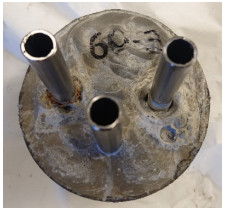
Cement-steel interfacial strength is an important measure for estimating the robustness and hydraulic sealing ability of wells. In this paper, laboratory experiments were performed in which small steel pipes (10 mm in diameter) were cemented in place within a Portland cement slurry under application of constant electrical potential difference between the pipes. The objective was to investigate whether there might be an observable difference between push-out strengths obtained with the pipes of different polarity (anode vs. cathode vs. reference nonpolarized pipe). The duration of the potential application and the magnitude of the potential difference were varied between the tests. The experiments demonstrated that at the higher potential difference (4 V), the duration of potential application had a noticeable effect on interfacial bonding. Application of 4 V for 24 h resulted in loss of bonding at cement-cathode interface, which could be attributed to massive water transportation to the cathode region by small radii cations. At the lower applied potential difference (1 V), there is an improvement in push-out strength at anode at short duration of potential application. This could be due to pore filling by precipitation of expansive minerals in pores and cement particles migration toward anode. The effect of potential on push-out strength in a hardened cement suggests that low potential difference applied for a short period of time might improve cement-steel interfacial strength.
Citation: Alexandre Lavrov, Benjamin Werner, Anna Stroisz, Thomas Monge Øia, Kamila Gawel, Malin Torsæter, Narjes Jafariesfad. Effect of electric field on push-out strength of cemented steel pipes[J]. AIMS Materials Science, 2021, 8(3): 373-389. doi: 10.3934/matersci.2021024
[1] | Alexandre Lavrov, Kamila Gawel, Malin Torsæter . Manipulating cement-steel interface by means of electric field: Experiment and potential applications. AIMS Materials Science, 2016, 3(3): 1199-1207. doi: 10.3934/matersci.2016.3.1199 |
[2] | Alexandre Lavrov, Elvia Anabela Chavez Panduro, Kamila Gawel, Malin Torsæter . Electrophoresis-induced structural changes at cement-steel interface. AIMS Materials Science, 2018, 5(3): 414-421. doi: 10.3934/matersci.2018.3.414 |
[3] | Mohamed Samy El-Feky, Passant Youssef, Ahmed Maher El-Tair, Sara Ibrahim, Mohamed Serag . Effect of nano silica addition on enhancing the performance of cement composites reinforced with nano cellulose fibers. AIMS Materials Science, 2019, 6(6): 864-883. doi: 10.3934/matersci.2019.6.864 |
[4] | Congyan Zhang, Feng Chen, Xudong Wang . Microstructural evolution and direct shear strength of cement-stabilized soil under freeze-thaw cycles. AIMS Materials Science, 2025, 12(1): 28-47. doi: 10.3934/matersci.2025003 |
[5] | Erno Widayanto, Agoes Soehardjono, Wisnumurti Wisnumurti, Achfas Zacoeb . The effect of vibropressing compaction process on the compressive strength based concrete paving blocks. AIMS Materials Science, 2020, 7(3): 203-216. doi: 10.3934/matersci.2020.3.203 |
[6] | M. Achyutha Kumar Reddy, V. Ranga Rao, K. Naga Chaitanya, Veerendrakumar C. Khed . Optimization of Bentocrete parameters using Response Surface Methodology (RSM). AIMS Materials Science, 2021, 8(2): 221-246. doi: 10.3934/matersci.2021015 |
[7] | Ahmed Al-Ramthan, Ruaa Al Mezrakchi . Investigation of cementitious composites reinforced with metallic nanomaterials, boric acid, and lime for infrastructure enhancement. AIMS Materials Science, 2024, 11(3): 495-514. doi: 10.3934/matersci.2024025 |
[8] | Mohamed Samy El-Feky, Passant Youssef, Ahmed El-Tair, Mohamed Serag . Indirect sonication effect on the dispersion, reactivity, and microstructure of ordinary portland cement matrix. AIMS Materials Science, 2019, 6(5): 781-797. doi: 10.3934/matersci.2019.5.781 |
[9] | Bauyrzhan Rakhadilov, Lyaila Bayatanova, Sherzod Kurbanbekov, Ravil Sulyubayev, Nurdaulet Shektibayev, Nurbol Berdimuratov . Investigation on the effect of technological parameters of electrolyte-plasma cementation method on phase structure and mechanical properties of structural steel 20X. AIMS Materials Science, 2023, 10(5): 934-947. doi: 10.3934/matersci.2023050 |
[10] | M. Kanta Rao, Ch. N. Satish Kumar . Influence of fly ash on hydration compounds of high-volume fly ash concrete. AIMS Materials Science, 2021, 8(2): 301-320. doi: 10.3934/matersci.2021020 |
Cement-steel interfacial strength is an important measure for estimating the robustness and hydraulic sealing ability of wells. In this paper, laboratory experiments were performed in which small steel pipes (10 mm in diameter) were cemented in place within a Portland cement slurry under application of constant electrical potential difference between the pipes. The objective was to investigate whether there might be an observable difference between push-out strengths obtained with the pipes of different polarity (anode vs. cathode vs. reference nonpolarized pipe). The duration of the potential application and the magnitude of the potential difference were varied between the tests. The experiments demonstrated that at the higher potential difference (4 V), the duration of potential application had a noticeable effect on interfacial bonding. Application of 4 V for 24 h resulted in loss of bonding at cement-cathode interface, which could be attributed to massive water transportation to the cathode region by small radii cations. At the lower applied potential difference (1 V), there is an improvement in push-out strength at anode at short duration of potential application. This could be due to pore filling by precipitation of expansive minerals in pores and cement particles migration toward anode. The effect of potential on push-out strength in a hardened cement suggests that low potential difference applied for a short period of time might improve cement-steel interfacial strength.
One of the primary concerns in well construction in oil, gas, CO2 storage and geothermal industries is well integrity: wells should not leak. For all these purposes, wells are constructed by drilling through sections of the subsurface and cementing in place steel pipes in the hole at predetermined intervals before drilling deeper. This results in wells obtaining a "telescopic" structure of cemented steel pipes of progressively smaller diameters with depth. The annular cement sheaths in these wells, which reside in the spaces between pipes, or between the drilled rock and pipes, should ensure both mechanical stability of the well and hydraulic sealing. Cement is a material chosen for well construction purposes because of its availability, price, robustness and similarity to surrounding geomaterials [1].
During the well life, annular cement is subject to thermal and mechanical loads as formation fluids are pumped out of the well or different fluids are injected into the well [2]. These stress variations may lead to failure in the annular cement in a number of ways [3]. In particular, tensile radial stresses acting at the interface between cement and casing may induce microannulus, i.e. a thin discontinuity (separation) between the cement and the casing [4,5]. Within the paradigm currently prevailing in the industry, tensile failure and formation of microannulus are counteracted by the bonding between cement and steel. Bonding strength is defined as the amount of tensile normal stress that needs to be applied at the interface in order to separate cement from steel.
Tensile strength of the interface is most interesting when the bonding strength is to be evaluated. Due to technical reasons, however, shear strength of the interface is most commonly measured in laboratory tests. Push-out test is used to measure the shear strength in the laboratory [1,6,7,8,9]. In this test, a steel pipe having the diameter on the order of 1 cm is cemented in bulk cement. After cement has hardened, an increasing axial displacement is applied to the pipe with a constant displacement rate. The axial load is monitored. The peak load achieved in the test, before the pipe slides out, divided by the cement-steel contact area, yields the push-out strength. This parameter is commonly accepted as a measure of cement-steel bonding strength.
The concept of bonding strength was recently challenged when it was found that this parameter depends on the pipe diameter in push-out tests: it decreases with the latter [10]. When the interface between steel and cement is flat (i.e., has infinite radius of curvature), the adhesive "bonding strength" may be as low as zero [11]. The non-zero push-out strength measured in laboratory experiments might be due e.g. to frictional resistance that develops at the interface because of non-zero normal stress that, in turn, might be due to cement shrinkage (as cement shrinks onto the pipe). Larger pipe diameter results in smaller normal stresses and, thus, in smaller frictional resistance, just as obtained in the experiments [10]. In downhole conditions, the bonding strength can be further reduced by impurities at the interface (e.g., leftover mud or spacer fluid that has not been properly removed before pumping cement, or influx of fluid from surrounding rock formations).
Low or zero magnitudes of the steel-cement bonding strength motivates continuous search for cement additives and casing coating materials that could improve the bonding quality. A radically different approach was recently proposed, namely to improve the bonding by applying electric potential to the well pipe, thereby inducing electrophoresis in cement [12]. Cement slurries contain charged solid particles [13,14]. Experiments indicate that placing two electrodes in a Portland G cement slurry and applying potential difference between them results in a clump of cement accumulating at the positive electrode, while the negative electrode is effectively kept clean. A reference electrode with no potential in the same slurry showed intermediate levels of cement slurry bonding [12]. In addition to the visually observed clumping of cement slurry at the positive electrode, microscopic properties of the transition zone between cement and steel are also different at the positive and negative electrodes [15].
These results may be due to several effects, including electrophoresis: when electric field is applied to the slurry, charged particles start moving towards the electrode of the opposite polarity [16]. The phenomenon of electrophoresis was discovered at the beginning of 1800s and has found several industrial applications over the past two centuries. Electrokinetic-based techniques have been applied in concrete industry. They have also been considered for application in well construction. These techniques can be used to modify microstructure of cement-based systems and enhance their performance in the long term [17].
Preliminary experiments with electrophoresis were reported in [12]. The tests in these experiments were terminated before cement could set. Therefore, push-out strength was not measured. It was only visually observed that a clump of cement was attached to the positive electrode when the electrode was extracted from the slurry after 18 minutes of exposure to the electric field (18 V was applied between the electrodes). If electrophoresis is to be used in wells to improve cement-steel bonding, the bonding strength of the hardened cement needs to be quantified for both electrodes. Furthermore, the concept, if successful, needs to be tested for different cement compositions, potential magnitudes, types of current (AC vs. DC, different shapes of the AC signal, etc.), temperatures, and pressures. The objective of the current study was to investigate the effect of potential applied to cemented steel pipes on the push-out strength after cement has hardened.
A remark is due, at this point, on the feasibility of using potential on casing to improve the cement-casing bonding in wells. Even though the practical aspects of potential application to a tubing in the well might seem challenging, this task can be accomplished in at least two ways, as demonstrated in previous studies. As one option, potential could be applied directly to the tubing. This has been recently done in Iceland, where potential applied to casing strings in two neighbouring wells was used to map the conductive fracture network between the wells placed in a geothermal reservoir [18]. In another study [19,20], it was proposed to apply (negative) electric potential to drill bits during well drilling in order to repel clay particles and to improve lubrication. However, even though applying potential to the drillpipe or casing appears to be technically feasible, leakage currents may be an issue for the "electric casing" concept in our case. These currents might prevent a uniform effect on the cement-steel contact along the entire casing string, which can be many hundred meters long. As a second option, therefore, electric potential can be created on the pipe by using an electrostatic coating. As an example, electro-negative surface coating has been applied to drill bits in order to repel clay particles and thus reduce bit balling [21]. This was achieved by applying a nitriding process to the steel surface. A similar approach might be envisioned for the current proposed "electric casing". The surface potential could be more uniform and more controlled in this case compared to a direct application of potential.
It should be noted at this point that the objective of the study reported herein was not to develop a practical method of applying potential on casing but to investigate the fundamental question of whether such potential can indeed improve the bonding strength between steel and cement.
Two series of experiments were performed. In the first series (17 experiments), the potential difference between anode and cathode was 4 V. In the second series (15 experiments), the potential difference between anode and cathode was 1 V. In each experiment, three stainless steel pipes were placed in a bucket with Portland G cement slurry (Figure 1). The same slurry composition (w/c = 0.44) and cement preparation method were used in all the experiments. Pipes were placed in cement in such way that they went through the whole cement body. Potential was applied between two of these electrodes, while the third electrode had zero applied potential and thus served as a reference electrode in push-out strength measurements. A special setup was developed in order to ensure that the pipes remained parallel during cement hardening (Figure 2). All pipes had the same diameter, 10 mm in order to avoid the size-dependency reported in [10]. A source of constant electric potential Keysight Technologies B2901A Precision Source/Measure Unit was used to apply potential between the pipes (Figure 2) and to measure the variation in current over time during the potential application. The potential difference applied between the pipes (4 V or 1 V) was held constant during the duration of potential application. The duration of potential application was 1 min, 5 min, 10 min, 60 min, or 24 h. The subsequent curing time was 3 d in all experiments. Even if this curing time is shorter than that applied in real well situations (typically 7 d), it was kept constant in all experiments that are compared in our study, and our work can thus give a reliable indication of the bonding effect of a given voltage-time treatment. Potential was always applied continuously and always at the very beginning of the curing time, 10 min after mixing cement powder with water. Experiments were conducted at ambient temperature (around 23 ℃) and atmospheric pressure.
After cement had hardened, a push-out test with constant displacement rate was performed on each of the three electrodes. Setup for the applied push-out test is shown in Figure 3. The order of testing of the three pipes was varied randomly between the tests in order to ensure that no systematic error be introduced by the order of testing1. Push-out tests were performed on an MTS load frame with the maximum loading capacity of 10 kN. The displacement rate during push-out test was 0.2 mm/min in all tests; after the peak load was reached, the displacement rate was increased to 2 mm/min and was maintained constant at that level.
1It should be noted that the distance between the cemented pipes was deemed sufficient to avoid interference between the pipes during the push-out tests, cf. Figure 1.
From the peak load obtained in a push-out test, the push-out strength was evaluated for each electrode in each test, by dividing the peak load by the measured area of the cement-steel contact.
The results obtained with 4 V DC are shown in Table 1 and Figures 4–6. It follows from Table 1 that push-out strength at the positive electrode, S+, was higher than push-out strength at the negative electrode, S-, in about half of the tests (9 tests out of 17). This is not what we had expected before we carried out the testing campaign. This apparent lack of strength enhancement at the positive electrode is, most likely, due to corrosion. This is indirectly confirmed by comparing the values of S+ and S- to the push-out strength measured at the reference electrode (no potential), S0. We have S- < S0 in 13 tests out of 17 (this is as expected), but S+ < S0 in 16 tests out of 17. Significant corrosion at the positive electrode was also confirmed by visual observation (Figure 7). Note also that in the four tests performed with potential application during 24 h (tests 64–67 in Table 1), the strength at the negative electrode (cathode) was measured to be zero: the pipe could be easily removed from the cement by hand. This could be due to the following reasons:
Specimen ID | Electrode polarity | Potential application duration | Push-out strength (MPa) |
50 | positive | 1 min | 0.87 |
negative | 1 min | 2.01 | |
reference | 1 min | 2.01 | |
51 | positive | 1 min | 2.10 |
negative | 1 min | 1.15 | |
reference | 1 min | 1.78 | |
52 | positive | 1 min | 1.26 |
negative | 1 min | 1.24 | |
reference | 1 min | 1.83 | |
53 | positive | 5 min | 0.64 |
negative | 5 min | 1.87 | |
reference | 5 min | 1.67 | |
55 | positive | 5 min | 0.24 |
negative | 5 min | 1.02 | |
reference | 5 min | 1.55 | |
56 | positive | 10 min | 0.34 |
negative | 10 min | 0.98 | |
reference | 10 min | 0.90 | |
57 | positive | 10 min | 0.44 |
negative | 10 min | 1.49 | |
reference | 10 min | 1.70 | |
58 | positive | 10 min | 2.33 |
negative | 10 min | 0.68 | |
reference | 10 min | 2.37 | |
59 | positive | 10 min | 0.33 |
negative | 10 min | 1.64 | |
reference | 10 min | 1.29 | |
60 | positive | 60 min | 0.43 |
negative | 60 min | 0.26 | |
reference | 60 min | 1.17 | |
61 | positive | 60 min | 0.37 |
negative | 60 min | 0.17 | |
reference | 60 min | 1.46 | |
62 | positive | 60 min | 0.24 |
negative | 60 min | 0.45 | |
reference | 60 min | 1.00 | |
63 | positive | 60 min | 0.38 |
negative | 60 min | 0.63 | |
reference | 60 min | 1.66 | |
64 | positive | 24 h | 1.23 |
negative | 24 h | 0.00 | |
reference | 24 h | 1.28 | |
65 | positive | 24 h | 0.81 |
negative | 24 h | 0.00 | |
reference | 24 h | 1.51 | |
66 | positive | 24 h | 1.34 |
negative | 24 h | 0.00 | |
reference | 24 h | 1.72 | |
67 | positive | 24 h | 1.12 |
negative | 24 h | 0.00 | |
reference | 24 h | 1.50 |
● Hydrogen production at that electrode since the applied potential difference of 4 V was above the electrolysis threshold of water that is 1.23 V
● Water film formation at the electrode surface due to transportation of high amount of water to cathode region under the applied electric field [22,23].
The main mechanism seems to be water transportation as the bonding at the other electrode (anode) was not that much affected by gas formation at its surface. The effect of gas production and water displacement at cathode region is clearly seen in Figure 7 (the void area around the farmost electrode in the image).
In order to eliminate the artifacts caused by water electrolysis, another series of experiments were conducted, this time with the potential difference of 1 V. The rest of the settings were identical to those used in experiments with 4 V. The results obtained with 1 V are shown in Table 2 and Figures 8–10.
Specimen ID | Electrode polarity | Potential application duration | Push-out strength (MPa) |
68 | positive | 1 min | 0.92 |
negative | 1 min | 1.21 | |
reference | 1 min | 0.78 | |
69 | positive | 1 min | 0.64 |
negative | 1 min | 0.72 | |
reference | 1 min | 0.57 | |
70 | positive | 1 min | 1.12 |
negative | 1 min | 1.02 | |
reference | 1 min | 0.95 | |
71 | positive | 5 min | 0.60 |
negative | 5 min | 0.61 | |
reference | 5 min | 0.54 | |
72 | positive | 5 min | 0.95 |
negative | 5 min | 0.84 | |
reference | 5 min | 0.92 | |
73 | positive | 5 min | 1.45 |
negative | 5 min | 1.18 | |
reference | 5 min | 1.36 | |
74 | positive | 10 min | 1.05 |
negative | 10 min | 0.85 | |
reference | 10 min | 0.89 | |
75 | positive | 10 min | 1.29 |
negative | 10 min | 0.77 | |
reference | 10 min | 1.31 | |
76 | positive | 10 min | 1.50 |
negative | 10 min | 1.16 | |
reference | 10 min | 1.30 | |
77 | positive | 60 min | 0.93 |
negative | 60 min | 1.11 | |
reference | 60 min | 1.10 | |
78 | positive | 60 min | 0.77 |
negative | 60 min | 0.28 | |
reference | 60 min | 0.78 | |
79 | positive | 60 min | 0.61 |
negative | 60 min | 0.64 | |
reference | 60 min | 0.91 | |
80 | positive | 24 h | 0.44 |
negative | 24 h | 0.67 | |
reference | 24 h | 0.52 | |
81 | positive | 24 h | 0.71 |
negative | 24 h | 1.15 | |
reference | 24 h | 0.98 | |
82 | positive | 24 h | 1.33 |
negative | 24 h | 1.50 | |
reference | 24 h | 1.56 |
It follows from Table 2 that push-out strength at the positive electrode, S+, was higher than push-out strength at the negative electrode, S-, in only 50% of the tests (7 tests out of 15; Figure 8). This is consistent with the results obtained with 4 V and is, again, contrary to what was expected before the testing campaign.
There is, however, a remarkable difference between the results obtained with 4 V and 1 V—in the latter case, and at potential application durations 1 min and 5 min, push-out strength values at the positive electrode were always higher than at the reference electrode. This is illustrated in Table 3 which displays ratios of push-out strength values obtained at anode (S+), cathode (S-), and reference electrode (S0), and in Figure 9, where the ratio between the two push out strength values is shown as a function of potential application duration. The strengthening effect of positive potential is most pronounced at the potential application duration of 1 min and is ca. 10–20% in those tests (tests No. 68, 69 and 70 in Table 2). Curiously, the push-out strength at cathode in those tests is also improved (compared to the reference pipe; Figure 10). In tests No. 68 and 69, the push-out strength at the cathode is even higher than at the anode.
Potential application duration (min) | S-/S+ | S-/S0 | S+/S0 |
1 | 1.32 | 1.55 | 1.18 |
1 | 1.13 | 1.26 | 1.12 |
1 | 0.91 | 1.07 | 1.18 |
5 | 1.02 | 1.13 | 1.11 |
5 | 0.88 | 0.91 | 1.03 |
5 | 0.81 | 0.87 | 1.07 |
10 | 0.81 | 0.96 | 1.18 |
10 | 0.60 | 0.59 | 0.98 |
10 | 0.77 | 0.89 | 1.15 |
60 | 1.19 | 1.01 | 0.85 |
60 | 0.36 | 0.36 | 0.99 |
60 | 1.05 | 0.70 | 0.67 |
1440 (24 h) | 1.52 | 1.29 | 0.85 |
1440 (24 h) | 1.62 | 1.17 | 0.72 |
1440 (24 h) | 1.13 | 0.96 | 0.85 |
Figure 11 presents two examples of the current variation with time during application of 1 V and 4 V. The steady-state current measured at 4 V is far above its value at 1 V. Under potential of 4 V and 1 V, the steady state currents were 70 mA and 0.01 mA, respectively.
The results of the experiments suggest that, when the applied potential is higher than the electrolysis potential of water (1.23 V), there is no consistent effect of either negative or positive potential compared to the reference electrode (zero potential). When the applied potential is below the electrolysis potential, and the potential application duration is short (1 min in our experiments), it significantly improves the push-out strength at both negative and positive electrode, namely by 10% to 50 %. The fact that this improvement occurs both at anode and cathode suggests that the mechanism behind this improvement is not only electrophoresis, as previously assumed [12].
There are several electrokinetic processes that take place at the cement-steel interface under the application of electric field. When an electric field is applied to an aqueous cement mixture, three migration mechanisms are in play [17]:
● Cement particles migration due to electrophoresis
● Ionic species movement due to electromigration
● Water migration due to electroosmosis
In the pore solution of fresh cement paste, ions such as OH–, SO42–, Na+, K+, and Ca2+ are present. Under an electric field, anions are repelled from the cathode and thus migrate in the direction of anode. Similarly, cations migrate to the cathode region [24]. The rate of ion migration depends on the applied electric field and the mobility of the ions, which is influenced by their charge, hydrodynamic diameter and the solution viscosity [25]. The mobility of the ions in the solution is expected to increase in the order Na+ < Ca2+ < K+ < SO42– < OH– [25,26]. Additionally, water molecules are transported to the electrodes as the ions migrating toward the electrode with the opposite sign [27]. This affects the water/cement ratio at the vicinity of the electrodes, which can significantly affect the cement-electrode interfacial bonding properties.
Under potential of 1 V (except for 1 V/24 h) and 4 V, the bonding strength at cathode decreases with increasing duration of potential application. Cement samples treated under 4 V for 24 h presented loss of bonding at cathode. This could be mainly due to high amount of water transported toward cathode with cations such as K+ and Na+, which have a high capacity in water carriage due to their small ionic radii [24]. Additionally, accumulation of alkali ions in the cathode region provokes formation of alkali hydroxides which can initiate softening of cement paste by increasing the solubility of cement silicate hydrates [24]. In addition, the alkaline conditions in the vicinity of the negative electrode may promote precipitation of portlandite, which may improve the push-out strength at the negative electrode.
Moreover, at 4 V, water electrolysis happens, which results in the formation of gas bubbles in the vicinity of electrodes. This can also be an extra source of bonding strength reduction, especially at the cathode where twice as large volume of gas is released as at anode. It has been previously shown that the main consequence of the gas evolution at the metal/concrete interface is the formation of pores due to the trapping of bubbles during hardening process which contributes to reduction of the contact area between metal and concrete and leads to adhesion retardation [28]. Application of 1 V for 24 h did not show a severe effect on bonding at cathode as observed for samples treated at 4 V. The bonding was slightly better at cathode compared to bonding at anode and reference electrode. This might be due to much lower electromigration force acting on ions under application of 1 V in comparison to 4 V. Thus, the transportation of ions and water under 1 V is far less than their transportation under 4 V. The measured steady-state currents under application of 1 V and 4 V were 0.01 mA and 70 mA respectively (Figure 11). However, the observed results for samples treated at 1 V for shorter duration suggest that they follow a trend similar to samples treated at 4 V. Therefore, further investigation is required to explain the observed result for sample treated at 1 V for 24 h.
At the positive electrode, it is difficult to find a consistent behaviour due to several opposing processes occurring at the anode-cement interface. Generally, the corrosion products at the electrode surface, especially at high voltages, could be detrimental to the bonding strength. However, at 1 V, slight formation of rust at anode surface may lead to increased push-out strength due to increased friction. Another process which may support enhancement of bonding is migration of negatively charged cement particles toward anode. This could be beneficial for particle compaction at the cement-anode interface resulting in better bonding. However, the mobility of cement particles is much lower than the mobility of common ions present in the pore solution. Thus, at 1 V, the migration rate of ions is more pronounced than that of cement particles, but at higher voltages cement particles accumulation at anode surface is obvious alongside the ions migration. Another process which could be increasing or decreasing the bonding quality at cement-anode interface is migration of sulphate ions to the anode region. The increased concentration of sulphate ions may lead to the formation of larger amounts of sulphate-containing phases such as gypsum and ettringite. On one hand, this may enhance expansive capabilities of cement which mitigates cement shrinkage, and also can result in tighter cement structure due to precipitation of expansive minerals in empty pores [29,30]. On the other hand, in case of applying high voltages, excessive formation of expansive phases occurs alongside consumption of calcium hydroxide, and massive formation of crystals can reduce the interfacial bonding [31]. Additionally, excessive expansion can destroy the microstructure of hardened cement by formation of cracks.
Student t-tests were performed on the data obtained with 1 V potential applied for 1 min. The t-tests have shown that, when all of the data is included, there is no significant difference between the strength values at anode and reference electrode. Neither is there a significant difference in strength between the cathode and the reference electrode for the overall dataset. In each experiment, however, the strength at the anode is higher than that at the reference electrode, and the strength at the cathode is higher than that at the reference electrode. The explanation for the outcome of the t-tests is that there is a large spread (scatter) between the strength values obtained at the anode (and, respectively, cathode) in different tests. This spread is so large that it exceeds the difference between each pair of electrodes in individual tests. It should be stressed, however, that in each individual test there is a consistent effect of the electric potential on push-out strength.
The experiments have confirmed that electric potential applied during cement hardening can be used to increase the push-out strength of steel pipes in Portland cement. Two necessary conditions must be met for this to work: the potential must be below the water electrolysis threshold, and the duration of potential application must be sufficiently short. It is still to be further investigated whether the effect persists at realistic conditions in industrial applications, with complex cement compositions and diverse environmental conditions.
The fact that both positive and negative low potential improve the strength suggests that AC could be used instead of DC. Further experiments should aim to investigate the effect of AC on adhesion and push-out strength. The challenge is how to separate contributions from the complex electrophoretic and electrochemical processes occurring at cement/steel interfaces to push-out strength changes. Further research should also address this topic.
This publication was produced in the project "Voltage on casing for improved well cement quality" (267651/E20) funded by the Research Council of Norway through the PETROMAKS2 program. Financial support from grant number 285568 "Well fossilization for P & A" funded by the Research Council of Norway is also acknowledged.
There is no conflict of interests.
[1] | Nelson EB, Guillot D (2006) Well Cementing, 2nd Eds., Schlumberger. |
[2] | Lavrov A, Torsæter M (2016) Physics and Mechanics of Primary Well Cementing, Springer. |
[3] |
Bois AP, Garnier A, Rodot F, et al. (2011) How to prevent loss of zonal isolation through a comprehensive analysis of microannulus formation. SPE Drill Completion 26: 13-31. doi: 10.2118/124719-PA
![]() |
[4] |
Aursand P, Hammer M, Lavrov A, et al. (2017) Well integrity for CO2 injection from ships: Simulation of the effect of flow and material parameters on thermal stresses. Int J Greenh Gas Con 62: 130-141. doi: 10.1016/j.ijggc.2017.04.007
![]() |
[5] |
Lavrov A, Torsæter M (2018) All microannuli are not created equal: Role of uncertainty and stochastic properties in well leakage prediction. Int J Greenh Gas Con 79: 323-328. doi: 10.1016/j.ijggc.2018.09.001
![]() |
[6] | Carpenter RB, Brady JL, Blount CG (1992) The effects of temperature and cement admixes on bond strength. J Petrol Technol 44: 880-886. |
[7] |
Carter LG, Evans GW (1964) A study of cement-pipe bonding. J Petrol Technol 16: 157-160. doi: 10.2118/764-PA
![]() |
[8] | Kakumoto M, Yoneda J, Tenma N, et al. (2012) Frictional strength between casing and cement under confining pressure. The 22nd International Offshore and Polar Engineering Conference, 77-82. |
[9] |
Sanz B, Planas J, Sancho JM (2018) Study of the loss of bond in reinforced concrete specimens with accelerated corrosion by means of push-out tests. Constr Build Mater 160: 598-609. doi: 10.1016/j.conbuildmat.2017.11.093
![]() |
[10] | Lavrov A, Bhuiyan M, Stroisz A (2019) Push-out test: Why bother? J Petrol Sci Eng 172: 297-302. |
[11] |
Lavrov A, Gawel K, Stroisz A, et al. (2017) Failure modes in three-point bending tests of cement-steel, cement-cement and cement-sandstone bi-material beams. Constr Build Mater 152: 880-886. doi: 10.1016/j.conbuildmat.2017.07.017
![]() |
[12] |
Lavrov A, Gawel K, Torsæter M (2016) Manipulating cement-steel interface by means of electric field: Experiment and potential applications. AIMS Mater Sci 3: 1199-1207. doi: 10.3934/matersci.2016.3.1199
![]() |
[13] |
Nachbaur L, Nkinamubanzi PC, Nonat A, et al. (1998) Electrokinetic properties which control the coagulation of silicate cement suspensions during early age hydration. J Colloid Interf Sci 202: 261-268. doi: 10.1006/jcis.1998.5445
![]() |
[14] |
Hodne H, Saasen A (2000) The effect of the cement zeta potential and slurry conductivity on the consistency of oil-well cement slurries. Cement Concrete Res 30: 1767-1772. doi: 10.1016/S0008-8846(00)00417-8
![]() |
[15] |
Lavrov A, Panduro EAC, Gawel K, et al. (2018) Electrophoresis-induced structural changes at cement-steel interface. AIMS Mater Sci 5: 414-421. doi: 10.3934/matersci.2018.3.414
![]() |
[16] | Westermeier R (2016) Electrophoresis in Practice, 5 Eds., Wiley. |
[17] | Jafariesfad N, Geiker MR, Sangesland S, et al. (2020) Electrokinetics application in concrete and well construction. ASME 2020 39th International Conference on Ocean, Offshore and Arctic Engineering (OMAE 2020). |
[18] | Magnusdottir L, Jonsson MT (2018) Geothermal well casings used as electrodes in a resistivity study at Reykjanes reservoir in Iceland. MDPI Proc 2: 475-480. |
[19] |
Roy S, Cooper GA (1993) Prevention of bit balling in shales—Preliminary results. SPE Drill Compl 8: 195-200. doi: 10.2118/23870-PA
![]() |
[20] | Cooper GA, Roy S (1994) Prevention of bit balling by electro-osmosis. SPE Western Regional Meeting, 23-25. |
[21] | Smith L, Mody FK, Hale A, et al. (1996) Successful field application of an electro-negative "coating" to reduce bit balling tendencies in water based mud. SPE/IADC Drilling Conference. |
[22] |
Goudjil N, Djelal C, Vanhove Y, et al. (2014) Impact of temperature on the demoulding of concrete elements with a polarization process. Constr Build Mater 54: 402-412. doi: 10.1016/j.conbuildmat.2013.12.034
![]() |
[23] |
Goudjil N, Vanhove Y, Djelal C, et al. (2012) Electro-osmosis applied for formwork removal of concrete. J Adv Concr Technol 10: 301-312. doi: 10.3151/jact.10.301
![]() |
[24] |
Ihekwaba NM, Hope BB, Hansson CM (1996) Pull-out and bond degradation of steel rebars in ECE concrete. Cement Concrete Res 26: 267-282. doi: 10.1016/0008-8846(95)00210-3
![]() |
[25] | Atkins P, De Paula J (2013) Elements of Physical Chemistry, USA: Oxford University Press. |
[26] |
Buenfeld NR, Glass GK, Hassanein AM, et al. (1998) Chloride transport in concrete subjected to electric field. J Mater Civil Eng 10: 220-228. doi: 10.1061/(ASCE)0899-1561(1998)10:4(220)
![]() |
[27] | Aligizaki KK (2012) Mechanisms of ion transport in cement-based materials during the application of corrosion mitigating electrical techniques. CORROSION 2012. |
[28] |
Di Franco F, Zaffora A, Megna B, et al. (2021) Heterogeneous crystallization of zinc hydroxystannate on galvanized steel for enhancing the bond strength at the rebar/concrete interface. Chem Eng J 405: 126943. doi: 10.1016/j.cej.2020.126943
![]() |
[29] |
Li W, Fall M (2016) Sulphate effect on the early age strength and self-desiccation of cemented paste backfill. Constr Build Mater 106: 296-304. doi: 10.1016/j.conbuildmat.2015.12.124
![]() |
[30] |
Pokharel M, Fall M (2013) Combined influence of sulphate and temperature on the saturated hydraulic conductivity of hardened cemented paste backfill. Cement Concrete Comp 38: 21-28. doi: 10.1016/j.cemconcomp.2013.03.015
![]() |
[31] |
Liu H, Bu Y, Nazari A, et al. (2016) Low elastic modulus and expansive well cement system: The application of gypsum microsphere. Constr Build Mater 106: 27-34. doi: 10.1016/j.conbuildmat.2015.12.105
![]() |
1. | Kamila Gawel, Sigurd Wenner, Narjes Jafariesfad, Malin Torsæter, Harald Justnes, Portland cement hydration in the vicinity of electrically polarized conductive surfaces, 2022, 134, 09589465, 104792, 10.1016/j.cemconcomp.2022.104792 | |
2. | Marcello Congro, Hans Joakim Skadsem, Katherine Beltrán-Jiménez, Deane Roehl, Experimental and numerical study on the pushout shear strength of conventional and expanding cement–casing sections for well integrity, 2024, 234, 29498910, 212638, 10.1016/j.geoen.2024.212638 |
Specimen ID | Electrode polarity | Potential application duration | Push-out strength (MPa) |
50 | positive | 1 min | 0.87 |
negative | 1 min | 2.01 | |
reference | 1 min | 2.01 | |
51 | positive | 1 min | 2.10 |
negative | 1 min | 1.15 | |
reference | 1 min | 1.78 | |
52 | positive | 1 min | 1.26 |
negative | 1 min | 1.24 | |
reference | 1 min | 1.83 | |
53 | positive | 5 min | 0.64 |
negative | 5 min | 1.87 | |
reference | 5 min | 1.67 | |
55 | positive | 5 min | 0.24 |
negative | 5 min | 1.02 | |
reference | 5 min | 1.55 | |
56 | positive | 10 min | 0.34 |
negative | 10 min | 0.98 | |
reference | 10 min | 0.90 | |
57 | positive | 10 min | 0.44 |
negative | 10 min | 1.49 | |
reference | 10 min | 1.70 | |
58 | positive | 10 min | 2.33 |
negative | 10 min | 0.68 | |
reference | 10 min | 2.37 | |
59 | positive | 10 min | 0.33 |
negative | 10 min | 1.64 | |
reference | 10 min | 1.29 | |
60 | positive | 60 min | 0.43 |
negative | 60 min | 0.26 | |
reference | 60 min | 1.17 | |
61 | positive | 60 min | 0.37 |
negative | 60 min | 0.17 | |
reference | 60 min | 1.46 | |
62 | positive | 60 min | 0.24 |
negative | 60 min | 0.45 | |
reference | 60 min | 1.00 | |
63 | positive | 60 min | 0.38 |
negative | 60 min | 0.63 | |
reference | 60 min | 1.66 | |
64 | positive | 24 h | 1.23 |
negative | 24 h | 0.00 | |
reference | 24 h | 1.28 | |
65 | positive | 24 h | 0.81 |
negative | 24 h | 0.00 | |
reference | 24 h | 1.51 | |
66 | positive | 24 h | 1.34 |
negative | 24 h | 0.00 | |
reference | 24 h | 1.72 | |
67 | positive | 24 h | 1.12 |
negative | 24 h | 0.00 | |
reference | 24 h | 1.50 |
Specimen ID | Electrode polarity | Potential application duration | Push-out strength (MPa) |
68 | positive | 1 min | 0.92 |
negative | 1 min | 1.21 | |
reference | 1 min | 0.78 | |
69 | positive | 1 min | 0.64 |
negative | 1 min | 0.72 | |
reference | 1 min | 0.57 | |
70 | positive | 1 min | 1.12 |
negative | 1 min | 1.02 | |
reference | 1 min | 0.95 | |
71 | positive | 5 min | 0.60 |
negative | 5 min | 0.61 | |
reference | 5 min | 0.54 | |
72 | positive | 5 min | 0.95 |
negative | 5 min | 0.84 | |
reference | 5 min | 0.92 | |
73 | positive | 5 min | 1.45 |
negative | 5 min | 1.18 | |
reference | 5 min | 1.36 | |
74 | positive | 10 min | 1.05 |
negative | 10 min | 0.85 | |
reference | 10 min | 0.89 | |
75 | positive | 10 min | 1.29 |
negative | 10 min | 0.77 | |
reference | 10 min | 1.31 | |
76 | positive | 10 min | 1.50 |
negative | 10 min | 1.16 | |
reference | 10 min | 1.30 | |
77 | positive | 60 min | 0.93 |
negative | 60 min | 1.11 | |
reference | 60 min | 1.10 | |
78 | positive | 60 min | 0.77 |
negative | 60 min | 0.28 | |
reference | 60 min | 0.78 | |
79 | positive | 60 min | 0.61 |
negative | 60 min | 0.64 | |
reference | 60 min | 0.91 | |
80 | positive | 24 h | 0.44 |
negative | 24 h | 0.67 | |
reference | 24 h | 0.52 | |
81 | positive | 24 h | 0.71 |
negative | 24 h | 1.15 | |
reference | 24 h | 0.98 | |
82 | positive | 24 h | 1.33 |
negative | 24 h | 1.50 | |
reference | 24 h | 1.56 |
Potential application duration (min) | S-/S+ | S-/S0 | S+/S0 |
1 | 1.32 | 1.55 | 1.18 |
1 | 1.13 | 1.26 | 1.12 |
1 | 0.91 | 1.07 | 1.18 |
5 | 1.02 | 1.13 | 1.11 |
5 | 0.88 | 0.91 | 1.03 |
5 | 0.81 | 0.87 | 1.07 |
10 | 0.81 | 0.96 | 1.18 |
10 | 0.60 | 0.59 | 0.98 |
10 | 0.77 | 0.89 | 1.15 |
60 | 1.19 | 1.01 | 0.85 |
60 | 0.36 | 0.36 | 0.99 |
60 | 1.05 | 0.70 | 0.67 |
1440 (24 h) | 1.52 | 1.29 | 0.85 |
1440 (24 h) | 1.62 | 1.17 | 0.72 |
1440 (24 h) | 1.13 | 0.96 | 0.85 |
Specimen ID | Electrode polarity | Potential application duration | Push-out strength (MPa) |
50 | positive | 1 min | 0.87 |
negative | 1 min | 2.01 | |
reference | 1 min | 2.01 | |
51 | positive | 1 min | 2.10 |
negative | 1 min | 1.15 | |
reference | 1 min | 1.78 | |
52 | positive | 1 min | 1.26 |
negative | 1 min | 1.24 | |
reference | 1 min | 1.83 | |
53 | positive | 5 min | 0.64 |
negative | 5 min | 1.87 | |
reference | 5 min | 1.67 | |
55 | positive | 5 min | 0.24 |
negative | 5 min | 1.02 | |
reference | 5 min | 1.55 | |
56 | positive | 10 min | 0.34 |
negative | 10 min | 0.98 | |
reference | 10 min | 0.90 | |
57 | positive | 10 min | 0.44 |
negative | 10 min | 1.49 | |
reference | 10 min | 1.70 | |
58 | positive | 10 min | 2.33 |
negative | 10 min | 0.68 | |
reference | 10 min | 2.37 | |
59 | positive | 10 min | 0.33 |
negative | 10 min | 1.64 | |
reference | 10 min | 1.29 | |
60 | positive | 60 min | 0.43 |
negative | 60 min | 0.26 | |
reference | 60 min | 1.17 | |
61 | positive | 60 min | 0.37 |
negative | 60 min | 0.17 | |
reference | 60 min | 1.46 | |
62 | positive | 60 min | 0.24 |
negative | 60 min | 0.45 | |
reference | 60 min | 1.00 | |
63 | positive | 60 min | 0.38 |
negative | 60 min | 0.63 | |
reference | 60 min | 1.66 | |
64 | positive | 24 h | 1.23 |
negative | 24 h | 0.00 | |
reference | 24 h | 1.28 | |
65 | positive | 24 h | 0.81 |
negative | 24 h | 0.00 | |
reference | 24 h | 1.51 | |
66 | positive | 24 h | 1.34 |
negative | 24 h | 0.00 | |
reference | 24 h | 1.72 | |
67 | positive | 24 h | 1.12 |
negative | 24 h | 0.00 | |
reference | 24 h | 1.50 |
Specimen ID | Electrode polarity | Potential application duration | Push-out strength (MPa) |
68 | positive | 1 min | 0.92 |
negative | 1 min | 1.21 | |
reference | 1 min | 0.78 | |
69 | positive | 1 min | 0.64 |
negative | 1 min | 0.72 | |
reference | 1 min | 0.57 | |
70 | positive | 1 min | 1.12 |
negative | 1 min | 1.02 | |
reference | 1 min | 0.95 | |
71 | positive | 5 min | 0.60 |
negative | 5 min | 0.61 | |
reference | 5 min | 0.54 | |
72 | positive | 5 min | 0.95 |
negative | 5 min | 0.84 | |
reference | 5 min | 0.92 | |
73 | positive | 5 min | 1.45 |
negative | 5 min | 1.18 | |
reference | 5 min | 1.36 | |
74 | positive | 10 min | 1.05 |
negative | 10 min | 0.85 | |
reference | 10 min | 0.89 | |
75 | positive | 10 min | 1.29 |
negative | 10 min | 0.77 | |
reference | 10 min | 1.31 | |
76 | positive | 10 min | 1.50 |
negative | 10 min | 1.16 | |
reference | 10 min | 1.30 | |
77 | positive | 60 min | 0.93 |
negative | 60 min | 1.11 | |
reference | 60 min | 1.10 | |
78 | positive | 60 min | 0.77 |
negative | 60 min | 0.28 | |
reference | 60 min | 0.78 | |
79 | positive | 60 min | 0.61 |
negative | 60 min | 0.64 | |
reference | 60 min | 0.91 | |
80 | positive | 24 h | 0.44 |
negative | 24 h | 0.67 | |
reference | 24 h | 0.52 | |
81 | positive | 24 h | 0.71 |
negative | 24 h | 1.15 | |
reference | 24 h | 0.98 | |
82 | positive | 24 h | 1.33 |
negative | 24 h | 1.50 | |
reference | 24 h | 1.56 |
Potential application duration (min) | S-/S+ | S-/S0 | S+/S0 |
1 | 1.32 | 1.55 | 1.18 |
1 | 1.13 | 1.26 | 1.12 |
1 | 0.91 | 1.07 | 1.18 |
5 | 1.02 | 1.13 | 1.11 |
5 | 0.88 | 0.91 | 1.03 |
5 | 0.81 | 0.87 | 1.07 |
10 | 0.81 | 0.96 | 1.18 |
10 | 0.60 | 0.59 | 0.98 |
10 | 0.77 | 0.89 | 1.15 |
60 | 1.19 | 1.01 | 0.85 |
60 | 0.36 | 0.36 | 0.99 |
60 | 1.05 | 0.70 | 0.67 |
1440 (24 h) | 1.52 | 1.29 | 0.85 |
1440 (24 h) | 1.62 | 1.17 | 0.72 |
1440 (24 h) | 1.13 | 0.96 | 0.85 |