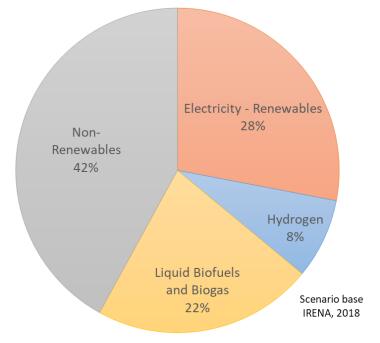
Citation: Antzela Fivga, Lais Galileu Speranza, Carolina Musse Branco, Miloud Ouadi, Andreas Hornung. A review on the current state of the art for the production of advanced liquid biofuels[J]. AIMS Energy, 2019, 7(1): 46-76. doi: 10.3934/energy.2019.1.46
[1] | Eric Danso-Boateng, Osei-Wusu Achaw . Bioenergy and biofuel production from biomass using thermochemical conversions technologies—a review. AIMS Energy, 2022, 10(4): 585-647. doi: 10.3934/energy.2022030 |
[2] | Gbadebo Oladosu . An economic evaluation of alternative biofuel deployment scenarios in the USA. AIMS Energy, 2017, 5(3): 374-396. doi: 10.3934/energy.2017.3.374 |
[3] | Shouyun Cheng, Lin Wei, Xianhui Zhao, Yinbin Huang, Douglas Raynie, Changling Qiu, John Kiratu, Yong Yu . Directly catalytic upgrading bio-oil vapor produced by prairie cordgrass pyrolysis over Ni/HZSM-5 using a two stage reactor. AIMS Energy, 2015, 3(2): 227-240. doi: 10.3934/energy.2015.2.227 |
[4] | Michael E. Salassi, Lawrence L. Falconer, Tyler B. Mark, Michael A. Deliberto, Brian M. Hilbun, Todd L. Cooper . Economic Potential for Energy Cane Production as a Cellulosic Biofuel Feedstock in the Southeastern United States. AIMS Energy, 2015, 3(1): 25-40. doi: 10.3934/energy.2015.1.25 |
[5] | Pallav Purohit, Subash Dhar . Lignocellulosic biofuels in India: current perspectives, potential issues and future prospects. AIMS Energy, 2018, 6(3): 453-486. doi: 10.3934/energy.2018.3.453 |
[6] | Anil Markandya, Kishore Dhavala, Alessandro Palma . The role of flexible biofuel policies in meeting biofuel mandates. AIMS Energy, 2018, 6(3): 530-550. doi: 10.3934/energy.2018.3.530 |
[7] | Lihao Chen, Hu Wu, Kunio Yoshikawa . Research on upgrading of pyrolysis oil from Japanese cedar by blending with biodiesel. AIMS Energy, 2015, 3(4): 869-883. doi: 10.3934/energy.2015.4.869 |
[8] | Gustavo Aguilar, Pranjali D. Muley, Charles Henkel, Dorin Boldor . Effects of biomass particle size on yield and composition of pyrolysis bio-oil derived from Chinese tallow tree (Triadica Sebifera L.) and energy cane (Saccharum complex) in an inductively heated reactor. AIMS Energy, 2015, 3(4): 838-850. doi: 10.3934/energy.2015.4.838 |
[9] | Yadessa Gonfa Keneni, Jorge Mario Marchetti . Oil extraction from plant seeds for biodiesel production. AIMS Energy, 2017, 5(2): 316-340. doi: 10.3934/energy.2017.2.316 |
[10] | Mikael Lantz, Emma Kreuger, Lovisa Björnsson . An economic comparison of dedicated crops vs agricultural residues as feedstock for biogas of vehicle fuel quality. AIMS Energy, 2017, 5(5): 838-863. doi: 10.3934/energy.2017.5.838 |
The need for energy security, as well as, environmental concerns, are the main drivers behind the growth of bioenergy and consequently biofuels, in recent years. In 2009 the EU issued a mandatory environmental directive, Renewable Energy Directive 2009/28/EC, regarding renewable energy, to address environmental problems that have arisen from the use of fossil fuels in energy generation. This directive specified that 20% of all energy in the EU-27 should be from renewable sources, with 10% of road transport energy coming from biofuels, by the end of 2020. Moreover, in 2012, an amendment of the directive required that first generation derived biofuels should be limited to 5%, reinforcing the need for further development of second-generation advanced biofuels. A report from the International Renewable Energy Agency (IRENA) projects a scenario with 22% of transportation fuels coming from liquid biofuels and biogas by 2050 (Figure 1) [1].
In addition to changes in legislation, the use of fossil fuels releases greenhouse gases (GHG) into the atmosphere and contributes to the atmospheric CO2 concentration, which is directly related with climate change. Subsequently, there is renewed interest in the production of liquid biofuels from biomass since their use has the potential to reduce CO2 emissions [2]. "First generation" biofuels can contribute to CO2 emissions reduction, but they compete with land used for arable and pastoral farming; therefore, first generation biofuels are not included in this review. "Second generation" liquid biofuels are produced from non-food biomass, including agricultural and forest biomass residues, dedicated energy crops, lignocellulosic fraction of municipal and industrial solid waste [3]. Furthermore, waste vegetable oils and waste animal fats can be used for the generation of liquid biofuels. The same type of biomass can generate different sustainable liquid fuels depending on the applied technology. Figure 2 illustrates the fuels discussed in this paper. Challenges associated with the production of such fuels include cost effectiveness and technical issues.
Advanced liquid biofuels that are studied in this review include bioethanol, biodiesel, bio-methanol, dimethyl-ether, bio-oil, biobutanol, and biojet. Such biofuels (i.e. biodiesel and bioethanol) are characterized either by their ability to blend with existing petroleum fuels, or by their ability to be used in existing internal combustion engines. To preserve the integrity of engine manufacturer warrantees and ensure the same engine combustion, emissions, and performance output, second generation liquid biofuels are required to have similar properties to existing petroleum fuels. These properties among others include heating value, octane number, viscosity, water content, and flash point. Figure 3 shows how fossil fuels can be replaced by sustainable biofuels and their application.
In order to produce biofuels, researchers are developing and improving different pathways that can be divided into two main conversion routes, thermochemical or biochemical. The most studied biochemical routes are fermentation and transesterification processes, the most studied thermochemical routes are pyrolysis, gasification, and Fischer Tropsch processes. The sustainability of the pathways for the production of liquid biofuels significantly depends on the type of feedstock used and the end product specifications. Therefore, there is no best pathway or solution to produce renewable liquid fuels. This paper aims to provide an up to date review on the most promising second generation liquid biofuels and the sustainable pathways for their production. Challenges concerning the commercialisation of these biofuels are also discussed.
Bioethanol is commonly produced from the fermentation of sugars and can be used as a petrol substitute to fuel spark ignition engines. Another pathway is through fermentation of syngas. Petrol is a liquid consisting of C4–C12 hydrocarbons and is produced by cracking crude oil. Ethanol can be used in its pure form (E-100) or blended with petrol. It should be noted that the use of pure ethanol (E-100) requires engine modifications to overcome issues associated with fuel compression, timing of injection, and engine corrosion. Bioethanol can be blended up to 10% and 15 % with petrol according to the requirements in the EN 15376 and ASTM D4806 specifications, respectively. The important properties of pure ethanol (E100) and its 10% blend with petrol (E10) can be seen in Table 1 and are compared with pure petrol.
Properties | Petrol | E-100 | E-10 |
Viscosity mm2/s | 0.48–0.84 | 1.57 (20 ℃) | 0.53 (30 ℃) |
Flash Point ℃ | −65 | 13 | −40 |
RON ℃ | 86.4–100 | 108.6–114 | 87.4–94 |
MON ℃ | 80–98.8 | 89.7–112 | 86–99.9 |
Octane number | 86–94 | 98–100 | - |
Cloud point ℃ | −22 | - | 8 |
Pour point ℃ | (−17)–(−19) | - | 0 |
MJ/Kg | 41.9–44.4 | 26–30 | 33.19–44.22 |
It can be observed that pure ethanol has a higher octane number than petrol suggesting that it has higher anti knocking properties. The flashpoint of ethanol and the blend is also higher than petrol making the fuel safer to handle during transport. Moreover, ethanol has a lower heating value.
There are two processing routes for the conversion of lignocellulosic biomass into bioethanol: Fermentation of carbohydrates resulting from the hydrolysis of biomass into bioethanol and the fermentation of syngas. The alcohol produced from the fermentation of carbohydrates or syngas can be subjected further to ethanol dehydration, oligomerization, distillation, and hydrogenation to produce liquid biofuels, such as biojet fuel and green diesel.
Bioethanol is currently produced from starch/sugar based biomass such as wheat and corn, but issues arise concerning the sustainability of such feedstocks since they compete with human food [6]. Alternative, lignocellulosic biomass can be used for the production of ethanol, but additional technological steps are required, making the process more complicated and costly. Another shortcoming of bioethanol production from sugars is that the process of fermentation is lengthy, usually taking hours or days to complete.
Either acid or enzymatic hydrolysis (also known as saccharification) is required to convert the hemicellulose and cellulose constituents of lignocellulosic biomass into fermentable sugars. The lignin, cellulose, and hemicellulose structure, form a chemical and physical barrier preventing the access of enzymes and the hydrolysis of biomass to produce fermentable sugars. This requires the separation of lignin from the biomass structure, reduction in the crystallinity of cellulose, and alterations in the surface area and porosity of the biomass [7]. Hydrolysis of cellulose and hemicellulose results in the generation of mainly hexoses (glucose) and pentoses, respectively, although some hexoses can also be obtained from hemicellulose.
The main steps for the production of bioethanol from lignocellulosic biomass are pretreatment and/or detoxification, hydrolysis, fermentation, and product recovery [8]. Crushing the feedstock and mixing it with water is required prior to pretreatment to generate slurry. Zhu et al. concluded that the selection of the appropriate pretreatment technology significantly depends on feedstock type [9]. Biochemical fermentation of carbohydrates resulting from the hydrolysis of biomass takes place under the presence of specific microorganisms (yeast or bacteria) at temperatures of up to approximately 38 ℃ with either a batch, fed-batch, or continuous mode bioreactor. The selection of appropriate microorganisms depends on pretreatment conditions, fermentation conditions, and reactor configuration. Furthermore, the hydrolysate of lignocellulosic biomass can contain mixtures of sugars, such as pentoses and hexoses, and the desirable microorganisms should be able to convert both type of sugars. Zabed et al. presented a comprehensive overview on the technological approaches and microbial contribution to the conversion of lignocellulosic biomass into ethanol [8]. Following pretreatment and hydrolysis the sugars released are then fermented by the relevant microorganisms and converted into ethanol. The microorganisms can be acquired from yeast, bacteria, and filamentous funghi and are chosen based on the ethanol yields that they can achieve in addition to the inhibitor tolerance.
Ethanol yields depend on the biomass structure, pretreatment method, type of sugars (five or six carbon sugars), concentration of sugars in the hydrolysates, type of microorganisms, and the fermentation process conditions. The integration of hydrolysis and fermentation is also an important step to achieve process sustainability and high ethanol yields. De Silva et al. investigated the use of carnauba straw residue to produce ethanol by the simultaneous saccharification and fermentation (SSF) process [10]. The SSF approach involves both cellulose hydrolysis and fermentation of hexose sugars in a single reactor. The pretreatment methods applied on the sample included hydrothermal (HT), alkaline (AL), and acid-alkaline (AA) treatment. It was shown that the AL pretreatment resulted in the most efficient removal of lignin and hemicellulose. Moreover, enzymatic hydrolysis of the AL treated sample converted 64.43% to sugars. The maximum ethanol concentration was achieved by using Kluyveromyces marxianus ATCC-36907 cultivated at 45 ℃ and generated 7.53 g/L of ethanol. Further work by Nguyen et al. studied the effectiveness of popping pretreatment in the saccharification process and its consequent effect on bioethanol yields, using coffee beans, cassava starch, and coconut [11]. Results revealed that saccharification efficiencies, after enzymatic hydrolysis, were increased significantly in all the popping-pretreated samples compared to the non-pretreated samples. The total fermentable sugars after pretreatment reached values up to 22.6 g/L, in comparison with the samples without pretreatment, which only achieved maximum values of 7.8 g/L.
Nguyen et al. also investigated the effect of separate hydrolysis and fermentation (SHF) and SSF processing on bioethanol production and foundthe SSF process more promising than the SHF process [11]. In their study ethanol conversion yields from the popping-pretreated sample (mixture of coffee beans, cassava starch, and coconut) using the SSF approach reached 88.1%, which is significantly greater than the yields of 76.8% (9.5 g/L) achieved by the SHF process. The SSF configuration was previously shown to be more effective in terms of ethanol concentration and conversion yields, in the conversion of corn stover and loblolly pine, when compared with SHF [12]. Ethanol yields of 84% (17.3 g/L) and 77% (15.4 g/L) were achieved from the SSF processing of corn stover and loblolly pine, respectively, while the yields were lower (76% for corn stover and 67% for loblolly pine), for the SHF processing. Dahnum et al. also study the influence of SHF and SSF on ethanol yields using empty fruit bunch [13]. Similar to the previous studies the SSF approach produced the highest concentration of ethanol.
Cotana et al. investigated the potential of the SHF and semi-simultaneous saccharification and fermentation (SSSF) configurations for ethanol production using cardoon [14]. Steam explosion was the pretreatment method selected for the study. Similar to the previous studies the SSSF process displayed better results in terms of ethanol yields and length of the process. Another study used delignified coconut waste and cactus to compare the SSF and SSSF approach [15]. Similar, to Cotana et al., the SSSF configuration resulted in higher ethanol yields (up to 89.15%) when compared to SSF.
Ishola et al. examined the potential of the simultaneous saccharification, filtration, and fermentation (SSFF) process of spruce chips on ethanol yields [16]. This process configuration involves the combination of SHF and SSF, with fermentation broth circulated between the hydrolysis and fermentation vessels. The samples were chemically pretreated with SO2 impregnation and exposed to a pressure of 22 bars, and a temperature of 215 ℃ for 5 minutes. Approximately, 31.1 g/L of ethanol was produced in the hydrolysis reactor after 96 hours of processing, which corresponds to 85.0% of the theoretical yield.
Another configuration for ethanol production is simultaneous saccharification and co-fermentation (SSCF) which involves both cellulose hydrolysis and fermentation of hexose and pentose sugars in a single reactor. Liu et al. used a dry biorefining approach including dry acid pretreatment, disk milling, and biodetoxification of corn stover, wheat straw, rice straw, sugarcane bagasse, and poplar sawdust to maximise the potential of SSCF [17]. The most promising feedstock was wheat straw, which produced 101.4 g/L of ethanol.
Consolidated bioprocess (CBP) is another process configuration, where hydrolysis and fermentation take place in the same vessel simultaneously, as well as, producing the required hydrolytic enzymes within the process [18]. Horisawa et al. investigated the potential of direct ethanol production from wood chips in a single reactor under anaerobic conditions using the white rot fungus Schizophyllum commune NBRC 4928 [19]. This fungus was selected due its ability to produces enzymes that degrade all biomass constitutes including lignin, cellulose and hemicellulose. Initial tests were performed with polysacchatides and monosaccharides to determine the fungus's ability to produce ethanol from various types of sugar. Results show that the rate of saccharification was slower for polysacchatides fermentation. Concerning the fermentation of wood chips, successful delignification and ethanol production were achieved by also adding the lignin-degrading fungus T. cucumeris IWA5b to the culture. The study demonstrated that the combined use of lignin and polysaccharide degrading fungi was successful and that direct ethanol production from lignocellulosic biomass, without pretreatment, could be feasible. Huang et al. also demonstrated the feasibility of producing ethanol directly from sugarcane bagasse (without pretreatment) using the Recombinant Trichoderma reesei Strain HJ48 [20]. The maximum ethanol concentration produced was 3.1 g/L after 120 hours of cultivation. Recent work by Loaces et al. showed that Arundo donax biomass can be converted into ethanol by a genetically modified E. coli under a SSF process configuration. It should be noted that the biomass was pretreated with 2% sulfuric acid in mild conditions [21].
Another pathway for production of ethanol is through fermentation of syngas. Lignocellulosic waste materials can be converted initially through gasification into a gas mixture (syngas) consisting of carbon monoxide (CO), carbon dioxide (CO2), hydrogen (H2), methane (CH4), water vapour, and short chain hydrocarbon gases [22]. During gasification, all biomass components are utilised, including lignin, which is the main advantage of the process when compared with saccharification fermentation where only hemicellulose and cellulose are consumed.
The fermentation of syngas involves mixing together carbon monoxide, hydrogen, and carbon dioxide, which are converted into acetate, followed by ethanol. Typical reactions are the following:
4CO+2H2O→CH3COOH+2CO2 | (1) |
6CO+3H2O→C2H5OH+4CO2 | (2) |
6H2+2CO2→C2H5OH+3H2O | (3) |
Syngas produced from gasification contains impurities, such as nitrous oxide, alkali compounds, and tars. Impurities can affect microbial activities and the pH of the fermenting broth, which could lead to cell toxicity, thus gas cleaning is required prior to fermentation. The optimum temperature range for the mesophilic bacteria is 37–40 ℃, whereas for the thermophilic bacteria the range is 55–80 ℃. The process takes place under strict anaerobic conditions. The most promising microorganisms are acetogens, such as C. carboxidivorans and A. bacchi, which can metabolize CO, CO2, and H2 to alcohols and organic acids [23,24]. These microorganisms use two metabolic steps, an acidogenic, and a solventogenic. The acidogenic step involves the main bacterial growth where acids are produced with little or no production of alcohols. The generation of ethanol occurs in the solventogenic step in which alcohol is produced from the formed acids or to a lesser extent, directly from syngas consumption.
Syngas fermentation was performed using a two-stage continuous system with two stirred tank reactors connected in series by Abubackar et al. [25]. The effectiveness of the microorganism clostridium carboxidivorans on the production of acids and alcohols was investigated in continues mode. Syngas (CO:CO2:H2:N2; 30:10:20:40; vol%) was supplied at a constant flow rate while a nutrient medium was provided at different flow rates (8.1–30 ml/h). The bioreactors were maintained at different pH levels to enhance acidogenesis (pH 6) and stimulate solventogenesis (pH 5). The highest ethanol concentration was 1.51 g/L and it was achieved for medium flow rates of 22 ml/h. Previous work by Fernández-Naveira et al. used the same medium as mentioned previously to investigate the conversion of syngas by Clostridium carboxidivorans into hexanol, butanol, and ethanol (H-B-E fermentation) [26]. Syngas with composition of CO:CO2:H2:N2 (20:20:10:50) was provided continuously at 10 mL/min using a two-stage continuous system with two stirred tank reactors connected in series. The maximum concentrations of ethanol, butanol, and hexanol, were achieved at a pH of 5.75 and were 2.7 g/L, 1.9 g/L, and 0.85 g/L, respectively.
Devarapalli et al. investigated the use of Clostridium ragsdalei, which is another acetogen microorganism, for the conversion of syngas into ethanol [27]. A trickle bed reactor was utilised as the fermentation bioreactor while a syngas mixture of CO:CO2:H2:N2 (38:28.5:28.5:5), as well as, the medium, were fed continuously. The highest ethanol concentration (5.7 g/L) was accomplished at 200 ml/min of liquid flow rate and 4.6 sccm syngas flow rate. An interesting approach to enhance ethanol production during syngas fermentation was to use biochar as a medium to serve as nutrients to the Clostridium ragsdalei since it contains mineral and metals [28]. The study compared four fermentation media containing biochar from switchgrass, forage sorghum, red cedar, and poultry litter, with a standard yeast extract medium. Syngas fermentations were conducted in 250 mL bottle reactors at 150 rpm and 37 ℃ with syngas containing CO:H2:CO2 (40:30:30) by volume. The poultry litter derived biochar medium showed the highest ethanol improvement (58.9%) in comparison to the yeast medium. It is believed that this is due the high release of Na, K, Ca, Mg, S and P from the biochar derived medium.
The use of a mixed culture in a corn steep liquor containing A. bacchi strain CP15 and C. propionicum was also researched [29]. Syngas fermentation with cell recycle was performed in a 7 L continuous stirred tank reactor with a syngas composition of CO:CO2:H2:N2 (20:15:5:60) by volume. The mixed culture medium was able to produce 8 g/L, 6 g/L and 1 g/L of ethanol, n-propanol and n-butanol, respectively.
Biobutanol (C4H9OH) can be used as a petrol substitute since its properties are comparable to petroleum derived petrol. It can be produced from lignocellulosic biomass via the process of fermentation. Similar to the fermentation of lignocellulosic biomass to ethanol (mentioned in Section 2.1.1) pretreatment steps are also required. The important properties of pure biobutanol can be seen in Table 2 and are compared with pure petrol.
Properties | Biobutanol | Petrol |
Boiling point (℃) | 118 | 200 |
Freezing point (℃) | −89 | −40 |
Density (kg/m3) | 810 | 760 |
Heat of vaporization (MJ/kg) | 0.43 | 0.36 |
Energy density (MJ/L) | 30 | 32 |
Cetane no | ~25 | 5–20 |
Flash point (℃) | 35 | −42 |
Auto-ignition temperature (℃) | 397 | 257 |
Biobutanol can be produced by the same pathways as bioethanol; Figure 4 illustrates the production routes of bioethanol and biobutanol. As mentioned previously, butanol is produced simultaneously with ethanol from the fermentation of sugars or syngas [26,28]. Biobutanol production from fermentation of syngas including recent technological advances was discussed in the bioethanol section. With regards to fermentation of sugars, the conventional pathway for biobutanol production is the acetone-butanol-ethanol (ABE) fermentation route using the microorganism Clostridium acetobutylicum. The main challenge is the recovery of butanol from the fermentation broth, since it is difficult to exceed 2% (v/v), while ethanol can reach yields of up to 15% (v/v).
Xue et al. investigated the potential of Jerusalem artichoke stalk (JAS) as a feedstock for microbial butanol production and the vapour stripping-vapor permeation (VSVP) process for butanol recovery [32]. JAS was subjected initially to alkaline pretreatment followed by enzymatic hydrolysis to achieve delignification and fermentable sugar release. It was found that 11.8 g/L of butanol was produced under the optimum conditions using a Clostridium microorganism. Moreover, the VSVP process proved to be more productive for butanol recovery from the fermentation broth, than conventional pervaporation process. Further work by Xue et al. [33] reviewed the problems and advances in butanol production by Clostridium acetobutylicum to achieve process feasibility. It was concluded that in-situ product recovery techniques can lead to a reduction in the production cost of biobutanol, since the continuous removal and purification of inhibitory products during fermentation, results in the generation of ABE in a concentrated solution. Furthermore, genome editing of Clostridium acetobutylicum could lead to a significant improvement in biobutanol yields.
Biodiesel can be defined as fatty acid methyl/ethyl ester (FAME and FAEE) derived from transesterification and esterification of vegetable oils or animal fats and alcohol (methanol or ethanol), usually in the presence of a basic, acid, or enzyme catalyst [34]. Currently, first generation biodiesel is produced on a large scale and is blended with fossil derived diesel. It is regulated by the standards ASTM D6751 and EN 14214. Table 3 shows the key properties and differences between regulated biodiesels and fossil diesel.
Properties | Biodiesel (ASTM D6751) | Biodiesel (EN 14214) | Fossil diesel |
Density 15 ℃ (kg/m3) | 880 | 860–900 | 820–850 |
Viscosity @ 40 ℃ (cSt) | 1.9–6.0 | 3.5–5.0 | 2.04–3.23 |
Calorific value (MJ/kg) | - | 35 | 42–48 |
Acidity total (mgKOH/g) | Max. 0.50 | Max. 0.5 | 0.02 |
Cetane number (min) | Min. 47 | Min. 51 | Min. 40 |
Iodine number (max) | - | 120 | - |
Flash point (℃) | Min. 93 | Min. 120 | Min. 52 |
Pour point (℃) | −15 to 10 | - | −35 to −15 |
Cloud point (℃) | −3 to 12 | - | −15 to 5 |
Cold filter plugging point (℃) | 19 | Max. 5 | 5 |
Copper strip corrosion (3 h–50 ℃) | Max. 3 | Min. 1 | Max. 3 |
Sulphur % (ppm) | Max. 15 | Max. 10 | Max. 15 |
Sulphated ash % (m/m) | Max. 0.02 | Max. 0.02 | Max. 0.01 |
Oxidation stability (min, 110 ℃) | 3 | 6 | - |
Compared to fossil diesel, biodiesel has low sulphur and aromatics content, high biodegradability, low stability (which can be increased with the addition of antioxidants) [35] and high NOx emissions when burned [36].
Biodiesel is produced through the transesterification/esterification reaction. The oil (triglycerides and free fat acids (FFA)) reacts with an alcohol (usually methanol) in the presence of a catalyst (mainly alkaline) to form alkyl esters (fatty acid methyl ester (FAME) when reacted with methanol) and glycerol or water. The exemplified reactions are below:
Triglycerides+3alcohol→3ethylesters+glycerol | (4) |
Fattyacid+alcohol→ethylester+water | (5) |
Many studies have been performed to identify the best catalyst for biodiesel production. The most commonly used catalysts are the alkaline ones (NaOH and KOH), however they require less water and FFA in the oil, so this route is limited by the feedstock properties. Waste cooking oil, for example, has a large amount of FFA and is not suitable for this route. Therefore, more catalytic routes have been developed including heterogeneous catalysts, acid catalysts, and enzymes [37]. The latest studies focus on the use of heterogeneous catalysts from biological waste because of their high activity, tolerance to water, non-toxicity, and enviromental benefits [38].
Other studies have focussed on eliminating catalysts all together by using supercritical fluids including, subcritical hydrolysis for lipid extraction integrated into supercritical esterification and, direct supercritical transesterification. The advantage of these approaches is their high tolerance to water and FFA, therefore they are more suitable for cooking oil and wet biomass (algae). However, their efficiency and economic feasibility need to be improved in order to make these technologies viable for larger scale applications [39].
Another biofuel that can be blended or replace fossil diesel is green or renewable diesel [40]. Green diesel is derived from the diesel fraction of upgraded bio-oil or Fischer–Tropsch (FT) wax. In this case, green diesel, has not been derived from the transesterification process and can be obtained by hydroprocessing (HDO), followed by cracking or isomerisation, of bio-oil or FT wax. This technology will be explained further in Section 2.6.2 and Section 2.8.1.2. However, it is not commonly used yet, as its production costs are higher when compared to biodiesel, and operating conditions are more complex (higher temperatures and pressures). Green diesel has a higher cetane number (around 70–90) when compared to biodiesel (50–65) and diesel (40) and a higher range of cloud point (from −20 to 20 ℃) due to isomerisation after the HDO step [41]. Thus, it is more stable. Moreover, green diesel has a higher calorific value, lower oxygen content, lubricity, density, and viscosity when compared with biodiesel [42].
Biomethanol is an alcohol (CH3OH) that can be produced by catalytic (usually copper, zinc or chromium oxides) hydrogenation of syngas (carbon monoxide and carbon dioxide) or biogas (methane) [43,44]. Its production can be divided into 3 reactions:
CO+2H2→←\vboxto.5ex\vssCH3OH(twostages:CO+H2→←\vboxto.5ex\vssCH2OfollowedbyCH2O+H2→←\vboxto.5ex\vssCH3OH) | (6) |
CO2+3H2→←\vboxto.5ex\vssCH3OH+H2O | (7) |
CH4+H2O→←\vboxto.5ex\vssCH2OH+H2O | (8) |
The reactions occur at 200–300 ℃ and 50–100 bar and the use of catalysts are required in order to force thermodynamic equilibrium for methanol production. The recycling of the unreacted gas and the required cooling systems (due to the exothermic nature of the reaction) are responsible for the main costs of the synthesis process [45].
For methanol synthesis, the syngas ratio (H2/CO2) is required to be higher than 2. Thus, cleaning of syngas is carried out before methanol generation in order to optimize its composition. Furthermore, syngas contains impurities, such as sulphur and chlorides that can be harmful to the environment and/or deactivate the catalyst [46]. Another way of optimising the process is the conversion of CO to CO2 using a water gas shift catalyst or a catalytic membrane reactor immediately after the gasification process [47]. CO2 is then converted to methanol by catalytic hydrogenation. The produced biomethanol also requires a purification step in order to meet specifications. This process can be realised at a competitive price when biomethanol is used as a biofuel blend and methanol can be directed to the production of other fuels such as biodiesel, DME, and OME [47]. Biomethanol production can be simplified with the approach presented in Figure 5 below:
It has been shown that biomethanol has a competitive cost production and GHG emissions reduction when compared to methanol production from fossil fuels [48]. Biomethanol can be used as direct blending with petrol and maritime fuel, for transesterification, and as feedstock for DME/OME synthesis [49].
Poly (oxymethylene) dimethyl ethers (OME) and dimethyl ether (DME) are diesel substitutes and can be used in compression ignition engines without major modifications. Biomethanol can be used as feedstock for the generation of OME/DME. The DME structure is CH3OCH3, while OME is H3CO(CH2O)nCH3, with n from 2 to 8, preferably 3 to 5 for diesel replacement [48]. The properties of these fuels in comparison with diesel are presented in Table 4 [49,50].
Properties | DME | OME | Fossil diesel |
Molecular weight | 46.07 | 76–196.2 | 96 |
Density 20 ℃ (kg/m3) | 660 | 960–1105 | 800–840 |
Viscosity @ 40 ℃ (cSt) | 0.12–0.15 | 0.64–1.75 | 2–4 |
Calorific value (MJ/kg) | 28.5 | 18.5–23.3 | 42.5 |
Cetane number (min) | 55–60 | 60–90 | Min. 40 |
DME has a high oxygen content, low viscosity, low lubrication, and LHV when compared to fossil diesel fuel [51]. DME has already been tested in diesel engines; information regarding emissions and performance are established. When compared to diesel combustion, DME emits lower levels of particulate matter, HC, and nitrous oxides (NOx) [51], but also has inferior performance (due to the lower LHV) [52]. OME does not contain impurities and has a cetane number higher than conventional diesel, but it has a lower HHV. Costs analysis confirms that OME production could be even cheaper than diesel production [50].
The main pathway for DME production is methanol dehydration in a catalytic gas-phase reactor followed by purification and distillation [53]. Common catalysts used are solid-acid catalysts, such as alumina, zeolites, AlPO4, and CuO/ZrO2. DME synthesis usually occurs in slurry or fixed bed reactors, but the process can also take place in fluidized-bed reactors, coupled and dual type, as well as, membrane reactors [54]. The reaction of the commercialised process is presented below:
2CH3OH→CH3OCH3+H2O | (9) |
A promising route that is currently being studied is DME production in a one stage reactor. DME can be produced directly from syngas, at 250–400 ℃ and pressures higher than 10 bar, in an exothermic reaction using a bi-functional catalyst that is able to synthesise methanol followed by DME. The process is strongly influenced by the presence of water, H2/CO ratio, CO2 content, and reaction temperature [56].
For OME production, the methanol is utilised by a metal oxide catalytic process (or with silver catalyst) to produce formaldehyde as shown in the reactions below:
CH3O+1/2O2→CH2O+H2O | (10) |
CH3O→CH2O+H2 | (11) |
From the formaldehyde, trioxane is produced with the use of sulphuric acid (3CH2O → (CH2O)3) and methylal is produced by a reaction-distillation process with an acidic heterogeneous catalyst (2CH3OH + CH2O ⇄ CH3O-CH2O-CH3 + H2O) [50]. The most used catalysts are liquid catalysts (mineral acid (H2SO4) or ionic liquids) and heterogeneous catalysts (ion exchange resin, carbon marerial, solid superacid, zeolite and others) [55].
The catalytic steps involved in OME synthesis is the main drawback of the process. Therefore, further research has been undertaken aiming to simplify the process with more efficient and feasible catalysts [57].
Further optimisations regarding the feasibility of the DME/OME routes has been investigated in regards to the optimization of the gasification and methanol process. Parvez (2018) showed that CO2-enhanced gasification resulted in better energy efficiency and less environmental impact when producing DME compared to conventional gasification [56].
Bio-oil is the primary product from the process of pyrolysis, which can be obtained from the thermal decomposition of lignocellulose biomass with rapid heating in the absence of oxygen followed by rapid quenching of the vapour products. It is a multicomponent mixture consisting of hundreds of different sized molecules obtained from the depolymerisation and fragmentation of cellulose, hemicellulose, and lignin [57]. A typical compound distribution in bio-oil includes acids, esters, alcohols, ketones, aldehydes, sugars, furans, hydrocarbons (such as alkene, aromatics), phenols (such as phenols, anisoles, catechols, guaiacols, syringols), water, and fragments of cellulose and lignin [58,59]. The composition and yields of bio-oil are significantly dependent on the process operating parameters, reactor configuration, and feedstock type.
Bio-oil can be used as a substitute for fuel oil or diesel in many industrial boilers, furnaces, and static engines for heat and power generation. The USA has developed the ASTM D7544, which covers the specification of pyrolysis liquid produced from biomass for use in various types of fuel-burning equipment.
Significant upgrading of bio-oil is required to meet engine specifications, since its physiochemical properties vary significant from those of conventional fossil fuels (Table 5). The main reason for the differences between bio-oil and transportation fuels is the high content of oxygen in bio-oil, which tends to resemble its original biomass [60]. Furthermore, it is immiscible with fossil fuels, because of its high polarity and hydrophilic nature. The indigenous undesired properties of bio-oil that makes it unsuitable as a transportation fuel are given below:
Analysis | Typical wood derived bio-oil | Fossil diesel | LFO Motor/heating EN590 |
Water, wt.% | 20–30 | ∼0 | ∼0 |
Stability | Unstable* | ||
Viscosity (40 ℃), cSt | 15–35 | 2.04–3.23 | 2.0–4.5 |
Density (15 ℃), kg/dm3 | 1.10–1.30c | 0.820–0.850 | Max. 0.845 |
Flash point, ℃ | 40–110d | Min. 52 | Min.60 |
Pour point, ℃ | −9–36 | −35−15 | −5 min |
LHV, MJ/kg | 13–18c | 42–48 | 42.6 |
Distillability | Non-distillable | Distillable | Distillable |
*Polymerisation occurs during heating for prolonged periods. |
● Low heating value,
● Immiscible with fossil transportation fuels,
● Acidity,
● High oxygen content,
● High viscosity,
● High water content,
● High solid content.
Bio-oil can be used in other applications, such as a food flavouring and chemical production, however our focus is on its potential as a biofuel for transportation.
Pyrolysis is defined as the thermal decomposition of organic matter in the complete absence of oxygen (usually nitrogen). Pyrolysis takes place in the temperature range 280–850 ℃ depending on the nature of the feedstock, the desired products, and the particular pyrolysis process employed. Depending on the heating rate and vapour phase residence time, pyrolysis can be classified into several categories. Slow pyrolysis is a batch process characterised by long vapour residence time (5–30 min), slow heat transfer rates up to 2 ℃/s, and low reactor temperatures ranging from 300–500 ℃. Intermediate pyrolysis is carried out in the temperature range 300–500 ℃ with heat transfer rates up to 1000 ℃/s. Fast pyrolysis is a continuous process and requires high heat transfer rates (>1000 ℃/s), short vapour residence time (1 s), and a relatively high temperature (450–600 ℃). Moreover, feedstock drying is necessary in fast pyrolysis, while slow and intermediate pyrolysis process feedstocks with higher moisture levels. Even though fast pyrolysis produces the highest bio-oil yields (up to 75 wt.% expressed on biomass basis), it has been shown that intermediate pyrolysis can produce better quality of bio-oil (low tar yield and viscosity) [62]. The processes described above occur under atmospheric pressure.
In addition to the previous categorisation, hydrogen can be used instead of an inert nitrogen environment. Hydropyrolysis takes place under a pressurised hydrogen atmosphere, which results in the reduction of unsaturated hydrocarbons and formation of fewer compounds in the bio-oil with higher selectivity [63]. It seems that the presence of hydrogen avoids the random thermal cracking that takes place under a nitrogen environment and promotes the systematic bond cleavage in the structure of biomass, thus increasing the quality of the produced bio-oil. Pressurised water can also be used to achieve the thermochemical conversion of biomass into bio-oil in a process termed hydrothermal liquefaction [64]. Typical operating temperatures are 250–374 ℃ and operating pressures from 4–22 MPa. Another promising pyrolysis mode is microwave pyrolysis [65]. The fundamental difference here is that microwave waves heat the biomass particles from within and not by external heat transfer from a high temperature heat source.
● Catalytic hydrotreatment
The process takes place at high pressure (up to 200 bar) and moderate temperature (up to 400 ℃) in the presence of a heterogeneous catalyst. A hydrogen source is necessary to achieve the removal of the oxygenated compounds in bio-oil, such as ketones and carboxylic acids, and to produce an oil suitable to be used as a feedstock in a biorefinery or blend with diesel. Hydrotreatment rejects oxygen as water by catalytic reaction with hydrogen [66].
(CH2O)+H2→Catalyst→(CH2)+H2O | (12) |
Gollacota et al. summarised the following different type of reactions that occur during the process: Hydrodeoxygenation, hydrogenation, hydrogenolysis, hydrocracking, dehydration, and decarboxylation [67]. Hydrotreating (HT) gives a naphtha-like product that requires further refining to produce transport fuels, such as aviation fuel and green diesel [68].
Commonly applied catalysts for the hytrotreating of bio-oil or bio-oil model compounds are alumina or aluminosilicate supported sulfided CoMo and NiMo catalysts. This review focuses on the upgrading of actual bio-oil, thus work regarding bio-oil model compounds is not discussed further. The main work involving the testing of sulphided CoMo or NiMo catalysts on wood derived bio-oil was conducted in the 1980s and 1990s [69,70]. Their results showed that even though the catalysts were effective in the enhancement of bio-oil, several issues, such as low upgraded bio-oil yields and catalyst deactivation caused by carbon/coke deposition, required further research. The disadvantage of alumina as a support material for the HT catalysts was its instability at high temperatures in the high water environment of the bio-oil. Thus, carbon-supported sulphided CoMo and NiMo catalysts were also tested as HT catalysts by Elliot et al. [71].
Alternatively, noble metals have been tested, dispersed on active charcoal supports or metal oxides, for the HT of bio-oil [72,73,74]. Wildschut et al. used Ru, Rh, Pd and Pt over different supports to assess their effect on the deoxygenation of bio-oil in comparison with conventional HT catalysts. It was found that the Ru/C catalyst was greater than the HT catalysts with reference to bio-oil yields (up to 60 wt.%) and deoxygenation level (up to 90 wt.%). The type of catalyst precursor on catalyst performance was also found to play a role on the HT of bio-oil [76]. However, the high cost of noble metals significantly affects the industrialisation of the process.
Inexpensive non-sulphided transition metal catalysts over various support materials, such as aluminosilicate and zeolite, have been studied for their HDO activity for bio-oil upgrading. Ni-based catalysts with three different support materials (active carbon, SBA-15 and Al-SBA-15) and their catalytic effects were tested with poplar derived bio-oil by Oh et al. [75]. The Ni/SBA-15 catalyst was found to show the highest degree of deoxygenation and upgraded bio-oil yields by 47.7 wt.%.
Xu et al. investigated the effect of a non-sulphided bimetallic catalyst, MoNi/γ-Al2O3, for upgrading of pine sawdust derived bio-oil [76]. The catalyst seemed to improved pH and water content, but the oxygen content was not reduced significantly. The influence of the non-sulphided bimetallic FeCo/SiO2 catalyst, as well as, the monometallic Co/SiO2 and Fe/SiO2 catalysts, on deoxygenation of pine sawdust derived bio-oil was also tested [77]. The bimetallic Fe-Co/SiO2 catalysts decreased the upgraded bio-oil yields (23.85–26.94 wt.%) and increased the gas yields (10.35–22.90 wt.%). The bimetallic catalysts showed an improvement on HDO performance over the monometallic catalysts, but they produced lower upgraded bio-oil yields (23.85–26.94 wt.% in comparison of 31.23–33.91 wt.%).
Furthermore, activated carbon supported Ni, Co and Mo phosphide catalysts have been shown to be promising for HT [78]. Guo et al. investigated the effect of phosphorus content on the deoxygenation of bio-oil by varying the metal/P ratio [79]. It was found that the addition of phosphorous to a certain level resulted in the improvement of H2 consumption, upgraded oil yields, and increased the degree of deoxygenation. The Ni-based catalysts seemed more promising than Co-based catalysts with regards to hydrogenation and HDO activities.
● Zeolite cracking
Zeolite catalysts can be used to improve the quality of bio-oil in two configurations. One mode is in-situ upgrading which involves the integration of catalysts into the pyrolysis system. The other configuration involves catalytic upgrading as a downstream (decoupled) process. The process takes place under atmospheric pressure and does not require the presence of hydrogen. The reactions described for the HT process also take place in zeolite cracking, but the cracking reactions are the primary ones. Zeolite cracking rejects oxygen as CO2 and H2O, generating liquid hydrocarbon products through the remaining hydrocarbon fraction [80].
C1H1.33O0.43+0.26O2→0.65CH1.2+0.34CO2+0.27H2O | (13) |
ZSM-5 has been used extensively as a catalyst by a number of researchers to improve the quality of bio-oil. Comprehensive work was performed by Williams and Horne to study the effect of ZSM-5 on pyrolysis product yields and chemical distribution using a fluidised bed reactor [81]. The catalyst was placed at the reactor freeboard as a fixed bed (in-situ configuration). Results showed that the oil yields were reduced from 40.4 to 5.5 wt.% of biomass, while a reduction was also observed in the molecular weight (from 30–1300 u to 50–600 u) of the bio-oil. The chemical distribution of the bio-oil was also affected, particularly the formation of monocyclic aromatic hydrocarbons and polycyclic aromatic hydrocarbons (PAH).
Furthermore, the influence of ZSM-5 temperature has been investigated. Catalytic experiments were performed over a range of temperatures from 400–600 ℃ [82]. It was found that the total liquid yields, molecular weight and oxygenated compounds (such as phenols and benzenediol) in bio-oil were reduced. On the contrary, the concentration of aromatic hydrocarbons and PAH were increased. Li et al. also investigated the effect of catalytic reaction temperature (390,410,450,470,500, or 550 ℃) and WHSV (1 to 5 h−1) on bio-oil using ZSM-5 [83]. The reactor configuration involved a fluidized bed reactor for pyrolysis coupled with a secondary fixed bed reactor for upgrading. It was observed that acid and ketones were reduced, whereas hydroxybenzene and monocyclic or dicyclic aromatic hydrocarbons were increased. Both researchers found that as catalytic temperature increased the upgraded bio-oil yields decreased while the opposite trend was observed for the gas yields. This is due the decomposition of bio-oil to light gases and carbon at higher temperatures. It should be noted that it is necessary to establish the optimum degree of cracking, where a sufficient amount of oxygen is removed but the yields of upgraded bio-oil are not too low. Catalytic fast pyrolysis (CFP) bio-oils with different organic oxygen contents (4–18 wt.%) were prepared in a bench-scale dual fluidized bed reactor system by ex-situ CFP of southern pine over HZSM-5, and the oils were subsequently hydrotreated over a sulphided CoMo catalyst at 170 bar [84].
The main properties for the catalytic activity of zeolite catalysts are their shape selectivity and acidity. The limitations of the pore size (5A) of H-ZSM-5 in the case of large molecules justified further research using zeolite materials with larger pore size, such as MCM-41 and zeolite Y.
Williams and Horne [85] studied the effect of different zeolite structures and activated alumina on bio-oil. Regarding the product yields, stainless steel balls, Na-ZSM-5, H-ZSM-5, Y and activated alumina showed a reduction in organic liquid yields (blank run—40.41%) of 11.80, 6.01, 5.47, 1.13 and 3.12 respectively, expressed on wt.% of biomass feed. The overall conclusions were that all the zeolites produced hydrocarbons (aromatic and PAHs); Y-zeolite formed higher PAHs levels compared to the other catalysts; ZSM-5 was the most effective catalyst; hydrocarbon yields were low, when expressed on wt.% of biomass feed.
Extensive work related to the acidity and metal incorporation of catalysts was conducted by Antonakou et al. [86]. Pyrolysis experiments using Al-MCM-41 catalysts with various acidities (Si:Al ratios of 20, 40, 60) and metal containing Al-MCM-41catalysts (Cu, Fe and Zn) were conducted using a bench scale fixed bed reactor. An increase was observed in the amount of phenols and hydrocarbons in bio-oil, while the opposite effect occurred for the oxygenated compounds. It should be highlighted that a reduction in acids, carbonyls, and heavy compounds was also observed. The organic yields, though, decreased by about 9 wt.% (on biomass basis) when catalysts were applied.
Metal oxide catalysts have also been tested for their catalytic effect on pyrolysis oils [87,88]. The effect of ZnO on bio-oil was studied by Nokkosmäki et al. in a fluidised bed reactor with capacity of 1 kg/h−1, with the catalytic fixed bed reactor connected into the side stream of the reactor system [89]. The pyrolysis reaction temperature was 525 ℃, while the catalytic reaction temperature was 400 ℃. Results revealed that the ZnO derived bio-oil had lower viscosity thus indicating an improvement in stability. Putun et al investigated the effect of MgO on pyrolysis product yields [90]. A fixed bed reactor was used with the catalyst placed as a bed material inside the reactor. Oxygen content of the treated bio-oil was reduced from 9.56% to 4.90% when different amounts of catalysts were applied.
● Filtration
Bio-oil contains impurities, such as alkali metals and particulates, which cause problems in certain applications. Hot-vapour filtration can be used to reduce the solid content of the oil to less than 0.01% and the alkali content to less than 10 ppm [82,89]. However, bio-oil requires further upgrading since the primary reason for its immiscibility with fossil fuels is its oxygen content.
● Supercritical fluids (SCFs)
A fluid is defined as supercritical when its pressure and temperature go beyond its critical point and it has the ability to dissolve materials that are not normally soluble in either the liquid or gaseous phase of the SCFs. In the case of bio-oil production, the use of SCF organic solvents, results in an oil with higher caloric values, lower viscosity, and higher yields [90]. Typical SCFs organic solvents have been identified by Baloch et al. and include ethanol, butanol, acetones, methanol, n-hexanol, 2-propanol, and 1, 4-di-oxane [91].
● Solvent addition/esterification
Esterification can reduce the acidity of bio-oil by removing the carboxylic acids. The reaction takes place in the presence of a catalyst and a solvent to generate esters. Catalysts used for esterification are solid acid, solid alkali, and ionic liquid ion exchange resins [92,93,94].
● Emulsification (emulsions)
Emulsification is a physical method for upgrading bio-oil. Homogenous emulsion of bio-oil with diesel can be achieved by agitation with an emulsifier [95].
Biojet fuel or renewable aviation fuel is a biomass derived fuel and contains hydrocarbons with a boiling range similar to fossil jet fuel (170–300 ℃). Fossil jet fuel is composed of approximately 20% paraffin, 40% isoparaffin, 20% naphthenes and 20% aromatics. Depending on the pathway, biojet fuel does not always contain aromatic compounds. Mixtures of up to 50% biojet fuel with aviation fossil fuels have been established as a standard to overcome this issue. Biojet fuel is only certified if it has similar properties with fossil jet fuel, such as energy content and density. Some characteristics of biojet fuel (according to ASTMD 7566) that are similar to fossil jet fuel are presented in Table 6 [96].
Properties | Biojet fuel |
Acidity, total (mgKOH/g) | 0.1 max |
Flash point (℃) | 38 min |
Density @15 ℃ (kg/m3) | 775–840 |
Freezing point (℃), max | −40 JetA; −47 JetA1 |
Viscosity @ −20 ℃ (cSt) | 8, max |
Net heat of comb (MJ/kg) | 42.8, min |
Certified biojet fuel can be blended up to 50% with conventional aviation fossil fuel according to the requirements in the ASTM D7566 specification. The following processes have been certified by the standard for production of renewable aviation fuel.
HRJ also known as hydroprocessed esters and fatty acids (HEFA) are paraffinic liquids with the chemical formula CnH2n+2. HRJs are produced by the hydrodeoxygenation of triglyceride-based feedstocks, followed by isomerisation and cracking, forming fuels equivalent to conventional aviation fossil fuel. The use of bio-oil as a triglyceride-based feedstock is not yet certified.
The triglyceride-based feedstock is firstly converted to lineal long chain hydrocarbons, under high pressure and temperature in the presence of hydrogen and a solid catalyst (hydrodeoxygenation, see Section 2.6.2); by-products formed are water, carbon monoxide, and carbon dioxide. Isomerisation and cracking convert the lineal long chain hydrocarbons into the hydrocarbon chains that are in the range C8 to C16 (biojet fuel). Light gases, naphtha, and green diesel are produced in addition to biojet fuel. In comparison to fossil fuels, HRJ fuels possess a higher cetane number, lower aromatic content, lower sulphur content, and potentially lower GHG emissions.
The hydrotreating process has been demonstrated at pilot plant level by UOP Honeywell for the production of renewable jet fuel using second-generation oils as feedstock [97]. It should be noted that information concerning the type of catalyst involved in the UOP Honeywell process is not publicly available. There are few studies in literature focussing on hydrotreating of sustainable feedstocks for biojet fuel production. Promising work has been performed by Robota et al. regarding the conversion of algal triglycerides to biodiesel and HEFA jet fuel fractions [98]. The proposed process involves deoxygenation, hydrogenation, and hydro isomerisation using a 3% Pd/carbon, a 0.5% Pt/alumina, and a 0.5% Pt/US-Y zeolite catalyst, respectively. Choi et al. studied the use of a Pt/TiO2 catalyst with a W addition for the deoxygenation of Jatropha fatty acid derived from Jatropha oil by hydrolysis [99]. The deoxygenation reaction was carried out in a fixed-bed reactor without the presence of hydrogen producing saturated hydrocarbons (C17 and C15) with a degree of deoxygenation of 86%.
Zhao et al. investigated the upgrading of non-edible sunflower oils over a ZSM-5 catalyst in a fixed-bed reactor, at three different reaction temperatures (450 ℃, 500 ℃ and 550 ℃), followed by distillation [100]. The maximum conversion efficiency of sunflower oils to hydrocarbon fuels was 30.1% and was realised at 550 ℃. Even though the properties of the hydrocarbon fraction were improved after upgrading and distillation, further refining is required to remove the remaining oxygen atoms. Liu et al. used Ni supported on moderate acidic zeolites to produce biojet fuel from castor oil by hydroprocessing in a continuous-flow fixed-bed microreactor followed by isomerization and hydrocracking [101]. The main observation of this work was that the acid strength of zeolite had an important role in the conversion of castor oil into biojet range alkanes. It should be mentioned that the oils produced meet all of the basic jet-fuel mixing requirements according to ASTM D7566. The conversion of waste cooking oil to jet biofuel has also been researched with nickel-based mesoporous zeolite Y catalyst [102]. Moreover, NiMo, CoMo, and NiW sulfide catalysts were also applied during hydrodeoxygenation of waste cooking oil [103]. During both studies the deoxygenation of cooking oil was achieved and converted into jet range alkanes, but further investigation is required to achieve higher fuel yields.
FT fuels are biomass derived hydrocarbon fuels, which are produced from the catalytic conversion of syngas. The integration of gasification with Fisher Tropsch synthesis shows great potential as a sustainable route for production of biodiesel and biojet fuel from biomass [104,105,106,107]. Process temperature varies from 700–1000 ℃ and requires a gasifying agent, such as steam or air. The process is carried out under atmospheric pressure typically with a fixed bed gasifier which is categorised as either updraft, downdraft, or crossdraft [108].
Fischer Tropsch technology involves conversion of syngas into long chain hydrocarbon products, either straight or branched. FT synthesis occurs in two temperature ranges, a low temperature FT (LTFT) and a high temperature FT (HTFT), which range between 200–240 ℃ and 300–350 ℃, respectively [109]. The low temperature process uses either iron or cobalt catalysts, while the high temperature process uses iron-based catalysts [110,111]. Pressures range from 10–60 bar. Typical reactor types are circulated fluidised bed and fluidised bed for HTFT and tubular fixed bed and slurry phase for LTFT [109].
FT synthesis converts the gasification gas mixture into a mixture of light (C1–C4), naphtha (C5–C11), diesel (C12–C20) and heavier hydrocarbons/wax (>C20) [112,113]. The latter requires further catalytic hydrocracking to produce biojet fuel and green diesel. Liquid product yields from FT synthesis can be up to 95%. This crude FT product requires further processing for the synthesis of the FT fuel. The composition of the crude FT product strongly depends on the H2/CO ratio, the catalyst, pressure, and temperature process conditions. Furthermore, cracking and isomerization of the crude FT product generates FT fuel with hydrocarbon chains that are in the range C8–C16, corresponding to biojet fuel.
Recent work by Hillestad et al. demonstrated the feasibility of a power and biomass plant for the production of Fischer-Tropsch biojet fuel compared to a conventional Biomass-to-Liquid (BtL) process [114]. It was shown that the carbon efficiency of a conventional BtL process can be increased from 38% to more than 90%. This was achieved by adding hydrogen from high temperature steam electrolysis in a solid oxide electrolysis cell (SOEC), with high temperature steam generated from the hot syngas. Moreover, SOEC produces oxygen, which is supplied as oxidant in the gasifier, thereby eliminating the need for a cryogenic air separation unit. Previously, Viguié et al. presented the BioTfueL project, which produces biojet fuel and green diesel from second generation feedstocks [115]. This project focuses on the original concept of co-processing (biomass and fossil feedstock). The selection of the appropriate catalyst for hydrocracking of crude FT is also an important parameter to achieve process feasibility. Hanaoka et al. produced biojet fuel by hydrocracking an FT product derived from woody biomass via gasification [116]. The maximum jet fuel yield was 29.1 C-mol% with a Pt-loaded zeolite catalyst with particle size of 7.6 nm.
SIP fuels, were formerly known as direct-sugar-to-hydrocarbon (DSHC) fuels. The process involves the biochemical fermentation of carbohydrate sugars to hydrocarbon fuels through purification and hydroprocesing, without producing ethanol first. The sugars can be derived from the hydrolysis of biomass or from direct sugar sources such as sugar cane residues. Blends of 10% volume of SIPs with aviation fossil fuels are permitted by ASTM D7566.
ATJ fuels are produced by thermal and biochemical fermentation of carbohydrates obtained from the hydrolysis of biomass. The sugars extracted by hydrolysis are fermented, followed by distillation to get bio alcohol. Direct use of alcohol as jet fuel requires engine modification, thus further processing needs to occur to produce a suitable jet fuel. The next steps are alcohol dehydration, oligomerisation, hydrogenation followed by distillation to produce a biojet fuel similar to fossil aviation fuel. Additionally, the process produces naphtha and diesel. Lanzatech is the world's first large scale ATJ facility producing commercial quantities of fuel in the UK [117]. The commercial facility will convert ethanol produced from waste to biojet.
Other promising pathways for biojet fuel production that are not yet certified by the standard are:
● Catalytic hydro-thermolysis (CH) fuels, also termed hydrothermal liquefaction. The same process is followed as described for the SIPs, but it involves catalytic conversion of sugars instead of biochemical fermentation.
● Hydro-treated depolymerized cellulosic jet (HDCJ), also known as fast pyrolysis with upgrading to jet fuel.
● Gas fermentation process. Instead of catalytically upgrading FT syngas to biojet fuel, it is also possible to ferment syngas to liquid biofuels. The cooled syngas can be fermented to ethanol or butanol by acetogenic bacteria followed by oligomerisation and hydrogenation to produce biojet fuel.
Various pathways have been developed for the production of second generation liquid biofuels. This review considers only sustainable feedstocks that do not compete with food production including sugar and starch crop residues, lignocellulosic biomass and waste, and non edible oils (or fats). Figure 6 illustrates the fuels and their production routes.
Sugar and starch type agricultural residues are converted through biochemical fermentation to bioethanol or biobuthanol. Further processing through hydroprocessing and cracking/isomerization produces biojet fuel and green diesel. Another approach for the latter fuels using sugar and starch feedstocks is through catalytic conversion followed by hydroprocessing and cracking/isomerization. Lignocellulosic feedstocks can be converted to sugars by hydrolysis, syngas by gasification or bio-oil by pyrolysis. The produced syngas can be directed to biochemical fermentation, Fisher-Tropsch and biometanol synthesis. Biomethanol (generated from the methanol synthesis) can be used directly as biofuel or to generate DME and OME. Pyrolysis derived bio-oil can be subjected to further processing through zeolite cracking or hydro-deoxygenation to produce a de-oxygenated bio-oil which after cracking/isomerization produces biojet fuel, petrol, and green diesel. Oils and fats can be directed either to zeolite cracking and hydro-deoxygenation or to transesterification and esterification, to generate green diesel and biodiesel, respectively. A comparison of the main advantages and disadvantages of the technological pathways for second generation liquid biofuels are summarised in Table 7.
Product | Pathway | Advantages | Challenges |
Ethanol | Biochemical fermentation from sugars | Well-developed route Acid/enzymatic step allows for feedstock diversification | Development of microorganisms to be able to convert both type of sugars Research on process integration is required to achieve process feasibility |
Fermentation of syngas | All biomass components are utilised, including lignin | Syngas conditioning is required | |
Butanol | Biochemical fermentation from sugars | Simultaneous process with ethanol production | Product recovery process |
Fermentation of syngas | |||
Biodiesel | Catalytic Transesterification | Well-developed route Market ready for the product | Catalyst developed for first generation oils |
Supercritical Transesterification | High feedstock tolerance | Expensive process when compared to the catalytic route Extreme conditions and high energy demand (more development needed) | |
Green diesel | Bio-oil upgrading (HDO and HC) | Less feedstock limitation Similarity with fossil diesel | Bio-oil production technology challenges Catalyst |
Biomethanol | Gasification + MeOH Synthesis | Cost competitive with methanol from fossil fuels Developed market for the product | Gasification process challenges Syngas conditioning |
DME/OME | DME/OME Synthesis | Used as diesel replacement Not expensive | Inferior performance compared to the fossil fuel Challenges from the methanol production |
Petrol | Hydroprocessing followed by cracking/isomerisation | Several production routes | Further development on processing of bio-oil Low yields, is produced as a by-product |
Biojet fuel | Hydroprocessing of triglycerides | Cost competitive than the other biojet routes | Cost of catalysts and hydrogen Limited feedstock tolerance Product refining |
Biochemical fermentation of sugars to hydrocarbons | Fewer technological steps than ATJ fuels | Product refining | |
Biochemical fermentation of sugars to ethanol followed by hydrogenation | Less feedstock limitation | Product refining | |
FT synthesis | All biomass components are utilised, including lignin | Cost of FT synthesis |
The technoeconomic feasibility of a production pathway chosen for fuel production is dependant on a number of different factors, such as market demand, feedstock availability, and market readiness in each location. Location on its own is also an important factor, influencing both the feedstock supply chain and plant construction and commissioning costs. In Brazil the abundance of arable land, as well as, the availability of sugar cane and bagasse, has lead to the dominance of bioethanol in the Brazilian market. In addition to geographical, political influence has also been an important driver of the bioethanol market in Brazil today, where public policy has helped to create the largest flexible-fuel fleet in the world [118].
Feedstock availability is another important parameter affecting process feasibility. Thus pathways that allow for feedstock diversification present an important advantage when compared with technologies that can only process limited feedstocks. One of the most significant advantages of thermochemical technologies (see Table 7), such as gasification and pyrolysis, is the high diversity of feedstock, from waste (household, food, municipal, sewage sludge) to animal manure, including forest and agricultural biomass residues. Hamelinck and Faaij estimated the feedstock costs as 45–58% of the total fuel production costs, highlighting the importance of feedstock flexibility [119]. Biofuels production costs are highly dependent on feedstock price [120], which can vary considerable with the type, season, and country. Consequently, technologies that use a variety of feedstocks are attractive, allowing the most economical feedstock to be used at any given time.
Additional technological steps required to address end user product specifications, will further increase the overall costs and need to be taken into consideration. For example, the addition of the hydrolysis (acid/enzymatic) step to the biochemical route to process lignocellulosic biomass results in higher costs and technological complexity but it allows for feedstock flexibility. The effect of economies of scales is also a significant factor in biofuel production costs, thus a comprehensive technoeconomic study is required to assess the feasibility of each route to produce a specific biofuel [121].
Further factors that require consideration are market readiness and technological maturity. Many of the presented technologies are commercially mature because they have been successfully applied for many years to first generation biofuels. Technologies such as gasification which only requires small modifications in order to produce second generation biofuels. Gasifiers are already commercially spread around the world; there are more than 270 operational plants, mostly in Asia and Australia, and over 100 more currently under construction [122]. On the other hand, some technologies, such as biochemical fermentation, require further modifications to produce second generation biofuels. These additional technological steps make the process costlier and more complicated, and are therefore hindering its commercial adoption.
Taking into consideration factors such as technological maturity, the market, feedstock availability and location, each technology presents its own advantages and disadvantages. As a result a detailed process design and technoeconomic analysis is required to assess the feasibility of any route to produce a specific biofuel.
The transition from fossils fuels to advanced liquid biofuels will have an enormous impact on global climate change due to the resulting reduction in GHG emissions. The production of advanced liquid biofuels cannot rely solely on a specific process since each technology strongly depends on biomass feedstock composition. To add to this complexity, the final product obtained from each technology and feedstock varies in quality and type. The integration of technologies and variety into the biomass supply chain can overcome some/all of the issues associated with cost and product quality.
The authors declare no conflict of interest.
[1] | IRENA (2018) Global energy transformation: A roadmap to 2050. Int Renew Energ Agency, Abu Dhabi. |
[2] | IEA (2010) Sustainable production of second-generation biofuels: Potential and perspectives in major economies and developing countries. Int Energy Agency, IEA/OECD, Paris. |
[3] |
Ho DP, Ngo HH, Guo W (2014) A mini review on renewable sources for biofuel. Bioresour Technol 169: 742–749. doi: 10.1016/j.biortech.2014.07.022
![]() |
[4] |
Mahmudul HM, Hagos FY, Mamat R, et al. (2017) Production, characterization and performance of biodiesel as an alternative fuel in diesel engines-a review. Renew Sust Energ Rev 72: 497–509. doi: 10.1016/j.rser.2017.01.001
![]() |
[5] |
Al-Mashhadani H, Fernando S (2017) Properties, performance, and applications of biofuel blends: a review. AIMS Energy 5: 735–767. doi: 10.3934/energy.2017.4.735
![]() |
[6] | Küüt A, Ritslaid K, Küüt K, et al. (2019) Chapter 3-State of the Art on the Conventional Processes for Ethanol Production. Ethanol, 61–101. |
[7] |
Zabed H, Sahu JN, Suely A, et al. (2017) Bioethanol production from renewable sources: Current perspectives and technological progress. Renew Sust Energ Rev 71: 475–501. doi: 10.1016/j.rser.2016.12.076
![]() |
[8] |
Zabed H, Sahu JN, Boyce AN, et al. (2016) Fuel ethanol production from lignocellulosic biomass: An overview on feedstocks and technological approaches. Renew Sust Energ Rev 66: 751–774. doi: 10.1016/j.rser.2016.08.038
![]() |
[9] |
Zhu JY, Pan XJ (2010) Woody biomass pretreatment for cellulosic ethanol production: Technology and energy consumption evaluation. Bioresour Technol 101: 4992–5002. doi: 10.1016/j.biortech.2009.11.007
![]() |
[10] |
da Silva FL, de Oliveira Campos A, dos Santos DA (2018) Valorization of an agroextractive residue-Carnauba straw-for the production of bioethanol by simultaneous saccharification and fermentation (SSF). Renew Energy 127: 661–669. doi: 10.1016/j.renene.2018.05.025
![]() |
[11] |
Nguyen QA, Yang J, Bae HJ (2017) Bioethanol production from individual and mixed agricultural biomass residues. Ind Crop Prod 95: 718–725. doi: 10.1016/j.indcrop.2016.11.040
![]() |
[12] | Rana V, Eckard AD, Ahring BK (2014) Comparison of SHF and SSF of wet exploded corn stover and loblolly pine using in-house enzymes produced from T. reesei RUT C30 and A. saccharolyticus. SpringerPlus 3: 516. |
[13] |
Dahnum D, Tasum SO, Triwahyuni E (2015) Comparison of SHF and SSF Processes Using Enzyme and Dry Yeast for Optimization of Bioethanol Production from Empty Fruit Bunch. Energy Procedia 68: 107–116. doi: 10.1016/j.egypro.2015.03.238
![]() |
[14] |
Cotana F, Cavalaglio G, Gelosia M, et al. (2015) A comparison between SHF and SSSF processes from cardoon for ethanol production. Ind Crop Prod 69: 424–432. doi: 10.1016/j.indcrop.2015.02.064
![]() |
[15] |
Gonçalves FA, Ruiz HA, da Costa Nogueira C, et al. (2014) Comparison of delignified coconuts waste and cactus for fuel-ethanol production by the simultaneous and semi-simultaneous saccharification and fermentation strategies. Fuel 131: 66–76. doi: 10.1016/j.fuel.2014.04.021
![]() |
[16] |
Ishola MM, Jahandideh A, Haidarian B, et al. (2013) Simultaneous saccharification, filtration and fermentation (SSFF): A novel method for bioethanol production from lignocellulosic biomass. Bioresour Technol 133: 68–73. doi: 10.1016/j.biortech.2013.01.130
![]() |
[17] | Liu G, Zhang Q, Li H, et al. (2017) Dry biorefining maximizes the potentials of simultaneous saccharification and co-fermentation for cellulosic ethanol production. Biotechnol Bioeng 115: 60–69. |
[18] |
den Haan R, van Rensburg E, Rose SH, et al. (2015) Progress and challenges in the engineering of non-cellulolytic microorganisms for consolidated bioprocessing. Curr Opin Biotechnol 33: 15–22. doi: 10.1016/j.copbio.2014.09.008
![]() |
[19] |
Horisawa S, Ando H, Ariga O (2015) Direct ethanol production from cellulosic materials by consolidated biological processing using the wood rot fungus Schizophyllum commune. Bioresour Technol 197: 37–41. doi: 10.1016/j.biortech.2015.08.031
![]() |
[20] | Huang J, Chen D, Wei Y, et al. (2014) Direct ethanol production from lignocellulosic sugars and sugarcane bagasse by a recombinant Trichoderma reesei strain HJ48. Sci World J 2014: 798683. |
[21] |
Loaces I, Schein S, Noya F (2017) Ethanol production by Escherichia coli from Arundo donax biomass under SSF, SHF or CBP process configurations and in situ production of a multifunctional glucanase and xylanase. Bioresour Technol 224: 307–313. doi: 10.1016/j.biortech.2016.10.075
![]() |
[22] |
Bridgwater AV (2003) Renewable Fuels and Chemicals by Thermal Processing of Biomass. Chem Eng J 91: 87–102. doi: 10.1016/S1385-8947(02)00142-0
![]() |
[23] |
Acharya B, Roy P, Dutta A (2014) Review of syngas fermentation processes for bioethanol. Biofuels 5: 551–564. doi: 10.1080/17597269.2014.1002996
![]() |
[24] | Devarapalli M, Atiyeh HK (2015) A review of conversion processes for bioethanol production with a focus on syngas fermentation. Biofuel Res J 7: 268–280. |
[25] |
Abubackar HN, Veiga MC, Kennes C (2018) Production of acids and alcohols from syngas in a two-stage continuous fermentation process. Bioresour Technol 253: 227–234. doi: 10.1016/j.biortech.2018.01.026
![]() |
[26] |
Fernández-Naveira Á, Veiga MC, Kennes C (2017) Effect of pH control on the anaerobic H-B-E fermentation of syngas in bioreactors. J Chem Technol Biot 92: 1178–1185. doi: 10.1002/jctb.5232
![]() |
[27] |
Devarapalli M, Atiyeh HK, Phillips JR (2016) Ethanol production during semi-continuous syngas fermentation in a trickle bed reactor using Clostridium ragsdalei. Bioresour Technol 209: 56–65. doi: 10.1016/j.biortech.2016.02.086
![]() |
[28] |
Sun X, Atiyeh HK, Kumar A, et al. (2018) Enhanced ethanol production by Clostridium ragsdalei from syngas by incorporating biochar in the fermentation medium. Bioresour Technol 247: 291–301. doi: 10.1016/j.biortech.2017.09.060
![]() |
[29] |
Liu K, Atiyeh HK, Stevenson BS, et al. (2014) Continuous syngas fermentation for the production of ethanol, n-propanol and n-butanol. Bioresour Technol 151: 69–77. doi: 10.1016/j.biortech.2013.10.059
![]() |
[30] |
Kumar S, Cho JH, Park J, et al. (2013) Advances in diesel-alcohol blends and their effects on the performance and emissions of diesel engines. Renew Sust Energ Rev 22: 46–72. doi: 10.1016/j.rser.2013.01.017
![]() |
[31] |
Elfasakhany A (2017) Investigations on performance and pollutant emissions of spark-ignition engines fueled with n-butanol-, isobutanol-, ethanol-, methanol-, and acetone-gasoline blends: A comparative study. Renew Sust Energ Rev 71: 404–413. doi: 10.1016/j.rser.2016.12.070
![]() |
[32] |
Xue C, Zhang X, Wang J, et al. (2017) The advanced strategy for enhancing biobutanol production and high-efficient product recovery with reduced wastewater generation. Biotechnol Biofuels 10: 148. doi: 10.1186/s13068-017-0836-7
![]() |
[33] |
Xue C, Zhao J, Chen L (2017) Recent advances and state-of-the-art strategies in strain and process engineering for biobutanol production by Clostridium acetobutylicum. Biotechnol Adv 35: 310–322. doi: 10.1016/j.biotechadv.2017.01.007
![]() |
[34] |
Suresh M, Jawahar CP, Richard A (2018) A review on biodiesel production, combustion, performance, and emission characteristics of non-edible oils in variable compression ratio diesel engine using biodiesel and its blends. Renew Sust Energ Rev 92: 38–49. doi: 10.1016/j.rser.2018.04.048
![]() |
[35] |
Saluja RS, Kumar V, Sham R (2016) Stability of biodiesel-a review. Renew Sust Energ Rev 62: 866–881. doi: 10.1016/j.rser.2016.05.001
![]() |
[36] |
Knothe G, Razon LF (2017) Biodiesel fuels. Prog Energ Combust 58: 36–59. doi: 10.1016/j.pecs.2016.08.001
![]() |
[37] |
Abdullah SHYS, Hanapi NHM, Azid A, et al. (2017) A review of biomass-derived heterogeneous catalyst for a sustainable biodiesel production. Renew Sust Energ Rev 70: 1040–1051. doi: 10.1016/j.rser.2016.12.008
![]() |
[38] |
Islam A, Taufiq-Yap YH, Chan ES, et al. (2014) Advances in solid-catalytic and non-catalytic technologies for biodiesel production. Energ Convers Manage 88: 1200–1218. doi: 10.1016/j.enconman.2014.04.037
![]() |
[39] |
Okoro OV, Sun Z, Birch J (2018) Catalyst-Free Biodiesel Production Methods: A Comparative Technical and Environmental Evaluation. Sustainability 10: 127. doi: 10.3390/su10010127
![]() |
[40] |
Othman MF, Adam A, Najafi G, et al. (2017) Green fuel as alternative fuel for diesel engine: A review. Renew Sust Energ Rev 80: 694–709. doi: 10.1016/j.rser.2017.05.140
![]() |
[41] |
Vonortas A, Papayannakos N (2014) Comparative analysis of biodiesel versus green diesel. Wiley Interdiscip Rev Energy Environ 3: 3–23. doi: 10.1002/wene.78
![]() |
[42] |
Manchanda T, Tyagi R, Sharma DK (2018) Comparison of fuel characteristics of green (renewable) diesel with biodiesel obtainable from algal oil and vegetable oil. Energy Sources Part A 40: 54–59. doi: 10.1080/15567036.2017.1405109
![]() |
[43] |
Shamsul NS, Kamarudin SK, Rahman NA, et al. (2014) An overview on the production of bio-methanol as potential renewable energy. Renew Sust Energ Rev 33: 578–588. doi: 10.1016/j.rser.2014.02.024
![]() |
[44] | Minteer SD (2011) Biochemical production of other bioalcohols: Biomethanol, biopropanol, bioglycerol, and bioethylene glycol, In: Rafael Luque, Juan Campelo, James Clark (Editors.), Handbook of Biofuels Production, Woodhead Publishing 11: 258–265. |
[45] | Dalena F, Senatore A, Marino A, et al. (2018) Methanol Production and Applications: An Overview. Methanol 1: 3–28. |
[46] |
Iaquaniello G, Centi G, Salladini A, et al. (2017) Waste-to-methanol: Process and economics assessment. Bioresour Technol 243: 611–619. doi: 10.1016/j.biortech.2017.06.172
![]() |
[47] |
Svanberg M, Ellis J, Lundgren J, et al. (2018) Renewable methanol as a fuel for the shipping industry. Renew Sust Energ Rev 94: 1217–1228. doi: 10.1016/j.rser.2018.06.058
![]() |
[48] |
Schmitz N, Burger J, Ströfer E (2016) From methanol to the oxygenated diesel fuel poly(oxymethylene) dimethyl ether: An assessment of the production costs. Fuel 185: 67–72. doi: 10.1016/j.fuel.2016.07.085
![]() |
[49] |
Park SH, Lee CS (2014) Applicability of dimethyl ether (DME) in a compression ignition engine as an alternative fuel. Energ Convers Manage 86: 848–863. doi: 10.1016/j.enconman.2014.06.051
![]() |
[50] |
Lautenschütz L, Oestreich D, Seidenspinner P, et al. (2016) Physico-chemical properties and fuel characteristics of oxymethylene dialkyl ethers. Fuel 173: 129–137. doi: 10.1016/j.fuel.2016.01.060
![]() |
[51] |
Thomas G, Feng B, Veeraragavan A (2014) Emissions from DME combustion in diesel engines and their implications on meeting future emission norms: A review. Fuel Process Technol 119: 286–304. doi: 10.1016/j.fuproc.2013.10.018
![]() |
[52] |
Kim HJ, Park SH (2016) Optimization study on exhaust emissions and fuel consumption in a dimethyl ether (DME) fueled diesel engine. Fuel 182: 541–549. doi: 10.1016/j.fuel.2016.06.001
![]() |
[53] |
Bîldea CS, Győrgy R, Brunchi CC, et al. (2017) Optimal design of intensified processes for DME synthesis. Comput Chem Eng 105: 142–151. doi: 10.1016/j.compchemeng.2017.01.004
![]() |
[54] |
Azizi Z, Rezaeimanesh M, Tohidian T, et al. (2014) Dimethyl ether: A review of technologies and production challenges. Chem Eng Process 82: 150–172. doi: 10.1016/j.cep.2014.06.007
![]() |
[55] |
Baranowski CJ, Bahmanpour AM, Kröcher O (2017) Catalytic synthesis of polyoxymethylene dimethyl ethers (OME): A review. Appl Catal B-Environ 217: 407–420. doi: 10.1016/j.apcatb.2017.06.007
![]() |
[56] |
Parvez AM, Wu T, Li S, et al. (2018) Bio-DME production based on conventional and CO2-enhanced gasification of biomass: A comparative study on exergy and environmental impacts. Biomass Bioenerg 110: 105–113. doi: 10.1016/j.biombioe.2018.01.016
![]() |
[57] |
Mythili R, Venkatachalam P, Subramanian P (2013) Characterization of bioresidues for bio-oil production through pyrolysis. Bioresour Technol 138: 71–78. doi: 10.1016/j.biortech.2013.03.161
![]() |
[58] |
Mosier N, Wyman C, Dale B, et al. (2005) Features of promising technologies for pretreatment of lignocellulosic biomass. Bioresour Technol 96: 673–686. doi: 10.1016/j.biortech.2004.06.025
![]() |
[59] |
Czernik S, Bridgwater AV (2004) Overview of applications of biomass fast pyrolysis oil. Energ Fuel 18: 590–598. doi: 10.1021/ef034067u
![]() |
[60] |
Oasmaa A, Czernik S (1999) Fuel Oil Quality of Biomass Pyrolysis Oils: State of the Art for the End Users. Energ Fuel 13: 914–921. doi: 10.1021/ef980272b
![]() |
[61] |
Lehto J, Oasmaa A, Solantausta Y, et al. (2014) Review of fuel oil quality and combustion of fast pyrolysis bio-oils from lignocellulosic biomass. Appl Energ 116: 178–190. doi: 10.1016/j.apenergy.2013.11.040
![]() |
[62] | Hornung A, Apfelbacher A, Sagi S (2011) Intermediate pyrolysis: A sustainable biomass-to-energy concept-Biothermal valorisation of biomass (BtVB) process. J Sci Ind Res 70: 664–667. |
[63] |
Bridgwater AV (2012) Review of fast pyrolysis of biomass and product upgrading. Biomass Bioenerg 38: 68–94. doi: 10.1016/j.biombioe.2011.01.048
![]() |
[64] |
Gollakota ARK, Kishore N, Gu S (2018) A review on hydrothermal liquefaction of biomass. Renew Sust Energ Rev 81: 1378–1392. doi: 10.1016/j.rser.2017.05.178
![]() |
[65] | Huang YF, Chiueh PT, Lo SL (2016) A review on microwave pyrolysis of lignocellulosic biomass. Sust Environ Res 26: 103–109. |
[66] |
Furimsky E (2000) Catalytic hydrodeoxygenation. Appl Catal A-Gen 199: 147–190. doi: 10.1016/S0926-860X(99)00555-4
![]() |
[67] |
Gollakota ARK, Reddy M, Subramanyam MD, et al. (2016) A review on the upgradation techniques of pyrolysis oil. Renew Sust Energ Rev 58: 1543–1568. doi: 10.1016/j.rser.2015.12.180
![]() |
[68] |
Bridgwater AV (2012) Review of fast pyrolysis of biomass and product upgrading. Biomass Bioenerg 38: 68–94. doi: 10.1016/j.biombioe.2011.01.048
![]() |
[69] | Elliott D, Baker E (1983) Biomass Liquefaction Product Analysis and Upgrading. Pacific Northwest Lab: Richland, WA, USA. |
[70] | Baker EG, Elliott DC (1988) Catalytic hydrotreating of biomass derived oils, In: Soltes J, Milne TA, Pyrolysis oils from biomass e producing, analysing and upgrading, 228–240. |
[71] |
Elliott DC, Hart TR, Neuenschwander GG, et al. (2012) Catalytic hydroprocessing of fast pyrolysis bio-oil from pine sawdust. Energ Fuel 26: 3891–3896. doi: 10.1021/ef3004587
![]() |
[72] |
Wildschut J, Mahfud FH, Venderbosch RH (2009) Hydrotreatment of Fast Pyrolysis Oil Using Heterogeneous Noble-Metal Catalysts. Ind Eng Chem Res 48: 10324–10334. doi: 10.1021/ie9006003
![]() |
[73] | Chaiwat W, Gunawan R, Gholizadeh M, et al. (2013) Upgrading of bio-oil into advanced biofuels and chemicals. Part II. Importance of holdup of heavy species during the hydrotreatment of bio-oil in a continuous packed-bed catalytic reactor. Fuel 112: 302–310. |
[74] |
Wildschut J, Melian-Cabrera I, Heeres HJ (2010) Catalyst studies on the hydrotreatment of fast pyrolysis oil. Appl Catal B-Environ 99: 298–306. doi: 10.1016/j.apcatb.2010.06.036
![]() |
[75] |
Oh S, Choi HS, Choi IG, et al. (2017) Evaluation of hydrodeoxygenation reactivity of pyrolysis bio-oil with various Ni-based catalysts for improvement of fuel properties. RSC Adv 7: 15116–15126. doi: 10.1039/C7RA01166K
![]() |
[76] |
Xu Y, Wang T, Ma L, et al. (2010) Upgrading of the liquid fuel from fast pyrolysis of biomass over MoNi/γ-Al2O3 catalysts. Appl Energ 87: 2886–2891. doi: 10.1016/j.apenergy.2009.10.028
![]() |
[77] |
Cheng S, Wei L, Julson J, et al. (2017) Upgrading pyrolysis bio-oil through hydrodeoxygenation (HDO) using non-sulfided Fe-Co/SiO2 catalyst. Energ Convers Manage 150: 331–342. doi: 10.1016/j.enconman.2017.08.024
![]() |
[78] | Guo C, Rao KTV, Reyhanitash E, et al. (2016) Novel inexpensive transition metal phosphide catalysts for upgrading of pyrolysis oil via hydrodeoxygenation. React Eng Kinet Catal 62: 3664–3672. |
[79] |
Guo C, Rao KTV, Yuan Z (2018) Hydrodeoxygenation of fast pyrolysis oil with novel activated carbon-supported NiP and CoP catalysts. Chem Eng Sci 178: 248–259. doi: 10.1016/j.ces.2017.12.048
![]() |
[80] | Bridgwater AV (2012) Upgrading biomass fast pyrolysis liquids. TC-Biomass 2011 Special Issue. |
[81] |
Williams PT, Horne PA (1995) The influence of catalyst regeneration on the composition of zeolite-upgraded biomass pyrolysis oils. Fuel 74: 1839–1851. doi: 10.1016/0016-2361(95)80017-C
![]() |
[82] |
Williams PT, Nugranad N (2000) Comparison of products from the pyrolysis and catalytic pyrolysis of rice husks. Energy 25: 493–513. doi: 10.1016/S0360-5442(00)00009-8
![]() |
[83] |
Li HY, Yan YJ, Ren ZW (2008) Online upgrading of organic vapours from the fast pyrolysis of biomass. J Fuel Chem Technol 36: 666–671. doi: 10.1016/S1872-5813(09)60002-5
![]() |
[84] |
Iisa K, French RJ, Orton KA, et al. (2017) Production of low-oxygen bio-oil via ex situ catalytic fast pyrolysis and hydrotreating. Fuel 207: 413–422. doi: 10.1016/j.fuel.2017.06.098
![]() |
[85] |
Williams PT, Horne PA (1995) The influence of catalyst type on the composition of upgraded biomass pyrolysis oils. J Anal Appl Pyrol 31: 39–61. doi: 10.1016/0165-2370(94)00847-T
![]() |
[86] |
Antonakou E, Lappas A, Nilsen MH, et al. (2006) Evaluation of various types of Al-MCM-41 materials as catalysts in biomass pyrolysis for the production of bio-fuels and chemicals. Fuel 85: 2202–2212. doi: 10.1016/j.fuel.2006.03.021
![]() |
[87] |
Nokkosmäki MI, Kuoppala ET, Leppämäki EA, et al. (1998) A novel test method for cracking catalysts. J Anal Appl Pyrol 44: 193–204. doi: 10.1016/S0165-2370(97)00080-6
![]() |
[88] |
Pütün E (2010) Catalytic pyrolysis of biomass: Effects of pyrolysis temperature, sweeping gas flow rate and MgO catalyst. Energy 35: 2761–2766. doi: 10.1016/j.energy.2010.02.024
![]() |
[89] | Sitzmann J (2009) Upgrading of fast pyrolysis oils by hot filtration, Available from: https://research.aston.ac.uk/portal/en/theses/upgrading-of-fast-pyrolysis-oils-by-hot-filtration(28597c38-605b-44a3-917c-3748fa8da8ab).html. |
[90] |
Xiu S, Shahbazi A (2012) Bio-oil production and upgrading research: A review. Renew Sust Energ Rev 16: 4406–4414. doi: 10.1016/j.rser.2012.04.028
![]() |
[91] |
Baloch HA, Nizamuddin S, Siddiqui MTH, et al. (2018) Recent advances in production and upgrading of bio-oil from biomass: A critical overview. J Environ Chem Eng 6: 5101–5118. doi: 10.1016/j.jece.2018.07.050
![]() |
[92] |
Wang JJ, Chang J, Fan J (2010) Upgrading of Bio-oil by Catalytic Esterification and Determination of Acid Number for Evaluating Esterification Degree. Energ Fuel 24: 3251–3255. doi: 10.1021/ef1000634
![]() |
[93] |
Liu Y, Li Z, Leahy JJ (2015) Catalytically Upgrading Bio-oil via Esterification. Energ Fuel 29: 3691–3698. doi: 10.1021/acs.energyfuels.5b00163
![]() |
[94] |
Wu L, Hu X, Wang S (2018) Acid-treatment of bio-oil in methanol: The distinct catalytic behaviours of a mineral acid catalyst and a solid acid catalyst. Fuel 212: 412–421. doi: 10.1016/j.fuel.2017.10.049
![]() |
[95] |
Lin BJ, Chen WH, Budzianowski WM, et al. (2016) Emulsification analysis of bio-oil and diesel under various combinations of emulsifiers. Appl Energ 178: 746–757. doi: 10.1016/j.apenergy.2016.06.104
![]() |
[96] |
Gutiérrez-Antonio C, Gómez-Castro FI, de Lira-Flores JA, et al. (2017) A review on the production processes of renewable jet fuel. Renew Sust Energ Rev 79: 709–729. doi: 10.1016/j.rser.2017.05.108
![]() |
[97] | UOP Honeywell (2017) Honeywell Green Jet Fuel. Available from: https://www.uop.com/processing-solutions/renewables/green-jet-fuel/ [accessed October 31, 2018]. |
[98] |
Robota HJ, Alger JC, Shafer L (2013) Converting Algal Triglycerides to Diesel and HEFA Jet Fuel Fractions. Energ Fuel 27: 985–996. doi: 10.1021/ef301977b
![]() |
[99] |
Choi IH, Lee JS, Kim CU, et al. (2018) Production of bio-jet fuel range alkanes from catalytic deoxygenation of Jatropha fatty acids on a WOx/Pt/TiO2 catalyst. Fuel 215: 675–685. doi: 10.1016/j.fuel.2017.11.094
![]() |
[100] |
Zhao X, Wei L, Julson J, et al. (2015) Catalytic cracking of non-edible sunflower oil over ZSM-5 for hydrocarbon bio-jet fuel. New Biotechnol 32: 300. doi: 10.1016/j.nbt.2015.01.004
![]() |
[101] |
Liu S, Zhu Q, Guan Q, et al. (2015) Bio-aviation fuel production from hydroprocessing castor oil promoted by the nickel-based bifunctional catalysts. Bioresour Technol 183: 93–100. doi: 10.1016/j.biortech.2015.02.056
![]() |
[102] |
Li T, Cheng J, Huang R, et al. (2015) Conversion of waste cooking oil to jet biofuel with nickel-based mesoporous zeolite Y catalyst. Bioresour Technol 197: 289–294. doi: 10.1016/j.biortech.2015.08.115
![]() |
[103] |
Toba M, Abe Y, Kuramochi H, et al. (2011) Hydrodeoxygenation of waste vegetable oil over sulfide catalysts. Catal Today 164: 533–537. doi: 10.1016/j.cattod.2010.11.049
![]() |
[104] |
Tijmensen MJA, Faaij APC, Hamelinck CN (2002) Exploration of the possibilities for production of Fischer-Tropsch liquids and power via biomass gasification. Biomass Bioenerg 23: 129–152. doi: 10.1016/S0961-9534(02)00037-5
![]() |
[105] |
Larson ED, Jin H, Celik FE (2009) Large-scale gasification-based co-production of fuels and electricity from switchgrass. Biofuels Bioprod Biorefin 3: 174–194. doi: 10.1002/bbb.137
![]() |
[106] |
Hamelinck CN, Faaij APC, den Uil H, et al. (2004) Production of FT transportation fuels from biomass; technical options, process analysis and optimization, and development potential. Energy 29: 1743–1771. doi: 10.1016/j.energy.2004.01.002
![]() |
[107] | Choudhury HA, Chakma S, Moholkar VS (2015) Chapter 14-Biomass Gasification Integrated Fischer-Tropsch Synthesis: Perspectives, Opportunities and Challenges, In: Pandey A, Bhaskar T, Stöcker M, Sukumaran RK (Editors.), Recent Advances in Thermo-Chemical Conversion of Biomass, Elsevier, Boston, 383–435. |
[108] |
Susastriawan AAP, Saptoadi H (2017) Small-scale downdraft gasifiers for biomass gasification: A review. Renew Sust Energ Rev 76: 989–1003. doi: 10.1016/j.rser.2017.03.112
![]() |
[109] |
Dry ME (2004) Present and future applications of the Fischer-Tropsch process. Appl Catal A-Gen 276: 1–3. doi: 10.1016/j.apcata.2004.08.014
![]() |
[110] |
den Breejen JP, Sietsma JRA, Friedrich H, et al. (2010) Design of supported of cobalt catalysts with maximum activity for the Fischer-Tropsch synthesis. J Catal 270: 146–152. doi: 10.1016/j.jcat.2009.12.015
![]() |
[111] |
Davis BH (2009) Fischer-Tropsch synthesis: Reaction mechanisms for iron catalysts. Catal Today 141: 25–33. doi: 10.1016/j.cattod.2008.03.005
![]() |
[112] | Subiranas M, Schaub A (2007) Combining Fischer-Tropsch (FT) and hydrocarbon reactions under FT reaction conditions-Catalyst and reactor studies with Co or Fe and Pt/ZSM-5. Int J Chem React Eng 5: A78. |
[113] |
Rosyadi E, Priyanto U, Roesyadi A, et al. (2011) Biofuel production by hydrocracking of biomass FT wax over NiMo/Al2O3-SiO2 catalyst. J Jpn Inst Energy 90: 1171–1176. doi: 10.3775/jie.90.1171
![]() |
[114] |
Hillestad M, Ostadi M, Alamo Serrano Gd (2018) Improving carbon efficiency and profitability of the biomass to liquid process with hydrogen from renewable power. Fuel 234: 1431–1451. doi: 10.1016/j.fuel.2018.08.004
![]() |
[115] | Viguié JC, Ullrich N, Porot P, et al. (2013) BioTfueL project: Targeting the development of second-generation biodiesel and biojet fuels. Oil Gas Sci Technol 68: 953–946. |
[116] |
Hanaoka T, Miyazawa T, Shimura K, et al. (2015) Jet fuel synthesis in hydrocracking of Fischer-Tropsch product over Pt-loaded zeolite catalysts prepared using microemulsions. Fuel Process Technol 129: 139–146. doi: 10.1016/j.fuproc.2014.09.011
![]() |
[117] | LanzaTech (2018) UK Government Grant to Develop World First Waste Carbon to Jet Fuel Project. Available from: http://www.lanzatech.com/lanzatech-virgin-atlantic-secure-uk-government-grant-develop-world-first-waste-carbon-jet-fuel-project-uk/ [assessed November 1, 2018]. |
[118] |
de Freitas LC, Kanekov S (2011) Ethanol demand under the flex-fuel technology regime in Brazil. Energy Economics 33:1146-1154. doi: 10.1016/j.eneco.2011.03.011
![]() |
[119] |
Hamelinck CN, Faaij APC (2006) Outlook for advanced biofuels. Energ Policy 34: 3268–3283. doi: 10.1016/j.enpol.2005.06.012
![]() |
[120] |
Carriquiry MA, Du X, Timilsina GR (2011) Second generation biofuels: Economics and policies. Energ Policy 39: 4222–4234. doi: 10.1016/j.enpol.2011.04.036
![]() |
[121] |
Fivga A, Dimitriou I (2018) Pyrolysis of plastic waste for production of heavy fuel substitute: A techno-economic assessment. Energy 149: 865–874. doi: 10.1016/j.energy.2018.02.094
![]() |
[122] | Global Syngas Technologies Council. Available from: https://www.globalsyngas.org/resources/the-gasification-industry/ [assessed November 1, 2018]. |
1. | Arianna Callegari, Silvia Bolognesi, Daniele Cecconet, Andrea G. Capodaglio, Production technologies, current role, and future prospects of biofuels feedstocks: A state-of-the-art review, 2020, 50, 1064-3389, 384, 10.1080/10643389.2019.1629801 | |
2. | Miloud Ouadi, Antzela Fivga, Hessam Jahangiri, Muhammad Saghir, Andreas Hornung, A Review of the Valorization of Paper Industry Wastes by Thermochemical Conversion, 2019, 58, 0888-5885, 15914, 10.1021/acs.iecr.9b00635 | |
3. | Gabriel S. Aruwajoye, Alaika Kassim, Akshay K. Saha, Evariste B. Gueguim Kana, Prospects for the Improvement of Bioethanol and Biohydrogen Production from Mixed Starch-Based Agricultural Wastes, 2020, 13, 1996-1073, 6609, 10.3390/en13246609 | |
4. | Antzela Fivga, Hessam Jahangiri, Muhammad Asif Bashir, Artur J. Majewski, Andreas Hornung, Miloud Ouadi, Demonstration of catalytic properties of de-inking sludge char as a carbon based sacrificial catalyst, 2020, 146, 01652370, 104773, 10.1016/j.jaap.2020.104773 | |
5. | A. A. Porsin, E. N. Vlasova, A. L. Nuzhdin, P. V. Aleksandrov, G. A. Bukhtiyarova, Co-Processing of Straight Run Gas Oil-Rapeseed Oil Mixture Using Sulfide NiMo Catalyst on Zeolite-Containing Support, 2019, 92, 1070-4272, 1797, 10.1134/S1070427219120228 | |
6. | Ramya Ganesan, S. Manigandan, Melvin S. Samuel, Rajasree Shanmuganathan, Kathirvel Brindhadevi, Nguyen Thuy Lan Chi, Pham Anh Duc, Arivalagan Pugazhendhi, A review on prospective production of biofuel from microalgae, 2020, 27, 2215017X, e00509, 10.1016/j.btre.2020.e00509 | |
7. | Azeem Bo Strunck, Anil Suri, Vittorio Boffa, Effect of Temperature and Branched Crosslinkers on Supported Graphene Oxide Pervaporation Membranes for Ethanol Dehydration, 2020, 10, 2079-4991, 1571, 10.3390/nano10081571 | |
8. | Bertram Geinitz, Aline Hüser, Marcel Mann, Jochen Büchs, Gas Fermentation Expands the Scope of a Process Network for Material Conversion, 2020, 92, 0009-286X, 1665, 10.1002/cite.202000086 | |
9. | E.N. Vlasova, A.A. Porsin, P.V. Aleksandrov, A.L. Nuzhdin, G.A. Bukhtiyarova, Co‐processing of rapeseed oil — straight run gas oil mixture: Comparative study of sulfide CoMo/Al2O3-SAPO-11 and NiMo/Al2O3-SAPO-11 catalysts, 2020, 09205861, 10.1016/j.cattod.2020.11.017 | |
10. | Simon Boecker, Björn-Johannes Harder, Regina Kutscha, Stefan Pflügl, Steffen Klamt, Increasing ATP turnover boosts productivity of 2,3-butanediol synthesis in Escherichia coli, 2021, 20, 1475-2859, 10.1186/s12934-021-01554-x | |
11. | Amir Mahboubi, Shilan Elyasi, Wim Doyen, Heleen De Wever, Mohammad J. Taherzadeh, Concentration-driven reverse membrane bioreactor for the fermentation of highly inhibitory lignocellulosic hydrolysate, 2020, 92, 13595113, 409, 10.1016/j.procbio.2020.01.031 | |
12. | A. Mahboubi, C. Uwineza, W. Doyen, H. De Wever, M.J. Taherzadeh, Intensification of lignocellulosic bioethanol production process using continuous double-staged immersed membrane bioreactors, 2020, 296, 09608524, 122314, 10.1016/j.biortech.2019.122314 | |
13. | Dulce J. Hernández-Melchor, Beni Camacho-Pérez, Elvira Ríos-Leal, Jesus Alarcón-Bonilla, Pablo A. López-Pérez, Modelling and multi-objective optimization for simulation of hydrogen production using a photosynthetic consortium, 2020, 18, 1542-6580, 10.1515/ijcre-2020-0019 | |
14. | Ayesha Shahid, Abd ur Rehman, Muhammad Usman, Muhammad Umer Farooq Ashraf, Muhammad Rizwan Javed, Aqib Zafar Khan, Saba Shahid Gill, Muhammad Aamer Mehmood, Engineering the metabolic pathways of lipid biosynthesis to develop robust microalgal strains for biodiesel production, 2020, 67, 0885-4513, 41, 10.1002/bab.1812 | |
15. | E.N. Vlasova, A.A. Porsin, P.V. Aleksandrov, A.L. Nuzhdin, G.A. Bukhtiyarova, Co-hydroprocessing of straight-run gasoil – Rapeseed oil mixture over stacked bed Mo/Al2O3 + NiMo/Al2O3-SAPO-11 catalysts, 2021, 285, 00162361, 119504, 10.1016/j.fuel.2020.119504 | |
16. | Saeed Firouzi, Mohammad Sadegh Allahyari, Mohammadreza Isazadeh, Amin Nikkhah, Sam Van Haute, Hybrid multi-criteria decision-making approach to select appropriate biomass resources for biofuel production, 2021, 770, 00489697, 144449, 10.1016/j.scitotenv.2020.144449 | |
17. | Deepinder Jot Singh Aulakh, Kiari Goni Boulama, Jon G. Pharoah, On the reduction of electric energy consumption in electrolysis: A thermodynamic study, 2021, 03603199, 10.1016/j.ijhydene.2021.02.161 | |
18. | Pratima Bajpai, 2021, Chapter 8, 978-981-15-8778-8, 161, 10.1007/978-981-15-8779-5_8 | |
19. | Jon M. Wells, Susan E. Crow, Samir Kumar Khanal, Scott Turn, Andrew Hashimoto, Jim Kiniry, Norman Meki, Anaerobic Digestion and Hot Water Pretreatment of Tropically Grown C4 Energy Grasses: Mass, Carbon, and Energy Conversions from Field Biomass to Fuels, 2021, 11, 2073-4395, 838, 10.3390/agronomy11050838 | |
20. | Medhat Elkelawy, Hagar Alm-Eldin Bastawissi, Ahmed Mohamed Radwan, Mohamed Taha Ismail, Mostafa El-Sheekh, 2022, 9780128237649, 331, 10.1016/B978-0-12-823764-9.00003-0 | |
21. | Atia Al-Shuhoomi, Saif Al-Bahry, Yahya Al-Wahaibi, Sanket J. Joshi, 2021, Chapter 9, 978-981-16-1861-1, 231, 10.1007/978-981-16-1862-8_9 | |
22. | Dmitry V. Boguslavsky, Konstantin S. Sharov, Natalia P. Sharova, Using Alternative Sources of Energy for Decarbonization: A Piece of Cake, but How to Cook This Cake?, 2022, 19, 1660-4601, 16286, 10.3390/ijerph192316286 | |
23. | Mia Gotovuša, Mihovil Medić, Fabio Faraguna, Matea Šibalić, Lucija Konjević, Jelena Parlov Vuković, Marko Racar, Fatty acids propyl esters: Synthesis optimization and application properties of their blends with diesel and 1-propanol, 2022, 185, 09601481, 655, 10.1016/j.renene.2021.12.088 | |
24. | Anders S. Nielsen, M. Ostadi, Bjørn Austbø, M. Hillestad, Gonzalo del Alamo, Odne Burheim, Enhancing the efficiency of power- and biomass-to-liquid fuel processes using fuel-assisted solid oxide electrolysis cells, 2022, 321, 00162361, 123987, 10.1016/j.fuel.2022.123987 | |
25. | Palas Samanta, Tarakeshwar Senapati, Sukhendu Dey, Apurba Ratan Ghosh, 2023, 9781119808138, 46, 10.1002/9781119808428.ch3 | |
26. | Yi Fang, Wangliang Li, Siming You, 2022, 9780128243886, 379, 10.1016/B978-0-12-824388-6.00023-3 | |
27. | 2022, 9781119888833, 1, 10.1002/9781119888864.ch1 | |
28. | Alison S. Tomlin, Air Quality and Climate Impacts of Biomass Use as an Energy Source: A Review, 2021, 35, 0887-0624, 14213, 10.1021/acs.energyfuels.1c01523 | |
29. | Jakub Frankowski, Aleksandra Wawro, Jolanta Batog, Katarzyna Szambelan, Agnieszka Łacka, Bioethanol Production Efficiency from Sorghum Waste Biomass, 2022, 15, 1996-1073, 3132, 10.3390/en15093132 | |
30. | Monika Yadav, Venkatesh Balan, Sunita Varjani, Vinay Kumar Tyagi, Gaurav Chaudhary, Nidhi Pareek, Vivekanand Vivekanand, Multidisciplinary Pretreatment Approaches to Improve the Bio-methane Production from Lignocellulosic Biomass, 2023, 16, 1939-1234, 228, 10.1007/s12155-022-10489-z | |
31. | P. S. Awodi, T. N. Nwagu, J. Tivkaa, A. B. Ella, J. C. Ogbonna, Simultaneous saccharification and fermentation of pawpaw (Carica papaya) seeds for ethanol production, 2021, 34, 2229-4473, 671, 10.1007/s42535-021-00231-z | |
32. | Jesus R. Melendez, Bence Mátyás, Sufia Hena, Daniel A. Lowy, Ahmed El Salous, Perspectives in the production of bioethanol: A review of sustainable methods, technologies, and bioprocesses, 2022, 160, 13640321, 112260, 10.1016/j.rser.2022.112260 | |
33. | Sampath Gunukula, Laleh Emdadi, Asher C. Leff, Sampath A. Karunarathne, Sichao Cheng, Wei Wu, Dongxia Liu, Dat T. Tran, Ex-situ catalytic fast pyrolysis of wood chips over lamellar MFI zeolite supported nickel catalyst, 2023, 169, 01652370, 105821, 10.1016/j.jaap.2022.105821 | |
34. | Héctor de Paz Carmona, Jakub Frątczak, Zdeněk Tišler, José Miguel Hidalgo Herrador, Phonolite Material as Catalyst Support for the Hydrotreatment of Gas Oil and Vegetable Oil Type Feedstocks, 2022, 15, 1996-1944, 386, 10.3390/ma15010386 | |
35. | Shivali Banerjee, Vijay Singh, 2023, Chapter 3, 978-981-19-7480-9, 63, 10.1007/978-981-19-7481-6_3 | |
36. | Ramita Khanongnuch, Haris Nalakath Abubackar, Tugba Keskin, Mine Gungormusler, Gozde Duman, Ayushi Aggarwal, Shishir Kumar Behera, Lu Li, Büşra Bayar, Eldon R. Rene, Bioprocesses for resource recovery from waste gases: Current trends and industrial applications, 2022, 156, 13640321, 111926, 10.1016/j.rser.2021.111926 | |
37. | Neeraj K. Aggarwal, Naveen Kumar, Mahak Mittal, 2022, Chapter 10, 978-3-031-05090-9, 119, 10.1007/978-3-031-05091-6_10 | |
38. | Sukhendu Dey, Palas Samanta, Tarakeshwar Senapati, Apurba Ratan Ghosh, Sandipan Pal, 2022, Chapter 104-1, 978-981-16-4921-9, 1, 10.1007/978-981-16-4921-9_104-1 | |
39. | Mohit Yadav, Imre Szenti, Marietta Ábel, Ákos Szamosvölgyi, Kornéli B Ábrahámné, János Kiss, Pap Zsolt, András Sápi, Ákos Kukovecz, Zoltán Kónya, Concentrated Platinum‐Gallium Nanoalloy for Hydrogen Production from the Catalytic Steam Reforming of Ethanol, 2023, 15, 1867-3880, 10.1002/cctc.202200717 | |
40. | Abdul M. Petersen, Farai Chireshe, Oseweuba Okoro, Johann Gorgens, Johan Van Dyk, Evaluating refinery configurations for deriving sustainable aviation fuel from ethanol or syncrude, 2021, 219, 03783820, 106879, 10.1016/j.fuproc.2021.106879 | |
41. | Dalim Kumer Roy, Mohammad Zoynal Abedin, Potentiality of biodiesel and bioethanol production from feedstock in Bangladesh: A review, 2022, 8, 24058440, e11213, 10.1016/j.heliyon.2022.e11213 | |
42. | Krishnaveni Muthan, Merlin Sobia Poomani, Iyyadurai Mariappan, Venkatesh Subramanian, 2022, Chapter 8, 978-981-19-2911-3, 141, 10.1007/978-981-19-2912-0_8 | |
43. | Héctor de Paz Carmona, Aleš Vráblík, José Miguel Hidalgo Herrador, Romana Velvarská, Radek Černý, Animal fats as a suitable feedstock for co-processing with atmospheric gas oil, 2021, 5, 2398-4902, 4955, 10.1039/D1SE00917F | |
44. | Dalim Kumer Roy, Mohammad Zoynal Abedin, Potentiality of Biodiesel and Bioethanol Production from Feedstock in Bangladesh: A Review, 2021, 1556-5068, 10.2139/ssrn.3990736 | |
45. | Shengnan Li, Haixing Chang, Shiyu Zhang, Shih-Hsin Ho, Production of sustainable biofuels from microalgae with CO2 bio-sequestration and life cycle assessment, 2023, 00139351, 115730, 10.1016/j.envres.2023.115730 | |
46. | Morenike Ajike Peters, Carine Tondo Alves, Jude Azubuike Onwudili, A Review of Current and Emerging Production Technologies for Biomass-Derived Sustainable Aviation Fuels, 2023, 16, 1996-1073, 6100, 10.3390/en16166100 | |
47. | Ward Suijs, Rik De Graeve, Sebastian Verhelst, An exploratory study of knock intensity in a large-bore heavy-duty methanol engine, 2024, 302, 01968904, 118089, 10.1016/j.enconman.2024.118089 | |
48. | Dixita Chettri, Ashwani Kumar Verma, Anil Kumar Verma, Exploring the potential of microalgae cell factories for generation of biofuels, 2024, 15, 1759-7269, 245, 10.1080/17597269.2023.2233805 | |
49. | Sharron Ratshoshi, Hembe Elie Mukaya, Diakanua Nkazi, Hydrocracking of non‐edible vegetable oil and waste cooking oils for the production of light hydrocarbon fuels: A review, 2024, 102, 0008-4034, 3014, 10.1002/cjce.25255 | |
50. | Mohamed Ashour, Abdallah Tageldein Mansour, Yousef A. Alkhamis, Mostafa Elshobary, Usage of Chlorella and diverse microalgae for CO2 capture - towards a bioenergy revolution, 2024, 12, 2296-4185, 10.3389/fbioe.2024.1387519 | |
51. | Elissavet Emmanouilidou, Anastasia Lazaridou, Sophia Mitkidou, Nikolaos C. Kokkinos, E. Zervas, Biodiesel production from edible and non-edible biomasses and its characterization, 2023, 436, 2267-1242, 04003, 10.1051/e3sconf/202343604003 | |
52. | Vikas Sharma, Abul Kalam Hossain, Ganesh Duraisamy, Gareth Griffiths, Microalgal Biodiesel: A Challenging Route toward a Sustainable Aviation Fuel, 2023, 9, 2311-5637, 907, 10.3390/fermentation9100907 | |
53. | Muhammad Tawalbeh, Sara Maen Asaad, Abdullah Ali, Sara Rashid Al Kindi, Amani Al-Othman, 2024, 9780323952118, 245, 10.1016/B978-0-323-95211-8.00006-3 | |
54. | Márcio C.M. Souza, Francisco A.D. Maia, Vasco L. Pinto, Maria J.F. Costa, Aruzza M.M. Araújo, Djalma R. da Silva, Anne Gabriella D. Santos, Amanda D. Gondim, Highly porous cobalt and molybdenum-containing ordered silica applied to pyrolysis of sunflower oil into bio-hydrocarbons, 2023, 215, 09601481, 118962, 10.1016/j.renene.2023.118962 | |
55. | M. Dossow, V. Dieterich, A. Hanel, S. Fendt, 2022, 978-1-83916-393-7, 337, 10.1039/9781839167829-00337 | |
56. | Sukhendu Dey, Palas Samanta, Tarakeshwar Senapati, Apurba Ratan Ghosh, Sandipan Pal, 2025, Chapter 104, 978-981-97-4617-0, 1703, 10.1007/978-981-97-4618-7_104 | |
57. | Trashi Agrah Singh, Payal Basu, Tanim Arpit Singh, Ranjan Singh, 2025, 9780443315565, 15, 10.1016/B978-0-443-31556-5.00002-5 |
Properties | Petrol | E-100 | E-10 |
Viscosity mm2/s | 0.48–0.84 | 1.57 (20 ℃) | 0.53 (30 ℃) |
Flash Point ℃ | −65 | 13 | −40 |
RON ℃ | 86.4–100 | 108.6–114 | 87.4–94 |
MON ℃ | 80–98.8 | 89.7–112 | 86–99.9 |
Octane number | 86–94 | 98–100 | - |
Cloud point ℃ | −22 | - | 8 |
Pour point ℃ | (−17)–(−19) | - | 0 |
MJ/Kg | 41.9–44.4 | 26–30 | 33.19–44.22 |
Properties | Biobutanol | Petrol |
Boiling point (℃) | 118 | 200 |
Freezing point (℃) | −89 | −40 |
Density (kg/m3) | 810 | 760 |
Heat of vaporization (MJ/kg) | 0.43 | 0.36 |
Energy density (MJ/L) | 30 | 32 |
Cetane no | ~25 | 5–20 |
Flash point (℃) | 35 | −42 |
Auto-ignition temperature (℃) | 397 | 257 |
Properties | Biodiesel (ASTM D6751) | Biodiesel (EN 14214) | Fossil diesel |
Density 15 ℃ (kg/m3) | 880 | 860–900 | 820–850 |
Viscosity @ 40 ℃ (cSt) | 1.9–6.0 | 3.5–5.0 | 2.04–3.23 |
Calorific value (MJ/kg) | - | 35 | 42–48 |
Acidity total (mgKOH/g) | Max. 0.50 | Max. 0.5 | 0.02 |
Cetane number (min) | Min. 47 | Min. 51 | Min. 40 |
Iodine number (max) | - | 120 | - |
Flash point (℃) | Min. 93 | Min. 120 | Min. 52 |
Pour point (℃) | −15 to 10 | - | −35 to −15 |
Cloud point (℃) | −3 to 12 | - | −15 to 5 |
Cold filter plugging point (℃) | 19 | Max. 5 | 5 |
Copper strip corrosion (3 h–50 ℃) | Max. 3 | Min. 1 | Max. 3 |
Sulphur % (ppm) | Max. 15 | Max. 10 | Max. 15 |
Sulphated ash % (m/m) | Max. 0.02 | Max. 0.02 | Max. 0.01 |
Oxidation stability (min, 110 ℃) | 3 | 6 | - |
Properties | DME | OME | Fossil diesel |
Molecular weight | 46.07 | 76–196.2 | 96 |
Density 20 ℃ (kg/m3) | 660 | 960–1105 | 800–840 |
Viscosity @ 40 ℃ (cSt) | 0.12–0.15 | 0.64–1.75 | 2–4 |
Calorific value (MJ/kg) | 28.5 | 18.5–23.3 | 42.5 |
Cetane number (min) | 55–60 | 60–90 | Min. 40 |
Analysis | Typical wood derived bio-oil | Fossil diesel | LFO Motor/heating EN590 |
Water, wt.% | 20–30 | ∼0 | ∼0 |
Stability | Unstable* | ||
Viscosity (40 ℃), cSt | 15–35 | 2.04–3.23 | 2.0–4.5 |
Density (15 ℃), kg/dm3 | 1.10–1.30c | 0.820–0.850 | Max. 0.845 |
Flash point, ℃ | 40–110d | Min. 52 | Min.60 |
Pour point, ℃ | −9–36 | −35−15 | −5 min |
LHV, MJ/kg | 13–18c | 42–48 | 42.6 |
Distillability | Non-distillable | Distillable | Distillable |
*Polymerisation occurs during heating for prolonged periods. |
Properties | Biojet fuel |
Acidity, total (mgKOH/g) | 0.1 max |
Flash point (℃) | 38 min |
Density @15 ℃ (kg/m3) | 775–840 |
Freezing point (℃), max | −40 JetA; −47 JetA1 |
Viscosity @ −20 ℃ (cSt) | 8, max |
Net heat of comb (MJ/kg) | 42.8, min |
Product | Pathway | Advantages | Challenges |
Ethanol | Biochemical fermentation from sugars | Well-developed route Acid/enzymatic step allows for feedstock diversification | Development of microorganisms to be able to convert both type of sugars Research on process integration is required to achieve process feasibility |
Fermentation of syngas | All biomass components are utilised, including lignin | Syngas conditioning is required | |
Butanol | Biochemical fermentation from sugars | Simultaneous process with ethanol production | Product recovery process |
Fermentation of syngas | |||
Biodiesel | Catalytic Transesterification | Well-developed route Market ready for the product | Catalyst developed for first generation oils |
Supercritical Transesterification | High feedstock tolerance | Expensive process when compared to the catalytic route Extreme conditions and high energy demand (more development needed) | |
Green diesel | Bio-oil upgrading (HDO and HC) | Less feedstock limitation Similarity with fossil diesel | Bio-oil production technology challenges Catalyst |
Biomethanol | Gasification + MeOH Synthesis | Cost competitive with methanol from fossil fuels Developed market for the product | Gasification process challenges Syngas conditioning |
DME/OME | DME/OME Synthesis | Used as diesel replacement Not expensive | Inferior performance compared to the fossil fuel Challenges from the methanol production |
Petrol | Hydroprocessing followed by cracking/isomerisation | Several production routes | Further development on processing of bio-oil Low yields, is produced as a by-product |
Biojet fuel | Hydroprocessing of triglycerides | Cost competitive than the other biojet routes | Cost of catalysts and hydrogen Limited feedstock tolerance Product refining |
Biochemical fermentation of sugars to hydrocarbons | Fewer technological steps than ATJ fuels | Product refining | |
Biochemical fermentation of sugars to ethanol followed by hydrogenation | Less feedstock limitation | Product refining | |
FT synthesis | All biomass components are utilised, including lignin | Cost of FT synthesis |
Properties | Petrol | E-100 | E-10 |
Viscosity mm2/s | 0.48–0.84 | 1.57 (20 ℃) | 0.53 (30 ℃) |
Flash Point ℃ | −65 | 13 | −40 |
RON ℃ | 86.4–100 | 108.6–114 | 87.4–94 |
MON ℃ | 80–98.8 | 89.7–112 | 86–99.9 |
Octane number | 86–94 | 98–100 | - |
Cloud point ℃ | −22 | - | 8 |
Pour point ℃ | (−17)–(−19) | - | 0 |
MJ/Kg | 41.9–44.4 | 26–30 | 33.19–44.22 |
Properties | Biobutanol | Petrol |
Boiling point (℃) | 118 | 200 |
Freezing point (℃) | −89 | −40 |
Density (kg/m3) | 810 | 760 |
Heat of vaporization (MJ/kg) | 0.43 | 0.36 |
Energy density (MJ/L) | 30 | 32 |
Cetane no | ~25 | 5–20 |
Flash point (℃) | 35 | −42 |
Auto-ignition temperature (℃) | 397 | 257 |
Properties | Biodiesel (ASTM D6751) | Biodiesel (EN 14214) | Fossil diesel |
Density 15 ℃ (kg/m3) | 880 | 860–900 | 820–850 |
Viscosity @ 40 ℃ (cSt) | 1.9–6.0 | 3.5–5.0 | 2.04–3.23 |
Calorific value (MJ/kg) | - | 35 | 42–48 |
Acidity total (mgKOH/g) | Max. 0.50 | Max. 0.5 | 0.02 |
Cetane number (min) | Min. 47 | Min. 51 | Min. 40 |
Iodine number (max) | - | 120 | - |
Flash point (℃) | Min. 93 | Min. 120 | Min. 52 |
Pour point (℃) | −15 to 10 | - | −35 to −15 |
Cloud point (℃) | −3 to 12 | - | −15 to 5 |
Cold filter plugging point (℃) | 19 | Max. 5 | 5 |
Copper strip corrosion (3 h–50 ℃) | Max. 3 | Min. 1 | Max. 3 |
Sulphur % (ppm) | Max. 15 | Max. 10 | Max. 15 |
Sulphated ash % (m/m) | Max. 0.02 | Max. 0.02 | Max. 0.01 |
Oxidation stability (min, 110 ℃) | 3 | 6 | - |
Properties | DME | OME | Fossil diesel |
Molecular weight | 46.07 | 76–196.2 | 96 |
Density 20 ℃ (kg/m3) | 660 | 960–1105 | 800–840 |
Viscosity @ 40 ℃ (cSt) | 0.12–0.15 | 0.64–1.75 | 2–4 |
Calorific value (MJ/kg) | 28.5 | 18.5–23.3 | 42.5 |
Cetane number (min) | 55–60 | 60–90 | Min. 40 |
Analysis | Typical wood derived bio-oil | Fossil diesel | LFO Motor/heating EN590 |
Water, wt.% | 20–30 | ∼0 | ∼0 |
Stability | Unstable* | ||
Viscosity (40 ℃), cSt | 15–35 | 2.04–3.23 | 2.0–4.5 |
Density (15 ℃), kg/dm3 | 1.10–1.30c | 0.820–0.850 | Max. 0.845 |
Flash point, ℃ | 40–110d | Min. 52 | Min.60 |
Pour point, ℃ | −9–36 | −35−15 | −5 min |
LHV, MJ/kg | 13–18c | 42–48 | 42.6 |
Distillability | Non-distillable | Distillable | Distillable |
*Polymerisation occurs during heating for prolonged periods. |
Properties | Biojet fuel |
Acidity, total (mgKOH/g) | 0.1 max |
Flash point (℃) | 38 min |
Density @15 ℃ (kg/m3) | 775–840 |
Freezing point (℃), max | −40 JetA; −47 JetA1 |
Viscosity @ −20 ℃ (cSt) | 8, max |
Net heat of comb (MJ/kg) | 42.8, min |
Product | Pathway | Advantages | Challenges |
Ethanol | Biochemical fermentation from sugars | Well-developed route Acid/enzymatic step allows for feedstock diversification | Development of microorganisms to be able to convert both type of sugars Research on process integration is required to achieve process feasibility |
Fermentation of syngas | All biomass components are utilised, including lignin | Syngas conditioning is required | |
Butanol | Biochemical fermentation from sugars | Simultaneous process with ethanol production | Product recovery process |
Fermentation of syngas | |||
Biodiesel | Catalytic Transesterification | Well-developed route Market ready for the product | Catalyst developed for first generation oils |
Supercritical Transesterification | High feedstock tolerance | Expensive process when compared to the catalytic route Extreme conditions and high energy demand (more development needed) | |
Green diesel | Bio-oil upgrading (HDO and HC) | Less feedstock limitation Similarity with fossil diesel | Bio-oil production technology challenges Catalyst |
Biomethanol | Gasification + MeOH Synthesis | Cost competitive with methanol from fossil fuels Developed market for the product | Gasification process challenges Syngas conditioning |
DME/OME | DME/OME Synthesis | Used as diesel replacement Not expensive | Inferior performance compared to the fossil fuel Challenges from the methanol production |
Petrol | Hydroprocessing followed by cracking/isomerisation | Several production routes | Further development on processing of bio-oil Low yields, is produced as a by-product |
Biojet fuel | Hydroprocessing of triglycerides | Cost competitive than the other biojet routes | Cost of catalysts and hydrogen Limited feedstock tolerance Product refining |
Biochemical fermentation of sugars to hydrocarbons | Fewer technological steps than ATJ fuels | Product refining | |
Biochemical fermentation of sugars to ethanol followed by hydrogenation | Less feedstock limitation | Product refining | |
FT synthesis | All biomass components are utilised, including lignin | Cost of FT synthesis |