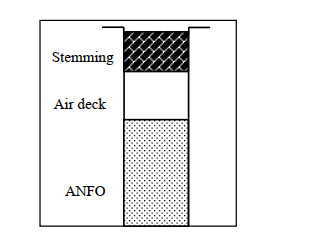
The blasting operation is an integral part of mines, and it is still being used as the most economical tool to fragment and displace rock mass. Appropriate blast optimization alleviates undesirable side effects, such as ground vibration, air blasts and flyrock, and it and enhances rock fragmentation. Blast optimization can also be effective in reducing the overall mining cost. One way of reducing blasting side effects is to use deck charges instead of continuous ones. The location of the deck(s) is still considered an unanswered question for many researchers. In this study, an investigation was carried out to find an appropriate air deck position(s) within the blast hole. For this, air decks were placed at three different positions (top, middle and bottom) within a blast hole at Cheshmeh-Parvar gypsum and Chah-Gaz iron ore mines to understand and evaluate air deck location impact on blast fragmentation and blast nuisances. The results were compared based on the existing blasting practices at both mines, as well as the air-deck blasting results. The results obtained from the blasting were very satisfactory; it was found that charging with a top air deck, as compared to current blasting practices, causes a decrement in the specific charge, as well as a decrement of 38% in the back break and 50% in flyrock; the average size of fragments obtained from blasting was increased by 26%. Thus, it can be said that the top air deck is more advantageous than the bottom air deck in terms of reducing undesired blasting consequences.
Citation: Masoud Monjezi, Hamed Amiri, Mir Naser Seyed Mousavi, Jafar Khademi Hamidi, Manoj Khandelwal. Comparison and application of top and bottom air decks to improve blasting operations[J]. AIMS Geosciences, 2023, 9(1): 16-33. doi: 10.3934/geosci.2023002
[1] | Mohammad Mirzehi Kalateh Kazemi, Zohreh Nabavi, Manoj Khandelwal . Prediction of blast-induced air overpressure using a hybrid machine learning model and gene expression programming (GEP): A case study from an iron ore mine. AIMS Geosciences, 2023, 9(2): 357-381. doi: 10.3934/geosci.2023019 |
[2] | Elvis Ishimwe, Richard A. Coffman, Kyle M. Rollins . Predicting blast-induced liquefaction within the New Madrid Seismic Zone. AIMS Geosciences, 2020, 6(1): 71-91. doi: 10.3934/geosci.2020006 |
[3] | Andre Vervoort . Impact of the closure of a coal district on the environmental issue of long-term surface movements. AIMS Geosciences, 2022, 8(3): 326-345. doi: 10.3934/geosci.2022019 |
[4] | Alessia Nannoni, Federica Meloni, Marco Benvenuti, Jacopo Cabassi, Francesco Ciani, Pilario Costagliola, Silvia Fornasaro, Pierfranco Lattanzi, Marta Lazzaroni, Barbara Nisi, Guia Morelli, Valentina Rimondi, Orlando Vaselli . Environmental impact of past Hg mining activities in the Monte Amiata district, Italy: A summary of recent studies. AIMS Geosciences, 2022, 8(4): 525-551. doi: 10.3934/geosci.2022029 |
[5] | Gustavo E. Ratto, Fabián Videla, Jorge Reyna Almandos, Ricardo Maronna . Air quality at La Plata Conglomerate, Argentina: Review and prospective study to improve the present situation. AIMS Geosciences, 2018, 4(1): 88-125. doi: 10.3934/geosci.2018.1.88 |
[6] | Jolanta Kwiatkowska-Malina, Andrzej Szymon Borkowski . Geostatistical modelling of soil contamination with arsenic, cadmium, lead, and nickel: the Silesian voivodeship, Poland case study. AIMS Geosciences, 2020, 6(2): 135-148. doi: 10.3934/geosci.2020009 |
[7] | Dina Gubanova, Otto Chkhetiani, Anna Vinogradova, Andrey Skorokhod, Mikhail Iordanskii . Atmospheric transport of dust aerosol from arid zones to the Moscow region during fall 2020. AIMS Geosciences, 2022, 8(2): 277-302. doi: 10.3934/geosci.2022017 |
[8] | Diaka Sidibé, Mamadou Diallo, Ahmed Amara Konaté, Muhammad Zaheer . Geotechnical investigations of lead-silver ore processing residues at the Auzelles site, Auvergne (France). AIMS Geosciences, 2024, 10(4): 735-758. doi: 10.3934/geosci.2024036 |
[9] | Mario Batubara, Masa-yuki Yamamoto, Islam Hosni Hemdan Eldedsouki Hamama, Musthofa Lathif, Ibnu Fathrio . Measurement and characterization of infrasound waves from the March 25, 2023 thunderstorm at the near equatorial. AIMS Geosciences, 2023, 9(4): 652-671. doi: 10.3934/geosci.2023035 |
[10] | Brian E. Bunker, Jason A. Tullis, Jackson D. Cothren, Jesse Casana, Mohamed H. Aly . Object-based Dimensionality Reduction in Land Surface Phenology Classification. AIMS Geosciences, 2016, 2(4): 302-328. doi: 10.3934/geosci.2016.4.302 |
The blasting operation is an integral part of mines, and it is still being used as the most economical tool to fragment and displace rock mass. Appropriate blast optimization alleviates undesirable side effects, such as ground vibration, air blasts and flyrock, and it and enhances rock fragmentation. Blast optimization can also be effective in reducing the overall mining cost. One way of reducing blasting side effects is to use deck charges instead of continuous ones. The location of the deck(s) is still considered an unanswered question for many researchers. In this study, an investigation was carried out to find an appropriate air deck position(s) within the blast hole. For this, air decks were placed at three different positions (top, middle and bottom) within a blast hole at Cheshmeh-Parvar gypsum and Chah-Gaz iron ore mines to understand and evaluate air deck location impact on blast fragmentation and blast nuisances. The results were compared based on the existing blasting practices at both mines, as well as the air-deck blasting results. The results obtained from the blasting were very satisfactory; it was found that charging with a top air deck, as compared to current blasting practices, causes a decrement in the specific charge, as well as a decrement of 38% in the back break and 50% in flyrock; the average size of fragments obtained from blasting was increased by 26%. Thus, it can be said that the top air deck is more advantageous than the bottom air deck in terms of reducing undesired blasting consequences.
A huge amount of energy is generated by the explosive detonation in a blast hole, using high temperature and pressure to fragment and displace the rock mass. Studies have shown that only a part of this energy is used for the genuine fragmentation and displacement of the rock mass; the rest is transferred to the surroundings and creates a number of undesirable blast nuisances, i.e., blast vibration, back break, air blasts, flyrock, noise, etc. [1,2,3,4,5]. Controlling and reducing the blast induces side effects that will result in two general outcomes: reducing the damage to the remaining rock and consuming a larger fraction of blast energy to fragment the rock mass. Most of the surface mines face such types of blasting problems. Therefore, there is a need for action to minimize and control the blast undesired events without neglecting safety and stability. It is also required to minimize improper fragmentation, which is mostly the main objective of the blasting operation. Moreover, the production blasting costs should be kept in mind to ensure the feasibility of the operation. Normally, the controllable blast design parameters are optimized to minimize the explosive cost. Air decking, a branch of deck charging, is currently being implemented for better utilization of explosive energy. This technique has been used in many open-pit mines to decrease explosive consumption while maintaining the required fragmentation [6,7,8,9,10,11,12,13,14,15,16,17,18]. With this technique, one or two air gaps are fabricated in the charge column. In this way, explosive energy will effectively be transferred to the rock mass, causing more uniform rock fragments. It also lessens excessive crushing in the close vicinity of the charge. Air-deck blasting was first successfully practiced in 1893 [11]. The main advantage of air decking is to produce dynamic oscillations of strain waves, which are influential in better rock fragmentation. The various merits of air decking have garnered attention from researchers who want to employ it to diminish the blasting of unwanted and hazardous events, i.e., ground vibration, air blasts, toe-related problems, flyrock [4,8,9,10]. Air decks have been used in blasting operations to improve fragmentation by amplifying the induced fracturing, which has a significant economic effect on subsequent size reduction processes [16,17,18,19,20,21,22,23].
Hayat and Tariq [24] attempted to convince the mining industry of Pakistan to utilize air deck charging, but they failed due to some unjustified decisions in their research. In another study performed by Saqib et al., two different series of blasting experiments were practiced on concrete blocks, one for determining the proper position of the air gaps, and the other for finding out the suitable length of the air deck [13]. The position of the charge within the blast hole plays an important role in achieving optimal blasting results and reducing blast damage [25]. Shin et al. successfully used multiple deck blasts with electronic detonators to decrease vibration level, improve construction performance and reduce construction time in a shaft sinking project [15]. Zhang et al. experimentally studied the effects of the structures of decoupled charges and filler materials on the blasting results in physical models. They concluded that the decoupling coefficient and type and nature of the filling medium are enormously influential in the blasting outcomes [17]. Zuo et al. investigated the blast-induced fracture characteristics for iron ore samples by using a deck charging technique. They found that an optimal decoupling coefficient range should be implemented for two reasons, i.e., to prevent the creation of unwanted transgranular fractures at the crack surface and excessive fragmentation. The former corresponds to small decoupling coefficients, while the latter is related to very large decoupling coefficients [20]. Jang et al. studied the effects of a water deck on rock blasting. It is well-known fact that the presence of water in blast holes can be hazardous when performing blasting operations. However, they tried to isolate the water at the hole bottom and separated it from the explosive column. In this way, they altered the harmful effect of water into a beneficial one [18]. In another research study, Yin et al. found that adding air deck in the middle of a blast hole yields better efficiency. They also concluded that the application of deck charging equalizes the gas pressure throughout the hole length and increases the time for the rock to be fragmented [21]. A technique for smooth blasting was introduced by Ma et al. for the purpose of excavating a tunnel in a competent rock [22]. With this technique, using a critical distance strategy, the distribution of explosives in the conventional deck charging system was changed, resulting in production cost reduction, operation process simplification, production efficiency improvement, etc. Zhang et al., utilized deck charging in an open-pit mine to reduce blast complaints in the nearby residential area [19]. They expressed that applying this method is completely justified from technical and economic points of view. Sazid and Singh explained the air-deck blasting mechanism, emphasizing numerical modeling employment for a better understanding of the technique [23].
When detonation is carried out with a continuous charge in a blast hole, the initial detonation pressure is many times greater than the strength of the rock. Due to the propagation of a strong shock wave through the surrounding rock, excessive crushing is near the blast hole. Surface mine depths are increasing day by day. Some of the mines are operating at a very marginal profit due to the exhaustion of high-grade minerals. Effective and efficient explosive energy utilization is very crucial to make such mines profitable without affecting rock fragmentation. So, it is crucial to decrease the blast hole explosive charge and replace it with decking.
To diminish the environmental impacts and sustain the required fragment sizes, air-deck blasting has been applied for the past few decades. Air decking is nothing but creating an empty space in a blast hole. The location of the air deck could be at the bottom, middle or top of the charge column. Depending on the surrounding rock conditions, a solid or water deck may also be positioned in a blast hole to decrease the explosive charge. Sometimes, a part of the charge is left without any solid or liquid substance and only air decking is used. Though a number of studies have been carried out by various researchers related to air decking, its location impacts on rock fragmentation and blast nuisances have not been studied in detail.
Therefore, in this study, an attempt was made to study the viability of an air deck in blasting operations to find its appropriate location within a blast hole and thus minimize the blast nuisances and enhance the fragmentation.
An air deck encompasses the use of one or more airborne gaps within a column charge to optimize fragmentation and reduce specific charges and blast nuisances. The application of this technique has led to revolutionary changes in the field of blasting. The benefits of this technique have a long history, originating in 1891. Jimeno [26] mentioned that Saunders was the first to invent this technique in Germany in 1891.
Figure 1 shows a schematic diagram of a blast hole and the air deck position at the top of the hole [27].
A number of researchers have done extensive research on air decking applications in their experiments. Melnikov and Marchenko concluded in their experiments that the use of an air deck reduced the explosive charge by 10 to 30%, and fragmentation was also improved [28]. Bussey and Borg used an air deck in a pre-flash bombing; it reduced stamp costs by 25% and blast costs by 50% [29]. Rowlands concluded that the use of an air deck would save 15 to 20% in terms of explosive quantity, without compromising the blast results [6]. Mead et al. used an air deck in their experiments to reduce explosives by 15 to 35%; they achieved better results without any adverse side effects [7]. Jhanwar et al. conducted experiments using air decking and found that this method improved fragmentation and reduced the explosive column charge by 10 to 35%. They concluded that the use of air decking would control flyrock and back breaking [8].
Chiappetta has claimed that, by creating an air deck inside the column charge, the amount of extra drilling can be reduced or eliminated, 33% of the ground vibration and 16 to 25% of the explosive consumption can be reduced and fragmentation can be increased by 25% [27].
Melnikov was the first to describe the blasting mechanism in an air-to-air manner and stated that the available free space would re-expand the explosive energy within the hole [26,28]. Melnikov assumed that the existing air deck acts as a reflection of the waves inside the blast hole [9,28].
Melnikov's assumption can be expressed more precisely, that is, when the detonation of an explosive charge takes place within a blast hole, compression waves generate. When this compressional wave encounters a discontinuity or a common interface between two different materials (both stone, or one stone and the other air), part of the compressional wave energy is reflected (ER) and partly transmitted to the next material (ET) [26,28].
The type of waves reflected or transmitted to another medium is largely dependent on the impedance of the materials in the two environments (Eq 1). The rock impedance shows the reflection and refractive index of the waves in different materials; it also expresses the energy transferability of the rock in mathematical form. The reflected energy (Eq 2) and the dispersed energy (Eq 3) at the interface of two different materials are as follows [30].
Ie=De∗Ve | (1) |
ηR=(I2−I1)2(I2+I1)2 | (2) |
ηT=1−(I2−I1)2(I2+I1)2 | (3) |
where
Ie : Impedance of the environment (kg/m2·s)
De : Density of the environment (kg/m3)
Ve : Rock wave velocity (m/s)
ηR : Energy factor reflected from the interface of two substances
ηT : Energy coefficient for passing through the interface of two materials
I1 : Impedance of the first environment (kg/m3·s)
I2 : Impedance of the second environment (kg/m3·s)
The term (I2 − I1) specifies the type of reflected wave. If (I2 − I1) is negative, it is a type of tensile wave; otherwise it is compressive. If I2 > I1, some of the energy is reflected and some of the interconnected interfaces pass through the environment, and both are of a type of compression. If I2 = I1, all energy will be pressurized into the second medium and there will be no reflection of energy. If I2 < I1, some energy passes through the tensile force and part of the tensile energy. The most severe condition is I1 / I2 = ∞; in which case, all of the compressional waves are returned to the tidal range after a collision with the second medium [26]. This model is the same as that for an air deck because the air density is zero and, thus, the air impedance (I2) is zero. The available space reduces the initial pressure of the hole and instead allows pressure waves to last longer on the rock. This method reduces the energy loss of the explosive during the extraction of stones while also transferring the remaining energy to break the rock [30].
In other experiments conducted by Melnikov et al, the average velocity of the waves was caused by the detonation of a continuous charge (Figure 2) and there was a cost associated with air breakdown (Figure 3). By observing the following images, it can be seen that the continuous load, i.e., the load pressure applied in one step when using the spacing in the charge column, generates secondary pulses to stimulate the expansion of the gases within the blast hole [10].
The air decking position is another important issue on which researchers do not have a strong consensus, and different researchers suggest a different location based on their experience [29]. In general, aerial decking can be positioned at three different points from the top:
1. Bottom of the charge column and above the ground (Figure 4a);
2. Middle of the charge column (Figure 4b);
3. The exercise above the column charge and below the stemming (Figure 4c) [29].
Mead et al. concluded that the air deck between the charge and the higher or lower types had a greater effect on fragmentation (Figure 5) [7].
Saqib et al. carried out a number of explosive tests on concrete blocks and simulated real-life detonation conditions on a small scale. He concluded that the insertion of an air deck in the middle of the charge generates smaller rock fragments, and that the insertion of an air deck nearby to the stemming or ground produces coarse fragments (Figure 6) [13].
Lu and Hustrulid mentioned that it would be more beneficial to place the air deck on top of the charge column because, in this case, the explosive energy will be able to expand into the air deck created above the column and exert condensed but prolonged stress in the collar zone of the blast hole [14].
In this study, air-deck blasts were carried out at two different open-pit mines, i.e., Cheshmeh-Parvar Gypsum mine and Chah-Gaz iron ore mine. The first mine is located in the east of Tehran, whereas the second mine is situated in central Iran in the Bafgh-Saghand formation.
The two studied mines are exposed in the metasomatite metamorphic rock belt from the intrusive mass; it is a combination of diorite, andesite and porphyry basalt. The outcrop of sedimentary-volcanic rocks attributed to Infra-Cambrian has provided suitable conditions for the formation of mineral reserves in the area. In addition, severe crushing and the presence of voids in the sedimentary-volcanic host rock facilitate the transport and migration of ore fluids; these are the main factors in the formation of reserves.
The purpose of the test blasting in these mines was to investigate the effects of air decking and its location on the blast results. For this purpose, eight different blasts were conducted in the first mine, and a single try was considered for the second mine. In Case 1, two blasts were performed conventionally (i.e., without insertion of an air deck inside the column charge), and in three cases, air decking was used at the top of the charge; the remaining three blasts were done with air decking at the bottom of the charge. The charging patterns of the blast holes with top and bottom air decks are shown in Figure 7. All of these eight experiments were carried out at the same location with the same blast design parameters to maintain the same geological characteristics of the rock mass (Table 1).
Design Parameters | Normal Blasting | Blasting with Air Deck |
Hole Length (m) | 7 | 7 |
Hole Diameter (in) | 3 | 3 |
Burden (m) | 2.7 | 2.7 |
Spacing (m) | 3 | 3 |
Explosive Charge Length (m) | 5.9 | 4.9 |
Stemming Length(m) | 1.1 | 1.1 |
Subdrilling Length (m) | 0 | 0 |
Power Decking Length (m) | 0 | 1 |
Filling Length (m) | 7 | 6 |
As shown in Table 1, the amount of explosives consumed is reduced per meter of air deck length by using the top airdeck method.
In the Chah-Gaz mine (Case 2), to compare the explosion with and without an airdeck, the explosive block was divided into two parts. In this way, half of the blast holes were charged with an air deck and the other half were normal (Figure 8).
The blast holes were drilled in four rows with block dimensions of 68 m, 18 m and 10 m for length, width and height, respectively. For the holes with bottom air decks, a 1-m sub-drilling, which is done for normal blast holes, was totally omitted. A considerable cost related to the drilling and charging of sub-drilling was reduced from the total costs with the omission of sub-drilling.
The blast design parameters commonly used in mine case 2 are presented in Table 2.
Design Parameters | Normal Blasting | Blasting With Power Deck |
Hole Length (m) | 10 | 10 |
Hole Diameter (Inch) | 4.5 | 4.5 |
Burden (m) | 4 | 4 |
Spacing (m) | 5 | 5 |
Explosive Charge Length (m) | 8.25 | 7.5 |
Stemming Length (m) | 2.75 | 2.5 |
Sub-drilling Length (m) | 1 | 0 |
Power Decking Length (m) | 0 | 1 |
Filling Length (m) | 11 | 9 |
As can be seen in Table 2, sub-drilling has been eliminated in the blast with a bottom air deck, which reduces drilling in the blast using an air deck, as well as the amount of explosive consumed.
For Case 1, which involved a PVC tube with a length of 1 m and diameter of 5.6 cm, was used to create the air deck (Figure 9), whereas, in Case 2, a 2.5-cm diameter PVC pipe 85 cm in length with a flexible basket attached to the top of it was used to create the air deck. This assemblage was easy to insert into the blast holes. The basket, which was filled with a small amount of inert (non-explosive) materials, helps the pipe to be positioned in the center of the blast hole (Figure 10).
The results of both types of experimental blasts were evaluated in terms of the fragment size, flyrock, back break, air blast, ground vibration, muck pile profile and economical aspects.
The main objective of the mine blasting is to achieve an appropriate fragmentation. Fragmentation quality has a vital role in the efficiency of a mineral processing plant, as well as the loading and hauling, and it can be an ultimate concern when reducing the total cost.
To compare the fragments of the blasting of three conventional methods with the top and bottom air decks, the mean fragmentation size (MFS) parameter obtained via Eq 4 was used.
MFS=∑( sieve size )∗( percent remaining on sieve )、.. | (4) |
After preparing the images, they are considered as input for the software program through which the boundaries of the fragments were marked for further actions. It is noted that, in the images, the blue color is considered a mask which is not incorporated into the calculations (Figure 12).
In Tables 3 and 4, the MFS for each blast is given.
Mean Fragmentation Size (cm) | Stemming Technique |
20.58 | Without air decking |
19.46 | Without air decking |
27 | Top air decking |
28.5 | Top air decking |
24 | Top air decking |
28.2 | Bottom air decking |
27.1 | Bottom air decking |
25.5 | Bottom air decking |
Mean Fragmentation Size (cm) | Stemming Technique |
64.1 | Without air decking |
17.3 | Bottom air decking |
According to Table 3, for Case 1, the MFS obtained via conventional blasting was 20.22 cm, while that for the top and bottom air deck was 26.51 and 24.27 cm, respectively. As it is seen from this table, the application of the air deck increased the MFS, which is important for the loading and hauling equipment efficiency on one hand, and the primary crusher performance on another hand. Unlike Case 1, a conflicting result can be seen in Case 2, where the MFS was drastically reduced from 64.10 to 17.30 cm. It is noted that, in the Chah-Gaz mine, there was a toe-related problem in the currently practiced blasting operation, and as a well-known fact of multi-row blasting, when the creation of a toe exists, especially in the front rows, there is a chance of poor fragmentation, which is concurrent to boulder production, which in turn increases the MFS.
An unwanted throw of the rock fragments in a blasting operation is called flyrock [31]. Massey and Siu mentioned that the existence of loose rock can also affect flyrock intensity [32]. Gustavsson, suggested that flyrock is in a direct relationship with the specific charge [33]. The amount of observed flyrock for Case 1 is shown in Table 5. According to this table, the average flyrock distance in conventional blasting is approximately 25 m. Whereas, in the operations associated with the top and bottom air decks, the average flyrock distance was about 10.33 and 16.66 m, respectively. The same trend of reducing flyrock was also observed in Case 2.
Flyrock (m) | Stemming Technique |
26 | Without air decking |
24 | Without air decking |
11 | Top air decking |
10 | Top air decking |
10 | Top air decking |
20 | Bottom air decking |
18 | Bottom air decking |
12 | Bottom air decking |
The back break is considered as the fractured rocks beyond the last row of the blast holes [34]. This phenomenon should be prevented while performing blasting operations in open-pit mines. Slope stability can be adversely affected by back breaks because of rock deterioration. The most influential factors in back break creation are an excessive burden, elongated stemming [35], inappropriate delay timing and a high number of blast hole rows [36]. The amounts of back breaks caused by eight trial blasting tests at the Cheshmeh-Parvar mine are shown in Table 6. As seen in Table 6, the application of deck charging has a significant role in reducing back breaks. Another important point in this regard is that the top air deck was more effective than the bottom air deck.
Back break (m) | Stemming Technique |
2.3 | Without air decking |
2.2 | Without air decking |
0.9 | Top air decking |
0.9 | Top air decking |
1.1 | Top air decking |
1.5 | Bottom air decking |
2 | Bottom air decking |
1.9 | Bottom air decking |
The back break in Case 2 was also noticeable during normal blasting without deck charging (Figure 13). As is seen in this figure, cracks of up to 15 cm were created in the remaining pit wall. Also, Figure 13 shows that fragmented rocks were successfully displaced, that there was no sign of a back break when using the air deck method and that the remaining wall after the blasting operation was quite smooth, which is favorable for the next blast.
Explosions and some earthquakes produce very similar seismic signals [37]. Charge per delay is one of the most influential parameters for air blast and ground vibration intensity. According to the relevant literature, there is a basic relationship between peak particle velocity and charge per delay (Eq 4) [24].
PPV=Qa | (5) |
where Q is the maximum charge per delay (kg), PPV is the peak particle velocity (m/s) and a is a constant with the first approximation of 0.8.
In this study, it was obvious that, in Cases 1 and 2, the explosive consumption or charge per delay was reduced when using an air deck. Therefore, it can be concluded that the air blast and ground vibration would be lessened by using the air deck method. It is noted that this event was visible during the blasting operations for Cases 1 and 2.
It should be noted that, in all the experiments, the type of explosive used was fixed and the aim was to investigate the effect of air deck positioning. The explosives included the main charge ANFO, with a density of 0.85 g/cm3 and velocity of detonation of 3700 m/s, emulsion cartridges were also used as a primer.
The muck pile profile is influential on the loading and haulage equipment performance. For instance, shovels can efficiently be used when the muck pile is higher [20]. One of the merits of air-deck blasting is that it enables a higher muck. In Cases 1 and 2, a proper muck pile profile was observed while implementing an air deck in the blast holes. As can be seen in Figure 15, the sketch with a blue boundary shows air-deck blasting with an appropriate muck pile profile, but the green boundary shows a dispersed muck pile, which is the result of normal blasting.
The economical aspects should be considered in any commercial activity. In this study, an attempt was made to demonstrate the technical effectiveness of air-deck blasting; accordingly, the economic benefits of this technique can be proven. Cost savings related to air deck utilization can be divided into two parts, i.e., direct and indirect costs. The former includes the amount of drilled blast holes and charged explosives, whereas the latter includes savings related to productivity improvement of the downstream operations, including loading and haulage. In this section, only direct cost savings of the Chah-Gaz mine are presented. It is noted that the costs are expressed in the US dollar. Considering that the cost reduction related to drilling and blasting, which was calculated at around USD 30, 000/ =, and the cost related to providing the air deck assemblage, i.e., USD 10, 000/ =, then the difference of USD 20, 000/ = would be the cost savings associated with utilizing the air deck technique.
Based on the presented materials, the overall conclusion that can be drawn from this study is that the use of air decking, in addition to the reduction of costs, leads to optimized use of the explosive energy; and, it reduces the loss of explosive energy via unfavorable phenomena, such as retardation, rock-throwing and earth vibration. The following are the merits of air deck application:
• Reduction in explosive consumption;
• A decrease in the length of the drilled blast holes by inserting an air deck (1 m) and omitting sub-drilling (1 m) due to the use of a bottom air deck; of course, only for the Chah-Gaz mine;
• Resolving blasting operation-related unwanted phenomena, including the back break, air blast, toe-related problems, ground vibration and flyrock;
• Improvement of rock fragmentation;
• Increased loading and haulage operation by the creation of an appropriate muck pile profile.
On behalf of all authors, the corresponding author states that there is no conflict of interest.
[1] | Saghatforoush A (2014) Optimization of Explosive Operations using the Ant Colony Algorithm in Delkan Iron Ore Mining. Master thesis, Tarbiat Modares University. |
[2] |
Armaghani DJ, Mahdiyar A, Hasanipanah M, et al. (2016) Risk Assessment and Prediction of Flyrock Distance by Combined Multiple Regression Analysis and Monte Carlo Simulation of Quarry Blasting. Rock Mech Rock Eng 49: 3631–3641. https://doi.org/10.1007/s00603-016-1015-z doi: 10.1007/s00603-016-1015-z
![]() |
[3] |
Khandelwal M, Saadat M (2015) A Dimensional Analysis Approach to Study Blast-Induced Ground Vibration. Rock Mech Rock Eng 48: 727–735. https://doi.org/10.1007/s00603-014-0604-y doi: 10.1007/s00603-014-0604-y
![]() |
[4] |
Rezaeineshat A, Monjezi M, Mehrdanesh A, et al. (2020) Optimization of blasting design in open pit limestone mines with the aim of reducing ground vibration using robust techniques. Geomech Geophys Geo-energ Geo-resour 6: 40. https://doi.org/10.1007/s40948-020-00164-y doi: 10.1007/s40948-020-00164-y
![]() |
[5] |
Tribe J, Koroznikova L, Khandelwal M, et al. (2021) Evaluation and Assessment of Blast-Induced Ground Vibrations in an Underground Gold Mine: A Case Study. Nat Resour Res 30: 4673–4694. https://doi.org/10.1007/s11053-021-09943-0 doi: 10.1007/s11053-021-09943-0
![]() |
[6] | Rowlands MD (1989) Separating explosive charges with Airdecks to improve fragmentation whilst reducing explosive usage. In Proceedings of second large open-pit mining conference. Latrobe Valley, Vic (Melbourne: Australian Institute of Mining and Metallurgy). |
[7] | Mead DJ, Moxon NT, Danell RE, et al. (1993) The use of air-decks in production blasting. In Proceedings of the 19th annual conference on explosives and blasting technique. international society of explosives engineers, Cleveland, Ohio, USA, 219–226. |
[8] |
Jhanwar JC, Jethwa JL, Reddy A (2000) Influence of air-deck blasting on fragmentation in jointed rocks in an open-pit manganese mine. Eng Geol 57: 13–29. https://doi.org/10.1016/S0013-7952(99)00125-8 doi: 10.1016/S0013-7952(99)00125-8
![]() |
[9] |
Akbari M, Lashkaripour G, Bafghi AY, et al. (2015) Blastability evaluation for rock mass fragmentation in Iran central iron ore mines. Int J Min Sci Technol 25: 59–66. https://doi.org/10.1016/j.ijmst.2014.11.008 doi: 10.1016/j.ijmst.2014.11.008
![]() |
[10] | Pradhan M, Balakrishnan V, Pradhan GK (2015) Use of discarded water bottles in blasting-An Innovative Enviro-Friendly Technique. Int J Chem Environ Biol Sci 3: 51–53. |
[11] |
Jhanwar JC (2011) Theory and Practice of Airdeck Blasting in Mines and Surface Excavations. Geotech Geol Eng 29: 651–663. https://doi.org/10.1007/s10706-011-9425-x doi: 10.1007/s10706-011-9425-x
![]() |
[12] | Terrett P, Steyn SA, Rorke AJ (1995) Airdecking at Duvha, a technical evaluation. In Proc. Sixth high-tech Seminar, State-of-the-Art Blasting Technology Instrumentation and Explosives Applications, Boston Massachusetts, USA, 87–599. |
[13] | Saqib SS, Tariq M, Ali Z (2015) Improving Rock Fragmentation Using Airdeck Blasting Technique. Pak J Eng Appl Sci 15: 46–52. |
[14] |
Lu W, Hustrulid W (2003) A further study on the mechanism of air-decking. Fragblast 7: 231–255. https://doi.org/10.1076/frag.7.4.231.23532 doi: 10.1076/frag.7.4.231.23532
![]() |
[15] | Shin CO, KO TY, Lee SC, et al. (2011) Application of multiple-deck-charge blasting with electronic detonator at DTL2 Contract 915 in Singapore. Underground Singapore. |
[16] | Hayat MB, Alaghab L, Alia D (2020) Air Decks in Surface Blasting Operations. J Min Sci 55: 922–929. |
[17] | Zhang Y, Luo Y, Wan S, et al. (2020) Influence of Decoupled Charge Structure and Filler on the Blasting Effect. Shock Vib, 8866449. https://doi.org/10.1155/2020/8866449 |
[18] |
Jang H, Handel D, Ko Y, et al., (2018) Effects of Water Deck on Rock Blasting Performance. Int J Rock Mech Min Sci 112: 77–83. https://doi.org/10.1016/j.ijrmms.2018.09.006 doi: 10.1016/j.ijrmms.2018.09.006
![]() |
[19] | Zhang XJ, Wang XG, Yu YL, et al. (2018) The Application of Deck Charge Technology in Hua Neng open pit Mine. In ICEMEE, E3S Web of Conferences 38. https://doi.org/10.1051/e3sconf/20183803031 |
[20] |
Zuo J, Yang R, Gong M, et al. (2022) Fracture characteristics of iron ore under uncoupled blast loading. Int J Min Sci Technol 32: 657–677. https://doi.org/10.1016/j.ijmst.2022.03.008 doi: 10.1016/j.ijmst.2022.03.008
![]() |
[21] | Yin Z, Wang D, Wang X, et al. (2021) Optimization and Application of Spacing Parameter for Loosening Blasting with 24-m-High Bench in Barun Open-Pit Mine. Shock Vib, 6670276. https://doi.org/10.1155/2021/6670276 |
[22] |
Ma C, Xie W, Zelin L, et al. (2020) A New Technology for Smooth Blasting without Detonating Cord for Rock Tunnel Excavation. Appl Sci 10: 6764. https://doi.org/10.3390/app10196764 doi: 10.3390/app10196764
![]() |
[23] | Sazid M, Singh TN (2013) Mechanism of Air Deck Technique in Rock Blasting- A Brief Review. INDOROCK, Fourth Indian Rock Conference. |
[24] | Hayat MB, Tariq M (2012) Optimization of Bench Blasting using Airdeck Blasting Technique. M.Sc. thesis, The University of Engineering and Technology Lahore, Pakistan. |
[25] |
Correa CE (2003) Use of Airdecks to reduce subdrilling in Escondido mine. Fragblast 7: 79–86. https://doi.org/10.1076/frag.7.2.79.15895 doi: 10.1076/frag.7.2.79.15895
![]() |
[26] | Jimeno CL, Jimeno EL, Carcedo FJA (1995) Drilling and blasting of rocks. Rotterdam. |
[27] | Chiappetta RF (2004) Blasting technique to eliminate subgrade drilling, improve fragmentation, reduce explosive consumption and lower ground vibrations. J Explos Eng 21: 10–18. |
[28] | Melnikov NV, Marchenko LN (1971) Effective methods of application of explosive energy in mining and construction. In Twelfth symposium on dynamic rock mechanics. AIME, New York, 350–378. |
[29] | Bussey J, Borg DG (1988) Pre-splitting with the new air-deck technique. Proceedings of 14th conference on explosive and blasting technique, explosive engineers annual meet, Anaheim, California, 197. |
[30] |
Broch E, Franklin JA (1972) The Point-Load Strength Test. Int J Rock Mech Min Sci 9: 669–697. https://doi.org/10.1016/0148-9062(72)90030-7 doi: 10.1016/0148-9062(72)90030-7
![]() |
[31] | Siskind DE, Kopp JW (1995) Blasting accidents in mines, a 16-year summary. International Society of Explosives Engineers. |
[32] | Massey JB, Siu K L (2003) Investigation of Flyrock incident at clear water bay road on 6 June. Civ Eng Dep Gov Hong Kong Spec Adm Reg Hong Kong, 49. |
[33] | Gustafsson R (1973) Swedish Blasting Technique and Mining SPI, Gothenburg, Sweden. |
[34] | Rustan A (1998) Rock blasting terms and symbols. AA Balkema, 193. https://doi.org/10.1201/9781466571785 |
[35] | Konya CJ, Walter EJ (1991) Rock blasting and overbreak control. United States. Federal Highway Administration. |
[36] | Gates WCB, Ortiz LT, Florez RM (2005) Analysis of rockfall and blasting backbreak problems. In The 40th US Symposium on Rock Mechanics (USRMS), Anchorage, Alaska. |
[37] | Mining Engineering System Organization (2012) Guide to assessing and controlling the consequences of blasting in surface mines. |
Design Parameters | Normal Blasting | Blasting with Air Deck |
Hole Length (m) | 7 | 7 |
Hole Diameter (in) | 3 | 3 |
Burden (m) | 2.7 | 2.7 |
Spacing (m) | 3 | 3 |
Explosive Charge Length (m) | 5.9 | 4.9 |
Stemming Length(m) | 1.1 | 1.1 |
Subdrilling Length (m) | 0 | 0 |
Power Decking Length (m) | 0 | 1 |
Filling Length (m) | 7 | 6 |
Design Parameters | Normal Blasting | Blasting With Power Deck |
Hole Length (m) | 10 | 10 |
Hole Diameter (Inch) | 4.5 | 4.5 |
Burden (m) | 4 | 4 |
Spacing (m) | 5 | 5 |
Explosive Charge Length (m) | 8.25 | 7.5 |
Stemming Length (m) | 2.75 | 2.5 |
Sub-drilling Length (m) | 1 | 0 |
Power Decking Length (m) | 0 | 1 |
Filling Length (m) | 11 | 9 |
Mean Fragmentation Size (cm) | Stemming Technique |
20.58 | Without air decking |
19.46 | Without air decking |
27 | Top air decking |
28.5 | Top air decking |
24 | Top air decking |
28.2 | Bottom air decking |
27.1 | Bottom air decking |
25.5 | Bottom air decking |
Mean Fragmentation Size (cm) | Stemming Technique |
64.1 | Without air decking |
17.3 | Bottom air decking |
Flyrock (m) | Stemming Technique |
26 | Without air decking |
24 | Without air decking |
11 | Top air decking |
10 | Top air decking |
10 | Top air decking |
20 | Bottom air decking |
18 | Bottom air decking |
12 | Bottom air decking |
Back break (m) | Stemming Technique |
2.3 | Without air decking |
2.2 | Without air decking |
0.9 | Top air decking |
0.9 | Top air decking |
1.1 | Top air decking |
1.5 | Bottom air decking |
2 | Bottom air decking |
1.9 | Bottom air decking |
Design Parameters | Normal Blasting | Blasting with Air Deck |
Hole Length (m) | 7 | 7 |
Hole Diameter (in) | 3 | 3 |
Burden (m) | 2.7 | 2.7 |
Spacing (m) | 3 | 3 |
Explosive Charge Length (m) | 5.9 | 4.9 |
Stemming Length(m) | 1.1 | 1.1 |
Subdrilling Length (m) | 0 | 0 |
Power Decking Length (m) | 0 | 1 |
Filling Length (m) | 7 | 6 |
Design Parameters | Normal Blasting | Blasting With Power Deck |
Hole Length (m) | 10 | 10 |
Hole Diameter (Inch) | 4.5 | 4.5 |
Burden (m) | 4 | 4 |
Spacing (m) | 5 | 5 |
Explosive Charge Length (m) | 8.25 | 7.5 |
Stemming Length (m) | 2.75 | 2.5 |
Sub-drilling Length (m) | 1 | 0 |
Power Decking Length (m) | 0 | 1 |
Filling Length (m) | 11 | 9 |
Mean Fragmentation Size (cm) | Stemming Technique |
20.58 | Without air decking |
19.46 | Without air decking |
27 | Top air decking |
28.5 | Top air decking |
24 | Top air decking |
28.2 | Bottom air decking |
27.1 | Bottom air decking |
25.5 | Bottom air decking |
Mean Fragmentation Size (cm) | Stemming Technique |
64.1 | Without air decking |
17.3 | Bottom air decking |
Flyrock (m) | Stemming Technique |
26 | Without air decking |
24 | Without air decking |
11 | Top air decking |
10 | Top air decking |
10 | Top air decking |
20 | Bottom air decking |
18 | Bottom air decking |
12 | Bottom air decking |
Back break (m) | Stemming Technique |
2.3 | Without air decking |
2.2 | Without air decking |
0.9 | Top air decking |
0.9 | Top air decking |
1.1 | Top air decking |
1.5 | Bottom air decking |
2 | Bottom air decking |
1.9 | Bottom air decking |