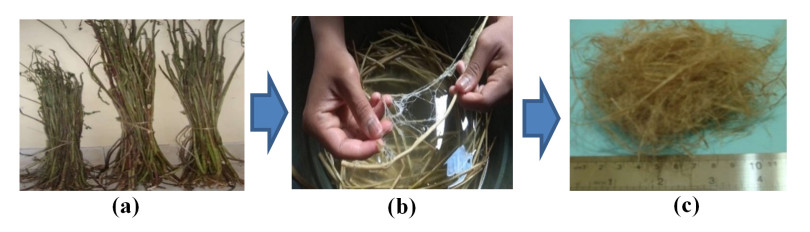
The advantage properties of stinging nettle (Urtica dioica L.) fiber compared to other natural fibers are its strength and lightweight. These fibers can be used as a substitute for synthetic fibers for reinforcing epoxy resin composite hybrid materials. This study aimed to determine the flexural properties of epoxy resin composite hybrids reinforced with stinging nettle fiber with weight ratios: 10%, 15%, and 20%, and chemical treatment of silane on the fibers: 3%, 6%, and 9%. The method of making composites was by hand lay-up, at room temperature, holding time 12 h, and using a load of 10 psi. Flexural testing used the RTG 1250 type test tool concerning the ASTM D790-3 standard. The results showed that the ratio of stinging nettle fiber composition to the epoxy resin matrix and silane treatment had a significant effect on flexural strength. Hybrid composite with 10% fiber and 3% silane treatment mode had the lowest flexural strength at 32.065 MPa and the highest flexural strength at 20% fiber and 9% silane treatment at 49.325 MPa. The highest strain was 0.0284 mm/mm in the 20% fiber and 9% treatment and the lowest was 0.0141 mm/mm in the 10% fiber and 3% silane treatment. Therefore, stinging nettle fiber-reinforced epoxy resin hybrid composites are able to withstand bending loads due to their high flexural properties. With the increase in fiber composition, the increase in silane concentration provides increased strain so that the flexural ability will be better.
Citation: Iketut Suarsana, Igpagus Suryawan, NPG Suardana, Suprapta Winaya, Rudy Soenoko, Budiarsa Suyasa, Wijaya Sunu, Made Rasta. Flexural strength of hybrid composite resin epoxy reinforced stinging nettle fiber with silane chemical treatment[J]. AIMS Materials Science, 2021, 8(2): 185-199. doi: 10.3934/matersci.2021013
[1] | Hendra Suherman, Yovial Mahyoedin, Afdal Zaky, Jarot Raharjo, Talitha Amalia Suherman, Irmayani Irmayani . Investigation of the mechanical properties of bio-composites based on loading kenaf fiber and molding process parameters. AIMS Materials Science, 2024, 11(6): 1165-1178. doi: 10.3934/matersci.2024057 |
[2] | Neerajkumar Wayzode, Vinod Suryawanshi . Mechanical properties of graphene nanoplatelets reinforced glass/epoxy composites manufactured using resin film infusion process. AIMS Materials Science, 2023, 10(4): 693-709. doi: 10.3934/matersci.2023038 |
[3] | Araya Abera Betelie, Anthony Nicholas Sinclair, Mark Kortschot, Yanxi Li, Daniel Tilahun Redda . Mechanical properties of sisal-epoxy composites as functions of fiber-to-epoxy ratio. AIMS Materials Science, 2019, 6(6): 985-996. doi: 10.3934/matersci.2019.6.985 |
[4] | Araya Abera Betelie, Yonas Tsegaye Megera, Daniel Telahun Redda, Antony Sinclair . Experimental investigation of fracture toughness for treated sisal epoxy composite. AIMS Materials Science, 2018, 5(1): 93-104. doi: 10.3934/matersci.2018.1.93 |
[5] | Prashant Tripathi, Vivek Kumar Gupta, Anurag Dixit, Raghvendra Kumar Mishra, Satpal Sharma . Development and characterization of low cost jute, bagasse and glass fiber reinforced advanced hybrid epoxy composites. AIMS Materials Science, 2018, 5(2): 320-337. doi: 10.3934/matersci.2018.2.320 |
[6] | Jaafar Sh. AbdulRazaq, Abdul Kareem F. Hassan, Nuha H. Jasim . Characterization of the mechanical properties and thermal conductivity of epoxy-silica functionally graded materials. AIMS Materials Science, 2023, 10(1): 182-199. doi: 10.3934/matersci.2023010 |
[7] | Mohammed O. Atteaa Al-hassany, Ali Al-Dulaimy, Amir Al-Sammarraie, Abed Fares Ali . Effect of fiberglass form on the tensile and bending characteristic of epoxy composite material. AIMS Materials Science, 2020, 7(5): 583-595. doi: 10.3934/matersci.2020.5.583 |
[8] | Chaitra Srikanth, G.M. Madhu, Shreyas J. Kashyap . Enhanced structural, thermal, mechanical and electrical properties of nano ZTA/epoxy composites. AIMS Materials Science, 2022, 9(2): 214-235. doi: 10.3934/matersci.2022013 |
[9] | Kiyotaka Obunai, Daisuke Mikami, Tadao Fukuta, Koichi Ozaki . Microstructure and mechanical properties of newly developed SiC-C/C composites under atmospheric conditions. AIMS Materials Science, 2018, 5(3): 494-507. doi: 10.3934/matersci.2018.3.494 |
[10] | Mohammed Y. Abdellah, Hamzah Alharthi, Mohamed K. Hassan, Ahmed F. Mohamed . Effect of specimen size on natural vibration of open hole copper/glass-reinforced epoxy laminate composites. AIMS Materials Science, 2020, 7(4): 499-517. doi: 10.3934/matersci.2020.4.499 |
The advantage properties of stinging nettle (Urtica dioica L.) fiber compared to other natural fibers are its strength and lightweight. These fibers can be used as a substitute for synthetic fibers for reinforcing epoxy resin composite hybrid materials. This study aimed to determine the flexural properties of epoxy resin composite hybrids reinforced with stinging nettle fiber with weight ratios: 10%, 15%, and 20%, and chemical treatment of silane on the fibers: 3%, 6%, and 9%. The method of making composites was by hand lay-up, at room temperature, holding time 12 h, and using a load of 10 psi. Flexural testing used the RTG 1250 type test tool concerning the ASTM D790-3 standard. The results showed that the ratio of stinging nettle fiber composition to the epoxy resin matrix and silane treatment had a significant effect on flexural strength. Hybrid composite with 10% fiber and 3% silane treatment mode had the lowest flexural strength at 32.065 MPa and the highest flexural strength at 20% fiber and 9% silane treatment at 49.325 MPa. The highest strain was 0.0284 mm/mm in the 20% fiber and 9% treatment and the lowest was 0.0141 mm/mm in the 10% fiber and 3% silane treatment. Therefore, stinging nettle fiber-reinforced epoxy resin hybrid composites are able to withstand bending loads due to their high flexural properties. With the increase in fiber composition, the increase in silane concentration provides increased strain so that the flexural ability will be better.
Stinging nettle plant (Urtica dioica L.) is an organic plant that grows in fertile soil, which can grow to a height of 1.20 meters. The stinging nettle plant has fiber in the bark and is suitable for cultivation in central Europe, tends to produce fibers with extremely high tensile strength and fineness. Apart from growing in Europe, stinging nettle also grows in all temperate regions such as Asia and North America [1]. In Asia, stinging nettle can be obtained, one of which is in the country of Indonesia, especially the Tabanan district, Bali. The property and performance enhancement of natural fiber composites is key to achieving acceptable properties similar to conventional fibres [2]. However, the weakness of natural fibers is that the bond between the matrix and the fiber is not good, resulting in weak composite properties. Chemical treatment can improve the bond between fiber and matrix so that the properties of the composite are better than without treatment [3]. Stinging nettle has good fiber in the bark of the stem. Fiber extraction from the bark can be done using the water retting method.
Chemical treatment of natural fibers is carried out by immersing them in a solution containing silicon (Si), one of the chemical treatments with a solution containing silicon is called silane treatment [4]. Silane treatment can be done by mixing the silane agent with ethanol/distilled water solution. The silane coupling agent has hydroxy groups which can be attracted to the hydroxy groups on the surface of the natural fibers so that the silane can come into contact with the matrix resin. This causes the organo-functional groups to react with the matrix resin, forming strong bonds [3].
Silane is an intermediate material that is used to make a bond between two special materials, so silane is called a coupling agent. Silane treatment is applied by mixing silane with ethanol solvent or distilled water in a ratio of 80:20, the mixing of which can be done in a container. Silane works on the interface between parts of inorganic and organic materials to combine the two types of materials. Chemical modification of natural fibers can improve adhesion between fiber and matrix. The mechanical properties increase because the interface bonds of each of the composition variations bind to each other or provide reinforcement [5,6].
Weak interfaces can be repaired by adding a coupling agent or modification to the fiber surface. Chemical modification of the nettle stem fiber surface can be done by silane treatment which can remove lignin and hemicellulose in the fiber. Silane will increase the bonding as well as avoid the loose bond between the fiber and the interface matrix during the use of the composite. Debonding occurs because the bonds between the fibers and the matrix are imperfect. This is because it is blocked by a wax-like layer on the surface of the fiber, resulting in the breaking of the bonds between the fibers and the matrix and causing holes to form in the matrix [7].
Research by Haameem et al. [8] on polymer reinforced elephant grass with short fibers, using a volume fraction calculation with a random orientation. The results obtained are the fiber fraction 10% flexural strength 32.1 MPa, at 15% flexural strength 33.6 MPa, at 20% flexural strength 37.1 MPa, and 25% flexural strength 47.9 Mpa. The results of this study also showed an increase in flexural strength due to an increase in fiber fraction.
Previous research stated that short kenaf fiber reinforced epoxy composites with 6% NaOH treatment showed that the optimal flexural strength was 46 MPa at a 40% fiber volume fraction. The flexural strength is obtained by the spray composite manufacturing method, where the resin is sprayed onto the mold surface which has been filled with kenaf fibers in a tortuous arrangement. Then the mold was heated with an electric heater at 500 ºС, for 25 min at a pressure of 6 MPa. After that, the composite was heated in an oven at 80 ºС for 12 h [9].
Previous research by Haameem et al. [8] and Ashok Kumar et al. [10] showed that composites with short fiber reinforcement and with the addition of fiber fractions provide increased ability to withstand bending loads and flexural strain. This deals with efficient load transfer between fibers–resin–fibers.
Natural fibers are an important component, which can be applied to industries such as textiles, paper making, packaging, and building materials [11]. Natural fibers have many advantages over other synthetic fibers, which include advantages such as good acoustic properties, thermal insulation, low density, low cost, and high bending strength [12]. Natural fibers treated with silane can provide better tensile strength properties compared to untreated natural fibers. In research by Asim et al. [13], fiber treatment will help develop high-performance KF and PALF reinforced polymer composites for industrial applications.
Silane treatment is widely used to modify the hygroscopic properties of natural fibers [14]. Previous studies regarding the use of silane as a treatment for natural fibers have been carried out by Sepe et al. [15], Lu et al. [16], and Alix et al. [17]. Sepe et al. [15] in their research studied the effect of alkali and silane treatments on the mechanical properties of hemp/epoxy composites. The results indicated that the alkaline treatment followed by the application of (3-glycidyloxypropyl) trimethoxysilane could improve the mechanical properties of the composites. Other studies regarding silane treatment were also conducted by Lu et al. [16] who examined the effect of silane treatment on the mechanical performance of bamboo fiber/epoxy resin composites, which gave the result that alkaline and silane treatment increased tensile strength but slightly decreased impact strength. The chemical treatment of flax fiber has also been studied by Alix et al. [17] with various chemicals, which are maleic anhydride, acetic anhydride, methacryloxy propyl trimethoxy silane, and styrene, which gave the result that only silane treatment increased the tensile modulus and strength of the flax fiber while other chemicals reduce the mechanical properties of the fiber.
Application of natural fiber (luffa) as a concrete mixture, the addition of 1% and 2% of luffa results in increased compression, stress, and bending test results [18]. Composites can be made in hybrid or bio-composite composites, testing and processing the mechanical properties of hybrid composites using graphene/epoxy with alumina [19], while the process is degradable hybrid natural fiber polymer composites [20].
This study analyzed the effect of the concentration of chemical treatment on stinging nettle fibers to determine changes in the flexural strength of hybrid composites. The solution used in the stinging nettle fiber immersion is silane. This study examined the effect of silane concentration in fibers: 3%, 6%, and 9% on the reinforcement of the epoxy composite material according to the flexural strength and strain of the composite. The method of making test specimens by hand lay-up, fiber length 5 mm, and random fiber orientation. Details of the research object and experimental protocol are presented in the materials and methods section. The measurement results will be presented and analyzed in the results and discussion section.
One of the stinging nettle plants that can be harvested is in Pupuan Village, Tabanan, Bali Indonesia and each plant that is harvested has a minimum height of 120 cm, so that the specimens have similar physical characteristics. The stems of the stinging nettle plant are then dried in the sun for about a week, then soaked in distilled water to extract the fiber. The process of taking fiber from stinging nettle plant shown in Figure 1.
The fibers were taken by decortication, that is, the fibers were carefully separated from the bark using a simple tool. The retting process was carried out at the Laboratory of Basic Phenomena of Mechanical Engineering, Udayana University. Stinging nettle fiber has an average density of 0.72 g/cm3 and a high specific stiffness [21]. Natural fibers before being used as reinforcing materials in composites must be cleaned of various impurities that can reduce the strength of the fibers.
Chemical modification of the stinging nettle stem fiber surface can be done by chemical silane treatment, which removes lignin and hemicellulose in the fiber and strengthens the adhesion of the matrix with fibers. Distilled water was used to wash the fibers, and silane was used to improve the bonding of the fibers to the matrix. The stems of nettle plants were cut into ±500 mm and dried for 4 days using sunlight. After the stems of the nettle plant were dry, the fibers were soaked in distilled water for 5 days at free air temperature until the fibers seemed to naturally separate from the stems. Nettle plant fiber that had been obtained, was dried again for 2 days. The fibers were treated with 3%, 6%, and 9% silane solutions for 2 h respectively, with the aim of removing lignin and increasing fiber adhesive. Then the fibers were cut to a length of 5 mm which were used as fiber specimens in the matrix.
Soaking with a silane solution can reduce the fiber diameter which has the potential to reduce the maximum force. Silane can be used to reduce the hydroxyl groups of fibers and provide better interface bonds between fibers and matrices. The hydrolysable alkoxy group leads to the formation of silanols to reduce water absorption. The hydroxyl groups of the fibers react with silanol, forming stable covalent bonds to the cell walls. Chemical absorption leads to the surface of the fiber. Silane is able to reduce the swelling of fibers by creating interconnected networks due to covalent bonds [22]. The comparison of fiber diameter without treatment and with treatment is shown in Figure 2.
The matrix used was unsaturated epoxy resin, which is a type of thermoset resin. Epoxy resins are a class of organic chemical bonding systems used in the preparation of special coatings or adhesives. Epoxy is a thermosetting polymer which is a reaction product of epoxy resin and amino hardener. The composition of the epoxy resin with hardner is 2:1. Hardener serves to accelerate the hardening process of the resin liquid [23].
The hand lay-up making process is a composite hybrid laminating process. The resin and reinforcement layers were manually bonded onto the exposed mold surface one by one until the desired component thickness is achieved. The specimen making was done by hand lay-up process and it is shown in Figure 3.
The next step was done by manually pouring the resin into the mold with randomly arranged fibers then applying pressure as well as leveling the surface. This process was repeated until the desired thickness is achieved. The mold can be used after applying the glycerin thinly and evenly on the inside. The resin and catalyst are mixed with a proportion of 1% catalyst in a measuring cup, after which the two components are stirred until well blended. The fiber and resin mixture is poured into the mold, leveled, and pressurized at 10 psi so that the reinforcement and binder are evenly distributed throughout the mold [23]. In this process, the resin was directly in contact with air and the molding process was carried out at room temperature. This hand lay-up method is usually used for very large components, such as the manufacture of aircraft bodies, vehicle bodies, bathtubs, boats [24].
This study examined the effect of weight fraction and silane treatment of Tabanan stinging nettle fiber on the flexural strength, strain, and elastic modulus of epoxy composite hybrid materials. The test specimen was made by hand lay-up method, using fibers with a length of 5 mm and the orientation of the random fibers in the mold as shown in Figure 3.
Testing and specimen manufacturing was carried out at the Metallurgy Laboratory of the Mechanical Engineering Study Program, Faculty of Engineering, Udayana University. The tool used in the bending test is the RTG 1250 type test tool using the ASTM D790-3 standard. The test specimen dimensions include 120.7 mm × 15 mm × 7 mm, as shown in Figure 4.
The value of bending strength depends on the type of material and loading. Flexural testing is carried out by applying pressure to the top of the specimen so that the bottom will experience tensile stress. This will result in the failure of the composite test due to the inability to withstand the tensile stress received. The flexural strength on the upper side is the same as the bending strength on the lower side. This test has been carried out by Sari and Sinarep [25] with three points bending. As illustrated in Figure 5, showed the stem specimen was pressed at the top. The calculation of bending stress uses the Eq 1 according to the ASTM D790-03 standard.
σL=3P·L2b·d2 | (1) |
where σL is flexture stress (MPa), P is flexture load (N), L is the cross-sectional length of the specimen (mm), b is the width of the specimen (mm), and d is the thickness of the specimen (mm).
The flexural strain of the specimen being tested can be calculated using the following Eq 2:
εL=6δ·dL2 | (2) |
where εL is flexural strain (mm/mm), δ is the deflection of specimen (mm), L is the distance of support (mm), and d is the thickness of specimen (mm).
The modulus of elasticity requires a straight-line tangent to the elastic region of the specimen (m). The value of m is obtained through a linear line drawn on the load and elongation graph. The modulus of elasticity can be calculated using the following Eq 3:
EL=L3·m4b·d3 | (3) |
where EL is the modulus of flexural elasticity (GPa), L is the cross-sectional length of the specimen (mm), b is the width of the specimen (mm), d the thickness of the specimen (mm), and m is the straight lines tangent of the load-deflection curve (N/mm).
Figure 6 shows the scanning electron microscope (SEM) tool used in the test. This type of tool is an SEM JEOL JSM 5900 at 10 kV with a magnification of 20, 100, and 500 µm. SEM is an electron microscope that is widely used to analyze the microstructure of composite materials. The working principle of SEM is that two-electron rays are used simultaneously. One strike specimen was used to test and the other strike is a cathode ray tube (CRT) giving an image display. SEM used X-rays that have a wavelength of 4 × 10−3 nm or about 100000 times shorter than the wavelength of visible light. The detector used in SEM is a secondary electron [26].
The process of making a composite resin hybrid test specimen began by mixing the brown fiber with a matrix according to the composition variation, and the molding process was carried out using the hand lay-up method, which is a composite hybrid laminating process. Then the composition treatment of stinging nettle fiber (A) and treatment of silane concentration (B) was made. Comparison of fiber weight composition with the concentration of silane chemical solution is (A/B). So the research design is as follows (A1/B1), (A1/B2), (A1/B3); (A2/B1) and (A2/B2); (A3/B3) as shown in Table 1. The capital letter A stands for fiber composition, B functions as a chemical concentration treatment of silane solution. The suffix number is used as a code for differences in fiber composition and differences in the concentration of the silane chemical ocean. The ratio of stinging nettle fiber and chemical treatment was 10% fiber (A1)/3% silane (B1) and 15% fiber (A2)/3% silane (B1) and 20% fiber (A3)/3% silane (B1). The differences in the weight composition of the fiber with the resin were 10%, 15%, and 20%. The test result value is the average value of the test with three repetitions, which can be seen in Table 1.
Composition | Flexure strength (MPa) | Flexure strain (mm/mm) | Modulus (GPa) |
A1/B1 | 32065 | 0.0141 | 2212 |
A1/B2 | 36367 | 0.0174 | 2285 |
A1/B3 | 40425 | 0.0178 | 2405 |
A2/B1 | 41028 | 0.0189 | 2665 |
A2/B2 | 43455 | 0.0222 | 2755 |
A2/B3 | 45874 | 0.0241 | 2825 |
A3/B1 | 46659 | 0.0248 | 2955 |
A3/B2 | 47956 | 0.0275 | 3075 |
A3/B3 | 49325 | 0.0284 | 3195 |
Figure 7 shows the stress-strain curve that occurs in a composite fiber-reinforced hybrid. The curve shows that the stress increases directly proportional to the increase in the weight fraction of the fiber. This is due to improved load transfer and stress at the fiber–resin interface, perfect resin bonding to the fibers in the fiber lamination process.
The addition of stinging nettle fiber was able to increase the composite stress, as seen from the increased flexural strength with increasing silane treatment. The larger the fiber weight fraction, the higher its flexural strength. Stinging nettle fiber treated with silane solution can increase the flexural strength, where the higher the silane concentration in the fiber treatment, the resulting increased strength and strain. This is due to the immersion of natural fiber-reinforced composites in different silane concentrations.
Theoretically, the properties of the composite material are strongly influenced by the constituents used in reinforcing the composite matrix. To improve the characteristics and performance of epoxy resin composites, hybridization is generally seen as a good solution. Comparison of fiber and silane treatment in epoxy resin matrix composites as an approach that can affect the flexural strength of the composite [8]. Flexural strength testing uses the ASTM D790-03 standard with the 3-point bending method, where the specimen is placed on two pedestals with the distance has been determined, then given the load in the middle of the pedestal with a constant loading. The value of the flexural strength is calculated from the average of 3 samples. The test results of an epoxy resin material on the fiber composition of 10% silane treatment 3% obtained the lowest flexural strength of the composite hybrid at 32.065 MPa and the highest flexural strength composition of 20% fiber with 9% silane treatment was 49.325 MPa. The flexural strength of the stinging nettle composite increased with the addition of the fiber fraction composition in the matrix. The increased flexural strength of the stinging nettle fiber reinforcing composites was due to the addition of fiber weight fraction and the increase in the chemical solution treatment of silane. This is due to the more the fibers are evenly distributed, the flexural load is more evenly distributed between the fibers and the adhesive ability increases.
Figure 8 shows the flexural strength of the jelatang fiber reinforced epoxy resin composite on silane concentration treatment. Comparison of fiber reinforcement in the matrix shows that the flexural strength of the fiber composition A1, A2, A3 and chemical treatment of silane B1, B2, and B3 increases linearly. This can be seen in the composition A1/B1, the flexural strength of 32.065 MPa and the composition of A1/B2 is 36.367 MPa and the composition of A1/B3 is 40.425 MPa. The variation of the weight fraction between the fibers and the matrix as a composite constituent greatly affects the bending stress value, where the greater the fiber weight fraction, the higher the bending stress because the high number of fibers can withstand a large bending load. This is due to whether the bonds are homogeneous or not between the fibers and the matrix, as shown in relationship between fiber weight fraction and flexural strength. In this study, the concentration of silane solution also gave the effect of increasing the flexural strength from a concentration of 3% to 9%. This is because the diameter is increasingly shrinking and denser due to the treated fibers, which can be seen in the comparison of fiber diameter without and with treatment. The percentage increase in flexural strength from composition and treatment (A1/B1) to treatment (A3/B1) by an average of 7.37%. As research by Haameem et al. [8] on polymers reinforced with elephant grass fiber with short fibers, using a volume fraction calculation with a random orientation, also shows an increase in flexural strength due to an increase in fiber fraction.
Figure 9 shows the flexural strain of a hybrid composite with differences in fiber composition and silane treatment. The flexural strain on composite hybrid specimens were tested with variations in fiber weight fraction of 10%, 15%, and 20% and silane chemical treatment of 3%, 6%, and 9%. The flexural strain value was calculated from the average of the three treatment samples. The results of the epoxy resin material test at 10% fiber composition with 3% silane treatment obtained the lowest composite hybrid flexural strain (A1/B1) at 0.0141 mm/mm and the highest flexural strain composition of 20% fiber with 9% silane treatment (A3/B3) of 0.0284 mm/mm. Hybridization is an effective means of changing the flexural tensile properties of composite materials. The flexural strain results were 0.0241 mm/mm at 15% fiber composition, 9% silane treatment (A2/B3) and 0.0189 mm/mm at 15% fiber composition 3% silane treatment (A2/B1). As shown in Figure 9, the results of the flexural strain on the specimens with the fiber weight fraction and constituent matrices have increased. This can occur due to the increasing number of fibers and having a homogeneous bond between the fibers and the optimal matrix. The amount of fiber composition that is too much or too little will affect the deflection value acting on the specimen. With the addition of the fiber weight fraction in the composite, there was a significant increase in the flexural strain. As research by Haameem et al. [8] and Ashok Kumar et al. [10] states that short fiber-reinforced composites and the addition of fiber fractions cause the ability to withstand flexural loads and increased flexural strain. This deals with efficient load transfer between fibers–resin–fibers.
Figure 10 shows the results of testing the fiber weight fraction in the matrix to the flexural modulus with three types of weight fraction variations in the fiber and silane chemical treatment. This test used a fiber weight ratio: 10, 15, and 20%, and silane treatment of 3%, 6%, and 9%. For the composition of the fiber in the composite 10% showed the flexural modulus of 2.214, 2.285, and 2.405 GPa, respectively. The fiber composition of the 15% composite showed the flexural modulus: 2.665, 2.755, and 2.825 GPa, respectively. The fiber composition of the 20% composite showed the flexural modulus: 2.955, 3.075, and 3.195 GPa, respectively. It can be concluded that the lowest bending modulus at 10% fiber composition by weight is 2.214 GPa and the largest modulus occurs at 20% fiber composition at 3.195 GPa. The value of the bending modulus was influenced by the value of m (tangent straight line on the load deflection curve). The m value was obtained from the comparison between the load received and the strain that occurs in the specimen so that the m value was strongly influenced by the proportion of fibers with the optimum matrix in the specimen. This can be seen in the highest flexural modulus value of the specimen at the composition of 20% fiber. This result is supported by research by Haameem et al. [8] on the tensile modulus for fiber fraction 10% tensile modulus 2.20 GPa, at 15% tensile modulus 2.40 GPa, at 20% tensile modulus 2.70 GPa, and 25% tensile modulus 3.20 Gpa. The results of this study provide the same statement as research on hybrid stinging nettle epoxy resin composites about an increase in the flexural modulus due to an increase in fiber fraction. This is also supported by research that natural fibers have mechanical properties, which in the longitudinal section have tensile toughness of 10.8 Mpa, the elastic modulus of 387.4 MPa, split toughness of 5.03%, and in the cross-section have tensile toughness of 4.32 MPa, elastic modulus of 169.3 MPa and split toughness of 3.7% [27].
Figure 11 depicts the internal condition of the hybrid composite after testing. The internal condition of the specimens was confirmed using a scanning electron microscope (SEM) JEOL JSM 5900 at 10 kV. As can be seen in the results of the 10% fiber weight fraction of 3% Silane treatment which has the lowest flexural strength, SEM observations of Figure 11a show that there are pull out fibers from the matrix, and it can be seen that the distribution of fibers in the test material was not quite evenly agglomeration in the matrix. Furthermore, in Figure 11b, c the fibers appear to be stronger and more even and the pullout decreases from the matrix.
The results showed that the composition of the fiber weight fraction and silane chemical treatment had a significant effect on the flexural properties of composite hybrids. Hybrid composites with the sequence mode A1/B1, the lowest bending strength 32.065 MPa, the flexural strain 0.0141 mm/mm, the bending modulus of 2.214 GPa and the highest in the A3/B3 order mode, the flexural strength was 49.325 MPa, the flexural strain is 0.0284 mm/mm, the modulus 3.195 GPa. Furthermore, it was shown that epoxy resin hybrid composites can operate as a marine vessel body material, a vehicle body that is able to accept bending loads. It can be concluded that the composition and treatment of fibers in a hybrid composite of epoxy resin reinforced with stinging nettle fiber has a significant effect, so it is effective to modify the composite material in engineering materials. In fact, Tabanan stinging nettle fiber has a higher flexural strength than other natural fibers. Therefore, it is an excellent composite reinforcing material. Furthermore, it can be concluded that fiber composition is an effective factor affecting the characteristics and structure of the material.
The author is grateful to the Republic of Indonesia, Ministry of Research, Technology and Higher Education, Head of the Laboratory of Phenomenon of Udayana University, Mechanical Engineering Study Program, Faculty of Engineering Brawijaya University for providing facilities and supporting the realization of this research.
All authors declare no conflicts of interest in this paper.
[1] | Hegi G (1998) Illustrierte Flora von Mitteleuropa I/3. Spermatophyta. Angiospermae. Monocotyledones 1(2), 3 Eds., Berlin: Blackwell Verlag GmbH. |
[2] |
Mulenga TK, Ude AU, Vivekanandhan C (2020) Concise review on the mechanical characteristics of hybrid natural fibres with filler content. AIMS Mater Sci 7: 650-664. doi: 10.3934/matersci.2020.5.650
![]() |
[3] |
Xie Y, Hill CAS, Xiao Z, et al. (2010) Silane coupling agents used for natural fiber/polymer composites: A review. Compos Part A-Appl S 41: 806-819. doi: 10.1016/j.compositesa.2010.03.005
![]() |
[4] |
Kushwaha PK, Kumar R (2010) Studies on water absorption of bamboo-polyester composites: Effect of silane treatment of mercerized bamboo. Polym-Plast Technol 49: 45-52. doi: 10.1080/03602550903283026
![]() |
[5] |
Jesson DA, Watts JF (2012) The interface and interphase in polymer matrix composites: Effect on mechanical properties and methods for identification. Polym Rev 52: 321-354. doi: 10.1080/15583724.2012.710288
![]() |
[6] |
Suarsana K, Soenoko R (2015) Hardness, density and porosity of Al/(SiCw+Al2O3p) composite by powder metallurgy process without and with sintering. Appl Mech Mater 776: 246-252. doi: 10.4028/www.scientific.net/AMM.776.246
![]() |
[7] | Maryanti B, Sonief A, Wahyudi S (2011) Effect of alkalization of coconut-polyester fiber composites on tensile strength. Mech Eng 2: 123-129. |
[8] |
Haameem M, Majid MS, Afendi M, et al. (2016) Mechanical properties of Napier grass fibre/polyester composites. Compos Struct 136: 1-10. doi: 10.1016/j.compstruct.2015.09.051
![]() |
[9] |
Aziz SH, Ansell MP (2004) The effect of alkalization and fibre alignment on the mechanical and thermal properties of kenaf and hemp bast fibre composites: Part 1—polyester resin matrix. Compos Sci Technol 64: 1219-1230. doi: 10.1016/j.compscitech.2003.10.001
![]() |
[10] |
Kumar MA, Reddy GR, Bharathi YS, et al. (2010) Frictional coefficient, hardness, impact strength, and chemical resistance of reinforced sisal-glass fiber epoxy hybrid composites. J Compos Mater 26: 3195-3202. doi: 10.1177/0021998310371551
![]() |
[11] |
Ashori A (2006) Nonwood fibers—A potential source of raw material in papermaking. Polym-Plast Technol 45: 1133-1136. doi: 10.1080/03602550600728976
![]() |
[12] |
Petchwattana N, Covavisaruch S (2014) Mechanical and morphological properties of wood plastic biocomposites prepared from toughened poly (lactic acid) and rubber wood sawdust (hevea brasiliensis). J Bionic Eng 11: 630-637. doi: 10.1016/S1672-6529(14)60074-3
![]() |
[13] |
Asim M, Jawaid M, Abdan K, et al. (2016) Effect of alkali and silane treatments on mechanical and fibre-matrix bond strength of kenaf and pineapple leaf fibres. J Bionic Eng 13: 426-435. doi: 10.1016/S1672-6529(16)60315-3
![]() |
[14] |
Fathi B, Foruzanmehr M, Elkoun S, et al. (2019) Novel approach for silane treatment of flax fiber to improve the interfacial adhesion in flax/bio epoxy composites. J Compos Mater 53: 2229-2238. doi: 10.1177/0021998318824643
![]() |
[15] |
Sepe R, Bollino F, Boccarusso L, et al. (2017) Influence of chemical treatments on mechanical properties of hemp fiber reinforced composites. Compos Part B-Eng 133: 210-217. doi: 10.1016/j.compositesb.2017.09.030
![]() |
[16] |
Lu T, Jiang M, Jiang Z, et al. (2013) Effect of surface modification of bamboo cellulose fibers on mechanical properties of cellulose/epoxy composites. Compos Part B-Eng 51: 28-34. doi: 10.1016/j.compositesb.2013.02.031
![]() |
[17] |
Alix S, Philippe E, Bessadok A, et al. (2009) Effect of chemical treatments on water sorption and mechanical properties of flax fibres. Bioresource Technol 100: 4742-4749. doi: 10.1016/j.biortech.2009.04.067
![]() |
[18] | Sen S, Ankit (2018) An experimental study of concrete mix by adding natural fiber (zucchini fiber/luffa fiber). Int J Civ Eng Technol 9: 724-732. |
[19] | Shetty D, Shetty N (2019) A literature review on processing and testing of mechanical properties of hybrid composites using graphene/epoxy with alumina. Int J Mech Eng Technol 10: 1263-1274. |
[20] | Alex S, Retnam SJ (2014) A review on degradable hybrid natural fibre polymer composites. Int J Des Manuf Technol 5: 137-141. |
[21] | Bacci L, Baronti S, Predieri S, et al. (2009) Fiber yield and quality of fiber nettle (Urtica dioica L.) cultivated in Italy. Ind Crop Prod 29: 480-484. |
[22] |
Ali A, Shaker K, Nawab Y, et al. (2018) Hydrophobic treatment of natural fibers and their composites—A review. J Ind Text 47: 2153-2183. doi: 10.1177/1528083716654468
![]() |
[23] | Suryawan IGP, Suardana NPG, Winaya INS, et al. (2020) A study on correlation between hardness and thermal conductivity of polymer composites reinforced with stinging nettle fiber. Int J Civ Eng Technol 11: 94-104. |
[24] | Biswas S, Anurag J (2019) Fabrication of composite laminates, In: Bajpai PK, Singh I, Reinforced Polymer Composites: Processing, Characterization and Post Life Cycle Assessment, 1 Ed., New Jersey: John Wiley & Sons, 39-53. |
[25] | Sari NH, Sinarep S (2011) Analysis of bending strength of epoxy composites with nylon fiber reinforcement. Mech Eng Dynam 1: 1-6. |
[26] |
Choudhary OP, Choudhary P (2017) Scanning electron microscope: advantages and disadvantages in imaging components. Int J Curr Microbiol Appl Sci 6: 1877-1882. doi: 10.20546/ijcmas.2017.605.207
![]() |
[27] | Huda S (2008) Composites from chicken feather and cornhusk—preparation and characterization[PhD's thesis]. University of Nebraska, Lincoln. |
1. | Manash Protim Mudoi, Shishir Sinha, Vijay Parthasarthy, Polymer composite material with nettle fiber reinforcement: A review, 2021, 16, 2589014X, 100860, 10.1016/j.biteb.2021.100860 | |
2. | Fazilay Abbès, Shihua Xu, Boussad Abbès, Characterization of Mechanical and Damping Properties of Nettle and Glass Fiber Reinforced Hybrid Composites, 2022, 6, 2504-477X, 238, 10.3390/jcs6080238 | |
3. | Manash Protim Mudoi, Shishir Sinha, Vijay Parthasarthy, Optimizing the alkali treatment of cellulosic Himalayan nettle fibre for reinforcement in polymer composites, 2022, 296, 01448617, 119937, 10.1016/j.carbpol.2022.119937 | |
4. | Manash Protim Mudoi, Shilpi Agarwal, Shailey Singhal, Abhimanyu Singh Khichi, 2022, Chapter 199-1, 978-981-16-4921-9, 1, 10.1007/978-981-16-4921-9_199-1 | |
5. | I. G. P. Agus Suryawan, N. P. G. Suardana, Iketut Suarsana, Wayan Widhiada, Linggih Sulenggar Putra, 2023, 2568, 0094-243X, 040020, 10.1063/5.0115011 | |
6. | Ayodele Abraham Ajayi, Mohan Turup Pandurangan, Krishnan Kanny, Influence of hybridizing fillers on mechanical properties of foam composite panel, 2023, 63, 0032-3888, 2565, 10.1002/pen.26396 | |
7. | Yasuyuki KANDA, Ryosuke HIGA, Compression molding of hybrid composite material using waste concrete powder and bagasse fiber, 2024, 90, 2187-9761, 24-00038, 10.1299/transjsme.24-00038 | |
8. | Tomasz M. Majka, Radosław Piech, Marcin Piechaczek, Krzysztof Adam Ostrowski, The Influence of Urtica dioica and Vitis vinifera Fibers on the Thermal Properties and Flammability of Polylactide Composites, 2024, 17, 1996-1944, 1256, 10.3390/ma17061256 | |
9. | Sivasubramanian Palanisamy, Mayandi Kalimuthu, Carlo Santulli, Murugesan Palaniappan, Rajini Nagarajan, Cristiano Fragassa, Tailoring Epoxy Composites with Acacia caesia Bark Fibers: Evaluating the Effects of Fiber Amount and Length on Material Characteristics, 2023, 11, 2079-6439, 63, 10.3390/fib11070063 | |
10. | Manash Protim Mudoi, Shishir Sinha, Vijay Parthasarthy, Himalayan nettle fibre-reinforced polymer composite: a physical, mechanical, and thermal analysis, 2023, 2190-6815, 10.1007/s13399-023-04819-0 | |
11. | Dharna Bhardwaj, Anand Giri, Vinod Kumar, Vimal Chandra Srivastava, Nettle (Urtica spp.) phytotomy and applications: Crop variety selection and advanced product development for the manufacturing of natural fiber composites, 2024, 210, 09266690, 118180, 10.1016/j.indcrop.2024.118180 | |
12. | Danuta Matykiewicz, Beata Dudziec, Katarzyna Skórczewska, Kamila Sałasińska, The Effect of Silanes Treatments on Thermal and Mechanical Properties of Nettle Fibre/Bio Epoxy Composites, 2024, 21, 1544-0478, 10.1080/15440478.2024.2332913 | |
13. | Ioana-Maria Toplicean, Rebeca-Didina Ianuș, Adina-Daniela Datcu, An Overview on Nettle Studies, Compounds, Processing and the Relation with Circular Bioeconomy, 2024, 13, 2223-7747, 3529, 10.3390/plants13243529 | |
14. | Manash Protim Mudoi, Shilpi Agarwal, Shailey Singhal, Abhimanyu Singh Khichi, 2025, Chapter 199, 978-981-97-4617-0, 213, 10.1007/978-981-97-4618-7_199 |
Composition | Flexure strength (MPa) | Flexure strain (mm/mm) | Modulus (GPa) |
A1/B1 | 32065 | 0.0141 | 2212 |
A1/B2 | 36367 | 0.0174 | 2285 |
A1/B3 | 40425 | 0.0178 | 2405 |
A2/B1 | 41028 | 0.0189 | 2665 |
A2/B2 | 43455 | 0.0222 | 2755 |
A2/B3 | 45874 | 0.0241 | 2825 |
A3/B1 | 46659 | 0.0248 | 2955 |
A3/B2 | 47956 | 0.0275 | 3075 |
A3/B3 | 49325 | 0.0284 | 3195 |