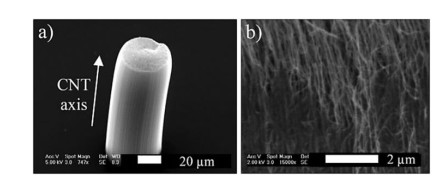
Citation: Robiul Islam Rubel, Md. Hasan Ali, Md. Abu Jafor, Md. Mahmodul Alam. Carbon nanotubes agglomeration in reinforced composites: A review[J]. AIMS Materials Science, 2019, 6(5): 756-780. doi: 10.3934/matersci.2019.5.756
[1] | Nataliya A. Sakharova, Jorge M. Antunes, Andre F. G. Pereira, Jose V. Fernandes . Developments in the evaluation of elastic properties of carbon nanotubes and their heterojunctions by numerical simulation. AIMS Materials Science, 2017, 4(3): 706-737. doi: 10.3934/matersci.2017.3.706 |
[2] | Mateo Duarte, Johan A. Oquendo, Sebastián Vallejo, Johnattan Vargas, Yamile Cardona-Maya, Cesar A. Isaza . Fabrication of FRP/CNT hybrid laminate composites and their effect on interlaminar and mechanical properties. AIMS Materials Science, 2024, 11(6): 1125-1144. doi: 10.3934/matersci.2024054 |
[3] | Mateo Duarte, Andrés Benítez, Katiuska Gómez, Benjamín Zuluaga D, Juan Meza, Yamile Cardona-Maya, Juan S. Rudas, César Isaza . Nanomechanical characterization of a metal matrix composite reinforced with carbon nanotubes. AIMS Materials Science, 2020, 7(1): 33-45. doi: 10.3934/matersci.2020.1.33 |
[4] | Okechukwu Okafor, Abimbola Popoola, Olawale Popoola, Samson Adeosun . Surface modification of carbon nanotubes and their nanocomposites for fuel cell applications: A review. AIMS Materials Science, 2024, 11(2): 369-414. doi: 10.3934/matersci.2024020 |
[5] | Jinji Luo, Beate Krause, Petra Pötschke . Melt-mixed thermoplastic composites containing carbon nanotubes for thermoelectric applications. AIMS Materials Science, 2016, 3(3): 1107-1116. doi: 10.3934/matersci.2016.3.1107 |
[6] | Carlos A. Sánchez, Yamile Cardona-Maya, Andrés D. Morales, Juan S. Rudas, Cesar A. Isaza . Development and evaluation of polyvinyl alcohol films reinforced with carbon nanotubes and alumina for manufacturing hybrid metal matrix composites by the sandwich technique. AIMS Materials Science, 2021, 8(2): 149-165. doi: 10.3934/matersci.2021011 |
[7] | Mohd Shahneel Saharudin, Rasheed Atif, Syafawati Hasbi, Muhammad Naguib Ahmad Nazri, Nur Ubaidah Saidin, Yusof Abdullah . Synergistic effects of halloysite and carbon nanotubes (HNTs + CNTs) on the mechanical properties of epoxy nanocomposites. AIMS Materials Science, 2019, 6(6): 900-910. doi: 10.3934/matersci.2019.6.900 |
[8] | Harikrishnan Pulikkalparambil, Jyotishkumar Parameswaranpillai, Jinu Jacob George, Krittirash Yorseng, Suchart Siengchin . Physical and thermo-mechanical properties of bionano reinforced poly(butylene adipate-co-terephthalate), hemp/CNF/Ag-NPs composites. AIMS Materials Science, 2017, 4(3): 814-831. doi: 10.3934/matersci.2017.3.814 |
[9] | D. M. S. Costa, M. A. R. Loja . Assessing the static behavior of hybrid CNT-metal-ceramic composite plates. AIMS Materials Science, 2016, 3(3): 808-831. doi: 10.3934/matersci.2016.3.808 |
[10] | DavidWood, Dale K. Hensley, Nicholas Roberts . Enhanced thermal conductance of polymer composites through embeddingaligned carbon nanofibers. AIMS Materials Science, 2016, 3(3): 851-861. doi: 10.3934/matersci.2016.3.851 |
CNTs have regarded as nano-scale reinforcements elements led to promising results in improving a wide spectrum of properties for an engineering problem. Since the discovery of CNTs by Iijima [1] in 1991, it is considered ideal reinforcements of various range of composites due to their exceptional strength, high Young's modulus (YS) and low density [2,3,4,5,6,7]. It is viewed as a 1D substance and may arrange in one direction or randomly distributed. Randomly disperse CNTs decreases with higher weight/volume fractions owing to the formation of CNT agglomerates [8,9]. This agglomeration is sometimes referring as clustering or bundling effect in many researches. Figure 1a shows the CNT pillar regarding the direction of the CNT axis and Figure 1b shows the alignment of the 1D CNTs. Randomly orientated, agglomeration/agammaegation and in homogeneous distributions are influenced by the presence of a chemical substance (chemical treatment), surface coatings, post-treatment strongly influences physical properties of CNTs reinforced due to the high surface-to-volume ratios of CNTs in the matrix [7,10,11].
The matrixes are pertaining to metallic matrices, ceramics matrices, polymer matrices, fiber matrices, etc. Researchers are using continuous and discontinuous reinforcements with CNTs to enhance the properties of different matrices approximately from the last two decades. Even hybrid composites containing CNTs have tried by many research groups for few sophistical purposes.
CNTs/polymer matrix composites, CNTs/metal matrix composites, CNTs/fiber matrix composites, CNTs/graphene matrix composites and CNTs/ceramics matrix composites have been praised for having extraordinary features like strength, electrical and thermal properties, light weight, stiffness, chemical inertness, damping properties, etc. than any other standard composites [12,13,14,15]. Since the overall electrical performance of CNT reinforced composites dominated by the inter-molecular conductive network, the influence of the CNTs entanglement is a critical issue [16,17]. The use of CNTs are now not limited with absolute engineering concept, rather has been expanded for energy, environmental, and medical branches [18]. CNTs regarded as quasi 1D nanomaterials that have a tendency to agammaegate in bundles when forming composites [19]. Dispersion of CNTs has few health effects and seems that agglomeration likely inspires this. CNTs have a more possibility to be aerosolized. CNTs reinforced composites during abrasion released protruding CNTs, agglomerates of CNTs, and freestanding CNTs [20,21,22]. In spite of having marvelous properties, CNTs is sometimes avoided due to its agglomeration effect. Another form of carbon is becoming popular such as graphene. Graphene is being used to form metal, polymer matrix composites [23].
The CNTs has now classified as single wall carbon nanotubes (SWCNTs), double wall carbon nanotubes (DWCNTs), multiwall carbon nano tubes (MWCNTs) and so forth depending on their constructions/microstructure. However, for CNTs reinforced composites microstructure variation, damage and agglomeration behavior of CNTs pre-consideration for property improvement [24,25,26]. Any metallic matrix, alloy show cluster of reinforced particles among the grain boundary area depending on their vol% or wt%, the porosity of based metals, and grain size [27,28]. CNTs have a strong intermolecular attraction called van der Waals force [29,30]. CNTs tube to tube interactions also reduced physical properties compared to those in a dispersed state [31].
This force entangles the triangular lattice structure of CNTs and produces bundling effect called clustering or agglomeration [32,33]. Even agglomeration exists irrespective of SWCNTs, DWCNTs, Amino-modified double wall carbon nanotubes (DWCNTs–NH2), MWCNTs and COOH-modified thin multi-wall nanotubes (MWCNTs–COOH) [33]. Agglomeration of CNTs affects the size (diameter/length) and distributions of filer materials/particles and overall is likely to decrease the aspect ratio, while significant insights have been achieved on various processing techniques, post-processing, strengthening, treatment, etc [34]. Many unresolved issues still need to be addressed theoretically as well as experimentally to harness the maximum benefit of CNTs reinforced composites. Thus, the choice of the matrix for reinforcement, processing route, and the processing parameters are very important.
On the other hand, those are mandatory criteria to provide a uniform distribution of CNTs in the base matrix and good matrix-reinforcement interface. The surface of CNTs clusters are highly tortuous and considerably influence by processing techniques and chemical treatment solution. A good chemical agent can potentially reduce agglomeration tendency even after post processing [35]. To proclaim the uniform dispersion of CNTs in the matrix, several methods have been reported based on the processing route. They are ball milling, sonication, stirring (mechanical/magnetic), etc. followed by post-treatment [36,37,38,39]. The post-treatment also contribute for untangling of CNTs clusters and must not damage its structure. This clustering or agglomeration behavior is also real for any other composites that produce binary phase. The grain boundary becomes the agglomeration zone in two-phase CNTs-matrix interface [40,41]. A cluster of catalytic chemical vapor deposition-grown multi-wall carbon nanotubes is shown in Figure 2.
CNTs not only form clusters during reinforcement, but it also remains in cluster form when it is even pure. Most of the researchers worked with clustered CNTs when received from any company irrespective the way they produced [43]. In most of the composites, after a certain amount of CNTs, there is no significant additional reinforcing effect due to agglomeration [44]. Even after acidic, alcoholic, milling, functionalizing is done to reduce the agglomeration tendency, CNTs agglomerated at high contain rate. In this review, we have studied the effect of agglomeration on metal matrix, polymer, epoxy resin, ceramic matrix composites. In this work, we have presented some graphical and statistical evidence after reviewing numerous research papers.
The agglomeration or clustering is a more acute problem for metal matrix composites. It is hard to disperse CNTs inside the metal matrix to prevent the formation of large CNTs clusters or agammaegates due to their electrostatic and van der Waals forces as well as the density difference between CNTs and metal matrix composites [45,46]. The agglomeration and poor distribution of CNTs as reinforcement particles within a metal matrix depend on many factors such as homogeneity, the orientation of CNTs, nanotube matrix adhesion, nanotube aspect ratio, and the volume/weight fraction of nanotubes in the matrix [47]. The most common ever tried is Aluminum (Al) matrix. Simões et al. [48] worked on the 1.00 vol% of CNTs reinforced in the Al matrix and found enhance properties by Powder Metallurgy (PM) route with Sonication techniques for dispersion. However, the SEM image in Figure 3 shows the darks spotted region around the grain boundaries and depicted as clustering or agglomeration of CNTs. Better dispersion method produces less clustering effect up to 1.0 vol% of CNTs in Al. The size and cluster increase with vol% of CNTs increase in reinforcement. In the same work, the researcher has summarized the clustering effect in an Al/CNTs and Ni/CNT composites depending on the grain size presented in Table 1. In their work, the introduction of more than 1 vol% CNTs reduce the mechanical properties while enhancing the clustering effect and soften the formed composite. This introduction also creates non-uniformed dispersion of CNTs with poor texture effect.
Composites | CNT content (vol%) | Porosity and CNT clusters (vol%) | Maximum size of CNT clusters (μm) | Average grain size (μm) |
Al/CNT | 0 | 1.00 | - | 17 |
0.50 | 4.88 | 89 | 16 | |
0.75 | 6.53 | 102 | 15 | |
1.00 | 5.95 | 78 | 16 | |
1.50 | 7.38 | 177 | 16 | |
Ni/CNT | 0 | 1.05 | - | 15 |
0.50 | 3.22 | 83 | 14 | |
0.75 | 3.96 | 155 | 13 | |
1.00 | 6.67 | 137 | 14 | |
1.50 | 12.47 | 310 | 16 |
Agglomeration not only effects on the mechanical properties but also on the machining characteristics. Woo et al. [49] tried an exceptional method of producing Al/CNTs powder by cryogenic milling. Al particles have ductility compared to 5 wt% and 10 wt% Al/CNTs composites. When sintered, Al particle welding may be more pronounced leading to the large particle agglomerates. The change of agglomeration is presented in Raman analysis publicized in Figure 4 showing the growth of clusters spotted on the surface. These clusters adversely affect the machining process and subsequent micro/nano finishing operations.
In Al/CNTs, CNTs exist in the form of bigger agglomerates and are co-embedded in the matrix. Figure 4 shows the comparison of optical microscopy and Raman images of Al powder and Al/CNT powder particles milled for different duration of time. The Raman image shows the distribution of the integrated intensity (area under the curve) of the CNT Raman signal in the wave number range of 1320–1420 cm−1 [49].
Powder can rolling technique was successfully implemented in order to get carbon nanotubes reinforced aluminum strips and better dispersion of the nanotubes was made possible [50]. Good uniform distribution of CNTs without agglomeration of Al matrix reported being found in ultrasonic and ball mill attrition [51,52]. Pham et al. [44] observed that CNTs percentage could be increased up to 3 wt% for Copper (Cu)/CNTs composite with an effective increase of Brinell hardness as presented in Figure 5. An increasing trend of CNTs drops the hardness due to clustering or agglomeration of CNTs in a large group. Some researcher is suggesting chemical treatment of CNTs before composite formation to prevent the clustering effect. However, the dispersion of Cu particles can be enhanced by molecular level mixing of Cu particles in functionalized CNTs in a solvent. Presence of CNTs clusters in processed composites especially when CNTs are more than 1 wt%, has often led to a reduction in the properties instead of improvement. For example, the effect of CNTs agglomeration on the conductivity of Magnesium (Mg) matrix has been studied by Nai et al. [54]. Liu et al. [55] suggested Ultrasonic dispersion to disperse CNTs in Mg alloy (AZ91D) and using a dispersion agent due to the strong interface bond between CNTs and Mg alloy matrix.
During a review of metal matrix nanocomposites, Malaki et al. [56] emphasized the use of dispersing techniques (e.g., melt ultra-sonication) to avoid agglomeration of nanoparticles. However, in their work the de-agglomeration of nanoparticle clusters in the matrix is possible but need special in-situ observation to develop a dynamic principle. Park et al. [57] attributed the difficulty of dispersing the 1–5 wt% CNTs in Mg matrix due to the stickiness of CNTs. This group coated CNTs with Silicon (Si) to reduce the agglomeration behavior and sintered the composite. However, the results are not as imperative as expected. Thus, they further smash the sintered product using zirconia ball (10 mm dia) in a tri-axial vibrating-type ball miller with a rolling rate of 1200 rpm for 12 h in presence of argon gas. The resulting uniformed dispersion of MWCNTs is shown in Figure 6.
However, sintering and hot extrusion as the post-treatment process damage CNT structure. Even for the successful sintering CNTs agglomerates around the grain boundaries [58]. Researchers are continuously working to enhance the interfacial characteristics of CNT in the matrix as reinforcement elements. Reinforced Mg–CNTs composites are more adversely affected by the clustering effect of CNTs compare to Nickel (Ni) coated Ni/CNTs in Mg matrix. The consequence has discussed by Nai et al. [54]. They observed simultaneous enhancements of the micro-hardness, ultimate tensile strength and yield strength (0.2%) by 41%, 39%, and 64% respectively for the Mg/CNTs (0.3 wt%) composites with Ni coating on CNTs.
From Figure 7a [54] it is depicted that small clusters of CNTs are formed in some areas of the monolithic Mg/CNTs reinforced composites. In these cluster zones, CNTs come into contact directly among themselves other rather than with the Mg particles. Thus, effective bonding is hindered between the CNTs and the Mg particles resulting in the associated porosity and low fracture toughness. In contrast, the addition of Ni coating on CNTs prevents the clustering of Ni–CNTs (Figure 7b) [59]. Yamanaka et al. [60] used laser near-net shape melting processing of Ni/MWCNT composites. Physical properties such as thermal conductivity reduce up to half of the original conductivity of pure Ni. The reasons are reported to be the presence of a large amount of porosity and CNTs degradation into carbides, a large amount of porosity and CNT degradation into carbides and agglomerations also mention by other few authors [60,61,62]. The sintered direction has also the influence of thermal conductivity up to 3 vol% and 4 vol% [60]. Beyond this percentage, conductivity has reported being decreasing constantly due to large agglomeration phenomenon. The large number of CNTs in the Ni matrix caused restriction of CNTs movement and form cluster. For Ni/MWCNTs, the 5 vol% MWCNTs SEM image is shown below. The presence of cluster CNTs, as in Figure 8, is confirmed in the CNTs concentrated parts of the sample.
In 1 vol% Cu/CNT composite formation by Equal Channel Angular Pressing (ECAP), the researcher has primarily used ethanol and vibration treatment for an hour with an ultrasonic cleaner to isolate agglomerated CNTs powder. Afterward, severe plastic deformation by ECAP techniques appears effective in de-agglomerated the CNTs in the Cu matrix for multiple numbers of treatment [63]. An increasing number of ECAP passes can effectively break the cluster CNT agglomerates to form better dispersion of CNTs in the Cu matrix as shown in Figure 9 [64].
In a similar type of work, ball milled Al/CNTs powders have used for bonding Mg sheet. In this case, Al/CNTs function as an intermetallic compound containing and occurring CNTs inter-diffusion into the Mg sheet. Due to shear flow, CNTs become separated from Al/CNTs bond and eventually distributed uniformly in Mg matrix [54,65]. Researcher working on the CNTs agglomeration undoubtedly concluded that wt/vol% increase of CNTs as reinforced particles accelerated the clustering effect [66]. Akinwekomi et al. [67] attempted to develop Mg/CNTs composite by rapid sintering method. The properties improvement remains acceptable up to 3 vol% of CNTs. Increase the volume fraction of CNTs to 5 vol% in the composite mixture is not successful, as agglomerates of CNTs remain on the alloy powder (dashed circle) in Figure 10b, c.
To reduce the agglomeration and clustering, in AZ61/5 vol% CNT is milled for 60 min. The milling of the composite mixture for 60 min does not significantly improve the dispersion of the CNTs and some agglomerates can still be seen in Figure 10c. Therefore, further Mg-based AZ61 matrix is restricted to reinforced with a maximum of 3 vol% of CNTs processing. CNTs agglomerations exist irrespective of the processing techniques and found for Mg-based alloy process through stir friction process. Magnesium alloy (RZ 5) with Boron Carbide, MWCNTs particles reinforcement are founded with no agglomeration effect [68]. Figure 11 shows that Mg particles become shattered with no agglomeration effect. However, this research is based on the grain size difference of the matrix and reinforcement materials and low contaminations. The density of the CNT reinforced composites possibly comparable up to 8 wt% CNTs. Addition of CNTs beyond this amount causes a decrease of composite density drastically due to agglomeration and clustering [69,70]. Electroless deposition and spark plasma sintering are capable to remove the agglomeration problem of the MWCNTs and the grain growth problem of the nanocrystalline Cu matrix [71]. In a similar manner, a lot of researches have done on such a study. A statistical analysis is shown in Table 2.
Matrix | Reinforcement & strengthening method | CNTs (vol/wt%) | Presence of agglomerates & remarks | Ref. |
Cu | Ultrasonic cleaning + particles composite system + spark plasma sintering | 5, 10 wt% | Yes. CNTs are aggregated into ropes or knotted lumps due to strong inter-tube van der Waals attraction. | [6] |
Cuprous oxide | Vacuum hot pressing at H2 atmosphere | 0, 1, 3, 5 wt% | Yes, at 5 wt%. Thermal conductivity decreases with the increase of the CNTs concentration. | [72] |
Al | Ball milling + Sonication | 2 wt% | Yes. Adverse effects on the properties of final composite products due to the increased porosity. | [73] |
2024Al matrix | Cold isostatic pressing + Hot pressing | 1 wt% | Yes, but low. Elastic modulus and the tensile strength were enhanced markedly. | [74] |
Aluminum–silicon alloy powders | Spray drying | 5, 10 wt% | Yes, 10 wt%. Partial CNT surface damage in case of the 10 wt% CNT coating due to CNT mesh formation and smaller size of spray dried agglomerate. | [75] |
Al | Ball milling | 2 wt% | Yes. Presence of clusters at the early stage of milling which acts as the precipitates results in the lower Young's modulus. | [76] |
Al | Ball milling + Nanodispersion | 0.8, 1.6 vol% | Yes. Poor dispersion of CNTs in the matrix exhibited a non-uniform fracture surface. No aggregations in secondary steps are claimed. | [77] |
Magnesium oxychloride + epoxy | Magnesium oxychloride cement pastes were prepared by ratios of MgO:MgCl2 = 2.2:1. Then coated with epoxy/CNTs | 0, 0.02 wt% | Yes. Water consistency value increases by the addition of CNTs due to that the additional high specific surface area acts as an interface for an efficient stress transfer and causes the strong tendency of the CNTs to form agglomerates. | [78] |
AZ91 + Mg | Melt stirring + high-pressure die casting | 0.1, 0.5, 1 wt% | Yes, at 1 wt%. Agglomerates of entangled MWCNTs with a size of up to 2 µm can be observed. | [79] |
Al | Induction melting | 0, 0.1, 0.2 vol% | No. No cluster or segregation of the nanotubes was seen. | [80] |
Mg | Hot isostatic pressing under high pressure. | 1, 2 wt% | Yes. Homogeneous dispersion of MWCNTs in Mg matrix is obtained. | [81] |
Ag | Modified molecular level mixing method | 0, 6, 12 vol% | Yes, at 12 vol%. Electrical conductivity reduces. | [82] |
Cu | Melt stirring | 0.1 wt% | Yes. The micrograph shows that the raw MWCNTs are agglomerated in big bundles. This act as defects instead of reinforcements. | [83] |
Al (AA5XXX) | Ball milling + hot isostatic pressed + extrusion | 2 wt% | Yes. CNTs clusters were dispersed and claimed as uniform distribution. | [84] |
Polymer and ceramics have shown well dispersion characteristics than metal matrix composites and are being considered since the innovation of CNTs in 1991 [53]. If CNTs disperse in the matrix, they can be hardly identified due to their small size, the only agglomerated portion could be visualized. This agglomeration can further be promoted by a temperature increase in pre- or post-processing of the composites is shown in Figure 12. Thus, before composite formation, the cured CNTs is better to keep into the refrigerator to prevent agglomeration growth [42]. The CNTs network in epoxy resin is affected by the shear force rates. This shearing force with low shear rates (0.001–0.1 s−1) produce CNTs agglomeration while shearing with high shear rates (1–100 s−1) destroyed the clusters. The electrical percolation threshold for this type of composites depends on the calendered and non-calendered CNT/epoxy suspensions.
In a similar type of work, Bisphenol F-based epoxy resin/CNTs were investigated. Beforehand, the processed mixture was cured with diethyl toluene diamine. The optical micrographs and Raman analysis show reduced agglomeration and a homogeneous distribution of MWCNTs in the epoxy matrix. The solvent-free method is the reasons behind this reduced tendency [85]. The better the dispersion of CNTs in epoxy resin, the better the electrical conductivity is achievable [85,86,87]. Shi et al. [88] and Alian et al. [89] develop an elastic model to analysis the agglomeration behavior mathematically. The model was also followed by RAE model which is an analytical micromechanics method. Rafiee et al. [90] used RAE method to study the young modulus of CNTs/polymer composites. They studied agglomeration, non-uniformed dispersion and wavy pattern of CNTs as random parameters by Equivalent fiber theory [91], N3M method [92]. The results concluded are the change of Young modulus with single/multilayer CNTs construction, clustering size, etc. in the two-phase sphere model.
Peng et al. [93] develop modeling to create a 2D finite element modeling of nanocomposite with polymer nanoparticles. They showed that the degree of clustering has a strong influence on the elastic modulus of the nanocomposite. The agglomeration effect can be reduced by using treated CNTs in reinforcement.
Ma et al. [94] has worked on the amino-functionalization to reduce the clustering effects. The clustering effect further forms CNTs ropes and tangle larger. This amino-functionalization has proven effective up to 1 wt% of CNTs in epoxy–polymer composites. This can be justified by the SEM image is shown in Figure 13. Javadinejad et al. [95] applied numerical FEM to demonstrate the clustering effect of CNTs in the composite as shown in Figure 14. Figure 14 shows a 3D view of four colonies in different volume fractions of CNTs. The colonization/agglomeration effect increases with the increase of vol% of CNTs in epoxy resin is shown in Figure 15.
Polymer/CNT composites, ultrasound and high-speed shearing is a powerful dispersion method. They are the simplest and suitable to increase the dispersion of CNTs in a polymer matrix [96]. If the dispersion is not worked effectively, it may be leading to many defect sites (agglomerate, bundle together and entangle) in the composites and limit the efficiency of CNTs on polymer matrices. Nguyen-Tran et al. [97] have found agglomeration for carbon fiber-reinforced polyamide-6/polypropylene composites. CNTs of 1.5 wt% significantly introduce agglomeration defects and reduce mechanical properties.
Figure 16 shows the image of a fracture surface also contains agglomerated CNTs that are claimed as low fracture toughness. Villoria et al. [98] compute the properties of CNT clusters by their developed model as in Eqs 1 and 2. The model could be applied to any type of fiber reinforcement where agglomeration of CNTs is present.
kdsc=km+(kcluster−km)Cc1+kcluster−kmkm+4μm3 | (1) |
μdsc=μm[1−15(1−vm)(1−μclusterμm)Cc7−5vm+2(4−5vm)μclusterμm] | (2) |
Where Cc refers to the volume fraction of agglomerations zone which is related to the overall CNTs fraction by Vf=CfCc, Cf being the CNT concentration in of a cluster.
Li et al. [99] obtained the same effect for CNT-reinforced carbon/carbon composites. As CNTs content increases up to 1.2 wt%, inter-laminar shearing strength increases by 30%. But, like the other CNTs shearing strength starts to decrease as CNTs content increases up to 1.5 wt%. Agglomeration attributed to a lot of CNTs content ends up in the decrease of contacted space between CNTs and matrix and reduces the result of resistance to delamination. Hence, inter-laminar shearing strength decreases. The SEM image of the failure surface of nanocomposites is given below in the Figure 17.
Agglomeration of CNTs leads to non-homogenous dispersion with small assemblies of CNT reinforcements in certain points throughout the composite. That causes a decrease in the mechanical properties [100,101]. Some researchers have proposed degassing the CNTs powder to remove moisture from the powders. The moisture content of only 0.1 wt% shows considerable agglomeration [102]. Moisture added weight of the composites and act as an interfacial agent of intermolecular attraction. The dispersion defect and agglomeration are clearly visible for Casini et al. [103] experiments. Inadequately scattered CNTs in the polymer matrix appeared by the biggest size of agglomerates. Figure 18 displays the representative microscopy images of polypropylene compounds containing 0.5 vol% for each kind of CNTs considered are non-functionalized, functionalized with amino groups (–NH2), functionalized with carboxyl groups (–COOH) [103]. Long CNTs have a diameter of 8 nm, and length of 10–30 μm. Therefore, aspect ratio becomes 2500 for long CNTs than the short CNTs. Entangling and agglomeration of CNTs are accelerated by this high aspect ratio [104]. Krause et al. [105] worked to gain better electrical properties of polycarbonate/CNT composites. These composites required a high degree of CNT dispersion within the thermoplastic matrix.
They observed clustering of CNTs in polycarbonate due to strong interactions between neighbored CNTs caused by high van der Waals forces and physical entanglements. The research group suggested shortening of CNTs length by ball milling. This suggestion is better to explain by Ahn et al. [106] who described that MWCNTs tend to be compacted by the impact of the milling balls. Afterward, SEM image shows CNTs form agglomerates with increased size during the ball milling process. On the same time, these agglomerated CNTs adversely affect the dispersibility. The researcher has simulated the effect of CNTs agglomeration in computer-generated samples. For example, Tarlton et al. [107] developed an algorithm called Monte Carlo hopping algorithm showing that uniformly disperses decrease conductivity of chae with the sacrifice of mobility and vice versa. They found that when the CNTs focus was near the permeation edge, a progressively uniform CNTs dissemination could be accomplished and lead to an improved conductivity.
Recently it has been shown how bundling or agglomeration of DWCNTs affects the behavior of the composite. Dispersion of the CNTs within the polymer matrix plays a key role in the preparation of the conducting nanocomposites. TEM and Raman spectroscopy have been used by Tishkova et al. [108] to characterize the distribution of the DWCNTs in the polymer matrix. Figure 19 represents examples of the TEM images of 0.8 wt% DWCNTs/poly (ether-ether-ketone) composite (PEEK). Figure 19a shows a DWCNTs agglomerated surrounding by PEEK matrix particles. From the images of Figure 19b, it is revealed an inhomogeneous dispersion of CNTs in the polymer matrix and most of the nanotubes form large agglomerates.
Domínguez et al. [32] show the bundling effect SWCNTs in a polymer matrix by Raman analysis as shown in Figure 20. They characterized the dispersion of SWCNTs by X-ray diffraction, Raman Spectroscopy, and TEM is shown in Figure 20a, b, c, respectively. Figure 20a indicated desegregation because of the bundle's lattice peaks disappearance [109]. Figure 20b supported the de-bundling of SWCNTs due to the radial breathing mode shift displacement [110]. From TEM micrographics of Figure 20c, it is clear that individual polymer warps the CNTs and produce bundles of 3–4 tubes at a different spot.
Again, MWCNTs filled polypropylene (PP) nanocomposites prepared through PP/MWNT master-batch dilution process was found with insignificant agglomeration tendency. The master-batch dilution assisted with a high shear extruder eliminates significant agglomeration of MWCNTs [111]. However, this happens for only 1 wt% of CNTs. Increase in wt% agammaegates CNTs as clusters clearly visible by SEM images is shown in Figure 21. Kumar et al. [112] describe an express method called Representative Volume Element (RVE) model to incorporate the effects of CNTs agglomeration on the elastic behavior of CNTs reinforcement in polymer composites. The vertically aligned CNTs–polymer architecture presented by García et al. [8] and Bello et al. [113] has described reducing the agglomeration effect. CNTs potentially modify glass–fiber reinforced polymer (GFRP) composite laminates. Researches tried to form such composite laminates using ultrasonication and the hand lay-up method [114]. CNTs content of 0.75% resin (phr) improves interlaminar shear strength and flexural strength 15.7% and 9.2%, respectively. Though agglomeration reduces the interlaminar shear strength.
With further increase of the content of CNTs become easily, induce an agglomeration of CNTs is shown in Figure 22. When MWCNTs is epoxidized with polysulfide resin to form CNTs/epoxy polysulfide nanocomposites, agglomeration in the nanocomposites with a higher content of MWCNTs act as large particles. The clusters then create space/void to contain higher apparent filler loading. These agglomerates confine polymer particles in the void space between MWCNTs and effectively reduce the volume fraction of the epoxy polysulfide matrix [115,116]. CNTs/polysulfone composites with 0.068 wt% CNTs also agglomerate similarly, but CNTs-to-CNTs contact after the percolating network increases conductivity for this case [117].
In the word of Yurdakul et al. [118] electric field effects on CNTs/vinyl ester has affected by the agglomeration of CNTs. Composite formed by vinyl ester matrix containing low content (0.05, 0.1 and 0.3 wt%) of DWCNTs and MWCNTS with and without amine functional groups brings synergetic effect to reorient the agglomerated CNTs clusters. This synergetic effect modifies the distribution of radicals in the resin. In bulk composite (large CNTs contents) due to the synergetic effect, field-induced agglomeration and cluster formation occurs. Li et al. [119] studied electrical conductivity about the CNTs/polymer composites. As the CNTs concentration increases within the composite, the number of the molecular interfaces increases. From Figure 23, we can see that dielectric constant increases with increasing MWCNT concentration. When pristine MWCNTS reaches 0.06 vol% and oxidized MWCNTs reaches 0.08 vol%, they are at percolation threshold energy. More concentration of CNTs beyond this value will agglomerate MWCNTs. CNTs produces cluster in cement pastes [120]. MWCNTs (up to 0.5 wt% of cement) with/without surfactant were characterized. Composites with surfactant has found with 0.25% increased tensile strength and better mechanical properties. In a similar manner, a lot of researches have done on such a study. A statistical (Table 3) is given below.
Matrix | Reinforcement & strengthening method | CNTs vol/wt% | Presence of agglomerates & remarks | Ref. |
Epoxy system | Sonication | 0.025, 0.05 wt% | Yes. Good dispersion was not achieved. | [33] |
- | - | - | Yes. A review paper that has described a lot about agglomeration of CNTs in the polymer matrix. | [121] |
Polypropylene | Melt mixing | 0.5–7.5 wt% | Yes. Low agglomeration effect due to melt dispersion. Lower matrix viscosity promotes secondary agglomeration during the compression molding step. | [122] |
Polyvinyl alcohol | Used prepared sample to study machining | 1, 2, 4 wt% | Yes. CNTs loading beyond 4 wt%, the CNTs were observed to form clusters within the polymer matrix. | [123] |
Polystyrene | Injection moulding process | 20 wt% | Yes. Monte Carlo model was used for simulation to predict the electrical conductivity. The agglomeration has been neglected. | [124] |
Polymer | Injection molding | 1 wt% | Yes. Both partial alignment and MWCNTs agglomeration were observed. | [125] |
Polyvinyl alcohol | Solvent method | Not mentioned | Yes. Substantial agglomerates of nanotubes are visible. | [126] |
Vinyl alcohol | Melt mixing | 0.1, 0.3, 0.5, 1 wt% | Yes. Entanglement of CNTs reduce conductivity. | [127] |
Epoxy | Sonication | Varying ranges | Yes. Varying cluster/aggregate depending on the composites. | [128] |
Vinyl alcohol | Gum arabic treatment | 2 wt% | Yes. Interfere with the tensile properties. | [129] |
Modelling the behavior of CNTs composites is therefore a long queue of scientific works, both theoretical and experimental approaches. Kundalwal et al. [130] worked on the micro-mechanics of CNTs/fiber composites and discussed about some theoretical model. Kundalwal also proposed SWCNTs/fiber analysis model called Fuzzy model [131]. Typical issue covered by the model is agglomeration of CNTs, the misalignment and the difficulty in manufacturing very long CNTs. The same model is quite effective for polymer also. Feng et al. [132] used micro and nano approaches to elucidates the key factors of CNTs agglomeration, that influence the mechanical properties of formed composites. Wernik et al. [133] analyzed agglomeration in embedded nano-reinforced adhesive for the case of 3.0 wt% CNT loading. Results shows that composite may begin to degrade for agglomeration. They suggested to investigate the effect of CNTs agglomeration. Thus research introduces additional parameters related to the size and density of the agglomerates with the conclusion of a micro model. Some research made on multiscale model of hybrid composites such as Eshelby–Mori–Tanaka model isotropic hybrid material [134,135]. This scheme takes into account the agglomeration of the nanoparticles in the CNTs/polymer/fiber laminated composites.
This review on CNTs agglomeration comprises the overview of reinforcement structure, the bonding method, dispersion method, and consequences of clustering of CNTs along with their effects. The review has retrieved the following outcomes by a sharp understanding of the cited literature. They are:
(a) CNTs remained in agammaegated form when prepared due to van der Walls forces. Dispersion method can considerably reduce this tendency. However, re-agglomeration is common when contamination increases.
(b) Metal matrix CNTs reinforced composites have more agglomeration than polymer, epoxy, ceramics, etc.
(c) Agglomeration/clustering of CNTs has a direct effect on the thermal, electrical, and mechanical properties of composites. They act as a barrier to load transfer among the grains. Thus all physical properties are reduced.
(d) Maximum volumetric/weight percentage addition is limited with a maximum of 20% for metal matrix, and 5 % for polymer, epoxy, ceramics etc. However, 2–5% CNTs/metallic matrix and 0–2% CNTs/polymer, epoxy, ceramics, etc. are recorded common. Agglomeration occurs around the grain boundaries.
(e) Few rare earth/CNTs are available materials, but their production method is the major concentrated rather than agglomeration.
The authors declare no conflict of interest.
[1] |
Iijima S (1991) Helical microtubules of graphitic carbon. Nature 354: 56–58. doi: 10.1038/354056a0
![]() |
[2] |
Zhu X, Zhao YG, Wu M, et al. (2016) Effect of initial aluminum alloy particle size on the damage of carbon nanotubes during ball milling. Materials 9: 173. doi: 10.3390/ma9030173
![]() |
[3] |
Thostenson ET, Ren Z, Chou TW (2001) Advances in the science and technology of carbon nanotubes and their composites: a review. Compos Sci Technol 61: 1899–1912. doi: 10.1016/S0266-3538(01)00094-X
![]() |
[4] |
Baksh SR, Lahiri D, Agarwal A (2010) Carbon nanotube reinforced metal matrix composites-a review. Int Mater Rev 55: 41–64. doi: 10.1179/095066009X12572530170543
![]() |
[5] |
Dai H (2002) Carbon nanotubes: opportunities and challenges. Surf Sci 500: 218–241. doi: 10.1016/S0039-6028(01)01558-8
![]() |
[6] |
Chu K, Guo H, Jia C, et al. (2010) Thermal properties of carbon nanotube–copper composites for thermal management applications. Nanoscale Res Lett 5: 868–874. doi: 10.1007/s11671-010-9577-2
![]() |
[7] | Sun Y (2010) Mechanical properties of carbon nanotube/metal composites [PhD's thesis]. University of Central Florida, USA. |
[8] |
Garcia EJ, Hart AJ, Wardle BL, et al. (2007) Fabrication and nanocompression testing of aligned carbon-nanotube-polymer nanocomposites. Adv Mater 19: 2151–2156. doi: 10.1002/adma.200700237
![]() |
[9] |
Yengejeh SI, Kazemi SA, Öchsner A (2017) Carbon nanotubes as reinforcement in composites: A review of the analytical, numerical and experimental approaches. Comput Mater Sci 136: 85–101. doi: 10.1016/j.commatsci.2017.04.023
![]() |
[10] | Wardle BL (2009) Nanocomposites and nano-engineered composites reinforced with aligned carbon nanotubes. Proceedings of the 17th International Conference on Composite Materials, Edinburgh, UK, 27–31. |
[11] | Munir KS, Kingshott P, Wen C (2014) Carbon nanotube reinforced titanium metal matrix composites prepared by powder metallurgy-a review. Crit Rev Solid State 40: 38–55. |
[12] | Khare R, Bose S (2005) Carbon nanotube based composites-a review. J Miner Mater Char Eng 4: 31–46. |
[13] | Ajayan PM, Schadler LS, Braun PV (2003) Nanocomposite Science and Technology, Germany: Wiley-VCH, 1–75. |
[14] |
Breuer O, Sundararaj U (2004) Big returns from small fibers: a review of polymer/carbon nanotube composites. Polym Compos 25: 630–645. doi: 10.1002/pc.20058
![]() |
[15] | Yang BJ, Cho KJ, Kim GM, et al. (2014) Effect of CNT agglomeration on the electrical conductivity and percolation threshold of nanocomposites: a micromechanics-based approach. Comp Model Eng Sci 103: 343–365. |
[16] |
Pan Y, Weng GJ, Meguid SA, et al. (2011) Percolation threshold and electrical conductivity of a two-phase composite containing randomly oriented ellipsoidal inclusions. J Appl Phys 110: 123715. doi: 10.1063/1.3671675
![]() |
[17] |
Azarniya A, Safavi MS, Sovizi S, et al. (2017) Metallurgical challenges in carbon nanotube-reinforced metal matrix nanocomposites. Metals 7: 384. doi: 10.3390/met7100384
![]() |
[18] |
Lyu H, Gao B, He F, et al. (2017) Ball-milled carbon nanomaterials for energy and environmental applications. ACS Sustain Chem Eng 5: 9568–9585. doi: 10.1021/acssuschemeng.7b02170
![]() |
[19] | Wang D, Chen L (2010) Temperature and pH-responsive ―smart‖ carbon nanotube dispersions. In: Balasubramanian K, Burghard M, Carbon Nanotubes: Methods and Protocols, 1 Ed., New York: Humana Press, 27–38. |
[20] |
Schlagenhauf L, Nuesch F, Wang J (2014) Release of carbon nanotubes from polymer nanocomposites. Fibers 2: 108–127. doi: 10.3390/fib2020108
![]() |
[21] |
Methner M, Crawford C, Geraci C (2012) Evaluation of the potential airborne release of carbon nanofibers during the preparation, grinding, and cutting of epoxy-based nanocomposite material. J Occup Environ Hyg 9: 308–318. doi: 10.1080/15459624.2012.670790
![]() |
[22] |
Golanski L, Guiot A, Pras M, et al. (2012) Release-ability of nano fillers from different nanomaterials (toward the acceptability of nanoproduct). J Nanopart Res 14: 962. doi: 10.1007/s11051-012-0962-x
![]() |
[23] |
Rashad M, Pan F, Tang A, et al. (2015) Development of magnesium-graphene nanoplatelets composite. J Compos Mater 49: 285–293. doi: 10.1177/0021998313518360
![]() |
[24] |
Jiang LY, Huang Y, Jiang H, et al. (2006) A cohesive law for carbon nanotube/polymer interfaces based on the van der Waals force. J Mech Phys Solids 54: 2436–2452. doi: 10.1016/j.jmps.2006.04.009
![]() |
[25] |
Hertel T, Walkup RE, Avouris P (1998) Deformation of carbon nanotubes by surface van der Waals forces. Phys Rev B 58: 13870–13873. doi: 10.1103/PhysRevB.58.13870
![]() |
[26] | Yamamoto T, Miyauchi Y, Motoyanagi J, et al. (2004) Improved bath sonication method for dispersion of individual single-walled carbon nanotubes using new triphenylene-based surfactant. Jpn J Appl Phys 47: 2000–2004. |
[27] |
Subramanian J, Seetharaman S, Gupta M (2015) Processing and properties of aluminum and magnesium based composites containing amorphous reinforcement: a review. Metals 5: 743–762. doi: 10.3390/met5020743
![]() |
[28] |
Ballóková B, Sülleiová K, Besterci M, et al. (2016) Micromechanisms of fracture of magnesium based composite after superplastic deformation. Powder Metall Prog 16: 117–122. doi: 10.1515/pmp-2016-0010
![]() |
[29] | Lee JH, Rhee KY (2009) Silane treatment of carbon nanotubes and its effect on the tribological behavior of carbon nanotube/epoxy nanocomposites. J Nanosci Nanotechno 9: 6948–6952. |
[30] | Chen Y, Conway M, Fitzgerald J (2003) Carbon nanotubes formed in graphite after mechanical grinding and thermal annealing. Appl Phys A 76: 633–636. |
[31] |
Reich S, Thomsen C, Maultzsch (2004) Carbon nanotubes-basic concepts and physical properties. ChemPhysChem 5: 1914–1915. doi: 10.1002/cphc.200400387
![]() |
[32] | Gonzalez-Domínguez JM, Maser W, Benito A, et al. (2008) Carbon nanotubes dispersion towards polymer integration. NanoSpain2008, Braga, Portugal. |
[33] | Inam F, Peijs T (2007) Re-agglomeration of carbon nanotubes in two-part epoxy system; influence of the concentration. Proceedings of the 5th International Bhurbhan Conference on Applied Science and Technology, Islamabad, Pakistan. |
[34] | Song WS (2016) Percolation, electrical conductivity, and emi shield analysis of CNT composites [BD's thesis]. Georgia Institute of Technology, USA. |
[35] | Deriabina O, Lebovka N, Bulavin L, et al. (2013) Regulation of dispersion of carbon nanotubes in a mixture of good and bad solvents. arXiv 1304.5679. |
[36] |
Arai S, Saito T, Endo M (2010) Cu–MWCNT composite films fabricated by electrodeposition. J Electrochem Soc 157: D147–D153. doi: 10.1149/1.3280034
![]() |
[37] |
Smart SK, Ren WC, Cheng HM, et al. (2007) Shortened double-walled carbon nanotubes by high-energy ball milling. Int J Nanotechnol 4: 618–633. doi: 10.1504/IJNT.2007.014756
![]() |
[38] |
Simões S, Viana F, Reis MAL, et al. (2016) Microstructural characterization of aluminum-carbon nanotube nanocomposites produced using different dispersion methods. Microsc Microanal 22: 725–732. doi: 10.1017/S143192761600057X
![]() |
[39] |
Simões S, Viana F, Reis MAL, et al. (2014) Improved dispersion of carbon nanotubes in aluminum composites. Compos Struct 108: 992–1000. doi: 10.1016/j.compstruct.2013.10.043
![]() |
[40] |
Rashad M, Pan F, Asif M, et al. (2015) Improved mechanical proprieties of ―magnesium based composites‖ with titanium-aluminum hybrids. J Magnesium Alloy 3: 1–9. doi: 10.1016/j.jma.2014.12.010
![]() |
[41] |
Lamura G, Andreone A, Yang Y, et al. (2007) High-crystalline single-and double-walled carbon nanotube mats grown by chemical vapor deposition. J Phys Chem C 111: 15154–15159. doi: 10.1021/jp073940f
![]() |
[42] | Lott JZ (2009) Study of the network formation of carbon nanotubes in epoxy matrices for electrical conductivity improvement [PhD's thesis]. Technical University, Germany. |
[43] | Vallejo SS (2014) Development of carbon nanotube-reinforced nickel matrix composites: processing, microstructure and physical properties [PhD's thesis]. Saarland University, Germany. |
[44] |
Pham VT, Bui HT, Tran BT, et al. (2011) The effect of sintering temperature on the mechanical properties of a Cu/CNT nanocomposite prepared via a powder metallurgy method. Adv Nat Sci Nanosci Nanotechnol 2: 015006. doi: 10.1088/2043-6262/2/1/015006
![]() |
[45] |
Neubauer E, Kitzmantel M, Hulman M (2010) Potential and challenges of metal-matrix-composites reinforced with carbon nanofibers and carbon nanotubes. Compos Sci Technol 70: 2228–2236. doi: 10.1016/j.compscitech.2010.09.003
![]() |
[46] | Tian L, Zheng L, Ren L, et al. (2018) Future prospects of carbon nanotubes reinforced metal matrix composite. Res Dev Material Sci 3: 226–228. |
[47] |
Esawi AMK, Morsi K, Sayed A, et al. (2009) Fabrication and properties of dispersed carbon nanotube-aluminum composites. Mater Sci Eng A 508: 167–173. doi: 10.1016/j.msea.2009.01.002
![]() |
[48] |
Simões S, Viana F, Reis MAL, et al. (2017) Aluminum and nickel matrix composites reinforced by CNTs: dispersion/mixture by ultrasonication. Metals 7: 279. doi: 10.3390/met7070279
![]() |
[49] |
Woo DJ, Bottolfson BA, Brewer LN, et al. (2014) Low temperature synthesis of carbon nanotube-reinforced aluminum metal composite powders using cryogenic milling. J Mater Res 29: 2644–2656. doi: 10.1557/jmr.2014.300
![]() |
[50] |
Esawi AMK, Borady MAE (2008) Carbon nanotube-reinforced aluminum strips. Compos Sci Technol 68: 486–492. doi: 10.1016/j.compscitech.2007.06.030
![]() |
[51] | Zare H, Toroghinejad MR, Meratian M (2012) Dispersion of multi walled carbon nanotubes in aluminum powders with ultrasonic and ball mill attrition. Proceedings of the International Conference on Mechanical, Automotive and Materials Engineering, Dubai, 218–220. |
[52] | Toozandehjani M, Matori KA, Ostovan F, et al. (2017) Carbon nanotubes reinforced aluminum matrix composites-A review of processing techniques. PJSRR 3: 70–92. |
[53] |
Cha S, Kim KT, Arshad SN, et al. (2005) Extraordinary strengthening effect of carbon nanotubes in metal-matrix nanocomposites processed by molecular-level mixing. Adv Mater 17: 1377–1381. doi: 10.1002/adma.200401933
![]() |
[54] |
Nai, MH, Wei J, Gupta M (2014) Interface tailoring to enhance mechanical properties of carbon nanotube reinforced magnesium composites. Mater Des 60: 490–495. doi: 10.1016/j.matdes.2014.04.011
![]() |
[55] |
Liu SY, Gao FP, Zhang QY, et al. (2010) Fabrication of carbon nanotubes reinforced AZ91D composites by ultrasonic processing. T Nonferr Metal Soc 20: 1222–1227. doi: 10.1016/S1003-6326(09)60282-X
![]() |
[56] | Malaki M, Xu W, Kasar AK, et al. (2019). Advanced metal matrix nanocomposites. Metals 9: 330. |
[57] |
Park Y, Cho K, Park I, et al. (2011) Fabrication and mechanical properties of magnesium matrix composite reinforced with Si coated carbon nanotubes. Procedia Eng 10: 1446–1450. doi: 10.1016/j.proeng.2011.04.240
![]() |
[58] | Umma A, Maleque MA, Iskandar IY, et al. (2012) Carbon nano tube reinforced aluminium matrix nano-composite: a critical review. AJBAS 6: 69–75. |
[59] | Dey A, Pandey KM (2015) Magnesium metal matrix composites-A review. Rev Adv Mater Sci 42: 58–67. |
[60] |
Yamanaka S, Gonda R, Kawasaki A, et al. (2007) Fabrication and thermal properties of carbon nanotube/nickel composite by spark plasma sintering method. Mater Trans 48: 2506–2512. doi: 10.2320/matertrans.MRA2007084
![]() |
[61] |
Stahl H, Appenzeller J, Martel R, et al. (2000) Intertube coupling in ropes of single-wall carbon nanotubes. Phys Rev Lett 85: 5186–5189. doi: 10.1103/PhysRevLett.85.5186
![]() |
[62] | Hwang JY, Singh ARP, Banerjee R, et al. (2009) Processing and thermal conductivity of carbon nanotube-reinforced nickel matrix composites. Proceedings of the ASME 2009 Heat Transfer Summer Conference Collocated with the InterPACK09 and 3rd Energy Sustainability Conferences, San Francisco, USA. |
[63] | Pham Q, Jeong YG, Yoon SC, et al. (2007) Carbon nanotube reinforced metal matrix nanocomposites via equal channel angular pressing. Mater Sci Forum 534–536: 245–248. |
[64] | Pham Q, Jeong YG, Hong SH, et al. (2006) Equal channel angular pressing of carbon nanotube reinforced metal matrix nanocomposites. Key Eng Mater 326–328: 325–328. |
[65] |
Yoo SJ, Han SH, Kim WJ (2012) Magnesium matrix composites fabricated by using accumulative roll bonding of magnesium sheets coated with carbon–nanotube-containing aluminum powders. Scripta Mater 67: 129–132. doi: 10.1016/j.scriptamat.2012.03.040
![]() |
[66] |
Zare Y (2016) Study of nanoparticles aggregation/agglomeration in polymer particulate nanocomposites by mechanical properties. Compos Part A-Appl S 84: 158–164. doi: 10.1016/j.compositesa.2016.01.020
![]() |
[67] |
Akinwekomi AD, Law WC, Choy MT, et al. (2018) Processing and characterisation of carbon nanotube-reinforced magnesium alloy composite foams by rapid microwave sintering. Mater Sci Eng A 726: 82–92. doi: 10.1016/j.msea.2018.04.069
![]() |
[68] |
Vedabouriswaran G, Aravindan S (2018) Development and characterization studies on magnesium alloy (RZ 5) surface metal matrix composites through friction stir processing. J Magnes Alloy 6: 145–163. doi: 10.1016/j.jma.2018.03.001
![]() |
[69] |
Tu JP, Yang YZ, Wang LY, et al. (2001) Tribological properties of carbon-nanotube-reinforced copper composites. Tribol Lett 10: 225–228. doi: 10.1023/A:1016662114589
![]() |
[70] |
He C, Zhao N, Shi C, et al. (2007) An approach to obtaining homogeneously dispersed carbon nanotubes in Al powders for preparing reinforced Al-matrix composites. Adv Mater 19: 1128–1132. doi: 10.1002/adma.200601381
![]() |
[71] |
Wang H, Zhang ZH, Hu ZY, et al. (2016) Synergistic strengthening effect of nanocrystalline copper reinforced with carbon nanotubes. Sci Rep 6: 26258. doi: 10.1038/srep26258
![]() |
[72] | Xiong Y, Chen X (2016) Carbon nanotube reinforced Cu matrix composites by hot pressing for CNTs embedded composite particles. Academia J Sci Res 4: 075–080. |
[73] | Javadi AH, Mirdamadi S, Faghisani MA, et al. (2011) Investigation of new method to achieve well dispersed multiwall carbon nanotubes reinforced Al matrix composites. Int J Mate Metall Eng 5: 906–912. |
[74] |
Deng C, Zhang X, Wang DZ, et al. (2007) Preparation and characterization of carbon nanotubes/aluminum matrix. Mater Lett 61: 1725–1728. doi: 10.1016/j.matlet.2006.07.119
![]() |
[75] |
Bakshi SR, Singh V, Seal S, et al. (2009) Aluminum composite reinforced with multiwalled carbon nanotubes from plasma spraying of spray dried powders. Surf Coat Tech 203: 1544–1554. doi: 10.1016/j.surfcoat.2008.12.004
![]() |
[76] |
Ostovan F, Matori KA, Toozandehjani M, et al. (2016) Nanomechanical behavior of multi-walled carbon nanotubes particulate reinforced aluminum nanocomposites prepared by ball milling. Materials 9: 140. doi: 10.3390/ma9030140
![]() |
[77] |
Noguchi T, Magario A, Fukazawa S, et al. (2004) Carbon nanotube/aluminium composites with uniform dispersion. Mater Trans 45: 602–604. doi: 10.2320/matertrans.45.602
![]() |
[78] | Kandeel A, Etman M, Sharara AM, et al. (2010) Effect of carbon nanotubes (CNTs) on the physicomechanical properties of magnesium oxychloride cement pastes. Proceedings of the International Conference On Nano-Technology for Green and Sustainable Construction, Cairo, Egypt. |
[79] |
Li Q, Rottmair CA, Singer RF (2010) CNT reinforced light metal composites produced by melt stirring and by high pressure die casting. Compos Sci Technol 70: 2242–2247. doi: 10.1016/j.compscitech.2010.05.024
![]() |
[80] |
Mansoor M, Shahid M (2016) Carbon nanotube-reinforced aluminum composite produced by induction melting. J Appl Res Technol 14: 215–224. doi: 10.1016/j.jart.2016.05.002
![]() |
[81] | Yang J (2005) Carbon nanotubes as reinforcements and interface modifiers in metal matrix composites [PhD's thesis]. Federal Institute of Technology, Switzerland. |
[82] | Pala H, Sharma V, Kumar R, et al. (2012) Facile synthesis and electrical conductivity of carbon nanotube reinforced nanosilver composite. Z Naturforsch A 67a: 679–684. |
[83] | Hippmann S, Li Q, Addinal R, et al. (2013) Carbon nanotubes-reinforced copper matrix composites produced by melt stirring. Proc IMechE Part N: J Nanoeng Nanosys 227: 63–66. |
[84] | Stein J, Lenczowski B, Fréty N, et al. (2001) High-performance metal matrix composites reinforced by carbon nanotubes. Proceedings of the 18th International Conference on Composites Materials, Jeju Island, Korea. |
[85] |
Gupta ML, Sydlik SA, Schnorr JM, et al. (2013) The effect of mixing methods on the dispersion of carbon nanotubes during the solvent-free processing of multiwalled carbon nanotube/epoxy composites. J Polym Sci Pol Phys 51: 410–420. doi: 10.1002/polb.23225
![]() |
[86] | Barrau S, Demont P, Perez E, et al. (2003) Effect of palmitic acid on the electrical conductivity of carbon nanotubes-epoxy resin composites. Macromolecules 36: 9678–9680. |
[87] |
Song YS, Youn JR (2005) Influence of dispersion states of carbon nanotubes on physical properties of epoxy nanocomposites. Carbon 43: 1378–1385. doi: 10.1016/j.carbon.2005.01.007
![]() |
[88] |
Shi DL, Feng XQ, Huang YY, et al. (2004) The Effect of nanotube waviness and agglomeration on the elastic property of carbon nanotube-reinforced composites. J Eng Mater Technol 126: 250–257. doi: 10.1115/1.1751182
![]() |
[89] |
Alian AR, El-Borgi S, Meguid SA (2016) Multiscale modeling of the effect of waviness and agglomeration of CNTs on the elastic properties of nanocomposites. Comput Mater Sci 117: 195–204. doi: 10.1016/j.commatsci.2016.01.029
![]() |
[90] | Rafiee R, Firouzbakht V (2014) Predicting Young's modulus of aggregated carbon nanotube reinforced polymer. Mech Adv Compos Struct 1: 9–16. |
[91] |
Shokrieh MM, Rafiee R (2010) Investigation of nanotube length effect on the reinforcement efficiency in carbon nanotube based composites. Compos Struct 92: 2415–2420. doi: 10.1016/j.compstruct.2010.02.018
![]() |
[92] |
Shokrieh MM, Rafiee R (2012) Development of a full range multi-scale model to obtain elastic properties of CNT/polymer composites. Iran Polym J 21: 397–402. doi: 10.1007/s13726-012-0043-0
![]() |
[93] |
Peng R, Zhou H, Wang H, et al. (2012) Modeling of nano-reinforced polymer composites: microstructure effect on Young's modulus. Comput Mater Sci 60: 19–31. doi: 10.1016/j.commatsci.2012.03.010
![]() |
[94] |
Ma PC, Mo SY, Tang BZ, et al. (2010) Dispersion, interfacial interaction and re-agglomeration of functionalized carbon nanotubes in epoxy composites. Carbon 48: 1824–1834. doi: 10.1016/j.carbon.2010.01.028
![]() |
[95] |
Javadinejad M, Mashayekhi M, Karevan M, et al. (2018) Using the equivalent fiber approach in two-scale modeling of the elastic behavior of carbon nanotube/epoxy nanocomposite. Nanomaterials 8: 696. doi: 10.3390/nano8090696
![]() |
[96] | Swain SK, Jena I (2010) Polymer/carbon nanotube nanocomposites: a novel material. Asian J Chem 22: 1–15. |
[97] |
Nguyen-Tran HD, Hoang VT, Do VT, et al. (2018) Effect of multiwalled carbon nanotubes on the mechanical properties of carbon fiber-reinforced polyamide-6/polypropylene composites for lightweight automotive parts. Materials 11: 429. doi: 10.3390/ma11030429
![]() |
[98] |
Villoria RGD, Miravete A (2007) Mechanical model to evaluate the effect of the dispersion in nanocomposites. Acta Mater 55: 3025–3031. doi: 10.1016/j.actamat.2007.01.007
![]() |
[99] | Li YL, Shen MY, Su HS, et al. (2012) A Study on mechanical properties of cnt-reinforced carbon/carbon composites. J Nanomater, 262694. |
[100] |
Morsi K (2001) Review: reaction synthesis processing of Ni–Al intermetallic materials. Mater Sci Eng 299: 1–15. doi: 10.1016/S0921-5093(00)01407-6
![]() |
[101] | Bundy VK (2018) The effect of carbon nanotube (CNT) Length on the microstructure of Ni–CNT powders and their potential for reactive processing [MD's thesis]. San Diego State University, USA. |
[102] | German RM (2005) Powder Metallurgy & Particulate Materials Processing. Princeton: Metal Powder Industries Federation. |
[103] |
Casini R, Papari G, Andreone A, et al. (2015) Dispersion of carbon nanotubes in melt compounded polypropylene based composites investigated by THz spectroscopy. Opt Express 23: 18181–18192. doi: 10.1364/OE.23.018181
![]() |
[104] |
Munir KS, Wen C (2016) Deterioration of the strong sp2 carbon network in carbon nanotubes during the mechanical dispersion processi–a review. Crit Rev Solid State 41: 347–66. doi: 10.1080/10408436.2015.1127205
![]() |
[105] |
Krause B, Villmow T, Boldt R, et al. (2011) Influence of dry grinding in a ball mill on the length of multiwalled carbon nanotubes and their dispersion and percolation behaviour in melt mixed polycarbonate composites. Compos Sci Technol 71: 1145–1153. doi: 10.1016/j.compscitech.2011.04.004
![]() |
[106] | Ahn JH, Shin HS, Kim YJ, et al. (2007) Structural modification of carbon nanotubes by various ball milling. J Alloy Compd 434–435: 428–432. |
[107] |
Tarlton T, Sullivan E, Brown J, et al. (2017) The role of agglomeration in the conductivity of carbon nanotube composites near percolation. J Appl Phys 121: 085103. doi: 10.1063/1.4977100
![]() |
[108] |
Tishkova V, Raynal PI, Puech P, et al. (2011) Electrical conductivity and Raman imaging of double wall carbon nanotubes in a polymer matrix. Compos Sci Technol 71: 1326–1330. doi: 10.1016/j.compscitech.2011.05.001
![]() |
[109] |
Schvartzman-Cohen R, Levi-Kalisman Y, Nativ-Roth E, et al. (2004) Generic approach for dispersing single-walled carbon nanotubes: the strength of a weak interaction. Langmuir 20: 6085–6088. doi: 10.1021/la049344j
![]() |
[110] |
Alvarez L, Righi A, Rols S, et al. (1999) On the Raman spectrum of nanobundles of single wall carbon nanotubes. Mater Res Soc Symp Pro 593:107–112. doi: 10.1557/PROC-593-107
![]() |
[111] | Prashantha k, Soulestin J, Lacrampe MF, et al. (2010) Electrical and dielectric properties of multi-walled carbon nanotube filled polypropylene nanocomposites. Polym Polym Compos 18: 489–494. |
[112] | Kumar P, Srinivas J (2017) Elastic behavior of CNT-reinforced polymer composites with discontinuities in CNT configurations. Mater Sci Eng 178: 012016. |
[113] | Bello D, Wardle BL, Yamamoto N, et al. (2009) Exposures to nanoscale particles and fibers during handling, processing, and machining of nanocomposites and nanoengineered composites reinforced with aligned carbon nanotubes. Proceedings of the 17th International Conference on Composite Materials, Edinburgh, UK. |
[114] | Yip MC, Lin YC, Wu CL (2011) Effect of multi-walled carbon nanotubes addition on mechanical properties of polymer composites laminate. Polym Polym Compos 19: 131–140. |
[115] |
Hadavand BS, Javid KM, Gharagozlou M (2013) Mechanical properties of multi-walled carbon nanotube/epoxy polysulfide nanocomposite. Mater Des 50: 62–67. doi: 10.1016/j.matdes.2013.02.039
![]() |
[116] |
Bai JB, Allaoui A (2003) Effect of the length and the aggregate size of MWNTs on the improvement efficiency of the mechanical and electrical properties of nanocomposites-experimental investigation. Compos Part A-Appl S 34: 689–694. doi: 10.1016/S1359-835X(03)00140-4
![]() |
[117] |
Aguilar JO, Bautista-Quijano JR, Avilés F (2010) Influence of carbon nanotube clustering on the electrical conductivity of polymer composite films. Express Polym Lett 4: 292–299. doi: 10.3144/expresspolymlett.2010.37
![]() |
[118] |
Yurdakul H, Seyhan AT, Turan S, et al. (2010) Electric field effects on CNTs/vinyl ester suspensions and the resulting electrical and thermal composite properties. Compos Sci Technol 70: 2102–2110. doi: 10.1016/j.compscitech.2010.08.007
![]() |
[119] |
Li Q, Xue QZ, Gao XL, et al. (2009) Temperature dependence of the electrical properties of the carbon nanotube/polymer composites. Express Polym Lett 3: 769–777. doi: 10.3144/expresspolymlett.2009.95
![]() |
[120] |
Jang SH, Kawashima S, Yin H (2016) Influence of carbon nanotube clustering on mechanical and electrical properties of cement pastes. Materials 9: 220. doi: 10.3390/ma9040220
![]() |
[121] |
Andrews R, Weisenberger MC (2004) Carbon nanotube polymer composites. Curr Opin Solid Stm 8: 31–37. doi: 10.1016/j.cossms.2003.10.006
![]() |
[122] |
Pötschke P, Mothes F, Krause B, et al. (2019) Melt-mixed PP/MWCNT composites: influence of CNT incorporation strategy and matrix viscosity on filler dispersion and electrical resistivity. Polymers 11: 189. doi: 10.3390/polym11020189
![]() |
[123] | Jiang L (2013) Development of an enhanced microstructure-level machining model for carbon nanotube reinforced polymer composites using cohesive zone interface [MD's thesis]. University of Illinois, Champaign. |
[124] | Mahmoodi M (2013) Electrical, thermal, and machining behaviour of injection moulded polymeric CNT nanocomposites [PhD's thesis]. University of Calgary, Alberta. |
[125] | Mahmoodi M, Paz TM, Park SS (2013) Characterization and micro end milling of graphene nano platelet (GNP) and carbon nanotube (CNT) filled nanocomposites, Proceedings of the 8th International Conference on MicroManufacturing, Victoria, Canada. |
[126] |
Zygoń P, Gwoździk M, Peszke J, et al. (2015) Comparison of properties of polymer composite materials reinforced with carbon nanotubes. Arch Metall Mater 60: 193–198. doi: 10.1515/amm-2015-0031
![]() |
[127] | Wang Z (2007) Reinforcing efficiency of carbon nanotubes in poly (vinyl alcohol) composites [PhD's thesis]. University of London, London. |
[128] |
Wang T, Song B, Qiao K, et al. (2018) Effect of dimensions and agglomerations of carbon nanotubes on synchronous enhancement of mechanical and damping properties of epoxy nanocomposites. Nanomaterials 8: 996. doi: 10.3390/nano8120996
![]() |
[129] |
Ni W, Wang B, Wang H, et al. (2006) Fabrication and properties of carbon nanotube and poly (vinyl alcohol) composites. J Macromol Sci B 45: 659–664. doi: 10.1080/00222340600770335
![]() |
[130] | Kundalwal SI (2017) Review on micromechanics of nano-and micro-fiber reinforced composites. Polym Composite 39: 4243–4274. |
[131] |
Kundalwal SI, Ray MC (2011) Micromechanical analysis of fuzzy fiber reinforced composites. Int J Mech Mater Des 7: 149–166. doi: 10.1007/s10999-011-9156-4
![]() |
[132] | Feng XQ, Shi DL, Huang YG, et al. (2007) Micromechanics and multiscale mechanics of carbon nanotubes-reinforced composites, In: Sih GC, Multiscaling in Molecular and Continuum Mechanics: Interaction of Time and Size from Macro to Nano, The Netherlands: Springer Dordrecht, 103–139. |
[133] |
Wernik JM, Meguid SA (2014) Multiscale micromechanical modeling of the constitutive response of carbon nanotube-reinforced structural adhesives. Int J Solids Struct 51: 2575–2589. doi: 10.1016/j.ijsolstr.2014.03.009
![]() |
[134] | Tornabene F, Bacciocchi M, Fantuzzi N, Reddy JN, et al. (2017) Multiscale approach for three-phase CNT/polymer/fiber laminated nanocomposite structures. Polym Compos 40: E102–E126. |
[135] | Seidel GD, Hammerand DC, Lagoudas DC (2007) Analytic and computational micromechanics of clustering and interphase effects in carbon nanotube composites. Sandia Report, Sandia National Laboratories, USA. |
1. | Bashida V. Basheer, Jinu Jacob George, Suchart Siengchin, Jyotishkumar Parameswaranpillai, Polymer grafted carbon nanotubes—Synthesis, properties, and applications: A review, 2020, 22, 2352507X, 100429, 10.1016/j.nanoso.2020.100429 | |
2. | Mohd Nurazzi Norizan, Muhammad Harussani Moklis, Siti Zulaikha Ngah Demon, Norhana Abdul Halim, Alinda Samsuri, Imran Syakir Mohamad, Victor Feizal Knight, Norli Abdullah, Carbon nanotubes: functionalisation and their application in chemical sensors, 2020, 10, 2046-2069, 43704, 10.1039/D0RA09438B | |
3. | Ahmed Gamal El-Shamy, Polyvinyl alcohol and silver decorated carbon quantum-dots for new nano-composites with application electromagnetic interface (EMI) shielding, 2020, 146, 03009440, 105747, 10.1016/j.porgcoat.2020.105747 | |
4. | Rami J. Sldozian, A.G. Tkachev, I.V. Burakova, Z.A. Mikhаleva, Improve the mechanical properties of lightweight foamed concrete by using nanomodified sand, 2021, 34, 23527102, 101923, 10.1016/j.jobe.2020.101923 | |
5. | Saowapa T. Niyomthai, Prasit Pavasant, Pitt Supaphol, Adsorption study of bovine serum albumin onto multiwalled carbon nanotubes, 2020, 33, 22147853, 1814, 10.1016/j.matpr.2020.05.060 | |
6. | M. Alajmi, K.R. Alrashdan, T. Alsaeed, A. Shalwan, Tribological characteristics of graphite epoxy composites using adhesive wear experiments, 2020, 9, 22387854, 13671, 10.1016/j.jmrt.2020.09.106 | |
7. | Venkataramanan Srinivasan, Selvaraj Kunjiappan, Ponnusamy Palanisamy, A brief review of carbon nanotube reinforced metal matrix composites for aerospace and defense applications, 2021, 2008-9295, 10.1007/s40089-021-00328-y | |
8. | S. S. Godara, P. K. Mahato, Micromechanical technique based prediction of effective properties for hybrid smart nanocomposites, 2020, 1537-6494, 1, 10.1080/15376494.2020.1851827 | |
9. | Ohood Q Alsmairat, Feilin Gou, Christopher M Dmuchowski, Paul R Chiarot, Cheol Park, Ron N Miles, Changhong Ke, Quantifying the interfacial load transfer in electrospun carbon nanotube polymer nanocomposite microfibers by using in situ Raman micromechanical characterization techniques, 2020, 53, 0022-3727, 365302, 10.1088/1361-6463/ab8fdd | |
10. | Barbara Salles Macena da Cruz, Lucas Galhardo Pimenta Tienne, Fernanda Fabbri Gondim, Ludmila Silva Candido, Maria de Fátima Vieira Marques, Erica Gervasoni Chaves, Influence of the addition of multi‐walled carbon nanotubes on the thermal and mechanical properties of polyamide‐11 before and after aging tests, 2021, 138, 0021-8995, 50071, 10.1002/app.50071 | |
11. | Mengxuan Zhang, Guoqing Ning, Zhihua Xiao, Binder‐Assisted Dispersion of Agglomerated Carbon Nanotubes for Efficiently Establishing Conductive Networks in Cathodes of Li‐Ion Batteries, 2020, 8, 2194-4288, 2000589, 10.1002/ente.202000589 | |
12. | Débora S. Craveiro, Maria A. R. Loja, An Assessment of Thick Nanocomposite Plates’ Behavior under the Influence of Carbon Nanotubes Agglomeration, 2021, 5, 2504-477X, 41, 10.3390/jcs5020041 | |
13. | Devesh Punera, The effect of agglomeration and slightly weakened CNT–matrix interface on free vibration response of cylindrical nanocomposites, 2021, 0001-5970, 10.1007/s00707-020-02933-y | |
14. | Kar Fei Chan, Mohd Hafiz Mohd Zaid, Md Shuhazlly Mamat, Shahira Liza, Masaki Tanemura, Yazid Yaakob, Recent Developments in Carbon Nanotubes-Reinforced Ceramic Matrix Composites: A Review on Dispersion and Densification Techniques, 2021, 11, 2073-4352, 457, 10.3390/cryst11050457 | |
15. | Mlungisi Martin Ngoma, Machodi Mathaba, Kapil Moothi, Removal of Cu2+, Fe2+, Ni2+, Zn2+ and Cl− from Industrial wastewater using a Polyethersulfone/Carbon Nanotube/Polyvinyl alcohol composite membrane, 2021, 26670100, 100116, 10.1016/j.envc.2021.100116 | |
16. | Nur Aina I. M. Mokhtar, Ruzniza M. Zawawi, Wan M. Khairul, Nor A. Yusof, Electrochemical and optical sensors made of composites of metal–organic frameworks and carbon-based materials. A review, 2022, 20, 1610-3653, 3099, 10.1007/s10311-022-01403-2 | |
17. | Kai Zhang, Xiaojun Tang, Fuzheng Guo, Kangli Xiao, Dexin Zheng, Yunsheng Ma, Qingsong Zhao, Fangxin Wang, Bin Yang, Improved Dynamic Compressive and Electro-Thermal Properties of Hybrid Nanocomposite Visa Physical Modification, 2022, 13, 2079-4991, 52, 10.3390/nano13010052 | |
18. | Karamvir Singh, Sandeep Sharma, Monish Gupta, C.C. Tripathi, Fabrication of serpentine and I structured graphene-CNT based highly sensitive and flexible strain sensors, 2021, 250, 01679317, 111631, 10.1016/j.mee.2021.111631 | |
19. | Balakrishna Adhikari, B.N. Singh, A Coupled Mori–Tanaka model and FEM RVE approach for the geometrical nonlinear dynamic response of the FG-CNTRC plate based on a novel shear strain function using isogeometric finite element procedure, 2022, 280, 02638223, 114947, 10.1016/j.compstruct.2021.114947 | |
20. | Karamvir Singh, Monish Gupta, C. C. Tripathi, Fabrication of flexible and sensitive laser-patterned serpentine-structured graphene–CNT paper for strain sensor applications, 2022, 128, 0947-8396, 10.1007/s00339-022-06276-4 | |
21. | Qiuyan Duan, Bijian Lan, Yinxiang Lv, Highly Dispersed, Adhesive Carbon Nanotube Ink for Strain and Pressure Sensors, 2022, 14, 1944-8244, 1973, 10.1021/acsami.1c20133 | |
22. | Chloe Curtis-Smith, Marianna Rogers, Jingyao Dai, Erick Gonzalez, Carina Xiaochen Li, Yuying Lin, Ashley L. Kaiser, Jeonyoon Lee, Brian L. Wardle, 2023, Fabrication and Characterization of Carbon Nanotube/Bismaleimide Nanocomposite Laminates with Ultrahigh Nanofiber Volume Fraction, 978-1-62410-699-6, 10.2514/6.2023-2031 | |
23. | Fei Teng, Jian Wu, Benlong Su, Youshan Wang, Enhanced adhesion friction behaviors of nature rubber composites by applications of carbon nanotube: Experiment and molecular insight, 2023, 181, 0301679X, 108333, 10.1016/j.triboint.2023.108333 | |
24. | Evangelos Kasapis, Konstantina Tsitoni, Gkreti-Maria Manesi, Ioannis Moutsios, Dimitrios Moschovas, Dmitry V. Vashurkin, Denis S. Kotlyarskiy, Dimitri A. Ivanov, Apostolos Avgeropoulos, Self-assembly behavior of ultra-high molecular weight in-situ anionically synthesized polymer matrix composite materials “grafted from” single- or multi-wall CNTs, 2021, 235, 00323861, 124243, 10.1016/j.polymer.2021.124243 | |
25. | Zarina Saidova, Grigory Yakovlev, Zoltán Orbán, Valery Grakhov, Larisa Urkhanova, Solbon Lkhasaranov, Cement Compositions Modified with Dispersed Magnesium Silicate Dihydrate- and Carbon-Based Additives, 2022, 2, 2673-7108, 101, 10.3390/constrmater2020008 | |
26. | Fumio Ogawa, Chitoshi Masuda, Fabrication and the mechanical and physical properties of nanocarbon-reinforced light metal matrix composites: A review and future directions, 2021, 820, 09215093, 141542, 10.1016/j.msea.2021.141542 | |
27. | Ronny Thapelo Tebeta, Daniel Makundwaneyi Madyira, Asghar Mohammadpour Fattahi, Harry Magadhlela Ngwangwa, 2022, Investigation of Tensile Properties of Polyamide-Calcium Carbonate Nanocomposites at Various Temperatures, 978-1-6654-8400-8, 182, 10.1109/ICMIMT55556.2022.9845274 | |
28. | Raghuram V. Pucha, Shivani Kundalia, Nikhil Nandikanti, Devon Phelps, 2022, Analysis of Hybrid Composites with Nanofillers using Representative Volume Element and Laminate Models, 978-1-62410-631-6, 10.2514/6.2022-0500 | |
29. | Simona Luminita Nica, Mirela-Fernanda Zaltariov, Daniela Pamfil, Alexandra Bargan, Daniela Rusu, Delia Mihaela Raţă, Constantin Găină, Leonard Ionut Atanase, MWCNTs Composites-Based on New Chemically Modified Polysulfone Matrix for Biomedical Applications, 2022, 12, 2079-4991, 1502, 10.3390/nano12091502 | |
30. | Kangda Hao, Yongkang Gao, Lianyong Xu, Yongdian Han, Lei Zhao, Wenjin Ren, Plasticity improvement coupled by carbon nanotubes and beam oscillation in laser-arc hybrid welding of magnesium alloy, 2022, 857, 09215093, 144093, 10.1016/j.msea.2022.144093 | |
31. | Ranjeet Kumar Singh, Swati Gangwar, Dhirendra Kumar Singh, Experimental analysis with grey relational analysis–analytic hierarchy process‐based hybrid optimization to analyze the effect of graphene nanoparticle reinforced ultra‐high molecular weight polyethylene/n‐HAp for hip joint, 2022, 43, 0272-8397, 6489, 10.1002/pc.26962 | |
32. | Stelios K. Georgantzinos, Panagiotis Antoniou, Stylianos Markolefas, Georgios Giannopoulos, Finite element predictions on vibrations of laminated composite plates incorporating the random orientation, agglomeration, and waviness of carbon nanotubes, 2022, 233, 0001-5970, 2031, 10.1007/s00707-022-03179-6 | |
33. | K. Eskandary, Mohammad Shishesaz, Shapour Moradi, Buckling analysis of composite conical shells reinforced by agglomerated functionally graded carbon nanotube, 2022, 22, 1644-9665, 10.1007/s43452-022-00440-6 | |
34. | Chika Oliver Ujah, Daramy Vandi Von Kallon, Trends in Aluminium Matrix Composite Development, 2022, 12, 2073-4352, 1357, 10.3390/cryst12101357 | |
35. | Yunqing He, Xiaoying Lin, Yue Feng, Binghong Luo, Mingxian Liu, Carbon Nanotube Ink Dispersed by Chitin Nanocrystals for Thermoelectric Converter for Self‐Powering Multifunctional Wearable Electronics, 2022, 9, 2198-3844, 2204675, 10.1002/advs.202204675 | |
36. | Muharrem Pul, The effect of carbon nanotube amount in machining of ZA-27 matrix carbon nanotube reinforced nano composite, 2022, 27, 1517-7076, 10.1590/s1517-707620220002.1326 | |
37. | Liudmyla Rozhdestvenska, Kateryna Kudelko, Yevhen Kolomiiets, Yuliya Dzyazko , Volodymyr Ogenko, MEMBRANES FUNCTIONALIZED WITH 1d, 2d and 3d CARBON MATERIALS, 2021, 87, 2708-129X, 79, 10.33609/2708-129X.87.04.2021.79-110 | |
38. | Robert Birundu Onyancha, Kingsley Eghonghon Ukhurebor, Uyiosa Osagie Aigbe, Otolorin Adelaja Osibote, Heri Septya Kusuma, Handoko Darmokoesoemo, Vincent Aizebeoje Balogun, A systematic review on the detection and monitoring of toxic gases using carbon nanotube-based biosensors, 2021, 34, 22141804, 100463, 10.1016/j.sbsr.2021.100463 | |
39. | Seyed Ali Mirsalehi, Amir Ali Youzbashi, Amjad Sazgar, Characterization of the interface and interphase region in the multi-walled carbon nanotube modified epoxy resin/carbon fiber hybrid nanocomposite, 2022, 29, 0927-6440, 675, 10.1080/09276440.2021.1996921 | |
40. | Salwa EL Garouge, Mostapha Tarfaoui, Hassan EL Minor, Amine Bendarma, The improvement of the physical and mechanical properties of CNTs based composite material, 2022, 52, 22147853, 64, 10.1016/j.matpr.2021.10.312 | |
41. | Mohammad Hossein Mirmusavi, Mehdi Ahmadian, Saeed Karbasi, Polycaprolactone-chitosan/multi-walled carbon nanotube: A highly strengthened electrospun nanocomposite scaffold for cartilage tissue engineering, 2022, 209, 01418130, 1801, 10.1016/j.ijbiomac.2022.04.152 | |
42. | Federica Zaccardi, Elisa Toto, Fabrizio Marra, Maria Gabriella Santonicola, Susanna Laurenzi, Hybrid Carbon Nanocomposites Made of Aerospace-Grade Epoxy Showing Synergistic Effects in Electrical Properties and High Processability, 2023, 15, 2073-4360, 1163, 10.3390/polym15051163 | |
43. | Wenkai Li, Zhiyong Xie, Shi Qiu, Haodong Zeng, Minqi Liu, Gangsheng Wu, Improved Performance of Composite Bipolar Plates for PEMFC Modified by Homogeneously Dispersed Multi-Walled Carbon Nanotube Networks Prepared by In Situ Chemical Deposition, 2023, 13, 2079-4991, 365, 10.3390/nano13020365 | |
44. | Stelios K. Georgantzinos, Panagiotis A. Antoniou, Georgios I. Giannopoulos, Antonios Fatsis, Stylianos I. Markolefas, Design of Laminated Composite Plates with Carbon Nanotube Inclusions against Buckling: Waviness and Agglomeration Effects, 2021, 11, 2079-4991, 2261, 10.3390/nano11092261 | |
45. | Ryan Nam, Ji Eun Lee, Michael Jakubinek, Behnam Ashrafi, Hani E. Naguib, Soft electrothermal actuator array for surface morphing application, 2023, 0883-7694, 10.1557/s43577-022-00474-4 | |
46. | Zuveria Firdouz, Pragya Tripathi, K. Mondal, Kantesh Balani, Effect of carbonaceous reinforcements on anticorrosive and magnetic properties of Ni-Cu based composite coatings prepared by pulsed electrodeposition, 2022, 441, 02578972, 128560, 10.1016/j.surfcoat.2022.128560 | |
47. | Abdul Aziz, Syed Shaheen Shah, Mohammad A. Jafar Mazumder, Munetaka Oyama, Abdul‐Rahman Al‐Betar, Carbon Nanofiber and Poly[2‐(methacryloyloxy) ethyl] Trimethylammonium Chloride Composite as a New Benchmark Carbon‐based Electrocatalyst for Sulfide Oxidation, 2021, 16, 1861-4728, 1570, 10.1002/asia.202100309 | |
48. | Hasret Akgün, Ece Yapıcı, Aysun Özkan, Zerrin Günkaya, Müfide Banar, A combined multi-criteria decision-making approach for the selection of carbon-based nanomaterials in phase change materials, 2023, 60, 2352152X, 106619, 10.1016/j.est.2023.106619 | |
49. | Nutthapong Poompiew, Prasit Pattananuwat, Chuanchom Aumnate, Allen Jonathan Román, Tim A. Osswald, Pranut Potiyaraj, 3D printable resin/carbon nanotube composites for wearable strain sensors: Enhancing mechanical and electrical properties, 2023, 8, 24682179, 100546, 10.1016/j.jsamd.2023.100546 | |
50. | Ajahar Khan, Khalid A. Alamry, Raed H. Althomali, 2023, 9783527350728, 241, 10.1002/9783527838790.ch11 | |
51. | Peiqi Li, Junxing Liu, Sungwun Her, Erfan Zal Nezhad, Seungmin Lim, Sungchul Bae, Synthesis of Highly-Dispersed Graphene Oxide Nanoribbons–Functionalized Carbon Nanotubes–Graphene Oxide (GNFG) Complex and Its Application in Enhancing the Mechanical Properties of Cementitious Composites, 2021, 11, 2079-4991, 1669, 10.3390/nano11071669 | |
52. | Divyansh Upreti, T. Umasankar Patro, 2022, Chapter 13, 978-981-16-8390-9, 227, 10.1007/978-981-16-8391-6_13 | |
53. | Olusoji Oluremi Ayodele, Mary Ajimegoh Awotunde, Bukola Joseph Babalola, Peter Apata Olubambi, The influence of dispersion time on the mechanical properties of spark plasma–sintered carbon nanotubes reinforced nickel-aluminum matrix composites, 2022, 120, 0268-3768, 4113, 10.1007/s00170-022-08933-7 | |
54. | Vijaya Chalivendra, 2023, 9780323988308, 437, 10.1016/B978-0-323-98830-8.00009-6 | |
55. | Pardis Ghahramani, Rasool Moradi‐Dastjerdi, Kamran Behdinan, Hani E. Naguib, Mechanical characterization of multifunctional highly porous carbon nanotube‐reinforced foams, 2023, 0272-8397, 10.1002/pc.27226 | |
56. | Sujata Singh, Chandan Srivastava, Engineering the Protective Oxide Chemistry for Enhanced Corrosion Protection Performance of FeCuCrNiCo-CNT Composite Coatings in 3.5 M NaCl Solution Corrosive Media, 2023, 1073-5623, 10.1007/s11661-023-06994-1 | |
57. | Jitendra Chavhan, Ramesh Rathod, Vipin Tandon, Suresh Umare, Awanikumar Patil, Structural and physico-chemical properties of electroactive polyamide/multi-walled carbon nanotubes nanocomposites, 2022, 29, 24680230, 101765, 10.1016/j.surfin.2022.101765 | |
58. | Binh M. Trinh, Boon P. Chang, Tizazu H. Mekonnen, The barrier properties of sustainable multiphase and multicomponent packaging materials: A review, 2023, 133, 00796425, 101071, 10.1016/j.pmatsci.2023.101071 | |
59. | A. G. Sheinerman, Mechanical Properties of Metal Matrix Composites with Graphene and Carbon Nanotubes, 2022, 123, 0031-918X, 57, 10.1134/S0031918X22010124 | |
60. | M.A. Azmah Hanim, S.N. Hadirah, T.T. Dele‐Afolabi, D.W. Jung, S.M. Sapuan, C.N. Aiza Jaafar, Microstructure and hardness properties of aluminum matrix composites reinforced with iron (iii) oxide nanoparticles and carbon nanotubes, 2022, 53, 0933-5137, 1121, 10.1002/mawe.202100246 | |
61. | Qiuyan Duan, Yinxiang Lu, Silk Sericin As a Green Adhesive to Fabricate a Textile Strain Sensor with Excellent Electromagnetic Shielding Performance, 2021, 13, 1944-8244, 28832, 10.1021/acsami.1c05671 | |
62. | Echeverry-Cardona Laura, Cabanzo Rafael, Quintero-Orozco Jorge, Castillo-Cuero Harvi Alirio, Rodríguez-Restrepo Laura Victoria, Restrepo-Parra Elisabeth, Effects of Molarity and Storage Time of MWCNTs on the Properties of Cement Paste, 2022, 15, 1996-1944, 9035, 10.3390/ma15249035 | |
63. | Satheesh Kumar Balu, V. Sampath, Swetha Andra, Srinivasan Alagar, S. Manisha Vidyavathy, Fabrication of carbon and silver nanomaterials incorporated hydroxyapatite nanocomposites: Enhanced biological and mechanical performances for biomedical applications, 2021, 128, 09284931, 112296, 10.1016/j.msec.2021.112296 | |
64. | Hanumantharaya Rangaswamy, Harsha H. M, Manjunath Patel Gowdru Chandrashekarappa, Danil Yu Pimenov, Khaled Giasin, Szymon Wojciechowski, Experimental investigation and optimization of compression moulding parameters for MWCNT/glass/kevlar/epoxy composites on mechanical and tribological properties, 2021, 15, 22387854, 327, 10.1016/j.jmrt.2021.08.037 | |
65. | Francesco Tornabene, Matteo Viscoti, Rossana Dimitri, 2024, 9780443219498, 63, 10.1016/B978-0-443-21949-8.00003-6 | |
66. | Ayodele Abraham Ajayi, Mohan Turup Pandurangan, Krishnan Kanny, Influence of hybridizing fillers on mechanical properties of foam composite panel, 2023, 63, 0032-3888, 2565, 10.1002/pen.26396 | |
67. | Muhammad Zulhiqmi Mohd Jamil, Mohammad Syahid Mohd Isa, Sufian Raja, Mohd Ridha bin Muhamad, Farazila Yusof, Hijaz Kamal Hasnan, Mohd Fadzil Jamaludin, Zbigniew Brytan, Huihong Liu, Tetsuo Suga, Yoshiaki Morisada, Hidetoshi Fujii, Friction Stir Alloying AZ61 Magnesium Alloy and Mild Steel with Zn-CNT Additive, 2024, 77, 0972-2815, 435, 10.1007/s12666-023-03124-8 | |
68. | Xinming Wang, Jing Zhong, Revisiting the effects of carbon nanotube agglomerates in cement, 2025, 231, 00086223, 119710, 10.1016/j.carbon.2024.119710 | |
69. | Pankaj Shrivastava, Syed Nasimul Alam, Arka Ghosh, Ventrapragada Bramaramba, Nityananda Sahoo, Wenbin Zhou, Krishanu Biswas, Enhanced physical and mechanical properties of Cu-based nanocomposites with bundled multi-layered carbon nanotubes incorporation: fabrication and comparative analysis via conventional sintering and SPS techniques, 2024, 0924-3046, 1, 10.1080/09243046.2024.2381299 | |
70. | Ibaa M. H. Zwain, Ali Sadiq Alithari, Improving the fatigue life of composite by using multiwall carbon nanotubes, 2023, 13, 2391-5439, 10.1515/eng-2022-0490 | |
71. | Yeo Yi Xuan, M.J.M. Ridzuan, M.S. Abdul Majid, M.T.A. Rahman, Ferriawan Yudhanto, Azduwin Khasri, Mohd Shihabudin Ismail, Influence of multi-walled carbon nanotubes on thermal behaviour and mechanical properties of pineapple leaf fibre-based natural rubber composites, 2024, 30, 22387854, 8608, 10.1016/j.jmrt.2024.05.239 | |
72. | N. Salman Tabrizi, M. Yavari, Structural modification of CNT-C xerogel through synthesis parameters, 2024, 378, 13871811, 113260, 10.1016/j.micromeso.2024.113260 | |
73. | Bakytzhan Sariyev, Alina Abdikadyr, Temirlan Baitikenov, Yerbolat Anuarbekov, Boris Golman, Christos Spitas, Thermal properties and mechanical behavior of hot pressed PEEK/graphite thin film laminate composites, 2023, 13, 2045-2322, 10.1038/s41598-023-39905-w | |
74. | Zaili Hou, Sonia E. Chavez, Anna Marie LaChance, Michael D. Jones, Cole D. French, Aidan M. Walsh, Montgomery T. Shaw, Luyi Sun, Polyvinyl alcohol (PVA)/montmorillonite (MMT) nanocomposite coatings via a rotational coating method, 2024, 7, 2522-0128, 10.1007/s42114-024-00965-9 | |
75. | V. V. Tytarenko, V. A. Zabludovsky, Quantum mechanical modeling of the interaction of ultradispersed diamond particles with nickel ions, 2023, 27, 10274642, 10.30970/jps.27.4602 | |
76. | Xudong Song, Qi Zhang, Hong Wu, Shaoyun Guo, Jianhui Qiu, Highly Efficient Dispersion of Individual Multiwalled Carbon Nanotubes by Polylactide in High Elastic State, 2023, 62, 0888-5885, 5042, 10.1021/acs.iecr.2c04609 | |
77. | Thế Dũng Đinh, Trần Hùng Nguyễn, Đức Dương Lã, Nghiên cứu chế tạo vật liệu compozit trên nền nhựa polyamide 6 và sợi cacbon ngắn, 2023, 88, 1859-1043, 95, 10.54939/1859-1043.j.mst.88.2023.95-100 | |
78. | Atif Khurshid Wani, Zehra Khan, Saikat Sena, Nahid Akhtar, Maha Awjan Alreshdi, Krishna Kumar Yadav, Abdullah M. Alkahtani, Ab Waheed Wani, Farida Rahayu, Chendy Tafakresnanto, Evy Latifah, Budi Hariyono, Zainal Arifin, Lienda Bashier Eltayeb, Carbon nanotubes in plant dynamics: Unravelling multifaceted roles and phytotoxic implications, 2024, 210, 09819428, 108628, 10.1016/j.plaphy.2024.108628 | |
79. | Anurag Kamal, Anoop Kumar Shukla, Vijay M. Shinde, High-strength C/SiC joints prepared using a novel Ni-Si-CNTs-based filler, 2023, 43, 09552219, 7411, 10.1016/j.jeurceramsoc.2023.08.024 | |
80. | Mehdi Ranjbar-Roeintan, A circular plate with a central hole reinforced with agglomerated CNTs under impact loading, 2023, 19, 1573-6105, 876, 10.1108/MMMS-01-2023-0025 | |
81. | Y. Hamadi, M. Reihanian, Kh. Gheisari, Khalil Ranjbar, CNTs Agglomeration Effect on Wear and Mechanical Behaviors of FeCoNiMn Medium Entropy Alloys, 2024, 77, 0972-2815, 3517, 10.1007/s12666-024-03406-9 | |
82. | Leyla Ünal, Viviane Maccio‐Figgemeier, Lukas Haneke, Gebrekidan Gebresilassie Eshetu, Johannes Kasnatscheew, Martin Winter, Egbert Figgemeier, Prelithiated Carbon Nanotube‐Embedded Silicon‐based Negative Electrodes for High‐Energy Density Lithium‐Ion Batteries, 2024, 11, 2196-7350, 10.1002/admi.202400024 | |
83. | Yibo Gao, Jianlin Luo, Zhiqing Li, Fei Teng, Jigang Zhang, Song Gao, Minglei Ma, Xiaoyang Zhou, Xuejun Tao, Dispersion of carbon nanotubes in aqueous cementitious materials: A review, 2023, 12, 2191-9097, 10.1515/ntrev-2022-0560 | |
84. | Alexandra Liever, Yingtao Liu, Shreya Vemuganti, Effect of immediate curing at elevated temperatures on the tensile and interfacial properties of carbon fiber-epoxy composites, 2024, 6, 2631-6331, 035001, 10.1088/2631-6331/ad5b4a | |
85. | Tengfei Zhao, Mohammad Javad Bayat, Amin kalhori, Kamran Asemi, Free vibration analysis of functionally graded multilayer hybrid composite cylindrical shell panel reinforced by GPLs and CNTs surrounded by Winkler elastic foundation, 2024, 308, 01410296, 117975, 10.1016/j.engstruct.2024.117975 | |
86. | Ping-An Chen, Yu Liu, Jiangnan Xia, Jiaqi Ding, Yu Zhang, Zhenqi Gong, Xi Zeng, Jiakun Xue, Guowei Liu, Lang Jiang, Lei Liao, Yuanyuan Hu, Photolithography-Free, Solution-Processable Perovskite Electrodes for High-Performance Organic Transistors, 2024, 1530-6984, 10.1021/acs.nanolett.4c03151 | |
87. | Mücahit Kocaman, Hamdullah Çuvalcı, Aykut Çanakçı, The effect of novel advanced method on the properties of novolac hybrid nanocomposites reinforced with carbon nanotube and glass fiber, 2023, 140, 0021-8995, 10.1002/app.54366 | |
88. | Mohammad Shadabfar, Morteza Ehsani, Hossein Ali Khonakdar, Majid Abdouss, Enhanced the properties of carbon‐paste nanocomposite by carboxylation of multi‐walled carbon nanotubes, 2024, 45, 0272-8397, 475, 10.1002/pc.27792 | |
89. | Yashesh Darji, Dilipkumar S. Patel, Dhaval M. Patel, Ankit D. Oza, Manoj Kumar, Manish Gupta, Ruby Pant, Identifying the most significant parameter in stir casting process for optimizing the effect of nano reinforcement MWCNT on AA 7075-T651, 2023, 10, 2737-5994, 10.1142/S2737599423400133 | |
90. | C. Chu, L. Shan, M. S. H. Al-Furjan, A. Farrokhian, R. Kolahchi, Energy absorption, free and forced vibrations of flexoelectric nanocomposite magnetostrictive sandwich nanoplates with single sinusoidal edge on the frictional torsional viscoelastic medium, 2023, 23, 1644-9665, 10.1007/s43452-023-00756-x | |
91. | Anna A. Dokuchaeva, Sergey V. Vladimirov, Vsevolod P. Borodin, Elena V. Karpova, Andrey A. Vaver, Gleb E. Shiliaev, Dmitry S. Chebochakov, Vasily A. Kuznetsov, Nikolay V. Surovtsev, Sergey V. Adichtchev, Alexander G. Malikov, Mikhail A. Gulov, Irina Y. Zhuravleva, Influence of Single-Wall Carbon Nanotube Suspension on the Mechanical Properties of Polymeric Films and Electrospun Scaffolds, 2023, 24, 1422-0067, 11092, 10.3390/ijms241311092 | |
92. | Anh Tuan Le, Quentin Govignon, Samuel Rivallant, Thierry Cutard, Mode I and mode II fracture behavior in nano‐engineered long fiber reinforced composites, 2023, 44, 0272-8397, 4016, 10.1002/pc.27374 | |
93. | Anh Tuan Le, Quentin Govignon, Samuel Rivallant, Thierry Cutard, Composite laminates reinforced by vertically aligned carbon nanotubes: Detailed manufacturing process, from nanotubes transfer to composite consolidation, 2023, 57, 0021-9983, 4239, 10.1177/00219983231207441 | |
94. | Taegeon Kil, Jin-Ho Bae, Hyun-No Yoon, Haeng-Ki Lee, Review of Recent Advances in the Electrical/Mechanical Characteristics of Nanocomposites and Multi-scale Modeling of Nanocomposites, 2023, 36, 1229-3059, 131, 10.7734/COSEIK.2023.36.2.131 | |
95. | Dung The Dinh, Ha Duc Ninh, Hung Tran Nguyen, Dat Huu Nguyen, Giang Vu Nguyen, Tung Huy Nguyen, Kien Trung Pham, Duong Duc La, Polyamide 6/carbon fibre composite: An investigation of carbon fibre modifying pathways for improving mechanical properties, 2024, 53, 1465-8011, 190, 10.1177/14658011241253553 | |
96. | Thi Thom Tran, Dinh Kien Nguyen, Dynamics of inclined CNTRC sandwich beams under a moving mass with influence of CNT agglomeration, 2023, 351, 1873-7234, 373, 10.5802/crmeca.226 | |
97. | Justine Marie E. Abarro, Jon Nyner L. Gavan, Daniel Eldrei D. Loresca, Maura Andrea A. Ortega, Eugene A. Esparcia, Julie Anne D. R. Paraggua, A Tale of Nickel-Iron Batteries: Its Resurgence in the Age of Modern Batteries, 2023, 9, 2313-0105, 383, 10.3390/batteries9070383 | |
98. | Miguel Humberto Bocanegra-Bernal, Armando Reyes-Rojas, Hilda Esperanza Esparza-Ponce, Alfredo Aguilar-Elguézabal, Skepticism regarding the use of carbon nanotubes as reinforcing agent in ceramics for biomedical applications: A critical review, 2024, 0954-4062, 10.1177/09544062241288657 | |
99. | Nguyen Duy Phon, Tran Ngoc Doan, Duong Van Quang, Phung Van Minh, Thermoelastic analysis of FG-CNTRC cylindrical shells with various boundary conditions and temperature-dependent characteristics using quasi-3D higher-order shear deformation theory, 2024, 0892-7057, 10.1177/08927057241274332 | |
100. | Dengpeng Chen, Yanzhi Cai, Laifei Cheng, Siyu Guo, Tingting Liu, Shaohua Huang, Haiming Yu, Yuhan Wang, Zhongyi Hu, Dongyun Gui, Structure and function design of carbon nanotube-based flexible strain sensors and their application, 2024, 225, 02632241, 113992, 10.1016/j.measurement.2023.113992 | |
101. | N. Karthikeyan, Jesuarockiam Naveen, Enhanced flexural and vibration behavior of interleaved CFRP composite joints with modified multiwalled carbon nanotube adhesives for aerospace and aircraft applications, 2024, 0272-8397, 10.1002/pc.29357 | |
102. | Alaa Almansoori, Katalin Balázsi, Csaba Balázsi, Advances, Challenges, and Applications of Graphene and Carbon Nanotube-Reinforced Engineering Ceramics, 2024, 14, 2079-4991, 1881, 10.3390/nano14231881 | |
103. | Han Du, Xiaoao Chen, Huaiping Ding, Xiaochun Yin, Yu Su, George J. Weng, The effect of adding graphene oxide into CNT/polymer system on the CNT dispersion and mechanical properties of the hybrid nanocomposites, 2025, 53, 24522139, 102196, 10.1016/j.coco.2024.102196 | |
104. | Nimra Naeem, Sajid Butt, Zoha Afzal, Muhammad Waseem Akram, Muhammad Irfan, Muhammad Atiq Ur Rehman, Abrar H. Baluch, Ghufran ur Rehman, Muhammad Umer Farooq, Facile development of carbon nanotube (CNT)-based flexible thermoelectric materials for energy-harvesting applications, 2025, 15, 2046-2069, 569, 10.1039/D4RA02914C | |
105. | Juan Li, Juanyin Liu, Nonlinear Optimized PID Vibration Control of Thermal-Dependent FG Composite Porous Plates Reinforced by Agglomerated CNTs, 2025, 25, 0219-4554, 10.1142/S0219455425500348 | |
106. | Mohamad Tizmaghz Nejad, Davvod Akbari, Milad Mohammadi, Alireza Rahiminejad, The Nondestructive Inspection of Agglomeration in Nanocomposite Parts Using Shearography and Improving the Results with Design of Experiment, 2024, 60, 1061-8309, 1407, 10.1134/S1061830924602605 | |
107. | Anshika Babbar, Gurpreet Singh, Vasundhara Singh, R.S. Walia, Progress and recent developments in carbon nanotube (CNT) based composite coatings for tribological and bio-tribological applications, 2025, 1226086X, 10.1016/j.jiec.2025.01.031 | |
108. | Ayub KarimzadGhavidel, Tahsin Tecelli Opoz, Mahsa Mahdavinia, Gholamreza Kiani, Mahmoud Moradi, Achieving exceptional mechanical and thermal properties in ABS/MWCNTs nanocomposites with minimal CNT loading via electromechanical dispersion technique, 2025, 0272-8397, 10.1002/pc.29602 | |
109. | Gulnare Ahmetli, Suheyla Kocaman, Nijat Musayev, Javidan Gasimov, Nimet Özmeral, Hybrid epoxy composites based on tire waste-derived carbon black and eggshells with enhanced properties and aging life in different environmental conditions, 2025, 507, 13858947, 160701, 10.1016/j.cej.2025.160701 | |
110. | Essam B. Moustafa, Abdulraheem H. Alyoubi, Mahmoud A. Alzahrani, Ahmed O. Mosleh, Asmaa M. Khalil, Fly Ash, TiO2, hBN, and B4C Nanoparticle Reinforcement: A Novel Approach to Magnesium Metal via Powder Metallurgy, 2025, 1438-1656, 10.1002/adem.202402261 | |
111. | Davood Rahmatabadi, Mohammad Amin Yousefi, Shahrooz Shamsolhodaei, Majid Baniassadi, Karen Abrinia, Mahdi Bodaghi, Mostafa Baghani, 4D Printing of Polyethylene Glycol‐Grafted Carbon Nanotube‐Reinforced Polyvinyl Chloride–Polycaprolactone Composites for Enhanced Shape Recovery and Thermomechanical Performance, 2025, 2640-4567, 10.1002/aisy.202500113 |
Composites | CNT content (vol%) | Porosity and CNT clusters (vol%) | Maximum size of CNT clusters (μm) | Average grain size (μm) |
Al/CNT | 0 | 1.00 | - | 17 |
0.50 | 4.88 | 89 | 16 | |
0.75 | 6.53 | 102 | 15 | |
1.00 | 5.95 | 78 | 16 | |
1.50 | 7.38 | 177 | 16 | |
Ni/CNT | 0 | 1.05 | - | 15 |
0.50 | 3.22 | 83 | 14 | |
0.75 | 3.96 | 155 | 13 | |
1.00 | 6.67 | 137 | 14 | |
1.50 | 12.47 | 310 | 16 |
Matrix | Reinforcement & strengthening method | CNTs (vol/wt%) | Presence of agglomerates & remarks | Ref. |
Cu | Ultrasonic cleaning + particles composite system + spark plasma sintering | 5, 10 wt% | Yes. CNTs are aggregated into ropes or knotted lumps due to strong inter-tube van der Waals attraction. | [6] |
Cuprous oxide | Vacuum hot pressing at H2 atmosphere | 0, 1, 3, 5 wt% | Yes, at 5 wt%. Thermal conductivity decreases with the increase of the CNTs concentration. | [72] |
Al | Ball milling + Sonication | 2 wt% | Yes. Adverse effects on the properties of final composite products due to the increased porosity. | [73] |
2024Al matrix | Cold isostatic pressing + Hot pressing | 1 wt% | Yes, but low. Elastic modulus and the tensile strength were enhanced markedly. | [74] |
Aluminum–silicon alloy powders | Spray drying | 5, 10 wt% | Yes, 10 wt%. Partial CNT surface damage in case of the 10 wt% CNT coating due to CNT mesh formation and smaller size of spray dried agglomerate. | [75] |
Al | Ball milling | 2 wt% | Yes. Presence of clusters at the early stage of milling which acts as the precipitates results in the lower Young's modulus. | [76] |
Al | Ball milling + Nanodispersion | 0.8, 1.6 vol% | Yes. Poor dispersion of CNTs in the matrix exhibited a non-uniform fracture surface. No aggregations in secondary steps are claimed. | [77] |
Magnesium oxychloride + epoxy | Magnesium oxychloride cement pastes were prepared by ratios of MgO:MgCl2 = 2.2:1. Then coated with epoxy/CNTs | 0, 0.02 wt% | Yes. Water consistency value increases by the addition of CNTs due to that the additional high specific surface area acts as an interface for an efficient stress transfer and causes the strong tendency of the CNTs to form agglomerates. | [78] |
AZ91 + Mg | Melt stirring + high-pressure die casting | 0.1, 0.5, 1 wt% | Yes, at 1 wt%. Agglomerates of entangled MWCNTs with a size of up to 2 µm can be observed. | [79] |
Al | Induction melting | 0, 0.1, 0.2 vol% | No. No cluster or segregation of the nanotubes was seen. | [80] |
Mg | Hot isostatic pressing under high pressure. | 1, 2 wt% | Yes. Homogeneous dispersion of MWCNTs in Mg matrix is obtained. | [81] |
Ag | Modified molecular level mixing method | 0, 6, 12 vol% | Yes, at 12 vol%. Electrical conductivity reduces. | [82] |
Cu | Melt stirring | 0.1 wt% | Yes. The micrograph shows that the raw MWCNTs are agglomerated in big bundles. This act as defects instead of reinforcements. | [83] |
Al (AA5XXX) | Ball milling + hot isostatic pressed + extrusion | 2 wt% | Yes. CNTs clusters were dispersed and claimed as uniform distribution. | [84] |
Matrix | Reinforcement & strengthening method | CNTs vol/wt% | Presence of agglomerates & remarks | Ref. |
Epoxy system | Sonication | 0.025, 0.05 wt% | Yes. Good dispersion was not achieved. | [33] |
- | - | - | Yes. A review paper that has described a lot about agglomeration of CNTs in the polymer matrix. | [121] |
Polypropylene | Melt mixing | 0.5–7.5 wt% | Yes. Low agglomeration effect due to melt dispersion. Lower matrix viscosity promotes secondary agglomeration during the compression molding step. | [122] |
Polyvinyl alcohol | Used prepared sample to study machining | 1, 2, 4 wt% | Yes. CNTs loading beyond 4 wt%, the CNTs were observed to form clusters within the polymer matrix. | [123] |
Polystyrene | Injection moulding process | 20 wt% | Yes. Monte Carlo model was used for simulation to predict the electrical conductivity. The agglomeration has been neglected. | [124] |
Polymer | Injection molding | 1 wt% | Yes. Both partial alignment and MWCNTs agglomeration were observed. | [125] |
Polyvinyl alcohol | Solvent method | Not mentioned | Yes. Substantial agglomerates of nanotubes are visible. | [126] |
Vinyl alcohol | Melt mixing | 0.1, 0.3, 0.5, 1 wt% | Yes. Entanglement of CNTs reduce conductivity. | [127] |
Epoxy | Sonication | Varying ranges | Yes. Varying cluster/aggregate depending on the composites. | [128] |
Vinyl alcohol | Gum arabic treatment | 2 wt% | Yes. Interfere with the tensile properties. | [129] |
Composites | CNT content (vol%) | Porosity and CNT clusters (vol%) | Maximum size of CNT clusters (μm) | Average grain size (μm) |
Al/CNT | 0 | 1.00 | - | 17 |
0.50 | 4.88 | 89 | 16 | |
0.75 | 6.53 | 102 | 15 | |
1.00 | 5.95 | 78 | 16 | |
1.50 | 7.38 | 177 | 16 | |
Ni/CNT | 0 | 1.05 | - | 15 |
0.50 | 3.22 | 83 | 14 | |
0.75 | 3.96 | 155 | 13 | |
1.00 | 6.67 | 137 | 14 | |
1.50 | 12.47 | 310 | 16 |
Matrix | Reinforcement & strengthening method | CNTs (vol/wt%) | Presence of agglomerates & remarks | Ref. |
Cu | Ultrasonic cleaning + particles composite system + spark plasma sintering | 5, 10 wt% | Yes. CNTs are aggregated into ropes or knotted lumps due to strong inter-tube van der Waals attraction. | [6] |
Cuprous oxide | Vacuum hot pressing at H2 atmosphere | 0, 1, 3, 5 wt% | Yes, at 5 wt%. Thermal conductivity decreases with the increase of the CNTs concentration. | [72] |
Al | Ball milling + Sonication | 2 wt% | Yes. Adverse effects on the properties of final composite products due to the increased porosity. | [73] |
2024Al matrix | Cold isostatic pressing + Hot pressing | 1 wt% | Yes, but low. Elastic modulus and the tensile strength were enhanced markedly. | [74] |
Aluminum–silicon alloy powders | Spray drying | 5, 10 wt% | Yes, 10 wt%. Partial CNT surface damage in case of the 10 wt% CNT coating due to CNT mesh formation and smaller size of spray dried agglomerate. | [75] |
Al | Ball milling | 2 wt% | Yes. Presence of clusters at the early stage of milling which acts as the precipitates results in the lower Young's modulus. | [76] |
Al | Ball milling + Nanodispersion | 0.8, 1.6 vol% | Yes. Poor dispersion of CNTs in the matrix exhibited a non-uniform fracture surface. No aggregations in secondary steps are claimed. | [77] |
Magnesium oxychloride + epoxy | Magnesium oxychloride cement pastes were prepared by ratios of MgO:MgCl2 = 2.2:1. Then coated with epoxy/CNTs | 0, 0.02 wt% | Yes. Water consistency value increases by the addition of CNTs due to that the additional high specific surface area acts as an interface for an efficient stress transfer and causes the strong tendency of the CNTs to form agglomerates. | [78] |
AZ91 + Mg | Melt stirring + high-pressure die casting | 0.1, 0.5, 1 wt% | Yes, at 1 wt%. Agglomerates of entangled MWCNTs with a size of up to 2 µm can be observed. | [79] |
Al | Induction melting | 0, 0.1, 0.2 vol% | No. No cluster or segregation of the nanotubes was seen. | [80] |
Mg | Hot isostatic pressing under high pressure. | 1, 2 wt% | Yes. Homogeneous dispersion of MWCNTs in Mg matrix is obtained. | [81] |
Ag | Modified molecular level mixing method | 0, 6, 12 vol% | Yes, at 12 vol%. Electrical conductivity reduces. | [82] |
Cu | Melt stirring | 0.1 wt% | Yes. The micrograph shows that the raw MWCNTs are agglomerated in big bundles. This act as defects instead of reinforcements. | [83] |
Al (AA5XXX) | Ball milling + hot isostatic pressed + extrusion | 2 wt% | Yes. CNTs clusters were dispersed and claimed as uniform distribution. | [84] |
Matrix | Reinforcement & strengthening method | CNTs vol/wt% | Presence of agglomerates & remarks | Ref. |
Epoxy system | Sonication | 0.025, 0.05 wt% | Yes. Good dispersion was not achieved. | [33] |
- | - | - | Yes. A review paper that has described a lot about agglomeration of CNTs in the polymer matrix. | [121] |
Polypropylene | Melt mixing | 0.5–7.5 wt% | Yes. Low agglomeration effect due to melt dispersion. Lower matrix viscosity promotes secondary agglomeration during the compression molding step. | [122] |
Polyvinyl alcohol | Used prepared sample to study machining | 1, 2, 4 wt% | Yes. CNTs loading beyond 4 wt%, the CNTs were observed to form clusters within the polymer matrix. | [123] |
Polystyrene | Injection moulding process | 20 wt% | Yes. Monte Carlo model was used for simulation to predict the electrical conductivity. The agglomeration has been neglected. | [124] |
Polymer | Injection molding | 1 wt% | Yes. Both partial alignment and MWCNTs agglomeration were observed. | [125] |
Polyvinyl alcohol | Solvent method | Not mentioned | Yes. Substantial agglomerates of nanotubes are visible. | [126] |
Vinyl alcohol | Melt mixing | 0.1, 0.3, 0.5, 1 wt% | Yes. Entanglement of CNTs reduce conductivity. | [127] |
Epoxy | Sonication | Varying ranges | Yes. Varying cluster/aggregate depending on the composites. | [128] |
Vinyl alcohol | Gum arabic treatment | 2 wt% | Yes. Interfere with the tensile properties. | [129] |