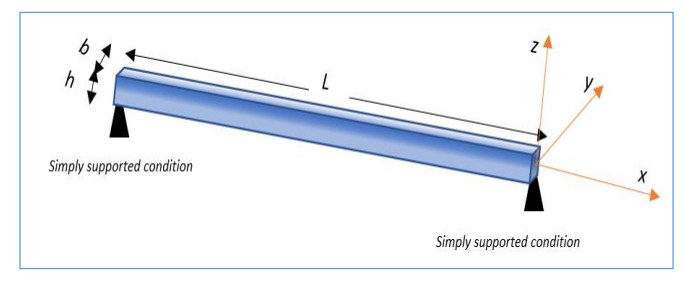
This research focuses on exploring the free vibration behavior of functionally graded (FG) nano-beams. To calculate the effective properties of the FG nano-beam, which varies solely in the thickness direction, the four homogenization schemes Mori-Tanaka, Tamura, Reuss and Voigt are employed. This study employs high-order shear deformation nano-beam theory and derives the governing equations of motion using nonlocal differential constitutive relations of Eringen. Hamilton's principle is utilized in conjunction with the refined three variables beam theory. The consideration of a length scale parameter accounts for small-scale effects. Analytical solutions are obtained for a simply supported FG nano-beam and compared with existing literature solutions. The research also investigates the influence of different homogenization schemes, the nonlocal parameter, beam aspect ratio and various material compositions on the dynamic response of the FG nano-beam.
Citation: Abdelhak Berkia, Billel Rebai, Bilal Litouche, Soufiane Abbas, Khelifa Mansouri. Investigating parametric homogenization models for natural frequency of FGM nano beams[J]. AIMS Materials Science, 2023, 10(5): 891-908. doi: 10.3934/matersci.2023048
[1] | Bhavik Ardeshana, Umang Jani, Ajay Patel, Anand Joshi . An approach to modelling and simulation of single-walled carbon nanocones for sensing applications. AIMS Materials Science, 2017, 4(4): 1010-1028. doi: 10.3934/matersci.2017.4.1010 |
[2] | Andrea Somogyi, Cristian Mocuta . Possibilities and Challenges of Scanning Hard X-ray Spectro-microscopy Techniques in Material Sciences. AIMS Materials Science, 2015, 2(2): 122-162. doi: 10.3934/matersci.2015.2.122 |
[3] | Mateo Duarte, Andrés Benítez, Katiuska Gómez, Benjamín Zuluaga D, Juan Meza, Yamile Cardona-Maya, Juan S. Rudas, César Isaza . Nanomechanical characterization of a metal matrix composite reinforced with carbon nanotubes. AIMS Materials Science, 2020, 7(1): 33-45. doi: 10.3934/matersci.2020.1.33 |
[4] | Carlos A. Sánchez, Yamile Cardona-Maya, Andrés D. Morales, Juan S. Rudas, Cesar A. Isaza . Development and evaluation of polyvinyl alcohol films reinforced with carbon nanotubes and alumina for manufacturing hybrid metal matrix composites by the sandwich technique. AIMS Materials Science, 2021, 8(2): 149-165. doi: 10.3934/matersci.2021011 |
[5] | Luis Gutierrez-Rivera, Robert Peters, Steven Dew, Maria Stepanova . Surface-enhanced Raman spectroscopy detection of protein-ligand binding using D-glucose and glucose binding protein on nanostructured plasmonic substrates. AIMS Materials Science, 2017, 4(2): 522-539. doi: 10.3934/matersci.2017.2.522 |
[6] | Yamen Ibrahim Elbahy, Maged A. Youssef, M. Meshaly . Numerical investigation of reinforced-concrete beam-column joints retrofitted using external superelastic shape memory alloy bars. AIMS Materials Science, 2021, 8(5): 716-738. doi: 10.3934/matersci.2021043 |
[7] | Mohammed Y. Abdellah, Hamzah Alharthi, Mohamed K. Hassan, Ahmed F. Mohamed . Effect of specimen size on natural vibration of open hole copper/glass-reinforced epoxy laminate composites. AIMS Materials Science, 2020, 7(4): 499-517. doi: 10.3934/matersci.2020.4.499 |
[8] | M.A.R. Loja, André Carvalho, Ines C.J. Barbosa . A study on the static behavior of functionally graded I-shaped beams. AIMS Materials Science, 2024, 11(1): 28-57. doi: 10.3934/matersci.2024002 |
[9] | Rebai Billel . Contribution to study the effect of (Reuss, LRVE, Tamura) models on the axial and shear stress of sandwich FGM plate (Ti–6A1–4V/ZrO2) subjected on linear and nonlinear thermal loads. AIMS Materials Science, 2023, 10(1): 26-39. doi: 10.3934/matersci.2023002 |
[10] | M. Rajanish, N. V. Nanjundaradhya, Ramesh S. Sharma, H. K. Shivananda, Alok Hegde . Directional Interlaminar Shear Strength (ILSS) of nano-modified epoxy/unidirectional glass fibre composite. AIMS Materials Science, 2018, 5(4): 603-613. doi: 10.3934/matersci.2018.4.603 |
This research focuses on exploring the free vibration behavior of functionally graded (FG) nano-beams. To calculate the effective properties of the FG nano-beam, which varies solely in the thickness direction, the four homogenization schemes Mori-Tanaka, Tamura, Reuss and Voigt are employed. This study employs high-order shear deformation nano-beam theory and derives the governing equations of motion using nonlocal differential constitutive relations of Eringen. Hamilton's principle is utilized in conjunction with the refined three variables beam theory. The consideration of a length scale parameter accounts for small-scale effects. Analytical solutions are obtained for a simply supported FG nano-beam and compared with existing literature solutions. The research also investigates the influence of different homogenization schemes, the nonlocal parameter, beam aspect ratio and various material compositions on the dynamic response of the FG nano-beam.
Nano-beam materials are composites made up of nanotubes, nanowires and nanoparticles which are manipulated on a nanoscale level and used in a variety of applications. Researchers have utilized Eringen's nonlocal elasticity theory to investigate the static deformation, free vibration, bending, buckling and wave properties of nano-beams and other structures like nano-plates and curved nano-shells [1,2,3].
Recent research on nanobeam functionally graded beams has gained traction, with various studies conducted to explore the current state of this field. This discussion provides an in-depth analysis of the published articles, offering insight into potential applications of this technology. By examining current trends, potential improvements and applications, this research can help to further our understanding of nanobeam functionally graded beams and their utility. In their study, Vinh and Tounsi [4] investigated the free vibration of functionally graded doubly curved nanoshells using nonlocal first-order shear deformation theory. They compared the frequencies obtained to existing results and examined the effects of nonlocal parameters and the power-law index on the nanoshells. Additionally, in their later work [5] they determined the effect of a spatial variation in the nonlocal parameter on the free vibration of functionally graded sandwich (FGSW) nanoplates, finding that the natural frequencies were significantly reduced. Cuong-Le et al. investigated the linear and nonlinear solutions of a sigmoid functionally graded material nanoplate with porous effects, using isogeometric finite element formulation to examine the effects of power indexes, aspect ratios, nonlocal and strain gradient parameters [6]. Liu et al. sought to understand the dynamic deflection response of an exponentially functionally graded material (E-FGM) nanoplate embedded in a visco-elastic foundation when subjected to a moving load, utilizing third-order shear deformation theory, Eringen nonlocal elasticity and a state-space method to analyze the influence of nonlocality, volume fraction index, porosity index, visco-elastic foundation coefficients and velocity and time span of a moving load on the forced vibration of the nanoplate [7]. Faghidian and Tounsi studied wave dispersion and free vibrations of elastic nano-beams through the mixture unified gradient theory, providing insight into the augmented elasticity theory's effectiveness in softening and stiffening responses [8]. John Peddieson utilized nonlocal elasticity theory to develop a nonlocal Benoulli/Euler beam model for cantilever beams [9], and Xu Mingtian [10] applied the same theory in combination with an integral equation approach to investigate the free transverse vibrations of nano-to-micron scale beams. Rebai Billel has studied the effects of homogenization models on the stress, deflection and vibration behavior of functionally graded plates subjected to thermal and mechanical loads [11,12,13]. Reddy et al. have evaluated the static bending, vibration, and buckling responses of beams with various boundary conditions using nonlocal differential constitutive relations of Eringen. They have presented analytical solutions and numerical results to show the effect of nonlocal behavior on deflections, buckling loads and natural frequencies of beams [14,15]. Zhang and Qing introduced well-posed two-phase nonlocal models for nanobeam vibrations based on higher-order shear deformation theory. Their work also encompassed the examination of refined shear deformation beams' buckling behavior under thermal loading [16]. Additionally, Zhang, Schiavone and Qing extended their research to encompass hygro-thermal vibration analysis of nanobeams. This analysis employed stress-driven nonlocal theory and incorporated two-variable shear assumptions [17,18]. Ebrahimi has examined the vibration characteristics of magneto-electro-thermo-elastic functionally graded nano-beams in the framework of third order shear deformation theory [19], while Thai et al. have presented a nonlocal sinusoidal shear deformation beam theory for the bending, buckling and vibration of nano-beams [20]. Eltaher et al. have conducted a free vibration analysis of size-dependent functionally graded nano-beams using the finite element method based on the nonlocal continuum model of Eringen [21] and Nazemezhad et al. have investigated the nonlinear free vibration of functionally graded nano-beams with immovable ends using nonlocal elasticity and Euler-Bernoulli beam theory [22]. Ebrahimi has studied the static stability and free vibration characteristics of functionally graded nano-beams using a nonlocal couple stress theory [23]; Hadji et al. have investigated the free vibration of porous functionally graded nano-beams using a new nonlocal hyperbolic shear deformation beam theory [24]; Youcef et al. have focused on the behavior of non-local shear deformation beam theory for the vibration of functionally graded (FG) nano-beams with porosities [25]; and Shariati et al. have examined the size-dependent vibrations and stability of axially functionally graded (AFG) nano-beams using a nonlocal elasticity theory [26].
Other research conducted by Cornacchia et al. delved into the analytical solutions pertaining to the linear vibrations and buckling of nano plates [27]. Following suit, Tocci Monaco et al. conducted an in-depth investigation into the critical temperatures associated with magneto-electro-elastic nonlocal strain gradient plates [28]. Luciano et al. contributed significantly by exploring free flexural vibrations in nanobeams with non-classical boundary conditions [29]. Additionally, Fabbrocino et al. made substantial strides in the field with their research on dynamic crack growth utilizing a moving mesh method. These research endeavors collectively offer invaluable insights and research findings, advancing the knowledge base in these areas of study [30].
Several researchers have examined the oscillations, bending and buckling effects, vibration characteristics, static and dynamic characteristics and nonlinear bending of power functionally graded micro plate (PFGM) microplates, microbeams, nano-beams and elasto-plastic beams based on the classical beam theory, modified couple stress theory, Euler-Bernoulli beam kinematic theory, non-local elasticity theory, higher-order shear beam deformation theories, strain gradient theory and Bernoulli-Euler beam model, respectively [31,32,33,34,35,36,37,38,39,40,41,42,43,44,45,46].
In recent findings by Wu et al. on dynamics of nanostructures including vibrations in graphene sheets and nanobeams, this work validates computational models for accurate prediction of natural frequencies across a wide parameter space [47,48].
B. Karami et al. investigated the free vibration behavior of a curved microbeam composed of a functionally graded material (FGM) using the modified strain gradient theory of elasticity and first-order shear deformation theory. In the study, various homogenization models, such as Voigt, Reuss, Hashin-Shtrikman bounds and cubic local representative volume elements (LRVE) schemes were employed to determine the effective material properties of the FGM curved microbeam [49].
Compared to earlier investigations using simple models like Euler-Bernoulli beam theory, current research utilizes more advanced approaches like higher-order shear deformation theory and isogeometric finite element formulation to capture complex behaviors of functional nanobeams. Advantages include analyzing complex geometries, deflections, porosities and foundations for practicable insight. Challenges remain around computational efficiency for real applications. Overall trends point to a focus on novel materials, geometries and theories to progress functional nanobeam research toward utilization through solving practical engineering problems.
This research uses the Mori-Tanaka, Tamura, Reuss and Voigt homogenization schemes and the high-order shear deformation nano-beam theory to derive the governing equations of motion using Hamilton's principle and the nonlocal differential constitutive relations of Eringen. Analytical solutions are then obtained from this data and compared with other solutions in the literature. The effects of the various homogenization schemes, nonlocal parameter, beam aspect ratio and material compositions on the dynamic response of the FG nano-beam are also investigated. This study undertakes a first-of-its-kind comparative vibration analysis of FGM nano-beams using four homogenization techniques and comprehensive parametric study of nonlocal parameters, gradient indices, volume fractions and geometries. This work provides new insights into the natural frequencies and mode shapes. The comparative homogenization scheme analysis and extensive vibrational behavior investigation pave the way for optimized design and future stability, buckling and wave propagation studies of FGM nano-beams.
Figure 1 shows FG nano-beam of length L, width b and thickness h. The material on the top surface (z = +h/2) of the plate is ceramic and is graded to metal at the bottom surface of the plate (z = −h/2).
The volume distribution fraction through the thickness has been identified as the following function, using Eq 1, where p is the material index.
V(z)=(2z+h2h)p | (1) |
The micromechanics models chosen for the comparison study are detailed in sections 2.1. to 2.4.
Mixture law, also known as the Voigt model, is a mathematical model that describes the behavior of a composite material. It assumes that the properties of the composite material are obtained by combining the properties of the individual components in a linear manner. It is used to calculate the effective modulus of elasticity, strength and other properties of a composite material using Eq 2 [50].
P(z)=PcV(z)+Pm(1−V(z)) | (2) |
The Reuss model is a mathematical model used to calculate the effective properties of a composite material. It assumes that the properties of the composite material are obtained by averaging the properties of the individual components. It is used to calculate the effective modulus of elasticity, strength and other properties of a composite material. Eq 3 calculates the proprieties of FG structures with the assumption that the stress is uniform through the thickness [51].
P(z)=PcPmPc(1−V(z))+PmV(z) | (3) |
The Tamura model is a mathematical model used to calculate the effective properties of a composite material. It is based on the concept of strain energy density and assumes that the properties of the composite material are obtained by combining the properties of the individual components in a non-linear manner. It is used to calculate the effective modulus of elasticity, strength and other properties of a composite material using Eq 4 [52].
The method of Tamura is another way to express the linear law of Voigt where the empirical term q "stress-to-strain transfer" has been added in formulation [53].
P(z)=(1−V(z))Pm(q−Pc)+V(z)PcPc(1−V(z))+PmV(z)(1−V(z))(q−Pc)+V(z)Pc(q−Pm) | (4) |
The Mori-Tanaka method is a homogenization scheme used to estimate the effective properties of FGM. This method was developed by Mori and Tanaka in 1973 and is based on the assumption that the material properties in the microstructure can be represented by a representative volume element (RVE). The method uses small strain theory and assumes that the RVE is composed of an assembly of small particles of different materials which interact through elasticity. The Mori-Tanaka method can also be used to calculate the effective thermal conductivity and effective electrical conductivity of the FGM using Eq 5 [54].
The Mori-Tanaka homogenization scheme formulation is given by [55,56,57,58]:
P(z)=Pm+V(z)(Pc−Pm)1+(1−V(z))(3Pc−Pm)3Pm+4 | (5) |
where P(z) is the effective material property. Pm and Pc are the properties of the metal and ceramic faces of the beam respectively.
The displacement field of the current theory is based on the assumption that in-plane and transverse displacements are split into bending and shear components, that bending parts of in-plane displacement are similar to d'Euler Bernoulli theory and that shear parts of in-plane displacement induce hyperbolic variations of shear strains and shear stresses which vanish on the top and bottom surfaces of the beam. Those result in the following displacement field, as shown in Eq 6:
u(x,z,t)=u0(x,t)−z∂wb∂x+f(z)∂ws∂xw(x,z,t)=wb(x,t)+ws(x,t) | (6) |
Here, u0(x,t) denotes the displacements along the x coordinate directions of a point on the mid-plane of the beam; wb(x,t) and ws(x,t) are the bending and shear components of the transverse displacements, respectively. The nonzero strains associated with the displacement field are shown in Eq 7:
εx=ε0x+zkbx+f(z)ksxetγxz=g(z)γsxz | (7) |
where:ε0x=∂u0∂x, kbx= −∂2wb∂x2, ksx=−∂2ws∂x2, γsxz = ∂ws∂x, f(z)= −14z+53z(zh)2, g= 54−5(zh)2.
The nonlocal constitutive relation for the macroscopic stress takes the following form, as shown in Eq 8:
σx−μd2σxdx2=Eεxτxz−μd2τxzdx2=Gγxz | (8) |
where E and G are Young's modulus and shear modulus, respectively. Moreover, e0 is a material constant, and a is the internal characteristic length. Once the nonlocal parameter μ=(e0a)2 is equal to zero, we obtain the constitutive relations of the local theories.
Hamilton's principle is used herein to derive the equations of motion. We have obtained:
∫L0∫A(σxδεx+τzxδγzx)dAdx−∫L0∫Aρ[¨u0δu0+(¨wb+¨ws)δ(wb+ws)]dAdx=0 | (9) |
Integrating by parts Eq 9, and collecting the coefficients of δu0, δwb and δws, the following equations of stability are obtained by Eq 10:
δu0:dNdx=I0¨u0δwb:d2Mbdx2=I0(¨wb+¨ws)−I2d2¨wbdx2δws:d2Msdx2+dQdx=I0(¨wb+¨ws)−I284d2¨wsdx2 | (10) |
where N, Mb, Ms and Q are stress resultants and they are defined by:
(N,Mb,Ms)=∫A (1,z,f)σxdA | (11) |
Q=∫A gτxzdA | (12) |
And (I0,I2) are mass inertias defined as:
(I0,I2)=∫A(1,z2)ρ(z)dA | (13) |
Substituting Eqs 11–13 into Eq 8 and integrating through the thickness of the beam, the stress resultants are related to the generalized displacements by the relations:
N−μd2Ndx2=Adu0dx−Bd2wbdx2−Bsd2wsdx2Mb−μd2Mbdx2=Bdu0dx−Dd2wbdx2−Dsd2wsdx2Ms−μd2Msdx2=Bdu0dx−Dd2wbdx2−Hsd2wsdx2Q−μd2Qdx2=Asdwsdx | (14) |
where: {A,B,D,‾E,F,H}=∫A {1,z,z2,z3,z4,z6}E(z)dA, Bs=−14B+53h2‾E, Ds=−14D+53h2F, Hs=116D−56h2F+259h4H, {A55,D55,F55}=∫A {1,z2,z4}G(z)dA, As=2516A55−252h2D55+25h4F55.
Substituting from Eq 14 into Eq 8, we obtain the following equation in terms of (u0,wb,ws):
Ad2u0dx2−Bd3wbdx3−Bsd3wsdx3=I0(¨u0−μd2¨u0dx2)Bd3u0dx3−Dd4wbdx4−Dsd4wsdx4=I0((¨wb+¨ws)−μd2(¨wb+¨ws)dx2)−I2(d2¨wbdx2−μd4¨wbdx4)Bsd3u0dx3−Dsd4wbdx4−Hsd4wsdx4+Asd2wsdx2=I0((¨wb+¨ws)−μd2(¨wb+¨ws)dx2)−I284(d2¨wsdx2−μd4¨wsdx4) | (15) |
Following the Navier solution procedure, we assume the solution form for u0, wb, ws that satisfies simply-supported FG conditions.
{u0wbws}=∑∞m=1{Uncos(αx)eiωtWbnsin(αx)eiωtWsnsin(αx)eiωt} | (16) |
where Un, Wbn and Wsn are arbitrary parameters to be determined, ω is the eigen-frequency associated with (n)th eigen-mode.
Substituting Eq 16 into Eq 15, the analytical solutions can be obtained from the Eq 17:
([Aα2−Bα3−Bsα3−Bα3Dα4Dsα4−Bsα3Dsα4Hsα4+Asα2]−(1+μα2)ω2[I0−I1α−J1α−I1αI0+I2α2I0+J2α2−J1αI0+J2α2I0+K2α2]){UnWbnWsn}={000} | (17) |
This section compares the proposed homogenization model with the one published by Zemri et al. [59] in order to verify the accuracy of different homogenization models (Reuss, Tamura and Mori-Tanaka). It also provides a parametric analysis of the effects of the nonlocal parameter, the material index, the length-to-thickness ratio and the type of phases constituting the FGM nano-beam on its natural frequency.
The Tanaka, Tamura, and Reuss model was compared to and validated with the Voigt model used by Zemri et al. [59] to ensure the accuracy of the results. The material properties of the FGM nano-beams, consisting of six different combinations of stainless steel (SUS304) and aluminum (Al) with either zirconia (ZrO2), aluminia (Al2O3) or silicon carbide (SiC), are shown in Table 1. These combinations are named FGM1–1 SUS304/ZrO2, FGM1–2 SUS304/Al2O3, FGM1–3 SUS304/SiC, FGM2–1 Al/ZrO2, FGM2–2 Al/Al2O3 and FGM2–3 Al/SiC FGM nano-beams, respectively.
Young's modulus (GPa) | Mass density (kg/m3) | Poisson' sratio | |
Stainless steel (SUS304) | 210 | 7800 | 0.3 |
Aluminum (Al) | 70 | 2702 | 0.3 |
Airconia (ZrO2) | 151 | 3000 | 0.3 |
Aluminia (Al2O3) | 380 | 3800 | 0.3 |
Silicon carbide (SiC) | 420 | 3210 | 0.3 |
In all cases, we present the non-dimensional frequency defined as shown in Eq 18:
−ω=ωL2√ρcAEcI | (18) |
Tables 2 and 3 provide a comprehensive comparison of the fundamental frequency of nano-beams for the four different models: Voigt, Tanka, Tamura and Reuss. The varying length-to-thickness ratios and material indices of the nonlocal parameter indicate that the results are reliable and accurate. The validation results show good agreement across the different models, demonstrating the trustworthiness of the models.
l/h | p | 0 | 0.5 | 1 | |||||||||
Zemri | Tanaka | Tamura | Reuss | Zemri | Tanaka | Tamura | Reuss | Zemri | Tanaka | Tamura | Reuss | ||
10 | 0 | 9.7075 | 9.7075 | 9.7075 | 9.7075 | 9.5899 | 9.5899 | 9.5899 | 9.5899 | 9.2612 | 9.2612 | 9.2612 | 9.2612 |
1 | 6.8814 | 6.6246 | 7.0040 | 7.0040 | 6.7981 | 6.5444 | 6.9192 | 6.9191 | 6.5651 | 6.3201 | 6.6820 | 6.6820 | |
3 | 6.0755 | 5.9100 | 6.1186 | 6.1185 | 6.0019 | 5.8384 | 6.0444 | 6.0444 | 5.7962 | 5.6383 | 5.8373 | 5.8373 | |
10 | 5.5768 | 5.4494 | 5.5425 | 5.5425 | 5.5092 | 5.3834 | 5.4754 | 5.4754 | 5.3204 | 5.1989 | 5.2877 | 5.2877 | |
30 | 0 | 9.8511 | 9.8510 | 9.8510 | 9.8510 | 9.8376 | 9.8376 | 9.8376 | 9.8376 | 9.7975 | 9.7975 | 9.7975 | 9.7975 |
1 | 6.9832 | 6.7265 | 7.1113 | 7.1113 | 6.9737 | 6.7173 | 7.1016 | 7.1015 | 6.9452 | 6.6899 | 7.0726 | 7.0726 | |
3 | 6.1712 | 6.0038 | 6.2162 | 6.2161 | 6.1627 | 5.9956 | 6.2077 | 6.2076 | 6.1376 | 5.9711 | 6.1823 | 6.1823 | |
10 | 5.6655 | 5.5340 | 5.6290 | 5.6290 | 5.6578 | 5.5264 | 5.6213 | 5.6213 | 5.6347 | 5.5039 | 5.5984 | 5.5984 | |
100 | 0 | 9.8679 | 9.8679 | 9.8679 | 9.8679 | 9.8667 | 9.8667 | 9.8667 | 9.8667 | 9.8631 | 9.8631 | 9.8630 | 9.8630 |
1 | 6.9952 | 6.7384 | 7.1239 | 7.1239 | 6.9943 | 6.7376 | 7.1230 | 7.1230 | 6.9917 | 6.7351 | 7.1204 | 7.1204 | |
3 | 6.1824 | 6.0148 | 6.2276 | 6.2276 | 6.1817 | 6.0140 | 6.2269 | 6.2268 | 6.1794 | 6.0118 | 6.2246 | 6.2245 | |
10 | 5.6759 | 5.5439 | 5.6392 | 5.6391 | 5.6752 | 5.5432 | 5.6385 | 5.6385 | 5.6731 | 5.5411 | 5.6364 | 5.6364 |
l/h | p | 1.5 | 2 | ||||||
Zemri | Tanaka | Tamura | Reuss | Zemri | Tanaka | Tamura | Reuss | ||
10 | 0 | 8.7813 | 8.7813 | 8.7813 | 8.7813 | 8.2197 | 8.2197 | 8.2197 | 8.2196 |
1 | 6.2249 | 5.9926 | 6.3357 | 6.3357 | 5.8267 | 5.6093 | 5.9305 | 5.9305 | |
3 | 5.4959 | 5.3462 | 5.5348 | 5.5348 | 5.1443 | 5.0042 | 5.1808 | 5.1808 | |
10 | 5.0447 | 4.9295 | 5.0137 | 5.0137 | 4.7221 | 4.6142 | 4.6930 | 4.6930 | |
30 | 0 | 9.7318 | 9.7318 | 9.7317 | 9.7317 | 9.6419 | 9.6418 | 9.6419 | 9.6418 |
1 | 6.8987 | 6.6450 | 7.0252 | 7.0251 | 6.8349 | 6.5836 | 6.9603 | 6.9603 | |
3 | 6.0964 | 5.9310 | 6.1409 | 6.1408 | 6.0401 | 5.8763 | 6.0841 | 6.0841 | |
10 | 5.5969 | 5.4669 | 5.5608 | 5.5608 | 5.5452 | 5.4164 | 5.5095 | 5.5094 | |
100 | 0 | 9.8570 | 9.8570 | 9.8570 | 9.8569 | 9.8485 | 9.8485 | 9.8485 | 9.8485 |
1 | 6.9874 | 6.7310 | 7.1160 | 7.1160 | 6.9814 | 6.7252 | 7.1099 | 7.1099 | |
3 | 6.1756 | 6.0081 | 6.2207 | 6.2207 | 6.1703 | 6.0030 | 6.2154 | 6.2153 | |
10 | 5.6697 | 5.5377 | 5.6329 | 5.6329 | 5.6648 | 5.5330 | 5.6281 | 5.6280 |
Figure 2 demonstrates the variation in the natural frequency of an FGM nano beam when evaluated using four homogenization models (Voigt, Tamura, Tanak and Reuss) with a length-to-thickness ratio of 10 to 100, material index of 1 and a nonlocal parameter of 4.
It can be seen from Figure 2 that the natural frequency of the FGM nano-beam increases with the length-to-thickness ratio l for all four homogenization models. As the l/h ratio increases, the beam becomes longer and thinner, resulting in an increase in natural frequency. It is also notable that the Reuss and Tamura models provide the same natural frequency values, while the Voigt and Tanak models give lower values. This discrepancy is due to the assumptions made in each model. Furthermore, the relative difference between the natural frequency evaluated using the four homogenization models decreases as the length-to-thickness ratio increases, albeit only slightly The relative difference = [ω(Reuss) – ω(Voigt, Tamura, Tanak)]/ω(Reuss) between the natural frequency of the FGM nano-beam evaluated using the four homogenization models is 0.059 when l is 10 and 0.038 when l is 100.
Figure 3 shows how the natural frequency of an FGM nano-beam changes as the nonlocal parameter ranges from 0 to 5, while keeping the material index at 1 and length-to-thickness ratio at 10, when evaluated using four different homogenization models (Voigt, Tamura, Tanak and Reuss).
The data in Figure 3 displays that, as the nonlocal parameter increases from 0 to 5, the natural frequency of an FGM nano-beam decreases and the Tanak model gives the lowest frequency value. Among the models, the Voigt model shows the most pronounced decrease in natural frequency, dropping from 6.881 to 5.630 (a decrease of 1.251). The Tanak model shows a decrease of 1.231 from 6.625 to 5.394. The Tamura and Reuss models show a decrease of 0.707 from 7.004 to 6.297. This decrease in frequency is due to the nonlocal parameter making the beam stiffer, which in turn reduces its natural frequency. The larger the nonlocal parameter, the more rigid the beam becomes and thus the lower the frequency.
Figure 4 presents the natural frequency of an FGM nano-beam evaluated with four homogenization models (Voigt, Tamura, Tanak and Reuss) when the material index p is changed from 0 to 30, and length-to-thickness ratio and nonlocal parameter are both kept at 10 and 4, respectively.
The natural frequency decreases as the material index increases in Figure 4. The Tanak model produces the smallest values of natural frequency, which means that the nano-beam is the most flexible when evaluated with this model.
In this section, the impact of various metal and ceramic material combinations on the natural frequency of an FGM nano-beam is studied through a parametric analysis. The figure depicts the natural frequency of FGM nano-beams composed of six different combinations of stainless steel (SUS304) and aluminum (Al) with either zirconia (ZrO2), aluminia (Al2O3) or silicon carbide (SiC). The frequency is calculated using the Reuss model with different l/h ratios, ranging from 10 to 100, a material index of 1 and a nonlocal parameter of 4.
As shown in Figure 5, the length-to-thickness ratio (l/h) has a crucial impact on the natural frequency of FGM nano-beams. As l/h increases, the natural frequency of the FGM nano-beams also increases. In this figure, FGM12 SUS304/Al2O3 has the highest natural frequency among the FGM nano-beams due to its high elastic modulus and low density compared to other FGM nano-beams. Conversely, FGM2–3 Al/SiC has the lowest natural frequency due to its low elastic modulus and high density. It is evident that the natural frequency of FGM nano-beams is greatly influenced by both their length-to-thickness ratio (l/h) and material properties.
This comprehensive parametric study and validation of four homogenization models advances our understanding of predicting the natural frequencies of functionally graded nano-beams. The results for varying length-to-thickness ratios, material indices and nonlocal parameters show excellent agreement across the Voigt, Tanka, Tamura and Reuss models. The relative difference in predicted natural frequencies between models decreases slightly as the length-to-thickness ratio increases. Furthermore, there are significant effects of the nonlocal parameter, material index and constitutive phases on the natural frequency. These findings provide justification that the validated computational homogenization techniques presented can reliably determine the natural frequencies of FGM nano-beams across a range of geometric and material parameters. Researchers can confidently utilize these models to gain new insights into the dynamic characteristics of nano-beams. The comprehensive parametric study and model validation represents an important advancement to the field by establishing these homogenization techniques as trusted tools for the design and analysis of nano-beams. This work elucidates the complex interplay between nano-beam dimensions, materials and intrinsic size effects, moving nano-scale research forward.
The authors declare they have not used Artificial Intelligence (AI) tools in the creation of this article.
All authors declare no conflict of interest in this paper.
[1] |
Eringen AC (1972) Nonlocal polar elastic continua. Int J Eng Sci 10: 1–16. https://doi.org/10.1016/0020–7225(72)90070–5 doi: 10.1016/0020–7225(72)90070–5
![]() |
[2] |
Eringen AC (1983) On differential equations of nonlocal elasticity and solutions of screw dislocation and surface waves. J Appl Phys 54: 4703–4710. https://doi.org/10.1063/1.332803 doi: 10.1063/1.332803
![]() |
[3] |
Eringen AC, Edelen DGB (1972) On nonlocal elasticity. Int J Eng Sci 10: 233–248. https://doi.org/10.1016/0020–7225(72)90039–0 doi: 10.1016/0020–7225(72)90039–0
![]() |
[4] |
Van VP, Tounsi A (2022) Free vibration analysis of functionally graded doubly curved nanoshells using nonlocal first-order shear deformation theory with variable nonlocal parameters. Thin Wall Struct 174: 109084. https://doi.org/10.1016/j.tws.2022.109084 doi: 10.1016/j.tws.2022.109084
![]() |
[5] |
Van VP, Van CN, Tounsi A (2022) Static bending and buckling analysis of bi-directional functionally graded porous plates using an improved first-order shear deformation theory and FEM. Eur J Mech A-Solid 96: 104743. https://doi.org/10.1016/j.euromechsol.2022.104743 doi: 10.1016/j.euromechsol.2022.104743
![]() |
[6] |
Cuong LT, Nguyen KD, Le MH, et al. (2022) Nonlinear bending analysis of porous sigmoid FGM nanoplate via IGA and nonlocal strain gradient theory. Adv Nano Res 12: 441–455. https://doi.org/10.12989/anr.2022.12.5.441 doi: 10.12989/anr.2022.12.5.441
![]() |
[7] |
Liu G, Wu S, Shahsavari D, et al. (2022) Dynamics of imperfect inhomogeneous nanoplate with exponentially-varying properties resting on viscoelastic foundation. Eur J Mech A-Solid 95: 104649. https://doi.org/10.1016/j.euromechsol.2022.104649 doi: 10.1016/j.euromechsol.2022.104649
![]() |
[8] |
Faghidian SA, Tounsi A (2022) Dynamic characteristics of mixture unified gradient elastic nanobeams. FU Mech Eng 20: 539–552. https://doi.org/10.22190/FUME220703035F doi: 10.22190/FUME220703035F
![]() |
[9] |
Peddieson J, Buchanan GR, McNitt RP (2003) Application of nonlocal continuum models to nanotechnology. In J Eng Sci 41: 305–312. https://doi.org/10.1016/S0020–7225(02)00210–0 doi: 10.1016/S0020–7225(02)00210–0
![]() |
[10] |
Xu M (2006) Free transverse vibrations of nano-to-micron scale beams. P Roy Soc A-Math Phy 462: 2977–2995. https://doi.org/10.1098/rspa.2006.1712 doi: 10.1098/rspa.2006.1712
![]() |
[11] |
Billel R (2023) Contribution to study the effect of (Reuss, LRVE, Tamura) models on the axial and shear stress of sandwich FGM plate (Ti-6A1-4V/ZrO2) subjected on linear and nonlinear thermal loads. AIMS Mater Sci 10: 26–39. https://doi.org/10.3934/matersci.2023002 doi: 10.3934/matersci.2023002
![]() |
[12] | Billel R (2022) Effect of the idealization models and thermal loads on deflection behavior of sandwich FGM plate. 2022 International Conference on Electrical Engineering and Photonics, 260–264. https://doi.org/0.1109/EExPolytech56308.2022.9950823 |
[13] |
Rebai B, Mansouri K, Chitour M, et al. (2023) Effect of idealization models on deflection of functionally graded material (FGM) plate. J Nano-Electron Phys 15: 01022. https://doi.org/10.21272/jnep.15(1).01022 doi: 10.21272/jnep.15(1).01022
![]() |
[14] |
Reddy JN (2007) Nonlocal theories for bending, buckling and vibration of beams. Int J Eng Sci 45: 288–307. https://doi.org/10.1016/j.ijengsci.2007.04.004 doi: 10.1016/j.ijengsci.2007.04.004
![]() |
[15] |
Reddy JN, Pang SD (2008) Nonlocal continuum theories of beams for the analysis of carbon nanotubes. J Appl Phys 103: 023511. https://doi.org/10.1063/1.2833431 doi: 10.1063/1.2833431
![]() |
[16] |
Zhang P, Schiavone P, Qing H (2023) Hygro-thermal vibration study of nanobeams on size-dependent visco-pasternak foundation via stress-driven nonlocal theory in conjunction with two-variable shear deformation assumption. Compos Struct 312: 116870. https://doi.org/10.1016/j.compstruct.2023.116870 doi: 10.1016/j.compstruct.2023.116870
![]() |
[17] |
Zhang P, Schiavone P, Qing H (2022) Two-phase local/nonlocal mixture models for buckling analysis of higher-order refined shear deformation beams under thermal effect. Mech Adv Mater Struc 29: 7605–7622. https://doi.org/10.1080/15376494.2021.2003489 doi: 10.1080/15376494.2021.2003489
![]() |
[18] |
Zhang P, Qing H (2022) Well-posed two-phase nonlocal integral models for free vibration of nanobeams in context with higher-order refined shear deformation theory. J Vib Control 28: 3808–3822. https://doi.org/10.1177/10775463211039902 doi: 10.1177/10775463211039902
![]() |
[19] |
Ebrahimi F, Barati MR, Zenkour AM (2017) Vibration analysis of smart embedded shear deformable nonhomogeneous piezoelectric nanoscale beams based on nonlocal elasticity theory. Int J Aeronaut Space 18: 255–269. https://doi.org/10.5139/IJASS.2017.18.2.255 doi: 10.5139/IJASS.2017.18.2.255
![]() |
[20] |
Eltaher MA, Emam SA, Mahmoud FF (2012) Free vibration analysis of functionally graded size-dependent nanobeams. App Math Comput 218: 7406–7420. https://doi.org/10.1016/j.amc.2011.12.090 doi: 10.1016/j.amc.2011.12.090
![]() |
[21] |
Nazemnezhad R, Hosseini-Hashemi S (2014) Nonlocal nonlinear free vibration of functionally graded nano-beams. Compos Struct 110: 192–199. https://doi.org/10.1016/j.compsruct.2013.12.006 doi: 10.1016/j.compsruct.2013.12.006
![]() |
[22] |
Ebrahimi F, Barati MR, Civalek O (2020) Application of Chebyshev-Ritz method for static stability and vibration analysis of nonlocal microstructure-dependent nanostructures. Eng Comput-Germany 36: 953–964. https://doi.org/10.1007/s00366–019–00742–z doi: 10.1007/s00366–019–00742–z
![]() |
[23] |
Hadji L, Avcar M (2021) Nonlocal free vibration analysis of porous FG nano-beams using hyperbolic shear deformation beam theory. Adv Nano Res 10: 281–293. https://doi.org/10.12989/anr.2021.10.3.281 doi: 10.12989/anr.2021.10.3.281
![]() |
[24] |
Youcef G, Ahmed H, Abdelillah B, et al. (2020) Porosity-dependent free vibration analysis of FG nanobeam using non-local shear deformation and energy principle. Adv Nano Res 8: 37–47. https://doi.org/10.12989/anr.2020.8.1.037 doi: 10.12989/anr.2020.8.1.037
![]() |
[25] |
Shariati A, Jung DW, Sedighi HM, et al. (2020). On the vibrations and stability of moving viscoelastic axiallyfunctionally graded nano-beams. Materials 13: 1707. https://doi.org/10.3390/ma13071707 doi: 10.3390/ma13071707
![]() |
[26] |
Cornacchia F, Fabbrocino F, Fantuzzi N, et al. (2021) Analytical solution of cross-and angle-ply nano plates with strain gradient theory for linear vibrations and buckling. Mech Adv Mater Struc 28: 1201–1215. https://doi.org/10.1080/15376494.2019.1655613 doi: 10.1080/15376494.2019.1655613
![]() |
[27] |
Tocci MG, Fantuzzi N, Fabbrocino F, et al. (2021) Critical temperatures for vibrations and buckling of magneto-electro-elastic nonlocal strain gradient plates. Nanomaterials 11: 87. https://doi.org/10.3390/nano11010087 doi: 10.3390/nano11010087
![]() |
[28] |
Luciano R, Darban H, Bartolomeo C, et al. (2020) Free flexural vibrations of nanobeams with non-classical boundary conditions using stress-driven nonlocal model. Mech Res Commun 107: 103536. https://doi.org/10.1016/j.mechrescom.2020.103536 doi: 10.1016/j.mechrescom.2020.103536
![]() |
[29] |
Fabbrocino F, Funari MF, Greco F, et al. (2019) Dynamic crack growth based on moving mesh method. Compos Part B-Eng 174: 107053. https://doi.org/10.1016/j.compositesb.2019.107053 doi: 10.1016/j.compositesb.2019.107053
![]() |
[30] |
Fan F, Xu Y, Sahmani S, et al. (2020) Modified couple stress-based geometrically nonlinear oscillations of porous functionally graded microplates using NURBS-based isogeometric approach. Comput Method Appl M 372: 113400. https://doi.org/10.1016/j.cma.2020.113400 doi: 10.1016/j.cma.2020.113400
![]() |
[31] |
Hou F, Wu S, Moradi Z, et al. (2022) The computational modeling for the static analysis of axially functionally micro cylindrical imperfect beam applying the computer simulation. Eng Comput-Germany 38: 3217–3235. https://doi.org/10.1007/s00366–021–01456–x doi: 10.1007/s00366–021–01456–x
![]() |
[32] |
Li L, Li XB, Hu YJ (2018) Nonlinear bending of a two-dimensionally functionally graded beam. Compos Struct 184: 1049–1061. https://doi.org/10.1016/j.compstruct.2017.10.087 doi: 10.1016/j.compstruct.2017.10.087
![]() |
[33] |
Ye T, Qian D (2019) Nonlinear vibration analysis of a bi-directional functionally beam under hygro-thermal loads. Compos Struct 225: 111076. https://doi.org/10.1016/j.compstruct.2019.111076 doi: 10.1016/j.compstruct.2019.111076
![]() |
[34] |
Dehrouyeh-Semnani AM (2018) On the thermally induced non-linear response of functionally beams. Int J Eng Sci 125: 53–74. https://doi.org/10.1016/j.ijengsci.2017.12.001 doi: 10.1016/j.ijengsci.2017.12.001
![]() |
[35] |
Krysko AV, Awrejcewicz J, Pavlov SP, et al. (2017) Chaotic dynamics of the size-dependent non-linear micro-beam model. Commun Nonlinear Sci 50: 16–28. https://doi.org/10.1016/j.cnsns.2017.02.015 doi: 10.1016/j.cnsns.2017.02.015
![]() |
[36] |
Eltaher MA, Fouda N, El-midany T, et al. (2018) Modified porosity model in analysis of functionally graded porous nano-beams. J Braz Soc Mech Sci Eng 40: 1–10. https://doi.org/10.1007/s40430–018–1065–0 doi: 10.1007/s40430–018–1065–0
![]() |
[37] |
Mirjavadi SS, Mohasel AB, Khezel M, et al. (2018) Nonlinear vibration and buckling of functionally graded porous nanoscaled beams. J Braz Soc Mech Sci Eng 40: 1–12. https://doi.org/10.1007/s40430–018–1272–8 doi: 10.1007/s40430–018–1272–8
![]() |
[38] |
Shafiei N, Mirjavadi SS, Afshari BM, et al. (2017) Vibration of two-dimensional imperfect functionally (2D-FG) porous nano-/micro-beams. Comput Method Appl M 322: 615–632. https://doi.org/10.1016/j.cma.2017.05.007 doi: 10.1016/j.cma.2017.05.007
![]() |
[39] |
She GL, Yuan FG, Ren YR (2017) Thermal buckling and post-buckling analysis of functionally graded beams based on a general higher-order shear deformation theory. Appl Math Model 47: 340–357. https://doi.org/10.1016/j.apm.2017.03.014 doi: 10.1016/j.apm.2017.03.014
![]() |
[40] |
Belarbi M, Houari M, Daikh AA, et al. (2021) Nonlocal finite element model for the bending and buckling analysis of functionally graded nano-beams using a novel shear deformation theory. Composite Struct 264: 113712. https://doi.org/10.1016/j.compstruct.2019.02.089 doi: 10.1016/j.compstruct.2019.02.089
![]() |
[41] |
Akbaş ŞD, Dastjerdi S, Akgöz B, et al. (2021) Dynamic analysis of functionally graded porous microbeams under moving load. Transp Porous Med 142: 209–227. https://doi.org/10.1007/s11242–021–01686–z doi: 10.1007/s11242–021–01686–z
![]() |
[42] |
Dang VH, Do QC (2021) Nonlinear vibration and stability of functionally graded porous microbeam under electrostatic actuation. Arch Appl Mech 91: 2301–2329. https://doi.org/10.1007/s00419–021–01884–7 doi: 10.1007/s00419–021–01884–7
![]() |
[43] |
Pham QH, Tran VK, Tran TT, et al. (2022) Dynamic instability of mag-netically embedded functionally porous nano-beams using the strain gradient theory. Alex Eng J 61: 10025–10044. https://doi.org/10.1016/j.aej.2022.03.007 doi: 10.1016/j.aej.2022.03.007
![]() |
[44] |
Hosseini SA, Hamidi BA, Behrouzinia A (2022) A new model for non-linear vibration of functionally graded porous nano-beam based on non-local curvature and strain gradient tensors. J Vib Control 29: 4290–4301. https://doi.org/10.1177/10775463221114945 doi: 10.1177/10775463221114945
![]() |
[45] |
Nguyen DK, Nguyen KV, Dinh V, et al. (2018) Nonlinear bending of elasto-plastic functionally ceramic-metal beams subjected to nonuniform distributed loads. Appl Math Comput 333: 443–459. https://doi.org/10.1016/j.amc.2018.03.100 doi: 10.1016/j.amc.2018.03.100
![]() |
[46] |
Wu Q, Qi G (2021) Quantum dynamics for Al-doped graphene composite sheet under hydrogen atom impact. Appl Math Model 90: 1120–1129. https://doi.org/10.1016/j.apm.2020.10.025 doi: 10.1016/j.apm.2020.10.025
![]() |
[47] |
Wu Q, Yao M, Li M, et al. (2020) Nonlinear coupling vibrations of graphene composite laminated sheets impacted by particles. Appl Math Model 93: 75–88. https://doi.org/10.1016/j.apm.2020.12.008 doi: 10.1016/j.apm.2020.12.008
![]() |
[48] |
Wu Q, Yao M, Niu Y (2022) Nonplanar free and forced vibrations of an imperfect nanobeam employing nonlocal strain gradient theory. Commun Nonlinear Sci 114: 106692. https://doi.org/10.1016/j.cnsns.2022.106692 doi: 10.1016/j.cnsns.2022.106692
![]() |
[49] |
Karami B, Shahsavari D, Janghorban M, et al. (2019) Resonance behavior of functionally graded polymer composite nanoplates reinforced with graphene nanoplatelets. Int J Mech Sci 156: 94–105. https://doi.org/10.1016/j.ijmecsci.2019.03.036 doi: 10.1016/j.ijmecsci.2019.03.036
![]() |
[50] |
Voigt W (1889) Ueber die Beziehung zwischen den beiden Elasticitätsconstanten isotroper Körper. Ann Phys-Berlin 274: 573–587. https://doi.org/10.1002/andp.18892741206 doi: 10.1002/andp.18892741206
![]() |
[51] |
Reuß A (1929) Berechnung der fließgrenze von mischkristallen auf grund der plastizitätsbedingung für einkristalle. Z Angew Math Mech 9: 49–58. https://doi.org/10.1002/zamm.19290090104 doi: 10.1002/zamm.19290090104
![]() |
[52] |
Gasik MM, Lilius RR (1994) Evaluation of properties of W/Cu functional gradient materials by micromechanical model. Comp Mater Sci 3: 41–49. https://doi.org/10.1016/0927–0256(94)90151–1 doi: 10.1016/0927–0256(94)90151–1
![]() |
[53] |
Zuiker JR (1995) Functionally graded materials: Choice of micromechanics model and limitations in property variation. Compos Eng 5: 807–819. https://doi.org/10.1016/0961–9526(95)00031–H doi: 10.1016/0961–9526(95)00031–H
![]() |
[54] | Tamura I, Tomota Y, Ozawa M (1973) Strength and ductility of Fe-Ni-C alloys composed of austenite and martensite with various strength. Proc Third Int Conf Strength Met Alloy 3: 611–615. |
[55] |
Mori T, Tanaka K (1973) Average stress in matrix and average elastic energy of materials with misfitting inclusions. Acta Metall 21: 571–574. https://doi.org/10.1016/0001–6160(73)90064–3 doi: 10.1016/0001–6160(73)90064–3
![]() |
[56] |
Belabed Z, Houari MSA, Tounsi A, et al. (2014) An efficient and simple higher order shear and normal deformation theory for functionally graded material (FGM) plates. Compos Part B-Eng 60: 274–283. https://doi.org/10.1016/j.compositesb.2013.12.057 doi: 10.1016/j.compositesb.2013.12.057
![]() |
[57] |
Valizadeh N, Natarajan S, Gonzalez-Estrada OA, et al. (2013) NURBS-based finite element analysis of functionally graded plates: Static bending, vibration, buckling and flutter. Compos Struct 99: 309–326. https://doi.org/10.1016/j.compstruct.2012.11.008 doi: 10.1016/j.compstruct.2012.11.008
![]() |
[58] |
Cheng ZQ, Batra RC (2000) Three-dimensional thermoelastic deformations of a functionally graded elliptic plate. Compos Eng 31: 97–106. https://doi.org/10.1016/S1359–8368(99)00069–4 doi: 10.1016/S1359–8368(99)00069–4
![]() |
[59] |
Zemri A, Houari MSA, Bousahla AA, et al. (2015) A mechanical response of functionally graded nanoscale beam: An assessment of a refined nonlocal shear deformation theory beam theory. Struct Eng Mech 54: 693–710. https://doi.org/10.12989/SEM.2015.54.4.693 doi: 10.12989/SEM.2015.54.4.693
![]() |
1. | Yuda Hu, Tao Yang, Magneto-thermoelastic coupled resonance characteristics of a rotating functionally graded ferromagnetic cylindrical shell under double harmonic line loads, 2024, 145, 12709638, 108871, 10.1016/j.ast.2024.108871 | |
2. | Mostefa Rabehi, Billel Rebai, Mustapha Meradjah, Malek Hadji, Parametric investigations on dynamic responses of porous functionally graded al/al2o3 plates: effects of homogenization models and material distributions, 2024, 5, 2764-0981, e9051, 10.54021/seesv5n2-323 | |
3. | Abdelmadjid Chehhat, Billel Rebai, Convective heat transfer analysis of circular tube-annular tube systems with nanofluids: a comparative study, 2024, 5, 2764-0981, e9386, 10.54021/seesv5n2-359 | |
4. | Bouali Hichem, Faicel Khadraoui, Mourad Chitour, Khelifa Mansouri, Sofiane Touati, Haithem Boumediri, Nabil Himeur, Berkia Abdelhak, The impact of notch length and applied pressure on the development of confinement stress T within a pipe arc subjected to internal pressure, 2024, 5, 2764-0981, e12024, 10.54021/seesv5n2-754 | |
5. | Abir Lamari, Hicham Bourouina, Nonlocal Vibration Response of Double FG Porous Microbeams Adsorber with 2D PSH Network Under Magnetic Intensity for Large Frequency Range, 2025, 13, 2523-3920, 10.1007/s42417-024-01571-1 | |
6. | Mostefa Rabehi, Billel Rebai, Mustapha Meradjah, Ashraf M. Zenkour, Porosity Investigations on Dynamic Responses of FG Plates via a Modified Quasi-3D Shear Deformation Theory, 2025, 13, 2523-3920, 10.1007/s42417-024-01681-w |
Young's modulus (GPa) | Mass density (kg/m3) | Poisson' sratio | |
Stainless steel (SUS304) | 210 | 7800 | 0.3 |
Aluminum (Al) | 70 | 2702 | 0.3 |
Airconia (ZrO2) | 151 | 3000 | 0.3 |
Aluminia (Al2O3) | 380 | 3800 | 0.3 |
Silicon carbide (SiC) | 420 | 3210 | 0.3 |
l/h | p | 0 | 0.5 | 1 | |||||||||
Zemri | Tanaka | Tamura | Reuss | Zemri | Tanaka | Tamura | Reuss | Zemri | Tanaka | Tamura | Reuss | ||
10 | 0 | 9.7075 | 9.7075 | 9.7075 | 9.7075 | 9.5899 | 9.5899 | 9.5899 | 9.5899 | 9.2612 | 9.2612 | 9.2612 | 9.2612 |
1 | 6.8814 | 6.6246 | 7.0040 | 7.0040 | 6.7981 | 6.5444 | 6.9192 | 6.9191 | 6.5651 | 6.3201 | 6.6820 | 6.6820 | |
3 | 6.0755 | 5.9100 | 6.1186 | 6.1185 | 6.0019 | 5.8384 | 6.0444 | 6.0444 | 5.7962 | 5.6383 | 5.8373 | 5.8373 | |
10 | 5.5768 | 5.4494 | 5.5425 | 5.5425 | 5.5092 | 5.3834 | 5.4754 | 5.4754 | 5.3204 | 5.1989 | 5.2877 | 5.2877 | |
30 | 0 | 9.8511 | 9.8510 | 9.8510 | 9.8510 | 9.8376 | 9.8376 | 9.8376 | 9.8376 | 9.7975 | 9.7975 | 9.7975 | 9.7975 |
1 | 6.9832 | 6.7265 | 7.1113 | 7.1113 | 6.9737 | 6.7173 | 7.1016 | 7.1015 | 6.9452 | 6.6899 | 7.0726 | 7.0726 | |
3 | 6.1712 | 6.0038 | 6.2162 | 6.2161 | 6.1627 | 5.9956 | 6.2077 | 6.2076 | 6.1376 | 5.9711 | 6.1823 | 6.1823 | |
10 | 5.6655 | 5.5340 | 5.6290 | 5.6290 | 5.6578 | 5.5264 | 5.6213 | 5.6213 | 5.6347 | 5.5039 | 5.5984 | 5.5984 | |
100 | 0 | 9.8679 | 9.8679 | 9.8679 | 9.8679 | 9.8667 | 9.8667 | 9.8667 | 9.8667 | 9.8631 | 9.8631 | 9.8630 | 9.8630 |
1 | 6.9952 | 6.7384 | 7.1239 | 7.1239 | 6.9943 | 6.7376 | 7.1230 | 7.1230 | 6.9917 | 6.7351 | 7.1204 | 7.1204 | |
3 | 6.1824 | 6.0148 | 6.2276 | 6.2276 | 6.1817 | 6.0140 | 6.2269 | 6.2268 | 6.1794 | 6.0118 | 6.2246 | 6.2245 | |
10 | 5.6759 | 5.5439 | 5.6392 | 5.6391 | 5.6752 | 5.5432 | 5.6385 | 5.6385 | 5.6731 | 5.5411 | 5.6364 | 5.6364 |
l/h | p | 1.5 | 2 | ||||||
Zemri | Tanaka | Tamura | Reuss | Zemri | Tanaka | Tamura | Reuss | ||
10 | 0 | 8.7813 | 8.7813 | 8.7813 | 8.7813 | 8.2197 | 8.2197 | 8.2197 | 8.2196 |
1 | 6.2249 | 5.9926 | 6.3357 | 6.3357 | 5.8267 | 5.6093 | 5.9305 | 5.9305 | |
3 | 5.4959 | 5.3462 | 5.5348 | 5.5348 | 5.1443 | 5.0042 | 5.1808 | 5.1808 | |
10 | 5.0447 | 4.9295 | 5.0137 | 5.0137 | 4.7221 | 4.6142 | 4.6930 | 4.6930 | |
30 | 0 | 9.7318 | 9.7318 | 9.7317 | 9.7317 | 9.6419 | 9.6418 | 9.6419 | 9.6418 |
1 | 6.8987 | 6.6450 | 7.0252 | 7.0251 | 6.8349 | 6.5836 | 6.9603 | 6.9603 | |
3 | 6.0964 | 5.9310 | 6.1409 | 6.1408 | 6.0401 | 5.8763 | 6.0841 | 6.0841 | |
10 | 5.5969 | 5.4669 | 5.5608 | 5.5608 | 5.5452 | 5.4164 | 5.5095 | 5.5094 | |
100 | 0 | 9.8570 | 9.8570 | 9.8570 | 9.8569 | 9.8485 | 9.8485 | 9.8485 | 9.8485 |
1 | 6.9874 | 6.7310 | 7.1160 | 7.1160 | 6.9814 | 6.7252 | 7.1099 | 7.1099 | |
3 | 6.1756 | 6.0081 | 6.2207 | 6.2207 | 6.1703 | 6.0030 | 6.2154 | 6.2153 | |
10 | 5.6697 | 5.5377 | 5.6329 | 5.6329 | 5.6648 | 5.5330 | 5.6281 | 5.6280 |
Young's modulus (GPa) | Mass density (kg/m3) | Poisson' sratio | |
Stainless steel (SUS304) | 210 | 7800 | 0.3 |
Aluminum (Al) | 70 | 2702 | 0.3 |
Airconia (ZrO2) | 151 | 3000 | 0.3 |
Aluminia (Al2O3) | 380 | 3800 | 0.3 |
Silicon carbide (SiC) | 420 | 3210 | 0.3 |
l/h | p | 0 | 0.5 | 1 | |||||||||
Zemri | Tanaka | Tamura | Reuss | Zemri | Tanaka | Tamura | Reuss | Zemri | Tanaka | Tamura | Reuss | ||
10 | 0 | 9.7075 | 9.7075 | 9.7075 | 9.7075 | 9.5899 | 9.5899 | 9.5899 | 9.5899 | 9.2612 | 9.2612 | 9.2612 | 9.2612 |
1 | 6.8814 | 6.6246 | 7.0040 | 7.0040 | 6.7981 | 6.5444 | 6.9192 | 6.9191 | 6.5651 | 6.3201 | 6.6820 | 6.6820 | |
3 | 6.0755 | 5.9100 | 6.1186 | 6.1185 | 6.0019 | 5.8384 | 6.0444 | 6.0444 | 5.7962 | 5.6383 | 5.8373 | 5.8373 | |
10 | 5.5768 | 5.4494 | 5.5425 | 5.5425 | 5.5092 | 5.3834 | 5.4754 | 5.4754 | 5.3204 | 5.1989 | 5.2877 | 5.2877 | |
30 | 0 | 9.8511 | 9.8510 | 9.8510 | 9.8510 | 9.8376 | 9.8376 | 9.8376 | 9.8376 | 9.7975 | 9.7975 | 9.7975 | 9.7975 |
1 | 6.9832 | 6.7265 | 7.1113 | 7.1113 | 6.9737 | 6.7173 | 7.1016 | 7.1015 | 6.9452 | 6.6899 | 7.0726 | 7.0726 | |
3 | 6.1712 | 6.0038 | 6.2162 | 6.2161 | 6.1627 | 5.9956 | 6.2077 | 6.2076 | 6.1376 | 5.9711 | 6.1823 | 6.1823 | |
10 | 5.6655 | 5.5340 | 5.6290 | 5.6290 | 5.6578 | 5.5264 | 5.6213 | 5.6213 | 5.6347 | 5.5039 | 5.5984 | 5.5984 | |
100 | 0 | 9.8679 | 9.8679 | 9.8679 | 9.8679 | 9.8667 | 9.8667 | 9.8667 | 9.8667 | 9.8631 | 9.8631 | 9.8630 | 9.8630 |
1 | 6.9952 | 6.7384 | 7.1239 | 7.1239 | 6.9943 | 6.7376 | 7.1230 | 7.1230 | 6.9917 | 6.7351 | 7.1204 | 7.1204 | |
3 | 6.1824 | 6.0148 | 6.2276 | 6.2276 | 6.1817 | 6.0140 | 6.2269 | 6.2268 | 6.1794 | 6.0118 | 6.2246 | 6.2245 | |
10 | 5.6759 | 5.5439 | 5.6392 | 5.6391 | 5.6752 | 5.5432 | 5.6385 | 5.6385 | 5.6731 | 5.5411 | 5.6364 | 5.6364 |
l/h | p | 1.5 | 2 | ||||||
Zemri | Tanaka | Tamura | Reuss | Zemri | Tanaka | Tamura | Reuss | ||
10 | 0 | 8.7813 | 8.7813 | 8.7813 | 8.7813 | 8.2197 | 8.2197 | 8.2197 | 8.2196 |
1 | 6.2249 | 5.9926 | 6.3357 | 6.3357 | 5.8267 | 5.6093 | 5.9305 | 5.9305 | |
3 | 5.4959 | 5.3462 | 5.5348 | 5.5348 | 5.1443 | 5.0042 | 5.1808 | 5.1808 | |
10 | 5.0447 | 4.9295 | 5.0137 | 5.0137 | 4.7221 | 4.6142 | 4.6930 | 4.6930 | |
30 | 0 | 9.7318 | 9.7318 | 9.7317 | 9.7317 | 9.6419 | 9.6418 | 9.6419 | 9.6418 |
1 | 6.8987 | 6.6450 | 7.0252 | 7.0251 | 6.8349 | 6.5836 | 6.9603 | 6.9603 | |
3 | 6.0964 | 5.9310 | 6.1409 | 6.1408 | 6.0401 | 5.8763 | 6.0841 | 6.0841 | |
10 | 5.5969 | 5.4669 | 5.5608 | 5.5608 | 5.5452 | 5.4164 | 5.5095 | 5.5094 | |
100 | 0 | 9.8570 | 9.8570 | 9.8570 | 9.8569 | 9.8485 | 9.8485 | 9.8485 | 9.8485 |
1 | 6.9874 | 6.7310 | 7.1160 | 7.1160 | 6.9814 | 6.7252 | 7.1099 | 7.1099 | |
3 | 6.1756 | 6.0081 | 6.2207 | 6.2207 | 6.1703 | 6.0030 | 6.2154 | 6.2153 | |
10 | 5.6697 | 5.5377 | 5.6329 | 5.6329 | 5.6648 | 5.5330 | 5.6281 | 5.6280 |