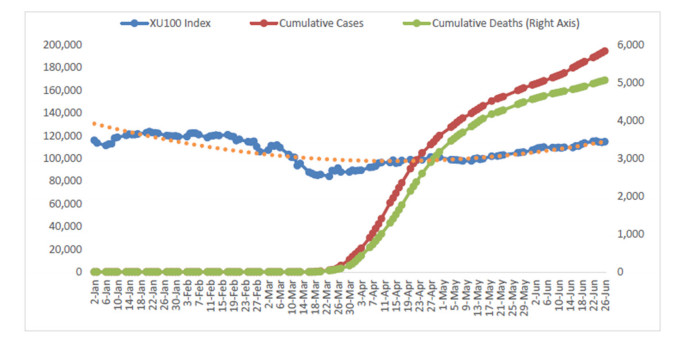
Citation: Claas Hüter, Mingxuan Lin, Diego Schicchi, Martin Hunkel, Ulrich Prahl, Robert Spatschek. A multiscale perspective on the kinetics of solid state transformations with application to bainite formation[J]. AIMS Materials Science, 2015, 2(4): 319-345. doi: 10.3934/matersci.2015.4.319
[1] | Ming-Zhen Xin, Bin-Guo Wang, Yashi Wang . Stationary distribution and extinction of a stochastic influenza virus model with disease resistance. Mathematical Biosciences and Engineering, 2022, 19(9): 9125-9146. doi: 10.3934/mbe.2022424 |
[2] | Tingting Xue, Xiaolin Fan, Zhiguo Chang . Dynamics of a stochastic SIRS epidemic model with standard incidence and vaccination. Mathematical Biosciences and Engineering, 2022, 19(10): 10618-10636. doi: 10.3934/mbe.2022496 |
[3] | Fathalla A. Rihan, Hebatallah J. Alsakaji . Analysis of a stochastic HBV infection model with delayed immune response. Mathematical Biosciences and Engineering, 2021, 18(5): 5194-5220. doi: 10.3934/mbe.2021264 |
[4] | Kangbo Bao, Qimin Zhang, Xining Li . A model of HBV infection with intervention strategies: dynamics analysis and numerical simulations. Mathematical Biosciences and Engineering, 2019, 16(4): 2562-2586. doi: 10.3934/mbe.2019129 |
[5] | Yang Chen, Wencai Zhao . Dynamical analysis of a stochastic SIRS epidemic model with saturating contact rate. Mathematical Biosciences and Engineering, 2020, 17(5): 5925-5943. doi: 10.3934/mbe.2020316 |
[6] | Helong Liu, Xinyu Song . Stationary distribution and extinction of a stochastic HIV/AIDS model with nonlinear incidence rate. Mathematical Biosciences and Engineering, 2024, 21(1): 1650-1671. doi: 10.3934/mbe.2024072 |
[7] | H. J. Alsakaji, F. A. Rihan, K. Udhayakumar, F. El Ktaibi . Stochastic tumor-immune interaction model with external treatments and time delays: An optimal control problem. Mathematical Biosciences and Engineering, 2023, 20(11): 19270-19299. doi: 10.3934/mbe.2023852 |
[8] | Tianfang Hou, Guijie Lan, Sanling Yuan, Tonghua Zhang . Threshold dynamics of a stochastic SIHR epidemic model of COVID-19 with general population-size dependent contact rate. Mathematical Biosciences and Engineering, 2022, 19(4): 4217-4236. doi: 10.3934/mbe.2022195 |
[9] | Divine Wanduku . The stochastic extinction and stability conditions for nonlinear malaria epidemics. Mathematical Biosciences and Engineering, 2019, 16(5): 3771-3806. doi: 10.3934/mbe.2019187 |
[10] | Xiaomeng Wang, Xue Wang, Xinzhu Guan, Yun Xu, Kangwei Xu, Qiang Gao, Rong Cai, Yongli Cai . The impact of ambient air pollution on an influenza model with partial immunity and vaccination. Mathematical Biosciences and Engineering, 2023, 20(6): 10284-10303. doi: 10.3934/mbe.2023451 |
The world has been faced with the Covid-19 common disease phenomenon recently. It originated from China at the end of 2019, spread to other countries, which are close to China in the first months of 2020, and has become pandemic in March 2020 (World Health Organization-WHO, 2020a). The Covid-19 pandemic has been influencing all countries deeply and negatively nowadays.
With the spreading of Covid-19 to countries, most economic and financial indicators have begun to deteriorate. In this context, negative developments have been seen in these indicators such as credit default swap (CDS) spreads, foreign exchange rates (FER), retention share, and net selling amount of foreign investors in equity markets, interest rates, and oil prices. All of these indicators are crucial in terms of roles and effects in economies (Orhan et al., 2019) because they affect foreign investment inflows to countries and investment decisions of foreign investors as well.
All countries pay attention to foreign investments. However, foreign investments have much more significance, especially in emerging countries. Emerging countries can mainly provide financing from external (international/foreign) sources because domestic savings are not sufficient to finance economic activities and growth. Hence, emerging countries try to attract much more foreign investments. By considering that there are two types of foreign investments, which are direct and portfolio (Karikari, 1992; Zengin et al., 2018), attracting more foreign direct investment is not easy because of the geopolitical and political considerations. On the other hand, stimulating foreign portfolio investments, which can be made via bonds, bills, and equities, is much easier concerning foreign direct investments.
Foreign investors consider the riskiness of countries in allocating funds among various asset opportunities to benefit from diversification (Dooley & Hutchison, 2009; Yang et al., 2018; Akhtaruzzaman et al., 2020a) in decreasing risks in the globalizing world. Besides, financial, fiscal, price, and macroeconomic stability in invested countries are significant for foreign investors. All these have a huge role in the financing and development of emerging countries via affecting the improvement of both the real and financial sectors.
Although increasing foreign investments is desired, there are also some arguments against the role of foreign investments in emerging countries. Especially, foreign portfolio investments have been criticized very often. Naturally, it is expected that foreign portfolio investments make effects on the financial markets (i.e. stock exchanges) of countries. Foreign investments affect the development of equity markets, prices, returns, and volatility (Hargis & Ramanlal, 1997; Bekaert & Harvey, 2003). However, the direction of foreign investment effects is not clear and crucial at this point. Levine & Zervos (1998), and Rogoff (1999) conclude that foreign capital inflows make a positive contribution to countries' growth and development. On the other hand, some have argued that retention share and net selling amount in this study have negative effects (Adabag & Ornelas, 2004) if foreign investors decrease the retention share and increase the net selling amount on emerging countries. Also, unfettered activities of foreign investors are evaluated as harmful by some researchers (Rodrik & Subramanian, 2009; Stiglitz, 2010).
On the other hand, there is a Covid-19 pandemic reality in the world that has been affecting all countries. There are nearly 9.9 million cases, and 497 thousand deaths because of the Covid-19 pandemic in the world as of 06.26.2020 (WHO, 2020b). Similarly, the Covid-19 pandemic increased in Turkey. Covid-19 has been determined on 03.10.2020 and the first death has occurred on 03.17.2020 in Turkey. Total cases have become 194.5 thousand and total deaths are 5 thousand in Turkey resulting from Covid-19 as of 06.26.2020 (Ministry of Health of Turkey-MHT, 2020).
While Covid-19 presents and continues to cause deaths, economic and financial indicators have been deteriorating in such an environment. Even, the pandemic causes unprecedented and destructive effects on economies and indicators (Goodell, 2020; Rizwan et al., 2020). Therefore, the Covid-19 pandemic should be considered in making any analysis, especially when examining macroeconomic and financial related issues such as the development of the main stock index. Also, it is seen that the level of economic activities has been decreasing in the time of Covid-19. Therefore, the negative effects of the pandemic have been felt deeply in emerging countries. In this context, Figure 1 presents the development of the XU100 index, cumulative cases, and deaths resulting from the Covid-19 pandemic in Turkey.
As Figure 1 shows, the XU100 index was relatively high before the Covid-19 pandemic times concerning in time of the Covid-19 pandemic. Also, total cumulative cases have reached 194.5 thousand and total deaths have become 5 thousand as of 06.26.2020 in Turkey.
Turkey has been taking measures to decrease the negative effects of the Covid-19 pandemic on the economy, corporations, households, and individuals which is similar to other countries affected by the pandemic (Akhtaruzzaman et al., 2020b; Gherghina et al., 2020; Kartal, 2020; Narayan et al., 2020; Phan & Narayan, 2020). Some of these measures could be summarized as local lockdowns, quarantines on residential areas, ban on flights, lowering the minimum payment requirements of credit cards, cash transfers to families in need, increasing the amount of funding markets by the central bank of the Republic of Turkey including buying governmental bonds, deferred credit payments to banks, deferred governmental (tax and social security premium) payments in various sectors, and minimum wage subsidies (Stanley, 2020; Official Gazette, 2020).
In summary, Turkey has been in the Covid-19 pandemic since 11.03.2020, there have been serious cumulative cases and deaths resulting from the Covid-19 pandemic, there is an important amount of foreign portfolio outflows from Turkey since the beginning of 2020, and the XU100 index has been decreasing and in low-level concerning before the Covid-19 pandemic period. The low-level of the stock exchange index causes the underpricing of Turkish assets and this situation is negative for Turkey. In this context, it could be beneficial to examine the effects of activities of foreign investors on the main stock exchange index in Covid-19 pandemic times and whether the effects of these factors vary according to period whether Turkey is in either before the Covid-19 pandemic period or in Covid-19 pandemic times. This determination could contribute to regulatory bodies to develop policies, take measures, and prevent the negative effects on main stock exchange indices. Hence foreign portfolio investments to Turkey via equities could be stimulated, and Turkey could have the opportunity to increase foreign portfolio inflows, and Turkish assets could be priced at their fair value that all affect the distribution of financial sources among alternative investment instruments including stock exchange.
The study aims to define the effects of activities of foreign investors on the XU100 index by performing the Engle-Granger cointegration test, the Toda-Yamamoto causality test, and MARS analysis. Daily data between 01.02.2020 and 06.26.2020, activities of foreign investors (retention share and net selling amount), and the presence of the Covid-19 pandemic are used for this aim. Turkey is focused on because of being a pioneering and leading emerging country and the main stock exchange index of Turkey decreased on average at an important amount during the Covid-19 pandemic period. Also, the main motivation of the study is that there are approximately Turkish Lira (TRY) 33 billion foreign portfolio outflows from Turkey stock market since 2020 beginning (Central Securities Depositories of Turkey-CSD, 2020) and whether the behavior of foreign investors are influential on the main stock exchange index of Turkey or not.
The main contributions of the study are that the study (ⅰ) is the pioneer study in Turkey examining the effects of foreign investors' activities on the main stock exchange index at Covid-19 age; (ⅱ) examines the XU100 index by focusing on mainly foreign investors' activities with using retention share and net selling amount as dependent variables; (ⅲ) performs Engle-Granger cointegration test and Toda-Yamamoto causality test. Also, the study employs the MARS method which is used for the first time to examine the changes of the XU100 index; (ⅳ) uses daily data between 01.02.2020 and 06.26.2020 which covers before and in time of the Covid-19 pandemic. Data for foreign retention share, which is calculated based on the openness of publicly traded companies in Borsa İstanbul (BIST), is also used for the first time.
The rest of the study is organized as follows. Part 2 explains the variables by benefitting from the literature, data, and methods used in the study. Part 3 presents the empirical results. Part 4 presents a findings-based discussion and policy implications. Part 5 concludes.
By considering that the study focuses on the effects of foreign investors' activities on the main stock exchange index, the XU100 index is used as a dependent variable because the XU100 index is the main stock exchange index in Turkey as in line with the studies of Kesik et al. (2016), and Kartal et al. (2020).
In the literature, some studies examine the causes of the main stock exchange indices' changes. In this context, a variety of macroeconomic and financial variables such as economic growth, foreign direct investments, foreign exchange rates, inflation, interest rates, money supply, production index, etc. are considered in these studies. For example, Kwon & Shin (1999) consider the production index, exchange rate, trade balance, and money supply. However, data for such variables are issued on a quarterly or monthly basis, and the study focuses on the Covid-19 pandemic times which requires working with the most recent (i.e. daily base) data. By considering this fact, Kartal et al. (2020) include CDS spreads, FER, foreign investors' retention share, and net selling amount as variables that have daily data. For these reasons, the mentioned macroeconomic variables are not considered and included in the study. Moreover, it is acknowledged that there is evolving literature concerning the Covid-19 pandemic and its effects on various economic and financial indicators.
On the other hand, foreign portfolio inflows, foreign investors' trading, and net selling amount of foreign investors in emerging economies are examined in various studies. Table 1 summarizes some of these studies.
Authors | Year | Scope | Period | Method | Results |
Clark & Berko | 1997 | Mexico | 1989/1–1996/3 | Regression | The increase in FPI causes an increase in stock prices. |
Bekaert & Harvey | 1998 | 17 Emerging Countries | 1977–1996 | GARCH | Increasing flows have a high correlation with returns. |
Dahlquist & Robertsson | 2004 | Sweden | 1993–1998 | VAR | Net purchases of foreign investors provide a permanent increase of stock prices. |
Baklacı | 2007 | Turkey | 1997/1–2006/4 | Granger causality & OLS | There is a significant bilateral interaction between FPI and stock returns. |
Boyer & Zheng | 2009 | United States | 1952–2004 | VAR & Regression | There is a significant positive relation between stock market returns and flows of foreign investors. |
Sevil et al. | 2012 | Turkey | 2006/1–2010/4 | VECM & Granger causality | There is causality from foreign investors to market index return. |
Vo | 2015 | Vietnam | 2006/2012 | GMM & Regression | Ownership of foreign investors decreases firm stock price volatility. |
Kesik et al. | 2016 | Turkey | 2005/2015 | Granger causality | FPI have an increasing impact on XU100 index. |
Liew et al. | 2018 | Malaysia | 2009/1–2016/12 | VAR & Granger causality | There is a one-way causality from gross inflows. |
Topaloğlu et al. | 2019 | 7 Emerging Countries | 2005–2016 | Panel data analysis | There is a significant and positive nexus between FPI and stock market returns. |
Angelovska | 2020 | Macedonia | 2005/1–2009/12 | Regression | Net inflows are connected with the rise of returns. |
David et al. | 2020 | 11 Countries | 79 Trading Days | Threshold cointegration | Shocks caused by diseases have an important effect on stock indices. |
Gupta & Ahmet | 2020 | India | 2002/1–2016/12 | ARDL | The performance of stock exchanges is one of the most important factors for FPI. |
Kartal et al. | 2020 | Turkey | 2020/1–2020/5 | Machine learning | The retention amount of foreign investors is influential in both the pre-pandemic and the pandemic periods. |
Kotishwar | 2020 | India | 2000/1–2019/12 | ARCH & OLS | FPI influence equity market volatility. |
Note: ARCH = Auto regressive conditional heteroscedasticity; ARDL = Autoregressive distributed lag; FPI = Foreign portfolio inflows; GARCH = Generalized autoregressive conditional heteroscedasticity; GMM = Generalized method of moments; OLS = Ordinary Least Squares; VAR = Vector autoregression; VECM = Vector error correction model. |
As Table 1 summarizes, various studies consider the effects of the foreign investors' activities on stock exchanges. These studies define that some of the foreign trading phenomena are not beneficial; foreign investors make the equity market more efficient and decrease the volatility in the long-run; the equity market index increases when foreign inflows increase. Therefore, it is most likely to make the effect of foreign investors' activities on the XU100 index. In this context, retention share and net selling amount of foreign investors are taken into account in the analysis as dependent variables by considering these studies since the study focuses on the effects of foreign investors' activities XU100 index. Besides, a positive relationship is expected between the XU100 index and retention share of foreign investors; and XU100 and net selling amount of foreign investors.
Moreover, as a black swan case, the Covid-19 pandemic is considered. It is acknowledged that there is a growing literature on the pandemic. By considering that stock market indices have been affected negatively by the pandemic (Adekoya & Kofi Nti, 2020; Al-Awadhi et al., 2020; Ali et al., 2020; Ashraf, 2020; Baker et al., 2020; Corbet et al., 2020; Engelhardt et al., 2020; Erdem, 2020; Gherghina et al., 2020; Liu et al., 2020; Mazur et al., 2020; Zhang et al., 2020), the presence of the pandemic in Turkey, which was seen for the first time on 03.10.2020, is taken into consideration. We use the beginning date of the pandemic in Turkey.
Table 2 summarizes the details of the variables considered in the analysis.
Variable | Symbol | Description | Effect | |
Type | Name | |||
Dependent | Main index | XU100 | The daily closing value of the BIST main index | |
Independent | Retention share | FSHARE | Daily retention share of foreign investors in BIST (%) | + |
Net selling | NETSELL | Daily net selling amount of foreign investors in BIST (TRY denominated amount) | - | |
Covid-19 | COVID | 1: If Covid-19 exists, 0: otherwise | - | |
Note: A positive (+) relationship means that XU100 increases when the independent variable increases. A negative (-) relationship means that XU100 decreases when the independent variable increases. |
This study focuses on Turkey by considering that there is a high amount of foreign portfolio outflows from the stock exchange since the 2020 year beginning and the main stock market index has decreased at an important amount. In this context, the study includes the period between 01.02.2020 and 06.26.2020. This period is selected to focus on the very recent period including Covid-19 pandemic times and the nearest period before the Covid-19 pandemic. Also, data for business days are considered because data of variables can be obtained only for the business day.
Data for the XU100 index are gathered from Bloomberg Terminal. Also, data for foreign investors' retention share and net selling amount are gathered from CSD (2020). Besides, data for Covid-19 situations are gathered from MHT (2020).
The first issue in the analysis is to test the stationarity of the variables to prevent spurious regression and misleading conclusions in turn. Although there is a variety of unit root tests to examine the stationary condition of the data set. Augmented Dickey-Fuller (ADF) is employed in the study to examine the stationarity by considering that this is mostly used in financial time series and studies.
The hypotheses of the ADF test are expressed as follows:
■ H0: Series include unit root (non-stationary).
■ H1: Series include no unit root (stationary).
If test statistics (prob.) of ADF are lower or equal to 0.05, then the H0 hypothesis is rejected which means that the series is stationary.
Engle-Granger cointegration test, which focuses on the long-term relationship among the variables of time-series, includes two steps procedure. In the first step, the stationarity of variables should be provided. After that, regression is applied. Residuals of the regression model are again examined in terms of stationarity by performing unit root tests. If residuals are stationary, then there is a long-term relationship (cointegration) between variables. In other words, these variables move together.
In the second step, the short-term relationship is analyzed with the estimation of an error correction model (ECM). Residual of the regression model could be used to estimate ECM if variables have a long-term relationship (Granger, 1969; Engle & Granger, 1987).
The hypotheses of the Engle-Granger cointegration test are expressed as follows:
■ H0: Variables are not cointegrated (Residuals of OLS include unit root).
■ H1: Variables are cointegrated (Residuals of OLS do not include unit root).
If test statistics (prob.) of the Engle-Granger cointegration test are lower or equal to 0.05, then the H0 hypothesis is rejected which means that there is causality between variables used in the analysis.
Cointegration tests are applied to analyze the long-term relationship between the main stock exchange index and the activities of foreign investors. Cointegration tests are much more appropriate compared to vector autoregression models because they can explore the dynamic co-movements between variables (Mukherjee & Naka, 1995). Therefore, cointegration tests are applied in the study.
Toda & Yamamoto causality test is employed to examine the relationship between variables. Unlike other causality tests, Toda & Yamamoto causality test does not require the stationary situation for variables to be used in the analysis (Dinçer et al., 2020). This is important because using the first difference of variables in the analysis may cause a lack of information and variables may be non-stationary (Tayyar, 2018).
There are two steps in applying the test. In the first step, the unit root test is applied to variables and the maximum cointegration degree (d) is determined. After that, lag lengths (k) are defined. In the second step, "k+dmax" lag formula is applied for estimation (Toda & Yamamoto, 1995).
The hypotheses of the Toda & Yamamoto causality test are expressed as follows:
■ H0: $ {\alpha }_{1i} $ = 0 and $ {\alpha }_{2i} $ = 0 (there is no causality from Y to X).
■ H1: $ {\alpha }_{1i} $ ≠ 0 and $ {\alpha }_{2i} $ ≠ 0 (there is causality from Y to X).
If test statistics (prob.) of Toda & Yamamoto causality test are lower or equal to 0.05, then the H0 hypothesis is rejected which means that there is causality between variables.
As a nonparametric regression modeling of high dimensional data to estimate underlying functional relationships between variables, the MARS method is firstly introduced by Friedman (1991). The main advantage of MARS is that this method does not require any pre-assumption although linear model regressions require some pre-assumptions.
There are two-steps in the MARS method. In the first step, the algorithm starts from a constant term that is the mean of the dependent values. In the second step, the piecewise linear segments, known as basis functions (BFs), are iteratively added to the model.
BFs are dependent on spline functions that are defined on a given segment and the end points of the segment are called knots. The forward step finds the potential knots to improve the performance and leads to overfitting.
A general MARS model could be formulated as in the equation below (Friedman, 1991):
$ Y\_t = {B}_{0}+{\sum }_{k = 1}^{K}{a}_{n}{B}_{n}\left({X}_{t}\right)+ \epsilon $ | (1) |
in which Y is the dependent variable and X represents independent variables. $ {B}_{0} $ denotes the constant term and $ {B}_{n}\left({X}_{t}\right) $ describes the basis function that is estimated by minimizing the residual sum of squares. $ {a}_{n} $ shows the coefficient of nth basis functions (Friedman, 1991). In the backward stepwise stage (pruning stage), it can be eliminated the redundant knots that have the least contribution to the complex model by using Generalized Cross-Validation (GCV). The best model is selected according to the highest coefficient of determination (R2) and the lowest GCV value (Hastie et al., 2009).
Before Covid-19 pandemic times, daily data includes 48 observations from 01.02.2020 and 03.09.2020. On the other side, daily data includes 74 observations that occurred between 03.10.2020 and 06.26.2020 which is related to Covid-19 pandemic times. Figure 2 shows the development of the retention share and net selling amount of foreign investors in Turkey.
As Figure 2 presents, the retention share of foreign investors has been decreasing from 65.9% to 52.4%. Besides, there are net selling amounts for all days except for a few days. These two figures imply that foreign investors' activities have not been supporting the XU100 index. Especially, foreign investors have been taking back their investments from Borsa İstanbul since the beginning of Covid-19 pandemic times in Turkey. As a result of this approach, retention share has been decreasing constantly.
Table 3 summarizes the descriptive statistics of the variables in both periods.
Period Variable | Before Covid-19 | Covid-19 | |||||
XU1001 | FSHARE2 | NETSELL3 | XU1001 | FSHARE2 | NETSELL3 | ||
Mean | 117,361.9 | 61.01856 | 215.9715 | 100,021.8 | 56.56831 | 234.6904 | |
Median | 119,408.5 | 60.73146 | 258.8678 | 99,069.46 | 57.31724 | 278.9121 | |
Maximum | 123,556.1 | 65.85941 | 786.5698 | 115,338.9 | 60.72814 | 1109.929 | |
Minimum | 103,524.0 | 58.88518 | −1029.742 | 84,246.17 | 52.37000 | -485.1429 | |
Std. Dev. | 4,931.612 | 1.547033 | 324.5663 | 85, 17.130 | 2.988219 | 263.4816 | |
Skewness | -0.982580 | 1.401699 | -1.151931 | 0.041302 | -0.114845 | -0.297241 | |
Kurtosis | 3.089060 | 5.100109 | 5.810881 | 2.087917 | 1.440857 | 4.418486 | |
Jarque-Bera | 7.739573 | 24.53900 | 26.41767 | 2.586051 | 7.658022 | 7.293661 | |
Probability | 0.020863 | 0.000005 | 0.000002 | 0.274439 | 0.021731 | 0.026074 | |
Observations | 48 | 48 | 48 | 74 | 74 | 74 | |
Note: 1 The dependent variable; 2 %; 3 million TRY. |
Before Covid-19 pandemic times, the XU100 index is 117,362 on average but it decreased to 103,524 level at the minimum and has reached 123,556 at the maximum. Besides, the retention share of foreign investors is 61% on average. The share decreased to 58.89% at the minimum and reached 65.86% at the maximum. Besides, the net selling amount of foreign investors became TRY 215.9 million on average. On the other hand, in Covid-19 pandemic times, the XU100 index is 100,021 on average but it decreased to 84,246 level at the minimum and increased 115,339 at the maximum. Besides, the retention share of foreign investors is 56.57% on average. The share decreased to 52.37% at the minimum and reached 60.73% at the maximum. Besides, the net selling amount of foreign investors is TRY 234.7 million on average. The descriptive statistics show that the figures for XU100, FSHARE, and NETSELL vary for the period whether Turkey is in the Covid-19 pandemic or not.
Table 4 presents the results of the ADF unit root test in both periods.
Period | Variable | ADF Test | |
Level (Prob.) | 1st Difference (Prob.) | ||
Before Covid-19 | XU100 | 0.9562 | 0.0002 |
FSHARE | 0.2782 | 0.0002 | |
NETSELL | 0.0003 | 0.0000 | |
In Covid-19 | XU100 | 0.9449 | 0.0000 |
FSHARE | 0.8625 | 0.0089 | |
NETSELL | 0.0231 | 0.0000 |
Before Covid-19 pandemic times, the probability values of the XU100 index and retention share of foreign investors are greater than 0.05. Therefore, these variables have a unit root and are non-stationary. On the other hand, the first difference of the variables has probability values that are lower than 0.05 meaning that they are stationary. In other words, the null hypothesis of one unit root against the alternative of stationarity cannot be rejected in levels of variables, but is rejected in their first differences, I (1). Therefore, the first differences of these variables are used in the analysis. Moreover, the net selling amount of foreign investors are stationary at levels. The stationarity condition of all variables is the same for in Covid-19 pandemic times.
Considering the stationarity results of the dataset which present that variables are stationary at different levels, it is decided to apply Toda & Yamamoto causality test. Moreover, MARS analysis is performed to examine the consistency of results.
In the context of the Engle-Granger cointegration test, the regression model is applied first and the stationarity of residuals is examined secondly. Table 5 shows the results of the unit root test for residuals for the period which is before the Covid-19 pandemic.
Period | Variable | ADF Test (Prob.) |
Before Covid-19 | XU100 & FSHARE | 0.0002 |
XU100 & NETSELL | 0.0009 | |
Covid-19 | XU100 & FSHARE | 0.0000 |
XU100 & NETSELL | 0.0001 |
As can be seen from Table 4, the probability values of the ADF test for residuals are lower than 0.05 which shows that there is a long-term cointegration between the XU100 index and the retention share of foreign investors. Besides, there is a long-term cointegration between the XU100 index and the net selling amount of foreign investors. Therefore, the XU100 index and retention share of foreign investors are cointegrated and move together in the long-run. Similarly, the XU100 index and net selling amount of foreign investors are cointegrated and moved together in the long-run. These findings are similar for both before the Covid-19 pandemic and in Covid-19 pandemic times.
In the context of the Toda-Yamamoto causality test, maximum cointegration degree (d) and lag lengths (k) are determined firstly and estimation is applied by using "k+dmax" formula. Table 6 shows the results of the lag length determination and maximum cointegration degree.
Period | Variable | Lag Lengths (k) | Maximum Cointegration (dmax) | Estimation Degree (k+dmax) | |
Before Covid-19 | XU100 & FSHARE | 1 | 1 | 2 | |
XU100 & NETSELL | 1 | 0 | 1 | ||
Covid-19 | XU100 & FSHARE | 2 | 1 | 3 | |
XU100 & NETSELL | 2 | 0 | 2 |
By considering the results in Table 5, the estimation degree is determined as 2 for retention share and as 1 for the net selling amount of foreign investors in the period which is before the Covid-19 pandemic. On the other hand, the estimation degree is determined as 3 for retention share and as 2 for net selling amount of foreign investors in the period which is in the Covid-19 pandemic.
Table 7 shows the results of the Toda-Yamamoto causality test.
Period | Variable | Estimation Degree (k+dmax) | Prob. | Result |
Before Covid-19 | FSHARE XU100 | 2 | 0.6940 | No Causality |
NETSELL XU100 | 1 | 0.3609 | No Causality | |
Covid-19 | FSHARE XU100 | 3 | 0.4120 | No Causality |
NETSELL XU100 | 2 | 0.2685 | No Causality |
According to the results in Table 6, there is no causality from the retention share of foreign investors and the net selling amount of foreign investors to the XU100 index in both periods. On the other hand, the probability values of the test imply that there is a nexus from the independent variables to the XU100 index at low confidence intervals. Moreover, the probability values of the test prove that there is an increasing role in the index from before the pandemic to the pandemic period. The results are important because the retention share of foreign investors and the net selling amount of foreign investors could be much more influential on the index when they are evaluated with the other indicators that are included in the analysis.
MARS method creates 4 models and BF1 is determined as the best model based on GCV and R2 statistics for the period which is before Covid-19 pandemic times. Table 8 presents the details of the variables' importance and Table 9 shows the details of the best model.
Variable | Importance Level | −GCV |
FSHARE | 100.000 | 0.248383E+08 |
NETSELL | 0.000 | 0.198267E+08 |
Basis Functions | Details | Coefficient |
Constant | 114,549.0783 | |
BF9 | max(0, FSHARE − 59.550) | 1,856.921 |
F Test: 21.274 (0.000) Adjusted R2: 0.301 |
According to the best model, the most significant variable on the XU100 index is the retention share of foreign investors in time which is before the Covid-19 pandemic.
Adjusted R2 of the best MARS model is 0.301 before Covid-19 pandemic times. These results imply that only the variables used in the analysis, which are retention share and net selling amount of foreign investors, explain 30.1% changes in the XU100 index.
On the other hand, MARS creates 17 models and BF2 is selected as the best model based on GCV and R2 statistics for the period which is in Covid-19 pandemic times. Table 10 presents the details of the variables' importance.
Variable | Importance Level | −GCV |
FSHARE | 100.000 | 0.735352E + 08 |
NETSELL | 45.652 | 0.286564E + 08 |
Also, Table 11 presents the details of the best model.
Basis Functions | Details | Coefficient |
Constant | 103,278.07 | |
BF1 | max(0, FSHARE − 53.780) | - |
BF2 | max(0, 53.780 − FSHARE) | 7,685.579 |
BF3 | max(0, NETSELL + 485.140) * BF1 | −2.215 |
F Test: 150.531 (0.000) Adjusted R2: 0.804 |
According to the best model, the most significant variable on the XU100 index is the retention share of foreign investors at the time of the Covid-19 pandemic. This result is also similar to the before Covid-19 pandemic times. However, there is an important difference that the net selling amount of foreign investors affects the XU100 index in the time of the Covid-19 period. Moreover, MARS determines that there are interactions between FSHARE and NETSELL in the time of the Covid-19 pandemic.
The adjusted R2 of the best MARS model is 0.804 in the time of the Covid-19 pandemic. These results imply that only the variables used in the analysis, which are retention share and net selling amount of foreign investors, explain 80.4% changes in the XU100 index.
In the study, the Engle-Granger cointegration test, Toda-Yamamoto causality test, MARS analysis are performed to examine the changes in the XU100 index by taking into consideration the retention share and net selling amount of foreign investors as independent variables. Engle-Granger cointegration test shows that the XU100 index is cointegrated with retention share and net selling amount of foreign investors in the long-term. However, the Toda-Yamamoto causality test presents that this relationship between the XU100 index and the independent variables is not at the level of causality. Moreover, MARS analysis defines that although the retention share of foreign investors is influential on the XU100 index for the period which is before the Covid-19 pandemic, however, net selling amount of foreign investors is also influential for the period which is in Covid-19 pandemic.
The analysis results define that the XU100 index is affected by the activities of foreign investors before and in Covid-19 pandemic times. The retention share of foreign investors is influential for both periods according to all methods used. This result is consistent with Kartal et al. (2020). Also, the effect of the net selling amount of foreign investors is increased in Covid-19 pandemic times as expected. However, it was not influential on the XU100 index before the Covid-19 pandemic according to the results of MARS. This result is not consistent with Kartal et al. (2020) that who determine that it is effective on the index although its effect is low. Moreover, there is not a causality relationship between the XU100 index and independent variables according to the Toda-Yamamoto causality test. When we evaluate all these results obtained from the test, they imply that although the activities of foreign investors affect the XU100 index, these are not the sole and main determinants of the XU100 index. Therefore, other determinants, which are not included in the study, should be taken into consideration to determine how the XU100 index change over before the pandemic and the pandemic periods.
By taking into consideration the analysis results, it could be recommended that the critical barriers in independent variables should not be exceeded. In other words, the retention share of foreign investors should be kept above 53.78%, and the net selling amount of foreign investors should be kept under the TRY 485 million so as not to cause a decreasing effect on the XU100 index. However, this should be not provided by increasing legal barriers and restricting the elbowroom of foreign investors such as prohibiting the short-selling. Instead, the attention of foreign investors should be increased by applying structural reforms like a positive real interest rate instead of a negative real interest rate and foreign portfolio inflows should be steered up in turn. By considering that Turkey is in time of Covid-19, and Turkey has not the capacity to lower the negative effects of global factors, Turkey could focus on macroeconomic and market variables which are mostly under the control of the country.
Also, other policies could be developed and applied by Turkish regulatory authorities. In such a process, the relationship between variables should be considered as MARS analysis shows because there is an interaction between the retention share and net selling amount of foreign investors. Therefore, the outcomes of measures to be taken on XU100 should be predicted before implementation.
The study examines the effects of foreign investors' activities on the main stock exchange indices by using Turkey's data before and in the time of the Covid-19 Pandemic. That is why because emerging countries need foreign financing sources, foreign portfolio investments have significance for these countries, equity investments are one of the important foreign portfolio investment tools to be used, and there is a Covid-19 pandemic since 03.10.2020 in Turkey. In this context, the XU100 index as a dependent variable, and retention share and net selling amount of foreign investors as independent variables are used, presence of Covid-19 pandemic is considered, and daily data between 01.02.2020 and 06.26.2020 (including 122 observations) is analyzed with performing Engle-Granger cointegration test, Toda-Yamamoto causality test, and MARS analysis.
As a result of the analysis, the findings reveal that the effects of retention share and net selling amount of foreign investors on the XU100 index vary according to period whether Turkey is in Covid-19 time or not according to the results of MARS. Besides, the power of effects varies according to period. Moreover, the results imply that the Covid-19 pandemic causes the increasing effect of the net selling amount of foreign investors on the XU100 index. On the other hand, there is not a relationship between the index and independent variables at the causality level which is surprising because it is expected that there could be a relationship at the causality level which reflecting a strong effect. Turkey could decrease the outflows of foreign investments from the stock exchange and prevent the underpricing of assets in turn.
In the study, Turkey is examined because there is quite volatile behavior in the XU100 index, retention share, and net selling amount, especially during the Covid-19 pandemic. By taking measures to decrease the negative effects, Turkey could attract more foreign portfolio investments. Also, additional analysis for Turkey at the end of the Covid-19 pandemic would contribute to the literature, and new policy proposals could be recommended based on the results of forthcoming studies. On the other hand, including different country groups like Venezuela, Argentina, Ukraine, which have some problems in terms of foreign investments, could help extend current literature. Similar results are expected for these countries and other emerging countries as well. On the other hand, the cointegration between the variables could be at the causality level which reflects that those countries are much more dependent on foreign portfolio inflows. Moreover, new variables could be included in the new analysis, and other methods like machine learning algorithms, neural networks, threshold cointegration model, and wavelet coherence approach could be applied in forthcoming studies.
The author declares no conflicts of interest in this paper.
[1] | Smith CS (1960) A History of Metallography, University of Chicago Press. |
[2] |
Fielding L (2013) The bainite controversy. Mater Sci Techn 29:383–399. doi: 10.1179/1743284712Y.0000000157
![]() |
[3] |
van Bohemen S, Siemtsma J (2008) Modeling of isothermal bainite formation based on nucleation kinetics. Int J Mat Res 99:739–747. doi: 10.3139/146.101695
![]() |
[4] |
Gaude-Fugarolas D, Jacques PJ (2006) A new physical model for the kinetics of the bainite transformation. ISIJ Inter 46:712–717. doi: 10.2355/isijinternational.46.712
![]() |
[5] |
Rees GI, Bhadeshia H (1992) Bainite transformation kinetics Part 1: Modified model. Mater Sci Techn 8:985–993. doi: 10.1179/mst.1992.8.11.985
![]() |
[6] |
Tzeng TC (2000) Autocatalysis in bainite transformations. Mater Sci Eng A 293:185–190. doi: 10.1016/S0921-5093(00)01221-1
![]() |
[7] |
Zolotoresvky N, Nesterova E, Titovets Y, et al. (2013) Modeling the effect of austenite deformation on the bainite structure parameters in low carbon microalloyed steels. Int J Mat Res 104:337–343. doi: 10.3139/146.110872
![]() |
[8] | Hunkel M, Lübben T, Hoffmann F, et al. (1999) Modellierung der bainitischen und perlitischen Umwandlung bei Stählen. HTM Härterei-Techn Mitt 54:365–373. |
[9] | Quidort D, Brechet YJM (2002) A model of isothermal and non isothermal transformation kinetics of bainite in 0.5% C steels. ISIJ Inter 42:1010–1017. |
[10] |
Maier H-J, Ahrens U (2002) Isothermal bainitic transformation on low alloy steels: factors limiting prediction of the resulting material’s properties. Z Metallk 93:712–718. doi: 10.3139/146.020712
![]() |
[11] |
Freiwillig R, Kudrman J, Chraska P (1976) Bainite transformation in deformed austenite. Metall Trans A 7:1091–1097. doi: 10.1007/BF02656591
![]() |
[12] |
Holzweissig M, Canadinc D, Maier H-J (2012) In-situ characterization of transformation plasticity during an isothermal austenite-to-bainite phase transformation. Mater Char 65:100–108. doi: 10.1016/j.matchar.2012.01.007
![]() |
[13] |
Su T, Veaus M, Aeby-Gautier E, et al. (2003) Effect of tensile stresses on bainitic isothermal transformation. J Phys IV France 112:293–296. doi: 10.1051/jp4:2003886
![]() |
[14] |
Su T, Aeby-Gautier E, Denis S (2006) Morphology changes in bainite formed under stress. Scripta Mater 54:2185–2189. doi: 10.1016/j.scriptamat.2006.02.031
![]() |
[15] |
Hase K, Garcia-Mateo C, Bhadeshia H (2004) Bainite Formation influenced by large stress. Mater Sci Techn 20:1499–1505. doi: 10.1179/026708304X6130
![]() |
[16] |
Kundu S, Hase K, Bhadeshia S (2007) Crystallographic texture of stress affected bainite. Proc Royal Soc A 463:2309–2328. doi: 10.1098/rspa.2007.1881
![]() |
[17] | Fuijiwara K, Okaguchi S, Ohtani H (1995) Effect of hot deformation on bainite structure in low carbon steels. ISIJ Inter 15:1006–1012. |
[18] |
Min J, Lin J, Min Y, et al. (2012) On the ferrite and bainite transformation in isothermally deformed 22MnB5 steels. Mater Sci Eng A 550:375–387. doi: 10.1016/j.msea.2012.04.091
![]() |
[19] |
Nikravesh M, Naderi M, Akbari GH (2012) Influence of hot plastic deformation and cooling rate on martensite and bainite start temperatures in 22MnB5 steel. Mater Sci Eng A A 540:24–29. doi: 10.1016/j.msea.2012.01.018
![]() |
[20] |
Karbasian H, Tekkaya AE (2010) A review on hot stamping. J Mat Proc Tech 210:2103. doi: 10.1016/j.jmatprotec.2010.07.019
![]() |
[21] | Feuser P, Schweiker T, Merklein M (2011) Partially hot-formed parts from 22MnB5 - process window. ICTP Aachen 10:408. |
[22] |
Chen L (2002) Phase fields models for microstructure evolution. Annu Rev Mater Res 32:113. doi: 10.1146/annurev.matsci.32.112001.132041
![]() |
[23] |
Wang Y, Jin YM, Khachaturyan AG (2004) The effects of free surfaces on martensite microstructures: 3D phase field microelasticity simulation study. Acta Mat 52:1039. doi: 10.1016/j.actamat.2003.10.037
![]() |
[24] | Micress microstructure evolution simulation software, www.micress.de. |
[25] |
Loginova I, Agren J, Amberg G (2004) On the formation ofWidmanstätten ferrite in a binary Fe-C phase-field approach. Acta Materialia 52:4055–4063. doi: 10.1016/j.actamat.2004.05.033
![]() |
[26] | Song W, Prahl U, Bleck W, et al. (2011) Phase field simulations of bainitic phase transformation in 100Cr6. Supplemental proceedings: Materials Fabrication, Properties, Characterization, and Modeling 2:417–425. |
[27] | Song W (2014) Characterization and simulation of bainite transformation in high carbon bearing steel 100Cr6, PhD thesis RWTH Aachen University. |
[28] |
Arif T, Qin R (2013) A phase field model for bainitic transformation. Computational Materials Science 77:230–235. doi: 10.1016/j.commatsci.2013.04.044
![]() |
[29] |
Arif T, Qin R (2014) A phase field model for the formation of martensite and bainite. Advanced materials research 922:31–36. doi: 10.4028/www.scientific.net/AMR.922.31
![]() |
[30] |
Qin R, Bhadeshia H (2009) Phase field model to study the effect of interface anisotropy on the crystal morphological evolution of cubic metals. Acta Materialia 57:2210–2216. doi: 10.1016/j.actamat.2009.01.024
![]() |
[31] | Bhadeshia H (1987)Worked examples in the geometry of crystals, Institute of metals, London and Brookfield. |
[32] |
Bouville M, Ahluwalia R (2006) Interplay between diffusive and displacive phase transformations: Time-Temperature-Transformation diagrams and microstructures. Phys Rev Lett 97:055701. doi: 10.1103/PhysRevLett.97.055701
![]() |
[33] |
Kundin J, Raabe D, Emmerich H (2011) A phase field model for incoherent martensitic transformations including plastic accommodation processes in the austenite. Journal of the mechanics and physics of solids 59:2082–2102. doi: 10.1016/j.jmps.2011.07.001
![]() |
[34] |
Kundin J, Pogorelov E, Emmerich H (2015) Numerical investigation of the interaction between the martensitic transformation front and the plastic strain in austenite. Journal of the mechanics and physics of solids 76:65–83. doi: 10.1016/j.jmps.2014.12.007
![]() |
[35] |
Levitas V, Javanbakht M (2013) Phase field approach to interaction of phase transformation and dislocation evolution. Applied Physics Letters 102:251904. doi: 10.1063/1.4812488
![]() |
[36] | Roters F, Eisenlohr P, Hantcherli L, et al. (2010) Overview of constitutive laws, kinematics, homogenization and multiscale methods in crystal plasticity finite element modeling: Theory, experiments, applications. Acta Materialia 58:2210–2216. |
[37] | Johnson W, Mehl R (1939) Reaction kinetics in process of nucleation and growth. Trans AIME 135:416–458. |
[38] |
Avrami M (1941) Kinetics of phase change III: granulation, phase change and microstructure. J Chem Phys 9:177–184. doi: 10.1063/1.1750872
![]() |
[39] | Lee G, Kim S, Han H (2009) Finite element investigations for the role of transformation plasticity on springback in hot press forming process. Comp Mater Sci 47:556567. |
[40] | HunkelM(2012) Anisotropic transformation strain and transformation plasticity: two corresponding effects. Mat -wiss u Werkstofftech. 43:150–157. |
[41] | Lütjens J, Hunkel M (2013) The influence of the transformation plasticity effect on the simulation of partial press-hardening. Proc 4th Int Conf CHS2 319–327. |
[42] |
Brener EA, Marchenko VI, Spatschek R (2007) Influence of strain on the kinetics of phase transitions in solids. Phys Rev E 75:041604. doi: 10.1103/PhysRevE.75.041604
![]() |
[43] |
Fratzl P, Penrose O, Lebowitz JL (1999) Modelling of Phase Separation in Alloys with Coherent Elastic Misfit. J Stat Phys 95:1429. doi: 10.1023/A:1004587425006
![]() |
[44] | Freund L (1998) Dynamic fracture mechanics, Cambridge University Press. |
[45] |
Spatschek R, Brener E, Karma A (2011) Phase field modeling of crack propagation. Phil Mag 91:75. doi: 10.1080/14786431003773015
![]() |
[46] |
Chien FR, Clifton RJ, Nutt SR (1995) Stress-induced phase transformation in single crystal titanium carbide. J Am Ceram Soc 78:1537. doi: 10.1111/j.1151-2916.1995.tb08849.x
![]() |
[47] |
Spatschek R, Müller-Gugenberger C, Brener E A, et al. (2007) Phase field modelling of fracture and stress-induced phase transitions. Phys Rev E 75:066111. doi: 10.1103/PhysRevE.75.066111
![]() |
[48] |
Spatschek R, Eidel B (2013) Driving forces for interface kinetics and phase field models. Int J Solid and Structures 50:2424. doi: 10.1016/j.ijsolstr.2013.03.016
![]() |
[49] | Steinbach I (2011) Phase field models in materials science. Modelling and Simulation in Materials Science and Engineering 17:073001. |
[50] |
Steinbach I, Shchyglo O (2011) Phase field modelling of microstructure evolution in solids: Perspectives and challenges. Current opinion in solid state and materials science 15:87. doi: 10.1016/j.cossms.2011.01.001
![]() |
[51] |
Rao M, Sengupta S (2003) Nucleation of solids in solids: ferrite and martensite. Phys Rev Lett 91:045502. doi: 10.1103/PhysRevLett.91.045502
![]() |
[52] |
Brener EA, Iiordanskii SV, Marchenko VI (1999) Elastic effects on the kinetics of a phase transition. Phys Rev Lett 82:1506. doi: 10.1103/PhysRevLett.82.1506
![]() |
[53] |
Brener EA, Boussinot G, Hüter C, et al. (2009) Pattern formation during diffusional transformations in the presence of triple junctions and elastic effects. J Phys Cond Mat 21:464106. doi: 10.1088/0953-8984/21/46/464106
![]() |
[54] |
Pilipenko D, Brener EA, Hüter C (2008) Theory of dendritic growth in the presence of lattice strain. Phys Rev E 78:060603. doi: 10.1103/PhysRevE.78.060603
![]() |
[55] | Ivantsov GP (1947) PhD thesis Akad. Nauk. SSSR. |
[56] |
Steinbach I, Pezzolla F (1999) A generalized field method for multiphase transformations using interface fields. Physica D: Nonlinear Phenomena 134:385–393. doi: 10.1016/S0167-2789(99)00129-3
![]() |
[57] | Song W, von Appen J, Choi P, et al. (2013) Atomic-scale investigation of epsilon and theta precipitates in bainite in 100Cr6 bearing steel by atom probe tomography and ab initio calculations. Acta Materialia 61(20):7582–7590. |
[58] |
Eiken J, Boettger B, Steinbach I (2006) Multi-phase-field approach for multi-component alloys with extrapolation scheme for numerical application. Phys Rev E 73:066122. doi: 10.1103/PhysRevE.73.066122
![]() |
[59] | Steinbach I, Pezzolla F, Prieler R (1995) Grain selection in faceted crystal growth using the phase field theory. In: The 7th conference on on modeling of casting, welding and advanced solidification processes. |
[60] | Lukas H, Fries S, Sundman B (2007) Computational thermodynamics: The CALPHAD method, Cambridge University Press. |
[61] |
Rees GI, Shipway PH (1997) Modelling transformation plasticity during the growth of bainite under stress. Materials Science and Engineering A 223:168–178. doi: 10.1016/S0921-5093(96)10478-0
![]() |
[62] | Wolff M, Böhm M, Dalgic M, et al. (2008) Evaluation of models for TRIP and stress-dependent transformation behavior for the martensitic transformation of the steel 100Cr6. Comput Mater Sci 43:108114. |
[63] | Denis S (1997) Considering stress-phase transformation interaction in the calculation of heat treatment residual stresses. Series: International Centre for Mechanical Sciences 368:293–317. |
[64] |
Leblond J, Deveaux JC (1989) Mathematical modelling of transformation plasticity in steels I: Case of ideal-plastic phases. Int J Plasticity 5:551–572. doi: 10.1016/0749-6419(89)90001-6
![]() |
[65] | Fisher FD, Sun QP, Tanaka K (1996) Transformation-induced plasticity. Appl Mech Rev 49:317364. |
[66] | Leblond JB, Deveaux J (1984) A new kinetic model for anisothermal metallurgical transformation in steels including effect of austenite grain size. Acta Metallurgica 32:137146. |
[67] | ASTM International standard test methods for tension testing of metallic materials (2011). Available from: www.astm.org. |
[68] | HunkelM(2009) Anisotropic transformation strain and transformation plasticity: two corresponding effects. Mat -wiss u Werkstofftech. 40(5-6):466–472. |
[69] | Devaux J, Leblond JB, Bergheau JM (2000) Numerical study of the plastic behaviour of a low alloy steel during phase transformation. Journal of Shanghai Jiaotong University 3:206–212. |
[70] | Zwigl P, Dunand DC (1997) A non-linear model for internal stress superplasticity. Acta Materialia 45(12):5285–5294. |
[71] | Schicchi DS, Hunkel M (2015) Transformation plasticity effect during bainite transformation on a 22MnB5 Steel Grade. IDE 2015, Bremen, Germany. |
1. | Mustafa Tevfik KARTAL, Özer DEPREN, Serpil KILIÇ DEPREN, The relationship between mobility and COVID-19 pandemic: Daily evidence from an emerging country by causality analysis, 2021, 10, 25901982, 100366, 10.1016/j.trip.2021.100366 | |
2. | Mustafa Tevfik Kartal, Hasan Murat Ertuğrul, Talat Ulussever, The impacts of foreign portfolio flows and monetary policy responses on stock markets by considering COVID-19 pandemic: Evidence from Turkey, 2022, 22, 22148450, 12, 10.1016/j.bir.2021.06.003 | |
3. | Mohammed H. Alamoudi, Omer A. Bafail, BWM—RAPS Approach for Evaluating and Ranking Banking Sector Companies Based on Their Financial Indicators in the Saudi Stock Market, 2022, 15, 1911-8074, 467, 10.3390/jrfm15100467 | |
4. | Tomiwa Sunday Adebayo, Mustafa Tevfik Kartal, Effect of green bonds, oil prices, and COVID-19 on industrial CO2 emissions in the USA: Evidence from novel wavelet local multiple correlation approach, 2023, 0958-305X, 0958305X2311674, 10.1177/0958305X231167463 | |
5. | Herry Subagyo, Hersugondo Hersugondo, Wijaya Marcellino Candra, Kardison Lumban Batu, Dwi Eko Waluyo, Foreign investor portfolio flow and monetary policy response in the Indonesian stock market considering the COVID-19 pandemic, 2024, 21, 18104967, 88, 10.21511/imfi.21(1).2024.08 | |
6. | Abdulrahman T. Alsanousi, Ammar Y. Alqahtani, Anas A. Makki, Majed A. Baghdadi, A Hybrid MCDM Approach Using the BWM and the TOPSIS for a Financial Performance-Based Evaluation of Saudi Stocks, 2024, 15, 2078-2489, 258, 10.3390/info15050258 | |
7. | Mustafa Tevfik Kartal, Talat Ulussever, Ugur Korkut Pata, Serpil Kılıç Depren, Dynamic link between central bank reserves, credit default swap spreads, and foreign exchange rates: Evidence from Turkey by time series econometrics, 2023, 9, 24058440, e16392, 10.1016/j.heliyon.2023.e16392 |
Authors | Year | Scope | Period | Method | Results |
Clark & Berko | 1997 | Mexico | 1989/1–1996/3 | Regression | The increase in FPI causes an increase in stock prices. |
Bekaert & Harvey | 1998 | 17 Emerging Countries | 1977–1996 | GARCH | Increasing flows have a high correlation with returns. |
Dahlquist & Robertsson | 2004 | Sweden | 1993–1998 | VAR | Net purchases of foreign investors provide a permanent increase of stock prices. |
Baklacı | 2007 | Turkey | 1997/1–2006/4 | Granger causality & OLS | There is a significant bilateral interaction between FPI and stock returns. |
Boyer & Zheng | 2009 | United States | 1952–2004 | VAR & Regression | There is a significant positive relation between stock market returns and flows of foreign investors. |
Sevil et al. | 2012 | Turkey | 2006/1–2010/4 | VECM & Granger causality | There is causality from foreign investors to market index return. |
Vo | 2015 | Vietnam | 2006/2012 | GMM & Regression | Ownership of foreign investors decreases firm stock price volatility. |
Kesik et al. | 2016 | Turkey | 2005/2015 | Granger causality | FPI have an increasing impact on XU100 index. |
Liew et al. | 2018 | Malaysia | 2009/1–2016/12 | VAR & Granger causality | There is a one-way causality from gross inflows. |
Topaloğlu et al. | 2019 | 7 Emerging Countries | 2005–2016 | Panel data analysis | There is a significant and positive nexus between FPI and stock market returns. |
Angelovska | 2020 | Macedonia | 2005/1–2009/12 | Regression | Net inflows are connected with the rise of returns. |
David et al. | 2020 | 11 Countries | 79 Trading Days | Threshold cointegration | Shocks caused by diseases have an important effect on stock indices. |
Gupta & Ahmet | 2020 | India | 2002/1–2016/12 | ARDL | The performance of stock exchanges is one of the most important factors for FPI. |
Kartal et al. | 2020 | Turkey | 2020/1–2020/5 | Machine learning | The retention amount of foreign investors is influential in both the pre-pandemic and the pandemic periods. |
Kotishwar | 2020 | India | 2000/1–2019/12 | ARCH & OLS | FPI influence equity market volatility. |
Note: ARCH = Auto regressive conditional heteroscedasticity; ARDL = Autoregressive distributed lag; FPI = Foreign portfolio inflows; GARCH = Generalized autoregressive conditional heteroscedasticity; GMM = Generalized method of moments; OLS = Ordinary Least Squares; VAR = Vector autoregression; VECM = Vector error correction model. |
Variable | Symbol | Description | Effect | |
Type | Name | |||
Dependent | Main index | XU100 | The daily closing value of the BIST main index | |
Independent | Retention share | FSHARE | Daily retention share of foreign investors in BIST (%) | + |
Net selling | NETSELL | Daily net selling amount of foreign investors in BIST (TRY denominated amount) | - | |
Covid-19 | COVID | 1: If Covid-19 exists, 0: otherwise | - | |
Note: A positive (+) relationship means that XU100 increases when the independent variable increases. A negative (-) relationship means that XU100 decreases when the independent variable increases. |
Period Variable | Before Covid-19 | Covid-19 | |||||
XU1001 | FSHARE2 | NETSELL3 | XU1001 | FSHARE2 | NETSELL3 | ||
Mean | 117,361.9 | 61.01856 | 215.9715 | 100,021.8 | 56.56831 | 234.6904 | |
Median | 119,408.5 | 60.73146 | 258.8678 | 99,069.46 | 57.31724 | 278.9121 | |
Maximum | 123,556.1 | 65.85941 | 786.5698 | 115,338.9 | 60.72814 | 1109.929 | |
Minimum | 103,524.0 | 58.88518 | −1029.742 | 84,246.17 | 52.37000 | -485.1429 | |
Std. Dev. | 4,931.612 | 1.547033 | 324.5663 | 85, 17.130 | 2.988219 | 263.4816 | |
Skewness | -0.982580 | 1.401699 | -1.151931 | 0.041302 | -0.114845 | -0.297241 | |
Kurtosis | 3.089060 | 5.100109 | 5.810881 | 2.087917 | 1.440857 | 4.418486 | |
Jarque-Bera | 7.739573 | 24.53900 | 26.41767 | 2.586051 | 7.658022 | 7.293661 | |
Probability | 0.020863 | 0.000005 | 0.000002 | 0.274439 | 0.021731 | 0.026074 | |
Observations | 48 | 48 | 48 | 74 | 74 | 74 | |
Note: 1 The dependent variable; 2 %; 3 million TRY. |
Period | Variable | ADF Test | |
Level (Prob.) | 1st Difference (Prob.) | ||
Before Covid-19 | XU100 | 0.9562 | 0.0002 |
FSHARE | 0.2782 | 0.0002 | |
NETSELL | 0.0003 | 0.0000 | |
In Covid-19 | XU100 | 0.9449 | 0.0000 |
FSHARE | 0.8625 | 0.0089 | |
NETSELL | 0.0231 | 0.0000 |
Period | Variable | ADF Test (Prob.) |
Before Covid-19 | XU100 & FSHARE | 0.0002 |
XU100 & NETSELL | 0.0009 | |
Covid-19 | XU100 & FSHARE | 0.0000 |
XU100 & NETSELL | 0.0001 |
Period | Variable | Lag Lengths (k) | Maximum Cointegration (dmax) | Estimation Degree (k+dmax) | |
Before Covid-19 | XU100 & FSHARE | 1 | 1 | 2 | |
XU100 & NETSELL | 1 | 0 | 1 | ||
Covid-19 | XU100 & FSHARE | 2 | 1 | 3 | |
XU100 & NETSELL | 2 | 0 | 2 |
Period | Variable | Estimation Degree (k+dmax) | Prob. | Result |
Before Covid-19 | FSHARE XU100 | 2 | 0.6940 | No Causality |
NETSELL XU100 | 1 | 0.3609 | No Causality | |
Covid-19 | FSHARE XU100 | 3 | 0.4120 | No Causality |
NETSELL XU100 | 2 | 0.2685 | No Causality |
Variable | Importance Level | −GCV |
FSHARE | 100.000 | 0.248383E+08 |
NETSELL | 0.000 | 0.198267E+08 |
Basis Functions | Details | Coefficient |
Constant | 114,549.0783 | |
BF9 | max(0, FSHARE − 59.550) | 1,856.921 |
F Test: 21.274 (0.000) Adjusted R2: 0.301 |
Variable | Importance Level | −GCV |
FSHARE | 100.000 | 0.735352E + 08 |
NETSELL | 45.652 | 0.286564E + 08 |
Basis Functions | Details | Coefficient |
Constant | 103,278.07 | |
BF1 | max(0, FSHARE − 53.780) | - |
BF2 | max(0, 53.780 − FSHARE) | 7,685.579 |
BF3 | max(0, NETSELL + 485.140) * BF1 | −2.215 |
F Test: 150.531 (0.000) Adjusted R2: 0.804 |
Authors | Year | Scope | Period | Method | Results |
Clark & Berko | 1997 | Mexico | 1989/1–1996/3 | Regression | The increase in FPI causes an increase in stock prices. |
Bekaert & Harvey | 1998 | 17 Emerging Countries | 1977–1996 | GARCH | Increasing flows have a high correlation with returns. |
Dahlquist & Robertsson | 2004 | Sweden | 1993–1998 | VAR | Net purchases of foreign investors provide a permanent increase of stock prices. |
Baklacı | 2007 | Turkey | 1997/1–2006/4 | Granger causality & OLS | There is a significant bilateral interaction between FPI and stock returns. |
Boyer & Zheng | 2009 | United States | 1952–2004 | VAR & Regression | There is a significant positive relation between stock market returns and flows of foreign investors. |
Sevil et al. | 2012 | Turkey | 2006/1–2010/4 | VECM & Granger causality | There is causality from foreign investors to market index return. |
Vo | 2015 | Vietnam | 2006/2012 | GMM & Regression | Ownership of foreign investors decreases firm stock price volatility. |
Kesik et al. | 2016 | Turkey | 2005/2015 | Granger causality | FPI have an increasing impact on XU100 index. |
Liew et al. | 2018 | Malaysia | 2009/1–2016/12 | VAR & Granger causality | There is a one-way causality from gross inflows. |
Topaloğlu et al. | 2019 | 7 Emerging Countries | 2005–2016 | Panel data analysis | There is a significant and positive nexus between FPI and stock market returns. |
Angelovska | 2020 | Macedonia | 2005/1–2009/12 | Regression | Net inflows are connected with the rise of returns. |
David et al. | 2020 | 11 Countries | 79 Trading Days | Threshold cointegration | Shocks caused by diseases have an important effect on stock indices. |
Gupta & Ahmet | 2020 | India | 2002/1–2016/12 | ARDL | The performance of stock exchanges is one of the most important factors for FPI. |
Kartal et al. | 2020 | Turkey | 2020/1–2020/5 | Machine learning | The retention amount of foreign investors is influential in both the pre-pandemic and the pandemic periods. |
Kotishwar | 2020 | India | 2000/1–2019/12 | ARCH & OLS | FPI influence equity market volatility. |
Note: ARCH = Auto regressive conditional heteroscedasticity; ARDL = Autoregressive distributed lag; FPI = Foreign portfolio inflows; GARCH = Generalized autoregressive conditional heteroscedasticity; GMM = Generalized method of moments; OLS = Ordinary Least Squares; VAR = Vector autoregression; VECM = Vector error correction model. |
Variable | Symbol | Description | Effect | |
Type | Name | |||
Dependent | Main index | XU100 | The daily closing value of the BIST main index | |
Independent | Retention share | FSHARE | Daily retention share of foreign investors in BIST (%) | + |
Net selling | NETSELL | Daily net selling amount of foreign investors in BIST (TRY denominated amount) | - | |
Covid-19 | COVID | 1: If Covid-19 exists, 0: otherwise | - | |
Note: A positive (+) relationship means that XU100 increases when the independent variable increases. A negative (-) relationship means that XU100 decreases when the independent variable increases. |
Period Variable | Before Covid-19 | Covid-19 | |||||
XU1001 | FSHARE2 | NETSELL3 | XU1001 | FSHARE2 | NETSELL3 | ||
Mean | 117,361.9 | 61.01856 | 215.9715 | 100,021.8 | 56.56831 | 234.6904 | |
Median | 119,408.5 | 60.73146 | 258.8678 | 99,069.46 | 57.31724 | 278.9121 | |
Maximum | 123,556.1 | 65.85941 | 786.5698 | 115,338.9 | 60.72814 | 1109.929 | |
Minimum | 103,524.0 | 58.88518 | −1029.742 | 84,246.17 | 52.37000 | -485.1429 | |
Std. Dev. | 4,931.612 | 1.547033 | 324.5663 | 85, 17.130 | 2.988219 | 263.4816 | |
Skewness | -0.982580 | 1.401699 | -1.151931 | 0.041302 | -0.114845 | -0.297241 | |
Kurtosis | 3.089060 | 5.100109 | 5.810881 | 2.087917 | 1.440857 | 4.418486 | |
Jarque-Bera | 7.739573 | 24.53900 | 26.41767 | 2.586051 | 7.658022 | 7.293661 | |
Probability | 0.020863 | 0.000005 | 0.000002 | 0.274439 | 0.021731 | 0.026074 | |
Observations | 48 | 48 | 48 | 74 | 74 | 74 | |
Note: 1 The dependent variable; 2 %; 3 million TRY. |
Period | Variable | ADF Test | |
Level (Prob.) | 1st Difference (Prob.) | ||
Before Covid-19 | XU100 | 0.9562 | 0.0002 |
FSHARE | 0.2782 | 0.0002 | |
NETSELL | 0.0003 | 0.0000 | |
In Covid-19 | XU100 | 0.9449 | 0.0000 |
FSHARE | 0.8625 | 0.0089 | |
NETSELL | 0.0231 | 0.0000 |
Period | Variable | ADF Test (Prob.) |
Before Covid-19 | XU100 & FSHARE | 0.0002 |
XU100 & NETSELL | 0.0009 | |
Covid-19 | XU100 & FSHARE | 0.0000 |
XU100 & NETSELL | 0.0001 |
Period | Variable | Lag Lengths (k) | Maximum Cointegration (dmax) | Estimation Degree (k+dmax) | |
Before Covid-19 | XU100 & FSHARE | 1 | 1 | 2 | |
XU100 & NETSELL | 1 | 0 | 1 | ||
Covid-19 | XU100 & FSHARE | 2 | 1 | 3 | |
XU100 & NETSELL | 2 | 0 | 2 |
Period | Variable | Estimation Degree (k+dmax) | Prob. | Result |
Before Covid-19 | FSHARE XU100 | 2 | 0.6940 | No Causality |
NETSELL XU100 | 1 | 0.3609 | No Causality | |
Covid-19 | FSHARE XU100 | 3 | 0.4120 | No Causality |
NETSELL XU100 | 2 | 0.2685 | No Causality |
Variable | Importance Level | −GCV |
FSHARE | 100.000 | 0.248383E+08 |
NETSELL | 0.000 | 0.198267E+08 |
Basis Functions | Details | Coefficient |
Constant | 114,549.0783 | |
BF9 | max(0, FSHARE − 59.550) | 1,856.921 |
F Test: 21.274 (0.000) Adjusted R2: 0.301 |
Variable | Importance Level | −GCV |
FSHARE | 100.000 | 0.735352E + 08 |
NETSELL | 45.652 | 0.286564E + 08 |
Basis Functions | Details | Coefficient |
Constant | 103,278.07 | |
BF1 | max(0, FSHARE − 53.780) | - |
BF2 | max(0, 53.780 − FSHARE) | 7,685.579 |
BF3 | max(0, NETSELL + 485.140) * BF1 | −2.215 |
F Test: 150.531 (0.000) Adjusted R2: 0.804 |