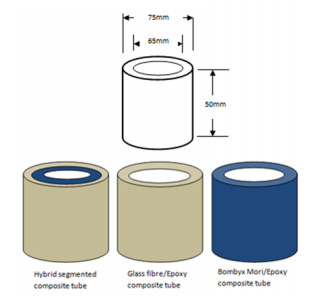
Citation: Albert Uchenna Ude, Che Husna Azhari. Crashworthiness response of natural silk-fibre glass hybrid reinforced epoxy cylindrical composite tubes under quasi-static load[J]. AIMS Materials Science, 2019, 6(5): 852-863. doi: 10.3934/matersci.2019.5.852
[1] | Albert Uchenna Ude, Che Husna Azhari . Lateral crashworthiness response of bombyx mori fibre/glass–fibre/epoxy hybrid composite cylindrical tubes-experimental. AIMS Materials Science, 2019, 6(6): 1227-1239. doi: 10.3934/matersci.2019.6.1227 |
[2] | Prashant Tripathi, Vivek Kumar Gupta, Anurag Dixit, Raghvendra Kumar Mishra, Satpal Sharma . Development and characterization of low cost jute, bagasse and glass fiber reinforced advanced hybrid epoxy composites. AIMS Materials Science, 2018, 5(2): 320-337. doi: 10.3934/matersci.2018.2.320 |
[3] | Ruaa Al-Mezrakchi, Ahmed Al-Ramthan, Shah Alam . Designing and modeling new generation of advanced hybrid composite sandwich structure armors for ballistic threats in defense applications. AIMS Materials Science, 2020, 7(5): 608-631. doi: 10.3934/matersci.2020.5.608 |
[4] | Kator Jeff Jomboh, Adele Dzikwi Garkida, Emmanuel Majiyebo Alemaka, Mohammed Kabir Yakubu, Vershima Cephas Alkali, Wilson Uzochukwu Eze, Nuhu Lawal . Properties and applications of natural, synthetic and hybrid fiber reinforced polymer composite: A review. AIMS Materials Science, 2024, 11(4): 774-801. doi: 10.3934/matersci.2024038 |
[5] | Mohammed Y. Abdellah, Hamzah Alharthi, Mohamed K. Hassan, Ahmed F. Mohamed . Effect of specimen size on natural vibration of open hole copper/glass-reinforced epoxy laminate composites. AIMS Materials Science, 2020, 7(4): 499-517. doi: 10.3934/matersci.2020.4.499 |
[6] | Iketut Suarsana, Igpagus Suryawan, NPG Suardana, Suprapta Winaya, Rudy Soenoko, Budiarsa Suyasa, Wijaya Sunu, Made Rasta . Flexural strength of hybrid composite resin epoxy reinforced stinging nettle fiber with silane chemical treatment. AIMS Materials Science, 2021, 8(2): 185-199. doi: 10.3934/matersci.2021013 |
[7] | Alessandro De Luca, Francesco Caputo . A review on analytical failure criteria for composite materials. AIMS Materials Science, 2017, 4(5): 1165-1185. doi: 10.3934/matersci.2017.5.1165 |
[8] | Ahmed Ali Farhan Ogaili, Ehsan S. Al-Ameen, Mohammed Salman Kadhim, Muhanad Nazar Mustafa . Evaluation of mechanical and electrical properties of GFRP composite strengthened with hybrid nanomaterial fillers. AIMS Materials Science, 2020, 7(1): 93-102. doi: 10.3934/matersci.2020.1.93 |
[9] | Venkatarajan Subbarayalu, Subbu Chinnaraman, Athijayamani Ayyanar, Jayaseelan Chinnapalanisamy . Mechanical properties of vinyl ester hybrid composite laminates reinforced with screw pine and glass fiber. AIMS Materials Science, 2024, 11(1): 114-128. doi: 10.3934/matersci.2024007 |
[10] | Neerajkumar Wayzode, Vinod Suryawanshi . Mechanical properties of graphene nanoplatelets reinforced glass/epoxy composites manufactured using resin film infusion process. AIMS Materials Science, 2023, 10(4): 693-709. doi: 10.3934/matersci.2023038 |
The demand for reinforced composites of high structural efficiency, capable of impact energy attenuation and possessing good crashworthiness has become of great interest in a number of industries including aerospace, automobile, shipping and sport industries to mention but a few. Fibre reinforced plastic (FRP) composite structural members play a major role in today's aerospace, automobile and advanced manufacturing systems because of their perceived advantages. These advantages include high strength to weight ratio, light weight compared to more traditional materials, and superior shock absorbing behaviour [1,2,3,4]. The energy attenuation characteristics of such member are vital for structural applications, especially when they are subjected to impact loading or collision with external objects. Their ability to absorb impact energy as they deform during impact results in less structural damage to other component parts or even occupants of the assembly. The investigation of crashworthiness parameter in composite structures is meant to predict the load carrying capability of such structures in other to avert disastrous or massive damage and protect the occupants in an event of collusion.
Research works in recent decades have shown that the use of fibre-reinforced plastic composite materials in automotive, marine and aerospace industries may result in significant efficient and economic benefits. These benefits include lower fuel consumption due to reduced structural weight and durability due to strength and stiffness properties [5,6,7,8]. Owing to these merits, attention has been devoted to using FRP composites for the enhancement of vehicle structural crashworthiness by their appliances in particular aerospace and automobile parts to serve as collapsible energy absorbers in an event of crash or collision with external objects [3]. They are both used as structural members that are able to absorb large amount of energy while deforming progressively in a controlled manners.
A review of previous investigations show that the study of crashworthiness parameters of diverse thin-walled tubes made from a range of fibre reinforced composites in various shapes and sizes has been carried out [2,4,9,10,11,12,13,14,15,16,17]. It was evidence from this review that most FRP composite fail in a brittle manner under axial compression load unlike their metallic counterpart which fails plastically. One common denominator among the composite structures is the predominant micro-cracks which initiates the unset of structural failures. Other reports from the literatures also indicated that FRP composite failure modes depend on the shape, size, material characteristics, environmental condition and the test parameters employed [7,15,16,18,19,20,21,22].
The search for an optimum FRP composite structure with supper superior crashworthy and energy attenuation properties is still a very viable current research area. Though, this search has led to many notable improvements and has increased tremendously the application of FRP composites in many aerospace and automobile components and parts. We have looked at natural silk fibre composite square tubes, triggered and non-triggered, cylindrical tubes under axial compression and low velocity impact of square plates in our previous investigation [2,3,4,17,23,24].
It is true that extensive research on failure behaviour and energy absorption of composite materials in diverse geometry has been investigated, but no report was found on fibre-glass (FG)/natural silk fibre (NS)/epoxy hybrid composite cylindrical tubes subjected to an axial quasi-static compression. Therefore the innovation of this research work was the characterization of fibre-glass/natural silk/epoxy hybrid composite. In this present investigation, fibre glass/natural silk/epoxy hybrid cylindrical composite tubes have been investigated and analyzed. Since the superior compression advantage of fibre glass and the tensile advantage of natural silk fibre were combined to fabricate the composite tube, better crashworthy characteristics is expected. The present study will then focus on which structure has the most functional crashworthy properties by absorbing the crushing energy in a safe and progressive manner and to determine the failure mechanism of the structures by comparing fibre-glass composite tubes, natural silk fibre composite tubes and FG/NS/epoxy hybrid composite tubes.
Three categories of specimen were used in this study; each set consist of 3 composite tubes made of the same composite materials. The first sets were made up of woven natural silk/epoxy cylindrical composite tubes consisting of 15 layers of woven natural silk (NS) fabric from Bombyx mori fibres and epoxy resin matrix (for more details on natural silk properties please refer to [2,4]). The second sets were fibre-glass tubes consisting of 5 layers of fibre-glass/epoxy and the third sets were NS/FG/epoxy hybrid composite tubes consisting of 9 layers of NS and 3 layers of GF. The length of each tube was 50 mm with a thickness of 10 mm and internal diameter of 65 mm. The schematic diagrams of the cylindrical composite tubes are shown in Figure 1.
The axial quasi-static tests were performed using a fully automated INSTRON MTS 810 universal testing machine with 250 kN loading capacity. All tests were performed at a constant test crosshead speed of 20 mm/min. There were no special conditioning of the specimen used in performing the test. The ambient condition of the laboratory at the time of the test was within the acceptable range. Temperature was between 23 to 26 ℃ and humidity was between 50% to 60%. All samples are placed between two rigid steel flat plates; three samples of each composite specimen are tested and the average value was recorded. The crushing load-displacement curve of each specimen is obtained from the computer software attached to the test machine. The absorbed energy is calculated by numerical integration of the load-displacement curve. The mean crushing load is decided by dividing the value of the absorbed energy by the crushing length.
Axial quasi-static compression on cylindrical composite tube configurations were carried out to assess the crashworthiness of the tubes. The amount of load which a structure can carry under quasi-static experimental crushing test can be considered through two load levels observed in a load versus displacement curve. The first load level is the initial crushing load, and the second load level is the average crushing load. The initial crushing load can be obtained directly from the load-displacement reaction, while the average crushing load can be obtained by averaging the crush load values over the crush displacements through the post-crush zone. There are three vital zones which help to interpret the load-displacement curve of any composite material specimen under quasi-static experimental test. First is the pre-crushing zone which indicates the elastic behaviour/nature of the composite material. The material seems to obey Hook's law at this zone. Once there is an initiation of failure in any part of the specimen, it marks the end of the zone. The second zone is known as the post-crushing zone; under this zone cyclic loads are prevalent indicating the spread of failure across the length of the specimen. These cyclic loads are categorized as average crushing loads. The third zone is known as the compaction zone, the crushed residue of the specimen compacts together leading to sudden increase in the load-displacement curve under this zone.
The crushing history and the load versus displacement curve behaviours of the axially compression crushing test for each composite configuration are shown in Figures 2–4. The photos depicting the crushing history are shown in Figures 2–4a while the load-displacement curves correlating with the crushing photos are shown in Figures 2–4b for easy viewing and analysis. From the evaluation of the load-displacement response of the tested specimens, it is possible to quantify the crashworthiness performance of the composite tubes by estimating the values of parameters such as peak load, average load, total and specific energy absorption as well as crushing force efficiency. A general observation show that all 3 composite tube configuration load-displacement curves behaved linearly until they reached the first peak load, then followed by sharp drops of the curve which signifies the inception of deformation in the tube. For fibre-glass/epoxy (FG/E) composite, the sharp drop occurred at 70 kN, 2.53 mm displacement; natural silk/epoxy (NS/E) composite at 34.83 kN, 2.03 mm displacement and fibre-glass/NS/epoxy hybrid composite at 186.97 kN, 3.04 mm displacement, respectively (see Figures 2-4b).
Observations showed in Figure 2a under FG/E composite tube specimen when the linear curve approached the first peak load value. Micro cracks were first initiated at the top of the composite tube due to the built up of local stress concentration around the metal plate-composite tube contact face. The initiation of cracks marked the end of linear curve at first peak. With further quasi-static compressive load on the tube, the micro cracks propagated into macro cracks downwards along the tube length forming outward fronds and displaying average crushing load oscillation along the curve. The fluctuating load value continued until the second peak was reached at 36.9 mm displacement and 99.5 kN peak load value (see Figure 2b). In the case of NS/E composite tube specimen Figure 3a, crack formation also began from the top of the tube, then propagated mid-way along the tube length, causing mid-length deformation and outside frond failure. The curve behaved in a similar manner as the FG/E until it reached a second peak value at 39.9 mm displacement and 86.9 kN peak load value (see Figure 3b). The hybrid composite specimen in Figure 4a behaved a little differently from the previous two specimens reported. Cracks and delamination of the laminate started from the bottom contact surface of the tube. Crushing was noticed from both side of the tube length as the deformation continued. The load-displacement curve behaved partially in similar manner like the two previous until it reached a second peak value at 39.8 mm displacement and 151 kN peak load value (see Figure 4b).
In other to correctly assess the crashworthiness performance of a thin-walled composite tube, parameters such as peak and average crush load, specific absorbed energy, total absorbed energy, generated during the test are interpreted and discussed.
Peak load is one of the most important parameters used in assessing the crushing behaviour of any thin-walled tube. This is because that data from load response can reveal the structural integrity at low-speed or even low energy collision/impact of the tube. It is always satisfying for a structure not to have permanent deformation after impact, as this deformation would be considered as adverse damage and bad attribute of the tubes structural integrity. Factors that influence the peak load values include the type of reinforcement involved, the fibre volume content, and the type of stacking sequence used. In the present investigation, the initial peak load and the average crushing load value for fibre glass (FG/epoxy) composite are 99.5 and 61.4 kN; NS/epoxy composite is 86.9 and 23.8 kN, and FG/NS/epoxy hybrid composite is 151 and 91.5 kN respectively as shown in Figure 5. As expected, the hybrid composite showed better performance in both peak and average load response while fibre glass performed better than natural silk fibre. Observation also showed that natural silk fibre composite tubes showed better progressive crushing behaviour.
Energy absorption response of a thin-wall composite structure is measured on the basis of the absorbed energy (Eabs) per unit mass (Munit) of the composite structure, known as specific energy absorption (SEA) and defined mathematically in Eq 1 as:
SEA=Absorbed energyMass of tube=EabsMunit | (1) |
The linear movement characteristics shown on the load-displacement curves were attributed to load attenuation via elastic strain energy in each composite tube configuration. Figure 6 show the values (SEA) of natural silk fibre, fibre-glass and NS/FG/ hybrid composites, plotted in chart form. It was observed that the hybrid composite tube was a better energy absorber than the others, this was expected.
Total energy absorption (Tmax), is measure of the total strain energy absorbed by the composite structure during the crushing test, and can be estimated as shown in Eq 2 using the area under the load-displacement curve expressed mathematically as:
Tmax=∫lmax0P(l)dl | (2) |
where P(l) is the instant crushing load and lmax is the total displacement.
Figure 7 shows the distribution of the total energy absorption capability of axially crushed composite tubes in diverse materials configurations. Fibre-glass/epoxy (FG) composite had an estimated value of 2457.367 J. Natural silk fibre/epoxy 950.033 J and FG/NS/epoxy hybrid had an estimated value of 3660.216 J, respectively. As depicts in the calculated values, hybrid epoxy composite tube absorbed more energy than the other two non-hybrid tubes.
Hybrid composite materials refers to the combination of two or more materials constituent at nanometre, molecular, micro or macro level to develop better material properties than each original constituent. Owing to this advantage, the hybrid composite which contains two or more types of fibre will certainly have more material property benefits as they will complement with what is lacking in each other. The hybrid composite strength depends upon the properties of the reinforcing fibres orientations, the fibre volume content, length of distinct fibres, sequential arrangement of the fibres and fibre to matrix interface bonding [25]. The difficulty of selecting the well-matched fibres and the level of their properties is the most important aspect when designing and fabricating hybrid composite, but it became possible to develop new hybrid composite material with elevated properties with careful arrangements of these parameters.
In summary, composite materials are preferred in impact energy applications due to its ability to absorb impact energy while deforming. The three composite configurations tested in this study absorbed energy through their different failure mechanisms. Observation showed that FG/epoxy composite absorbed its energy through progressive crushing mode. NS/epoxy composite absorbed via mid-length fracture and progressive crushing mode while FG/NS/epoxy hybrid composite absorbed its energy through laminate delamination and progressive crushing mode.
The crush force efficiency (CFE) is the ratio mean for crushing force (Pmean) which is divided by the crushing force or fist peak load (Pmax), see Eq 3:
CFE=PmeanPmax=FmeanFmax×100 | (3) |
The values calculated from this mathematical expression are very important in choosing superior crashworthy materials. The estimated value always ranges between 0 and 1.0. Very small values suggest a catastrophic of fracture failure mode while large values suggest progressive deformation failure mode. Figure 8 shows the chart of the data obtained from the calculation since different materials were involved. Varied data were also expected. Fibre-glass/epoxy composite tube generated approximately 0.6. Natural silk/epoxy composite tube generated approximately 0.3 and fibre-glass/natural silk/epoxy hybrid composite tube generated 0.5, respectively.
Diverse types of composite materials currently being used as structural materials in passenger vehicles, transportation of goods vehicles, aerospace industries and other industries, have extensively experienced the forces of progressive deformation and stable collapse. Basically, two type of failure mode mechanism exist in normal fibre reinforced polymer composite (FRPC). The first type is a progressive folding similar to ductile metallic or plastic tube formation. The second type of failure mode is a combination of fracture where most of the energy absorber composite tubes experience initially micro-fracture which later propagate into macro-fracture and is known as progressive crushing failure mode. However, Mamalis et al. [22] identified three distinct collapse mode namely in their investigation: Mode Ⅰ, Mode Ⅱ, and Mode Ⅲ representing end-crushing or delamination mode, mid-length collapse mode, and mixed mode of collapse failure mode. Another study by Weaver and Ashby as reported by [25], concluded that there are three main failure mechanisms of tubular structure under axial load, which was local buckling failure mode, global bucking failure mode, yield/fracture failure mode and axial crushing failure mode.
Figure 9 shows photographs of the collapse modes observed in the present investigation of cylindrical composite tubes. Natural silk composite tube experienced a circumferential fracture believed to have been initiated from a micro-macro crack due to axial applied load. This type of failure mode agreed to Mamalis Mode Ⅲ or Fracture/Yield of Weaver and Ashby investigations. Fibre glass composite tube showed top-bottom end-crushing collapse behaviour, which agreed with Mode Ⅰ of Mamalis' study. The hybrid material (natural silk/fibre glass hybrid) composite tube which is the main focus of this investigation showed top end-crushing failure mode and bottom end delamination collapse failure mode, a combination of Mode Ⅰ and Mode Ⅲ as suggested by Mamalis. This behaviour is attributed to the hybridization nature of the composite tube material. The residues of the collapsed tubes were also observed and investigated. Natural silk showed a ductile behaviour; Fibre glass showed a brittle behaviour while the hybrid showed a mixed behaviour of both brittle and ductile nature (see Figure 9).
The study to investigate the crashworthiness of natural silk fibre, fibre glass and natural silk/fibre glass hybrid reinforced epoxy cylindrical composite tubes has been investigated and analyzed, the following conclusions were made:
A comparison of the peak and average loads of the composite cylindrical tubes show that NS/FG hybrid reinforced epoxy composite tube, displayed superior peak and average load compared to only natural silk and only fibre glass reinforced composite tubes, this characteristic is attributed to the hybridization nature of the composite tube.
Total and specific energy absorption of the three (3) composite tube specimens tested were compared. The result show that NS/FG hybrid reinforced epoxy composite tube absorbed more energy with 51.8%, followed by fibre glass composite tubes with 43.8% and finally natural silk composite tubes with 13.4%. This performance is also attributed to the hybrid nature of the composite tube under investigation.
The crushing efficiencies of the tested composite tubes have been compared. The result shows that FG/epoxy composite tube has slightly better crashworthiness capability than NS/FG/epoxy hybrid and natural silk composite tubes. This is attributed to the superior compressive load absorption capability of fibre glass.
The three configuration of tested specimen showed diverse modes of collapse. Natural silk composite tube experienced a circumferential fracture believed to have been initiated from a micro-macro crack due to axial applied load and end-crushing failure mode. Fibre glass composite tube showed top-bottom end-crushing collapse behaviour, and natural silk/fibre glass/epoxy hybrid showed top end-crushing failure mode and bottom end delamination collapse failure mode, a mixture of Mode Ⅰ and Mode Ⅲ failure mode as suggested by Mamalis. This characteristic is also attributed to the hybridization nature of the tube.
No potential conflict of interest was reported by the authors.
[1] |
Ude A, Azhari C (2013) Experimental investigation on the response of woven natural silk fiber/epoxy sndwich composite panels under low velocity impact. Fiber Polym 14: 127-132. doi: 10.1007/s12221-013-0127-2
![]() |
[2] |
Eshkoor R, Ude A, Oshkovr S, et al. (2014) Failure mechanism of woven natural silk/epoxy rectangular composite tubes under axial quasi-static crushing test using trigger mechanism. Int J Impact Eng 64: 53-61. doi: 10.1016/j.ijimpeng.2013.09.004
![]() |
[3] |
Eshkoor R, Ude A, Sulong A, et al. (2015) Energy absorption and load carrying capability of woven natural silk epoxy-triggered composite tubes. Compos Part B-Eng 77: 10-18. doi: 10.1016/j.compositesb.2015.03.017
![]() |
[4] |
Ude A, Ariffin A, Azhari C (2013) Impact damage characteristics in reinforced woven natural silk/epoxy composite face-sheet and sandwich foam, coremat and honeycomb materials. Int J Impact Eng 58: 31-38. doi: 10.1016/j.ijimpeng.2013.03.003
![]() |
[5] |
Eshkoor R, Oshkovr S, Sulong A, et al. (2013) Comparative research on the crashworthiness characteristics of woven natural silk/epoxy composite tubes. Mater Design 47: 248-257. doi: 10.1016/j.matdes.2012.11.030
![]() |
[6] |
Eshkoor R, Oshkovr S, Sulong A, et al. (2013) Effect of trigger configuration on the crashworthiness characteristics of natural silk epoxy composite tubes. Compos Part B-Eng 55: 5-10. doi: 10.1016/j.compositesb.2013.05.022
![]() |
[7] |
Zhou J, Guan Z, Cantwell W (2018) The energy-absorbing behaviour of composite tubereinforced foams. Compos Part B-Eng 139: 227-237. doi: 10.1016/j.compositesb.2017.11.066
![]() |
[8] |
Alkbir M, Sapuan S, Nuraini A, et al. (2016) Fibre properties and crashworthiness parameters of natural fibre-reinforced composite structure: A literature review. Compos Struct 148: 59-73. doi: 10.1016/j.compstruct.2016.01.098
![]() |
[9] |
Abdewi EF, Sulaiman S, Hamouda AMS, et al. (2008) Quasi-static axial and lateral crushing of radial corrugated composite tubes. Thin Wall Struct 46: 320-332. doi: 10.1016/j.tws.2007.07.018
![]() |
[10] | Abosbaia A, Mahdi E, Hamouda A, et al. (2008) Energy absorption capability of laterally loaded segmented composite tubes. Compos Struct 70: 356-373. |
[11] |
Duarte I, Vesenjak M, Krstulović-Opara L, et al. (2015) Static and dynamic axial crush performance of in-situ foam-filled tubes. Compos Struct 124: 128-139. doi: 10.1016/j.compstruct.2015.01.014
![]() |
[12] |
Kim H, Shin D, Lee J, et al. (2014) Crashworthiness of aluminum/CFRP square hollow section beam under axial impact loading for crash box application. Compos Struct 112: 1-10. doi: 10.1016/j.compstruct.2014.01.042
![]() |
[13] |
Liu Q, Xing H, Ju Y, et al. (2014) Quasi-static axial crushing and transverse bending of double hat shaped CFRP tubes. Compos Struct 117: 1-11. doi: 10.1016/j.compstruct.2014.06.024
![]() |
[14] |
Mahdi E, Hamouda A, Sen A (2004) Quasi-static crushing behaviour of hybrid and nonhybrid natural fibre composite solid cones. Compos Struct 66: 647-663. doi: 10.1016/j.compstruct.2004.06.001
![]() |
[15] |
Mamalis A, Manolakos D, Ioannidis M, et al. (2009) On the crashworthiness of composite rectangular thin-walled tubes internally reinforced with aluminium or polymeric foams: Experimental and numerical simulation. Compos Struct 89: 416-423. doi: 10.1016/j.compstruct.2008.09.008
![]() |
[16] | Mamalis A, Manolakos D, Ioannidis M, et al. (2005) Crashworthy characteristics of axially statically compressed thin-walled square CFRP composite tubes: experimental. Compos Struct 63: 347-360. |
[17] |
Oshkovr S, Eshkoor R, Taher S, et al. (2012) Crashworthiness characteristics investigation of silk/epoxy composite square tubes. Compos Struct 94: 2337-2342. doi: 10.1016/j.compstruct.2012.03.031
![]() |
[18] |
Striewe J, Reuter C, Sauerland K, et al. (2018) Manufacturing and crashworthiness of fabric-reinforced thermoplastic composites. Thin Wall Struct 123: 501-508. doi: 10.1016/j.tws.2017.11.011
![]() |
[19] |
Kathiresan M, Manisekar K (2017) Low velocity axial collapse behavior of E-glass fiber/epoxy composite conical frusta. Compos Struct 166: 1-11. doi: 10.1016/j.compstruct.2017.01.041
![]() |
[20] |
Zhang Z, Sun W, Zhao Y, et al. (2018) Crashworthiness of different composite tubes by experiments and simulations. Compos Part B-Eng 143: 86-95. doi: 10.1016/j.compositesb.2018.01.021
![]() |
[21] |
Mamalis A, Manolakos D, Ioannidis M, et al. (2005) On the response of thin-walled CFRP composite tubular components subjected to static and dynamic axial compressive loading: experimental. Compos Struct 69: 407-420. doi: 10.1016/j.compstruct.2004.07.021
![]() |
[22] |
Mamalis A, Robinson M, Manolakos D, et al. (1997) Crashworthy capability of composite material structures. Compos Struct 37: 109-134. doi: 10.1016/S0263-8223(97)80005-0
![]() |
[23] |
Oshkovr S, Taher S, Oshkour A, et al. (2013) Finite element modelling of axially crushed silk/epoxy composite square tubes. Compos Struct 95: 411-418. doi: 10.1016/j.compstruct.2012.07.032
![]() |
[24] |
Ude A, Eshkoor R, Azhari C (2017) Crashworthy characteristics of axial quasi-statically compressed Bombyx mori composite cylindrical tubes: experimental. Fiber Polym 18: 1594-1601. doi: 10.1007/s12221-017-1235-1
![]() |
[25] | Supian A, Sapuan S, Zuhri M, et al. (2018) Hybrid reinforced thermoset polymer composite in energy absorption tube application: A review. Def Technol 281: 112-118. |
1. | A.B.M. Supian, S.M. Sapuan, M.Y.M. Zuhri, E.S. Zainudin, H.H. Ya, H.N. Hisham, Effect of winding orientation on energy absorption and failure modes of filament wound kenaf/glass fibre reinforced epoxy hybrid composite tubes under intermediate-velocity impact (IVI) load, 2021, 10, 22387854, 1, 10.1016/j.jmrt.2020.11.103 | |
2. | Mohamed Ibrahim Abd El Aal, Mahmoud M. Awd Allah, Marwa A. Abd El‐baky, Carbon‐glass reinforced epoxy hybrid composites for crashworthy structural applications, 2023, 0272-8397, 10.1002/pc.27290 | |
3. | Roberta M. Neves, Francisco M. Monticeli, José Humberto S. Almeida, Heitor Luiz Ornaghi, 2021, Chapter 1, 978-981-16-1853-6, 1, 10.1007/978-981-16-1854-3_1 | |
4. | Athul Joseph, Vishwas Mahesh, Vinyas Mahesh, Dineshkumar Harursampath, MAR Loja, Sumit Bhowmik, 2024, 9780323918664, 169, 10.1016/B978-0-323-91866-4.00003-2 | |
5. | Monica Capretti, Giulia Del Bianco, Valentina Giammaria, Simonetta Boria, Alessandro Scattina, Giovanni Belingardi, Vincenzo Castorani, Crashworthiness of flax and hybrid composite tubes subjected to quasi-static axial crushing: Experimental and numerical results, 2025, 354, 02638223, 118785, 10.1016/j.compstruct.2024.118785 |