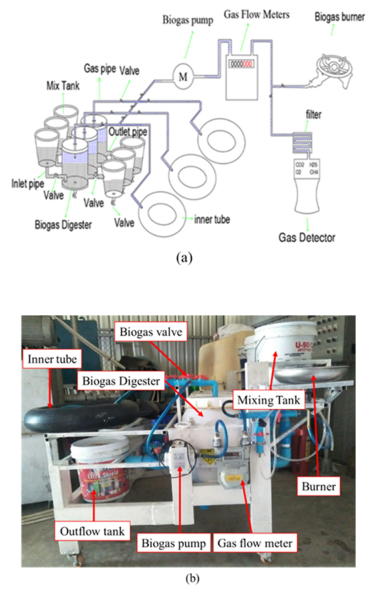
Sustainable waste management and renewable energy are crucial, particularly in Cambodia, where environmental concerns are rising. Organic waste, including cow dung (CD), pig dung (PD), and vegetable waste (VW), offers a promising source for biogas production and clean and renewable energy. However, the efficiency of this biogas production depends on the type of waste and processing conditions. We evaluated the quality, composition, and volume of biogas generated from organic waste, specifically CD, PD, and VW. Three experimental conditions were tested: 10 kg of CD with 10 liters of water, 5 kg of CD mixed with 5 kg of PD and 10 liters of water, and 5 kg of CD mixed with 5 kg of VW and 10 liters of water. As a result, the conversion of pure CD yielded a total volume of biogas up to 0.391 m3, with a methane percentage (CH4) of 69.18%. The CD mixed with PD, which produced only 0.362 m3 of biogas with a CH4 of 65.51%, and CD mixed with VW, which yielded a total biogas volume of only 0.319 m3 with a CH4 of 68.17%. From the result, it can be concluded that the bioconversion of pure CD into biogas was the most efficient compared to the other two conditions.
Citation: Sokna San, Seyla Heng, Vanna Torn, Chivon Choeung, Horchhong Cheng, Seiha Hun, Chanmoly Or. Production of biogas from co-substrates using cow dung, pig dung, and vegetable waste: A case study in Cambodia[J]. AIMS Energy, 2024, 12(5): 1010-1024. doi: 10.3934/energy.2024047
[1] | Muhammad Rashed Al Mamun, Anika Tasnim, Shahidul Bashar, Md. Jasim Uddin . Potentiality of biomethane production from slaughtered rumen digesta for reduction of environmental pollution. AIMS Energy, 2018, 6(5): 658-672. doi: 10.3934/energy.2018.5.658 |
[2] | Yonael Mezmur, Wondwossen Bogale . Simulation and experimental analysis of biogas upgrading. AIMS Energy, 2019, 7(3): 371-381. doi: 10.3934/energy.2019.3.371 |
[3] | Mikael Lantz, Emma Kreuger, Lovisa Björnsson . An economic comparison of dedicated crops vs agricultural residues as feedstock for biogas of vehicle fuel quality. AIMS Energy, 2017, 5(5): 838-863. doi: 10.3934/energy.2017.5.838 |
[4] | Sebastian Auburger, Richard Wüstholz, Eckart Petig, Enno Bahrs . Biogas digestate and its economic impact on farms and biogas plants according to the upper limit for nitrogen spreading—the case of nutrient-burdened areas in north-west Germany. AIMS Energy, 2015, 3(4): 740-759. doi: 10.3934/energy.2015.4.740 |
[5] | Tsepo Sechoala, Olawale Popoola, Temitope Ayodele . Economic and environmental assessment of electricity generation using biogas and heat energy from municipal solid waste: A case study of Lesotho. AIMS Energy, 2023, 11(2): 337-357. doi: 10.3934/energy.2023018 |
[6] | Gal Hochman, Shisi Wang, Qing Li, Paul D. Gottlieb, Fuqing Xu, Yebo Li . Cost of organic waste technologies: A case study for New Jersey. AIMS Energy, 2015, 3(3): 450-462. doi: 10.3934/energy.2015.3.450 |
[7] | Robinson J. Tanyi, Muyiwa S Adaramola . Bioenergy potential of agricultural crop residues and municipal solid waste in Cameroon. AIMS Energy, 2023, 11(1): 31-46. doi: 10.3934/energy.2023002 |
[8] | Constantinos S. Psomopoulos . Residue Derived Fuels as an Alternative Fuel for the Hellenic Power Generation Sector and their Potential for Emissions ReductionConstantinos S. Psomopoulos. AIMS Energy, 2014, 2(3): 321-341. doi: 10.3934/energy.2014.3.321 |
[9] | Juan A. Conesa, A. Domene . Synthesis gas production from various biomass feedstocks. AIMS Energy, 2013, 1(1): 17-27. doi: 10.3934/energy.2013.1.17 |
[10] | Muhammad Rashed Al Mamun, Shuichi Torii . Comparative Studies on Methane Upgradation of Biogas by Removing of Contaminant Gases Using Combined Chemical Methods. AIMS Energy, 2015, 3(3): 255-266. doi: 10.3934/energy.2015.3.255 |
Sustainable waste management and renewable energy are crucial, particularly in Cambodia, where environmental concerns are rising. Organic waste, including cow dung (CD), pig dung (PD), and vegetable waste (VW), offers a promising source for biogas production and clean and renewable energy. However, the efficiency of this biogas production depends on the type of waste and processing conditions. We evaluated the quality, composition, and volume of biogas generated from organic waste, specifically CD, PD, and VW. Three experimental conditions were tested: 10 kg of CD with 10 liters of water, 5 kg of CD mixed with 5 kg of PD and 10 liters of water, and 5 kg of CD mixed with 5 kg of VW and 10 liters of water. As a result, the conversion of pure CD yielded a total volume of biogas up to 0.391 m3, with a methane percentage (CH4) of 69.18%. The CD mixed with PD, which produced only 0.362 m3 of biogas with a CH4 of 65.51%, and CD mixed with VW, which yielded a total biogas volume of only 0.319 m3 with a CH4 of 68.17%. From the result, it can be concluded that the bioconversion of pure CD into biogas was the most efficient compared to the other two conditions.
The global community has taken notice of green technology and ecological sustainability due to the increasing severity of worldwide environmental pollution and energy shortages. Renewable energy has been vital in electricity production [1]. The increasing energy demand in Cambodia has resulted in a greater dependence on imported fossil fuels, burdening the economy and worsening environmental concerns, including health issues and climate change. To address these difficulties, the development of efficient and affordable bioprocesses for biomass and biogas-based energy, such as bio-hydrogen and bioethanol, presents a favorable alternative. This strategy can assist Cambodia in diminishing its reliance on fossil fuels, advancing sustainable development, and granting rural communities the ability to utilize clean, renewable energy sources [2,3,4]. It is worth noting that biogas has resulted in health benefits such as lower indoor particulate emissions, improved sanitation, and increased agricultural productivity through the use of digester bio-slurry, environmental benefits such as lower greenhouse gas emissions and wood consumption, and reduced workload for women and children. Furthermore, while deforestation is frequently caused by households gathering tree branches, the transition to biogas also helps to relieve pressure on forest resources.
Biogas, derived from organic materials, is a valuable renewable energy source primarily composed of methane (CH4) and carbon dioxide (CO2), with variable levels of hydrogen sulphide (H2S) and moisture. Its composition varies based on the source, typically containing 45–70% methane, 30–40% carbon dioxide, and 1–15% nitrogen. Biogas is versatile, used for cooking, heating, and as a starting material for chemical and biochemical production, such as hydrogen and synthesis gas [5]. The Anaerobic Digestion (AD) method consists of four distinct phases. In the hydrolysis phase, enzymes break down large, insoluble polymer feedstocks into soluble substrates, including amino acids and sugars. During the acidogenesis phase, fatty acids, sugars, and amino acids are converted into ammonia, organic acids, hydrogen (H2), and carbon dioxide (CO2). Volatile fatty acids (VFAs) are also produced alongside CO2 and H2. The acetogenesis phase involves the degradation of VFAs into acetic acids, H2, and CO2, and the last stage, methanogenesis turns formaldehyde, acetate, and hydrogen into methane, CO2 and water [6]. Biogas offers great potential as a renewable energy source, capable of producing both heat and power [7]. It primarily consists of feedstock sources like industrial waste (organic waste from MSW), agricultural waste, aquatic biomass (algae), energy crops (such as maize and barley), and animal manure [8]. The International Energy Agency (IEA, 2020) anticipates a 50% increase in biogas production by 2040. Renewable biogas production from organic waste contributes to reducing methane emissions from landfills, thereby mitigating global warming [9]. Nonetheless, Anaerobic Digestion (AD) systems come with their challenges, including long hydraulic retention times, low methane production, and the need for hard-to-degrade substrates, resulting in higher volume and capital costs. To enhance anaerobic digestion efficiency and methane yield [10], it is essential to preprocess feedstock with slow biodegradability and complex structures before digestion, as lignocellulose biomass presents difficulties due to its structural and chemical complexity [11]. Improved air quality and hygienic conditions have been achieved in both urban and rural areas when organic wastes is used as the source for AD systems. To reduce Hydraulic Retention Time (HRT), the pre-treated slurry is implemented to readily digested by microbes. This process also generates methane, serving as a renewable energy source.
Researchers have explored the potential for biogas production from both mono-digestion and co-digestion of cow manure and other organic wastes, without and with treatment. Regarding on study, researchers focused on the biogas production from cow dung in a batch and semi-continuous mode at 53 ℃; it showed that the content of the methane was 47% [12]. Researchers have conducted several studies on biogas production from cow dung (CD) and food waste to investigate the biogas yield and the impact of hydraulic retention time [13,14,15,16]. In 2020, the production of biogas of vegetable waste (VW) and cow dung was conducted using the water displacement method under four different ratios. It showed that the ratio 1:1:2 of cow dung, VW, and water obtained better results compared to others [17]. From [18] the comparison of biogas production from CD and pig dung (PD) was conducted under mesophilic condition at the laboratory scales and the result showed that the pig manure obtained higher biogas volume. The comparison of biogas produced from wetland grass and cow manure are conducted for 45-days investigation. To improve the quality of biogas production, the Ca(OH)2, NaOH, and H2O are used to remove the H2S, which enhances the bio-methane production. It was observed that H2O, Ca(OH)2, and NaOH removed H2S from the biogas by 55.56, 98.75, and 98.89%, respectively. The Ca(OH)2, and NaOH increase methane production by 85.9, and 88.04% [19]. The review [20] highlighted the cavitation and electrolysis treatments, which are the methods for intensifying biogas production from waste. Despite the extensive research on biogas production from various organic wastes with or without pretreatment, no studies have specifically been conducted in the context of Cambodia. The existing literature lacks an analysis of how local conditions in Cambodia might affect biogas yields and the efficiency of co-digestion processes.
In developing countries, waste biomass is underutilized for solid biofuel production. For instance, from [21], selected Asian countries such as Vietnam, Cambodia, Bangladesh, Laos, Nepal, India, and Indonesia commonly use pig manure, cow manure, buffalo manure, and livestock manure as feedstock for small-scale biogas plants. Vietnam has constructed more than 100,000 household biogas plants [22]. According to [23], there are 28,110 biodigesters, equal to 6% of technical potential households in Cambodia, and most of the biodigesters use cow manure and pig manure. Specifically, in the context of Cambodia, several potential studies have been conducted on biomass and biogas. Some researchers focused on the potential of rice husk to generate electricity in Cambodia [24,25,26]. A study was conducted on the production and quality of biogas using cow manure in Cambodia, and the result showed that the average percentage of methane was around 52% and the average concentrations of hydrogen sulfide was around 390 to 604 ppm [27]. Other researchers have evaluated biogas production from water spinach combined with buffalo manure in Cambodia to determine the effect on methane production [28]. Although there are multiple studies regarding biogas production from 100% CD and combinations of CD with grass, vegetables, fruit, food waste, PD, and other waste, in Cambodia, the study of the combination of CD with PD or CD with VW is not reported despite the abundance of these substrates in this country.
In this paper, we investigate biogas production using co-substrates such as pure CD, CD mixed with PD, and CD mixed with VW. The anaerobic digesting method has received significant interest in both academic study and industrial applications, as previously stated. Nevertheless, it is important to mention that the literature does not include research on the feedstock substrates examined in this case. Despite the abundance of CD, PD, and VW in Cambodia, there has been no reported research into the production of biogas from these substrates. Therefore, our objective is to compare the biogas and methane levels produced from PD, CD, and VW in the context of Cambodia local conditions. In the experiments, we compare the production of biogas, and the energy levels achieved by boiling water using electricity and biogas from these materials.
In this research, we developed a biogas digester system by first draw a schematic that is intricately connected to a gas pipe, as shown in Figure 1(a). Our initial requirement entails a 50 L plastic container featuring four holes: A 40 mm diameter opening on the left and the bottom, a 45 mm hole on the upper right, and a 16 mm hole at the top. These openings are linked to a pipe connector (21", 49", 60") and a PVC pipe (21", 49", 60"), which respectively serve as the inlet, outlet, and gas conduits, respectively. The PVC pipe is subsequently connected to valve no. 60 to prevent any potential blockages. Valve no. 60 is further linked to pipe connector no. 60, a crucial component for slurry disposal. Additionally, valve no. 49 is connected to pipe connector 49, functioning as a mixing tank for the uniform mixing of manure and water, thereby inducing a chemical reaction. Several other valves serve as drainage points during system cleaning. To ensure the integrity of the connections and to prevent water and gas leakages, Scotch tape and glue are applied at the connection points. This interconnected furnace system, as depicted in Figure 1(b), is also seamlessly integrated with the Gas Detector for enhanced functionality.
In this research, conducted in Cambodia's lowland regions, we embarked on a unique endeavor to collect various organic materials, including pure cow dung, PD, and VW, sourced directly from households. It is worth mentioning that the cow dung and PD were primarily acquired from small-scale farms, which are often integral to the agricultural practices in the area. The VW was chopped into small pieces, as shown in Figure 2, and then mixed with CD and water in a 1:1:2 ratio, as specified in Table 1. The raw materials, cow dung, and PD were mixed with water according to the ratios specified in Table 1 using a blender to ensure a homogeneous mixture. The blended mixture was then poured into each designated biogas digester and stored for 44 days to allow for anaerobic digestion and biogas production. To ensure the accuracy and comprehensiveness of our experiment, we meticulously gathered and documented the quantities of these materials, as outlined in Table 1. This quantitative data served as the foundation for our research, allowing us to precisely control and analyze the variables throughout the experiment. With a diverse range of substrates at our disposal, we took great care to store them separately, each in its designated place. The unique characteristics and properties of CD, PD, and VW made it crucial to maintain their integrity behaviors and potential applications of these organic materials under three different conditions. These conditions were carefully chosen to represent a variety of real-world scenarios, each with its specific set of challenges and opportunities. As we delved into the experiment, the results and observations obtained from these conditions promised to shed light on the valuable insights and applications that these organic materials could offer, not only in Cambodia's lowland regions but potentially in a broader context as well.
Substrates | Mixture (kg) | Water (Liter) |
Pure CD | 10 | 10 |
CD + VW | 5 + 5 | 10 |
CD + PD | 5 + 5 | 10 |
The results of the experiment were measured after 15 days using Portable Gas Detector Test model GT-1000-JMD4 for investigating the biogas composition, and biogas pump with Gas meter model JBD2.5-SA to measure volume of the produced biogas for every 7 days. The important parameters such as volume of biogas was measured, followed by the levels of Carbon Dioxide, Methane, and Hydrogen Sulfite, and energy level of produced biogas.
It is worth noting that in the production of biogas from co-substrates like CD, PD, and VW, common method bias may occur due to the use of a single instrument or measurement method, leading to potential inaccuracies in data collection, such as gas yield and substrate composition. Consistent experimental conditions can also introduce bias, masking the effects of varying parameters like temperature or substrate ratios. Moreover, relying on the same statistical method for all data analyses might skew the interpretation of results. Instrument bias, where systematic errors in equipment affect multiple measurements, further compounds the potential for common method bias in these studies.
To determine the effect of the substrates on the biogas production, the experimental data was statistically analyzed using R programming. First, the data was analyzed whether it was normalized or not using Shapiro Test. For normally distribution data, ANOVA was applied to establish which treatment was significantly different. For not normally distributed data, the Kruskal Wallis Test was used to indicate the significant difference.
To calculate the biogas yield, Total Solid (TS) and Volatile Solid (VS) in the slurry are used [29,30].
The amount of TS in the slurry
TS=TS%×Vslurry | (1) |
where TS is total solid in [kg], TS% is the percentage of TS from the literature or experimental (8–11%) TS of cow dung in the slurry [31], and from [32], the TS of cow dung in the slurry up to 15%. The optimum TS is 10% in [%], and Vslurry is mass of slurry in [kg].
The amount of VS in the slurry
VS=VS%×TS | (2) |
where VS is volatile solid in [kg], VS% is percentage of VS of TS from [30], and the VS content typically ranges from 60–80% of TS.
Biogas yield in terms of per kg of VS.
The total amount of degradable material present in the volatile solid is about 50% only [29] or digester efficiency around 50–80% [30], therefore,
VSused=ηd×VS | (3) |
Y=VSmeasured/VSused | (4) |
where VSused is the amount of degradable material present in the VS [kg], ηd is the digester efficiency, Vmeasured is the measured volume from the experiment [m3], and Y is biogas yield in [m3/kgVS].
To achieve the maximum volume of biogas production, we manipulated the testing duration across three conditions. The results showed that the first peak of biogas production occurred during the first 16 days due to the acetogenic stage of producing CO2, H2, and acetic acid. During this period, the biogas could not produce fire. The results also demonstrated that the highest amount of biogas yield and the second peak of CD was achieved within the 30 to 37 days, within the 27 to 31 days for the mixing of CD with PD, and within 35 to 39 for VW, as shown in Figure 3. In this second peak, the composition of the biogas was mostly methane from the methanogenic stage. However, as the testing duration increased beyond 16 days, the amount of biogas production gradually decreased due to the theoretical reduction of carbon dioxide. This trend was consistent for both the mixture of CD with PD and the mixture of CD with VW. For the 100% CD, the digester produced higher maximum volume of 0.099 m3 with a cumulative measured volume of 0.391 m3. In the case of the CD mixed with PD, the volume of biogas production gradually increased again within 27 to 31 days of testing that reached the maximum volume of 0.069 m3 with a cumulative measured volume of 0.362 m3 during the first 44 days. However, the highest volume of biogas yield for the CD mixed with VW occurred within the initial 16-day period with a maximum volume of 0.089 m3; its cumulative measured volume was 0.319 m3.
The amount of TS in the slurry
TS=TS%×Vslurry=0.11×20=2.2kg |
The amount of VS in slurry
VS=VS%×TS=0.8×2.2=1.76kg |
Biogas yield in terms of per kg of VS
VSused=ηd×VS=0.5×1.76=0.88kg |
YCD=VSmeasured/VSused=0.391/0.88=0.444m3/kgVS |
The amount of TS in the slurry
TSCP=TSCP%×VCPslurry=0.11×20=2.2kg |
The amount of VS in slurry
VSCP=VSCP%×TSCP=0.8×2.2=1.76kg |
Biogas yield in terms of per kg of VS
VSCPused=ηd×VSCP=0.5×1.76=0.88kg |
YCP=VSCPmeasured/VSCPused=0.362/0.88=0.411m3/kgVS |
The amount of TS in the slurry
TSCV=TSCV%×VCVslurry=0.11×20=2.2kg |
The amount of VS in slurry
VSCV=VSCV%×TSCV=0.8×2.2=1.76kg |
Biogas yield in terms of per kg of VS
VSCVused=ηd×VSCV=0.5×1.76=0.88kg |
YCP=VSCPmeasured/VSCPused=0.319/0.88=0.362m3/kgVS |
Based on [30], the biogas yield of CD is in the range 0.3 to 0.5 m3/kgVS; thus, the result from the calculation is acceptable. Furthermore, the theoretical biogas yield of PD and cattle manure were 516 l/kgVS and 469 l/kgVS, respectively [33]. Table 2 shows the measured volume from the experiment during the first 44 days and biogas yield from the calculation based on total solid of CD 11% in the slurry [31].
Treatments | Total solid (%) from the literature | Cumulative measured volume (m3) | Biogas yield (m3/kgVS) |
100% CD | 11 | 0.391 | 0.444 |
50% CD + 50% PD | 11 | 0.362 | 0.411 |
50% CD + 50% VW | 11 | 0.319 | 0.362 |
Carbon dioxide levels were measured in the biogas volumes as in the previous section across three different conditions. The results indicated that the percentage of carbon dioxide was higher during the initial two weeks in all three conditions such as 26.21%, 25.66%, and 33.1% for CD 100%, CD with PD, and CD with VW, respectively, as illustrated in Figure 4. This was due to the fermentative and acetogenic stages that bacteria break down organic waste, carbohydrates, fats, protein into CO2, H2, and acetic acid. However, following this initial period, the carbon dioxide percentage began to decrease. This decline can be attributed to the increase in methane percentage, which was in the methanogenic stage after two weeks, resulting in a reduction in the carbon dioxide percentage.
The percentage of methane was also measured from the volume of biogas in the previous section. The results showed that the percentage of methane was not very high during the first two weeks, even though the highest biogas volume was obtained for the mixture of the CD with PD and the mixture of CD with VW. The low methane percentage can be attributed to the high levels of carbon dioxide, as demonstrated in the previous section. We found that all three conditions exhibited a similar trend, with the amount of methane increasing as the duration increased. However, during the first 16 days, the combination of CD with VW was lower compared to the other conditions. It was the first stage that bacteria had to break down the VW. The highest methane production was achieved for pure CD and the CD with VW at the 44-day period, producing methane of 69.18% and 67.72%, respectively, as shown in Figure 5. This demonstrated that CD mixed with PD and CD mixed with VW provided good quality of biogas, ensuring good facility for the households constructed with digesters in the low land area in Cambodia.
From [21], in the central of Vietnam country, biogas plants from pig manure produced methane of 65.44% along with carbon dioxide of 29.31% for biogas plants younger than five years and methane concentrations of 64.57% and CO2 of 29.93% for biogas plants older than five years. The maximum average of CH4 and CO2 from [34] was 54.7 ± 10.74% and 42.3 ± 10.74%, respectively, and that from [35] was 55.8% and 43%, respectively, from anaerobic digestion of cow manure.
According to [36], hydrogen sulfide in the biogas causes corrosion of engines and metal pipes when the biogas is used as the fuel in combustion and electricity generation. The H2S in biogas ranges between 50–10,000 ppm depending on the feed material composition to the digester [37]. From [23], the standard concentration of H2S is less than 200 ppm for biogas engines and less than 1000 ppm for steam boilers. Hydrogen sulfide was also measured in this experiment. Similar to the other parameters, the concentration of hydrogen sulfide was determined from the volume of biogas and measured under three different conditions, as shown in Figure 6. The results indicated that the highest concentration of hydrogen sulfite was observed within the first 16-day period in the case of the mixture of CD with PD. While the pure CD and the mixture of CD with VW reached their highest levels of hydrogen sulfite during the first 23 days. Following these respective time frames, there was a decline in the levels of hydrogen sulfide. This decrease could be attributed to an increase in the percentage of methane, as illustrated in Section 3.3.2, occurring after the initial two-week period, which subsequently led to a corresponding reduction in the concentration of hydrogen sulfide.
After the experiment, the measured data were categorized, coded, and analyzed using Excel and R programming (version 4.3.3) to observe the difference between three combinations. First, the data was analyzed, whether it was normalized or not. Among the data, only the CH4 data was not normally distributed. For the normal distribution data, to observe the significance of combinations of the three conditions, the volume, CO2, and H2S data were analyzed using ANOVA. For the CH4 data, Kruskal Wallis Test was used due to the data not normally distributed. When p-value is greater than 0.05 at 95% confident interval means that there is not statistically significant difference among each treatment pair. Table 3 shows the p-value from the analyzed data. The results showed that 100% CD, CD with PD, and CD with VW were not significant (p > 0.05).
Composition | CH4 | CO2 | H2S | Volume |
p-value | 0.8521 | 0.736 | 0.506 | 0.658 |
To evaluate the energy content of biogas produced by a biogas plant, it is essential to conduct a comparative analysis between biogas boilers and electric water boilers. This evaluation involves quantifying the energy levels within biogas generated from pure CD, given its distinctive characteristics compared to the other two materials. It is important to note that all experiments were performed under identical conditions with the same volume of water. Furthermore, a key aspect of this study involves analyzing the electricity consumption required to heat 0.5 liters of water. This process involves raising the water temperature from an initial 31.1 degrees Celsius to its boiling point at 100 degrees Celsius, utilizing two different methods: Biogas and electricity. When using biogas, we found that 0.02 cubic meters of biogas were needed to achieve this heating process, while electricity consumption amounted to 0.05 kWh. From the experiment, the volume of biogas was also measured for the other two conditions after 44 days, and we found that the total volume of biogas generated from pure CD after 44 days was 0.391 m3, which is equivalent to 0.9725 kWh. Moreover, the mixture of CD with VW and the mixture of CD with PD are 0.362 m3 at 0.905 kWh and 0.319 m3 at 0.7975 kWh, respectively. In summary, pure CD outperforms the other two materials for biogas conversion for the people of Cambodia.
This study showcases the practical implementation of biogas conversion using three different organic materials: Pure CD, a mixture of CD with PD, and a mixture of CD with VW in lowland agricultural households in Cambodia. The experimental results reveal that pure CD, sourced from Cambodian lowland agricultural households, outperforms the other two materials, namely, the mixture of CD with PD and the mixture of CD with VW, in terms of biogas production. Over 44 days, pure CD yielded the highest volume of biogas at 0.391 m3, followed by the mixture of CD with VW at 0.362 m3 and the mixture of CD with PD at 0.319 m3. The increased biogas volume and higher methane percentage, as detailed in this study, hold significant promise for biogas conversion. Therefore, this research underscores the potential of pure CD to efficiently meet the biogas conversion requirements in Cambodia's lowland regions. Future studies will explore a broader range of substrate combinations and ratios to identify the most efficient mix for biogas production. Additionally, we will investigate the effects of varying process parameters such as temperature, pH, and retention time on biogas yield and methane content. By optimizing substrate selection and process conditions, we aim to enhance the efficiency and quality of biogas production, contributing to more sustainable renewable energy solutions.
The authors declare they have not used Artificial Intelligence (AI) tools in the creation of this article.
The authors declare no conflicts of interest.
Sokna San: Conceptualization, Methodology, Formal analysis, Writing—original draft, Writing—review and editing. Seyla Heng: Methodology, Data curation, Experiment. Vanna Torn: Formal analysis, Investigating, Software, Writing—review and editing. Chivon Choeung: Writing—review and editing, Resources, Software, Validation. Horchhong Cheng: Methodology, Supervision. Seiha Hun: Data analysis, Data curation, Software, Formal analysis. Chanmoly Or: Methodology, Supervision.
[1] |
Torn V, Seangwong P, Fernando N, et al. (2023) Performance improvement of flux switching permanent magnet wind generator using magnetic flux barrier design. Sustainability 15: 8867. https://10.3390/su15118867 doi: 10.3390/su15118867
![]() |
[2] |
Sekar S, Park S, Jung J, et al. (2023) Superb bifunctional water electrolysis activities of carbon nanotube-decorated lanthanum hydroxide nanocomposites. Int J Energy Res 2023: 1–13. https://doi.org/10.1155/2023/6685726 doi: 10.1155/2023/6685726
![]() |
[3] |
Douskova I, Doucha J, Livansky K, et al. (2009) Simultaneous flue gas bioremediation and reduction of microalgal biomass production costs. Appl Microbiol Biotechnol 82: 179–185. https://10.1007/s00253-008-1811-9 doi: 10.1007/s00253-008-1811-9
![]() |
[4] |
Hannon M, Gimpel J, Tran M, et al. (2010) Biofuels from algae: Challenges and potential. Biofuels 1: 763–784. https://10.4155/bfs.10.44 doi: 10.4155/bfs.10.44
![]() |
[5] |
Awe OW, Zhao Y, Nzihou A, et al. (2017) A review of biogas utilisation, purification and upgrading technologies. Waste Biomass Valor 8: 267–283. https://10.1007/s12649-016-9826-4 doi: 10.1007/s12649-016-9826-4
![]() |
[6] |
Kaushal R, Sandhu S, Kumar Soni M (2022) Anaerobic co-digestion of food waste, algae, and cow dung for biogas yield enhancement as a prospective approach for environmental sustainability. Sustainable Energy Technol Assess 52: 102236. https://doi.org/10.1016/j.seta.2022.102236 doi: 10.1016/j.seta.2022.102236
![]() |
[7] |
Belhocine A, Shinde D, Patil R (2021) Thermo-mechanical coupled analysis based design of ventilated brake disc using genetic algorithm and particle swarm optimization. JMST Adv 3: 41–54. https://doi.org/10.1007/s42791-021-00040-0 doi: 10.1007/s42791-021-00040-0
![]() |
[8] |
Atelge MR, Atabani AE, Banu JR, et al. (2020) A critical review of pretreatment technologies to enhance anaerobic digestion and energy recovery. Fuel 270: 117494. https://doi.org/10.1016/j.fuel.2020.117494 doi: 10.1016/j.fuel.2020.117494
![]() |
[9] |
Afzal A, Soudagar MEM, Belhocine A, et al. (2021) Thermal performance of compression ignition engine using high content biodiesels: A comparative study with diesel fuel. Sustainability 13: 7688. https://10.3390/su13147688 doi: 10.3390/su13147688
![]() |
[10] |
Abd Allah WE, Tawfik MA, Sagade AA, et al. (2021) Methane production enhancement of a family-scale biogas digester using cattle manure and corn stover under cold climates. Sustainable Energy Technol Assess 45: 101163. https://doi.org/10.1016/j.seta.2021.101163 doi: 10.1016/j.seta.2021.101163
![]() |
[11] |
Atelge MR, Atabani AE, Abut S, et al. (2021) Anaerobic co-digestion of oil-extracted spent coffee grounds with various wastes: Experimental and kinetic modeling studies. Bioresour Technol 322: 124470. https://10.1016/j.biortech.2020.124470 doi: 10.1016/j.biortech.2020.124470
![]() |
[12] | Abubakar B, Ismail N (2012) Anaerobic digestion of cow dung for biogas production. ARPN J Eng Appl Sci 7: 169–172. Available from: http://www.arpnjournals.com/jeas/research_papers/rp_2012/jeas_0212_635.pdf. |
[13] |
Curry N, Pillay P (2012) Biogas prediction and design of a food waste to energy system for the urban environment. Renewable Energy 41: 200–209. https://doi.org/10.1016/j.renene.2011.10.019 doi: 10.1016/j.renene.2011.10.019
![]() |
[14] |
Glivin G, Mariappan V, Premalatha M, et al. (2022) Comparative study of biogas production with cow dung and kitchen waste in Fiber-Reinforced Plastic (FRP) biodigesters. Mater Today: Proc 52: 2264–2267. https://doi.org/10.1016/j.matpr.2021.08.098 doi: 10.1016/j.matpr.2021.08.098
![]() |
[15] |
Achinas S, Euverink GJW (2019) Elevated biogas production from the anaerobic co-digestion of farmhouse waste: Insight into the process performance and kinetics. Waste Manag Res 37: 1240–1249. https://10.1177/0734242X19873383 doi: 10.1177/0734242X19873383
![]() |
[16] |
Bi S, Hong X, Yang H, et al. (2020) Effect of hydraulic retention time on anaerobic co-digestion of cattle manure and food waste. Renewable Energy 150: 213–220. https://doi.org/10.1016/j.renene.2019.12.091 doi: 10.1016/j.renene.2019.12.091
![]() |
[17] |
Bernard SS, Srinivasan T, Suresh G, et al. (2020) Production of biogas from anaerobic digestion of vegetable waste and cow dung. Mater Today: Proc 33: 1104–1106. https://doi.org/10.1016/j.matpr.2020.07.129 doi: 10.1016/j.matpr.2020.07.129
![]() |
[18] | Aremu MO, Agarry SE (2012) Comparison of biogas production from cow dung and pig dung under mesophilic condition. Int Refereed J Eng Sci 1: 16–21. Available from: https://www.irjes.com/Papers/vol1-issue4/Version%201/C141621.pdf. |
[19] |
Van Tran G, Ramaraj R, Balakrishnan D, et al. (2022) Simultaneous carbon dioxide reduction and methane generation in biogas for rural household use via anaerobic digestion of wetland grass with cow dung. Fuel 317: 123487. https://doi.org/10.1016/j.fuel.2022.123487 doi: 10.1016/j.fuel.2022.123487
![]() |
[20] |
Chubur V, Danylov D, Chernysh Y, et al. (2022) Methods for intensifying biogas production from waste: A scientometric review of cavitation and electrolysis treatments. Fermentation 8: 570. https://doi.org/10.3390/fermentation8100570 doi: 10.3390/fermentation8100570
![]() |
[21] |
Roubík H, Mazancová J, Le Dinh P, et al. (2018) Biogas quality across small-scale biogas plants: A case of central Vietnam. Energies 11: 1794. https://doi.org/10.3390/en11071794 doi: 10.3390/en11071794
![]() |
[22] |
Roubík H, Mazancová J, Banout J, et al. (2016) Addressing problems at small-scale biogas plants: A case study from central Vietnam. J Cleaner Prod 112: 2784–2792. https://doi.org/10.1016/j.jclepro.2015.09.114 doi: 10.1016/j.jclepro.2015.09.114
![]() |
[23] | National Biodigester Programme. Available from: http://nbp.org.kh/. |
[24] |
Pode R, Diouf B, Pode G (2015) Sustainable rural electrification using rice husk biomass energy: A case study of Cambodia. Renewable Sustainable Energy Rev 44: 530–542. https://doi.org/10.1016/j.rser.2015.01.018 doi: 10.1016/j.rser.2015.01.018
![]() |
[25] |
Nam S, Torn V, Choeung C, et al. (2024) The potential of rice husks for electrical energy generation in Cambodia. Int J Electr Electron Res 12: 611–616. https://doi.org/10.37391/IJEER.120237 doi: 10.37391/IJEER.120237
![]() |
[26] | Nguyen HN, Ha-Duong M, Van de Steene L (2015) A critical look at rice husk gasification in Cambodia: Technology and sustainability. Int Forum Green Technol Manage (IFGTM) 2015. Available from: https://hal.science/hal-01166547/document. |
[27] |
Lor L, Mihara M, Ngo B, et al. (2017) Production and quality of biogas from pilot biodigesters using cow manure. Livestock Res Rural Dev, 29. https://doi.org/10.32115/ijerd.11.2_92 doi: 10.32115/ijerd.11.2_92
![]() |
[28] | Yen S, Preston TR, Thuy NT (2017) Biogas production from water spinach combined with manure from buffaloes in an in vitro biodigester system. Gas 146: 140. Available from: http://www.lrrd.org/lrrd29/9/soph29165.html. |
[29] |
Jyothilakshmi R, Prakash SV (2016) Design, fabrication and experimentation of a small scale anaerobic biodigester for domestic biodegradable solid waste with energy recovery and sizing calculations. Proc Environ Sci 35: 749–755. https://doi.org/10.1016/j.proenv.2016.07.085 doi: 10.1016/j.proenv.2016.07.085
![]() |
[30] | In-depth analysis of biogas production from cow dung. Available from: https://www.linkedin.com/pulse/in-depth-analysis-biogas-production-from-cow-dung-jahagirdar-sanjeev-nw96f. |
[31] | Ituen EE, John NM, Bassey BE (2009) Biogas production from organic waste in Akwa IBOM state of Nigeria. In: Yanful EK (Ed.), Appropriate Technologies for Environmental Protection in the Developing World, Dordrecht, Springer Netherlands, 93–99. https://doi.org/10.1007/978-1-4020-9139-1_11 |
[32] | Triolo JM, Ward AJ, Pedersen L, et al. (2013) Characteristics of animal slurry as a key biomass for biogas production in Denmark. In: Matovic MD (Ed.), Biomass Now—Sustainable Growth and Use, InTech. https://doi.org/10.5772/54424 |
[33] |
Mø ller HB, Sommer SG, Ahring BK (2004) Methane productivity of manure, straw and solid fractions of manure. Biomass Bioenergy 26: 485–495. https://doi.org/10.1016/j.biombioe.2003.08.008 doi: 10.1016/j.biombioe.2003.08.008
![]() |
[34] |
Nganyira PD, Mahushi DJ, Balengayabo JG, et al. (2023) Quality of biogas generated through co-digestion of Brewer's spent grain and cattle dung. Energy Rep 10: 2330–2336. https://doi.org/10.1016/j.egyr.2023.09.012 doi: 10.1016/j.egyr.2023.09.012
![]() |
[35] |
Walozi R, Nabuuma B, Sebiti A (2016) Application of low pressure water scrubbing technique for increasing methane content in biogas. Universal J Agric Res 4: 60–65. https://doi.org/10.13189/ujar.2016.040206 doi: 10.13189/ujar.2016.040206
![]() |
[36] |
Wang H, Larson RA, Runge T (2019) Impacts to hydrogen sulfide concentrations in biogas when poplar wood chips, steam treated wood chips, and biochar are added to manure-based anaerobic digestion systems. Bioresour Technol Rep 7: 100232. https://doi.org/10.1016/j.biteb.2019.100232 doi: 10.1016/j.biteb.2019.100232
![]() |
[37] |
Mamun MRA, Torii S (2015) Removal of hydrogen sulfide (H2S) from biogas using zero-valent iron. J Clean Energy Technol 3: 428–432. https://doi.org/10.7763/JOCET.2015.V3.236 doi: 10.7763/JOCET.2015.V3.236
![]() |
Substrates | Mixture (kg) | Water (Liter) |
Pure CD | 10 | 10 |
CD + VW | 5 + 5 | 10 |
CD + PD | 5 + 5 | 10 |
Treatments | Total solid (%) from the literature | Cumulative measured volume (m3) | Biogas yield (m3/kgVS) |
100% CD | 11 | 0.391 | 0.444 |
50% CD + 50% PD | 11 | 0.362 | 0.411 |
50% CD + 50% VW | 11 | 0.319 | 0.362 |
Composition | CH4 | CO2 | H2S | Volume |
p-value | 0.8521 | 0.736 | 0.506 | 0.658 |
Substrates | Mixture (kg) | Water (Liter) |
Pure CD | 10 | 10 |
CD + VW | 5 + 5 | 10 |
CD + PD | 5 + 5 | 10 |
Treatments | Total solid (%) from the literature | Cumulative measured volume (m3) | Biogas yield (m3/kgVS) |
100% CD | 11 | 0.391 | 0.444 |
50% CD + 50% PD | 11 | 0.362 | 0.411 |
50% CD + 50% VW | 11 | 0.319 | 0.362 |
Composition | CH4 | CO2 | H2S | Volume |
p-value | 0.8521 | 0.736 | 0.506 | 0.658 |