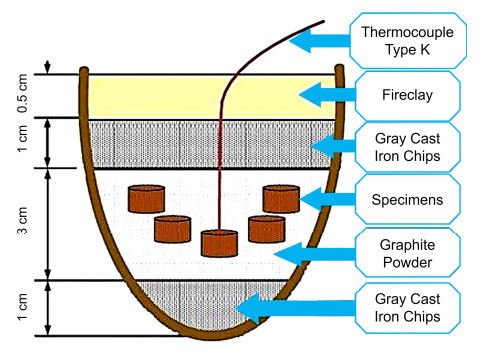
Nanoparticles of metal and other materials are a proven reinforcing material for producing a high-performance aluminum composite utilized in modern engineering applications. The ultrasonic mixing process is conducted to ensure a typical distribution of nanoparticles in the aluminum matrix. The present work aims to study the effect of copper nanoparticles on microhardness and physical properties of Al-composite prepared by powder metallurgy techniques with ultrasonic mixing. The aluminum nanocomposites were fabricated with different volume fractions (0, 5, 10, 15, 20, and 25 wt%) of Cu nanoparticles. To examine the effectiveness of the mixing, compacting, and sintering process, nanocomposites were characterized using field emission scanning electron microscopy (FESEM) and energy-dispersive X-ray (EDX) and elemental mapping analysis. A uniform distribution of Cu nanoparticles was established within the Al matrix. The composite was characterized by an increase in density and a decrease in porosity with increased Cu nanoparticles. Increasing Cu nanoparticles enhanced the mechanical properties of the Al-Cu composite through an increase in its hardness. A direct relationship between Cu nanoparticles and thermal and electrical conductivity was found; in particular, there was a distinct enhancement in electrical conductivity, as the composite with 25 wt% Cu nanoparticles reached 78.87% of the electrical conductivity of pure Cu.
Citation: Omar Hassan Mahmood, Mustafa Sh. Aljanabi, Farouk M. Mahdi. Effect of Cu nanoparticles on microhardness and physical properties of aluminum matrix composite prepared by PM[J]. AIMS Materials Science, 2025, 12(2): 245-257. doi: 10.3934/matersci.2025013
[1] | Abdulkader A. Annaz, Saif S. Irhayyim, Mohanad L. Hamada, Hashim Sh. Hammood . Comparative study of mechanical performance between Al–Graphite and Cu–Graphite self-lubricating composites reinforced by nano-Ag particles. AIMS Materials Science, 2020, 7(5): 534-551. doi: 10.3934/matersci.2020.5.534 |
[2] | Saif S. Irhayyim, Hashim Sh. Hammood, Hassan A. Abdulhadi . Effect of nano-TiO2 particles on mechanical performance of Al–CNT matrix composite. AIMS Materials Science, 2019, 6(6): 1124-1134. doi: 10.3934/matersci.2019.6.1124 |
[3] | Omar Bataineh, Abdullah F. Al-Dwairi, Zaid Ayoub, Mohammad Al-Omosh . DOE-based experimental investigation and optimization of hardness and corrosion rate for Cu-x%Al2O3 as processed by powder metallurgy. AIMS Materials Science, 2021, 8(3): 416-433. doi: 10.3934/matersci.2021026 |
[4] | H. Naresh, S. Prashantha, N.R. Banapurmath, M.A. Umarfarooq, Chandramouli Vadlamudi, Sanjay Krishnappa . Mechanical, fatigue, and superplasticity properties of Cu-Al-Mn, Cu-Al-Be-Mn shape memory alloy and their metal matrix composites. AIMS Materials Science, 2024, 11(1): 129-149. doi: 10.3934/matersci.2024008 |
[5] | Marek Konieczny . Mechanical properties and wear characterization of Al-Mg composites synthesized at different temperatures. AIMS Materials Science, 2024, 11(2): 309-322. doi: 10.3934/matersci.2024017 |
[6] | Saif S. Irhayyim, Hashim Sh. Hammood, Anmar D. Mahdi . Mechanical and wear properties of hybrid aluminum matrix composite reinforced with graphite and nano MgO particles prepared by powder metallurgy technique. AIMS Materials Science, 2020, 7(1): 103-115. doi: 10.3934/matersci.2020.1.103 |
[7] | Reginald Umunakwe, Ifeoma Janefrances Umunakwe, Uzoma Samuel Nwigwe, Wilson Uzochukwu Eze, Akinlabi Oyetunji . Review on properties of hybrid aluminum–ceramics/fly ash composites. AIMS Materials Science, 2020, 7(6): 859-870. doi: 10.3934/matersci.2020.6.859 |
[8] | Mohammed Nizam Khan, Sumesh Narayan, Ananthanarayanan Rajeshkannan . Influence of process parameters on the workability characteristics of sintered Al and Al–Cu composites during cold deformation. AIMS Materials Science, 2019, 6(3): 441-453. doi: 10.3934/matersci.2019.3.441 |
[9] | Bao Zhang, Xudong Wang, Liu Chen, Xingwu Li . Dynamic behavior of graphene reinforced aluminum composites. AIMS Materials Science, 2018, 5(2): 338-348. doi: 10.3934/matersci.2018.2.338 |
[10] | Ehsan Harati, Paul Kah . Laser welding of aluminum battery tab to variable Al/Cu busbars in Li-ion battery joint. AIMS Materials Science, 2022, 9(6): 884-918. doi: 10.3934/matersci.2022053 |
Nanoparticles of metal and other materials are a proven reinforcing material for producing a high-performance aluminum composite utilized in modern engineering applications. The ultrasonic mixing process is conducted to ensure a typical distribution of nanoparticles in the aluminum matrix. The present work aims to study the effect of copper nanoparticles on microhardness and physical properties of Al-composite prepared by powder metallurgy techniques with ultrasonic mixing. The aluminum nanocomposites were fabricated with different volume fractions (0, 5, 10, 15, 20, and 25 wt%) of Cu nanoparticles. To examine the effectiveness of the mixing, compacting, and sintering process, nanocomposites were characterized using field emission scanning electron microscopy (FESEM) and energy-dispersive X-ray (EDX) and elemental mapping analysis. A uniform distribution of Cu nanoparticles was established within the Al matrix. The composite was characterized by an increase in density and a decrease in porosity with increased Cu nanoparticles. Increasing Cu nanoparticles enhanced the mechanical properties of the Al-Cu composite through an increase in its hardness. A direct relationship between Cu nanoparticles and thermal and electrical conductivity was found; in particular, there was a distinct enhancement in electrical conductivity, as the composite with 25 wt% Cu nanoparticles reached 78.87% of the electrical conductivity of pure Cu.
Powder metallurgy (PM) is the most appropriate method for obtaining metal matrix composites. Its most significant advantage when compared with melting methods is a low processing temperature, resulting in no undesirable phases between the reinforcement and matrix. Furthermore, it also results in a good distribution of the reinforcement particles within the matrix at high combinations and allows near-net-shape parts, which are cost-effective. Parts made by PM have better properties than those produced through other processes (e.g., casting). This process is quick and it results in large quantities, hence being economical for powder metallurgy components [1].
Metal matrix composites (MMCs) are a particular type of composite material consisting of a matrix phase composed of metal or alloys and another component embedded in this metal matrix usually working as reinforcement. PM results in the possibility of regulating physical and mechanical properties by selecting suitable matrices and volume fractions of the reinforcement. Pricewise, composite manufacturing can be considered a cheap procedure due to its outstanding performance [2,3].
Aluminum matrix composites (AMCs) are still being extensively investigated by researchers despite the large amount of literature. AMCs are successfully used in several industries, such as aerospace, defense, automobile, and marine industries [4,5,6,7].
Copper nanoparticles (CuNps) became popular due to their great physical properties, unique among all metals. Cooper presents exclusive optical, thermal, and electrical features that render its wide usage, ranging from chemical sensors to photovoltaics [8]. Nowadays, CuNps are already standardly applied in antimicrobial coatings, wound dressings, keyboards, or biomedical devices. CuNps have also been recently considered as an alternative for noble metals in many applications [9,10] including electronics and heat transfer. Recent advances, such as in nanoparticle synthesis, facilitate the incorporation of these particles into composites, thereby significantly enhancing their mechanical properties [11,12].
Ultrasonic mixing is a technique that relies on the effective use of ultrasonic waves to thoroughly harness nanoparticles in different matrices. This technique is very efficient in solving problems related to the breakage of agglomerates and the proper distribution of nanoparticles. It includes the use of cavitation as well as acoustic streaming, which facilitates a uniform distribution of nanoparticles while enhancing the interfacial interactions between the particles and the matrix. This technique has resulted in improved mechanical and physical properties [13].
The incorporation of CuNps into aluminum (Al) composites significantly enhances their mechanical properties and microstructural characteristics. For instance, the addition of CuNp in Al nanocomposites, particularly when combined with graphene nanoplatelets (GNPs), results in a homogeneous distribution and the formation of intermetallic compounds such as Cu9Al4, which contribute to improved hardness and compressive strength. Specifically, the hardness of Al/Cu reinforced with 1.8 wt% GNPs increased by 51.9%, and the compressive stress reached 266.99 MPa [14].
In a previous study, two different methods of sintering were compared: vacuum sintering (VS) and microwave sintering (MS). The research revealed that AMCs strengthened with Cu particles displayed a homogeneous distribution of Cu particles within the Al framework as observed through microstructural analysis. This even distribution plays a role in maintaining mechanical properties across the material. Both hardness and compressive strength increased with increasing Cu content in the Al matrix. Specifically, for Al–9 vol.% Cu composite sintered using microwaves, there was a 137.2% increase in hardness and a 30.3% increase in strength. This enhancement can be attributed to the presence of copper particles that fortify the aluminum matrix [15]. The addition of Cu particles to Al-SiC matrix composites not only enhanced compressibility but also greatly improved thermal conductivity by approximately 100% with an increase in Cu content (from 0% to 30%) [16].
These research findings show how CuNps is essential for enhancing the microhardness and physical properties of Al composites in different applications. Therefore, our current study aims to explore how the presence of CuNps mixed by ultrasonic technique with Al microparticles influences the microhardness and physical properties of Al-Cu composites.
Al-CuNps composites with up to 25 wt% CuNps were prepared to enhance electrical and thermal conductivity while increasing hardness. The reinforcement of nano-copper powder in the Al-based composite was carried using the minimum necessary amount of copper, as higher copper content increases both the cost and density of the composite. The Al-CuNps composites were prepared using aluminum powder with 99.0% purity and a particle size of 50–100 µm, along with CuNps with 99.9% purity and 30 nm mean particle size. An electric balance with 0.00001 g accuracy was used to weigh metal powders. The powders were then suspended in 60 mL of ethanol (USP grade, 99.9%). The suspension was then ultrasonically agitated for 10 min using a VC40 Vibra-cell power unit. After ultrasonication, the suspension was dried in an oven at 110 ℃ for 24 h. The dried mixture was collected in a sealed vial. After obtaining a homogenous mixture, the powder was pressed at 500 MPa using a cylindrical steel mold with a hardness of 60 HRC. A uniaxial pressure was applied for 1 min using a universal testing machine with a 17-ton capacity to avoid elastic return. Cylindrical specimens with 10 mm in diameter and 6 mm in height were prepared for all Al-CuNps composites. The green specimens were sintered at 500 ℃ for 1 h in a muffle furnace. To protect the samples from oxidation, they were placed inside a ceramic container and surrounded by multilayers of graphite powder and gray cast iron chips with fireclay, as shown in Figure 1. This configuration was found to provide excellent protection against atmospheric oxygen.
To obtain results for all tests, three samples were measured for each percentage, and results were determined as the average.
Experimental density was measured according to ASTM B 962-08 by using the Archimedes principle. Theoretical density was calculated using the mixture rule. The difference between the theoretical density and experimental density was used to calculate the total porosity of the sintered specimens.
The metallographic characterization of the prepared composite samples was done using scanning electron microscopy (SEM) (JEOL, JSM-6510LV, Japan).
The hardness test was conducted in accordance with the ASTM E-384 standard on the prepared composite samples. The hardness of the composites was measured by applying a direct load of 500 g for 10 s on flat, smooth, polished, plane-parallel specimens of the composites using the digital automatic Micro Hardness Vickers HVST-1000z tester. Five measurements were performed on each sample, and their average was taken as a measure of the hardness of the specimen.
A heat conduction unit (P.A. Hilton Ltd, England) was used to determine thermal conductivity. Electrical conductivity was calculated using the Wiedemann–Franz law (Eq 1) [18]:
(1) |
Figure 2 illustrates the effects of copper content on the density of the Al-CuNp composite. Both theoretical and experimental densities increase as the Cu content increases. The increase in experimental density is first due to the higher density of Cu (8.94 g/cm3) compared to Al (2.7 g/cm3) and second to the nano size of Cu particles, which can improve the packing density of the material since they are small enough to fill gaps between aluminum particles. Moreover, CuNps present within the material can result in increased sintering process efficiency. These nanoparticles act as diffusion catalysts during sintering by facilitating atomic migration, resulting in material densification. Thus, a microstructure with less gaps and imperfections arises, thereby reducing porosity levels.
Figure 3 reveals the effect of copper content on the porosity of the Al-CuNps composite. Increasing the wt% of CuNps in the Al matrix decreases the porosity of the composite. This is due to the filling effect of CuNps in reducing the gaps between Al particles, even at Cu contents as high as 25 wt%. Another factor responsible for such reduced porosity is the role of CuNps in enhancing the densification of the composite during sintering by improving and accelerating atomic diffusion by providing a continuous path for this process.
Figures 4–6 showed the optical microscopy and FESEM images, EDX spectrum, and elemental mapping analysis for the Al composite with 10, 15, and 20 wt% of CuNps. These figures show a uniform distribution of CuNps within the prepared composite, indicating the effectiveness of the mixing procedure of ethanol/powder suspension and ultrasonic mixing.
The hardness values of the produced composites are presented in Figure 7. The hardness of Al-CuNps composites increased with an increased percentage of CuNps, and when compared to the unreinforced Al matrix. Hardness increased from 31 Hv0.5 to 172 Hv0.5 when Cu content increased from 0% to 25%, respectively. Several factors contribute to this:
● The higher hardness of copper compared with aluminum.
● The filling effect of CuNps and the concomitant effect in reducing porosity to a minimal value.
● This enhancement is primarily due to the effective dispersion and interaction of nanoparticles within the aluminum matrix, which is achieved through the ultrasonic mixing process.
● The role of CuNps in enhancing the diffusion process during sintering results in a better densification and consolidation of the produced composites with higher hardness. This is also supported by the results in [19].
● Predicted formation of hard intermetallic phases at the interface between Al and Cu particles; such phase includes Al2Cu and Al9Cu4 [20].
● The difference in thermal conductivity between aluminum and copper reduces thermal stress, accompanied by an increase in dislocation density at the interface. This higher dislocation density results in higher hardness of the composite [21].
Figures 8 and 9 show the effect of CuNps content on the thermal and electrical conductivity of the Al-CuNp composites, respectively. An increase in both conductivities was found with increased CuNp content, and the correlation was linear. Thermal and electrical conductivity increased from 241 to 321 W/m/K and from 32.2 × 106 to 43.85 × 106 S/m on increasing Cu content from 0% to 25%, respectively. This increase in conductivity is attributed to the high thermal and electrical conductivity of Cu (407 W/m/K and 55.6 × 106 S/m), as well as its effect as filler material, which increases the actual cross-section of the material by decreasing its porosity. Also, CuNps enhance both the densification and consolidation of the sintered composite. Enhancing the interface bonding also contributes to increased conductivities. The cavitation and acoustic streaming effects of ultrasonication ensure that nanoparticles are evenly dispersed, which is essential for maximizing the reinforcing effects of the nanoparticles. The electrical conductivity of composites with 25% Cu was 78.87% of the electrical conductivity of pure copper. This suggests a promising use of Al nanocomposites in electric and electronic applications, which require a combination of high electronic conductivities and light weight.
The results of the present study suggest the following conclusions:
1. Mixing through ethanol suspension and ultrasonic waves results in a uniform distribution of CuNps within the Al matrix.
2. The porosity of Al-CuNps composites decreases continuously with increased Cu content.
3. The density and thermal and electrical conductivities increase with increasing Cu content. In particular, the electrical conductivity of composites with 25% Cu reaches 78.87% of that of pure copper.
4. Hardness increases with increasing Cu content, reaching 172 HV at 25% Cu. Further increases in Cu content might lead to reduced values due to the agglomeration or less effective dispersion of the CuNps, which was not observed in the current study.
Future research should evaluate higher copper content ratios or increased sintering time and temperature.
The authors declare they have not used Artificial Intelligence (AI) tools in the creation of this article.
Farouk M. Mahdi: supervision, writing—review & editing; Omar Hassan Mahmood & Mustafa Sh. Aljanabi: conceptualization, methodology, investigation, data curation, writing—review, editing, investigation & data curation.
The authors declare no conflict of interest.
[1] |
Torralba JD, Da Costa CE, Velasco F (2003) P/M aluminum matrix composites: An overview. J Mater Process Tech 133: 203–206. https://doi.org/10.1016/S0924-0136(02)00234-0 doi: 10.1016/S0924-0136(02)00234-0
![]() |
[2] | Dieter GE, Bacon D (1988) Mechanical Metallurgy, New York: McGraw-Hill Companies. |
[3] |
Abtan NS, Jassim AH, Al-Janabi MSM (2018) Tensile strength, micro-hardness and microstructure of friction-stir-welding AA6061-T4 joints. Tikrit J Eng Sci 25: 51–56. https://doi.org/10.25130/tjes.25.4.09 doi: 10.25130/tjes.25.4.09
![]() |
[4] |
Raturi A, Mer KKS, Pant PK (2017) Synthesis and characterization of mechanical, tribological and micro structural behaviour of Al 7075 matrix reinforced with nano Al2O3 particles. Mater Today Proc 4: 2645–2658. https://doi.org/10.1016/J.MATPR.2017.02.139 doi: 10.1016/J.MATPR.2017.02.139
![]() |
[5] |
Jiang W, Zhu J, Li G, et al. (2021) Enhanced mechanical properties of 6082 aluminum alloy via SiC addition combined with squeeze casting. J Mater Sci Technol 88: 119–131. https://doi.org/10.1016/j.jmst.2021.01.077 doi: 10.1016/j.jmst.2021.01.077
![]() |
[6] |
Zhu J, Jiang W, Li G, et al. (2020) Microstructure and mechanical properties of SiCnp/Al6082 aluminum matrix composites prepared by squeeze casting combined with stir casting. J Mater Process Technol 283: 116699. https://doi.org/10.1016/j.jmatprotec.2020.116699 doi: 10.1016/j.jmatprotec.2020.116699
![]() |
[7] |
Annaz AA, Irhayyim SS, Hamada ML, et al. (2020) Comparative study of mechanical performance between Al–graphite and Cu–graphite self-lubricating composites reinforced by nano-Ag particles. AIMS Mater Sci 7: 534–551. https://doi.org/10.3934/matersci.2020.5.534 doi: 10.3934/matersci.2020.5.534
![]() |
[8] |
Rahimipour MR, Tofigh AA, Mazahery A, et al. (2013) Enhancement of abrasive wear resistance in consolidated Al matrix composites via extrusion process. Tribol Mater Surf Interfaces 7: 129–134. https://doi.org/10.1179/1751584x13y.0000000034 doi: 10.1179/1751584x13y.0000000034
![]() |
[9] |
Alaneme KK, Fajemisin AV, Maledi N (2019) Development of aluminium-based composites reinforced with steel and graphite particles: Structural, mechanical and wear characterization. J Mater Res Technol 8: 670–682. https://doi.org/10.1016/J.JMRT.2018.04.019 doi: 10.1016/J.JMRT.2018.04.019
![]() |
[10] | Talabi HK, Adewuyi BO, Olaniran O, et al. (2019) Mechanical and wear behavior of Al6063 reinforced with snail shell and copper nanoparticles. Ann Fac Eng Hunedoara 17: 81–85. |
[11] |
Afkham Y, Khosroshahi RA, Rahimpour S, et al. (2017) Enhanced mechanical properties of in situ aluminium matrix composites reinforced by alumina nanoparticles. Arch Civ Mech Eng 18: 215–226. https://doi.org/10.1016/j.acme.2017.06.011 doi: 10.1016/j.acme.2017.06.011
![]() |
[12] |
Sahin Y, Murphy S (1996) The effect of fibre orientation of the dry sliding wear of borsic-reinforced 2014 aluminium alloy. J Mater Sci 31: 5399–5407. https://doi.org/10.1007/bf01159309 doi: 10.1007/bf01159309
![]() |
[13] |
Mohanty P, Mahapatra R, Padhi P, et al. (2020) Ultrasonic cavitation: An approach to synthesize uniformly dispersed metal matrix nanocomposites—A review. Nano-Struct Nano-Objects 23: 100475. https://doi.org/10.1016/j.nanoso.2020.100475 doi: 10.1016/j.nanoso.2020.100475
![]() |
[14] |
Yehia HM, Elmetwally RAH, Elhabak AM, et al. (2023) Manufacturing of aluminum nano-composites reinforced with nano-copper and high graphene ratios using hot pressing technique. Materials 16: 7174. https://doi.org/10.3390/ma16227174 doi: 10.3390/ma16227174
![]() |
[15] |
Matli PR, Fareeha U, Shakoor RA, et al. (2017) A comparative study of structural and mechanical properties of Al–Cu composites prepared by vacuum and microwave sintering techniques. J Mater Res Technol 7: 165–172. https://doi.org/10.1016/j.jmrt.2017.10.003 doi: 10.1016/j.jmrt.2017.10.003
![]() |
[16] |
Wu D, Huang C, Wang Y, et al. (2019) Utilization of SiC and Cu particles to enhance thermal and mechanical properties of Al matrix composites. Materials 12: 2770. https://doi.org/10.3390/ma12172770 doi: 10.3390/ma12172770
![]() |
[17] |
Mahdi FM, Mahmood OH (2021) Effect of adding nano Ag on mechanical and physical properties of Cu–10% Fe prepared by powder metallurgy technique. Tikrit J Eng Sci 28: 13–20. http://dx.doi.org/10.25130/tjes.28.1.02 doi: 10.25130/tjes.28.1.02
![]() |
[18] |
Mahdi FM, Razooqi RN, Irhayyim SS (2017) The influence of the graphite content and milling time on the hardness, compressive strength and wear volume of copper–graphite composites prepared via powder metallurgy. Tikrit J Eng Sci 24: 38–44. https://doi.org/10.25130/tjes.24.3.07 doi: 10.25130/tjes.24.3.07
![]() |
[19] |
Humood HS (2017) Effect of pressing pressure on properties of copper-10% graphite composites prepared by powder metallurgy technique. Tikrit J Eng Sci 24: 28–34. https://doi.org/10.25130/tjes.24.2017.15 doi: 10.25130/tjes.24.2017.15
![]() |
[20] |
Kim K, Kim D, Park K, et al. (2019) Effect of intermetallic compounds on the thermal and mechanical properties of Al–Cu composite materials fabricated by spark plasma sintering. Materials 12: 1546. https://doi.org/10.3390/ma12091546 doi: 10.3390/ma12091546
![]() |
[21] |
Khamaj A, Farouk WM, Shewakh WM, et al. (2021) Effect of lattice structure evolution on the thermal and mechanical properties of Cu–Al2O3/GNPs nanocomposites. Ceram Int 47: 16511–16520. https://doi.org/10.1016/j.ceramint.2021.02.219 doi: 10.1016/j.ceramint.2021.02.219
![]() |