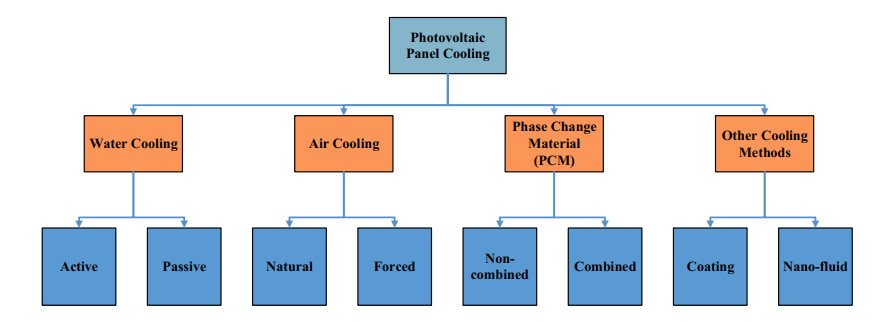
This work concerns a comparative experimental study of cooling PV panels by free and forced convection and using finned plates. To this end, four prototypes are considered: the first one with a PV panel alone without cooling techniques, the second one consists of a PV panel with a rectangular finned plate attached to its rear surface and cooled by free convection, a third prototype consists of a PV panel cooled by forced convection by three axial-flow fans and a fourth prototype consists of a PV panel with a rectangular finned plate attached to its rear surface and cooled by forced convection by three axial-flow fans. Results showed an increase of 3.01% in the efficiency of the PV panel with finned plate under forced convection, an increase of 2.55% in the efficiency of the PV panel with finned plate under free convection and an increase of 2.10% in the efficiency of the PV panel under forced convection. Economic and environmental studies are also conducted and estimations of savings per year and amount of carbon dioxide emission reductions are provided.
Citation: Tarek Ibrahim, Farouk Hachem, Mohamad Ramadan, Jalal Faraj, Georges El Achkar, Mahmoud Khaled. Cooling PV panels by free and forced convections: Experiments and comparative study[J]. AIMS Energy, 2023, 11(5): 774-794. doi: 10.3934/energy.2023038
[1] | Kaovinath Appalasamy, R Mamat, Sudhakar Kumarasamy . Smart thermal management of photovoltaic systems: Innovative strategies. AIMS Energy, 2025, 13(2): 309-353. doi: 10.3934/energy.2025013 |
[2] | Taliv Hussain, Mohd Ahsan Kamal, Adnan Hafiz . Comparative analysis of apple and orange during forced convection cooling: experimental and numerical investigation. AIMS Energy, 2021, 9(2): 193-212. doi: 10.3934/energy.2021011 |
[3] | Muzaffar Ali, Hafiz.M. Ali, Waqar Moazzam, M. Babar Saeed . Performance enhancement of PV cells through micro-channel cooling. AIMS Energy, 2015, 3(4): 699-710. doi: 10.3934/energy.2015.4.699 |
[4] | Kokou Aménuvéla Toka, Yawovi Nougbléga, Komi Apélété Amou . Optimization of hybrid photovoltaic-thermal systems integrated into buildings: Impact of bi-fluid exchangers and filling gases on the thermal and electrical performances of solar cells. AIMS Energy, 2024, 12(5): 1075-1095. doi: 10.3934/energy.2024051 |
[5] | Alemayehu T. Eneyaw, Demiss A. Amibe . Annual performance of photovoltaic-thermal system under actual operating condition of Dire Dawa in Ethiopia. AIMS Energy, 2019, 7(5): 539-556. doi: 10.3934/energy.2019.5.539 |
[6] | Sabir Rustemli, Zeki İlcihan, Gökhan Sahin, Wilfried G. J. H. M. van Sark . A novel design and simulation of a mechanical coordinate based photovoltaic solar tracking system. AIMS Energy, 2023, 11(5): 753-773. doi: 10.3934/energy.2023037 |
[7] | Abdulrahman Th. Mohammad, Amer Ibrahim Ismael . An equivalent photovoltaic solar system to solve the problems of electricity in Iraqi houses. AIMS Energy, 2019, 7(5): 660-670. doi: 10.3934/energy.2019.5.660 |
[8] | Miguel de Simón-Martín, Montserrat Díez-Mediavilla, Cristina Alonso-Tristán . Real Energy Payback Time and Carbon Footprint of a GCPVS. AIMS Energy, 2017, 5(1): 77-95. doi: 10.3934/energy.2017.1.77 |
[9] | Xian-long Meng, Cun-liang Liu, Xiao-hui Bai, De-hai Kong, Kun Du . Improvement of the performance of parabolic trough solar concentrator using freeform optics and CPV/T design. AIMS Energy, 2021, 9(2): 286-304. doi: 10.3934/energy.2021015 |
[10] | Dessie Tadele Embiale, Dawit Gudeta Gunjo, Chandraprabu Venkatachalam, Mohanram Parthiban . Experimental investigation and exergy and energy analysis of a forced convection solar fish dryer integrated with thermal energy storage. AIMS Energy, 2022, 10(3): 412-433. doi: 10.3934/energy.2022021 |
This work concerns a comparative experimental study of cooling PV panels by free and forced convection and using finned plates. To this end, four prototypes are considered: the first one with a PV panel alone without cooling techniques, the second one consists of a PV panel with a rectangular finned plate attached to its rear surface and cooled by free convection, a third prototype consists of a PV panel cooled by forced convection by three axial-flow fans and a fourth prototype consists of a PV panel with a rectangular finned plate attached to its rear surface and cooled by forced convection by three axial-flow fans. Results showed an increase of 3.01% in the efficiency of the PV panel with finned plate under forced convection, an increase of 2.55% in the efficiency of the PV panel with finned plate under free convection and an increase of 2.10% in the efficiency of the PV panel under forced convection. Economic and environmental studies are also conducted and estimations of savings per year and amount of carbon dioxide emission reductions are provided.
Increased fossil fuel usage has led to serious environmental problems and to the depletion of these resources [1,2]. Modern researches focus on decreasing the use of non-renewable energy resources and spur on the usage of renewable energy resources such as solar energy [3,4], wind energy [5,6,7], geothermal energy [8,9,10,11], hydropower [12] and biomass [13,14,15]. Heat recovery systems are also good means to reduce the consumption of fossil fuels [16,17,18,19,20,21].
Each year, Lebanon has more than 300 sunny days with up to 9 hours of sun light per day. With that amount of sunlight, the conversion of solar energy into electricity through photovoltaic panels would form a major power source feeding different sectors of daily electric usages. However, the increased hit of sunrays on the surface of the PV panel increases the temperature of the PV panel, which would decrease the output power significantly. The decrease in efficiency reaches up to 83% depending on the type of the PV panel. According to standard test conditions (STC), every one-degree Celsius rise above 25 ℃ would decrease the efficiency of the PV panel by 0.5% [22]. Different cooling methods, shown in Figure 1, were proposed by researchers.
Water cooling technique is divided into two categories: active and passive. Active method is characterized by the use of a pump to ensure the flow. In the passive method, no pump is needed and the liquid flows naturally. Forced and free convection of air-cooling technique differ by the use of a flow actuator in the first while letting buoyancy effect play its role in the latter. Cooling by phase change material (PCM) is either a non-combined cooling (the use of PCM without additives) or combined cooling (mixing PCM with aluminum or copper particles to increase thermal conductivity). Coating and nano-fluid cooling, accompanied with other cooling methods, are new methods used to cool PV panels.
Yuan et al. [23] discussed the effect of using water-pipe-based PV/T and PV/T with micro-channel heat pipe array (MHPA), both compared with a standard PV module under high ambient temperature. Results showed that water-pipe-based PV/T and PV/T with MHPA increased the performance of the cells in a PV panel. However, the best performance in this study was recorded by the water-pipe-based PV/T. ElMays et al. [24] enhanced the efficiency of the PV panel by 1.75% experimentally by using a rectangular finned plate acting as a heat sink placed at the rear surface of the PV panel under free convection. Hachem et al. [25] studied the effect of pure and combined PCM in cooling PV panels. Results showed efficiency enhancement of 5.8% when using combined PCM and 3% when using pure PCM. Nižetić et al. [26] discussed the importance of redesigning the rear surface of the PV panel in a way to dissipate heat outside of it and increase the output power. Al-Waeli et al. [27] used silicon carbide nanofluid in a PV/T system to enhance the PV thermal and electrical performance. Experiments were done in an indoor and outdoor environment. It was found that results were in agreement in both indoor and outdoor experimentation where performance enhancement and incremental efficiency rise were recorded. Kaldellis et al. [28] experimentally investigated the optimum tilt angle for a PV panel in Greek region. Experimental results showed that the optimum angle is 15° (±2.5°) for almost the entire summer. Irshad et al. [29] studied, in Malaysian weather conditions, experimentally and by simulation, the effect of a thermoelectric air duct system (TE-AD) aided with PV system. Agreement was noticed between experimental and numerical results when using a PV system with TE-AD operating at 6 A, which gave a temperature difference of 6.8 ℃ with a cooling capacity of 517.24 W and COP of 1.15. Moreover, the use of a PV system with TE-AD would save 1806.75 kWh/year. Luo et al. [30] numerically investigated the effect of a building integrated photovoltaic thermoelectric (BIPVTE) wall system. Results showed that the saving ratio was nearly 480% in Hong Kong of a BIPVTE and energy saving ranging from 29.19 to 62.94 kWh/m2 annually in six cities in China during hot summer and warm winter zone. Hussein et al. [31] investigated the effect of cooling photovoltaic panels numerically and experimentally by forced convection. Two configurations were studied and compared against the control PV. The first cooling method was blowing air using a blower to a lower duct while the second cooling method was supplying air by fans to the backside of the PV panel. Results showed that the use of fans increased the efficiency by 2.1% while the use of a blower increased the efficiency by 1.34%. Wang et al. [32] investigated numerically the use of curved eave and vortex generators in increasing the heat exchange by forced convection and decreasing the PV temperature. Results showed a temperature decrease of 5.89 ℃. Ahmad et al. [33] numerically studied the effect of a truncated multi-level heat sink on cooling the PV panel naturally. Results showed a decrease of 6.13% in PV temperature an increase in power by 2.87%. Yildirim et al. [34] numerically studied the effect of a water-based module in cooling a PV/T system. Results showed maximum electric and thermal efficiencies of 17.79% and 76.13% respectively. Bevilacqua et al. [35] experimentally investigated the effect of surface spraying of water in cooling PV panel. Results showed an increase of 7.8% in power and a decrease of 28.2% in cell temperature. Salman et al. [36] experimentally and numerically studied the effect of cooling PV panel by flowing water in porous media. Results showed a good agreement between numerical and experimental results. Temperature decreased by 9–14 ℃ when using porous media in cooling. This literature shows that cooling PV panels is still an interest among researchers and needs more studies in order to improve PV's efficiency. This domain needs more physical and transient analysis alongside energy balance to better address this problem and find new state of the art solutions.
Vaillon et al. [37] discussed techniques to decrease the thermal losses in PV panels. Results suggest that a basic amount of conductive or convective cooling is crucial. Glick et al. [38] investigated the effect of system inclination on the coefficient of convective heat transfer and system-level flow. Results showed a convection increase of 30–45% resulting in ~5% power output increase and +0.3%/year decrease of degradation in solar panel. Stanislawski et al. [39] numerically investigated the effect of arranging PV modules on increasing the convective heat transfer. Results showed an increase of 14.8% when arranging the PV module in a compact way compared to the standard arrangement. Glick et al. [40] experimentally studied heat transfer by convection for a scaled PV farm. Results showed an increase of 7% in the convective heat transfer due to variations in turbulence for the inflow. Also, convection increases when tilting the angle of the PV up to 30° whenever flow is hitting the array of PV panels from the backside. Prilliman et al. [41] discussed the effect of changing the spacing between the PV panels in a PV array on the convective heat transfer. Results showed that increasing the row spacing in PV arrays results in the improvement of levelized cost of energy by 2.15% in low ambient temperatures and high wind speed climates in the United States. Stanislawski et al. [42] investigated the effect of row spacing between PV panels in an array on increasing the convective heat transfer. Simulation results showed an increase of 14.8% and 4.0% in convective heat transfer cooling and output power respectively. In addition, PV temperature dropped by 6.6 ℃. Smith et al. [43] studied the effect of PV design and parameters in cooling the PV panels by convection. Study revealed a correlation between the geometry of the PV farm and the convective heat transfer. When using this correlation, convective heat transfer increases and as a result power output from PV panel and PV cells lifetime increases. Glick et al. [44] experimentally studied convection coefficient in a wind tunnel with particle-image-velocimetry and thermal measurements. The study shows that the orientation of the PV panels resulted in a complex flow of upwards-directed wakes.
As shown in the literature, cooling PV panels is a research subject that is taking high importance nowadays. There are several techniques and all are still under consideration. One category of cooling techniques is the cooling by convection: free or forced. Both cooling techniques by convection are supported by fins. To this end, it is important to study experimentally and quantify physically the effect of each of these techniques on the performance of PV panels: free convection, forced convection and use of fins. In this context, the present manuscript exposes a comparative experimental study of the effect of cooling PV panels by free and forced convection and by using fins. The originality of the work resides in (1) the experimental comparative study, (2) the case study along with economic and environmental evaluations and (3) physical and energy balance analysis. To this end, four prototypes are considered: the first one with a PV panel alone without cooling techniques, the second one consists of a PV panel with a rectangular finned plate attached to its rear surface and cooled by free convection, a third prototype consists of a PV panel cooled by forced convection by three axial-flow fans and a fourth prototype consists of a PV panel with a rectangular finned plate attached to its rear surface and cooled by forced convection by three axial-flow fans.
Section 2 of the manuscript is devoted to a theoretical background. Section 3 concerns the materials and methods. Section 4 presents the results and their associated discussions. Section 5 is devoted to economic and environmental aspects of the study. Finally, Section 6 draws the main conclusions of the work.
The effective area of a PV panel is the total area of the cells. In this case, each PV panel's area is represented by:
Aeff=∑(leff×weff) | (1) |
where:
Aeff: Frontal effective area of the PV panel (area receiving solar radiation).
leff: length of the cell.
weff: width of the cell.
The solar energy falling on the surface of the PV panel is represented as an input power given by:
Pin=G×Aeff×α | (2) |
where:
Pin: input power, power received from the sun.
G: Solar radiation.
Aeff: effective area.
α: absorptivity of glass.
The output power of the PV panels, is in the form of a D.C power given by:
Pout=Voc×Isc | (3) |
where:
Pout: output power by the PV panel.
Voc: open circuit voltage.
Isc: short circuit current.
The electric efficiency of the PV panel represents how efficient is the PV panel in converting the solar input power into electric output power, it is represented by:
ηelect=PoutPin×100 | (4) |
where:
ηelect: electric efficiency.
Pout: output power by the PV panel.
Pin: input power, power received from the sun.
Three cooling systems were studied in this paper in order to investigate the effect of free and forced convection in cooling photovoltaic panels. The designs were based on a numerical study made on COMSOL Multiphysics after many simulations attempts to get the optimum designs. The optimum design for the 69 × 35 cm PV panels used were a finned plate of 26 fins, with a 0.5 cm base thickness and a fin-height of 3.9 cm.
The main objective of the installment of a finned plate to the back surface of the PV panel is to increase the surface area which would increase the heat transferred by convection. A rectangular finned plate made of aluminum (of thermal conductivity k = 237 W/m·k) of 60 cm length, 24 cm width and 4.4 cm thick, shown in Figure 2, was designed for experimental testing. Before attachment, the back surface of the PV panel should be fully covered with thermal grease to ensure there are no air gaps between the rectangular finned plate and the back surface of the PV panel.
Since heat is not favorable inside the duct, a wooden air duct made of medium density fiberboard, shown in Figure 3, with a thermal conductivity k = 0.3 W/m·k was designed according to the PV panel's dimensions (69 cm × 35 cm) and with a depth upon to the ratio B/L = 0.0825 [31], where B is the depth and L is the length of the wooden duct. The wooden duct contained 3 axial flow fans with a power of 0.72 Watt were fixed at the front of it to ensure the forced convection process. Three axial flow fans of 0.72 Watt power were fixed in the front side of the wooden duct to ensure forced convection process. These fans were connected to two 12 DC batteries.
A total of four polycrystalline PV panels were used in this study to investigate the effect of free and forced convection in maintaining low temperature in the PV panels to increase their efficiency and output power. Figure 4 shows the four PV panels placed at an inclination angle of 80 degrees with the vertical according to the latitude of Bekaa valley (34.0089° N, 36.1453° E), Lebanon and directed toward the south to gain the maximum amount of sun light to hit their front surfaces. Experiment was made on the 11th of June, 2017 and measurements were conducted every 10 minutes for 7.5 hours (from 8:30 a.m. until 4 p.m.).
Each PV panel have an effective area of 0.1620 m2 with a maximum power output of 30 Watt at 25 ℃ at STC. The four PV panels were studied under an average ambient temperature of 34.96 ℃, an average solar irradiation of 773 W/m2, an average wind speed (natural air circulation) of 1.175 m/s and an average wooden duct air speed (fans speed at the outlet of the wooden ducts) of 0.46–0.47 m/s.
Figure 4 shows the experimental setup of the four PV panels. Where panel A is the standard PV used for comparing other PV results with, panel B is the free convection PV with rectangular finned plate, panel C is the forced convection PV and panel D is the forced convection PV with rectangular finned plate.
As shown in Figure 5, the aluminum finned plate was attached to the back of the PV panel to ensure the increase of the rear area which would increase the total heat lost with the fluid passing in between the rectangular fins.
Figure 6 shows isometric and rear views of the forced convection PV panel. As shown in the figure, three DC axial-flow fans were installed in the frontal region of the wooden duct enclosing the PV panel. The rear view shows that there is nothing inside the wooden duct that would block the fluid's buoyancy effect.
As shown in Figure 7, the isometric view of the PV panel shows the 3 axial-flow fans in the frontal region of the wooden duct. The rear view of the PV panel under forced convection with finned plate shows the aluminum rectangular finned plate located at the rear of the PV panel to increase the total area while being under forced convection by the DC-fans.
In the experimental setup, digital thermometers were used to measure the temperature at the surfaces of the PV panels and at the rectangular finned plates installed at the back of the PV panels. Digital thermometers were used in this study. The finned plate PV under free convection and the finned plate PV under forced convection had 3 thermometers each, one on the surface of the PV placed in the middle, the second was placed at the back of the PV and the third was placed on the middle of the finned plate. The forced convection PV and the standard PV panels had two thermometers each, one is placed in the middle of the surface of each PV and the other is placed on the middle of the backside of each PV. A total of 10 digital thermometers were used to record the temperatures.
Also, a solar power meter was used to measure the solar irradiation received by the panels from the sun and an anemometer to measure the speed of wind inside and outside of the ducts. Multi-meters were used associated with a rheostat adjusted every 10 minutes in order to obtain the maximum voltage and current. As shown in Figure 8, the ampere meter was installed in series with the PV panel and the rheostat while the voltmeter was installed in parallel.
In addition to the devices used, an Arduino board was programmed to cut the power off on the axial-flow fans in the forced convection cooling systems in order to decrease the power used by the fans. The Arduino board was programmed to cut the power off when the surface temperature 35 ℃ using a heat sensor placed in the middle of the frontal surface of the PV panel. Connections of the Arduino board were shown in Figure 9.
Ambient temperature and solar radiation were measured using digital thermometer and solar power meter of high precisions. The digital thermometer recording the ambient temperature was placed near the PV panels while the solar power meter was placed perpendicular to the surface of the PV panel to read the solar irradiation.
For experimental results validation, uncertainty analysis was made at the level of surface temperature and output power since the efficiencies of the solar panels depend mainly on the temperature and power values. Variations of the surface temperature and the output power were recorded for two different experiments under the same operating conditions and configurations.
It was found that the relative differences in surface temperature recorded for ambient temperatures of 37, 40, 33 and 29 ℃ were 0.757%, 0%, 2.325% and 0%. While the relative differences in power output recorded for solar radiations of 950,920,810 and 705 W/m2 were 0.542%, 0.840%, 1.468% and 0.876%.
With an average relative difference in surface temperature and power of 0.770% and 0.932% respectively and a 1% error in the digital thermometer and the multimeter used, the uncertainty was recorded to be 1.446% for surface temperature readings and 1.387% for power output readings resulting a 98.554% confidence in surface temperature measurements and 98.613% confidence in power output measurements.
The main objective of the cooling systems is to decrease the PV panel's temperature through free and forced convection and determine which method is the best in cooling and rising the PV's efficiency. Experiment was conducted and results were recorded simultaneously in order to study the surface temperatures, the output power with irradiation and the efficiencies of the four PV panels.
Front surface temperatures of the four PV panels were recorded using digital thermometers and plotted for analysis (Figure 10).
As shown in Figure 10, the maximum temperature was reached by the standard PV panel with an average of 45.3 ℃ while the minimum temperature was reached by the PV panel of the forced convection cooling system with finned plate with a value of 40.3 ℃. In addition to an average temperature of 42.8 ℃ and 44 ℃ recorded for the PV with free convection cooling system and the PV with forced convection cooling system respectively.
This shows the effectiveness of free and forced convection in cooling the PV panels. Showing moreover the efficacy of the constructed finned plate in dissipating heat to the atmosphere through increasing the surface area of dissipation.
The output power of the four PV panels was recorded using the rheostat and were plotted for comparison and analysis (Figure 11).
As the solar radiation increases in intensity, the power generated by the PV panels increases as well. The maximum output power was reached by the cooling system that was able to decrease the temperature of the PV as maximum as possible, Figure 11 shows that the forced convection cooling system with finned plate had the maximum power compared to the other cooling systems, which agrees with the temperature data. The maximum average power for the forced convection system with finned plate was 21.61 Watt. Also, the maximum average power reached by the free convection cooling system was 21 Watt and that of the forced convection was 20.56 Watt. These values have dropped in the standard PV panel to reach an average of 17.80 Watt.
The efficiency of each PV panel was calculated and plotted in the following figure (Figure 12).
As shown in Figure 12, the highest efficiency was reached by the forced convection cooling system with finned plate with an average of 17.66%. The second highest efficiency was recorded by the free convection PV panel with an average of 17.2%, followed by the forced convection cooling system with an average of 16.75%. The standard PV panel had the lowest efficiency with an average of 14.64%.
Consequently, it can be deduced that the efficiency of the PV panel increases by 3.01% when installing a forced convection cooling system with a finned plate to the PV panel, by 2.55% when installing a free convection cooling system to the PV panel and by 2.10% when installing a forced convection cooling system to the PV panel.
Table 1 reports the improved efficiencies, power and front temperatures for the three cooling systems.
Standard PV panel | Free convection cooling system with finned plate | Forced convection cooling system | Forced convection cooling system with finned plate | |
Efficiency [%] | 0 | 2.55 | 2.10 | 3.01 |
Power [Watt] | 0 | 3.2 | 2.76 | 3.81 |
Surface temperature difference [℃] | 0 | –2.46 | –1.30 | –4.94 |
The four PV panels are studied economically and environmentally in this section.
The economic study shows the savings of each PV per the months of the year (Figure 13), it also indicates the time needed by each system to return its initial investment value through ROI (Figure 14). Taking into consideration that the experiments were done in Lebanon, the price of every KWh of electricity in Lebanon was $0.09.
In order to calculate the total savings of each PV system, the power enhancement is multiplied by each month's sun hours. The total sun hours in Lebanon are found to be 4440 hours distributed over the 12 months of the year with varying values.
As shown in Figure 13, money savings increased gradually nearly from February to reach maximum values in all of the PV panels in May through July. In other words, in the summer season in Lebanon where the irradiation reaches its maximum values.
Also, Figure 13 shows that the highest value of money savings was recorded for the forced convection with finned plate PV panel throughout the year months. Followed by free convection with finned plate PV and forced convection. While the lowest value of money savings was recorded for the standard PV throughout the year months, as expected.
Forced convection with finned plate PV panel had an average savings of $8.6 per year, while the standard PV panel had $7.11. Free convection with finned plate PV and forced convection PV recorded averages of $8.4 and $8.2 respectively. Forced convection with finned plate PV had the highest value of money savings due to the ability of forced convection combined with a finned plate to decrease the temperature of the PV and increase its output power.
As shown in Figure 14, the forced convection with finned plate PV needs about 5.78 years to return its initial investment price, while the standard PV needs about 4.21 years. Forced convection PV and free convection with finned plate PV need about 4.86 and 4.76 years respectively to return the amount of money initially invested.
Although the three cooling systems enhanced the efficiency and power of the PVs containing them, but their prices were increased due to the materials bought and used to build them compared to the standard PV. Table 2 illustrates the price, savings and number of years needed to return the initial investment price of each PV.
Panels | Price [$] | Savings [$] | ROI period [years] |
Forced convection with finned plate PV | 50 | 8.64 | 5.79 |
Forced convection PV | 40 | 8.21 | 4.87 |
Free convection with finned plate PV | 40 | 8.39 | 4.77 |
Standard PV | 30 | 7.11 | 4.22 |
An environmental study was conducted in order to show the effect of each PV panel in reducing the CO2 levels compared to standard non-renewable energy electricity production methods.
When using renewable energy resources, the amount of CO2 emitted to the atmosphere decreases compared to the non-renewable energy resources. Figure 15 shows the amount of CO2 reduced by each PV per the months of the year. The amount of CO2 reduction started increasing gradually from February to reach its maximum values in the summer months (May, June, July), then decreased gradually to reach their minimum values in December.
The maximum value of CO2 reduction was recorded by the forced convection with finned plate PV with a total of 78.78 kg throughout the year while the lowest value of CO2 reduction was recorded by the standard PV with a total of 64.89 kg. The total CO2 reduction values for the free convection with finned plate PV and the forced convection PV were 76.56 kg and 74.95 kg respectively.
As was expected, the forced convection with finned plate cooling system had the highest CO2 reduction value due to its ability in cooling the PV panel in higher manners compared to the other PVs.
In order to validate the effect of free and forced convection in cooling the PV panel, an energy balance analysis was made at the level of the configurations (Figure 16). The rate of energy for the PV panels is represented by:
˙Ein−˙Eout+˙Egen=˙Est,PV | (5) |
where:
˙Ein is the rate of energy entering the system from the solar irradiation:
˙Ein=τ×α×I×A | (6) |
where τ is the transmittivity and α is the absorptivity of the first layer of the PV (glass).
˙Est,PV is the rate of stored energy in the PV panel:
˙Est,PV=m×cp×ΔT | (7) |
where m and cp are the mass and the specific heat of the PV panel respectively and ΔT is the temperature difference.
˙Egen is the power output by the PV panels and ˙Eout is the rate of energy dissipated outside the PV panel in convective form.
In this energy analysis, we calculated the rate of energy dissipated outside the PV using the following equation:
˙Eout=˙Ein−˙Egen−˙Est,PV | (8) |
As shown in Table 3, the decrease of the stored energy Δ˙Est due to cooling increased the energy ˙Eout dissipated from the PV panels and as a result temperature was decreased and power increased.
Configuration | ˙Eout/˙Ein | ˙Est/˙Ein | ˙Egen/˙Ein |
Control PV panel | 0.679 | 0.166 | 0.154 |
PV under forced convection | 0.682 | 0.143 | 0.175 |
PV under free convection with fins | 0.695 | 0.129 | 0.175 |
PV under forced convection with fins | 0.753 | 0.060 | 0.187 |
The ratio ˙Eout/˙Ein increased when temperature decreased due to cooling. ˙Eout/˙Ein was 0.679 for the control PV, this value increased after exposing the PV to a forced convection by fans to 0.682. Afterwards, cooling PV panels with free convection with finned plate and forced convection with finned plate increased the ˙Eout/˙Ein ratio to 0.695 and 0.753 respectively.
This energy balance study supports our claim that cooling the PV panel under free and forced convection increases its power output.
This study concerned a comparative experimental study of cooling PV panels by free and forced convection and using finned plates. With a confidence of 98.554% and 98.613% in both surface temperature and power output measurements respectively, the forced convection cooling system with finned plate is found to have the maximum impact in increasing the efficiency of the PV panel with a total of 3.01% compared to the standard PV panel in addition to a total increase of 3.81 Watt in the output power. Also, free convection cooling system was found to increase the efficiency by 2.55% and the power by 3.27 watt compared to the standard PV panel while forced convection cooling system increased the efficiency by 2.10% and the power by 2.75 watt compared to the standard PV panel.
Furthermore, energy balance approach supported the resulting power enhancment reached. The energy dissipated from the PV was increased and the stored energy was decreased after the addition of cooling techniques to the PV panel. Energy balance results showed an improvement in the energy dissipated from the cooled PV panels compared to the standard PV by 0.265% in the forced convection cooling system, by 1.99% in the free convection cooling system with finned plate and by 7.35% in the forced convection with finned plate cooling system.
Moreover, the PV panels with cooling systems showed a remarkable increase in money savings and CO2 reduction values compared to the standard PV panel.
The authors declare they have not used Artificial Intelligence (AI) tools in the creation of this article.
The authors declare no conflict of interest.
Tarek Ibrahim: data curation; formal analysis; investigation; methodology; validation; writing original draft. Farouk Hachem: conceptualization; formal analysis; investigation; methodology; project administration; supervision; writing, reviewing and editing. Mohamad Ramadan: Formal analysis; Investigation; Writing, reviewing and editing. Jalal Faraj: Formal analysis; Investigation; Writing, reviewing and editing. Georges El Achkar: Formal analysis; Investigation; Writing, reviewing and editing. Mahmoud Khaled: Conceptualization; Formal analysis; Investigation; Methodology; Project administration; Supervision; Writing, reviewing and editing.
[1] |
Moqbel S (2020) Evaluating bioreactor landfill as an energy source. Int J Energy Environ Eng 12: 23–30. https://doi.org/10.1007/s40095-020-00350-4 doi: 10.1007/s40095-020-00350-4
![]() |
[2] |
Attar A, Albatati F (2020) Wearable thermoelectric generators as energy harvesters for wireless body sensors. Int J Energy Environ Eng 12: 131–149. https://doi.org/10.1007/s40095-020-00365-x doi: 10.1007/s40095-020-00365-x
![]() |
[3] |
Prasad DMR, Senthilkumar R, Lakshmanarao G, et al. (2019) A critical review on thermal energy storage materials and systems for solar applications. AIMS Energy 7: 507–526. https://doi.org/10.3934/energy.2019.4.507 doi: 10.3934/energy.2019.4.507
![]() |
[4] |
Alhousni FK, Ismail FB, Okonkwo PC, et al. (2022) A review of PV solar energy system operations and applications in Dhofar Oman. AIMS Energy 10: 858–884. https://doi.org/10.3934/energy.2022039 doi: 10.3934/energy.2022039
![]() |
[5] |
Azevedo JAR, Mendonça F (2015) Small scale wind energy harvesting with maximum power tracking. AIMS Energy 3: 297–315. https://doi.org/10.3934/energy.2015.3.297 doi: 10.3934/energy.2015.3.297
![]() |
[6] |
Padhee M, Karki R (2018) Bulk system reliability impacts of forced wind energy curtailment. AIMS Energy 6: 505–520. https://doi.org/10.3934/energy.2018.3.505 doi: 10.3934/energy.2018.3.505
![]() |
[7] |
Ali NM, Ammari H (2022) Design of a hybrid wind-solar street lighting system to power LED lights on highway poles. AIMS Energy 10: 177–190. https://doi.org/10.3934/energy.2022010 doi: 10.3934/energy.2022010
![]() |
[8] |
Dewi MP, Setiawan AD, Latief Y, et al. (2022) Investment decisions under uncertainties in geothermal power generation. AIMS Energy 10: 844–857. https://doi.org/10.3934/energy.2022038 doi: 10.3934/energy.2022038
![]() |
[9] |
Schwartzman P, Schwartzman D (2021) Can the 1.5 ℃ warming target be met in a global transition to 100% renewable energy? AIMS Energy 9: 1170–1191. https://doi.org/10.3934/energy.2021054 doi: 10.3934/energy.2021054
![]() |
[10] |
Ludin GA, Amin M, Aminzay A, et al. (2016) Theoretical potential and utilization of renewable energy in Afghanistan. AIMS Energy 5: 1–19. https://doi.org/10.3934/energy.2017.1.1 doi: 10.3934/energy.2017.1.1
![]() |
[11] |
Peura P, Sjöholm P (2015) Sustainable or distributed energy—or both? Clarifying the basic concepts of reforming the energy sector. AIMS Energy 3: 241–254. https://doi.org/10.3934/energy.2015.2.241 doi: 10.3934/energy.2015.2.241
![]() |
[12] |
Katutsi V, Kaddu M, Migisha AG, et al. (2021) Overview of hydropower resources and development in Uganda. AIMS Energy 9: 1299–1320. https://doi.org/10.3934/energy.2021060 doi: 10.3934/energy.2021060
![]() |
[13] |
Danso-Boateng E, Achaw O-W (2022) Bioenergy and biofuel production from biomass using thermochemical conversions technologies—A review. AIMS Energy 10: 585–647. https://doi.org/10.3934/energy.2022030 doi: 10.3934/energy.2022030
![]() |
[14] |
Da Silva MV, Ferreira V, Pinho C (2021) Determination of biomass combustion rate in a domestic fixed bed boiler. AIMS Energy 9: 1067–1096. https://doi.org/10.3934/energy.2021049 doi: 10.3934/energy.2021049
![]() |
[15] |
Gamil MM, Lotfy ME, Hemeida AM, et al. (2021) Optimal sizing of a residential microgrid in Egypt under deterministic and stochastic conditions with PV/WG/Biomass energy integration. AIMS Energy 9: 483–515. https://doi.org/10.3934/energy.2021024 doi: 10.3934/energy.2021024
![]() |
[16] |
Tien TN, Vu Q, Duy VN (2022) Novel designs of thermoelectric generator for automotive waste heat recovery: A review. AIMS Energy 10: 922–942. https://doi.org/10.3934/energy.2022042 doi: 10.3934/energy.2022042
![]() |
[17] |
Hage HE, Ramadan M, Jaber H, et al. (2019) A short review on the techniques of waste heat recovery from domestic applications. Energy Sources A: Recovery Util Environ 42: 3019–3034. https://doi.org/10.1080/15567036.2019.1623940 doi: 10.1080/15567036.2019.1623940
![]() |
[18] |
Murr R, Ramadan M, Khaled M, et al. (2019) An iterative code to investigate heat pump performance improvement by exhaust gases heat recovery. Energy Sources A: Recovery Util Environ 41: 2207–2218. https://doi.org/10.1080/15567036.2018.1555625 doi: 10.1080/15567036.2018.1555625
![]() |
[19] |
Khaled M, Ramadan M (2017) Study of the thermal behavior of multi tube tank in heat recovery from chimney—Analysis and optimization. Heat Transfer Eng 39: 399–409. https://doi.org/10.1080/01457632.2017.1312864 doi: 10.1080/01457632.2017.1312864
![]() |
[20] |
Yang F, Yu Q, Zuo Z, et al. (2019) Thermodynamic analysis of waste heat recovery of aluminum dross in electrolytic aluminum industry. Energy Sources A: Recovery Util Environ 43: 1047–1059. https://doi.org/10.1080/15567036.2019.1634163 doi: 10.1080/15567036.2019.1634163
![]() |
[21] |
Zafar A, Su Y, Li L, et al. (2019) The numerical simulation and wellbore modelling of steam injection and stored heat recovery from light oil reservoir. Energy Sources A: Recovery Util Environ 43: 1–16. https://doi.org/10.1080/15567036.2019.1676331 doi: 10.1080/15567036.2019.1676331
![]() |
[22] | Emery K, Burdick J, Caiyem Y, et al. (1996) Temperature dependence of photovoltaic cells, modules and systems. Conference Record of the Twenty Fifth IEEE Photovoltaic Specialists Conference, Washington, DC, USA, 1275–1278. http://doi.org/10.1109/PVSC.1996.564365 |
[23] |
Yuan W, Ji J, Li Z, et al. (2018) Comparison study of the performance of two kinds of photovoltaic/thermal (PV/T) systems and a PV module at high ambient temperature. Energy 148: 1153–1161. https://doi.org/10.1016/j.energy.2018.01.121 doi: 10.1016/j.energy.2018.01.121
![]() |
[24] |
Mays AE, Ammar R, Hawa M, et al. (2017) Improving photovoltaic panel using finned plate of aluminum. Energy Proc 119: 812–817. https://doi.org/10.1016/j.egypro.2017.07.103 doi: 10.1016/j.egypro.2017.07.103
![]() |
[25] |
Hachem F, Abdulhay B, Ramadan M, et al. (2017) Improving the performance of photovoltaic cells using pure and combined phase change materials—Experiments and transient energy balance. Renewable Energy 107: 567–575. https://doi.org/10.1016/j.renene.2017.02.032 doi: 10.1016/j.renene.2017.02.032
![]() |
[26] |
Nižetić S, Čabo FG, Marinić-Kragić I, et al. (2016) Experimental and numerical investigation of a backside convective cooling mechanism on photovoltaic panels. Energy 111: 211–225. https://doi.org/10.1016/j.energy.2016.05.103 doi: 10.1016/j.energy.2016.05.103
![]() |
[27] |
Al-Waeli AHA, Chaichan MT, Kazem HA, et al. (2018) Comparison study of indoor/outdoor experiments of a photovoltaic thermal PV/T system containing SiC nanofluid as a coolant. Energy 151: 33–44. https://doi.org/10.1016/j.energy.2018.03.040 doi: 10.1016/j.energy.2018.03.040
![]() |
[28] |
Kaldellis JK, Zafirakis D (2012) Experimental investigation of the optimum photovoltaic panels' tilt angle during the summer period. Energy 38: 305–314. https://doi.org/10.1016/j.energy.2011.11.058 doi: 10.1016/j.energy.2011.11.058
![]() |
[29] |
Irshad K, Habib K, Basrawi F, et al. (2017) Study of a thermoelectric air duct system assisted by photovoltaic wall for space cooling in tropical climate. Energy 119: 504–522. https://doi.org/10.1016/j.energy.2016.10.110 doi: 10.1016/j.energy.2016.10.110
![]() |
[30] |
Luo Y, Zhang L, Liu Z, et al. (2018) Numerical evaluation on energy saving potential of a solar photovoltaic thermoelectric radiant wall system in cooling dominant climates. Energy 142: 384–399. https://doi.org/10.1016/j.energy.2017.10.050 doi: 10.1016/j.energy.2017.10.050
![]() |
[31] |
Hussien A, Eltayesh A, El-Batsh HM (2023) Experimental and numerical investigation for PV cooling by forced convection. Alex Eng J 64: 427–440. https://doi.org/10.1016/j.aej.2022.09.006 doi: 10.1016/j.aej.2022.09.006
![]() |
[32] |
Wang Y, Zhao T, Cao Z, et al. (2023) Numerical study on the forced convection enhancement of flat-roof integrated photovoltaic by passive components. Energy Build 289: 113063. https://doi.org/10.1016/j.enbuild.2023.113063 doi: 10.1016/j.enbuild.2023.113063
![]() |
[33] |
Ahmad EZ, Fazlizan A, Jarimi H, et al. (2021) Enhanced heat dissipation of truncated multi-level fin heat sink (MLFHS) in case of natural convection for photovoltaic cooling. Case Stud Therm Eng 28: 101578. https://doi.org/10.1016/j.csite.2021.101578 doi: 10.1016/j.csite.2021.101578
![]() |
[34] |
Yildirim MA, Cebula A, Sułowicz M (2022) A cooling design for photovoltaic panels—Water-based PV/T system. Energy 256: 124654. https://doi.org/10.1016/j.energy.2022.124654 doi: 10.1016/j.energy.2022.124654
![]() |
[35] |
Bevilacqua P, Bruno R, Rollo A, et al. (2022) A novel thermal model for PV panels with back surface spray cooling. Energy 255: 124401. https://doi.org/10.1016/j.energy.2022.124401 doi: 10.1016/j.energy.2022.124401
![]() |
[36] |
Salman AHA, Hilal KH, Ghadhban SA (2022) Enhancing performance of PV module using water flow through porous media. Case Stud Therm Eng 34: 102000. https://doi.org/10.1016/j.csite.2022.102000 doi: 10.1016/j.csite.2022.102000
![]() |
[37] |
Vaillon R, Dupré O, Cal RB, et al. (2018) Pathways for mitigating thermal losses in solar photovoltaics. Sci Rep 8: 13163. https://doi.org/10.1038/s41598-018-31257-0 doi: 10.1038/s41598-018-31257-0
![]() |
[38] |
Glick A, Ali N, Bossuyt J, et al. (2020) Utility-scale solar PV performance enhancements through system-level modifications. Sci Rep 10: 10505. https://doi.org/10.1038/s41598-020-66347-5 doi: 10.1038/s41598-020-66347-5
![]() |
[39] |
Stanislawski BJ, Margairaz F, Cal RB, et al. (2020) Potential of module arrangements to enhance convective cooling in solar photovoltaic arrays. Renewable Energy 157: 851–858. https://doi.org/10.1016/j.renene.2020.04.049 doi: 10.1016/j.renene.2020.04.049
![]() |
[40] |
Glick A, Smith SE, Ali N, et al. (2020) Influence of flow direction and turbulence intensity on heat transfer of utility-scale photovoltaic solar farms. Sol Energy 207: 173–182. https://doi.org/10.1016/j.solener.2020.05.061 doi: 10.1016/j.solener.2020.05.061
![]() |
[41] |
Prilliman M, Smith SE, Stanislawski BJ, et al (2022) Technoeconomic analysis of changing PV array convective cooling through changing array spacing. IEEE J Photovoltaic 12: 1586–1592. https://doi.org/10.1109/jphotov.2022.3201464 doi: 10.1109/jphotov.2022.3201464
![]() |
[42] |
Stanislawski B, Harman T, Silverman TJ, et al. (2022) Row spacing as a controller of solar module temperature and power output in solar farms. J Renewable Sustainable Energy 14: 063702. https://doi.org/10.1063/5.0123641 doi: 10.1063/5.0123641
![]() |
[43] |
Smith SE, Stanislawski BJ, Eng BK, et al. (2022) Viewing convection as a solar farm phenomenon broadens modern power predictions for solar photovoltaics. J Renewable Sustainable Energy 14: 063502. https://doi.org/10.1063/5.0105649 doi: 10.1063/5.0105649
![]() |
[44] |
Glick A, Ali N, Bossuyt J, et al. (2020) Infinite photovoltaic solar arrays: Considering flux of momentum and heat transfer. Renewable Energy 156: 791–803. https://doi.org/10.1016/j.renene.2020.03.183 doi: 10.1016/j.renene.2020.03.183
![]() |
1. | Ayman Abdel-Raheim Amr, Ali A. M. Hassan, Mazen Abdel-Salam, Abou Hashema M. El-Sayed, Active cooling of a photovoltaic module in hot-ambient temperatures: theory versus experiment, 2024, 2194-5756, 10.1515/ijeeps-2023-0398 | |
2. | Tarek Ibrahim, Modar El Hazar, Farouk Hachem, Mahmoud Khaled, A comprehensive experimental study of cooling photovoltaic panels using phase change materials under free and forced convection – Experiments and transient analysis, 2024, 81, 2352152X, 110511, 10.1016/j.est.2024.110511 | |
3. | Tarek Ibrahim, Jalal Faraj, Hicham El Hage, Khaled Chahine, Mehdi Mortazavi, Mahmoud Khaled, Theoretical parametric study of photovoltaic cooling by water—Energy enhancement and environmental-economic insights, 2024, 24, 26662027, 100988, 10.1016/j.ijft.2024.100988 | |
4. | Tarek Ibrahim, Jalal Faraj, Hicham El Hage, Rani Taher, Samer Ali, Mahmoud Khaled, Parametric enviro-economic analysis of cooling photovoltaic panels with phase change materials, 2025, 27, 26662027, 101151, 10.1016/j.ijft.2025.101151 |
Standard PV panel | Free convection cooling system with finned plate | Forced convection cooling system | Forced convection cooling system with finned plate | |
Efficiency [%] | 0 | 2.55 | 2.10 | 3.01 |
Power [Watt] | 0 | 3.2 | 2.76 | 3.81 |
Surface temperature difference [℃] | 0 | –2.46 | –1.30 | –4.94 |
Panels | Price [$] | Savings [$] | ROI period [years] |
Forced convection with finned plate PV | 50 | 8.64 | 5.79 |
Forced convection PV | 40 | 8.21 | 4.87 |
Free convection with finned plate PV | 40 | 8.39 | 4.77 |
Standard PV | 30 | 7.11 | 4.22 |
Configuration | ˙Eout/˙Ein | ˙Est/˙Ein | ˙Egen/˙Ein |
Control PV panel | 0.679 | 0.166 | 0.154 |
PV under forced convection | 0.682 | 0.143 | 0.175 |
PV under free convection with fins | 0.695 | 0.129 | 0.175 |
PV under forced convection with fins | 0.753 | 0.060 | 0.187 |
Standard PV panel | Free convection cooling system with finned plate | Forced convection cooling system | Forced convection cooling system with finned plate | |
Efficiency [%] | 0 | 2.55 | 2.10 | 3.01 |
Power [Watt] | 0 | 3.2 | 2.76 | 3.81 |
Surface temperature difference [℃] | 0 | –2.46 | –1.30 | –4.94 |
Panels | Price [$] | Savings [$] | ROI period [years] |
Forced convection with finned plate PV | 50 | 8.64 | 5.79 |
Forced convection PV | 40 | 8.21 | 4.87 |
Free convection with finned plate PV | 40 | 8.39 | 4.77 |
Standard PV | 30 | 7.11 | 4.22 |
Configuration | ˙Eout/˙Ein | ˙Est/˙Ein | ˙Egen/˙Ein |
Control PV panel | 0.679 | 0.166 | 0.154 |
PV under forced convection | 0.682 | 0.143 | 0.175 |
PV under free convection with fins | 0.695 | 0.129 | 0.175 |
PV under forced convection with fins | 0.753 | 0.060 | 0.187 |