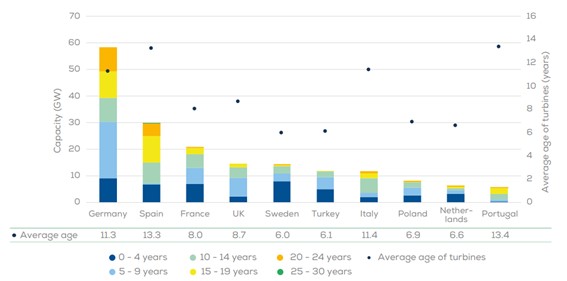
Wind energy has become a very interesting option regarding the replacement of fossil-based energy sources by renewable options. Despite its eco-friendly character, some challenges remain across the whole lifecycle of wind turbines. These are mainly related to the use of more sustainable materials and processes in the construction phase, to lifetime extension for the structures currently installed and to waste management at the end-of-life phase, the disassembly or decommissioning phase. Following worldwide concerns about sustainability, the circular economy and decarbonization, several projects have been addressing the themes identified, proposing alternatives that are more suitable and contribute to the body of knowledge in the sector towards enhanced environmental and technical performance.
This work presents the state of the art of the European wind energy sector, reflecting on the main drivers, barriers and challenges for circularity, while identifying knowledge gaps and strategic opportunities to develop new potential approaches. A compilation of key projects and main wind energy sites in Europe is shown, as well as a collection of lifecycle extension strategies and reported environmental impacts. Approaches to sustainability are highlighted, such as recyclability, eco-design and eco-efficiency of the turbine blades. Furthermore, the associated potential environmental, economic and societal impacts are put forward to support the implementation of more circular solutions, which can also contribute to reducing EU energy dependency and more integration of renewable sources. The key goal is to give an overview of the main challenges in the sector, namely, in what relates to potential circular solutions and strategies towards a higher level of sustainability.
Citation: Ana Ramos, Filipa Magalhães, Diogo Neves, Nelson Gonçalves, António Baptista, Teresa Mata, Nuno Correia. Wind energy sustainability in Europe—A review of knowledge gaps, opportunities and circular strategies[J]. Green Finance, 2023, 5(4): 562-602. doi: 10.3934/GF.2023022
[1] | Clement Allan Tisdell . Renewable energy use and the renewable energy sector’s development: public finance, environmental externalities and sustainability. Green Finance, 2019, 1(2): 156-173. doi: 10.3934/GF.2019.2.156 |
[2] | Wen-Tien Tsai . Green finance for mitigating greenhouse gases and promoting renewable energy development: Case study in Taiwan. Green Finance, 2024, 6(2): 249-264. doi: 10.3934/GF.2024010 |
[3] | Biljana Ilić, Dragica Stojanovic, Gordana Djukic . Green economy: mobilization of international capital for financing projects of renewable energy sources. Green Finance, 2019, 1(2): 94-109. doi: 10.3934/GF.2019.2.94 |
[4] | Yoram Krozer . Financing of the global shift to renewable energy and energy efficiency. Green Finance, 2019, 1(3): 264-278. doi: 10.3934/GF.2019.3.264 |
[5] | Reinhard Haas, Amela Ajanovic, Jasmine Ramsebner, Theresia Perger, Jaroslav Knápek, Jan W. Bleyl . Financing the future infrastructure of sustainable energy systems. Green Finance, 2021, 3(1): 90-118. doi: 10.3934/GF.2021006 |
[6] | Óscar Suárez-Fernández, José Manuel Maside-Sanfiz, Mª Celia López-Penabad, Mohammad Omar Alzghoul . Do diversity & inclusion of human capital affect ecoefficiency? Evidence for the energy sector. Green Finance, 2024, 6(3): 430-456. doi: 10.3934/GF.2024017 |
[7] | Amanda-Leigh O'Connell, Johan Schot . Operationalizing transformative capacity: State policy and the financing of sustainable energy transitions in developing countries. Green Finance, 2024, 6(4): 666-697. doi: 10.3934/GF.2024026 |
[8] | Goshu Desalegn . Insuring a greener future: How green insurance drives investment in sustainable projects in developing countries?. Green Finance, 2023, 5(2): 195-210. doi: 10.3934/GF.2023008 |
[9] | Laura Grumann, Mara Madaleno, Elisabete Vieira . The green finance dilemma: No impact without risk – a multiple case study on renewable energy investments. Green Finance, 2024, 6(3): 457-483. doi: 10.3934/GF.2024018 |
[10] | Mihaela Onofrei, Bogdan Narcis Fîrțescu, Florin Oprea, Dana Claudia Cojocaru . The effects of environmental patents on renewable energy consumption. Green Finance, 2024, 6(4): 630-648. doi: 10.3934/GF.2024024 |
Wind energy has become a very interesting option regarding the replacement of fossil-based energy sources by renewable options. Despite its eco-friendly character, some challenges remain across the whole lifecycle of wind turbines. These are mainly related to the use of more sustainable materials and processes in the construction phase, to lifetime extension for the structures currently installed and to waste management at the end-of-life phase, the disassembly or decommissioning phase. Following worldwide concerns about sustainability, the circular economy and decarbonization, several projects have been addressing the themes identified, proposing alternatives that are more suitable and contribute to the body of knowledge in the sector towards enhanced environmental and technical performance.
This work presents the state of the art of the European wind energy sector, reflecting on the main drivers, barriers and challenges for circularity, while identifying knowledge gaps and strategic opportunities to develop new potential approaches. A compilation of key projects and main wind energy sites in Europe is shown, as well as a collection of lifecycle extension strategies and reported environmental impacts. Approaches to sustainability are highlighted, such as recyclability, eco-design and eco-efficiency of the turbine blades. Furthermore, the associated potential environmental, economic and societal impacts are put forward to support the implementation of more circular solutions, which can also contribute to reducing EU energy dependency and more integration of renewable sources. The key goal is to give an overview of the main challenges in the sector, namely, in what relates to potential circular solutions and strategies towards a higher level of sustainability.
The Paris Agreement (United Nations, 2015) and the Sustainable Development Goals (United Nations, 2016) established by the United Nations are among the various instruments that promote sustainable development. These have gathered significant consensus among nations, enabling a stable framework for sustainable development, which should encompass societal, economic and environmental aspects in a concerted manner to pursue an integrated and just transition (Climate Justice Alliance, 2021).
In this context, the European Union set itself to a family of mandatory commitments, through packages such as the European Green Deal (European Commission, 2019), the Circular Economy Action Plan (European Commission, 2020) and regulations such as the taxonomy for sustainable activities, among which reaching climate neutrality by 2050 stands out. The European Green Deal foresees an action plan aiming to boost the efficient use of resources through the transition for a cleaner and more circular economy, restoring biodiversity and natural resources and reducing pollution. Also, in November 2022, the 27th Conference of the Parties, COP27, brought together experts and world leaders to discuss progress towards combating climate change. Although some commitments by the Parties of the United Nations Framework Convention on Climate Change were achieved, further efforts will be needed to reach the 1.5 ℃ target in the coming years.
Circular practices date back to our ancestors. However, the formal concept of circular economy has a more recent origin, and according to the Ellen MacArthur Foundation, it combines a series of principles, ranging from industrial ecology, life cycle thinking, eco-efficiency and biomimetics, among others. Despite its different definitions, the circular economy concept is based on three fundamental principles: (1) Preserve and increase natural capital by controlling finite resources and balancing renewable resource flows, (2) optimize the use of the available resources, and (3) promote the effectiveness of the systems, minimizing the externalities (Ellen MacArthur Foundation, 2020). There is still a natural trend today to associate the circular economy with waste management and recycling, but the concept is much broader: It involves preserving and regenerating resources that are already in use, maintaining their economic value at its maximum potential and for longer periods. In parallel, it consists of a systemic and integrated approach, from the point of view of supply and demand, promoting the use of renewable resources (Ellen MacArthur Foundation, 2019).
The European Union faces huge challenges in the energy field, especially now, with the conflict between Russia and Ukraine that seems to have no end in sight. Topics such as dependence on imports, limited diversification of energy sources, high and volatile energy prices, growing global energy demand, security risks affecting producers and transit countries, increasing threats derived from climate change, decarbonization, slow progress on energy efficiency, challenges posed by the increase in the renewable energy share, and the need for greater transparency integration and interconnection in energy markets fill the agendas of the main world decision-makers (Ciucci, 2021). A series of actions aiming to achieve an integrated energy market, security of energy supply and a sustainable energy sector must be in the center of the EU energy policy. The Renewable Energy Directive (European Commission, 2022) is the legal framework that sets the rules and targets for the development of renewable energy across all sectors of the economy.
Wind energy is paramount as a source of renewable energy with deployment all over the world and, as every economic sector, it must fully comply with the commitments for a circular economy in all steps of the value chain, from material selection and components manufacturing to dismantling of wind turbines and reintroduction of materials in the economy (Wind Europe, 2022). Despite being a relatively young industry, wind energy is sufficiently mature and is a competitive renewable energy source in the EU, playing an important role in the set of measures that aim to achieve carbon neutrality by 2050. Nevertheless, the wind sector faces some particular constraints that must be overcome, mainly the permitting process that, in some EU countries, represents an obstacle to the wind energy projects due to the length and complexity of the procedures. To surpass this limitation, in May 2022, the EU presented some additional measures in the form of a recommendation (European Commission, 2022) and an amendment of the Renewable Energy Directive (European Parliament, 2022), along with the publication of the REPower EU Plan (European Commission, 2022). In fact, this last plan comes up to respond to the global energy market disruption caused by the conflict between Russia and Ukraine, aiming to reduce EU dependency on Russian gas and oil. The European Commission raised the 2030 target for renewables share from 40% to 45%, and the energy saving 2030 target is set on 13%. The facilitation of the Power Purchase Agreements (PPAs) is also an important driver of the adoption of renewable energy sources. Although these agreements are increasing, the growing rate is still lower than expected.
Another mechanism that can accelerate the energy transition and promote the investment in this sector is the adoption of the EU Taxonomy Regulation 2020/8521, published in June 2020. This framework is intended to facilitate sustainable investment in a common taxonomy for all Member States in the European Commission. The taxonomy will help to determine if an investment is sustainable and is based on six environmental objectives: (1) climate change mitigation, (2) adaptation, (3) sustainable use and protection of water and marine resources, (4) transition to a circular economy, (5) pollution prevention and control and (6) protection and restoration of biodiversity and ecosystems. In July 2023, a new package of measures was set up, to boost and strengthen the EU sustainable finance framework, contributing to the accomplishment of the last four objectives. The electricity generated from wind power is an eligible activity in the EU taxonomy as it contributes to climate change mitigation and adaptation. Another mechanism related to these matters, and building on existing EU legislative framework and policies, such as the EU Green Deal, EU Taxonomy and EU Circular Economy Act, is the ESRS E5 – Resource use and circular economy2, one of the five standards of the European Sustainability Reporting Standards for the Environment that will help to define the way into a more circular vision. This preliminary standard is centered in the resource's inflows, including the circularity of materials, considering renewable and non-renewable resources, and outflows, based on information on products, materials and waste.
1https://eur-lex.europa.eu/legal-content/EN/TXT/?uri = celex:32020R0852.
All these actions and measures imply significant investments that the EU countries need to support in the forthcoming years, in order to promote diversification of energy sources, promote production of clean energy and increase energy saving. In this field, the EU provided a set of instruments and guidance to encourage investment in the renewable energy area. The mechanisms3 aim to promote renewable projects and intensify a closer cooperation between the EU countries to reduce import dependency. At the European level, the wind energy sector has been working to define a sustainable life cycle for the numerous materials resulting from the end of life of these assets. Waste from end-of-life wind turbines is mainly steel, metals, composites and electronic components. Currently, the recycling rate of a wind turbine is between 85% and 90% (Schmid et al., 2020), which includes the tower, parts of the foundation and some components of the gearbox and generator. One of the most significant challenges of the wind industry remains with the blades (Wind Europe, 2020), namely, in their collection, transport to appropriate location and management of the materials' final destination. These difficulties arise, on one hand, from the proportions of the component and, on the other hand, from the type of materials that they are made from (fiberglass and resins, among others). Composite materials are not exclusive from the wind sector but rather a cross-sectorial challenge. It is estimated that the waste generated from the blades will represent about 10% of the total composite waste by 2025 (Schmid et al., 2020). This reinforces the need for the engagement of all sectors dealing with this type of secondary materials, to establish a robust R-strategy scheme. One of the biggest challenges that the wind energy sector is facing today is the approaching end-of-life of most assets in Europe. According to international standards, the design lifetime of a wind turbine is set for about 20 years (International Electrotechnical Commission, 2005), and, to meet the targets set in the 2030 National Energy Climate Plans (Wind Europe, 2022), reflection is urgent for how to deal with this situation.
3https://eur-lex.europa.eu/legal-content/EN/TXT/?uri = uriserv:OJ.L_.2020.303.01.0001.01.ENG&toc = OJ:L:2020:303:TOC; https://energy.ec.europa.eu/eu-renewable-energy-financing-mechanism_en; https://energy.ec.europa.eu/system/files/2014-10/com_2013_public_intervention_swd04_en_1.pdf;
According to the Wind Europe association, in 2022, circa 220 GW of wind power capacity were operating in Europe. On the other hand, about 454 MW were decommissioned in the same year, the majority of them in Germany, Netherlands and Austria, all from onshore facilities (Komusanac et al., 2021). Today, about 14 GW of European assets are more than 20 years old, mainly in Germany, followed by Spain, Italy and France as illustrated in Figure 1. When looking for average numbers, Denmark, Spain and Portugal have the oldest fleets (Wind Europe, 2020).
Portugal had, by the end of 2020, an installed capacity of 5.8 GW distributed by a total of roughly 2849 wind turbines (around 8475 wind turbine blades), mostly located in the north of the country (INEGI and APREN, 2021). Between 2025 and 2031, in average terms, around 266 wind turbines per year (almost 800 blades per year) will reach their nominal lifetime, usually 20 years. There are three main options for these assets: (ⅰ) extend their operation life beyond their nominal expected lifetime, by estimating their remaining life and potentially replacing some components; (ⅱ) replace the wind turbines with more recent technology and with higher efficiency, in a process usually designated as repowering; or (ⅲ) completely dismantle the wind farm. Particularly if the latter two scenarios are chosen, several tons of materials will require a suitable destination. Nevertheless, most European countries are now opting for some kind of lifetime extension scheme, as often, legislative frameworks for repowering are not yet implemented. Therefore, a collaborative effort is required to better frame the state of the art of this topic in a holistic way, further addressing the potential opportunities and ways forward to reach a higher level of sustainability in the sector of wind energy. In this study, we report a compilation of data related to relevant questions such as the search for enhanced materials and designs, technological developments to improve recyclability, reusability, remanufacturing options, and application of new materials and technologies both to offshore and onshore units. Also, finding relations between wind technologies, waste generation and circular economy, as well as assessing the environmental, social and economic impacts, are important matters herein considered.
The outline of this paper is the following: section 1 is the Introduction, which sets the context for the topic in terms of legislation, regulatory mechanisms and guidelines; section 2 (Literature review) concerns the state of the art for turbines' materials, components, design and circularity issues of the associated technologies; section 3 refers to the gap analysis and potential opportunities to implement circular strategies and measure circularity; the last section states the main conclusions.
Although not in the form of a systematic literature review, this paper reflects the compilation of the key works and ideas about the actual panorama of the wind energy sector, in order for the authors to tentatively come up with innovative solutions and forward-looking insights. The strategy to gather the relevant literature was based on a collaborative approach, namely through content and knowledge sharing, complemented with literature search and networking particularly in the wind community. For the particular case of tables, information was synthesized as follows:
● Table 1: expert knowledge from two authors, who were part of the working teams in several of the referred projects and therefore were also aware of the related framework and literature; CORDIS platform;
Ref. | Year | Project name | Site | Remarks |
(LM Wind Power, 2022) | 2022 | ZEBRA | On and offshore | ● design and manufacture the wind industry's first 100% recyclable wind turbine blade |
(ECHT Community, 2023) | 2022 | Circular Wind Hub | --- | ● circular strategies in the wind sector |
(National Composites Centre, 2021) | 2021 | SusWind | Offshore | ● accelerating sustainable composite materials and technology for wind turbine blades |
(Bennet, 2021) | 2021 | ORE Catapult | Offshore | ● establishing reliable and efficient recycling in the wind sector |
(DecomBlades, 2021) | 2021 | DecomBlades | --- | ● establish functional, sustainable value chains to handle end of life wind turbine blades |
(Vestas, 2021) | 2021 | CETEC | On and offshore | ● new solution for full recyclability of wind turbine blades |
(bcircular, 2020) | 2020 | R3FIBER | --- | ● green technology to recycle wind turbine blades |
(ECHT Community, 2020) | 2020 | Moonshot Circular Wind Farms | --- | ● ideation process focussed on circular strategies in the wind industry |
(Nattional Composites Centre, 2019) | 2019 | ReDisCoveR Composites | --- | ● solve the issues faced by composites at the end of life |
(Interreg, 2018) | 2018 | DecomTools | Offshore | ● devising and developing eco-innovative concepts for offshore wind parks |
(Re-wind network, 2018) | 2018 | Re-Wind | On and offshore | ● repurposing wind blades |
(Markaide, 2018) | 2018 | AIRPOXY | --- | ● introduces a novel family of ground-breaking thermoset composites |
(Svendsen, 2017) | 2017 | Dreamwind | --- | ● development of new composite materials |
(SPIRE, 2017) | 2017 | Ecobulk | --- | ● formulating materials that allow high recycled content |
(Colledani, 2017) | 2017 | FiberEUse | --- | ● large scale demonstration of new circular economy value-chains based on the reuse of end-of-life fiber reinforced composites |
(Fraunhofer Institute for Wood Research Wilhelm-Klauditz-Institut, 2017) | 2017 | ReRoBalsa | --- | ● recovering balsa wood and plastic foam for the production of insulation materials |
(The German Federal Environment Agency, 2017) | 2017 | Ramboll BBB * | --- | ● develop a circular economy approach for end-of-life onshore wind turbines |
(Interreg, 2016) | 2016 | Recy-composite | On and offshore | ● three-level global cross-border approach: material recovery, thermochemical recycling and energy recovery |
(European Commission, 2016) | 2016 | Eco-turbine | On and offshore | ● flax based bio composites ● lamella type rectangular "wall" of series of blades |
(European Commission, 2016) | 2016 | PowderBlade | Offshore | ● carbon/glass fiber in powder epoxy |
(Universidad de Castilla la Mancha, 2015) | 2015 | NANOLEAP | Offshore | ● network of specialized pilot lines for the production of nanocomposite-based products |
(European Commission, 2015) | 2015 | SPARCARB | On and offshore | ● lightning protection of CFC structures |
(University of Bristol, 2014) | 2014 | HiPerDiF | --- | ● producing highly aligned discontinuous fiber composites |
(European Commission, 2014) | 2014 | AutowinSpec | Onshore | ● automatic blade condition monitoring |
(Fraunhofer Institute for Process Engineering and Packaging IVV, 2014) | 2014 | ForCycle | --- | ● recycling of high-quality metal-plastic composites |
(EV, 2013) | 2013 | WALiD | Offshore | ● cost-effective advanced lightweight design |
(Iberdrola, 2013) | 2013 | LIFE BRIO | --- | ● innovative and sustainable methodology for end-of-life wind turbine blades management |
(Cranfield University, 2013) | 2013 | EXHUME | --- | ● novel recycling and remanufacturing processes |
(GENVIND, 2012) | 2012 | Genvind Innovation Consortium | --- | ● sustainable recycling of composites |
(European Commission, 2012) | 2012 | CORETO | On and offshore | ● in-situ performance of major composite repair steps |
(AG, 2012) | 2012 | SELFRAG CFRP | --- | ● recycling of thermoset composite materials |
(Richerche, 2011) | 2011 | SUSRAC | --- | ● sustainable recycling of composites |
(STENA, 2009) | 2009 | LIFE07 ENV/S/000904 | --- | ● recycling of glass fibre reinforced plastics |
(European Commission, 2009a) | 2009 | WinTur | On and offshore | ● integration of acoustic emission and long-range ultrasonics |
(Plastic Omnium Auto Exterieur Services, 2009) | 2009 | EURECOMP | --- | ● recycling fibre-reinforced thermoset composites |
(European Commission 2009b) | 2009 | PROND | On and offshore | ● self-adaptive blade of small wind turbine |
(Hebo Engineering BV 2003) | 2003 | REACT | --- | ● recycling glass and carbon fibres |
*The project does not have an acronym; its complete name is "Developing a concept and measures for resource saving dismantling of wind turbines". |
● Table 2: knowledge shared within an international partnership created for this specific topic (ECHT Community, 2023), gathered also from institutions as Wind Europe and from an internal institutional work group, dealing with the current challenges and potential circular solutions for wind turbine blades; periodic publications of the German Wind Power Magazine were also a source of information; assessing information on websites as the one provided by Power Technology (Power Technology, 2019);
Ref. | Project | Region | Site | Capacity | Remarks |
(SSE Renewables, Equinor et al., 2010) | Dogger Bank | Multiregion* | Offshore | 2.4 GW | multiple substations interconnected |
(Netherlands Enterprise Agency, 2022) | Ijmuiden Ver | Netherlands | Offshore | 6 GW | 6 sites |
(Vattenfall, 2018) | Hollandse K. | Offshore | 3 GW | largest subsidy-free wind farm at sea | |
(PowerTechnology, 2019) | Gemini | Offshore | 600 MW | powers approximately 785,000 homes | |
(SSE Renewables, 2022) | Arklow Bank | Ireland | Offshore | 800 MW | only operational Irish offshore site now |
(WindEurope, 2023) | HywindTampen | Norway | Offshore | 88 MW | still under construction |
(Interesting Engineering, 2016) | Nordic Wind | Onshore | 1000 MW | Europe's largest onshore wind project | |
(Smart City Sweden, 2022) | Markbygden 1101 | Sweden | Onshore | 16.25 GW** | Europe's largest onshore windfarm |
(Eolien Maritime France, 2022) | Fécamp | France | Offshore | 500 MW | offsets 2 Mt of CO2/year |
(Iberdrola, 2020) | Saint-Brieuc | Offshore | 496 MW | 1st large-scale offshore site in Brittany | |
(WindEurope, 2023) | Saint-Nazaire | Offshore | 496 MW | still under construction | |
(Newman, 2018) | El Cabrito | Spain | Onshore | 30 MW | repowered in 2019 |
(Newman, 2018) | Sotavento | Onshore | 17.5 MW | real-time data available online | |
(Newman, 2018) | S. d'Abruzzo | Italy | Onshore | 13 MW | best-practice case |
(BKW, 2023) | Puglia | Onshore | 130 MW | allowed to significantly exceed BKW's 1,000 megawatt target | |
(Iberdrola, 2023) | Baltic Eagle | Germany | Offshore | 476 MW | avoids almost 1Mt of CO2/year |
(Power Technology, 2019) | Gode Wind | Offshore | 582 MW | powers 600,000 households | |
(Moray Offshore Renewable Power, 2014) | Moray East | UK | Offshore | 1.12 MW | provides 40% of Scotland's electricity |
(Orsted, 2022) | Hornsea 2 | Offshore | 1.3 GW | powers more than 1.4 million homes | |
(GmbH, 2022) | Triton Knoll | Offshore | 857 MW | largest offshore wind pipeline in the UK | |
(Newman, 2018) | North Hoyle | Offshore | 60 MW | Wales' first offshore wind farm | |
(Newman, 2018) | Walney | Offshore | 659 MW | world's largest operational offshore site | |
(Newman, 2018) | W.Duddon Sands | Offshore | 500 MW | serves more than 270,000 households | |
(Interesting Engineering, 2016) | Whitelee | Onshore | 539 MW | largest onshore wind farm in the UK | |
(Interesting Engineering, 2016) | Viking | Onshore | 457 MW | third largest wind farm in Scotland | |
(Power Technology, 2019) | F. Cogealac | Romania | Offshore | 600 MW | provides 10% of renewables in Romania |
*Germany, Denmark, Netherlands, UK ** for the highest capacity turbine, depending on the construction phase (https://markbygden1101.com/the-place-and-purpose/) |
● Table 3: thoroughly assessing key documents and their cited sources (for more than one layer of citation) for the particular case of R-strategies used in the sector, as is the case of (Jensen and Skelton, 2018; Committee, 2019; Rahimizadeh et al., 2019; Beauson et al., 2021; Beauson et al., 2021; Bennet, 2021; Intelligence, 2021; Rani et al., 2021; Velenturf, 2021; ELETAEN Association, 2022; Europe, 2022) etc.
Ref. | Year | Strategy | Application |
(Re-wind network, 2018; Jacobs, 2021; Joustra et al., 2021) | 2018, 2021 | Reuse; Repurpose | New turbine/blade; Platforms; docks; piers; jetties; buoys; seawalls; bridges; powerline poles; electricity transmission towers; cellphone towers; lighting and luminaire poles; sign support poles; sound barriers; access barriers; erosion barriers; shelters; glamping pods; canopies; roofing solutions; walls and foundations; partitions; feed bunks; |
(Medici et al., 2020; Architecture news & editorial desk, 2021, Jacobs, 2021) | 2021, 2020 | Repurpose | Bike sheds; playgrounds; public seats; bus stops; reefs |
(Bank et al., 2018) | 2018 | Repurpose | Housing applications |
(Schmid et al., 2020) | 2020 | Recycle | Furniture; automotive parts |
(Oliveux et al., 2015, Rani et al., 2021) | 2015, 2021 | Recycle | Replace small amounts of virgin fibers |
(Jensen and Skelton, 2018, ETIPWind Executive Committee, 2019; Jacobs, 2021; reNewsBiz, 2021) | 2021, 2019, 2018 | Recover; Recycle | Cement co-processing Industrial filler material |
(Bloomberg, 2021) | 2021 | Recycle | Sports gear |
(Jacobs, 2021; Velenturf, 2021) | 2021 | Recycle | Repurposed metal; surplus slag for construction aggregate; precast concrete; precast manhole; sandwich construction panels; cement; concrete blocks; energy |
● Table 4: literature search for dedicated keywords such as "wind energy environmental assessment", "wind turbines recycling impacts", "wind energy environmental impacts", etc.; then selecting literature that provided the information present in the table columns; also, reading literature reviews in the topic that could cite relevant works, such as (Tremeac and Meunier, 2009; Garrett and Rønde, 2013; Dai et al., 2015; Martínez et al., 2018; Ozoemena et al., 2018; Gomaa et al., 2019; Razdan and Garrett, 2019; Heng et al., 2021; Prabhu and Mukhopadhyay, 2021).
Wind turbine power (MW) | Ranking of life cycle stages' contribution to the impacts | Main environmental impact categories | Environmental impact value | Impact assessment method | Reference |
1.5 | RMA+M+I+T > OM > EL | GWP | 1.18 x 10−2 | CML | (Ozoemena et al., 2018) |
ODP | 1.24 x 10−9 | ||||
AP | 9.17 x 10−5 | ||||
EP* | 6.90 x 10−5 | ||||
POCP | 6.54 x 10−6 | ||||
2.0 | RMA+M > I > OM > T > EL | GWP | 1.80 x 10−2 | TRACI | (Alsaleh and Sattler, 2019) |
ODP | 2.69 x 10−9 | ||||
AP | 1.04 x 10−4 | ||||
EP* | 9.78 x 10−5 | ||||
S | 1.71 x 10−3 | ||||
2.0 | RMA+M+T > OM > I > EL | GWP | 7.70 x 10−3 | CML/ ReCiPe | (Garrett and Rønde, 2013) |
AP | 3.70 x 10−5 | ||||
EP** | 3.70 x 10−6 | ||||
POCP | 5.40 x 10−6 | ||||
2.0 | Information not available | GWP | 6.58 x 10−3 | CML Leiden 2000 | (Martínez et al., 2018) |
ODP | 5.21 x 10−10 | ||||
POCP | 2.13 x 10−6 | ||||
AP | 5.43 x 10−5 | ||||
EP* | 5.68 x 10−6 | ||||
3.0 | RMA+M > I > T > OM | GWP | 9.11 x 10−3 | TRACI | (Martínez et al., 2018) |
AP | 3.45 x 10−3 | ||||
EP** | 8.3 x 10−6 | ||||
ODP | 1.14 x 10−9 | ||||
S | 2.73 × 10−5 | ||||
ET | 2.9 x 10−2 | ||||
4.2 | RMA+M > I > OM > EL | GWP | 5.6 x 10−3 | CML | (Razdan and Garrett, 2019) |
AP | 2.2 x 10−5 | ||||
EP | 2.7 x 10−6 | ||||
POCP | 1.6 x 10−6 | ||||
4.5 | RMA+M+I > T > OM > EL | GWP | 1.60 x 10−2 | Impact 2002+ | (Tremeac and Meunier, 2009) |
RD | 3.00 x 10−4 | ||||
Life cycle stages: RMA - Raw materials acquisition; M – Manufacturing; I - Installation; OM - Operation and maintenance; T - Transportation; EL - End of life. Environmental Impact Categories: GWP = Global warming potential (kg CO2 eq/kWh), ODP = Ozone depletion potential (CFC-11eq/kWh), AP = Acidification potential (kg SO2 eq/kWh), EP* = Eutrophication potential (kg PO4 eq kg/kWh), EP** = Eutrophication potential (kg N eq/kWh), S = Smog (kg O3 eq/kWh), POCP = Photochemical ozone creation potential (kg C2H4 eq/kWh), RD = Resources depletion (GJ primary non-renewable energy/kWh), ET = Ecotoxicity (CTUe/kWh). |
From a material perspective, concerning life cycle and environmental burdens, wind power systems involve high quantities of material resources along the life cycle.
Figure 2 shows the typical wind turbine components and their main constituent materials.
It is important to notice that other trace materials also exist (aluminum, nickel, cobalt, balsa wood and rare earth metals such as neodymium and dysprosium) although there is currently not enough data to suitably estimate their quantities (Jacobs, 2021). The Hellenic Wind Energy Association has recently compiled a complete list of all the materials and the wind turbine parts in which they are located aiming to advise the stakeholders to adequately plan the needed facilities to process these materials, to accurately estimate the value of scrap achieved from decommissioning and to identify potentially harmful substances (ELETAEN Association, 2022). In line with this, regulations such as mandatory recycling of components or decommissioning cost studies are being introduced as permit requirements for wind energy projects. Additionally, best practices are being followed to better pursue not the minimum requirements but having a positive impact, following the EU taxonomy of "do no significant harm" (European Commission, 2021).
In terms of material usage, a recent report estimates that around 5,613 turbines will be decommissioned between 2021 and 2050 only in Scotland, generating up to 1.4 million tonnes of material, and that by 2040 circa 240 turbines per year will have to be managed (Jacobs, 2021). This represents over 60,000 tonnes of fiberglass and 90,000 tonnes of resin and balsa, which are currently being landfilled. Indeed, the understanding of the state of material utilization for wind power technology will help to optimize the distribution of wind energy facilities, improve the material efficiency associated with energy technology deployment and ultimately advance the green development of the wind power industry (Garrett and Rønde, 2013). The material efficiency and material flow analysis must become key aspects in energy production systems. Different studies assess these parameters in Wind Power Systems (Cognet et al., 2020; Yang et al., 2020; Farina and Anctil, 2022). After the stabilization of the general design of wind turbines in the early 90s, the main engineering objective was focused on increasing rotor diameter, as it determines the overall capacity of the machine. The rotor diameter is expected to continue growing for the foreseeable future as more and more power is extracted at each site (Wiser et al., 2021). Power extraction is a direct function of the area covered by the rotor and is therefore proportional to the square of the length of the blade–hence the incentive to increase blade length (Wiser et al., 2021). Therefore, to potentiate the power extraction, larger models have been produced. Rotor blades account for only a fraction of the weight of a wind turbine but constitute nearly a quarter of the manufacturing costs, therefore motivating the quest for saving resources in this specific component. These also foster the production of waste, as they comprise complex materials (German Wind Power Magazine, 2021). The difficulty level is amplified in the next decades by the forecasting for the waste material, for offshore and onshore (Lichtenegger et al., 2020; Chen et al., 2021; Heng et al., 2021).
Wind turbine blades are aerodynamic lift devices, which must operate within the designed wind speed parameters and perform turbine specific functions (such as pitch around the axis of blade rotation for control purposes) (Yang, 2020). As blades increase in size, they also become increasingly svelte, posing further bending and flutter (edge and flap-wise instability caused by a flow excitation that occurs close to the blade's natural frequency and causes significant periodic movements in the structure) and/or gravity induced fatigue issues to the designer. Furthermore, wind speed will also vary, causing flap-wise fatigue loads, which are of the order of magnitude of the lift loads that rotate the blade. Also, important gravity loads occur as the blades rotate (typically at below 85 m/s, > 300 km/h, tip speed) (Yang, 2020). In a typical rotation, a single blade undergoes a change in loading direction, as it is bent forwards, undergoes traction, is bent backwards and is compressed.
Considering the blade geometry and materials, the construction of wind turbine blades has developed to a stable configuration containing two shells and two shear webs (Mishnaevsky et al., 2017), as shown in Figure 3. Additional evolutions are expected to occur due to the continued extension of the blades, and the transportation difficulty they induce.
Within the blade itself, a common arrangement of materials includes a number of sandwich areas in the leading and trailing edges, as well as a stiffer laminates in a box beam arrangement consisting of the flange areas, which are integrated in the aeroshell, and the two shear webs. Material selection follows also the manufacturing (vacuum infusion) and integration approach (adhesively joining) that has become standard within the industry. This is done to comply with the requirements but also due to manufacturing quality, cost considerations, complexity of the shapes to produce, assembly process, abrasion and impact resistance (Brøndsted et al., 2005).
In the last decade, with the increased concerns on climate changes and environmental burdens in the energy sector, the challenges of wind power systems have been addressed with multiple studies, namely on recycling technologies which can provide solid answers towards end-of-life current issues. Recent research efforts focus on core materials, damping and aero-elasticity, structural health monitoring and recyclability (Jensen and Skelton, 2018). In the case of rotor blades recycling, recovery or reuse of material in other applications, different studies, technologies and circular economy-oriented projects have been carried out (Pimenta and Pinho, 2011; Cousins et al., 2019; Dorigato, 2021; Rani et al., 2021; Sommer and Walther, 2021). The main problems associated with the use of composite materials are related to lightning strike damage, crack propagation, fatigue life and adhesives (Marin et al., 2009; Shohag et al., 2017; Mishnaevsky, 2022). Regarding manufacturing issues, the most common ones relate to voids, curing, energy consumption, failure in filling, temperature damage and adhesive failure (Shah, 2014; Mishnaevsky and Thomsen, 2020). Lightning damages and fatigue are also considered issues with in-service systems, as well as abrasion.
Some interesting EU projects in wind turbine blades have also been developed over the years, as shown in Table 1.
From Table 1, it is possible to observe that the sector has been very active in dealing with several issues related to wind turbines and their components in the last 20 years. In general terms, this broadly matches the period where the first main sets of wind turbines entered the end of operations stage, triggering a series of projects that contributed to composite and glass fiber recycling (Hebo Engineering BV, 2003; SAS, 2009; STENA, 2009; Richerche, 2011; Selfrag, 2012), repairing and remanufacturing procedures (European Commission, 2012; Cranfield University, 2013), and design aspects (Fraunhofer Gesellschaft Zur Forderung Der Angewandten Forschung EV, 2013; LM Wind Power, 2022) to achieve a longer life. Gradually, the topics of the projects evolved to technical aspects more associated to complex materials (University of Bristol, 2014; Fraunhofer Institute for Process Engineering and Packaging IVV, 2014; Svendsen, 2017; Markaide, 2018; National Composites Centre, 2021), frameworks (Interreg, 2016; The German Federal Environment Agency, 2017; Community, 2020), and business models (Re-wind network, 2018). This is aligned with the current guidelines and overarching topics of circular economy and sustainable development, especially the projects connected to the development of innovative concepts, circular strategies, and integrated consortia covering the whole value chain (Colledani, 2017; DecomBlades, 2021).
The wind industry, driven by the decrease in low impact areas available at on-shore locations, has been directed to offshore that, in the last years has been under a rapid development (Clement, 2021). Its great potential in retrieving clean renewable energy has been widely supported by the economic and political decision makers (Wu et al., 2019a). In fact, the offshore wind technology presents, at this stage, a high readiness level when comparing with other renewable energy technologies. Its abundant wind resource and reduced environmental risk increases its general acceptance, its importance being widely recognized.
Offshore Wind Turbines (OWT's) are, nowadays, the main focus of wind technology development (Ren et al., 2021). Several factors have been driving this technology to more offshore areas, including the available wind resource, lower turbulence, space for establishment, lower transmission and distribution losses, lesser visual impact, and less noise pollution. Europe is the best example of this transition from on-shore to offshore technology (Jiang et al., 2017). The North Sea, due to its favorable wind conditions at shallow water conditions accounts for almost 70% of the world's cumulative offshore wind capacity.
Shallow water conditions are ideal for the installation of offshore bottom fixed structures, but the main portion of wind resources is found in deep waters, where the ground-based structures are not economically feasible. In recent years, the technology advancements on floating offshore wind turbines (FOWTs) allowed solutions for deeper water areas (Zhang et al., 2020; Rueter, 2021). The experience and technology from the offshore oil and gas industry have been applied to further the technological advancements of FOWTs. The main challenge of these types of structures is to achieve the dynamic stability of the floating support platforms. There are three main types of floating support platforms for FOWTs: (ⅰ) Semisubmersible; (ⅱ) Spar Buoy; and (ⅲ) Tension leg platforms (TLP) (Figure 4). Some of the most iconic projects using this technology are Hywind demo (Driscoll et al., 2016) in Norway, WindFloat (Maciel, 2010) in Portugal, Fukushima phase Ⅱ FOWT (Boccard, 2014) in Japan and Hywind Scotland (Skaare, 2017) in the UK. It is expected that, in the upcoming years, the FOWTs migrate to the semi-submersible type due to the advantages regarding its application for various water depths, low installation costs and recent developments of mooring systems and rope material. Both the TLP and the Spar Buoy present large costs for installation, transport, decommissioning and maintenance (Ren et al., 2021). The semi-submersible type allows a generic system to transport the assembled floating turbine platform to the desired location. Also, for decommissioning and maintenance, it is possible to transport the whole system for the port yards.
Recent developments of FOWT's present different shapes of the semi-submersible structure allowing also an increased number of wind turbines per floating unit. Some of the more recent developments regarding the FOWTs are the WindFloat, Dutch Tri-floater, Windsea, Windflo, Braceless, V-shaped, OC4-DeepCwind, X1Wind and W2Power (from Enerocean). However, the FOWTs still present some challenges, mainly due to their recent applications and therefore limited experience regarding the long-term stability issues of the structure and its hydrodynamic performance for different loads (Jiang et al., 2017).
The installation of OWT involves a complex framework in which many parts of a wind turbine are assembled and connected to the grid. It is even more difficult when this type of activity occurs mostly offshore (for FOWTs, only the grid connection needs to be performed offshore). The marine operations of offshore assembly are extremely challenging because it includes the installation of auxiliary equipment, therefore it must be held in limited timeline due to the weather conditions, and involves significant risks in lifting and assembly operations. Still, large technical developments are being made for installation vessels and equipment and engineering research to overcome the technical problems (Jiang, 2021).
Table 2 shows details for some of the currently largest wind operations in Europe.
As seen from Table 2, there are multiple wind energy projects throughout Europe, on and offshore in several different locations. This shows the enormous potential that this form of energy has to contribute to national grids as well as the market demands. Regarding technological evolution, notable gains have been seen in terms of production, Europe's largest onshore wind farm being expected to produce between 8 and 12 TWh of energy per year, while offshore there are sites producing up to 6 GW (Netherlands Enterprise Agency, 2022). Concerning the population covered, technology development (in terms of materials, structures, business models, etc.) enables most of the wind farms' production to reach thousands of consumers, offsetting a high yield of CO2 emissions per year (Eolien Maritime France, 2022, Iberdrola, 2023).
In the future it is expected that the offshore wind industry continues to grow more that the onshore industry, mainly in Europe and China. A significant transition is expected for deeper waters with the recent developments on FOWTs allowing more stable and improved wind conditions when comparing with onshore wind farms (Jiang et al., 2017, Rueter, 2021). Still, several technical aspects and adapting support industry needs to grow to reduce the overall levelized cost of energy (LCOE).
The circular economy can be described as an economic system based on the reuse and recycling of products and materials and the conservation of natural resources, while seeking to create value in every link of the system (Potting et al., 2017). Thus, developing recyclable and/or reusable materials could be the first step, allowing for a more circular economy, as seen in Figure 5.
Reusing products and recycling materials promotes conservation, because fewer natural resources need to be extracted to produce new materials. This implies less waste generated and less harmful substances released into the environment (air, water and soil). Furthermore, it creates a shift towards resource use and energy from renewable sources. Recycling can occur in a closed or open loop: closed if it occurs within the same product system, or open if it occurs in a different product system. Closed-loop solutions should be preferred over open-loop solutions, if the production process can incorporate recycled material without using extra energy or additives, avoiding materials collection and transportation and potentially reducing the environmental impacts. However, closed loop recycling is not always better than open loop recycling. Depending on the materials, products and industries specific targets should be set (Morseletto, 2020).
The main drivers for achieving circularity in the wind energy sector are especially related to the context surrounding the promotion of renewable energies, supported by the technological developments, the advanced design tools and the market demand for bigger and more efficient equipment (Ostachowicz et al., 2016). Usually, the bigger and longer the blades and the higher the turbines are installed, higher wind speeds will be available, therefore increasing the power produced. In fact, wind turbine dimensions have been increasing from 15 m diameter in 1985 to some current offshore solutions that reach more than 200 m diameter, with 14 MW nominal power (Siemens Gamesa, 2022). Some legislation also promotes circularity by reuse and recycling actions; nevertheless, there are some challenges associated to these activities (Cherrington et al., 2012; Potting et al., 2017). Another important promoter is definitely the cost of energy to enable investments. Several parameters must be taken into account such as installation costs, wind farm layout, maintenance costs among others to counterbalance the revenues achieved.
Upon analyzing the wind energy panorama, some aspects referring to the sustainability of the industry and the technological developments that contribute to advance circularity in the sector, Figure 6 resumes the main drivers, challenges and barriers related to the wind energy circularity.
As part of the sustainable transition, the authorities and the industry now claim that the turbine blades are not to be disposed of, and instead, these should be converted or recycled. Nevertheless, there are some major challenges preventing a faster evolution to the desired scenario. Among the main challenges that the sector faces to embrace full circularity is the fact that the majority of the currently installed blades are designed to last for a long time and manufactured with a complex net of materials to prevent breaking and weathering but with no sustainable end-of-life features incorporated. Despite promoting durability (which is obviously good), this hinders the blades' reuse or recycling when they finally reach the end-of-life and are a residue and not a resource.
On average, the recyclability of the wind turbine components is estimated to be about 80% (wt) (Cherrington et al., 2012). Although the metal components of the wind turbine are highly recyclable (e.g., steel, aluminum and copper) due to their intrinsic properties, the recyclability of the blades composite material is very low. In fact, although it is neither toxic nor harmful, the complex composite material (typically glass and/or carbon fibers in a cured thermoset polymeric/plastic matrix of polyester, epoxy resin or polyurethane adhesive) still presents a challenging problem for recycling or reuse, due to several factors (Cherrington et al., 2012):
(ⅰ) After about 20-year lifetime, the reduction in material quality, due to blades exposure to hostile weather conditions, may not be acceptable for their reuse;
(ⅱ) Due to their large dimensions, the dismantling, cutting and transporting of blades, entail logistical, environmental and economic problems;
(ⅲ) The cross-linked nature of the thermoset resins prevents them from being remolded;
(ⅳ) The composite material that the blades are made of is a complex mixture of different components (fibers, matrix and fillers);
(ⅴ) The mechanical recycling process damages individual fibers, reducing the material mechanical performance; and thus, it can only be used for less demanding applications (e.g. as filler for asphalt, or as aggregates in the construction industry);
(ⅵ) Since the European waste management policy has effectively managed to divert this type of composite materials' wastes from landfill disposal, the preferred alternative destination has been incineration with energy recovery (e.g., mixed with 10% municipal solid waste).
Besides the highlighted challenges, there are also a number of obstacles, namely bureaucratic rules and legislation, the problems associated to the establishment of a secondary market for recycled/recovered materials, parts or components, and the export of critical materials and sector waste (Cherrington et al., 2012). Regarding the possible materials to address, there are multiple advantages in using carbon fiber over glass fiber (superior strength and higher stiffness), but its higher cost per volume constitutes a key barrier to further advance this option (Jensen and Skelton, 2018).
Although recycling ranks low in the circular strategies hierarchy (Morseletto, 2020) as it is an energy- and water-intensive option, developing recyclable materials could be the first step to sustainable methods of waste disposal (Cherrington et al., 2012). The development of materials that can withstand multiple climate impacts, high variations in humidity and temperature, and mechanical and environmental loads over several decades, constitutes an extra problem (Mishnaevsky, 2021). Another difficulty is to find applications with sufficiently low requirements for mechanical properties, as the fibers from mechanical recycling usually show reduced reinforcement efficacy when used in new materials such as composites (Beauson et al., 2021). There are some methods to largely recover the initial strength, at the expense of raising the cost of the recycled fibers in opposition to the cheap virgin material. In the case of chemical recycling, upscaling issues seem to be hampering a better output, as to date these are not able to process composite waste in large quantities. On the other hand, there are economic parameters that also influence the project viability such as capital recovery factor and annual energy production (Ioannou et al., 2018). Additionally, maintenance costs are generally high, and there is lost revenue during repair periods for out-of-service turbines (Mishnaevsky, 2021).
Concerning decommissioning of wind turbines, both on-shore and offshore, the wind energy sector does not currently have an international standard on the matter, and, therefore, the European association of the wind energy sector challenged several stakeholders to elaborate a guideline in order to provide a sustainable decommissioning of the wind turbines (Wind Europe, 2020). The main purpose of this document was to propose to the International Electrotechnical Commission (IEC) an expansion of the scope of the technical specification for the standardization in the management of the wind turbines expected lifetime and beyond, and to include the decommissioning phase of wind turbines, assuring the forwarding of the respective waste via the specific paths. A new IEC working group will now dedicate some work to describe the tasks and considerations of the decommissioning process (IEC TS 61400-28-1 Decommissioning and preparation for recycling (European Commission, 2021)).
Another setback for the dismantling process is that the time for decommissioning of the wind turbines is not uniform as it depends on several factors like the economic viability of the project, the regulatory framework in effect, the profile of the investor, the applicable tariffs, among others. Presently, in Europe, about 4 GW of capacity have been decommissioned, representing around 50,000 tons of composite waste from the blades (Wind Europe, 2020). Over the next years, the volume of annual wind turbines to be decommissioned will strongly depend on the policies and incentives of each country as well on the electricity prices. Wind Europe association predicts that the blade waste can reach around 25,000 tons per year by 2025 and up to 52,000 tons per year by 2030 (Wind Europe, 2020). In order to accelerate the circularity of the sector, the wind industry calls for a Europe-wide landfill ban for the decommissioned wind turbine blades by 2025 (Wind Europe, 2020). This challenge implies a commitment on the reuse, recycling and recovery strategies.
After evaluating the most recent literature, technical reports and other documents emitted from the wind energy stakeholders, a series of knowledge gaps regarding contributions to circularity was detected. They encompass, for instance, matters related to the emission of material passports, certification, the challenge of integrating life cycle assessment (LCA) in tenders and their evaluation criteria, as well as applying it to the waste hierarchy (Morseletto, 2020). Additionally, implementing R-strategies to the wind turbines, their components and materials, establishing a broadly recognized common framework, modularity and eco-design, and design-for-decommissioning are still fields to explore, among others (Schmid et al., 2020; Bennet, 2021, Jacobs, 2021). There are also some concerning topics with no (or few) assessments conducted so far in Europe, namely the utilization of lead-free cables, the dematerialization of the sector, related waste prevention, disassembly of turbines, re-mining, energy recovery, recertification of components/parts and restoring of wind farm sites (Exter et al., 2021; German Wind Power Magazine, 2021; Velenturf, 2021).
These correspond to more technical aspects of the problem; nevertheless, the policy context should also be addressed to regulate important issues as extended producer responsibility (EPR), second-hand markets for used equipment and their components, as well as the business models associated to this, the export of critical materials and wastes, and incineration/landfill bans (Cherrington et al., 2012; Nguyen and Imholte, 2016; Jensen and Skelton, 2018, Prabhu and Mukhopadhyay, 2021). Sometimes, national policies are not aligned to international definitions, as wind markets develop at a different pace. Several regulatory instruments may be used by the authorities to incentivize recycling, including legally binding targets, landfill bans and/or taxes and requirements for EPR; nevertheless, enhanced harmonization of guidelines and legislation is necessary (Schmid et al., 2020). According to the European classification of wastes, different plastic categories may be attributed to composite blade waste (e.g., plastic waste from demolition and construction, plastic waste from organic chemical processes, waste glass-based fibrous materials from thermal processes, waste glass other than the previous ones, wastes not otherwise specified from thermal processes, plastics shavings and turnings from shaping and physical mechanical surface treatment of metals and plastics). Authorities need to ensure the application of a suitable code to blade waste, guaranteeing efficient sorting and collection (Schmid et al., 2020). This would also support secondary material markets, ensuring a more stable supply chain.
Concerning current challenges of the sector, the most highlighted are related to blade material, namely stiffness optimization, fatigue life, development of light weight structures, and damage prediction methods (Schmid et al., 2020). Material selection is mainly determined by price, availability, location and performance-related properties such as process abilities, material integrity, and the demand for longer wind turbine blades. Actually, materials research is considered an important area of investigation for the attainment of sector goals (Cherrington et al., 2012; Jensen and Skelton, 2018), and will be discussed in the following sections. There is also an economic opportunity related to the externalities of the wind energy sector, namely the non-environmental categories (Cherrington et al., 2012). This will be discussed in more detail in section 4.2.2. Also, the energy demand to use recycled composites is roughly one tenth of the energy needed to produce new material, therefore besides the innovation opportunity there is always energy efficiency and cost savings to achieve (Jensen and Skelton, 2018).
There are several approaches towards circularity, the R-strategies being among the most known ones. These comprise different actions, classified into 3 main aims: smarter product use and manufacture, extend lifespan of product and its parts and the useful application of materials. This sequence of strategies ranges from higher circularity levels to options that are closer to the linear system (Potting et al., 2017). Smarter production and use include refusing, rethinking and reducing in an effort to achieve the expected function with a completely different product, making product use more intensive and increasing its use and manufacturing efficiency.
The University of Leeds proposes a framework of 15 elements to optimize values for a sustainable circular economy: design for circularity, dematerialization, waste reduction, repair and maintenance, lifetime extension, reuse and refurbishing, remanufacture, disassembly, repowering, decommissioning, site recovery, recycling, landfill and controlled storage, re-mining and energy recovery (Circular, 2020). All of these are expected to deliver on social, environmental and economic values through the optimization of the technical value of materials, components and products. This might be achieved by narrowing, slowing down and closing the loop on resource flows, as well as safely reincorporating material flows into natural processes (Bennet, 2021). A combination of four circular strategies to aid in mitigating the shortage of materials, alleviating the need for critical metals while increasing their supply is put forward by Metabolic, Copper 8, Quintel Intelligence and Polaris: rethink, reduce, repair and recycle (Exter et al., 2021). A Danish innovation consortium identified a value circle for these materials, developing secondary applications based in five circular strategies: reuse, resize/reshape, recycle, recover and conversion (Jensen and Skelton, 2018).
Although only few European countries currently ban landfilling wind turbine blades, and while the European Commission is being pressured to extend it by 2025, some big players are already taking important measures to tackle sector-related waste management.
Vestas aims to produce zero-waste wind turbines by 2040 and LM Wind Power targets the same goal for 2030 (Radowitz, 2021), having become the first business in the wind industry to achieve carbon neutrality in 2018 (LM Wind Power, 2021). Orsted has committed to the sustainable reuse or recycling of turbine blades (Bloomberg, 2021; reNewsBiz, 2021), Endesa is celebrating its 10th anniversary since embracing the application of circular economy principles (repairing, refurbishing and reusing damaged wind turbine parts) (Energias Renovables, 2021), and Siemens Gamesa launched "RecyclableBlade", the world's first fully recyclable blade (Siemens Gamesa, 2021). Besides, the company has been also focusing the business on the repair and updating of nacelle components to be able to be reused in wind turbines, giving them a second useful life. The restored components contribute to minimize the generation of waste and avoid the consumption of new raw materials, energy consumption and the generation of more CO2 emissions during the production phase. Also, albeit wind turbines already present 85% to 90% recyclability rate, a growing number of tenders for wind energy requires even greater recyclability (ETIPWind Executive Committee, 2019).
LM Wind Power is already acting in some of these concepts, engaging with suppliers to reduce/eliminate the fiberglass waste and replace virgin materials as balsa wood with recycled plastic foams in the manufacturing of turbine blades. This contributes to the zero-waste goal by designing waste out from the value chain (Schupak, 2021). Regarding the waste that still persists, the company is increasing efforts to separate it by color to enable specific recycling routes, also stimulating markets for recycled materials. Lifetime extension strategies enclose reuse, repair, refurbish, remanufacture and repurpose. In the case of repurposing, literature refers to the adaptation of wind turbine blades into public infrastructures as bridges (Re-wind network, 2018) and bike sheds (Architecture news & editorial desk, 2021), playgrounds, garden benches, furniture (Ostachowicz et al., 2016) or even housing structures and other buildings (Bank et al., 2018). Table 3 presents some relevant works that show end-of-life applications for the sector.
Regarding the useful application/recovery of materials, it is present in solutions such as recycling the glass fibers from the blades and further using the material in automotive parts and sports gear (ELETAEN Association, 2022), and composite recycling through cement
co-processing (reNewsBiz, 2021), which reduces carbon footprint of cement by up to 16% (ETIPWind Executive Committee, 2019; Siemens Gamesa, 2021; German Wind Power Magazine, 2021). Among the recycling and energy recovery options for this kind of materials are gasification, solvolysis and high voltage pulse fragmentation, and pyrolysis, mechanical grinding and co-processing (ETIPWind Executive Committee, 2019). The current methods for disposing turbine blades are resumed to landfill, thermal recycling and mechanical recycling, albeit some authors mention four categories of recycling technologies: mechanical, thermal, chemical and reprocessing (Beauson et al., 2021; Bennet, 2021).
In fact, relative to the waste hierarchy in the sector, blades are the most representative elements of the end-of-life possible scenarios. Figure 7 presents the hierarchy for sustainable blade waste management.
Generally, prevention of blade waste might be accomplished mainly by reduction and substitution strategies in the design phase, while the reusability is also tightly related to design. Indeed, the ability to go under routine servicing and repair actions is necessary to achieve a blade's design lifetime. In the case of second life, refurbished turbines and components should pass a (re-)certification scheme to attest to their quality and safety (Schmid et al., 2020). Repurpose means re-using an existing part of the blade for a different function, commonly with lower value than the original. For instance, second-generation glass fiber is sold at a competitive price compared to virgin glass fiber, for use in automotive, marine and consumer products (Bloomberg, 2021). Recycling is a less circular option, as it requires energy to convert the blade into another product, while energy recovery is the last considered option before actually disposing these wastes in landfills. This recovery involves converting waste into a fuel or thermal energy, under a series of possible waste-to-energy technologies, as described in (Schmid et al., 2020; Beauson et al., 2021; Bennet, 2021). Landfill or incineration in the absence of energy recovery are the least preferred alternatives, disposal meaning that no value is recovered from the discarded resources, therefore no circularity being implied. In general, the residues generated from wind turbines are treated under three forms: full turbine, its parts, and individual materials (Jacobs, 2021). The most common applied strategies are the refurbishment of the turbine, reuse of its components, recycling and thermal processing of the materials.
Mechanical treatments refer to grinding and cement kiln co-processing, whereas thermal techniques include pyrolysis, gasification, incineration and microwave-assisted options. Chemical recycling encompasses solvolysis and electrochemical treatments, while reprocessing turn the reclaimed materials into secondary materials to be utilized in different applications. Reprocessing converts the discarded materials into milled fibers, chopped tows, pellets and non-woven mat (Bennet, 2021). DecomBlades (DecomBlades, 2021) is a project aiming to provide the basis for commercialization of sustainable recycling of wind turbine blades. This project covers recycling strategies such as pre-processing and shredding, pyrolysis and cement co-processing.
Given the actual context and implemented solutions, the next steps for a circular wind energy sector are the following (Jensen and Skelton, 2018; Schmid et al., 2020; Bennet, 2021; German Wind Power Magazine, 2021):
● promoting the development of novel high-performance materials for circularity (design for longer lifetime, reuse/repurpose and "from and for recycling" approach);
● shifting the focus of R & D activities to the supply chain to produce the end products rather than the recyclate with no clear destination;
● leveraging the diversity of active R & D projects on composites across different sectors to promote wind turbine blade recycling, namely, aerospace, automotive, marine applications, oil & gas, construction, defense, sports;
● establishing more reliable and efficient recycling processes;
● scaling-up carbon fiber recycling;
● conducting environmental assessments related to the choice of materials along the design phase, as well as to distinct end-of-life scenarios;
● performing integrated assessment of the environmental, social, economic and technical costs and benefits to reach balanced decisions and support policy-making with strong pleas.
On the one hand, further development and industrialization of alternative technologies should be fostered to provide alternative solutions for end-of-life management; on the other hand, national governments should standardize their implementation of EU regulations on waste treatment to support a market for recycled composites (Roland et al., 2021).
More than 100,000 tons of rare earth permanent magnets are consumed each year by the renewable energy sector (Roland et al., 2021). According to the Dutch ministry of infrastructure, to comply with the GHG emission reduction targets under the Paris Agreement, the global production of several rare earth metals used in wind turbines such as neodymium, terbium, indium, dysprosium, and praseodymium, must grow twelvefold by 2050 (not including other applications for these materials such as smartphones, tablets, laptops or electric vehicles) (van Exter et al., 2018). With some of them presenting recoverability rates as low as 1%, critical supply bottlenecks will be inevitable. The production monopoly and the illegal production schemes for these metals are also a concern (Nguyen and Imholte, 2016). The use of secondary raw materials presents lower environmental impacts than extracting virgin resources, which reinforces the need to recover and recycle these materials at the end-of-life stage (Roland et al., 2021). Therefore, resourcing to these will help to establish a secure supply of rare earth raw materials at no expense for the environment. Meanwhile, defining standards and certifications schemes to grant a sustainable re-use of these materials will promote innovation capacity in the value chain.
New material-based blades are also an urgent need. Thermoplastic solutions, recycled plastics, new resins and bio-materials such as sugarcane, beet crops, wood, wood pulp or bamboo present promising options, while "more decomposable epoxy" is also needed so that content can be extracted more easily from the composite structure. China's Heibei Zhangbei and Shandong Hekou wind farms use onshore wind turbine blades made of bamboo fibers and have been operated for many years (Siemens Gamesa, 2022). It is expected that these new materials provide enhanced chemical recyclability and reusability in mild conditions, so that the fibers retain most of their strength. Vestas is developing wooden turbine towers to dramatically reduce CO2 impact, in comparison to the current use of steel.
Despite the merits of renewable energy sources, the environmental impacts of the enclosure technologies must be accurately assessed throughout the entire life cycle. For that, data on the LCA of various technologies must be compiled, namely for the recycling, and adequate recommendations for the eco-design of energy systems must be extracted, as studied by Ratner et al (Ratner et al., 2020). Wind power systems and wind turbines have gained increased attention in the last decade, regarding the urgent need to be designed according to eco-design principles and circular design mind-set. In the scarce scientific works on the subject, Bonou et al. (2016) developed a new ecodesign framework to address the wind turbines development. The study was based on a long project where design iterations were assessed via LCA, for which an integrated approach was constructed. The study follows a previous introductory work on life cycle thinking, applied in the development case study of a Wind Power System (Bonou et al., 2015). Besides the key re-focus on the design stage, and the application of ecodesign techniques, the sustainability of a wind system should be evaluated in a broader way, aggregating efficiency, performance and eco-efficiency indicators that assess in detail either the environmental impacts and costs along all the life cycle stages (from cradle-to-grave spectrum or preferably in a circular mind-set of cradle-to-cradle). Maradin et al. (2021) conducted a study focused on the economic and technical aspects for the efficiency of wind power companies. More on the side of the technical performance of wind turbines and the cost optimization variable, Yassine et al (Yassine and Abdul-Wahab, 2020) worked on the simulation and energy prediction for different technologies, geographic localization and key operational parameters, regarding case studies in Oman. Wu et al (Wu et al., 2019b) presented a novel model for performance evaluation for sustainability of wind energy project using improved multi-criteria decision-making method, that was applied in the comparison of three real use cases in China. The framework is well described, covering in detail the triple bottom-line for sustainability assessment (economical, environmental and social KPIs). These latter types of approaches allow a more integrated assessment that can be used by different stakeholders, from utilities contractors, manufacturers, energy distributers and even government authorities. Despite the cited works proposals, different research gaps and industrial/economic needs must be addressed in the short term. For instance, more studies on the detailed comparison, at design stage, for solutions applied in on-shore versus different off-shore options; more scientific studies on aspects related to existent wind farms (what should be the best options regarding extended life-cycle projects, including retrofitting, refurbishment, remanufacturing, or repurpose applications that avoid landfill solutions); and developed extensive circular economy frameworks that can guide entities on the different life cycle phase of wind power systems (namely at design, operation, or end-of-life phases).
Vestas has applied the concept of eco-design on its new "Lego—style snap-on system" for wind turbines (Vestas, 2021). The company has been working with modularity at the component level since 2012, leading to the introduction of the first modular onshore turbines and the EnVentus platform in 2019. This new concept introduces a modularized nacelle design and will subsequently expand to encompass the whole turbine. By building modular pieces, not only the transport and maneuverability of the parts are smoothed, as well as all the logistics, construction, operation and maintenance allowing smart servicing solutions, upgrades and innovation possibilities. Furthermore, the disassembly of the structure at the end-of-life stage becomes easier, while also enabling further recoverability of the materials and simplified recycling processes.
Additive manufacturing (AM) is another approach leading to successful achievements, as for instance in the case of GE Renewable Energy (Wind Power Monthly, 2021), which uses this technique for wind farm towers lower than 30 meters, necessary for specific sites or wind farm sections. Sometimes, rather than the usual 90–120 meter long towers, smaller structures are required to maximize the total amount of clean, renewable energy that can be generated while lowering the project's carbon footprint by cutting down on the number of parts that need to be manufactured and transported from a distance. AM also makes it easier to incorporate recycled materials and secondary material flows, allowing the use of materials recovered from recycling blades of decommissioned wind turbines (Rahimizadeh et al., 2019). A relevant use of AM is on rapid prototyping, for faster development times (Poole and Phillips, 2015) and for testing purposes namely on small scale use cases. For the application of AM technologies for the tooling manufacturing of composite materials wind blades, different projects address this type of approach (Post et al., 2017; National Renewable Energy Laboratory, 2021; Post, 2021). Other specific use case for AM application regards the manufacturing permanent magnets (Wind Energy Technologies Office, 2022), as it minimizes the use and waste of critical, supply-limited rare earth materials and enables printing of complex shapes.
Recent LCA analyses (GE, 2020) have shown that advanced manufacturing processes can potentially reduce GHG emissions by 15% in the manufacturing of large castings at the top of a tower (i.e., hubs and bedplates), 10% in the tip, and 25% during the process of making tall towers. Besides the notorious environmental and technical gains, this also promotes partnerships and industrial symbiosis, as is the case with Holcim (GE Renewable Energy, 2021).
The transition to the circular economy is supported by different capabilities that, when combined, enable to connect different systems. Each of these systems presents inputs and outputs along the complete chain, or in this case, cycle. One of these concepts is the Internet of Things (IoT) that contributes to the transition to a circular economy supporting circular business models (Ingemarsdotter et al., 2019). The IoT facilitates the enhancement of tracking, monitoring, control, optimization and design. This way, efficiency can be increased leading to the extension of product lifetime, as opposed to the reuse and recycling considered as circular looping strategies. IoT enables the collection of large amounts of data and further real-time computing and big data analytics, leading to more competitive products (Stankovic, 2014; Li et al., 2015).
Monitoring systems of external conditions allows the production forecast and assessment of the structural integrity. This type of systems contributes for higher energy efficiency by adapting the equipment to external conditions, in real time. The use of reinforcement learning models enables to continuously improve the performance of the equipment by evaluation of the reward (e.g., energy production) obtained with the system (agent) when exposed to certain conditions (environment). This way, the operating conditions are automatically found, while the systems are operating. Artificial intelligence has wider applications and can be applied to the identification of patterns (on pictures, natural language processing, etc.) and contribute to the identification of conditions that lead to higher aging or degradation. This information can be used to predict future external conditions, as well as the response of the system to such conditions and aging.
The replacement of periodic (preventive) maintenance by predictive maintenance, through the real time monitoring, data processing resulting into more complex reports shown in digital twins, are valuable tools that enable OPEX (operational expenses) reduction. Artificial intelligence can be employed in order to identify anomalous situations and demand specific maintenance. Autonomous vehicles are, by one side a challenge (maneuverability, obstacles detection, operations) but also an important source of information, for example for blade or tower inspections, since they can operate on hazardous conditions, collecting information to aid the decision of maintenance or to feed complex models. With data acquisition from monitoring systems, enormous amounts of data emerge and must be handled. Data mining technologies can filter meaningful data and artificial intelligence can be used to detect patterns and correlations between parameters. Complex models result from this automatic data analysis without the need for human intervention.
One of the ways to attain life cycle extension is through the use of protective coatings (Momber and Marquardt, 2018) aiming to reduce the impact of external conditions. Corrosion protection systems are estimated to be 50 times less expensive than the repair requirements that they avoid. For example, offshore wind energy devices with this protection are expected to operate for longer than 25 years. Fouling and settlement of bio-based structures are also phenomena that contribute to faster aging and degradation of the materials, as well as the degradation of other protection coatings (such as anticorrosion coating). Offshore conditions provide conditions for the development of different species that settle on structures (Wilhelmsson and Malm, 2008).
Further than the resistance of materials to external loads, and additional protections that can be applied, such as coatings, some materials have self-healing properties. This type of properties is easily found in nature, from molecular scales up to merging of broken bones (Hager et al., 2010). The main investigations focus on metals, ceramics and polymers and consider the same principle: generation of a mobile phase, which can close cracks. Self-healing materials can extend the lifetime of components that can be applied in several sectors.
The lifetime extension of wind turbines, one of the business models proposed by the circular economy philosophy, is still an issue that raises many doubts in the sector however, there are already some technical guidelines that highlight several approaches to consider when evaluating the remaining useful life of the wind turbines. These were published by DNV GL (Det Norske Veritas GL, 2016a; Det Norske Veritas GL, 2016b), UL (2018), Megavind (2016), the German Association of Wind Energy (BWE, 2017), Bureau Veritas (BureauVeritas, 2017) and the Netherlands Electrotechnical Committee (NEN, 2016). In 2018, the IEC created a working group dedicated to compile the regulations, with the aim of publishing a technical specification accepted by the sector on life extension of wind turbines (IEC TS 61400-28 Wind energy generating systems—Part 28: Through life management and life extension of wind power assets) (European Commission, 2021). The main purpose is to evaluate the structural integrity of these assets, aiming to extend their operational life beyond the 20 years, without compromising the safety during their extended operation. When considering this strategy, the sector is increasing the value of their assets before they are discarded, reducing waste and saving new resources.
Although wind energy is considered a clean and environmentally conscious source of energy, as a wind turbine itself has no emissions while in use, there are carbon emissions during the wind turbine manufacture, maintenance and disposal stages, which may be reduced through the use of recycled materials. The goal is to reduce net carbon emissions over the entire life cycle. For this, the wind industry has the responsibility of reducing the environmental impacts throughout its life cycle on a Life Cycle Thinking (LCT) perspective (European Commission, 2010).
Life Cycle Thinking is defined as the way of thinking about a product or process throughout its life, considering all its economic, environmental and social consequences (European Commission, 2010), while LCA is a comprehensive and quantitative methodology to evaluate the potential environmental impacts of a product, process or system throughout their life cycle. The principles and framework for conducting LCA studies are defined by the international standards ISO 14040 (ISO. Technical Committee ISO/TC 207 2006a) and ISO 14044 (ISO. Technical Committee ISO/TC 207 2006b). According to these standards, the LCA methodology comprises four steps: (1) goal and scope definition, (2) Life Cycle Inventory Analysis (LCI), (3) Life Cycle Impact Assessment (LCIA), and (4) interpretation of the results. The LCA of a wind turbine considers the direct emissions at all life cycle stages, from materials acquisition, manufacturing/construction, transportation, installation/on-site erection and assembling, transport, operation and maintenance, and end of life dismantling, but also the environmental impacts associated with the consumption of resources during all these stages (Alsaleh and Sattler, 2019). Furthermore, a LCA makes it possible to quantify the contribution of the different life stages of a wind turbine to the relevant environmental impacts. It is a valuable tool to be used during the product design and development stage in order to identify which life cycle stages will contribute most to the environmental impacts and recommend solutions to reduce them.
Several LCA studies showed consistently that raw material acquisition and manufacturing ranks first in terms of environmental impacts, followed by installation and then operation and maintenance (Tremeac and Meunier, 2009; Garrett and Rønde, 2013; Ozoemena et al., 2018; Alsaleh and Sattler, 2019; Gomaa et al., 2019; Razdan and Garrett, 2019). Also, the end-of-life stage, including disposal of non-recycled wind turbine parts (landfill or incineration), weighs less on the overall environmental impacts of the turbine life cycle, which is also consistent among studies (Tremeac and Meunier, 2009; Garrett and Rønde, 2013; Ozoemena et al., 2018; Alsaleh and Sattler, 2019; Razdan and Garrett, 2019). The manufacturing phase not only contributes with greater impacts and emissions but also in terms of costs (Simons and Cheung, 2016). Table 4 compiles the most recent literature on LCA of wind turbines, according to the life cycle phase.
Figure 8 shows the diagram between the linear and circular approaches applied to the wind energy sector, illustrating how the recovery of materials might contribute to the circular economy, reducing the demand for virgin materials and the volume of landfilled residues.
The production of virgin carbon fibers depicts higher environmental impacts than the recycling and conversion of carbon fibers extracted from end-of-life blades, despite these requiring a thermal process (Bennet, 2021). In fact, the energy demand for the prevalent technologies for composite reclamation decreases in the following order: chemical processing (21–91 MJ/kg) > pyrolysis (24–30 MJ/kg) > microwave-based technologies (5–10 MJ/kg) > mechanical processes (0.1–4.8 MJ/kg). The variations seen for the energy demand depend on the processing conditions, solvolysis being definitely the process with the highest energy demand especially due to the high temperatures and pressures applied. The scalability of the process significantly influences these energy requirements, higher processing rates leading to processes that are more efficient. There has been much academic research and industry innovation programs related to end-of-life management for fiber-reinforced plastics aimed at creating a circular economy, some of them even promoting industrial symbiosis and partnerships to revalue these materials (Bennet, 2021).
In terms of emissions, overall, an onshore wind turbine built nowadays produces around 9 grams of CO2 for every kilowatt hour (kWh) it generates, while a new offshore plant in the sea emits 7 grams of CO2 per kWh (Rueter, 2021). Averagely speaking, wind turbines will be operated for 25 years, during which period, 40 times more energy is produced as compared to the amount required for its production, operation, maintenance and disposal. According to the German Environment Agency, wind power plants take 2.5 to 11 months to generate the amount of energy that was necessary to construct them. Compared with other technologies, wind power does well in terms of carbon emissions (Hendrich and Briem, 2021). By comparison, photovoltaic power plants emit 33 grams CO2 for every kWh generated. Meanwhile, power generated from natural gas produces 442 grams of CO2 per kWh, power from hard coal generates 864 grams of CO2 per kWh, and power from lignite, or brown coal entails 1,034 grams of CO2 per kWh. According to a study commissioned by the global anti-nuclear movement WISE, nuclear energy accounts for about 117 grams of CO2 per kWh, considering the emissions caused by uranium mining and the construction and operation of nuclear reactors (Rueter, 2021).
In Portugal, the wind energy sector has a remarkable trajectory culminating in a well-consolidated value chain, from investors, developers, O & M services, manufacturers, and R & D+I institutions, in order to harness the energy potential of this renewable resource. Presently, the sector has attracted industrial investment and has contributed to create new jobs and to the development of technical competences in several domains. On the other hand, Portugal is now on the top countries for the contribution of wind energy to electricity consumption. In 2020, the percentage of the average annual electricity demand covered by wind was of 26% (Wind Europe, 2022).
Social and economic perspectives are most of the times inter-dependent, but there are opportunities to develop the social aspects in an effortless manner, while the economic sphere is normally the focal point (Morthorst et al., 2009). For the aforementioned reasons wind energy is at a critical moment, its benefits speaking for themselves in the international economy, but it is necessary to develop strategies, from the design phase to managing the produced waste, and to improve opportunities to create circularity in the sector. This will enforce changes that, if well explored, could be the trigger for an enormous cultural and social evolution. Aspects such as lack of legislation, lack of incentives, illegal labor and waste exports are sensitive themes in the international panorama. Regarding waste exports, significant quantities of scrap residues are exported to other economies, namely developing countries, therefore transferring the associated problems to their fragile economies. These countries face challenges due to inadequate or absent waste management infrastructure, political strains and other societal problems, which tend to be exacerbated (Nguyen and Imholte, 2016). Additionally, environmental externalities such as health conditions, ecological impacts and climate change also account as social impacts. These aspects create a paradigm towards the so-called "friendliness" of the wind energy, exposing the other side of the coin, i.e., the precedents that if not solved beforehand will constitute rebound effects for a flourishing renewable energy source.
Concerning the economic impacts of the wind energy, the chief parameters governing wind power economics include investment costs (for instance auxiliary costs for foundations and grid connection), operation and maintenance costs, electricity production/average wind speed, turbine lifetime and discount rate (Morthorst et al., 2009). Electricity production and investment costs are the main parameters to consider, and, as electricity production greatly depends on wind conditions, it is critical to select the most suitable turbine for each project in order to achieve economic viability. Capital costs are dominated by the cost of the wind turbine itself (76% of total cost - production, blades, transformer, transport and installation), followed by the connection to the grid (9% of total cost - cables, sub-station, connection system, evacuation system) and, to a lesser extent, the cost of civil works (7% of total cost - foundations, roads and buildings) and buying the land (Blanco, 2009). Operating and maintenance (O & M) of offshore wind farms costs represent a considerable percentage of the LCOE. On average 23% of the total investment cost goes for O & M (Ren et al., 2021), where the maintenance costs represent the main portion. The downtime duration over the lifetime of offshore wind farms depends directly on the maintenance strategy. Such engineering structures require comprehensive inspections and repairs or replacement of faulty components. When comparing with the onshore wind farms, it represents two to three times higher maintenance costs. This is vital for the development of the offshore wind farm sector. Therefore, predictive analysis of O & M is one of the main developments regarding the OWTs. The total cost per kW of installed wind power capacity differs significantly between countries, as well as the construction of foundations and the grid connection. In Portugal, the share related to "other costs" refers to 32% of the turbine costs, whereas in Germany and Italy these are lowered to circa 24% and 21% respectively, and in Denmark these might be as low as 16%, depending on the turbine size and efficiency.
In the case of offshore wind strategy and costs, it is still far behind the on-shore wind, although the maturity of the offshore wind technology has increased the gradual expansion of the offshore wind farms. It is predicted that the EU investment will become close to the 20 billion? by 2030, 60% of which aimed at the offshore wind market (Wu et al., 2019a). Meanwhile, in China the market is booming, expecting an offshore wind power of about 200 GW of installed capacity in the upcoming decades. The investment per megawatt for offshore wind is still 50% more expensive than onshore. Nevertheless, this number tends to decrease due to recent technological developments. The capital expenditure for offshore wind is divided in the following shares: 31.8% related with the turbine development, 19.3% due to assembly and installation, 14.7% for substructure and foundation, 8.7% for construction, 8.6% for the electrical infrastructure and 5.1% for the decommissioning (Mone et al., 2017). The remaining is related with the parcel to contingency, commissioning, insurance, development, engineering and management, and port & staging. For floating offshore wind platform, the floating structure and anchoring are the most expensive components (36.2%), while turbines and installation represent 22% of the budget. The development of the floating structures still represents a considerable portion of the investment (Wu et al., 2019a).
Besides the revenues associated with product development, selling, installing and maintenance, there is a huge opportunity in the externalities of the wind energy sector. The assumed non-environmental externalities include subsidies, research and development costs, employment and effects on gross domestic product. Therefore, these also count as economic impacts for the production of wind energy. The European Wind Energy Association estimates external costs from 0.05 to 0.25 c?/kW h (Eurocent/kilowatt-hour) (Cherrington et al., 2012). Morthorst et al (Morthorst et al., 2009) define the typical wind farm finance structure including stakeholders as banks, equity investors, and leasing agents among all the contractors and suppliers. All these entities are economically impacted by wind energy projects, and, in a less objective way, social impacts will also be triggered.
Wind energy may be truly perceived as a remarkable opportunity to perform the desired transition to a decarbonized society. In Europe wind energy production has been raising, namely due to a favorable geography for such energy stream, while the integration in the electricity mix is also steadily accomplished. However, a general lack of consistent knowledge about the actual circularity panorama in the wind energy industry existed, especially concerning the combination of different features from the conception to the end-of-life phase.
This work reviewed major recent literature for this theme, and it highlighted some challenges for the industry specifically regarding materials, technologies, components and design features. Also, some drivers and barriers to circularity were pointed out, enabling the detection of research gaps and opportunities in the sector. Key examples of the implementation of the R-strategies in international wind energy projects were identified, eco-design and eco-efficiency being also noticed as important approaches to leverage the circularity among the interested stakeholders. Infrastructure monitoring and lifetime extension were also assessed to complement the study of sustainability in the sector, followed by a compilation of the most interesting LCA studies. The economic and social perspectives were lightly addressed, enforcing the need to promote more research under these components. All this aimed at shedding some light for the countries that are still behind in these matters, in order to serve as guidance for a faster evolution.
After thorough research on the current state of circularity in the wind energy sector, main findings were determined: for instance, the need to overcome fundamental obstacles such as the establishment of a secondary market for the valuable residues to be revalorized as resources; the implementation of symbiosis along the value chain; conducting accurate life cycle assessment in the design phase and for the proposed circular strategies, as significant research into their environmental impacts is still lacking; the need to further develop innovative techniques, processes and materials assisting technological advancements, especially related to the application of strategies such as reuse, refurbishment and retrofitting; and upscaling certain recycling processes (carbon fiber, for instance) as a means to pave the way for advances in recycling of other materials (glass fiber). In terms of environmental aspects, raw materials acquisition and manufacturing stages were identified as the ones leading to higher impacts (a parallel trend being seen for the capital costs), whereas the end-of-life step presented the lowest output. Advanced manufacturing technologies, such as AM, are very promising for specific aspects of tooling of wind turbine blades, small-scale blades, or even electric motor components. Regarding the socio-economic impacts, major investments in the field promote not only technology development but also the creation of new jobs; however, there is a fair amount of socially-related issues to be solved.
Nevertheless, the wind energy sector is moving forward, and every week new developments and initiatives appear from the stakeholders' side. To further accelerate the transition to a fully circular economy of the sector, a coordinated strategy is needed from all intervening entities, including policymakers and cross-sector partners. The standardization of practices through regulation is also a fundamental pillar to promote the success of this transition. As future trends to improve circularity and move towards a higher degree of sustainability in the sector, approaches such as predictive manufacturing, digital twin technology, the application of industry 5.0 concepts and enhanced monitoring systems are deemed to aid in this quest and support the growth of the wind energy industry.
All authors declare that they have not used Artificial Intelligence (AI) tools in the creation of this article.
This work is funded by national funds through the FCT – Fundação para a Ciência e a Tecnologia, I.P. and, when eligible, by COMPETE 2020 FEDER funds, under the Scientific Employment Stimulus - Individual Call (CEEC Individual) - 2021.03036.CEECIND/CP1680/CT0003. This work was financially supported by base Funding of the project UIDB/50022/2020 (LAETA), funded by national funds through FCT/MCTES (PIDDAC). Diogo Neves acknowledges the financial support from Norte2020 - RHAQ - NORTE-59-2019-30. Nelson Gonçalves acknowledges the EuReComp and Carbo4Power projects. The EuReComp has received funding from the European Union's Horizon 2020 Research and Innovation Programme under Grand Agreement No: 101058089. Carbo4Power project is supported by the European Union under the HORIZON2020 Framework Programme Grant Agreement no. 953192. Teresa Mata gratefully acknowledges the funding of Project NORTE-06-3559-FSE-000107, cofinanced by Programa Operacional Regional do Norte (NORTE2020), through Fundo Social Europeu (FSE).
The authors declare no conflict of interest.
[1] |
Alsaleh A, Sattler M (2019) Comprehensive life cycle assessment of large wind turbines in the US. Clean Technol Envir Policy 21: 887–903. https://doi.org/10.1007/s10098-019-01678-0 doi: 10.1007/s10098-019-01678-0
![]() |
[2] | Architecture news & editorial desk (2021) Wind turbine blades repurposed as bike sheds. Architechture & Design. Available from: https://www.architectureanddesign.com.au/news/danish-wind-turbine-blades-repurposed-as-bike-shed#. |
[3] |
Bank LC, Arias FR, Yazdanbakhsh A, et al. (2018) Concepts for Reusing Composite Materials from Decommissioned Wind Turbine Blades in Affordable Housing. Recycling 3: 3. https://doi.org/10.3390/recycling3010003 doi: 10.3390/recycling3010003
![]() |
[4] | bcircular (2020) R3FIBER—Green Blades for Green Energy. Available from https://www.bcircular.com/r3fiber/. |
[5] |
Beauson J, Laurent A, Rudolph DP et al. (2021) The complex end-of-life of wind turbine blades: A review of the European context. Renew Sust Energ Rev 155: 111847. https://doi.org/10.1016/j.rser.2021.111847 doi: 10.1016/j.rser.2021.111847
![]() |
[6] | Beauson J, McGugan M, Madsen B (2021) What to do with worn out wind turbine blades. Available from: https://windenergy.dtu.dk/english/news/2021/06/what-to-do-with-worn-out-wind-turbine-blades?id = 156ab69d-2b7c-40cd-a25c-204d49533b7c. |
[7] | Bennet L (2021) Sustainable Decommisioning: Wind Turbine Blade Recycling, Offshore Renewable Energy (ORE) Catapult. Available from: https://ore.catapult.org.uk/wp-content/uploads/2021/03/CORE_Full_Blade_Report_web.pdf. |
[8] | BKW (2023) BKW acquires the largest authorized wind project in Italy. Available from: https://www.bkw.ch/en/about-us/news/media/press-releases/bkw-acquires-the-largest-authorized-wind-project-in-italy. |
[9] |
Blanco MI (2009) The economics of wind energy. Renew Sust Energ Rev 13: 1372–1382. https://doi.org/10.1016/j.rser.2008.09.004 doi: 10.1016/j.rser.2008.09.004
![]() |
[10] | Bloomberg (2021) Wind Turbine Blades Get Recycled Into Auto Parts and Sports Gear. Available from: https://www.bloomberg.com/news/articles/2021-07-20/wind-turbine-blades-get-re-spun-as-auto-parts-sports-gear-bnef. |
[11] |
Boccard N (2014) The cost of nuclear electricity: France after Fukushima. Energy Policy 66: 450–461. https://doi.org/10.1016/j.enpol.2013.11.037 doi: 10.1016/j.enpol.2013.11.037
![]() |
[12] |
Bonou A, Olsen SI, Hauschild MZ (2015) Introducing life cycle thinking in product development–A case from Siemens Wind Power. CIRP Annals 64: 45–48. https://doi.org/10.1016/j.cirp.2015.04.053 doi: 10.1016/j.cirp.2015.04.053
![]() |
[13] |
Bonou A, Skelton K, Olsen SI (2016) Ecodesign framework for developing wind turbines. J Clean Prod 126: 643–653. https://doi.org/10.1016/j.jclepro.2016.02.093 doi: 10.1016/j.jclepro.2016.02.093
![]() |
[14] |
Brøndsted P, Lilholt H, Lystrup A (2005) Composite materials for wind power turbine blades. Annu Rev Mater Res 35: 505–538. https://doi.org/10.1146/annurev.matsci.35.100303.110641 doi: 10.1146/annurev.matsci.35.100303.110641
![]() |
[15] | BureauVeritas (2017) Move Forward with Confidence Guidelines for Wind Turbines Lifetime Extension. Technical Report 9. Available from: https://www.bureauveritas.com/white-papers/Wind-turbines. |
[16] | BWE (2017) Principles for the implementation of an evaluation and assessment with regard to the extended operation of wind energy plants. German Wind Energy Association, 68. |
[17] |
Chen Y, Cai G, Zheng L, et al. (2021) Modeling waste generation and end-of-life management of wind power development in Guangdong, China until 2050. Resour Conserv Recy 169: 105533. https://doi.org/10.1016/j.resconrec.2021.105533 doi: 10.1016/j.resconrec.2021.105533
![]() |
[18] |
Cherrington R, Goodship V, Meredith J, et al. (2012) Producer responsibility: Defining the incentive for recycling composite wind turbine blades in Europe. Energ Policy 47: 13–21. https://doi.org/10.1016/j.enpol.2012.03.076 doi: 10.1016/j.enpol.2012.03.076
![]() |
[19] | Circular - for resource and waste professionals (2020) Towards A Circular Economy Framework for Offshore Wind. Available from: https://www.circularonline.co.uk/research-reports/towards-a-circular-economy-framework-for-offshore-wind/. |
[20] | Ciucci M (2021) Energy policy: general principles. Fact Sheets on the European Union. European Parliament. |
[21] | Clement C (2021) Investigation of Floating Offshore Wind Turbine Hydrodynamics with Computational Fluid Dynamics. University of Normandie. Available from: https://tel.archives-ouvertes.fr/tel-03331232/document. |
[22] | Climate Justice Alliance (2021) Just Transitions - a framework for change. Available from: https://climatejusticealliance.org/just-transition/. |
[23] |
Cognet V, Courrech du Pont S, Thiria B (2020) Material optimization of flexible blades for wind turbines. Renew Energ 160: 1373–1384. https://doi.org/10.1016/j.renene.2020.05.188 doi: 10.1016/j.renene.2020.05.188
![]() |
[24] | Colledani M (2017) FiberEUse - Large scale demonstration of new circular economy value-chains based on the reuse of end-of-life fiber reinforced composites. Available from: http://www.fibereuse.eu/. |
[25] |
Cousins DS, Suzuki Y, Murray RE, et al. (2019) Recycling glass fiber thermoplastic composites from wind turbine blades. J Clean Prod 209: 1252–1263. https://doi.org/10.1016/j.jclepro.2018.10.286 doi: 10.1016/j.jclepro.2018.10.286
![]() |
[26] | Cranfield University (2013) EXHUME - Efficient X-sector use of HeterogeneoUs MatErials in Manufacturing. Available from: https://www.cranfield.ac.uk/case-studies/exhume. |
[27] |
Dai K, Bergot A, Liang C, et al. (2015) Environmental issues associated with wind energy – A review. Renew Energ 75: 911–921. https://doi.org/10.1016/j.renene.2014.10.074 doi: 10.1016/j.renene.2014.10.074
![]() |
[28] | DecomBlades (2021) DecomBlades. Available from: https://decomblades.dk/. |
[29] | Det Norske Veritas GL (2016a) Certification of lifetime extension of wind turbines. DNVGL-ST-0263. Available from: https://www.dnv.com/news/new-dnv-gl-standard-and-service-specification-for-lifetime-extension-of-wind-turbines-61059# |
[30] | Det Norske Veritas GL (2016b) Lifetime extension of wind turbines. DNVGL-ST-0262. Available from: https://www.dnv.com/news/new-dnv-gl-standard-and-service-specification-for-lifetime-extension-of-wind-turbines-61059#. |
[31] |
Dorigato A (2021) Recycling of thermosetting composites for wind blade application. Adv Ind Eng Polymer Res 4: 116–132. https://doi.org/10.1016/j.aiepr.2021.02.002 doi: 10.1016/j.aiepr.2021.02.002
![]() |
[32] |
Driscoll F, Jonkman J, Robertson A, et al. (2016) Validation of a FAST Model of the Statoil-hywind Demo Floating Wind Turbine. Energ Procedia 94: 3–19. https://doi.org/10.1016/j.egypro.2016.09.181 doi: 10.1016/j.egypro.2016.09.181
![]() |
[33] | ECHT Community (2020) Moonshot. Available from: https://www.echt.community/moonshot/. |
[34] | ECHT Community (2023) The Circular Wind Hub. Available from: https://www.echt.community/the-circular-wind-hub/. |
[35] | ELETAEN Association (2022) Re: Wind–Accelerating sustainability in decommissioning, ELETAEN - The Greek Wind Energy Association. Available from: https://www.livemedia.gr/video/450838. |
[36] | Ellen MacArthur Foundation (2019) Completing the picture: How the circular economy tackles climate change. Mater Econ: 71. |
[37] | Ellen MacArthur Foundation (2020) What is a circular economy? Available from: https://ellenmacarthurfoundation.org/topics/circular-economy-introduction/overview. |
[38] | Energias Renovables (2021) Endesa ha reparado o reutilizado 5.700 equipos y componentes eólicos de todos los tamaños en los últimos dos años. Energías Renovables. Spain. Available from: https://www.energias-renovables.com/eolica/endesa-ha-reparado-o-reutilizado-5-700-20211120. |
[39] | Eolien Maritime Franc (2022) Fécamp Offshore Wind Farm, Seine-Maritime. Available from: https://www.nsenergybusiness.com/projects/fecamp-offshore-wind-farm/. |
[40] | ETIPWind - European Technology & Innovation Platform on Wind Energy Executive Committee (2019) How wind is going circular - blade recycling. Available from: https://etipwind.eu/files/reports/ETIPWind-How-wind-is-going-circular-blade-recycling.pdf. |
[41] | European Comission (2019) Communication from the Commission to the European Parliament, the Council, the European Economic and Social Committee and the Committee of the Regions - The European Green Deal, 24. |
[42] | European Commission (2009a) In-situ wireless monitoring of on- and offshore WINd TURbine blades using energy harvesting technology. Brussels, CORDIS EU Research Results. |
[43] | European Commission (2009b) Small Wind Turbine Composite Blade PRoperties ON Demand by Means of Functionally Graded Materials. Brussels, CORDIS EU Research Results. |
[44] | European Commission (2010) A guide for business and policy makers to Life Cycle Thinking and Assessment. |
[45] | European Commission (2012) Adapted Composite Repair Tooling for in-situ wind turbine blades structural rehabilitation. Brussels, CORDIS EU Research Results. |
[46] | European Commission (2014) Automated mechanical property and fatigue life assessment of composite wind turbine blades in less than 4 hours. Brussels, CORDIS EU Research Results. |
[47] | European Commission (2015) Lightning protection of wind turbine blades with carbon fibre composite materials. Brussels, CORDIS EU Research Results. |
[48] | European Commission (2016) Commercialisation of Advanced Composite Material Technology: Carbon-Glass Hybrid in PowderEpoxy for Large (60–100m) Wind Turbine Blades. Brussels, CORDIS EU Research Results. |
[49] | European Commission (2016) Development of lamella type of wind turbine made of bio composite polymers. Brussels, CORDIS EU Research Results. |
[50] | European Commission (2020) A new Circular Economy Action Plan: For a cleaner and more competitive European Commission. European Commission. Communication, COM//98 final. |
[51] | European Commission (2021) Do no significant harm - Technical Guidance by the Commission. Recovery and Resilience Facility. Facility, European Commission. |
[52] | European Commission (2022) Commission Recommendation on speeding up permit-granting procedures for renewable energy projects and facilitating Power Purchase Agreements. Available from: https://eur-lex.europa.eu/legal-content/EN/TXT/?uri = PI_COM%3AC%282022%293219 & qid = 1653033569832. |
[53] | European Commission (2022) Renewable Energy Directive. Available from: https://energy.ec.europa.eu/topics/renewable-energy/renewable-energy-directive-targets-and-rules/renewable-energy-directive_en. |
[54] | European Commission (2022) REPowerEU: affordable, secure and sustainable energy for Europe. Available from: https://ec.europa.eu/info/strategy/priorities-2019-2024/european-green-deal/repowereu-affordable-secure-and-sustainable-energy-europe_en. |
[55] | European Parliament (2022) Proposal for a directive of the european parliament and of the council amending Directive (EU) 2018/2001 on the promotion of the use of energy from renewable sources, Directive 2010/31/EU on the energy performance of buildings and Directive 2012/27/EU on energy efficiency. |
[56] | Exter PV, Bosch JBS, Favrin S, er al. (2021) Towards a circular energy transition - Exploring solutions to mitigate surging demand for critical metals in the energy transition. Available from: https://www.copper8.com/wp-content/uploads/2021/11/Towards-A-Circular-Energy-Transtion.pdf. |
[57] |
Farina A, Anctil A (2022) Material consumption and environmental impact of wind turbines in the USA and globally. Resour Conserv Recy 176: 105938. https://doi.org/10.1016/j.resconrec.2021.105938 doi: 10.1016/j.resconrec.2021.105938
![]() |
[58] | Fraunhofer Gesellschaft Zur Forderung Der Angewandten Forschung EV (2013) WALiD - Wind Blade Using Cost-Effective Advanced Composite Lightweight Design. Available from: https://cordis.europa.eu/project/id/309985. |
[59] | Fraunhofer Institute for Process Engineering and Packaging IVV (2014) ForCycle - Recycling of metal-plastic composites and hybrid materials. Available from: https://www.ivv.fraunhofer.de/en/recycling-environment/recycling-of-plastic-composites/forcycle.html |
[60] | Fraunhofer Institute for Wood Research Wilhelm-Klauditz-Institut (2017) ReRoBalsa. Available from: https://www.wki.fraunhofer.de/en/research-projects/2017/ReRoBalsa_rotor-blades-recycling-balsa-wood-plastic-foam-for-insulation-materials.html. |
[61] |
Garrett P, Rønde K (2013) Life cycle assessment of wind power: comprehensive results from a state-of-the-art approach. Int J Life Cycle Ass 18: 37–48. https://doi.org/10.1007/s11367-012-0445-4 doi: 10.1007/s11367-012-0445-4
![]() |
[62] | GE Renewable Energy (2021) GE Renewable Energy and LafargeHolcim team up for a more circular wind industry. Available from: https://www.ge.com/news/press-releases/ge-renewable-energy-and-lafargeholcim-team-up-for-a-more-circular-wind-industry. |
[63] | GE (2020) GE sustainability report, GE. Available from: https://www.ge.com/sites/default/files/ge2020_sustainability_report.pdf#page = 38. |
[64] | German Wind Power Magazine (2021) Berlin, Germany, German Wind Energy Association. Available from: http://www.windindustry-in-germany.com/german-wind-power-magazine/issue/01-2021. |
[65] | GENVIND (2012) An innovation consortium. |
[66] | GmbH RR (2022) RWE announces further milestone for Triton Knoll Offshore Wind Farm. Available from: https://www.rwe.com/en/press/rwe-renewables/2022-01-13-rwe-announces-further-milestones-for-triton-knoll-offshore-wind-farm. |
[67] |
Gomaa MR. Rezk H, Mustafa RJ, et al. (2019) Evaluating the environmental impacts and energy performance of a wind farm system utilizing the life-cycle assessment method: A practical case study. Energies 12: 3263. https://doi.org/10.3390/en12173263 doi: 10.3390/en12173263
![]() |
[68] |
Hager MD, Greil P, Leyens C, et al. (2010) Self‐healing materials. Adv Mater 22: 5424–5430. https://doi.org/10.1002/adma.201003036 doi: 10.1002/adma.201003036
![]() |
[69] | Hebo Engineering BV (2003) REACT - Re-use of glassfibre reinforced plastics by selective shredding and re-activating the recyclate. Available from: https://cordis.europa.eu/project/id/G1ST-CT-2002-50287. |
[70] | Hendrich JHMRASA, Briem SWMHAK (2021) Aktualisierung und Bewertung der Ökobilanzen von Windenergie- und Photovoltaikanlagen unter Berücksichtigung aktueller Technologieentwicklungen. Climate Change 35/2021. |
[71] |
Heng H, Meng R, McKechnie J (2021) Wind turbine blade wastes and the environmental impacts in Canada. Waste Manage 133: 59–70. https://doi.org/10.1016/j.wasman.2021.07.032 doi: 10.1016/j.wasman.2021.07.032
![]() |
[72] | Iberdrola (2013) LIFE BRIO - Demonstration of Wind Turbine Rotor Blade Recycling into the Coal Clough Wind Farm Decommissioning Opportunity. Available from: http://www.lifebrio.eu/index.php/en/. |
[73] | Iberdrola (2020) SAINT-BRIEUC OFFSHORE WIND FARM. Available from: https://www.iberdrola.com/about-us/what-we-do/offshore-wind-energy/saint-brieuc-offshore-wind-farm. |
[74] | Iberdrola (2023) Baltic Eagle, our second large offshore wind farm in Germany. Available from: https://www.iberdrola.com/about-us/what-we-do/offshore-wind-energy/baltic-eagle-offshore-wind-farm. |
[75] | International Electrotechnical Commission (2005) IEC61400-1 Wind energy generation systems—Part 1: Design requirements. Int Electrotechnical Commission, 98. |
[76] | International Electrotechnical Commission (2021) Decommissioning and preparation for recycling. TC 88 - Wind energy generation systems, IEC. |
[77] | International Electrotechnical Commission (2021) Wind energy generation systems - Part 28: Through life management and life extension of wind power assets. TC 88 - Wind energy generation systems, IEC. |
[78] | INEGI and APREN (2021) Wind Farms in Portugal - December 2020. e2p.inegi.up.pt: 53. |
[79] |
Ingemarsdotter E, Jamsin E, Kortuem G, et al. (2019) Circular strategies enabled by the internet of things—A framework and analysis of current practice. Sustainability 11: 5689. https://doi.org/10.3390/su11205689 doi: 10.3390/su11205689
![]() |
[80] | Intelligence WB (2021) Wind energy in Europe-2020 Statistics and the outlook for 2021–2025. Belgium, WindEurope. |
[81] | Interesting Engineering (2016) Europe's largest onshore wind farms. Available from: https://interestingengineering.com/innovation/europes-largest-onshore-wind-farms. |
[82] | Interreg (2016) Recy-Composite Project. Available from: http://www.recycomposite-interreg.eu/index.php/en/presentation/recy-composite-project. |
[83] | Interreg (2018) DecomTools. Available from: https://northsearegion.eu/decomtools/. |
[84] |
Ioannou A, Angus A, Brennan F (2018) Parametric CAPEX, OPEX, and LCOE expressions for offshore wind farms based on global deployment parameters. Energ Source Part B 13: 281–290. https://doi.org/10.1080/15567249.2018.1461150 doi: 10.1080/15567249.2018.1461150
![]() |
[85] | ISO. Technical Committee ISO/TC 207a, Environmental management. Subcommittee SC 5., Life cycle assessment (2006) Environmental Management: Life Cycle Assessment: Principles and Framework. 14040: 2006, ISO. 14040: 2006. |
[86] | ISO. Technical Committee ISO/TC 207b, Environmental management. Subcommittee SC 5., Life cycle assessment (2006). Environmental management — Life cycle assessment — Requirements and guidelines. 14044: 2006, ISO. 14044: 2006. |
[87] | Jacobs (2021) The future of onshore wind decommissioning in Scotland. Scotland, Zero Waste Scotland. Available from: https://www.zerowastescotland.org.uk/sites/default/files/Onshore%20Wind%20Decommissioning%20Full%20Report%20FINAL2.pdf. |
[88] |
Jensen JP, Skelton K (2018) Wind turbine blade recycling: Experiences, challenges and possibilities in a circular economy. Renew Sust Energ Rev 97: 165–176. https://doi.org/10.1016/j.rser.2018.08.041 doi: 10.1016/j.rser.2018.08.041
![]() |
[89] |
Jiang Z (2021) Installation of offshore wind turbines: A technical review. Renew Sust Energ Rev 139: 110576. https://doi.org/10.1016/j.rser.2020.110576 doi: 10.1016/j.rser.2020.110576
![]() |
[90] |
Jiang Z, Hu W, Dong W, et al. (2017) Structural Reliability Analysis of Wind Turbines: A Review. Energies 10. https://doi.org/10.3390/en10122099 doi: 10.3390/en10122099
![]() |
[91] |
Joustra J, Flipsen B, Balkenende R (2021) Structural reuse of high end composite products: A design case study on wind turbine blades. Resour Conserv Recy 167: 105393. https://doi.org/10.1016/j.resconrec.2020.105393 doi: 10.1016/j.resconrec.2020.105393
![]() |
[92] | Komusanac I, Guy B, Fraile D, et al. (2021) Wind energy in Europe - 2020 Statistics and the outlook for 2021–2025. Wind Europe. |
[93] |
Li S, Xu LD, Zhao S (2015) The internet of things: a survey. Inform Syst Front 17: 243–259. https://doi.org/10.1007/s10796-014-9492-7 doi: 10.1007/s10796-014-9492-7
![]() |
[94] |
Lichtenegger G, Rentizelas AA, Trivyza N, et al. (2020) Offshore and onshore wind turbine blade waste material forecast at a regional level in Europe until 2050. Waste Manage 106: 120–131. https://doi.org/10.1016/j.wasman.2020.03.018 doi: 10.1016/j.wasman.2020.03.018
![]() |
[95] | LM Wind Power (2021) Our blade recycling initiatives. Available from: https://www.lmwindpower.com/en/sustainability/zero-waste-blades. |
[96] | LM Wind Power (2022) ZEBRA. Available from: https://www.lmwindpower.com/en/stories-and-press/stories/news-from-lm-places/zebra-project-launched. |
[97] | Maciel JG (2010) The WindFloat Project. Lisbon, Portugal, EDP. |
[98] |
Maradin D, Cerović L, Šegota A (2021) The efficiency of wind power companies in electricity generation. Energ Strat Rev 37: 100708. https://doi.org/10.1016/j.esr.2021.100708 doi: 10.1016/j.esr.2021.100708
![]() |
[99] |
Marin J, Barroso A, Paris F, et al. (2009) Study of fatigue damage in wind turbine blades. Eng Fail Anal 16: 656–668. https://doi.org/10.1016/j.engfailanal.2008.02.005 doi: 10.1016/j.engfailanal.2008.02.005
![]() |
[100] | Markaide N (2018) AIRPOXY - Develop thermoset composites parts for aeronautics. Available from: https://www.airpoxy.eu/. |
[101] |
Martínez E, Latorre-Biel J, Jiménez E, et al. (2018) Life cycle assessment of a wind farm repowering process. Renew Sust Energ Rev 93: 260–271. https://doi.org/10.1016/j.rser.2018.05.044 doi: 10.1016/j.rser.2018.05.044
![]() |
[102] |
Medici P, van den Dobbelsteen A, Peck D (2020) Safety and health concerns for the users of a playground, built with reused rotor blades from a dismantled wind turbine. Sustainability 12: 3626. https://doi.org/10.3390/su12093626 doi: 10.3390/su12093626
![]() |
[103] | Megavind (2016) Strategy for extending the useful lifetime of a wind turbine. 41. Available from: https://megavind.greenpowerdenmark.dk/publications/strategy-extending-the-useful-lifetime-of-a-wind-turbine |
[104] |
Mishnaevsky JL (2021) Current Challenges of Wind Energy Development: Materials Science Aspects. Phys Mesomech 24: 533–540. https://doi.org/10.1134/S1029959921050040 doi: 10.1134/S1029959921050040
![]() |
[105] |
Mishnaevsky Jr L, Thomsen K (2020) Costs of repair of wind turbine blades: Influence of technology aspects. Wind Energ 23: 2247–2255. https://doi.org/10.1002/we.2552 doi: 10.1002/we.2552
![]() |
[106] |
Mishnaevsky L (2022) Root Causes and Mechanisms of Failure of Wind Turbine Blades: Overview. Materials 15: 2959. https://doi.org/10.3390/ma15092959 doi: 10.3390/ma15092959
![]() |
[107] |
Mishnaevsky L, Branner K, Petersen HN, et al. (2017) Materials for wind turbine blades: an overview. Materials 10: 1285. https://doi.org/10.3390/ma10111285 doi: 10.3390/ma10111285
![]() |
[108] |
Momber A, Marquardt T (2018) Protective coatings for offshore wind energy devices (OWEAs): A review. J Coatings Technol Res 15: 13–40. https://doi.org/10.1007/s11998-017-9979-5 doi: 10.1007/s11998-017-9979-5
![]() |
[109] | Mone C, Hand M, Bolinger M, et al. (2017) 2015 Cost of Wind Energy Review, National Renewable Energy Lab. (NREL), Golden, CO (United States). |
[110] | Moray Offshore Renewable Power (2014) Moray East Offshore Windfarm. Available from: https://www.morayeast.com/news/moray-east-celebrates-installation-last-turbine. |
[111] |
Morseletto P (2020) Targets for a circular economy. Resour Conserv Recy 153: 104553. https://doi.org/10.1016/j.resconrec.2019.104553 doi: 10.1016/j.resconrec.2019.104553
![]() |
[112] | Morthorst PE, Auer H, Garrad A, et al. (2009) Wind Energy–The Facts, Part III The Economics of Wind Power, European Wind Energy Association. |
[113] | National Composites Centre (2019) ReDisCoveR Composites. Available from: https://www.nccuk.com/work-with-us/cross-catapult-projects/rediscover-composites/?popupclosed = true. |
[114] | National Composites Centre (2021) SusWind. Available from: https://www.nccuk.com/what-we-do/sustainability/suswind/. |
[115] | National Renewable Energy Laboratory (NRE) (2021) NREL Explores Innovative Manufacturing Approach for Next-Generation Wind Turbine Blades. Available from: https://www.nrel.gov/news/program/2021/manufacturing-next-generation-wind-turbines.html. |
[116] | NEN (2016) Principles and technical guidance for continued operation of onshore wind turbines - NPR 8400. 19. |
[117] | Netherland Enterprise Agency (NE) (2022) Ijmuiden Ver Wind Farm Zone. Available from: https://english.rvo.nl/information/offshore-wind-energy/ijmuiden-ver-wind-farm-zone. |
[118] | Newman N (2018) Wind-Power in europe Nic Newman Oxford. |
[119] |
Nguyen RT, Imholte DD (2016) China's Rare Earth Supply Chain: Illegal Production, and Response to new Cerium Demand. JOM 68: 1948–1956. https://doi.org/10.1007/s11837-016-1894-1 doi: 10.1007/s11837-016-1894-1
![]() |
[120] |
Oliveux G, Dandy LO, Leeke GA (2015) Current status of recycling of fibre reinforced polymers: Review of technologies, reuse and resulting properties. Prog Mater Sci 72: 61–99. https://doi.org/10.1016/j.pmatsci.2015.01.004 doi: 10.1016/j.pmatsci.2015.01.004
![]() |
[121] | Orsted GA (2022) Hornsea 2. Available from: https://hornseaprojects.co.uk/hornsea-project-two. |
[122] | Ostachowicz W, McGugan M, Schröder-Hinrichs JU, et al. (2016) MARE-WINT: new materials and reliability in offshore wind turbine technology, Springer Nature. https://doi.org/10.1007/978-3-319-39095-6 |
[123] |
Ozoemena M, Cheung WM, Hasan R (2018) Comparative LCA of technology improvement opportunities for a 1.5-MW wind turbine in the context of an onshore wind farm. Clean Technol Envir Policy 20: 173–190. https://doi.org/10.1007/s10098-017-1466-2 doi: 10.1007/s10098-017-1466-2
![]() |
[124] |
Pimenta S, Pinho ST (2011) Recycling carbon fibre reinforced polymers for structural applications: Technology review and market outlook. Waste Manage 31: 378–392. https://doi.org/10.1016/j.wasman.2010.09.019 doi: 10.1016/j.wasman.2010.09.019
![]() |
[125] | Plastic Omnium Auto Exterieur Services (2009) EURECOMP - Recycling Thermoset Composites of the SST. Available from: https://cordis.europa.eu/result/rcn/54152/en. |
[126] | Poole S, Phillips R (2015) Rapid prototyping of small wind turbine blades using additive manufacturing. 2015 pattern recognition association of South Africa and robotics and mechatronics international conference (PRASA-RobMech), IEEE. https://doi.org/10.1109/RoboMech.2015.7359521 |
[127] | Post BK (2021) T13 - Additive Manufacturing in Wind Turbine Components and Tooling. |
[128] | Program – Materials, Manufacturing, and Design Innovation, U.S. Department of Energy: 10. Available from: https://www.energy.gov/sites/default/files/2021-10/fy21peerreview-materialsandmanufacturing-ornl-post.pdf. |
[129] | Post BK, Richardson B, Lind R, et al. (2017) Big area additive manufacturing application in wind turbine molds. 2017 International Solid Freeform Fabrication Symposium, University of Texas at Austin. |
[130] | Potting J, Hekkert M, Worrell E, et al. (2017) Circular economy: measuring innovation in the product chain. PBL Publishers. |
[131] | Power Technology (2019) The biggest wind farms in Europe. Available from: https://www.power-technology.com/features/the-biggest-wind-farms-in-europe/. |
[132] |
Prabhu VS, Mukhopadhyay K (2021) Assessment of wind energy in india at the national and sub- national level: attributional lca exercise. Int J Green Energ 19: 1023–1048. https://doi.org/10.1080/15435075.2021.1978447 doi: 10.1080/15435075.2021.1978447
![]() |
[133] | Radowitz B (2021) LM Wind Power to make 'competitive and sustainable' zero-waste blades by 2030. Recharge - global news and intelligence for the energy transition, NHST Media Group. |
[134] |
Rahimizadeh A, Kalman J, Fayazbakhsh K, et al. (2019) Recycling of fiberglass wind turbine blades into reinforced filaments for use in Additive Manufacturing. Composites Part B Eng 175: 107101. https://doi.org/10.1016/j.compositesb.2019.107101 doi: 10.1016/j.compositesb.2019.107101
![]() |
[135] |
Rani M, Choudhary P, Krishnan V, et al. (2021) A review on recycling and reuse methods for carbon fiber/glass fiber composites waste from wind turbine blades. Composites Part B Eng 215: 108768. https://doi.org/10.1016/j.compositesb.2021.108768 doi: 10.1016/j.compositesb.2021.108768
![]() |
[136] |
Ratner S, Gomonov K, Revinova S, et al. (2020) Eco-design of energy production systems: the problem of renewable energy capacity recycling. Appl Sci 10: 4339. https://doi.org/10.3390/app10124339 doi: 10.3390/app10124339
![]() |
[137] | Razdan P, Garrett P (2019) Life Cycle Assessment of Electricity Production from an Onshore V136-4.2 MW Wind Plant. |
[138] |
Ren Z, Verma AS, Li Y, et al. (2021) Offshore wind turbine operations and maintenance: A state-of-the-art review. Renew Sust Energ Rev 144: 110886. https://doi.org/10.1016/j.rser.2021.110886 doi: 10.1016/j.rser.2021.110886
![]() |
[139] | reNewsBiz (2021) Siemens Gamesa launches recyclable blades. Available from: https://renews.biz/72091/. |
[140] | reNewsBiz (2021) Vestas looks to expand US blade recycling initiative. Available from: https://renews.biz/74404/vestas-looks-to-expand-us-blade-recycling-initiative/ |
[141] | Re-Wind network (2018) Re-Wind project. 2021. Available from: https://www.re-wind.info/. |
[142] | Richerche CND (2011) SUSRAC - Sustainable recycling of aircrafts composites. Available from: https://cordis.europa.eu/project/rcn/101279/reporting/en. |
[143] | Roland Gauß C, Burkhardt F, Carencotte M, et al. (2021) Rare Earth Magnets and Motors: A European Call for Action. Berlin, Germany, European Raw Materials Alliance. |
[144] | Rueter G (2021) How sustainable is wind power? DW. Germany, DW. |
[145] | Schmid M, Ramon N, Dierckx A, et al. (2020) Accelerating Wind Turbine Blade Circularity. Brussels, Belgium, Wind Europe. |
[146] | Schupak A (2021) Circular Economy: Wind Turbine Blade Maker Is Working To Turn Waste Into A Resource. Available from: https://www.ge.com/news/reports/circular-economy-wind-turbine-blade-maker-is-working-to-turn-waste-into-a-resource. |
[147] | Selfrag AG (2012) SELFRAG-CFRP - High Voltage Pulse Fragmentation Technology to recycle fibre-reinforced composites. Available from: https://cordis.europa.eu/project/id/323454/reporting. |
[148] | Shah OR (2014) Identification and characterization of mechanical and structural properties against static damage and fatigue of a composite floating wind turbine blade, University of Brest. Available from: https://tel.archives-ouvertes.fr/tel-02368497. |
[149] |
Shohag MAS, Hammel EC, Olawale DO, et al. (2017) Damage mitigation techniques in wind turbine blades: A review. Wind Eng 41: 185–210. https://doi.org/10.1177/0309524X17706862 doi: 10.1177/0309524X17706862
![]() |
[150] | Siemens Gamesa S (2021) Cementing solutions to blade recycling in Finland. Available from: https://www.siemensgamesa.com/en-int/explore/journal/2021/12/solutions-blades-recycling-finland. |
[151] | Siemens Gamesa (2021) A winning collaboration behind the RecyclableBlade. Available from: https://www.siemensgamesa.com/en-int/explore/journal/2021/11/recyclable-blade. |
[152] | Siemens Gamesa (2022) Offshore Wind Turbine. Available from: https://www.siemensgamesa.com/products-and-services/offshore/wind-turbine-sg-14-222-dd. |
[153] |
Simons PJ, Cheung WM (2016) Development of a quantitative analysis system for greener and economically sustainable wind farms. J Clean Prod 133: 886–898. https://doi.org/10.1016/j.jclepro.2016.06.030 doi: 10.1016/j.jclepro.2016.06.030
![]() |
[154] | Skaare B (2017) Development of the Hywind Concept. ASME 2017 36th International Conference on Ocean, Offshore and Arctic Engineering. https://doi.org/10.1016/j.jclepro.2016.06.030 |
[155] |
Sommer V, Walther G (2021) Recycling and recovery infrastructures for glass and carbon fiber reinforced plastic waste from wind energy industry: A European case study. Waste Manage 121: 265–275. https://doi.org/10.1016/j.wasman.2020.12.021 doi: 10.1016/j.wasman.2020.12.021
![]() |
[156] | SPIRE (2017) EcoBulk. Available from: https://www.ecobulk.eu/project/. |
[157] | SSE Renewables (2022) Arklow Bank - Offshore Infrastructure. Available from: https://www.sserenewables.com/offshore-wind/projects/arklow-bank-wind-park/offshore/. |
[158] | SSE Renewables, Equinor and Vargronn (2010) Dogger Bank Wind Farm. Available from: https://doggerbank.com/about/. |
[159] |
Stankovic JA (2014) Research directions for the internet of things. IEEE Int Things J 1: 3–9. https://doi.org/10.1109/JIOT.2014.2312291 doi: 10.1109/JIOT.2014.2312291
![]() |
[160] | STENA (2009) Recycling of Waste Glass Fibre Reinforced Plastic with Microwave Pyrolysis. Available from: https://documents.pub/document/recycling-of-waste-glass-fibre-reinforced-plastic-with-microwave-pyrolysis-.html?page = 2. |
[161] | Svendsen H (2017) DreamWind. Available from: https://www.dreamwind.dk/en/. |
[162] | Sweden SC (2022) Markbygden 1101 – Europe's Largest Onshore Windfarm. Available from: https://smartcitysweden.com/best-practice/423/markbygden-1101-europes-largest-onshore-wind-farm/. |
[163] | The German Federal Environment Agency (2017) Developing a concept and measures for resource saving dismantling of wind turbines. Available from: https://ramboll.com/media/environ/supporting-a-major-circular-economy-project-in-the-german-wind-energy-sector. |
[164] |
Tremeac B, Meunier F (2009) Life cycle analysis of 4.5 MW and 250 W wind turbines. Renew Sust Energ Rev 13: 2104–2110. https://doi.org/10.1016/j.rser.2009.01.001 doi: 10.1016/j.rser.2009.01.001
![]() |
[165] | UL (2018) Wind Turbine Generator - Life Time Extension (LTE) - UL 4143. 29. Available from: https://www.shopulstandards.com/ProductDetail.aspx?productId = UL4143_1_S_20180209. |
[166] | United Nations (2015) Paris Agreement. Report of the Conference of the Parties to the United Nations Framework Convention on Climate Change (21st Session, 2015: Paris). Retrived December, HeinOnline. |
[167] | United Nations (2016) Transforming our world: The 2030 agenda for sustainable development. A/RES/70/1. |
[168] | University of Bristol (2014) HiPerDiF - high performance discontinuous fibre. Available from: http://www.bristol.ac.uk/composites/research/hiperdif/. |
[169] | Universidad de Castilla la Mancha (2015) NANOLEAP - Nanocomposite for building constructions and civil infraestructures: European network pilot production line to promote industrial application cases. Available from: https://cordis.europa.eu/project/id/646397. |
[170] | van Exter P, Bosch S, Schipper B, et al. (2018) Metal Demand for Renewable Electricity Generation in The Netherlands—Navigating a Complex Supply Chain. Amsterdam, The Netherlands, Metabolic. |
[171] | Vattenfall (2018) Hollandse Kust. Available from: https://vattenfall-hollandsekust.nl/en/. |
[172] | Velenturf APM (2021) A Framework and Baseline for the Integration of a Sustainable Circular Economy in Offshore Wind. 14: 5540. https://doi.org/10.3390/en14175540 |
[173] | Vestas (2021) CETEC - Circular Economy for Thermosets Epoxy Composites. Available from: https://www.vestas.com/en/media/company-news/2021/new-coalition-of-industry-and-academia-to-commercialise-c3347473#!NewsView. |
[174] | Vestas (2021) Driving the energy transition by taking the next step in our modularisation journey. Available from: https://www.vestas.com/en/media/blog/technology/the-next-step-in-our-modularisation-journey. |
[175] |
Wilhelmsson D, Malm T (2008) Fouling assemblages on offshore wind power plants and adjacent substrata. Estuar Coast Shelf S 79: 459–466. https://doi.org/10.1016/j.ecss.2008.04.020 doi: 10.1016/j.ecss.2008.04.020
![]() |
[176] | Wind Energy Technologies Office (2022) New Study Explores 3D Printing of Permanent Magnets for Wind Turbines. Available from: https://www.energy.gov/eere/wind/articles/new-study-explores-3d-printing-permanent-magnets-wind-turbines. |
[177] | Wind Europe (2020) Decommissioning of onshore wind turbines - Industry Guidance Document. 53. |
[178] | Wind Europe (2020) How to build a circular economy for wind turbine blades through policy and partnerships: 13. |
[179] | Wind Europe (2021) Interative Data - Map of onshore wind farms. Wind Europe Intelligence Platform. |
[180] | Wind Europe (2023) European Offshore Wind Farms Map Public. Available from: https://windeurope.org/intelligence-platform/product/european-offshore-wind-farms-map-public/. |
[181] | Wind Europe (2022) National Energy & Climate Plans. Available from: https://windeurope.org/2030plans/#: ~: text = National%20Energy%20%26%20Climate%20Plans%20The%202030%20National, under%20the%20Governance%20Regulation%20adopted%20in%20December%202018. |
[182] | Wind Europe (2022) Wind Energy in Europe: 2021 Statistics and the Outlook for 2022–2026, Wind Europe Intelligence Platform. Available from: https://windeurope.org/intelligence-platform/product/wind-energy-in-europe-2021-statistics-and-the-outlook-for-2022-2026/. |
[183] | Wind Power Monthly (2021) GE Renewable Energy to trial 'gamechanging' 3D printing for offshore wind turbine nacelles. |
[184] | Wiser RH, Bolinger M, Hoen B, et al. (2021) Land-Based Wind Market Report: 2021 Edition, Lawrence Berkeley National Lab.(LBNL), Berkeley, CA (United States): 87. |
[185] |
Wu X, Hu Y, Li Y, et al. (2019a) Foundations of offshore wind turbines: A review. Renew Sust Energ Rev 104: 379–393. https://doi.org/10.1016/j.rser.2019.01.012 doi: 10.1016/j.rser.2019.01.012
![]() |
[186] | Wu J, Wang H, Wang W, et al. (2019b) Performance evaluation for sustainability of wind energy project using improved multi-criteria decision-making method. J Modern Power Syst Clean Energ 7: 1165–1176. https://doi.org/ 10.1007/s40565-019-0517-6 |
[187] |
Yang J, Zhang L, Chang Y, et al. (2020) Understanding the material efficiency of the wind power sector in China: A spatial-temporal assessment. Resour Conserv Recy 155: 104668. https://doi.org/10.1016/j.resconrec.2019.104668 doi: 10.1016/j.resconrec.2019.104668
![]() |
[188] |
Yang K (2020) Geometry design optimization of a wind turbine blade considering effects on aerodynamic performance by linearization. Energies 13: 2320. https://doi.org/10.3390/EN13092320 doi: 10.3390/EN13092320
![]() |
[189] |
Yassine C, Abdul-Wahab S (2020) Wind turbine performance analysis for energy cost minimization. Renew Wind Water Solar Energ 7. https://doi.org/10.1186/s40807-020-00062-7 doi: 10.1186/s40807-020-00062-7
![]() |
[190] | Zhang L, Shi W, Karimirad M, et al. (2020) Second-order hydrodynamic effects on the response of three semisubmersible floating offshore wind turbines. Ocean Eng 207: 107371. ttps://doi.org/10.1016/j.oceaneng.2020.107371 |
1. | Arben Gjukaj, Rexhep Shaqiri, Qamil Kabashi, Vezir Rexhepi, Renewable energy integration and distributed generation in Kosovo: Challenges and solutions for enhanced energy quality, 2024, 12, 2333-8334, 686, 10.3934/energy.2024032 | |
2. | Miguel S. Teixeira, Teresa M. Mata, Ana Lourenço, Filipa Oliveira, José Oliveira, António A. Martins, Life Cycle Assessment of Tinplate Aerosol Cans: Evaluating the Role of Photovoltaic Energy and Green Hydrogen in Environmental Impact Reduction, 2025, 12, 2076-3298, 73, 10.3390/environments12030073 |
Ref. | Year | Project name | Site | Remarks |
(LM Wind Power, 2022) | 2022 | ZEBRA | On and offshore | ● design and manufacture the wind industry's first 100% recyclable wind turbine blade |
(ECHT Community, 2023) | 2022 | Circular Wind Hub | --- | ● circular strategies in the wind sector |
(National Composites Centre, 2021) | 2021 | SusWind | Offshore | ● accelerating sustainable composite materials and technology for wind turbine blades |
(Bennet, 2021) | 2021 | ORE Catapult | Offshore | ● establishing reliable and efficient recycling in the wind sector |
(DecomBlades, 2021) | 2021 | DecomBlades | --- | ● establish functional, sustainable value chains to handle end of life wind turbine blades |
(Vestas, 2021) | 2021 | CETEC | On and offshore | ● new solution for full recyclability of wind turbine blades |
(bcircular, 2020) | 2020 | R3FIBER | --- | ● green technology to recycle wind turbine blades |
(ECHT Community, 2020) | 2020 | Moonshot Circular Wind Farms | --- | ● ideation process focussed on circular strategies in the wind industry |
(Nattional Composites Centre, 2019) | 2019 | ReDisCoveR Composites | --- | ● solve the issues faced by composites at the end of life |
(Interreg, 2018) | 2018 | DecomTools | Offshore | ● devising and developing eco-innovative concepts for offshore wind parks |
(Re-wind network, 2018) | 2018 | Re-Wind | On and offshore | ● repurposing wind blades |
(Markaide, 2018) | 2018 | AIRPOXY | --- | ● introduces a novel family of ground-breaking thermoset composites |
(Svendsen, 2017) | 2017 | Dreamwind | --- | ● development of new composite materials |
(SPIRE, 2017) | 2017 | Ecobulk | --- | ● formulating materials that allow high recycled content |
(Colledani, 2017) | 2017 | FiberEUse | --- | ● large scale demonstration of new circular economy value-chains based on the reuse of end-of-life fiber reinforced composites |
(Fraunhofer Institute for Wood Research Wilhelm-Klauditz-Institut, 2017) | 2017 | ReRoBalsa | --- | ● recovering balsa wood and plastic foam for the production of insulation materials |
(The German Federal Environment Agency, 2017) | 2017 | Ramboll BBB * | --- | ● develop a circular economy approach for end-of-life onshore wind turbines |
(Interreg, 2016) | 2016 | Recy-composite | On and offshore | ● three-level global cross-border approach: material recovery, thermochemical recycling and energy recovery |
(European Commission, 2016) | 2016 | Eco-turbine | On and offshore | ● flax based bio composites ● lamella type rectangular "wall" of series of blades |
(European Commission, 2016) | 2016 | PowderBlade | Offshore | ● carbon/glass fiber in powder epoxy |
(Universidad de Castilla la Mancha, 2015) | 2015 | NANOLEAP | Offshore | ● network of specialized pilot lines for the production of nanocomposite-based products |
(European Commission, 2015) | 2015 | SPARCARB | On and offshore | ● lightning protection of CFC structures |
(University of Bristol, 2014) | 2014 | HiPerDiF | --- | ● producing highly aligned discontinuous fiber composites |
(European Commission, 2014) | 2014 | AutowinSpec | Onshore | ● automatic blade condition monitoring |
(Fraunhofer Institute for Process Engineering and Packaging IVV, 2014) | 2014 | ForCycle | --- | ● recycling of high-quality metal-plastic composites |
(EV, 2013) | 2013 | WALiD | Offshore | ● cost-effective advanced lightweight design |
(Iberdrola, 2013) | 2013 | LIFE BRIO | --- | ● innovative and sustainable methodology for end-of-life wind turbine blades management |
(Cranfield University, 2013) | 2013 | EXHUME | --- | ● novel recycling and remanufacturing processes |
(GENVIND, 2012) | 2012 | Genvind Innovation Consortium | --- | ● sustainable recycling of composites |
(European Commission, 2012) | 2012 | CORETO | On and offshore | ● in-situ performance of major composite repair steps |
(AG, 2012) | 2012 | SELFRAG CFRP | --- | ● recycling of thermoset composite materials |
(Richerche, 2011) | 2011 | SUSRAC | --- | ● sustainable recycling of composites |
(STENA, 2009) | 2009 | LIFE07 ENV/S/000904 | --- | ● recycling of glass fibre reinforced plastics |
(European Commission, 2009a) | 2009 | WinTur | On and offshore | ● integration of acoustic emission and long-range ultrasonics |
(Plastic Omnium Auto Exterieur Services, 2009) | 2009 | EURECOMP | --- | ● recycling fibre-reinforced thermoset composites |
(European Commission 2009b) | 2009 | PROND | On and offshore | ● self-adaptive blade of small wind turbine |
(Hebo Engineering BV 2003) | 2003 | REACT | --- | ● recycling glass and carbon fibres |
*The project does not have an acronym; its complete name is "Developing a concept and measures for resource saving dismantling of wind turbines". |
Ref. | Project | Region | Site | Capacity | Remarks |
(SSE Renewables, Equinor et al., 2010) | Dogger Bank | Multiregion* | Offshore | 2.4 GW | multiple substations interconnected |
(Netherlands Enterprise Agency, 2022) | Ijmuiden Ver | Netherlands | Offshore | 6 GW | 6 sites |
(Vattenfall, 2018) | Hollandse K. | Offshore | 3 GW | largest subsidy-free wind farm at sea | |
(PowerTechnology, 2019) | Gemini | Offshore | 600 MW | powers approximately 785,000 homes | |
(SSE Renewables, 2022) | Arklow Bank | Ireland | Offshore | 800 MW | only operational Irish offshore site now |
(WindEurope, 2023) | HywindTampen | Norway | Offshore | 88 MW | still under construction |
(Interesting Engineering, 2016) | Nordic Wind | Onshore | 1000 MW | Europe's largest onshore wind project | |
(Smart City Sweden, 2022) | Markbygden 1101 | Sweden | Onshore | 16.25 GW** | Europe's largest onshore windfarm |
(Eolien Maritime France, 2022) | Fécamp | France | Offshore | 500 MW | offsets 2 Mt of CO2/year |
(Iberdrola, 2020) | Saint-Brieuc | Offshore | 496 MW | 1st large-scale offshore site in Brittany | |
(WindEurope, 2023) | Saint-Nazaire | Offshore | 496 MW | still under construction | |
(Newman, 2018) | El Cabrito | Spain | Onshore | 30 MW | repowered in 2019 |
(Newman, 2018) | Sotavento | Onshore | 17.5 MW | real-time data available online | |
(Newman, 2018) | S. d'Abruzzo | Italy | Onshore | 13 MW | best-practice case |
(BKW, 2023) | Puglia | Onshore | 130 MW | allowed to significantly exceed BKW's 1,000 megawatt target | |
(Iberdrola, 2023) | Baltic Eagle | Germany | Offshore | 476 MW | avoids almost 1Mt of CO2/year |
(Power Technology, 2019) | Gode Wind | Offshore | 582 MW | powers 600,000 households | |
(Moray Offshore Renewable Power, 2014) | Moray East | UK | Offshore | 1.12 MW | provides 40% of Scotland's electricity |
(Orsted, 2022) | Hornsea 2 | Offshore | 1.3 GW | powers more than 1.4 million homes | |
(GmbH, 2022) | Triton Knoll | Offshore | 857 MW | largest offshore wind pipeline in the UK | |
(Newman, 2018) | North Hoyle | Offshore | 60 MW | Wales' first offshore wind farm | |
(Newman, 2018) | Walney | Offshore | 659 MW | world's largest operational offshore site | |
(Newman, 2018) | W.Duddon Sands | Offshore | 500 MW | serves more than 270,000 households | |
(Interesting Engineering, 2016) | Whitelee | Onshore | 539 MW | largest onshore wind farm in the UK | |
(Interesting Engineering, 2016) | Viking | Onshore | 457 MW | third largest wind farm in Scotland | |
(Power Technology, 2019) | F. Cogealac | Romania | Offshore | 600 MW | provides 10% of renewables in Romania |
*Germany, Denmark, Netherlands, UK ** for the highest capacity turbine, depending on the construction phase (https://markbygden1101.com/the-place-and-purpose/) |
Ref. | Year | Strategy | Application |
(Re-wind network, 2018; Jacobs, 2021; Joustra et al., 2021) | 2018, 2021 | Reuse; Repurpose | New turbine/blade; Platforms; docks; piers; jetties; buoys; seawalls; bridges; powerline poles; electricity transmission towers; cellphone towers; lighting and luminaire poles; sign support poles; sound barriers; access barriers; erosion barriers; shelters; glamping pods; canopies; roofing solutions; walls and foundations; partitions; feed bunks; |
(Medici et al., 2020; Architecture news & editorial desk, 2021, Jacobs, 2021) | 2021, 2020 | Repurpose | Bike sheds; playgrounds; public seats; bus stops; reefs |
(Bank et al., 2018) | 2018 | Repurpose | Housing applications |
(Schmid et al., 2020) | 2020 | Recycle | Furniture; automotive parts |
(Oliveux et al., 2015, Rani et al., 2021) | 2015, 2021 | Recycle | Replace small amounts of virgin fibers |
(Jensen and Skelton, 2018, ETIPWind Executive Committee, 2019; Jacobs, 2021; reNewsBiz, 2021) | 2021, 2019, 2018 | Recover; Recycle | Cement co-processing Industrial filler material |
(Bloomberg, 2021) | 2021 | Recycle | Sports gear |
(Jacobs, 2021; Velenturf, 2021) | 2021 | Recycle | Repurposed metal; surplus slag for construction aggregate; precast concrete; precast manhole; sandwich construction panels; cement; concrete blocks; energy |
Wind turbine power (MW) | Ranking of life cycle stages' contribution to the impacts | Main environmental impact categories | Environmental impact value | Impact assessment method | Reference |
1.5 | RMA+M+I+T > OM > EL | GWP | 1.18 x 10−2 | CML | (Ozoemena et al., 2018) |
ODP | 1.24 x 10−9 | ||||
AP | 9.17 x 10−5 | ||||
EP* | 6.90 x 10−5 | ||||
POCP | 6.54 x 10−6 | ||||
2.0 | RMA+M > I > OM > T > EL | GWP | 1.80 x 10−2 | TRACI | (Alsaleh and Sattler, 2019) |
ODP | 2.69 x 10−9 | ||||
AP | 1.04 x 10−4 | ||||
EP* | 9.78 x 10−5 | ||||
S | 1.71 x 10−3 | ||||
2.0 | RMA+M+T > OM > I > EL | GWP | 7.70 x 10−3 | CML/ ReCiPe | (Garrett and Rønde, 2013) |
AP | 3.70 x 10−5 | ||||
EP** | 3.70 x 10−6 | ||||
POCP | 5.40 x 10−6 | ||||
2.0 | Information not available | GWP | 6.58 x 10−3 | CML Leiden 2000 | (Martínez et al., 2018) |
ODP | 5.21 x 10−10 | ||||
POCP | 2.13 x 10−6 | ||||
AP | 5.43 x 10−5 | ||||
EP* | 5.68 x 10−6 | ||||
3.0 | RMA+M > I > T > OM | GWP | 9.11 x 10−3 | TRACI | (Martínez et al., 2018) |
AP | 3.45 x 10−3 | ||||
EP** | 8.3 x 10−6 | ||||
ODP | 1.14 x 10−9 | ||||
S | 2.73 × 10−5 | ||||
ET | 2.9 x 10−2 | ||||
4.2 | RMA+M > I > OM > EL | GWP | 5.6 x 10−3 | CML | (Razdan and Garrett, 2019) |
AP | 2.2 x 10−5 | ||||
EP | 2.7 x 10−6 | ||||
POCP | 1.6 x 10−6 | ||||
4.5 | RMA+M+I > T > OM > EL | GWP | 1.60 x 10−2 | Impact 2002+ | (Tremeac and Meunier, 2009) |
RD | 3.00 x 10−4 | ||||
Life cycle stages: RMA - Raw materials acquisition; M – Manufacturing; I - Installation; OM - Operation and maintenance; T - Transportation; EL - End of life. Environmental Impact Categories: GWP = Global warming potential (kg CO2 eq/kWh), ODP = Ozone depletion potential (CFC-11eq/kWh), AP = Acidification potential (kg SO2 eq/kWh), EP* = Eutrophication potential (kg PO4 eq kg/kWh), EP** = Eutrophication potential (kg N eq/kWh), S = Smog (kg O3 eq/kWh), POCP = Photochemical ozone creation potential (kg C2H4 eq/kWh), RD = Resources depletion (GJ primary non-renewable energy/kWh), ET = Ecotoxicity (CTUe/kWh). |
Ref. | Year | Project name | Site | Remarks |
(LM Wind Power, 2022) | 2022 | ZEBRA | On and offshore | ● design and manufacture the wind industry's first 100% recyclable wind turbine blade |
(ECHT Community, 2023) | 2022 | Circular Wind Hub | --- | ● circular strategies in the wind sector |
(National Composites Centre, 2021) | 2021 | SusWind | Offshore | ● accelerating sustainable composite materials and technology for wind turbine blades |
(Bennet, 2021) | 2021 | ORE Catapult | Offshore | ● establishing reliable and efficient recycling in the wind sector |
(DecomBlades, 2021) | 2021 | DecomBlades | --- | ● establish functional, sustainable value chains to handle end of life wind turbine blades |
(Vestas, 2021) | 2021 | CETEC | On and offshore | ● new solution for full recyclability of wind turbine blades |
(bcircular, 2020) | 2020 | R3FIBER | --- | ● green technology to recycle wind turbine blades |
(ECHT Community, 2020) | 2020 | Moonshot Circular Wind Farms | --- | ● ideation process focussed on circular strategies in the wind industry |
(Nattional Composites Centre, 2019) | 2019 | ReDisCoveR Composites | --- | ● solve the issues faced by composites at the end of life |
(Interreg, 2018) | 2018 | DecomTools | Offshore | ● devising and developing eco-innovative concepts for offshore wind parks |
(Re-wind network, 2018) | 2018 | Re-Wind | On and offshore | ● repurposing wind blades |
(Markaide, 2018) | 2018 | AIRPOXY | --- | ● introduces a novel family of ground-breaking thermoset composites |
(Svendsen, 2017) | 2017 | Dreamwind | --- | ● development of new composite materials |
(SPIRE, 2017) | 2017 | Ecobulk | --- | ● formulating materials that allow high recycled content |
(Colledani, 2017) | 2017 | FiberEUse | --- | ● large scale demonstration of new circular economy value-chains based on the reuse of end-of-life fiber reinforced composites |
(Fraunhofer Institute for Wood Research Wilhelm-Klauditz-Institut, 2017) | 2017 | ReRoBalsa | --- | ● recovering balsa wood and plastic foam for the production of insulation materials |
(The German Federal Environment Agency, 2017) | 2017 | Ramboll BBB * | --- | ● develop a circular economy approach for end-of-life onshore wind turbines |
(Interreg, 2016) | 2016 | Recy-composite | On and offshore | ● three-level global cross-border approach: material recovery, thermochemical recycling and energy recovery |
(European Commission, 2016) | 2016 | Eco-turbine | On and offshore | ● flax based bio composites ● lamella type rectangular "wall" of series of blades |
(European Commission, 2016) | 2016 | PowderBlade | Offshore | ● carbon/glass fiber in powder epoxy |
(Universidad de Castilla la Mancha, 2015) | 2015 | NANOLEAP | Offshore | ● network of specialized pilot lines for the production of nanocomposite-based products |
(European Commission, 2015) | 2015 | SPARCARB | On and offshore | ● lightning protection of CFC structures |
(University of Bristol, 2014) | 2014 | HiPerDiF | --- | ● producing highly aligned discontinuous fiber composites |
(European Commission, 2014) | 2014 | AutowinSpec | Onshore | ● automatic blade condition monitoring |
(Fraunhofer Institute for Process Engineering and Packaging IVV, 2014) | 2014 | ForCycle | --- | ● recycling of high-quality metal-plastic composites |
(EV, 2013) | 2013 | WALiD | Offshore | ● cost-effective advanced lightweight design |
(Iberdrola, 2013) | 2013 | LIFE BRIO | --- | ● innovative and sustainable methodology for end-of-life wind turbine blades management |
(Cranfield University, 2013) | 2013 | EXHUME | --- | ● novel recycling and remanufacturing processes |
(GENVIND, 2012) | 2012 | Genvind Innovation Consortium | --- | ● sustainable recycling of composites |
(European Commission, 2012) | 2012 | CORETO | On and offshore | ● in-situ performance of major composite repair steps |
(AG, 2012) | 2012 | SELFRAG CFRP | --- | ● recycling of thermoset composite materials |
(Richerche, 2011) | 2011 | SUSRAC | --- | ● sustainable recycling of composites |
(STENA, 2009) | 2009 | LIFE07 ENV/S/000904 | --- | ● recycling of glass fibre reinforced plastics |
(European Commission, 2009a) | 2009 | WinTur | On and offshore | ● integration of acoustic emission and long-range ultrasonics |
(Plastic Omnium Auto Exterieur Services, 2009) | 2009 | EURECOMP | --- | ● recycling fibre-reinforced thermoset composites |
(European Commission 2009b) | 2009 | PROND | On and offshore | ● self-adaptive blade of small wind turbine |
(Hebo Engineering BV 2003) | 2003 | REACT | --- | ● recycling glass and carbon fibres |
*The project does not have an acronym; its complete name is "Developing a concept and measures for resource saving dismantling of wind turbines". |
Ref. | Project | Region | Site | Capacity | Remarks |
(SSE Renewables, Equinor et al., 2010) | Dogger Bank | Multiregion* | Offshore | 2.4 GW | multiple substations interconnected |
(Netherlands Enterprise Agency, 2022) | Ijmuiden Ver | Netherlands | Offshore | 6 GW | 6 sites |
(Vattenfall, 2018) | Hollandse K. | Offshore | 3 GW | largest subsidy-free wind farm at sea | |
(PowerTechnology, 2019) | Gemini | Offshore | 600 MW | powers approximately 785,000 homes | |
(SSE Renewables, 2022) | Arklow Bank | Ireland | Offshore | 800 MW | only operational Irish offshore site now |
(WindEurope, 2023) | HywindTampen | Norway | Offshore | 88 MW | still under construction |
(Interesting Engineering, 2016) | Nordic Wind | Onshore | 1000 MW | Europe's largest onshore wind project | |
(Smart City Sweden, 2022) | Markbygden 1101 | Sweden | Onshore | 16.25 GW** | Europe's largest onshore windfarm |
(Eolien Maritime France, 2022) | Fécamp | France | Offshore | 500 MW | offsets 2 Mt of CO2/year |
(Iberdrola, 2020) | Saint-Brieuc | Offshore | 496 MW | 1st large-scale offshore site in Brittany | |
(WindEurope, 2023) | Saint-Nazaire | Offshore | 496 MW | still under construction | |
(Newman, 2018) | El Cabrito | Spain | Onshore | 30 MW | repowered in 2019 |
(Newman, 2018) | Sotavento | Onshore | 17.5 MW | real-time data available online | |
(Newman, 2018) | S. d'Abruzzo | Italy | Onshore | 13 MW | best-practice case |
(BKW, 2023) | Puglia | Onshore | 130 MW | allowed to significantly exceed BKW's 1,000 megawatt target | |
(Iberdrola, 2023) | Baltic Eagle | Germany | Offshore | 476 MW | avoids almost 1Mt of CO2/year |
(Power Technology, 2019) | Gode Wind | Offshore | 582 MW | powers 600,000 households | |
(Moray Offshore Renewable Power, 2014) | Moray East | UK | Offshore | 1.12 MW | provides 40% of Scotland's electricity |
(Orsted, 2022) | Hornsea 2 | Offshore | 1.3 GW | powers more than 1.4 million homes | |
(GmbH, 2022) | Triton Knoll | Offshore | 857 MW | largest offshore wind pipeline in the UK | |
(Newman, 2018) | North Hoyle | Offshore | 60 MW | Wales' first offshore wind farm | |
(Newman, 2018) | Walney | Offshore | 659 MW | world's largest operational offshore site | |
(Newman, 2018) | W.Duddon Sands | Offshore | 500 MW | serves more than 270,000 households | |
(Interesting Engineering, 2016) | Whitelee | Onshore | 539 MW | largest onshore wind farm in the UK | |
(Interesting Engineering, 2016) | Viking | Onshore | 457 MW | third largest wind farm in Scotland | |
(Power Technology, 2019) | F. Cogealac | Romania | Offshore | 600 MW | provides 10% of renewables in Romania |
*Germany, Denmark, Netherlands, UK ** for the highest capacity turbine, depending on the construction phase (https://markbygden1101.com/the-place-and-purpose/) |
Ref. | Year | Strategy | Application |
(Re-wind network, 2018; Jacobs, 2021; Joustra et al., 2021) | 2018, 2021 | Reuse; Repurpose | New turbine/blade; Platforms; docks; piers; jetties; buoys; seawalls; bridges; powerline poles; electricity transmission towers; cellphone towers; lighting and luminaire poles; sign support poles; sound barriers; access barriers; erosion barriers; shelters; glamping pods; canopies; roofing solutions; walls and foundations; partitions; feed bunks; |
(Medici et al., 2020; Architecture news & editorial desk, 2021, Jacobs, 2021) | 2021, 2020 | Repurpose | Bike sheds; playgrounds; public seats; bus stops; reefs |
(Bank et al., 2018) | 2018 | Repurpose | Housing applications |
(Schmid et al., 2020) | 2020 | Recycle | Furniture; automotive parts |
(Oliveux et al., 2015, Rani et al., 2021) | 2015, 2021 | Recycle | Replace small amounts of virgin fibers |
(Jensen and Skelton, 2018, ETIPWind Executive Committee, 2019; Jacobs, 2021; reNewsBiz, 2021) | 2021, 2019, 2018 | Recover; Recycle | Cement co-processing Industrial filler material |
(Bloomberg, 2021) | 2021 | Recycle | Sports gear |
(Jacobs, 2021; Velenturf, 2021) | 2021 | Recycle | Repurposed metal; surplus slag for construction aggregate; precast concrete; precast manhole; sandwich construction panels; cement; concrete blocks; energy |
Wind turbine power (MW) | Ranking of life cycle stages' contribution to the impacts | Main environmental impact categories | Environmental impact value | Impact assessment method | Reference |
1.5 | RMA+M+I+T > OM > EL | GWP | 1.18 x 10−2 | CML | (Ozoemena et al., 2018) |
ODP | 1.24 x 10−9 | ||||
AP | 9.17 x 10−5 | ||||
EP* | 6.90 x 10−5 | ||||
POCP | 6.54 x 10−6 | ||||
2.0 | RMA+M > I > OM > T > EL | GWP | 1.80 x 10−2 | TRACI | (Alsaleh and Sattler, 2019) |
ODP | 2.69 x 10−9 | ||||
AP | 1.04 x 10−4 | ||||
EP* | 9.78 x 10−5 | ||||
S | 1.71 x 10−3 | ||||
2.0 | RMA+M+T > OM > I > EL | GWP | 7.70 x 10−3 | CML/ ReCiPe | (Garrett and Rønde, 2013) |
AP | 3.70 x 10−5 | ||||
EP** | 3.70 x 10−6 | ||||
POCP | 5.40 x 10−6 | ||||
2.0 | Information not available | GWP | 6.58 x 10−3 | CML Leiden 2000 | (Martínez et al., 2018) |
ODP | 5.21 x 10−10 | ||||
POCP | 2.13 x 10−6 | ||||
AP | 5.43 x 10−5 | ||||
EP* | 5.68 x 10−6 | ||||
3.0 | RMA+M > I > T > OM | GWP | 9.11 x 10−3 | TRACI | (Martínez et al., 2018) |
AP | 3.45 x 10−3 | ||||
EP** | 8.3 x 10−6 | ||||
ODP | 1.14 x 10−9 | ||||
S | 2.73 × 10−5 | ||||
ET | 2.9 x 10−2 | ||||
4.2 | RMA+M > I > OM > EL | GWP | 5.6 x 10−3 | CML | (Razdan and Garrett, 2019) |
AP | 2.2 x 10−5 | ||||
EP | 2.7 x 10−6 | ||||
POCP | 1.6 x 10−6 | ||||
4.5 | RMA+M+I > T > OM > EL | GWP | 1.60 x 10−2 | Impact 2002+ | (Tremeac and Meunier, 2009) |
RD | 3.00 x 10−4 | ||||
Life cycle stages: RMA - Raw materials acquisition; M – Manufacturing; I - Installation; OM - Operation and maintenance; T - Transportation; EL - End of life. Environmental Impact Categories: GWP = Global warming potential (kg CO2 eq/kWh), ODP = Ozone depletion potential (CFC-11eq/kWh), AP = Acidification potential (kg SO2 eq/kWh), EP* = Eutrophication potential (kg PO4 eq kg/kWh), EP** = Eutrophication potential (kg N eq/kWh), S = Smog (kg O3 eq/kWh), POCP = Photochemical ozone creation potential (kg C2H4 eq/kWh), RD = Resources depletion (GJ primary non-renewable energy/kWh), ET = Ecotoxicity (CTUe/kWh). |