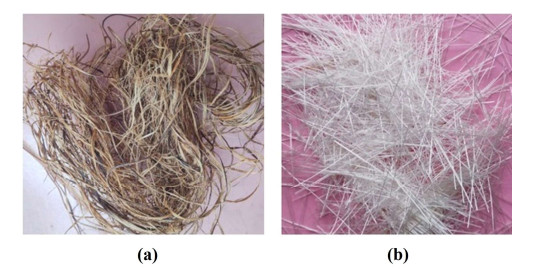
The screw pine and E-glass fibers were hybridized in the vinyl ester resin matrix to prepare the hybrid composite laminates in the present communication. Hybrid composite laminates at the constant volume fraction of 35.12% has been fabricated using the hot press compression molding in two forms, namely dispersed and skin-core, to evaluate the mechanical properties. Mechanical properties of composite laminates were studied based on the various volume fraction of glass fiber content (0, 3.32, 8.15, 12.44 and 16.53 vol.%). The scanning electron microscopy (HITACHI S-3000N) was used to study the fracture surface of composite laminates. The results of hybrid composite laminates were compared with a neat resin sample and screw pine fiber (35.12 vol.%) alone composite. The results revealed that the mechanical properties of both the type of composite laminates increased as glass fiber addition was increased. The SPF18.59/GF16.53 hybrid composite laminate exhibits the highest level of mechanical properties because of the concentration and higher elongation percentage of glass fibers. Moreover, the skin-core type composites perform better than those of the dispersed type hybrid composites. Because of the stretching nature of screw pine fibers, they elongate when the load is transferred from glass fibers to screw pine fibers, resulting in an increase in mechanical properties. The property values were predicted using a theoretical model, and it was found that the two were in good agreement.
Citation: Venkatarajan Subbarayalu, Subbu Chinnaraman, Athijayamani Ayyanar, Jayaseelan Chinnapalanisamy. Mechanical properties of vinyl ester hybrid composite laminates reinforced with screw pine and glass fiber[J]. AIMS Materials Science, 2024, 11(1): 114-128. doi: 10.3934/matersci.2024007
[1] | Prashant Tripathi, Vivek Kumar Gupta, Anurag Dixit, Raghvendra Kumar Mishra, Satpal Sharma . Development and characterization of low cost jute, bagasse and glass fiber reinforced advanced hybrid epoxy composites. AIMS Materials Science, 2018, 5(2): 320-337. doi: 10.3934/matersci.2018.2.320 |
[2] | Hendra Suherman, Yovial Mahyoedin, Afdal Zaky, Jarot Raharjo, Talitha Amalia Suherman, Irmayani Irmayani . Investigation of the mechanical properties of bio-composites based on loading kenaf fiber and molding process parameters. AIMS Materials Science, 2024, 11(6): 1165-1178. doi: 10.3934/matersci.2024057 |
[3] | Zulzamri Salleh, Md Mainul Islam, Jayantha Ananda Epaarachchi, Haibin Su . Mechanical properties of sandwich composite made of syntactic foam core and GFRP skins. AIMS Materials Science, 2016, 3(4): 1704-1727. doi: 10.3934/matersci.2016.4.1704 |
[4] | Kator Jeff Jomboh, Adele Dzikwi Garkida, Emmanuel Majiyebo Alemaka, Mohammed Kabir Yakubu, Vershima Cephas Alkali, Wilson Uzochukwu Eze, Nuhu Lawal . Properties and applications of natural, synthetic and hybrid fiber reinforced polymer composite: A review. AIMS Materials Science, 2024, 11(4): 774-801. doi: 10.3934/matersci.2024038 |
[5] | Mohammed Y. Abdellah, Hamzah Alharthi, Mohamed K. Hassan, Ahmed F. Mohamed . Effect of specimen size on natural vibration of open hole copper/glass-reinforced epoxy laminate composites. AIMS Materials Science, 2020, 7(4): 499-517. doi: 10.3934/matersci.2020.4.499 |
[6] | Ninis Hadi Haryanti, Suryajaya, Tetti Novalina Manik, Khaipanurani, Adik Bahanawan, Setiawan Khoirul Himmi . Characteristics of water chestnut (Eleocharis dulcis) long fiber reinforced composite modified by NaOH and hot water. AIMS Materials Science, 2024, 11(6): 1199-1219. doi: 10.3934/matersci.2024059 |
[7] | Kiyotaka Obunai, Daisuke Mikami, Tadao Fukuta, Koichi Ozaki . Microstructure and mechanical properties of newly developed SiC-C/C composites under atmospheric conditions. AIMS Materials Science, 2018, 5(3): 494-507. doi: 10.3934/matersci.2018.3.494 |
[8] | R.C.M. Sales-Contini, J.P. Costa, F.J.G. Silva, A.G. Pinto, R.D.S.G. Campilho, I.M. Pinto, V.F.C. Sousa, R.P. Martinho . Influence of laser marking parameters on data matrix code quality on polybutylene terephthalate/glass fiber composite surface using microscopy and spectroscopy techniques. AIMS Materials Science, 2024, 11(1): 150-172. doi: 10.3934/matersci.2024009 |
[9] | Iketut Suarsana, Igpagus Suryawan, NPG Suardana, Suprapta Winaya, Rudy Soenoko, Budiarsa Suyasa, Wijaya Sunu, Made Rasta . Flexural strength of hybrid composite resin epoxy reinforced stinging nettle fiber with silane chemical treatment. AIMS Materials Science, 2021, 8(2): 185-199. doi: 10.3934/matersci.2021013 |
[10] | Araya Abera Betelie, Anthony Nicholas Sinclair, Mark Kortschot, Yanxi Li, Daniel Tilahun Redda . Mechanical properties of sisal-epoxy composites as functions of fiber-to-epoxy ratio. AIMS Materials Science, 2019, 6(6): 985-996. doi: 10.3934/matersci.2019.6.985 |
The screw pine and E-glass fibers were hybridized in the vinyl ester resin matrix to prepare the hybrid composite laminates in the present communication. Hybrid composite laminates at the constant volume fraction of 35.12% has been fabricated using the hot press compression molding in two forms, namely dispersed and skin-core, to evaluate the mechanical properties. Mechanical properties of composite laminates were studied based on the various volume fraction of glass fiber content (0, 3.32, 8.15, 12.44 and 16.53 vol.%). The scanning electron microscopy (HITACHI S-3000N) was used to study the fracture surface of composite laminates. The results of hybrid composite laminates were compared with a neat resin sample and screw pine fiber (35.12 vol.%) alone composite. The results revealed that the mechanical properties of both the type of composite laminates increased as glass fiber addition was increased. The SPF18.59/GF16.53 hybrid composite laminate exhibits the highest level of mechanical properties because of the concentration and higher elongation percentage of glass fibers. Moreover, the skin-core type composites perform better than those of the dispersed type hybrid composites. Because of the stretching nature of screw pine fibers, they elongate when the load is transferred from glass fibers to screw pine fibers, resulting in an increase in mechanical properties. The property values were predicted using a theoretical model, and it was found that the two were in good agreement.
Environmentally friendly materials have come into consideration as a result of rising environmental awareness and public interest, new environmental rules and unsustainable petroleum consumption. In comparison to synthetic fibers like glass, carbon and aramid, natural cellulose fiber is one of the more environmentally friendly materials and has greater advantages due to low in weight and cost, renewable and biodegradable, etc. [1,2,3,4]. These composites are used in many different types of practical applications, such as household, structural and automotive parts [5,6,7,8]. However, natural fibers have a number of disadvantages, including processing-related pollution issues [9], increased moisture absorption [10], weaker strength characteristics [11] and poor interfacial bonding with polymer resin [12]. Material researchers have suggested the creation of hybrid fiber-reinforced polymer composites and the modification of both the fibers and the resin matrix in order to address these issues and enhance the properties of polymer composites filled with natural fibers [13,14,15].
Fiber-reinforced hybrid polymer composites are made up of two or more fibers arranged in a matrix system. Hybrid polymer composites are employed in a variety of applications, substituting wood, wood fiber composites and traditional materials. The hybrid fibers reinforced in the composites can withstand larger loads in multiple directions than single-fiber reinforcements, and the surrounding matrix preserves them in their proper orientation, acting as a load transfer medium between the fibers and the polymer [16,17]. Natural fibers can be combined with synthetic fibers, other natural fibers or natural or synthetic particles to generate polymer hybrid composites [18]. To be more competitive with synthetic fiber reinforced composites like glass fiber reinforced polymer composites, natural fiber reinforced polymer composites have lower modulus, lower strength and not as good moisture protection. When natural fibers are mixed with stronger and more corrosion-resistant manufactured fibers like glass fiber, the composite can be made stiffer, stronger and better at resisting water. Using hybrid reinforcement with two or more types of fibers, the advantageous things about one type of fiber could make up for the drawbacks about another. Because of this, the right design of the material could lead to a balance between performance and cost.
Several authors have focused their interest on the preparation and evaluation of performances of hybrid fibers reinforced polymer composites. Characterization of the hybrid oil palm empty fruit bunch/woven kenaf fabric-reinforced epoxy composites was carried out by Hanan et al. [19]. A good interfacial adhesion between the fiber and the matrix is indicated by an improvement in the tensile and flexural properties of the composite material. Palanikumar et al. [20] examined the mechanical properties of sisal and glass fiber-reinforced epoxy hybrid composites. The hybrid composites' tensile, flexural and impact properties improved, while hybridization reduced environmental impact. The results showed that sisal and glass fiber-reinforced eco-friendly hybrid composites can replace pure synthetic fiber-reinforced composites. Xian et al. [21] examined how sustained bending loading, water immersion and fiber hybrid mode affected carbon/glass fiber reinforced polymer composite mechanical properties. The results demonstrated that the random fiber hybrid mode completely develops carbon-glass fiber synergy. Additionally, the carbon/glass fiber/resin interface's discordant bearing behavior and stress concentration were greatly reduced, improving its mechanical properties. The mechanical properties and moisture absorption behavior of coconut coir and glass fiber-reinforced epoxy hybrid composites were investigated by Ashik et al. [22]. According to the results of the study, the inclusion of coconut coir and glass fiber laminate can improve the strength of the epoxy resin and be utilized as an alternate material for glass fiber-reinforced composite material.
The bio-based screw pine fibers are one of the widely accessible fiber resources in the south of India among the many bio-based natural cellulose fibers. Composites will advance as a result of the rational and reasonable usage of screw pine fibers as reinforcing agents. In addition, different forms of hybridization between natural and synthetic fibers can produce fibers with varying degrees of characteristics. Fiber-reinforced polymer composites with better characteristics can aid the development of the materials and engineering sectors. As a result, E-glass fibers are hybridized with screw pine fibers in the current work to manufacture dispersed and skin-core vinyl ester composite materials at 35.12 vol.% utilizing a hot press compression molding technique. The mechanical characteristics of hybrid composites with various amounts of screw pine and glass fiber while sustaining a constant overall fiber content were studied. Screw pine fibers and glass fibers are intimately intermingled in the first type, whereas screw pine fibers are compressed (skin-core) between E-glass fiber mats in the second. The microstructures on the fracture surface of composite specimens after testing were examined using a scanning electron microscope (SEM).
Hand scraping is used to obtain screw pine fibers from fresh screw pine plants, followed by pressing a ceramic plate against the screw pine leaf. Combing supports in the cleaning of the fiber bundles. The fibers are cleaned with running water and sun dried after being extracted. To remove both natural and synthetic contaminants, no chemical treatments are used. E-glass fibers, which are available in non-woven form, are utilized for hybridization. A vinyl ester polymer resin with a density of 1.145 g/cm3 is employed as the resin matrix. GVR Enterprises, Madurai, Tamil Nadu, India, offered all compounds comprising glass fibers. The digital images of used screw pine fibers and E-glass fibers is presented in Figure 1.
To generate dispersion type composites, screw pine and glass fibers are fully combined using a mechanical roller and compressed using a hydraulic compression machine with a weight of 45 t. The mat was then covered with a mixture of vinyl ester resin, catalyst and promoter, and the mold box was completely closed. The mold box was then allowed to cure for 48 h at room temperature.
To create skin-core type composites, glass fiber mats are sandwiched between screw pine fiber mats in the mold. The compressed fiber mats were then covered with a pour of vinyl ester resin that had been mixed with an accelerator, catalyst and promoter and was left to cure for 48 h at room temperature.
Composite specimens were cut in the dimension of 150 × 20 × 3 mm from the prepared composite plates. Mechanical testing was performed on the prepared composite specimens in accordance with American Society for Testing and Materials (ASTM) standards. Tensile tests were performed on composite specimens in accordance with ASTM D638-14 [23] utilizing a computerized universal testing machine with a crosshead speed of 2 mm/min. Flexural tests on the composite specimens were performed using ASTM D790-17 [24] on the same universal testing machine at a crosshead speed of 2 mm/min. Five samples were evaluated in total, and the average results were presented. After the testing, the cracked surfaces of the composite specimens were inspected with a scanning electron microscope (HITACHI S-3000N) at a voltage of 10 kV. Before being used, the composite specimens' surfaces were gold sputtered with an ion sputter apparatus. The methodology of present study is presented in flow chart form as show in Figure 2.
Numerous mechanical characteristics, including strength, toughness, elasticity, yield point, strain energy, resilience and elongation under load, are revealed by a stress-strain graph. The behavior of a material under a load or force is graphically depicted by a stress-strain curve. Stress and strain are the two characteristics that are plotted on the y-axis and x-axis, respectively. Figure 3a illustrates the stress-strain curve of dispersed type composites that are based on various volume fractions of glass and screw fine fiber. It was observed that 18.59SPF/16.53G hybrid composite reaches maximum stress of 58.4 MPa and strain of 3.1%. It was much higher than the other composite sample's stress and strain values. It may be owing to the concentration and higher elongation percentage of glass fibers. The slope of the graph steadily rose as a result of the relatively higher elongation of the glass fibers. As can be seen in Figure 3a, none of the curves deviated much from a straight line. This is something that can be determined by looking at the percentage of elongation at break that screw pine and glass fibers have when they are used in composite materials. Figure 3b depicts the range of values for the percentage of elongation that can be achieved by hybrid composites. The amount of glass fiber in composite materials has a direct correlation with the percentage of elongation that can be achieved by those materials [25]. It illustrates that an increase in the percentage of glass fiber in hybrid composites results in an increase in the failure strain of the hybrid composite.
The stress-strain curve of skin-core type composite laminates is depicted in Figure 4a. This curve is shown for a variety of screw pine and glass fiber volume ratios. At low strain, each of the curves followed a linear pattern; however, when the strain or load increased, the patterns diverged. Because the glass fibers share the load during the first load, the curves are linear when the strain is relatively modest. This is the most likely explanation for the phenomenon. When the strain of the hybrid composites reaches the failure strain of the screw pine fiber, the trends begin to shift. The stress versus strain graph for the 18.59SPF/16.53G composite specimen is practically linear compared with the other composite specimens. With a strain of 4.8%, the extreme obtained stress was 75.8 MPa. The glass fibers in this composite were strong to transmit the applied loads. Due to its stretching nature, screw pine fibers elongate when the load is transferred from glass fibers to them, resulting in an increase in slope. Figure 4b depicts the percentage of elongation variation that is associated with the hybrid skin-core composites. The percentage of elongation is proportionally increased along with the amount of glass fiber that is present. The percentages of elongation achieved by skin-core hybrid composites were significantly greater than those achieved by dispersed hybrid composites.
In the comparison of Figures 3 and 4, it was clearly identified that the level of attained stress and elongation of skin-core type composites is increased when compared to the dispersed type composites. Therefore, it was observed that the skin-core type composites may be perform better than the dispersed type composites.
Figure 5a illustrates the hybrid effect that screw pine and glass fiber composites have on the tensile strength of the material. It is clear that the addition of 3.32% volume of glass fiber results in a modest decrease in tensile strength, which is followed by a constant increase in tensile strength values as more glass fibers are added. It is possible that the initial addition of glass fibers at a volume fraction of 3.32% is not contributing to the increase in tensile characteristics because the amount added is insufficient. The tensile strength of the composite with the composition 26.97SPF/8.15GF is 49.1 MPa, which is 102% higher than the sample with the neat resin. Tensile strength is increased by 50.2% as compared to 31.80SPF/3.325GF, which is the previous standard. In addition to this, when contrasted with the sample of neat resin, the 21.68SPF/13.44GF composite demonstrates an improvement of 118.9%.
The composite with the value of 18.59SPF/16.53GF was found to have the highest value. This value is 140.3% greater than the value of the clean resin sample and it is 39% higher than the value of the 35.12SPF composite. Figure 5b illustrates the change in tensile modulus that can be expected from hybrid composites. The modulus values gradually increased as more glass fibers were included into the material. The initial addition of glass fibers (31.80SPF/3.32GF) resulted in a tensile modulus of 1950 MPa, which is 112.5% higher than the tensile modulus of the sample consisting of clean resin. The value of modulus that was obtained with a composite of 18.59SPF/16.53GF was 99.75% higher than the value that was obtained with a composite of 35.12SPF. This means that the maximum modulus value was obtained with this composite.
During the testing of the hybrid composite material, the presence of glass fibers assisted screw pine fibers in reducing crack growth in the material. As a direct consequence of this, the fracture became confined to a limited area and virtually assumed a horizontal orientation, as can be seen in Figure 5c. On the fracture surface of 18.59SPF/16.53GF composites, screw pine fiber failure, fiber-matrix de-bonding and glass fiber pullout are depicted in Figure 5c. It also depicts the dispersion of fibers in the dispersed type composite's poor bonding performance. As a consequence, composites' mechanical properties were decreased.
The hybrid effect of screw fine and glass fiber composites on hybrid composite tensile properties (skin-core type) is depicted in Figure 6a. The addition of glass fiber to skin-core hybrid composites increases their tensile strength. The inclusion of glass fibers at a volume of 3.32% and screw-pine fibers at a percentage of 31.80% results in an improvement of 104% over the sample of neat resin. When compared to the sample made from neat resin, the 21.68SPF/13.44G composite demonstrates an increase in tensile strength of 186%, measuring at 69.5MPa. In comparison to the neat resin sample and the 35.12SPF composite, the maximum tensile strength of the 18.59SPF/16.53G composite is 211.9% and 80.5% higher, respectively. It is clear from investigating the results that the tensile strength of skin-core hybrid composites is significantly higher than that of dispersed hybrid composites.
The variation in the tensile modulus of the hybrid composite for varying volume ratios of screw pine and glass fibers is shown in Figure 6b. The tensile modulus increases as the percentage of glass fiber increases. Skin-core hybrid composites have higher modulus values than dispersed hybrid composites. When the strain approached the screw pine fiber breakdown strain, the inner core of the skin-core hybrid composite initially cracked, causing the matrix to disintegrate and the glass fiber skin to delaminate [26]. A clear fiber and matrix fracture at the inner core of the screw pine results in a significant zone of delamination between the skin and the core fibers (Figure 6c). There is a limited indication of failure of glass fiber. Figure 6c also represents the fractured surface of the skin-core type composite and exhibits improved interfacial adhesion between the glass (high cohesion) and screw pine fibers.
Figure 7 displays comparison of the tensile strength values of dispersed and skin-core composites. It was observed that the skin-core composites clearly demonstrated the highest value when compared to dispersed type composites. This could be a result of the interfacial adhesion between the fibers and the matrix. The skin-core composite had the highest tensile strength at 18.59SPF/16.53G.
The strength of hybrid vinyl ester composites reinforced with screw pine and glass fibers is determined by the adhesion strength of these fibers to the matrix. In dispersed hybrid composites, when screw pine and glass fibers are combined, they form a large contact area, which reduces the bonding strength between the two materials. Because screw pine fibers are sandwiched between glass fiber sheets in skin-core hybrid composites, the contact area between screw pine and glass fibers is smaller than in dispersed hybrid composites. The strength of skin-core hybrid composites is greater than that of dispersed hybrid composites because of the high bonding strength between screw pine and glass fibers.
The flexural strength variation in dispersed hybrid composites can be observed in Figure 8a. The flexural strength values have continuously increased with the inclusion of glass fiber, as seen in Figure 8a. The flexural strength of the neat resin sample is 30.4 MPa, and the addition of 35.12 vol.% screw pine fibers improve that strength by 40.4% to 57.3 MPa. The first addition of 3.32% glass fibers improves the composite's flexural strength. The composite material with the highest flexural strength value was 18.59SPF/16.53GF. The flexural modulus variations of dispersed hybrid composites are seen in Figure 8b. The flexural modulus of vinyl ester composite increased increasing screw pine and glass fiber content, as shown in Figure 8b. The flexural modulus of the 35.12SPF compo-site is 2812 MPa, which is 153.8% greater than the neat resin sample.
The maximum modulus value of the 18.59SPF/16.53G composite is 337.3% higher than that of the neat resin sample and 72.3% greater than the 35.12SPF composite. The improvement of the composite 21.68SPF/13.44G over the composite 35.12SPF was 60.8%. Gradually, the addition of glass fibers increased the increase in flexural modulus values. This development indicates that glass fibers contributed to the enhancement of flexural modulus values [27]. Figure 8c depicts the fractured surface of the 18.59SPF/16.53G dispersed composite after flexural testing. The composite specimen's void and discontinuity were revealed to be the result of matrix failure. It was evidently indicative of fiber damage. A type of failure has been identified as brittle behavior.
Figure 9a, b depict variations in the flexural strength and modulus of skin-core hybrid composites. The flexural strength and modulus values continuously increase with increasing glass fiber content. 18.59SPF/16.53G was the composite with the maximum flexural modulus value. There was a 98.7% improvement in comparison to the 35.12 SPF composite. The 31.80SPF/3.32G composite had a flexural strength of 61.9 MPa, which was 8.6% greater than the 35.12SPF composite. However, it is 103.6% higher than the sample of the pure resin sample. The addition of 16.53% glass fiber enhances the flexural strength of vinyl ester composites by 235%. The addition of 3.32 % glass fiber and 31.80% screw pine fiber increases the flexural strength of dispersed hybrid composites by 40.4% and skin-core hybrid composites by 103.6%. Clearly, the fiber arrangements and distribution have a greater impact on the flexural properties of composites [28]. Figure 9c depicts the fractured surface of a skin-core composite material. It was discovered that improved fiber-to-matrix bonding with minimal fiber dislocation enhances the flexural properties of skin-core composites over dispersed-type composites.
Comparison of flexural strength values of dispersed and skin-core composites is presented in Figure 10. From the Figure 10, it was clearly seen that when compared to dispersed-type composites, the highest flexural strength values were obtained in the skin-core composites. It may be owing to better bonding strength between the reinforcement and resin matrix. The skin-core composite at 18.59SPF/16.53G had the highest flexural strength.
The mechanical properties of fiber-reinforced polymer composites can be predicted theoretically and compared to experimental results using a variety of models. The key advantage of this model is the low-cost and time-intensive experimentation. In terms of properties, the skin-core type composite outperforms the dispersed type composite. In the present investigation, the Hirsch model was utilized to predict the tensile strength of skin-core composites. The Hirsch model is stated as Eq 1 [29]:
σc=x(σmVm+σfVf)+(1−x)(σfVm)(σmVf+σfVm) | (1) |
where the f, m and c are the characteristic strength property of fiber, matrix and composite, respectively. Vm and Vf is the volume fraction of the matrix and the fiber, respectively. The parameter 'x' varies between 0 and 1, determining how much-applied applied load is transferred between the reinforcement and the matrix. The type of fiber, matrix and fiber-matrix interaction all influence the value of 'x'. The value of 'x' is fixed at 0.961 for this study, which corresponds to the experimental results. As illustrated in Figure 11, the tensile strength of the hybrid composites increased as the volume % of screw fine and glass fibers increased. It was also demonstrated that the model is predicted the tensile strength of 26.97SPF/8.15G and 21.68SPF/13.44G composites with less deviation compared to the 31.80SPF/3.32G and 18.59SPF/16.53G composites. However, the developed Hirsch model is reasonably accurate in predicting the tensile strength of the screw pine and glass fiber-reinforced vinyl ester hybrid composites and gives good agreement with experimental results. As a result, the Hirsch model may predict the tensile strength of screw pine and glass fiber-reinforced vinyl ester hybrid composites.
● The current state of literature indicates that natural fiber composites exhibit comparatively inferior behavior compared to synthetic fiber composites. However, hybridization improves mechanical behavior, as demonstrated by this study.
● Screw pine and glass fiber reinforced vinyl ester hybrid composites in dispersed and skin-core forms were developed and evaluated for tensile and flexural properties at different fiber contents.
● The incorporation of glass fibers into both hybrid composites enhances their mechanical properties by merging the advantageous features of screw pine fibers and the superior mechanical performance of glass fibers.
● The presence of higher glass fiber content in dispersed-type hybrid composites resulted in improved properties compared to composites with 3.32 vol.% glass fibers. This can be attributed to the inability of lower glass fiber content dispersion to contribute to stress transfer.
● Because of the hybridization of glass fibers as core material, mechanical properties increased with glass fiber content in the skin-core type, demonstrating their contribution to the enhancement of composite properties.
● The hybrid effect demonstrated that irrespective of the type of composite, the highest mechanical properties were attained with 18.59SPF/16.53G fiber composites.
● The mechanical properties of dispersed composites are lower than skin-core composites. The strength of the composites is enhanced as a result of the core's ability to distribute the applied load from one skin to another via the matrix, thereby facilitating the desired stress transfer.
● SEM study showed fiber-matrix de-bonding, fiber breakage and fiber delamination on the composite's fractured surface. Hirsch model may predict composite tensile strength. The theoretical and experimental values agreed.
The authors declare that they have not used Artificial Intelligence (AI) tools in the creation of this article.
The authors declare no conflict of interest.
[1] |
Athijayamani A, Thiruchitrambalam M, Natarajan U, et al. (2010) Influence of alkali-treated fibers on the mechanical properties and machinability of roselle and sisal fiber hybrid polyester composite. Polym Compos 31: 723–731. http://dx.doi.org/10.1002/pc.20853 doi: 10.1002/pc.20853
![]() |
[2] |
Thakur VK, Thakur MK, Gupta RK (2014) Review: Raw natural fiber–based polymer composites. Int J Polym Anal Ch 19: 256–271. http://dx.doi.org/10.1080/1023666X.2014.880016 doi: 10.1080/1023666X.2014.880016
![]() |
[3] |
Omrani E, Menezes PL, Rohatgi PK (2016) State of the art on tribological behavior of polymer matrix composites reinforced with natural fibers in the green materials world. Eng Sci Technol 19: 717–736. https://doi.org/10.1016/j.jestch.2015.10.007 doi: 10.1016/j.jestch.2015.10.007
![]() |
[4] |
Venkatarajan S, Subbu C, Athijayamani A, et al. (2022) Effects of fiber content and its chemical treatment on the mechanical properties of screw pine fiber reinforced vinyl ester composite. Mater Res Express 9: 1–10. https://doi.org/10.1088/2053-1591/ac7b16 doi: 10.1088/2053-1591/ac7b16
![]() |
[5] |
Gerald Arul Selvan M, Athijayamani A (2016) Mechanical properties of fragrant screwpine fiber reinforced unsaturated polyester composite: Effect of fiber length, fiber treatment and water absorption. Fibers Polym 17: 104–116. http://dx.doi.org/10.1007/s12221-016-5593-x doi: 10.1007/s12221-016-5593-x
![]() |
[6] |
Ahmad F, Choi HS, Park MK (2015) A review: Natural fiber composites selection in view of mechanical, light weight, and economic properties. Macromol Mater Eng 300:10–24. https://doi.org/10.1002/mame.201400089 doi: 10.1002/mame.201400089
![]() |
[7] |
Khalid MY, Al Rashid A, Arif ZU, et al. (2021) Recent advances in nanocellulose-based different biomaterials: Types, properties, and emerging applications. J Mater Res Technol 14: 2601–2623. https://doi.org/10.1016/j.jmrt.2021.07.128 doi: 10.1016/j.jmrt.2021.07.128
![]() |
[8] |
Venkatarajan S, Subbu C, Athijayamani A (2023) Evaluation of shear property of screw pine fiber/glass fiber reinforced vinyl ester hybrid composites. Mater Lett 332: 133538. https://doi.org/10.1016/j.matlet.2022.133538 doi: 10.1016/j.matlet.2022.133538
![]() |
[9] |
Balla VK, Kate KH, Satyavolu J, et al. (2019) Additive manufacturing of natural fiber reinforced polymer composites: Processing and prospects. Compos Part B-Eng 174: 106956. https://doi.org/10.1016/j.compositesb.2019.106956 doi: 10.1016/j.compositesb.2019.106956
![]() |
[10] |
Adhikari J, Biswas B, Chabri S, et al. (2017) Effect of functionalized metal oxides addition on the mechanical, thermal and swelling behaviour of polyester/jute composites. Eng Sci Technol 20: 760–774. https://doi.org/10.1016/j.jestch.2016.10.016 doi: 10.1016/j.jestch.2016.10.016
![]() |
[11] |
Sinha AK, Narang HK, Bhattacharya S (2017) Mechanical properties of natural fibre polymer composites. J Polym Eng 37: 879–895. https://doi.org/10.1515/polyeng-2016–0362 doi: 10.1515/polyeng-2016–0362
![]() |
[12] |
Mohammed MM, Rasidi M, Mohammed AM, et al. (2022) Interfacial bonding mechanisms of natural fibre-matrix composites: An overview. BioResources 17: 7031–7090. https://doi.org/10.15376/biores.17.4.Mohammed doi: 10.15376/biores.17.4.Mohammed
![]() |
[13] |
Sathishkumar TP, Naveen J, Satheeshkumar S (2014) Hybrid fiber reinforced polymer composites—A review. J Reinf Plast Comp 33: 454–471. https://doi.org/10.1177/0731684413516393 doi: 10.1177/0731684413516393
![]() |
[14] |
Cruz J, Fangueiro R (2016) Surface modification of natural fibers: A review. Procedia Eng 155: 285–288. http://dx.doi.org/10.1016/j.proeng.2016.08.030 doi: 10.1016/j.proeng.2016.08.030
![]() |
[15] |
Pankaj, Jawalkar C, Kant S (2023) Study on mechanical properties and delamination factor evaluation of chemically treated nettle fiber reinforced polymer composites. J Nat Fibers 20: 373–390. https://doi.org/10.1080/15440478.2022.2135053 doi: 10.1080/15440478.2022.2135053
![]() |
[16] |
Jawaid M, Abdul khalil HPS, Azman Hassan, et al. (2012) Effect of jute fibre loading on tensile and dynamic mechanical properties of oil palm epoxy composites. Compos Part B-Eng 45: 619–624. https://doi.org/10.1016/j.compositesb.2012.04.068 doi: 10.1016/j.compositesb.2012.04.068
![]() |
[17] | Pani D, Mishra P (2019) Study of mechanical properties of natural fiber reinforced hybrid polymer composites. Int J Adv Mech Eng 9: 1–6. |
[18] |
Mansor MR, Sapuan S, Zainudin ES, et al. (2013) Hybrid natural and glass fibers reinforced polymer composites material selection using analytical hierarchy process for automotive brake lever design. Mater Design 51: 484–492. http://dx.doi.org/10.1016/j.matdes.2013.04.072 doi: 10.1016/j.matdes.2013.04.072
![]() |
[19] |
Hanan F, Jawaid M, Paridah MT, et al. (2020) Characterization of hybrid oil palm empty fruit bunch/woven kenaf fabric-reinforced epoxy composites. Polymers 12: 2052. https://doi.org/10.3390/polym12092052 doi: 10.3390/polym12092052
![]() |
[20] |
Palanikumar K, Ramesh M, Hemachandra Reddy K (2016) Experimental investigation on the mechanical properties of green hybrid sisal and glass fiber reinforced polymer composites. J Nat Fibers 13: 321–331. https://doi.org/10.1080/15440478.2015.1029192 doi: 10.1080/15440478.2015.1029192
![]() |
[21] |
Xian G, Guo R, Li C (2022) Combined effects of sustained bending loading, water immersion and fiber hybrid mode on the mechanical properties of carbon/glass fiber reinforced polymer composite. Compos Struct 281:115060. https://doi.org/10.1016/j.compstruct.2021.115060 doi: 10.1016/j.compstruct.2021.115060
![]() |
[22] |
Ashik KP, Sharma RS, Jagannatha Guptha VL (2018) Investigation of moisture absorption and mechanical properties of natural/glass fiber reinforced polymer hybrid composites. Mater Today Proc 5: 3000–3007. https://doi.org/10.1016/j.matpr.2018.01.099 doi: 10.1016/j.matpr.2018.01.099
![]() |
[23] | ASTM D (2014) Standard test method for tensile properties of plastics. Annual Book of ASTM Standards 1–17. |
[24] | ASTM D (2017) Standard test methods for flexural properties of un-reinforced and reinforced plastics and electrical insulating materials 1. Annual Book of ASTM Standards 1–12. |
[25] |
Thomason JL (2008) The influence of fibre length, diameter and concentration on the strength and strain to failure of glass fibre-reinforced polyamide 6, 6. Compos Part A Appl Sci Manuf 39: 1618–1624. http://dx.doi.org/10.1016/j.compositesa.2008.07.002 doi: 10.1016/j.compositesa.2008.07.002
![]() |
[26] |
Ahmed H, Tamer H, Zeki C, et al. (2016) Developing high-performance hybrid green composites. Compos Part B-Eng 92: 384–394. https://doi.org/10.1016/j.compositesb.2016.02.051 doi: 10.1016/j.compositesb.2016.02.051
![]() |
[27] | Yu W, Xue H, Qian M (2017) Tensile and compressive properties of epoxy syntactic foams reinforced by short glass fiber. Indian J Eng Mater Sci 24: 283–289. http://nopr.niscpr.res.in/handle/123456789/43159 |
[28] |
Ary Subagia IDG, Kim FY, Tijing LD, et al. (2014) Effect of stacking sequence on the flexural properties of hybrid composites reinforced with carbon and basalt fibers. Compos Part B-Eng 58: 251–258. https://doi.org/10.1016/j.compositesb.2013.10.027 doi: 10.1016/j.compositesb.2013.10.027
![]() |
[29] |
Kalaprasad G, Joseph K, Thomas S, et al. (1997) Theoretical modelling of tensile properties of short sisal fibre-reinforced low-density polyethylene composites. J Mater Sci 32: 4261–4267. https://doi.org/10.1023/A:1018651218515 doi: 10.1023/A:1018651218515
![]() |
1. | Syed Mansoor Ahmad, M. C. Gowrishankar, Manjunath Shettar, Effect of boiling water soaking on the mechanical properties and durability of nanoclay-enhanced bamboo and glass fiber epoxy composites, 2025, 15, 2045-2322, 10.1038/s41598-025-87912-w |