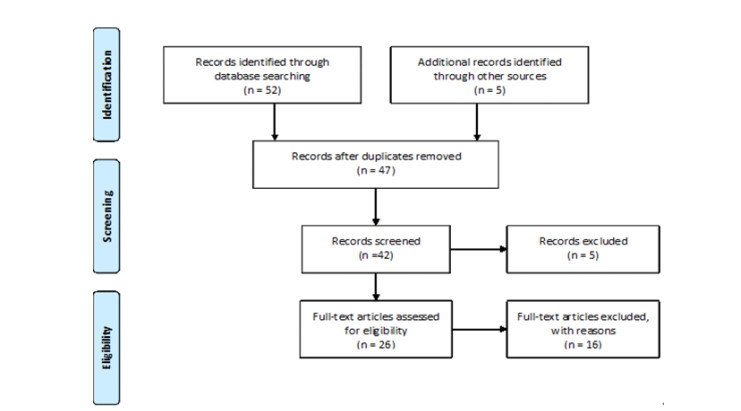
Polydimethylsiloxane (PDMS) has been a promising material for microfluidic, particularly in lab-on-chip. Due to the panoply of good physical, mechanical and chemical properties, namely, viscosity, modulus of elasticity, colour, thermal conductivity, thermal coefficient of expansion, its application has been increasingly requested in quite different areas. Despite such characteristics, there are also some drawbacks associated, and to overcome them, several strategies have been developed to modify PDMS. Given the great variety of relevant conducted research in this field, the present work aims to gather the most relevant information, the advantages and disadvantages of some of the techniques used, and also identify potential gaps and challenges in it. To this end, a systematic literature review was conducted by collecting data from four different databases, Science Direct, American Chemical Society, Scopus, and Springer. Two authors independently screened the references, extracted the key information, and assessed the quality of the included studies. After the analysis of the collected data, 25 studies were selected that addressed the various mechanical properties of PDMS and how to modify them in order to suit a particular application.
Citation: Inês Teixeira, Inês Castro, Violeta Carvalho, Cristina Rodrigues, Andrews Souza, Rui Lima, Senhorinha Teixeira, João Ribeiro. Polydimethylsiloxane mechanical properties: A systematic review[J]. AIMS Materials Science, 2021, 8(6): 952-973. doi: 10.3934/matersci.2021058
[1] | Eko Sasmito Hadi, Ojo Kurdi, Ari Wibawa BS, Rifky Ismail, Mohammad Tauviqirrahman . Influence of laser processing conditions for the manufacture of microchannels on ultrahigh molecular weight polyethylene coated with PDMS and PAA. AIMS Materials Science, 2022, 9(4): 554-571. doi: 10.3934/matersci.2022033 |
[2] | João E. Ribeiro, Hernani Lopes, Pedro Martins, Manuel Braz-César . Mechanical analysis of PDMS material using biaxial test. AIMS Materials Science, 2019, 6(1): 97-110. doi: 10.3934/matersci.2019.1.97 |
[3] | Jincong Chen, Xiaodong Zhao, Haiyan Zhao . A photothermal soft actuator based on graphene/PDMS composite materials reinforced by carbon fiber skeleton. AIMS Materials Science, 2025, 12(2): 301-317. doi: 10.3934/matersci.2025016 |
[4] | Kanishka Jha, Ravinder Kataria, Jagesvar Verma, Swastik Pradhan . Potential biodegradable matrices and fiber treatment for green composites: A review. AIMS Materials Science, 2019, 6(1): 119-138. doi: 10.3934/matersci.2019.1.119 |
[5] | Mnvrl Kumar, R. Ramakrishnan, Alnura Omarbekova, Santhosh Kumar. R . Experimental characterization of mechanical properties and microstructure study of polycarbonate (PC) reinforced acrylonitrile-butadiene-styrene (ABS) composite with varying PC loadings. AIMS Materials Science, 2021, 8(1): 18-28. doi: 10.3934/matersci.2021002 |
[6] | Pravina Kamini G., Kong Fah Tee, Jolius Gimbun, Siew Choo Chin . Biochar in cementitious material—A review on physical, chemical, mechanical, and durability properties. AIMS Materials Science, 2023, 10(3): 405-425. doi: 10.3934/matersci.2023022 |
[7] | Timothy K. Mulenga, Albert U. Ude, Chinnasamy Vivekanandhan . Concise review on the mechanical characteristics of hybrid natural fibres with filler content. AIMS Materials Science, 2020, 7(5): 650-664. doi: 10.3934/matersci.2020.5.650 |
[8] | Nataliya A. Sakharova, Jorge M. Antunes, Andre F. G. Pereira, Jose V. Fernandes . Developments in the evaluation of elastic properties of carbon nanotubes and their heterojunctions by numerical simulation. AIMS Materials Science, 2017, 4(3): 706-737. doi: 10.3934/matersci.2017.3.706 |
[9] | Zarina Aringozhina, Nurtoleu Magazov, Bauyrzhan Rakhadilov, Gulzhaz Uazyrkhanova, Auezhan Amanov . Effect of ultrasonic nanocrystalline surface modification on hardness and elastic modulus of Ti-6Al-4V alloy. AIMS Materials Science, 2025, 12(1): 101-117. doi: 10.3934/matersci.2025008 |
[10] | Harikrishnan Pulikkalparambil, Jyotishkumar Parameswaranpillai, Jinu Jacob George, Krittirash Yorseng, Suchart Siengchin . Physical and thermo-mechanical properties of bionano reinforced poly(butylene adipate-co-terephthalate), hemp/CNF/Ag-NPs composites. AIMS Materials Science, 2017, 4(3): 814-831. doi: 10.3934/matersci.2017.3.814 |
Polydimethylsiloxane (PDMS) has been a promising material for microfluidic, particularly in lab-on-chip. Due to the panoply of good physical, mechanical and chemical properties, namely, viscosity, modulus of elasticity, colour, thermal conductivity, thermal coefficient of expansion, its application has been increasingly requested in quite different areas. Despite such characteristics, there are also some drawbacks associated, and to overcome them, several strategies have been developed to modify PDMS. Given the great variety of relevant conducted research in this field, the present work aims to gather the most relevant information, the advantages and disadvantages of some of the techniques used, and also identify potential gaps and challenges in it. To this end, a systematic literature review was conducted by collecting data from four different databases, Science Direct, American Chemical Society, Scopus, and Springer. Two authors independently screened the references, extracted the key information, and assessed the quality of the included studies. After the analysis of the collected data, 25 studies were selected that addressed the various mechanical properties of PDMS and how to modify them in order to suit a particular application.
Polydimethylsiloxane (PDMS) is a silicon-based organic polymer composed of a repeating unit [SiO(CH3)2]. At room temperature, it is in the rubber state because it has a glass transition temperature of less than −120 ℃ [1]. PDMS is an elastomer polymer often constructed with micrometric dimensions for use in many science and engineering applications [2]. PDMS has been commonly used as an alternative to glass for manufacturing microfluidic devices, since the introduction into soft lithography using PDMS to produce mechanically robust devices for microfluidic purposes and/or creating lab-on-a-chip devices [3,4,5,6,7].
The main advantages of PDMS are: easy manufacturing, non-toxicity, non-flammability, good elasticity, optical transparency [8,9], biocompatibility [10,11], high gas permeability [12,13], high compressibility[14], high flexibility [15,16], viscoelasticity, and it is chemically and thermally stable [17,18,19]. In addition, PDMS is capable of modifying and blending with other materials, further expanding its application range [20,21]. For these reasons, this elastomer is widely used in lubricants [22], photovoltaic panels [23,24], optical systems (adaptive lenses) [25], blood analogues [26], microvalves [27] and in the soft lithography procedure, thus becoming one of the most widely used materials for microfluidic devices and lab-on-a-chip device creation [5,28,29,30]. PDMS also features simple processing, short time, easy control with low cost, easy to work with, and easy to change [4]. Furthermore, it is quite fast in its micro-molding prototyping ability and the ability to adhere to flat surfaces without the need to use adhesives. It is not brittle when compared to other materials such as glass or silicon [31]. PDMS also exhibits water and oxidation resistance, high impact strength, good electrical insulation, relatively insensitive to clear UV [32].
Moreover, PDMS offers high values of elasticity [33], due to the fact that exists in a very compact form. So, when subjected to a tensile force, the polymer is stretched releasing its stress, and then returns to its initial state when the load is removed. The polymer has its elasticity determined by the ability of its regions, which are close together, to slide over each other. This property is influenced by the number of cross-links that exist, the more cross-linked the PDMS, the less elastic it will be. As the PDMS is a soft material, it is very sensitive to low loads. In addition, PDMS is a visco-hyperelastic material, and strain rate effects are commonly observed [34,35,36].
However, it also has some disadvantages, such as its hydrophobic surface, which can cause difficulties when trying to investigate hydrophobic analytes, as biomolecules that often soak into the channel surfaces. Filling microchannels in PDMS can often be difficult [3], however, there are many methods used to improve the surface properties of PDMS [37,38], such as the use of oxygen plasma [39,40] The main disadvantage is that fibers and films are not formed due to the low cohesive forces. For this purpose, mass terminal groups are introduced to increase the cohesive forces of Polydimethylsiloxane [32].
Regarding its applicability, polydimethylsiloxane has been widely used in the field of analytical chemistry due to its favourable physicochemical properties and is gaining importance in the fabrication of lab-on-a-chip devices, as indicated above. These devices utilize a combination of mechanical, optical, and electrical properties of PDMS and thus have revolutionized bioanalysis [41]. On the other hand, PDMS has also been widely used in the biomedical industry due to its biocompatible material and biomechanical behaviour being similar to biological tissues, with applications in the study of aneurysm behaviour and devices such as micropumps, optical systems, and organ-on-a-chip platforms [34,42,43,44]. In an industrial context, silicones have been used in many protective coating systems for substrates due to their unique physical and chemical properties, namely, polydimethylsiloxanes because they have highly cross-linked molecular chains with enhanced mechanical properties [45]. On the other hand, PDMS has become a ubiquitous material for printing microcontacts, although there are few methods available to standardize a PDMS stamp completed in a single step [46].
In this paper, the main properties of PDMS will be mentioned, namely the mechanical properties. For example, the PDMS obtained with the standardized ratio of 10:1 with its curing agent, has a modulus of elasticity of G = 250 kPa, due to its low glass transition temperature (T = −125 ℃); low change of modulus of elasticity with temperature variation (1.1 kPa/C); small temperature variations of the physical constants (except for thermal expansivity α = 20 × 10−5 k−1); high dielectric strength (14 V/µm); a wide temperature range (−100 ℃ to 100 ℃) and low chemical reactivity, except at pH extremes [47].
The main objective of this systematic review is to show the existence of different ways to change the mechanical properties of PDMS, for example, modifying the formation ratio, curing time, and curing temperature [48]. On the other hand, it is intended to give a summary of treatments describing the results obtained in each one, in order to help the reader to choose the best treatment according to the characteristics that the PDMS needs to have for the intended application.
Since the start of the research on August 22 of 2020, studies were searched that included different ways to modify the mechanical properties of PDMS. For this, a search was conducted in ScienceDirect (SD), Scopus, American Chemical Society (ACS), and Springer. The keywords used were PDMS properties or PDMS polymer properties or Polydimethylsiloxane properties and PDMS mechanical properties. Exclusion criteria were review articles, systematic review articles, meta-analysis, book chapters, conference papers, patents, reports, content that has no interest in the research area, ambiguity, written in a language other than English, and publications before 2011. The analysis of the results was done following the Preferred Reporting Items for Systematic Reviews and Meta-analyses (PRISMA), whose flowchart is presented and summarized in Figure 1. This is a valuable tool that helps authors improve the reporting of systematic reviews and meta-analyses.
First, the related titles were selected. Subsequently, all abstracts were read and those that did not fit the objective of the systematic review were excluded. According to the defined exclusion criteria, the full texts were reviewed, and finally, the data were extracted. The data extracted were test design, setting, quantitative results and limitations of the reported study, and other important comments.
The findings of interest were how to change the properties of PDMS and how the change made contributes to improving a particular mechanical characteristic. It was noted that all the studies found used experimental methods and the discussion of results used comparative methods between pure PDMS and modified PDMS.
Some of the selected studies showed poor results, i.e. mechanical properties were weakened, others resorted to complex and ambiguous physical and chemical methods, e.g. molecular rearrangements.
After the inclusion and exclusion criteria were defined, the resulting titles were read and selected. Duplicate documentation was then removed, and the abstracts were further examined and evaluated. These first two steps were performed by 3 authors. However, the full reading was only performed by 2 authors.
Tables 1 and 2 show how the concordance of inclusion, exclusion and doubt (in abstract only) was reached. In case of doubt, the article was read in its entirety. Table 1 shows the different opinions that the authors may have, and which conclusion is reached, contemplating 3 opinions with the same evaluation weight. Note that in case of doubt, the study was fully read. Table 2 only contemplates the opinion of the two authors.
Opinions | Results | ||
Inclusion | Inclusion | Inclusion | Inclusion |
Doubt | Doubt | Doubt | Doubt |
Exclusion | Exclusion | Exclusion | Exclusion |
Inclusion | Doubt | Doubt | Inclusion |
Inclusion | Doubt | Inclusion | Inclusion |
Inclusion | Inclusion | Exclusion | Doubt |
Inclusion | Exclusion | Exclusion | Exclusion |
Exclusion | Doubt | Doubt | Exclusion |
Exclusion | Doubt | Inclusion | Doubt |
Exclusion | Exclusion | Inclusion | Exclusion |
Exclusion | Inclusion | Inclusion | Doubt |
Opinions | Results | |
Inclusion | Inclusion | Inclusion |
Exclusion | Exclusion | Exclusion |
Exclusion | Inclusion | Consult Adviser |
Inclusion | Exclusion | Consult Adviser |
The completion of the tables was considered unambiguously adequate. In case of disagreement, in the case of Table 2, the reading should be redone and discussed if the article is effectively included or excluded. In case of ongoing disagreement, the systematic review supervisor should be consulted.
Twenty-five studies were identified for review, of which were divided into different types of modification of the mechanical properties of PDMS.
Of these 25 studies, 8 were based on structural modifications, i.e., at the molecular structure level of PDMS, 2 studies related to modifications by chemical induction, 6 studies related to the incorporation of nanoparticles capable of improving mechanical properties, 2 studies related to numerical predictions, and 7 studies related to iterative methods, trial-error process, to determine which is the best method to improve mechanical properties and confirm this optimization. On the other hand, all the presented methods of improving the mechanical properties of PDMS tend to improve those that are required for a particular application. However, that improvement in one particular property may lead to the improvement of another, or, however, may lead to the weakening of another. Table 3 is presented a synthesis of different methods used to modify the main mechanical properties of PDMS.
Modification method | Principle of operation | Advantages | Disadvantages/limitation | Main results | Ref. |
Structural process | Dual-functional polymer system that combines shape memory with self-healing properties. It consists of a polymer network with permanent covalent crosslinking and abundant weak hydrogen bonds. The former introduces elasticity and maintains the permanent shape, and the latter contributes to the temporary shape via network rearrangement. | Capable of efficiently self-healing for 6 h at room temperature; The resulting polymer has shape memory effects triggered by body temperature. | The precise adjustment of the thermal transition temperature of shape memory polymer is highly complex. | The resultant polymer has shape memory effects triggered by body temperature. | [49] |
Study of the effect of aliphatic and aromatic diisocyanate structures on the mechanical properties, thermal degradation, hydrophobicity, and surface properties of polysiloxane-based polyurethane elastomers. | It provides the tensile properties of polysiloxane-based polyurethane elastomers using techniques such as Fourier transform infrared spectroscopy (FTIR), thermogravimetric analysis (TGA), X-ray photoelectron spectroscopy (XPS), X-ray diffraction (XRD), atomic force microscopy (AFM), contact angles (CA) and tensile testing. | - | In the tensile test, H12MDIPU shows the largest elongation at break. HDIPU shows a larger modulus, and TDIPU has the highest tensile strength. | [50] | |
Characterization of the viscoelastic behaviour of polymers using nanoindentation, showing a linear experimental relationship for PDMS samples with different viscosities and elasticities. | - | Nanoindentation is theoretically not sufficient and therefore conventional test results cannot be met. It may result from the difference in test methods, as nanoindentation evaluates local properties, while DMA evaluates average properties. More extensive research is needed in this area. | Experimentally measured coefficients described well the elastic and viscous behaviour expected from the crosslinking density of the PDMS samples. | [51] | |
Structural process | The use of treated Maghnite as catalyst and as inorganic reinforcement for the development of PDMS nanocomposites. | The increased mass ratio of Maghnite improves thermal stability; Improved mechanical properties of the nanocomposites compared to pure PDMS; the composite materials acquired good adsorption capacity compared to the pure polymer. Efficient, fast, and environmentally friendly method. |
- | The use of treated Maghnite, as a catalyst and as an inorganic reinforcement for the development of PDMS nanocomposites, has shown that it is an efficient, fast, and green method for obtaining PDMS nanocomposites with improved properties. | [52] |
Synthesis of copolymers of Polydimethylsiloxane and Polyethylene Oxide (PDMS-PEO) for the fabrication of amphiphilic surfaces. | The contact angle on the surface of the PDMS-PEO copolymer when placing the water droplet is equal to the contact angle of the native PDMS, however, after about 40 s, the droplet starts to spread, decreasing the contact angle. The larger the amount of vinyl incorporated, the smaller the contact angle will be. | When evaluating the absorbance spectrum, the copolymer is not as transparent as native PDMS, not absorbing significantly in the visible zone where most of the fluorescence measurement is done by laser. Young's modulus varies with the amount of vinyl added to PDMS. When it is low in amount, it exhibits a lower Young's modulus than the native PDMS for a ratio of 10:1. However as the amount of vinyl is increased, the Young's modulus increases, approaching the value of pure PDMS. |
The cross-linked copolymer (a material that allows for the incorporation of hydrophilic functional groups) exhibits acceptable for application to high speed, high-efficiency, and chemical separations. | [3] | |
Structural characteristics and gas permeation properties of bi-soft segment PDMS/PU membranes. | The vibration of SI-O-SI elongations increases with increasing PDMS membrane content. The permeabilities of CO2, O2, and N2 gases increase with increasing PDMS membrane content, while the CO2/N2 and O2/N2 ratios do not change significantly. |
The degree of crosslinking decreases sharply, when the PDMS content increases by 75% of its weight. With increasing PDMS content, some hydroxyl groups were not reacted, decreasing the degree of crosslinking. |
The permeability ratio was higher for the bisoft segment membranes described in this work than in the case of PDMS pure. | [53] | |
Structural process | Development of high durability superhydrophobic coatings against mechanical damage in abrasion tests. Obtaining PDMS with soot composite coatings that can be fabricated on various substrates such as glass, wood, stainless steel meshes, and plastics. | Hydrophobic coatings exhibit high durability against water spray; Superhydrophobic coatings exhibit excellent chemical resistance; They have high biocompatibility and can later be used in biomedical devices or implants to prevent blood coagulation. |
These hydrophobic coatings perform the worst in the wear test. | Successfully fabricated mechanically durable superhydrophobic PDMS-CSC-CS; It can tolerate high-strength sandpaper-based abrasion and ultrasonication tests; Also, it still showed super- wettable behaviours. |
[54] |
Flame treatment to generate PDMS nanostructures to improve superhydrophobia and superoleophobia. | The untreated and flame treated PDMS-PIL (square pillar pattern) surfaces show higher roughness when compared to PDMS-REC (rectangular pattern) and PDMS-FLT (flat PDMS); The longer the flame treatment duration generates more oxygen and silicon-based groups, leading to the formation of hydrophilic and the decrease in carbon concentration, which will make the surface superhydrophobic and superoleophobic. |
Flame treatment leads to a lack of surface roughness of the PDMS micropattern, negatively affecting the hydrophobicity. Therefore, the flame treatment should not exceed 30 s. | Surfaces exhibited superhydrophobic and superoleophobic properties that led to water and EG droplets rolling off almost immediately and the samples had great stability of superhydrophobicity and superoleophobicity. | [55] | |
Chemical process | Plasma treatment of the PDMS surface for optimization of optical properties and hydrophilicity. Two types of tests are tested, the first is a comparison between plain PDMS and a fused silica glass for the determination of the replica substrate. And the second test is the use of plasma to improve the hydrophilic properties of PDMS. |
In the visible light domain and being tested the smooth side of both PDMS and fused silica glass, PDMS shows 5% better transmittance, regarding the rough side, PDMS shows 17% better transmittance. Relatively to the reflectance the fused silica glass shows better than PDMS at the wavelength of 300-1200 nm, both on the smooth and rough side. PDMS is used as a replica substrate since it has a low cost and high activity in optical applications such as sunlight. Regarding plasma treatment, it shows a much higher root-mean-square surface roughness value after plasma treatment on both the smooth and rough sides; After plasma treatment, on the plasma surfaces, the roughness increases, the electric field strength increases, and the scattering regularity of free electron concentration increases. |
The surface thickness increases significantly after plasma treatment in both zones of the PDMS. | The results showed that the PDMS substrate presents a diversity of optical properties and also indicates that PDMS is a great potential to be used as a replica, low-cost, high-active substrate for optical applications, such as solar energy. | [4] |
Chemical process | Modification of the PDMS surface through a combination of physical and chemical modification routes. After the nanopattern PDMS was exposed to air plasma, a polyvinyl alcohol (PVA) treatment was performed. | The amount of oxygen in PVA- nano -PDMS is about 33%, higher than the value of 29% in pure nano-PDMS; With increasing plasma exposure time, the contact angle was decreased, improving its hydrophilicity; PDMS modified with the nanostructures shows better stability and lower contact angle values; If the amount of PVA layers increases, the contact angle decreases; The standardized PDMS with PVA coating has better long-term stability. |
There is no difference of any kind between the spectra of nanoPDMS and the plasma-treated sample, which confirmed that plasma treatment has no lasting influence on the surface hydrophilicity of PDMS. | Simple surface nanostructures combined with chemical modification improve the surface property and can solve the problem of long term stability. | [19] |
Incorporation of nanoparticles |
A simple and controllable foaming method is used to prepare PDMS foams by incorporating thermo-expandable hollow microspheres. | High compressive strength efficiency of movement energy absorption; Reinforces mechanical properties with softening behaviour; Provides foams with good toughness. |
Complicated processes with high energy consumption or poor controllability; The compressive modulus and strength of foam samples decrease with increasing microparticle content. |
The reinforced TEHM/PDMS foams with softening behaviour and high-efficient energy absorption were without any impact scars. | [56] |
Preparation of supramolecular polymer composites of PDMS nanofiber/vanadium pentoxide (V2O5) based on a reversible hydrogen bonding mechanism. | The addition of V2O5 nanofibers increases mechanical properties, namely tensile strength and improves curing efficiency compared to pure PDMS. | The curing efficiency decreases over time; Adding too many V2O5 nanofibers impairs the curing effect. |
The addition of V2O5 nanofibers increases the hydrogen bonding capability of the polymer and reduces the contact surface required for the hydrogen bonding, leading to increased healing efficiencies compared to neat polymer. | [57] | |
Incorporation of nanoparticles |
Addition of carbon nanotube nanocomposites to PDMS (CNTs). | The modulus of elasticity increases with the addition of CNTs in the PDMS matrix, gradually increasing with the increase of the CNTs percentage by weight; Regarding the dynamic results obtained, it is concluded that with the presence of the nanocomposites, the storage modulus increases; the loss of tangent is not significant; The addition of the CNTs in the PDMS matrix showed no effect on the viscoelastic behaviour of PDMS; The average hardness increases about 22% with the implementation of the nanocomposites. And the modulus of elasticity also increases about 25% in the case of nanoindentation tests and about 29% in tensile tests, when nanocomposites are present. |
According to the increase in the number of CNTs by weight, there are some imperfections on the fracture surface, as the amount of CNTs increases the imperfections become more severe. | Compared with the pure PDMS and 4.0 wt% PDMS/CNT nanocomposites, the increase in elastic modulus of pure PDMS after adding 4.0 wt% CNTs is 29.49% by tensile test. By using the nanoindentation test, the increase is 25.15%. | [1] |
Incorporation of metal nanoparticles (gold, silver, and platinum). | Increase of Young's modulus (3 times) compared to pure PDMS; This modification presents antimicrobial properties in the presence of silver microparticles; The incorporation of platinum or gold particles is used for optical or catalytic applications; Increased storage modulus and maintains damping modulus. |
Color change of the film. In the presence of gold particles, it turns ruby red and in the presence of silver particles, it turns brownish yellow when there is a reduction reaction with the curing agent of the PDMS pre-polymer. | Increase of Young's modulus. The young's modulus for nanoparticles containing films is 1.64 MPa and young's modulus of PDMS is 0.56 MPa; Increase storage modulus and maintains damping modulus; Change of color of the film, in a different types of particles; The curing agent of the PDMS pre-polymer works as a reduction reactor and a curing agent at the same time; The average modulus was found to be 1.7 ± 0.2 MPa for copolymer Ag-PDMS and 0.5 ± 0.1 MPa for PDMS; The nanoparticles containing film present antimicrobial characteristics. |
[58] | |
Incorporation of nanoparticles |
Incorporation of Fe2O3 particles (hematite). | Increase Young's modulus; Decrease tensile strength; Increase in hardness with increasing curing temperature; Decrease in hardness with increasing nanoparticle concentration between 0 and 2%; There is a linear relationship between the mechanical properties, and the concentration of nanoparticles was independent of the curing temperatures tested. |
- | Increase in Young's modulus by 170% from 1.36 to 3.71 MPa; Decrease in tensile strength by 65% with increasing nanoparticle concentration from 6.48 to 2.93 MPa; The linear increase between hardness and curing temperature; Decrease in hardness with increasing nanoparticles concentration in the matrix; When nanoparticles concentration increases, mechanical properties increase too. |
[59] |
Addition of silica nanoparticles (fumed silica A380 and mesoporous silica MCM-41). | The thermal and mechanical stability of PDMS is improved. In the case of MCM-41 Silica particles, the coefficient of thermal expansion decreases with increasing concentration; In the case of A380 Silica particles, they exhibit higher elastic modulus and better transparency due to smaller particle size compared to A380 Silica particles; Compared to pure PDMS, there is an increase in elastic modulus by about 7 times with the incorporation of silica particles. |
Decreased transmittance of PDMS when the incorporation of silica nanoparticles occurs, both A380 fumed silica and MCM-41 mesoporous silica; | In the case of MCM-41 Silica particles, the coefficient of thermal expansion decreases with increasing concentration; In the case of A380 Silica particles, they exhibit higher elastic modulus and better transparency than the bigger particle size of A380 silica particles; The elastic modulus increase by about 7 times with the incorporation of silica particles; The swelling ratio of PDMS in toluene was decreased to 0.68 when the concentration of nanoparticles was 10 wt%. A380 and MCM-41 nanoparticles had similar effects on the swelling property of PDMS. |
[60] | |
Incorporation of nanoparticles |
Incorporation of TiO2 (Titanium Dioxide) nanoparticles. | Demonstrates a photocatalytic effect on the coating film as there is an increase in absorbance in the UV region. It exhibits lower surface roughness, higher contact angle values, and better corrosion protection performance. It provides better barrier properties through reduced porosity and "zigzagging" of the polymer matrix diffusion pathway. | - | Higher concentrations of TiO2 nanoparticles reduce the glass transition temperatures (Tg) values due to the agglomeration tendency of the nanoparticles; This incorporation of TiO2 nanoparticles, increase contact angle values, lower surface roughness, and better corrosion protection process; PDMS resin was confirmed to be a suitable modifier that is able to enhance the hydrophobicity of the resulting coated surfaces without altering the curing level, glass transition temperature, dispersion state and the corrosion protection performance of TiO2-epoxy nanocomposite coating systems. |
[61] |
Simulation | Calculations are performed in the Materials Studio (MS) simulation environment using molecular dynamics (MD) theory. The results obtained are compared with experimental data. |
An innovative technique that saves materials since it promotes a computational prediction. | Approximations, for example, the elasticity of a polymer is a very complex problem, so for simplicity, the authors ignore surface effects and try to map the dependence of the bulk modulus on the crosslinking rate only. | The results seem to indicate that elastic properties of PDMS depend to the major extend on the crosslinking ratio and the particular network topology is of a less importance. | [62] |
Performing a biaxial tensile test at different speeds. Numerical studies using the most popular constitutive models were also performed for comparison with the experimental measurements. | Technique suitable for measuring displacement fields in hyperelastic materials; | The numerical models do not fully characterize the hyperelastic behaviour. | Based on the average error analysis of the constitutive model and of the displacement profiles, it was possible to establish a direct relationship. | [33] | |
Interactive process | A new high-performance functional composite was prepared by the paraffin-loaded fusion method with PDMS as the matrix. | Excellent performance in temperature-dependent thermal and mechanical properties; Excellent flexibility and heat absorption capacity; Can be useful for design and manufacturing in a wide range of potential applications. |
- | Thermal and mechanical properties can be improved greatly by considering the phase change characteristics of the paraffin components. | [15] |
Measurement of the mechanical properties of graded (layered) PDMS based on the ratio of base polymer blend to curing agent. | Great tenacity; Great compactness; Can be applied to produce flexible electronic components with extreme mechanical gradients and stronger graded adhesives. |
- | Graded PDMS was extended to a large elongation ratio before fracture and had a high upturn in stress at elongation, resulting in toughness values that were quite high. Increase the range of mechanical properties of graded PDMS, a material with more compatibility with technological processes was rendered. | [48] | |
Characterization of PDMS and compatibility study. To this end, 5 PDMS samples with a different cure, surface, and structural property ratios were forged; The PDMS formulations were analysed to investigate the effects with various biomedical processes, microfabrication, and micromachining. |
Shows the results of the various sample formulations when subjected to centrifugation, allowing you to get a speed-thickness graph; Chemical exposure and the effects on the degradation of the PDMS microtextures; Oxygen plasma exposure provides information about the recoverability of hydrophilicity, and demonstrates that at higher exposures, hydrophilicity does not decrease; Different sterilization techniques confirm the usefulness of different PDMS formulations for biomedical applications. On the other hand, different sterilization techniques allow a continuous or improved hydrophobic behaviour. Nanoindentation provides the various mechanical properties that each cure has. As for tensile testing, it is confirmed that tensile strength is higher the fewer sterilization effects. X-ray photoelectron spectroscopy provides the surface element concentration as a function of the amount of crosslinker. |
There were techniques applied that did not result in many contributions to optimize the mechanical properties or induce changes, for example, chemical immersion did not result in major changes in the hydrophilicity of the PDMS surface; Sterilization did not affect PDMS surface microtextures, element concentration, or hydrophilia. |
It was the PDMS with 14.3 wt% of cross-linker formulation that exhibited the highest tensile strength and storage modulus. Therefore, mechanical properties of PDMS could be altered (by changing the polymer to cross-linker ratio) without variations in surface chemistry. | [63] | |
Interactive process | Determination of the mechanical properties of a PDMS elastic rubber for sensor applications. | Thickness decreases with increasing rotation rate; Thickness increases with decreasing time; The shear modulus increases with temperature; The shear modulus is independent of the typical frequency used for an elastic material; For better adhesion of PDMS to an oxidized silicon wafer, a primer, such as TMSM was used. | - | The results show that PDMS is a rubber elastic material, with Young's modulus ≈ 750 kPa. When a primer is used, very good adhesion is obtained between cured PDMS and polished surfaces. Adhesive strengths up to 180 kPa | [47] |
Experimental study of the mechanical performance of PDMS at various temperatures. | The specific heat capacity of PDMS decreases along the glass transition temperature and increases with increasing temperature at a slow rate; With decreasing temperature, the thermal diffusivity of PDMS increases; The thermal conductivity of PDMS decreases with decreasing temperature; The coefficient of thermal expansion increases with increasing temperature; Hardness increases with decreasing temperature; Compression increases with decreasing temperature, leading to increased hardening. | - | The shore hardness and compressive modulus of PDMS significantly increased, with the decrease of temperature; The ultimate compressive strength increased first and then decreased with the decrease of temperature; With the decrease of temperature, the damage mode of PDMS material transitioned from micro-crack damage caused by plastic squeeze slip. |
[64] | |
Polymers confined to a small dimension are subjected to high deformation in order to realize the precision of the functioning of polymer devices at nanoscales. | For a given indentation, the slope increases with decreasing film thickness; Whether the indentation curves obtained by the Hertzian method of force indentation contact by a penetrator, or the force curves obtained by FEA simulation of thin compression elastomer, these all approximate for any given polymer thickness; Young's modulus varies with the regions where it is found, regions that have 3 different thicknesses. The first region where Young's modulus is independent of indentation, the second region where Young's modulus increases with indentation and exhibits increasing stiffness, and the third region just after contact where Young's modulus is extremely high initially and decreasing thereafter; The Young's modulus of the thin film, region 1, approaches the value of the bulk material; The measured Young's modulus can be dramatically reduced in small indentations, but significant contact hardening is permanence; The reduction in molecular mobility at the interface that is induced by the attraction between the identifier and the surface also contributes to surface hardening. | Small indentations of thin films of a polymer on a substrate lead to large deformations and hardening when the indentation depth approaches 45% of the sample thickness, which can lead to deviations from the experimental data and compromise the results. | The results described here will enable a predictive understanding of the mechanical properties of elastomeric materials under large deformations as can occur within microdevices. Also, the methods described here can be applied to understand heterogeneous and nonlinear materials. | [2] | |
Interactive process | Study of the influence of heating temperature on the mechanical properties (Young's modulus and ultimate tensile strength) of PDMS. | At the lowest temperature, at 100 ℃, the Young's modulus is the highest among all the temperatures tested; Heating time has little effect on Young's modulus at low temperature (100 ℃). However, the longer the heating time, the lower the Young's modulus; The PDMS membrane heated at 100 ℃ has 9 MPa and is stable over a long heating time; The thermal decomposition temperature of PDMS is high, approximately 310 ℃; For low heating temperatures, the mechanical properties are independent of the heating time. |
When the heating temperature is increased to 200 ℃, the maximum tensile strength is reduced to about 5 MPa, and the longer the heating time, the lower the UTS; Temperatures above 200 ℃, contribute to the decomposition of PDMS and consequently reduce the properties of PDMS. Also, longer heating time at temperatures above 200 ℃ will greatly reduce the mechanical strength of PDMS. |
Higher heating temperatures produce lower mechanical strength; The longer time of heating at a temperature greater than 200 ℃ will largely reduce the mechanical strength of PDMS; The reduced mechanical strength is attributed to the thermal decomposition which starts at a temperature of about 200 ℃ and reaches a peak at 310 ℃. |
[65] |
As shown in the results, there is a wide variety of methods to modify the mechanical properties of PDMS based on the molecular structure of PDMS, by synthesis, for example, to improve visibility (Figure 2a) [3], molecular rearrangement, for instance, for shape memory (Figure 2b) [49] or improvement of permeability (Figure 2c) [53], treatment at the structural level [55], like hydrophobia (Figure 2d) [54], coating to optimize the molecular structure [20] or indentation for characterization and structure improvement [17]. On the other hand, modifications can resort to chemical processes that despite being more complex are quite useful in decreasing to hydrophilic behaviour of PDMS.
As for the process of incorporation of nanoparticles, the process can be of varying complexities, for example, foams are complicated and consume a lot of energy in the process but have a very positive effect in terms of improved compressive strength, better toughness and better-softening behaviour [22]. The same happens with the incorporation of carbon nanotube nanocomposites, which darken the PDMS and lead the surface imperfections but improve the elasticity (Figure 3a) [1] and hardness of PDMS. As for the incorporation of Vanadium nanoparticles, these enhance better tensile strength and better curing efficiency, however, it darkens PDMS and excessive incorporation may impair the curing process [23] or thermo-expandable microspheres to improve energy absorption efficiency (Figure 3b) [56].
Regarding the process that used numerical simulation, this is without a doubt an innovative and promising idea since it can reduce the testing time and the associated cost. On the other hand, it is still a premature process, which needs many improvements and studies to give credibility to this process of analysis and optimization of mechanical properties. However, it can be used as a comparative and auxiliary tool to help in materials characterization (Figure 4a, b) [33].
So far, the authors are able to give an indication of the idea and the potential it may have, however, they report that many approximations are made [24]. The same happens with numerical studies capable of measuring the displacement of hyperelastic materials, however, their behaviour is not completely defined [25]. Finally, the iterative methods, trial-error, which has been adopted by several authors, to reach a sample capable of satisfying the need in face of the application or present studies about various samples tested for demonstration effect.
In the case of iterative studies for PDMS performance exposure, the authors prepare several PDMS samples with the study variable changed, for example, the study of several PDMS samples with different curing agents [14,27], resorts to the characterization of the samples and indicates the behaviour of all of them against pure PDMS, where in the first case, it indicates which of the samples shows better behaviour of toughness, compactness, and strength, while in the second case, the study explores the characteristics of the various samples for biomedical applications, microfabrication, and micromachining.
Other studies are also presented, for example, the effect of the heating temperature of PDMS and how this relates to the mechanical properties of PDMS [28,29], as well as subjecting samples to various deformations [14] or studying PDMS samples with a specific application, for example, for sensor applications [13].
It is relevant to compare and discuss the studies already conducted, pondering on the inherent characteristics of each of the studies, i.e., sensitivity and specificity of the appropriate tests presented in each study. However, it was not possible to make a comparison that was sufficiently faithful to reality, since not all studies provided the necessary information for this, and all were highly dependent on the application for which the modification is intended. In addition, another important parameter is the cost-effectiveness per trial of each method, which cannot be defined or inferred due to the lack of well-reasoned literature, i.e., only one article.
Therefore, the presentation expressed here is supported by a brief explanation of the modification process, main advantages, and disadvantages of each method. It would be relevant to compare the studies based on the specificity and sensitivity of the assays. However, we chose not to do so because not all studies provide these values were not considered due to the low number of samples tested.
The selected studies show that the most appropriate method to the application to which the improvement is intended should be adopted because not all have the same degree of complexity and not all focus on the improvement of the variable to be optimized.
In addition to the selected articles, others were read within the physical properties of PDMS. The reading of these articles is justified by the interrelation with the mechanical properties. Since the study of physical properties is necessary and determinant for the characterization of mechanical properties, it was found pertinent to analyze them [30].
This paper brings together different types of treatments that allow different types of changes in PDMS giving it various characteristics.
The treatments can be of various types, such as the incorporation of structural processes, chemical processes, and incorporation of nanoparticles.
However, to obtain results, some types of processes were used to visualize some results with the change of one more variable. The article studied present iteration processes for obtaining the expected results and simulation processes for visualizing results previously with the changes made.
Thus, the summary table (Table 3), presents what type of treatment to use for the intended application, knowing exactly what types of results are obtained for the treatment to be used, making it very easy to choose the type of changes that one wants to obtain in PDMS, from increasing the elasticity modulus, Young's modulus, transparency, tensile strength, stiffness, flexibility, among other characteristics.
By adding new elements to PDMS, the material, with the introduction of new mixtures, incorporations, and manipulations, will gain new applications at the industrial and commercial levels. On the other hand, the numerical part will tend to help and optimize the testing process as it allows to characterize and predict the behaviour it will have when manufactured, significantly reducing the time and cost with samples.
Inês Teixeira and Inês Castro acknowledge the scholarship granted by FCT. This work was supported in part by the projects NORTE-01-0145-FEDER-028178, NORTE-01-0145-FEDER-029394, and NORTE-01-0145-FEDER-030171 funded by NORTE 2020 Portugal Regional Operational Program under PORTUGAL 2020 Partnership Agreement through the European Regional Development Fund and the Fundação para a Ciência e Tecnologia (FCT). The authors also acknowledge the partial financial support by the projects UIDB/EEA/04436/2020, UIDB/EMS/04077/2020, UIDB/00319/2020 and UIDB/00690/2020 from FCT. Violeta Carvalho acknowledges the PhD scholarship UI/BD/151028/2021 attributed by FCT.
The authors declare no conflict of interest.
[1] | Wu CL, Lin HC, Hsu JS, et al. (2009) Static and dynamic mechanical properties of polydimethylsiloxane/carbon nanotube nanocomposites. Thin Solid Films 517: 4895-4901. |
[2] | Xu W, Chahine N, Sulchek T (2011) Extreme hardening of PDMS thin films due to high compressive strain and confined thickness. Langmuir 27: 8470-8477. |
[3] | Klasner SA, Metto EC, Roman GT, et al. (2009) Synthesis and characterization of a poly(dimethylsiloxane)-poly(ethylene oxide) block copolymer for fabrication of amphiphilic surfaces on microfluidic devices. Langmuir 25: 10390-10396. |
[4] | Zahid A, Dai B, Hong R, et al. (2017) Optical properties study of silicone polymer PDMS substrate surfaces modified by plasma treatment. Mater Res Express 4: 105301. |
[5] | Vlassov S, Oras S, Antsov M, et al. (2018) Adhesion and mechanical properties of PDMS-based materials probed with AFM: A review. Rev Adv Mater Sci 56: 62-78. |
[6] | Carvalho V, Gonçalves I, Lage T, et al. (2021) 3D printing techniques and their applications to organ‐on‐a‐chip platforms: A systematic review. Sensors 21: 3304. |
[7] | Carvalho V, Maia I, Souza A, et al. (2021) In vitro biomodels in stenotic arteries to perform blood analogues flow visualizations and measurements: A review. Open Biomed Eng J 14: 87-102. |
[8] | Kacik D, Martincek I (2017) Toluene optical fibre sensor based on air microcavity in PDMS. Opt Fiber Technol 34: 70-73. |
[9] | Park JS, Cabosky R, Ye Z, et al. (2018) Investigating the mechanical and optical properties of thin PDMS film by flat-punched indentation. Opt Mater 85: 153-161. |
[10] | A Souza, E Marques, C Balsa, et al. (2020) Characterization of shear strain on PDMS: Numerical and experimental approaches. Appl Sci 10: 3322. |
[11] | Montazerian H, Mohamed MGA, Montazeri MM, et al. (2019) Permeability and mechanical properties of gradient porous PDMS scaffolds fabricated by 3D-printed sacrificial templates designed with minimal surfaces. Acta Biomater 96: 149-160. |
[12] | Lamberti A, Marasso SL, Cocuzza MJR (2014) PDMS membranes with tunable gas permeability for microfluidic applications. RSC Adv 4: 61415-61419. |
[13] | Firpo G, Angeli E, Repetto L, et al. (2015) Permeability thickness dependence of polydimethylsiloxane (PDMS) membranes. J Membrane Sci 481: 1-8. |
[14] | Keane TJ, Badylak SF (2014) Biomaterials for tissue engineering applications. Semin Pediatr Surg 23: 112-118. |
[15] | Shi Y, Hu M, Xing Y, et al. (2020) Temperature-dependent thermal and mechanical properties of flexible functional PDMS/paraffin composites. Mater Des 185: 108219. |
[16] | Pinho D, Muñ oz-Sánchez BN, Anes CF, et al. (2019) Flexible PDMS microparticles to mimic RBCs in blood particulate analogue fluids. Mech Res Commun 100: 103399. |
[17] | Giri R, Naskar K, Nando GB (2012) Effect of electron beam irradiation on dynamic mechanical, thermal and morphological properties of LLDPE and PDMS rubber blends. Radiat Phys Chem 81: 1930-1942. |
[18] | Dalla Monta A, Razan F, Le Cam JB, et al. (2018) Using thickness-shear mode quartz resonator for characterizing the viscoelastic properties of PDMS during cross-linking, from the liquid to the solid state and at different temperatures. Sensor Actuat-A Phys 280: 107-113. |
[19] | Li J, Wang M, Shen Y (2012) Chemical modification on top of nanotopography to enhance surface properties of PDMS. Surf Coat Tech 206: 2161-2167. |
[20] | Yang C, Yuan YJ (2016) Investigation on the mechanism of nitrogen plasma modified PDMS bonding with SU-8. Appl Surf Sci 364: 815-821. |
[21] | Sales F, Souza A, Ariati R, et al. (2021) Composite material of PDMS with interchangeable transmittance: Study of optical, mechanical properties and wettability. J Compos Sci 5: 1-13. |
[22] | Ressel J, Seewald O, Bremser W, et al. (2020) Self-lubricating coatings via PDMS micro-gel dispersions. Prog Org Coat 146: 105705. |
[23] | Syafiq A, Vengadaesvaran B, Rahim NA, et al. (2019) Transparent self-cleaning coating of modified polydimethylsiloxane (PDMS) for real outdoor application. Prog Org Coat 131: 232-239. |
[24] | Park JY, Song H, Kim T, et al. (2016) PDMS-paraffin/graphene laminated films with electrothermally switchable haze. Carbon 96: 805-811. |
[25] | Wang W, Fang J (2007) Variable focusing microlens chip for potential sensing applications. IEEE Sens J 7: 11-17. |
[26] | Sadek SH, Rubio M, Lima R, et al. (2021) Blood particulate analogue fluids: A review. Materials 14: 2451. |
[27] | Wu X, Kim SH, Ji CH, et al. (2011) A solid hydraulically amplified piezoelectric microvalve. J Micromech Microeng 21: 095003. |
[28] | Maram SK, Barron B, Leung JC, et al. (2018) Fabrication and thermoresistive behaviour characterization of three-dimensional silver-polydimethylsiloxane (Ag-PDMS) microbridges in a mini-channel. Sensor Actuat A-Phys 277: 43-51. |
[29] | Akther F, Yakob SB, Nguyen NT, et al. (2020) Surface modification techniques for endothelial cell seeding in PDMS microfluidic devices. Biosensors 10: 182. |
[30] | Catarino SO, Rodrigues RO, Pinho D, et al. (2019) Blood cells separation and sorting techniques of passive microfluidic devices: From fabrication to applications. Micromachines 10: 593. |
[31] | Wolf MP, Salieb-Beugelaar GB, Hunziker P (2018) PDMS with designer functionalities—Properties, modifications strategies, and applications. Prog Polym Sci 83: 97-134. |
[32] | Anisimov AA, Zaytsev AV, Ol'shevskaya VA, et al. (2016) Polydimethylsiloxanes with bulk end groups: Synthesis and properties. Mendeleev Commun 26: 524-526. |
[33] | Ribeiro JE, Lopes H, Martins P, et al. (2019) Mechanical analysis of PDMS material using biaxial test. AIMS Mater Sci 6: 97-110. |
[34] | Victor A, Ribeiro JE, Araújo FF (2019) Study of PDMS characterization and its applications in biomedicine: A review. J Mech Eng Biomech 4: 1-9. |
[35] | Mata A, Fleischman AJ, Roy S (2005) Characterization of polydimethylsiloxane (PDMS) properties for biomedical micro/nanosystems. Biomed Microdevices 2: 281-293. |
[36] | Johnston ID, McCluskey DK, Tan CKL, et al. (2014) Mechanical characterization of bulk Sylgard 184 for microfluidics and microengineering. J Micromech Microeng 24: 035017. |
[37] | Kalulu M, Zhang W, Xia XK, et al. (2018) Hydrophilic surface modification of polydimetylsiloxane‐co‐2‐hydroxyethylmethacrylate (PDMS‐HEMA) by Silwet L‐77 (heptamethyltrisiloxane) surface treatment. Polym Adv Technol 29: 2601-2611. |
[38] | Gökaltun A, Kang YBA, Yarmush ML, et al. (2019) Simple surface modification of poly(dimethylsiloxane) via surface segregating smart polymers for biomicrofluidics. Sci Rep 9: 1-14. |
[39] | Bodas D, Rauch JY, Khan-Malek C (2008) Surface modification and aging studies of addition-curing silicone rubbers by oxygen plasma. Eur Polym J 44: 2130-2139. |
[40] | Bhattacharya S, Datta A, Berg JM, et al. (2005) Studies on surface wettability of poly(dimethyl) siloxane (PDMS) and glass under oxygen-plasma treatment and correlation with bond strength. J Microelectromech S 14: 590-597. |
[41] | Seethapathy S, Górecki T (2012) Applications of polydimethylsiloxane in analytical chemistry: A review. Anal Chim Acta 750: 48-62. |
[42] | Souza A, Souza MS, Pinho D, et al. (2020) 3D manufacturing of intracranial aneurysm biomodels for flow visualizations: Low cost fabrication processes. Mech Res Commun 107: 103535. |
[43] | Rodrigues RO, Pinho D, Bento D, et al. (2016) Wall expansion assessment of an intracranial aneurysm model by a 3D digital image correlation system. Measurement 88: 262-270. |
[44] | Rodrigues RO, Sousa PC, Gaspar J, et al. (2020) Organ-on-a-chip: A preclinical microfluidic platform for the progress of nanomedicine. Small 16: 2003517. |
[45] | Eduok U, Faye O, Szpunar J (2017) Recent developments and applications of protective silicone coatings: A review of PDMS functional materials. Prog Org Coat 111: 124-163. |
[46] | Russell MT, Pingree LSC, Hersam MC, et al. (2006) Microscale features and surface chemical functionality patterned by electron beam lithography: A novel route to poly(dimethylsiloxane) (PDMS) stamp fabrication. Langmuir 22: 6712-6718. |
[47] | Lötters JC, Olthuis W, Veltink PH, et al. (1997) The mechanical properties of the rubber elastic polymer polydimethylsiloxane for sensor applications. J Micromech Microeng 7: 145-147. |
[48] | Mohamed NS, Theng KC (2019) Mechanical properties of graded polydimethylsiloxane for flexible electronics. J Phys Conf Ser 1150: 012030. |
[49] | Lai HY, Wang HQ, Lai JC, et al. (2019) A self-healing and shape memory polymer that functions at body temperature. Molecules 24: 3224. |
[50] | Xu CA, Lu M, Tan Z, et al. (2020) Study on the surface properties and thermal stability of polysiloxane-based polyurethane elastomers with aliphatic and aromatic diisocyanate structures. Colloid Polym Sci 298: 1215-1226. |
[51] | Kim JH, Lee J, Kim W, et al. (2019) Characterization of viscoelastic behaviour of poly(dimethylsiloxane) by nanoindentation. Korean J Met Mater 57: 289-294. |
[52] | Kherroub DE, Boulaouche T (2020) Maghnite: Novel inorganic reinforcement for single-step synthesis of PDMS nanocomposites with improved thermal, mechanical and textural properties. Res Chem Intermed 46: 5199-5217. |
[53] | Queiroz DP, De Pinho MN (2005) Structural characteristics and gas permeation properties of polydimethylsiloxane/poly(propylene oxide) urethane/urea bi-soft segment membranes. Polymer 46: 2346-2353. |
[54] | Lin X, Park S, Choi D, et al. (2019) Mechanically durable superhydrophobic PDMS-candle soot composite coatings with high biocompatibility. J Ind Eng Chem 74: 79-85. |
[55] | Atthi N, Sripumkhai W, Pattamang P, et al. (2020) Superhydrophobic and superoleophobic properties enhancement on PDMS micro-structure using simple flame treatment method. Microelectron Eng 230: 111362. |
[56] | Cai JH, Huang ML, Chen XD, et al. (2021) Thermo-expandable microspheres strengthened polydimethylsiloxane foam with unique softening behaviour and high-efficient energy absorption. Appl Surf Sci 540: 148364. |
[57] | Berkem AS, Capoglu A, Nugay T, et al. (2018) Self-healable supramolecular vanadium pentoxide reinforced polydimethylsiloxane-graft-polyurethane composites. Polymers 11: 18-20. |
[58] | Goyal A, Kumar A, Patra PK, et al. (2009) In situ synthesis of metal nanoparticle embedded free standing multifunctional PDMS films. Macromol Rapid Commun 30: 1116-1122. |
[59] | Konku-Asase Y, Yaya A, Kan-Dapaah K (2020) Curing temperature effects on the tensile properties and hardness of γ-Fe2O3 reinforced PDMS nanocomposites. Adv Mater Sci Eng 2020. |
[60] | Liu J, Zong G, He L, et al. (2015) Effects of fumed and mesoporous silica nanoparticles on the properties of sylgard 184 polydimethylsiloxane. Micromachines 6: 855-864. |
[61] | Shafaamri A, Cheng CH, Wonnie Ma IA, et al. (2020) Effects of TiO2 nanoparticles on the overall performance and corrosion protection ability of neat epoxy and PDMS modified epoxy coating systems. Front Mater 6: 336. |
[62] | Fojtíková J, Kalvoda L (2018) Molecular dynamics simulations of poly(dimethylsiloxane) elasticity. Acta Phys Pol A 134: 857-858. |
[63] | Mata A, Fleischman AJ, Roy S (2005) Characterization of polydimethylsiloxane (PDMS) properties for biomedical micro/nanosystems. Biomed Microdevices 7: 281-293. |
[64] | Zhang G, Sun Y, Qian B, et al. (2020) Experimental study on mechanical performance of polydimethylsiloxane (PDMS) at various temperatures. Polym Test 90: 106670. |
[65] | Liu M, Sun J, Chen Q (2009) Influences of heating temperature on mechanical properties of polydimethylsiloxane. Sensor Actuat A-Phys 151: 42-45. |
1. | Chinyerem E. Onyekanne, Oluwaseun K. Oyewole, Ali A. Salifu, John D. Obayemi, Vitalis C. Anye, Chukwudalu C. Nwazojie, Killian C. Onwudiwe, Josephine C. Oparah, Toyin Aina, Chukwudi C. Ezeala, Theresa C. Ezenwafor, Olushola S. Odusanya, Winston O. Soboyejo, Mechanical and thermal properties of polydimethylsiloxane/magnetite nanocomposites for cancer treatment by localized hyperthermia and photothermal ablation, 2022, 139, 0021-8995, 10.1002/app.52667 | |
2. | Wenshuo Zhang, Yongheng Shi, Baoshun Wang, Ying Han, Rufan Zhang, High-strength electrospun polydimethylsiloxane/polytetrafluoroethylene hybrid membranes with stable and controllable coral-like structures, 2023, 164, 1359835X, 107316, 10.1016/j.compositesa.2022.107316 | |
3. | Karya Uysal, Ipek Seda Firat, Till Creutz, Inci Cansu Aydin, Gerhard M. Artmann, Nicole Teusch, Aysegül Temiz Artmann, A Novel In Vitro Wound Healing Assay Using Free-Standing, Ultra-Thin PDMS Membranes, 2022, 13, 2077-0375, 22, 10.3390/membranes13010022 | |
4. | Oluwadara E Moronkeji, Debashish Das, Sunho Lee, Kelly M Chang, Ioannis Chasiotis, Local electrical conductivity of carbon black/PDMS nanocomposites subjected to large deformations, 2023, 57, 0021-9983, 507, 10.1177/00219983231156253 | |
5. | Giulia Fredi, Matteo Favaro, Damiano Da Ros, Alessandro Pegoretti, Andrea Dorigato, Thermotropic Optical Response of Silicone–Paraffin Flexible Blends, 2022, 14, 2073-4360, 5117, 10.3390/polym14235117 | |
6. | Ronaldo Ariati, Flaminio Sales, Verônica Noronha, Rui Lima, João Ribeiro, Low-Cost Multifunctional Vacuum Chamber for Manufacturing PDMS Based Composites, 2022, 10, 2075-1702, 92, 10.3390/machines10020092 | |
7. | Ahmed Hashim Kareem, Mohammad Fathalilou, Ghader Rezazadeh, Modeling and analysis of a capacitive MEMS with a microstructured gap subjected to a mechanical shock, 2024, 0001-5970, 10.1007/s00707-024-04116-5 | |
8. | Govind Kumar Sharma, Nirmala Rachel James, Highly flexible, PEDOT:PSS-polyvinylpyrrolidone coated carbon nanofiber-polydimethylsiloxane composite for electromagnetic interference shielding, 2023, 296, 03796779, 117376, 10.1016/j.synthmet.2023.117376 | |
9. | Samira Valizadeh, Mohammad Fathalilou, Ghader Rezazadeh, Effects of the Temperature-Dependent Behavior of the Gap-Filling PDMS on the Response of a Capacitive MEMS to the Electrostatic Actuation, 2024, 16, 1758-8251, 10.1142/S1758825124500364 | |
10. | Hannah Varner, Tal Cohen, Explaining the spread in measurement of PDMS elastic properties: influence of test method and curing protocol, 2024, 1744-683X, 10.1039/D4SM00573B | |
11. | L. N. Krasil’nikova, Ya. A. Khamidulin, V. I. Voshchikov, E. D. Vasilieva, A. K. Kychkin, Chi Van Nguyen, A. M. Nikolaev, Yu. E. Gorshkova, O. A. Shilova, Weather-Resistant Organosilicate Coatings with Improved Water Resistance, 2024, 86, 1061-933X, 719, 10.1134/S1061933X24600593 | |
12. | Garbiela Tifui, Marius Dobromir, Lucel Sirghi, Stiffening of polydimethylsiloxane surface as result of exposure to low‐pressure argon discharge plasma, 2023, 20, 1612-8850, 10.1002/ppap.202300014 | |
13. | Soorya S. Raj, Romina Marie Mathew, Deljo Davis, Subramanyan Namboodiri Varanakkottu, Asha Srinivasan, Vinod T. P., Facile fabrication of stable wettability gradients on elastomeric surfaces for applications in water collection and controlled cell adhesion, 2023, 19, 1744-683X, 5560, 10.1039/D3SM00441D | |
14. | Hendrik Reese, Siew-Wan Ohl, Claus-Dieter Ohl, Cavitation bubble induced wall shear stress on an elastic boundary, 2023, 35, 1070-6631, 10.1063/5.0156507 | |
15. | Mohammed Nabeel, Mohanad Mousa, Béla Viskolcz, Béla Fiser, László Vanyorek, Recent Advances in Flexible Foam Pressure Sensors: Manufacturing, Characterization, and Applications – a Review, 2024, 64, 1558-3724, 449, 10.1080/15583724.2023.2262558 | |
16. | Shang Ge, Youzhi Zhu, Yun Zhu, Guiyou Wang, Guoming Chen, Shihong Liu, Ping Ye, Influence of amine chain extenders on morphology and performances of poly(dimethylsiloxane) based poly(urea‐urethane) elastomers, 2024, 62, 2642-4150, 4659, 10.1002/pol.20240438 | |
17. | Govind Kumar Sharma, Sneha L Joseph, Nirmala Rachel James, Recent Progress in Poly (3,4‐Ethylene Dioxythiophene): Polystyrene Sulfonate Based Composite Materials for Electromagnetic Interference Shielding, 2024, 9, 2365-709X, 10.1002/admt.202301203 | |
18. | Sangeetha Jayakumar, T. Saravanan, John Philip, A review on polymer nanocomposites as lead-free materials for diagnostic X-ray shielding: Recent advances, challenges and future perspectives, 2023, 4, 2773207X, 100100, 10.1016/j.hybadv.2023.100100 | |
19. | Zhiyi Gao, Qi Zhang, Yuwei Wang, Wuxu Zhang, Jinyun Liu, Dan Xu, Xiangling Xia, Siqi Hu, Baoru Bian, Yongqing Zhao, Yuanzhao Wu, Yiwei Liu, Jie Shang, Run-Wei Li, 3D printing wide detection range and high sensitivity flexible pressure sensor and its applications, 2024, 196, 13815148, 105840, 10.1016/j.reactfunctpolym.2024.105840 | |
20. | Anna Powojska, Arkadiusz Mystkowski, Edison Gundabattini, Joanna Mystkowska, Spin-Coating Fabrication Method of PDMS/NdFeB Composites Using Chitosan/PCL Coating, 2024, 17, 1996-1944, 1973, 10.3390/ma17091973 | |
21. | Rajat Kumar, Ajay Kumar, Aditya Jain, Amit Kumar Goyal, Nanograting-assisted flexible Triboelectric Nanogenerator for active human motion detection, 2024, 131, 22112855, 110318, 10.1016/j.nanoen.2024.110318 | |
22. | Ahmed Hashim Kareem, Mohammad Fathalilou, Ghader Rezazadeh, Mathematical modeling of an electrostatic MEMS with tilted elastomeric micro-pillars, 2024, 131, 0307904X, 306, 10.1016/j.apm.2024.04.030 | |
23. | Zonglin Wang, Jun Zhang, Xudi Wang, Jun Wu, A permeability membrane-type leak element based on PDMS, 2024, 220, 0042207X, 112853, 10.1016/j.vacuum.2023.112853 | |
24. | Marianne Hollensteiner, Sabrina Sandriesser, Peter Augat, Open the pores – Polydimethylsiloxane influences the porous structure of cancellous bone surrogates for biomechanical testing of osteosyntheses, 2024, 165, 00219290, 112000, 10.1016/j.jbiomech.2024.112000 | |
25. | Hugo Puozzo, Shamil Saiev, Leïla Bonnaud, David Beljonne, Roberto Lazzaroni, Integrating Benzoxazine‐PDMS 3D Networks with Carbon Nanotubes for flexible Pressure Sensors, 2024, 30, 0947-6539, 10.1002/chem.202301791 | |
26. | David Victoria-Valenzuela, Ana Beatriz Morales-Cepeda, Exploring Some Kinetic Aspects of the Free Radical Polymerization of PDMS-MA, 2024, 12, 2227-9717, 376, 10.3390/pr12020376 | |
27. | Violeta Carvalho, Inês M. Gonçalves, Nelson Rodrigues, Paulo Sousa, Vânia Pinto, Graça Minas, Hirokazu Kaji, Su Ryon Shin, Raquel O. Rodrigues, Senhorinha F.C.F. Teixeira, Rui A. Lima, Numerical evaluation and experimental validation of fluid flow behavior within an organ-on-a-chip model, 2024, 243, 01692607, 107883, 10.1016/j.cmpb.2023.107883 | |
28. | L. N. Krasilnikova, Ya. A. Khamidulin, V. I. Voshchikov, E. D. Vasilieva, A. K. Kychkin, Chi Van Nguyen, A. M. Nikolaev, Yu. E. Gorshkova, O. A. Shilova, Atmospheric-Resistant Organosilicate Coatings with Improved Water Resistance, 2024, 86, 0023-2912, 595, 10.31857/S0023291224050071 | |
29. | Omar Akram Saleh Alwazzan, Mohammad Fathalilou, Ghader Rezazadeh, Coupled nonlinear modeling of a novel high-sensitivity MEMS capacitive accelerometer enhanced by tilted pillars, 2024, 0307904X, 115897, 10.1016/j.apm.2024.115897 | |
30. | Leila Shakiba, Mohammad Reza Salehi, Effects of stretching and bending on the performance of a PDMS-based polarization-sensitive terahertz metamaterial absorber, 2025, 100, 0031-8949, 025519, 10.1088/1402-4896/ada4ff | |
31. | Rajashree Borgohain, Paresh N. Patel, Polymeric Membranes in Contact Lens Technology for Glaucoma Treatment: Breakthroughs, Obstacles, and Emerging Opportunities, 2025, 36, 1042-7147, 10.1002/pat.70135 | |
32. | Gopal Verma, Kavita Mehlawat, Sandeep Kumar Chamoli, Wei Li, Probing elasticity of soft bio-material through optical nanoindentation, 2025, 37, 1070-6631, 10.1063/5.0259261 | |
33. | Aixiao Fu, Hafeez Ahmadi, Burak Ulusoy, Hao Wu, Ander Labaien Etxeberria, Kim Dam-Johansen, Formulation optimization of a silicon-based fire protective coating in terms of intumescent alkali silicate particles, 2025, 474, 09500618, 141143, 10.1016/j.conbuildmat.2025.141143 | |
34. | Hanisah Zainal Abidin, Nur Maizatul Azra Mukhtar, Ainorkhilah Mahmood, Nor Aimi Abdul Wahab, Rafidah Zainon, Nurul Syafiqah Roslan, Nur Iwani Nor Izaham, Aishah Zarzali Shah, Effect of tin filler composition on porosity in tin-polydimethylsiloxane composites, 2025, 0033-4545, 10.1515/pac-2024-0347 | |
35. | Giuliana Grasso, Stefania Forciniti, Valentina Onesto, Lara Pierantoni, David Caballero, Eliana D’Amone, Giuseppe Gigli, Rui L. Reis, Joaquim M. Oliveira, Loretta L. del Mercato, Engineered Ratiometric Sensory Electrospun Fibers for Oxygen Mapping in Complex Cultures and Tumor Microenvironment, 2025, 09565663, 117481, 10.1016/j.bios.2025.117481 |
Opinions | Results | ||
Inclusion | Inclusion | Inclusion | Inclusion |
Doubt | Doubt | Doubt | Doubt |
Exclusion | Exclusion | Exclusion | Exclusion |
Inclusion | Doubt | Doubt | Inclusion |
Inclusion | Doubt | Inclusion | Inclusion |
Inclusion | Inclusion | Exclusion | Doubt |
Inclusion | Exclusion | Exclusion | Exclusion |
Exclusion | Doubt | Doubt | Exclusion |
Exclusion | Doubt | Inclusion | Doubt |
Exclusion | Exclusion | Inclusion | Exclusion |
Exclusion | Inclusion | Inclusion | Doubt |
Opinions | Results | |
Inclusion | Inclusion | Inclusion |
Exclusion | Exclusion | Exclusion |
Exclusion | Inclusion | Consult Adviser |
Inclusion | Exclusion | Consult Adviser |
Modification method | Principle of operation | Advantages | Disadvantages/limitation | Main results | Ref. |
Structural process | Dual-functional polymer system that combines shape memory with self-healing properties. It consists of a polymer network with permanent covalent crosslinking and abundant weak hydrogen bonds. The former introduces elasticity and maintains the permanent shape, and the latter contributes to the temporary shape via network rearrangement. | Capable of efficiently self-healing for 6 h at room temperature; The resulting polymer has shape memory effects triggered by body temperature. | The precise adjustment of the thermal transition temperature of shape memory polymer is highly complex. | The resultant polymer has shape memory effects triggered by body temperature. | [49] |
Study of the effect of aliphatic and aromatic diisocyanate structures on the mechanical properties, thermal degradation, hydrophobicity, and surface properties of polysiloxane-based polyurethane elastomers. | It provides the tensile properties of polysiloxane-based polyurethane elastomers using techniques such as Fourier transform infrared spectroscopy (FTIR), thermogravimetric analysis (TGA), X-ray photoelectron spectroscopy (XPS), X-ray diffraction (XRD), atomic force microscopy (AFM), contact angles (CA) and tensile testing. | - | In the tensile test, H12MDIPU shows the largest elongation at break. HDIPU shows a larger modulus, and TDIPU has the highest tensile strength. | [50] | |
Characterization of the viscoelastic behaviour of polymers using nanoindentation, showing a linear experimental relationship for PDMS samples with different viscosities and elasticities. | - | Nanoindentation is theoretically not sufficient and therefore conventional test results cannot be met. It may result from the difference in test methods, as nanoindentation evaluates local properties, while DMA evaluates average properties. More extensive research is needed in this area. | Experimentally measured coefficients described well the elastic and viscous behaviour expected from the crosslinking density of the PDMS samples. | [51] | |
Structural process | The use of treated Maghnite as catalyst and as inorganic reinforcement for the development of PDMS nanocomposites. | The increased mass ratio of Maghnite improves thermal stability; Improved mechanical properties of the nanocomposites compared to pure PDMS; the composite materials acquired good adsorption capacity compared to the pure polymer. Efficient, fast, and environmentally friendly method. |
- | The use of treated Maghnite, as a catalyst and as an inorganic reinforcement for the development of PDMS nanocomposites, has shown that it is an efficient, fast, and green method for obtaining PDMS nanocomposites with improved properties. | [52] |
Synthesis of copolymers of Polydimethylsiloxane and Polyethylene Oxide (PDMS-PEO) for the fabrication of amphiphilic surfaces. | The contact angle on the surface of the PDMS-PEO copolymer when placing the water droplet is equal to the contact angle of the native PDMS, however, after about 40 s, the droplet starts to spread, decreasing the contact angle. The larger the amount of vinyl incorporated, the smaller the contact angle will be. | When evaluating the absorbance spectrum, the copolymer is not as transparent as native PDMS, not absorbing significantly in the visible zone where most of the fluorescence measurement is done by laser. Young's modulus varies with the amount of vinyl added to PDMS. When it is low in amount, it exhibits a lower Young's modulus than the native PDMS for a ratio of 10:1. However as the amount of vinyl is increased, the Young's modulus increases, approaching the value of pure PDMS. |
The cross-linked copolymer (a material that allows for the incorporation of hydrophilic functional groups) exhibits acceptable for application to high speed, high-efficiency, and chemical separations. | [3] | |
Structural characteristics and gas permeation properties of bi-soft segment PDMS/PU membranes. | The vibration of SI-O-SI elongations increases with increasing PDMS membrane content. The permeabilities of CO2, O2, and N2 gases increase with increasing PDMS membrane content, while the CO2/N2 and O2/N2 ratios do not change significantly. |
The degree of crosslinking decreases sharply, when the PDMS content increases by 75% of its weight. With increasing PDMS content, some hydroxyl groups were not reacted, decreasing the degree of crosslinking. |
The permeability ratio was higher for the bisoft segment membranes described in this work than in the case of PDMS pure. | [53] | |
Structural process | Development of high durability superhydrophobic coatings against mechanical damage in abrasion tests. Obtaining PDMS with soot composite coatings that can be fabricated on various substrates such as glass, wood, stainless steel meshes, and plastics. | Hydrophobic coatings exhibit high durability against water spray; Superhydrophobic coatings exhibit excellent chemical resistance; They have high biocompatibility and can later be used in biomedical devices or implants to prevent blood coagulation. |
These hydrophobic coatings perform the worst in the wear test. | Successfully fabricated mechanically durable superhydrophobic PDMS-CSC-CS; It can tolerate high-strength sandpaper-based abrasion and ultrasonication tests; Also, it still showed super- wettable behaviours. |
[54] |
Flame treatment to generate PDMS nanostructures to improve superhydrophobia and superoleophobia. | The untreated and flame treated PDMS-PIL (square pillar pattern) surfaces show higher roughness when compared to PDMS-REC (rectangular pattern) and PDMS-FLT (flat PDMS); The longer the flame treatment duration generates more oxygen and silicon-based groups, leading to the formation of hydrophilic and the decrease in carbon concentration, which will make the surface superhydrophobic and superoleophobic. |
Flame treatment leads to a lack of surface roughness of the PDMS micropattern, negatively affecting the hydrophobicity. Therefore, the flame treatment should not exceed 30 s. | Surfaces exhibited superhydrophobic and superoleophobic properties that led to water and EG droplets rolling off almost immediately and the samples had great stability of superhydrophobicity and superoleophobicity. | [55] | |
Chemical process | Plasma treatment of the PDMS surface for optimization of optical properties and hydrophilicity. Two types of tests are tested, the first is a comparison between plain PDMS and a fused silica glass for the determination of the replica substrate. And the second test is the use of plasma to improve the hydrophilic properties of PDMS. |
In the visible light domain and being tested the smooth side of both PDMS and fused silica glass, PDMS shows 5% better transmittance, regarding the rough side, PDMS shows 17% better transmittance. Relatively to the reflectance the fused silica glass shows better than PDMS at the wavelength of 300-1200 nm, both on the smooth and rough side. PDMS is used as a replica substrate since it has a low cost and high activity in optical applications such as sunlight. Regarding plasma treatment, it shows a much higher root-mean-square surface roughness value after plasma treatment on both the smooth and rough sides; After plasma treatment, on the plasma surfaces, the roughness increases, the electric field strength increases, and the scattering regularity of free electron concentration increases. |
The surface thickness increases significantly after plasma treatment in both zones of the PDMS. | The results showed that the PDMS substrate presents a diversity of optical properties and also indicates that PDMS is a great potential to be used as a replica, low-cost, high-active substrate for optical applications, such as solar energy. | [4] |
Chemical process | Modification of the PDMS surface through a combination of physical and chemical modification routes. After the nanopattern PDMS was exposed to air plasma, a polyvinyl alcohol (PVA) treatment was performed. | The amount of oxygen in PVA- nano -PDMS is about 33%, higher than the value of 29% in pure nano-PDMS; With increasing plasma exposure time, the contact angle was decreased, improving its hydrophilicity; PDMS modified with the nanostructures shows better stability and lower contact angle values; If the amount of PVA layers increases, the contact angle decreases; The standardized PDMS with PVA coating has better long-term stability. |
There is no difference of any kind between the spectra of nanoPDMS and the plasma-treated sample, which confirmed that plasma treatment has no lasting influence on the surface hydrophilicity of PDMS. | Simple surface nanostructures combined with chemical modification improve the surface property and can solve the problem of long term stability. | [19] |
Incorporation of nanoparticles |
A simple and controllable foaming method is used to prepare PDMS foams by incorporating thermo-expandable hollow microspheres. | High compressive strength efficiency of movement energy absorption; Reinforces mechanical properties with softening behaviour; Provides foams with good toughness. |
Complicated processes with high energy consumption or poor controllability; The compressive modulus and strength of foam samples decrease with increasing microparticle content. |
The reinforced TEHM/PDMS foams with softening behaviour and high-efficient energy absorption were without any impact scars. | [56] |
Preparation of supramolecular polymer composites of PDMS nanofiber/vanadium pentoxide (V2O5) based on a reversible hydrogen bonding mechanism. | The addition of V2O5 nanofibers increases mechanical properties, namely tensile strength and improves curing efficiency compared to pure PDMS. | The curing efficiency decreases over time; Adding too many V2O5 nanofibers impairs the curing effect. |
The addition of V2O5 nanofibers increases the hydrogen bonding capability of the polymer and reduces the contact surface required for the hydrogen bonding, leading to increased healing efficiencies compared to neat polymer. | [57] | |
Incorporation of nanoparticles |
Addition of carbon nanotube nanocomposites to PDMS (CNTs). | The modulus of elasticity increases with the addition of CNTs in the PDMS matrix, gradually increasing with the increase of the CNTs percentage by weight; Regarding the dynamic results obtained, it is concluded that with the presence of the nanocomposites, the storage modulus increases; the loss of tangent is not significant; The addition of the CNTs in the PDMS matrix showed no effect on the viscoelastic behaviour of PDMS; The average hardness increases about 22% with the implementation of the nanocomposites. And the modulus of elasticity also increases about 25% in the case of nanoindentation tests and about 29% in tensile tests, when nanocomposites are present. |
According to the increase in the number of CNTs by weight, there are some imperfections on the fracture surface, as the amount of CNTs increases the imperfections become more severe. | Compared with the pure PDMS and 4.0 wt% PDMS/CNT nanocomposites, the increase in elastic modulus of pure PDMS after adding 4.0 wt% CNTs is 29.49% by tensile test. By using the nanoindentation test, the increase is 25.15%. | [1] |
Incorporation of metal nanoparticles (gold, silver, and platinum). | Increase of Young's modulus (3 times) compared to pure PDMS; This modification presents antimicrobial properties in the presence of silver microparticles; The incorporation of platinum or gold particles is used for optical or catalytic applications; Increased storage modulus and maintains damping modulus. |
Color change of the film. In the presence of gold particles, it turns ruby red and in the presence of silver particles, it turns brownish yellow when there is a reduction reaction with the curing agent of the PDMS pre-polymer. | Increase of Young's modulus. The young's modulus for nanoparticles containing films is 1.64 MPa and young's modulus of PDMS is 0.56 MPa; Increase storage modulus and maintains damping modulus; Change of color of the film, in a different types of particles; The curing agent of the PDMS pre-polymer works as a reduction reactor and a curing agent at the same time; The average modulus was found to be 1.7 ± 0.2 MPa for copolymer Ag-PDMS and 0.5 ± 0.1 MPa for PDMS; The nanoparticles containing film present antimicrobial characteristics. |
[58] | |
Incorporation of nanoparticles |
Incorporation of Fe2O3 particles (hematite). | Increase Young's modulus; Decrease tensile strength; Increase in hardness with increasing curing temperature; Decrease in hardness with increasing nanoparticle concentration between 0 and 2%; There is a linear relationship between the mechanical properties, and the concentration of nanoparticles was independent of the curing temperatures tested. |
- | Increase in Young's modulus by 170% from 1.36 to 3.71 MPa; Decrease in tensile strength by 65% with increasing nanoparticle concentration from 6.48 to 2.93 MPa; The linear increase between hardness and curing temperature; Decrease in hardness with increasing nanoparticles concentration in the matrix; When nanoparticles concentration increases, mechanical properties increase too. |
[59] |
Addition of silica nanoparticles (fumed silica A380 and mesoporous silica MCM-41). | The thermal and mechanical stability of PDMS is improved. In the case of MCM-41 Silica particles, the coefficient of thermal expansion decreases with increasing concentration; In the case of A380 Silica particles, they exhibit higher elastic modulus and better transparency due to smaller particle size compared to A380 Silica particles; Compared to pure PDMS, there is an increase in elastic modulus by about 7 times with the incorporation of silica particles. |
Decreased transmittance of PDMS when the incorporation of silica nanoparticles occurs, both A380 fumed silica and MCM-41 mesoporous silica; | In the case of MCM-41 Silica particles, the coefficient of thermal expansion decreases with increasing concentration; In the case of A380 Silica particles, they exhibit higher elastic modulus and better transparency than the bigger particle size of A380 silica particles; The elastic modulus increase by about 7 times with the incorporation of silica particles; The swelling ratio of PDMS in toluene was decreased to 0.68 when the concentration of nanoparticles was 10 wt%. A380 and MCM-41 nanoparticles had similar effects on the swelling property of PDMS. |
[60] | |
Incorporation of nanoparticles |
Incorporation of TiO2 (Titanium Dioxide) nanoparticles. | Demonstrates a photocatalytic effect on the coating film as there is an increase in absorbance in the UV region. It exhibits lower surface roughness, higher contact angle values, and better corrosion protection performance. It provides better barrier properties through reduced porosity and "zigzagging" of the polymer matrix diffusion pathway. | - | Higher concentrations of TiO2 nanoparticles reduce the glass transition temperatures (Tg) values due to the agglomeration tendency of the nanoparticles; This incorporation of TiO2 nanoparticles, increase contact angle values, lower surface roughness, and better corrosion protection process; PDMS resin was confirmed to be a suitable modifier that is able to enhance the hydrophobicity of the resulting coated surfaces without altering the curing level, glass transition temperature, dispersion state and the corrosion protection performance of TiO2-epoxy nanocomposite coating systems. |
[61] |
Simulation | Calculations are performed in the Materials Studio (MS) simulation environment using molecular dynamics (MD) theory. The results obtained are compared with experimental data. |
An innovative technique that saves materials since it promotes a computational prediction. | Approximations, for example, the elasticity of a polymer is a very complex problem, so for simplicity, the authors ignore surface effects and try to map the dependence of the bulk modulus on the crosslinking rate only. | The results seem to indicate that elastic properties of PDMS depend to the major extend on the crosslinking ratio and the particular network topology is of a less importance. | [62] |
Performing a biaxial tensile test at different speeds. Numerical studies using the most popular constitutive models were also performed for comparison with the experimental measurements. | Technique suitable for measuring displacement fields in hyperelastic materials; | The numerical models do not fully characterize the hyperelastic behaviour. | Based on the average error analysis of the constitutive model and of the displacement profiles, it was possible to establish a direct relationship. | [33] | |
Interactive process | A new high-performance functional composite was prepared by the paraffin-loaded fusion method with PDMS as the matrix. | Excellent performance in temperature-dependent thermal and mechanical properties; Excellent flexibility and heat absorption capacity; Can be useful for design and manufacturing in a wide range of potential applications. |
- | Thermal and mechanical properties can be improved greatly by considering the phase change characteristics of the paraffin components. | [15] |
Measurement of the mechanical properties of graded (layered) PDMS based on the ratio of base polymer blend to curing agent. | Great tenacity; Great compactness; Can be applied to produce flexible electronic components with extreme mechanical gradients and stronger graded adhesives. |
- | Graded PDMS was extended to a large elongation ratio before fracture and had a high upturn in stress at elongation, resulting in toughness values that were quite high. Increase the range of mechanical properties of graded PDMS, a material with more compatibility with technological processes was rendered. | [48] | |
Characterization of PDMS and compatibility study. To this end, 5 PDMS samples with a different cure, surface, and structural property ratios were forged; The PDMS formulations were analysed to investigate the effects with various biomedical processes, microfabrication, and micromachining. |
Shows the results of the various sample formulations when subjected to centrifugation, allowing you to get a speed-thickness graph; Chemical exposure and the effects on the degradation of the PDMS microtextures; Oxygen plasma exposure provides information about the recoverability of hydrophilicity, and demonstrates that at higher exposures, hydrophilicity does not decrease; Different sterilization techniques confirm the usefulness of different PDMS formulations for biomedical applications. On the other hand, different sterilization techniques allow a continuous or improved hydrophobic behaviour. Nanoindentation provides the various mechanical properties that each cure has. As for tensile testing, it is confirmed that tensile strength is higher the fewer sterilization effects. X-ray photoelectron spectroscopy provides the surface element concentration as a function of the amount of crosslinker. |
There were techniques applied that did not result in many contributions to optimize the mechanical properties or induce changes, for example, chemical immersion did not result in major changes in the hydrophilicity of the PDMS surface; Sterilization did not affect PDMS surface microtextures, element concentration, or hydrophilia. |
It was the PDMS with 14.3 wt% of cross-linker formulation that exhibited the highest tensile strength and storage modulus. Therefore, mechanical properties of PDMS could be altered (by changing the polymer to cross-linker ratio) without variations in surface chemistry. | [63] | |
Interactive process | Determination of the mechanical properties of a PDMS elastic rubber for sensor applications. | Thickness decreases with increasing rotation rate; Thickness increases with decreasing time; The shear modulus increases with temperature; The shear modulus is independent of the typical frequency used for an elastic material; For better adhesion of PDMS to an oxidized silicon wafer, a primer, such as TMSM was used. | - | The results show that PDMS is a rubber elastic material, with Young's modulus ≈ 750 kPa. When a primer is used, very good adhesion is obtained between cured PDMS and polished surfaces. Adhesive strengths up to 180 kPa | [47] |
Experimental study of the mechanical performance of PDMS at various temperatures. | The specific heat capacity of PDMS decreases along the glass transition temperature and increases with increasing temperature at a slow rate; With decreasing temperature, the thermal diffusivity of PDMS increases; The thermal conductivity of PDMS decreases with decreasing temperature; The coefficient of thermal expansion increases with increasing temperature; Hardness increases with decreasing temperature; Compression increases with decreasing temperature, leading to increased hardening. | - | The shore hardness and compressive modulus of PDMS significantly increased, with the decrease of temperature; The ultimate compressive strength increased first and then decreased with the decrease of temperature; With the decrease of temperature, the damage mode of PDMS material transitioned from micro-crack damage caused by plastic squeeze slip. |
[64] | |
Polymers confined to a small dimension are subjected to high deformation in order to realize the precision of the functioning of polymer devices at nanoscales. | For a given indentation, the slope increases with decreasing film thickness; Whether the indentation curves obtained by the Hertzian method of force indentation contact by a penetrator, or the force curves obtained by FEA simulation of thin compression elastomer, these all approximate for any given polymer thickness; Young's modulus varies with the regions where it is found, regions that have 3 different thicknesses. The first region where Young's modulus is independent of indentation, the second region where Young's modulus increases with indentation and exhibits increasing stiffness, and the third region just after contact where Young's modulus is extremely high initially and decreasing thereafter; The Young's modulus of the thin film, region 1, approaches the value of the bulk material; The measured Young's modulus can be dramatically reduced in small indentations, but significant contact hardening is permanence; The reduction in molecular mobility at the interface that is induced by the attraction between the identifier and the surface also contributes to surface hardening. | Small indentations of thin films of a polymer on a substrate lead to large deformations and hardening when the indentation depth approaches 45% of the sample thickness, which can lead to deviations from the experimental data and compromise the results. | The results described here will enable a predictive understanding of the mechanical properties of elastomeric materials under large deformations as can occur within microdevices. Also, the methods described here can be applied to understand heterogeneous and nonlinear materials. | [2] | |
Interactive process | Study of the influence of heating temperature on the mechanical properties (Young's modulus and ultimate tensile strength) of PDMS. | At the lowest temperature, at 100 ℃, the Young's modulus is the highest among all the temperatures tested; Heating time has little effect on Young's modulus at low temperature (100 ℃). However, the longer the heating time, the lower the Young's modulus; The PDMS membrane heated at 100 ℃ has 9 MPa and is stable over a long heating time; The thermal decomposition temperature of PDMS is high, approximately 310 ℃; For low heating temperatures, the mechanical properties are independent of the heating time. |
When the heating temperature is increased to 200 ℃, the maximum tensile strength is reduced to about 5 MPa, and the longer the heating time, the lower the UTS; Temperatures above 200 ℃, contribute to the decomposition of PDMS and consequently reduce the properties of PDMS. Also, longer heating time at temperatures above 200 ℃ will greatly reduce the mechanical strength of PDMS. |
Higher heating temperatures produce lower mechanical strength; The longer time of heating at a temperature greater than 200 ℃ will largely reduce the mechanical strength of PDMS; The reduced mechanical strength is attributed to the thermal decomposition which starts at a temperature of about 200 ℃ and reaches a peak at 310 ℃. |
[65] |
Opinions | Results | ||
Inclusion | Inclusion | Inclusion | Inclusion |
Doubt | Doubt | Doubt | Doubt |
Exclusion | Exclusion | Exclusion | Exclusion |
Inclusion | Doubt | Doubt | Inclusion |
Inclusion | Doubt | Inclusion | Inclusion |
Inclusion | Inclusion | Exclusion | Doubt |
Inclusion | Exclusion | Exclusion | Exclusion |
Exclusion | Doubt | Doubt | Exclusion |
Exclusion | Doubt | Inclusion | Doubt |
Exclusion | Exclusion | Inclusion | Exclusion |
Exclusion | Inclusion | Inclusion | Doubt |
Opinions | Results | |
Inclusion | Inclusion | Inclusion |
Exclusion | Exclusion | Exclusion |
Exclusion | Inclusion | Consult Adviser |
Inclusion | Exclusion | Consult Adviser |
Modification method | Principle of operation | Advantages | Disadvantages/limitation | Main results | Ref. |
Structural process | Dual-functional polymer system that combines shape memory with self-healing properties. It consists of a polymer network with permanent covalent crosslinking and abundant weak hydrogen bonds. The former introduces elasticity and maintains the permanent shape, and the latter contributes to the temporary shape via network rearrangement. | Capable of efficiently self-healing for 6 h at room temperature; The resulting polymer has shape memory effects triggered by body temperature. | The precise adjustment of the thermal transition temperature of shape memory polymer is highly complex. | The resultant polymer has shape memory effects triggered by body temperature. | [49] |
Study of the effect of aliphatic and aromatic diisocyanate structures on the mechanical properties, thermal degradation, hydrophobicity, and surface properties of polysiloxane-based polyurethane elastomers. | It provides the tensile properties of polysiloxane-based polyurethane elastomers using techniques such as Fourier transform infrared spectroscopy (FTIR), thermogravimetric analysis (TGA), X-ray photoelectron spectroscopy (XPS), X-ray diffraction (XRD), atomic force microscopy (AFM), contact angles (CA) and tensile testing. | - | In the tensile test, H12MDIPU shows the largest elongation at break. HDIPU shows a larger modulus, and TDIPU has the highest tensile strength. | [50] | |
Characterization of the viscoelastic behaviour of polymers using nanoindentation, showing a linear experimental relationship for PDMS samples with different viscosities and elasticities. | - | Nanoindentation is theoretically not sufficient and therefore conventional test results cannot be met. It may result from the difference in test methods, as nanoindentation evaluates local properties, while DMA evaluates average properties. More extensive research is needed in this area. | Experimentally measured coefficients described well the elastic and viscous behaviour expected from the crosslinking density of the PDMS samples. | [51] | |
Structural process | The use of treated Maghnite as catalyst and as inorganic reinforcement for the development of PDMS nanocomposites. | The increased mass ratio of Maghnite improves thermal stability; Improved mechanical properties of the nanocomposites compared to pure PDMS; the composite materials acquired good adsorption capacity compared to the pure polymer. Efficient, fast, and environmentally friendly method. |
- | The use of treated Maghnite, as a catalyst and as an inorganic reinforcement for the development of PDMS nanocomposites, has shown that it is an efficient, fast, and green method for obtaining PDMS nanocomposites with improved properties. | [52] |
Synthesis of copolymers of Polydimethylsiloxane and Polyethylene Oxide (PDMS-PEO) for the fabrication of amphiphilic surfaces. | The contact angle on the surface of the PDMS-PEO copolymer when placing the water droplet is equal to the contact angle of the native PDMS, however, after about 40 s, the droplet starts to spread, decreasing the contact angle. The larger the amount of vinyl incorporated, the smaller the contact angle will be. | When evaluating the absorbance spectrum, the copolymer is not as transparent as native PDMS, not absorbing significantly in the visible zone where most of the fluorescence measurement is done by laser. Young's modulus varies with the amount of vinyl added to PDMS. When it is low in amount, it exhibits a lower Young's modulus than the native PDMS for a ratio of 10:1. However as the amount of vinyl is increased, the Young's modulus increases, approaching the value of pure PDMS. |
The cross-linked copolymer (a material that allows for the incorporation of hydrophilic functional groups) exhibits acceptable for application to high speed, high-efficiency, and chemical separations. | [3] | |
Structural characteristics and gas permeation properties of bi-soft segment PDMS/PU membranes. | The vibration of SI-O-SI elongations increases with increasing PDMS membrane content. The permeabilities of CO2, O2, and N2 gases increase with increasing PDMS membrane content, while the CO2/N2 and O2/N2 ratios do not change significantly. |
The degree of crosslinking decreases sharply, when the PDMS content increases by 75% of its weight. With increasing PDMS content, some hydroxyl groups were not reacted, decreasing the degree of crosslinking. |
The permeability ratio was higher for the bisoft segment membranes described in this work than in the case of PDMS pure. | [53] | |
Structural process | Development of high durability superhydrophobic coatings against mechanical damage in abrasion tests. Obtaining PDMS with soot composite coatings that can be fabricated on various substrates such as glass, wood, stainless steel meshes, and plastics. | Hydrophobic coatings exhibit high durability against water spray; Superhydrophobic coatings exhibit excellent chemical resistance; They have high biocompatibility and can later be used in biomedical devices or implants to prevent blood coagulation. |
These hydrophobic coatings perform the worst in the wear test. | Successfully fabricated mechanically durable superhydrophobic PDMS-CSC-CS; It can tolerate high-strength sandpaper-based abrasion and ultrasonication tests; Also, it still showed super- wettable behaviours. |
[54] |
Flame treatment to generate PDMS nanostructures to improve superhydrophobia and superoleophobia. | The untreated and flame treated PDMS-PIL (square pillar pattern) surfaces show higher roughness when compared to PDMS-REC (rectangular pattern) and PDMS-FLT (flat PDMS); The longer the flame treatment duration generates more oxygen and silicon-based groups, leading to the formation of hydrophilic and the decrease in carbon concentration, which will make the surface superhydrophobic and superoleophobic. |
Flame treatment leads to a lack of surface roughness of the PDMS micropattern, negatively affecting the hydrophobicity. Therefore, the flame treatment should not exceed 30 s. | Surfaces exhibited superhydrophobic and superoleophobic properties that led to water and EG droplets rolling off almost immediately and the samples had great stability of superhydrophobicity and superoleophobicity. | [55] | |
Chemical process | Plasma treatment of the PDMS surface for optimization of optical properties and hydrophilicity. Two types of tests are tested, the first is a comparison between plain PDMS and a fused silica glass for the determination of the replica substrate. And the second test is the use of plasma to improve the hydrophilic properties of PDMS. |
In the visible light domain and being tested the smooth side of both PDMS and fused silica glass, PDMS shows 5% better transmittance, regarding the rough side, PDMS shows 17% better transmittance. Relatively to the reflectance the fused silica glass shows better than PDMS at the wavelength of 300-1200 nm, both on the smooth and rough side. PDMS is used as a replica substrate since it has a low cost and high activity in optical applications such as sunlight. Regarding plasma treatment, it shows a much higher root-mean-square surface roughness value after plasma treatment on both the smooth and rough sides; After plasma treatment, on the plasma surfaces, the roughness increases, the electric field strength increases, and the scattering regularity of free electron concentration increases. |
The surface thickness increases significantly after plasma treatment in both zones of the PDMS. | The results showed that the PDMS substrate presents a diversity of optical properties and also indicates that PDMS is a great potential to be used as a replica, low-cost, high-active substrate for optical applications, such as solar energy. | [4] |
Chemical process | Modification of the PDMS surface through a combination of physical and chemical modification routes. After the nanopattern PDMS was exposed to air plasma, a polyvinyl alcohol (PVA) treatment was performed. | The amount of oxygen in PVA- nano -PDMS is about 33%, higher than the value of 29% in pure nano-PDMS; With increasing plasma exposure time, the contact angle was decreased, improving its hydrophilicity; PDMS modified with the nanostructures shows better stability and lower contact angle values; If the amount of PVA layers increases, the contact angle decreases; The standardized PDMS with PVA coating has better long-term stability. |
There is no difference of any kind between the spectra of nanoPDMS and the plasma-treated sample, which confirmed that plasma treatment has no lasting influence on the surface hydrophilicity of PDMS. | Simple surface nanostructures combined with chemical modification improve the surface property and can solve the problem of long term stability. | [19] |
Incorporation of nanoparticles |
A simple and controllable foaming method is used to prepare PDMS foams by incorporating thermo-expandable hollow microspheres. | High compressive strength efficiency of movement energy absorption; Reinforces mechanical properties with softening behaviour; Provides foams with good toughness. |
Complicated processes with high energy consumption or poor controllability; The compressive modulus and strength of foam samples decrease with increasing microparticle content. |
The reinforced TEHM/PDMS foams with softening behaviour and high-efficient energy absorption were without any impact scars. | [56] |
Preparation of supramolecular polymer composites of PDMS nanofiber/vanadium pentoxide (V2O5) based on a reversible hydrogen bonding mechanism. | The addition of V2O5 nanofibers increases mechanical properties, namely tensile strength and improves curing efficiency compared to pure PDMS. | The curing efficiency decreases over time; Adding too many V2O5 nanofibers impairs the curing effect. |
The addition of V2O5 nanofibers increases the hydrogen bonding capability of the polymer and reduces the contact surface required for the hydrogen bonding, leading to increased healing efficiencies compared to neat polymer. | [57] | |
Incorporation of nanoparticles |
Addition of carbon nanotube nanocomposites to PDMS (CNTs). | The modulus of elasticity increases with the addition of CNTs in the PDMS matrix, gradually increasing with the increase of the CNTs percentage by weight; Regarding the dynamic results obtained, it is concluded that with the presence of the nanocomposites, the storage modulus increases; the loss of tangent is not significant; The addition of the CNTs in the PDMS matrix showed no effect on the viscoelastic behaviour of PDMS; The average hardness increases about 22% with the implementation of the nanocomposites. And the modulus of elasticity also increases about 25% in the case of nanoindentation tests and about 29% in tensile tests, when nanocomposites are present. |
According to the increase in the number of CNTs by weight, there are some imperfections on the fracture surface, as the amount of CNTs increases the imperfections become more severe. | Compared with the pure PDMS and 4.0 wt% PDMS/CNT nanocomposites, the increase in elastic modulus of pure PDMS after adding 4.0 wt% CNTs is 29.49% by tensile test. By using the nanoindentation test, the increase is 25.15%. | [1] |
Incorporation of metal nanoparticles (gold, silver, and platinum). | Increase of Young's modulus (3 times) compared to pure PDMS; This modification presents antimicrobial properties in the presence of silver microparticles; The incorporation of platinum or gold particles is used for optical or catalytic applications; Increased storage modulus and maintains damping modulus. |
Color change of the film. In the presence of gold particles, it turns ruby red and in the presence of silver particles, it turns brownish yellow when there is a reduction reaction with the curing agent of the PDMS pre-polymer. | Increase of Young's modulus. The young's modulus for nanoparticles containing films is 1.64 MPa and young's modulus of PDMS is 0.56 MPa; Increase storage modulus and maintains damping modulus; Change of color of the film, in a different types of particles; The curing agent of the PDMS pre-polymer works as a reduction reactor and a curing agent at the same time; The average modulus was found to be 1.7 ± 0.2 MPa for copolymer Ag-PDMS and 0.5 ± 0.1 MPa for PDMS; The nanoparticles containing film present antimicrobial characteristics. |
[58] | |
Incorporation of nanoparticles |
Incorporation of Fe2O3 particles (hematite). | Increase Young's modulus; Decrease tensile strength; Increase in hardness with increasing curing temperature; Decrease in hardness with increasing nanoparticle concentration between 0 and 2%; There is a linear relationship between the mechanical properties, and the concentration of nanoparticles was independent of the curing temperatures tested. |
- | Increase in Young's modulus by 170% from 1.36 to 3.71 MPa; Decrease in tensile strength by 65% with increasing nanoparticle concentration from 6.48 to 2.93 MPa; The linear increase between hardness and curing temperature; Decrease in hardness with increasing nanoparticles concentration in the matrix; When nanoparticles concentration increases, mechanical properties increase too. |
[59] |
Addition of silica nanoparticles (fumed silica A380 and mesoporous silica MCM-41). | The thermal and mechanical stability of PDMS is improved. In the case of MCM-41 Silica particles, the coefficient of thermal expansion decreases with increasing concentration; In the case of A380 Silica particles, they exhibit higher elastic modulus and better transparency due to smaller particle size compared to A380 Silica particles; Compared to pure PDMS, there is an increase in elastic modulus by about 7 times with the incorporation of silica particles. |
Decreased transmittance of PDMS when the incorporation of silica nanoparticles occurs, both A380 fumed silica and MCM-41 mesoporous silica; | In the case of MCM-41 Silica particles, the coefficient of thermal expansion decreases with increasing concentration; In the case of A380 Silica particles, they exhibit higher elastic modulus and better transparency than the bigger particle size of A380 silica particles; The elastic modulus increase by about 7 times with the incorporation of silica particles; The swelling ratio of PDMS in toluene was decreased to 0.68 when the concentration of nanoparticles was 10 wt%. A380 and MCM-41 nanoparticles had similar effects on the swelling property of PDMS. |
[60] | |
Incorporation of nanoparticles |
Incorporation of TiO2 (Titanium Dioxide) nanoparticles. | Demonstrates a photocatalytic effect on the coating film as there is an increase in absorbance in the UV region. It exhibits lower surface roughness, higher contact angle values, and better corrosion protection performance. It provides better barrier properties through reduced porosity and "zigzagging" of the polymer matrix diffusion pathway. | - | Higher concentrations of TiO2 nanoparticles reduce the glass transition temperatures (Tg) values due to the agglomeration tendency of the nanoparticles; This incorporation of TiO2 nanoparticles, increase contact angle values, lower surface roughness, and better corrosion protection process; PDMS resin was confirmed to be a suitable modifier that is able to enhance the hydrophobicity of the resulting coated surfaces without altering the curing level, glass transition temperature, dispersion state and the corrosion protection performance of TiO2-epoxy nanocomposite coating systems. |
[61] |
Simulation | Calculations are performed in the Materials Studio (MS) simulation environment using molecular dynamics (MD) theory. The results obtained are compared with experimental data. |
An innovative technique that saves materials since it promotes a computational prediction. | Approximations, for example, the elasticity of a polymer is a very complex problem, so for simplicity, the authors ignore surface effects and try to map the dependence of the bulk modulus on the crosslinking rate only. | The results seem to indicate that elastic properties of PDMS depend to the major extend on the crosslinking ratio and the particular network topology is of a less importance. | [62] |
Performing a biaxial tensile test at different speeds. Numerical studies using the most popular constitutive models were also performed for comparison with the experimental measurements. | Technique suitable for measuring displacement fields in hyperelastic materials; | The numerical models do not fully characterize the hyperelastic behaviour. | Based on the average error analysis of the constitutive model and of the displacement profiles, it was possible to establish a direct relationship. | [33] | |
Interactive process | A new high-performance functional composite was prepared by the paraffin-loaded fusion method with PDMS as the matrix. | Excellent performance in temperature-dependent thermal and mechanical properties; Excellent flexibility and heat absorption capacity; Can be useful for design and manufacturing in a wide range of potential applications. |
- | Thermal and mechanical properties can be improved greatly by considering the phase change characteristics of the paraffin components. | [15] |
Measurement of the mechanical properties of graded (layered) PDMS based on the ratio of base polymer blend to curing agent. | Great tenacity; Great compactness; Can be applied to produce flexible electronic components with extreme mechanical gradients and stronger graded adhesives. |
- | Graded PDMS was extended to a large elongation ratio before fracture and had a high upturn in stress at elongation, resulting in toughness values that were quite high. Increase the range of mechanical properties of graded PDMS, a material with more compatibility with technological processes was rendered. | [48] | |
Characterization of PDMS and compatibility study. To this end, 5 PDMS samples with a different cure, surface, and structural property ratios were forged; The PDMS formulations were analysed to investigate the effects with various biomedical processes, microfabrication, and micromachining. |
Shows the results of the various sample formulations when subjected to centrifugation, allowing you to get a speed-thickness graph; Chemical exposure and the effects on the degradation of the PDMS microtextures; Oxygen plasma exposure provides information about the recoverability of hydrophilicity, and demonstrates that at higher exposures, hydrophilicity does not decrease; Different sterilization techniques confirm the usefulness of different PDMS formulations for biomedical applications. On the other hand, different sterilization techniques allow a continuous or improved hydrophobic behaviour. Nanoindentation provides the various mechanical properties that each cure has. As for tensile testing, it is confirmed that tensile strength is higher the fewer sterilization effects. X-ray photoelectron spectroscopy provides the surface element concentration as a function of the amount of crosslinker. |
There were techniques applied that did not result in many contributions to optimize the mechanical properties or induce changes, for example, chemical immersion did not result in major changes in the hydrophilicity of the PDMS surface; Sterilization did not affect PDMS surface microtextures, element concentration, or hydrophilia. |
It was the PDMS with 14.3 wt% of cross-linker formulation that exhibited the highest tensile strength and storage modulus. Therefore, mechanical properties of PDMS could be altered (by changing the polymer to cross-linker ratio) without variations in surface chemistry. | [63] | |
Interactive process | Determination of the mechanical properties of a PDMS elastic rubber for sensor applications. | Thickness decreases with increasing rotation rate; Thickness increases with decreasing time; The shear modulus increases with temperature; The shear modulus is independent of the typical frequency used for an elastic material; For better adhesion of PDMS to an oxidized silicon wafer, a primer, such as TMSM was used. | - | The results show that PDMS is a rubber elastic material, with Young's modulus ≈ 750 kPa. When a primer is used, very good adhesion is obtained between cured PDMS and polished surfaces. Adhesive strengths up to 180 kPa | [47] |
Experimental study of the mechanical performance of PDMS at various temperatures. | The specific heat capacity of PDMS decreases along the glass transition temperature and increases with increasing temperature at a slow rate; With decreasing temperature, the thermal diffusivity of PDMS increases; The thermal conductivity of PDMS decreases with decreasing temperature; The coefficient of thermal expansion increases with increasing temperature; Hardness increases with decreasing temperature; Compression increases with decreasing temperature, leading to increased hardening. | - | The shore hardness and compressive modulus of PDMS significantly increased, with the decrease of temperature; The ultimate compressive strength increased first and then decreased with the decrease of temperature; With the decrease of temperature, the damage mode of PDMS material transitioned from micro-crack damage caused by plastic squeeze slip. |
[64] | |
Polymers confined to a small dimension are subjected to high deformation in order to realize the precision of the functioning of polymer devices at nanoscales. | For a given indentation, the slope increases with decreasing film thickness; Whether the indentation curves obtained by the Hertzian method of force indentation contact by a penetrator, or the force curves obtained by FEA simulation of thin compression elastomer, these all approximate for any given polymer thickness; Young's modulus varies with the regions where it is found, regions that have 3 different thicknesses. The first region where Young's modulus is independent of indentation, the second region where Young's modulus increases with indentation and exhibits increasing stiffness, and the third region just after contact where Young's modulus is extremely high initially and decreasing thereafter; The Young's modulus of the thin film, region 1, approaches the value of the bulk material; The measured Young's modulus can be dramatically reduced in small indentations, but significant contact hardening is permanence; The reduction in molecular mobility at the interface that is induced by the attraction between the identifier and the surface also contributes to surface hardening. | Small indentations of thin films of a polymer on a substrate lead to large deformations and hardening when the indentation depth approaches 45% of the sample thickness, which can lead to deviations from the experimental data and compromise the results. | The results described here will enable a predictive understanding of the mechanical properties of elastomeric materials under large deformations as can occur within microdevices. Also, the methods described here can be applied to understand heterogeneous and nonlinear materials. | [2] | |
Interactive process | Study of the influence of heating temperature on the mechanical properties (Young's modulus and ultimate tensile strength) of PDMS. | At the lowest temperature, at 100 ℃, the Young's modulus is the highest among all the temperatures tested; Heating time has little effect on Young's modulus at low temperature (100 ℃). However, the longer the heating time, the lower the Young's modulus; The PDMS membrane heated at 100 ℃ has 9 MPa and is stable over a long heating time; The thermal decomposition temperature of PDMS is high, approximately 310 ℃; For low heating temperatures, the mechanical properties are independent of the heating time. |
When the heating temperature is increased to 200 ℃, the maximum tensile strength is reduced to about 5 MPa, and the longer the heating time, the lower the UTS; Temperatures above 200 ℃, contribute to the decomposition of PDMS and consequently reduce the properties of PDMS. Also, longer heating time at temperatures above 200 ℃ will greatly reduce the mechanical strength of PDMS. |
Higher heating temperatures produce lower mechanical strength; The longer time of heating at a temperature greater than 200 ℃ will largely reduce the mechanical strength of PDMS; The reduced mechanical strength is attributed to the thermal decomposition which starts at a temperature of about 200 ℃ and reaches a peak at 310 ℃. |
[65] |