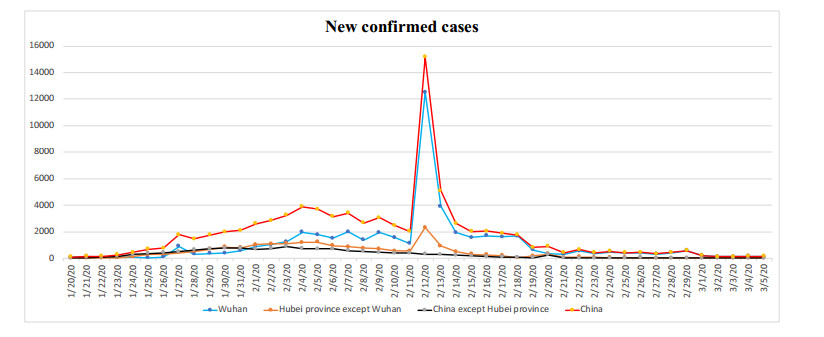
Citation: John Campbell. Crack populations in metals[J]. AIMS Materials Science, 2016, 3(4): 1436-1442. doi: 10.3934/matersci.2016.4.1436
[1] | Liping Wang, Jing Wang, Hongyong Zhao, Yangyang Shi, Kai Wang, Peng Wu, Lei Shi . Modelling and assessing the effects of medical resources on transmission of novel coronavirus (COVID-19) in Wuhan, China. Mathematical Biosciences and Engineering, 2020, 17(4): 2936-2949. doi: 10.3934/mbe.2020165 |
[2] | David Moreno-Martos, Sean Foley, Benjamin Parcell, Dumitru Trucu, Raluca Eftimie . A computational investigation of COVID-19 transmission inside hospital wards and associated costs. Mathematical Biosciences and Engineering, 2022, 19(7): 6504-6522. doi: 10.3934/mbe.2022306 |
[3] | Qian Shen . Research of mortality risk prediction based on hospital admission data for COVID-19 patients. Mathematical Biosciences and Engineering, 2023, 20(3): 5333-5351. doi: 10.3934/mbe.2023247 |
[4] | Zhihao Zhang, Ting Zeng, Yijia Wang, Yinxia Su, Xianghua Tian, Guoxiang Ma, Zemin Luan, Fengjun Li . Prediction Model of hospitalization time of COVID-19 patients based on Gradient Boosted Regression Trees. Mathematical Biosciences and Engineering, 2023, 20(6): 10444-10458. doi: 10.3934/mbe.2023459 |
[5] | Javad Hassannataj Joloudari, Faezeh Azizi, Issa Nodehi, Mohammad Ali Nematollahi, Fateme Kamrannejhad, Edris Hassannatajjeloudari, Roohallah Alizadehsani, Sheikh Mohammed Shariful Islam . Developing a Deep Neural Network model for COVID-19 diagnosis based on CT scan images. Mathematical Biosciences and Engineering, 2023, 20(9): 16236-16258. doi: 10.3934/mbe.2023725 |
[6] | Sarita Bugalia, Jai Prakash Tripathi, Hao Wang . Mathematical modeling of intervention and low medical resource availability with delays: Applications to COVID-19 outbreaks in Spain and Italy. Mathematical Biosciences and Engineering, 2021, 18(5): 5865-5920. doi: 10.3934/mbe.2021295 |
[7] | Sarafa A. Iyaniwura, Musa Rabiu, Jummy F. David, Jude D. Kong . Assessing the impact of adherence to Non-pharmaceutical interventions and indirect transmission on the dynamics of COVID-19: a mathematical modelling study. Mathematical Biosciences and Engineering, 2021, 18(6): 8905-8932. doi: 10.3934/mbe.2021439 |
[8] | Sarafa A. Iyaniwura, Rabiu Musa, Jude D. Kong . A generalized distributed delay model of COVID-19: An endemic model with immunity waning. Mathematical Biosciences and Engineering, 2023, 20(3): 5379-5412. doi: 10.3934/mbe.2023249 |
[9] | Xiangtao Chen, Yuting Bai, Peng Wang, Jiawei Luo . Data augmentation based semi-supervised method to improve COVID-19 CT classification. Mathematical Biosciences and Engineering, 2023, 20(4): 6838-6852. doi: 10.3934/mbe.2023294 |
[10] | Aili Wang, Xueying Zhang, Rong Yan, Duo Bai, Jingmin He . Evaluating the impact of multiple factors on the control of COVID-19 epidemic: A modelling analysis using India as a case study. Mathematical Biosciences and Engineering, 2023, 20(4): 6237-6272. doi: 10.3934/mbe.2023269 |
SARS-CoV-2, as a novel coronavirus, was first identified by the Chinese authorities in Wuhan, Hubei Province of China, which has caused the pneumonia (COVID-19) outbreak in China and other countries [1,2]. Until 05 March 2020, it has spread to all provinces of the mainland China and led to a total of 80552 confirmed cases with 3042 deaths [3]. The number of the confirmed cases is still increasing and the restriction of work causes a tremendous hit on Chinese society and economic.
Since December 2019, a series of pneumonia cases emerged in Wuhan, Chinese public health authorities have taken very rapidly responsive strategies including active case finding, closing Huanan Seafood Wholesale Market, improving public awareness of self-protection measures and so on [4]. Despite all of those, the number of infection cases has been continuously increasing. Due to the quick increase in confirmed cases of COVID-19, the Chinese government revised the law to add COVID-19 as class B agent on 20 January 2020, and then Public health officials classified the novel virus as class A agent [5]. In order to prevent further spread of COVID-19 nationally and globally, the government of Wuhan carried out a lockdown at 10:00 on 23 January 2020 [6]. Some interventions, including intensive contact tracing followed by quarantine of individuals, isolation of infected individuals and travel restrictions have been implemented, while the number of new confirmed cases increased in Wuhan and other cities continuously (see Figure 1).
COVID-19 is difficult to diagnose, and a delay between the onset of symptoms and accurate diagnosis is frequently observed. It is worth noting that, except reported confirmed cases of pneumonia, there are still many undiagnosed and delayed-diagnosis infections due to lacks of diagnostic reagents for the virus and the long waiting time for diagnosis [7,8]. Considering the person-to-person transmission [9,10], the undiagnosed infections have the ability and possibility to transmit the virus to other public susceptible people or family members during their searching for or waiting for a diagnosable hospital, and hence increase the risk of spatial transmission and potential infection of COVID-19. The most important aspects are the ability to diagnose and identify the infected in time, and the treatment of the confirmed patients.
The impact of delay in diagnosis on the infectious diseases such as foot-and-mouth disease, mycobacterium tuberculosis and African viral hemorrhagic fever has been extensively studied [11,12,13]. Those studies indicate that delay in diagnosis could increase both infections and economical loss. In particular, for Ebola, the rapid diagnostic tests and early detection of Ebola could allow early triaging of patients, thereby reduce the potential for nosocomial transmission and epidemic size [14,15,16]. In addition, the delay in diagnosis is closely associated with the substantially case fatality. Therefore, assessing the effect of delay in diagnosis is of crucial importance for the transmission and control of COVID-19.
Mathematical modeling studies on COVID-19 focused on the prediction of confirmed cases of the novel coronavirus pneumonia in Wuhan and other cities[17,19,20,21], the estimation of basic reproduction number (R0) based on the data of reported confirmed cases[17,18,22,23], the estimation of the unreported number of COVID-19 cases in China in the first stage of the outbreak [24], and also the potential risks of disease spreading [25,26]. Some authors [27,28] evaluated effects of the Wuhan travel restrictions or lock-down of the city in response to the novel coronavirus outbreak. However, the effect of delay in diagnosis on the dynamic evolution of COVID-19 has not been studied yet.
The principal purpose of this study is to present a dynamical model for transmission dynamics of COVID-19 and to evaluate the effect of delay in diagnosis on epidemic trend and characteristics of COVID-19. The main findings shed new insight on the disease interventions and control.
The data of confirmed COVID-19 cases in mainland China was collected from the National Health Commission of the People's Republic of China [5]. Data information includes the cumulative number of confirmed cases and the new number of confirmed cases, shown in Tables 1 and 2. The number of cumulative confirmed cases remained at 41 from 1 to 15 January 2020 according to the official report, i.e., no new case was reported during these 15 days, which appears inconsistent with the following rapid growth of the epidemic since 16 January 2020. The data set from 15 January to 02 February 2020 is used for model calibration, while the data set from 03 February to 05 March 2020 is applied for model validation.
Date(day/month) | 15 Jan | 16 Jan | 17 Jan | 18 Jan | 19 Jan | 20 Jan | 21 Jan |
Cumulative cases | 41 | 45 | 62 | 121 | 224 | 291 | 440 |
New cases | 0 | 4 | 17 | 59 | 78 | 77 | 149 |
Date(day/month) | 22 Jan | 23 Jan | 24 Jan | 25 Jan | 26 Jan | 27 Jan | 28 Jan |
Cumulative cases | 571 | 830 | 1287 | 1975 | 2744 | 4515 | 5974 |
New cases | 131 | 259 | 444 | 688 | 769 | 1771 | 1459 |
Date(day/month) | 29 Jan | 30 Jan | 31 Jan | 01 Feb | 02 Feb | ||
Cumulative cases | 7711 | 9692 | 11791 | 14380 | 17205 | ||
New cases | 1737 | 1982 | 2102 | 2590 | 2829 |
Date(day/month) | 03 Feb | 04 Feb | 05 Feb | 06 Feb | 07 Feb | 08 Feb | 09 Feb |
Cumulative cases | 20438 | 24324 | 28018 | 31161 | 34546 | 37198 | 40171 |
New cases | 3235 | 3887 | 3694 | 3143 | 3399 | 2656 | 3062 |
Date(day/month) | 10 Feb | 11 Feb | 12 Feb | 13 Feb | 14 Feb | 15 Feb | 16 Feb |
Cumulative cases | 42638 | 44653 | 59804 | 63851 | 66492 | 68501 | 70549 |
New cases | 2478 | 2015 | 15152 | 5090 | 2641 | 2009 | 2048 |
Date(day/month) | 17 Feb | 18 Feb | 19 Feb | 20 Feb | 21 Feb | 22 Feb | 23 Feb |
Cumulative cases | 72436 | 74185 | 74579 | 75456 | 76288 | 76936 | 77150 |
New cases | 1886 | 1749 | 820 | 889 | 397 | 648 | 409 |
Date(day/month) | 24 Feb | 25 Feb | 26 Feb | 27 Feb | 28 Feb | 29 Feb | 01 Mar |
Cumulative cases | 77658 | 78604 | 78497 | 78824 | 79251 | 79824 | 80026 |
New cases | 508 | 406 | 443 | 327 | 427 | 573 | 202 |
Date(day/month) | 02 Mar | 03 Mar | 04 Mar | 05 Mar | |||
Cumulative cases | 80151 | 80270 | 80409 | 80552 | |||
New cases | 125 | 119 | 139 | 143 |
According to the clinical progression of COVID-19 and epidemiological status of individuals, we establish a compartmental model of SEIR type, where delay in diagnosis is considered. Assume that the infected individuals are in two different situations, some are in resource-rich setting and can be diagnosed in time while others are in resource-poor setting and can not be timely diagnosed with a longer diagnostic waiting time. Everyone in the population is susceptible. All the infected individuals will be admitted into hospitals as soon as they are diagnosed.
The population is divided into susceptible (S), self-quarantine susceptible (Sq), exposed (E), infectious with timely diagnosis (I1), infectious with delayed diagnosis (I2), hospitalized (H) and recovered (R). V denotes the virus in the environment. A schematic description of the model is depicted in Figure 2.
The susceptible individuals can move to the compartment Sq at rate q by staying at home for quarantine. The self-quarantined individuals are released from quarantine and become susceptible again at rate q1. The susceptible individuals are infected via contact with exposed individuals, infectious individuals, and also virus. All the newly SARS-CoV-2-infected individuals are assumed to be asymptomatic but are capable of infecting the susceptible (move into E). The exposed individuals become infectious (symptomatic) after incubation period 1/ω. In reality, only a proportion ϕ of symptomatic patients could be diagnosed in time, while the rest may be delayed to be diagnosed due to limited hospital or diagnostic resources. Then the infectious with timely diagnosis I1 are decreased after 1/γ1 days as soon as they are diagnosed (move into H). The infectious with delayed diagnosis I2 are diagnosed and hospitalized after 1/γ2 days, where 1/γ1<1/γ2. The hospitalized individuals are decreased at recovery rate m. All infections (I1, I2, H) are decreased by diseased-induced death rate μ. The virus in the environment comes from both the exposed and the infectious at rate fi (i=1,2,3) and it is cleared at rate dv. The transfer diagram in Figure 2 leads to
{dSdt=−(βeE+βi1I1+βi2I2+βvV)S−qS+q1Sq,dSqdt=qS−q1Sq,dEdt=(βeE+βi1I1+βi2I2+βvV)S−ωE,dI1dt=ϕωE−γ1I1−μI1,dI2dt=(1−ϕ)ωE−γ2I2−μI2,dHdt=γ1I1+γ2I2−mH−μH,dRdt=mH,dVdt=f1E+f2I1+f3I2−dvV, | (2.1) |
where βe, βi1, βi2, and βv denote the transmission rates from the exposed, infectious with or without timely diagnosis, and virus in the environment to the susceptible, respectively. fi, i=1,2,3 is the virus released rate via the exposed and the infectious. Here all parameters are assumed to be positive and their biological significance, default values, and reference resources are summarized in Table 3.
Parameter | Description | Value (Range) | Unit | Source |
q | Self-quarantined rate of the susceptible | 1/10 | day−1 | Estimated |
q1 | Transition rate of self-quarantined individuals to the susceptible | 1/200000 | day−1 | Estimated |
βe | Transmission rate from the exposed to the susceptible | 3.511×10−8 (10−8,10−7) | day−1 | Estimated |
βi1 | Transmission rate from the infectious with timely diagnosis to the susceptible | 3.112×10−8 (0.91∗10−8,10−7) | day−1 | Estimated |
βi2 | Transmission rate from the infectious with delayed diagnosis to the susceptible | 1.098×10−7 (1.1∗10−8,3∗10−7) | day−1 | Estimated |
βv | Transmission rate from the susceptible to the exposed (infected by virus) | 1.009×10−10 (10−11,9∗10−10) | day−1 | Estimated |
1/ω | Incubation period | 5.2 | day | [10] |
ϕ | Proportion of the infectious with timely diagnosis | 0.4(0.3,0.65) | – | Estimated |
1/γ1 | Waiting time of the infectious for timely diagnosis | 2.9(1,5) | day | [29] |
1/γ2 | Waiting time of the infectious for delayed diagnosis | 10 (5,20) | day | Estimated |
μ | Disease-induced death rate | 1.7826×10−5 | day−1 | [17] |
m | Recovery rate of the hospitalized | 1/14 | day−1 | [9] |
f1 | Virus released rate of the exposed | 1440 (864,2160) | day−1 | Estimated |
f2 | Virus released rate of the infectious with timely-diagnosis | 1008 (432,1440) | day−1 | Estimated |
f3 | Virus released rate of the infectious with delayed-diagnosis | 1728 (864,2592) | day−1 | Estimated |
dv | Clear rate of virus in the environment | 144 (115.2,172.8) | day−1 | Estimated |
S(0) | Initial value of the susceptible | 11081000 | – | [30] |
Sq(0) | Initial value of the self-quarantined susceptible | 159 | – | Estimated |
E(0) | Initial value of the exposed | 399 | – | [5] |
I1(0) | Initial value of the infectious with timely diagnosis | 28 | – | Estimated |
I2(0) | Initial value of the infectious with delayed diagnosis | 54 | – | Estimated |
H(0) | Initial value of the hospitalized | 41 | – | [5] |
R(0) | Initial value of the recovered | 12 | – | [5] |
V(0) | Initial value of virus in the environment | 21080 | – | Estimated |
We use the least-square method to carry out the parameter estimation, which is implemented by the command fmincon, a part of the optimization toolbox in MATLAB. The least-square estimation is to find the parameter values to minimize the following objective function
f(Θ,n)=n∑j=1(I(t)−ˆI(t))2, |
where Θ is a parameter vector to be estimated, n is the number of reported data, ˆI(t) is the actual reported confirmed cases, and I(t) is the theoretical confirmed at day t. The dynamics of I(t) is governed by
dI(t)dt=γ1I1+γ2I2, |
where I1 and I2 are determined by model (2.1).
From the data of confirmed cases in mainland China and in Wuhan, we set 15 January 2020 as the initial time. Since the COVID-19 infectious cases before 15 January 2020 were all in Wuhan, we set the population size of Wuhan as the initial value of the susceptible, i.e., S(0)=11081000. On 15 January, 41 cases were confirmed and hospitalized, then H(0)=41; 12 cases were recovered, hence R(0)=12. We set E(0)=399 because the suspected cases on 15 January 2020 is 399. The incubation period of COVID-19 is estimated to be 5.2 [10], hence ω=1/5.2. The average waiting time of the infectious with timely diagnosis is 2.9 day [29], thus γ1=1/2.9. It is reported that the infectious individuals can recover within two weeks [30], thus the recovery rate m is 1/14.
We use the method in §2.3 to estimate parameter values by fitting model with the data of confirmed cases of COVID-19 (see Table 1). The fitting results of model (2.1) with the confirmed cases are given in Figure 3 and the estimated parameter values are listed in Table 3.
With the increase of the medical supply and reasonable allocation of medical resources, the resources-dependent parameters ϕ, γ1 and γ2 increase with respect to time t and the correlation of those parameters with t are estimated as ϕ=0.4+0.6t/(t+3), 1/γ1=2.9−0.9t/(t+5) and 1/γ2=10−7t/(t+5). From Table 3, it is observed that, among the transmission rates (βi1, βi2, βe, βv), the transmission rate βi2 of the infectious with delayed diagnosis is the biggest. It indicates that the infectious with delayed diagnosis plays a critical role in the spread of COVID-19. Although the transmission rate βv is much smaller than the other threes, it may ignite the spread of COVID-19. Even if there are no exposed or infectious individuals, the susceptible could be infected by accidental contacts with virus in environment.
Moreover, Figure 3 shows the fitting results of model (2.1) with the reported data of confirmed cases. It is seen that our model prediction shows a similar trend to the reported data of both the new confirmed cases and cumulative confirmed cases. In particular, if the efficiency of diagnosis keeps increasing as ϕ=0.4+0.6t/(t+3), 1/γ1=2.9−0.9t/(t+5) and 1/γ2=10−7t/(t+5), the predicted values of cumulative confirmed cases will increase further and provide very good fit with the reported data of cumulative confirmed cases. From Figure 3(a), it is observed that, from 06 to 13 February, the prediction of model (2.1) somewhat deviates from the reported data of new confirmed cases. The possible reason is that the diagnosed-efficiency parameters ϕ, γ1 and γ2 in the model keep increasing with time t continuously, while in the real-world application, the medical supply and medical resources increased intermittently. The intermittent increase of medical resources makes the actual diagnosis efficiency being different from the model estimation. In addition, from 12 February, the clinically diagnosed cases were statistically seen as the new confirmed cases in Hubei province, and the inclusion of those cases drives the surge in the number of new confirmed on 12 and 13 February. Model (2.1) makes a good prediction of the new confirmed cases from 14 February to 05 March 2020.
The basic reproductive number R0 is a measure of the potential for an infectious disease to spread through an immunologically naive population. It is defined as the average number of secondary cases generated by a single infectious case in a completely susceptible population. Based on (2.1), by the next generation matrix method [31], the basic reproduction number reads
R0=S0[βeω+βi1ϕγ1+μ+βi2(1−ϕ)γ2+μ+βv(f1(γ1+μ)(γ2+μ)+f2ϕω(γ2+μ)+f3(1−ϕ)ω(γ1+μ))dv(γ1+μ)(γ2+μ)ω], | (3.1) |
where S0 is the initial value of the susceptible.
The basic reproduction number R0 is a significant indicator in both transmission risks and control of an infectious disease. In order to provide a comprehensive understanding of the influence of different input parameters and their variations on the model outcomes, and to characterize the most important parameters, the sensitivity analysis is conducted by obtaining the partial rank correlation coefficients (PRCCs) [32] for various parameters against R0.
The parameters considered in the sensitive analysis include transmission rates (βe, βi1, βi2, βv), factors related to the diagnosis efforts (γ1, γ2, ϕ), virus released rates (f1, f2, f3) and clear rate of virus (dv). Figure 4 (a) illustrates the PRCCs of R0 with respect to model parameters. It suggests that R0 is more sensitive to βe, βi2, βi1 and βv in order among the transmission rates. That is to say, the exposed and the infectious with delayed diagnosis contribute more to the transmission and spread of COVID-19, compared with the infectious with timely diagnosis and virus. In addition, the PRCCs values of γ1, γ2, and ϕ are also big. From Figure 4(b), the increase of ϕ and γ2 can significantly reduce the value of R0, which verifies that delay in diagnosis plays a critical role in the transmission of COVID-19. Therefore, the richness and distribution of medical resources and the early timely diagnosis are also very important for the prevention and control of COVID-19.
In order to further explore the possible impact of enhanced diagnosis efficiency and resources richness on the disease transmission, we plot the predicted new confirmed cases (γ1I1(t)+γ2I2(t)) and new infections (I1(t)+I2(t)) with respect to the proportion of the infectious with timely diagnosis ϕ and delayed diagnosed rate γ2.
In reality, resources such as abundant diagnostic test kits, diagnosable hospitals, and available beds have been supplied to support the diagnosis and treatment of COVID-19 since 02 February, the proportion ϕ of the infectious with timely diagnosis is gradually improved as time goes on due to the increasing supply of diagnostic resources. We set ϕ=ϕ0+(1−ϕ0)t/(t+a), where ϕ0 (its estimated value is 0.4 listed in Table 3) is the basic proportion and a represents the time when the proportion improves to (1+ϕ0)/2.
Figure 5 depicts the effect of the proportion ϕ of the infectious with timely diagnosis on the number of confirmed cases. With the increasing of ϕ, the number of new confirmed cases increases first and then decreases, while the number of cumulative confirmed cases always decreases; the peak value of the new confirmed cases decreases and the peak time of the new confirmed cases arrives much earlier. Specifically, compared with the baseline scenario with ϕ=0.4, when ϕ is increased to 0.7 in one week (ϕ=0.4+0.6t/(t+7)), three days (ϕ=0.4+0.6t/(t+3)), or one day (ϕ=0.4+0.6t/(t+1)), then the peak time of new confirmed cases arrives 5 days, 7 days, or 8.5 days earlier, the peak value of new confirmed cases decreases by 33.4%, 37.8%, or 42.5%, and the number of cumulative confirmed cases decreases by 14.7%, 21.3%, or 28.2% on 05 March 2020, respectively. Similarly, the increasing of ϕ leads to the decrease of both new infections (include confirmed cases and potential infections) and cumulative infections (see Figure 6). In particular, compared with the basic scenario with ϕ=0.4, the number of new infection and cumulative infection with ϕ=0.4+0.6t/(t+1) decreases by 88.8% and 51.6% on 05 March 2020, respectively. In summary, increasing ϕ can significantly shorten the peak time and reduce the peak value of new confirmed cases and new infections, then reduce the cumulative number of confirmed cases and total infections (Figures 5 and 6).
In resource-poor setting, the infectious individuals have to wait for longer time for diagnosis due to limited amount of diagnostic equipments and low diagnostic efficiency of the test kits etc. The waiting time for delayed diagnosis is critical for disease transmission and control. Note that the estimated value of delayed diagnosis rate γ2 is 1/10, we consider 1/γ2=10 (days) as the baseline scenario. Next, we investigate the effect of the waiting time for delayed diagnosis on the new and cumulative infection. In Figure 7, compared with the baseline scenario, when the waiting time for delayed diagnosis is extended by 3 days (i.e., 1/γ2=13) since 02 February, the number of new infected individuals on 05 March 2020 increases by 52.1%, while if the waiting time for delayed diagnosis is shorten by 3 days (1/γ2=7) or by 7 days (1/γ2=3), the number of new infections reduces by 51.0% or 78.2% on 05 March 2020, respectively. Moreover, the number of cumulative infections on 05 March 2020 will decrease drastically (by 66.7%) if all the infectious can be diagnosed within three days of onset (1/γ2=3 and 1/γ1=2.9). In summary, increasing γ2 shortens the peak time, decreases the peak value of new infections, and reduces the number of cumulative infections.
In this study, based on the reported data of COVID-19 in mainland China, a compartmental dynamic model of SEIR type is formulated to investigate the effect of delay in diagnosis on the transmission and spread of COVID-19. Sensitive analysis evaluates the PRCCs for various parameters against R0, which together with the contour plot, reveals that the proportion ϕ of the infectious with timely diagnosis and the delayed diagnosis rate γ2 are of considerable importance for the control of COVID-19. Numerical simulations prove that increasing ϕ (i.e., improve the richness of diagnostic resources) and γ2 (i.e., improve the diagnosis efficiency) can shorten the peak time, reduce the peak value of new confirmed cases and new infection, the cumulative number of confirmed cases and total infection, and hence can significantly reduce the transmission risk and further infections of COVID-19. Therefore, the resources supply and diagnosis efficiency are essential for an early diagnosis and timely and definitive treatment.
Note that, with the increasing of ϕ, the number of new confirmed cases increases first and then decreases, as shown in Figure 5(a). This finding is consistent with the scenario in Wuhan and Hubei province (Figure 1). During the early stage of COVID-19 in Wuhan and Hubei province, the insufficiency and unbalanced distribution of diagnostic resources (e.g., lack of diagnosable hospital, available beds, diagnostic test kits, diagnostic equipments and low diagnostic efficiency of the test kits etc) caused a delay in the diagnosis and an increased mortality. So that COVID-19 incidence and prevalence are increasing very quickly.
As a matter of fact, extraordinary efforts have been made by national and provincial governments of China, especially in Hubei province and Wuhan. 'Compartment hospitals' have been built to treat mild cases, and nationwide support such as plenty of healthcare staff and treatment equipments has been employed to treat more infections in Wuhan since 02 February 2020. As of 03 February, the novel coronavirus nucleic acid testing capability of Wuhan have increased to 4196 samples per day from an initial 200 samples. On 08 February 2020, the National Health Commission of the People's Republic of China issued the fifth edition of the Diagnosis and Treatment Plan for the Coronavirus, which adds CT and clinical standards to provide evidence for diagnosis and treatment. So that the COVID-19 patients can receive timely diagnosis and early standardized treatment as soon as possible and the diagnosis efficiency is quickly improved. The timely diagnosis and treatment of patients are greatly speeded up in Wuhan. As of 13 February, a total of ten 'compartment hospitals' with 6960 beds have been available and about 5600 patients have been admitted. As a result, the number of new confirmed cases in Wuhan increased sharply on 12 February and then showed a decline since February 13 (Figure 1), the evolution trend is consistent with the fitting result in Figure 3 (a).
A precise and early diagnosis/treatment is highly important in COVID-19. As mentioned above, it is effective to reduce the transmission risk by reducing the waiting time and increasing the proportion of infections with timely diagnosis, and hence can facilitate the prevention and control of COVID-19. However, only the early diagnosis and effective treatment can not eliminate COVID-19. Figure 8(a) depicts that the new confirmed cases remain at some positive level even if all the infective individuals can be timely diagnosed as soon as possible. Figure 8(b) shows that, the basic reproduction number R0 sharply decreases with the increasing of ϕ and γ2, but R0 can not decrease to the level less than 1, R0 is still 3.1021>1 and the new infection on 05 March 2020 is 102 even when ϕ=1, γ1=γ2=1. From the web-news [33,34], Italy will adjust its policy that to do less samples so that they will not report so many cases to avoid public panic, Japanese Government said they will only focus on the treatment of serious patients, and they will limit the tests only for the samples that would meet the 'criteria'. Our findings warn that such ideas are very dangerous.
The prevention, control, diagnosis, and treatment are among the most crucial issues in COVID-19, they are highly integrated and can never be separated. The timely diagnosis and effective treatment can destock the capacity of the infected individuals and reduce nosocomial infection while the prevention and control can suppress the increment of new infection and hence reduce the burden in the hospitals. The principles for the prevention and control of infectious disease are to control the source of infection, to cut off the routes of transmission, and to protect susceptible individuals. A combining multiple measures must be simultaneously implemented. The most key and useful strategy and measures for the control of COVID-19 in China are to detect cases early, isolate every patients, trace every contacts, provide quality clinical care, prevent hospital outbreaks, prevent community transmission, avoid public panic and rumor, progress vaccines and therapeutics. In this light, it is important to thoroughly understand transmission dynamics and implement effective prevention and control programs as well as early diagnosis and timely treatment. It is crucial and important to establish a joint strategy involving prevention, control, and medical treatment. The strategy should be systematic, scientific, normative, and works perfectly.
This research was supported by National Natural Science Foundation of P. R. China (Nos. 11671072, 11271065).
The authors declare no conflict of interest.
[1] |
Campbell J (2015) The consolidation of metals: the origin of bifilms. J Mater Sci 51: 96–106. doi: 10.1007/s11003-015-9814-z
![]() |
[2] | Campbell J (2011) The origin of Griffith cracks. Metall Mater Trans B 42B: 1091–1097. |
[3] | Griffith AA (1920) The phenomenon of rupture and flow in solids. Phil Trans Roy Soc A 221: 163–198. |
[4] | Barenblatt GI (1959) The formation of equilibrium cracks during brittle fracture. PMM 23: 434–444. |
[5] |
Willis JR (1967) A comparison of the fracture criteria of Griffith and Barenblatt. J Mech Phys Solids 15: 151–162. doi: 10.1016/0022-5096(67)90029-4
![]() |
[6] | Campbell J (2015) Complete Casting Handbook 2nd Edition, Elsevier, Oxford, UK. |
[7] | Raiszadeh R, Griffiths WD (2008) Duration of the atmosphere in a bifilm. Metall Mater Trans B 39B: 298–303. |
[8] | Boivert M, Christoperson D, L’Esperance G (2016) Observation of nanometric silicon oxide bifilms in a water-atomized hypereutectic cast iron powder. Metall Mater Trans B 47B: 2971–2978. |
[9] |
Wang KG, Glicksman ME (2015) Phase coarsening in thin films. JOM 67: 1905–1912. doi: 10.1007/s11837-015-1338-3
![]() |
[10] | Xu J, Huang F, Wang X (2016) Formation mechanism of CaS-Al2O3 inclusions in low sulfur Al-killed steel after calcium treatment. Metall Matem Trans B 47B: 1217–1227. |
[11] |
Campbell J (2016) Melting, remelting and casting for clean steel. Steel Res Int 87: 1–13. doi: 10.1002/srin.201670011
![]() |
[12] | Frost S (2015) Nuclear flaws raise safety questions in two Belgian reactors. Mater World (The Institute of Materials, Minerals and Mining, London, UK) 23: 16. |
[13] | Campbell J (2012) Stop pouring, start casting. Int J Metalcast 6: 7–18. |
[14] | Campbell J (2015) Quality Castings—A personal account of the development of the cosworth casting process. American Foundry Soc., Schaumburg, IL, USA. Originally published 2013 by Aspect Design, Malvern, UK. |
1. | Keng-Wei Lee, Tsair-Wei Chien, Yu-Tsen Yeh, Willy Chou, Hsien-Yi Wang, An online time-to-event dashboard comparing the effective control of COVID-19 among continents using the inflection point on an ogive curve, 2021, 100, 0025-7974, e24749, 10.1097/MD.0000000000024749 | |
2. | Aziz Eftekhari, Mahdieh Alipour, Leila Chodari, Solmaz Maleki Dizaj, Mohammadreza Ardalan, Mohammad Samiei, Simin Sharifi, Sepideh Zununi Vahed, Irada Huseynova, Rovshan Khalilov, Elham Ahmadian, Magali Cucchiarini, A Comprehensive Review of Detection Methods for SARS-CoV-2, 2021, 9, 2076-2607, 232, 10.3390/microorganisms9020232 | |
3. | Jianping Geng, Jun Yu, Tao Lu, Yinhe Wang, Yang Cao, A Silent Infection Pandemic of COVID-19: Epidemiological Investigation and Hypothetical Models, 2020, 2020, 1712-9532, 1, 10.1155/2020/5120253 | |
4. | Wei-Tsong Wang, Su-Ying Wu, Knowledge management based on information technology in response to COVID-19 crisis, 2020, 1477-8238, 1, 10.1080/14778238.2020.1860665 | |
5. | Prasantha Bharathi Dhandapani, Dumitru Baleanu, Jayakumar Thippan, Vinoth Sivakumar, On stiff, fuzzy IRD-14 day average transmission model of COVID-19 pandemic disease, 2020, 7, 2375-1495, 208, 10.3934/bioeng.2020018 | |
6. | Ali Moussaoui, Pierre Auger, E. Augeraud, M. Banerjee, J.-S. Dhersin, A. d'Onofrio, T. Lipniacki, S. Petrovskii, Chi Tran, A. Veber-Delattre, E. Vergu, V. Volpert, Prediction of confinement effects on the number of Covid-19 outbreak in Algeria, 2020, 15, 0973-5348, 37, 10.1051/mmnp/2020028 | |
7. | Joshua Asamoah, Zhen Jin, Baba Seidu, F.T. Odoro, Gui-Quan Sun, Faris Alzahrani, Mathematical Modelling and Sensitivity Assessment of COVID-19 Outbreak for Ghana and Egypt, 2020, 1556-5068, 10.2139/ssrn.3612877 | |
8. | Michael J. Loeffelholz, David Alland, Susan M. Butler-Wu, Utsav Pandey, Carlo Frederico Perno, Alice Nava, Karen C. Carroll, Heba Mostafa, Emma Davies, Ashley McEwan, Jennifer L. Rakeman, Randal C. Fowler, Jean-Michel Pawlotsky, Slim Fourati, Sukalyani Banik, Padmapriya P. Banada, Shobha Swaminathan, Soumitesh Chakravorty, Robert W. Kwiatkowski, Victor C. Chu, JoAnn Kop, Rajiv Gaur, Mandy L. Y. Sin, Duy Nguyen, Simranjit Singh, Na Zhang, David H. Persing, Alexander J. McAdam, Multicenter Evaluation of the Cepheid Xpert Xpress SARS-CoV-2 Test, 2020, 58, 0095-1137, 10.1128/JCM.00926-20 | |
9. | Isaac Owusu-Mensah, Lanre Akinyemi, Bismark Oduro, Olaniyi S. Iyiola, A fractional order approach to modeling and simulations of the novel COVID-19, 2020, 2020, 1687-1847, 10.1186/s13662-020-03141-7 | |
10. | Sanjeet Singh, Jayaram R., A Review of Potential Antiviral Drugs and Vaccines to Treat COVID-19, 2020, 14, 2581690X, 765, 10.22207/JPAM.14.SPL1.14 | |
11. | Joshua Kiddy K. Asamoah, Zhen Jin, Gui-Quan Sun, Baba Seidu, Ernest Yankson, Afeez Abidemi, F.T. Oduro, Faris Alzahrani, Stephen E. Moore, Eric Okyere, Sensitivity assessment and optimal economic evaluation of a new COVID-19 compartmental epidemic model with control interventions, 2021, 09600779, 110885, 10.1016/j.chaos.2021.110885 | |
12. | Jianzhe Huang, Guoyuan Qi, Effects of control measures on the dynamics of COVID-19 and double-peak behavior in Spain, 2020, 101, 0924-090X, 1889, 10.1007/s11071-020-05901-2 | |
13. | Madeshwari Ezhilan, Indhu Suresh, Noel Nesakumar, SARS-CoV, MERS-CoV and SARS-CoV-2: A Diagnostic Challenge, 2021, 168, 02632241, 108335, 10.1016/j.measurement.2020.108335 | |
14. | Laio Magno, Thais Aranha Rossi, Fernanda Washington de Mendonça-Lima, Carina Carvalho dos Santos, Guilherme Barreto Campos, Lucas Miranda Marques, Marcos Pereira, Nilia Maria de Brito Lima Prado, Inês Dourado, Desafios e propostas para ampliação da testagem e diagnóstico para COVID-19 no Brasil, 2020, 25, 1678-4561, 3355, 10.1590/1413-81232020259.17812020 | |
15. | Daniele Lilleri, Federica Zavaglio, Elisa Gabanti, Giuseppe Gerna, Eloisa Arbustini, Patrick Tang, Analysis of the SARS-CoV-2 epidemic in Italy: The role of local and interventional factors in the control of the epidemic, 2020, 15, 1932-6203, e0242305, 10.1371/journal.pone.0242305 | |
16. | Hend Alrasheed, Alhanoof Althnian, Heba Kurdi, Heila Al-Mgren, Sulaiman Alharbi, COVID-19 Spread in Saudi Arabia: Modeling, Simulation and Analysis, 2020, 17, 1660-4601, 7744, 10.3390/ijerph17217744 | |
17. | Lin-Yen Wang, Tsair-Wei Chien, Willy Chou, Using the IPcase Index with Inflection Points and the Corresponding Case Numbers to Identify the Impact Hit by COVID-19 in China: An Observation Study, 2021, 18, 1660-4601, 1994, 10.3390/ijerph18041994 | |
18. | Kyent-Yon Yie, Tsair-Wei Chien, Yu-Tsen Yeh, Willy Chou, Shih-Bin Su, Using Social Network Analysis to Identify Spatiotemporal Spread Patterns of COVID-19 around the World: Online Dashboard Development, 2021, 18, 1660-4601, 2461, 10.3390/ijerph18052461 | |
19. | Sijia Liu, Ni Yao, Yanru Qiu, Chengqi He, Predictive performance of SOFA and qSOFA for in-hospital mortality in severe novel coronavirus disease, 2020, 38, 07356757, 2074, 10.1016/j.ajem.2020.07.019 | |
20. | Giovanni Sotgiu, Claudia C. Dobler, Social stigma in the time of coronavirus disease 2019, 2020, 56, 0903-1936, 2002461, 10.1183/13993003.02461-2020 | |
21. | Ali Traoré, Fourtoua Victorien Konané, Modeling the effects of contact tracing on COVID-19 transmission, 2020, 2020, 1687-1847, 10.1186/s13662-020-02972-8 | |
22. | Afeez Abidemi, Zaitul Marlizawati Zainuddin, Nur Arina Bazilah Aziz, Impact of control interventions on COVID-19 population dynamics in Malaysia: a mathematical study, 2021, 136, 2190-5444, 10.1140/epjp/s13360-021-01205-5 | |
23. | K. N. Schneider, C. L. Correa-Martínez, G. Gosheger, C. Rickert, D. Schorn, A. Mellmann, V. Schwierzeck, S. Kampmeier, Assessing the spreading potential of an undetected case of COVID-19 in orthopaedic surgery, 2020, 0936-8051, 10.1007/s00402-020-03516-1 | |
24. | Feng Zhou, Chong You, Xiaoyu Zhang, Kaihuan Qian, Yan Hou, Yanhui Gao, Xiao-Hua Zhou, Epidemiological Characteristics and Factors Associated with Critical Time Intervals of COVID-19 in Eighteen Provinces, China: A Retrospective Study, 2021, 102, 12019712, 123, 10.1016/j.ijid.2020.09.1487 | |
25. | Yushan Wu, Xiang Yan, Shi Zhao, Jingxuan Wang, Jinjun Ran, Dong Dong, Maggie Wang, Hong Fung, Eng-kiong Yeoh, Roger Yat-Nork Chung, Association of time to diagnosis with socioeconomic position and geographical accessibility to healthcare among symptomatic COVID-19 patients: A retrospective study in Hong Kong, 2020, 66, 13538292, 102465, 10.1016/j.healthplace.2020.102465 | |
26. | Xinchen Yu, Guoyuan Qi, Jianbing Hu, Analysis of second outbreak of COVID-19 after relaxation of control measures in India, 2020, 0924-090X, 10.1007/s11071-020-05989-6 | |
27. | P.H.T. Schimit, A model based on cellular automata to estimate the social isolation impact on COVID-19 spreading in Brazil, 2021, 200, 01692607, 105832, 10.1016/j.cmpb.2020.105832 | |
28. | Christopher R. Carpenter, Philip A. Mudd, Colin P. West, Erin Wilber, Scott T. Wilber, Shahriar Zehtabchi, Diagnosing COVID‐19 in the Emergency Department: A Scoping Review of Clinical Examinations, Laboratory Tests, Imaging Accuracy, and Biases, 2020, 27, 1069-6563, 653, 10.1111/acem.14048 | |
29. | Yong Li, Lian-Wen Wang, Zhi-Hang Peng, Hong-Bing Shen, Basic reproduction number and predicted trends of coronavirus disease 2019 epidemic in the mainland of China, 2020, 9, 2049-9957, 10.1186/s40249-020-00704-4 | |
30. | Nour K. Younis, Rana O. Zareef, Mohammad Ali N. Maktabi, Rami Mahfouz, The Era of the Coronavirus Disease 2019 Pandemic: A Review on Dynamics, Clinical Symptoms and Complications, Diagnosis, and Treatment, 2021, 25, 1945-0265, 85, 10.1089/gtmb.2020.0227 | |
31. | Heungsup Sung, Myung-Guk Han, Cheon-Kwon Yoo, Sang-Won Lee, Yoon-Seok Chung, Jae-Sun Park, Mi-Na Kim, Hyukmin Lee, Ki Ho Hong, Moon-Woo Seong, Kyunghoon Lee, Sail Chun, Wee Gyo Lee, Gye-Cheol Kwon, Won-Ki Min, Nationwide External Quality Assessment of SARS-CoV-2 Molecular Testing, South Korea, 2020, 26, 1080-6040, 2353, 10.3201/eid2610.202551 | |
32. | Olumuyiwa James Peter, Sania Qureshi, Abdullahi Yusuf, Mohammed Al-Shomrani, Abioye Abioye Idowu, A new mathematical model of COVID-19 using real data from Pakistan, 2021, 24, 22113797, 104098, 10.1016/j.rinp.2021.104098 | |
33. | Nicola Serra, Paola Di Carlo, Teresa Rea, Consolato M. Sergi, Diffusion modeling of COVID-19 under lockdown, 2021, 33, 1070-6631, 041903, 10.1063/5.0044061 | |
34. | Anna-Leena Lohiniva, Timothee Dub, Lotta Hagberg, Hanna Nohynek, Jennifer Yourkavitch, Learning about COVID-19-related stigma, quarantine and isolation experiences in Finland, 2021, 16, 1932-6203, e0247962, 10.1371/journal.pone.0247962 | |
35. | Ketki Jawade, Akhauri Yash Sinha, Sharad Bhagat, Shilpa Bhowmick, Bhagyashree Chauhan, Snehal Kaginkar, Harsha Palav, Nandini Kasarpalkar, Pratik Devadiga, Kalyani Karandikar, Sachee Agarwal, Jayanthi Shastri, Kiran Munne, Vikrant M. Bhor, Smita D. Mahale, Subhanjan Bhowmik, Dhanashree Jagtap, Vainav Patel, A novel ORF-1a based SARS-CoV-2 RT-PCR assay to resolve inconclusive samples, 2021, 12019712, 10.1016/j.ijid.2021.04.006 | |
36. | Matthew O. Adewole, Akindele A. Onifade, Farah A. Abdullah, Funmilayo Kasali, Ahmad I. M. Ismail, Modeling the Dynamics of COVID-19 in Nigeria, 2021, 7, 2349-5103, 10.1007/s40819-021-01014-5 | |
37. | Ayfer Ozturk, Stigmatization spreads faster than the virus. Viruses do not discriminate, and neither should we.” Combatting the stigmatization surrounding coronavirus disease (COVID‐19) pandemic, 2021, 0031-5990, 10.1111/ppc.12815 | |
38. | Jonghoo Lee, Jae‐Uk Song, Diagnostic accuracy of the Cepheid Xpert Xpress and the Abbott ID NOW assay for rapid detection of SARS‐CoV‐2: A systematic review and meta‐analysis, 2021, 0146-6615, 10.1002/jmv.26994 | |
39. | S.O. Akindeinde, Eric Okyere, A.O. Adewumi, R.S. Lebelo, Olanrewaju. O. Fabelurin, Stephen. E. Moore, Caputo Fractional-order SEIRP model for COVID-19 epidemic, 2021, 11100168, 10.1016/j.aej.2021.04.097 | |
40. | Tsz-Lik Chan, Hsiang-Yu Yuan, Wing-Cheong Lo, Modeling COVID-19 Transmission Dynamics With Self-Learning Population Behavioral Change, 2021, 9, 2296-2565, 10.3389/fpubh.2021.768852 | |
41. | Florina Silvia Iliescu, Ana Maria Ionescu, Larisa Gogianu, Monica Simion, Violeta Dediu, Mariana Carmen Chifiriuc, Gratiela Gradisteanu Pircalabioru, Ciprian Iliescu, Point-of-Care Testing—The Key in the Battle against SARS-CoV-2 Pandemic, 2021, 12, 2072-666X, 1464, 10.3390/mi12121464 | |
42. | H. Rwezaura, S.Y. Tchoumi, J.M. Tchuenche, Impact of environmental transmission and contact rates on Covid-19 dynamics: A simulation study, 2021, 27, 23529148, 100807, 10.1016/j.imu.2021.100807 | |
43. | Sina Ahmadi, Seyed Fahim Irandoost, Ahmad Ahmadi, Javad Yoosefi Lebni, Mohammad Ali Mohammadi Gharehghani, Nafe Baba Safari, Explaining Experiences, Challenges and Adaptation Strategies in COVID-19 Patients: A Qualitative Study in Iran, 2022, 9, 2296-2565, 10.3389/fpubh.2021.778026 | |
44. | Neera Marathe, Aashutosh Asati, Alok Pratap Singh, Manoj Indurkar, Saritesh Kuma Thakur, Epidemiological Factors and Clinical Course of COVID-19 in Patients Who Died Following the Disease in Dedicated COVID Hospital, Rewa District, Madhya Pradesh - A Retrospective Study, 2021, 8, 23492562, 1739, 10.18410/jebmh/2021/329 | |
45. | Abdulla All Noman, Mustafizur Rahaman, Tahmid Hasan Pranto, Rashedur M. Rahman, Blockchain for medical collaboration: A federated learning-based approach for multi-class respiratory disease classification, 2023, 3, 27724425, 100135, 10.1016/j.health.2023.100135 | |
46. | Xinyu Liu, Yuting Ding, Stability and Numerical Simulations of a New SVIR Model with Two Delays on COVID-19 Booster Vaccination, 2022, 10, 2227-7390, 1772, 10.3390/math10101772 | |
47. | Jianbing Hu, Guoyuan Qi, Xinchen Yu, Lin Xu, Modeling and staged assessments of the controllability of spread for repeated outbreaks of COVID-19, 2021, 106, 0924-090X, 1411, 10.1007/s11071-021-06568-z | |
48. | Getachew Beyecha Batu, Eshetu Dadi Gurmu, Mathematical Model of the Transmission Dynamics of Novel Corona Virus (COVID-19) Pandamic Disease with Optimal Control, 2021, 15, 1998-0140, 195, 10.46300/9101.2021.15.27 | |
49. | Gianni Gori Savellini, Gabriele Anichini, Chiara Terrosi, Shibily Prathyumnan, Claudia Gandolfo, Stefano Marini, Maria Grazia Cusi, Kileen L. Shier, Comparative Performance of a New SARS-CoV-2 Rapid Detection System, 2021, 9, 2165-0497, 10.1128/Spectrum.00205-21 | |
50. | Kang-Ting Tsai, Tsair-Wei Chien, Ju-Kuo Lin, Yu-Tsen Yeh, Willy Chou, Comparison of prediction accuracies between mathematical models to make projections of confirmed cases during the COVID-19 pandamic by country/region, 2021, 100, 0025-7974, e28134, 10.1097/MD.0000000000028134 | |
51. | Sacrifice Nana-Kyere, Francis Agyei Boateng, Paddy Jonathan, Anthony Donkor, Glory Kofi Hoggar, Banon Desmond Titus, Daniel Kwarteng, Isaac Kwasi Adu, Andrei Korobeinikov, Global Analysis and Optimal Control Model of COVID-19, 2022, 2022, 1748-6718, 1, 10.1155/2022/9491847 | |
52. | Chunxia Cao, Yue Li, Shaobo Fu, Yongzhong Zhang, Ning Li, Shike Hou, Haojun Fan, Patient delay in a coronavirus disease 2019 (COVID-19) outbreak in Tianjin, China from January to February 2020, 2022, 121, 09296646, 1248, 10.1016/j.jfma.2021.11.003 | |
53. | Wei Deng, Guoyuan Qi, Xinchen Yu, Optimal control strategy for COVID-19 concerning both life and economy based on deep reinforcement learning* , 2021, 30, 1674-1056, 120203, 10.1088/1674-1056/ac3229 | |
54. | Maheswari Rangasamy, Nazek Alessa, Prasantha Bharathi Dhandapani, Karuppusamy Loganathan, Dynamics of a Novel IVRD Pandemic Model of a Large Population over a Long Time with Efficient Numerical Methods, 2022, 14, 2073-8994, 1919, 10.3390/sym14091919 | |
55. | Xiangyun Shi, Xiwen Gao, Xueyong Zhou, Yongfeng Li, Analysis of an SQEIAR epidemic model with media coverage and asymptomatic infection, 2021, 6, 2473-6988, 12298, 10.3934/math.2021712 | |
56. | Innokentiy A. Kastalskiy, Evgeniya V. Pankratova, Evgeny M. Mirkes, Victor B. Kazantsev, Alexander N. Gorban, Social stress drives the multi-wave dynamics of COVID-19 outbreaks, 2021, 11, 2045-2322, 10.1038/s41598-021-01317-z | |
57. | Yinan Cai, Michael W. Golay, A dynamic Bayesian network‐based emergency decision‐making framework highlighting emergency propagations: Illustrated using the Fukushima nuclear accidents and the Covid‐19 pandemic, 2022, 0272-4332, 10.1111/risa.13928 | |
58. | Stephen E. Moore, Hetsron L. Nyandjo-Bamen, Olivier Menoukeu-Pamen, Joshua Kiddy K. Asamoah, Zhen Jin, Global stability dynamics and sensitivity assessment of COVID-19 with timely-delayed diagnosis in Ghana, 2022, 10, 2544-7297, 87, 10.1515/cmb-2022-0134 | |
59. | Ichiro Nakamoto, Jilin Zhang, Modeling the underestimation of COVID-19 infection, 2021, 25, 22113797, 104271, 10.1016/j.rinp.2021.104271 | |
60. | Jinxing Guan, Yang Zhao, Yongyue Wei, Sipeng Shen, Dongfang You, Ruyang Zhang, Theis Lange, Feng Chen, Transmission dynamics model and the coronavirus disease 2019 epidemic: applications and challenges, 2022, 2, 2749-9642, 89, 10.1515/mr-2021-0022 | |
61. | Maheswari Rangasamy, Christophe Chesneau, Carlos Martin-Barreiro, Víctor Leiva, On a Novel Dynamics of SEIR Epidemic Models with a Potential Application to COVID-19, 2022, 14, 2073-8994, 1436, 10.3390/sym14071436 | |
62. | Janelle Patel, Nikki Christofferson, Kellie J. Goodlet, Pharmacist-provided SARS-CoV-2 testing targeting a majority-Hispanic community during the early COVID-19 pandemic: Results of a patient perception survey, 2022, 62, 15443191, 187, 10.1016/j.japh.2021.08.015 | |
63. | Sharifah Norsyahindah Syed Nor, Nur Syafiqah Rasanang, Salmah Karman, Wan Safwani Wan Kamarul Zaman, Sulaiman Wadi Harun, Hamzah Arof, A Review: Surface Plasmon Resonance-Based Biosensor for Early Screening of SARS-CoV2 Infection, 2022, 10, 2169-3536, 1228, 10.1109/ACCESS.2021.3138981 | |
64. | Hua-Ying Chuang, Tsair-Wei Chien, Willy Chou, Chen-Yu Wang, Kang-Ting Tsai, Comparison of prediction accuracies between two mathematical models for the assessment of COVID-19 damage at the early stage and throughout 2020, 2022, 101, 1536-5964, e29718, 10.1097/MD.0000000000029718 | |
65. | Jiandong Lu, Xiaolei Wang, Liguo Fei, Guo Chen, Yuqiang Feng, Effects of social media empowerment on COVID-19 preventive behaviors in China, 2023, 0959-3845, 10.1108/ITP-05-2022-0412 | |
66. | Joyce Owens Kobusingye, Mitima Jean-Marie Limenyande, Harriet Mayinja, Impact of turnaround time in delivery of Covid-19 results and surveillance: a case of points of entry, Uganda, 2022, 5, 2664-2824, 10.37432/jieph.supp.2022.5.1.04.1 | |
67. | Edward Acheampong, Eric Okyere, Samuel Iddi, Joseph H.K. Bonney, Joshua Kiddy K. Asamoah, Jonathan A.D. Wattis, Rachel L. Gomes, Mathematical modelling of earlier stages of COVID-19 transmission dynamics in Ghana, 2022, 34, 22113797, 105193, 10.1016/j.rinp.2022.105193 | |
68. | Ismaïl Alsaïdi, Frédéric De Sousa Santos, Bérengère Plard, Elise Janvier, Aurélie Tinland, Abdelmajid Hafni, Emilie Mosnier, Factors associated with SARS-CoV2 infection and care pathways among the most vulnerable populations living in Marseille: a case control study, 2021, 21, 1471-2458, 10.1186/s12889-021-11716-6 | |
69. | Jeong Su Park, The More You Know about COVID-19 Diagnostic Testing, the More You Understand, 2021, 26, 2671-9886, 45, 10.14192/kjicp.2021.26.2.45 | |
70. | Parvaiz Ahmad Naik, Jian Zu, Muhammad Bilal Ghori, Mehraj-ud-din Naik, Modeling the effects of the contaminated environments on COVID-19 transmission in India, 2021, 29, 22113797, 104774, 10.1016/j.rinp.2021.104774 | |
71. | Yung-Shuo Kao, Kun-Te Lin, A Meta-Analysis of Computerized Tomography-Based Radiomics for the Diagnosis of COVID-19 and Viral Pneumonia, 2021, 11, 2075-4418, 991, 10.3390/diagnostics11060991 | |
72. | Gunnar Völkel, Axel Fürstberger, Julian D Schwab, Silke D Werle, Nensi Ikonomi, Thomas Gscheidmeier, Johann M Kraus, Alexander Groß, Martin Holderried, Julien Balig, Franz Jobst, Peter Kuhn, Klaus A Kuhn, Oliver Kohlbacher, Udo X Kaisers, Thomas Seufferlein, Hans A Kestler, Patient Empowerment During the COVID-19 Pandemic by Ensuring Safe and Fast Communication of Test Results: Implementation and Performance of a Tracking System, 2021, 23, 1438-8871, e27348, 10.2196/27348 | |
73. | Lasko Basnarkov, Igor Tomovski, Trifce Sandev, Ljupco Kocarev, Non-Markovian SIR epidemic spreading model of COVID-19, 2022, 160, 09600779, 112286, 10.1016/j.chaos.2022.112286 | |
74. | Sofia K. Mettler, Jewel Park, Orhun Özbek, Linus K. Mettler, Po-Han Ho, Hye Chang Rhim, Marloes H. Maathuis, The importance of timely contact tracing — A simulation study, 2021, 108, 12019712, 309, 10.1016/j.ijid.2021.04.029 | |
75. | Nam Xuan Ha, Truong Le-Van, Nguyen Hai Nam, Akshay Raut, Joseph Varney, Nguyen Tien Huy, A problem of self-isolation in Japan: The relationship between self-isolation and COVID-19 community case, 2022, 12, 2228-6497, 192, 10.34172/hpp.2022.24 | |
76. | Dewa Putu Wiadnyana Putra, Marcellinus Andy Rudhito, 2022, 2575, 0094-243X, 030001, 10.1063/5.0108052 | |
77. | Michael A. Rowland, Todd M. Swannack, Michael L. Mayo, Matthew Parno, Matthew Farthing, Ian Dettwiller, Glover George, William England, Molly Reif, Jeffrey Cegan, Benjamin Trump, Igor Linkov, Brandon Lafferty, Todd Bridges, COVID-19 infection data encode a dynamic reproduction number in response to policy decisions with secondary wave implications, 2021, 11, 2045-2322, 10.1038/s41598-021-90227-1 | |
78. | Silvana Nair Leite, Jorge Antonio Zepeda Bermudez, Débora Melecchi, Adelir Rodrigues da Veiga, Ana Liani Beisl Oliveira, Artur Custódio Moreira de Sousa, Célia Machado Gervásio Chaves, Fernanda Manzini, Lidiane Silva Dutra, Luísa Arueira Chaves, Marco Aurélio Pereira, Maria Eufrásia Oliveira Lima, Moysés Longinho Toniolo, Ronald Ferreira dos Santos, Silvânia Dantas, Jorge Carlos Santos da Costa, Projeto Integra: fortalecimento da participação social na agenda das políticas, serviços e tecnologias em saúde, 2021, 26, 1678-4561, 5589, 10.1590/1413-812320212611.18212021 | |
79. | Fatemeh Asadi-Mehregan, Pouria Assari, Mehdi Dehghan, The numerical solution of a mathematical model of the Covid-19 pandemic utilizing a meshless local discrete Galerkin method, 2022, 0177-0667, 10.1007/s00366-022-01749-9 | |
80. | Suresh K. Joishy, Michito Sadohara, Masaru Kurihara, Yasuharu Tokuda, Complexity of the Diagnosis of COVID-19 in the Context of Pandemicity: Need for Excellence in Diagnostic Acumen, 2022, 43, 2092-6715, 16, 10.4082/kjfm.20.0188 | |
81. | Somjit Nath, Mayank Baranwal, Harshad Khadilkar, 2021, Revisiting State Augmentation methods for Reinforcement Learning with Stochastic Delays, 9781450384469, 1346, 10.1145/3459637.3482386 | |
82. | Mahender Aileni, Gulab Khan Rohela, Phanikanth Jogam, Shakuntala Soujanya, Baohong Zhang, Biotechnological Perspectives to Combat the COVID-19 Pandemic: Precise Diagnostics and Inevitable Vaccine Paradigms, 2022, 11, 2073-4409, 1182, 10.3390/cells11071182 | |
83. | Chadia Haddad, Sandrella Bou Malhab, Diana Malaeb, Hala Sacre, Danielle Saadeh, Vanessa Mourtada, Pascale Salameh, Stigma toward people with COVID-19 among the Lebanese population: a cross-sectional study of correlates and mediating effects, 2021, 9, 2050-7283, 10.1186/s40359-021-00646-y | |
84. | Gokul Chandra Biswas, Swapnila Choudhury, Mohammad Mahbub Rabbani, Jagotamoy Das, A Review on Potential Electrochemical Point-of-Care Tests Targeting Pandemic Infectious Disease Detection: COVID-19 as a Reference, 2022, 10, 2227-9040, 269, 10.3390/chemosensors10070269 | |
85. | Xinmiao Rong, Huidi Chu, Liu Yang, Shaosi Tan, Chao Yang, Pei Yuan, Yi Tan, Linhua Zhou, Yawen Liu, Qing Zhen, Shishen Wang, Meng Fan, Huaiping Zhu, Recursive Zero-COVID model and quantitation of control efforts of the Omicron epidemic in Jilin province, 2023, 8, 24680427, 11, 10.1016/j.idm.2022.11.007 | |
86. | Lingyun Zhu, Wei Dong, Qing Sun, Esteban Abelardo Hernandez Vargas, Xin Du, 2021, Estimation of the Unreported Infections of COVID-19 based on an Extended Stochastic Susceptible-Exposed-Infective-Recovered Model, 978-1-6654-2423-3, 953, 10.1109/DDCLS52934.2021.9455548 | |
87. | Rishabh Khatri, Jay Patel, Jun Song, Henry P. Parkman, New-onset functional dyspepsia after COVID-19, 2023, 4, 2691-3895, e0266, 10.1097/MD9.0000000000000266 | |
88. | Adam Sadowski, Zbigniew Galar, Robert Walasek, Grzegorz Zimon, Per Engelseth, Big data insight on global mobility during the Covid-19 pandemic lockdown, 2021, 8, 2196-1115, 10.1186/s40537-021-00474-2 | |
89. | Keren Dopelt, Nadav Davidovitch, Nikol Davidov, Ira Plot, Hagai Boas, Paul Barach, “As if we are branded with the mark of Cain”: stigma, guilt, and shame experienced by COVID-19 survivors in Israel - a qualitative study, 2023, 1046-1310, 10.1007/s12144-023-04241-9 | |
90. | Guihong Fan, Juan Li, Jacques Bélair, Huaiping Zhu, Delayed Model for the Transmission and Control of COVID-19 with Fangcang Shelter Hospitals, 2023, 83, 0036-1399, 276, 10.1137/21M146154X | |
91. | Jayanta Kumar Ghosh, Sudhanshu Kumar Biswas, Susmita Sarkar, Uttam Ghosh, Mathematical modelling of COVID-19: A case study of Italy, 2022, 194, 03784754, 1, 10.1016/j.matcom.2021.11.008 | |
92. | Katherine South, Suzanne Bakken, Theresa Koleck, Veronica Barcelona, Noemie Elhadad, Caitlin Dreisbach, Women’s Experiences of Symptoms of Suspected or Confirmed COVID-19 Illness During the Pandemic, 2022, 26, 17514851, 450, 10.1016/j.nwh.2022.09.005 | |
93. | Katie Hogan, Briana Macedo, Venkata Macha, Arko Barman, Xiaoqian Jiang, Contact Tracing Apps: Lessons Learned on Privacy, Autonomy, and the Need for Detailed and Thoughtful Implementation, 2021, 9, 2291-9694, e27449, 10.2196/27449 | |
94. | Daw-Hsin Yang, Tsair-Wei Chien, Yu-Tsen Yeh, Ting-Ya Yang, Willy Chou, Ju-Kuo Lin, Using the absolute advantage coefficient (AAC) to measure the strength of damage hit by COVID-19 in India on a growth-share matrix, 2021, 26, 2047-783X, 10.1186/s40001-021-00528-4 | |
95. | Rico Januar Sitorus, Irzanita Wathan, Hibsah Ridwan, Hariadi Wibisono, Lesti Nuraini, Gandi Kosim, Nugi Nurdin, Hatta Mamat, Iche Andrayani, Nyoman Yudi Antara, Merry Natalia, Transmission dynamics of novel Coronavirus–SARS-CoV-2 in South Sumatera, Indonesia, 2021, 11, 22133984, 100777, 10.1016/j.cegh.2021.100777 | |
96. | Jonghoo Lee, Jae-Uk Song, Sung Ryul Shim, Comparing the diagnostic accuracy of rapid antigen detection tests to real time polymerase chain reaction in the diagnosis of SARS-CoV-2 infection: A systematic review and meta-analysis, 2021, 144, 13866532, 104985, 10.1016/j.jcv.2021.104985 | |
97. | Yue Deng, Siming Xing, Meixia Zhu, Jinzhi Lei, Impact of insufficient detection in COVID-19 outbreaks, 2021, 18, 1551-0018, 9727, 10.3934/mbe.2021476 | |
98. | Gokul Chandra Biswas, Md. Taufiqur Mannan Khan, Jagotamoy Das, Wearable nucleic acid testing platform - A perspective on rapid self-diagnosis and surveillance of infectious diseases, 2023, 226, 09565663, 115115, 10.1016/j.bios.2023.115115 | |
99. | Sam Yu-Chieh Ho, Tsair-Wei Chien, Yang Shao, Ju-Hao Hsieh, Visualizing the features of inflection point shown on a temporal bar graph using the data of COVID-19 pandemic, 2022, 101, 0025-7974, e28749, 10.1097/MD.0000000000028749 | |
100. | Olumuyiwa J. Peter, Amjad S. Shaikh, Mohammed O. Ibrahim, Kottakkaran Sooppy Nisar, Dumitru Baleanu, Ilyas Khan, Adesoye I. Abioye, Analysis and Dynamics of Fractional Order Mathematical Model of COVID-19 in Nigeria Using Atangana-Baleanu Operator, 2021, 66, 1546-2226, 1823, 10.32604/cmc.2020.012314 | |
101. | Iulian A. Bratu, Lucian C. Dinca, Cristian M. Enescu, Mirela Stanciu, The Role of Social Media in Public Forest Management Policies during COVID-19: Implications for Stakeholder Engagement, 2022, 14, 2071-1050, 3778, 10.3390/su14073778 | |
102. | Linhua Zhou, Xinmiao Rong, Meng Fan, Liu Yang, Huidi Chu, Ling Xue, Guorong Hu, Siyu Liu, Zhijun Zeng, Ming Chen, Wei Sun, Jiamin Liu, Yawen Liu, Shishen Wang, Huaiping Zhu, Modeling and Evaluation of the Joint Prevention and Control Mechanism for Curbing COVID-19 in Wuhan, 2022, 84, 0092-8240, 10.1007/s11538-021-00983-4 | |
103. | Olaniyi Iyiola, Bismark Oduro, Trevor Zabilowicz, Bose Iyiola, Daniel Kenes, System of Time Fractional Models for COVID-19: Modeling, Analysis and Solutions, 2021, 13, 2073-8994, 787, 10.3390/sym13050787 | |
104. | A. Ya. Nikitin, M. V. Chesnokova, S. V. Balakhonov, Algorithm and Results of Short-Term Forecast of Changes in the COVID-19 Spread Coefcient in the Constituent Entities of the Russian Federation, 2021, 2658-719X, 98, 10.21055/0370-1069-2021-3-98-105 | |
105. | Julliana Gonçalves Marques, Luiz Affonso Guedes, Márjory Cristiany da Costa Abreu, Evaluating Time Influence over Performance of Machine-Learning-Based Diagnosis: A Case Study of COVID-19 Pandemic in Brazil, 2022, 20, 1660-4601, 136, 10.3390/ijerph20010136 | |
106. | Justin M. Calabrese, Jeffery Demers, How optimal allocation of limited testing capacity changes epidemic dynamics, 2022, 538, 00225193, 111017, 10.1016/j.jtbi.2022.111017 | |
107. | M. Abdelhakem, A. Ahmed, D. Baleanu, M. El-kady, Monic Chebyshev pseudospectral differentiation matrices for higher-order IVPs and BVPs: applications to certain types of real-life problems, 2022, 41, 2238-3603, 10.1007/s40314-022-01940-0 | |
108. | Mastaneh Alinezhadi, Niloofar Neisi, Mojtaba Rasti, Maniya Arshadi, Mehdi Parsanahad, Bahman Cheraghian, Evaluation of False Negative Among SARS-COV-2 Patients with Negative Real-time PCR Result Using Nested-RT PCR, 2022, 15, 2008-3645, 10.5812/jjm-122889 | |
109. | Rhys P.D. Inward, Felix Jackson, Abhishek Dasgupta, Graham Lee, Anya Lindström Battle, Kris V. Parag, Moritz U.G. Kraemer, Impact of spatiotemporal heterogeneity in COVID-19 disease surveillance on epidemiological parameters and case growth rates, 2022, 41, 17554365, 100627, 10.1016/j.epidem.2022.100627 | |
110. | Ahuod S. Alsheri, Aeshah A. Alraeza, Mona R. Afia, Mathematical modeling of the effect of quarantine rate on controlling the infection of COVID19 in the population of Saudi Arabia, 2022, 61, 11100168, 6843, 10.1016/j.aej.2021.12.033 | |
111. | Sabuj Kanti Mistry, A. R. M. Mehrab Ali, Uday Narayan Yadav, Md. Nazmul Huda, Md. Mahmudur Rahman, Manika Saha, Md. Ashfikur Rahman, David Lim, Saruna Ghimire, Stigma toward people with COVID-19 among Bangladeshi older adults, 2022, 10, 2296-2565, 10.3389/fpubh.2022.982095 | |
112. | Kassiani Mellou, Spyros Sapounas, Ioannis Panagoulias, Maria Gkova, Kalliopi Papadima, Anastasia Andreopoulou, Danai Kalotychou, Michalis Chatzopoulos, Kassiani Gkolfinopoulou, Vassiliki Papaevangelou, Sotirios Tsiodras, Georgios Panagiotakopoulos, Theoklis Zaoutis, Dimitrios Paraskevis, Time Lag between COVID-19 Diagnosis and Symptoms Onset for Different Population Groups: Evidence That Self-Testing in Schools Was Associated with Timely Diagnosis among Children, 2022, 12, 2075-1729, 1305, 10.3390/life12091305 | |
113. | Ofosuhene O. Apenteng, Bismark Oduro, Isaac Owusu-Mensah, A compartmental model to investigate the dynamics of the COVID-19 pandemic: A case study in five countries, 2021, 14, 1793-5245, 2150027, 10.1142/S1793524521500273 | |
114. | Abdullah Khamis Alzahrani, Oyoon Abdul Razzaq, Najeeb Alam Khan, Ali Saleh Alshomrani, Malik Zaka Ullah, Transmissibility of epidemic diseases caused by delay with local proportional fractional derivative, 2021, 2021, 1687-1847, 10.1186/s13662-021-03435-4 | |
115. | Seyed Ali Rakhshan, Mahdi Soltani Nejad, Marzie Zaj, Fatemeh Helen Ghane, Global analysis and prediction scenario of infectious outbreaks by recurrent dynamic model and machine learning models: A case study on COVID-19, 2023, 00104825, 106817, 10.1016/j.compbiomed.2023.106817 | |
116. | Sebastian Sattler, Dina Maskileyson, Eric Racine, Eldad Davidov, Alice Escande, Stigmatization in the context of the COVID-19 pandemic: a survey experiment using attribution theory and the familiarity hypothesis, 2023, 23, 1471-2458, 10.1186/s12889-023-15234-5 | |
117. | Yijun Lou, Feng-Bin Wang, A Reaction-Diffusion Model with Spatially Inhomogeneous Delays, 2023, 1040-7294, 10.1007/s10884-023-10254-6 | |
118. | Sulifu Bao, Zhi-Hua Hu, Xiaohui Wang, An integrated optimization control model of combining epidemic and production–inventory models and its numerical simulations, 2023, 126, 10075704, 107490, 10.1016/j.cnsns.2023.107490 | |
119. | Prasantha Bharathi Dhandapani, Víctor Leiva, Carlos Martin-Barreiro, Maheswari Rangasamy, On a Novel Dynamics of a SIVR Model Using a Laplace Adomian Decomposition Based on a Vaccination Strategy, 2023, 7, 2504-3110, 407, 10.3390/fractalfract7050407 | |
120. | Xueru Xu, Li Luo, Huyang Xu, Yuanchen Fang, The emergency hierarchical medical system in China: Improving patient waiting times and operation management, 2024, 17, 2047-9700, 660, 10.1080/20479700.2023.2229525 | |
121. | Ali Azargoonjahromi, Role of the SARS-CoV-2 Virus in Brain Cells, 2024, 37, 0882-8245, 61, 10.1089/vim.2023.0116 | |
122. | Shimeng Dong, Jinlong Lv, Wanbiao Ma, Boralahala Gamage Sampath Aruna Pradeep, A COVID-19 Infection Model Considering the Factors of Environmental Vectors and Re-Positives and Its Application to Data Fitting in Japan and Italy, 2023, 15, 1999-4915, 1201, 10.3390/v15051201 | |
123. | Teddy Lazebnik, Computational applications of extended SIR models: A review focused on airborne pandemics, 2023, 483, 03043800, 110422, 10.1016/j.ecolmodel.2023.110422 | |
124. | Padma Bhushan Borah, Hemanta Kumar Sarmah, 2024, Chapter 41, 978-3-031-52964-1, 517, 10.1007/978-3-031-52965-8_41 | |
125. | Marwa Gamal, M. El-Kady, M. Abdelhakem, Solving real-life BVPs via the second derivative Chebyshev pseudo-Galerkin method, 2024, 35, 0129-1831, 10.1142/S012918312450089X | |
126. | Neville J. Ford, Mathematical modelling of problems with delay and after-effect, 2024, 01689274, 10.1016/j.apnum.2024.10.007 | |
127. | 德玉 郭, A Dynamics Model of COVID-19 with Transition from the Asymptomatic to the Symptomatic Infected Individuals, 2023, 12, 2324-7991, 2457, 10.12677/AAM.2023.125248 | |
128. | Atifa Sarwar, Abdulsalam Almadani, Emmanuel O. Agu, Few-shot meta-learning for pre-symptomatic detection of Covid-19 from limited health tracker data, 2024, 32, 23526483, 100459, 10.1016/j.smhl.2024.100459 | |
129. | Chuanqing Xu, Zonghao Zhang, Xiaotong Huang, Kedeng Cheng, Songbai Guo, Xiaojing Wang, Maoxing Liu, Xiaoling Liu, A study on the transmission dynamics of COVID-19 considering the impact of asymptomatic infection, 2023, 17, 1751-3758, 10.1080/17513758.2023.2244980 | |
130. | Akanksha Jain, Sonia Bajaj, Parag Jain, Ashish Majumdar, Ayushi Singh, Pranay Soni, A review on biotechnologically derived techniques to combat COVID-19 situation, 2023, 8, 27726320, 100112, 10.1016/j.hsr.2023.100112 | |
131. | Laura A. Rodríguez-Villamizar, Alexander Torres Prieto, Ruth A. Martínez-Vega, Lina M. Vera-Cala, Epidemia por COVID-19 en Santander 2020: análisis epidemiológico desde un enfoque territorial por provincias, 2022, 53, 01210807, 10.18273/saluduis.53.e:21040 | |
132. | Elham Sabouri, Amin Saburi, Reza Gerami, Tina Zeraati, Ehsan Saburi, Mostafa Ghanei, Computerized Intelligence and Mathematical Models for COVID-19 Diagnosis: A Review, 2023, 9, 2322-1143, 55, 10.61186/jhehp.9.2.55 | |
133. | Dina Abdelhamid, Wedad Albalawi, Kottakkaran Sooppy Nisar, A. Abdel-Aty, Suliman Alsaeed, M. Abdelhakem, Mixed Chebyshev and Legendre polynomials differentiation matrices for solving initial-boundary value problems, 2023, 8, 2473-6988, 24609, 10.3934/math.20231255 | |
134. | Emeka F. Obiajulu, Andrew Omame, Simeon C. Inyama, Uchenna H. Diala, Salman A. AlQahtani, Mabrook S. Al-Rakhami, Abdulaziz M. Alawwad, Abdullilah A. Alotaibi, Analysis of a non-integer order mathematical model for double strains of dengue and COVID-19 co-circulation using an efficient finite-difference method, 2023, 13, 2045-2322, 10.1038/s41598-023-44825-w | |
135. | Ali Hadianfar, Sedigheh Rastaghi, Hamed Tabesh, Azadeh Saki, Application of distributed lag models and spatial analysis for comparing the performance of the COVID-19 control decisions in European countries, 2023, 13, 2045-2322, 10.1038/s41598-023-44830-z | |
136. | S. Swetha, S. Sindu Devi, K. Kannan, Optimal Control Strategies for COVID-19 Using SEIQR Mathematical Model, 2024, 0369-8203, 10.1007/s40010-024-00898-4 | |
137. | Hassan A. Alsattar, Sarah Qahtan, Aws Alaa Zaidan, Muhammet Deveci, Luis Martinez, Dragan Pamucar, Witold Pedrycz, Developing deep transfer and machine learning models of chest X-ray for diagnosing COVID-19 cases using probabilistic single-valued neutrosophic hesitant fuzzy, 2024, 236, 09574174, 121300, 10.1016/j.eswa.2023.121300 | |
138. | Michael Fralick, Jason A. Moggridge, Makenna Wiebe, Lucas Castellani, Allison McGeer, Bryan Feenstra, Aaron Hinz, Alexandra M.A. Hicks, Laura A. Hug, Alex Wong, Tamara Van Bakel, Sawith Abeygunawardena, Tasha Burhunduli, Hebah S. Mejbel, Rees Kassen, Nisha Thampi, Derek MacFadden, Caroline Nott, SARS-CoV-2 burden on the floor was associated with COVID-19 cases and outbreaks in two acute care hospitals: a prospective cohort study, 2024, 0899-823X, 1, 10.1017/ice.2024.121 | |
139. | Alexis Dorta-Gorrín, Jesús Navas-Méndez, Mónica Gozalo-Margüello, Laura Miralles, Lorena García-Hevia, Detection of SARS-CoV-2 Based on Nucleic Acid Amplification Tests (NAATs) and Its Integration into Nanomedicine and Microfluidic Devices as Point-of-Care Testing (POCT), 2023, 24, 1422-0067, 10233, 10.3390/ijms241210233 | |
140. | 勇盛 赵, Dynamical Analysis of a COVID-19 Transmission Model with Vaccination, 2024, 13, 2324-7991, 1187, 10.12677/aam.2024.134109 | |
141. | Raheleh Khanduzi, Amin Jajarmi, Asiyeh Ebrahimzadeh, Mehdi Shahini, A novel collocation method with a coronavirus optimization algorithm for the optimal control of COVID-19: A case study of Wuhan, China, 2024, 178, 00104825, 108680, 10.1016/j.compbiomed.2024.108680 | |
142. | Mohamed Amouch, Noureddine Karim, Fractional-order mathematical modeling of COVID-19 dynamics with different types of transmission, 2023, 0, 2155-3289, 0, 10.3934/naco.2023019 | |
143. | Sulifu Bao, Zhi-Hua Hu, A new model of the transmission dynamics of COVID-19 propagation with vaccination and recommended treatments, 2023, 111, 0924-090X, 20465, 10.1007/s11071-023-08914-9 | |
144. | S. Sankaranarayanan, An approach to statistical analysis-using the average transmission model of Covid 19, 2020, 8, 23193786, 2158, 10.26637/MJM0804/0141 | |
145. | Rico Januar Sitorus, Hariadi Wibisono, Hibsah Ridwan, Nyoman Yudi Antara, Merry Natalia Panjaitan, Reymart V. Sangalang, TRACING OF COVID-19 TRANSMISSION BASED ON CLOSE CONTACT POPULATION: CASES IN SOUTH SUMATRA, 2023, 11, 2541-092X, 9, 10.20473/jbe.V11I12023.9-16 | |
146. | Nicholas P. McCormick, Oluchukwu M. Ezeala, Spencer H. Durham, Salisa C. Westrick, Assessing barriers to COVID-19 diagnostic testing in community pharmacies: Insights from Alabama, 2024, 15443191, 102286, 10.1016/j.japh.2024.102286 | |
147. | Ruchi Bhoot, Suved Sanjay Ghanmode, Yogesh Simmhan, TARIS: Scalable Incremental Processing of Time-Respecting Algorithms on Streaming Graphs, 2024, 35, 1045-9219, 2527, 10.1109/TPDS.2024.3471574 | |
148. | Lidong Zhou, Qixing Han, The threshold of a stochastic SIVS model with saturated incidence based on logarithmic Ornstein-Uhlenbeck process, 2025, 0022247X, 129253, 10.1016/j.jmaa.2025.129253 | |
149. | Younes Mousania, Salman Karimi, Ali Farmani, Designing High-Performance SPR Biosensor Using Hybrid Structure of BifeO3 and 2D Material for SARS-CoV-2 Detection, 2025, 1557-1963, 10.1007/s11468-024-02516-w | |
150. | Haibo Bao, Ye He, Epidemic dynamics with awareness cascade of positive and negative information on delayed multiplex networks, 2025, 35, 1054-1500, 10.1063/5.0247513 | |
151. | Alberto Landi, Giulio Pisaneschi, Marco Laurino, Piero Manfredi, Optimal social distancing in pandemic preparedness and lessons from COVID-19: Intervention intensity and infective travelers, 2025, 604, 00225193, 112072, 10.1016/j.jtbi.2025.112072 |
Date(day/month) | 15 Jan | 16 Jan | 17 Jan | 18 Jan | 19 Jan | 20 Jan | 21 Jan |
Cumulative cases | 41 | 45 | 62 | 121 | 224 | 291 | 440 |
New cases | 0 | 4 | 17 | 59 | 78 | 77 | 149 |
Date(day/month) | 22 Jan | 23 Jan | 24 Jan | 25 Jan | 26 Jan | 27 Jan | 28 Jan |
Cumulative cases | 571 | 830 | 1287 | 1975 | 2744 | 4515 | 5974 |
New cases | 131 | 259 | 444 | 688 | 769 | 1771 | 1459 |
Date(day/month) | 29 Jan | 30 Jan | 31 Jan | 01 Feb | 02 Feb | ||
Cumulative cases | 7711 | 9692 | 11791 | 14380 | 17205 | ||
New cases | 1737 | 1982 | 2102 | 2590 | 2829 |
Date(day/month) | 03 Feb | 04 Feb | 05 Feb | 06 Feb | 07 Feb | 08 Feb | 09 Feb |
Cumulative cases | 20438 | 24324 | 28018 | 31161 | 34546 | 37198 | 40171 |
New cases | 3235 | 3887 | 3694 | 3143 | 3399 | 2656 | 3062 |
Date(day/month) | 10 Feb | 11 Feb | 12 Feb | 13 Feb | 14 Feb | 15 Feb | 16 Feb |
Cumulative cases | 42638 | 44653 | 59804 | 63851 | 66492 | 68501 | 70549 |
New cases | 2478 | 2015 | 15152 | 5090 | 2641 | 2009 | 2048 |
Date(day/month) | 17 Feb | 18 Feb | 19 Feb | 20 Feb | 21 Feb | 22 Feb | 23 Feb |
Cumulative cases | 72436 | 74185 | 74579 | 75456 | 76288 | 76936 | 77150 |
New cases | 1886 | 1749 | 820 | 889 | 397 | 648 | 409 |
Date(day/month) | 24 Feb | 25 Feb | 26 Feb | 27 Feb | 28 Feb | 29 Feb | 01 Mar |
Cumulative cases | 77658 | 78604 | 78497 | 78824 | 79251 | 79824 | 80026 |
New cases | 508 | 406 | 443 | 327 | 427 | 573 | 202 |
Date(day/month) | 02 Mar | 03 Mar | 04 Mar | 05 Mar | |||
Cumulative cases | 80151 | 80270 | 80409 | 80552 | |||
New cases | 125 | 119 | 139 | 143 |
Parameter | Description | Value (Range) | Unit | Source |
q | Self-quarantined rate of the susceptible | 1/10 | day−1 | Estimated |
q1 | Transition rate of self-quarantined individuals to the susceptible | 1/200000 | day−1 | Estimated |
βe | Transmission rate from the exposed to the susceptible | 3.511×10−8 (10−8,10−7) | day−1 | Estimated |
βi1 | Transmission rate from the infectious with timely diagnosis to the susceptible | 3.112×10−8 (0.91∗10−8,10−7) | day−1 | Estimated |
βi2 | Transmission rate from the infectious with delayed diagnosis to the susceptible | 1.098×10−7 (1.1∗10−8,3∗10−7) | day−1 | Estimated |
βv | Transmission rate from the susceptible to the exposed (infected by virus) | 1.009×10−10 (10−11,9∗10−10) | day−1 | Estimated |
1/ω | Incubation period | 5.2 | day | [10] |
ϕ | Proportion of the infectious with timely diagnosis | 0.4(0.3,0.65) | – | Estimated |
1/γ1 | Waiting time of the infectious for timely diagnosis | 2.9(1,5) | day | [29] |
1/γ2 | Waiting time of the infectious for delayed diagnosis | 10 (5,20) | day | Estimated |
μ | Disease-induced death rate | 1.7826×10−5 | day−1 | [17] |
m | Recovery rate of the hospitalized | 1/14 | day−1 | [9] |
f1 | Virus released rate of the exposed | 1440 (864,2160) | day−1 | Estimated |
f2 | Virus released rate of the infectious with timely-diagnosis | 1008 (432,1440) | day−1 | Estimated |
f3 | Virus released rate of the infectious with delayed-diagnosis | 1728 (864,2592) | day−1 | Estimated |
dv | Clear rate of virus in the environment | 144 (115.2,172.8) | day−1 | Estimated |
S(0) | Initial value of the susceptible | 11081000 | – | [30] |
Sq(0) | Initial value of the self-quarantined susceptible | 159 | – | Estimated |
E(0) | Initial value of the exposed | 399 | – | [5] |
I1(0) | Initial value of the infectious with timely diagnosis | 28 | – | Estimated |
I2(0) | Initial value of the infectious with delayed diagnosis | 54 | – | Estimated |
H(0) | Initial value of the hospitalized | 41 | – | [5] |
R(0) | Initial value of the recovered | 12 | – | [5] |
V(0) | Initial value of virus in the environment | 21080 | – | Estimated |
Date(day/month) | 15 Jan | 16 Jan | 17 Jan | 18 Jan | 19 Jan | 20 Jan | 21 Jan |
Cumulative cases | 41 | 45 | 62 | 121 | 224 | 291 | 440 |
New cases | 0 | 4 | 17 | 59 | 78 | 77 | 149 |
Date(day/month) | 22 Jan | 23 Jan | 24 Jan | 25 Jan | 26 Jan | 27 Jan | 28 Jan |
Cumulative cases | 571 | 830 | 1287 | 1975 | 2744 | 4515 | 5974 |
New cases | 131 | 259 | 444 | 688 | 769 | 1771 | 1459 |
Date(day/month) | 29 Jan | 30 Jan | 31 Jan | 01 Feb | 02 Feb | ||
Cumulative cases | 7711 | 9692 | 11791 | 14380 | 17205 | ||
New cases | 1737 | 1982 | 2102 | 2590 | 2829 |
Date(day/month) | 03 Feb | 04 Feb | 05 Feb | 06 Feb | 07 Feb | 08 Feb | 09 Feb |
Cumulative cases | 20438 | 24324 | 28018 | 31161 | 34546 | 37198 | 40171 |
New cases | 3235 | 3887 | 3694 | 3143 | 3399 | 2656 | 3062 |
Date(day/month) | 10 Feb | 11 Feb | 12 Feb | 13 Feb | 14 Feb | 15 Feb | 16 Feb |
Cumulative cases | 42638 | 44653 | 59804 | 63851 | 66492 | 68501 | 70549 |
New cases | 2478 | 2015 | 15152 | 5090 | 2641 | 2009 | 2048 |
Date(day/month) | 17 Feb | 18 Feb | 19 Feb | 20 Feb | 21 Feb | 22 Feb | 23 Feb |
Cumulative cases | 72436 | 74185 | 74579 | 75456 | 76288 | 76936 | 77150 |
New cases | 1886 | 1749 | 820 | 889 | 397 | 648 | 409 |
Date(day/month) | 24 Feb | 25 Feb | 26 Feb | 27 Feb | 28 Feb | 29 Feb | 01 Mar |
Cumulative cases | 77658 | 78604 | 78497 | 78824 | 79251 | 79824 | 80026 |
New cases | 508 | 406 | 443 | 327 | 427 | 573 | 202 |
Date(day/month) | 02 Mar | 03 Mar | 04 Mar | 05 Mar | |||
Cumulative cases | 80151 | 80270 | 80409 | 80552 | |||
New cases | 125 | 119 | 139 | 143 |
Parameter | Description | Value (Range) | Unit | Source |
q | Self-quarantined rate of the susceptible | 1/10 | day−1 | Estimated |
q1 | Transition rate of self-quarantined individuals to the susceptible | 1/200000 | day−1 | Estimated |
βe | Transmission rate from the exposed to the susceptible | 3.511×10−8 (10−8,10−7) | day−1 | Estimated |
βi1 | Transmission rate from the infectious with timely diagnosis to the susceptible | 3.112×10−8 (0.91∗10−8,10−7) | day−1 | Estimated |
βi2 | Transmission rate from the infectious with delayed diagnosis to the susceptible | 1.098×10−7 (1.1∗10−8,3∗10−7) | day−1 | Estimated |
βv | Transmission rate from the susceptible to the exposed (infected by virus) | 1.009×10−10 (10−11,9∗10−10) | day−1 | Estimated |
1/ω | Incubation period | 5.2 | day | [10] |
ϕ | Proportion of the infectious with timely diagnosis | 0.4(0.3,0.65) | – | Estimated |
1/γ1 | Waiting time of the infectious for timely diagnosis | 2.9(1,5) | day | [29] |
1/γ2 | Waiting time of the infectious for delayed diagnosis | 10 (5,20) | day | Estimated |
μ | Disease-induced death rate | 1.7826×10−5 | day−1 | [17] |
m | Recovery rate of the hospitalized | 1/14 | day−1 | [9] |
f1 | Virus released rate of the exposed | 1440 (864,2160) | day−1 | Estimated |
f2 | Virus released rate of the infectious with timely-diagnosis | 1008 (432,1440) | day−1 | Estimated |
f3 | Virus released rate of the infectious with delayed-diagnosis | 1728 (864,2592) | day−1 | Estimated |
dv | Clear rate of virus in the environment | 144 (115.2,172.8) | day−1 | Estimated |
S(0) | Initial value of the susceptible | 11081000 | – | [30] |
Sq(0) | Initial value of the self-quarantined susceptible | 159 | – | Estimated |
E(0) | Initial value of the exposed | 399 | – | [5] |
I1(0) | Initial value of the infectious with timely diagnosis | 28 | – | Estimated |
I2(0) | Initial value of the infectious with delayed diagnosis | 54 | – | Estimated |
H(0) | Initial value of the hospitalized | 41 | – | [5] |
R(0) | Initial value of the recovered | 12 | – | [5] |
V(0) | Initial value of virus in the environment | 21080 | – | Estimated |