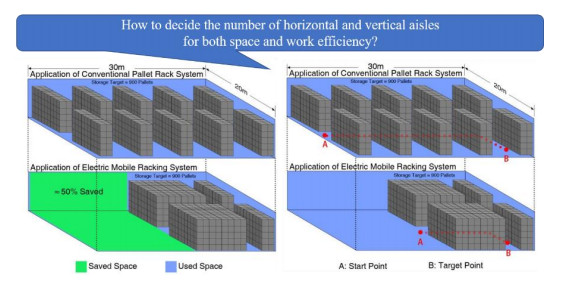
Labor cost reduction and resourceful space utilization are essential for efficient warehouse operation. In these challenges, mobile rack technology can increase storage space by 75% or more. The mobile racking system is a system where racks are constructed on a mobile base and steered by rails on the floor. Driven by an electrical motor, the mobile base moves along the rails to open one or more access aisles. Moving rack technology eliminates aisle space between racks and increases storage space by synchronizing wheels or rails. Hence, companies can stock and access a high volume of products while enduring space-efficient. Minimizing the cost per pallet is especially critical for cooler and freezer facilities. However, there is no straightforward solution to determining the optimal layout of a mobile rack warehouse. When designing a mobile rack warehouse, you can increase storage space by a minimum of aisles, but it can reduce work efficiency at the same time. Therefore, it is necessary to determine the appropriate layout of mobile racks considering both work efficiency and space efficiency. This study proposes a practical layout of a mobile rack warehouse to harmonize work and space efficiency. To validate the model, we examine several numerical examples and analyze the warehouse area, the total amount of rack movement, and working hours. Depending on the operating cost, a different layout is suggested.
Citation: Dong Yun Shin, Jaeyoung Lee, Hyesung Seok. A study of layout determination of mobile rack warehouse[J]. AIMS Environmental Science, 2023, 10(4): 467-477. doi: 10.3934/environsci.2023026
[1] | Catherine S. Jarnevich, Tracy R. Holcombe, Catherine Cullinane Thomas, Leonardo Frid, Aaryn Olsson . Simulating long-term effectiveness and efficiency of management scenarios for an invasive grass. AIMS Environmental Science, 2015, 2(2): 427-447. doi: 10.3934/environsci.2015.2.427 |
[2] | Sonia Prestamburgo, Filippo Sgroi, Adriano Venudo, Carlo Zanin . Universal design as resilient urban space plan strategy. New scenarios for environmental resources' sustainable management. AIMS Environmental Science, 2021, 8(4): 321-340. doi: 10.3934/environsci.2021021 |
[3] | Laura Romero, Modesto Pérez-Sánchez, P. Amparo López-Jiménez . Improvement of sustainability indicators when traditional water management changes: a case study in Alicante (Spain). AIMS Environmental Science, 2017, 4(3): 502-522. doi: 10.3934/environsci.2017.3.502 |
[4] | Amir Hedayati Aghmashhadi, Giuseppe T. Cirella, Samaneh Zahedi, Azadeh Kazemi . Water resource policy support system of the Caspian Basin. AIMS Environmental Science, 2019, 6(4): 242-261. doi: 10.3934/environsci.2019.4.242 |
[5] | Miguel Mora-Pérez, Ignacio Guillen-Guillamón, Petra Amparo López-Jiménez . A CFD study for evaluating the effects of natural ventilation on indoor comfort conditions. AIMS Environmental Science, 2017, 4(2): 289-309. doi: 10.3934/environsci.2017.2.289 |
[6] | Beatriz Gullón, Belén Gómez, José Luis Alonso, Remedios Yáñez . Environmentally friendly technologies for obtaining high sugars concentrations from invasive woody species. AIMS Environmental Science, 2015, 2(4): 884-898. doi: 10.3934/environsci.2015.4.884 |
[7] | Novi Sylvia, Husni Husin, Abrar Muslim, Yunardi, Aden Syahrullah, Hary Purnomo, Rozanna Dewi, Yazid Bindar . Design and performance of a cyclone separator integrated with a bottom ash bed for the removal of fine particulate matter in a palm oil mill: A simulation study. AIMS Environmental Science, 2023, 10(3): 341-355. doi: 10.3934/environsci.2023020 |
[8] | Winai Meesang, Erawan Baothong, Aphichat Srichat, Sawai Mattapha, Wiwat Kaensa, Pathomsorn Juthakanok, Wipaporn Kitisriworaphan, Kanda Saosoong . Effectiveness of the genus Riccia (Marchantiophyta: Ricciaceae) as a biofilter for particulate matter adsorption from air pollution. AIMS Environmental Science, 2023, 10(1): 157-177. doi: 10.3934/environsci.2023009 |
[9] | Martina Grifoni, Francesca Pedron, Gianniantonio Petruzzelli, Irene Rosellini, Meri Barbafieri, Elisabetta Franchi, Roberto Bagatin . Assessment of repeated harvests on mercury and arsenic phytoextraction in a multi-contaminated industrial soil. AIMS Environmental Science, 2017, 4(2): 187-205. doi: 10.3934/environsci.2017.2.187 |
[10] | Afshin Meraj, Tina Shoa, Fereshteh Sadeghi Naieni Fard, Hassan Mina . A comprehensive bi-objective optimization model to design circular supply chain networks for sustainable electric vehicle batteries. AIMS Environmental Science, 2024, 11(2): 279-303. doi: 10.3934/environsci.2024013 |
Labor cost reduction and resourceful space utilization are essential for efficient warehouse operation. In these challenges, mobile rack technology can increase storage space by 75% or more. The mobile racking system is a system where racks are constructed on a mobile base and steered by rails on the floor. Driven by an electrical motor, the mobile base moves along the rails to open one or more access aisles. Moving rack technology eliminates aisle space between racks and increases storage space by synchronizing wheels or rails. Hence, companies can stock and access a high volume of products while enduring space-efficient. Minimizing the cost per pallet is especially critical for cooler and freezer facilities. However, there is no straightforward solution to determining the optimal layout of a mobile rack warehouse. When designing a mobile rack warehouse, you can increase storage space by a minimum of aisles, but it can reduce work efficiency at the same time. Therefore, it is necessary to determine the appropriate layout of mobile racks considering both work efficiency and space efficiency. This study proposes a practical layout of a mobile rack warehouse to harmonize work and space efficiency. To validate the model, we examine several numerical examples and analyze the warehouse area, the total amount of rack movement, and working hours. Depending on the operating cost, a different layout is suggested.
The effective storage layout makes the optimal physical placement and management of products in warehouses possible by adjusting the distance between products. Storage layout design problems have been frequently studied. In general, the number of pickers, picking lines, and arrangement of units have to be optimized. Warehouses and logistics centers have emerged for storage, but their practical concern is space utilization. Improvement in space efficiency is important for warehouses in terms of costs. As a result of examining difficulties in operating the distribution center, 34.8% lack of storage space, 27% lack of manpower, and 22.8% lack of automation were cited as the most urgent concerns of the distribution center [1,2]. Also, there have been various high-technologies recently [3]. Automated mobile racking systems are implemented supported by the Internet of Things (IoT) of supply chains. These integrated systems consist of rack tracks connected to the warehouse floor and movable racking units. Hence, they can enhance the use of central storage locations. Another model is Very Narrow Aisle Vehicles (VNA) for mobile-rack warehouses. These fully automated machines move between rack aisles to pick or store inventory using IoT-enabled laser sensors. In addition, a mobile racking warehouse is appropriate for cold storage because it can compactly store a large amount of inventory while dynamically moving racks. In such a circumstance, the mobile rack system becomes more promising and can resolve various problems by maximizing the storage capacity in limited space.
A rack is a storage frame for industrial products, consisting of columns and shelves. The rack systems can double or triple the storage capacity and area by utilizing the space available in factories or warehouses [4]. Among them, a mobile rack doubles the space efficiency because it represents half of the fixed rack space by installing mobile rails on the building floor. However, the distribution of the mobile rack system to logistics centers or warehouses is too slow. According to a survey on the recognition of the mobile rack, there is generally no intention to replace the existing rack system with an electric mobile rack system. The biggest problem is the high initial investment cost required to introduce automation equipment. As it is not easy to expand or reduce the warehouse automation system after its installation, and the initial cost is enormous, careful and reasonable design procedures are required for the initial introduction [5].
Simulation can be used in this situation. Through simulation, a system to be constructed can be tested in advance. Therefore, simulation makes it possible to conduct a feasibility study and to compare alternatives before constructing a new system, and thus can be used as a tool to reduce the risks of investment [6]. In particular, it is possible to model the dynamic characteristics of a warehouse system, the modeling of which is difficult with mathematical methods, and to analyze most warehouse systems [7]. Studies have been conducted to correct the existing models using simulation and to overcome impractical assumptions for warehouses that introduced the mobile rack system. Kim et al. (2016) proposed a control algorithm optimized considering the travel time and operating cost and verified the algorithm using simulation [8]. Shin et al. (2016) analyzed factors affecting the operation of a mobile rack warehouse, proposed a heuristic algorithm that reflected the analysis results, and quantified the efficiency through numerical experiments [9]. Shin et al. (2016) proposed an efficient cargo placement form through a simulation of the cargo placement form inside a mobile rack warehouse [10]. They concluded that the case with diagonally located entrances is the most inefficient, and the case in which the cargo is placed near entrances is the most efficient among cargo placement forms.
However, most studies regarding mobile rack warehouses only focused on pick-up and delivery schedule, and the effect of the warehouse layout was not discussed. Hence, in this study, we study the effect of warehouse layout to save space and time and determine warehouse layout using simulation.
There are various studies regarding order sequencing, aisle location, and storage assignment in a mobile rack warehouse. Manizni (2006) showed that an intelligent placing of the product could reduce the order picking time and costs [12]. Boysen et al. (2017) formulated the basic order sequencing and aisle relocation problem in mobile rack warehouses [13]. They analyze the trade-off between the aisle relocation effort and space utilization. In other studies, they also formulate the model to solve batching and sequencing of picking orders [14]. Lamballais et al. (2017) propose queuing models for robotic mobile fulfillment systems considering travel time and utilization [15]. On the other hand, Zhang et al. (2019) propose a Genetic Algorithm based method for the storage location assignment problem [16]. Some studies about the Kiva system, a special parts-to-picker-based order processing system, have been conducted. Weidinger et al. (2018) also deal with the storage assignment problem in the Kiva system by using a new metaheuristic method [17]. Lee et al. (2019) developed a cyber-physical system model for a smart robotic warehouse [18]. da Costa Barros and Nascimento (2021) reviewed the studies regarding robotic mobile warehouses, and Wang et al. (2021) designed the robot scheduling under the mobile rack system [19,20]. Wang et al. (2021) also addressed the allocation of stock-keeping units in traditional and mobile-rack warehouses [21]. However, most studies are about the various types of stationary rack warehouses, e.g., robotic mobile warehouses. Traditional robotic mobile fulfillment systems handle warehouse management, including routing, product location assignment aisle computation, and order-batching and packing [19]. There are many studies in that area. However, they only consider a static layout of the warehouse, e.g., traditional layout design, Fishbone design, and Flying-V layouts. On the other hand, a mobile rack warehouse is a dynamic layout warehouse, i.e., the layout can be changed depending on the pick-up schedule. We can think about the same decision-making problems under a mobile rack warehouse, but the layout design has to be determined first. We referred to the studies regarding with layout of the robotic mobile fulfillment systems. However, due to the complexity of the dynamic layout, we consider a traditional layout design but under a varying number of aisles. Moving racks can reduce a significant amount of picking time, but the related research is very few [22]. An analysis of the mobile rack warehouse layout is also highly required.
The general analysis of warehouse operation and layout design are reviewed in de Koster et al. (2007) and Gu et al. (2007) [23,24]. Also, many studies conduct the optimal coordinates of facilities to minimize travel time, e.g., [25,26]. There are various important variables that must be determined for a given warehouse. Important variables that affect the performance of a warehouse include the number of gateways for vehicle entry, the determination of a traffic line of vehicles that minimizes vehicle interference, and the layout of the warehouse. Lee (1995) proposed an analysis method for estimating the work performance of mobile rack automated warehouses, which have the highest space efficiency among the automated warehouses [5]. Hwang and Cho (2003) propose the evaluation model for the order-picking warehouse in the supply center to analyze the rack size, number of transporters, and so on [26]. Especially, Baek and Shin (2009) conducted a study to determine the number of gateways for vehicle entry, and Baek and Ko (2013) conducted a study to determine a traffic line of vehicles for the efficient operation of a warehouse [27,28]. Setting the layout of a warehouse is very important for improving the efficiency of the warehouse. The flow of vehicles that deliver products out of a warehouse significantly affects the product output. In an automated warehouse that utilizes mobile racks, vehicles may be delayed due to the movement of the mobile racks. This may cause a delay between vehicles. To address this problem, free space must be increased. The increase in the free space, however, decreases the space efficiency, which is the benefit of the mobile rack system, while increasing the time efficiency. Therefore, there is a trade-off between time and space efficiency depending on the layout setting. It is necessary to determine the optimal layout in terms of the total cost and reflect the layout to the warehouse design. Boysen et al. conducted the relevant study but mainly focused on order sequencing combined with an aisle relocation problem. They evaluated various order scheduling rules, e.g., First come, first served (FCFS), Most shared aisles (MSR), and Simulated annealing (heuristics). The warehouse layout can highly affect the performance of such order scheduling. Also, because they simultaneously considered the aisle relocation problem by applying a Hamilton path, it is difficult to separately analyze the effect of warehouse layout. Hence, in our study, we propose a more direct and basic way to evaluate the effect of warehouse layout without order sequencing and aisle relocation issues.
A virtual warehouse environment was implemented using 1–5 horizontal free spaces and 0–4 vertical free spaces. Figure 2 shows the case with one horizontal free space and one vertical free space. The "Entrance" in Figure 2 is the starting and arrival point of vehicles. In addition, when one or two vehicles are used out of a total of three vehicles, the resting vehicles are located in a waiting place before they enter the warehouse. Figure 3 shows the mobile rack warehouse consisting of 256 racks. The unit rack consists of four spaces, and its height was fixed to 1. Moreover, free space was required to move the goods on each rack during work. For the movement of the racks, one unit line (two-line pair) containing racks could be moved, but the racks in a unit line could not be separated. Previous studies are divided into ones that researched the single mobile rack system that can be separated only in the horizontal direction and others that researched the multi-mobile rack system that can be separated in the vertical direction. As an example, Kim et al. (2016) conducted a study on the work control algorithm for multiple mobile racks [8]. For the multi-mobile rack system, the space efficiency is higher compared to the single mobile rack system, but the initial cost is higher, and the complexity of the algorithm rapidly increases. Therefore, in this study, simulation was performed for the single mobile rack system that can be separated only in the horizontal or vertical direction.
To minimize unnecessary rack movement and standby time, as well as total work hours, a well-organized work schedule is required. In this study, scheduling was performed based on the following work priority determination criteria. The priority is referred to the Boysen et al. [13].
Work priority
1st priority: Work for the first line on the entrance side
This work is performed first because the work efficiency is the highest, and separate rack movement is not required.
2nd priority: Work that can be performed without rack movement
Rack movement can be minimized by first performing work that became possible due to the free space generated after rack movement.
3rd priority: Work for the last line in the warehouse
If rack movement is inevitable, work hours can be reduced by vehicles performing work for the last line while the racks are moved. When work priorities are determined, the work with the 1st priority must be placed first, followed by the work with the 2nd and 3rd priorities. If multiple tasks have the same priority, work scheduling is performed based on the closer distance.
Vehicles perform assigned work based on the above scheduling. The rules inside the warehouse for the vehicle flow are as follows.
Vehicle flow rule
1) A position close to the work position is selected when the vertical passage is traveled.
2) Travel in both directions is possible for both the vertical passage and the horizontal passage, which is the free passage, and there is no fixed direction.
3) After reaching the work position, the vehicle returns to the starting position with products through the same path before.
4) If two carts in opposite directions meet, either moves sideways to allow the other cart to continue traveling and then return to its path.
5) When rack movement is required while vehicles are traveling, such movement can be performed only when it does not overlap the paths of the vehicles. In other words, vehicle movement has a priority and should not be affected.
There are three assumptions as below.
1) Three vehicles are operated, and each vehicle has its own number. When they collide with each other, one with a higher number moves sideways. For the dynamic characteristics of the vehicles, direction changes or acceleration are not considered, and they travel one space per unit time. If the work quantity is three or less, the vehicles wait at the entrance. They wait at the starting position even though the waiting place is not separately specified.
2) The unit dimensions of the cargo are the same. For the dynamic characteristics of rack movement, acceleration is not considered, and the racks move one space per unit time. The racks move by the unit line, and the racks cannot be separated because of the single rack system. The racks move only when there is no vehicle path that crosses their free space.
3) Work occurs in a random distribution. The starting point and arrival point for movement to the working spot are the same. To prevent vehicle congestion at the starting and arrival points, the exiting direction varies depending on the work position, and the upper part is determined as the entering part.
There are a total of 25 scenarios. For each scenario, the time consumed for work and the amount of rack movement were measured. These and the warehouse size were converted into costs, and the total cost was compared. Total cost is proportional to the average of three performance measures, e.g., warehouse area, rack movement amount, and working hours. The system parameter is multiplied by the total cost. We used MATLAB R2020b in a laptop with 64 bits of Windows 11 operating system, an Intel i7 processor, and 16 GB of RAM for calculation.
The simulation was performed for a total of 25 scenarios. For each scenario, the warehouse area, rack movement amount, and work hours were measured. To compare the measured variables, they were normalized by setting the average of each value to 100, and the results for horizontal division and vertical division are shown in Figures 4 and 5. As the number of horizontal divisions increased, both the rack movement amount and work hours showed a tendency to decrease. Therefore, the design must be performed to increase the number of horizontal divisions as much as possible in an actual situation by comparing the increasing and decreasing costs depending on the warehouse area. As for the comparison of each variable according to the number of vertical divisions, the work hours sharply decreased when the number of vertical divisions was odd, and the work hours were longer when the number of vertical divisions was even than when it was odd. Moreover, contrary to the number of horizontal divisions, the work hours increased as the number of vertical divisions increased. This is because work was delayed as the rack movement overlapped the vehicle movement in some sections. Moreover, the work hours were shorter when the number of vertical divisions was odd because the center was used as the reference when vertical divisions were made in odd numbers during simulation. When vertical divisions were made in even numbers, the vertical line generated in the center disappeared, and the maximum dispersion level was achieved. The rack movement amount showed a tendency to decrease sharply as the number of vertical divisions increased. However, it rapidly decreased initially, and the decrement was slowly reduced. Therefore, if the number of vertical divisions is increased to four or higher, the cost of the increase in the warehouse area will be higher. According to the simulation results, the best results were obtained when the number of vertical divisions was one. Still, the number must be determined considering the actual warehouse area cost and operating cost.
Number of carts | Horizontal divisions | Vertical divisions | Warehouse area | Rack movement amount | Total work hours |
3 | 1 | 0 | 462 | 1459.91 | 3046.12 |
3 | 2 | 0 | 506 | 1422.74 | 3057.56 |
3 | 3 | 0 | 550 | 1413.51 | 3016.77 |
3 | 4 | 0 | 594 | 1404.42 | 2875.91 |
3 | 5 | 0 | 638 | 1384.32 | 2901.60 |
3 | 1 | 1 | 504 | 1264.11 | 2400.72 |
3 | 2 | 1 | 552 | 1246.00 | 2402.19 |
3 | 3 | 1 | 600 | 1242.20 | 2345.16 |
3 | 4 | 1 | 648 | 1243.05 | 2302.15 |
3 | 5 | 1 | 696 | 1192.98 | 2351.75 |
3 | 1 | 2 | 546 | 1199.30 | 2615.64 |
3 | 2 | 2 | 598 | 1148.76 | 2704.18 |
3 | 3 | 2 | 650 | 1154.24 | 2668.88 |
3 | 4 | 2 | 702 | 1127.16 | 2609.67 |
3 | 5 | 2 | 754 | 1122.60 | 2593.40 |
3 | 1 | 3 | 588 | 1149.39 | 2417.11 |
3 | 2 | 3 | 644 | 1138.66 | 2504.55 |
3 | 3 | 3 | 700 | 1126.44 | 2475.80 |
3 | 4 | 3 | 756 | 1118.76 | 2435.82 |
3 | 5 | 3 | 812 | 1124.85 | 2377.61 |
3 | 1 | 4 | 630 | 1129.22 | 2632.08 |
3 | 2 | 4 | 690 | 1109.50 | 2661.63 |
3 | 3 | 4 | 750 | 1111.58 | 2670.89 |
3 | 4 | 4 | 810 | 1061.94 | 2598.57 |
3 | 5 | 4 | 870 | 1062.36 | 2539.83 |
This study analyzed the influence of changes in the warehouse layout on the elements related to warehouse costs. Specifically, the changes in the numbers of horizontal and vertical divisions to design an automated warehouse that utilizes mobile racks are discussed. An experiment was performed using 25 scenarios to investigate the influence on the warehouse. The impact on each element was studied by analyzing the experiment results, and the virtual cost optimization decision-making was performed. In particular, phenomena such as vehicle movement, speed, congestion, vehicle delay, and rack system movement were visually presented through the animation function of the simulation. The results are listed as follows.
1) The rack movement amount decreased sharply as vertical divisions increased. However, it rapidly decreased initially, and the decrement was slowly reduced.
2) When vertical divisions were made in even numbers, the vertical line generated in the center disappeared, and the maximum dispersion level was achieved.
3) The work hours sharply decreased when the number of vertical divisions was odd, and the work hours were longer when the number of vertical divisions was even than when it was odd.
Future studies will consider the constraints of pick-up and different mobile rack designs for specific conditions, such as urgent tasks and limited resources.
The authors declare they have not used Artificial Intelligence (AI) tools in the creation of this article.
This work was supported by the Hongik University
There is no conflict of interest.
[1] | Lee JW (2015) East Asian Logistics Trends, 2015: 92–101. |
[2] | Choi S H, Hong K M, Kim H J. (2018) A Study on Needs of the Logistics Technology in Korea, Korea Maritime Institute. |
[3] | https://www.hankyung.com/news/article/2016102515801 |
[4] | https://www.datexcorp.com/2022-warehousing-update-mobile-racking-systems/ |
[5] | Lee M K (1995) Travel-Time Analysis for an Automated Mobile Racking System. J Korean Inst Ind Eng 21: 195–206. |
[6] | Seila A F, Ceric V, Tadikamalla P R. Applied simulation modeling[M]. Duxbury Press, 2003. |
[7] | Yun Y S, Seo S C, Lee S C (2000) Productivity Analysis of a Car Parts Assembly Line Using a 3D Simulation Tool. J Korean Inst Plant Eng 5. |
[8] | Kim HS, Yoo SS, Cheon GM. (2016) A study on the multi-mobile rack work control algorithm. Proceedings of the Conference of the Korean Operations Research and Management Science Society 738–761. |
[9] | Shin JY, Park HJ, Kim HS. (2016) Development of algorithm for optimum management using mobile-rack in distribution c enter. J Korean Soc Supply Chain Manag 16: 1–10. |
[10] | Shin JY, Kim HS, Park HJ (2016) A study on an efficient cargo placement algorithm inside a mobile rack warehouse. Proceedings of the Spring Conference of the Korean Institute of Industrial Engineers 4493–4511. |
[11] | https://www.jracking.com/mobile-racking-system/automatic-electric-mobile-pallet-rack.html |
[12] | Manzini R (2006) Correlated storage assignment in an order picking system. Int J Ind Eng-theory 13 384–394. |
[13] |
Boysen N, Briskorn D, Emde S (2017) Sequencing of picking orders in mobile rack warehouses. Eur J Oper Res 259: 293–307. https://doi.org/10.1016/j.ejor.2016.09.046 doi: 10.1016/j.ejor.2016.09.046
![]() |
[14] |
Boysen N, Briskorn D, Emde S (2017) Parts-to-picker based order processing in a rack-moving mobile robots environment. Eur J Oper Res 262: 550–562. https://doi.org/10.1016/j.ejor.2017.03.053 doi: 10.1016/j.ejor.2017.03.053
![]() |
[15] |
Lamballais T, Roy D, De Koster M B M. 2017. Estimating performance in a robotic mobile fulfillment system. Eur J Oper Res 256: 976–990. https://doi.org/10.1016/j.ejor.2016.06.063 doi: 10.1016/j.ejor.2016.06.063
![]() |
[16] | Zhang D, Si Y, Tian Z, et al. 2019. A Genetic-Algorithm Based Method for Storage Location Assignments in Mobile Rack Warehouses. In 2019 IEEE Global Communications Conference (GLOBECOM) (1–6). https://doi.org/10.1109/GLOBECOM38437.2019.9013447 |
[17] |
Weidinger F, Boysen N, Briskorn D 2018. Storage assignment with rack-moving mobile robots in KIVA warehouses. Transport Sci 52: 1479–1495. https://doi.org/10.1287/trsc.2018.0826 doi: 10.1287/trsc.2018.0826
![]() |
[18] | Lee C K M, Lin B, Ng K K H, et al. (2019) Smart robotic mobile fulfillment system with dynamic conflict-free strategies considering cyber-physical integration. Advanced Engineering Informatics, 42, 100998. https://doi.org/10.1016/j.aei.2019.100998 |
[19] |
da Costa Barros Í R, Nascimento T P (2021) Robotic Mobile Fulfillment Systems: A survey on recent developments and research opportunities. Robot Auton Syst 137: 103729. https://doi.org/10.1016/j.robot.2021.103729 doi: 10.1016/j.robot.2021.103729
![]() |
[20] |
Wang Z, Sheu J B, Teo C P, et al. (2021) Robot Scheduling for Mobile‐Rack Warehouses: Human–Robot Coordinated Order Picking Systems. Prod Oper Manag https://doi.org/10.1111/poms.13406 doi: 10.1111/poms.13406
![]() |
[21] | Wang Z, Xu W, Hu X, et al. (2021) Inventory allocation to robotic mobile-rack and picker-to-part warehouses at minimum order-splitting and replenishment costs. Ann Oper Res 1–25. https://doi.org/10.1007/s10479-021-04190-1 |
[22] |
Foroughi A, Boysen N, Emde S, et al. (2021) High-density storage with mobile racks: Picker routing and product location. J Oper Res Soc 72: 535–553. https://doi.org/10.1080/01605682.2019.1700180 doi: 10.1080/01605682.2019.1700180
![]() |
[23] |
De Koster R, Le-Duc T, Roodbergen K J. 2007. Design and control of warehouse order picking: a literature review. Eur J Oper Res 182: 481–501. https://doi.org/10.1016/j.ejor.2006.07.009 doi: 10.1016/j.ejor.2006.07.009
![]() |
[24] |
Gu J, Goetschalckx M, McGinnis L F. 2007. Research on warehouse operation: a comprehensive review. Eur J Oper Res 177: 1–21. https://doi.org/10.1016/j.ejor.2006.02.025 doi: 10.1016/j.ejor.2006.02.025
![]() |
[25] | Jeong D, Seo Y. 2018. Golden section search and hybrid tabu search-simulated annealing for layout design of unequal-sized facilities with fixed input and output points. Int J Ind Eng 25. |
[26] | Hwang H S, Cho G S 2003. A performance analysis of transporters for order picking warehouse design. Int J Ind Eng-Theory Appl Pract 10: 614–620. |
[27] | Baek J K, Shin H J 2009. A simulation for warehouse traffic using ARENA. Korean Manag Consult Rev 9: 95–108. |
[28] |
Baek J K, Shin H J. 2013. A simulation for warehouse considering traffic. J Korea Soc Simul 22: 119–128. https://doi.org/10.9709/JKSS.2013.22.4.119 doi: 10.9709/JKSS.2013.22.4.119
![]() |
Number of carts | Horizontal divisions | Vertical divisions | Warehouse area | Rack movement amount | Total work hours |
3 | 1 | 0 | 462 | 1459.91 | 3046.12 |
3 | 2 | 0 | 506 | 1422.74 | 3057.56 |
3 | 3 | 0 | 550 | 1413.51 | 3016.77 |
3 | 4 | 0 | 594 | 1404.42 | 2875.91 |
3 | 5 | 0 | 638 | 1384.32 | 2901.60 |
3 | 1 | 1 | 504 | 1264.11 | 2400.72 |
3 | 2 | 1 | 552 | 1246.00 | 2402.19 |
3 | 3 | 1 | 600 | 1242.20 | 2345.16 |
3 | 4 | 1 | 648 | 1243.05 | 2302.15 |
3 | 5 | 1 | 696 | 1192.98 | 2351.75 |
3 | 1 | 2 | 546 | 1199.30 | 2615.64 |
3 | 2 | 2 | 598 | 1148.76 | 2704.18 |
3 | 3 | 2 | 650 | 1154.24 | 2668.88 |
3 | 4 | 2 | 702 | 1127.16 | 2609.67 |
3 | 5 | 2 | 754 | 1122.60 | 2593.40 |
3 | 1 | 3 | 588 | 1149.39 | 2417.11 |
3 | 2 | 3 | 644 | 1138.66 | 2504.55 |
3 | 3 | 3 | 700 | 1126.44 | 2475.80 |
3 | 4 | 3 | 756 | 1118.76 | 2435.82 |
3 | 5 | 3 | 812 | 1124.85 | 2377.61 |
3 | 1 | 4 | 630 | 1129.22 | 2632.08 |
3 | 2 | 4 | 690 | 1109.50 | 2661.63 |
3 | 3 | 4 | 750 | 1111.58 | 2670.89 |
3 | 4 | 4 | 810 | 1061.94 | 2598.57 |
3 | 5 | 4 | 870 | 1062.36 | 2539.83 |
Number of carts | Horizontal divisions | Vertical divisions | Warehouse area | Rack movement amount | Total work hours |
3 | 1 | 0 | 462 | 1459.91 | 3046.12 |
3 | 2 | 0 | 506 | 1422.74 | 3057.56 |
3 | 3 | 0 | 550 | 1413.51 | 3016.77 |
3 | 4 | 0 | 594 | 1404.42 | 2875.91 |
3 | 5 | 0 | 638 | 1384.32 | 2901.60 |
3 | 1 | 1 | 504 | 1264.11 | 2400.72 |
3 | 2 | 1 | 552 | 1246.00 | 2402.19 |
3 | 3 | 1 | 600 | 1242.20 | 2345.16 |
3 | 4 | 1 | 648 | 1243.05 | 2302.15 |
3 | 5 | 1 | 696 | 1192.98 | 2351.75 |
3 | 1 | 2 | 546 | 1199.30 | 2615.64 |
3 | 2 | 2 | 598 | 1148.76 | 2704.18 |
3 | 3 | 2 | 650 | 1154.24 | 2668.88 |
3 | 4 | 2 | 702 | 1127.16 | 2609.67 |
3 | 5 | 2 | 754 | 1122.60 | 2593.40 |
3 | 1 | 3 | 588 | 1149.39 | 2417.11 |
3 | 2 | 3 | 644 | 1138.66 | 2504.55 |
3 | 3 | 3 | 700 | 1126.44 | 2475.80 |
3 | 4 | 3 | 756 | 1118.76 | 2435.82 |
3 | 5 | 3 | 812 | 1124.85 | 2377.61 |
3 | 1 | 4 | 630 | 1129.22 | 2632.08 |
3 | 2 | 4 | 690 | 1109.50 | 2661.63 |
3 | 3 | 4 | 750 | 1111.58 | 2670.89 |
3 | 4 | 4 | 810 | 1061.94 | 2598.57 |
3 | 5 | 4 | 870 | 1062.36 | 2539.83 |