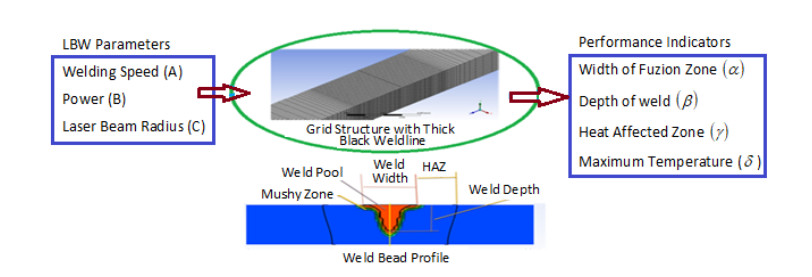
Airborne viruses such as SARS-CoV-2 are partly spread through aerosols containing viral particles. Inhalation of infectious airborne particles can lead to infection, a route that can be even more predominant than droplet or contact transmission. To study the transmission between a susceptible and an infected person, we estimated the distribution of arrival times of small diffusing aerosol particles to the inhaled region located below the nose until the number of particles reaches a critical threshold. Our results suggested that although contamination by continuous respiration can take approximately 90 min at a distance of 0.5 m, it is reduced to a few minutes when coughing or sneezing. Interestingly, there is not much difference between outdoors and indoors when the air is still. When a window is open inside an office, the infection time is reduced. Finally, wearing a mask leads to a delay in the time to infection. To conclude, diffusion analysis provides several key timescales of viral airborne transmission.
Citation: U. Dobramysl, C. Sieben, D. Holcman. Mean time to infection by small diffusing droplets containing SARS-CoV-2 during close social contacts[J]. Networks and Heterogeneous Media, 2024, 19(1): 384-404. doi: 10.3934/nhm.2024017
[1] | Ehsan Harati, Paul Kah . Laser welding of aluminum battery tab to variable Al/Cu busbars in Li-ion battery joint. AIMS Materials Science, 2022, 9(6): 884-918. doi: 10.3934/matersci.2022053 |
[2] | Shashi Bahl, Tarunpreet Singh, Virinder Kumar, Shankar Sehgal, Ashok Kumar Bagha . A systematic review on recent progress in advanced joining techniques of the lightweight materials. AIMS Materials Science, 2021, 8(1): 62-81. doi: 10.3934/matersci.2021005 |
[3] | Cahya Sutowo, Galih Senopati, Andika W Pramono, Sugeng Supriadi, Bambang Suharno . Microstructures, mechanical properties, and corrosion behavior of novel multi-component Ti-6Mo-6Nb-xSn-xMn alloys for biomedical applications. AIMS Materials Science, 2020, 7(2): 192-202. doi: 10.3934/matersci.2020.2.192 |
[4] | Francois Njock Bayock, Paul Kah, Kibong Marius Tony . Heat input effects on mechanical constraints and microstructural constituents of MAG and laser 316L austenitic stainless-steel welded joints. AIMS Materials Science, 2022, 9(2): 236-254. doi: 10.3934/matersci.2022014 |
[5] | Sharlane Costa, Maria S. Souza, Manuel B. César, José Gonçalves, João E. Ribeiro . Experimental and numerical study to minimize the residual stresses in welding of 6082-T6 aluminum alloy. AIMS Materials Science, 2021, 8(2): 271-282. doi: 10.3934/matersci.2021018 |
[6] | Zarina Aringozhina, Nurtoleu Magazov, Bauyrzhan Rakhadilov, Gulzhaz Uazyrkhanova, Auezhan Amanov . Effect of ultrasonic nanocrystalline surface modification on hardness and elastic modulus of Ti-6Al-4V alloy. AIMS Materials Science, 2025, 12(1): 101-117. doi: 10.3934/matersci.2025008 |
[7] | Muhammad Awwaluddin, Sri Hastuty, Djoko Hadi Prajitno, Makmuri, Budi Prasetiyo, Yudi Irawadi, Jekki Hendrawan, Harry Purnama, Eko Agus Nugroho . Effect of Yttrium on corrosion resistance of Zr-based alloys in Ringer's lactate solution for biomaterial applications. AIMS Materials Science, 2024, 11(3): 565-584. doi: 10.3934/matersci.2024028 |
[8] | Kipkurui N Ronoh, Fredrick M Mwema, Stephen A Akinlabi, Esther T Akinlabi, Nancy W Karuri, Harrison T Ngetha . Effects of cooling conditions and grinding depth on sustainable surface grinding of Ti-6Al-4V: Taguchi approach. AIMS Materials Science, 2019, 6(5): 697-712. doi: 10.3934/matersci.2019.5.697 |
[9] | N. S. Biradar . Effect of transverse mechanical arc oscillation on hot cracking (solidification & liquation) and weld metal properties of AA2014 T6 TIG welds. AIMS Materials Science, 2016, 3(4): 1544-1560. doi: 10.3934/matersci.2016.4.1544 |
[10] | Paul Kah, Pavel Layus, Benoit Ndiwe . Submerged arc welding process peculiarities in application for Arctic structures. AIMS Materials Science, 2022, 9(3): 498-511. doi: 10.3934/matersci.2022029 |
Airborne viruses such as SARS-CoV-2 are partly spread through aerosols containing viral particles. Inhalation of infectious airborne particles can lead to infection, a route that can be even more predominant than droplet or contact transmission. To study the transmission between a susceptible and an infected person, we estimated the distribution of arrival times of small diffusing aerosol particles to the inhaled region located below the nose until the number of particles reaches a critical threshold. Our results suggested that although contamination by continuous respiration can take approximately 90 min at a distance of 0.5 m, it is reduced to a few minutes when coughing or sneezing. Interestingly, there is not much difference between outdoors and indoors when the air is still. When a window is open inside an office, the infection time is reduced. Finally, wearing a mask leads to a delay in the time to infection. To conclude, diffusion analysis provides several key timescales of viral airborne transmission.
Because of small fusion zone and low distortion, laser welding (LW) is gaining industrial importance day by day. Weld quality depends on the weld bead geometry [1,2,3]. Titanium alloys are treated as good corrosion resistance and lightweight materials. They are of great demand in automotive, aerospace, nuclear and biomedical industries [4]. Researchers are in the continuous process of developing models to simplify the time-consuming simulations. For welding of titanium alloys, laser beam welding (LBW) is opted due to its versatility, high specific heat input, and flexibility. For optimal process conditions, its weld strength is close to that of parent material. However, the potential weldability issues are low elongation, corrosion resistance and inferior fatigue properties [5].
Denney and Metzobower have made an interesting discussion on LBW of titanium [6]. Du et al. have carried out LBW (laser beam welding) simulations and presented fully penetrated weld bead geometry profiles [7]. Benyounis et al. have adopted RSM (response surface methodology) and examined the influence of focal position, speed and laser power on the weld bead geometry of medium steel carbon steel [8]. Liao and Yu have examined the weld bead profiles of thin stainless steel sheets performing pulse laser welding by varying the laser energy and incident angle [9]. Akman et al. have examined the effect of pulse duration and energy on DOP (depth of penetration) by analyzing microstructures and strength properties [10]. ANN (artificial neural network) approach is adopted for investigating the weld geometry [11]. Yamashita et al. and Takemori et al. have performed simulations on LW process [12,13].
Sathiya et al. have followed the Taguchi approach and found the optimal LW parameters for alloy 904L [14]. Shanmugam et al. have utilized ANSYS and performed FEA (finite element analysis) for generating weld bead profiles of AISI 304 varying beam power, incident angle and exposure time [15]. Squillace et al. have examined the influence of LBW parameters on morphology, tensile and fatigue properties [16]. Cherepanov et al. have performed simulations on the thermo-physical processes at LW of alloys possessing refractory nanoparticles [17]. Cao et al. have made investigations on the porosities in the LBW of butt joints [18]. Song et al. have analyzed the residual stress distribution in titanium welds [19]. Akbari et al. have performed simulations on pulsed LW of Ti–6Al–4V alloy and observed 2% to 17% deviation in temperature distribution and melt pool geometry [20]. Gao et al. have examined the influence of LW parameters on porosity formation [21]. Gao et al. have achieved better titanium alloy strength properties with medium OLF (overlapping factor) [22]. The shapes of the molten pool from numerical simulations of Azizpour et al. are comparable with measured data [23]. Akbari et al. have adopted an ANN approach and performed simulations for temperature distribution and melt pool geometry [24]. Zhan et al. have made investigations on invar 36 alloy conducting MIG welding and hybrid laser-MIG welding [25]. Zhan et al. have made consistent assessments with experiments on the microstructure of Ti–6Al–2Zr–1Mo–1V LBW joints [26]. Oliveira et al. have made a survey on the joining of NiTi shape memory alloys [27]. LW of NiTi and Ti6Al4V utilizing niobium interlayer is examined in [28]. High quality of weld joints can be produced through fiber LW of AA6061-T6 [29]. Gursel et al. have observed crack risk in Nd:YAG laser welding [30]. Caiazzo et al. have made investigations on LW of 3 mm thick Ti6Al4V alloy plates and recommended optimal LW parameters to lower the undercut and porosity [31]. Kumar et al. have reported the effect of the scanning speed and beam power on the fiber LW of Ti6Al4V alloy [32]. Kumar et al. have performed simulations and LBW tests on 1 mm thick Ti–6Al–4V alloy sheets varying welding speed and laser power [33]. Samples annealed at 980 ℃ yield tensile strength of 1048 MPa, which is above 4% to that of conventional weld samples. Auwal et al. have discussed the effect of LW parameters weld defects [34]. Kumar et al. have reported optimal parameters, which yielded high tensile strength in pulsed Nd:YAG LW of Monel 400 and Hastelloy C276 sheets [35]. Jiang et al. have carried out simulations and experiments on LW of Ti–6Al–4V alloy varying average power, beam diameter and pulse energy [36]. Kumar and Sinha have made investigations on pulsed Nd:YAG LW of Ti6Al4V alloy varying heat input and presented bead profile, micro-hardness and tensile strength [37].
LBW process will be generally either in conduction or in keyhole mode [38]. Welding in conduction mode is carried out above melting and below vaporization of materials. Thermal convection due to Marangoni flow will be there in addition to heat conduction. In keyhole welding, the surface temperature is above the threshold of boiling point. A hole will be formed in the weld pool after vaporization. Defects (like spatter and blowholes) are introduced upon creation of strong recoil pressure on the melt in the keyhole welding process. Conduction welding is a stable process. It is possible to achieve high quality welds free of pores and spatter [39]. To perform good quality of welding, there is a need for reliable simulation tools and weld equipment's [40,41]. Numerical simulations are required to minimize the cost and time-consuming trial tests, which provide the temperature field and the weld bead geometry. High-speed video recording is required to examine the process on the weld pool surface.
This paper adopts the Taguchi's L9 OA (orthogonal array) in the numerical simulations to obtain optimal LBW process parameters for thin Ti–6Al–4V alloy sheets. By utilizing the Taguchi's design of experiments, empirical relations are developed for performance indicators in LBW simulations performing few trial runs. Narrow weld bead width with full depth of penetration is arrived by varying the LBW parameters. Empirical relations represent the weld bead profile. A set of optimal LBW parameters is finalized adopting a multi-objective optimization procedure.
Thermal history in the weld is essential for assessing the strength of weld joint. To improve the quality of weld, selection of optimal LBW parameters plays an important role. The time-consuming trial and error-based methods are expensive. A CFD Model is required for carrying out thermo-fluid analysis to generate the weld bead profile. A 3D model for LBW is developed (incorporating buoyancy and Marnangoni stress). ANSYS Fluent embodied with VC++ code is utilized to assess the generic nature of the model by comparing the measured weld bead profiles of different materials (viz., SS304L, carbon steel, zircoly-4 and Zr-1%Nb) [42,43,44,45,46,47]. In the present study, 2 mm thick Ti–6Al–4V alloy plates (having 50mm length and 20mm width) are considered to perform LBW simulations. Figure 1 shows the LBW parameters and performance indicators. For the 3 LBW process parameters with 3 levels, full factorial design of experiments requires 27 tests, whereas 9 tests are needed as per the Taguchi's L9 OA.
Numerical simulations are performed by varying 8 to 12 m/s welding speed; 150 to 250 W power; and 0.5 to 1.5 mm laser beam diameter. As in [43], the simulations are based on the solution of N–S (Navier–Stokes) equations, k-𝜀 equation in the regions of mushy zone and weld pool. The temperature dependent properties of Ti–6Al–4V alloy are considered [48]. Specific heat of solid is 670 J/(kg·K), whereas in case liquids it is 730 J/(kg·K). Viscosity of liquid is 0.005 kg/(m·s). Melting heat is 370000 J/kg. Solidus temperature (Ts) is 1878 K. Liquidus temperature (TL) is 1928 K.
Density, ρ (kg/m3) in terms of temperature, T (K) is Eq 1.
ρ=4466.2−0.154 T for T<1878K =31.34 T−18467 for 1878<T<1928K =5076.8−0.68 T for T>1928K | (1) |
The source term (or momentum frictional dissipation) in the mushy zone is Eq 2 [49,50].
→Sw=103 →w Amush for T<1878K ={(0.02T−37.56)3+10−3}−1×(38.56−0.02)2Amush for 1878<T<1928K=0 for T>1928K | (2) |
Here →w is the pull velocity and Amush is a constant of the mushy zone.
Thermal conductivity, κ (W·m−1·K−1) in terms of T (K) is Eq 3.
κ=−0.32+1.46×10−2 T for 1400<T<1850K=−6.66+1.83×10−2 T for 1950<T<2700K | (3) |
Following the welding process simulations [42,43,44,45,46,47] and considering the Ti–6Al–4V alloy properties, weld pool cross-section is generated specifying the welding speed (A), power (B) and the laser beam diameter (C) as per Taguchi's L9 OA. Details on the identification of optimal LBW parameters are presented in the next section.
Taguchi method is useful to design with few welding experiments for the process variables and the assigned levels. Analysis of variance (ANOVA) results will be helpful in identifying the optimal welding parameters. From the experimental data, it is possible to generate the data for the full factorial design of experiments. A simple statistical approach, known as the Taguchi method [51] recommends an orthogonal array (OA) to perform few tests for obtaining performance indicators (PIs). From these tests, it is possible to generate PIs for all combinations of the levels of input process variables. That is the possibility of generating data for the full factorial design of experiments. Obviously, this approach minimizes the cost as well as the time-consuming trial and error-based tests. A few of the successfully solved engineering/industrial optimization problems are damages due to drilling of composites [52,53,54,55], stage and satellite separation problems in space vehicles [56,57,58], performance of heat exchangers [59], design of planetary gears [60,61], welding process [62,63,64,65,66,67], machining process [68,69,70,71,72,73], and fuel engine performance [74,75,76,77].
Taguchi method [51] recommends L9 OA for LBW process variables, npv = 3 with levels, nvl = 3. The minimum test runs (Ntests) required is Eq 4.
Ntests=1+npv×(nvl−1)=1+3×(3−1)=7 | (4) |
This could be the reason why Taguchi method [51] recommends L9 OA. Tables 1 and 2, Figure 2 present numerical simulations of the PIs (viz., width of fusion zone, α (mm), depth of weld, β (mm), heat affected zone, γ (mm) and maximum temperature, δ (K)) and the simulated weld bead profiles for the nine test runs. Substituting Ntests = 9 and nvl = 3 in Eq 4, one gets npv = 4, which indicates the possibility of accommodating 4 process variables in 9 test runs. Modelling and Numerical simulations (utilizing ANSYS Fluent V16.0 with Vc++ code) are validated by comparing the measured weld bead profiles of different materials (viz., SS304L, carbon steel, zircoly-4 and Zr-1%Nb) [42,43,44,45,46,47]. As in [43], Table 1 introduces a fictitious parameter (D). ANOVA (analysis of variance) results are presented in Table 3. %Contribution of B is significant on the grand mean value of both α and β. %Contribution of A, B and C on α are 8.3%, 88.5% and 2.6% respectively, whereas 26.8%, 52.7% and 19.4% are respectively on β. Sum of the %Contributions of A, B and C on α and β are 99.5% and 99%. Hence, the %Contribution of D on both α and β are 0.5% and 1%, which are nothing but the error (%).
From ANOVA Table 3, the optimal LBW process variables to achieve minimum α (width of fusion zone) are A3B1C3, in which subscripts denote the levels of the process variables. The optimal LBW process variables to achieve maximum β (depth of weld) are A1B3C1. These two sets of optimal LBW process variables are found to be different for achieving minimum α and maximum β. If the set of LBW process variables is not in L9 OA of Table 2, then confirmation tests to obtain the PIs are mandatory.
LBW parameters | Designation | Level-1 | Level-2 | Level-3 |
Welding speed (mm/sec) | A | 8 | 10 | 12 |
Power (W) | B | 150 | 200 | 250 |
Laser beam diameter (mm) | C | 0.5 | 1.0 | 1.5 |
Fictitious | D | d1 | d2 | d3 |
Test S. No. | LBW parameters (levels) | Performance indicators | |||||||
A | B | C | D | α (mm) | β (mm) | γ (mm) | δ (K) | ||
1 | 1 | 1 | 1 | 1 | 2.062 | 1.597 | 1.545 | 2887 | |
2 | 1 | 2 | 2 | 2 | 2.796 | 2.000 | 1.489 | 2889 | |
3 | 1 | 3 | 3 | 3 | 3.438 | 2.000 | 1.491 | 2591 | |
4 | 2 | 1 | 2 | 3 | 1.651 | 1.090 | 1.227 | 2443 | |
5 | 2 | 2 | 3 | 1 | 2.218 | 1.186 | 1.257 | 2415 | |
6 | 2 | 3 | 1 | 2 | 3.390 | 2.000 | 1.454 | 3617 | |
7 | 3 | 1 | 3 | 2 | 1.454 | 0.696 | 1.058 | 2197 | |
8 | 3 | 2 | 1 | 3 | 2.458 | 1.684 | 1.397 | 3330 | |
9 | 3 | 3 | 2 | 1 | 3.008 | 1.681 | 1.344 | 2895 |
LBW parameters | 1 – Mean | 2 − Mean | 3 – Mean | Sum of squares | %Contribution | |
Width of fusion zone, α (mm): grand mean = 2.497 | A | 2.765 | 2.420 | 2.307 | 0.343 | 8.3 |
B | 1.722 | 2.491 | 3.279 | 3.633 | 88.5 | |
C | 2.637 | 2.485 | 2.370 | 0.107 | 2.6 | |
D | 2.429 | 2.547 | 2.516 | 0.022 | 0.5 | |
Depth of weld penetration, β (mm): grand mean = 1.548 | A | 1.886 | 1.425 | 1.354 | 0.461 | 26.8 |
B | 1.128 | 1.623 | 1.894 | 0.906 | 52.7 | |
C | 1.760 | 1.590 | 1.294 | 0.334 | 19.4 | |
D | 1.488 | 1.565 | 1.591 | 0.017 | 1.0 | |
Heat affected zone, γ (mm): grand mean = 1.362 | A | 1.508 | 1.313 | 1.266 | 0.099 | 50.0 |
B | 1.277 | 1.381 | 1.430 | 0.037 | 18.5 | |
C | 1.465 | 1.353 | 1.269 | 0.058 | 29.5 | |
D | 1.382 | 1.334 | 1.372 | 0.004 | 2.0 | |
Maximum Temperature, δ (K): grand mean = 2807.1 | A | 2789 | 2825 | 2807 | 1944 | 0.1 |
B | 2509 | 2878 | 3034 | 436576 | 26.4 | |
C | 3278 | 2742 | 2401 | 1172576 | 70.8 | |
D | 2732 | 2901 | 2788 | 44316 | 2.7 |
Utilizing the additive law [51], estimates of PIs from the results of ANOVA Table 3 obtained are as follows. Let Ψ be the PI and ˆΨ is its estimate for the process variables (Ai, Bj, Ck, Dl) in which the levels are indicated by subscripts i, j, k, l varying from 1 to 3. Designating Ψ(Ai), Ψ(Bj), Ψ(Ck) and Ψ(Dl) as mean values of Ψ corresponding to the levels of the respective process variables. Ψmean, is the grand mean of the PI for nine test runs. As per the additive law [51], estimate ˆΨ for the specified (Ai, Bj, Ck, Dl) is Eq 5.
ˆΨ=Ψ(Ai, Bj, Ck, Dl)=Ψmean+(Ψ(Ai)−Ψmean)+(Ψ(Bj)−Ψmean) +(Ψ(Ck)−Ψmean)+(Ψ(Dl)−Ψmean) | (5) |
In case of 3 input variables (Ai, Bj, Ck), Eq 5 reduces to Eq 6.
ˆΨ=Ψ(Ai, Bj, Ck, )=Ψmean+(Ψ(Ai)−Ψmean)+(Ψ(Bj)−Ψmean) +(Ψ(Ck)−Ψmean) | (6) |
The deviation of the estimates from Eqs 5 and 6 is Ψ(Dl) − Ψmean. For 3 levels (l = 1, 2, 3), 3 deviations are obtained. As in [43], the range of estimates is obtained through superposition of the minimum and maximum deviations to the estimates of Eq 6. Numerical simulations of α, β, γ and δ in Tables 4–7 are within the range of estimates. The minimum and maximum deviations for α, β, γ and δ are (−0.07, 0.05), (−0.06, 0.04), (−0.029, 0.02) and (−74.8, 98.9) respectively.
Test S. No. | Simulation | Eq 6 (npv = 3) | RE (%) | Eq 5 (npv = 4) | Range of estimates | |
From | To | |||||
1 | 2.062 | 2.130 | −3.3 | 2.062 | 2.062 | 2.179 |
2 | 2.796 | 2.747 | 1.8 | 2.796 | 2.679 | 2.796 |
3 | 3.438 | 3.420 | 0.5 | 3.438 | 3.352 | 3.469 |
4 | 1.651 | 1.633 | 1.1 | 1.651 | 1.565 | 1.682 |
5 | 2.218 | 2.286 | −3.1 | 2.218 | 2.218 | 2.335 |
6 | 3.390 | 3.341 | 1.4 | 3.390 | 3.273 | 3.390 |
7 | 1.454 | 1.405 | 3.4 | 1.454 | 1.337 | 1.454 |
8 | 2.458 | 2.440 | 0.7 | 2.458 | 2.372 | 2.489 |
9 | 3.008 | 3.076 | −2.3 | 3.008 | 3.008 | 3.125 |
Test S. No. | Simulation | Eq 6 (npv = 3) | RE (%) | Eq 5 (npv = 4) | Range of estimates | |
From | To | |||||
1 | 1.597 | 1.66 | −3.9 | 1.597 | 1.597 | 1.700 |
2 | 2.000 | 1.98 | 1.0 | 2.000 | 1.923 | 2.026 |
3 | 2.000 | 1.96 | 2.0 | 2.000 | 1.897 | 2.000 |
4 | 1.090 | 1.05 | 3.7 | 1.090 | 0.987 | 1.090 |
5 | 1.186 | 1.25 | −5.4 | 1.186 | 1.186 | 1.289 |
6 | 2.000 | 1.98 | 1.0 | 2.000 | 1.923 | 2.026 |
7 | 0.696 | 0.68 | 2.3 | 0.696 | 0.619 | 0.722 |
8 | 1.684 | 1.64 | 2.6 | 1.684 | 1.581 | 1.684 |
9 | 1.681 | 1.74 | −3.5 | 1.681 | 1.681 | 1.784 |
Test S. No. | Simulation | Eq 6 (npv = 3) | RE (%) | Eq 5 (npv = 4) | Range of estimates | |
From | To | |||||
1 | 1.545 | 1.525 | 1.3 | 1.545 | 1.497 | 1.545 |
2 | 1.489 | 1.518 | −1.9 | 1.489 | 1.489 | 1.537 |
3 | 1.491 | 1.482 | 0.6 | 1.491 | 1.453 | 1.501 |
4 | 1.227 | 1.218 | 0.7 | 1.227 | 1.189 | 1.237 |
5 | 1.257 | 1.237 | 1.6 | 1.257 | 1.209 | 1.257 |
6 | 1.454 | 1.483 | −2.0 | 1.454 | 1.454 | 1.502 |
7 | 1.058 | 1.087 | −2.7 | 1.058 | 1.058 | 1.106 |
8 | 1.397 | 1.388 | 0.6 | 1.397 | 1.359 | 1.407 |
9 | 1.344 | 1.324 | 1.5 | 1.344 | 1.296 | 1.344 |
Test S. No. | Simulation | Eq 6 (npv = 3) | RE (%) | Eq 5 (npv = 4) | Range of estimates | |
From | To | |||||
1 | 2887 | 2961 | −2.6 | 2887 | 2887 | 3055 |
2 | 2889 | 2795 | 3.2 | 2889 | 2720 | 2889 |
3 | 2591 | 2610 | −0.7 | 2591 | 2535 | 2704 |
4 | 2443 | 2462 | −0.8 | 2443 | 2387 | 2556 |
5 | 2415 | 2490 | −3.1 | 2415 | 2415 | 2583 |
6 | 3617 | 3523 | 2.6 | 3617 | 3448 | 3617 |
7 | 2197 | 2103 | 4.3 | 2197 | 2028 | 2197 |
8 | 3330 | 3349 | −0.6 | 3330 | 3274 | 3443 |
9 | 2895 | 2970 | −2.6 | 2895 | 2895 | 3063 |
Following the concept of additive law, empirical relations for the PIs (α, β, γ and δ) are developed (from the results of ANOVA Table 3) in the form Eqs 7–10.
α=2.401−0.229ξ1+0.116ξ21+0.778ξ2+0.01ξ22−0.133ξ3+0.018ξ23 | (7) |
β=1.543−0.256ξ1+0.184ξ21+0.383ξ2−0.113ξ22−0.233ξ3−0.063ξ23 | (8) |
γ=1.322−0.121ξ1+0.075ξ21+0.077ξ2−0.028ξ22−0.098ξ3+0.014ξ23 | (9) |
δ=2831+9.17ξ1−26.83ξ21+262.67ξ2−106.33ξ22−438.5ξ3+97.17ξ23 | (10) |
Here ζ1 = 0.5A − 5; ζ2 = 0.02B − 4; and ζ3 = 2C – 2. The range of estimates for PIs (α, β, γ and δ) from empirical relations Eqs 7–10 is obtained by superimposing the respective minimum and maximum deviations. Figures 3–6 show the estimates of α, β, γ and δ for all possible 27 combinations ((((AiBjCk), k = 1, 2, 3), j = 1, 2, 3), i = 1, 2, 3) of LBW parameters. Numerical simulations in Table 2 for the test runs in these Figures 3–6 are within the expected range (that is within lower and upper bounds).
(A3B1C3) and (A1B3C1) are two different sets of input process variables identified for minimum α and maximum β. To select a set of input process variables, a multi-objective optimization technique [64,65] is followed here by constructing a single objective function (ζ) in terms of α and β (after normalizing with αmax and βmax) and introducing weighing factors ω1 ∈ [0, 1] and ω2 = 1 − ω1.
The single objective function (ζ) is Eq 11.
ζ=ω1 ζ1+ω2 ζ2 = ω1(ααmax)+ω2(βmaxβ−1) | (11) |
Minimization of ζ implies maximization of β and minimization of α for a set of input process variables. Table 8 presents the data for ζ generated from Table 8 consider equal weighting (ω1 = ω2=12). ANOVA results are also presented in Table 8. The optimal input variables selected for the minimum ζ are A1B2C1. These correspond to welding speed = 8 mm/s; power = 200 W and laser beam diameter = 0.5 mm. The PIs for these input variables are not in the Taguchi L9 OA of Table 1. Hence, numerical simulations are performed by specifying the identified optimal input variables for obtaining the weld bead profile. Table 9 gives weld bead profiles for the single and multiple objective optimization problems. Numerical simulations are comparable to the range of PIs estimated from empirical relations Eqs 7–10. Figures 7–9 show the weld bead profile for max depth of weld, minimum bead width and optimum depth and width.
Test S. No. | LBW parameters | ζ1(=ααmax) | ζ2(βmaxβ−1) | ζ (=ω1ζ1+ω2ζ2) Eq 11 | ||
A (mm/s) | B (W) | C (mm) | ||||
1 | 8 | 150 | 0.5 | 0.600 | 0.252 | 0.426 |
2 | 8 | 200 | 1.0 | 0.813 | 0 | 0.407 |
3 | 8 | 250 | 1.5 | 1.000 | 0 | 0.500 |
4 | 10 | 150 | 1.0 | 0.480 | 0.835 | 0.658 |
5 | 10 | 200 | 1.5 | 0.645 | 0.686 | 0.666 |
6 | 10 | 250 | 0.5 | 0.986 | 0.000 | 0.493 |
7 | 12 | 150 | 1.5 | 0.423 | 1.874 | 1.148 |
8 | 12 | 200 | 0.5 | 0.715 | 0.188 | 0.451 |
9 | 12 | 250 | 1.0 | 0.875 | 0.190 | 0.532 |
ANOVA results on ζ | ||||||
1 − Mean | 0.4443 | 0.7440 | 0.4567 | - | - | - |
2 − Mean | 0.6057 | 0.5080 | 0.5323 | - | - | - |
3 − Mean | 0.7103 | 0.5083 | 0.7713 | - | - | - |
Optimum LBW parameters | Approach | Width of fusion zone, α (mm) | Depth of weld, β (mm) | Size of HAZ, γ (mm) | Maximum temperature, δ (mm) |
Maximum depth of weld: A1B3C1 (ω1 = 0, ω2 = 1) | Simulations | 4.02 | 2 | 1.602 | 3445 |
Additive law | 3.686 | 2.42 | 1.678 | 3487 | |
Expected range | 3.618–3.736 | 2.363–2.466 | 1.650–1.698 | 3412–3581 | |
Minimum width: A3B1C3 (ω1 = 1, ω2 = 0) | Simulations | 1.454 | 0.696 | 1.058 | 2197 |
Additive law | 1.405 | 0.680 | 1.087 | 2103 | |
Expected range | 1.337–1.454 | 0.619–0.722 | 1.058–1.106 | 2028–2197 | |
Optimum depth and width: A1B2C1 (ω1 = ω2 = 0.5) | Simulations | 3.048 | 2 | 1.576 | 3194 |
Additive law | 2.898 | 2.15 | 1.630 | 3330 | |
Expected range | 2.830–2.948 | 2.093–2.196 | 1.601–1.649 | 3256–3424 |
Numerical simulations are performed on the laser beam welding (LBW) of 2 mm thick Ti–6Al–4V alloy sheets. Taguchi's design of experiments is followed to conduct few simulations. Following the concept of additive law in Taguchi's approach, the performance indicators (PIs), namely, width of fusion zone (α) and depth of penetration (β) are estimated and validated with simulation results for the input process variables in each test run of the Taguchi's L9 OA (orthogonal array).
● Empirical relations are developed for PIs.
● Modified Taguchi approach provides the range of estimates for PIs.
● Optimal LBW process parameters are identified through a multi-objective optimization.
● Numerical simulations for the optimal LBW parameters are within the range of estimates.
● Incorporation of Taguchi approach in numerical simulations minimizes the trial and error-based test runs thereby reduction in computational time in selecting the optimal LBW parameters.
Future work is directed towards experimentation for investigating the microstructures and formation of defects in welding of Ti–6Al–4V with different welding processes (viz., electron beam welding, laser beam welding, plasma arc welding and TIG welding), and their influence on the properties.
The authors wish to thank the authorities of Koneru Lakshmaiah Education Foundation, India for providing facilities to carry out this work. The authors are grateful to the reviewers for their constructive criticism to improve the quality of presentation.
All authors declare no conflicts of interest in this paper.
[1] |
R. H. Alford, J. A. Kasel, P. J. Gerone, V. Knight, Human influenza resulting from aerosol inhalation, Proceedings of the Society for Experimental Biology and Medicine, 122 (1966), 800–804. https://doi.org/10.3181/00379727-122-31255 doi: 10.3181/00379727-122-31255
![]() |
[2] |
M. Alsved, A. Matamis, R. Bohlin, M. Richter, P. E. Bengtsson, C. J. Fraenkel, et al., Exhaled respiratory particles during singing and talking, Aerosol Sci Tech, 54 (2020), 1245–1248. https://doi.org/10.1080/02786826.2020.1812502 doi: 10.1080/02786826.2020.1812502
![]() |
[3] | P. Anfinrud, C. E. Bax, V. Stadnytskyi, A. Bax, Could Sars-Cov-2 be transmitted via speech droplets?, MedRxiv, [Preprint], (2020), [cited 2024 April 04]. Available from: https://doi.org/10.1101/2020.04.02.20051177 |
[4] |
S. Asadi, A. S. Wexler, C. D. Cappa, S. Barreda, N. M. Bouvier, W. D. Ristenpart, Aerosol emission and superemission during human speech increase with voice loudness, Sci. Rep., 9 (2019), 1–10. https://doi.org/10.1038/s41598-019-38808-z doi: 10.1038/s41598-019-38808-z
![]() |
[5] |
M. P. Atkinson, L. M. Wein, Quantifying the routes of transmission for pandemic influenza, Bull. Math. Biol., 70 (2008), 820–867. https://doi.org/10.1007/s11538-007-9281-2 doi: 10.1007/s11538-007-9281-2
![]() |
[6] |
D. K. Chu, E. A. Akl, S. Duda, K. Solo, S. Yaacoub, H. J. Schünemann, et al., Physical distancing, face masks, and eye protection to prevent person-to-person transmission of Sars-Cov-2 and Covid-19: a systematic review and meta-analysis, The Lancet, 395 (2020), 1973–1987. https://doi.org/10.1016/S0140-6736(20)31142-9 doi: 10.1016/S0140-6736(20)31142-9
![]() |
[7] |
B. J. Cowling, D. K. Ip, V. J. Fang, P. Suntarattiwong, S. J. Olsen, J. Levy, et al., Aerosol transmission is an important mode of influenza a virus spread, Nat Commun, 4 (2013), 1–6. https://doi.org/10.1038/ncomms2922 doi: 10.1038/ncomms2922
![]() |
[8] | EMG (Environmental and Modelling Group), Transmission of SARS-CoV-2 and Mitigating Measures. Scientific Advisory Group for Emergencies, 2020. Available from: https://www.gov.uk/government/publications/transmission-of-sars-cov-2-and-mitigating-measures-update-4-june-2020 |
[9] |
P. Fabian, J. J. McDevitt, W. H. DeHaan, R. O. P. Fung, B. J. Cowling, K. H. Chan, et al., Influenza virus in human exhaled breath: An observational study, Plos One, 3 (2008), 1–6. https://doi.org/10.1371/journal.pone.0002691 doi: 10.1371/journal.pone.0002691
![]() |
[10] | J. Gawn, M. Clayton, C. Makison, B. Crook, Evaluating the protection afforded by surgical masks against influenza bioaerosols, Health and Safety Executive, 2008. https://api.semanticscholar.org/CorpusID: 36385715 |
[11] |
F. K. Gregson, N. A. Watson, C. M. Orton, A. E. Haddrell, L. P. McCarthy, T. J. Finnie, et al., Comparing aerosol concentrations and particle size distributions generated by singing, speaking and breathing, Aerosol Sci Tech, 55 (2021), 681–691. https://doi.org/10.1080/02786826.2021.1883544 doi: 10.1080/02786826.2021.1883544
![]() |
[12] |
K. M. Gustin, J. M. Katz, T. M. Tumpey, T. R. Maines, Comparison of the levels of infectious virus in respirable aerosols exhaled by ferrets infected with influenza viruses exhibiting diverse transmissibility phenotypes, J. Virol., 87 (2013), 7864–7873. https://doi.org/10.1128/jvi.00719-13 doi: 10.1128/jvi.00719-13
![]() |
[13] |
N. H. Leung, D. K. Chu, E. Y. Shiu, K. H. Chan, J. J. McDevitt, B. J. Hau, et al., Respiratory virus shedding in exhaled breath and efficacy of face masks, Nat. Med., 26 (2020), 676–680. https://doi.org/10.1038/s41591-020-0843-2 doi: 10.1038/s41591-020-0843-2
![]() |
[14] |
Q. Li, X. Guan, P. Wu, X. Wang, L. Zhou, Y. Tong, et al., Early transmission dynamics in wuhan, china, of novel coronavirus–infected pneumonia, N Engl J Med, 382 (2020), 1199–1207. https://doi/full/10.1056/NEJMOa2001316 doi: 10.1056/NEJMOa2001316
![]() |
[15] |
W. G. Lindsley, F. M. Blachere, K. A. Davis, T. A. Pearce, M. A. Fisher, R. Khakoo, et al., Distribution of airborne influenza virus and respiratory syncytial virus in an urgent care medical clinic, Clin. Infect. Dis., 50 (2010), 693–698. https://doi.org/10.1086/650457 doi: 10.1086/650457
![]() |
[16] |
W. G. Lindsley, T. A. Pearce, J. B. Hudnall, K. A. Davis, S. M. Davis, M. A. Fisher, et al., Quantity and size distribution of cough-generated aerosol particles produced by influenza patients during and after illness, J Occup Environ Hyg, 9 (2012), 443–449. https://doi.org/10.1080/15459624.2012.684582 doi: 10.1080/15459624.2012.684582
![]() |
[17] |
Y. Liu, Z. Ning, Y. Chen, M. Guo, Y. Liu, N. K. Gali, et al., Aerodynamic analysis of Sars-Cov-2 in two wuhan hospitals, Nature, 582 (2020), 557–560. https://doi.org/10.1038/s41586-020-2271-3 doi: 10.1038/s41586-020-2271-3
![]() |
[18] |
D. K. Milton, M. P. Fabian, B. J. Cowling, M. L. Grantham, J. J. McDevitt, Influenza virus aerosols in human exhaled breath: particle size, culturability, and effect of surgical masks, Plos Pathog, 9 (2013), e1003205. https://doi.org/10.1371/journal.ppat.1003205 doi: 10.1371/journal.ppat.1003205
![]() |
[19] |
N. Nikitin, E. Petrova, E. Trifonova, O. Karpova, Influenza virus aerosols in the air and their infectiousness, Adv. Virus. Res., 2014. https://doi.org/10.1155/2014/859090 doi: 10.1155/2014/859090
![]() |
[20] |
H. Qian, T. Miao, L. Li, X. Zheng, D. Luo, Y. Li, Indoor transmission of Sars-Cov-2, Indoor Air, 31 (2020), 639–645. https://doi.org/10.1111/ina.12766 doi: 10.1111/ina.12766
![]() |
[21] | J. Reingruber, A. Papale, D. Holcman, Monitoring and predicting Sars-Cov-2 epidemic in france after deconfinement using a multiscale and age-dependent model, MedRxiv, [Preprint], (2020), [cited 2024 April 04]. Available from: https://doi.org/10.1101/2020.05.15.20099465 |
[22] | Roundups and Rapid Reactions, Expert reaction to questions about covid-19 and viral load. Science Media Centre, 2020. Available from https://www.sciencemediacentre.org/expert-reaction-to-questions-about-covid-19-and-viral-load. |
[23] | S. Samuel, Why you're unlikely to get the coronavirus from runners or cyclists, VOX, 2020. Available from: https://www.vox.com/future-perfect/2020/4/24/21233226/coronavirus-runners-cyclists-airborne-infectious-dose |
[24] | Z. Schuss, Theory and applications of stochastic processes: an analytical approach, Berlin: Springer Science & Business Media, 2009. |
[25] | J. H. Seinfeld, S. N. Pandis, Atmospheric chemistry and physics: from air pollution to climate change, New York: John Wiley & Sons, 2016. |
[26] |
V. Stadnytskyi, C. E. Bax, A. Bax, P. Anfinrud, The airborne lifetime of small speech droplets and their potential importance in Sars-Cov-2 transmission, PNAS, 117 (2020), 11875–11877. https://doi.org/10.1073/pnas.2006874117 doi: 10.1073/pnas.2006874117
![]() |
[27] |
J. W. Tang, W. P. Bahnfleth, P. M. Bluyssen, G. Buonanno, J. L. Jimenez, J. Kurnitski, et al., Dismantling myths on the airborne transmission of severe acute respiratory syndrome coronavirus-2 (Sars-Cov-2), J. Hosp. Infect., 110 (2021), 89–96. https://doi.org/10.1016/j.jhin.2020.12.022 doi: 10.1016/j.jhin.2020.12.022
![]() |
[28] | R. Tellier, Review of aerosol transmission of influenza a virus, Emerg Infect Dis., 12 (2006), 1657–1662. https://doi.org/10.3201%2Feid1211.060426 |
[29] |
R. Tellier, Aerosol transmission of influenza a virus: a review of new studies, J. R. Soc. Interface., 6 (2009), S783–S790. https://doi.org/10.1098/rsif.2009.0302.focus doi: 10.1098/rsif.2009.0302.focus
![]() |
[30] |
R. Tellier, Y. Li, B. J. Cowling, J. W. Tang, Recognition of aerosol transmission of infectious agents: a commentary, BMC Infect Dis, 19 (2019), 1–9. https://doi.org/10.1186/s12879-019-3707-y doi: 10.1186/s12879-019-3707-y
![]() |
[31] |
J. Wang, G. Du, Covid-19 may transmit through aerosol, Ir J Med Sci, 189 (2020), 1143–1144. https://doi.org/10.1007/s11845-020-02218-2 doi: 10.1007/s11845-020-02218-2
![]() |
[32] |
C. Ward, M. Dempsey, C. Ring, R. Kempson, L. Zhang, D. Gor, et al., Design and performance testing of quantitative real time pcr assays for influenza a and b viral load measurement, J Clin Virol, 29 (2004), 179–188. https://doi.org/10.1016/S1386-6532(03)00122-7 doi: 10.1016/S1386-6532(03)00122-7
![]() |
[33] |
J. Yan, M. Grantham, J. Pantelic, P. J. B. De Mesquita, B. Albert, F. Liu, et al., Infectious virus in exhaled breath of symptomatic seasonal influenza cases from a college community, PNAS, 115 (2018), 1081–1086. https://doi.org/10.1073/pnas.1716561115 doi: 10.1073/pnas.1716561115
![]() |
1. | Vlad Andrei Ciubotariu, Maria Crina Radu, Eugen Herghelegiu, Valentin Zichil, Cosmin Constantin Grigoras, Elena Nechita, Structural and Behaviour Optimization of Tubular Structures Made of Tailor Welded Blanks by Applying Taguchi and Genetic Algorithms Methods, 2022, 12, 2076-3417, 6794, 10.3390/app12136794 | |
2. | K. V. Durga Rajesh, Boggarapu Nageswara Rao, R. Sriram Swaroop, V. Surya Kiran, Tanya Buddi, Swadesh Kumar Singh, Utilization of the modified Taguchi approach to seek optimal design parameters for improving the heat transfer coefficient of a wire mesh fin heat sink, 2024, 18, 1955-2513, 3357, 10.1007/s12008-023-01556-6 | |
3. | Peter Omoniyi, Uttam Acharya, Stephen Akinlabi, Tien-Chien Jen, Esther Akinlabi, Taguchi-Grey relational analysis driven multi-objective optimization of weld bead geometry and hardness in laser welded Ti6Al4V Alloy, 2024, 1955-2513, 10.1007/s12008-024-01880-5 |
LBW parameters | Designation | Level-1 | Level-2 | Level-3 |
Welding speed (mm/sec) | A | 8 | 10 | 12 |
Power (W) | B | 150 | 200 | 250 |
Laser beam diameter (mm) | C | 0.5 | 1.0 | 1.5 |
Fictitious | D | d1 | d2 | d3 |
Test S. No. | LBW parameters (levels) | Performance indicators | |||||||
A | B | C | D | α (mm) | β (mm) | γ (mm) | δ (K) | ||
1 | 1 | 1 | 1 | 1 | 2.062 | 1.597 | 1.545 | 2887 | |
2 | 1 | 2 | 2 | 2 | 2.796 | 2.000 | 1.489 | 2889 | |
3 | 1 | 3 | 3 | 3 | 3.438 | 2.000 | 1.491 | 2591 | |
4 | 2 | 1 | 2 | 3 | 1.651 | 1.090 | 1.227 | 2443 | |
5 | 2 | 2 | 3 | 1 | 2.218 | 1.186 | 1.257 | 2415 | |
6 | 2 | 3 | 1 | 2 | 3.390 | 2.000 | 1.454 | 3617 | |
7 | 3 | 1 | 3 | 2 | 1.454 | 0.696 | 1.058 | 2197 | |
8 | 3 | 2 | 1 | 3 | 2.458 | 1.684 | 1.397 | 3330 | |
9 | 3 | 3 | 2 | 1 | 3.008 | 1.681 | 1.344 | 2895 |
LBW parameters | 1 – Mean | 2 − Mean | 3 – Mean | Sum of squares | %Contribution | |
Width of fusion zone, α (mm): grand mean = 2.497 | A | 2.765 | 2.420 | 2.307 | 0.343 | 8.3 |
B | 1.722 | 2.491 | 3.279 | 3.633 | 88.5 | |
C | 2.637 | 2.485 | 2.370 | 0.107 | 2.6 | |
D | 2.429 | 2.547 | 2.516 | 0.022 | 0.5 | |
Depth of weld penetration, β (mm): grand mean = 1.548 | A | 1.886 | 1.425 | 1.354 | 0.461 | 26.8 |
B | 1.128 | 1.623 | 1.894 | 0.906 | 52.7 | |
C | 1.760 | 1.590 | 1.294 | 0.334 | 19.4 | |
D | 1.488 | 1.565 | 1.591 | 0.017 | 1.0 | |
Heat affected zone, γ (mm): grand mean = 1.362 | A | 1.508 | 1.313 | 1.266 | 0.099 | 50.0 |
B | 1.277 | 1.381 | 1.430 | 0.037 | 18.5 | |
C | 1.465 | 1.353 | 1.269 | 0.058 | 29.5 | |
D | 1.382 | 1.334 | 1.372 | 0.004 | 2.0 | |
Maximum Temperature, δ (K): grand mean = 2807.1 | A | 2789 | 2825 | 2807 | 1944 | 0.1 |
B | 2509 | 2878 | 3034 | 436576 | 26.4 | |
C | 3278 | 2742 | 2401 | 1172576 | 70.8 | |
D | 2732 | 2901 | 2788 | 44316 | 2.7 |
Test S. No. | Simulation | Eq 6 (npv = 3) | RE (%) | Eq 5 (npv = 4) | Range of estimates | |
From | To | |||||
1 | 2.062 | 2.130 | −3.3 | 2.062 | 2.062 | 2.179 |
2 | 2.796 | 2.747 | 1.8 | 2.796 | 2.679 | 2.796 |
3 | 3.438 | 3.420 | 0.5 | 3.438 | 3.352 | 3.469 |
4 | 1.651 | 1.633 | 1.1 | 1.651 | 1.565 | 1.682 |
5 | 2.218 | 2.286 | −3.1 | 2.218 | 2.218 | 2.335 |
6 | 3.390 | 3.341 | 1.4 | 3.390 | 3.273 | 3.390 |
7 | 1.454 | 1.405 | 3.4 | 1.454 | 1.337 | 1.454 |
8 | 2.458 | 2.440 | 0.7 | 2.458 | 2.372 | 2.489 |
9 | 3.008 | 3.076 | −2.3 | 3.008 | 3.008 | 3.125 |
Test S. No. | Simulation | Eq 6 (npv = 3) | RE (%) | Eq 5 (npv = 4) | Range of estimates | |
From | To | |||||
1 | 1.597 | 1.66 | −3.9 | 1.597 | 1.597 | 1.700 |
2 | 2.000 | 1.98 | 1.0 | 2.000 | 1.923 | 2.026 |
3 | 2.000 | 1.96 | 2.0 | 2.000 | 1.897 | 2.000 |
4 | 1.090 | 1.05 | 3.7 | 1.090 | 0.987 | 1.090 |
5 | 1.186 | 1.25 | −5.4 | 1.186 | 1.186 | 1.289 |
6 | 2.000 | 1.98 | 1.0 | 2.000 | 1.923 | 2.026 |
7 | 0.696 | 0.68 | 2.3 | 0.696 | 0.619 | 0.722 |
8 | 1.684 | 1.64 | 2.6 | 1.684 | 1.581 | 1.684 |
9 | 1.681 | 1.74 | −3.5 | 1.681 | 1.681 | 1.784 |
Test S. No. | Simulation | Eq 6 (npv = 3) | RE (%) | Eq 5 (npv = 4) | Range of estimates | |
From | To | |||||
1 | 1.545 | 1.525 | 1.3 | 1.545 | 1.497 | 1.545 |
2 | 1.489 | 1.518 | −1.9 | 1.489 | 1.489 | 1.537 |
3 | 1.491 | 1.482 | 0.6 | 1.491 | 1.453 | 1.501 |
4 | 1.227 | 1.218 | 0.7 | 1.227 | 1.189 | 1.237 |
5 | 1.257 | 1.237 | 1.6 | 1.257 | 1.209 | 1.257 |
6 | 1.454 | 1.483 | −2.0 | 1.454 | 1.454 | 1.502 |
7 | 1.058 | 1.087 | −2.7 | 1.058 | 1.058 | 1.106 |
8 | 1.397 | 1.388 | 0.6 | 1.397 | 1.359 | 1.407 |
9 | 1.344 | 1.324 | 1.5 | 1.344 | 1.296 | 1.344 |
Test S. No. | Simulation | Eq 6 (npv = 3) | RE (%) | Eq 5 (npv = 4) | Range of estimates | |
From | To | |||||
1 | 2887 | 2961 | −2.6 | 2887 | 2887 | 3055 |
2 | 2889 | 2795 | 3.2 | 2889 | 2720 | 2889 |
3 | 2591 | 2610 | −0.7 | 2591 | 2535 | 2704 |
4 | 2443 | 2462 | −0.8 | 2443 | 2387 | 2556 |
5 | 2415 | 2490 | −3.1 | 2415 | 2415 | 2583 |
6 | 3617 | 3523 | 2.6 | 3617 | 3448 | 3617 |
7 | 2197 | 2103 | 4.3 | 2197 | 2028 | 2197 |
8 | 3330 | 3349 | −0.6 | 3330 | 3274 | 3443 |
9 | 2895 | 2970 | −2.6 | 2895 | 2895 | 3063 |
Test S. No. | LBW parameters | ζ1(=ααmax) | ζ2(βmaxβ−1) | ζ (=ω1ζ1+ω2ζ2) Eq 11 | ||
A (mm/s) | B (W) | C (mm) | ||||
1 | 8 | 150 | 0.5 | 0.600 | 0.252 | 0.426 |
2 | 8 | 200 | 1.0 | 0.813 | 0 | 0.407 |
3 | 8 | 250 | 1.5 | 1.000 | 0 | 0.500 |
4 | 10 | 150 | 1.0 | 0.480 | 0.835 | 0.658 |
5 | 10 | 200 | 1.5 | 0.645 | 0.686 | 0.666 |
6 | 10 | 250 | 0.5 | 0.986 | 0.000 | 0.493 |
7 | 12 | 150 | 1.5 | 0.423 | 1.874 | 1.148 |
8 | 12 | 200 | 0.5 | 0.715 | 0.188 | 0.451 |
9 | 12 | 250 | 1.0 | 0.875 | 0.190 | 0.532 |
ANOVA results on ζ | ||||||
1 − Mean | 0.4443 | 0.7440 | 0.4567 | - | - | - |
2 − Mean | 0.6057 | 0.5080 | 0.5323 | - | - | - |
3 − Mean | 0.7103 | 0.5083 | 0.7713 | - | - | - |
Optimum LBW parameters | Approach | Width of fusion zone, α (mm) | Depth of weld, β (mm) | Size of HAZ, γ (mm) | Maximum temperature, δ (mm) |
Maximum depth of weld: A1B3C1 (ω1 = 0, ω2 = 1) | Simulations | 4.02 | 2 | 1.602 | 3445 |
Additive law | 3.686 | 2.42 | 1.678 | 3487 | |
Expected range | 3.618–3.736 | 2.363–2.466 | 1.650–1.698 | 3412–3581 | |
Minimum width: A3B1C3 (ω1 = 1, ω2 = 0) | Simulations | 1.454 | 0.696 | 1.058 | 2197 |
Additive law | 1.405 | 0.680 | 1.087 | 2103 | |
Expected range | 1.337–1.454 | 0.619–0.722 | 1.058–1.106 | 2028–2197 | |
Optimum depth and width: A1B2C1 (ω1 = ω2 = 0.5) | Simulations | 3.048 | 2 | 1.576 | 3194 |
Additive law | 2.898 | 2.15 | 1.630 | 3330 | |
Expected range | 2.830–2.948 | 2.093–2.196 | 1.601–1.649 | 3256–3424 |
LBW parameters | Designation | Level-1 | Level-2 | Level-3 |
Welding speed (mm/sec) | A | 8 | 10 | 12 |
Power (W) | B | 150 | 200 | 250 |
Laser beam diameter (mm) | C | 0.5 | 1.0 | 1.5 |
Fictitious | D | d1 | d2 | d3 |
Test S. No. | LBW parameters (levels) | Performance indicators | |||||||
A | B | C | D | α (mm) | β (mm) | γ (mm) | δ (K) | ||
1 | 1 | 1 | 1 | 1 | 2.062 | 1.597 | 1.545 | 2887 | |
2 | 1 | 2 | 2 | 2 | 2.796 | 2.000 | 1.489 | 2889 | |
3 | 1 | 3 | 3 | 3 | 3.438 | 2.000 | 1.491 | 2591 | |
4 | 2 | 1 | 2 | 3 | 1.651 | 1.090 | 1.227 | 2443 | |
5 | 2 | 2 | 3 | 1 | 2.218 | 1.186 | 1.257 | 2415 | |
6 | 2 | 3 | 1 | 2 | 3.390 | 2.000 | 1.454 | 3617 | |
7 | 3 | 1 | 3 | 2 | 1.454 | 0.696 | 1.058 | 2197 | |
8 | 3 | 2 | 1 | 3 | 2.458 | 1.684 | 1.397 | 3330 | |
9 | 3 | 3 | 2 | 1 | 3.008 | 1.681 | 1.344 | 2895 |
LBW parameters | 1 – Mean | 2 − Mean | 3 – Mean | Sum of squares | %Contribution | |
Width of fusion zone, α (mm): grand mean = 2.497 | A | 2.765 | 2.420 | 2.307 | 0.343 | 8.3 |
B | 1.722 | 2.491 | 3.279 | 3.633 | 88.5 | |
C | 2.637 | 2.485 | 2.370 | 0.107 | 2.6 | |
D | 2.429 | 2.547 | 2.516 | 0.022 | 0.5 | |
Depth of weld penetration, β (mm): grand mean = 1.548 | A | 1.886 | 1.425 | 1.354 | 0.461 | 26.8 |
B | 1.128 | 1.623 | 1.894 | 0.906 | 52.7 | |
C | 1.760 | 1.590 | 1.294 | 0.334 | 19.4 | |
D | 1.488 | 1.565 | 1.591 | 0.017 | 1.0 | |
Heat affected zone, γ (mm): grand mean = 1.362 | A | 1.508 | 1.313 | 1.266 | 0.099 | 50.0 |
B | 1.277 | 1.381 | 1.430 | 0.037 | 18.5 | |
C | 1.465 | 1.353 | 1.269 | 0.058 | 29.5 | |
D | 1.382 | 1.334 | 1.372 | 0.004 | 2.0 | |
Maximum Temperature, δ (K): grand mean = 2807.1 | A | 2789 | 2825 | 2807 | 1944 | 0.1 |
B | 2509 | 2878 | 3034 | 436576 | 26.4 | |
C | 3278 | 2742 | 2401 | 1172576 | 70.8 | |
D | 2732 | 2901 | 2788 | 44316 | 2.7 |
Test S. No. | Simulation | Eq 6 (npv = 3) | RE (%) | Eq 5 (npv = 4) | Range of estimates | |
From | To | |||||
1 | 2.062 | 2.130 | −3.3 | 2.062 | 2.062 | 2.179 |
2 | 2.796 | 2.747 | 1.8 | 2.796 | 2.679 | 2.796 |
3 | 3.438 | 3.420 | 0.5 | 3.438 | 3.352 | 3.469 |
4 | 1.651 | 1.633 | 1.1 | 1.651 | 1.565 | 1.682 |
5 | 2.218 | 2.286 | −3.1 | 2.218 | 2.218 | 2.335 |
6 | 3.390 | 3.341 | 1.4 | 3.390 | 3.273 | 3.390 |
7 | 1.454 | 1.405 | 3.4 | 1.454 | 1.337 | 1.454 |
8 | 2.458 | 2.440 | 0.7 | 2.458 | 2.372 | 2.489 |
9 | 3.008 | 3.076 | −2.3 | 3.008 | 3.008 | 3.125 |
Test S. No. | Simulation | Eq 6 (npv = 3) | RE (%) | Eq 5 (npv = 4) | Range of estimates | |
From | To | |||||
1 | 1.597 | 1.66 | −3.9 | 1.597 | 1.597 | 1.700 |
2 | 2.000 | 1.98 | 1.0 | 2.000 | 1.923 | 2.026 |
3 | 2.000 | 1.96 | 2.0 | 2.000 | 1.897 | 2.000 |
4 | 1.090 | 1.05 | 3.7 | 1.090 | 0.987 | 1.090 |
5 | 1.186 | 1.25 | −5.4 | 1.186 | 1.186 | 1.289 |
6 | 2.000 | 1.98 | 1.0 | 2.000 | 1.923 | 2.026 |
7 | 0.696 | 0.68 | 2.3 | 0.696 | 0.619 | 0.722 |
8 | 1.684 | 1.64 | 2.6 | 1.684 | 1.581 | 1.684 |
9 | 1.681 | 1.74 | −3.5 | 1.681 | 1.681 | 1.784 |
Test S. No. | Simulation | Eq 6 (npv = 3) | RE (%) | Eq 5 (npv = 4) | Range of estimates | |
From | To | |||||
1 | 1.545 | 1.525 | 1.3 | 1.545 | 1.497 | 1.545 |
2 | 1.489 | 1.518 | −1.9 | 1.489 | 1.489 | 1.537 |
3 | 1.491 | 1.482 | 0.6 | 1.491 | 1.453 | 1.501 |
4 | 1.227 | 1.218 | 0.7 | 1.227 | 1.189 | 1.237 |
5 | 1.257 | 1.237 | 1.6 | 1.257 | 1.209 | 1.257 |
6 | 1.454 | 1.483 | −2.0 | 1.454 | 1.454 | 1.502 |
7 | 1.058 | 1.087 | −2.7 | 1.058 | 1.058 | 1.106 |
8 | 1.397 | 1.388 | 0.6 | 1.397 | 1.359 | 1.407 |
9 | 1.344 | 1.324 | 1.5 | 1.344 | 1.296 | 1.344 |
Test S. No. | Simulation | Eq 6 (npv = 3) | RE (%) | Eq 5 (npv = 4) | Range of estimates | |
From | To | |||||
1 | 2887 | 2961 | −2.6 | 2887 | 2887 | 3055 |
2 | 2889 | 2795 | 3.2 | 2889 | 2720 | 2889 |
3 | 2591 | 2610 | −0.7 | 2591 | 2535 | 2704 |
4 | 2443 | 2462 | −0.8 | 2443 | 2387 | 2556 |
5 | 2415 | 2490 | −3.1 | 2415 | 2415 | 2583 |
6 | 3617 | 3523 | 2.6 | 3617 | 3448 | 3617 |
7 | 2197 | 2103 | 4.3 | 2197 | 2028 | 2197 |
8 | 3330 | 3349 | −0.6 | 3330 | 3274 | 3443 |
9 | 2895 | 2970 | −2.6 | 2895 | 2895 | 3063 |
Test S. No. | LBW parameters | ζ1(=ααmax) | ζ2(βmaxβ−1) | ζ (=ω1ζ1+ω2ζ2) Eq 11 | ||
A (mm/s) | B (W) | C (mm) | ||||
1 | 8 | 150 | 0.5 | 0.600 | 0.252 | 0.426 |
2 | 8 | 200 | 1.0 | 0.813 | 0 | 0.407 |
3 | 8 | 250 | 1.5 | 1.000 | 0 | 0.500 |
4 | 10 | 150 | 1.0 | 0.480 | 0.835 | 0.658 |
5 | 10 | 200 | 1.5 | 0.645 | 0.686 | 0.666 |
6 | 10 | 250 | 0.5 | 0.986 | 0.000 | 0.493 |
7 | 12 | 150 | 1.5 | 0.423 | 1.874 | 1.148 |
8 | 12 | 200 | 0.5 | 0.715 | 0.188 | 0.451 |
9 | 12 | 250 | 1.0 | 0.875 | 0.190 | 0.532 |
ANOVA results on ζ | ||||||
1 − Mean | 0.4443 | 0.7440 | 0.4567 | - | - | - |
2 − Mean | 0.6057 | 0.5080 | 0.5323 | - | - | - |
3 − Mean | 0.7103 | 0.5083 | 0.7713 | - | - | - |
Optimum LBW parameters | Approach | Width of fusion zone, α (mm) | Depth of weld, β (mm) | Size of HAZ, γ (mm) | Maximum temperature, δ (mm) |
Maximum depth of weld: A1B3C1 (ω1 = 0, ω2 = 1) | Simulations | 4.02 | 2 | 1.602 | 3445 |
Additive law | 3.686 | 2.42 | 1.678 | 3487 | |
Expected range | 3.618–3.736 | 2.363–2.466 | 1.650–1.698 | 3412–3581 | |
Minimum width: A3B1C3 (ω1 = 1, ω2 = 0) | Simulations | 1.454 | 0.696 | 1.058 | 2197 |
Additive law | 1.405 | 0.680 | 1.087 | 2103 | |
Expected range | 1.337–1.454 | 0.619–0.722 | 1.058–1.106 | 2028–2197 | |
Optimum depth and width: A1B2C1 (ω1 = ω2 = 0.5) | Simulations | 3.048 | 2 | 1.576 | 3194 |
Additive law | 2.898 | 2.15 | 1.630 | 3330 | |
Expected range | 2.830–2.948 | 2.093–2.196 | 1.601–1.649 | 3256–3424 |