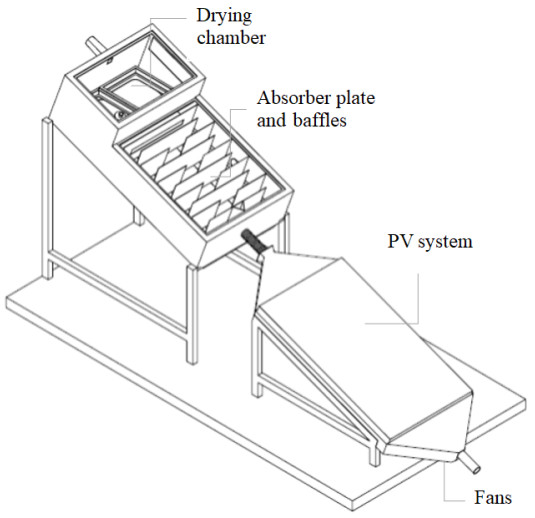
This paper presents a hybrid solar dryer with baffles disposed of on the solar collector. When the levels of solar radiation are low, an electrical heater is used to increase the drying air temperature. A photovoltaic system feeds the electrical heater and the fans, and it is also used to preheat the drying air, increasing the temperature at the inlet of the solar collector. Experimental results of corn drying indicated that the baffles augmented the energy efficiency of the system (from 23.5 to 24.9%) and the temperature rise in the solar collector (from 13.5 to 20.2 ℃), reducing the time required for the corn to reach the final desired moisture content.
Citation: Cristiana Brasil Maia, Gisele Mol da Silva, Luiz Felippe Guardia Bianchi, André Guimarães Ferreira. Performance study of a baffled solar dryer[J]. AIMS Energy, 2021, 9(6): 1136-1146. doi: 10.3934/energy.2021052
[1] | Dessie Tadele Embiale, Dawit Gudeta Gunjo, Chandraprabu Venkatachalam, Mohanram Parthiban . Experimental investigation and exergy and energy analysis of a forced convection solar fish dryer integrated with thermal energy storage. AIMS Energy, 2022, 10(3): 412-433. doi: 10.3934/energy.2022021 |
[2] | Nadwan Majeed Ali, Handri Ammari . Design of a hybrid wind-solar street lighting system to power LED lights on highway poles. AIMS Energy, 2022, 10(2): 177-190. doi: 10.3934/energy.2022010 |
[3] | Xiaolong Wang, Lingning Zhang, Yuan Chang, Yang Song, Liang Wang . Numerical simulation study on heat performance and pressure loss of solar air heater with sinusoidal baffles. AIMS Energy, 2024, 12(3): 617-638. doi: 10.3934/energy.2024029 |
[4] | Fadhil Khadoum Alhousni, Firas Basim Ismail, Paul C. Okonkwo, Hassan Mohamed, Bright O. Okonkwo, Omar A. Al-Shahri . A review of PV solar energy system operations and applications in Dhofar Oman. AIMS Energy, 2022, 10(4): 858-884. doi: 10.3934/energy.2022039 |
[5] | Virendra Sharma, Lata Gidwani . Recognition of disturbances in hybrid power system interfaced with battery energy storage system using combined features of Stockwell transform and Hilbert transform. AIMS Energy, 2019, 7(5): 671-687. doi: 10.3934/energy.2019.5.671 |
[6] | Michael O. Dioha, Atul Kumar . Rooftop solar PV for urban residential buildings of Nigeria: A preliminary attempt towards potential estimation. AIMS Energy, 2018, 6(5): 710-734. doi: 10.3934/energy.2018.5.710 |
[7] | Jin H. Jo, Kadi Ilves, Tyler Barth, Ellen Leszczynski . Implementation of a large-scale solar photovoltaic system at a higher education institution in Illinois, USA. AIMS Energy, 2017, 5(1): 54-62. doi: 10.3934/energy.2017.1.54 |
[8] | Aaron St. Leger . Demand response impacts on off-grid hybrid photovoltaic-diesel generator microgrids. AIMS Energy, 2015, 3(3): 360-376. doi: 10.3934/energy.2015.3.360 |
[9] | Mulualem T. Yeshalem, Baseem Khan . Design of an off-grid hybrid PV/wind power system for remote mobile base station: A case study. AIMS Energy, 2017, 5(1): 96-112. doi: 10.3934/energy.2017.1.96 |
[10] | Chris Thankan, August Winters, Jin Ho Jo, Matt Aldeman . Feasibility of applying Illinois Solar for All (ILSFA) to the Bloomington Normal Water Reclamation District. AIMS Energy, 2021, 9(1): 117-137. doi: 10.3934/energy.2021007 |
This paper presents a hybrid solar dryer with baffles disposed of on the solar collector. When the levels of solar radiation are low, an electrical heater is used to increase the drying air temperature. A photovoltaic system feeds the electrical heater and the fans, and it is also used to preheat the drying air, increasing the temperature at the inlet of the solar collector. Experimental results of corn drying indicated that the baffles augmented the energy efficiency of the system (from 23.5 to 24.9%) and the temperature rise in the solar collector (from 13.5 to 20.2 ℃), reducing the time required for the corn to reach the final desired moisture content.
The world is facing a significant increase in the population, which entails an increase in food production [1]. It is important not only to increase food production but also to reduce the loss and waste of food. About one-third of the production of food for humanity is lost or wasted [2]. Reducing food waste is an increasingly urgent challenge faced worldwide. Drying is a greatly advanced form of food preservation, and it has been conducted since olden times [3]. The reduction in product moisture content can reduce the action of enzymes, bacteria, fungi, and molds [4]. However, drying consumes a huge amount of energy [5], usually from biomass, electricity, fossil fuels, natural gas, and solar energy [6]. These thermal drying methods were responsible for about 10–20% of world energy consumption by the industries in 2011 [7]. Solar energy is one of the most relevant renewable energy sources [8]. It is the major source of non-conventional energy and can be used to replace conventional methods of drying.
In open sun drying (OSD), the products are exposed directly to solar radiation [9]. It is a cheap method, but the products can easily be contaminated by dust, pollution, and damages from animals, birds, or insects. Furthermore, they can suffer degradation through exposure to storms, dew, or additional losses due to insufficient or non-uniform drying conditions [6]. Solar dryers are interesting choices to reduce losses from OSD and are being extensively studied. Solar dryers are classified as direct or indirect types, depending on where the solar radiation reaches. In the direct type, the solar radiation directly reaches the products, placed inside a drying chamber. In the indirect type, the drying air is heated by a solar collector [10]. One of the main drawbacks of solar dryers is their dependence on weather conditions. To minimize or overcome this disadvantage, hybrid solar dryers use additional energy from other sources. The additional energy is provided by different sources. A new configuration of a hybrid dryer, consisting of a solar-gas collector and a drying chamber, was proposed and built by [11]. When the dryer operated in solar mode, the thermal efficiency was 42%, in gas mode, 37%, and in hybrid mode, 40%. A numerical analysis of a hybrid geothermal PCM flat plate solar collector dryer was developed by [12]. The dryer presented superior efficiency and productivity, but the authors described high initial costs and a long payback period. A solar-biomass hybrid greenhouse dryer was developed and built in Kenya [13]. Banana slices were dried in the dryer operating in three different modes: solar, biomass, and solar-biomass, with average hourly exergy efficiencies of 65, 59, and 67%. A forced convection solar dryer using solar energy and electrical energy was used to assess the drying of apple peels [14]. The authors evaluated the influence of the temperature and volumetric rate of the drying air on the energy efficiency of the system, concluding that the energy efficiency increases with the temperature and with the reduction of the airflow rate. Solar energy can be employed as an additional energy source in photovoltaic (PV) panels. An indirect solar dryer was used to dry green chili and okra [15]. PV panels are used to run the inlet fans. A hybrid solar greenhouse dryer coupled to a PV system and solar collectors was evaluated in Saudi Arabia to dry tomatoes [16]. A photovoltaic-thermal (PVT) hybrid solar dryer using evacuated tube collectors was studied by [17] to dry cassava in India.
An additional energy source is important to ensure a continuous energy supply to the drying air, promoting uniform drying conditions. The thermal efficiency of the dryer can be enhanced through geometric modifications, such as the inclusion of fins or baffles. The drying of cassava roots chips in an indirect solar dryer was evaluated by [18], comparing the results with and without the inclusion of a solar collector. The effect of increasing the path of the drying air by integration of four black painted transverse fins was evaluated by [19]. A CFD analysis was performed by [5] to identify the influence of fins on the thermal storage system of an indirect dryer, comparing the results of the system with and without fins. A numerical analysis was also accomplished by [3], evaluating an indirect solar dryer without thermal energy storage (TES), with TES having a phase change material (PCM), and with TES with fins and PCM. A numerical and experimental analysis of the influence of square-spiral fins on a quadruple-flow solar air collector was performed by [8]. Performance tests of solar drying were performed, and the authors concluded that the developed system was successful in improving energy capture by the solar collector. A numerical and experimental study of the influence of perforated baffles in the solar collector of a dryer was conducted by [20]. The system was studied with parallel-pass with zero, single and double baffles. For the drying of celery root, the system operating with double baffles presented a higher average and maximum instantaneous thermal efficiency. A V-grooved solar collector with baffles was used to increase the performance of a solar cabinet dryer for drying potato chips [21]. The results were compared with a flat plate solar collector in the dryer. It was observed an increase in the efficiency of the system with the solar collector with baffles.
Literature survey reveals the use of PV panels in several hybrid solar dryers, but it is scarce in the combined use of PV panels and baffles. Also, the generated energy by the PV system is generally employed only to run an electric heater and/or fans. In this paper, the energy provided by the PV system feeds an electrical heater and fans, but the PV module is also employed to increase the drying air temperature, which is not seen in the literature. An analysis of corn grains inside this dryer is presented in [22], with a special focus on the First Law of Thermodynamics. The analysis was improved, including an assessment of the system by the Second Law of Thermodynamics in [23]. In a subsequent analysis [9], the dryer was assessed using different control volumes in the analysis, concluding that the control volume defined plays an important role in the efficiency values. In the present work, the dryer was modified to incorporate baffles in the solar collector. Experimental tests were conducted during the summer for the system with and without baffles operating in Belo Horizonte, Brazil (latitude 19.9°S and longitude 43.8°W), and the drying curves of corn and the energy efficiency of the system were compared.
The solar dryer was designed and installed in Belo Horizonte, Brazil (19.9°S latitude and 43.8°W longitude), which has an Aw (Equatorial savannah with dry winter) climate, according to the Koppen-Geiger climate classification [24,25]. The experimental tests were conducted in the summer, on two consecutive days. On the first day, the system operated with baffles, and on the second day, without baffles.
The dryer consists of fans, a PV system, a solar collector, and a drying chamber (Figure 1). The width is 1000 mm, the length is1800 mm and the height is 500 mm. The PV system is composed of a PV module, a charge controller, and two batteries, and it feeds the fans, allowing the system to operate without any input of external electricity. The solar collector is composed of an absorber plate and baffles.
The airflow enters the system forced by the fans and flows inside a duct under the PV module, in which it is heated by the module bottom surface enabling the drying air to reach the solar collector with a temperature higher than the ambient temperature. Furthermore, it is well known that high surface temperatures reduce PV efficiency [26]. The heat transfer from the PV surface by the drying air has beneficial effects of increasing its efficiency [27]. After the PV, the air enters the solar collector and is heated by the absorber plate. The purpose of the baffles is to increase the heat transfer area, increasing the system efficiency. The drying air is directed to the drying chamber where the drying products are placed in trays. The wet airflow leaves the system through a circular tube.
16 kg of hybrid corn grains, hard type, with an initial moisture content of 20% w.b., were employed in the experiment. The initial wet basis moisture content was determined by inserting a sample of the products in a stove at 105 ℃, for a period of 24 h, and evaluating the mass before and after this period.
The temperature of the airflow and the wall temperatures were measured using K-type thermocouples. The inlet and outlet air humidity were measured using humidity sensors (AKSO, AK174 model). The mass flow rate was determined based on the inlet airflow velocity, measured using an ICEL (NA-4870) anemometer. The solar radiation was measured using a pyranometer (Hukseflux thermal sensor, SR05, DA2 model). The samples of corn were weighted with a digital electronic balance (Toledo, 9094 model). An uncertainty analysis was performed based on [28], and the results are shown in Table 1.
Measured variable | Expanded uncertainty |
Temperature (k-type thermocouple) | ±2.2 ℃ |
Temperature (Thermo-psychrometer) | ±0.5% |
Relative humidity | ±3% RH |
Solar radiation | ±1% |
Mass | ±1 g |
Velocity | ±3% |
Initial moisture content | ±1% |
Instantaneous moisture content | ±2% |
The conservation equations for mass and energy are given by [29].
(˙mda)in=(˙mda)out=˙mda | (1) |
win˙mda+(˙mstH2O)p=wout˙mda | (2) |
˙mda, (˙mda)in, (˙mda)out, (˙mstH2O)in, (˙mstH2O)out and (˙mstH2O)p are, respectively, the mass flow rate of the dry air, of the dry air at the inlet and outlet of the drying system, and of the humidity of the product. win and wout are, respectively, the air absolute humidity at the inlet and outlet of the drying system.
Neglecting the mechanical work in the process, the First Law of Thermodynamics is given by [30]:
˙Q=∑out˙m(h+12v2+gz)−∑in˙m(h+12v2+gz) | (3) |
where ˙m is the mass flow rate, h is the specific enthalpy, v is the velocity, and z is the height. ˙Q represents the heat transfer, determined by the solar radiation transferred to the system by the PV module, the absorber plate, and the top surface of the drying chamber.
The energy efficiency ηI is the ratio between the energy expended and the energy provided to the system:
ηI=∑out˙m(h+12v2+gz)−∑in˙m(h+12v2+gz)(Am+Aa+Ac)G | (4) |
Am, Aa and Ac represent, respectively, the areas of the PV module surface, the absorber plate, and the top of the drying chamber. G is the solar irradiation.
For each product, the drying curve defines the drying characteristics for that product at specific conditions, showing the drying rate or moisture content versus drying time.
The initial wet basis moisture content can be expressed as [7]:
Wsp=(msp)i−(msp)e(msp)i | (5) |
(msp)i and (msp)e represent, respectively, the initial mass and the final mass of the sample placed in the oven. The instantaneous wet basis moisture content is given by [31]:
Wx=1−[(mp)i(mp)xx(100−Wsp)] | (6) |
(mp)i and (mp)x are, respectively, the initial and the instantaneous product mass.
Figure 2 presents the incident solar radiation and ambient temperature. The sky was partially overcast during the tests. On the first test (with baffles), the maximum solar radiation reached was 1040 W/m2, with an average value of 805 W/m2. The maximum ambient temperature was 37 ℃, with an average of 32 ℃. On the second test (without baffles), the maximum solar radiation was 1110 W/m2, with an average value of 752 W/m2. The maximum ambient temperature was 38 ℃, with an average of 34 ℃. During the tests, the average velocity at the system inlet and volumetric flow rate were, respectively, 2.6 m/s and 0.010 m3/s.
The temperatures in the solar collector inlet and outlet are also shown in Figure 2. It can be seen that, as expected, the drying air temperature increases through the solar collector. For the first day, it was observed a sudden decrease of the solar radiation, decreasing the ambient temperature and the inlet and outlet solar collector temperatures. Even with the lower values of incident solar radiation in the afternoon, the system operating with baffles obtained higher temperatures at the solar collector outlet. It is worth mentioning that the temperature rise was higher for the system with baffles (20.2 ℃, compared with the system without baffles, 13.5 ℃), as indicated in Figure 3. For both tests, the temperature rise was small at the beginning of the day. With the increase of the solar radiation levels, the temperature rise in the solar collector increased.
The drying curves are shown in Figure 4. The moisture content (wet basis) is presented in a nondimensional form, with the ratio between instantaneous moisture content and the initial moisture content versus drying time. In the initial period, when the surface of the products is saturated and evaporation occurs unceasingly [7], the rate at which the moisture is removed is mostly dependent on the ambient conditions and the initial moisture content of the products [32]. The small variation of the drying rates at the beginning may be attributed to the small variation in the temperature inside the drying chamber at the beginning of the drying test in both tests. The initial moisture content of the products was higher in the test without baffles, explaining the initial higher rates for this test. After the middle of the day, the solar radiation levels dropped in the test with the baffles, reducing the temperature at the inlet of the solar collector. However, the inclusion of baffles increased the heat remotion from the baffles, increasing the temperature inside the solar collector and increasing the drying rate.
The energy efficiency is presented in Figure 5. The energy efficiency depends mainly on the variation of the enthalpy from the inlet to the outlet and the incident solar radiation. The average energy efficiency was higher for the dryer with baffles (24.9%), when compared to the dryer without baffles (23.5%). In the morning, the temperature rise in the solar collector is slightly higher in the test with baffles. However, as the solar radiation is significantly higher, the instantaneous efficiency decreases. In the late morning and afternoon, the temperature rise was higher, increasing the efficiency. Occasional drops in the efficiency may be attributed to the presence of clouds. The highest values of efficiency found are attributed to sudden falls of the solar radiation, as seen in Figure 2. The energy efficiency values are consistent with the literature values. A comprehensive review of the energy efficiency of solar dyers was performed by [6], describing values from 21 to 69%. The drying of apple slices and mint leaves in a double-pass solar air dryer resulted in energy efficiencies varying between 2.20% and 26.46% [33]. An average efficiency of 53% was found for the drying of mango slices in an indirect forced convection solar dryer [34]. It is important to highlight, however, that the energy efficiency depends on the type of solar dryer and the dried product.
This work presents experimental results of a hybrid solar dryer, coupled to a PV system, used to dry corn. It was assessed the effect of the use of baffles in the solar collector. Results indicated that the use of baffles increased the temperature rise of the air in the solar collector, increasing the drying air temperature. For an average solar radiation of approximately 780 W/m2, the temperature rise in the solar collector increased from 13.5 ℃ to 20.2 ℃ when using the baffles. It resulted in a higher average energy efficiency of the system (from 23.5 to 24.9%), and in a reduction of the drying time. It can be concluded, therefore, that the use of baffles improved the performance of the dryer, with low costs increase.
This study was financed in part by the Coordenação de Aperfeiçoamento de Pessoal de Nível Superior—Brasil (CAPES)—Finance Code 001. The authors are also thankful to CNPq, FAPEMIG, CEFET-MG, and PUC Minas.
The authors declare no conflict of interest.
Cristiana Maia: Conceptualization, Writing—Original draft presentation, Gisele Silva: Investigation, Luiz Bianchi: Resources, André Ferreira: Resources, Writing- Reviewing and Editing.
[1] |
Udomkun P, Romuli S, Schock S, et al. (2020) Review of solar dryers for agricultural products in Asia and Africa: An innovation landscape approach. J Environ Manage 268: 110730. doi: 10.1016/j.jenvman.2020.110730
![]() |
[2] |
Shabanali H, Aramyan LH, Sijtsema SJ, et al. (2021) The relationship between household food waste and food security in Tehran city : The role of urban women in household management. Ind Mark Manage 97: 71-83. doi: 10.1016/j.indmarman.2021.06.016
![]() |
[3] |
Madhankumar S, Viswanathan K, Wu W (2021) Energy, exergy and environmental impact analysis on the novel indirect solar dryer with fins inserted phase change material. Renewable Energy 176: 280-294. doi: 10.1016/j.renene.2021.05.085
![]() |
[4] |
Mohana Y, Mohanapriya R, Anukiruthika T, et al. (2020) Solar dryers for food applications: Concepts, designs, and recent advances. Sol Energy 208: 321-344. doi: 10.1016/j.solener.2020.07.098
![]() |
[5] |
Yadav S, Chandramohan VP (2020) Performance comparison of thermal energy storage system for indirect solar dryer with and without finned copper tube. Sustainable Energy Technol Assess 37: 100609. doi: 10.1016/j.seta.2019.100609
![]() |
[6] |
Lingayat AB, Chandramohan VP, Raju VRK, et al. (2020) A review on indirect type solar dryers for agricultural crops-Dryer setup, its performance, energy storage and important highlights. Appl Energy 258: 114005. doi: 10.1016/j.apenergy.2019.114005
![]() |
[7] |
Belessiotis V, Delyannis E (2011) Solar drying. Sol Energy 85: 1665-1691. doi: 10.1016/j.solener.2009.10.001
![]() |
[8] |
Khanlari A, Sözen A, Afshari F, et al. (2021) Energy-exergy and sustainability analysis of a PV-driven quadruple-flow solar drying system. Renewable Energy 175: 1151-1166. doi: 10.1016/j.renene.2021.05.062
![]() |
[9] |
Silva GM da, Ferreira AG, Coutinho RM, et al. (2020) Thermodynamic analysis of a sustainable hybrid dryer. Sol Energy 208: 388-398. doi: 10.1016/j.solener.2020.08.014
![]() |
[10] |
Kamarulzaman A, Hasanuzzaman M, Rahim NA (2021) Global advancement of solar drying technologies and its future prospects: A review. Sol Energy 221: 559-582. doi: 10.1016/j.solener.2021.04.056
![]() |
[11] |
Zoukit A, El Ferouali H, Salhi I, et al. (2019) Simulation, design and experimental performance evaluation of an innovative hybrid solar-gas dryer. Energy 189: 116279. doi: 10.1016/j.energy.2019.116279
![]() |
[12] |
Ananno AA, Masud MH, Dabnichki P, et al. (2020) Design and numerical analysis of a hybrid geothermal PCM flat plate solar collector dryer for developing countries. Sol Energy 196: 270-286. doi: 10.1016/j.solener.2019.11.069
![]() |
[13] |
Kiburi FG, Kanali CL, Kituu GM, et al. (2020) Performance evaluation and economic feasibility of a Solar-Biomass hybrid greenhouse dryer for drying banana slices. Renewable Energy Focus 34: 60-68. doi: 10.1016/j.ref.2020.06.009
![]() |
[14] |
Moussaoui H, Bahammou Y, Tagnamas Z, et al. (2021) Application of solar drying on the apple peels using an indirect hybrid solar-electrical forced convection dryer. Renewable Energy 168: 131-140. doi: 10.1016/j.renene.2020.12.046
![]() |
[15] |
Goud M, Reddy MVV, Chandramohan VP, et al. (2019) A novel indirect solar dryer with inlet fans powered by solar PV panels: Drying kinetics of Capsicum Annum and Abelmoschus esculentus with dryer performance. Sol Energy 194: 871-885. doi: 10.1016/j.solener.2019.11.031
![]() |
[16] |
Azam MM, Eltawil MA, Amer BMA (2020) Thermal analysis of PV system and solar collector integrated with greenhouse dryer for drying tomatoes. Energy 212: 118764. doi: 10.1016/j.energy.2020.118764
![]() |
[17] |
Veeramanipriya E, Umayal Sundari AR (2021) Performance evaluation of hybrid photovoltaic thermal (PVT) solar dryer for drying of cassava. Sol Energy 215: 240-251. doi: 10.1016/j.solener.2020.12.027
![]() |
[18] |
Simo-Tagne M, Tagne Tagne A, Ndukwu MC, et al. (2021) Numerical study of the drying of cassava roots chips using an indirect solar dryer in natural convection. AgriEngineering 3: 138-157. doi: 10.3390/agriengineering3010009
![]() |
[19] |
Mahmood AJ, Aldabbagh LBY, Egelioglu F (2015) Investigation of single and double pass solar air heater with transverse fins and a package wire mesh layer. Energy Convers Manage 89: 599-607. doi: 10.1016/j.enconman.2014.10.028
![]() |
[20] |
Khanlari A, Güler HÖ, Tuncer AD, et al. (2020) Experimental and numerical study of the effect of integrating plus-shaped perforated baffles to solar air collector in drying application. Renewable Energy 145: 1677-1692. doi: 10.1016/j.renene.2019.07.076
![]() |
[21] |
Sethi CK, Acharya SK, Ghanem SR, et al. (2021) Exergy, energy and economic analysis of a V-groove assist rotating tray type solar cabinet dryer for drying potato chips. J Stored Prod Res 93: 101861. doi: 10.1016/j.jspr.2021.101861
![]() |
[22] | Silva GM da, Ferreira AG, Coutinho RM, et al. (2020) Experimental analysis of corn drying in a sustainable solar dryer. J Adv Res Fluid Mech Therm Sci, 67. |
[23] |
Silva GM da, Ferreira AG, Coutinho RM, et al. (2021) Energy and exergy analysis of the drying of corn grains. Renewable Energy 163: 1942-1950. doi: 10.1016/j.renene.2020.10.116
![]() |
[24] |
Peel MC, Finlayson BL, McMahon TA (2007) Updated world map of the Köppen-Geiger climate classification. Hydrol Earth Syst Sci 11: 1633-1644. doi: 10.5194/hess-11-1633-2007
![]() |
[25] | Reboita MS, Rodrigues M, Silva LF, et al. (2016) Aspectos climáticos do estado de Minas Gerais. Revista Bras Climatologia 18: 307-326. |
[26] |
Rahmatmand A, Harrison SJ, Oosthuizen PH (2020) An innovative method to control surface temperature of a rooftop photovoltaic system. Sol Energy 195: 581-591. doi: 10.1016/j.solener.2019.11.043
![]() |
[27] | Odeh S, Behnia M (2009) Improving photovoltaic module efficiency using water cooling. Heat Transfer Engineering, 30. |
[28] | Group 1 of the Joint Committee for Guides in Metrology (JCGM/WG1) (2008) Evaluation of measurement data-Guide to the expression of uncertainty in measurement. International Organization for Standardization Geneva ISBN 50: 134. |
[29] |
Dincer I, Rosen MA (2007) Exergy, environment and sustainable development, EXERGY, 36-59. doi: 10.1016/B978-008044529-8.50006-9
![]() |
[30] | Moran MJ, Shapiro HN (2006) Fundamentals of Engineering Thermodynamics, 5th Edition. |
[31] |
Ferreira AG, Gonçalves LM, Maia CB (2014) Solar drying of a solid waste from steel wire industry. Appl Therm Eng 73: 104-110. doi: 10.1016/j.applthermaleng.2014.07.047
![]() |
[32] |
Ekechukwu OV (1999) Review of solar-energy drying systems I: an overview of drying principles and theory. Energy Convers Manage 40: 593-613. doi: 10.1016/S0196-8904(98)00092-2
![]() |
[33] |
Şevik S, Aktaş M, Dolgun EC, et al. (2019) Performance analysis of solar and solar-infrared dryer of mint and apple slices using energy-exergy methodology. Sol Energy 180: 537-549. doi: 10.1016/j.solener.2019.01.049
![]() |
[34] |
Wang W, Li M, Hassanien RHE, et al. (2018) Thermal performance of indirect forced convection solar dryer and kinetics analysis of mango. Appl Therm Eng 134: 310-321. doi: 10.1016/j.applthermaleng.2018.01.115
![]() |
1. | Zeinab Rezvani, Hamid Mortezapour, Mehran Ameri, Hamid‐Reza Akhavan, Selçuk Arslan, Energy and exergy analysis of a water bed‐infrared dryer coupled with a photovoltaic‐thermal collector, 2022, 45, 0145-8876, 10.1111/jfpe.14058 |
Measured variable | Expanded uncertainty |
Temperature (k-type thermocouple) | ±2.2 ℃ |
Temperature (Thermo-psychrometer) | ±0.5% |
Relative humidity | ±3% RH |
Solar radiation | ±1% |
Mass | ±1 g |
Velocity | ±3% |
Initial moisture content | ±1% |
Instantaneous moisture content | ±2% |