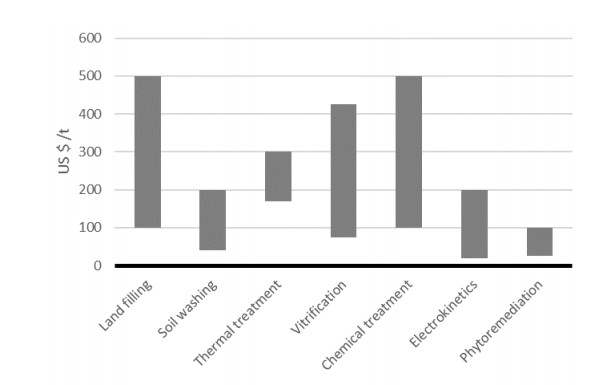
Citation: Jonathan B. Norman, Marcelle McManus. The techno-economic viability of bio-synthetic natural gas production utilising willow grown on contaminated land[J]. AIMS Energy, 2019, 7(3): 285-312. doi: 10.3934/energy.2019.3.285
[1] | Eric Danso-Boateng, Osei-Wusu Achaw . Bioenergy and biofuel production from biomass using thermochemical conversions technologies—a review. AIMS Energy, 2022, 10(4): 585-647. doi: 10.3934/energy.2022030 |
[2] | Hamad AlMohamadi . Production of gasoline from municipal solid waste via steam gasification, methanol synthesis, and Methanol-to-Gasoline technologies: A techno-economic assessment. AIMS Energy, 2021, 9(1): 50-67. doi: 10.3934/energy.2021004 |
[3] | Kevin R Caffrey, Mari S Chinn, Matthew W Veal . Biomass supply chain management in North Carolina (part 1): predictive model for cropland conversion to biomass feedstocks. AIMS Energy, 2016, 4(2): 256-279. doi: 10.3934/energy.2016.2.256 |
[4] | Romain Akpahou, Marshet M. Admas, Muyiwa S Adaramola . Evaluation of a bioenergy resource of agricultural residues and municipal solid wastes in Benin. AIMS Energy, 2024, 12(1): 167-189. doi: 10.3934/energy.2024008 |
[5] | Charalambos Chasos, George Karagiorgis, Chris Christodoulou . Technical and Feasibility Analysis of Gasoline and Natural Gas Fuelled Vehicles. AIMS Energy, 2014, 2(1): 71-88. doi: 10.3934/energy.2014.1.71 |
[6] | Ankita Juneja, Ganti S. Murthy . Evaluating the potential of renewable diesel production from algae cultured on wastewater: techno-economic analysis and life cycle assessment. AIMS Energy, 2017, 5(2): 239-257. doi: 10.3934/energy.2017.2.239 |
[7] | Poritosh Roy, Animesh Dutta, Bill Deen . Miscanthus: a promising feedstock for lignocellulosic ethanol industry in Ontario, Canada. AIMS Energy, 2015, 3(4): 562-575. doi: 10.3934/energy.2015.4.562 |
[8] | Daido Fujita, Takahiko Miyazaki . Techno-economic analysis on the balance of plant (BOP) equipment due to switching fuel from natural gas to hydrogen in gas turbine power plants. AIMS Energy, 2024, 12(2): 464-480. doi: 10.3934/energy.2024021 |
[9] | Antzela Fivga, Lais Galileu Speranza, Carolina Musse Branco, Miloud Ouadi, Andreas Hornung . A review on the current state of the art for the production of advanced liquid biofuels. AIMS Energy, 2019, 7(1): 46-76. doi: 10.3934/energy.2019.1.46 |
[10] | Mousa Tawfeeq, Alan R. Collins, Adam Nowak . The dynamic response of coal consumption to energy prices and GDP: An ARDL approach to the U.S.. AIMS Energy, 2020, 8(6): 1156-1172. doi: 10.3934/energy.2020.6.1156 |
Land is legally defined as "contaminated land" by the UK government [1] as that: "where substances are causing or could cause: significant harm to people, property or protected species; significant pollution of surface waters (for example lakes and rivers) or groundwater; harm to people as a result of activity". These contaminated sites have varying histories, and they may previously have been agricultural land which has become contaminated, the site of a factory, mine, steel mill, refinery or landfill [1]. Such sites may contain a variety of contaminants including heavy metals, oils and tars, chemical substances and preparations, like solvents, gases, asbestos, and radioactive substances [1]. The most common contaminants across the whole of Europe are heavy metals [2] and these are similarly the most common contaminant in England [3], with the most frequent metals and metalloids being Arsenic, Lead, Nickel, Chromium, Cadmium, Mercury and Zinc [3]. The impacts on human health of such contaminants are well recognised [4]. Potentially contaminated sites are estimated at around 3 million within Europe [5], with the true number likely to grow considerably as increased registration of sites is undertaken. No detailed mapping of these sites appears to be available and often estimations of the issue give information only as the number of sites, and not the area covered by such sites. This indicates the lack of data and difficulty measuring the extent of contaminated land. Land that is contaminated requires cleaning (remediation), both to remove the risk to human health and to allow the development of the land, for example to agricultural land or housing.
There are a range of methods, and associated costs, available to remediate contaminated land as shown in Figure 1. Most of these require excavation of the soil, and many techniques involve treatment or disposal offsite (landfilling). In certain situations, it may be possible to undertake some cleaning operations in situ. The most common remediation technique used on contaminated sites in England between 2000 and 2014 was excavation and disposal or capping [3]. Phytoremediation offers the opportunity to remediate contaminated land by growing plants on the land that take up the contaminants during their growth cycle. By harvesting the plants, the contaminants are then removed from the land [6]. Phytoremediation offers a potentially cheaper option than other forms of remediation [7] (also see Figure 1), offering lower capital and operating costs [8]. The main costs of phytoremediation are tilling and preparation of soil, planting, weed and pest control, harvesting and disposal of biomass [8]. Phytoremediation is often more publicly acceptable than other remediation options, being aesthetically pleasing on many contaminated sites and not requiring soil excavation [8]. However, phytoremediation will not be possible at all sites. Matching of the plant species with the contaminants is required [7], and there is a limited depth to which remediation is possible (due to root depth). In addition, total clean-up may not be possible [8]. Phytoremediation is particularly suited to large sites with relatively low levels of contamination [9]. It can also be used on highly decontaminated land to stabilise sites until there is the funding or technology available for full decontamination [6].
Rural locations are generally more suitable for phytoremediation, as in the industrial belt of a city, for example, land is highly valued and phytoremediation will not be so attractive [10], with more rapid remediation technologies preferred. Access to the land for harvesting is sometimes problematic in urban areas. Never the less, sometimes inert contaminated sites are left unused for several years—during this period it is possible that phytoremediation could be used to perform part of the remediation process. The main limitation with phytoremediation is the time required for remediation, which is in the order of years [8]. Estimates of the time for remediation range from 18 months to 16 years, dependent on the characteristics of the site and plant species [8]. Phytoremediation therefore requires considerable planning efforts and a long-term view to the clean-up and development of a contaminated site. Phytoremediation can be combined with other soil treatments (e.g. soil washing). This could be especially interesting where mixed contaminants necessitate multiple approaches to decontamination [7]. The combination of multiple species could also be used to clean multiple contaminants [11].
A possible method of phytoremediation is to grow crops which can be used to produce energy [7,11]. This provides a cheap source of land to grow such crops, is not in competition with agricultural land and provides the co-benefits of remediation of the land [7]. As the harvested crop has elevated levels of contaminants its processing has to be carefully controlled so that these contaminants are not reemitted to the environment in subsequent processing. Care also needs to be taken so that equipment used in the processing of crops is not damaged by the presence of these contaminants. This opportunity has two main benefits: the remediation of contaminated land and the production of bioenergy. It may be that one or the other of these benefits can be prioritised and this can influence the process. For example if uptake of contaminants is maximised through the selection of species and additive soil agents remediation is maximised but the feedstock can be more difficult to deal with. Conversely if the selection of species and site minimises contaminant uptake the remediation service provided is more limited, but the production of bioenergy is possibly made easier. As shown in Figure 1 the expected costs of phytoremediation vary by a factor of four. Costs at a certain site will depend on the specific conditions of the site. It may be that if remediation of land is prioritised then a higher cost is acceptable. The current contribution is concerned with the phytoremediation of heavy metals, using willow, and the production of bioenergy. Other energy crops, including perennial grasses and flowering plants are suitable for phytoremediation and energy production [6,12]. Alternatives may offer advantages over willow dependent on a specific site [6]. Willow is an established energy crop and shows good phytoremediation of heavy metals [7,13,14] (although its suitability needs to be assessed on a case-by-case basis based on the combination of heavy metals at a site, the depth of contamination and other factors, such as soil chemistry). Heavy metals, as discussed above are the most prevalent contaminant in Europe and England. Further unlike certain organic contaminants heavy metals are not broken down by the plant [6,7] and so remain an issue throughout further processing.
A key consideration in the widespread adoption of phytoremediation is the availability of suitable contaminated land. However, there is considerable uncertainty around the amount of contaminated land in the UK. Specifically, there is uncertainty regarding exactly where contaminated sites are, what contaminants are present (and at what levels) and the size of the contaminated sites. This is the minimum required information to be able to begin identifying individual sites and clusters of sites that could be useful in providing land to grow bioenergy crops. Since the year 2000, local councils are required to have an inspection strategy to identify sites that are contaminated, under Part 2A of the Environmental Protection Act 1990 [3]. However, although a strategy is required to help identify sites, this is often linked to when land is identified through the planning process for development. This often means areas that are not identified for development are not inspected. As an indication of the difficulty in the task of identifying contaminated sites, in response to a 2014 survey only 60% of councils in England responded, and of these respondents there had been £32 million spent on assessing 11,000 sites, of which remediation work was required on 511 sites. 10,000 more sites were identified as requiring inspection. The size and level of potential contamination in these sites is unknown.
In the absence of more detailed information, areas of heavy industry can be used as a proxy to indicate likely sites of contamination [9]. It has been estimated that as much of 1–1.5% of UK land area may be considered derelict and in need of remediation, with much of this potentially available for energy cropping [6]. This is broadly in line with an estimation by the Environment Agency of 50,000 to 300,000 ha of contaminated land [6], split between 100,000 sites, with 5,000 to 20,000 of these sites requiring decontamination under legislation [6] (note the high levels of uncertainty attached to these values). The uncertainty prevents an assessment of the overall potential for such an opportunity and the identification of clusters of contaminated land that may make such an opportunity locally attractive. In addition, without having information on contaminated land available it is not possible to plan remediation with the timescale necessary for phytoremediation to be a viable option. If contaminated sites are not properly investigated until they are being developed for other uses this is too late for phytoremediation to be considered.
The combustion of biomass to provide heating is well established, both throughout human history and in more modern hot-water heating systems. Capturing the energy from combustion of biomass to generate electricity, often by co-firing with coal, is also becoming widespread. There are additional opportunities to convert biomass into an energy vector that can improve its characteristics in terms of the ease of transport of the vector, its energy density (by mass or volume), the potential end uses of the vector and the end use efficiency. Examples of such vectors include bio-synthetic natural gas (SNG), biohydrogen and liquid fuels. A substantial advantage of these fuels over other forms of renewable energy is their potential to directly replace fossil fuels, therefore using existing infrastructure and end use devices. Additionally, the ability to store energy in these forms is advantageous compared to the intermittency that many renewable solutions experience (in the absence of adequate storage options).
The gasification processing route is assessed in the current work. It is well suited to lignocellulosic biomass (such as willow) [15]. Gasification is a thermochemical process, which converts a solid fuel to a gaseous fuel, consisting mainly of hydrogen and carbon monoxide [16,17]. This "syngas" can be combusted for heat or power [18]. Alternatively, syngas can be used as an intermediate product to manufacture a range of final products, including bio-synthetic natural gas (bioSNG) [19,20], biohydrogen [21,22], liquid fuels and value chemicals [16,18]. The focus of the current work is the production of bioSNG (with the potential for biohydrogen also discussed). The gasification route to bioSNG production offers a more efficient route than anaerobic digestion (AD) [23]. The process route also offers a relatively pure stream of carbon dioxide and so can be combined with carbon capture and storage (CCS) technology [20]. BioSNG represents a fuel that can be immediately distributed through the existing gas grid and used to directly replace natural gas in heating systems (both domestic and industrial), there is also interest in its use as a low carbon transport fuel, especially for heavy goods vehicle, where electrification may pose additional challenges to those faced by passenger vehicles. BioSNG is also referred to as biomethane, for consistency the term bioSNG is used throughout the current contribution.
The aim of the current study is to perform a technoeconomic assessment of the production of bioSNG via the gasification of willow grown on contaminated land. The objectives are listed here, the layout of the paper broadly follows these objectives.
1. To identify the most promising process route, for the production of bioSNG via gasification of willow grown on contaminated land.
2. To assess the technical barriers and opportunities to the implementation of this route.
3. To perform an economic analysis of the chosen process route, including an assessment of uncertainty in key parameters and their effect on economic feasibility.
4. To use the findings to assess the technoeconomic feasibility of the identified process route and to make recommendations for the future development of this opportunity.
There are two drivers for the opportunity of producing bioenergy from willow grown on contaminated land. The remediation service that is provided to the land and the ability to produce bioenergy, without utilising agricultural land. If one of these drivers is given preference it may affect decisions regarding the opportunity. This is discussed throughout the current work.
Figure 2 indicates the main subsystems involved in the production of bioSNG via the route of interest. Willow is grown on contaminated land (potentially at a number of sites), contributing to the remediation of that land (the timescale of remediation and whether total remediation is possible will depend on the characteristics of the individual sites); it is chipped and delivered to the gasification installation; bioSNG is produced to UK gas grid specifications; the bioSNG can be used to replace natural gas in providing heating and transport services; additional flows to the gasification installation include energy and other consumables; waste flows include carbon dioxideand byproducts from cleaning processes. The scope of the current work is indicated by the dashed line in Figure 2, it is the gasification process that is of principal interest here—that is taking the processed woodchip grown on contaminated land and producing bioSNG suitable for injection into the UK grid. The costs and the regulations regarding grid injection are based on the case of the UK. The flows that cross this system boundary are considered but the up or downstream processes are not assessed in detail here. Therefore, the activities that take place on the contaminated land are not considered in detail, the interest is the feedstock arriving at the installation. Some of these factors outside the system boundary are discussed in reference to the results here, but are not part of the principal analysis. As the use of biomass grown on contaminated land for gasification is a novel topic previous work informing the current analysis includes assessments with a feedstock of clean wood and also waste. This then covers literature related to both the gasification of wood and dealing with contaminants (that are present in waste) in the gasification process. Energy values given here are in terms of net calorific value (NCV, or lower heating value LHV), unless specified otherwise.
The process steps involved in the production of bioSNG through gasification can be broadly split into five steps [20]. The stages covered are:
1. Fuel preparation: this may take place offsite and includes drying and chipping.
2. Thermal treatment: gasification of the prepared feedstock to produce syngas, the intermediate product of the process.
3. Syngas cooling and cleaning: removal of tars, sulphur and chlorine compounds and heavy metals is required. Cleaning techniques include wet scrubbing, active carbon filtration and other gas polishing.
4. Methanation: through the use of a catalyst the cleaned syngas is converted to methane. This includes a water-shift reaction to convert carbon monoxide and water to hydrogen and carbon dioxide.
5. Purification: carbon dioxide, hydrogen and other gases are removed so the bioSNG meets gas grid or transport specifications. This may include the injection of additional gas such as propane to alter the calorific value of the gas.
In general, each step of the process has been utilised and proven [20]. However, the combination of steps to produce bioSNG from a feedstock grown on contaminated land is novel. The combination of similar steps to produce bioSNG from virgin biomass or waste feedstocks is an area that is reaching demonstration stage [20]. However, no industrial scale commercial installation for SNG production from biomass is in operation [24].
The important variations (as they relate to the current study) on this broad process route are discussed further below. More detail on specific process routes can be viewed in other reports (for example [25]), it is not the intention of the current work to go deeply into a description of the technical processes involved. The integration of the process steps to recover and recycle heat (through water and steam systems) is key to the installation efficiency [25]. Excess heat can be sold to local heat networks, or other demands, or if of sufficient quality can be converted to electricity to supply the on-site demand and be sold if sufficient supply exists [26].
Initial fuel preparation is considered outside the scope of the work, it is assumed that fuel is supplied, chipped with a moisture content (m.c.) of 25% and an energy density of 18 GJ/odt, which is in line with standard chipped willow [27]. The feedstock is further dried using heat recovered from the gasification process [25].
There is a wide choice of gasification technologies, including updraft fixed bed, downdraft fixed bed, entrained flow, bubbling fluidised bed, circulating fluid bed, dual fluidised bed and plasma [28]. Additionally, many of these designs, can be pressurised or atmospheric and can be air, oxygen or steam blown [17]. The choice of gasification technology is dependent on the feedstock and the use of the gas. The operation of specific gasification technologies will not be discussed in detail here, the reader is referred to a wide literature on the subject if further information is required, for example see [17,22,28,29].
Two technologies are recommended for the gasification of biomass for methanation and conversion to synthetic natural gas (bioSNG) [24]. These are indirect gasification and oxygen blown fluidised bed gasification. These are preferred as when making a grid quality bioSNG low values of inerts, such as nitrogen and argon are required [30]. Indirect gasifiers utilise two chambers that separate gasification and combustion, therefore air can be used for combustion, but a low nitrogen syngas is obtained as air is not passed to the gasification chamber. In contrast oxygen can be used with a single chamber fluidised bed gasifier, limiting nitrogen in the syngas. A principle advantage of indirect gasification is that the syngas produced can have a high methane content, limiting the requirement for further conversion. Indirect gasification has been found by some studies to be more energetically efficient in bioSNG production [31]. However, others have found the risk of nitrogen leakage into the syngas [23] and that indirect gasifiers produce higher levels of tars and volatile organic compounds that can be difficult to clean from the syngas [20,24]. Oxygen blown fluidised bed gasifiers have the advantage of being able to use both waste and biomass feedstocks [23], and are well suited to conversion for the production of biohydrogen [21] (the flexibility in terms of feedstock and final output in considered important here and discussed further throughout the paper). Some studies have found oxygen blown gasifiers to offer lower cost per unit of SNG produced, and a lower investment cost compared to an indirect gasifier [32]. The technology is more easily pressurised, which can decrease the volume of equipment required and it is therefore more suitable for high capacities [24], which can be important in lowering costs [32]. The additional requirement for oxygen is an additional cost however [19]
Zinn and Thunman [15] conclude that of these two technologies the best choice will be dependent on the experience and belief of the supplier and customer, with arguments for each technology. Heyne [24] found that both direct and indirect technologies performed equally well. As the commercial market for this application develops a technology winner may emerge by virtue of its proven use in earlier projects. In the current application an oxygen and steam blown fluidised bed gasifier is preferred, specifically with a plasma cleaning step, as discussed below. This technology has been developed by Advanced Plasma Power, for gasification of waste feedstocks [33]. In partnership with Cadent and Progressive Energy the developers have built a pilot installation and are currently commissioning a commercial facility [34]. The primary reasons for the choice of this gasification technology are:
1. Good information availability on both the process and the associated economics. Details as they are used in the current work are included below, the reader is referred to related publications for full details [20,25,30,34,35].
2. Building on a previously developed technology (within the UK) is seen as a less risky opportunity.
3. The technology was developed to use a waste-derived feedstock. This gives confidence in the ability of the process to clean the contaminants from the feedstock of interest in the current study. Processes that are only developed with clean biomass feedstocks are seen as significantly more risky in this regard.
4. The ability to use different fuels could be key to realising the potential of feedstocks grown on contaminated land (as discussed later in the paper).
The remainder of the current contribution refers to this process route: oxygen and steam blown fluidised bed gasification with a plasma cleaning step. For full details of the installation that this is based on, including Sankey and mass flow diagrams see associated references [20,25].
Although the removal of the increased contaminants that may be present in feedstock grown on contaminated land is an important consideration, the removal of contaminants present in feedstocks is not unique. Figure 3 shows the typical removal of contaminants required between syngas leaving a (clean) biomass gasifier and the requirements for the methanation step, in order to give satisfactory catalyst life. The difficulty associated with cleaning is not in bulk removal of contaminants, but getting down to the final ppm/ppb levels [23]. The data showing absolute levels of contaminants in syngas when leaving the gasifier and required by the methanation step are shown in the supplementary information.
The level of contaminants that exist in willow grown on contaminated land is dependent on the level of contaminants in the soil, the precise species of willow and soil type [4,7,10,11,36]. Soil can also be treated by microbes, micronutrients or chelating agents to increase the uptake of contaminants [7,9,13] (although such treatments can also increase the risk of leaching of heavy metals from the soil [13]). The level of contaminants in the feedstock can therefore be controlled to some extent for a given piece of contaminated land by selection of species and soil additives. A choice can be made to maximise the uptake of contaminants and the phytoremediation service provided, or to minimise contaminant uptake (and land remediation) but to have a less contaminated (and therefore more easily utilised) feedstock. Even in the case of minimum remediation there would be services provided to the contaminated land by immobilising contaminants and stabilising soil [7]. There is also the potential to pre-process the feedstock, using washing for example, which can remove some contaminants before the gasification process [7].
Due to the possible variations in contaminant level present in the feedstock it is difficult to make a confident estimation of the range of contaminants that might be faced. A meta analysis on the uptake of heavy metals in willow notes that there are "contradictory and inconsistent results" on the accumulation of cadmium, lead and zinc accumulation in parts of willow [37]. The meta analysis concluded that all parts of the plant accumulated significantly higher levels of these contaminants than in uncontaminated soils, although there was significant variation among different parts of the plant [37]. Similarly, a review of biomass production on contaminated land found large differences in the bioaccumulation (that is the ratio of element in the biomass compared to in the soil) [10]. For example, the range of the bioaccumulation factor for cadmium found in the wood of a single species (Salix viminalis) ranged from 0.72 to 16.8 based on four studies [10]. Therefore, rather than base contaminant removal steps on the contaminant levels in willow from a limited number of case studies, the approach taken here is to base contaminant removal on the processes used when a waste derived feedstock is utilised. This is likely a conservative assessment, the heavy metal content found in waste derived fuel and in waste wood is substantially higher than that found in phytoremediating plants [38,39]. This approach means that an installation fitted to remove contaminants in this manner will also be able to utilise waste derived feedstocks, which can be a considerable advantage for the technology's prospects (see the discussion section). The supplementary information includes information on the concentration of contaminants in willow grown on contaminated land in comparison to the contaminants in municipal solid waste [38] and in comparison to the soil in which the willow was grown [14]. The reported contaminants vary significantly between these two studies and are broadly indicative of the range of contaminants that may be seen in such a feedstock,
Coal is the most widely used feedstock for gasification worldwide [40]. The process is used mainly to produce chemicals, although liquid and gaseous fuel production and fertiliser production are all becoming increasingly common [40]. Whilst coal gasification uses entrained gas flow technology followed by scrubbing techniques to clean the syngas it is not economic to use these same cleaning techniques on a modestly scaled installation using a waste or biomass feedstock [30] (although variations on these techniques are utilised). A diagram showing the thermal treatment and syngas cooling and cleaning stages is shown in the supplementary information. The first step of cleaning in the process assessed here is a high temperature syngas treatment stage (at around 1200C), which comprises an electric arc plasma converter [30]. The combination of this plasma cleaning with the fluidised bed gasification unit comprise the Gasplasma process developed by Advanced Plasma Power [33]. The plasma converter breaks down (cracks) tars, heavy metals, chars and sulphur bearing species [27,30]. This then allows conventional dry and wet gas processing and polishing technique to clean the syngas to the levels required for methanation.
In subsequent cleaning steps syngas is cooled to 200C (generating steam used elsewhere in the process [25]), following this is a dry filter, a wet acid scrubber [25] and an oxidative alkaline wet scrubber [30] (see [20,25] for more details). The effluent and condensate from the scrubber are treated and discharged to the sewer [25]. Following this the syngas passes through two polishing guard beds required to meet stringent contaminant limits (see Figure 3). The first removes residual hydrogen chloride, the second removes heavy metals (the plasma converter and scrubbing processes earlier in the process having provided initial bulk removal of these contaminants) [25]. After compression and heating, two further reactors remove alkenes, halogens and sulphur to parts per billion.
After cleaning of the syngas, a water gas shift is carried out so the majority of carbon monoxide in the syngas reacts with steam over a catalyst to form hydrogen and carbon dioxide [25]. Following this the gas is cooled and heat recovered. Methanation takes place in a number of reactors, over a catalyst that promotes both the shift and methanation reactions [25]. Carbon dioxide is then removed using activated potassium carbonate solution as the solvent [25]. The produced gas is then dried to meet grid specifications, the gas is odourised and exported to the grid. Depending on local grid characteristics small quantities of propane may be added [25]. A key challenge is reduction of hydrogen content to 0.1% to comply with grid specifications. A relaxation of this limit to 0.5% would benefit bioSNG production [20].
The fate of heavy metals (and other contaminants) from the bioSNG process is of importance, if they were reemitted to the environment the benefits of phytoremediation would be lost. During gasification heavy metals are found in the bottom ash, fly ash, and are volatised [6,14,39]. In a small scale, fixed bed, downdraft gasifier concentrations of cadmium, lead and zinc were found to be in higher concentrations in the filter fly ash in comparison to the bed, bottom or cyclone ashes, whereas chromium, copper and nickel were more evenly split between these locations [14]. Whilst gasifier ash from a clean biomass feedstock may be used as a fertiliser this is not possible with ash from a contaminated feedstock [6]. In the process assessed here the plasma converter produces a stable and inert product, which may be used as a construction material, rather than the ash of a conventional gasification unit [41]. This avoids the issue of leaching of contaminants from disposed ash [41]. The other by products such as air pollution control residues must be disposed of through proper channels and the costs of this are included in the calculations elsewhere in the paper.
The level of policy support available has been found to be key to the development of bioSNG production via gasification technology [20,23]. There are two primary mechanisms in the UK that support the production of bioSNG. These are the Renewable Heat Incentive (RHI) [42] and the Renewable Transport Fuels Obligation [43], which supports bioSNG under the Renewable Transport Fuel Certificates (RTFC) scheme. As is indicated by the names, these are designed to promote the use of bioSNG in heating and transport respectively. Where bioSNG is injected into the grid support can be claimed under either of these policies (but see the restrictions on the RTFCs discussed below). The primary difference for the owner of an installation producing bioSNG is the level of support available. The RHI pays a fixed level of support (although this level has changed considerably over the years that the RHI has been operating, see Figure 4 below) that falls with the amount of bioSNG injected [44]. In contrast the RTFCs are traded by fuel suppliers (who have to meet certain criteria for producing renewable fuels) and so do not have a fixed price. However, the certificates have a "buy-out" price that sets a maximum price (this is 30p/certificate), historical information on the traded price of these certificates are available [45]. BioSNG is eligible for 1.9 certificates per kg [46], as a dedicated energy crop the bioSNG produced in the current application would also be able to claim double certificates [47]1.
1 The classification of the feedstock as a dedicated energy crop, for the purposes of this policy, was confirmed by the Biofuels Transport division of the Department for Transport in the UK. Personal communication, email with Paul Rothwell, Policy Adviser, Low Carbon Fuels, Department for Transport email, 20th May 2018.
Figure 5 shows support offered under the RHI and RTFCs for a 20 MW output installation, operating for 7800 hours annually. The stepped level of support under the RHI shows the three tiers of payment, the highest level of support is available for the first 23% of output here. The RHI has recently increased for bioSNG (as of May 2018), the previous rates are shown in Figure 4 for comparison. The level of support given to an installation under the RHI is based on the date it was accredited. The levels for the RTFC shown in Figure 5 represent prices of 10p, 20p and 30p per certificate, representing a range of possible prices for the certificates [46]. The area under the curve represents the total support available per year to the installation. It may be that an installation chooses to claim a proportion of output under the RHI (at the maximum level of support) before switching to the RTFCs for the remainder of output. In order to sell RTFCs to fuel suppliers there must be sufficient users of natural gas/bioSNG fuelled vehicles. Securing such a contract to supply bioSNG for transport may be difficult [20], if the market for natural gas vehicles grows this will become less of a barrier.
One of the principle advantages of phytoremediation is its low cost in comparison to other remediation options (see Figure 1). How the benefits offered from remediation are translated to a feedstock price for bioSNG production is a difficult question, a considerable range of phytoremediation costs is presented in Figure 1, with a range of site specific factors influencing the costs. The costs of planting, growing and harvesting a crop on contaminated land would be expected to be similar to the costs when using clean land, for two otherwise comparable sites. There may be additional costs in ensuring there is no "leakage" of the contaminants during the process [8].
The costs of the willow grown on contaminated land (the feedstock for the current study) are likely less dependent on the costs of the phytoremediation scheme however than the prices of alternative feedstocks. It is therefore insightful to examine these alternative feedstocks to determine the maximum and minimum prices that a feedstock grown on contaminated land could command. One possible end use of phytoremediating crops is to landfill the crops, in this way the contaminants are removed from remediated land and disposed of in a manner that prevents reemitting of contaminants [48]. Disposal of biomass can be a major cost of phytoremediation, such disposal costs are included in Figure 1. These disposal costs vary by region, and the data shown in Figure 1, which is for the USA [8], will differ in this respect from the UK. In order to avoid this disposal route and the associated gate fee of landfilling the crops it may be that the operator of a bioSNG installation is able to claim a benefit from using this feedstock. This is commonly the case where a waste derived fuel is used in such an installation. Gate fees for non-hazardous waste (including landfill tax) are around £107/tonne [49]. A demonstration bioSNG gasification installation in the UK gets a benefit of around £50/tonne for refuse derived fuel (RDF, some processing is required to produce this feedstock from the waste that would be landfilled)2. At the other end of the cost spectrum are energy crops grown on clean land. In 2009 prices of wood chips used for heating in the UK were in the range £60–90/tonne (central case £80/tonne) for an industrial user, where the chips were at 25% m.c. with an energy density of 18 GJ/odt [27]. These prices were predicted to increase to £83–£104/tonne by 2020 [27]. The feedstock grown on contaminated land would not sell for a higher price than that grown on clean land, the operator would also not be able to claim a benefit greater than the cost of landfilling the crop. An illustrative case of where the price may lie could come from waste wood. This can often contain contaminants [50] and if landfilled requires a gate fee (around £35/tonne [49]), however due to its value as a fuel it can sell for £10/tonne (approximate price from a bioSNG demonstration facility for grade C waste wood2). The price at which an energy crop will sell for also influences the economics of the remediation scheme that supplies the crop. This is an important consideration but outside of the scope of the current assessment. The approach of the current analysis is to calculate what feedstock costs would be required for a project to be economic given the value of other input parameters (as discussed below).
2 Personal communication, email with Andrew Cornell (Advanced Plasma Power), email, 1st February 2018.
Key to the outcome and predicted success is the driver, and associated counterfactual, whether the goal of the project is to remediate land or to produce bioenergy. If land remediation is the primary goal and provides a strong economic case for the phytoremediation then feedstock sales are likely of secondary importance. Conversely, if the primary objective is to produce a feedstock to sell to produce bioenergy and land remediation is not considered a high value service (or the characteristics of the feedstock and land are such that remediation is not achieved at a significant level) then maximising the value from the sale of the feedstock may be of primary importance to the project. Whether a single actor controls both the growth of the feedstock, land remediation and bioSNG production, or whether multiple actors are involved (including different owners of various parcels of land, with different drivers) could influence how the overall economics of such a project are viewed.
The key unknown in the economic assessment is the feedstock cost. The approach here is therefore to assess what feedstock cost would be required to make the process economically viable. This is determined by conducting a cost-benefit analysis for the annual costs of a facility. The capital costs are annualised using a relevant hurdle rate for the initial investment.
The required feedstock costs are calculated using Eq 1:
Feedstockcosts=Revenues−(CAPEXEAC+OPEX)Feedstockrequired | (1) |
where Revenues consist of those from selling the bioSNG produced and the policy support available (as discussed above). CAPEXEAC is the equivalent annual cost of capital expenditure (see below), and OPEX is the operating costs, which comprise labour, consumables, maintenance, energy costs (specifically electricity and natural gas, see below) and other costs.
The annualised capital cost is calculated using Eq 2.
CAPEXEAC=CAPEX⋅r1−(1+r)−n | (2) |
where CAPEX is the total capital cost (detailed below), r is the hurdle rate for the capital investment, and n the lifetime of the project (in years).
The feedstock required (given in annual energy terms) is calculated given the annual output of the installation and the gross efficiency of the process, ηgross (that is the output of bioSNG per unit of feedstock input).
Feedstockrequired=bioSNGoutputηgross | (3) |
Calculating feedstock required in energy terms means the feedstock costs are given per unit of energy demand. To convert to feedstock costs per tonne, and assuming a 25% moisture content [27].
Feedstockcosts(pertonne)=Feedstockcosts(perunitofenergy)⋅Energydensitywillow(energyperodt)⋅0.75 | (4) |
Given the emerging nature of the technology there is considerable uncertainty with any economic assessment. To capture this for key input parameters a central value, maximum and minimum value are estimated from the given literature (see below). Two approaches are taken to assess uncertainty, Monte Carlo analysis and sensitivity analysis. The Monte Carlo analysis utilses a triangular distribution fit to each input parameter with the central value representing the mode in the distribution and the maximum and minimum values representing its limits. By running the model a large number of times and sampling from the distribution of each input parameter the distribution of the result (in this case feedstock cost) is found. Sensitivity analysis is conducted to identify the most important input parameters for influencing the feedstock price. A one-at-a-time sensitivity analysis is conducted. For each parameter the effect on feedstock price of the parameter taking its maximum and minimum values, whilst all other parameters are held at their central value is used to identify the most important parameters.
Much of the costs data are based on those available for an nth of a kind installation with a rated output of 76 MW bioSNG [35]. It was felt appropriate to use cost estimates for an established nth of a kind installation as the use of feedstocks grown on contaminated land is likely to be pursued after the technology is first established with waste and clean biomass feedstocks. Costs are shown in Table 1, this table along with full references for each parameter is given in the supplementary information. Maximum and minimum expected values of the parameters are given to allow an uncertainty analysis. In addition to information on the costing and operations of a demonstration installation of the process route considered here [25,35] studies of similar bioSNG gasification systems were drawn on [21,23,26] and energy cost data was taken from government statistics and projections [51]. The costs used are based on utilising a waste feedstock (RDF). The operating costs with a waste feedstock will likely be higher than with a biomass feedstock grown on contaminated land, due to increased cleaning consumables and the costs of disposing residues from air pollution control2. Estimating the extent of this cost reduction is not possible without tests on specific feedstocks, here the full costs as with a waste feedstock have been retained as a conservative estimate. Heat recovery is practiced throughout the installation, this includes the use of excess steam to produce electricity [25], the electrical demand shown in Table 1 is the net grid demand beyond this self-generation.
Parameter | Unit | Value | Min | Max |
Load factor | Proportion | 0.9 | 0.85 | 0.95 |
Hurdle rate | Percentage | 10% | 8% | 12% |
Lifetime | Years | 25 | 20 | 30 |
Capital cost for 76 MW bioSNG output installation | £million | 150.7 | 105.5 | 195.9 |
Capital cost scaling factor | - | 0.6 | 0.5 | 0.7 |
Labour cost for 76 MW bioSNG output installation | £million/year | 1.8 | 1.3 | 2.3 |
Labour cost scaling factor | - | 0.15 | 0.1 | 0.2 |
Consumables costs for 76 MW bioSNG output installation | £million/year | 3.1 | 2.2 | 4.0 |
Consumables costs scaling factor | - | 1 | 0.9 | 1 |
Maintenance costs for 76 MW bioSNG output installation | £million/year | 2.9 | 2.0 | 3.8 |
Maintenance costs scaling factor | - | 0.6 | 0.5 | 0.7 |
Other operating costs for 76 MW bioSNG output installation | £million/yr | 3.5 | 2.5 | 4.6 |
Other operating costs scaling factor | - | 0.6 | 0.5 | 0.7 |
Gross efficiency | output bioSNG per input of feedstock energy | 64% | 57% | 70% |
Natural gas energy demand | input required per unit of bioSNG output | 0.01 | 0.009 | 0.011 |
Electricity demand required | input required per unit of bioSNG output | 0.095 | 0.086 | 0.105 |
Wholesale gas price | £/GJ | 7.05 | 3.58 | 8.73 |
Electricity price (retail, industry) | £/GJ | 36.01 | 29.64 | 39.03 |
Natural gas retail price | £/GJ | 10.97 | 6.15 | 12.9 |
Energy density willow | GJ/odt | 18 | ||
Policy support RTFC | £/GJ bioSNG | 15.2 | 7.6 | 22.8 |
Policy support RHI | £/GJ bioSNG | 10.1 | 7.8 | 17.3 |
The input parameters are assumed to stay constant throughout the lifetime of the project. In reality some of these costs, specifically those related to energy and other operating costs will vary. The costs as assessed here can be considered the mean costs throughout the life of the project.
Much of the costs data is based on a 76 MW output installation (as this was the installation with best data availability [35]), costs are scaled to different size installations according to Eq 5[52].
Pb=Pa(cbca)x | (5) |
where P is the purchased cost of equipment, c is the capacity of the equipment and x is the scaling factor. The subscript a refers to the base case (here the 76 MW output installation) and the subscript b the case for which cost information is required. 0.6 is often used as the scaling factor for installation equipment [52]. Here the scaling factor is estimated for each component of the capital and operating costs utilising available data. The scaling factors are shown in Table 1.
When a bioSNG installation uses a biomass or waste feedstock then due to the distributed nature of the feedstock and its lower energy density (in comparison to coal, which is used as the feedstock in large gasification installation), an output of 10–100 MW is considered possible [30]. Due to the more restricted nature of feedstock grown on contaminated land any installation is likely to be towards the lower end of this range. Two sizes of installation are examined in the results here, 20 MW and 50 MW output.
Figure 6 shows the breakdown of capital costs for the base case of a 76 MW installation. The breakdown of costs is similar for a smaller installation [35].
Figure 7 shows the annualised costs associated with a 20 MW output installation. Feedstock costs are not shown, the costs shown in Figure 7 are used to calculate the required feedstock costs for a viable installation. For the case shown if the RHI is claimed, a benefit of £71/tonne of feedstock is required, if the RTFC is claimed, a benefit of £30/tonne is required (a benefit is indicated by the negative cost). A similar proportional breakdown of costs is found for a 50 MW installation (this is shown in the supplementary information), the feedstock costs required for a 50 MW installation are a benefit of £25/tonne if claiming support under the RHI and a cost of £30/tonne if claiming under the RTFC. These costs should be considered alongside the costs from using waste-derived fuels (−£50/t), waste wood (£10/t) and clean feedstock costs (£80–100/t). It may be the case that the optimal strategy for claiming support is achieved by claiming the highest support available under the RHI and then switching to the RTFC as the RHI drops to a lower level (see Figure 5). This would give slightly increased feedstock costs (or reduced benefits required) than those given here.
Figure 8 shows how the required feedstock cost varies with the size of installation when claiming support under the RHI or RTFC. This is due to the scaling effect of costs. As the installation size increases the proportion of output that it is possible to claim the maximum level of support for under the RHI reduces. Therefore installation size influences feedstock costs less dramatically when claiming under the RHI than for the RTFC. For the case of claiming under the RTFC the size of installation required to give an estimated feedstock cost of a benefit of £50/t and a cost of £10/t are 16 MW and 36 MW output respectively (these costs are comparable to those seen with a waste-derived feedstock and waste wood).
Figure 9 shows the results of a Monte Carlo analysis using a triangular distribution for each of the input parameters shown in Table 1. The distribution for policy support is based on the values for the RTFC given in Table 1. Cases for a 20 MW and 50 MW output installation are shown. Table 2 shows the results of the Monte Carlo analysis in numerical form. The probability of the feedstock cost being higher than each value is shown for the 20 MW and 50 MW output installation. For example, there is a 66% chance that the feedstock cost can be higher than −50£/t for the 20 MW installation and there is a 22% chance of the feedstock cost being higher than 50£/t for the 50 MW installation.
Feedstock cost (£/t) | 20 MW output | 50 MW output |
−50 | 66% | 99.5% |
0 | 15% | 78% |
10 | 9% | 68% |
30 | 2% | 44% |
50 | 0.3% | 22% |
80 | 0% | 4% |
The results of a sensitivity analysis for a 50 MW installation are shown in Figure 10. Parameters are varied between the minimum and maximum values shown in Table 1, whilst all others are held at their central value. Policy support variation is based on that given for the RTFC in Table 1. The cost of feedstock is most sensitive to expected variations in policy support, wholesale gas price (the price that the resultant bioSNG is sold at), capital expenditure, hurdle rate and load factor. Policy support, wholesale gas price and capital expenditure have the potential variance to move the price of feedstock below £10/t (the level of waste wood) by themselves. Similar results in terms of which are the most sensitive parameters are obtained for the case of the 20 MW installation, these are shown in supplementary information. In the 20 MW case the CAPEX and CAPEX scale factor assume more importance.
Figure 11 shows how the most important parameters identified in Figure 10 combine to influence feedstock price. In each of the subplots of Figure 11 two parameters are varied and the effect on feedstock price is shown, whilst all other parameters are held at their central value. The most important parameter identified in Figure 10, policy support, is used in each of the four cases and how this combines with variation in wholesale gas price, capital expenditure, hurdle rate and load factor to influence feedstock price is shown in Figure 11. Results are shown for a 50 MW installation. As an example of result interpretation, referring to the top left of Figure 11 (the case of policy support and bioSNG price variation) for policy support of £20/GJ and a bioSNG price of £4/GJ the feedstock price is around £45/tonne, for a policy support of £10/GJ and a bioSNG price of £5/GJ the feedstock price is around −£35/tonne (a benefit is required). Figure 11 confirms policy support as the most important input in determining the required feedstock cost, with the wholesale price of gas and the capital expenditure variations also being significant.
The results show that although technically feasible, if the driver is energy production, there is not currently a clear economic case for producing bioSNG through gasification using energy crops grown on contaminated land. For energy production, the viability is strongly dependent on the price (or gate fee) that the feedstock will command. The level of policy support available is also found to be a key parameter, alongside (to a lesser extent) the wholesale price of bioSNG and the capital expenditure required for the installation.
The price (or gate fee) of the feedstock is important to the viability of the project but also of considerable uncertainty, as such a feedstock is not currently produced and sold commercially. The approach in the current analysis was to compare the feedstock price that was economically viable, to the price of comparable feedstocks. An important consideration in this assessment is whether the goal of the growth of energy crops on contaminated land is primarily to remediate the land, or primarily to produce a commercial crop. In the former case it may be that a lesser price for the crop is acceptable and is taken as an additional benefit of the land remediation (or even that the grower will pay for the crop to be taken away, the use of the crop then becoming a benefit for the plant operator). In the latter case it may be that a price more comparable to conventional energy crops is desired (with some consideration for the lower quality of the feedstock produced and the co-benefit of land remediation). The range of prices assessed in this study, comparing the feedstock price to that for waste-derived fuels, waste wood and "clean" energy crops seems a reasonable approach for the current purposes. The final use of the energy crops is also an important consideration and whether the gasification route or another bioenergy production route is preferred would require a more complete analysis. Alternative uses of contaminated willow including combustion [10,53] and pyrolysis [54,55] are also possible and will have their own benefits and barriers. Here the focus is the gasification production route.
A considerable barrier for potential investors may be the uncertainty of policy support. One possible support mechanism, the Renewable Heat Incentive (RHI) has historically shown considerable variation in the level of support available (see Figure 4). The other main support mechanism, Renewable Transport Fuel Certificates (RTFCs) are inherently uncertain in the level of support offered, as they are traded certificates (given the still emerging nature of the gas-fuelled transport market the future value of such certificates is especially uncertain). Carbon dioxide capture and sequestration (or use) is possible with the technology assessed, as a relatively pure stream of carbon dioxide is removed from the installation as part of the process. Given a financial incentive to sequester carbon dioxide, this may provide economic benefits, which are not assessed here. Clear financial pricing of environmental costs and benefits could give investors more clarity in investing in technologies such as that discussed here, and could replace the existing policies. An additional consideration when assessing phytoremediation is the recovery of metals. Such an opportunity could offer advantages in terms of economics (especially in the case of recovery of rare and valuable metals) and environmental considerations. It may be that such "phytomining" is possible with hyperaccumulating species, dependent on the combination of metal and species, with genetic modification perhaps representing the future of this area [56,57]. Such phytomining is not likely to be economic using willow however [58].
A larger installation (of 50 MW) shows a significantly better economic case than a smaller (20 MW) installation. It may be difficult to fuel a larger installation size solely by energy crops grown on contaminated land. Given an average annual yield from a willow plantation of 10 odt/ha [59] the land requirements to fuel the 20 MW and 50 MW installation are 4,900 and 12,300 ha respectively. The distribution of such suitable land is also of importance in assessing the opportunity, as the catchment area of a gasification installation must be such that excessive transport doesn't make such a scheme unviable from an economic, or an environmental perspective. Therefore, fuelling larger system with a combination of waste derived fuels and energy crops may be an approach that improves the project economics. This is viable with the chosen technology, with the gasifier able to operate on biomass or waste derived fuels [25]. Waste derived fuels have the advantage of commanding a benefit when used as a feedstock due to the avoided gate fee from the alternative disposal via landfill, and they are widely available. Under the RHI and RTFCs they only receive support for the biogenic proportion of the feedstock. They will also likely have higher operating costs. One barrier to the use of multiple feedstocks are that the suppliers of waste will prefer a contract that takes waste at all times, not for only part of the year. However, with careful planning from the outset of a project this is unlikely to be an insurmountable barrier.
The potential for the technology assessed here is dependent on the continuing demand for natural gas, and synthetic natural gas in the heating market, alongside, to some extent the development of demand in the transport market. The influence of fuels that are produced from a feedstock grown on contaminated land are likely to be a minor player in the development of future energy systems and the market and development of technology would need to be driven by waste and/or clean biomass fuelled systems to some extent. The further uptake of anaerobic digestion and the production of bioSNG via this production route could also help the development of a suitable market. If heating and transport systems were to be wholly electrified it is unlikely that the technology would continue to be developed. The existence of the gas grid for transporting bioSNG is a major advantage for the technology going forward, as is the fact that it is fully fungible for natural gas. The evolution of gas networks (mostly using hydrogen derived from fossil gas) has been found by some to be significantly cheaper and with less practical obstacles than electric heating systems [60].
The gasification process is a viable production route for hydrogen from biomass [61,62]. There is potential to use similar technology to the gasification process discussed here to produce biohydrogen. Potential markets for biohydrogen includes the enrichment of the natural gas grid [21,63], conversion of the natural gas network (and end use devices) to hydrogen [64], supply to industry (potentially based around a cluster of industrial users of hydrogen) [63] and its use within transport [63]. Biohydrogen production through gasification is significantly more efficient than bioSNG production [63]. Similarly to bioSNG the individual parts of the biohydrogen production process are well-established and tested (although a commercial level facility is not) [21]. The most risky part of the process is the production of a high quality syngas (similarly to bioSNG) and these risks are potentially greater when producing bioSNG due to more sensitive catalysts. Therefore the successful deployment of bioSNG production should give high confidence for the potential to produce biohydrogen [21]. A bioSNG installation has the flexibility to convert to biohydrogen production, and can be converted at a relatively low cost [20]. The carbon savings available through biohydrogen production are greater than bioSNG production (when both are combined with CCS) [63], although the cost for biohydrogen production will likely be higher than bioSNG
An important consideration in the future opportunity for bioSNG production through the route discussed here, which is outside the scope of the current work, is a full assessment of the environmental impacts of such an approach. Whilst work has been conducted on the impact of the gasification process (with a waste derived feedstock and clean biomass feedstock) [65,66,67], this would need to be built on for the case of the feedstock grown on contaminated land. Important additional considerations would be the effect that the land remediation has on the environmental assessment (for different levels of contamination) and how possible increased transport requirements with such a feedstock could impact the findings.
In order to produce energy and power there is a need to think creatively about energy sources. Therefore, a techno economic assessment has been undertaken on the production of energy from crops grown on contaminated soils. The route analysed involves gasification to produce bioSNG. The drivers of such a system are twofold: energy production and land remediation. The work highlights a critical shortcoming in management of contaminated land sites as there is currently no clear information held regarding the whereabouts, type and level of contaminated land in the UK, despite their being a regulatory requirement on local authorities to identify such sites.
The results show that the costs associated with using the system to remediate land are lower than conventional alternatives, but require forward temporal planning which is not often evident or possible. Cost viability, if considered only for energy production, depends on the feedstock selling for a significantly lower price than virgin feedstock, alongside a combination of strong policy incentives, natural gas prices and a long-term demand for gas products. Larger gasifiers are more economically viable, but provision of material grown from contaminated land would be unlikely to fulfil demand. Therefore, coupling systems with waste material as a feedstock is beneficial, but has resultant policy implications as current financial incentives are different for such materials.
If the driver for the system is land remediation, the system can be economically viable compared with alternatives. Additionally, the system can be marginally economically viable if there are sufficient fiscal incentives when only energy production is the driver. Never the less, in most of the scenarios, the results show that in order to be financially viable currently, biomass grown on contaminated land should command a gate fee for processing to bioSNG to be cost effective. Therefore, biomass produced in this manner will effectively become a waste product of land remediation. This has significant implications unless the value of remediation can be captured in the analysis.
The paper has shown how the impact of variable price factors and drivers demonstrate how the techno economic assessment can be used to highlight significant, and varying, contributors to financial success. Although demonstrated here for contaminated land bioenergy production, this approach can be utilised across multiple energy systems in the future.
This research was supported by EPSRC grant number: EP/P024823/1. The authors would like to thank the anonymous reviewers for their suggestions, which have made this a stronger paper. All data is provided in the main paper or supplementary information.
All authors declare no conflicts of interest in this paper.
[1] | gov.uk, Contaminated land (2018) Available from: https://www.gov.uk/contaminated-land. |
[2] | European Environment Agency, Progress in management of contaminated sites (2017) Available from: https://www.eea.europa.eu/data-and-maps/indicators/progress-in-management-of-contaminated-sites-3. |
[3] | Environment Agency (2016) Dealing with contaminated land in England. A review for progress from April 2000 to December 2013 with Part 2A of the Environmental Protection Act 1990. Bristol, UK: Environment Agency. |
[4] | Science Communication Unit, University of the West of England, Bristol, (2013) Science for Environment Policy In-depth Report: Soil Contamination: Impacts on Human Health. European Commission DG Environment. |
[5] | FAO, ITPS (2015) Status of the World's Soil Resources. Rome, Italy: Food and Agriculture Organization of the United Nations and Intergovernmental Technical Panel on Soils. |
[6] | Britt C, Bullard M, Hickman G, et al. (2002) Bioenergy crops and bioremediation - A review. London, UK: Department for Food Environment and Rural Affairs. |
[7] |
Gomes HI (2012) Phytoremediation for bioenergy: challenges and opportunities. Environ Technol Rev 1: 59–66. doi: 10.1080/09593330.2012.696715
![]() |
[8] | Glass DJ (1999) Economic potential of phytoremediation. In: Raskin I, Ensley B, editors. Phytoremediation of toxic metals: using plants to clean up the environment. Chichester, UK: Wiley, 15–31. |
[9] | Van Ginneken L, Meers E, Guisson R, et al. (2007) Phytoremediation for heavy metal‐contaminated soils combined with bioenergy production. J Environ Eng Landsc 15: 227–236. |
[10] |
Evangelou MWH, Conesa HM, Robinson BH, et al. (2012) Biomass Production on Trace Element–Contaminated Land: A Review. Environ Eng Sci 29: 823–839. doi: 10.1089/ees.2011.0428
![]() |
[11] |
Tripathi V, Edrisi SA, Abhilash PC (2016) Towards the coupling of phytoremediation with bioenergy production. Renew Sust Energ Rev 57: 1386–1389. doi: 10.1016/j.rser.2015.12.116
![]() |
[12] |
Pandey VC, Bajpai O, Singh N (2016) Energy crops in sustainable phytoremediation. Renew Sust Energ Rev 54: 58–73. doi: 10.1016/j.rser.2015.09.078
![]() |
[13] | Tangahu BV, Sheikh Abdullah SR, Basri H, et al. (2011) A Review on Heavy Metals (As, Pb, and Hg) Uptake by Plants through Phytoremediation. Int J Chem Eng 2011: 31. |
[14] |
Vervaeke P, Tack FMG, Navez F, et al. (2006) Fate of heavy metals during fixed bed downdraft gasification of willow wood harvested from contaminated sites. Biomass Bioenerg 30: 58–65. doi: 10.1016/j.biombioe.2005.07.001
![]() |
[15] | Zinn E, Thunman H (2016) Göteborg Energi: Vehicle Fuel From Organic Waste. Industrial Biorenewables: John Wiley & Sons, Inc. pp. 255–265. |
[16] | Mozaffarian M, Zwart RWR (2003) Feasibility of biomass/ waste-related SNG production technologies. Petten, The Netherlands: ECN-Biomass Systems. |
[17] | Sadaka S (2017) Gasification, Producer Gas and Syngas. USA: University of Arkansas. |
[18] | ETI (2017) Targetting new and cleaner uses for wastes and biomass using gasification. An ETI insights report. Loughborough, UK: Energy Technologies Institute. |
[19] | van der Meijden CM, Rabou LPLM, Van der Drift A, et al. (2011) Large scale production of bio methane from wood. International Gas Union Research Conference IGRC. Seoul, South Korea. |
[20] | gogreengas (2015) BioSNG Demonstration Plant. Project Close-Down Report. Swindon, UK: gogreengas. |
[21] | Progressive Energy Ltd and Advanced Plasma Power Limited (2017) Biohydrogen: Production of hydrogen by gasification of waste. An NIA assessment of Biohydrogen production and opportunities for implementation on the gas network. Coventry, UK: Cadent Gas Ltd. |
[22] |
McKendry P (2002) Energy production from biomass (part 3): gasification technologies. Bioresource Technol 83: 55–63. doi: 10.1016/S0960-8524(01)00120-1
![]() |
[23] | Progressive Energy and CNG Services (2010) Bio-SNG. Feasibility Study. Establishment of a Regional Project.: NEPIC National Grid and Centrica. |
[24] | Heyne S (2013) Bio-SNG from Thermal Gasification - Process Synthesis, Integration and Performance. Gotebury, Sweden: Chalmers University of Technology. |
[25] | gogreengas (2017) BioSNG Demonstration Plant. Summary of Plant Design. Full scale BioSNG design and assessment of scale-up risks. Swindon, UK: gogreengas. |
[26] | e4tech (2010) The potential for bioSNG production in the UK. NNFCC D. NNFCC project 10/008 NNFCC project 10/008. |
[27] | e4tech (2010) Biomass prices in the heat and electricity sectors in the UK.: Department of Energy and Climate Change. URN 10D/546 URN 10D/546. |
[28] | e4tech (2009) Review of Technologies for Gasification of Biomass and Wastes. NNFCC D. NNFCC project 09/008 NNFCC project 09/008. |
[29] |
Sikarwar VS, Zhao M, Clough P, et al. (2016) An overview of advances in biomass gasification. Energ Environ Sci 9: 2939–2977. doi: 10.1039/C6EE00935B
![]() |
[30] | gogreengas (2015) BioSNG Demonstration Plant. Summary of Technical Results. Results of test and experiments on the demonstration plant. Swindon, UK: gogreengas. |
[31] |
van der Meijden CM, Veringa HJ, Rabou LPLM (2010) The production of synthetic natural gas (SNG): A comparison of three wood gasification systems for energy balance and overall efficiency. Biomass Bioenerg 34: 302–311. doi: 10.1016/j.biombioe.2009.11.001
![]() |
[32] |
Gassner M, Maréchal F (2009) Thermo-economic process model for thermochemical production of Synthetic Natural Gas (SNG) from lignocellulosic biomass. Biomass Bioenerg 33: 1587–1604. doi: 10.1016/j.biombioe.2009.08.004
![]() |
[33] | Advanced Plasma Power (2018) Available from: https://advancedplasmapower.com/. |
[34] | gogreengas (2018) Available from: https://gogreengas.com/. |
[35] | gogreengas (2015) BioSNG Demonstration Plant. Summary of Commercial Results. Commercial model of full scale BioSNG plants. Swindon, UK: gogreengas. |
[36] |
Mleczek M, Rutkowski P, Rissmann I, et al. (2010) Biomass productivity and phytoremediation potential of Salix alba and Salix viminalis. Biomass Bioenerg 34: 1410–1418. doi: 10.1016/j.biombioe.2010.04.012
![]() |
[37] |
Tőzsér D, Magura T, Simon E (2017) Heavy metal uptake by plant parts of willow species: A meta-analysis. J Hazard Mater 336: 101–109. doi: 10.1016/j.jhazmat.2017.03.068
![]() |
[38] |
Keller C, Ludwig C, Davoli F, et al. (2005) Thermal Treatment of Metal-Enriched Biomass Produced from Heavy Metal Phytoextraction. Environ Sci Technol 39: 3359–3367. doi: 10.1021/es0484101
![]() |
[39] | Nzihou A, Stanmore B (2013) The fate of heavy metals during combustion and gasification of contaminated biomass-A brief review. J Hazard Mater 256: 56–66. |
[40] | Gasification and syngas technologies council (2017) Available from: http://www.gasification-syngas.org/. |
[41] | Advanced Plasma Power (2018) Plasmarok - Recovered from the Advanced Plasma Power Gasplasma energy from waste process. Swindon, UK: APP. |
[42] | ofgem, Non-domestic Renewable Heat Incentive (RHI) (2018) Available from: https://www.ofgem.gov.uk/environmental-programmes/non-domestic-rhi. |
[43] | Department for Transport, Renewable Transport Fuel Obligation (2012) Available from: https://www.gov.uk/guidance/renewable-transport-fuels-obligation. |
[44] | ofgem, Tariffs and payments: Non-Domestic RHI (2018) Available from: https://www.ofgem.gov.uk/environmental-programmes/non-domestic-rhi/contacts-guidance-and-resources/tariffs-and-payments-non-domestic-rhi. |
[45] | energy census, [RE]fuel Report (2018) Available from: https://www.energycensus.com/refuel-report/. |
[46] | NNFCC, Biomethane RTFC Calculator (2018) Available from: https://www.nnfcc.co.uk/publications/tool-biomethane-rtfc-calculator. |
[47] | Department for Transport (2018) Renewable Transport Fuel Obligation Guidance Part One Process Guidance. Year 11: 15/4/18 to 31/12/18. |
[48] | Vigil M, Marey-Pérez MF, Martinez Huerta G, et al. (2015) Is phytoremediation without biomass valorization sustainable? - Comparative LCA of landfilling vs. anaerobic co-digestion. Sci Total Environ 505: 844–850. |
[49] | WRAP (2017) Comparing the costs of waste treatment options. Banburr, UK: WRAP. |
[50] |
Edo M, Björn E, Persson P-E, et al. (2016) Assessment of chemical and material contamination in waste wood fuels – A case study ranging over nine years. Waste Manage 49: 311–319. doi: 10.1016/j.wasman.2015.11.048
![]() |
[51] | Department for Business Energy and Industrial Strategy (2017) BEIS 2017 Updated Energy & Emissions Projections. Annex M Growth assumptions and prices. |
[52] | Remer DS, Chai LH (1990) Design cost factors for scaling-up engineering equipment. Chem Eng Prog 86: 77–82. |
[53] |
Sas-Nowosielska A, Kucharski R, Małkowski E, et al. (2004) Phytoextraction crop disposal-an unsolved problem. Environ Pollut 128: 373–379. doi: 10.1016/j.envpol.2003.09.012
![]() |
[54] |
Kuppens T, Van Dael M, Vanreppelen K, et al. (2015) Techno-economic assessment of fast pyrolysis for the valorization of short rotation coppice cultivated for phytoextraction. J Clean Prod 88: 336–344. doi: 10.1016/j.jclepro.2014.07.023
![]() |
[55] | Lievens C, Yperman J, Vangronsveld J, et al. (2008) Study of the potential valorisation of heavy metal contaminated biomass via phytoremediation by fast pyrolysis: Part I. Influence of temperature, biomass species and solid heat carrier on the behaviour of heavy metals. Fuel 87: 1894–1905. |
[56] |
Brooks RR, Chambers MF, Nicks LJ, et al. (1998) Phytomining. Trends Plant Sci 3: 359–362. doi: 10.1016/S1360-1385(98)01283-7
![]() |
[57] | Chaney RL, Angle JS, Broadhurst CL, et al. (2007) Improved Understanding of Hyperaccumulation Yields Commercial Phytoextraction and Phytomining Technologies J Environ Qual 36: 1429–1443. |
[58] |
Šyc M, Pohořelý M, Kameníková P, et al. (2012) Willow trees from heavy metals phytoextraction as energy crops. Biomass Bioenerg 37: 106–113. doi: 10.1016/j.biombioe.2011.12.025
![]() |
[59] | SAC (2008) Agriculture and Rural Development Factsheet. Willow Short Rotation Coppice: Is it commercially viable? |
[60] | KPMG (2016) 2050 Energy Scenarios. The UK Gas Networks role in a 2050 whole energy system. London, UK: KPMG LLP. |
[61] |
Balat H, Kırtay E (2010) Hydrogen from biomass – Present scenario and future prospects. Int J Hydrogen Energ 35: 7416–7426. doi: 10.1016/j.ijhydene.2010.04.137
![]() |
[62] |
Ni M, Leung DYC, Leung MKH, et al. (2006) An overview of hydrogen production from biomass. Fuel Process Technol 87: 461–472. doi: 10.1016/j.fuproc.2005.11.003
![]() |
[63] | Progressive Energy Ltd (2017) The Liverpool-Manchester Hydrogen Cluster: A Low Cost, Deliverable Project. Coventry, UK: Cadent. |
[64] | Northern Gas Networks, Wales & west Utilities, KIWA, et al. (2016) H21 Leeds City Gate. Northern Gas Networks. |
[65] |
Evangelisti S, Tagliaferri C, Clift R, et al. (2015) Integrated gasification and plasma cleaning for waste treatment: A life cycle perspective. Waste Manage 43: 485–496. doi: 10.1016/j.wasman.2015.05.037
![]() |
[66] |
Evangelisti S, Tagliaferri C, Clift R, et al. (2015) Life cycle assessment of conventional and two-stage advanced energy-from-waste technologies for municipal solid waste treatment. J Clean Prod 100: 212–223. doi: 10.1016/j.jclepro.2015.03.062
![]() |
[67] |
Tagliaferri C, Evangelisti S, Clift R, et al. (2016) Life cycle assessment of conventional and advanced two-stage energy-from-waste technologies for methane production. J Clean Prod 129: 144–158. doi: 10.1016/j.jclepro.2016.04.092
![]() |
![]() |
![]() |
1. | Helena Moreira, Sofia I. A. Pereira, Michel Mench, Carlos Garbisu, Petra Kidd, Paula M. L. Castro, Phytomanagement of Metal(loid)-Contaminated Soils: Options, Efficiency and Value, 2021, 9, 2296-665X, 10.3389/fenvs.2021.661423 | |
2. | Ana Ramos, Abel Rouboa, Life cycle thinking of plasma gasification as a waste-to-energy tool: Review on environmental, economic and social aspects, 2022, 153, 13640321, 111762, 10.1016/j.rser.2021.111762 | |
3. | Marina Stella Silva Pimenta, Francis Lebreux Desilets, Adriano Pinto Mariano, Virginie Chambost, Alain Boutet, Paul R. Stuart, Competitive assessment of biofuel strategies for a case study in eastern Canada: techno‐economic and multi‐criteria decision‐making analysis, 2025, 1932-104X, 10.1002/bbb.2729 |
Parameter | Unit | Value | Min | Max |
Load factor | Proportion | 0.9 | 0.85 | 0.95 |
Hurdle rate | Percentage | 10% | 8% | 12% |
Lifetime | Years | 25 | 20 | 30 |
Capital cost for 76 MW bioSNG output installation | £million | 150.7 | 105.5 | 195.9 |
Capital cost scaling factor | - | 0.6 | 0.5 | 0.7 |
Labour cost for 76 MW bioSNG output installation | £million/year | 1.8 | 1.3 | 2.3 |
Labour cost scaling factor | - | 0.15 | 0.1 | 0.2 |
Consumables costs for 76 MW bioSNG output installation | £million/year | 3.1 | 2.2 | 4.0 |
Consumables costs scaling factor | - | 1 | 0.9 | 1 |
Maintenance costs for 76 MW bioSNG output installation | £million/year | 2.9 | 2.0 | 3.8 |
Maintenance costs scaling factor | - | 0.6 | 0.5 | 0.7 |
Other operating costs for 76 MW bioSNG output installation | £million/yr | 3.5 | 2.5 | 4.6 |
Other operating costs scaling factor | - | 0.6 | 0.5 | 0.7 |
Gross efficiency | output bioSNG per input of feedstock energy | 64% | 57% | 70% |
Natural gas energy demand | input required per unit of bioSNG output | 0.01 | 0.009 | 0.011 |
Electricity demand required | input required per unit of bioSNG output | 0.095 | 0.086 | 0.105 |
Wholesale gas price | £/GJ | 7.05 | 3.58 | 8.73 |
Electricity price (retail, industry) | £/GJ | 36.01 | 29.64 | 39.03 |
Natural gas retail price | £/GJ | 10.97 | 6.15 | 12.9 |
Energy density willow | GJ/odt | 18 | ||
Policy support RTFC | £/GJ bioSNG | 15.2 | 7.6 | 22.8 |
Policy support RHI | £/GJ bioSNG | 10.1 | 7.8 | 17.3 |
Feedstock cost (£/t) | 20 MW output | 50 MW output |
−50 | 66% | 99.5% |
0 | 15% | 78% |
10 | 9% | 68% |
30 | 2% | 44% |
50 | 0.3% | 22% |
80 | 0% | 4% |
Parameter | Unit | Value | Min | Max |
Load factor | Proportion | 0.9 | 0.85 | 0.95 |
Hurdle rate | Percentage | 10% | 8% | 12% |
Lifetime | Years | 25 | 20 | 30 |
Capital cost for 76 MW bioSNG output installation | £million | 150.7 | 105.5 | 195.9 |
Capital cost scaling factor | - | 0.6 | 0.5 | 0.7 |
Labour cost for 76 MW bioSNG output installation | £million/year | 1.8 | 1.3 | 2.3 |
Labour cost scaling factor | - | 0.15 | 0.1 | 0.2 |
Consumables costs for 76 MW bioSNG output installation | £million/year | 3.1 | 2.2 | 4.0 |
Consumables costs scaling factor | - | 1 | 0.9 | 1 |
Maintenance costs for 76 MW bioSNG output installation | £million/year | 2.9 | 2.0 | 3.8 |
Maintenance costs scaling factor | - | 0.6 | 0.5 | 0.7 |
Other operating costs for 76 MW bioSNG output installation | £million/yr | 3.5 | 2.5 | 4.6 |
Other operating costs scaling factor | - | 0.6 | 0.5 | 0.7 |
Gross efficiency | output bioSNG per input of feedstock energy | 64% | 57% | 70% |
Natural gas energy demand | input required per unit of bioSNG output | 0.01 | 0.009 | 0.011 |
Electricity demand required | input required per unit of bioSNG output | 0.095 | 0.086 | 0.105 |
Wholesale gas price | £/GJ | 7.05 | 3.58 | 8.73 |
Electricity price (retail, industry) | £/GJ | 36.01 | 29.64 | 39.03 |
Natural gas retail price | £/GJ | 10.97 | 6.15 | 12.9 |
Energy density willow | GJ/odt | 18 | ||
Policy support RTFC | £/GJ bioSNG | 15.2 | 7.6 | 22.8 |
Policy support RHI | £/GJ bioSNG | 10.1 | 7.8 | 17.3 |
Feedstock cost (£/t) | 20 MW output | 50 MW output |
−50 | 66% | 99.5% |
0 | 15% | 78% |
10 | 9% | 68% |
30 | 2% | 44% |
50 | 0.3% | 22% |
80 | 0% | 4% |