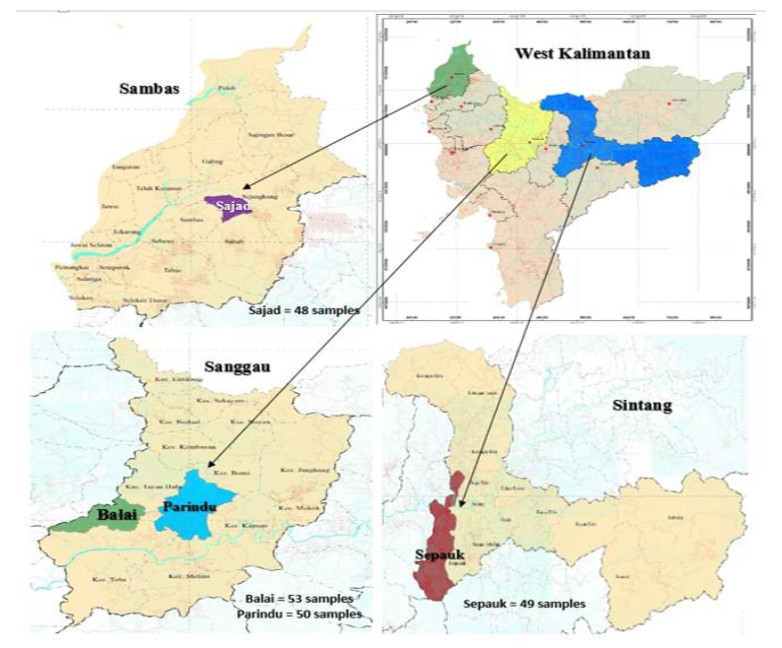
Fluidized bed granulation (FBG) is a widely used granulation technology in the pharmaceutical industry. However, defluidization caused by the formation of large aggregates poses a challenge to FBG, particularly in traditional Chinese medicine (TCM) due to its complex physicochemical properties of aqueous extracts. Therefore, this study aims to identify the complex relationships between physicochemical characteristics and defluidization using data mining methods. Initially, 50 types of TCM were decocted and assessed for their potential influence on defluidization using a set of 11 physical properties and 10 chemical components, utilizing the loss rate as an evaluation index. Subsequently, the random forest (RF) and Apriori algorithms were utilized to uncover intricate association rules among physicochemical characteristics and defluidization. The RF algorithm analysis revealed the top 8 critical factors associated with defluidization. These factors include physical properties like glass transition temperature (Tg) and dynamic surface tension (DST) of DST100ms, DST1000ms, DST10ms and conductivity, in addition to chemical components such as fructose, glucose and protein contents. The results from Apriori algorithm demonstrated that lower Tg and conductivity were associated with an increased risk of defluidization, resulting in a higher loss rate. Moreover, DST100ms, DST1000ms and DST10ms exhibited a contrasting trend in the physical properties Specifically, defluidization probability increases when Tg and conductivity dip below 29.04℃ and 6.21 ms/m respectively, coupled with DST10ms, DST100ms and DST1000ms values exceeding 70.40 mN/m, 66.66 mN/m and 61.58 mN/m, respectively. Moreover, an elevated content of low molecular weight saccharides was associated with a higher occurrence of defluidization, accompanied by an increased loss rate. In contrast, protein content displayed an opposite trend regarding chemical properties. Precisely, the defluidization likelihood amplifies when fructose and glucose contents surpass 20.35 mg/g and 34.05 mg/g respectively, and protein concentration is less than 1.63 mg/g. Finally, evaluation criteria for defluidization were proposed based on these results, which could be used to avoid this situation during the granulation process. This study demonstrated that the RF and Apriori algorithms are effective data mining methods capable of uncovering key factors affecting defluidization.
Citation: Sai Fu, Yuting Luo, Yuling Liu, Qian Liao, Shasha Kong, Anhui Yang, Longfei Lin, Hui Li. Mining association rules between the granulation feasibility and physicochemical properties of aqueous extracts from Chinese herbal medicine in fluidized bed granulation[J]. Mathematical Biosciences and Engineering, 2023, 20(11): 19065-19085. doi: 10.3934/mbe.2023843
[1] | Priscilla Charmaine Kwade, Benjamin Kweku Lugu, Sadia Lukman, Carl Edem Quist, Jianxun Chu . Farmers’ attitude towards the use of genetically modified crop technology in Southern Ghana: The mediating role of risk perception. AIMS Agriculture and Food, 2019, 4(4): 833-853. doi: 10.3934/agrfood.2019.4.833 |
[2] | Hashim Durrani, Ainuddin Syed, Amjad Khan, Alam Tareen, Nisar Ahmed Durrani, Bashir Ahmed Khwajakhail . Understanding farmers' risk perception to drought vulnerability in Balochistan, Pakistan. AIMS Agriculture and Food, 2021, 6(1): 82-105. doi: 10.3934/agrfood.2021006 |
[3] | Angelina De Pascale, Carlo Giannetto, Agata Zirilli, Angela Alibrandi, Maurizio Lanfranchi . How Mediterranean winegrowers perceive climate change. AIMS Agriculture and Food, 2023, 8(2): 440-460. doi: 10.3934/agrfood.2023023 |
[4] | Danar Praseptiangga, Jessica M. Guevara Zambrano, Adhitya Pitara Sanjaya, Dimas Rahadian Aji Muhammad . Challenges in the development of the cocoa and chocolate industry in Indonesia: A case study in Madiun, East Java. AIMS Agriculture and Food, 2020, 5(4): 920-937. doi: 10.3934/agrfood.2020.4.920 |
[5] | Martha Tampaki, Georgia Koutouzidou, Katerina Melfou, Athanasios Ragkos, Ioannis A. Giantsis . The contrasting mosaic of consumers' knowledge on local plant genetic resources sustainability vis a vis the unawareness for indigenous farm animal breeds. AIMS Agriculture and Food, 2024, 9(2): 645-665. doi: 10.3934/agrfood.2024035 |
[6] | Raulston Derrick Gillette, Norio Sakai, Godfrid Erasme Ibikoule . Role and impact of contract farming under various pricing standards: A case of Guyana's rice sector. AIMS Agriculture and Food, 2024, 9(1): 336-355. doi: 10.3934/agrfood.2024020 |
[7] | Robert Ugochukwu Onyeneke, Chinyere Augusta Nwajiuba, Chukwuemeka Chinonso Emenekwe, Anurika Nwajiuba, Chinenye Judith Onyeneke, Precious Ohalete, Uwazie Iyke Uwazie . Climate change adaptation in Nigerian agricultural sector: A systematic review and resilience check of adaptation measures. AIMS Agriculture and Food, 2019, 4(4): 967-1006. doi: 10.3934/agrfood.2019.4.967 |
[8] | W. Mupangwa, S. Walker, E. Masvaya, M. Magombeyi, P. Munguambe . Rainfall risk and the potential of reduced tillage systems to conserve soil water in semi-arid cropping systems of southern Africa. AIMS Agriculture and Food, 2016, 1(1): 85-101. doi: 10.3934/agrfood.2016.1.85 |
[9] | Y.T. Bahta . Smallholder livestock farmers coping and adaptation strategies to agricultural drought. AIMS Agriculture and Food, 2020, 5(4): 964-982. doi: 10.3934/agrfood.2020.4.964 |
[10] | Maurizio Canavari, Federico Gori, Selene Righi, Elena Viganò . Factors fostering and hindering farmers' intention to adopt organic agriculture in the Pesaro-Urbino province (Italy). AIMS Agriculture and Food, 2022, 7(1): 108-129. doi: 10.3934/agrfood.2022008 |
Fluidized bed granulation (FBG) is a widely used granulation technology in the pharmaceutical industry. However, defluidization caused by the formation of large aggregates poses a challenge to FBG, particularly in traditional Chinese medicine (TCM) due to its complex physicochemical properties of aqueous extracts. Therefore, this study aims to identify the complex relationships between physicochemical characteristics and defluidization using data mining methods. Initially, 50 types of TCM were decocted and assessed for their potential influence on defluidization using a set of 11 physical properties and 10 chemical components, utilizing the loss rate as an evaluation index. Subsequently, the random forest (RF) and Apriori algorithms were utilized to uncover intricate association rules among physicochemical characteristics and defluidization. The RF algorithm analysis revealed the top 8 critical factors associated with defluidization. These factors include physical properties like glass transition temperature (Tg) and dynamic surface tension (DST) of DST100ms, DST1000ms, DST10ms and conductivity, in addition to chemical components such as fructose, glucose and protein contents. The results from Apriori algorithm demonstrated that lower Tg and conductivity were associated with an increased risk of defluidization, resulting in a higher loss rate. Moreover, DST100ms, DST1000ms and DST10ms exhibited a contrasting trend in the physical properties Specifically, defluidization probability increases when Tg and conductivity dip below 29.04℃ and 6.21 ms/m respectively, coupled with DST10ms, DST100ms and DST1000ms values exceeding 70.40 mN/m, 66.66 mN/m and 61.58 mN/m, respectively. Moreover, an elevated content of low molecular weight saccharides was associated with a higher occurrence of defluidization, accompanied by an increased loss rate. In contrast, protein content displayed an opposite trend regarding chemical properties. Precisely, the defluidization likelihood amplifies when fructose and glucose contents surpass 20.35 mg/g and 34.05 mg/g respectively, and protein concentration is less than 1.63 mg/g. Finally, evaluation criteria for defluidization were proposed based on these results, which could be used to avoid this situation during the granulation process. This study demonstrated that the RF and Apriori algorithms are effective data mining methods capable of uncovering key factors affecting defluidization.
Risk and uncertainty are significant issues in the agricultural sector [1,2], which cause vulnerabilities in yields and losses in crop production [2,3,4]. Risks in the agricultural sector can affect the input and output allocation decisions [2], affect farmers' household income [5,6] and cause unstable economic growth in developing countries [7]. In the last few years, risks in the agricultural sector have continued to rise, making it essential for farmers to manage the risks and keep farming activities stable [6,8,9].
The risks faced by farmers significantly affect an individual's decision-making behavior, which may differ from the actual condition. Farmers often make decisions based on their feelings, expectations and observation [10]. The assessment of agricultural risks is critical for two reasons. First, a risk strategy cannot be evaluated based on the expected outcomes without considering the magnitude of the risks. Second, risk assessment can help farmers develop effective risk strategies to reduce the likelihood of significant losses and avoid extreme events, such as business bankruptcy [11].
Risk assessment can be conducted by identifying farmers' risk perception based on farming experience, observation and learning from previous events [11,12,13]. This assessment is beneficial for stakeholders and policymakers in understanding environmental conditions [14], addressing agricultural risks [15,16] and planning an efficient risk strategy [9,17]. Huet et al. and The World Bank [7,18] suggested two indicators to identify risk perception in the agricultural sector based on risk likelihood and consequences. It is essential to assess these indicators, as farmers can have the same perception regarding risk probability but different in evaluating the impact [19]. In addition, Sjoberg et al. [20] stated that accurate and precise risk perception could raise farmers' ability to predict and manage risks.
Furthermore, agricultural decision-making is also based on risk attitudes [2,17,21], whether farmers are risk-averse, risk-neutral or risk-taking. The difference in risk attitude is closely related to the farmers' financial condition and readiness to face the consequences of profit or loss from taking risks. A risk-averse attitude becomes a reasonable option for farmers with small capital and inability to accept losses, but this can be problematic for farmers' income and well-being [12]. Risk aversion will also impact the inefficient allocation of resources and business management decisions [11].
The subject of this study is Indonesian rubber farming, which has the largest rubber area in the world and produces around 23.8% of the world's rubber supplies [22]. Indonesian total rubber exports in 2020 were recorded at 2.28 million tonnes, with an export value of US$ 3.01 billion [22]. The export destinations for rubber include the United States, Japan, China, India and other countries. In Indonesia, most rubber plantations (90%) are handled by 2.3 million smallholder farmers [22]. These conditions were also similar in other rubber-producing countries, such as Thailand [23], Malaysia [24,25,26] and China [27,28,29]. Smallholder farmers are characterized by a lack of capital, low assets and poor managerial skills, which makes them vulnerable to price fluctuations and market uncertainties [25,26,30]. Based on statistical data, Indonesia has the largest rubber area in the world. However, rubber production is in the second position after Thailand, which shows low rubber productivity in Indonesia [22]. Rubber productivity in Indonesia in 2020 was 1,018 kg/ha/year [22], while rubber-producing countries such as Thailand and Malaysia have higher productivity.
The low productivity of rubber plantations is due to various risk factors, such as climate change, plant disease and price change risks [31]. The climate change risk in rubber farming is related to high rainfall and rainy days, causing a decrease in tapping frequency and latex productivity [24,32,33]. The disease risks in rubber plants are rubber leaf fall and white root fungus, causing a decrease in rubber productivity [34,35,36]. The price change risk is related to the decline in rubber prices influenced by global market conditions. In 2011, the rubber price reached its highest value and has continued to decline until now [37,38,39,40]. The increasing volatility in rubber prices and a long period of low prices are thought to be among the main reasons for the decline in production [30,38,40,41,42]. The rubber price decline also decreases household income, farmers' welfare and purchasing power for primary and secondary goods [28,31].
The risk accumulation can cause production variability and affect productivity and farm income. Therefore, we address this study to understand rubber farmers' environmental conditions and direct the appropriate risk management. The research objective was to identify farmers' risk perception, risk attitude and determinant factors for smallholder rubber farmers. The study's findings assist stakeholders and policymakers in comprehending the risk and facilitate providing the farmers with programs and policies to mitigate the risks. Furthermore, this paper enriches the literature on risk perception and attitude in the agricultural sector in three ways. First, it focused on plantation crops (especially rubber crops), while previous studies were concerned with food crops [1,11,43,44], fishery [12,45,46] and livestock [10,47,48]. Second, the study identified perceptions based on each type of risk because the risk differences will affect the risk perception [2,11,15,43]. Third, the study identifies risk perceptions and attitudes that are critical in shaping the management capabilities of farmers and directs appropriate decision-making in addressing agricultural risks [15,16].
Risk refers to uncertain consequences or the likelihood of exposure leading to unfavorable conditions [6]. Previous research mainly focused on two risk categories: production risk and market risk [5,9]. Production risk occurs due to factors related to biological, ecological and technological changes [5,7,49]. This risk is closely associated with climate variability [4,50,51,52,53] and plant diseases [2,4,9,11]. Market risk is related to the fluctuation and volatility of input and output prices in farming activities [11,13,47,51]. Market risk often burdens farmers because the causative factors are beyond farmers' control and directly impact household income [5,49]. Multiple agricultural risks can happen simultaneously, so several policy interventions are needed to overcome these risks.
Decision-making in risky situations always makes a trade-off between losses and profits. If there is a possibility of experiencing losses, then there is an opportunity to get profit. Farmers must be able to decide on various alternative strategies that can be done with multiple risks. The ability of farmers to deal with risk depends mainly on risk perception, which is influenced by farming experience, observation and learning from previous events [11,12]. Risk perception is a person's subjective assessment of the probability and consequence of an event [7]. Every risk perception can differ depending on farmer and farm characteristics [19]. Previous research has found determining factors of farmers' risk perception, such as farmers' age [2,11,15,44], education [44,54], farming experience [2,44,54,55,56], farm area [11,44,54,55] and family size [2,44].
Differences in perceptions of each farmer will determine farmers' risk attitudes and strategies for dealing with risks. Risk attitude is a person's response due to their perception while facing significant risk [57]. An individual's attitude will vary depending on how the individual or group understands the risks. A situation that is considered too risky by one person can be regarded as less risky and acceptable to others [57]. Risk attitudes are generally grouped into three categories: risk averse, risk neutral, and risk loving [58]. Being risk-averse is a typical attitude shown by most smallholder farmers [1,2,11,16,21]. Farmers' risk attitudes are relevant to their decision to adopt risk strategies [21,53]. A risk-averse farmer will avoid the risks and try to reduce, transfer or avoid the risks [59]. A risk-averse attitude becomes an obstacle for farmers in increasing their income and household welfare [12], impacting the inefficient allocation of resources and the ability to mitigate the risks [11]. Based on previous studies, farmers' risk aversion is influenced by various factors, such as age [2,15,44,47], education [2,15,44,47,48], farming experience [16,44], farm size [16,21,47], family size [16,21] and farmers' risk perception [16].
The research was conducted from October 2021 until March 2022. The research location was selected in West Kalimantan Province, as one of the main centers for rubber plantations in Indonesia, with contributions to land area and rubber production of 10.68% and 8.27%, respectively [22]. Furthermore, the implementation of rubber farming in this region has experienced various risks, causing low rubber productivity (960 kg/ha/year), which is lower than Indonesia's productivity (1,018 kg/ha/year) [60]. The risks of climate change, plant disease attacks and decreased rubber prices have resulted in low productivity in West Kalimantan [61].
The research location was selected using a multistage sampling technique. The first step is to determine the location of the district with the criteria for the main rubber production center in West Kalimantan, namely, in Sanggau, Sintang and Sambas districts, with contributions of 23.87%, 15.03%, and 6.64% of the total production, respectively [62]. The second step determines the subdistrict's site: Balai and Parindu in Sanggau district, Sepauk in Sintang district and Sajad in Sambas district (Figure 1). The selection of subdistricts considers the main area for rubber production in each district. In addition, the selected locations also have a Rubber Processing and Marketing Unit (RPMU), which helps farmers to improve rubber quality and acts as an intermediary for farmers to market rubber directly to factories. Next, in the third step, we select the sample using simple random sampling based on the proportional size of the rubber farmers' population in each subdistrict. The selected sample was 200 farmers (53 farmers in Balai, 49 in Sepauk, 50 in Parindu and 48 in Sajad).
Data collection was carried out by individual interviews with farmers using questionnaires that contain three main sections. Section 1 is about farmers and farm characteristics. Section 2 includes indicators to assess risk perceptions based on risk likelihood and consequences. Section 3 contains Holt and Laury's experiment to identify risk attitudes. The data included in the questionnaires (farmers, farm characteristics and indicators) were based on a literature review. The pretest questionnaire was conducted to test the validity and reliability using 30 samples, and the findings indicated that the instrument was valid and reliable.
The measurement of risk perception was carried out for climate change, plant disease and price change risks based on their likelihood and consequence using a Likert scale, as presented in Table 1. The likelihood category is based on the percentage of risk probability in rubber farming with a percentage of 0–100% and then divided by the number of classes. Consequence categories were based on the percentage of losses in yields due to risk, and the indicators were adopted from The World Bank's guidelines in agricultural risk assessment [7]. Following earlier studies from Akhtar et al. and Khan et al. [11,17], the next step of risk assessment is combining the two indicators using a risk matrix and determining the risk category (Figure 2). A risk matrix is compiled by placing the likelihood score on the vertical dimension and the consequence score on the horizontal dimension and then adding up the scores to get a total score of 2–10. The risk is low if the total score is 2–5 and high if the total score is 6–10 [2,11,17]. The total score was calculated for each farmer for each type of risk because farmers can have different perceptions of different risk types.
Likert scale | Likelihood category | Consequence category |
5 | Very often (risk probability ≥ 80%) | Very high (losses in yields ≥ 50 %) |
4 | Often (risk probability 60–80%) | High (losses in yields 30–50%) |
3 | Occasionally (risk probability 40–60%) | Middle (losses in yields 15–30%) |
2 | Rare (risk probability 20–40%) | Low (losses in yields 5–15%) |
1 | Very rare (Risk probability 0–20%) | Very low (losses in yields < 5%) |
Risk attitude analysis was conducted using Holt and Laury's experiments, and other researchers have widely used this method [12,47,63,64]. Experiments were designed explicitly by modifying the Holt and Laury method based on agricultural activities in the research area. Farmers were asked to select between two types of farming activities (A and B), as presented in Table 2. The A activity generates IDR 1,083,000 (highest income) and IDR 733,300 (lowest income), while the B activity generates IDR 1,616,700 (highest income) and IDR 366,700 (lowest income). Respondents were asked to choose between two options (choice A or B) 10 times in each scenario with a different income probability. The probability of generating the highest income increased from 0% to 100% (probability 1). In contrast, the probability of generating the lowest income decreased from 100% to 0% (probability 2).
Scenario | Probability 1 vs. Probability 2 |
Activity A (IDR) |
Activity B (IDR) |
Net expected value | CRRA ranges | Risk aversion class |
1 | 10% vs 90% | 1,083,000 vs 733,300 | 1,616,700 vs 366,700 | 276,600 | r < −2.06 | RL4 |
2 | 20% vs 80% | 1,083,000 vs 733,300 | 1,616,700 vs 366,700 | 186,600 | −2.06 < r ≤ −1.13 | RL3 |
3 | 30% vs 70% | 1,083,000 vs 733,300 | 1,616,700 vs 366,700 | 96,600 | −1.13 < r ≤ −0.53 | RL2 |
4 | 40% vs 60% | 1,083,000 vs 733,300 | 1,616,700 vs 366,700 | 6,600 | −0.53 < r ≤ −0.04 | RL1 |
5 | 50% vs 50% | 1,083,000 vs 733,300 | 1,616,700 vs 366,700 | −83,400 | −0.04 < r ≤ 0.41 | RN |
6 | 60% vs 40% | 1,083,000 vs 733,300 | 1,616,700 vs 366,700 | −173,400 | 0.41 < r ≤ 0.85 | RA1 |
7 | 70% vs 30% | 1,083,000 vs 733,300 | 1,616,700 vs 366,700 | −263,400 | 0.85 < r ≤ 1.32 | RA2 |
8 | 80% vs 20% | 1,083,000 vs 733,300 | 1,616,700 vs 366,700 | −353,400 | 1.32 < r ≤ 1.88 | RA3 |
9 | 90% vs 10% | 1,083,000 vs 733,300 | 1,616,700 vs 366,700 | −443,400 | 1.88 < r ≤ 2.72 | RA4 |
10 | 100% vs 0% | 1,083,000 vs 733,300 | 1,616,700 vs 366,700 | −533,400 | 2.72 < r | RA5 |
Source: Author's calculation. |
The net expected value of each respondent's choice was calculated as follows (equation 1):
Netexpectedvalue=2∑s=1P(As)As−2∑s=1P(Bs)Bs | (1) |
For each activity (A or B), s = 1 indicates the preferred condition with the highest income, and s = 2 indicates the unpreferred condition with the lowest income. Both options have high and low expected values, but activity B has a higher risk (variance) because the expected yield varies more than A. Therefore, the A activity is considered a relatively safe option, and the B activity is risky. The expectation of B activity increases relative to the A activity when the question continues to the following scenario. Furthermore, this experiment assumes constant relative risk aversion / CRRA (r), which was defined (equation 2) as follows [47,64]:
(x)=x1−r1−r | (2) |
The number of options in the A activity illustrates the risk attitude. Risk-taker farmers select the safe choice (the A activity) fewer than five times, whereas risk-averse farmers select the A activity more than five times. Risk-indifferent farmers will select the A activity five times and switch to riskier alternatives (the B activity) [53,64,65]. The questionnaires were visualized using colored images to make it easier for respondents to understand this experiment [63].
Following the previous study by Huong et al. [54] and focusing on the dichotomous dependent variable, this research applied the logit model to identify the determinant factors of farmers' risk perception and attitude. Based on Hosmer et al. [66], the logit model is written in equations 3 and 4:
Pi=E(Y=1|X)=11+e−(β0+βiXi)=11+e−Zi | (3) |
Zi=β0+β1X1+β2X2+⋯+βnXn+μi | (4) |
where Pi is the probability of farmers' risk perception and attitude, β0 is an intercept, and β1, β2 and βn are the estimated coefficients. X1, X2, … and Xn are explanatory variables, and µi is the error term. Logit analysis was carried out four times: risk perception analysis for three different types of risk (climate change, plant disease and price changes) and risk attitude analysis. This study uses independent variables adopted from previous studies (farmers' age, education, family size, farm experience, farm size) combined with characteristics of rubber farming (rubber age, rubber plantation distance and use of rubber clones). Because the model was derived from the logit distribution, it is precise to measure the impact of the independent variables on the outcome probability, called the marginal effects. The marginal effects are calculated in equation 5 [67]:
δE(Y|X)δX=eβ0+βiXiβi1+eβ0+βiXi(1−eβ0+βiXiβi1+eβ0+βiXi)=eβ0+βiXiβ1(1+eβ0+βiXi)2 | (5) |
The logit model was calculated using the maximum likelihood estimation and STATA 16 software. Before starting the analysis, we verified for multicollinearity using the Variance Inflation Factor and Tolerance test. The results showed that there was no multicollinearity in the model.
Table 3 presents the descriptive statistics of explanatory variables in this research. Farmers' and farm characteristics have important influences on the farmers' ability to assess and mitigate the risk [17]. In this study, farmers are in the productive age category (44 years), with a minimum of 25 years and a maximum of 75 years. Farmers' age generally affects their physical condition, mindset and ability to adopt technologies and innovations in farming activities. Farmers have an average of eight years of schooling (with a minimum of 2 years and a maximum of 17 years), but at least they can read, write and count, which can assist them in managing their farms. Farmers have an average experience of 17 years (with a minimum of 7 years and a maximum of 50 years). Even though farmers' education is relatively low, farmers have a high level of farming experience, which can help them to assess and mitigate the risks.
Variables | Description | Min | Max | Mean | Std. Dev. |
Farmers' and farm characteristics | |||||
Farmers' age | Age of farmer (years) | 25 | 75 | 43.85 | 9.17 |
Education | Formal education of farmer (years) | 2 | 17 | 8.2 | 2.43 |
Family size | Number of family members (persons) | 2 | 7 | 4.46 | 1.03 |
Farming experience | Farming experience (years) | 7 | 50 | 17.34 | 7.45 |
Rubber plantation size | Total rubber plantation area (hectares) | 1 | 3 | 1.49 | 0.50 |
Rubber age | Age of rubber trees (years) | 6 | 27 | 13.08 | 4.00 |
Distance (km) | The distance from the plantation to the village center (km) | 0.5 | 6 | 2.32 | 1.11 |
Use of rubber clone | 1 = apply rubber clone, 0 = otherwise | 0 | 1 | 0.76 | 0.43 |
Risk perception | |||||
Climate change | 1 = if perceived as high risk, 0 = otherwise | 0 | 1 | 0.81 | 0.40 |
Plant disease | 1 = if perceived as high risk, 0 = otherwise | 0 | 1 | 0.69 | 0.46 |
Price change | 1 = if perceived as high risk, 0 = otherwise | 0 | 1 | 0.75 | 0.43 |
Risk attitude | |||||
Risk aversion | 1 = risk averse, 0 = otherwise | 0 | 1 | 0.80 | 0.40 |
Source: Data analysis, 2022. |
In terms of farm size, farmers have an average of 1.49 hectares of rubber area (minimum of 1 hectare and maximum of 3 hectares), owned privately and managed by farmers and their household members. Farmers have an average of four family members (with a minimum of 2 persons and a maximum of 7 persons). If the family members were in productive age, they could be alternative labor for farming activities. Most farmers have rubber trees in their productive age of 10-20 years, with an average of 13 years, thereby giving farmers opportunities to increase rubber production and farm income. The mean distance from the rubber plantation to the village center was 2.32 km (with a minimum of 0.5 km and a maximum of 6 km). From the interview results, farmers tap the trees quite often (at least every two days and sometimes more), and the distance is more important in this situation. The long distance from the rubber plantation to the village center will make it difficult for farmers to maintain and tap the trees. Next, the study results indicated that most rubber farmers (76%) use rubber clones (PB 260), and the rest use local seeds. These results were similar to earlier research which stated that the use of cloned rubber in Indonesia is still low, resulting in lower productivity [68].
The farmers' risk perception results showed that most farmers perceive climate change, plant diseases and price changes as high risks, with percentages of 81%, 69% and 75%, respectively. The details of farmer risk perception based on the likelihood and consequence categories are presented in Figures 3 and 4. Regarding the risk of climate change, most farmers (48%) perceived the risk probability in the occasional category and the risk consequence in the middle category (48%). The probability response in the often-very often happens categories was 35.5%, and the response in the rare-very rare categories was 16.5%. In the risk consequence response, the response in the high-very high categories was 31%, and the response in the low-very low categories was 21%. This result shows that most farmers perceive climate change as an occasional-often risk with a middle-high impact on yield loss, and based on the risk matrix, this risk was categorized as high risk.
Regarding the risk of plant diseases, most farmers (42.5%) perceived the risk probability in the occasional category and the risk consequence in the middle category (39%). The probability response in the often-very often happens categories was 30.5%, and the response in the rare-very rare categories was 27%. In the risk consequence response, the response in the high-very high categories was 17.5%, and the response in the low-very low categories was 43.5%. This result shows that most farmers perceive plant diseases as an occasional-often risk but with a low-middle impact on yield loss. In the risk matrix, even though the risk has a low-middle impact on farming, if the risk probability is in the occasional-often category, then the risk is categorized as high risk.
Regarding the risk of price changes, most farmers (45%) responded to the risk probability in the occasional category and the risk consequence in the middle category (42.5%). The response in the probability categories of often or very often happens was 39%, and the response in the rarely-very rarely categories was 16%. In the risk impact category, the high-very high response was 25.5%, and the low-very low response was 32%. This result shows that most farmers perceive price changes as an occasional-often risk but with a low-middle impact on yield loss. Based on the risk matrix, this risk is categorized as high risk. Other findings in Holt and Laury's method showed that most rubber farmers were risk-averse (80%), only 5.5% were risk-loving, and the rest were risk-neutral (14.50%).
The logit model results in Tables 4 and 5 present the parameter estimates and marginal effects of the influences of farmers and farm characteristics on risk perceptions and attitudes. Marginal effects provide a more detailed discussion about the average effect of changes in independent variables on the change in the outcome probability. Based on the logit results, all ρ values were less than 0.000, meaning that the models are fit. In addition, Pseudo R-squared in the model ranges from 0.300 to 0.446, showing that the models are fit to clarify the risk perception and attitude.
Variable | Risk perception | Risk attitude | ||
Climate change | Plant disease | Price change | ||
Farmers' and farm characteristics | ||||
Farmers' age | 0.094**(0.042) | 0.116***(0.036) | 0.168***(0.044) | −0.195***(0.054) |
Education | −0.124 (0.097) | −0.139 (0.088) | 0.566***(0.130) | −0.174 (0.138) |
Family size | −0.481**(0.245) | 0.045 (0.204) | −1.108***(0.286) | 0.449 (0.330) |
Farming experience | −0.263***(0.058) | −0.170***(0.047) | −0.063 (0.048) | −0.026 (0.059) |
Rubber plantation size | −0.668 (0.490) | 1.137***(0.414) | −0.546 (0.479) | 0.338 (0.574) |
Rubber age | −0.090 (0.066) | 0.134**(0.066) | 0.173**(0.079) | 0.687***(0.137) |
Distance | 0.671*** (0.267) | 0.889***(0.220) | 0.717***(0.258) | 0.552** (0.277) |
Use of rubber clone | −0.218 (0.642) | −1.744***(0.631) | 1.672***(0.557) | −2.421***(0.852) |
Risk perception | ||||
Climate change | NA | NA | NA | −0.235 (0.953) |
Plant disease | −0.902 (0.646) | |||
Price change | 1.499**(0.617) | |||
Constant | 6.636***(2.179) | −3.985**(1.760) | −8.37***(2.137) | 2.105 (2.552) |
LR statistic (Prob) | 65.869*** | 74.326*** | 72.991*** | 89.313*** |
R-squared | 0.339 | 0.300 | 0.328 | 0.446 |
*** p < 0.01, ** p < 0.05, * p < 0.1, standard errors in parentheses. Source: Data analysis, 2022. |
Variable | Risk perception | Risk attitude | ||
Climate change | Plant disease | Price change | ||
Farmers' and farm characteristics | ||||
Farmers' age | 0.009**(0.004) | 0.016***(0.005) | 0.020***(0.005) | −0.017***(0.004) |
Education | −0.012 (0.009) | −0.019 (0.012) | 0.068***(0.013) | −0.015 (0.012) |
Family size | −0.048**(0.024) | 0.006 (0.029) | −0.133***(0.029) | 0.039 (0.028) |
Farming experience | −0.026***(0.005) | −0.024***(0.006) | −0.008 (0.006) | −0.002 (0.005) |
Rubber plantation size | −0.066 (0.048) | 0.161***(0.054) | −0.655 (0.057) | 0.029 (0.049) |
Rubber age | −0.009 (0.007) | 0.019**(0.009) | 0.021**(0.009) | 0.059***(0.008) |
Distance | 0.067*** (0.025) | 0.126***(0.026) | 0.086***(0.029) | 0.048**(0.023) |
Use of rubber clone | −0.021 (0.061) | −0.227***(0.065) | 0.222***(0.072) | −0.173***(0.044) |
Risk perception | ||||
Climate change | NA | NA | NA | −0.020 (0.078) |
Plant disease | −0.075 (0.050) | |||
Price change | 0.144**(0.062) | |||
*** p < 0.01, ** p < 0.05, * p < 0.1, standard errors in parentheses. Source: Data analysis, 2022. |
Farmers' age has a significant and positive effect on risk perceptions of climate change (p < 0.05), plant disease (p < 0.01) and price change (p < 0.01). The marginal effects show that a unit increase in the farmers' age will increase farmers' probabilities of perceiving climate change, plant diseases and price change as high risks by 0.9%, 1.6% and 2.0%, respectively. Farmers' education significantly affects price change risk perception (p < 0.01) but not that for climate change and plant disease. The marginal effects show that a unit increase in education will increase farmers' probability of perceiving price change as high risk by 6.8%. Regarding family size, the logit results found that this variable has a significant negative effect on risk perception of climate change (p < 0.05) and price change (p < 0.01) but not for plant disease. According to the marginal effects, a unit increase in family members will decrease the farmers' probabilities of perceiving climate change and price change as high risks by 4.8% and 13.3%, respectively.
In the case of farming experience, this variable has a negative effect on the risk perception of climate change (p < 0.01) and plant disease (p < 0.01). The marginal effects show that a unit increase in farming experience will decrease the farmers' probabilities of perceiving climate change and plant disease as high risks by 2.6% and 2.4%, respectively. Rubber plantation size positively affects the risk perception of plant disease (p < 0.01), and the marginal effects show that a unit increase in rubber area will increase the farmers' probability of perceiving plant disease as high risk by 16.1%. Rubber age positively affects the risk perception of plant disease (p < 0.05) and price change (p < 0.05). The marginal effects show that a unit increase in rubber age will increase farmers' probabilities of perceiving plant diseases and price change as high risks by 1.9% and 2.1%, respectively.
The distance from the rubber plantation to the village center positively affects all risk perceptions (p < 0.01), which means that farmers whose plantations are far from the village center tend to perceive climate change, plant diseases and price changes as high risks. The marginal effects show that a unit increase in rubber plantation distance will increase the farmer's probabilities of perceiving climate change, plant diseases and price change as high risks by 6.7%, 12.6% and 8.6%, respectively. The study results also indicated that using a rubber clone affects risk perception differently. This variable positively affects the price change risk perception (p < 0.01) but negatively affects that of plant disease (p < 0.01). The marginal effects show that if farmers use rubber clones, they will have a 22.2% higher probability of perceiving price change as high risk and a 22.7% lower probability of perceiving plant diseases as high risk.
Tables 4 and 5 also describe the determinant factors of farmers' risk attitudes. Farmers' age negatively affects risk aversion (p < 0.01), and the marginal effects show that a unit increase in farmers' age will decrease the probability of farmers' risk aversion by 1.7%. In the case of rubber age, this variable positively affects risk aversion (p < 0.01), and the marginal effects show that a unit increase in rubber age will increase the probability of farmers' risk aversion by 5.9%. The distance from the plantation to the village center positively affects risk aversion (p < 0.05). The marginal effects show that a unit increase in plantation distance to the village center will increase the probability of farmers' risk aversion by 4.8%.
In contrast, using rubber clones negatively affects risk aversion (p < 0.01). The marginal effects indicate that if farmers use rubber clones, the probability of their being risk-averse will decrease by 17.3%. Furthermore, the logit models also found that price change risk perception positively affects farmers' risk aversion (p < 0.05). The marginal effects indicate that if farmers perceive price change as high risk, they will have a 14.4% higher probability of being risk-averse.
Figure 5 shows the schematic framework to describe the research comprehensively. The results of parameters and marginal effects in the logit model are summarized in a flowchart. The left and right sides of the framework present the influence of rubber farmers' and farm characteristics on risk perception and attitude, respectively. The flowchart also shows the influence of risk perception on risk aversion. The black connectors in the flowchart indicate a positive effect on the variables, while the red connectors indicate a negative effect. The values in connector lines show the significance levels and marginal effects, and the value in square parentheses for each characteristic shows the variable's mean.
This research focuses on three main risks in rubber farming: climate change, plant diseases and price change. The study found that most rubber farmers perceived climate change, plant diseases and price change as high risks. The risk of climate change in rubber plantations is related to increased rainfall and rainy days, significantly affecting farming activities. The rainy season makes it difficult for farmers to tap latex, which reduces latex production. The main climatic factors that affect rubber tapping are rainfall intensity, quantity, time and duration [33]. Farmers typically tap the latex at dawn or very early in the morning. Farmers will delay the tapping if persistent and heavy rain occurs. If the rain occurs during tapping time, rainwater will fall onto the tree flow to the tree trunk and branches and then enter the tapping cup. The tapping results will be wasted since they are mixed with rainwater. If there is frequent rain in a certain period, it will significantly reduce rubber production. Ruangsri et al. and Sdoodee & Rongsawat [23,69] stated that increased rainfall and rainy days in Thailand cause decreases in tapping frequency and rubber productivity. Rubber farmers in Myanmar also experienced the negative impact of climate change on irregular tapping days, low productivity and high tapping cost [32].
Regarding rubber plant diseases, the majority of farmers perceived rubber diseases as high risk. Previous studies reported a severe attack of leaf fall disease, which decreased rubber production in Indonesia, Malaysia, India and Thailand [33,70]. Leaf fall disease also attacks rubber plantations in Latin America, causing repeated defoliation of rubber trees [34]. In Indonesia, leaf fall disease causes leaf drop of up to 75–90%, and rubber production decreases by 25–45% [36]. In addition, rubber trees are also susceptible to white root fungal disease that causes latex yield loss and tree death [71]. Previous research also reported the presence of this disease in several rubber-producing countries, including Malaysia [35,71] and Thailand [72].
Moreover, most rubber farmers also perceived price change as a high risk since it is related to the decline in output prices, which significantly impacts rubber farming. Rubber is an export commodity, and global market conditions influence the rubber price. The fluctuations in rubber prices have led to the vulnerability of rubber farmers' livelihoods in Thailand [38,42], China [29,37], Indonesia [73] and other rubber-producing countries. The decline in rubber prices has a multiplier effect on reduced income, farmers' investment ability, purchasing power and land conversion to more prospective crops [74]. Previous studies highlighted farmers' efforts to overcome the risk and reduce the dependence on rubber farming, for example, through income diversification [37,41,42].
The logit model found that farmers' and farm characteristics were important in shaping the ability of farmers to perceive the risks. Farmers' age and the distance from the plantation to the village center affect all risk perceptions (climate change, plant disease and price change). In the case of several other variables (education, family size, farming experience, rubber plantation size, rubber age and use of rubber clones), there are different findings. One variable can affect the perception of one type of risk but not affect another risk. Previous studies also reported different results regarding the effects of independent variables on different risk perceptions [11,15,54,75,76].
Our logit model found that farmers' age positively affects risk perception. The oldest farmers will perceive climate change, plant disease and price change as a high risk. This finding confirmed previous studies, which showed that farmers' age had a positive effect on the risk perception of climate change [11,43,77,78], plant disease [43] and price change [2,15,76,78]. Elderly farmers generally experience a decrease in physical ability in farming activities. Meanwhile, rubber farming requires more energy and time for tapping and plant maintenance [79]. In a risky situation, it will be more difficult for elderly farmers to run their farms. This is why farmers perceive climate change, plant diseases and price changes as major threats to their rubber farming.
The positive effect of farmers' education on risk perception means that educated farmers perceive price change as a high risk. The same result was similar to previous studies, which found that experienced farmers perceive price change as high risk [14,44]. Education is essential for farmers because it can increase farmers' insight, skills, managerial abilities and technology adoption [80,81,82]. Based on the survey results, most farmers have low education, which affects their ability to obtain information and technology related to agricultural activities. This variable had no significant effect on the risk perception of climate change and plant diseases. This could happen due to a lack of education, making it difficult for farmers to predict and mitigate the risks. Previous studies also reported different results regarding the effect of education on the different types of risk [11,76]. Since the farmers' formal education is relatively low, this study suggests developing and increasing informal education programs such as training and counseling to increase farmers' knowledge about farming management and risk mitigation.
Furthermore, the family size variable shows a negative effect on risk perception. Farmers with many family members perceive climate and price changes as low risk. A case study in Pakistan also identified the negative effect of family size on risk perception of climate change and price change [2]. Based on our survey, most farmers use family labor (wife, son or other family members) to carry out activities on the rubber plantation: for example, to maintain and tap the rubber. Farmers can save production costs by using labor families, which makes them perceive the climate and price changes as low risk. Research from Tongkaemkaew & Chambon [83] showed the same result, stating that family members are the primary source of labor in smallholder rubber plantations.
Regarding farming experience, this variable has a negative effect on the risk perception of climate change and plant disease, which means that experienced farmers perceived climate change and plant disease as low risk. This result is consistent with previous studies, which stated that experienced farmers show a low-risk perception of climate change [11,56] and plant disease [11,76,78]. In general, experienced farmers can predict the probability of climate change, know the plant disease symptoms, prevent and control the disease and overcome the risk impact. Experienced farmers can also determine the right time to tap during the rainy season and can minimize the possibility of latex mixing with water during the rainy season. On the other hand, this variable does not affect price change risk perception because the rubber price depends on global market prices. Most farmers also sell their rubber through collectors, which makes them not have a bargaining position. The results aligned with previous studies stated that farming experience affects the risk perception of climate change and plant diseases but does not affect the risk perception of price change [56].
The logit analysis also revealed that the rubber plantation area positively affects the risk perception of plant disease. The rubber plant diseases such as leaf fall disease and white root fungus result in decreased latex production [36,71]. Larger farm areas make it difficult for farmers to perform more intensive farm maintenance, making them perceive plant diseases as a high risk. Furthermore, the high costs that farmers must incur to prevent and control rubber plant diseases are the main obstacle to overcoming this risk [35].
Regarding the age of rubber trees, this variable positively affects the risk perception of plant disease and price change. Farmers consider plant disease a high risk since old rubber trees are more prone to disease and produce less latex, mainly after the productive age (20 years) [84]. Furthermore, the decline in production and rubber price will decrease farm income, leading farmers to perceive price changes as a high risk. In contrast, the rubber age has no significant effect on climate change risk. Climate change affects rubber plants throughout their growth period. The rainy season affects farmers' activities in maintaining trees, clearing weeds and tapping [23,33,69].
The distance from the rubber plantation to the village center positively affects risk perceptions. Farmers whose plantations are far from the village center tend to perceive climate change, plant diseases and price changes as high risks. Previous research also found the positive effects of farm distance to the city on risk perception of climate change [15], price change [14,15,44,76] and plant disease [2]. Generally, the village center is the primary location for providing input facilities, marketing and a place to access information. It is difficult for the farmers to perform farm maintenance, tap and transport the rubber to the collector if the farm is far from the village center. Similarly, Akhtar et al. and Iqbal et al. [11,15] stated that farmers near the village center could better access information and communicate more efficiently with input sub-dealers or collectors.
The study results indicated that using a rubber clone affects risk perception differently. This variable positively affects price change risk perception but negatively affects that of plant disease. Adopting rubber clones requires more farm maintenance and inputs than local seeds. Hence, farmers feel difficulties when the output price decreases. On the contrary, farmers who use rubber clones perceived plant disease as low risk because rubber clones are more resistant to disease than the local ones. A similar previous study also stated the potential high production and resistance to disease as advantages of rubber clones [39,68,85].
Based on Holt and Laury's experimental method, we can conclude that most farmers were risk-averse. Farming activities vulnerable to uncertainty are the main reason for farmers' risk aversion. Ouattara et al. [86] stated that under conditions of uncertainty, risk-averse farmers tend to reduce their land allocation for perennial crops and switch to annual crops. In line with this research, Djanibekov & Villamor stated that the higher the farmer's risk aversion, the larger the rubber agroforestry area [87]. Furthermore, Moser & Mubhoff's research found that rubber farmers in Indonesia were risk averse, influencing farmers' decision to use inputs such as fertilizer and herbicide [63]. Risk-averse farmers make production and management decisions that are less risky and with lower returns [21].
Regarding farmers' risk attitude, we found that age has a negative effect on risk aversion, which means that older farmers were less risk-averse. In other words, older farmers are more willing to take risks than young farmers. This might happen due to their confidence and desire to manage their farming activities. The same results were also relevant for farmers in Pakistan [2,15,75]. The variable of rubber age had a positive effect on risk aversion, which means that increasing the rubber age will make farmers more risk averse. Typically, rubber trees start to produce at five years [61]. However, in the case of smallholder farmers with limited input, rubber trees are rarely tapped before seven years. Rubber trees can reach optimal production at 15-20 years, and the production will decrease after 20 years. This condition decreases farm income and makes the farmers more risk-averse. Farmers can increase production by replanting rubber trees older than 30 by using rubber clones. Rubber tree replanting could maintain the productivity of natural rubber by substituting unproductive trees with productive rubber trees [88,89].
The distance from the plantation to the village center positively affected risk aversion, indicating that the location of the plantation being far from the village center will increase farmers' risk aversion. The remote area of the farm will make it difficult for the farmers to carry out farming activities (fertilization, farm maintenance and tapping). It will require additional transportation costs, thus making farmers more risk-averse. Previous research also stated that the farm's distance from the city positively affects risk-averse attitudes [78].
Regarding rubber clones, the results also found that this variable had a negative effect on risk aversion. Farmers who adopt rubber clones are less risk-averse than farmers who use local ones because rubber clones have higher production potential and income. Farmers who use rubber clones show a more adaptive attitude toward innovation and technology, which can encourage the farmers to increase production and income. In the research location, farmers adopted the PB 260 clone. This clone shows the best performance among other clones even in low input conditions, provides more latex and increases rubber productivity [68,85,89]. Given the importance of using rubber clones, this research suggests that the government can develop and reproduce rubber clones and provide motivation and assistance to farmers in using rubber clones [26].
The price change risk perception positively affected farmers' risk aversion. Farmers who perceive price change as high risk will be more risk-averse. The decline in global rubber prices for several years has reduced rubber production and farm incomes. As a result, farmers will perceive price changes as high risk, making them more risk-averse. Previous research conducted by Saqib et al. [16] confirmed this finding, stating that farmers with high-risk perceptions were more risk-averse than farmers with low-risk perceptions.
This study had several limitations. First, this study was based mainly on survey results, perceptions, experimental methods and interviews. Farmers' answers depend on how they understand the questionnaires, which may influence the responses. Second, this study was conducted in West Kalimantan, Indonesia. Studies in other regions in Indonesia with different geographical areas or planting systems will improve the study results. Third, the proposed model could be enhanced for future research in several ways: 1) by adding data regarding farmers' strategies to minimize and mitigate the risks; 2) by adding other explanatory variables which could influence farmers' risk perception and risk attitudes, such as ethnic group and geographical area; 3) by exploring other possible types of risk which have a severe impact in rubber farming, such as financial risk and institutional risk.
These study results are valid for smallholder rubber farmers in West Kalimantan Province. However, it may be interesting to study if similar results would be found in other regions of Indonesia and other rubber-producer countries. Based on the risk likelihood and consequence combination, the study results indicated that most rubber farmers perceive climate change, plant disease and price change as high risks. The study also found that most rubber farmers were risk-averse. Logit model estimation found that all models fit, and most of the farmers' and farms' characteristics were significant. Farmers' age, education, rubber plantation size, rubber age, distance from the plantation to the village center and rubber clones positively affected risk perceptions, while family size and farming experience had a negative effect. Regarding risk attitude, the variables of rubber age, distance from the plantation to the village center and price change risk perception positively affected farmers' risk aversion. In contrast, farmers' age and the use of rubber clones had a negative effect.
The study results are important for policymakers, because they consider socio-economic characteristics, risk perceptions and risk attitudes, to develop appropriate policies to help farmers mitigate the risks: for example, increasing informal education programs such as training and counseling. The government and stakeholders can motivate and enable farmers to replant old/damaged rubber trees using rubber clones with higher yield potential and more disease resistance. Additionally, to facilitate farming activities, it is necessary to improve communication, transportation access and road facilities and infrastructure.
We are grateful for the PhD fellowship offered by the Indonesian Ministry of Education, Culture, Research, and Technology. We also want to thank the anonymous reviewers for their suggestions and insightful remarks.
The authors state no conflict of interest in this research.
[1] |
S. M. Iveson, J. D. Litster, K. Hapgood, B. J. Ennis, Nucleation, growth and breakage phenomena in agitated wet granulation processes: A review, Powder Technol., 117 (2001), 3–39. https://doi.org/10.1016/S0032-5910(01)00313-8 doi: 10.1016/S0032-5910(01)00313-8
![]() |
[2] |
S. V. Moraga, M. P. Villa, D. E. Bertín, I. M. Cotabarren, J. Piña, M. Pedernera, et al., Fluidized-bed melt granulation: The effect of operating variables on process performance and granule properties, Powder Technol., 286 (2015), 654–667. https://doi.org/10.1016/j.powtec.2015.09.006 doi: 10.1016/j.powtec.2015.09.006
![]() |
[3] |
G. Strenzke, R. Dürr, A. Bück, E. Tsotsas, Influence of operating parameters on process behavior and product quality in continuous spray fluidized bed agglomeration, Powder Technol., 375 (2020), 210–220. https://doi.org/10.1016/j.powtec.2020.07.083 doi: 10.1016/j.powtec.2020.07.083
![]() |
[4] |
H. Aziz, S. N. Ahsan, G. De Simone, Y. J. Gao, B. Chaudhuri, Computational modeling of drying of pharmaceutical wet granules in a fluidized bed dryer using coupled CFD-DEM approach, AAPS PharmSciTech, 59 (2022). https://doi.org/10.1208/s12249-021-02180-x doi: 10.1208/s12249-021-02180-x
![]() |
[5] |
K. Vorlander, L. Bahlmann, A. Kwade, J. H. Finke, I. Kampen, Effect of process parameters, protectants and carrier materials on the survival of yeast cells during fluidized bed granulation for tableting, Pharmaceutics, 15 (2023), 884. https://doi.org/10.3390/pharmaceutics15030884 doi: 10.3390/pharmaceutics15030884
![]() |
[6] | ICH Harmonised Tripartite Guideline Pharmaceutical Development Q8 R2 Guideline; ICH: Geneva, Switzerland, 2009, 1–24. |
[7] |
F. Sun, B. Xu, S. Dai, Y. Zhang, Z. Lin, Y. Qiao, A novel framework to aid the development of design space across multi-unit operation pharmaceutical processes—A case study of panax notoginseng saponins immediate release tablet, Pharmaceutics, 11 (2019), 474. https://doi.org/10.3390/pharmaceutics11090474 doi: 10.3390/pharmaceutics11090474
![]() |
[8] |
L. S. Ming, Z. Li, F. Wu, R. F. Du, Y. Feng, A two-step approach for fluidized bed granulation in pharmaceutical processing: Assessing different models for design and control, PloS One, 12 (2017). https://doi.org/10.1371/journal.pone.0180209 doi: 10.1371/journal.pone.0180209
![]() |
[9] |
J. Krzywanski, D. Urbaniak, H. Otwinowski, T. Wylecial, M. Sosnowski, Fluidized bed jet milling process optimized for mass and particle size with a fuzzy logic approach, Materials, 13 (2020), 3303. https://doi.org/10.3390/ma13153303 doi: 10.3390/ma13153303
![]() |
[10] |
M. Sen, D. Barrasso, R. Singh, R. Ramachandran, A multi-scale hybrid CFD-DEM-PBM description of a fluid-bed granulation process, Processes, 2 (2014), 89–111. https://doi.org/10.3390/pr2010089 doi: 10.3390/pr2010089
![]() |
[11] |
H. Aoki, Y. Hattori, T. Sasaki, M. Otsuka, Comparative study on the real-time monitoring of a fluid bed drying process of extruded granules using near-infrared spectroscopy and audible acoustic emission, Int. J. Pharm., 619 (2022), 121689. https://doi.org/10.1016/j.ijpharm.2022.121689 doi: 10.1016/j.ijpharm.2022.121689
![]() |
[12] |
M. Nadda, S. K. Shah, S. Roy, A. Yadav, CFD-based deep neural networks (DNN) model for predicting the hydrodynamics of fluidized beds, Digit. Chem. Eng., 8 (2023), 100113. https://doi.org/10.1016/j.dche.2023.100113 doi: 10.1016/j.dche.2023.100113
![]() |
[13] |
A. Tamrakar, R. Ramachandran, CFD-DEM-PBM coupled model development and validation of a 3D top-spray fluidized bed wet granulation process, Chem. Eng. Sci., 125 (2019), 249–270. https://doi.org/10.1016/j.compchemeng.2019.01.023 doi: 10.1016/j.compchemeng.2019.01.023
![]() |
[14] |
S. V. Muddu, A. Tamrakar, P. Pandey, R. Ramachandran, Model development and validation of fluid bed wet granulation with dry binder addition using a population balance model methodology, Processes, 6 (2018), 154. https://doi.org/10.3390/pr6090154 doi: 10.3390/pr6090154
![]() |
[15] |
K. K. Win, W. Nowak, H. Matsuda, M. Hasatani, Z. Bis, J. Krzywanski, et al., Transport velocity of coarse particles in multi-solid fluidized bed, JCEJ, 28 (1995), 535–540. https://doi.org/10.1252/jcej.28.535 doi: 10.1252/jcej.28.535
![]() |
[16] |
J. Liu, T. Liu, G. Mu, J. Chen, Wavelet based calibration model building of NIR spectroscopy for in-situ measurement of granule moisture content during fluidized bed drying, Chem. Eng. Sci., 226 (2020), 115867. https://doi.org/10.1016/j.ces.2020.115867 doi: 10.1016/j.ces.2020.115867
![]() |
[17] |
R. F. Nascimento, M. F. Ávila, A. G. P. da Silva, O. P. Taranto, L. E. Kurozawa, The formation of solid bridges during agglomeration in a fluidized bed: Investigation by Raman spectroscopy and image analyses, Powder Technol., 420 (2023), 118377. https://doi.org/10.1016/j.powtec.2023.118377 doi: 10.1016/j.powtec.2023.118377
![]() |
[18] |
H. Otwinowski, J. Krzywanski, D. Urbaniak, T. Wylecial, M. Sosnowski, Comprehensive knowledge-driven ai system for air classification process, Materials, 15 (2021), 45. https://doi.org/10.3390/ma15010045 doi: 10.3390/ma15010045
![]() |
[19] |
V. Todaro, A. M, Healy Development and characterization of ibuprofen co-crystals granules prepared via fluidized bed granulation in a one-step process–A design of experiment approach, Drug Dev. Ind. Pharm., 47 (2021), 292–301. https://doi.org/10.1080/03639045.2021.1879836 doi: 10.1080/03639045.2021.1879836
![]() |
[20] |
K. Kramm, M. Orth, A. Teiwes, J. C. Kammerhofer, V. Meunier, S. Pietsch‐Braune, et al., Influence of nozzle parameters on spray pattern and droplet characteristics for a two‐fluid nozzle, Chem. Ing. Tech., 95 (2023), 151–159. https://doi.org/10.1002/cite.202200152 doi: 10.1002/cite.202200152
![]() |
[21] |
R. Xue, Y. Ruan, X. Liu, L. Chen, X. Zhang, Y. Hou, et al., Experimental study of liquid nitrogen spray characteristics in atmospheric environment, Appl. Therm. Eng., 142 (2018), 717–722. https://doi.org/10.1016/j.applthermaleng.2018.07.056 doi: 10.1016/j.applthermaleng.2018.07.056
![]() |
[22] |
P. D. Hede, P. Bach, A. D. Jensen Two-fluid spray atomisation and pneumatic nozzles for fluid bed coating/agglomeration purposes: A review, Chem. Eng. Sci., 63 (2008), 3821–3842. https://doi.org/10.1016/j.ces.2008.04.014 doi: 10.1016/j.ces.2008.04.014
![]() |
[23] | C. Vesvey, J. Cronlein, A. Breuer, S. Gerstner, Fluid bed nozzle spray characterization of an aqueous ethylcellulose dispersion for particle taste-masking applications, AAPS Poster Reprint, (2014), 3–6. |
[24] |
R. Zhang, T. Hoffmann, E. Tsotsas, Novel technique for coating of fine particles using fluidized bed and aerosol atomizer, Processes, 8 (2020), 1525. https://doi.org/10.3390/pr8121525 doi: 10.3390/pr8121525
![]() |
[25] |
M. Orth, P. Kieckhefen, S. Pietsch, S. Heinrich, Correlating granule surface structure morphology and process conditions in fluidized bed layering spray granulation, KONA Powder Part. J., 39 (2022), 230–239. https://doi.org/10.14356/kona.2022016 doi: 10.14356/kona.2022016
![]() |
[26] |
R. Maharjan, S. H. Jeong Application of different models to evaluate the key factors of fluidized bed layering granulation and their influence on granule characteristics, Powder Technol., 408 (2022), 117737. https://doi.org/10.1016/j.powtec.2022.117737 doi: 10.1016/j.powtec.2022.117737
![]() |
[27] |
B. Düsenberg, A. K. Singh, J. Schmidt, A. Bück, Spray agglomeration of polymer particles: Influence of spray parameters on shape factors, Powder Technol., 422 (2023), 118491. https://doi.org/10.1016/j.powtec.2023.118491 doi: 10.1016/j.powtec.2023.118491
![]() |
[28] |
J. Tang, D. Chen, R. Wang, Study on the bed collapse in the shaping process of Shenmai granules, Pharm. Care Res., 21 (2020), 23–25. https://doi.org/10.5428/pcar20210105 doi: 10.5428/pcar20210105
![]() |
[29] |
P. Stähle, V. Gaukel, H. P. Schuchmann, Influence of feed viscosity on the two-phase flow inside the exit orifice of an effervescent atomizer and on resulting spray characteristics, Food Res. Int., 77 (2015), 55–62. https://doi.org/10.1016/j.foodres.2015.04.047 doi: 10.1016/j.foodres.2015.04.047
![]() |
[30] |
I. M. Andersson, M. Glantz, M. Alexander, A. Millqvist-Fureby, M. Paulsson, B. Bergenståhl, Impact of surface properties on morphology of spray-dried milk serum protein/lactose systems, Int. Dairy J., 85 (2018), 86–95. https://doi.org/10.1016/j.idairyj.2018.04.011 doi: 10.1016/j.idairyj.2018.04.011
![]() |
[31] |
M. Hemati, R. Cherif, K. Saleh, V. Pont. Fluidized bed coating and granulation: influence of process-related variables and physicochemical properties on the growth kinetics, Powder Technol., 130 (2003), 18–34. https://doi.org/10.1016/S0032-5910(02)00221-8 doi: 10.1016/S0032-5910(02)00221-8
![]() |
[32] |
T. Y. Du, J. C. Xu, S. N. Zhu, X. J. Yao, J. Guo, W. Q. Lv, Effects of spray drying, freeze drying, and vacuum drying on physicochemical and nutritional properties of protein peptide powder from salted duck egg white, Front. Nutr., 9 (2022). https://doi.org/10.3389/fnut.2022.1026903 doi: 10.3389/fnut.2022.1026903
![]() |
[33] |
Q. L. Shi, Z. X. Fang, B. Bhandari, Effect of addition of whey protein isolate on spray-drying behavior of honey with maltodextrin as a carrier material, Dry. Technol., 31 (2013), 1681–1692. https://doi.org/10.1080/07373937.2013.783593 doi: 10.1080/07373937.2013.783593
![]() |
[34] |
A. C. Karaca, O. Guzel, M. M. Ak, Effects of processing conditions and formulation on spray drying of sour cherry juice concentrate, J. Sci. Food Agric., 96 (2016), 449–455. https://doi.org/10.1002/jsfa.7110 doi: 10.1002/jsfa.7110
![]() |
[35] |
H. Cheng, C. H. Lu, G. F. Xu, L. J. Zhao, M. Lu, Y. J. Wang, Optimization of spray-drying process parameters to study anti-sticking effect of hydroxypropyl methyl cellulose-VLV on corni fructus extracts, AAPS PharmSciTech, 23 (2022). https://doi.org/10.1208/s12249-022-02215-x doi: 10.1208/s12249-022-02215-x
![]() |
[36] |
J. Zeng, L. S. Ming, J. M. Wang, T. Huang, B. B. Liu, L. L. Feng, et al., Empirical prediction model-based process optimization for droplet size and spraying angle during pharmaceutical fluidized bed granulation, Pharm. Devt. Technol., 25 (2020), 720–728. https://doi.org/10.1080/10837450.2020.1738461 doi: 10.1080/10837450.2020.1738461
![]() |
[37] | H. Liu, Q. Zhang, J. Wang, J. Wu, H. Cui, Determination of six main components of organic acids in eight medicines by HPLC, J. Chin. Med. Mater., 40 (2017), 1130–1133. |
[38] | H. Qu, C. Feng, M. Xie, J. Zhu, Y. Sun, P. Cui, et al., Effect of different processing methods on the content of polygahatous polysaccharides, J. Hunan Univ. CM, 35 (2015), 53–55. |
[39] |
G. Shanmugasundar, M. Vanitha, R. Čep, V. Kumar, K. Kalita, M. Ramachandran, A comparative study of linear, random forest and adaboost regressions for modeling non-traditional machining, Processes, 9 (2021), 2015. https://doi.org/10.3390/pr9112015 doi: 10.3390/pr9112015
![]() |
[40] |
R. García-Carretero, R. Holgado-Cuadrado, Ó. Barquero-Pérez, Assessment of classification models and relevant features on nonalcoholic steatohepatitis using random forest, Entropy, 23 (2021), 763. https://doi.org/10.3390/e23060763 doi: 10.3390/e23060763
![]() |
[41] |
L. W. Li, Y. P. Wu, Y. P. Huang, B. Li, M. F. S.Miao, Z. Q. Deng, Optimized apriori algorithm for deformation response analysis of landslide hazards, Comput. Geosci., 170 (2023), 105261. https://doi.org/10.1016/j.cageo.2022.105261 doi: 10.1016/j.cageo.2022.105261
![]() |
[42] |
Y. J. Wang, Y. L. Xie, D. S. Xu, X. Lin, Y. Feng, Y. L. Hong, Hydroxypropyl methylcellulose reduces particle adhesion and improves recovery of herbal extracts during spray drying of Chinese herbal medicines, Dry. Technol., 32 (2014), 557–566. https://doi.org/10.1080/07373937.2013.843543 doi: 10.1080/07373937.2013.843543
![]() |
[43] |
C. Avilés-Avilés, E. Dumoulin, C. Turchiuli, Fluidised bed agglomeration of particles with different glass transition temperatures, Powder Technol., 270 (2015), 445–452. https://doi.org/10.1016/j.powtec.2014.03.026 doi: 10.1016/j.powtec.2014.03.026
![]() |
[44] |
M. B. Braga, S. C. D. Rocha, M. D. Hubinger, Spray-Drying of milk-blackberry pulp mixture: Effect of carrier agent on the physical properties of powder, water sorption, and glass transition temperature, J. Food Sci., 83 (2018), 1650–1659. https://doi.org/10.1111/1750-3841.14187 doi: 10.1111/1750-3841.14187
![]() |
[45] |
P. D. Liu, J. X. Li, C. H. Lu, L. J. Zhao, X. Lin, Y. J. Wang, et al., Data mining-based detection of the physical and chemical characteristics of Chinese medical herbs aqueous decoction in spray drying yield, Dry. Technol., 39 (2021), 896–904. https://doi.org/10.1080/07373937.2020.1728304 doi: 10.1080/07373937.2020.1728304
![]() |
[46] |
S. Jafari, S. M. Jafari, M. Ebrahimi, I. Kijpatanasilp, K. Assatarakul, A decade overview and prospect of spray drying encapsulation of bioactives from fruit products: Characterization, food application and in vitro gastrointestinal digestion, Food Hydrocoll, 134 (2023). https://doi.org/10.1016/j.foodhyd.2022.108068 doi: 10.1016/j.foodhyd.2022.108068
![]() |
[47] |
Z. X. Fang, B. Bhandari, Comparing the efficiency of protein and maltodextrin on spray drying of bayberry juice, Food Res. Int., 48(2012), 478–483. https://doi.org/10.1016/j.foodres.2012.05.025 doi: 10.1016/j.foodres.2012.05.025
![]() |
[48] |
R. T. Hoskin, M. H. Grace, J. Xiong, M. A. Lila, Spray-drying microencapsulation of blackcurrant and cocoa polyphenols using underexplored plant-based protein sources, J. Food Sci., 88 (2023), 2665–2678. https://doi.org/10.1111/1750-3841.16590 doi: 10.1111/1750-3841.16590
![]() |
1. | Md. Shakhawat Hossain, Assessing smallholder farmers’ flood risk behavior and their willingness to pay for crop insurance as a risk coping strategy in northern Bangladesh, 2024, 0921-030X, 10.1007/s11069-024-06958-7 | |
2. | Olha Aleksandrova, Imre Fertő, Ants-Hannes Viira, Investments, subsidies and financial constraints in Estonian agriculture, 2023, 83, 0002-1466, 597, 10.1108/AFR-10-2022-0132 | |
3. | Salsabila Aulia Rahmadani, Jangkung Handoyo Mulyo, Muh Amat Nasir, A. Sudarmaji, R. Naila Khusna Syarifah, L. Na'imatul Bayyinah, H. Rahayuani Ratnaningsih, Z. Az Zahroh, W. Hidayati, Shallot Production Risk: Case Study in Gunungkidul Region Yogyakarta Province, 2025, 158, 2117-4458, 02003, 10.1051/bioconf/202515802003 | |
4. | Masahiko Ota, Lina Fatayati Syarifa, Aprizal Alamsyah, Iman Satra Nugraha, Hajar Asywadi, Retno Lestari, Sanya Khaerunnisa, Achmad Eka Satria, Tri Rapani Febbiyanti, Socioeconomic effects of Pestalotiopsis rubber leaf fall disease on smallholders in South Sumatra, Indonesia, 2025, 7, 2675-1240, 2025371, 10.31893/multiscience.2025371 | |
5. | David Colozza, Isabella Guo, Sri Wahyuni Sukotjo, Astrid Citra Padmita, Rene Gerard Galera, Endang Sulastri, Inti Wikanestri, Mamadou Ndiaye, The impact of climate change on child nutrition in Indonesia: a conceptual framework and scoping review of the available evidence, 2025, 9, 2399-9772, e002980, 10.1136/bmjpo-2024-002980 |
Likert scale | Likelihood category | Consequence category |
5 | Very often (risk probability ≥ 80%) | Very high (losses in yields ≥ 50 %) |
4 | Often (risk probability 60–80%) | High (losses in yields 30–50%) |
3 | Occasionally (risk probability 40–60%) | Middle (losses in yields 15–30%) |
2 | Rare (risk probability 20–40%) | Low (losses in yields 5–15%) |
1 | Very rare (Risk probability 0–20%) | Very low (losses in yields < 5%) |
Scenario | Probability 1 vs. Probability 2 |
Activity A (IDR) |
Activity B (IDR) |
Net expected value | CRRA ranges | Risk aversion class |
1 | 10% vs 90% | 1,083,000 vs 733,300 | 1,616,700 vs 366,700 | 276,600 | r < −2.06 | RL4 |
2 | 20% vs 80% | 1,083,000 vs 733,300 | 1,616,700 vs 366,700 | 186,600 | −2.06 < r ≤ −1.13 | RL3 |
3 | 30% vs 70% | 1,083,000 vs 733,300 | 1,616,700 vs 366,700 | 96,600 | −1.13 < r ≤ −0.53 | RL2 |
4 | 40% vs 60% | 1,083,000 vs 733,300 | 1,616,700 vs 366,700 | 6,600 | −0.53 < r ≤ −0.04 | RL1 |
5 | 50% vs 50% | 1,083,000 vs 733,300 | 1,616,700 vs 366,700 | −83,400 | −0.04 < r ≤ 0.41 | RN |
6 | 60% vs 40% | 1,083,000 vs 733,300 | 1,616,700 vs 366,700 | −173,400 | 0.41 < r ≤ 0.85 | RA1 |
7 | 70% vs 30% | 1,083,000 vs 733,300 | 1,616,700 vs 366,700 | −263,400 | 0.85 < r ≤ 1.32 | RA2 |
8 | 80% vs 20% | 1,083,000 vs 733,300 | 1,616,700 vs 366,700 | −353,400 | 1.32 < r ≤ 1.88 | RA3 |
9 | 90% vs 10% | 1,083,000 vs 733,300 | 1,616,700 vs 366,700 | −443,400 | 1.88 < r ≤ 2.72 | RA4 |
10 | 100% vs 0% | 1,083,000 vs 733,300 | 1,616,700 vs 366,700 | −533,400 | 2.72 < r | RA5 |
Source: Author's calculation. |
Variables | Description | Min | Max | Mean | Std. Dev. |
Farmers' and farm characteristics | |||||
Farmers' age | Age of farmer (years) | 25 | 75 | 43.85 | 9.17 |
Education | Formal education of farmer (years) | 2 | 17 | 8.2 | 2.43 |
Family size | Number of family members (persons) | 2 | 7 | 4.46 | 1.03 |
Farming experience | Farming experience (years) | 7 | 50 | 17.34 | 7.45 |
Rubber plantation size | Total rubber plantation area (hectares) | 1 | 3 | 1.49 | 0.50 |
Rubber age | Age of rubber trees (years) | 6 | 27 | 13.08 | 4.00 |
Distance (km) | The distance from the plantation to the village center (km) | 0.5 | 6 | 2.32 | 1.11 |
Use of rubber clone | 1 = apply rubber clone, 0 = otherwise | 0 | 1 | 0.76 | 0.43 |
Risk perception | |||||
Climate change | 1 = if perceived as high risk, 0 = otherwise | 0 | 1 | 0.81 | 0.40 |
Plant disease | 1 = if perceived as high risk, 0 = otherwise | 0 | 1 | 0.69 | 0.46 |
Price change | 1 = if perceived as high risk, 0 = otherwise | 0 | 1 | 0.75 | 0.43 |
Risk attitude | |||||
Risk aversion | 1 = risk averse, 0 = otherwise | 0 | 1 | 0.80 | 0.40 |
Source: Data analysis, 2022. |
Variable | Risk perception | Risk attitude | ||
Climate change | Plant disease | Price change | ||
Farmers' and farm characteristics | ||||
Farmers' age | 0.094**(0.042) | 0.116***(0.036) | 0.168***(0.044) | −0.195***(0.054) |
Education | −0.124 (0.097) | −0.139 (0.088) | 0.566***(0.130) | −0.174 (0.138) |
Family size | −0.481**(0.245) | 0.045 (0.204) | −1.108***(0.286) | 0.449 (0.330) |
Farming experience | −0.263***(0.058) | −0.170***(0.047) | −0.063 (0.048) | −0.026 (0.059) |
Rubber plantation size | −0.668 (0.490) | 1.137***(0.414) | −0.546 (0.479) | 0.338 (0.574) |
Rubber age | −0.090 (0.066) | 0.134**(0.066) | 0.173**(0.079) | 0.687***(0.137) |
Distance | 0.671*** (0.267) | 0.889***(0.220) | 0.717***(0.258) | 0.552** (0.277) |
Use of rubber clone | −0.218 (0.642) | −1.744***(0.631) | 1.672***(0.557) | −2.421***(0.852) |
Risk perception | ||||
Climate change | NA | NA | NA | −0.235 (0.953) |
Plant disease | −0.902 (0.646) | |||
Price change | 1.499**(0.617) | |||
Constant | 6.636***(2.179) | −3.985**(1.760) | −8.37***(2.137) | 2.105 (2.552) |
LR statistic (Prob) | 65.869*** | 74.326*** | 72.991*** | 89.313*** |
R-squared | 0.339 | 0.300 | 0.328 | 0.446 |
*** p < 0.01, ** p < 0.05, * p < 0.1, standard errors in parentheses. Source: Data analysis, 2022. |
Variable | Risk perception | Risk attitude | ||
Climate change | Plant disease | Price change | ||
Farmers' and farm characteristics | ||||
Farmers' age | 0.009**(0.004) | 0.016***(0.005) | 0.020***(0.005) | −0.017***(0.004) |
Education | −0.012 (0.009) | −0.019 (0.012) | 0.068***(0.013) | −0.015 (0.012) |
Family size | −0.048**(0.024) | 0.006 (0.029) | −0.133***(0.029) | 0.039 (0.028) |
Farming experience | −0.026***(0.005) | −0.024***(0.006) | −0.008 (0.006) | −0.002 (0.005) |
Rubber plantation size | −0.066 (0.048) | 0.161***(0.054) | −0.655 (0.057) | 0.029 (0.049) |
Rubber age | −0.009 (0.007) | 0.019**(0.009) | 0.021**(0.009) | 0.059***(0.008) |
Distance | 0.067*** (0.025) | 0.126***(0.026) | 0.086***(0.029) | 0.048**(0.023) |
Use of rubber clone | −0.021 (0.061) | −0.227***(0.065) | 0.222***(0.072) | −0.173***(0.044) |
Risk perception | ||||
Climate change | NA | NA | NA | −0.020 (0.078) |
Plant disease | −0.075 (0.050) | |||
Price change | 0.144**(0.062) | |||
*** p < 0.01, ** p < 0.05, * p < 0.1, standard errors in parentheses. Source: Data analysis, 2022. |
Likert scale | Likelihood category | Consequence category |
5 | Very often (risk probability ≥ 80%) | Very high (losses in yields ≥ 50 %) |
4 | Often (risk probability 60–80%) | High (losses in yields 30–50%) |
3 | Occasionally (risk probability 40–60%) | Middle (losses in yields 15–30%) |
2 | Rare (risk probability 20–40%) | Low (losses in yields 5–15%) |
1 | Very rare (Risk probability 0–20%) | Very low (losses in yields < 5%) |
Scenario | Probability 1 vs. Probability 2 |
Activity A (IDR) |
Activity B (IDR) |
Net expected value | CRRA ranges | Risk aversion class |
1 | 10% vs 90% | 1,083,000 vs 733,300 | 1,616,700 vs 366,700 | 276,600 | r < −2.06 | RL4 |
2 | 20% vs 80% | 1,083,000 vs 733,300 | 1,616,700 vs 366,700 | 186,600 | −2.06 < r ≤ −1.13 | RL3 |
3 | 30% vs 70% | 1,083,000 vs 733,300 | 1,616,700 vs 366,700 | 96,600 | −1.13 < r ≤ −0.53 | RL2 |
4 | 40% vs 60% | 1,083,000 vs 733,300 | 1,616,700 vs 366,700 | 6,600 | −0.53 < r ≤ −0.04 | RL1 |
5 | 50% vs 50% | 1,083,000 vs 733,300 | 1,616,700 vs 366,700 | −83,400 | −0.04 < r ≤ 0.41 | RN |
6 | 60% vs 40% | 1,083,000 vs 733,300 | 1,616,700 vs 366,700 | −173,400 | 0.41 < r ≤ 0.85 | RA1 |
7 | 70% vs 30% | 1,083,000 vs 733,300 | 1,616,700 vs 366,700 | −263,400 | 0.85 < r ≤ 1.32 | RA2 |
8 | 80% vs 20% | 1,083,000 vs 733,300 | 1,616,700 vs 366,700 | −353,400 | 1.32 < r ≤ 1.88 | RA3 |
9 | 90% vs 10% | 1,083,000 vs 733,300 | 1,616,700 vs 366,700 | −443,400 | 1.88 < r ≤ 2.72 | RA4 |
10 | 100% vs 0% | 1,083,000 vs 733,300 | 1,616,700 vs 366,700 | −533,400 | 2.72 < r | RA5 |
Source: Author's calculation. |
Variables | Description | Min | Max | Mean | Std. Dev. |
Farmers' and farm characteristics | |||||
Farmers' age | Age of farmer (years) | 25 | 75 | 43.85 | 9.17 |
Education | Formal education of farmer (years) | 2 | 17 | 8.2 | 2.43 |
Family size | Number of family members (persons) | 2 | 7 | 4.46 | 1.03 |
Farming experience | Farming experience (years) | 7 | 50 | 17.34 | 7.45 |
Rubber plantation size | Total rubber plantation area (hectares) | 1 | 3 | 1.49 | 0.50 |
Rubber age | Age of rubber trees (years) | 6 | 27 | 13.08 | 4.00 |
Distance (km) | The distance from the plantation to the village center (km) | 0.5 | 6 | 2.32 | 1.11 |
Use of rubber clone | 1 = apply rubber clone, 0 = otherwise | 0 | 1 | 0.76 | 0.43 |
Risk perception | |||||
Climate change | 1 = if perceived as high risk, 0 = otherwise | 0 | 1 | 0.81 | 0.40 |
Plant disease | 1 = if perceived as high risk, 0 = otherwise | 0 | 1 | 0.69 | 0.46 |
Price change | 1 = if perceived as high risk, 0 = otherwise | 0 | 1 | 0.75 | 0.43 |
Risk attitude | |||||
Risk aversion | 1 = risk averse, 0 = otherwise | 0 | 1 | 0.80 | 0.40 |
Source: Data analysis, 2022. |
Variable | Risk perception | Risk attitude | ||
Climate change | Plant disease | Price change | ||
Farmers' and farm characteristics | ||||
Farmers' age | 0.094**(0.042) | 0.116***(0.036) | 0.168***(0.044) | −0.195***(0.054) |
Education | −0.124 (0.097) | −0.139 (0.088) | 0.566***(0.130) | −0.174 (0.138) |
Family size | −0.481**(0.245) | 0.045 (0.204) | −1.108***(0.286) | 0.449 (0.330) |
Farming experience | −0.263***(0.058) | −0.170***(0.047) | −0.063 (0.048) | −0.026 (0.059) |
Rubber plantation size | −0.668 (0.490) | 1.137***(0.414) | −0.546 (0.479) | 0.338 (0.574) |
Rubber age | −0.090 (0.066) | 0.134**(0.066) | 0.173**(0.079) | 0.687***(0.137) |
Distance | 0.671*** (0.267) | 0.889***(0.220) | 0.717***(0.258) | 0.552** (0.277) |
Use of rubber clone | −0.218 (0.642) | −1.744***(0.631) | 1.672***(0.557) | −2.421***(0.852) |
Risk perception | ||||
Climate change | NA | NA | NA | −0.235 (0.953) |
Plant disease | −0.902 (0.646) | |||
Price change | 1.499**(0.617) | |||
Constant | 6.636***(2.179) | −3.985**(1.760) | −8.37***(2.137) | 2.105 (2.552) |
LR statistic (Prob) | 65.869*** | 74.326*** | 72.991*** | 89.313*** |
R-squared | 0.339 | 0.300 | 0.328 | 0.446 |
*** p < 0.01, ** p < 0.05, * p < 0.1, standard errors in parentheses. Source: Data analysis, 2022. |
Variable | Risk perception | Risk attitude | ||
Climate change | Plant disease | Price change | ||
Farmers' and farm characteristics | ||||
Farmers' age | 0.009**(0.004) | 0.016***(0.005) | 0.020***(0.005) | −0.017***(0.004) |
Education | −0.012 (0.009) | −0.019 (0.012) | 0.068***(0.013) | −0.015 (0.012) |
Family size | −0.048**(0.024) | 0.006 (0.029) | −0.133***(0.029) | 0.039 (0.028) |
Farming experience | −0.026***(0.005) | −0.024***(0.006) | −0.008 (0.006) | −0.002 (0.005) |
Rubber plantation size | −0.066 (0.048) | 0.161***(0.054) | −0.655 (0.057) | 0.029 (0.049) |
Rubber age | −0.009 (0.007) | 0.019**(0.009) | 0.021**(0.009) | 0.059***(0.008) |
Distance | 0.067*** (0.025) | 0.126***(0.026) | 0.086***(0.029) | 0.048**(0.023) |
Use of rubber clone | −0.021 (0.061) | −0.227***(0.065) | 0.222***(0.072) | −0.173***(0.044) |
Risk perception | ||||
Climate change | NA | NA | NA | −0.020 (0.078) |
Plant disease | −0.075 (0.050) | |||
Price change | 0.144**(0.062) | |||
*** p < 0.01, ** p < 0.05, * p < 0.1, standard errors in parentheses. Source: Data analysis, 2022. |