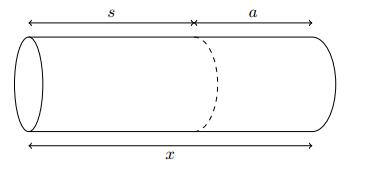
schematic representation of the variables on an E. coli bacterium
.Sugarcane leaves are the main residue constitute approximately 14% of the total weight of the remaining sugarcane after harvesting. An effective method for processing sugarcane leaves residues is needed at low cost without causing any environmental problem. This research aims to disclose the effect of sugarcane leaves densification method applied prior to pyrolysis process in a pilot scale reactor. To evaluate the process and its product, the experiments were carried out into two types: (i) pyrolysis of sugarcane leaves without densification at 320 ℃ with a variation of pyrolysis time for 100,120, and 130 minutes and (ii) pyrolysis of densified sugarcane leaves with the variation of pyrolysis temperature 320 ℃ and 420 ℃. The investigated conditions showed that the effect of sugarcane leaves densification prolong the pyrolysis time up to 240 minutes at a pyrolysis temperature of 320 ℃, and increased the yield of biochar and bio-oil products up to 41% and 38%, respectively. However, in term of the physical properties of biochar products, the fixed carbon content decreased by 7% when the sugarcane leaves were compacted. While other parameters found no significant difference in pyrolysis at 320 ℃, the effect of sugarcane leaves densification is very beneficial especially when the pyrolysis was performed at 420 ℃.
Citation: Adi Setiawan, Ananda Fringki, M. Iqbal Hifzi, Shafira Riskina, Jalaluddin, Eddy Kurniawan, Burhanuddin. The effect of feedstock densification on the process and product properties of sugarcane leaves pyrolysis[J]. AIMS Environmental Science, 2024, 11(6): 866-882. doi: 10.3934/environsci.2024043
[1] | Pierre Gabriel, Hugo Martin . Steady distribution of the incremental model for bacteria proliferation. Networks and Heterogeneous Media, 2019, 14(1): 149-171. doi: 10.3934/nhm.2019008 |
[2] | Fadia Bekkal-Brikci, Giovanna Chiorino, Khalid Boushaba . G1/S transition and cell population dynamics. Networks and Heterogeneous Media, 2009, 4(1): 67-90. doi: 10.3934/nhm.2009.4.67 |
[3] | Pierre Degond, Sophie Hecht, Nicolas Vauchelet . Incompressible limit of a continuum model of tissue growth for two cell populations. Networks and Heterogeneous Media, 2020, 15(1): 57-85. doi: 10.3934/nhm.2020003 |
[4] | Paulo Amorim, Alessandro Margheri, Carlota Rebelo . Modeling disease awareness and variable susceptibility with a structured epidemic model. Networks and Heterogeneous Media, 2024, 19(1): 262-290. doi: 10.3934/nhm.2024012 |
[5] | Piotr Gwiazda, Karolina Kropielnicka, Anna Marciniak-Czochra . The Escalator Boxcar Train method for a system of age-structured equations. Networks and Heterogeneous Media, 2016, 11(1): 123-143. doi: 10.3934/nhm.2016.11.123 |
[6] | Martino Bardi . Explicit solutions of some linear-quadratic mean field games. Networks and Heterogeneous Media, 2012, 7(2): 243-261. doi: 10.3934/nhm.2012.7.243 |
[7] | Peter V. Gordon, Cyrill B. Muratov . Self-similarity and long-time behavior of solutions of the diffusion equation with nonlinear absorption and a boundary source. Networks and Heterogeneous Media, 2012, 7(4): 767-780. doi: 10.3934/nhm.2012.7.767 |
[8] | Yacine Chitour, Guilherme Mazanti, Mario Sigalotti . Stability of non-autonomous difference equations with applications to transport and wave propagation on networks. Networks and Heterogeneous Media, 2016, 11(4): 563-601. doi: 10.3934/nhm.2016010 |
[9] | Dieter Armbruster, Christian Ringhofer, Andrea Thatcher . A kinetic model for an agent based market simulation. Networks and Heterogeneous Media, 2015, 10(3): 527-542. doi: 10.3934/nhm.2015.10.527 |
[10] | Andrea Tosin . Multiphase modeling and qualitative analysis of the growth of tumor cords. Networks and Heterogeneous Media, 2008, 3(1): 43-83. doi: 10.3934/nhm.2008.3.43 |
Sugarcane leaves are the main residue constitute approximately 14% of the total weight of the remaining sugarcane after harvesting. An effective method for processing sugarcane leaves residues is needed at low cost without causing any environmental problem. This research aims to disclose the effect of sugarcane leaves densification method applied prior to pyrolysis process in a pilot scale reactor. To evaluate the process and its product, the experiments were carried out into two types: (i) pyrolysis of sugarcane leaves without densification at 320 ℃ with a variation of pyrolysis time for 100,120, and 130 minutes and (ii) pyrolysis of densified sugarcane leaves with the variation of pyrolysis temperature 320 ℃ and 420 ℃. The investigated conditions showed that the effect of sugarcane leaves densification prolong the pyrolysis time up to 240 minutes at a pyrolysis temperature of 320 ℃, and increased the yield of biochar and bio-oil products up to 41% and 38%, respectively. However, in term of the physical properties of biochar products, the fixed carbon content decreased by 7% when the sugarcane leaves were compacted. While other parameters found no significant difference in pyrolysis at 320 ℃, the effect of sugarcane leaves densification is very beneficial especially when the pyrolysis was performed at 420 ℃.
In structured population dynamics, finding the structuring variable(s) which best describes a phenomenon is a crucial question. For a population of proliferating cells or bacteria the variables usually considered are age, size (see [27,12,18]) or a combination of both (see [1,24,10] for modeling and [26,12,10,6] for mathematical analysis). Recent experimental work highlighted the limits of these models to describe bacteria, and a new variable to trigger division emerged: the size-increment, namely the size gained since the birth of the cell (see [22] and references therein for a review of the genesis of the related model). This so called 'adder principle ensures homeostasis with no feedback from the bacteria and explains many experimental data. In this model, bacteria are described by two parameters: their size-increment and their size, respectively denoted by
{∂tn(t,a,x)+∂a(g(x)n(t,a,x))+∂x(g(x)n(t,a,x))+B(a)g(x)n(t,a,x)=0,t≥0, x>a>0,g(x)n(t,0,x)=4g(2x)∫∞0B(a)n(t,a,2x)da,t≥0, x>0. |
The function
∂tn(t,a,x)+∂a(g(x)n(t,a,x))+∂x(g(x)n(t,a,x))+B(a)g(x)n(t,a,x)=0,t≥0, x>a>0, | (1a) |
g(x)n(t,0,x)=∫10g(xz)∫∞0B(a)n(t,a,xz)da dμ(z)z,t≥0, x>0. | (1b) |
It appears that this model is a particular case of the one proposed in the pioneer work [10] for plants growing in a single dimension, mixing age and size control. Indeed, in this paper the authors noticed that in the case of a deterministic and positive growth rate, a size/age model is equivalent to a size/birth-size through the relation
First, we want the sum of the daughters sizes to be equal to the size of the mother. This rule, called mass conservation, prescribes
∫10zdμ(z)=1. | (2) |
We also assume that the division does not produce any arbitrarily small daughter by imposing that the support of
θ:=infsuppμ>0and∃η∈(θ,1), suppμ⊂[θ,η]. | (3) |
In particular, these assumptions imply that the mean number of daughters
∃b≥0,suppB=[b,∞), | (4) |
see [8] for instance. It will be useful in our study to define the associated survivor function
Ψ(a)=e−∫a0B(z)dz. |
For a given increment
∃k0>0,Ψ(a)=+∞O(a−k0). | (5) |
This assumption on the decay at infinity of the survivor function enables a wide variety of division rates. For instance, it is satisfied if there exists
∀a≥A,B(a)≥k0a. |
The function
Φ=BΨ=−Ψ′ | (6) |
which is the probability distribution that a cell divides at increment
∬xn(t,a,x)dadx=et∬xn0(a,x)dadx. | (7) |
This implies that if we look for a solution with separated variables
∂a(xN(a,x))+∂x(xN(a,x))+(1+xB(a))N(a,x)=0,x>a>0, | (8a) |
N(0,x)=∫10∫∞0B(a)N(a,xz)da dμ(z)z2,x>0, | (8b) |
N(a,x)≥0,x≥a≥0, | (8c) |
∫∞0∫x0N(a,x)dadx=1. | (8d) |
It is convenient to define the set
Theorem 1.1. Let
N:(a,x)∈X↦Ψ(a)x2f(x−a) | (9) |
where
f∈L1(R+,xldx) |
for all
suppf=[bθ,∞) |
with
The fast decay of the function
Notice also that for the function
The article is organised as follows. In Section 2 we reduce the Perron eigenvalue problem with two variables to a fixed point problem for an integral operator in dimension one. Section 3 is dedicated to proving the existence and uniqueness of the fixed point by using functional analysis and Laplace transform methods. In Section 4 we go through the usefulness of knowing
Our study consists in constructing a solution to the eigenproblem (8) from the solution of a fixed point problem. First, we notice that the size
M(a,s):=N(a,a+s). | (10) |
Thanks to this relation, it is equivalent to prove the existence of an eigenvector for the increment-size system or for the increment/birth-size system. To determine the equation verified by
∂a((a+s)M(a,s))+(1+(a+s)B(a))M(a,s)=0. |
Writing the non-local boundary condition (8b) with the new variables takes less calculation and more interpretation. In (8b) the number of cells born at size
M(0,s)=∫ηθ∫sz0B(a)M(a,sz−a)da dμ(z)z2 |
since there is no mass for
∂a((a+s)M(a,s))+(1+(a+s)B(a))M(a,s)=0,a,s>0, | (11a) |
M(0,s)=∫ηθ∫sz0B(a)M(a,sz−a)da dμ(z)z2,s>0, | (11b) |
M(a,s)≥0,a,s≥0, | (11c) |
∫R2+M(a,s)dads=1. | (11d) |
Considering the variable
M(a,s)=Ψ(a)(a+s)2s2M(0,s). |
Having this expression in mind, we note that for any nonnegative function
Mf:(a,s)↦Ψ(a)(a+s)2f(s) |
is a solution of (11a) and satisfies (11c). Then it remains to choose the appropriate function
Tf(s)=∫ηθ∫sz0Φ(sz−a)f(a)dadμ(z), | (12) |
where
Lemma 2.1. The function
Proof.
Mf satisfies (11b)⟺f(s)s2=∫ηθ∫sz0B(a)Ψ(a)(sz)2f(sz−a)da dμ(z)z2⟺f(s)=∫ηθ∫sz0Φ(a)f(sz−a)da dμ(z)⟺f(s)=∫ηθ∫sz0Φ(sz−a)f(a)da dμ(z)⟺f(s)=Tf(s) |
The operator
Lemma 2.2. For all
Proof. We start with
∫βα|Tf(s)|slds≤∫ηθ∫βαsl∫sz0Φ(sz−a)|f(a)|dadsdμ(z)≤∫ηθ∫αz0|f(a)|∫βαΦ(sz−a)sldsdadμ(z)+∫ηθ∫βzαz|f(a)|∫βzaΦ(sz−a)sldsdadμ(z)≤∫ηθ∫αz0|f(a)|∫βz−aαz−aΦ(σ)(a+σ)lzl+1dσdadμ(z)+∫ηθ∫βzαz|f(a)|∫βz−a0Φ(σ)(a+σ)lzl+1dσdadμ(z)≤∫ηθzl+1∫αz0|f(a)|aldadμ(z)+∫ηθzl+1∫∞αz|f(a)|aldadμ(z)≤θl‖f‖L1(R+,slds), |
which gives the conclusion by passing to the limits
For the second part we begin with the proof that under condition (5), for any
∫∞0Φ(a)akda<∞. |
First, recall that
∫β0Φ(a)akda≤∫10Φ(a)da+∫β1Φ(a)akda≤1+k∫β1Ψ(a)ak−1da |
and the last integral converges when
∫β0|Tf(s)|skds≤∫ηθ∫β0sk∫sz0Φ(sz−a)|f(a)|dadsdμ(z)=∫ηθ∫βz0|f(a)|∫βz−a0Φ(σ)(a+σ)kzk+1dσdadμ(z)≤C∫ηθzk+1∫βz0|f(a)|ak∫βz−a0Φ(σ)dσdadμ(z)+C∫ηθzk+1∫βz0|f(a)|∫βz−a0Φ(σ)σkdσdadμ(z)≤Cηk(‖f‖L1(R+,skds)+‖Φ‖L1(R+,skds)‖f‖L1(R+)). |
In this section we prove the existence of a unique nonnegative and normalized fixed point of the operator
Let us first recall some definitions from the Banach lattices theory (for more details, see [9,23]). Let
f≥0 if and only if f(s)≥0 ν-a.e. on Ω. |
Furthermore, endowed with its standard norm, the space
To prove the existence of an eigenvector associated to the eigenvalue
Theorem 3.1. Let
Due to a lack of compactness of the operator
TΣf(s)=∫ηθ∫min(sz,Σ)bθΦ(sz−a)f(a)dadμ(z) | (13) |
={∫ηθ∫szbθΦ(sz−a)f(a)dadμ(z),bθ≤s<θΣ,∫sΣθ∫ΣbθΦ(sz−a)f(a)dadμ(z)+∫ηsΣ∫szbθΦ(sz−a)f(a)dadμ(z),θΣ≤s≤ηΣ,∫ηθ∫ΣbθΦ(sz−a)f(a)dadμ(z),ηΣ<s≤Σ. |
Defining the lower bound of the domain as
The following lemma ensures that the truncated operator
Lemma 3.2. If
(Tf)|[bθ,Σ]=TΣ(f|[bθ,Σ]). |
Lemma 3.2 is a straightforward consequence of the definition of operator
{∀ϵ>0, ∀ω⊂⊂Ω, ∃δ∈(0,dist(ω,cΩ)) such that ‖τhf−f‖L1(ω,ν)<ϵ, ∀h∈(−δ,δ), ∀f∈F | (14) |
{∀ϵ>0, ∃ω⊂⊂Ω, such that ‖f‖L1(Ω∖ω,ν)<ϵ, ∀f∈F | (15) |
where
Theorem 3.3 (from [3], corollary 4.27). If
Using Theorem 3.1, we prove the existence of an eigenpair
Proposition 1. Let
Applying Theorem 3.3, to
F={TΣf,f∈L1((bθ,Σ),slds),‖f‖L1((bθ,Σ),slds)≤1}, |
which is bounded in
Lemma 3.4. Let
Σ>max(b1−θ,1), |
the set
Proof of Lemma 3.4. The set
∫βα|TΣf(s+h)−TΣf(s)|slds≤∫θΣ−hα|TΣf(s+h)−TΣf(s)|slds=:(A)+∫θΣθΣ−h|TΣf(s+h)−TΣf(s)|slds=:(B)+∫ηΣ−hθΣ|TΣf(s+h)−TΣf(s)|slds=:(C)+∫ηΣηΣ−h|TΣf(s+h)−TΣf(s)|slds=:(D)+∫βηΣ|TΣf(s+h)−TΣf(s)|slds=:(E). |
since for
(C)=∫ηΣ−hθΣ|TΣf(s+h)−TΣf(s)|slds≤∫ηΣ−hθΣ|∫s+hΣθ∫ΣbθΦ(s+hz−a)f(a)dadμ(z)−∫sΣθ∫ΣbθΦ(sz−a)f(a)dadμ(z)|slds+∫ηΣ−hθΣ|∫ηs+hΣ∫s+hzbθΦ(s+hz−a)f(a)dadμ(z)−∫ηsΣ∫szbθΦ(sz−a)f(a)dadμ(z)|slds≤∫ηΣ−hθΣsl∫sΣθ∫Σbθ|Φ(s+hz−a)−Φ(sz−a)||f(a)|dadμ(z)ds=:(C1)+∫ηΣ−hθΣsl∫s+hΣsΣ∫ΣbθΦ(s+hz−a)|f(a)|dadμ(z)ds=:(C2) |
+∫ηΣ−hθΣsl∫ηs+hΣ∫szbθ|Φ(s+hz−a)−Φ(sz−a)||f(a)|dadμ(z)ds=:(C3)+∫ηΣ−hθΣsl∫ηs+hΣ∫s+hzszΦ(s+hz−a)|f(a)|dadμ(z)ds=:(C4)+∫ηΣ−hθΣsl∫s+hΣsΣ∫szbθΦ(s+hz−a)|f(a)|dadμ(z)ds=:(C5) |
The integrals
(C1)=∫ηΣ−hθΣsl∫sΣθ∫Σbθ|Φ(s+hz−a)−Φ(sz−a)||f(a)|dadμ(z)ds=∫η−hΣθ∫Σbθ|f(a)|∫ηΣ−hzΣ|Φ(s+hz−a)−Φ(sz−a)|sldsdadμ(z)=∫η−hΣθzl+1∫Σbθ|f(a)|∫ηΣ−hz−aΣ−a|τhzΦ(σ)−Φ(σ)|(a+σ)ldσdadμ(z)=∫η−hΣθzl+1∫Σbθ|f(a)|al∫ηΣ−hz−aΣ−a|τhzΦ(σ)−Φ(σ)|dσdadμ(z)≤θlsupε∈[θ,η]‖τhεΦ−Φ‖L1(R+). |
These integrals are as small as needed when
(C2)=∫ηΣ−hθΣsl∫s+hΣsΣ∫ΣbθΦ(s+hz−a)|f(a)|dadμ(z)ds=∫θ+hΣθ∫Σbθ|f(a)|∫zΣθΣΦ(s+hz−a)sldsdadμ(z)+∫η−hΣθ+hΣ∫Σbθ|f(a)|∫zΣzΣ−hΦ(s+hz−a)sldsdadμ(z)+∫ηη−hΣ∫Σbθ|f(a)|∫ηΣ−hzΣ−hΦ(s+hz−a)sldsdadμ(z)≤∫ηθ∫Σbθ|f(a)|∫zΣzΣ−hΦ(s+hz−a)sldsdadμ(z)=∫ηθzl+1∫Σbθ|f(a)|∫Σ−aΣ−hz−aΦ(σ+hz)(a+σ)ldσdadμ(z)≤∫ηθzl+1∫Σbθ|f(a)|al∫Σ−aΣ−hz−aΦ(σ+hz)dσdadμ(z)≤θlsup|I|=hθ∫IΦ(a)da |
which is small when
(C4)=∫ηΣ−hθΣsl∫ηs+hΣ∫s+hzszΦ(s+hz−a)|f(a)|dadμ(z)ds=∫ηθ+hΣ∫zΣ−hθΣsl∫s+hzszΦ(s+hz−a)|f(a)|dadsdμ(z)=∫ηθ+hΣ∫zΣ−hθΣsl∫0−hzΦ(hz+a′)|f(sz−a′)|da′dsdμ(z)=∫ηθ+hΣ∫0−hzΦ(hz+a′)∫zΣ−hθΣ|f(sz−a′)|sldsda′dμ(z)=∫ηθ+hΣzl+1∫0−hzΦ(hz+a′)∫Σ−hz−a′θΣz−a′|f(σ)|(σ+a′)ldσda′dμ(z)≤∫ηθ+hΣzl+1∫0−hzΦ(hz+a′)da′dμ(z)≤θl(1−Ψ(hθ)), |
and the continuity of
(B)=∫θΣθΣ−h|∫s+hΣθ∫ΣbθΦ(s+hz−a)f(a)dadμ(z)+∫ηs+hΣ∫s+hzbθΦ(s+hz−a)f(a)dadμ(z)−∫ηθ∫szbθΦ(sz−a)f(a)dadμ(z)|slds≤∫ηθ∫Σbθ|f(a)|∫θΣθΣ−h[Φ(s+hz−a)+Φ(sz−a)]sldsdadμ(z)≤∫ηθzl+1∫Σbθ|f(a)|al∫θΣz−aθΣ−hz−a[Φ(σ+hz)+Φ(σ)]dσdadμ(z)≤2θlsup|I|=hθ∫IΦ(a)da |
and again the last term vanishes as
∫αbθ|TΣf(s)|slds |
≤∫αbθsl∫ηθ∫szbθΦ(sz−a)|f(a)|dadμ(z)ds≤∫ηθ∫bθzbθ|f(a)|∫αbθΦ(sz−a)sldsdadμ(z)+∫ηθ∫αzbθz|f(a)|∫αzaΦ(sz−a)sldsdadμ(z)≤∫ηθzl+1∫bθzbθ(Ψ(bθz−a)−Ψ(αz−a))|f(a)|aldazdμ(z)+∫ηθ∫αzbθz(1−Ψ(αz−a))|f(a)|aldazdμ(z)≤θl(1−Ψ(α−bθθ)), | (16) |
since for
As done before, we choose a
∫Σβ|TΣf(s)|slds≤∫ηθ∫Σbθ|f(a)|∫ΣβΦ(sz−a)sldsdadμ(z)≤∫ηθzl+1∫Σbθ|f(a)|al∫Σz−aβz−aΦ(σ)dσdadμ(z)≤θlsup|I|=Σ−βθ∫IΦ(a)da, | (17) |
which is small when
We have checked the assumptions of Theorem 3.3 for the family
To prove the irreducibility of the operator
TΣf(s)={∫sηbθf(a)∫ηθΦ(sz−a)dμ(z)da+∫sθsηf(a)∫saθΦ(sz−a)dμ(z)da,bθ≤s<θΣ,∫sηbθf(a)∫ηθΦ(sz−a)dμ(z)da+∫Σsηf(a)∫saθΦ(sz−a)dμ(z)da,θΣ≤s≤ηΣ,∫Σbθf(a)∫ηθΦ(sz−a)dμ(z)da,ηΣ<s≤Σ. |
Lemma 3.5. Let
Proof. Let
TΣfω(s)≥∫s0+ζs0∫θ+ξθΦ(sz−a)dμ(z)fω(a)da. |
For
Proof of Proposition 1. Lemma 3.4 shows that the set
We now want to show that up to a subsequence,
Proposition 2. Under hypotheses (2)- (5) there exists a nonnegative and normalized fixed point
f∈L1(R+,(sk+sl)ds) |
for all
First, we will show that the sequence
Lemma 3.6. If
1−Ψ((1η−1)Σ)≤ρΣ≤1−Ψ(Σθ−bθ). | (18) |
Proof. Integrating the equality
ρΣ∫ΣbθfΣ(s)ds=∫θΣbθ∫ηθ∫szbθΦ(sz−a)f(a)dadμ(z)ds=:(A)+∫ηΣθΣ∫sΣθ∫ΣbθΦ(sz−a)f(a)dadμ(z)ds=:(B)+∫ηΣθΣ∫ηsΣ∫szbθΦ(sz−a)f(a)dadμ(z)ds=:(C)+∫ΣηΣ∫ηθ∫ΣbθΦ(sz−a)f(a)dadμ(z)ds=:(D) |
(A)=∫ηθ∫bθzbθfΣ(a)∫θΣbθzΦ(sz−a)dsdadμ(z)+∫ηθ∫θΣzbθzfΣ(a)∫θΣzaΦ(sz−a)dsdadμ(z)=∫ηθz∫bθzbθfΣ(a)[Ψ(bθz−a)−Ψ(θΣz−a)]dadμ(z)+∫ηθz∫θΣzbθzfΣ(a)[1−Ψ(θΣz−a)]dadμ(z)(B)=∫ηθfΣ(a)∫Σbθ∫ηΣzΣΦ(sz−a)dsdadμ(z)=∫ηθz∫ΣbθfΣ(a)[Ψ(Σ−a)−Ψ(ηΣz−a)]dadμ(z) |
(C)=∫ηθ∫θΣzbθfΣ(a)∫zΣθΣΦ(sz−a)dsdadμ(z)+∫ηθ∫ΣθΣzfΣ(a)∫zΣzaΦ(sz−a)dsdadμ(z)=∫ηθz∫θΣzbθfΣ(a)[Ψ(θΣz−a)−Ψ(Σ−a)]dadμ(z)+∫ηθz∫ΣθΣzfΣ(a)[1−Ψ(Σ−a)]dadμ(z)(D)=∫ηθ∫ΣbθfΣ(a)∫ΣηΣΦ(sz−a)dsdadμ(z)=∫ηθz∫ΣbθfΣ(a)[Ψ(ηΣz−a)−Ψ(Σz−a)]dadμ(z) |
Then notice that for
bθz−a≤bθz−bθ=bθ(1z−1)≤bθ(1θ−1)=b, |
so as in the computations leading to (16),
ρΣ∫ΣbθfΣ(s)ds=∫ΣbθfΣ(s)ds−∫ηθz∫ΣbθΨ(Σz−a)fΣ(a)dadμ(z). | (19) |
Using the fact that the function
Now we show that up to a subsequence,
Σ0:=inf{Σ>max(11−θb,1) such that ρΣ>12}. |
Lemma 3.7. Under hypotheses (2), (3), (4) and (5), the set of eigenfunctions
Proof. Let
‖τhfΣ−fΣ‖L1(ω,(sk+sl)ds)≤2‖τhTΣfΣ−TΣfΣ‖L1(ω,(sk+sl)ds)≤2(βk+αl)‖τhTΣfΣ−TΣfΣ‖L1([α,β])≤2(βk+αl)‖τhTΣfΣ−TΣfΣ‖L1([α,Σ]). |
The last quantity is small when
‖fΣ‖L1((bθ,α),(sk+sl)ds)=1ρΣ∫αbθTΣfΣ(s)(sk+sl)ds≤2∫αbθTΣfΣ(s)slds+2αk∫αbθTΣfΣ(s)ds≤2θl(1−Ψ(α−bθθ))+2αk(1−Ψ(α−bθθ))≤2(θl+αk)(1−Ψ(α−bθθ)) |
which is again independent of
ρΣ∫ΣβfΣ(a)da=∫θΣβTΣfΣ(a)da+∫ηΣθΣTΣfΣ(a)da+∫ΣηΣTΣfΣ(a)da. |
For the first integral, we compute
∫θΣβTΣfΣ(a)da=∫ηθz∫βzbθ[Ψ(βz−a)−Ψ(θΣz−a)]fΣ(a)dadμ(z)+∫ηθz∫θΣzβz[1−Ψ(θΣz−a)]fΣ(a)dadμ(z). |
The two other integrals correspond to the integrals
ρΣ∫ΣβfΣ(a)da=∫ηθz∫βzbθΨ(βz−a)fΣ(a)dadμ(z)+∫ηθz∫ΣβzfΣ(a)dadμ(z)−∫ηθz∫ΣbθΨ(Σz−a)fΣ(a)dadμ(z). |
We deal with the last integral using (19) and obtain after interverting integrals
ρΣ∫ΣβfΣ(a)da=∫βηbθfΣ(a)∫ηθzΨ(βz−a)dμ(z)da+∫βθβηfΣ(a)∫βaθzΨ(βz−a)dμ(z)da+∫βθβηfΣ(a)∫ηβazdμ(z)da+∫ΣβθfΣ(a)da+ρΣ∫ΣbθfΣ(a)da−∫ΣbθfΣ(a)da⟺∫βηbθfΣ(a)da=∫βηbθfΣ(a)∫ηθzΨ(βz−a)dμ(z)da+∫βθβηfΣ(a)∫βaθzΨ(βz−a)dμ(z)da+ρΣ∫βbθfΣ(a)da−∫βθβηfΣ(a)∫βaθzdμ(z)da⟺∫βηβfΣ(a)∫ηθz[1−Ψ(βz−a)]dμ(z)da+(1−ρΣ)∫βbθfΣ(a)da+∫βθβηfΣ(a)∫βaθz[1−Ψ(βz−a)]dμ(z)da=∫βbθfΣ(a)∫ηθzΨ(βz−a)dμ(z)da |
Since
∫rββfΣ(a)∫ηθz[1−Ψ(βz−a)]dμ(z)da≤∫βbθfΣ(a)∫ηθzΨ(βz−a)dμ(z)da, |
then
(1−Ψ((1η−r)β))∫rββfΣ(a)da≤Ψ((1η−1)β), |
and finally
∫rββfΣ(a)(al+ak)da≤(βl+(rβ)k)Ψ((1η−1)β)(1−Ψ((1η−r)β))≤4(rβ)kΨ((1η−1)β) |
for
∫∞βfΣ(s)(sk+sl)ds=∞∑j=0∫rj+1βrjβfS(s)(sk+sl)ds≤4rk∞∑j=0(rjβ)kΨ((1η−1)rjβ) |
≤4Crk∞∑j=0(rjβ)k((1η−1)rjβ)−k0≤Ck,k0,η,rβk0−k |
due to hypothesis (5), for
We are now ready to prove the existence and uniqueness of a fixed point for the operator
Proof of Proposition 2. We have proved in Lemma 3.7 that the set of eigenfunctions
‖f−Tf‖L1(R+,(sk+sl)ds)≤‖f−fΣ‖L1(R+,(sk+sl)ds)+(1−ρΣ)+‖TΣfΣ−Tf‖L1(R+,(sk+sl)ds). |
The first term of the right-hand side tends to zero as
‖TΣfΣ−Tf‖L1(R+,(sk+sl)ds)≤‖TΣfΣ−TfΣ‖L1(R+,(sk+sl)ds)⏟=0+‖T(f−fΣ)‖L1(R+,(sk+sl)ds)≤‖f−fΣ‖L1(R+,(sk+sl)ds) |
due to Lemma 3.2 and to the continuity of
To prove uniqueness of the fixed point, we consider
f(s)=∫ηθΦ∗f(sz)dμ(z). | (20) |
Since
L[f−f1](y)=∫ηθL[f−f1](zy)L[Φ](zy)zdμ(z). | (21) |
The Laplace transform
L[f−f1](0)=∫∞0f(s)ds−∫∞0f1(s)ds=0. |
We now define the functions
¯L(y)=supx∈[0,y]L[f−f1](x) and L_(y)=infx∈[0,y]L[f−f1](x). |
By continuity in
∀y≥0,¯L(y)≥0, L_(y)≤0. |
From (21), we obtain the inequality
L[f−f1](y)≤¯L(ηy)∫ηθL[Φ](zy)zdμ(z)≤¯L(ηy), |
since
L[f−f1](x)≤¯L(ηx)≤¯L(ηy), |
from which we deduce
¯L(y)≤¯L(ηy). | (22) |
Iterating (22), we obtain for all
¯L(y)≤¯L(ηjy). |
Letting
It remains to prove that
We are now ready to prove the main theorem of the paper.
Proof of Theorem 1.1. Combining Lemma 2.1 and Proposition 2, we construct a solution to (11) using
M(a,s):=ψ(a)(a+s)2f(s). |
It remains to prove uniqueness of the solution in the appropriate space. This solution belongs to
∫∞bθ∫∞0M(a,s)(1+s2)dads=∫∞bθ∫∞01(a+s)2f(s)Ψ(a)dads+∫∞bθ∫∞0s2(a+s)2f(s)Ψ(a)dads≤∫∞bθf(s)s−2∫∞0Ψ(a)dads+∫∞bθf(s)∫∞0Ψ(a)dads=‖f‖L1((bθ,∞),(1+s−2)ds)<∞ |
because
M1(a,s)=Ψ(a)(a+s)2f1(s). |
For
∫∞0f1(s)ds=1β−α∫∞0∫βα(a+s)2Ψ(a)M1(a,s)dads≤2(β2+1)(β−α)Ψ(β)‖M1‖L1(R+,(1+s2)ds), |
and this ensures that
Now that we have solved the eigenvalue problem, we would like to characterize the asymptotic behaviour of a solution
|n(t,a,x)|≤CetN(a,x),t≥0, x>a>0. | (23) |
It is usually ensured by the hypothesis
H[n]=∫∞bθ∫x−bθ0xN(a,x)H(n(a,x)N(a,x))dadx |
which satisfies the following entropy property.
Proposition 3. If
ddtH[n(t,⋅,⋅)e−t]=−D[n(t,⋅,⋅)e−t], | (24) |
with
D[n]=∫∞bθx2N(0,x)[∫ηθ∫xz−bθ0H(n(a,xz)N(a,xz))dνx(a,z)−H(∫ηθ∫xz−bθ0n(a,xz)N(a,xz)dνx(a,z))]dx |
where
Before proving this proposition, we make a remark about the conservative problem (i.e. when only one daughter out of two is kept after division). In this case, the dominant eigenvalue is
∂∂a(x2N)+∂∂x(x2N)=−x2BN, | (25) |
which might also be obtained multiplying (8a) by
Proof. Easy computations lead to
∂∂tne−tN+x∂∂ane−tN+x∂∂xne−tN=0, |
where
∂∂t(xNH(ne−tN))+∂∂a(x2NH(ne−tN))+∂∂x(x2NH(ne−tN))=−x2BNH(ne−tN), | (26) |
and integrating (26) over
ddt∬(bθ,∞)×(0,x−bθ)xNH(ne−tN)dadx=∫∞bθx2N(0,x)H(n(t,0,x)e−tN(0,x))dx−∫∞bθx2N(x−bθ,x)H(n(t,x−bθ,x)e−tN(x−bθ,x))dx+∫∞0(a+bθ)2N(a,a+bθ)H(n(t,a,a+bθ)e−tN(a,a+bθ))da−∫∞bθ∫x−bθ0x2BNH(ne−tN)dadx=∫∞bθx2N(0,x)H(e−tN(0,x)∫ηθ∫xz−bθ0B(a)n(t,a,xz)dadμ(z)z2)dx−2∫ηθ∫∞bθ∫x−bθ0x2BNH(ne−tN)dadxzdμ(z)=∫∞bθx2N(0,x)H(∫ηθ∫xz−bθ0n(t,a,xz)e−tN(a,xz)dνx(a,z))dx−2∫ηθ∫bθzbθ∫xz−bθ0x2B(a)N(a,xz)H(n(t,a,xz)e−tN(a,xz))dadxdμ(z)z2−2∫ηθ∫∞bθ∫xz−bθ0x2B(a)N(a,xz)H(n(t,a,xz)e−tN(a,xz))dadxdμ(z)z2=∫∞bθx2N(0,x)[H(∫ηθ∫xz−bθ0n(t,a,xz)e−tN(a,xz)dνx(a,z))−∫ηθ∫xz−bθ0H(n(t,a,xz)e−tN(a,xz))dνx(a,z)]dx, |
since for
Appropriate choices of the function
λj=1+2ijπlog2,Nj(a,x)=x1−λjN(a,x),ϕj(a,x)=xλj, |
so we expect a behavior as in [2], i.e. the convergence of
∑j∈Z⟨n0,ϕj⟩e2ijπtlog2Nj(a,x), |
where
We have proved the existence and uniqueness of a solution of the eigenproblem (8) in the special yet biologically relevant case of linear growth rate with a self-similar fragmentation kernel. Hypotheses on both this kernel and the division rate are fairly general.
As possible future work we can imagine to extend the result to general growth rates. In this case the Perron eigenvalue is not explicit and it has to be determined in the same time as the eigenfunction, as in [26,12,6]. If we denote by
Pλ(s)=∫10e−λ∫szsdug(u)(Φ∗Pλ)(sz)dμ(z)z |
with
N:(a,x)↦Ψ(a)g(x)e−λ∫x0dαg(α)Pλ(x−a). |
Additionally for nonlinear growth rates, the function
The other natural continuation of the present work is the proof of the well-posedness and the long-time behavior of the evolution equation, as in [26,12]. To do so one can take advantage of the General Relative Entropy as in [14,4,2] or use general spectral methods [28,16].
The authors are very grateful to Marie Doumic for having suggested them the problem treated in this paper, and for the many fruitful discussions.
[1] |
Purwanto SK, Sinaga O (2021) Exploring the relationship between fossil fuel energy consumption, renewable energy consumption and human capital index: A study from Thailand. Int J Energy Econ Policy 11: 106–113. https://doi.org/10.32479/ijeep.10910 doi: 10.32479/ijeep.10910
![]() |
[2] |
Ashokkumar V, Venkatkarthick R, Jayashree S, et al. (2022) Recent advances in lignocellulosic biomass for biofuels and value-added bioproducts - A critical review. Bioresour Technol 344: 126195. https://doi.org/10.1016/j.biortech.2021.126195 doi: 10.1016/j.biortech.2021.126195
![]() |
[3] |
Algayyim SJM, Yusaf T, Hamza NH, et al. (2022) Sugarcane Biomass as a Source of Biofuel for Internal Combustion Engines (Ethanol and Acetone-Butanol-Ethanol): A Review of Economic Challenges. Energies 15. https://doi.org/10.3390/en15228644 doi: 10.3390/en15228644
![]() |
[4] |
Ruslan K, Prasetyo OR (2021) Policy Paper No. 42 Plantation Crop Productivity: Coffee, Sugarcane, and Cocoa. Cent Indones Policy Stud. https://doi.org/10.35497/349327 doi: 10.35497/349327
![]() |
[5] |
Nugraha MG, Mozasurya ED, Hidayat M, et al. (2023) Evaluation of combustion characteristics in biomass residues open burning. Mater Today Proc 87: 45–50. https://doi.org/10.1016/j.matpr.2023.02.098 doi: 10.1016/j.matpr.2023.02.098
![]() |
[6] |
Choi H, Kim YT, Tsang YF, et al. (2023) Integration of thermochemical conversion processes for waste-to-energy: A review. Korean J Chem Eng 40: 1815–1821. https://doi.org/10.1007/s11814-023-1494-z doi: 10.1007/s11814-023-1494-z
![]() |
[7] |
Yaashikaa PR, Kumar PS, Varjani S, et al. (2020) A critical review on the biochar production techniques, characterization, stability and applications for circular bioeconomy. Biotechnol Reports 28: e00570. https://doi.org/10.1016/j.btre.2020.e00570 doi: 10.1016/j.btre.2020.e00570
![]() |
[8] |
Charusiri W, Vitidsant T (2018) Biofuel production via the pyrolysis of sugarcane (Saccharum officinarum L.) leaves: Characterization of the optimal conditions. Sustain Chem Pharm 10: 71–78. https://doi.org/10.1016/j.scp.2018.09.005 doi: 10.1016/j.scp.2018.09.005
![]() |
[9] |
Conag AT, Villahermosa JER, Cabatingan LK, et al. (2018) Energy densification of sugarcane leaves through torrefaction under minimized oxidative atmosphere. Energy Sustain Dev 42. https://doi.org/10.1016/j.esd.2017.11.004 doi: 10.1016/j.esd.2017.11.004
![]() |
[10] |
Toscano Miranda N, Lopes Motta I, Maciel Filho R, et al. (2021) Sugarcane bagasse pyrolysis: A review of operating conditions and products properties. Renew Sustain Energy Rev 149: 111394. https://doi.org/10.1016/j.rser.2021.111394 doi: 10.1016/j.rser.2021.111394
![]() |
[11] |
Alchalil, Setiawan A, Juwaini, et al. (2021) Effect of Densification Pressure on Physical and Combustion Properties of Binderless Briquettes Made from Rice-Husk and Coffee-Pulp. Lect Notes Mech Eng 1–8. https://doi.org/10.1007/978-981-16-0736-3_1 doi: 10.1007/978-981-16-0736-3_1
![]() |
[12] | Rifanida, Riskina S, Setiawan A, et al. (2023) The Effect of Varying Torrefaction Temperature on the Physical and Mechanical Properties of Briquettes Made from King Grass. 21: 1–5. |
[13] | Aryati T, Williansyah A, Zulnazri, et al. (2021) Slow Pyrolysis of Areca-Nut Fibres in a-Pilot Scale Batch Reactor, Proceedings of the 2nd International Conference on Experimental and Computational Mechanics in Engineering, 263–270. https://doi.org/10.1007/978-981-16-0736-3_26 |
[14] | Standar Nasional Indonesia (1995) Arang Aktif Teknis SNI 06-3730-1995. |
[15] |
Sun J, He F, Pan Y, et al. (2017) Effects of pyrolysis temperature and residence time on physicochemical properties of different biochar types. Acta Agric Scand Sect B Soil Plant Sci 67: 12–22. https://doi.org/10.1080/09064710.2016.1214745 doi: 10.1080/09064710.2016.1214745
![]() |
[16] |
Kakom SM, Abdelmonem NM, Ismail IM, et al. (2023) Activated Carbon from Sugarcane Bagasse Pyrolysis for Heavy Metals Adsorption. Sugar Tech 25: 619–629. https://doi.org/10.1007/s12355-022-01214-3 doi: 10.1007/s12355-022-01214-3
![]() |
[17] |
Hongthong S, Sangsida W, Wongcharee S, et al. (2024) Enhanced Biochar Production via Co-Pyrolysis of Biomass Residual with Plastic Waste after Recycling Process. Int J Chem Eng 2024: 1–17. https://doi.org/10.1155/2024/1176275 doi: 10.1155/2024/1176275
![]() |
[18] |
Qazi Sohaib AM, Younas M (2017) Fast pyrolysis of sugarcane bagasse: Effect of pyrolysis conditions on final product distribution and properties. Energy Sources, Part A Recover Util Environ Eff 39: 184–190. https://doi.org/10.1080/15567036.2016.1212292 doi: 10.1080/15567036.2016.1212292
![]() |
[19] | Pecha MB, Garcia-Perez M (2020) Chapter 29 - Pyrolysis of lignocellulosic biomass: oil, char, and gas, In: Dahiya A (Ed.), Bioenergy (Second Edition), Academic Press, 581–619. https://doi.org/10.1016/B978-0-12-815497-7.00029-4 |
[20] |
Kawamoto H (2017) Lignin pyrolysis reactions. J Wood Sci 63: 117–132. https://doi.org/10.1007/s10086-016-1606-z doi: 10.1007/s10086-016-1606-z
![]() |
[21] |
Zhao C, Jiang E, Chen A (2017) Volatile production from pyrolysis of cellulose, hemicellulose and lignin. J Energy Inst 90: 902–913. https://doi.org/10.1016/j.joei.2016.08.004 doi: 10.1016/j.joei.2016.08.004
![]() |
[22] |
Zhao L, Sun Z-F, Pan X-W, et al. (2023) Sewage sludge derived biochar for environmental improvement: Advances, challenges, and solutions. Water Res X 18: 100167. https://doi.org/10.1016/j.wroa.2023.100167 doi: 10.1016/j.wroa.2023.100167
![]() |
[23] |
Trippe KM, Griffith SM, Banowetz GM, et al. (2015) Changes in Soil Chemistry following Wood and Grass Biochar Amendments to an Acidic Agricultural Production Soil. Agron J 107: 1440–1446. https://doi.org/10.2134/agronj14.0593 doi: 10.2134/agronj14.0593
![]() |
[24] |
Al-Rumaihi A, Shahbaz M, Mckay G, et al. (2022) A review of pyrolysis technologies and feedstock: A blending approach for plastic and biomass towards optimum biochar yield. Renew Sustain Energy Rev 167: 112715. https://doi.org/10.1016/j.rser.2022.112715 doi: 10.1016/j.rser.2022.112715
![]() |
[25] |
Yang H, Jiang J, Zhang B, et al. (2021) Experimental study on light volatile products from thermal decomposition of lignin monomer model compounds: effect of temperature, residence time and methoxyl group. RSC Adv 11: 37067–37082. https://doi.org/10.1039/D1RA06743E doi: 10.1039/D1RA06743E
![]() |
[26] |
Herrera K, Morales LF, Tarazona NA, et al. (2022) Use of Biochar from Rice Husk Pyrolysis: Part A: Recovery as an Adsorbent in the Removal of Emerging Compounds. ACS Omega 7: 7625–7637. https://doi.org/10.1021/acsomega.1c06147 doi: 10.1021/acsomega.1c06147
![]() |
[27] |
Reyes L, Abdelouahed L, Mohabeer C, et al. (2021) Energetic and exergetic study of the pyrolysis of lignocellulosic biomasses, cellulose, hemicellulose and lignin. Energy Convers Manag 244: 114459. https://doi.org/10.1016/j.enconman.2021.114459 doi: 10.1016/j.enconman.2021.114459
![]() |
[28] |
Vilas-Boas ACM, Tarelho LAC, Oliveira HSM, et al. (2024) Valorisation of residual biomass by pyrolysis: influence of process conditions on products. Sustain Energy Fuels 8: 379–396. https://doi.org/10.1039/D3SE01216F doi: 10.1039/D3SE01216F
![]() |
[29] |
Maj G (2018) Emission factors and energy properties of agro and forest biomass in aspect of sustainability of energy sector. Energies 11. https://doi.org/10.3390/en11061516 doi: 10.3390/en11061516
![]() |
[30] |
Yang X, Kang K, Qiu L, et al. (2020) Effects of carbonization conditions on the yield and fixed carbon content of biochar from pruned apple tree branches. Renew Energy 146: 1691–1699. https://doi.org/10.1016/j.renene.2019.07.148 doi: 10.1016/j.renene.2019.07.148
![]() |
[31] |
Conesa JA, Sánchez NE, Garrido MA, et al. (2016) Semivolatile and Volatile Compound Evolution during Pyrolysis and Combustion of Colombian Coffee Husk. Energy and Fuels 30: 7827–7833. https://doi.org/10.1021/acs.energyfuels.6b00791 doi: 10.1021/acs.energyfuels.6b00791
![]() |
[32] |
Gruss I, Twardowski JP, Latawiec A, et al. (2019) Risk assessment of low-temperature biochar used as soil amendment on soil mesofauna. Environ Sci Pollut Res 26: 18230–18239. https://doi.org/10.1007/s11356-019-05153-7 doi: 10.1007/s11356-019-05153-7
![]() |
[33] |
Nurazzi NM, Asyraf MRM, Rayung M, et al. (2021) Thermogravimetric Analysis Properties of Cellulosic Natural Fiber Polymer Composites: A Review on Influence of Chemical Treatments. Polymers (Basel) 13. https://doi.org/10.3390/polym13162710 doi: 10.3390/polym13162710
![]() |
[34] | Mulabagal V, Baah D, Egiebor N, et al. (2020) Biochar from Biomass: A Strategy for Carbon Dioxide Sequestration, Soil Amendment, Power Generation, and CO2 Utilization. |
[35] |
Adeniyi AG, Odetoye TE, Titiloye J, et al. (2019) A Thermodynamic Study of Rice Husk (Oryza Sativa) Pyrolysis. Eur J Sustain Dev Res 3: 1–10. https://doi.org/10.29333/ejosdr/5830 doi: 10.29333/ejosdr/5830
![]() |
[36] |
Bhavsar PA, Jagadale MH, Khandetod YP, et al. (2018) Proximate Analysis of Selected Non Woody Biomass. Int J Curr Microbiol Appl Sci 7: 2846–2849. https://doi.org/10.20546/ijcmas.2018.709.353 doi: 10.20546/ijcmas.2018.709.353
![]() |
[37] |
Zama EF, Zhu Y-G, Reid BJ, et al. (2017) The role of biochar properties in influencing the sorption and desorption of Pb(Ⅱ), Cd(Ⅱ) and As(Ⅲ) in aqueous solution. J Clean Prod 148: 127–136. https://doi.org/10.1016/j.jclepro.2017.01.125 doi: 10.1016/j.jclepro.2017.01.125
![]() |
[38] |
Das P, Ganesh A, Wangikar P (2004) Influence of pretreatment for deashing of sugarcane bagasse on pyrolysis products. Biomass and Bioenergy 27: 445–457. https://doi.org/10.1016/j.biombioe.2004.04.002 doi: 10.1016/j.biombioe.2004.04.002
![]() |
[39] |
Erdogan E, Atila B, Mumme J, et al. (2015) Characterization of products from hydrothermal carbonization of orange pomace including anaerobic digestibility of process liquor. Bioresour Technol 196: 35–42. https://doi.org/10.1016/j.biortech.2015.06.115 doi: 10.1016/j.biortech.2015.06.115
![]() |
[40] |
Rä isä nen U, Pitkä nen I, Halttunen H, et al. (2003) Formation of the main degradation compounds from arabinose, xylose, mannose and arabinitol during pyrolysis. J Therm Anal Calorim 72: 481–488. https://doi.org/10.1023/A:1024557011975 doi: 10.1023/A:1024557011975
![]() |
[41] |
Tsai WT, Lee MK, Chang YM (2006) Fast pyrolysis of rice straw, sugarcane bagasse and coconut shell in an induction-heating reactor. J Anal Appl Pyrol 76: 230–237. https://doi.org/10.1016/j.jaap.2005.11.007 doi: 10.1016/j.jaap.2005.11.007
![]() |
[42] |
Hu X, Gholizadeh M (2019) Biomass pyrolysis: A review of the process development and challenges from initial researches up to the commercialisation stage. J Energy Chem 39: 109–143. https://doi.org/10.1016/j.jechem.2019.01.024 doi: 10.1016/j.jechem.2019.01.024
![]() |
[43] |
Bhavaniramya S, Vishnupriya S, Al-Aboody MS, et al. (2019) Role of essential oils in food safety: Antimicrobial and antioxidant applications. Grain Oil Sci Technol 2: 49–55. https://doi.org/10.1016/j.gaost.2019.03.001 doi: 10.1016/j.gaost.2019.03.001
![]() |
1. | Bertrand Cloez, Benoîte de Saporta, Tristan Roget, Long-time behavior and Darwinian optimality for an asymmetric size-structured branching process, 2021, 83, 0303-6812, 10.1007/s00285-021-01695-y | |
2. | Pierre Gabriel, Hugo Martin, Periodic asymptotic dynamics of the measure solutions to an equal mitosis equation, 2022, 5, 2644-9463, 275, 10.5802/ahl.123 | |
3. | Katarzyna Pichór, Ryszard Rudnicki, Cell cycle length and long‐time behavior of an age‐size model, 2022, 45, 0170-4214, 5797, 10.1002/mma.8139 | |
4. | Mingtao Xia, Chris D. Greenman, Tom Chou, PDE Models of Adder Mechanisms in Cellular Proliferation, 2020, 80, 0036-1399, 1307, 10.1137/19M1246754 | |
5. | Ignacio Madrid, Exponential Ergodicity of a Degenerate Age-Size Piecewise Deterministic Process, 2023, 187, 0167-8019, 10.1007/s10440-023-00597-z |