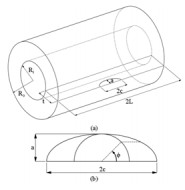
Citation: Mordechai Perl, Tomer Saley. The cumulative detrimental impact of pressure and autofrettage on the fatigue life of an externally cracked modern tank gun barrel[J]. AIMS Materials Science, 2019, 6(5): 833-851. doi: 10.3934/matersci.2019.5.833
[1] | Yanmei Zhang, Mu Fan, Zhongmin Xiao . Nonlinear elastic-plastic stress investigations on two interacting 3-D cracks in offshore pipelines subjected to different loadings. AIMS Materials Science, 2016, 3(4): 1321-1339. doi: 10.3934/matersci.2016.4.1321 |
[2] | Genshichiro Katsumata, Valéry Lacroix, Yinsheng Li . Effect of interaction of embedded crack and free surface on remaining fatigue life. AIMS Materials Science, 2016, 3(4): 1748-1758. doi: 10.3934/matersci.2016.4.1748 |
[3] | R. Citarella, V. Giannella, M. A. Lepore, J. Fellinger . FEM-DBEM approach to analyse crack scenarios in a baffle cooling pipe undergoing heat flux from the plasma. AIMS Materials Science, 2017, 4(2): 391-412. doi: 10.3934/matersci.2017.2.391 |
[4] | Pawan Kumar, B B Verma . Propagation of corrosion induced fatigue crack in aluminum alloy. AIMS Materials Science, 2022, 9(3): 512-521. doi: 10.3934/matersci.2022030 |
[5] | Jian-Feng Wen, Yong Zhan, Shan-Tung Tu, Fu-Zhen Xuan . A combination rule for multiple surface cracks based on fatigue crack growth life. AIMS Materials Science, 2016, 3(4): 1649-1664. doi: 10.3934/matersci.2016.4.1649 |
[6] | Masanori Kikuchi . Study on multiple surface crack growth and coalescence behaviors. AIMS Materials Science, 2016, 3(4): 1623-1631. doi: 10.3934/matersci.2016.4.1623 |
[7] | Kai Lu, Yinsheng Li . Fatigue crack growth calculations for two adjacent surface cracks using combination rules in fitness-for-service codes. AIMS Materials Science, 2017, 4(2): 439-451. doi: 10.3934/matersci.2017.2.439 |
[8] | R. Citarella, M. Lepore, M. Perrella, C. Calì . Multiple crack propagation by DBEM in a riveted lap-joint. AIMS Materials Science, 2016, 3(4): 1577-1586. doi: 10.3934/matersci.2016.4.1577 |
[9] | Pierre Dulieu, Valéry Lacroix . Mutual interaction of stress concentration and stress intensity factor between semi-circular notch and crack. AIMS Materials Science, 2016, 3(4): 1520-1533. doi: 10.3934/matersci.2016.4.1520 |
[10] | A.-V. Phan . Dynamic stress intensity factor analysis of the interaction between multiple impact-loaded cracks in infinite domains. AIMS Materials Science, 2016, 3(4): 1683-1695. doi: 10.3934/matersci.2016.4.1683 |
A: Crack depth; Ap: Paris' constant; c: Crack half length; E: Young's modulus; K00: Normalizing SIF (Eq 1); KI: Mode I SIF; KIA: Mode I SIF due to autofrettage; KIN: Combined SIF; KINmax: Maximum combined SIF; KIP: Mode I SIF due to internal pressure; KIP, avg: Average SIF along the crack front due to internal pressure; L: Cylinder's half length; np: Paris' constant; N: Number of fatigue cycles; Nf: Number of fatigue cycles to failure; P: Internal pressure; Ri: Inner radius of the barrel; Ro: Outer radius of the barrel; r, θ, z: Cylindrical coordinates; t: Barrel's wall thickness; Δϕ: Parametric angle interval; ε: Level of autofrettage; ν: Poisson's ratio; ξ: Intensity of the adverse effect of autofrettage on external cracks; σθθ: Hoop stress component; σy: Initial yield stress; ϕ: Parametric angle (Figure 1b); χ: Crack growth rate ratio; Hill: Hill's autofrettage; Hyd: Hydraulic autofrettage; Swage: Swage autofrettage; DEM: Displacement extrapolation method; DOF: Degrees of freedom; FE: Finite element; FEM: Finite element method; LEFM: Linear elastic fracture mechanics; MBT: Main battle tank; RSF: Residual stress field; SIF: Stress intensity factor.
In order to attain maximal firing range and armor penetrability, modern main battle tanks (MBTs) gun barrels are subjected to very high chamber pressure, severe temperature gradients, and a harsh corrosive environment. In order to acquire these capabilities, modern gun barrels are autofrettaged. Overstraining on the one hand enhances the internal pressure the gun can withstand and reduces its susceptibility to internal cracking at the bore. But on the other hand, autofrettage has an inherent detrimental effect resulting from the tensile hoop stress it induces at the outer part of the gun's wall, which increases sensitivity to external cracking. Gun barrels are overstrained by one of two processes: Hydraulic autofrettage and Swage autofrettage both of which bear these intrinsic advantageous and adverse effects.
The design of the barrel might introduce to its outer surface functional geometrical discontinuities such as keyseats, grooves, part-through holes, etc. Furthermore, as a result of operational field conditions, the outer surface of the barrel might get scratched. During firing, the exterior of the barrel is subjected to repeated action of high pressure loads, and simultaneously it is exposed to corrosive materials and an agammaessive environment. The presence of stress concentrators, the repeated loading, and the corrosive environment, may result in initiating a semi-elliptical radial crack growing from the barrel's external surface into the barrel's wall. This fatigue crack might become critical causing catastrophic failure of the barrel at a certain point [1].
Fatigue crack growth rate of such an external crack is controlled by the prevailing combined stress intensity factor (SIF) KIN, which consists of two components: KIP—the SIF caused by internal pressure; KIA—the positive SIF due to the tensile residual stresses induced by autofrettage. The combined SIF KIN = KIP + KIA depends on both the internal pressure in the barrel as well as on the residual hoop stress induced by autofrettage.
Recently, Perl and Saley [2] evaluated, for the first time, KIA distributions along the front of a single external crack resulting from the three types of autofrettage: Swage, Hydraulic, and Hill's. These distributions were calculated for a large number of crack configurations. In order to enable the evaluation of the barrel's fatigue life due to external cracking, KIN needs to be calculated. Therefore, the purpose of the present analysis to evaluate KIN values based on adequate KIP values, for a single external crack prevailing in an autofrettaged modern gun barrel. This is done by applying a novel, realistic, and experimentally based autofrettage model presented in [1]. This model enables a very accurate replication of both Hydraulic and Swage autofrettage RSFs in a fully or partially overstrained barrel. For comparison reasons, Hill's [3] RSF is also applied. SIFs for a typical smooth gun barrel of radii ratio R0/Ri = 2, for a wide range of crack depth to wall-thickness ratios (a/t = 0.005–0.1), for various crack ellipticities (a/c = 0.2–1.0), and for five levels of autofrettage (ε = 40%, 60%, 70%, 80% and 100%) are evaluated.
In Perl and Saley [2], a detailed description of the novel realistic autofrettage suggested by Perl and Perry [4] is presented. This model, which is totally based on the experimentally measured stress-strain curve under repeated reversed loading, accurately describes the material behavior including the Bauschinger effect in both tension and compression. The results of this new model applied to a gun made of a typical Cr–Ni–Mo–V barrel-steel (a modified AISI 4340) are presented in Figure 1 of [2] together with Hill's solution. Figure 1 in [2] represent the distribution of the hoop residual stress component, σResθθ, for Hydraulic, Swage and Hill's autofrettage, and for a partially or fully (ε = 40%, 70%, and 100%) overstrained barrel. The same exact results are herein used in the determination of the combined SIF KIN. The residual stress fields of all three types of autofrettage are embodied in the FE analysis using an equivalent temperature field emulating it very accurately. The discrete values of the equivalent temperature field are calculated using the general algorithm developed by Perl [5]. A detailed description of obtaining the equivalent temperature field and its incorporation in the FE analysis is given in Perl [5].
As in [2], the three dimensional analysis of the cracked barrel is based on linear elastic fracture mechanics (LEFM). The tube is modeled as an elastic cylinder of inner radius Ri, outer radius R0, and wall thickness t (R0/Ri = 2, and t = Ri) and length 2L. The cylinder contains an external, radial, semi-elliptical crack of length 2c and depth a. The cylinder containing one crack is presented in Figure 1a. In order to avoid end effects, the ratio of the cylinder length to its inner radius L/Ri is taken at least as 4.
The barrel is assumed to be made of a typical Cr–Ni–Mo–V barrel steel (a modified AISI 4340) with an initial yield stress of σy = 1050 MPa, Young modulus E = 203 GPa and Poisson's ratio ν = 0.3. As a modern tank gun is considered, the internal pressure is set to be p = 608 MPa. The SIFs KIP and KIN are calculated by the displacement extrapolation (DEM) and the J-integral methods, the same two methods used to calculate KIA in [2]. In the case of very shallow cracks of a/t = 0.005, SIFs are calculated along the crack front at intervals of Δϕ = 3.6° for cracks of a/c ≥ 0.4, and at intervals of Δϕ = 2.25° for cracks of a/c = 0.2. For deeper cracks (a/t ≥ 0.01), SIFs are calculated along the crack front at intervals of Δϕ = 1.8° for cracks of a/c ≥ 0.4, and at intervals of Δϕ = 1.125° for cracks of a/c = 0.2.
Only a quarter of the cylinder must be analyzed due to the various symmetries of the geometrical configuration (see Figure 2a). A toroidal shape volume consisting of four layers of 20-node isoparametric brick elements is meshed along the entire crack front (see Figure 2). In the first layer, the brick elements are collapsed to wedges forming singular elements [6], to accommodate the singular stress field in the vicinity of the crack front. On top of this layer, three additional layers of 20-node isoparametric brick elements are meshed. The rest of the model is meshed with 10-node tetrahedron elements. In order to maintain high accuracy, the elements near the crack front are chosen to be small, and their size is gradually increased when moving away from it (see Figure 2). The numerical model is solved using the commercial ANSYS 13.0 FE code [7]. The autofrettage residual stress field is incorporated in the FE analysis using an equivalent temperature field, as previously explained. Stress intensity factors are extracted from the FE results employing two methods built into ANSYS: the J-integral [8], and the crack-face displacement extrapolation method. SIFs are calculated at discrete points equally spaced along the crack front, identical to those employed in [2]. In order to maintain the same high accuracy attained for KIA [2] in calculating KIP and KIN, the same FE model is used with an identical element breakdown for each of the crack configurations solved.
In [2], the model was thoroughly validated. KIP values obtained by the present model were compared to values obtained by API-579-1 [9], using the weight function method. The present values were found to be within less than 1% of the AIP-579-1 values (see Figure 5 of reference [2]), except for the inner surface point where they differ by about 4%. Furthermore, convergence tests were conducted in order to determine the number of degrees of freedom (DOF) necessary to obtain high accuracy. Those tests show that above 1200000 DOF the error in the SIF is less than about 0.02%. Thus, in order to ensure the same accuracy for KIP and KIN as obtained for KIA in [2], 1600000 DOF are herein employed in all cases. All KIP values obtained in the present analysis are based on exactly the same mesh as the one used for KIA in [2], the same number of DOF, and are evaluated twice employing two independent methods: the J-integral and the DEM procedures.
Values of KIP—the SIF caused by internal pressure and the combined SIF KIN = KIP + KIA are evaluated for a single external radial crack prevailing in a typical barrel of radii ratio R0/Ri = 2, a wide range of relevant crack depth to wall-thickness ratios a/t = 0.005, 0.01, 0.04, 0.07, and 0.1, various crack ellipticities a/c = 0.2, 0.4, 0.6, 0.8, and 1.0, and five levels of Swage, Hydraulic and Hill's autofrettage ε = 40%, 60%, 70%, 80%, and 100%. In total, 375 different 3D external crack cases are analyzed. The values of KIA needed for the evaluation on KIN are imported from [2].
In order to obtain the value of the combined SIF KIN, it is necessary to superimpose the values of KIP on KIA. Thus, their values need to be normalized with respect to the same normalizing SIF which is chosen to be
K00=p√Ri | (1) |
KIP distributions along the crack front are presented separately for semi-circular cracks a/c = 1.0 and for semi-elliptical ones a/c < 1.0.
Figures 3 and 4 represent KIP/K00 distributions along the crack fronts of two semi-circular external cracks of depths a/t = 0.005 and a/t = 0.1 respectively. It is important to note that while in the case of an internal crack KIP results from the cumulative effect of both the hoop stress σθθ and the internal pressure p that fully penetrates the crack cavity, in the case of an external crack KIP results only from the prevailing hoop stress in the barrel's wall. The pattern in Figures 3 and 4 are qualitatively similar to those of their internal cracks counterparts [10]. However, in the case of external cracks, KIP/K00 maximum occurs near the barrel's outer surface (ϕ = 0°) and its value decreases monotonically towards the crack deepest points (ϕ = 90°). As previously noted, internal cracks unlike external cracks, are affected by the penetration of the internal pressure p into the crack's cavity. Thus, for a shallow crack, for example, a/t = 0.005, KIPmax of an internal crack is four times larger than that of the external one.
In the case of semi-elliptical cracks, the pattern of KIP/K00 distribution along their fronts is ellipticity dependent. Three distinct patterns can be observed:
Cracks of ellipticity 1.0 > a/c > 0.8
For crack ellipticities larger than a/c = 0.8, KIP/K00 distribution along the crack front is like that of semi-circular cracks as presented in Figures 3 and 4.
Cracks of ellipticity 0.8 > a/c ≥ 0
Typical KIP/K00 distributions along slender semi-elliptical cracks of a/c = 0.2 and of depths a/t = 0.005 and 0.1 are presented in Figures 5 and 6. In this case, KIP/K00 slightly drops from its initial value at the outer surface of the barrel reaching a minimum at ϕ = 4.5°, and then monotonically increases until reaching its maximum at the deepest point of the crack ϕ = 90°.
Cracks of ellipticity a/c = 0.8
Cracks of ellipticity a/c = 0.8, such as those presented in Figures 7 and 8, have an almost uniform distribution of KIP/K00 along their entire front and are commonly coined as iso-KI cracks. In Figures 7 and 8 the difference between the maximum and the minimum values of KIP/K00 is less than 4%, and thus, practically KIPmin/KIPmax ≈ 1. It is worthwhile noting that there is experimental evidence [11] that no matter what the initial ellipticity of a fatigue crack is, as it grows it tends to reach the ellipticity of a/c ≈ 0.8.
The fatigue process is momentarily controlled by the instantaneous prevailing maximal SIF. In the case of a non-autofrettaged barrel, it is KIPmax, the maximal SIF due to internal pressure that controls fracture processes, while in an autofrettaged vessel, fatigue and fracture are controlled by KINmax, the maximal combined SIF, which accounts for both effects: internal pressure and autofrettage.
In order to determine KINmax magnitude and its location along the crack front, one must first superimpose the distributions of KIP and KIA in order to obtain KIN distribution for any particular crack configuration. KIP values were calculated in the present analysis, and KIA values are imported from our previous paper [2]. To enable the superposition KIP and KIA were normalized to the same K00. As the normalizer involves the internal pressure (see Eq 1) and as KIA values depend on the material's properties (see section 3) one should bear in mind that the values of KIN/K00 and KINmax/K00 that will be presented hereafter, are a special case for the particular material chosen in this analysis, and for an internal pressure of p = 608 MPa.
Figures 9 and 10 represent the normalized combined SIF KIN/K00 distributions along the fronts of two typical semi-circular external cracks of relative depths of a/t = 0.005, and 0.1, respectively, prevailing in a fully overstrained barrel by all three types of autofrettage: Hydraulic, Swage and Hill's. All KIN/K00 distributions follow a similar pattern: maximum near the outer surface of the barrel, ϕ = 0°, and then a monotonic decrease towards the crack's deepest point at ϕ = 90°.
In both cases presented in Figures 9 and 10, KINmax/K00 for Swage autofrettage is 4–6% higher than that for Hydraulic autofrettage. Hill's "ideal" autofrettage yields much higher non-realistic KINmax/K00 values. To emphasize these results, Table 1 summarizes the relative values for KINmax for various crack depths for the three types of autofrettage.
Relative values of KINmax for ε = 100% | Relative crack depth | ||||
a/t = 0.005 | a/t = 0/01 | a/t = 0.04 | a/t = 0.07 | a/t = 1.00 | |
KSwageINmax/KHillINmax | 0.87 | 0.87 | 0.88 | 0.89 | 0.89 |
KHydINmax/KHillINmax | 0.83 | 0.84 | 0.84 | 0.84 | 0.84 |
KSwageINmax/KHydINmax | 1.05 | 1.04 | 1.05 | 1.06 | 1.06 |
From Table 1 it can be seen that in the case of an externally cracked barrel:
a. The difference between the combined SIF KIN for Swage and Hydraulic autofrettage is between 4% to 6%.
b. The combined SIF KIN for both Swage and Hydraulic autofrettage are lower than Hill's by about 13% to 17%.
The typical critical crack length for a modern gun barrel is (a/t)cr ≈ 0.1, and the combined SIF KIN for Hydraulic and Swage autofrettage is 13% to 17% lower than that of Hill's. Thus, based on Paris' law (np = 2.7 see [10]), it would mean that crack growth rate for Hydraulic and Swage would be about 60–69% slower than that predict by Hill's, resulting in a higher fatigue life of 65% to 45% relative the one evaluated by Hill's model. Furthermore, based on this data, the fatigue life of an Hydraulically autofrettage barrel would be at least 11% higher than that of a Swaged autofrettage barrel.
As in the cases of KIP/K00 and KIA/K00, the pattern of KIN/K00 distribution along the crack front of a semi-elliptical crack depends on the crack's ellipticity. Three distinct groups can be identified:
Cracks of ellipticity 1.0 > a/c > 0.8
For crack ellipticities larger than a/c = 0.8, KIN/K00 distributions along the crack front of external cracks is similar to those of semi-circular cracks as presented in Figures 9 and 10, and will not be further discussed herein.
Cracks of ellipticity 0.7 > a/c > 0
Typical KIN/K00 distributions for two slender semi-elliptical cracks (a/c = 0.2) of depths a/t = 0.005 and 0.1 are presented in Figures 11 and 12. In this cases, KIN/K00 slightly drops from its initial value at the outer surface of the barrel reaching a minimum at ϕ = 4.5°, and then monotonically increases until reaching its maximum at the deepest point of the crack ϕ = 90°. In Table 2, the relative values for KINmax for slender semi-elliptical cracks (a/c = 0.2) of various depths for the three types of autofrettage are presented.
Relative values of KINmax for ε = 100% | Relative crack depth | ||||
a/t = 0.005 | a/t = 0/01 | a/t = 0.04 | a/t = 0.07 | a/t = 1.00 | |
KSwageINmax/KHillINmax | 0.87 | 0.88 | 0.90 | 0.93 | 0.95 |
KHydINmax/KHillINmax | 0.84 | 0.84 | 0.85 | 0.85 | 0.86 |
KSwageINmax/KHydINmax | 1.04 | 1.05 | 1.06 | 1.09 | 1.10 |
KHydINmax/KHillINmax in this case is practically constant, like in the case of semi-circular cracks. KINmax for hydraulic autofrettage is about 14% to 16% lower than that's of Hill. However, unlike in the case of semi-circular cracks, KSwageINmax/KHillINmax increases with crack depth from 0.87 for the shallowest crack to 0.95 for the deepest one. Consequently, KSwageINmax/KHydINmax increases with crack depth and therefore, Hydraulic autofrettage would predict a longer fatigue life at least by about 11% than Swage autofrettage for a barrel with an external slender semi-elliptical crack.
Cracks of ellipticity 0.8 ≥ a/c ≥ 0.7
This group of cracks exhibits iso-KIN/K00 distributions as shown in Figures 13 and 14. KIN/K00 distributions for Hill's autofrettage are iso through the range of ellipticities 0.8 ≥ a/c ≥ 0.7. In the cases of Hydraulic and Swage autofrettage iso-KIN/K00 curves occur for cracks of ellipticity of a/c = 0.8.
Figure 15a-c represents KIN/K00 for an external radial semi-circular crack of depth a/t = 0.005 prevailing in an overstrained to three different levels of Hill's, swage and hydraulic autofrettage of ε = 100%, 70%, and 40%. Unlike in the case of an internally cracked tube [10], in the case of an externally cracked barrel a reduction in the level of overstraining has a positive effect in reducing the maximum prevailing SIF KINmax for all three types of autofrettage. In the case of an external semi-circular crack of depth a/t = 0.005, Table 3 represents the ratio of the maximum SIF in a fully autofrettaged barrel, KINmax (ε = 100%), to that of a partially autofrettaged tube for Hill's, swage, and hydraulic autofrettage levels of ε = 40%, 60%, and 70%.
Relative KINmax for various levels of autofrettage | Type of autofrettage | ||
Hill | Hydraulic | Swage | |
KINmax (ε = 100%)/KINmax (ε = 40%) | 2.00 | 1.85 | 1.85 |
KINmax (ε = 100%)/KINmax (ε = 60%) | 1.59 | 1.54 | 1.33 |
KINmax (ε = 100%)/KINmax (ε = 70%) | 1.41 | 1.39 | 1.22 |
As can be anticipated, unlike in the case of an internal crack, in the case of an external one the combined SIF KIN/K00 decreases as the level of overstraining decreases for all types of autofrettage. For example, if the level of autofrettage is reduced from ε = 100% to ε = 70%, KINmax decreases by 29%, 28%, and 18% for Hill's, Hydraulic and Swage autofrettage, respectively.
The intensity of the adverse effect of autofrettage on an external crack can be defined as Eq 2:
ξ(%)=KINmax−KIPmaxKIPmax⋅100% | (2) |
ξ represents the percentage by which KIA, the SIF due to autofrettage, increases the prevailing effective SIF, KIN above and beyond KIP, the SIF due only to internal pressure. The larger ξ, the higher the adverse effect of autofrettage on external cracking of the barrel.
Figure 16a-c exhibits the intensity of the adverse effect of full overstraining (ε = 100%), on external cracks of various depth and ellipticities for the three types of autofrettage. When cracks are shallow a/t ≤ 0.01, the most substantial region of crack growth, ξ is practically constant and independent of crack depth and ellipticity, and has the values of ξ ≈ 160%, 130% and 120% for Hill's, Swage and Hydraulic autofrettage, respectively. As previously stated, the most of the barrel's fatigue life is spent when cracks are very shallow. Crack growth rate in an autofrettaged barrel is given by Paris' Law as:
(dadn)autofrettaged=Ap(KINmax)np | (3) |
and for a non-autofrettaged barrel by:
(dadn)non−autofrettaged=Ap(KIPmax)np | (4) |
dividing Eq 3 by Eq 4 and using Eq 2 yields:
χ=(dadn)autofrettaged/(dadn)non−autofrettaged=(1+ξ)np | (5) |
Please note that in Eq 5 ξ is taken as a decimal fraction.
In order to obtain a preliminary estimate of the effect of full autofrettage (ε = 100%) on the total fatigue life of an externally cracked barrel Nf, let's assume for a gun barrel steel np = 2.7, and that χ21, and thus ξ, are practically constant throughout the entire fatigue process for very shallow cracks (see Figure 16). Based on these simplifying assumptions, the following total fatigue life ratios are obtained:
1χ2 usually changes throughout the fatigue process as it depends on the instantaneous crack ellipticity and depth, the barrel's geometry and its level of autofrettage. In fatigue life calculations, ξ needs to be updated throughout the process.
((Nf)non−autofrettaged(Nf)autofrettaged)Swage=(1+ξ)np≈9.5 | (6) |
((Nf)non−autofrettaged(Nf)autofrettaged)Hyd=(1+ξ)np≈8.4 | (7) |
In this case, autofrettage reduces the fatigue life of an externally cracked barrel by a factor of 9.5 and 8.4 for Swage and Hydraulic autofrettage, respectively. These rough results reflect the tremendous detrimental effect autofrettage has on shortening, by almost an order of magnitude, the fatigue life of an externally overstrained cracked barrel as compared to a non autofrettaged tube. Furthermore, it can be seen that in the case of external cracking unlike in the case of internal cracking [10]. Hydraulic autofrettage has a 13% advantage over Swage autofrettage. The high ξ value predicted by Hill's model is definitely non-realistic as it predicts a reduction in the fatigue life by a factor of almost 14.
In the case of deeper cracks, 0.1≥ a/t ≥ 0.01, while for Hill's and Hydraulic autofrettage, ξ slowly decreases with crack depth in a practically linear manner for Swage autofrettage ξ slightly increases with crack depth. This difference is a direct result of the different residual hoop stress distributions for the three types of autofrettage (see Figure 1 of [2]).
In order to further investigate the intensity of the adverse effect of overstraining on the fatigue life, ξ was evaluated for barrels containing a single external semi-circular crack of depths 0.1≥ a/t ≥ 0.005 fully or partially overstrained (ε = 100%, 70%, and 40%) by the three types of autofrettage (a) Hill, (b) Swage, and (c) Hydraulic is presented in Figure 17. In this case of a semi-circular external crack, ξ is practically crack-depth independent. As could have been anticipated, as the level of autofrettage is reduced the intensity of its adverse effect on external cracks decreases. For example, when the level of overstraining is reduced from 100% to 70%, ξ decreases by about: 80%, 38%, 65% for Hill's, Swage and Hydraulic autofrettage, respectively.
The combined SIF KIN = KIP + KIAfor a single external radial 3D crack prevailing in an overstrained smooth gun barrel was evaluated for 375 cases examining the effects of the type and the level of autofrettage, as well as the influence of the crack's geometry. KIN values were evaluated for three types of autofrettage: Swage, Hydraulic and Hill's, for five levels of overstraining ε = 40%, 60%, 70%, 80%, and 100%, for crack depths of a/t = 0.005, 0.01, 0.04, 0.07, and 0.1, and for various crack ellipticities a/c = 0.2, 0.4, 0.6, 0.8, and 1.0. Furthermore, in order to keep uniform accuracy, KIP values for all the above geometrical crack configurations were evaluated using an identical mesh to the one used for the evaluation of the corresponding KIA in [2].
All three types of autofrettage are found to considerably shorten the fatigue life of an externally cracked barrel, as compared to a non-autofrettaged barrel's fatigue life. However, the magnitude of this adverse effect is autofrettage-type dependent. Unlike in the case of internal cracking [2], in the case of external cracking Hydraulic autofrettage is found to be superior to the Swage one predicting a 13% higher barrel's fatigue life, as presented in the case in section 5.4. Hill's "ideal" autofrettage is found to be non-realistic, yielding exaggerated underestimates of the barrel's fatigue life. This is a direct consequence of the fact that Hill's residual stress field (RSF) ignores the Bauschinger effect, which in the case of the realistic Swage and Hydraulic RSF, results in a substantial reduction of the material's yield stress and thus, in lower KIN values.
Reducing the level of autofrettage reduces considerably the intensity of adverse effect of overstraining on external cracks for all types of autofrettage and thus, considerably prolonging the barrel's fatigue life. For example, reducing ε from 100% to 70% results in a decrease of ξ of about 80%, 38%, 65% for Hill's, Swage and Hydraulic autofrettage, respectively.
The authors declare no conflict of interests.
[1] | Kapp JA (1985) Predicting catastrophic outside diameter initiated fatigue failure of thick-walled cylinders using low cycle fatigue data. ARLCBTR-85035, Benet Weapons Laboratory, Watervliet. |
[2] | Perl M, Saley T (2019) The detrimental effect of Swage and Hydraulic autofrettage on externally cracked modern gun barrels. Def Technol 15 146-153. |
[3] | Hill R (1950) The Mathematical Theory of Plasticity, New York: Oxford University Press. |
[4] | Perl M, Perry J (2006) An experimental-numerical determination of the three dimensional autofrettage residual stress field incorporating bauschinger effect. J Press Vess-T ASME 128: 173-178. |
[5] |
Perl M (1988) The temperature field for simulating partial autofrettage in an elasto-plastic thick-walled cylinder. J Press Vess-T ASME 110: 100-102. doi: 10.1115/1.3265552
![]() |
[6] |
Barsom RS (1976) On the use of isoparametric finite elements in linear fracture mechanics. International. Int J Numer Meth Eng 10: 25-37. doi: 10.1002/nme.1620100103
![]() |
[7] | ANSYS Release 13.0 (2010) Available from: https://www.ansys.com/products/structures. |
[8] | Rice JR (1968) A path independent integral and the approximate analysis of strain Concentration by notched and cracks. J Appl Math 35: 379-386. |
[9] | API 579-1/ASME FFS-1 Fitness for Service (2007) Available from: gost-snip.su › download › api_5791_asme_ffs1_fitnessforservice. |
[10] | Perl M, Saley T (2017) Swage and hydraulic autofrettage impact on fracture endurance and fatigue life of an internally cracked smooth gun barrel part II-The combined effect of pressure and overstraining. Eng Fract Mech 182c: 386-399. |
[11] |
Lin XB, Smith RA (1998) Fatigue growth prediction of internal surface cracks in pressure vessels. J PressVess-T ASME 120: 17-23. doi: 10.1115/1.2841878
![]() |
1. | M. Perl, T. Saley, Internal Versus External Cracking—Their Impact on the Fatigue Life of Modern Smoothbore Autofrettaged Tank Gun Barrels, 2021, 143, 0094-9930, 10.1115/1.4048068 | |
2. | Naveed Hussain, Faisal Qayyum, Riffat Asim Pasha, Masood Shah, Development of multi-physics numerical simulation model to investigate thermo-mechanical fatigue crack propagation in an autofrettaged gun barrel, 2020, 22149147, 10.1016/j.dt.2020.09.005 | |
3. | Deepak Kumar, Sahil Kalra, Mayank Shekhar Jha, A concise review on degradation of gun barrels and its health monitoring techniques, 2022, 142, 13506307, 106791, 10.1016/j.engfailanal.2022.106791 | |
4. | Mohammad Sajjad Khodayari, Rahman Seifi, Bursting Pressure of the Autofrettaged and Interferenced Double-Layer Cylinder with an Internal Surface Crack, 2024, 24, 1547-7029, 721, 10.1007/s11668-024-01876-z |
Relative values of KINmax for ε = 100% | Relative crack depth | ||||
a/t = 0.005 | a/t = 0/01 | a/t = 0.04 | a/t = 0.07 | a/t = 1.00 | |
KSwageINmax/KHillINmax | 0.87 | 0.87 | 0.88 | 0.89 | 0.89 |
KHydINmax/KHillINmax | 0.83 | 0.84 | 0.84 | 0.84 | 0.84 |
KSwageINmax/KHydINmax | 1.05 | 1.04 | 1.05 | 1.06 | 1.06 |
Relative values of KINmax for ε = 100% | Relative crack depth | ||||
a/t = 0.005 | a/t = 0/01 | a/t = 0.04 | a/t = 0.07 | a/t = 1.00 | |
KSwageINmax/KHillINmax | 0.87 | 0.88 | 0.90 | 0.93 | 0.95 |
KHydINmax/KHillINmax | 0.84 | 0.84 | 0.85 | 0.85 | 0.86 |
KSwageINmax/KHydINmax | 1.04 | 1.05 | 1.06 | 1.09 | 1.10 |
Relative KINmax for various levels of autofrettage | Type of autofrettage | ||
Hill | Hydraulic | Swage | |
KINmax (ε = 100%)/KINmax (ε = 40%) | 2.00 | 1.85 | 1.85 |
KINmax (ε = 100%)/KINmax (ε = 60%) | 1.59 | 1.54 | 1.33 |
KINmax (ε = 100%)/KINmax (ε = 70%) | 1.41 | 1.39 | 1.22 |
Relative values of KINmax for ε = 100% | Relative crack depth | ||||
a/t = 0.005 | a/t = 0/01 | a/t = 0.04 | a/t = 0.07 | a/t = 1.00 | |
KSwageINmax/KHillINmax | 0.87 | 0.87 | 0.88 | 0.89 | 0.89 |
KHydINmax/KHillINmax | 0.83 | 0.84 | 0.84 | 0.84 | 0.84 |
KSwageINmax/KHydINmax | 1.05 | 1.04 | 1.05 | 1.06 | 1.06 |
Relative values of KINmax for ε = 100% | Relative crack depth | ||||
a/t = 0.005 | a/t = 0/01 | a/t = 0.04 | a/t = 0.07 | a/t = 1.00 | |
KSwageINmax/KHillINmax | 0.87 | 0.88 | 0.90 | 0.93 | 0.95 |
KHydINmax/KHillINmax | 0.84 | 0.84 | 0.85 | 0.85 | 0.86 |
KSwageINmax/KHydINmax | 1.04 | 1.05 | 1.06 | 1.09 | 1.10 |
Relative KINmax for various levels of autofrettage | Type of autofrettage | ||
Hill | Hydraulic | Swage | |
KINmax (ε = 100%)/KINmax (ε = 40%) | 2.00 | 1.85 | 1.85 |
KINmax (ε = 100%)/KINmax (ε = 60%) | 1.59 | 1.54 | 1.33 |
KINmax (ε = 100%)/KINmax (ε = 70%) | 1.41 | 1.39 | 1.22 |