1 is balanced in range of |SoC1−SoC2|<ϵ, ϵ is the balance threshold set by technical requirements, relay 2 opens, the entire circuit including L1, L2 and capacitor Ci is isolated from two cells, there is no current leaked through the cells, inductors, and capacitors, so no electricity is wasted. When two cells have the difference of SoCs out of desired range |SoC1–SoC2|≥ϵ, relay 1 turns on, the capacitor Ci and 2 inductors L1, L2are connected to the cells, the cell balance circuit operates. If SoC1>SoC2, relay 1 turns on, the energy of cell 1 transfers to cell 2 based on the principle of the Cuk converter. If SoC2>SoC1 relay 1 turns off, the energy of cell 2 is transferred to cell 1. Microprocessor PIC18F2685 exports the PWM signal with desired duty to MOSFET and the signals to control relays in order to control the energy balance of two cells. In the switching period, the amount of energy transferred from cell to cell depends on the frequency and duty of the PWM signal applied to MOSFET. The manipulated variable of balance control loop can be choosen flexibly (duty or frequency). The communication RS485 of the energy balancing circuit with fixed address receives the message from the BMS, the BMS implements the SoC estimation, state of health (SoH) estimation, and cell balance control. The message frame is "ADD_Freq_Relay_Duty", in which:
● Add: the address of the cell balancing circuit (00 to 255)
● Freq: the frequency of PWM signal (10 kHz to 20 kHz)
● Relay:
00—turn off two relays; the cell balancing circuit is isolated from cells
10—turn on relay 2, turn off relay 1, energy of cell i transfer to cell i + 1
11—turn on relay 2, turn on relay 1, energy of cell i + 1 transfer to cell i
● Relay: switch duty (0% to 99%)
The advantages of the proposed energy balancing circuit for two adjacent cells in this work include:
● No dissipating unnecessarily the electrical energy of cells
● Expanding easily the number of energy balance circuit for the cell string with large number cells by using RS845 communication protocol
● Suitable for different energy equalizing control strategies (equalizing based on SoC or voltage of cells). The capability of remotely equalizing control via network or directly equalizing control by balancing circuit itself.
● No need for multiple level DC source to open MOSFETs of energy balance circuits.
The photo of the printed circuit board of the proposed energy balancing circuit are shown in Figure 4 below.
Figure 5 depicts the main plug circuit, it helps expand the number of energy balancing circuit for cell string with number of cells larger. In this figure, six balancing circuits are plugged in the main plug circuit to equalize for 7 cells. This design can be applied to the battery string with maximum 256 cells connected in series.
For this proposed balancing circuits, the direct or remote balancing control algorithm can be easily applied. With direct balance control, the simple balancing control algorithm (using either voltage or SoC comparison) is installed to microprocessor PIC18F2685 to balance two adjacent cells. For complicated balancing methods (optimal balance, the SoH-aware active cell balancing etc.), the control algorithm is implemented remotely by BMS using RS485 communication.
This experimental test using optimal balance control strategy using SoC feedback for battery string with 7 cells SAMSUNG 22P connected in series is conducted to proof the performing effectively of the proposed cell balance circuit in this paper. The experimental system is shown in Figure 6. The physical parameters of cell SAMSUNG 22P are listed in Table 1.
Model | ICR18650-22P |
Capacity | 2150 mAh Rated |
Voltage | 3.62 V Nominal |
Charging | 4.20 V Maximum; 1075 mA Standard; 2150 mA Maximum |
Discharging | 2.75 V Cutoff; 430 mA Standard; 10000 mA Maximum |
A measurement module is used to measure voltages of cells, current of pack and cell temperature. The voltage signals of cells are converted to 10-bit digital signals to transfer to computer via RS485 communication. The load is motor YONG-CHIDA-id67 240W,24V,10A BLDC with a maximum speed of 295rmp. The power supply is 195WOwon ODP 3032 (36V, maximum current 6A) with two programmable channels. To equalize the energy level of 07 cells, 06 proposed balance circuits in this paper are used with their parameters listed in the Table 2. The energy transferred between two adjacent cells is directly proportional to current of balance circuits, the balance current amplitude depends on the duty of PWM applied to MOSFET. In this test, the duty of PWM is ranged from 0 to 0.5which corresponds to the range of 0% to 50%.
L | C | T | f | SoCmin | SoCmax | Icmax | Idmax |
0.1 mH | 470 µF | 1s | 10 kHz | 5% | 95% | –1.5 A | 2 A |
The computer with configuration Core(TM) i3-6100 CPU 3.70 GHz 16 GB RAM is installed LABVIEW and MATLAB softwares, those software play role of the battery management systems (BMS) to estimate SoC and control optimal balance of cells. MATLAB software is used to estimate SoC of cells based on sigma-point Kalman filter and control cell balancing based on SQP algorithm [17,18]. LabVIEW 2018 is used to create the graphical user interface; the MATLAB software is embedded in LabVIEW to run the algorithms online. Flow chart of the algorithm of optimal balance control implemented in the BMS is plotted in Figure 7.
The charging/discharging and cell equalizing are conducted simultaneously in this test, the initial SoC of cells is listed in Table 3. Figure 8 depicts the varying of current in the test. The time total for the test is 3000s. In the first 600s and in the periods of time 1250s to 1800s and 2480s to 2780s, the cells were discharged with a discharge current of 1.5A. For the periods of time 600s to 1250s and 1800s to 2480s, the cells are charged with a constant current of 1A. From 1780s to 3000s, the cells are no charge/discharge. Figure 9 and Figure 10 show the changing in voltage of cells and the temperature of cell 5 during SoC balance experiment of cells. The results of the optimally equalizing process of the cells are shown in Figure 11. With the initial SoC of cells as shown in Table 3, the cells have the same SoC equal to 53% after a time of 3000s. equalizing process is stopped by BMS system when the SoC deviation of cells is within ±1%.
Cell 1 | Cell 2 | Cell 3 | Cell 4 | Cell 5 | Cell 6 | Cell 7 |
76 | 86 | 62 | 96 | 48 | 91 | 72 |
In Figure 11, for the first 600 seconds, 7 cells are discharged and equalized simultaneously, SoCs of cell 2, cell 4 and cell 6 are reduced more than the remaining cells' SoCs in the string because those cells transfer charge to adjacent cells with lower SoC levels. In the period of time from 600 seconds to 1250 seconds, the cells are charged, so the their SoC increases, but SoC of cell 4 is reduced because it transfers charge to the cell 3, cell 5. SoCs of cell 2 and cell 6 slowly increase because they transfer energy to adjacent cells with lower SoCs. SoCs of cells 3 and 5 increase strongly due to both being charged and being received charge from cells 4 and 6. SoC of cell 7 increases significantly because it is charged and received charge from cell 6 simultaneously.
At the time of 1200 seconds, two groups of cells with approximate SoC levels are formed including group of cell 6 and cell 7 and group of cell 1, cell 2, cell 3, cell 4 and cell 5. During a period of time from 1250 seconds to the 1780 seconds, the cells in the string are discharged, their SoCs are reduced, the cells with higher SoC level (cell 6, cell 7) decrease more than the others with lower SoC levels because they discharge and transfer energy simultaneously to adjacent cells with lower SoCs. During the time of 1780 seconds to 2480 seconds, all cells in the string are charged, the group of cells with lower SoC levels (cell 1, cell 2, cell 3, cell 4, cell 5) have the increasing of SoC larger than the group of cell 6 and cell 7 because they are charged and received the energy from cell 6 and cell 7 simultaneously. At the time of approximate 2500 seconds, SoC of the two groups are balanced, so all SoC of cells in the string are equal, it means that energy levels of all cells in the string are equalized.
In the period of time from 2480 seconds to 2780 seconds, all cells are discharged, so their SoCs are decreased, the SoC's decreasing rates of two groups are same because their SoCs are approximately equal. In the period of time from 2780 seconds to 3000 seconds, all cells have no charging/discharging, their energy levels are still equalized continuously, the equalizing process is ended at the time of the SoC differences of all cells in the string smaller than 1%. Figures 12 to 17 are the detailed descriptions of the energy transfering control between two adjacent cells implemented by 6 balance circuits.
Figure 12 depicts the energy transfering control between cells 1 and 2 performed by balance circuit 1. For the first 450 seconds, cell 2 transferred energy to cell 1 with maximum amplitude (duty = 0.5). At the time of 450 seconds and forward, the SoCs of two cells were nearly same, the energy transfer amplitude was gradually decreased, the duty of PWM signal was decreased from 0.5 to 0 at the time of 600 seconds, then the 2 cells had the same SoC level. For the period of 600 seconds and forwards, two cells were charged, cell 1 had a SoC higher than SoC of cell 2, because cell 2 transferred the energy to adjacent cell 3, cell 1 transferred energy to cell 2 until the time of 2780 seconds, at that time SoCs of two cells are nearly the same, then cell 2 transferred energy to cell 1 with smaller amplitude to maintain the energy equalizing process.
Similar to the explanation of Figure 12 and Figures 13 to 17 show the control of the charge transferring process to adjacent cells performed by the remaining balancing circuits. For the balance circuit 5, the energy transfer process is only conducted in the one direction from cell 6 to cell 5 for the entire equalizing process, because cell 6 initially had the highest SoC (96%), and cell 5 had the lowest SoC (48%). This test is carried out under the scenario of discharge/charge and equalizing control simultaneously, so the time for equalizing will be longer (approximately 3000 secondsas shown in the figures). If the the cells are equalized under scenario with no discharging/charging, the equalizing process could be faster.
This paper has presented the design of the energy balance circuit for two adjacent Lithium-ion battery cells in the battery string based on the modifying of the principle of bidirectional CuK converter. This design only uses 01 MOSFET to transfer energy between two adjacent cells, 1 relay to control the energy transfer direction, 01 relay to connect/disconnect the energy balance circuit to cells. The energy balance control can be implemented directly by each the energy balance circuit or remotely by BMS using RS485 communication. This balance circuit is suitable for different cell equalizing control strategies (equalizing based on SoC or voltage of cells). This design eliminates the need for a multiple level DC source to open 2n MOSFETs, which leads to inconvenience when designing n−1 energy balance circuits based on the principle of bidirectional CuK converter for a battery string with n cells connected in series. This design eliminates the energy loss on the elements of balance circuits when the cells are equalized, this design also is expanded easily for the battery string with large number of cells. The practical optimal energy equalizing control for 07 serial Samsung 22 P battery cells based on SoC feedback was implemented to prove the efficiency of the balance circuit proposed in this article. This balance circuits can be effectively applied to the balance control problem of battery with high power formed by Lithium-Ion cells in electric vehicles or in the electrical storage stations applied in renewable energy systems.
This research was supported by Thai Nguyen University of Technology, TNUT, Viet Nam.
The authors declare no conflict of interest.
[1] |
Rahimi EH, Ojha U, Baronti F, et al. (2013) Battery management system: An overview of its application in the smart grid and electric vehicles. IEEE Ind Electron Mag 7: 4–16. https://doi.org/10.1109/MIE.2013.2250351 doi: 10.1109/MIE.2013.2250351
![]() |
[2] |
Rivera Barrera JP, Muñoz Galeano N, Sarmiento-Maldonado HO (2017) SoC estimation for lithium-ion batteries: Review and future challenges. Electron 6: 102–120. https://doi.org/10.3390/electronics6040102 doi: 10.3390/electronics6040102
![]() |
[3] |
Alvarez DA, Estévez B, Adyr A, et al. (2020) A review of battery equalizer circuits for electric vehicle applications. Energ 13: 5688–5705. https://doi.org/10.3390/en13215688 doi: 10.3390/en13215688
![]() |
[4] | How Lithium-Ion batteries in EVs catch fire. Available from: https://adreesh-ghoshal.medium.com/how-lithium-ion-batteries-in-evs-catch-fire-9d166c5b3af1. |
[5] |
Wu TZ, Ji F, Liao L, et al. (2019) Voltage-SOC balancing control scheme for series-connected lithium-ion battery packs. J Energy Storage 25: 100895. https://doi.org/10.1016/j.est.2019.100895 doi: 10.1016/j.est.2019.100895
![]() |
[6] |
Hauser A, Kuhn R (2015) Cell balancing, battery state estimation, and safety aspects of battery management systems for electric vehicles. Adv Battery Technol Electr Veh 2015: 283–326. https://doi.org/10.1016/B978-1-78242-377-5.00012-1 doi: 10.1016/B978-1-78242-377-5.00012-1
![]() |
[7] |
Shang Y, Zhang C, Cui N, et al. (2015) A cell-to-Cell battery equalizer with zerocurrent switching and zero-voltage gap based on quasi-resonant LC converter and boost converter. IEEE Trans Power Electron 30: 3731–3747. https://doi.org/10.1109/TPEL.2014.2345672 doi: 10.1109/TPEL.2014.2345672
![]() |
[8] |
Cao J, Schofield N, Emadi A (2008) Battery balancing methods: A comprehensive review. IEEE Vehicle Power and Propulsion Conference 2008: 1–6. http://doi:10.1109/VPPC.2008.4677669 doi: 10.1109/VPPC.2008.4677669
![]() |
[9] |
Ouyang Q, Chen J, Xu C, et al. (2016) Cell balancing control for serially connected lithium-ion batteries. American Control Conference (ACC), 3095–3100. https://doi:10.1109/ACC.2016.7525393 doi: 10.1109/ACC.2016.7525393
![]() |
[10] |
Gallardo-Lozano J, Romero-Cadaval E, Milanes-Montero MI, et al. (2014) Battery equalization active methods. J Power Sources 246: 934–949. https://doi.org/10.1016/j.jpowsour.2013.08.026 doi: 10.1016/j.jpowsour.2013.08.026
![]() |
[11] |
Moore S, Schneider P (2001) A review of cell equalization methods for lithium ion and lithium polymer battery systems. SAE 2001 World Congress 0959: 1–7. https://doi.org/10.4271/2001-01-0959 doi: 10.4271/2001-01-0959
![]() |
[12] | Sanjaya M (2006) Switching power supplies A to Z, 1st edition, eBook, ISBN-9780080461557. Available from: https://www.elsevier.com/books/switching-power-supplies-a-z/maniktala/978-0-7506-7970-1. |
[13] |
Maksimovic D, Cuk S (1991) A unified analysis of PWM converters in discontinuous modes. IEEE Trans Power Electron 6: 476–490. https://doi.org/10.1109/63.85890[A1] doi: 10.1109/63.85890
![]() |
[14] |
Wu ST, Chang YN, Chang CY, et al. (2019) A fast charging balancing circuit for LiFePO4 battery. Electron 8: 1144. https://doi.org/10.3390/electronics8101144 doi: 10.3390/electronics8101144
![]() |
[15] |
Guo Z, Zhu H (2012) An application of communication system on the navigation light's filament status based on RS-485. 2nd International Conference on Remote Sensing, Environment and Transportation Engineering, 1–3. https://doi.org/10.1109/RSETE.2012.6260381 doi: 10.1109/RSETE.2012.6260381
![]() |
[16] |
Chi NV, Thuy NV (2020) Soc estimation of the Lithium-Ion battery pack using a Sigma point Kalman filter based on a cell's second order dynamic model. Appl Sci 10: 1896. https://doi.org/10.3390/app10051896 doi: 10.3390/app10051896
![]() |
[17] |
Christof B, Helmut M (2000) SQP-methods for solving optimal control problems with control and state constraints: adjoint variables, sensitivity analysis and real-time control. J Comput Appl Math 120: 85–108. https://doi.org/10.1016/S0377-0427(00)00305-8 doi: 10.1016/S0377-0427(00)00305-8
![]() |
[18] | Constrained nonlinear optimization algorithm, 2022. Available from: https://www.mathworks.com/help/optim/ug/constrained-nonlinear-optimizationalgorithms.html. |
[19] |
Rahman I, Riawan DC, Ashari M (2019) Design and implementation of DC-DC bidirectional Cuk converter with average current mode control for lead acid battery testing. International Seminar on Intelligent Technology and Its Applications (ISITIA) 2019: 183–188. https://doi.org/10.1109/ISITIA.2019.8937200 doi: 10.1109/ISITIA.2019.8937200
![]() |
1. | Chuanwei Zhang, Weixin Sun, Jing Huang, Zhan Xia, Chenxi Li, Xusheng Xu, Research on serial lithium‐ion battery alternating discharge equalization control systems, 2023, 11, 2050-0505, 4687, 10.1002/ese3.1608 | |
2. | Yasin Izadi, Reza Beiranvand, A Comprehensive Review of Battery and Supercapacitor Cells Voltage-Equalizer Circuits, 2023, 38, 0885-8993, 15671, 10.1109/TPEL.2023.3310574 | |
3. | Ankit Kumar Sharma, Shimi Sudha Letha, Poonam Syal, Sarita Rathee, Ajay Kumar, 2025, 9781394225019, 1, 10.1002/9781394225040.ch1 |
Model | ICR18650-22P |
Capacity | 2150 mAh Rated |
Voltage | 3.62 V Nominal |
Charging | 4.20 V Maximum; 1075 mA Standard; 2150 mA Maximum |
Discharging | 2.75 V Cutoff; 430 mA Standard; 10000 mA Maximum |
L | C | T | f | SoCmin | SoCmax | Icmax | Idmax |
0.1 mH | 470 µF | 1s | 10 kHz | 5% | 95% | –1.5 A | 2 A |
Cell 1 | Cell 2 | Cell 3 | Cell 4 | Cell 5 | Cell 6 | Cell 7 |
76 | 86 | 62 | 96 | 48 | 91 | 72 |
Model | ICR18650-22P |
Capacity | 2150 mAh Rated |
Voltage | 3.62 V Nominal |
Charging | 4.20 V Maximum; 1075 mA Standard; 2150 mA Maximum |
Discharging | 2.75 V Cutoff; 430 mA Standard; 10000 mA Maximum |
L | C | T | f | SoCmin | SoCmax | Icmax | Idmax |
0.1 mH | 470 µF | 1s | 10 kHz | 5% | 95% | –1.5 A | 2 A |
Cell 1 | Cell 2 | Cell 3 | Cell 4 | Cell 5 | Cell 6 | Cell 7 |
76 | 86 | 62 | 96 | 48 | 91 | 72 |