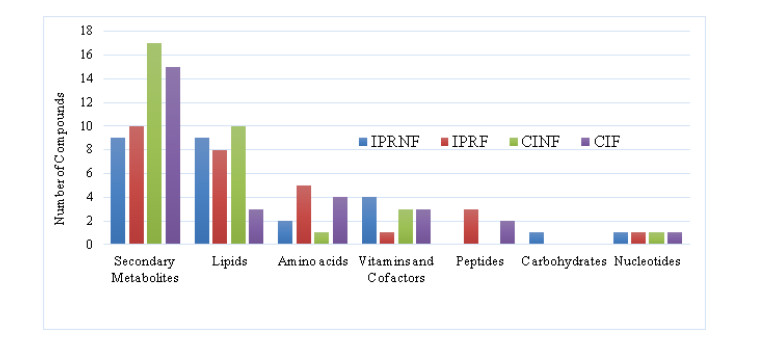
This paper studies the integration of flywheel energy storage system (FESS) to a synchronous condenser (SC) and its effect on the stability margin of the power system. To show the applicability of FESS-integrated SC in mitigating sudden power loss and sudden load implementation, the experimental and simulation results are presented.
Citation: Parveen Tania, Sanjari Mohammad J., Arace Luke. Inertia compensation of power grid with flywheel-integrated synchronous condenser[J]. AIMS Energy, 2023, 11(3): 404-422. doi: 10.3934/energy.2023021
[1] | Aliou Badara Kouyate, Vincent Logah, Robert Clement Abaidoo, Francis Marthy Tetteh, Mensah Bonsu, Sidiki Gabriel Dembélé . Phosphorus sorption characteristics in the Sahel: Estimates from soils in Mali. AIMS Agriculture and Food, 2023, 8(4): 995-1009. doi: 10.3934/agrfood.2023053 |
[2] | Syajariah Sanusi, Huck Ywih Ch’ng, Suhaimi Othman . Effects of incubation period and Christmas Island rock phosphate with different rate of rice straw compost on phosphorus availability in acid soil. AIMS Agriculture and Food, 2018, 3(4): 384-396. doi: 10.3934/agrfood.2018.4.384 |
[3] | Zhi Yuan Sia, Huck Ywih Ch'ng, Jeng Young Liew . Amending inorganic fertilizers with rice straw compost to improve soil nutrients availability, nutrients uptake, and dry matter production of maize (Zea mays L.) cultivated on a tropical acid soil. AIMS Agriculture and Food, 2019, 4(4): 1020-1033. doi: 10.3934/agrfood.2019.4.1020 |
[4] | Dhanya Praveen, Ramachandran Andimuthu, K. Palanivelu . The urgent call for land degradation vulnerability assessment for conserving land quality in the purview of climate change: Perspective from South Indian Coast. AIMS Agriculture and Food, 2016, 1(3): 330-341. doi: 10.3934/agrfood.2016.3.330 |
[5] | Nicholas Mawira Gitonga, Gilbert Koskey, Ezekiel Mugendi Njeru, John M. Maingi, Richard Cheruiyot . Dual inoculation of soybean with Rhizophagus irregularis and commercial Bradyrhizobium japonicum increases nitrogen fixation and growth in organic and conventional soils. AIMS Agriculture and Food, 2021, 6(2): 478-495. doi: 10.3934/agrfood.2021028 |
[6] | Apori Samuel Obeng, Adams Sadick, Emmanuel Hanyabui, Mohammed Musah, Murongo Marius, Mark Kwasi Acheampong . Evaluation of soil fertility status in oil palm plantations in the Western Region of Ghana. AIMS Agriculture and Food, 2020, 5(4): 938-949. doi: 10.3934/agrfood.2020.4.938 |
[7] | Janice Liang, Travis Reynolds, Alemayehu Wassie, Cathy Collins, Atalel Wubalem . Effects of exotic Eucalyptus spp. plantations on soil properties in and around sacred natural sites in the northern Ethiopian Highlands. AIMS Agriculture and Food, 2016, 1(2): 175-193. doi: 10.3934/agrfood.2016.2.175 |
[8] | Muhammad Rendana, Wan Mohd Razi Idris, Sahibin Abdul Rahim, Zulfahmi Ali Rahman, Tukimat Lihan, Habibah Jamil . Reclamation of acid sulphate soils in paddy cultivation area with organic amendments. AIMS Agriculture and Food, 2018, 3(3): 358-371. doi: 10.3934/agrfood.2018.3.358 |
[9] | Widowati, Sutoyo, Hidayati Karamina, Wahyu Fikrinda . Soil amendment impact to soil organic matter and physical properties on the three soil types after second corn cultivation. AIMS Agriculture and Food, 2020, 5(1): 150-168. doi: 10.3934/agrfood.2020.1.150 |
[10] | Gunavathy Selvarajh, Huck Ywih Ch'ng, Norhafizah Md Zain . Effects of rice husk biochar in minimizing ammonia volatilization from urea fertilizer applied under waterlogged condition. AIMS Agriculture and Food, 2021, 6(1): 159-171. doi: 10.3934/agrfood.2021010 |
This paper studies the integration of flywheel energy storage system (FESS) to a synchronous condenser (SC) and its effect on the stability margin of the power system. To show the applicability of FESS-integrated SC in mitigating sudden power loss and sudden load implementation, the experimental and simulation results are presented.
Rice is a staple food in Indonesia, which is one of the largest rice producers in the world. According to BPS-Statistics Indonesia, rice production touched 54.60 million tons in 2019 [1]. Polished rice is the primary product of rice, of which rice bran is the main by-product, followed by rice husk and germ. Rice bran consists of 8-12 percent of the by-product from the rice milling process [2].
Rice bran is used mainly as animal feed in Indonesia. There are not many studies on bioactivity, especially using animal model of diseases. Several studies show the potency of rice bran as food, especially as a functional ingredient, due to its beneficial bioactive compound content. The active bioactive compounds of rice bran are γ-oryzanol, polyphenols, phytosterols, tocopherols, tocotrienols, adenosine, ferulic acid, and adenosine, which can function as antioxidants and chemopreventive agents, with properties of lowering blood pressure and regulating cholesterol synthesis [3,4,5,6] Further, in some pigmented rice cultivars, rice bran is the part where the pigment is concentrated. The well-known pigmented rice in Indonesia is black rice. Black rice bran has a higher total phenolic content (TPC), anthocyanins, flavonoids, and antioxidant activity than polished red and white rice bran [7].
Solid-state fermentation (SSF) is known to enhance the bioactive compounds of rice bran [8]. This method uses solid media for microbial growth. The advantages of SSF are avoidance of lipid hydrolysis, minimum water requirements, low risk of contamination, and high yield of fermentation product [9]. Earlier studies and our own showed that SSF, by using Rhizopus oligosporus, can increase TPC and antioxidant activity [10,11]. Further, our results showed that SSF with R. oligosporus offers the optimum fermentation conditions for rice bran in Inpari 30 and Cempo Ireng for 72 hours at 30 ℃ [11].
The non-volatile compounds in rice bran have been studied in varieties of Calrose, Dixiebelle, and Neptune [12,13]. 453 compounds were found, consisting of amino acids, carbohydrates, vitamins and cofactors, lipids, nucleotides, peptides, secondary metabolites, and xenobiotics. Other studies have shown that fermentation treatment affects the number and diversity of bioactive compounds of rice bran [14]. Based on these findings, the non-volatile compounds of fermented and non-fermented rice bran may differ between rice varieties. Research has not been carried out on the non-volatile compounds in fermented and non-fermented bran, especially for rice bran varieties in Indonesia. Therefore, the purpose of this study was to analyze and compare non-volatile compounds of fermented and non-fermented rice bran of two varieties -i.e., Inpari 30 (IPR30) and Cempo Ireng (CI)- and their blood pressure lowering activity, by using a spontaneously hypertensive animal model. The IPR30 cultivar, another Ciherang cultivar (white rice) widely consumed in Indonesia and CI black rice cultivar, a variety of local pigmented rice planted in Bogor-West Java, Indonesia, were studied in this regard.
The sample used in this study was brown rice IPR30 obtained from Indonesian Center for Rice Research, Indonesian Agency for Agricultural Research and Development, Ministry of Agriculture, Subang, West Java, Indonesia and paddy CI from the local farmer in Bogor, West Java, Indonesia. Paddy of CI was de-hulled by a Rice Machine-THU (Satake, Japan) to obtain brown rice. Two types of brown rice were polished by mini rice mill processing (Satake Grain Testing Mill, Hiroshima, Japan) as described previously [11]. The samples were divided into non-fermented IPR30 rice bran (IPRNF), fermented IPR30 rice bran (IPRF), non-fermented CI rice bran (CINF), and fermented CI rice bran (CIF).
R. oligosporus were obtained from the Indonesian Culture Collection, Research Center for Biology, the Indonesian Institute of Science, Cibinong, Indonesia. The R. oligosporus were asseverated on potato dextrose agar media. The preparation of the culture and fermentation process followed the method used in a previous study [11]. The fermented and non-fermented samples were freeze-dried using a freeze-dryer (Labconco, USA) before further analysis.
Sample extraction was done as described by [15,16], with modifications. Samples were dissolved in distilled water with 20% (w/v). The solutions were centrifuged (5223 x g, 10 minutes, 4 ℃) and then extracted by the solid phase extraction method. For every five mL of supernatant, one ml of lidocaine (internal standard) was added, resulting in 2.0083 µM of lidocaine in the supernatant. Thereafter, six ml of solution two was inserted into the cartridge (Oasis HLB 12 mL). Samples were vacuumed to remove their water and salt content. Samples were then eluted with methanol 5% and 1.5 mL were collected for analysis. For the animal study, the water extract of fermented RB was used by an oral single dose experiment.
Non-volatile compounds were analyzed using Ultra performance liquid chromatography-tandem mass spectrometry (UPLC-MS/MS), as described in [12] with modifications. The liquid chromatography instrument used in this study was Waters ACQUITY UPLC H-Class System with C18 column (1.8 µm, 2.1 × 100 mm) at 50 ℃, while the mass spectrometry was Xevo G2-S quadrupole time-of-flight mass spectrometry (QToF-MS/MS) with electrospray ionization spray (ESI) system. For MS, the ion positive mode was used between 70-1000 m/z. Before injection, samples were filtered with a 0.2 µm syringe filter. Five µL of the sample was injected with mobile phase (A), 0.1% formic acid in water and (B), 0.1% formic acid in methanol (0% B to 70% B for 4 minutes, 70-98% B for 0.5 minutes, 98% B for 0.9 minutes). The observed injection flow rate was 0.2 mL per minute for 23 minutes. Masslynx v4.1 was used to identify the non-volatile compounds in the sample. The non-volatile compound data were then cross-checked with MassBank, Human Metabolome Database (HMDB) and Kyoto Encyclopedia of Genes and Genomes (KEGG) data [13]. The relative concentration of non-volatile compounds in the sample were determined by comparing the percentage area between sample and internal standard (lidocaine), based on the concentration of internal standard. The relative concentration was then converted into ppm units.
The male SHRSP/Izumo strain (Japan SLC, Shizuoka, Japan) was used in these studies. The rats were housed in individual stainless-steel cages in a controlled atmosphere (temperature, 23 ± 2 ℃; humidity, 50 ± 10%; 12 h light-dark cycle) as per a previous study [4]. The Animal Research-Animal Care Committee approved the experimental plan for the present study of Tohoku University (2016AgA-024). The entire experiment was conducted following the guidelines issued by this committee and Japanese governmental legislation (2005). The water extract of fermented RB (CI and IPR30, 72 h fermentation) was used to determine the BP-lowering effect in SHRSP. The number of animals used in this study, concentration of the sample in the treated group, and control were similar to our previous study [11]. The blood pressure measurement was by the tail-cuff method with a BP meter as described in the previous study [4].
The data are described as the mean ± SD. One way analysis of variance using SPSS version 22.0 was performed by two-way analysis (SPSS, Inc., Chicago, IL, USA) followed by Duncan's multiple range test for blood pressure study. The categorization of non-volatile compounds based on their relative concentration was analyzed by principal component analysis (PCA) with XLSTAT 2019.
The non-volatile compounds of fermented and non-fermented rice bran of Inpari 30 and Cempo Ireng are presented in Supplementary Table 1. These were classified into 36 secondary metabolites, 16 lipids, 8 amino acids, 7 vitamins and cofactors, 3 peptides, one carbohydrate, and one nucleotide (Figure 1). Fermentation of Inpari 30 and Cempo Ireng rice bran produced new compounds that were not found in the non-fermented samples.
The highest concentration of secondary metabolites found in IPRNF consisted of n, n-diethyl phenylacetamide (MS25), while in IPRF rice bran, the contents were dominated by 2-acetylpyrrole (MS29) and momilactone B (MS7). A study on n, n-diethyl phenylacetamide has shown that it can be used as an insect repellent [17] and 2-acetylpyrrole has hepatoprotective properties [18]. Several studies have shown momilactone B exhibiting inhibitory activities on α-amylase and α-glucosidase, as well as anti-cancer activities by increasing apoptosis in cancer cells [19,20]. In CINF rice bran, the dominant secondary metabolites were myrigalone A (MS36), kojic acid (MS9) and 4-methylbenzoic acid (MS11). Myrigalone A has been known to show antibacterial properties and kojic acid is a chelating agent produced during aerobic fungal fermentation [21].
The most abundant compounds from the lipid in IPRNF and IPRF were leukotriene A4 (LD8) and aminocaproic acid (LD6). The dominant lipid compounds in CINF and CIF were lacinilene C 7-methyl ether (LD2) and phytosphingosine (LD9) respectively. Lacinilene C 7-methyl ether is known to have antibacterial properties [22]. Phytosphingosine has shown anti-inflammatory and antibacterial properties in skin disorders, besides playing a role in transcription activation in peroxisome proliferator-activated receptor [23,24].
Amino acids with the highest concentration found in IPRNF and IPRF were norvaline (AA2) and l-phenylalanine (AA7) respectively. Norvaline is a byproduct of branched-chain amino acid synthesis, which can also act as arginase inhibitor [25]. L-phenylalanine is involved in neurotransmitters, hormones, and skin pigment synthesis in humans [26]. The highest concentration of amino acids in CINF and CIF were 3-methyldioxyindole (AA6) and indoleacrylic acid (AA8) respectively. Indoleacrylic acid has been known to be produced during tryptophan degradation.
The dominant compounds found in the vitamins and cofactors group in IPRNF and IPRF were trigonelline (VK5) and pantothenic acid (VK2) respectively. Trigonelline is found only in IPRNF rice bran and is involved in treating diabetes by lowering the blood glucose level, increasing insulin sensitivity, and decreasing lipid peroxidation [27]. Pantothenic acid is synthesized by R. oligosporus from β-alanine and pantoic acid [28]. The dominant compound in the vitamins and cofactors in CINF and CIF were nicotinic acid (VK1) and 7-aminomethyl-7-carbaguanine (VK6), respectively. Nicotinic acid prevents atherosclerosis by increasing high-density lipoprotein, and decreasing triglyceride level and oxidative stress [29].
Non-volatile compounds from the peptide group were detected only in the fermented samples. The most abundant peptide found in IPRF and CIF were phenylalanyl-isoleucine (PD3) and leucyl-isoleucine (PD2), respectively. According to an earlier study, Leucyl-isoleucine increases monocytes and platelet level in rats and stimulates AMPK phosphorylation [30,31].
Principal component analysis (PCA) was applied to compare the differences of quantum in non-volatile compounds among the samples. The PCA of non-volatile compounds is shown in Figure 2. Non-fermented rice bran samples (IPRNF and CINF) were located in a quadrant different from fermented rice bran (IPRF and CIF), indicating that fermentation influenced non-volatile compound production. Adenosine (NA) generally was found the most in non-volatile compounds across all the samples. In the fermented sample of Inpari 30, the level of n, n-diethyl phenylacetamide (MS25), indoleacrylic acid (AA8), and l-phenylalanine (AA7) were higher, compared to non-fermented rice bran. Other major non-volatile compounds found in IPRNF samples were leukotriene A4 (LD8) and trigonelline (VK5).
On the other hand, fermentation of the Cempo Ireng variety showed an increase in quercetin (MS15), isorhamnetin 7-glucoside (MS16), isorhamnetin (MS17), and nicotinic acid (VK1) levels. In Cempo Ireng samples, the non-volatile compounds with the highest concentration after adenosine were different. In CINF, it was myrigalone A (MS36), while CIF leucyl-isoleucine (PD2) and phenylalanyl-isoleucine (PD3) showed similar concentrations. These compounds are likely to have originated from arachidonic acid, nicotinic acid and nicotinamide, phenylalanine, tryptophan, and dipeptide metabolism. The major non-volatile compounds from each classification from PCA analysis are summarized in Figure 3. The list of non-volatile compounds and its statistical analyses shown in Supplementary Table 1 (Supplementary data).
Adenosine is a compound necessary for production of energy within the body, and is created from purine metabolism. As a phytochemical found in rice bran, adenosine has the effect of lowering blood pressure, helps to treat hyperlipidemia, increases insulin activity, and preventing hypertension in the stroke-prone spontaneously hypertensive rat (SHRSP) [5]. In humans, adenosine has neuromodulator and neuroprotective functions, reduces epilepsy, and regulates the sleep cycle [32,33,34].
Several studies of these compounds have shown them to have beneficial effects for the body, which includes lowering blood pressure, improving the immune and digestive systems, as well as having neuromodulator, neuroprotective, chemo preventive and antidiabetic properties. Further, other studies have also found that these bioactive compounds play a part in preventing gastric ulcer and improving hormone and melanin synthesis [26,27,30,32].
The proposed metabolic pathways found in rice bran are shown in Figure 4. Previous studies shown that rice bran has contained non-volatile compounds (12-14). Our study carried out non-volatile compound of fermented and non-fermented rice bran varieties in Indonesia. Pathways related to the compounds in the fermented and non-fermented Inpari 30 rice bran were the metabolism of valine and the citric acid cycle, respectively. Folate metabolism was found in fermented Cempo Ireng rice bran, while pentatonic acid, vitamin B6, and benzoxazinoid metabolism were found in non-fermented Cempo Ireng rice bran. Fermented versions of both fermented Inpari 30 and Cempo Ireng rice bran produced compounds from the metabolism of tyrosine, phenylalanine, pantothenic acid and dipeptide that was not detected in the non-fermented samples.
Non-volatile compounds in fermented Inpari 30 and Cempo Ireng rice brans were identified as metabolic pathways from tyrosine, phenylalanine, pantothenic acid, folic acid, dipeptide, terpenoid, and sphingolipid. The presence of dipeptide and amino acid compounds indicated that the samples were attributed to rice bran protein degradation by R. oligosporus-synthesized protease [35]. Similarly, metabolites of pantothenic and folic acid were also utilized by fungi, as they are components necessary for fungal metabolic activities [36]. Comparatively, compounds from sphingolipid metabolism are commonly found in fungal plasma membrane [37]. Fungi sphingolipids known to be involved in hyphal morphogenesis are produced during sphingolipid metabolism with serine and palmitoyl-CoA as its precursor [38,39], similar to the terpenoid found in fermented rice bran produced by the fungal mevalonate pathway [40].
This study also investigated whether fermented RB showed any blood pressure-lowering effects after administration of a single oral dose (40 mg/kg body weight) (Table 1). Twelve-week-old male SHRSP with a systolic blood pressure (sBP) of approximately 170 mmHg, were used in this study. The result showed that there was similar sBP of the control group before and after administration. The sBP showed a significant decrease after 6h administration of IPRF (p < 0.05), compared to the control group. A blood pressure lowering activity was also found as sBP was decreasing from 2 h after administration until the end of the study. This study was consistent with the previous study by using Inpari 30 fermented RB [11]. Further, this study also showed evidence of adenosine as one of the identified bioactive compounds in rice bran [5].
Group | 0 h | 2 h | 4 h | 6 h |
Control | 172.3 ± 13.1 | 172.0 ± 8.1 | 161.3 ± 6.5 | 168.0 ± 3.0 |
CIF | 176.8 ± 9.1 | 175.3 ± 2.9 | 165.3 ± 13.3 | 166.8 ± 8.5 |
Change b (%) | - | +1.9 | +2.4 | −0.7 |
IPRF | 171.3 ± 5.0 | 152.3 ± 14.3 | 142.0 ± 12.4 | 141.5 ± 12.2* |
Change b (%) | - | −12.9 | −13.6 | −18.7 |
Note: a Values are given as means ± SD, n = 4. *A significantly different (p < 0.05) versus Control after statistical analysis by one-way analysis of variance using SPSS version 22 software (SPSS, Inc., Chicago, IL, USA) followed by Duncan's multiple range test. |
This study strengthened the proposition that IPRF is a good source of functional ingredient that can be effective in decreasing hypertension in an animal model of metabolic syndrome-related diseases. Future studies are required to specify the IPRF mechanism of blood pressure-lowering activity and other functionalities in relation to metabolic diseases.
Different rice varieties and fermentation processes influence the concentration and types of non-volatile compounds in rice bran. Adenosine was found to have the greatest concentration of non-volatile compound in rice bran. Fermentation of rice bran samples from IPR30 and CI varieties generated compounds from tyrosine, phenylalanine, pentatonic acid, dipeptide, sphingolipid and terpenoid metabolism, which were not found in the non-fermented rice bran. Fermentation of rice bran can produce and enhance non-volatile compounds as anti-hypertensive effect in an animal model of hypertension. Further, this study found adenosine to be a useful marker for non-volatile compounds in rice bran.
We would like to thank to the Ministry Research and Technology/BRIN RI for research funding. The partial of the research was supported by a grant from the collaboration research of JSPS and DIKTI RI.
All authors declare no conflict of interest.
Compounds | Codes | HMDB ID | Relative Concentrations (ppm) | Effects | References | |||
Inpari 30 | Cempo Ireng | |||||||
Non-fermented | Fermented | Non-fermented | Fermented | |||||
(Amino acids) | ||||||||
Meta-tyrosine | AA1 | 0059720 | ND | 0.0266* | ND | ND | Immunoprotective | [41] |
Reduces metastasis | [42] | |||||||
Norvaline | AA2 | 0013716 | 0.0253* | 0.0008* | ND | ND | Arginase inhibitor | [31] |
N-Acetyltryptophan | AA3 | 0013713 | ND | 0.0039* | ND | ND | Antioxidant | [43] |
1H-Imidazole-1-acetic acid | AA4 | 0029736 | ND | ND | ND | 0.0033* | - | - |
L-DOPA | AA5 | 0000181 | ND | ND | ND | 0.0050* | Treatment of Parkinson Dissease (by increasing dopamine levels in brain) | [44] |
3-Methyldioxyindole | AA6 | 0004186 | ND | ND | 0.0011 ± 0.0003 | ND | - | - |
L-Phenylalanine | AA7 | 0000159 | ND | 0.2413 ± 0.2051a | ND | 0.0360 ± 0.0080b | Neurotransmitter synthesis, hormones and pigments synthesis | [26] |
Indoleacrylic acid | AA8 | 0000734 | 0.0115*a | 0.1806 ± 0.1412b | ND | 0.0395 ± 0.0011a | Improves the instentines functions | [45] |
(Carbohydrates) | ||||||||
Succinic acid | KH | 0000254 | 0.0002* | ND | ND | ND | Antioxidant, Imrpove the immune and nervous functions | [46] |
(Lipids) | ||||||||
Cincassiol B | LD1 | 0036855 | ND | 0, 0208* | ND | ND | - | - |
Lacinilene C 7-methyl ether | LD2 | 0036456 | 0.0129 ± 0.0015 | 0.0058* | 0.0134* | 0.0023* | Antimicrobial | [22] |
Valdiic acid | LD3 | 0040980 | ND | 0.0088 ± 0.0108 | ND | ND | - | - |
Prostaglandin C1(1-) | LD4 | 0062756 | 0.0102 ± 0.0029 | ND | 0.0090 ± 0.0017 | ND | - | - |
10-Oxo-11-octadecen-13-olide | LD5 | 0029786 | 0.0041* | ND | 0.0109* | ND | - | - |
Aminocaproic acid | LD6 | 0001901 | ND | 0.0390* | ND | 0.0037* | Antifibrinolytic | [47] |
L-Octanoylcarnitine | LD7 | 0000791 | ND | 0.0180* | 0.0091 ± 0.0052 | ND | - | - |
Leukotriene A4 | LD8 | 0029016 | 0.0352 ± 0.0288 | 0.0131 ± 0.0063 | 0.0110* | ND | The parent molecule for the biosynthesis of all leukotrienes | [48] |
Phytosphingosine | LD9 | 0004610 | ND | 0.0126*b | 0.0114 ± 0.0031a | 0.0049 ± 0.0042b | ● Anti-inlammatory and antibacterial in skin disorders | [31] |
● Activates the transcription activity on PPAR | [23] | |||||||
(Ent-2alpha, 3beta, 15beta, 16beta)-15, 16-Epoxy-2, 3-kauranediol | LD10 | 0038688 | 0.0201 ± 0.0099b | ND | 0.0019*a | ND | - | - |
Dehydroabietic acid | LD11 | 0031127 | 0.0263* | ND | ND | ND | ● Anti-inflammatory in obese people | [49] |
● Activates the SIRT1 enzymes | [50] | |||||||
13, 14-Dihydro-15-keto-PGE2 | LD12 | 0002776 | ND | ND | 0.0010* | ND | Increases the growth of pancreatic celss | [51] |
3-hydroxyundecanoyl carnitine | LD13 | 0061637 | ND | ND | 0.0102 ± 0.0031 | ND | - | - |
Leukotriene C4 | LD14 | 0001198 | 0.0095* | ND | ND | ND | Lipid mediator for inflammation | [52] |
5-Hexyltetrahydro-2-furanoctanoic acid | LD15 | 0029018 | 0.0105* | ND | 0.0021* | ND | - | - |
(Z)-13-Oxo-9-octadecenoic acid | LD16 | 0029796 | 0.0094* | 0.0072* | ND | ND | - | - |
(Nucleotides) | ||||||||
Adenosine | NA | 0000050 | 0.0838 ± 0.1053 | 0.4323 ± 0.1236 | 0.2119 ± 0.0142 | 0.3007 ± 0.1602 | ● Neuromodulator | [34] |
● Neuroprotective | [33] | |||||||
● Reduces epilepsy | [32] | |||||||
● Regulates the sleep cycle | [53] | |||||||
● Lowering blood pressure | [5] | |||||||
(Secondary Metabolites) | ||||||||
Cohumulone | MS1 | 0033981 | ND | 0.0052* | ND | ND | Aldo keto reductase inhibitors | [54] |
3-O-Methylmethyldopa | MS2 | 0142154 | ND | 0.0022 ± 0.0005 | ND | ND | - | - |
2, 6-Dimethoxy-4-propylphenol | MS3 | 0036226 | ND | 0.0007 ± 0.0001 | ND | ND | - | - |
Alpha-curcumene | MS4 | 0059878 | ND | 0.0017±0.0004 | ND | ND | ● Antimicrobial | [55] |
● Induced apoptosis | [56] | |||||||
Cuscohygrine | MS5 | 0030290 | ND | 0.0033* | 0.0051* | 0.0028* | - | - |
3-Tert-butyl-4-hydroxyanisole | MS6 | 0059925 | ND | 0.0015* | 0.0184* | ND | The building blocks of butylated hydroxyanisole (BHA) | [57] |
Momilactone B | MS7 | 0036749 | ND | 0.0153* | ND | ND | ● α-Amylase and α-Glucosidase inhibitors | [20] |
● Cancer chemopreventive | [19] | |||||||
2-Indolecarboxylic acid | MS8 | 0002285 | 0.0024* | ND | 0.0023* | ND | Antioxidant | [58] |
Kojic acid | MS9 | 0032923 | 0.0061 ± 0.0016 | ND | 0.0103 ± 0.0010 | ND | ● Tyrosinase inhibitors | [59] |
● Immunomodulator | [9] | |||||||
L-1, 2, 3, 4-Tetrahydro-beta-carboline-3-carboxylic acid | MS10 | 0035665 | 0.0008* | ND | ND | ND | - | - |
4-Methylbenzoic acid | MS11 | 0029635 | 0.0010*a | ND | ND | 0.0385 ± 0.0103b | - | - |
2-Methylhippuric acid | MS12 | 0011723 | 0.0006* | ND | ND | ND | - | - |
Momilactone A | MS13 | 0036748 | 0.0020* | ND | ND | ND | ● α-Amylase and α-Glucosidase inhibitors | [20] |
Coumarin | MS14 | 0001218 | 0.0009* | ND | ND | ND | ● Antimicrobial | [60) |
● Acetylcholinesterase (AChE) inhibitor | [61] | |||||||
Quercetin | MS15 | 0005794 | ND | ND | 0.0050 ± 0.0031 | 0.0057 ± 0.0028 | ● Antioxidant | [62] |
● Decreases activation of dendytic celss for the treatment of inflammation, autoimmunity and transplantation | [61] | |||||||
● Antiviral activity against dengue fever | [63] | |||||||
● Lowering blood pressure in people with hypertension | [64] | |||||||
● Reduces symptoms of non-alcoholic fatty liver dissease | [65] | |||||||
Isorhamnetin 7-glucoside | MS16 | 0029479 | ND | ND | 0.0089 ± 0.0050 | 0.0165 ± 0.0009 | Antioxidant | [66] |
Isorhamnetin | MS17 | 0002655 | ND | ND | 0.0048* | 0.0121* | Treats cerebral vascular complications associated with diabetes | [67] |
2-Hydroxy-2-phenylpropanoic acid | MS18 | 0142137 | ND | ND | 0.0045 ± 0.0007a | 0.0029 ± 0.0013b | - | - |
2-Phenylpropionaldehyde dimethyl acetal | MS19 | 0032468 | ND | ND | ND | 0.0055 ± 0.0022 | - | - |
Naringenin | MS20 | 0002670 | ND | ND | ND | 0.0037* | ● Hepatoprotector | [68] |
● Reduces TNF- α production | [69] | |||||||
● Anti-hyperglycemia | [70] | |||||||
● Cardioprotective | [71] | |||||||
● Antiviral activity against dengue fever | [72] | |||||||
● Inhibits the proliferation and migration of prostate cancer cells | [73] | |||||||
Phenprocoumon | MS21 | 0015081 | ND | ND | ND | 0.0058* | ● Anticoagulant | [74] |
Isovanillic acid | MS22 | 0060003 | ND | ND | 0.0042 ± 0.0011 | ND | ● Antibacterial | [75] |
● Antioxidant | [76] | |||||||
Antimicrobial | [60] | |||||||
2, 6-Dimethoxybenzoic acid | MS23 | 0029273 | ND | ND | 0.0106* | ND | - | - |
Benzoic acid | MS24 | 0001870 | ND | ND | 0.0009 ± 0.0003 | ND | Inhibits the growth of resistant bacteria | [77] |
N, N-diethyl phenylacetamide | MS25 | 0032635 | 0.0090* | 0.0096* | 0.0066* | 0.0263* | Mosquitos repellent | [17] |
Oryzalide B | MS27 | 0037592 | ND | ND | ND | 0.0053 ± 0.0032 | Antibacterial | [78] |
Acetylvalerenolic acid | MS28 | 0035687 | ND | ND | ND | 0.0045* | - | - |
MS29 | 0035882 | ND | 0.0309 | ND | ND | Hepatoprotector | [18] | |
Dimboa-glc | MS30 | 0029710 | ND | ND | 0.0089 ± 0.0056 | ND | - | - |
2-Decylfuran | MS31 | 0032215 | ND | ND | ND | 0.0015 | - | - |
Piperenol A triacetate | MS32 | 0041535 | ND | 0.0129* | ND | ND | - | - |
Ginsenoyne G | MS33 | 0039589 | ND | ND | 0.0025 | ND | - | - |
Acetylpterosin C | MS34 | 0030764 | 0.0053* | ND | ND | ND | - | - |
1, 3, 11-Tridecatriene-5, 7, 9-triyne | MS35 | 0034294 | ND | ND | 0.0160 | ND | - | - |
Myrigalone A | MS36 | 0037245 | ND | ND | 0.0278* | 0.0256* | Antibacterial | [79] |
(Vitamins dan cofactors) | ||||||||
Nicotinic acid | VK1 | 0001488 | 0.0114 ± 0.0007 | ND | 0.0060 ± 0.0025 | 0.0076 ± 0.0009 | Increases HDL cholesterol and lowers triglycerides for the treatment of atherosclerosis | [29] |
Pantothenic acid | VK2 | 0000210 | ND | ND | ND | 0.0028 ± 0.0010 | Substrates for the synthesis of coenzyme A and ACP (acyl carrier protein) | [80] |
2-Hydroxypyridine | VK3 | 0013751 | 0.0008* | ND | ND | ND | - | - |
4-Methyl-5-thiazoleethanol | VK4 | - | 0.0175 ± 0.0014 | ND | 0.0066 ± 0.0021 | ND | - | - |
Trigonelline | VK5 | 0000875 | 0.0344 ± 0.0247 | ND | ND | ND | ● Increases cell sensitivity to anticancer and apoptotic drugs | [81] |
● Prevents gastric ulcer induced by indomethacin | [82] | |||||||
● Lowering blood sugar and lipid as well as increasing insulin sensitivity for diabetes | ||||||||
● Inhibits neurons loss in hypocampus | [83] | |||||||
7-Aminomethyl-7-carbaguanine | VK6 | 0011690 | ND | ND | ND | 0.0132* | - | - |
Pyridoxal | VK7 | 0001545 | ND | ND | 0.0066 ± 0.0021 | ND | ● Cofactors in various amino acids metabolism | [84] |
● Maintains the nervous systems in infants | [85] | |||||||
(Peptides) | ||||||||
Leucyl-valine | PD1 | 0028942 | ND | 0.0222 ± 0.0162 | ND | ND | Increases the expression of glutathione peroxidase, antioxidants and cell protection agents | [86] |
Leucyl-isoleucine | PD2 | 0028932 | ND | 0.0653 ± 0.0436 | ND | 0.0596 ± 0.0263 | Increases the stimulation of AMPK phosphorylation (5'-AMP protein kinase), monocytes, and platelets | [30] |
Note: The presentation of the relative value data for the compounds comes from the calculation of the average relative area of the compound from 3 replications ± deviation standard; ND = Not Detected; * = compound obtained only in 1 replication; Numbers on the same line with different letters indicate significant differences (p < 0.05). |
[1] | Igbinovia FO (2019) Reactive power compensation in modern electricity grid architecture with the synchronous condenser. PhD thesis, Czech Technical University in Prague. |
[2] |
Balint H, Istvan V, Istvan T (2019) Effect of decreasing synchronous inertia on power dynamics-overview of recent experiences and marketisation of services. Int Trans Electr Energy Syst 29: e12128. https://doi.org/10.1002/2050-7038.12128 doi: 10.1002/2050-7038.12128
![]() |
[3] |
Mustafa EA, Keith RP (2019) Combination of synchronous condenser and synthetic inertia for frequency stability enhancement in low-inertia systems. IEEE Trans Sustainable Energy 10: 997–1005. https://doi.org/10.1109/TSTE.2018.2856938 doi: 10.1109/TSTE.2018.2856938
![]() |
[4] | Kaushik D, Feng G, Edgar N (2020) Frequency stability of power system with large share of wind power under storm conditions. Modern Power Syst Clean Energy |
[5] | AEMO. Black system in South Australia on Wednesday 28 September 2016. |
[6] | Zhou L, Qi ZP (2019) Modeling and control of a flywheel energy storage system for uninterruptible power supply. IEEE, 2009 International Conference on Sustainable Power Generation and Supply. https://doi.org/10.1109/SUPERGEN.2009.5348077 |
[7] | Gu H, Yan R, Saha T (2019) Review of system strength and inertia requirements for the national electricity market of Australia. CSEE J Power Energy Syst 5: 295–305. |
[8] |
Gu HJ, Yanand RF, Saha T (2018) Minimum synchronous inertia requirement of renewable power systems. IEEE Trans Power Syst 33:1533–1543. https://doi.org/10.1109/TPWRS.2017.2720621 doi: 10.1109/TPWRS.2017.2720621
![]() |
[9] | Li F, John K, Tom R (2006) A preliminary analysis of the economics of using distributed energy as a source of reactive power supply. The U.S. Department of Energy. https://doi.org/10.2172/930730 |
[10] |
Rezkalla M, Pertl M, Marinelli M (2018) Electric power system inertia: requirements, challenges and solutions. Electr Eng 100: 2677–2693. https://doi.org/10.1007/s00202-018-0739-z doi: 10.1007/s00202-018-0739-z
![]() |
[11] |
Bolund B, Bernhoff H, Leijon M (2007) Flywheel energy and power storage systems. Renewable Sustainable Energy Rev 11: 235–258. https://doi.org/10.1016/j.rser.2005.01.004 doi: 10.1016/j.rser.2005.01.004
![]() |
[12] |
Zhang Y, Zhang X, Qian T (2020) Modeling and simulation of a passive variable inertia flywheel for diesel generators. Energy Rep 6: 58–68. https://doi.org/10.1016/j.egyr.2020.01.001 doi: 10.1016/j.egyr.2020.01.001
![]() |
[13] |
Mohanan V, Mareels MYI, Evans JR (2020) Stabilising influence of a synchronous condenser in low inertia networks. IET Gener Transm Distrib 14: 3582–3593. https://doi.org/10.1049/iet-gtd.2020.0178 doi: 10.1049/iet-gtd.2020.0178
![]() |
[14] |
Teleke S, Abdulahovic T, Thiringer T (2008) Dynamic performance comparison of synchronous condenser and SVC. IEEE Trans Power Deliv 23: 1606–1612. https://doi.org/10.1109/TPWRD.2007.916109 doi: 10.1109/TPWRD.2007.916109
![]() |
[15] | Igbinovia OF, Fandi G, Zden (2016) Optimal location of the synchronous condenser in electric-power system networks. 1–6. https://doi.org/10.1109/EPE.2016.7521731 |
[16] | Palone F, Gatta FM, Geri A, et al. (2019) New synchronous condenser-flywheel systems for a decarbonized sardinian power system. IEEE Milan PowerTech 1–6. https://doi.org/10.1109/PTC.2019.8810780 |
[17] | Liu Y, Yang S, Zhang S, et al. (2014) Comparison of synchronous condenser and STATCOM for inertial response support. 2014 IEEE Energy Conversion Congress and Exposition (ECCE), Pittsburgh, PA, USA, 2684–2690. https://doi.org/10.1109/ECCE.2014.6953761 |
[18] |
Nguyen TH, Yang G, Nielsen AH (2019) Combination of synchronous condenser and synthetic inertia for frequency stability enhancement in low-inertia systems. IEEE Trans Sustainable Energy 10: 997–1005. https://doi.org/10.1109/TSTE.2018.2856938 doi: 10.1109/TSTE.2018.2856938
![]() |
[19] |
Saarinen L, Norrlund P, Yang W (2017) Linear synthetic inertia for improved frequency quality and reduced hydropower wear and tear. Int J Electri Power Energy Syst 98: 488–495. https://doi.org/10.1016/j.ijepes.2017.12.007 doi: 10.1016/j.ijepes.2017.12.007
![]() |
[20] | ABB Australia (2020) Synchronous condenser packages: Solving the challenges of renewable energy integration. |
[21] | Jia J, Yang G, Nielsen AH, et al. (2017) Synchronous condenser allocation for improving system short circuit ratio. 2018 5th International Conference on Electric Power and Energy Conversion Systems (EPECS), Kitakyushu, Japan, 1–5. https://doi.org/10.1109/EPECS.2018.8443358 |
[22] | Labvolt (2020) Available from: https://www.labvolt.com/about_us. |
[23] | J Gonçalves de Oliveira (2011) Power control systems in a flywheel based all-electric driveline. 2011: 102. Uppsala: Acta Universitatis Upsaliensis. Available from: http://www.diva-portal.org/smash/record.jsf?pid = diva2%3A434755 & dswid = 7105. |
[24] |
Amiryar ME, Pullen KR (2017) A Review of flywheel energy storage system technologies and their applications. Appl Sci 7: 286. https://doi.org/10.3390/app7030286 doi: 10.3390/app7030286
![]() |
[25] | Fooladivanda D, Mancini G, Garg S (2014) State of charge evolution equations for flywheels. Available from: https://arXiv.org/pdf/1411.1680. |
[26] |
Freeman E, Occello D, Barnes F (2016) Energy storage for electrical systems in the USA. AIMS Energy 4: 856–875. https://doi.org/10.3934/energy.2016.6.856 doi: 10.3934/energy.2016.6.856
![]() |
[27] | Gonzalez F, Sumper A, Bellimunt O (2012) Modeling and validation of a flywheel energy storage Lab-Setup. IEEE PES Innovative Smart Grid Technologies Europe (ISGT Europe), Berlin. |
[28] | Pullen KR (2022) Flywheel energy storage. Storing Energy (Second Edition), 207–242. https://doi.org/10.1016/B978-0-12-824510-1.00035-0 |
[29] |
Amiryar ME, Pullen KR, Nankoo D (2018) Development of a high-fidelity model for an electrically driven energy storage flywheel suitable for small scale residential applications. Appl Sci 8: 1–29. https://doi.org/10.3390/app8030453 doi: 10.3390/app8030453
![]() |
[30] |
Ulbig A, Borsche TS, Andersson G (2014) Impact of low rotational inertia on power system stability and operation. IFAC Proc Vol 47: 7290–7297. https://doi.org/10.3182/20140824-6-ZA-1003.02615 doi: 10.3182/20140824-6-ZA-1003.02615
![]() |
[31] |
Zeng F, Zhang J, Chen G, et al. (2020) Online estimation of power system inertia constant under normal operating conditions. IEEE Access 8: 101426–101436. https://doi.org/10.1109/ACCESS.2020.2997728 doi: 10.1109/ACCESS.2020.2997728
![]() |
[32] |
Ashton P, Saunders C, Taylor G, et al. (2015) Inertia estimation of the GB power system using synchrophasor measurements. IEEE Trans Power Syst 30: 701–709. https://doi.org/10.1109/TPWRS.2014.2333776 doi: 10.1109/TPWRS.2014.2333776
![]() |
[33] |
Taher AM, Hasanien HM, Abdel Aleem SHE, et al. (2023) Optimal model predictive control of energy storage devices for frequency stability of modern power systems. J Energy Storage 57: 106310. https://doi.org/10.1016/j.est.2022.106310 doi: 10.1016/j.est.2022.106310
![]() |
[34] |
Hany HM, Tostado-Véliz M, Turky RA, et al. (2022) Hybrid adaptive controlled flywheel energy storage units for transient stability improvement of wind farms. J Energy Storage 54: 105262. https://doi.org/10.1016/j.est.2022.105262 doi: 10.1016/j.est.2022.105262
![]() |
1. | Nicolás Puentes Montealegre, Johanna Santamaría Vanegas, Carlos Eduardo Ñústez-López, Gladys Rozo, Control of N-NH4+ and K+ leaching in potato using a carrageenan hydrogel, 2022, 40, 2357-3732, 85, 10.15446/agron.colomb.v40n1.98526 | |
2. | Berhanu Dinssa, Eyasu Elias, Evaluation of phosphate sorption capacity and external phosphorus requirement of some agricultural soils of the southwestern Ethiopian highlands, 2021, 18, 2356-1424, 136, 10.20961/stjssa.v18i2.51325 | |
3. | Sonal Bhardwaj, Rajesh Kaushal, Prakriti Jhilta, Anchal Rana, Bhawna Dipta, 2022, Chapter 5, 978-981-19-0732-6, 131, 10.1007/978-981-19-0733-3_5 | |
4. | Septi Nurul Aini, Wilda Yanti, Astriana Rahmi Setiawati, Dedy Prasetyo, Jamalam Lumbanraja, 2022, 2563, 0094-243X, 080010, 10.1063/5.0103239 | |
5. | Ye Tian, Chupei Shi, Carolina Urbina Malo, Steve Kwatcho Kengdo, Jakob Heinzle, Erich Inselsbacher, Franz Ottner, Werner Borken, Kerstin Michel, Andreas Schindlbacher, Wolfgang Wanek, Long-term soil warming decreases microbial phosphorus utilization by increasing abiotic phosphorus sorption and phosphorus losses, 2023, 14, 2041-1723, 10.1038/s41467-023-36527-8 | |
6. | Cassio Rafael Costa dos Santos, Osvaldo Ryohei Kato, Norberto Cornejo Noronha, Luana do Socorro Freitas Souza, Eric Victor de Oliveira Ferreira, Gilson Sérgio Bastos de Matos, Dênmora Gomes de Araújo, Marcos André Piedade Gama, Phosphorus adsorption in a degraded soil under forestry recovery after bauxite mining in Paragominas, eastern Amazon, Brazil, 2023, 1085-3278, 10.1002/ldr.4593 | |
7. | Milton Garcia Costa, Marcilene Machado dos Santos Sarah, Renato de Mello Prado, Luiz Fabiano Palaretti, Marisa de Cássia Piccolo, Jonas Pereira de Souza Júnior, Impact of Si on C, N, and P stoichiometric homeostasis favors nutrition and stem dry mass accumulation in sugarcane cultivated in tropical soils with different water regimes, 2022, 13, 1664-462X, 10.3389/fpls.2022.949909 | |
8. | Mas Teddy Sutriadi, Syaiful Anwar, Budi Mulyanto, Adi Jaya, Maria Serrano, Improving Upland Acid Soil Properties And Increasing Maize Yield By Phosphate Rock Application With Organic Acids, 2022, 2022, 1687-8167, 1, 10.1155/2022/9720632 | |
9. | Prisca Divra Johan, Osumanu Haruna Ahmed, Nur Aainaa Hasbullah, Latifah Omar, Puvan Paramisparam, Nur Hidayah Hamidi, Mohamadu Boyie Jalloh, Adiza Alhassan Musah, Phosphorus Sorption following the Application of Charcoal and Sago (Metroxylon sagu) Bark Ash to Acid Soils, 2022, 12, 2073-4395, 3020, 10.3390/agronomy12123020 | |
10. | Kambiz Mootab Laleh, Majid Ghorbani Javid, Iraj Alahdadi, Elias Soltani, Saeid Soufizadeh, José Luis González-Andújar, Wheat Yield Gap Assessment in Using the Comparative Performance Analysis (CPA), 2023, 13, 2073-4395, 705, 10.3390/agronomy13030705 | |
11. | Júlia Rodrigues Macedo, Silvino Guimarães Moreira, Flávio Araújo de Moraes, Daniel de Souza Reis Junior, Devison Souza Peixoto, Bruno Montoani Silva, Júnior Cézar Resende Silva, The management of phosphate fertilization affects soil phosphorus and yield of autumn/winter crops, 2022, 45, 1807-8621, e57336, 10.4025/actasciagron.v45i1.57336 | |
12. | F. S. Tariq, C. H. Abdulrahman, M. S. Rasheed, Kinetics of Phosphorus Adsorption in The Calcareous Soils of Kurdistan Region, Iraqi, 2021, 761, 1755-1307, 012016, 10.1088/1755-1315/761/1/012016 | |
13. | Hariane Luiz Santos, Gustavo Ferreira da Silva, Melina Rodrigues Alves Carnietto, Laura Costa Oliveira, Carlos Henrique de Castro Nogueira, Marcelo de Almeida Silva, Bacillus velezensis Associated with Organomineral Fertilizer and Reduced Phosphate Doses Improves Soil Microbial—Chemical Properties and Biomass of Sugarcane, 2022, 12, 2073-4395, 2701, 10.3390/agronomy12112701 | |
14. | Abd Hamid Izzah, Wan Yahaya Wan-Asrina, Abd Wahid Samsuri, Idris Wan-Mohd-Razi, Vijayanathan Jeyanny, Effects of Three Rainfall Patterns on Soil Chemical Properties in Black Pepper Cultivation in a Hilly Topography, 2021, 45, 2231-8542, 103, 10.47836/pjtas.45.1.06 | |
15. | Reginawanti Hindersah, Agusthinus Marthin Kalay, Abraham Talahaturuson, Rice yield grown in different fertilizer combination and planting methods: Case study in Buru Island, Indonesia, 2022, 7, 2391-9531, 871, 10.1515/opag-2022-0148 | |
16. | Nadeesha Ukwattage, U.V. Lakmalie, Sequential Phosphorus Fractionation to Understand the Fate of Phosphorus Fertilizer in Sandy Ultisol, Amended with Biochar and Coal Fly Ash, 2022, 53, 0010-3624, 2622, 10.1080/00103624.2022.2072861 | |
17. | Mayra Maniero Rodrigues, Douglas Gomes Viana, Guilherme Lucio Martins, Adijailton José de Souza, Júlio Flávio Osti, Fernando Carvalho Oliveira, Marcelo Corrêa Alves, Aline Renee Coscione, Jussara Borges Regitano, Use of a Concerning Sewage Sludge in the Manufacture of Organomineral Fertilizers: Agronomical Implications and Sustainable Disposal, 2023, 0718-9508, 10.1007/s42729-023-01235-1 | |
18. | Deyvielen Maria Ramos Alves, Jairo Neves de Oliveira, Renato de Mello Prado, Patrícia Messias Ferreira, Silicon in the form of nanosilica mitigates P toxicity in scarlet eggplant, 2023, 13, 2045-2322, 10.1038/s41598-023-36412-w | |
19. | Aliou Badara Kouyate, Vincent Logah, Robert Clement Abaidoo, Francis Marthy Tetteh, Mensah Bonsu, Sidiki Gabriel Dembélé, Phosphorus sorption characteristics in the Sahel: Estimates from soils in Mali, 2023, 8, 2471-2086, 995, 10.3934/agrfood.2023053 | |
20. | Elisson Girardi, Igor Felipe Zampier, Poliana Horst Petranski, Katia Cylene Lombardi, Fabrício William de Ávila, Soil fertility and yerba mate (Ilex paraguariensis A. St. Hil.) growth under sheep manure or mineral fertilization in monoculture or intercropped with Mimosa scabrella Benth., 2024, 98, 0167-4366, 81, 10.1007/s10457-023-00892-6 | |
21. | C. C. Chukwuma, C. J. Oraegbunam, S. D. Ndzeshala, Y. Uchida, V. U. Ugwu, S. E. Obalum, C. A. Igwe, Phosphorus Mineralization in Two Lithologically Dissimilar Tropical Soils as Influenced by Animal Manure Type and Amendment-To-Sampling Time Interval, 2024, 55, 0010-3624, 707, 10.1080/00103624.2023.2276269 | |
22. | Kehinde Ojeniyi, Chirinda Ngonidzashe, Krishna Devkota, Donald Madukwe, Optimizing split-fertilizer applications for enhanced maize yield and nutrient use efficiency in Nigeria's Middle-belt, 2024, 10, 24058440, e37747, 10.1016/j.heliyon.2024.e37747 | |
23. | Bianca Cavalcante da Silva, Milton Garcia Costa, Ismael de Jesus Matos Viégas, Jairo Osvaldo Cazetta, Rafael Moises Alves, Diocléa Almeida Seabra Silva², Impact of Nutrient Omissions on Growth and Biomass Nutrition in Young Plants of Cupuaçu Tree (Theobroma grandiflorum (Willd. ex Spreng.) Shum), 2024, 0718-9508, 10.1007/s42729-024-02072-6 | |
24. | Bignyan Ranjan Sahoo, Ashish Kumar Dash, Kiran Kumar Mohapatra, Shraddha Mohanty, Suman G. Sahu, Bidwan Ranjan Sahoo, Meenakhi Prusty, Elora Priyadarshini, Strategic management of nano-fertilizers for sustainable rice yield, grain quality, and soil health, 2024, 12, 2296-665X, 10.3389/fenvs.2024.1420505 | |
25. | Christon J. Hurst, 2023, 9781119849971, 1, 10.1002/9781119850007.ch1 | |
26. | Ankita Kumari, Himanshu Sharma, Archana Kumari, Priyanka Sharma, Nishit Pathak, Rani Singh, Abdel Rahman Al-Tawaha, Devendra Kumar Pandey, Mahipal S. Shekhawat, Sayanti Mandal, 2024, 9780443160820, 53, 10.1016/B978-0-443-16082-0.00014-X | |
27. | Wuye Ria Andayanie, Praptiningsih Gamawati Adinurani, Martin Lukito, Glomus mosseae AND Pseudomonas fluorescens AGAINST Soybean mosaic virus UNDER DRIP IRRIGATION SYSTEM, 2024, 31, 1907-770X, 181, 10.11598/btb.2024.31.2.1889 | |
28. | Andrezza Maia de Lima, Lucia Helena Garófalo Chaves, Josely Dantas Fernandes, Antonio Fernandes Monteiro Filho, Élida Barbosa Corrêa, Maria do Socorro Bezerra Duarte, Gustavo Tomio Magalhães Kubo, Phosphorus adsorption after the incubation of clay soil with different doses of biochar, 2024, 48, 1981-1829, 10.1590/1413-7054202448016724 | |
29. | Janani Palihakkara, Lucy Burkitt, Paramsothy Jeyakumar, Chammi P. Attanayake, Exploring Phosphorus Dynamics in Submerged Soils and Its Implications on the Inconsistent Rice Yield Response to Added Inorganic Phosphorus Fertilisers in Paddy Soils in Sri Lanka, 2024, 24, 0718-9508, 1, 10.1007/s42729-023-01553-4 | |
30. | Emanuelle Valeska Bilhar Araújo, Cláudia Majolo, Ithalo Gomes de Lima, Jéssica Pinheiro dos Santos, Aleksander Westphal Muniz, Solubilização de fosfatos e potássio por bactérias rizosféricas - uma revisão, 2024, 12, 843, 10.31413/nat.v12i4.17576 | |
31. | Nusrat Jahan, Upoma Mahmud, Md. Zulfikar Khan, Sustainable plant-soil phosphorus management in agricultural systems: challenges, environmental impacts and innovative solutions, 2025, 2, 3005-1223, 10.1007/s44378-025-00039-2 | |
32. | Milton Garcia Costa, Bianca Cavalcante da Silva, Deyvielen Maria Ramos Alves, Paulo Sergio Rodrigues de Lima, Renato de Mello Prado, Silicon, by modulating homeostasis and nutritional efficiency, increases the antioxidant action and tolerance of bell peppers to phosphorus deficiency, 2025, 343, 03044238, 114093, 10.1016/j.scienta.2025.114093 | |
33. | Daniela Yaffar, Julia Brenner, Anthony P. Walker, Matthew E. Craig, Elliot Vaughan, Erika Marín-Spiotta, Manuel Matos, Samuel Rios, Melanie A. Mayes, The Freundlich isotherm equation best represents phosphate sorption across soil orders and land use types in tropical soils of Puerto Rico, 2025, 168, 1573-515X, 10.1007/s10533-025-01218-7 |
Group | 0 h | 2 h | 4 h | 6 h |
Control | 172.3 ± 13.1 | 172.0 ± 8.1 | 161.3 ± 6.5 | 168.0 ± 3.0 |
CIF | 176.8 ± 9.1 | 175.3 ± 2.9 | 165.3 ± 13.3 | 166.8 ± 8.5 |
Change b (%) | - | +1.9 | +2.4 | −0.7 |
IPRF | 171.3 ± 5.0 | 152.3 ± 14.3 | 142.0 ± 12.4 | 141.5 ± 12.2* |
Change b (%) | - | −12.9 | −13.6 | −18.7 |
Note: a Values are given as means ± SD, n = 4. *A significantly different (p < 0.05) versus Control after statistical analysis by one-way analysis of variance using SPSS version 22 software (SPSS, Inc., Chicago, IL, USA) followed by Duncan's multiple range test. |
Compounds | Codes | HMDB ID | Relative Concentrations (ppm) | Effects | References | |||
Inpari 30 | Cempo Ireng | |||||||
Non-fermented | Fermented | Non-fermented | Fermented | |||||
(Amino acids) | ||||||||
Meta-tyrosine | AA1 | 0059720 | ND | 0.0266* | ND | ND | Immunoprotective | [41] |
Reduces metastasis | [42] | |||||||
Norvaline | AA2 | 0013716 | 0.0253* | 0.0008* | ND | ND | Arginase inhibitor | [31] |
N-Acetyltryptophan | AA3 | 0013713 | ND | 0.0039* | ND | ND | Antioxidant | [43] |
1H-Imidazole-1-acetic acid | AA4 | 0029736 | ND | ND | ND | 0.0033* | - | - |
L-DOPA | AA5 | 0000181 | ND | ND | ND | 0.0050* | Treatment of Parkinson Dissease (by increasing dopamine levels in brain) | [44] |
3-Methyldioxyindole | AA6 | 0004186 | ND | ND | 0.0011 ± 0.0003 | ND | - | - |
L-Phenylalanine | AA7 | 0000159 | ND | 0.2413 ± 0.2051a | ND | 0.0360 ± 0.0080b | Neurotransmitter synthesis, hormones and pigments synthesis | [26] |
Indoleacrylic acid | AA8 | 0000734 | 0.0115*a | 0.1806 ± 0.1412b | ND | 0.0395 ± 0.0011a | Improves the instentines functions | [45] |
(Carbohydrates) | ||||||||
Succinic acid | KH | 0000254 | 0.0002* | ND | ND | ND | Antioxidant, Imrpove the immune and nervous functions | [46] |
(Lipids) | ||||||||
Cincassiol B | LD1 | 0036855 | ND | 0, 0208* | ND | ND | - | - |
Lacinilene C 7-methyl ether | LD2 | 0036456 | 0.0129 ± 0.0015 | 0.0058* | 0.0134* | 0.0023* | Antimicrobial | [22] |
Valdiic acid | LD3 | 0040980 | ND | 0.0088 ± 0.0108 | ND | ND | - | - |
Prostaglandin C1(1-) | LD4 | 0062756 | 0.0102 ± 0.0029 | ND | 0.0090 ± 0.0017 | ND | - | - |
10-Oxo-11-octadecen-13-olide | LD5 | 0029786 | 0.0041* | ND | 0.0109* | ND | - | - |
Aminocaproic acid | LD6 | 0001901 | ND | 0.0390* | ND | 0.0037* | Antifibrinolytic | [47] |
L-Octanoylcarnitine | LD7 | 0000791 | ND | 0.0180* | 0.0091 ± 0.0052 | ND | - | - |
Leukotriene A4 | LD8 | 0029016 | 0.0352 ± 0.0288 | 0.0131 ± 0.0063 | 0.0110* | ND | The parent molecule for the biosynthesis of all leukotrienes | [48] |
Phytosphingosine | LD9 | 0004610 | ND | 0.0126*b | 0.0114 ± 0.0031a | 0.0049 ± 0.0042b | ● Anti-inlammatory and antibacterial in skin disorders | [31] |
● Activates the transcription activity on PPAR | [23] | |||||||
(Ent-2alpha, 3beta, 15beta, 16beta)-15, 16-Epoxy-2, 3-kauranediol | LD10 | 0038688 | 0.0201 ± 0.0099b | ND | 0.0019*a | ND | - | - |
Dehydroabietic acid | LD11 | 0031127 | 0.0263* | ND | ND | ND | ● Anti-inflammatory in obese people | [49] |
● Activates the SIRT1 enzymes | [50] | |||||||
13, 14-Dihydro-15-keto-PGE2 | LD12 | 0002776 | ND | ND | 0.0010* | ND | Increases the growth of pancreatic celss | [51] |
3-hydroxyundecanoyl carnitine | LD13 | 0061637 | ND | ND | 0.0102 ± 0.0031 | ND | - | - |
Leukotriene C4 | LD14 | 0001198 | 0.0095* | ND | ND | ND | Lipid mediator for inflammation | [52] |
5-Hexyltetrahydro-2-furanoctanoic acid | LD15 | 0029018 | 0.0105* | ND | 0.0021* | ND | - | - |
(Z)-13-Oxo-9-octadecenoic acid | LD16 | 0029796 | 0.0094* | 0.0072* | ND | ND | - | - |
(Nucleotides) | ||||||||
Adenosine | NA | 0000050 | 0.0838 ± 0.1053 | 0.4323 ± 0.1236 | 0.2119 ± 0.0142 | 0.3007 ± 0.1602 | ● Neuromodulator | [34] |
● Neuroprotective | [33] | |||||||
● Reduces epilepsy | [32] | |||||||
● Regulates the sleep cycle | [53] | |||||||
● Lowering blood pressure | [5] | |||||||
(Secondary Metabolites) | ||||||||
Cohumulone | MS1 | 0033981 | ND | 0.0052* | ND | ND | Aldo keto reductase inhibitors | [54] |
3-O-Methylmethyldopa | MS2 | 0142154 | ND | 0.0022 ± 0.0005 | ND | ND | - | - |
2, 6-Dimethoxy-4-propylphenol | MS3 | 0036226 | ND | 0.0007 ± 0.0001 | ND | ND | - | - |
Alpha-curcumene | MS4 | 0059878 | ND | 0.0017±0.0004 | ND | ND | ● Antimicrobial | [55] |
● Induced apoptosis | [56] | |||||||
Cuscohygrine | MS5 | 0030290 | ND | 0.0033* | 0.0051* | 0.0028* | - | - |
3-Tert-butyl-4-hydroxyanisole | MS6 | 0059925 | ND | 0.0015* | 0.0184* | ND | The building blocks of butylated hydroxyanisole (BHA) | [57] |
Momilactone B | MS7 | 0036749 | ND | 0.0153* | ND | ND | ● α-Amylase and α-Glucosidase inhibitors | [20] |
● Cancer chemopreventive | [19] | |||||||
2-Indolecarboxylic acid | MS8 | 0002285 | 0.0024* | ND | 0.0023* | ND | Antioxidant | [58] |
Kojic acid | MS9 | 0032923 | 0.0061 ± 0.0016 | ND | 0.0103 ± 0.0010 | ND | ● Tyrosinase inhibitors | [59] |
● Immunomodulator | [9] | |||||||
L-1, 2, 3, 4-Tetrahydro-beta-carboline-3-carboxylic acid | MS10 | 0035665 | 0.0008* | ND | ND | ND | - | - |
4-Methylbenzoic acid | MS11 | 0029635 | 0.0010*a | ND | ND | 0.0385 ± 0.0103b | - | - |
2-Methylhippuric acid | MS12 | 0011723 | 0.0006* | ND | ND | ND | - | - |
Momilactone A | MS13 | 0036748 | 0.0020* | ND | ND | ND | ● α-Amylase and α-Glucosidase inhibitors | [20] |
Coumarin | MS14 | 0001218 | 0.0009* | ND | ND | ND | ● Antimicrobial | [60) |
● Acetylcholinesterase (AChE) inhibitor | [61] | |||||||
Quercetin | MS15 | 0005794 | ND | ND | 0.0050 ± 0.0031 | 0.0057 ± 0.0028 | ● Antioxidant | [62] |
● Decreases activation of dendytic celss for the treatment of inflammation, autoimmunity and transplantation | [61] | |||||||
● Antiviral activity against dengue fever | [63] | |||||||
● Lowering blood pressure in people with hypertension | [64] | |||||||
● Reduces symptoms of non-alcoholic fatty liver dissease | [65] | |||||||
Isorhamnetin 7-glucoside | MS16 | 0029479 | ND | ND | 0.0089 ± 0.0050 | 0.0165 ± 0.0009 | Antioxidant | [66] |
Isorhamnetin | MS17 | 0002655 | ND | ND | 0.0048* | 0.0121* | Treats cerebral vascular complications associated with diabetes | [67] |
2-Hydroxy-2-phenylpropanoic acid | MS18 | 0142137 | ND | ND | 0.0045 ± 0.0007a | 0.0029 ± 0.0013b | - | - |
2-Phenylpropionaldehyde dimethyl acetal | MS19 | 0032468 | ND | ND | ND | 0.0055 ± 0.0022 | - | - |
Naringenin | MS20 | 0002670 | ND | ND | ND | 0.0037* | ● Hepatoprotector | [68] |
● Reduces TNF- α production | [69] | |||||||
● Anti-hyperglycemia | [70] | |||||||
● Cardioprotective | [71] | |||||||
● Antiviral activity against dengue fever | [72] | |||||||
● Inhibits the proliferation and migration of prostate cancer cells | [73] | |||||||
Phenprocoumon | MS21 | 0015081 | ND | ND | ND | 0.0058* | ● Anticoagulant | [74] |
Isovanillic acid | MS22 | 0060003 | ND | ND | 0.0042 ± 0.0011 | ND | ● Antibacterial | [75] |
● Antioxidant | [76] | |||||||
Antimicrobial | [60] | |||||||
2, 6-Dimethoxybenzoic acid | MS23 | 0029273 | ND | ND | 0.0106* | ND | - | - |
Benzoic acid | MS24 | 0001870 | ND | ND | 0.0009 ± 0.0003 | ND | Inhibits the growth of resistant bacteria | [77] |
N, N-diethyl phenylacetamide | MS25 | 0032635 | 0.0090* | 0.0096* | 0.0066* | 0.0263* | Mosquitos repellent | [17] |
Oryzalide B | MS27 | 0037592 | ND | ND | ND | 0.0053 ± 0.0032 | Antibacterial | [78] |
Acetylvalerenolic acid | MS28 | 0035687 | ND | ND | ND | 0.0045* | - | - |
MS29 | 0035882 | ND | 0.0309 | ND | ND | Hepatoprotector | [18] | |
Dimboa-glc | MS30 | 0029710 | ND | ND | 0.0089 ± 0.0056 | ND | - | - |
2-Decylfuran | MS31 | 0032215 | ND | ND | ND | 0.0015 | - | - |
Piperenol A triacetate | MS32 | 0041535 | ND | 0.0129* | ND | ND | - | - |
Ginsenoyne G | MS33 | 0039589 | ND | ND | 0.0025 | ND | - | - |
Acetylpterosin C | MS34 | 0030764 | 0.0053* | ND | ND | ND | - | - |
1, 3, 11-Tridecatriene-5, 7, 9-triyne | MS35 | 0034294 | ND | ND | 0.0160 | ND | - | - |
Myrigalone A | MS36 | 0037245 | ND | ND | 0.0278* | 0.0256* | Antibacterial | [79] |
(Vitamins dan cofactors) | ||||||||
Nicotinic acid | VK1 | 0001488 | 0.0114 ± 0.0007 | ND | 0.0060 ± 0.0025 | 0.0076 ± 0.0009 | Increases HDL cholesterol and lowers triglycerides for the treatment of atherosclerosis | [29] |
Pantothenic acid | VK2 | 0000210 | ND | ND | ND | 0.0028 ± 0.0010 | Substrates for the synthesis of coenzyme A and ACP (acyl carrier protein) | [80] |
2-Hydroxypyridine | VK3 | 0013751 | 0.0008* | ND | ND | ND | - | - |
4-Methyl-5-thiazoleethanol | VK4 | - | 0.0175 ± 0.0014 | ND | 0.0066 ± 0.0021 | ND | - | - |
Trigonelline | VK5 | 0000875 | 0.0344 ± 0.0247 | ND | ND | ND | ● Increases cell sensitivity to anticancer and apoptotic drugs | [81] |
● Prevents gastric ulcer induced by indomethacin | [82] | |||||||
● Lowering blood sugar and lipid as well as increasing insulin sensitivity for diabetes | ||||||||
● Inhibits neurons loss in hypocampus | [83] | |||||||
7-Aminomethyl-7-carbaguanine | VK6 | 0011690 | ND | ND | ND | 0.0132* | - | - |
Pyridoxal | VK7 | 0001545 | ND | ND | 0.0066 ± 0.0021 | ND | ● Cofactors in various amino acids metabolism | [84] |
● Maintains the nervous systems in infants | [85] | |||||||
(Peptides) | ||||||||
Leucyl-valine | PD1 | 0028942 | ND | 0.0222 ± 0.0162 | ND | ND | Increases the expression of glutathione peroxidase, antioxidants and cell protection agents | [86] |
Leucyl-isoleucine | PD2 | 0028932 | ND | 0.0653 ± 0.0436 | ND | 0.0596 ± 0.0263 | Increases the stimulation of AMPK phosphorylation (5'-AMP protein kinase), monocytes, and platelets | [30] |
Note: The presentation of the relative value data for the compounds comes from the calculation of the average relative area of the compound from 3 replications ± deviation standard; ND = Not Detected; * = compound obtained only in 1 replication; Numbers on the same line with different letters indicate significant differences (p < 0.05). |
Group | 0 h | 2 h | 4 h | 6 h |
Control | 172.3 ± 13.1 | 172.0 ± 8.1 | 161.3 ± 6.5 | 168.0 ± 3.0 |
CIF | 176.8 ± 9.1 | 175.3 ± 2.9 | 165.3 ± 13.3 | 166.8 ± 8.5 |
Change b (%) | - | +1.9 | +2.4 | −0.7 |
IPRF | 171.3 ± 5.0 | 152.3 ± 14.3 | 142.0 ± 12.4 | 141.5 ± 12.2* |
Change b (%) | - | −12.9 | −13.6 | −18.7 |
Note: a Values are given as means ± SD, n = 4. *A significantly different (p < 0.05) versus Control after statistical analysis by one-way analysis of variance using SPSS version 22 software (SPSS, Inc., Chicago, IL, USA) followed by Duncan's multiple range test. |
Compounds | Codes | HMDB ID | Relative Concentrations (ppm) | Effects | References | |||
Inpari 30 | Cempo Ireng | |||||||
Non-fermented | Fermented | Non-fermented | Fermented | |||||
(Amino acids) | ||||||||
Meta-tyrosine | AA1 | 0059720 | ND | 0.0266* | ND | ND | Immunoprotective | [41] |
Reduces metastasis | [42] | |||||||
Norvaline | AA2 | 0013716 | 0.0253* | 0.0008* | ND | ND | Arginase inhibitor | [31] |
N-Acetyltryptophan | AA3 | 0013713 | ND | 0.0039* | ND | ND | Antioxidant | [43] |
1H-Imidazole-1-acetic acid | AA4 | 0029736 | ND | ND | ND | 0.0033* | - | - |
L-DOPA | AA5 | 0000181 | ND | ND | ND | 0.0050* | Treatment of Parkinson Dissease (by increasing dopamine levels in brain) | [44] |
3-Methyldioxyindole | AA6 | 0004186 | ND | ND | 0.0011 ± 0.0003 | ND | - | - |
L-Phenylalanine | AA7 | 0000159 | ND | 0.2413 ± 0.2051a | ND | 0.0360 ± 0.0080b | Neurotransmitter synthesis, hormones and pigments synthesis | [26] |
Indoleacrylic acid | AA8 | 0000734 | 0.0115*a | 0.1806 ± 0.1412b | ND | 0.0395 ± 0.0011a | Improves the instentines functions | [45] |
(Carbohydrates) | ||||||||
Succinic acid | KH | 0000254 | 0.0002* | ND | ND | ND | Antioxidant, Imrpove the immune and nervous functions | [46] |
(Lipids) | ||||||||
Cincassiol B | LD1 | 0036855 | ND | 0, 0208* | ND | ND | - | - |
Lacinilene C 7-methyl ether | LD2 | 0036456 | 0.0129 ± 0.0015 | 0.0058* | 0.0134* | 0.0023* | Antimicrobial | [22] |
Valdiic acid | LD3 | 0040980 | ND | 0.0088 ± 0.0108 | ND | ND | - | - |
Prostaglandin C1(1-) | LD4 | 0062756 | 0.0102 ± 0.0029 | ND | 0.0090 ± 0.0017 | ND | - | - |
10-Oxo-11-octadecen-13-olide | LD5 | 0029786 | 0.0041* | ND | 0.0109* | ND | - | - |
Aminocaproic acid | LD6 | 0001901 | ND | 0.0390* | ND | 0.0037* | Antifibrinolytic | [47] |
L-Octanoylcarnitine | LD7 | 0000791 | ND | 0.0180* | 0.0091 ± 0.0052 | ND | - | - |
Leukotriene A4 | LD8 | 0029016 | 0.0352 ± 0.0288 | 0.0131 ± 0.0063 | 0.0110* | ND | The parent molecule for the biosynthesis of all leukotrienes | [48] |
Phytosphingosine | LD9 | 0004610 | ND | 0.0126*b | 0.0114 ± 0.0031a | 0.0049 ± 0.0042b | ● Anti-inlammatory and antibacterial in skin disorders | [31] |
● Activates the transcription activity on PPAR | [23] | |||||||
(Ent-2alpha, 3beta, 15beta, 16beta)-15, 16-Epoxy-2, 3-kauranediol | LD10 | 0038688 | 0.0201 ± 0.0099b | ND | 0.0019*a | ND | - | - |
Dehydroabietic acid | LD11 | 0031127 | 0.0263* | ND | ND | ND | ● Anti-inflammatory in obese people | [49] |
● Activates the SIRT1 enzymes | [50] | |||||||
13, 14-Dihydro-15-keto-PGE2 | LD12 | 0002776 | ND | ND | 0.0010* | ND | Increases the growth of pancreatic celss | [51] |
3-hydroxyundecanoyl carnitine | LD13 | 0061637 | ND | ND | 0.0102 ± 0.0031 | ND | - | - |
Leukotriene C4 | LD14 | 0001198 | 0.0095* | ND | ND | ND | Lipid mediator for inflammation | [52] |
5-Hexyltetrahydro-2-furanoctanoic acid | LD15 | 0029018 | 0.0105* | ND | 0.0021* | ND | - | - |
(Z)-13-Oxo-9-octadecenoic acid | LD16 | 0029796 | 0.0094* | 0.0072* | ND | ND | - | - |
(Nucleotides) | ||||||||
Adenosine | NA | 0000050 | 0.0838 ± 0.1053 | 0.4323 ± 0.1236 | 0.2119 ± 0.0142 | 0.3007 ± 0.1602 | ● Neuromodulator | [34] |
● Neuroprotective | [33] | |||||||
● Reduces epilepsy | [32] | |||||||
● Regulates the sleep cycle | [53] | |||||||
● Lowering blood pressure | [5] | |||||||
(Secondary Metabolites) | ||||||||
Cohumulone | MS1 | 0033981 | ND | 0.0052* | ND | ND | Aldo keto reductase inhibitors | [54] |
3-O-Methylmethyldopa | MS2 | 0142154 | ND | 0.0022 ± 0.0005 | ND | ND | - | - |
2, 6-Dimethoxy-4-propylphenol | MS3 | 0036226 | ND | 0.0007 ± 0.0001 | ND | ND | - | - |
Alpha-curcumene | MS4 | 0059878 | ND | 0.0017±0.0004 | ND | ND | ● Antimicrobial | [55] |
● Induced apoptosis | [56] | |||||||
Cuscohygrine | MS5 | 0030290 | ND | 0.0033* | 0.0051* | 0.0028* | - | - |
3-Tert-butyl-4-hydroxyanisole | MS6 | 0059925 | ND | 0.0015* | 0.0184* | ND | The building blocks of butylated hydroxyanisole (BHA) | [57] |
Momilactone B | MS7 | 0036749 | ND | 0.0153* | ND | ND | ● α-Amylase and α-Glucosidase inhibitors | [20] |
● Cancer chemopreventive | [19] | |||||||
2-Indolecarboxylic acid | MS8 | 0002285 | 0.0024* | ND | 0.0023* | ND | Antioxidant | [58] |
Kojic acid | MS9 | 0032923 | 0.0061 ± 0.0016 | ND | 0.0103 ± 0.0010 | ND | ● Tyrosinase inhibitors | [59] |
● Immunomodulator | [9] | |||||||
L-1, 2, 3, 4-Tetrahydro-beta-carboline-3-carboxylic acid | MS10 | 0035665 | 0.0008* | ND | ND | ND | - | - |
4-Methylbenzoic acid | MS11 | 0029635 | 0.0010*a | ND | ND | 0.0385 ± 0.0103b | - | - |
2-Methylhippuric acid | MS12 | 0011723 | 0.0006* | ND | ND | ND | - | - |
Momilactone A | MS13 | 0036748 | 0.0020* | ND | ND | ND | ● α-Amylase and α-Glucosidase inhibitors | [20] |
Coumarin | MS14 | 0001218 | 0.0009* | ND | ND | ND | ● Antimicrobial | [60) |
● Acetylcholinesterase (AChE) inhibitor | [61] | |||||||
Quercetin | MS15 | 0005794 | ND | ND | 0.0050 ± 0.0031 | 0.0057 ± 0.0028 | ● Antioxidant | [62] |
● Decreases activation of dendytic celss for the treatment of inflammation, autoimmunity and transplantation | [61] | |||||||
● Antiviral activity against dengue fever | [63] | |||||||
● Lowering blood pressure in people with hypertension | [64] | |||||||
● Reduces symptoms of non-alcoholic fatty liver dissease | [65] | |||||||
Isorhamnetin 7-glucoside | MS16 | 0029479 | ND | ND | 0.0089 ± 0.0050 | 0.0165 ± 0.0009 | Antioxidant | [66] |
Isorhamnetin | MS17 | 0002655 | ND | ND | 0.0048* | 0.0121* | Treats cerebral vascular complications associated with diabetes | [67] |
2-Hydroxy-2-phenylpropanoic acid | MS18 | 0142137 | ND | ND | 0.0045 ± 0.0007a | 0.0029 ± 0.0013b | - | - |
2-Phenylpropionaldehyde dimethyl acetal | MS19 | 0032468 | ND | ND | ND | 0.0055 ± 0.0022 | - | - |
Naringenin | MS20 | 0002670 | ND | ND | ND | 0.0037* | ● Hepatoprotector | [68] |
● Reduces TNF- α production | [69] | |||||||
● Anti-hyperglycemia | [70] | |||||||
● Cardioprotective | [71] | |||||||
● Antiviral activity against dengue fever | [72] | |||||||
● Inhibits the proliferation and migration of prostate cancer cells | [73] | |||||||
Phenprocoumon | MS21 | 0015081 | ND | ND | ND | 0.0058* | ● Anticoagulant | [74] |
Isovanillic acid | MS22 | 0060003 | ND | ND | 0.0042 ± 0.0011 | ND | ● Antibacterial | [75] |
● Antioxidant | [76] | |||||||
Antimicrobial | [60] | |||||||
2, 6-Dimethoxybenzoic acid | MS23 | 0029273 | ND | ND | 0.0106* | ND | - | - |
Benzoic acid | MS24 | 0001870 | ND | ND | 0.0009 ± 0.0003 | ND | Inhibits the growth of resistant bacteria | [77] |
N, N-diethyl phenylacetamide | MS25 | 0032635 | 0.0090* | 0.0096* | 0.0066* | 0.0263* | Mosquitos repellent | [17] |
Oryzalide B | MS27 | 0037592 | ND | ND | ND | 0.0053 ± 0.0032 | Antibacterial | [78] |
Acetylvalerenolic acid | MS28 | 0035687 | ND | ND | ND | 0.0045* | - | - |
MS29 | 0035882 | ND | 0.0309 | ND | ND | Hepatoprotector | [18] | |
Dimboa-glc | MS30 | 0029710 | ND | ND | 0.0089 ± 0.0056 | ND | - | - |
2-Decylfuran | MS31 | 0032215 | ND | ND | ND | 0.0015 | - | - |
Piperenol A triacetate | MS32 | 0041535 | ND | 0.0129* | ND | ND | - | - |
Ginsenoyne G | MS33 | 0039589 | ND | ND | 0.0025 | ND | - | - |
Acetylpterosin C | MS34 | 0030764 | 0.0053* | ND | ND | ND | - | - |
1, 3, 11-Tridecatriene-5, 7, 9-triyne | MS35 | 0034294 | ND | ND | 0.0160 | ND | - | - |
Myrigalone A | MS36 | 0037245 | ND | ND | 0.0278* | 0.0256* | Antibacterial | [79] |
(Vitamins dan cofactors) | ||||||||
Nicotinic acid | VK1 | 0001488 | 0.0114 ± 0.0007 | ND | 0.0060 ± 0.0025 | 0.0076 ± 0.0009 | Increases HDL cholesterol and lowers triglycerides for the treatment of atherosclerosis | [29] |
Pantothenic acid | VK2 | 0000210 | ND | ND | ND | 0.0028 ± 0.0010 | Substrates for the synthesis of coenzyme A and ACP (acyl carrier protein) | [80] |
2-Hydroxypyridine | VK3 | 0013751 | 0.0008* | ND | ND | ND | - | - |
4-Methyl-5-thiazoleethanol | VK4 | - | 0.0175 ± 0.0014 | ND | 0.0066 ± 0.0021 | ND | - | - |
Trigonelline | VK5 | 0000875 | 0.0344 ± 0.0247 | ND | ND | ND | ● Increases cell sensitivity to anticancer and apoptotic drugs | [81] |
● Prevents gastric ulcer induced by indomethacin | [82] | |||||||
● Lowering blood sugar and lipid as well as increasing insulin sensitivity for diabetes | ||||||||
● Inhibits neurons loss in hypocampus | [83] | |||||||
7-Aminomethyl-7-carbaguanine | VK6 | 0011690 | ND | ND | ND | 0.0132* | - | - |
Pyridoxal | VK7 | 0001545 | ND | ND | 0.0066 ± 0.0021 | ND | ● Cofactors in various amino acids metabolism | [84] |
● Maintains the nervous systems in infants | [85] | |||||||
(Peptides) | ||||||||
Leucyl-valine | PD1 | 0028942 | ND | 0.0222 ± 0.0162 | ND | ND | Increases the expression of glutathione peroxidase, antioxidants and cell protection agents | [86] |
Leucyl-isoleucine | PD2 | 0028932 | ND | 0.0653 ± 0.0436 | ND | 0.0596 ± 0.0263 | Increases the stimulation of AMPK phosphorylation (5'-AMP protein kinase), monocytes, and platelets | [30] |
Note: The presentation of the relative value data for the compounds comes from the calculation of the average relative area of the compound from 3 replications ± deviation standard; ND = Not Detected; * = compound obtained only in 1 replication; Numbers on the same line with different letters indicate significant differences (p < 0.05). |